DOI:
10.1039/D0RA03800H
(Paper)
RSC Adv., 2020,
10, 28100-28105
Preparation of Ni-IL/SiO2 and its catalytic performance for one-pot sequential synthesis of 2-propylheptanol from n-valeraldehyde
Received
28th April 2020
, Accepted 20th July 2020
First published on 28th July 2020
Abstract
A novel silica-immobilized nickel and acid ionic liquid (Ni-IL/SiO2) catalyst was prepared by combining a bonding procedure with an impregnation operation and was characterized by means of X-ray diffraction (XRD), Fourier transform infrared (FT-IR) spectra, X-ray photoelectron spectroscopy (XPS) and thermogravimetric analysis (TGA) techniques. Its catalytic performance was evaluated for the one-pot synthesis of 2-propylheptanol (2-PH) via a sequential n-valeraldehyde self-condensation and hydrogenation reaction. As a result, Ni-IL/SiO2 showed an excellent catalytic activity for the one-pot synthesis of 2-PH, affording a 2-PH selectivity of 75.4% at a n-valeraldehyde conversion of 100% and the sum of 2-PH and pentanol selectivity reached 98.6% under the suitable reaction conditions.
1. Introduction
2-Propylheptanol (2-PH), an important plasticizer alcohol, can be used for synthesizing a series of plasticizers by esterification with phthalic anhydride, trimellitic anhydride and adipic acid, etc. Bis(2-propylheptyl) phthalate (DPHP) is a major 2-PH-derived plasticizer. Compared with dioctyl phthalate (DOP) derived from 2-ethylhexanol, DPHP has the advantages of low toxicity and less volatility and can meet the requirements for health, safety and environmental protection.1 The industrial production of 2-PH mainly includes three reaction steps: hydroformylation of butene, self-condensation of n-valeraldehyde, and hydrogenation of 2-propyl-2-heptenal. One-pot synthesis of 2-PH by sequential aldol condensation and hydrogenation reaction from n-valeraldehyde can shorten the process flow, reduce energy consumption, and lower equipment and operating costs. So the one-pot synthesis of 2-PH is of academic and commercial importance.
The one-pot synthesis of 2-PH by sequential aldol condensation and hydrogenation from n-valeraldehyde is categorized as a type of reaction integration. At present, the research on the reaction integration of n-valeraldehyde self-condensation and 2-propyl-2-heptenal hydrogenation is rarely reported. Instead some researchers including our group have investigated a similar reaction integration of n-butyraldehyde self-condensation and sucessive hydrogenation.2–8 Liang et al.4 studied this reaction integration using a bifunctional catalyst of Ni/Ce–Al2O3 and realized one-step synthesis of 2-ethylhexanol from n-butyraldehyde, attaining a 2-ethylhexanol selectivity of 66.9% at a n-butyraldehyde conversion of 100%. Li et al.5,6 obtained similar 2-ethylhexanol selectivity and n-butyraldehyde conversion over Ni/La–Al2O3 catalyst for one-pot sequential synthesis of 2-ethylhexanol. Patankar et al.7 prepared a Cu–Mg–Al catalyst for this reaction integration and obtained a 2-ethylhexanol selectivity of 90% at a 30% of n-butyraldehyde conversion. Miao et al.8 obtained a 2-ethylhexanol selectivity of 73.5% at a complete n-butyraldehyde conversion using a Cu–Mg–Fe catalyst for one-step synthesis of 2-ethylhexanol from n-butyraldehyde. It can be inferred from the above researches that the reaction integration of n-butyraldehyde self-condensation and sucessive hydrogenation needs a multifunctional catalyst with both acid/base active site (for aldol condensation) and metal active site (for hydrogenation). So the reaction integration of n-valeraldehyde self-condensation and sucessive hydrogenation for one-pot synthesis of 2-PH form n-valeraldehyde requires a metal–acid/base multifunctional catalyst either.
We once evaluated the catalytic performance of an acid ionic liquid [HSO3-b-N(Et)3]p-TSA in n-butyraldehyde self-condensation and the catalytic performance of an acid–base bifunctional ionic liquid [PEmim]Cl-0.5Zn(CH3COO)2 in n-valeraldehyde self-condensation. Pretty good results were attained: 2-ethyl-2-hexenal selectivity of 87.8% was achieved at a n-butyraldehyde conversion of 89.7% over [HSO3-b-N(Et)3]p-TSA while 2-propyl-2-heptanal selectivity of 86.6% was obtained at a n-valeraldehyde conversion of 94.7% over [PEmim]Cl-0.5Zn(CH3COO)2.9,10 Moreover, supported Ni-based or Cu-based catalysts show excellent catalytic performance for hydrogenation of 2-propyl-2-heptenal.11–14 So a combination of an acidic ionic liquid or an acid–base bifunctional ionic liquid with supported Ni or Cu catalyst will be expected to show a good catalytic performance for the one-pot synthesis of 2-PH form n-valeraldehyde. Besides, the immobilization of ionic liquid can reduce the usage of ionic liquid, simplify separation and purification operation, and impose a specially designed environment around the catalytic site, being beneficial to inhibit the side reactions and enhance the product selectivity.15,16 With such ideas in mind, we prepared a silica-immobilized nickel and acid ionic liquid (Ni-IL/SiO2) catalyst and characterized its structure and property by means of FT-IR, TGA, XRD and XPS analysis. To our delight, Ni-IL/SiO2 showed an excellent catalytic performance for the one-pot synthesis of 2-PH from n-valeraldehyde, laying a foundation for establishing a new green technology for 2-PH synthesis.
2. Experimental
2.1. Preparation of Ni-IL/SiO2
The process for preparation of Ni-IL/SiO2 comprises two steps: firstly an acid ionic liquid was immobilized on silica to form silica-immobilized acid ionic liquid (IL/SiO2), and then nickel was introduced in IL/SiO2 to obtain the target catalyst Ni-IL/SiO2.
(1) Preparation of IL/SiO2. A IL/SiO2 sample was prepared by a bonding procedure.17 The mixture of silica, toluene and 3-chloropropyl triethoxysilane was stirred for 6 h under reflux of toluene to obtain a chloropropyl functionalized silica (Intermediate Product-1, IP-1). Then IP-1, potassium iodide and excess imidazole were dispersed in anhydrous toluene and the mixture was refluxed at 110 °C for 16 h to give a 3-(1-imidazole)propyl functionalized silica (IP-2). Next, IP-2 was mixed with a solution of 1,3-propane sultone and toluene and then the mixture was stirred at 100 °C for 6 h to attain a silica-immobilized amphoteric salt (IP-3). After that, CF3SO3H was added dropwise into a mixture of IP-3 and toluene. The resulting mixture was heated to 80 °C and kept for 5 h to afford an immobilized sulfonic acid functional ionic liquid, IL/SiO2. The structure of IL/SiO2 is presented in Scheme 1.
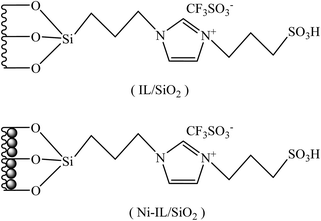 |
| Scheme 1 Structure diagrams of IL/SiO2 and Ni-IL/SiO2. | |
(2) Preparation of Ni-IL/SiO2. Ni-IL/SiO2 catalyst was prepared by impregnating a nickel nitrate aqueous solution into the IL/SiO2 sample and then reduction by NaBH4 under 40 °C for 4 h. The structure of Ni-IL/SiO2 is shown in Scheme 1 either.
2.2. Catalyst characterization
A NICOLET NEXUS 470 infrared spectroscopy (Thermo Electron Corp., USA) was used for the FTIR measurement of samples. The spectra were recorded between 400 and 4000 cm−1 at a resolution of 4 cm−1. The thermal stability of samples was determined using a SDT Q600 simultaneous thermal analyzer (TA Instruments Corp., USA). The test was carried out under a flowing air atmosphere (40 mL min−1) with a heating rate of 10 °C min−1 in the range from room temperature to 700 °C. The binding energy of Ni on the catalyst surface was measured using a Kratos Axis Ultra DLD photoelectron spectrometer (Kratos Analytical, Manchester, England). All the binding energy data were calibrated with C 1s = 284.6 eV as an internal standard. X-ray diffraction (XRD) patterns were recorded with a Rigaku D/max-2550 diffractometer (Rigaku International Corp., Japan) using Cu Kα radiation at 100 mA and 40 kV. The scan range covered from 5° to 90° at a rate of 6° min−1.
2.3. Catalytic performance evaluation
The catalytic performance of Ni-IL/SiO2 for one-pot synthesis of 2-PH by sequential n-valeraldehyde self-condensation and hydrogenation was evaluated in a 100 mL stainless steel autoclave. In a typical procedure, 30 mL (about 24 g) of n-valeraldehyde and 4.5 g of Ni-IL/SiO2 catalyst were added into the autoclave, and the air inside was replaced by nitrogen. The mixture was heated to 200 °C and held for 1.5 h with stirring. Then H2 was introduced into the reaction system without cooling and separation. The hydrogenation reaction was carried out for 8.0 h under 3.0 MPa of H2 pressure. After the completion of reaction, the mixture solution was filtered to remove the catalyst and the filtrate was analyzed on a gas chromatograph equipped with a FID and a KB-1 capillary column and quantified by the internal standard analysis method.
3. Results and discussion
3.1. Characterization of Ni-IL/SiO2 catalyst
The XRD patterns of Ni(NO3)2-IL/SiO2 and Ni-IL/SiO2 are shown in Fig. 1. No characteristic peaks of Ni(NO3)2 are observed in Ni(NO3)2-IL/SiO2, indicating that the supported Ni(NO3)2 has small particle sizes and is homogeneously dispersed on the surface of IL/SiO2. For Ni-IL/SiO2 catalyst, a very weak and board characteristic peak centered at 2 theta of 44.5° corresponds to amorphous Ni0, indicating that Ni2+ has been reduced to Ni0 successfully in Ni-IL/SiO2. After the reaction, some diffraction peaks are observed at around 2 theta of 44.5° and 52.0° (Fig. 1(c)), which attribute to the Ni0(100) and Ni0(220) planes.18 There are two possible explanations for the change in characteristic peak of Ni0: further reduction under H2 atmosphere, or aggregation and growth of Ni grains.
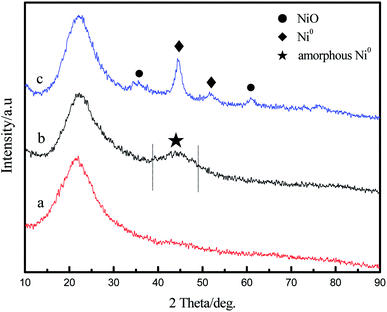 |
| Fig. 1 XRD patterns of Ni(NO3)2-IL/SiO2 and fresh and recovered Ni-IL/SiO2 (a) Ni(NO3)2-IL/SiO2, (b) fresh Ni-IL/SiO2, (c) recovered Ni-IL/SiO2. | |
To further analyze the chemical states of nickel, the samples were characterized by XPS analysis. Fig. 2 displays Ni 2p spectra of the catalyst before and after reduction. It can be seen from Fig. 2(a) that the binding energies of Ni 2p3/2 and Ni 2p1/2 in Ni(NO3)2-IL/SiO2 are respectively 857.2 eV and 874.8 eV, which are ascribed to Ni2+ of Ni(NO3)2. There are two valence states of nickel in Ni-IL/SiO2 (Fig. 2(b)). The binding energies at around 852.7 eV and 870.0 eV for the Ni 2p3/2 are attributed to Ni0 (metallic Ni) whereas the Ni 2p3/2 and Ni 2p1/2 peaks at 856.2 eV and 873.9 eV are attributed to Ni2+ of NiO.19 An absence of Ni2+ of Ni(NO3)2 in Ni-IL/SiO2 indicates Ni(NO3)2 has been completely reduced by NaBH4. It also demonstrates that the enhancement of XRD diffraction peaks of Ni0 in the recovered catalyst is caused by the aggregation and growth of Ni grains. The presence of NiO in Ni-IL/SiO2 may be due to the reoxidation of metallic nickel by contacting air in the analysis process.14
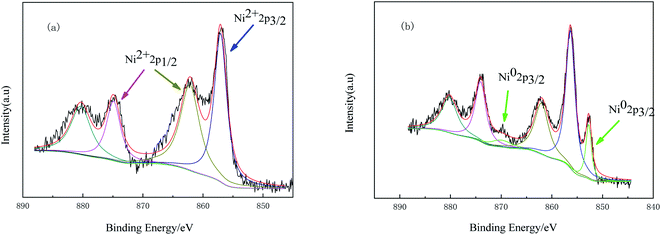 |
| Fig. 2 XPS Ni 2p spectra of (a) Ni(NO3)2-IL/SiO2 and (b) Ni-IL/SiO2. | |
The FT-IR spectra of silica and the prepared IL/SiO2 and Ni-IL/SiO2 are shown in Fig. 3. The broad band around 3445 cm−1 belongs to asymmetric stretching vibration of –OH on the support surface. The band at 1625 cm−1 is associated with the bending vibration of H–O–H. The bands at 809 cm−1 and 1099 cm−1 are assigned to symmetrical and asymmetric stretching vibration of Si–O–Si while the bending vibration of Si–OH is observed at 967 cm−1.20 Compared with silica support, a new band at 641 cm−1 attributed to the bending vibration of C–F appears in IL/SiO2 while the bending vibration of Si–OH weakens obviously, indicating the reaction of Si–OH with the coupling agent and the immobilization of ionic liquids on the support. Fortunately, the FT-IR spectrum changes little for the supported nickel catalyst Ni-IL/SiO2. Combined with the results of XRD and XPS, it is confirmed that the ionic liquid and nickel has been successfully grafted onto the surface of silica.
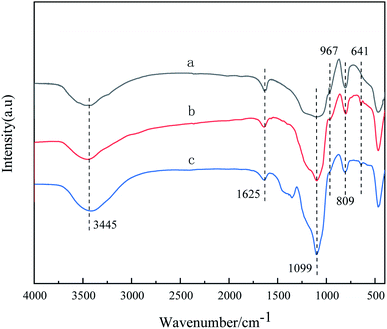 |
| Fig. 3 FT-IR spectra of silica, IL/SiO2 andNi-IL/SiO2 (a) silica, (b) IL/SiO2, (c) Ni-IL/SiO2. | |
Fig. 4 presents the TGA curves of IL/SiO2 and Ni-IL/SiO2. There are two steps of weight loss for the two samples. The first weight loss occurs at about 70 °C, which is attributed to the physically adsorbed water and residual organic solvents during the process for preparation of catalysts. The second weight loss at higher than 330 °C is related to the decomposition of the ionic liquids on the surface of supports.21 The analysis results demonstrate that Ni-IL/SiO2 shows the same thermal stability as IL/SiO2 and its weight loss rate is slightly lower than that for IL/SiO2. This could be attributed to the decline in ionic liquid amount per unit mass of sample because of the introduction of nickel for Ni-IL/SiO2.
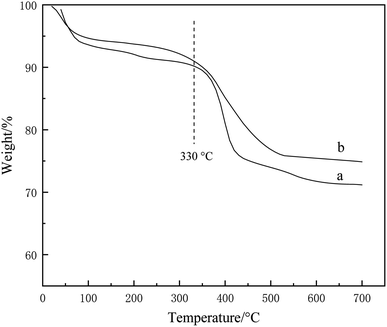 |
| Fig. 4 TGA curves of IL/SiO2 and Ni-IL/SiO2 (a) IL/SiO2, (b) Ni-IL/SiO2. | |
3.2. Catalytic performance of Ni-IL/SiO2 for one-pot synthesis of 2-PH
The catalytic performance of Ni-IL/SiO2 for one-pot synthesis of 2-PH was evaluated at 200 °C for 1.5 h first and then H2 was introduced for hydrogenation under 3.0 MPa of H2 pressure for 8.0 h. As a result, the selectivity of 2-PH and pentanol was respectively 58.7% and 25.6% at a n-valeraldehyde conversion of 100%. The catalytic performance of Ni-IL/SiO2 is affected greatly by the reaction conditions. To improve the catalytic performance of Ni-IL/SiO2, the effects of reaction conditions such as Ni-IL/SiO2 dosage, hydrogen pressure, reaction temperature and reaction time were investigated.
3.2.1 Effect of catalyst dosage. The results of effect of Ni-IL/SiO2 dosage are listed in Table 1. With an increase of weight percentage of Ni-IL/SiO2, n-valeraldehyde conversion increased from 95.3% to 100% while the selectivity of 2-PH increased first, reached its highest point at a weight percentage of Ni-IL/SiO2 of 15%, and then decreased. The selectivity of 2-propylheptanal changed adversely with 2-PH. The results suggest that the hydrogenation of 2-propyl-2-heptenal to 2-PH proceeds in two steps: C
C bond of 2-propyl-2-heptenal is hydrogenated to 2-propylheptanal first and then C
O bond of 2-propylheptanal is hydrogenated to 2-PH, as shown in eqn (1). The selectivity of 2-propyl-2-heptenal was quite low and changed little, indicating that the hydrogenation of C
C bond is easier than that of C
O bond and thus the hydrogenation of C
O bond is the controlling step. |
 | (1) |
Table 1 Effect of catalyst amount on the catalytic performance of Ni-IL/SiO2a
Catalyst amount/% |
XV/% |
SPO/% |
S2-PHEA/% |
S2-PHA/% |
S2-PH/% |
Reaction conditions: T = 200 °C; n-valeraldehyde self-condensation: t = 1.5 h; hydrogenation: PH2 = 3 MPa, t = 8 h. V: n-valeraldehyde; PO: pentanol; 2-PHEA: 2-propyl-2-heptenal; 2-PHA: 2-propylheptanal; 2-PH: 2-propylheptanol. X: conversion; S: selectivity. |
5 |
95.3 |
20.4 |
0.7 |
70.6 |
3.4 |
10 |
100 |
25.6 |
0.8 |
12.8 |
58.7 |
15 |
100 |
27.4 |
0.9 |
2.30 |
69.0 |
20 |
100 |
24.7 |
0.9 |
10.4 |
63.0 |
3.2.2 Effect of hydrogen pressure. The effect of hydrogen pressure was investigated and the results are listed in Table 2. When the hydrogen pressure was 2.0 MPa, there was a certain amount of 2-propylheptanal left after the reaction, which demonstrates once again the hydrogenation of C
C bond is easier than that of C
O bond. With increasing hydrogen pressure, the catalytic activity for the hydrogenation of C
O bond was improved: the selectivity of both 2-propyl-2-heptenal and 2-propylheptanal decreased and 2-PH selectivity increased obviously. When the hydrogen pressure was 4.0 MPa, the highest 2-PH selectivity of 75.4% was reached and the sum of the selectivity of 2-PH and pentanol was 98.6%.
Table 2 Effect of hydrogen pressure on the catalytic performance of Ni-IL/SiO2a
Reaction pressure/MPa |
XV/% |
SPO/% |
S2-PHEA/% |
S2-PHA/% |
S2-PH/% |
Reaction conditions: T = 200 °C, a weight percentage of catalyst = 15%; n-valeraldehyde self-condensation: t = 1.5 h; hydrogenation: t = 8 h. V: n-valeraldehyde; PO: pentanol; 2-PHEA: 2-propyl-2-heptenal; 2-PHA: 2-propylheptanal; 2-PH: 2-propylheptanol. X: conversion; S: selectivity. |
2 |
100 |
28.2 |
2.3 |
36.8 |
28.3 |
3 |
100 |
27.4 |
0.9 |
2.3 |
69.0 |
4 |
100 |
23.2 |
0.4 |
0.5 |
75.4 |
5 |
100 |
24.9 |
0.2 |
0.1 |
70.5 |
3.2.3 Effect of reaction time. The effect of reaction time listed in Table 3 shows that reaction time has a significant influence on the catalytic performance. A low 2-PH selectivity of 47.1% at a reaction time of 6 h was obtained because 2-propylheptanal was not fully hydrogenated. With the prolonging of reaction time, 2-PH selectivity increased while 2-propylheptanal selectivity decreased. When the reaction proceeded for 8 h, 2-propylheptanal was almost completely hydrogenated to 2-PH. With further prolonging reaction time, some side-reactions of 2-PH and n-valeraldehyde could be promoted, resulting in the decrease of 2-PH selectivity.5
Table 3 Effect of reaction time on the catalytic performance of Ni-IL/SiO2a
Reaction time/h |
XV/% |
SPO/% |
S2-PHEA/% |
S2-PHA/% |
S2-PH/% |
Reaction conditions: a weight percentage of catalyst = 15%, T = 200 °C; n-valeraldehyde self-condensation: t = 1.5 h; hydrogenation: PH2 = 4 MPa. V: n-valeraldehyde; PO: pentanol; 2-PHEA: 2-propyl-2-heptenal; 2-PHA: 2-propylheptanal; 2-PH: 2-propylheptanol. X: conversion; S: selectivity. |
6 |
100 |
25.7 |
3.1 |
23.8 |
47.1 |
8 |
100 |
23.2 |
0.4 |
0.5 |
75.4 |
10 |
100 |
22.4 |
0.1 |
0 |
72.9 |
3.2.4 Effect of reaction temperature. Table 4 shows the effect of reaction temperature. The highest 2-PH selectivity of 75.4% was obtained with a n-valeraldehyde conversion of 100% at 200 °C. A decrease of reaction temperature mainly reduced the hydrogenation rate of C
O bond, resulting an increase of 2-propylheptanal selectivity. However, deep self-condensation of n-valeraldehyde could be accelerated at a reaction temperature above 200 °C, affecting the generation of pentanol and 2-PH.
Table 4 Effect of reaction temperature on the catalytic performance of Ni-IL/SiO2a
Reaction temperature/°C |
XV/% |
SPO/% |
S2-PHEA/% |
S2-PHA/% |
S2-PH/% |
Reaction conditions: a weight percentage of catalyst = 15%; n-valeraldehyde self-condensation: t = 1.5 h; hydrogenation: PH2 = 4 MPa, t = 8 h. V: n-valeraldehyde; PO: pentanol; 2-PHEA: 2-propyl-2-heptenal; 2-PHA: 2-propylheptanal; 2-PH: 2-propylheptanol. X: conversion; S: selectivity. |
190 |
99.8 |
27.1 |
3.6 |
24.6 |
43.8 |
200 |
100 |
23.2 |
0.4 |
0.5 |
75.4 |
210 |
100 |
22.1 |
0 |
0.2 |
65.8 |
Thus an improved catalytic performance of Ni-IL/SiO2 was attained by investigating the effect of reaction conditions: a 2-PH selectivity of 75.4% with a n-valeraldehyde conversion of 100% under the conditions of 15 wt% of Ni-IL/SiO2, a hydrogen pressure of 4 MPa, 200 °C, and 8 h. The Ni/Ce–Al2O3 catalyst reported in our previous work of one-pot synthesis of 2-ethylhexanol4 was applied in the one-pot synthesis of 2-PH via sequential self-condensation and hydrogenation from n-valeraldehyde under the above suitable reaction conditions. A 2-PH selectivity of 69.3% with a complete n-valeraldehyde conversion was obtained, indicating that the catalytic performance of Ni-IL/SiO2 is better than that of Ni/Ce–Al2O3 for one-pot synthesis of 2-PH.
4. Conclusions
A novel Ni-IL/SiO2 catalyst was prepared for one-pot synthesis of 2-PH via sequential self-condensation and hydrogenation from n-valeraldehyde. The characterization results demonstrate that Ni(NO3)2 was reduced to Ni completely by NaBH4, and Ni-IL/SiO2 has a good thermal stability below 330 °C. The prepared catalyst shows an excellent catalytic performance in one-pot synthesis of 2-PH: the selectivity of 2-PH attained 75.4% at a n-valeraldehyde conversion of 100% and the sum of 2-PH and pentanol selectivity reached 98.6% under the suitable reaction conditions. The hydrogenation of C
O bond of 2-propyl-2-heptenal is more difficult than that of C
C bond, and is the controlling step.
Conflicts of interest
There are no conflicts to declare.
Acknowledgements
This work was financially supported by the National Natural Science Foundation of China (21978066, 21506046), Basic Research Program of Hebei Province for Natural Science Foundation and Key Basic Research Project (18964308D), and Natural Science Foundation of Hebei Province (B2018202220). The authors are gratefully appreciative of their contributions.
References
- L. Zhao, H. An, X. Zhao and Y. Wang, Ind. Eng. Chem. Res., 2016, 55, 12326 CrossRef CAS.
- T. Seki, J.-D. Grunwaldt and A. Baiker, Chem. Commun., 2007, 34, 3562 RSC.
- C. A. Hamilton, S. D. Jackson and G. J. Kelly, Appl. Catal., A, 2004, 263, 63 CrossRef CAS.
- N. Liang, X. Zhang, H. An, X. Zhao and Y. Wang, Green Chem., 2015, 17, 2959 RSC.
- Y. Li, X. Liu, H. An, X. Zhao and Y. Wang, Ind. Eng. Chem. Res., 2016, 55, 6293 CrossRef CAS.
- Y. Li, X. Liu, H. An, X. Zhao and Y. Wang, J. Chem. Ind. Eng., 2017, 68, 1381 CAS.
- S. C. Patankar and G. D. Yadav, Catal. Today, 2017, 291, 223 CrossRef CAS.
- S. Miao, H. An, X. Zhao and Y. Wang, React. Kinet., Mech. Catal., 2019, 128, 395 CrossRef CAS.
- X. Zhang, H. An, H. Zhang, X. Zhao and Y. Wang, Ind. Eng. Chem. Res., 2014, 53, 16707 CrossRef CAS.
- H. An, Y. Kong, Q. Yang, X. Zhao and Y. Wang, J. Chem. Technol. Biotechnol., 2020, 95, 710 CrossRef CAS.
- Z. Sun, J. Chem. Ind. Eng., 2007, 28, 8 CAS.
- Z. Tang, Y. Zhou and Y. Feng, Appl. Catal., A, 2004, 273, 171 CrossRef CAS.
- T. Zhang, J. Shi and S. Zhang, Petrochem. Technol., 2012, 41, 653 CAS.
- L. Zhao, PhD thesis, Hebei University of Technology, 2018.
- A. Dhar, N. S. Kumar, M. Khimani, A. S. Al-Fatesh, A. A. Ibrahim, A. H. Fakeeha, H. Patelc and R. L. Vekariya, RSC Adv., 2020, 10, 15282 RSC.
- A. S. Amarasekara, Chem. Rev., 2016, 116, 6133 CrossRef CAS PubMed.
- H. An, J. Tian, X. Zhao and Y. Wang, J. Chem. Ind. Eng., 2015, 66, 171 CAS.
- S. K. Sharma and R. V. Jasra, Indian J. Chem., 2015, 54, 451 Search PubMed.
- C. C. Torres, J. B. Alderete, C. Mella and B. Pawelec, J. Mol. Catal. A: Chem., 2016, 423, 441 CrossRef CAS.
- P. Han, H. Zhang, X. Qiu, X. Ji and L. Gao, J. Mol. Catal. A: Chem., 2008, 295, 57 CrossRef CAS.
- M. Vafaeezadeh, Z. B. Dizicheh and M. M. Hashemi, Catal. Commun., 2013, 41, 96 CrossRef CAS.
|
This journal is © The Royal Society of Chemistry 2020 |
Click here to see how this site uses Cookies. View our privacy policy here.