DOI:
10.1039/D0RA03782F
(Paper)
RSC Adv., 2020,
10, 25408-25417
High-performance water-borne fluorescent acrylic-based adhesive: synthesis and application†
Received
27th April 2020
, Accepted 16th June 2020
First published on 3rd July 2020
Abstract
Water-borne adhesives have immense importance in cellulose-based materials, where their durability, handling, and strength remain to be a major concern. The present work demonstrates the development of three water-borne adhesives, namely, poly(1-vinyl-2-pyrrolidone-co-acrylic acid), poly(acrylonitrile-co-acrylic acid), and poly(1-vinyl-2-pyrrolidone-co-acrylonitrile-co-acrylic acid) applicable for cellulose-based materials. These acrylic-acid based adhesives were characterized by Fourier-transform infra-red spectroscopy, thermogravimetric analysis, X-ray diffraction, gel permeation chromatography, and universal testing machine. The synthesized polymer adhesives can be stored in the powder form for a longer period, thus utilizing less space. In order to use as adhesives, suitable formulations can be prepared in water. The adhesives show thermal stability up to 300 °C. Our studies show that poly(1-vinyl-2-pyrrolidone-co-acrylonitrile-co-acrylic acid) showed higher lap shear strength (ASTM D-906) than commercially available adhesives. In addition, these adhesives, being fluorescent in nature, can be detected under UV light and thus are applicable for the detection of fractured joints of any specimen. This property also helps in anti-counterfeiting applications, thus adding further to their utility.
1. Introduction
Adhesives are arguably one of the most demanding areas of research that are applicable in the design of items ranging from small decorative to electronics,1 automobiles,2 and space industries.3 Adhesives are one of the many sources of industries that decide the economic well-being of a nation. Adhesives have been an integral part of human life since the early civilizations. The first commercial glue was obtained in Holland in 1690; casein glue was manufactured in Switzerland in the early nineteenth century.4,5 In modern times, the synthesis of adhesives is carried out using different polymeric materials, such as polyurethanes, epoxy, acrylates, and cyanoacrylates.
Acrylic acid-containing polymers, due to their extensive cross-linking ability, are highly accepted in different applications such as wound dressing,6 drug delivery,7 and environmental safety.8 In coatings and furnishings, acrylic-based adhesives are considered to be the most suitable owing to their durability, cure speed, strength, and low toxicity.9 Because of these advantages, acrylic-based adhesives are widely used in various industries, such as dentistry, civil constructions, engineering, and textiles.10–13
Water-borne adhesives are easy to handle and safe to use. As the World Health Organisation (WHO) and the government agencies are emphasizing on reducing the use of organic solvents, thus adhesives obtained without the use of organic solvents are in demand. Furthermore, with regard to the emission of organic solvents into the atmosphere, water-borne adhesives meet the restricted European environmental legislation (Directive 1999/13/CE). Water-borne adhesives, such as solvent-borne adhesives, do not emit volatile solvents during curing.14 Among water-borne adhesives, acrylic-based water-borne adhesives have been the focus of research for the last few years. They can be tuned to control the glass transition temperature and the cross-linking density; they have low plateau modulus and are cost-effective as well.15–17 They are expected to have high strength due to the hydrogen bonding of water with the polar groups.18 Due to the factors mentioned above, acrylic adhesives have been the critical choice for the bonding of cellulosic materials.19,20 There are four different types of cellulose, namely, I, II, III, and IV, of which I and II are naturally occurring, and III and IV are derived.21 Cellulose-based materials, such as papers, woods, cardboards, ply, and plant fibers, are an important part of our daily use. Cellulose is used in furnishing, textiles, medicines, electrical equipment, food packaging, and building materials.22–25 These materials as adherents require adhesives that give high strength and can withstand high temperatures. Water-borne adhesives are suitable for these adherents because of the ability of cellulose to absorb water molecules via H-bonding.
Another major issue with commercially available adhesives is their reduced storage lifespan as they dry up once the seal is opened. Adhesives in the form of powder could be a solution to the short lifespan. Very little research has been carried out in the field of powdered adhesives, and their applications and scope26,27 to meet the long-term storage demand. Moreover, the thermal stability of commercially available adhesives is are poor, making them unsuitable in high temperature applications. Many research groups have conducted experiments to develop adhesives based on high temperature-resistant epoxy28 and polyurethane29 but temperature-resistant acrylic-based adhesives are very rare without using any stabilizing agents.30 Again, the market value of commercially available adhesives can be increased manifold if they have fluorescence characteristics. Fluorescent adhesive systems can be of great utility in crafts and designs for the easy detection of fractured joints. Earlier reports suggest the use of fluorescent dyes for imparting the fluorescence characteristic to adhesive systems31 but this may lead to health and environmental issues.32 Fluorescent adhesives are widely used in various fields, such as dental care, medical care, and visualization of fingerprints.33
Keeping all these aspects in mind, we have attempted to formulate three sets of acrylic-based water-borne powder adhesives for cellulosic materials, which are thermally stable and fluorescent. The adhesion of cellulosic materials, i.e., wood and paper bonded by these water-borne acrylic systems, were studied and compared with that of the best quality commercially available adhesive in the local market. One of our adhesive formulations showed almost double the lap shear strength compared to the commercially available adhesive. To the best of our knowledge, this is the first report of the formulation of acrylic-based water-borne thermally stable powder adhesive systems with fluorescence property, which has the added benefit of anti-counterfeiting application. In short, we present three ideal cost-effective water-based adhesives that can address all the issues related to adhesives for our daily use.
2. Experimental
2.1. Materials
1-Vinyl-2-pyrrolidone (VP) was purchased from Sigma Aldrich; crylonitrile (Acn) and acrylic acid (Acr) were purchased from Merck. Azobisisobutyronitrile (AIBN) was obtained from Spectrochem. Acetone, dimethylformamide (DMF), dimethylsulfoxide (DMSO), and chloroform were purchased from Merck. Milli-Q water was used wherever necessary. All these materials were of analytical grade and were used without further purification.
2.2. Preparation of P(VP-Acr)
0.05 mol (3.43 mL) Acr was added dropwise to 0.05 mol (5.34 mL) VP with a pinch (approximately 0.005 g) of AIBN as the initiator and the stirring was continued for 1 hour. The reaction flask was then evacuated by a vacuum pump and kept at 60 °C for 3 hours. After the completion of the reaction, a stiff yellowish solid lump, the copolymer of VP and Acr, namely, poly(1-vinyl-2-pyrrolidone-co-acrylic acid) [denoted by P(VP-Acr)], was formed. The material thus obtained was then taken out with the help of a spatula and kept in a desiccator for 24 hours. The dried polymer was crushed to a powder with the help of a mortar and pestle. The powder material thus obtained was stored in an airtight container for further use as an adhesive.
2.3. Preparation of P(Acn-Acr)
The P(Acn-Acr) adhesive was obtained by a procedure similar to that reported in Section 2.2. Acn was used instead of VP along with Acr as the monomers and a similar procedure was carried out to obtain a solid lump. After the completion of the reaction, an off-white-colored stiff solid lump, the copolymer of Acn and Acr, namely, poly(acrylonitrile-co-acrylic acid) [denoted by P(Acn-Acr)], was formed. This copolymer was also crushed to a powder and stored in an airtight container for further use as an adhesive.
2.4. Preparation of P(VP-Acn-Acr)
0.05 mol of VP (5.34 mL) and Acn (3.27 mL) were mixed with 0.005 g AIBN and kept under stirring conditions. This was followed by the addition of 0.05 mol of Acr (3.43 mL) dropwise and stirring was continued for another 1 hour. The reaction flask was then evacuated by a vacuum pump and then kept at 60 °C for 3 hours. A light yellow-coloured stiff solid lump, namely, poly(1-vinyl-2-pyrrolidone-co-acrylonitrile-co-acrylic acid), was obtained [denoted by P(VP-Acn-Acr)], which was crushed to a powder and stored in an airtight container for further use as an adhesive.
2.5. Preparation of paper samples for the adhesive test
The applications of our adhesive systems were checked in different sets of paper materials. The specimens were prepared as per the ASTM-D1876 peel method (T peel test), as shown in Fig. 1(A), to test the adhesive strength. Four sets of paper samples were taken for the test with different GSM (Gram per Square Meter) values, as shown in the ESI, Fig. S1(A).† Normal A4 size map litho paper (GSM value = 75), oil paper (GSM value = 40.85), chart paper (GSM value = 118), and hard paper of carton material (GSM value = 212) were considered and the adhesives were applied.
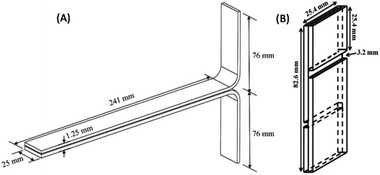 |
| Fig. 1 (A) Dimensions of a paper specimen prepared for the adhesive tests as per ASTM-D1876; (B) dimensions of the wood specimen prepared for the adhesive tests as per ASTM D-906. | |
2.6. Preparation of the wood sample for the adhesive test
The adhesive test was performed for wooden materials. For testing the adhesive strength, we took a wood specimen of Gmelina Arborea, which is popularly known as Gomari (in local Assamese language) and is extensively used in households and furnishing. The moisture content of the wood specimen was calculated as per the ASTM D-4442 method34 and was found to be 10.55%. The wood was then cut into required pieces to make the samples of dimensions as per the ASTM D-906 (Fig. 1(B)) standard and polished using sandpaper (Fig. S1(B)).† The test samples were made by applying the formed adhesives, after dispersion in water. The average thickness of the adhesive layers was 0.158 mm and the area density of the applied adhesive was 0.4 mg mm−2. The samples were kept in dry conditions away from moisture before the application of the adhesive.
2.7. Lap shear strength test
The lap shear strength test determined the adhesive strength. It is further a measure for the cohesion (inner strength) of the adhesive and gives information about the quality of the adhesive.
The lap shear strength was calculated according to eqn (1).35
|
Shear strength (σM) = Fmax/A,
| (1) |
where
Fmax(
N) is the observed maximum failing load (force) and
A (mm
2) is the bonding surface area of the sample.
2.8. Methods
The Fourier-transform infra-red (FT-IR) spectra were recorded by using a PerkinElmer FT-IR spectrophotometer in the transmission mode. Since the polymers could be ground to a fine powder, the FT-IR spectra were recorded in the KBr mode by making pellets. The samples were handled carefully and always stored in a desiccator to avoid contact with moisture.
The thermal properties of the polymer adhesives were examined by thermogravimetric analysis (TGA) using a PerkinElmer TGA 4000 thermogravimetric analyzer at a heating rate of 10 °C min−1 in a nitrogen environment with a gas flow rate of 20 mL min−1.
The X-ray diffraction (XRD) patterns were collected on a Bruker D8 Advance diffractometer using Cu radiation operating at 40 kV and 40 mA at a scan rate of 2 s per step.
The molecular masses of the copolymers were recorded using gel permeation chromatography (GPC) using a Waters Corporation chromatograph (UV-Vis detection-2489, USA).
The lap shear strength was measured by a Hounselfield (England) Universal Testing Machine (UTM), Model H 100K-S (having a maximum load cell of 100 kN). All the measurements were taken using a load cell of 250 N.
3. Results and discussion
3.1. Chemical synthesis
Acrylic acid (Acr) is known to be widely used as a precursor for the synthesis of the adhesives. In all the reactions mentioned above, Acr was taken as a common monomer owing to its adhesive formulation property. By varying the other monomers, the required set of adhesive formulations can be obtained. It may be assumed that the reaction proceeds in the following way: Acr is a monomer with an acidic group and a terminal alkene. In the presence of another monomer, free radical polymerization takes place with the addition of a small amount of the initiator (AIBN). The terminal double bonds are polymerized, which leads to extensive cross-linking, eventually leading to the formation of a thickened mass of polymer lump, which can be crushed to a powder. Because of the presence of the polar –COOH group of Acr, it forms a highly cross-linked polymer with other monomers having polar moieties, such as VP and Acn. The monomers undergo the thermal polymerization reaction and form the respective copolymers with excellent adhesive properties.
The reactions were carried out at different concentrations of the monomers to get the optimized concentration (0.05 mol) of the monomers and optimum temperature (60 °C), which resulted in the best possible adhesive materials. Using the concentration of monomers other than that mentioned in the procedure did not yield the products of our interest. Other reaction conditions did not form a stiff polymer lump to be stored as a powder and also did not result in the gel-like adhesive with the addition of water. Scheme 1 shows the polymerization reaction of VP and Acr; Scheme 2 shows the reaction of Acn and Acr. We took acrylic acid as one of the monomers by varying the other two since acrylic acid was found to be the major component of the adhesive. The major role of acrylic acid in adhesive formulation was confirmed by the reaction between VP and Acn,36 which resulted in the formation of a polymer with no adhesive property.
 |
| Scheme 1 Schematic representation for the synthesis of the copolymer P(VP-Acr). | |
 |
| Scheme 2 Schematic representation for the synthesis of the copolymer P(Acn-Acr). | |
To obtain the best results, we carried out the copolymerization reaction of all the three monomers, i.e., VP, Acn, and Acr (shown in Scheme 3) to obtain the ideal product of our choice, i.e., the powdered water-borne adhesive with high thermal stability.
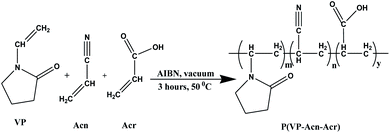 |
| Scheme 3 Schematic representation for the synthesis of the copolymer P(VP-Acn-Acr). | |
The synthesis of P(VP-Acn-Acr) was carried out earlier using N-methyl pyrrolidone as the solvent.37 But, in our present procedure, we carried out the synthesis without the use of a solvent, thus rendering more rigid products due to extensive cross linking.38
These obtained rigid polymers were crushed, ground to powder, and stored in an airtight container, as depicted in Fig. 2. The pictures of the polymer powders thus obtained were taken under normal light and UV light, as shown in Fig. 3. The pictures of the polyacrylic-based water-borne adhesive powders under UV lamp show that the adhesives are highly fluorescent, thus expanding their utility towards the detection of fracture joints after adhesion.
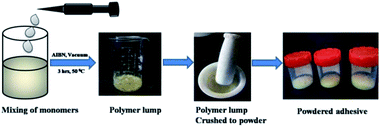 |
| Fig. 2 Series of steps depicting the formation and storage of the adhesive powder. | |
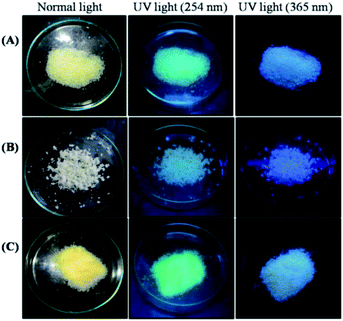 |
| Fig. 3 Photographic images of (A) P(VP-Acr), (B) P(Acn-Acr), and (C) P(VP-Acn-Acr) under normal light, UV light (254 nm), and UV light (365 nm), respectively. | |
3.2. Fourier-transform infra-red (FT-IR) analysis
The synthesized copolymers were characterized with the help of FT-IR spectroscopy. The FT-IR spectra of the copolymers, along with acrylic acid (Acr), are shown in Fig. 4. Acr shows a peak at 3452 cm−1 for carboxylic O–H stretching. All the three polymers, P(VP-Acr), P(Acn-Acr), and P(VP-Acn-Acr), show peaks at 3436, 3434, and 3436 cm−1, respectively, corresponding to carboxylic O–H stretching. The shift of the peak towards shorter wavelength indicates the involvement of the carboxylic O–H group of the copolymers in H-bonding. The peaks at 2934, 2926, and 2924 cm−1 correspond to alkane C–H stretching for P(VP-Acr), P(Acn-Acr), and P(VP-Acn-Acr), respectively, indicating the formation of alkanes by alkene polymerization. Acr, P(VP-Acr), P(Acn-Acr), and P(VP-Acn-Acr) show carboxylic C
O stretching peaks at 1710, 1726, and 1728 cm−1, respectively, hence showing an increase in THE stretching frequency, indicating that polymerization has taken place and the involvement of O–H group in hydrogen bonding. Acr shows a peak at 1628 cm−1 corresponding to the C
C stretching frequency, which is absent in all the three polymers, thus further confirming the polymerization of the alkenes. The presence of peaks at 1436, 1420, 1404, and 1422 cm−1 signify the C–H bending modes, and the peaks at 1220, 1162, 1666, and 1164 cm−1 correspond to the C–O stretching of Acr, P(VP-Acr), P(Acn-Acr), and P(VP-Acn-Acr), respectively. Apart from these, P(Acn-Acr) and P(VP-Acn-Acr) show peaks at 2248 and 2244 cm−1, respectively, which correspond to C–N (triple bond) stretching, which is absent in P(VP-Acr). Also, P(VP-Acr) and P(VP-Acn-Acr) both show peaks at 1658 and 1656 cm−1 corresponding to the carbonyl group of amide and an additional peak at 1288 cm−1 corresponding to C–N stretching, which is absent in P(Acn-Acr).
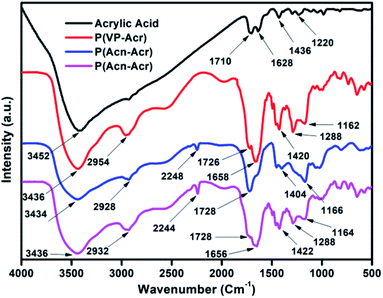 |
| Fig. 4 FT-IR spectra of Acr, P(VP-Acr), P(Acn-Acr), and P(VP-Acn-Acr). | |
The major changes in the FT-IR spectrum of acrylic acid on the formation of the polymers could be correlated with the reactions, as shown in Schemes 1–3. The probable H-bonding in P(VP-Acn-Acr), as described by the FT-IR results above, is shown in Fig. 5.
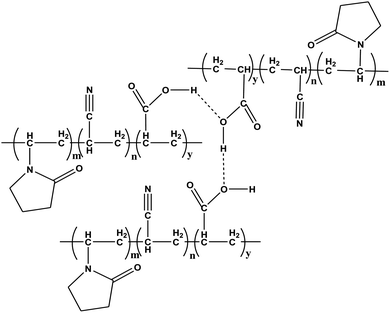 |
| Fig. 5 The probable H-bonding in P(VP-Acn-Acr). | |
3.3. Thermo-gravimetric analysis (TGA)
The TGA thermograms of the synthesized adhesives, along with the standard commercial adhesive, are shown in Fig. 6. The figure shows the thermal degradation patterns of the adhesives from room temperature up to 800 °C. The TGA spectra show the formation of thermally stable polymeric adhesive materials. For the copolymer P(VP-Acr), the weight loss of about 10% was observed from 100 °C up to 235 °C, which could be due to the loss of moisture. P(Acn-Acr) was found to be stable up to 200 °C, and no weight loss was observed. The TGA spectral data clearly shows that the most thermally stable copolymer is P(VP-Acn-Acr), which was found to be stable up to 300 °C. Hence, we can ascertain that P(VP-Acn-Acr) is the most stable adhesive and P(VP-Acr) is thermally the least stable among the synthesized adhesives. The thermal stability of our adhesive systems is much higher when compared to the standard commercial adhesive. This data explains the stability and hence the utility of the formed adhesive at high temperature. The formulation of the copolymer using all the three monomers was necessary to obtain the thermally stable adhesive. The reason for the high thermal stability of P(VP-Acn-Acr) might be the intra-molecular interaction and H-bonding of the different polar groups within the copolymer as compared to the other two copolymers, leading to synergistic interactions.39,40 Acrylic-based adhesives are known to be thermally very stable;40,41 however, it is challenging to synthesize an acrylic-based water-borne adhesive without any aromatic moiety possessing such excellent thermal stability,42 which we have successfully overcome. Obtaining a thermally stable water-borne adhesive is a challenging task. Most of the previous works reported the thermal stability of these adhesives below 300 °C, which is lesser than the values obtained by our system, P(VP-Acn-Acr). All the three synthesized polymer adhesives were completely degraded above 760 °C. Hence, our system could be a perfect water-borne adhesive for high-temperature applications. A comparison of our adhesive with few other water-borne adhesives is shown in Table 1.
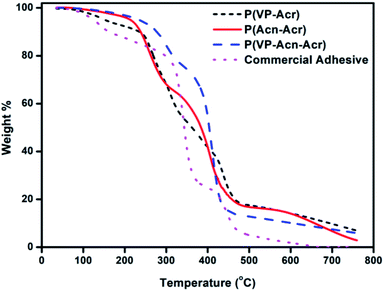 |
| Fig. 6 TGA spectra of the copolymers. | |
Table 1 Comparison of the thermal stability of the P(VP-Acn-Acr) adhesive with some earlier reported water-borne adhesive formulations
Sl. No |
Adhesive system |
Thermal stability |
Ref. |
1 |
P, N-flame retardant that enhances the mechanical strength of the adhesive |
Below 300 °C |
43 |
2 |
Glyc-methacrylate grafted enzyme-treated soybean meal adhesive |
Around 200 °C |
44 |
3 |
Nanoclay supported wood/phenol formaldehyde bond lines |
Below 200 °C |
45 |
4 |
Polyether siloxane diol modified polyurethane adhesive |
268 °C |
46 |
5 |
CNT modified acrylic resin-glycidyl methacrylate |
Below 200 °C |
47 |
6 |
Acrylic pressure-sensitive adhesive |
300 °C |
48 |
7 |
Effect of DMA on the properties of the acrylic latex adhesives |
Around 350 °C |
49 |
8 |
Silicone-based flame retardant adhesive in plywood |
Below 300 °C |
50 |
9 |
Poly(vinyl pyrrolidone-acrylonitrile-acrylic acid) powder adhesive |
300 °C |
Our system |
3.4. X-ray diffraction (XRD)
The XRD plots of the three polymers are shown in Fig. 7. The plots show no sharp peaks, indicating the amorphous behavior of the synthesized polymers, thus suggesting cross-linking. The corresponding peaks for P(VP-Acr), P(Acn-Acr), and P(VP-Acn-Acr) can be observed at the 2θ values of 19.81, 20.21, and 20.13, respectively. It can be noted that the position of the peaks is the same in all the three cases. However, the peak intensity is the least in the case of P(VP-Acn-Acr), suggesting the highest amount of cross-linking in the case of P(VP-Acn-Acr), causing the distortion of the intrinsic lattice arrangement. This distortion leads to a decrease in its crystallinity, thereby causing a decrease in the peak intensity.51,52 The amorphous nature of P(VP-Acn-Acr) also increases the grinding ability and dispersibility of the polymer, hence making it the most deserving candidate to be used as the adhesive.
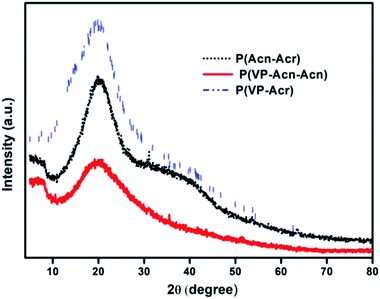 |
| Fig. 7 XRD analysis of the copolymers. | |
3.5. Composition of the commercial adhesive
Commercial water-borne adhesives are composed of different additives, along with the main component, polyvinyl acetate (PVAc). Together with PVAc, plasticizers such as dibutyl fumarate and anti-coalescing agent, such as polyvinyl alcohol, are used. Surfactants such as sodium lauryl sulfate, surface-active agents such as Triton X-200, and curing agents such as sodium carbonate are also present.53–56 Going through the compositions of the commercial adhesive, we can ascertain that our system could be cost-effective.
3.6. Formation of the adhesive gel
Unlike commercial adhesives, our adhesive formulations were achieved by mixing a specific amount of the powdered polymers with water to form the sticky gels. All three sets of polymers were mixed with water to form the respective adhesives. The quantity of water required for adhesive formation was determined by several trials and finally optimized. This step of optimization is important as the sol-to-gel ratio determines and controls the adhesive properties.57 100% w/v dispersion was taken as the standard for the formulation of the adhesive. Typically, 10 mL of water was added dropwise to 10 g of P(VP-Acr) and kept for about 40 minutes for dispersion. After 40 minutes, the polymer dispersion in water was mixed well with the help of a spatula to form a gel-like material, which was used as the adhesive. A similar procedure was used to obtain the adhesives of the polymer powders, P(Acn-Acr) and (VP-Acn-Acr).
The dispersion of the polymer powder, P(VP-Acn-Acr), was checked in different solvents, as shown in Fig. 8(A). The dispersion of P(VP-Acr) and P(Acn-Acr) was also observed in different solvents (ESI, Fig. S2 and S3†). The dispersion of the polymers in organic solvents did not result in the formation of the gel-like adhesive materials. Apart from water, ethanol forms a gel-like material on dispersion up to some extent. The adhesive gels were found to be almost soluble in high boiling solvents such as DMSO. The use of dispersion of DMSO as the adhesive would take longer curing time, which would eventually restrict the practical utility of the adhesives. Thus, water was found to be the most suitable solvent for the formulation of the adhesives, hence restricting the use of hazardous organic solvents. The adhesives formed after dispersion in water are shown in Fig. 8(B).
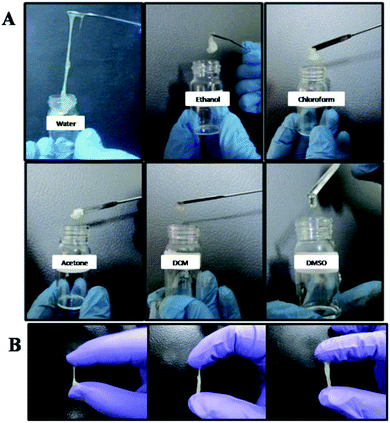 |
| Fig. 8 (A) Dispersion of the polymer powder P(VP-Acn-Acr), in various solvents; (B) dispersion of the polymers P(VP-Acr), P(Acn-Acr), and P(VP-Acn-Acr), respectively, in water as ready-to-use adhesive gels. | |
3.7. GPC analysis
The number average molecular mass (Mn) and weight average molecular mass (Mw) of the polymer adhesives were analysed with the help of GPC. The molecular mass distribution of the polymers is shown in the ESI (Fig. S4(A–C)).† The polydispersity index of P(VP-Acr), P(Acn-Acr), and P(VP-Acn-Acn) was found to be 1.0227, 1.0095, and 1.0122, respectively, which indicates that the formed polymer adhesives are monodisperse.
3.8. Lap shear strength test results
The lap shear strength of the adhesives was taken after applying the adhesive formulation on the surface of the specimen and then attached by applying a minimal force. A small amount of the adhesive formulation (1 g mL−1), typically 0.25 g of the adhesive powder dispersed in 0.25 mL water, was sufficient to be applied in an area of 6.25 cm2. Hence, the application rate of the adhesive was found to be approximately 0.4 mg mm−2 for the preparation of the samples for the lap shear strength test.
3.8.1. Lap shear strength of paper materials. The lap shear strength test of the paper materials was carried out as per the ASTM D-1867 peel method (T-peel test).58 All the adhesives were found to form an extremely strong bond with the paper materials. The oil paper seems to have low GSM value but it is stiffer than normal paper, although in the both cases, tensile failure occurs due to strong bonding with the adhesive. The adhesive strength was observed in three sets for each type of paper material. In all the sets of the three adhesives, specimen failure occurred due to extremely strong adhesive bonding, thus making our adhesives the perfect candidates for paper materials.
3.8.2. Lap shear strength test of wooden materials. All the acrylic acid-based water-borne adhesive formulations were applied to the wooden materials as per the standard ASTM D-906.59 The samples needed no heat curing after the application of the adhesives. The thickness of the adhesive layers was between 0.11 to 0.25 mm. The samples were kept in a desiccator for the lap shear strength test. The lap shear strength tests for the wooden materials were performed as per ASTM D-906 at room temperature. Before the lap shear strength test, the samples were kept at a humidity of 50% and a temperature of 23 °C for seven days (as per ASTM requirements).The lap shear strength tests were carried out for all the three adhesives applied on wooden materials in seven sets to obtain the perfect average strength of the adhesives. To check the real applicability and the market value, we have used one of the most widely used water-borne wood adhesives (commercially available) purchased from the local market and compared the strength with our products. The adhesive strength was calculated in terms of force/area, where the areas of contact of the two wooden parts with the adhesive, i.e., 625 mm2, were considered. P(VP-Acr) and P(Acn-Acr) show low values of lap shear strength when applied to wood. Interestingly, P(VP-Acn-Acr) shows much higher strength than all the other sets, including the commercially available adhesive. In fact, the maximum force required to rupture P(VP-Acn-Acr) was found to be 1344 N, which shows the effectiveness of the adhesive in binding wood materials. Moreover, P(VP-Acn-Acr) has the maximum thermal stability up to 300 °C. This result shows that the adhesive has great production value and can easily remains stable under extreme heat. The obtained values for all the adhesives are given in Table 2. The mean and the standard deviation of the values are presented in the ESI (Table S1).†
Table 2 Applied force and lap shear strength of the prepared adhesives and comparison with the commercially available adhesive
Adhesives |
Sl. No |
The maximum force required to rupture adhesive joints (N) |
Force/width (N mm−1) |
Lap shear strength maximum force/area (kPa) |
P(VP-Acr) adhesive |
1 |
122.90 |
4.726 |
486 |
2 |
172.90 |
6.570 |
3 |
127.00 |
4.922 |
4 |
29.65 |
1.136 |
5 |
77.40 |
2.964 |
6 |
16.65 |
0.638 |
7 |
304.00 |
11.740 |
P(Acn-Acr) adhesive |
1 |
13.85 |
0.521 |
78 |
2 |
22.50 |
0.843 |
3 |
5.35 |
0.2004 |
4 |
21.00 |
0.824 |
5 |
20.33 |
0.779 |
6 |
48.35 |
1.582 |
7 |
Specimen failure |
— |
P(VP-Acn-Acr) adhesive |
1 |
763.00 |
30.520 |
2150 |
2 |
693.00 |
26.650 |
3 |
763.00 |
29.350 |
4 |
710.00 |
27.300 |
5 |
1344.00 |
52.900 |
6 |
707.00 |
27.190 |
7 |
897.00 |
34.500 |
Commercial adhesive |
1 |
469.50 |
18.200 |
1331 |
2 |
627.00 |
24.300 |
3 |
555.00 |
20.940 |
4 |
401.50 |
15.560 |
5 |
832.00 |
31.760 |
6 |
303.60 |
11.950 |
7 |
288.00 |
11.350 |
For water-borne adhesives, the shear strength increases with the increase in cross linking.60 The high value of the adhesive shear strength of P(VP-Acn-Acr) might be due to the extensive cross-linking compared to the other two adhesives.
3.9. Fluorescence characteristics of the adhesives
The polymer adhesives P(VP-Acr), P(Acn-Acr), and P(VP-Acn-Acr) are all fluorescent in nature, as evident from the images under a UV lamp, as shown in Fig. 3. The reason for the fluorescence behaviour of the synthesized copolymers could be the internal charge transfer (ICT).61 Because of the absence of any conjugation/aromatic moieties in the polymers, fluorescence due to π to π* transition could be ruled out. Also, due to the presence of N-containing moieties, along with the chromophores, fluorescence due to aggregation-induced emission (AIE) could be ruled out.62 The presence of carbonyl groups as the chromophore might be responsible for ICT due to its easily accessible electrons, leading to the fluorescence characteristics of the adhesives.63 The fluorescent nature of the adhesive polymers makes them suitable for their utilization in crafts and museums to detect the fracture joints under a UV lamp. Also, the adhesives can be utilized in an anti-counterfeit application to deliver secret messages.
3.9.1. Fluorescence characteristics of the adhesives for the detection of joint fractures. Most of the adhesives used in museums and crafts are non-fluorescent, which makes it difficult to detect the fracture parts after the application of adhesives. McFadden et al. have successfully shown the utility of fluorescent adhesives for the detection of fracture joints in antiques and crafts.64 Most of the time, the development of the fluorescent adhesive required the use of dyes or additives, in which the leaching of dyes and additives from the resins may cause environmental and health problems. In this work, fluorescence adhesives were obtained without the use of external agents. The adhesives could be of great use in crafts to detect the fractured portion under a UV lamp (365 nm), whereas the fracture joints are unnoticeable under normal light. Fig. 9(A) shows a broken ceramic specimen bonded by P(VP-Acn-Acr) and the visibility of the bonded portion under long-wavelength UV light.
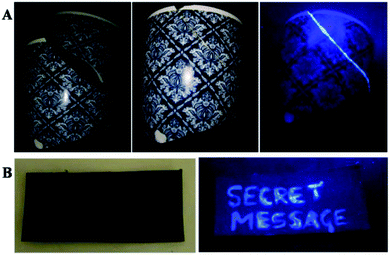 |
| Fig. 9 (A) The picture depicting the bonding of a broken specimen design (left) by P(VP-Acn-Acr) and the visibility of the broken joint under normal light (middle) and long-wavelength UV light (right); (B) the figure depicting the visibility of the words written by the adhesive under UV light (365 nm), which are invisible under normal light. | |
3.9.2. Applicability of the adhesives in anti-counterfeit applications. The adhesives being fluorescent can be useful in sending secret messages, which is an additional feature of the adhesive systems. In the past, polymers with anti-counterfeit applications have been developed but the reported anti-counterfeiting fluorescent polymeric materials were obtained by the addition of fluorescent media such as carbon dots.65 In our system, this property was obtained without the use of external fluorescent agents. Hence, our adhesives can be of additional use for anti-counterfeiting of different delicate designs, including logos and fingerprints, and to pass secret messages. Fig. 9(B) shows the visibility of ‘SECRET MESSAGE’ under UV light, which is not otherwise visible under normal light.
4. Conclusions
In this work, three water-borne adhesives, namely, poly(1-vinyl-2-pyrrolidone-co-acrylic acid), poly(acrylonitrile-co-acrylic acid), and poly(1-vinyl-2-pyrrolidone-co-acrylonitrile-co-acrylic acid) have been synthesized successfully. The synthesized acrylic-acid based adhesives were found to be water-based; hence, water formulations can be easily made. Being water-based, the adhesives minimize the problems associated with the use of toxic organic vapors in the adhesive industry. The best part of the synthesized adhesives is that they can be stored in the form of powders for the long-term use, which also makes them easy to carry and handle. The adhesives were found to be thermally stable; one of the adhesives showed thermal stability up to 300 °C. The lap shear strength of the adhesives was found to be appreciably high; one of our systems showed strength greater than one of the most popular commercially available adhesives. The adhesives were found to be fluorescent, without the addition of any external fluorescent agent. The fluorescence characteristic of the adhesives makes them suitable candidates for the detection of fractured joints under UV light, which is not otherwise visible under normal light, thus making them important tools in the craft-making industry and related to antiques. Moreover, the polymers can also be used as anti-counterfeiting agents in intelligence. Thus, in a nutshell, we tried to develop adhesives with multiple applications and better storage options, thus making them better options than commercially available adhesives.
Conflicts of interest
There are no conflicts to declare.
Acknowledgements
The authors are thankful to IASST and the Department of Science and Technology, Government of India for funding this work. The authors are also thankful to CIF-IASST, CIPET-Guwahati, and SAIC-Tezpur University for providing the instrumentation facilities.
Notes and references
- M. S. Miller, J. C. O'Kane, A. Niec, R. S. Carmichael and T. B. Carmichael, ACS Appl. Mater. Interfaces, 2013, 5, 10165–10172 CrossRef CAS PubMed
. - T. Barnes and I. Pashby, J. Mater. Process. Technol., 2000, 99, 72–79 CrossRef
. - J.-t. Zhang, H.-n. Lu and F.-q. Cao, J. Propul. Technol., 2008, 29, 13 Search PubMed
. - K. L. Mittal and A. Pizzi, in Handbook of Adhesive Technology, Revised and Expanded, CRC Press, 2003, pp. 9–20 Search PubMed
. - J. Delmonte, Technology of adhesives, 1947 Search PubMed
. - Y. Chen, Y. Zhang, F. Wang, W. Meng, X. Yang, P. Li, J. Jiang, H. Tan and Y. Zheng, Mater. Sci. Eng., C, 2016, 63, 18–29 CrossRef CAS PubMed
. - Y. Wang, J. Wang, Z. Yuan, H. Han, T. Li, L. Li and X. Guo, Colloids Surf., B, 2017, 152, 252–259 CrossRef CAS PubMed
. - M. Zhu, D. Hua, H. Pan, F. Wang, B. Manshian, S. J. Soenen, R. Xiong and C. Huang, J. Colloid Interface Sci., 2018, 511, 411–423 CrossRef CAS PubMed
. - N. M. Smeets, Eur. Polym. J., 2013, 49, 2528–2544 CrossRef CAS
. - L. Solhi, M. Atai, A. Nodehi, M. Imani, A. Ghaemi and K. Khosravi, Dent. Mater., 2012, 28, 369–377 CrossRef CAS PubMed
. - G. C. Mays and A. R. Hutchinson, Adhesives in civil engineering, Cambridge University Press, 1st edn, 2005 Search PubMed
. - A. Oliveira, K. Guimarães and N. Cerize, Eur. Polym. J., 2015, 71, 268–278 CrossRef CAS
. - K. Singha, Am. J. Polym. Sci., 2012, 2, 39–49 CrossRef CAS
. - A. Agirre, C. d. l. Heras-Alarcón, T. Wang, J. L. Keddie and J. M. Asua, ACS Appl. Mater. Interfaces, 2010, 2, 443–451 CrossRef CAS PubMed
. - D. Satas, Handbook of pressure sensitive adhesive technology, Springer US, 2nd edn, 1989 Search PubMed
. - M. Do Amaral, A. Roos, J. M. Asua and C. Creton, J. Colloid Interface Sci., 2005, 281, 325–338 CrossRef CAS PubMed
. - C. Creton and E. Papon, MRS Bull., 2003, 28, 419–423 CrossRef CAS
. - A. Lopez, E. Degrandi-Contraires, E. Canetta, C. Creton, J. L. Keddie and J. M. Asua, Langmuir, 2011, 27, 3878–3888 CrossRef CAS PubMed
. - T. Holt, K. Fazende, E. Jee, Q. Wu and J. A. Pojman, J. Appl. Polym. Sci., 2016, 133(40), 44064 CrossRef
. - X. Liu, C. Zhu, Q. Xiang and L. Dong, 5th International Conference on Advanced Materials and Computer Science (ICAMCS 2016), Atlantis Press, 2016 Search PubMed
. - R. C. R. Nunes, in Progress in Rubber Nanocomposites, Elsevier, 2017, pp. 463–494 Search PubMed
. - R. C. Law, Macromol. Symp., 2004, 208, 255–265 CrossRef CAS
. - Y. H. Jung, T.-H. Chang, H. Zhang, C. Yao, Q. Zheng, V. W. Yang, H. Mi, M. Kim, S. J. Cho and D.-W. Park, Nat. Commun., 2015, 6, 7170 CrossRef PubMed
. - D. Dhingra, M. Michael, H. Rajput and R. Patil, J. Food Sci.
Technol., 2012, 49, 255–266 CrossRef CAS PubMed
. - D. Klemm, B. Heublein, H. P. Fink and A. Bohn, Angew. Chem., Int. Ed., 2005, 44, 3358–3393 CrossRef CAS PubMed
. - J.-S. Park, B. W. Bang, S. J. Hong, E. Lee, K. S. Kwon, H. K. Kim, Y. W. Shin and D. H. Lee, Endoscopy, 2019, 51(05), 458–462 CrossRef PubMed
. - S. Fujii, S. Sawada, S. Nakayama, M. Kappl, K. Ueno, K. Shitajima, H.-J. Butt and Y. Nakamura, Mater. Horiz., 2016, 3, 47–52 RSC
. - B. K. Ahn, S. Kraft, D. Wang and X. S. Sun, Biomacromolecules, 2011, 12, 1839–1843 CrossRef CAS PubMed
. - D. Chattopadhyay and D. C. Webster, Prog. Polym. Sci., 2009, 34, 1068–1133 CrossRef CAS
. - J. J. Gallagher, M. A. Hillmyer and T. M. Reineke, ACS Sustainable Chem. Eng., 2016, 4, 3379–3387 CrossRef CAS
. - Y. Namura, T. Tsuruoka, C. Ryu, M. Kaketani and N. Shimizu, Eur. J. Orthod., 2010, 32, 620–626 CrossRef PubMed
. - P. H. D. Alpino, J. C. Pereira, N. R. Svizero, F. A. Rueggeberg and D. H. Pashley, J. Adhes. Dent., 2006, 8, 285 Search PubMed
. - H. L. Barros and V. Stefani, Forensic Sci. Int., 2016, 263, 83–91 CrossRef CAS PubMed
. - J. E. Reeb, M. R. Milota and W. D. K. Association, J. Sci. Res., 1999, 66–74 Search PubMed
. - Z. Wang, Z. Li, Z. Gu, Y. Hong and L. Cheng, Carbohydr. Polym., 2012, 88, 699–706 CrossRef CAS
. - S. Upadhyaya, R. Sarma, A. Barik and N. Sen Sarma, Adv. Polym. Technol., 2019, 2019, 1–12 CrossRef
. - L. Li, Z. Yin, F. Li, T. Xiang, Y. Chen and C. Zhao, J. Membr. Sci., 2010, 349, 56–64 CrossRef CAS
. - J. A. Brydson, Plastics materials, Elsevier, 7th edn, 1999 Search PubMed
. - Y. Jiugao, W. Ning and M. Xiaofei, Starch – Stärke, 2005, 57, 494–504 CrossRef
. - J. Araujo, W. Waldman and M. De Paoli, Polym. Degrad. Stab., 2008, 93, 1770–1775 CrossRef CAS
. - Y. Zhang, S. Qi, X. Wu and G. Duan, Synth. Met., 2011, 161, 516–522 CrossRef CAS
. - S. R. Hartshorn, Structural adhesives: chemistry and technology, Springer Science & Business Media, 1st edn, 2012 Search PubMed
. - S. Wang, X. Du, Y. Jiang, J. Xu, M. Zhou, H. Wang, X. Cheng and Z. Du, J. Colloid Interface Sci., 2019, 537, 197–205 CrossRef CAS PubMed
. - Z. Qin, Q. Gao, S. Zhang and J. Li, BioResources, 2013, 8, 5369–5379 CrossRef
. - X. Wang, S. Wang, X. Xie, L. Zhao, Y. Deng and Y. Li, Int. J. Adhes. Adhes., 2017, 74, 92–99 CrossRef CAS
. - H. Yan-ting, C. Zheng, D. Wei, Z. Fan and X. Zhong-yin, J. Thermoplast. Compos. Mater., 2017, 30, 107–120 CrossRef
. - M. Wu, S. Ge, C. Jiao, Z. Yan, H. Jiang, Y. Zhu, B. Dong, M. Dong and Z. Guo, Polymer, 2020, 122547 CrossRef CAS
. - Y. Xu, Y. Xu, W. Zhu, W. Zhang, Q. Gao and J. Li, Polymers, 2018, 10, 1016 CrossRef PubMed
. - C. Fang, Y. Jing, Y. Zong and Z. Lin, Int. J. Adhes. Adhes., 2016, 71, 105–111 CrossRef CAS
. - W. Wang, M. Zammarano, J. R. Shields, E. D. Knowlton, I. Kim, J. A. Gales, M. S. Hoehler and J. Li, Constr. Build. Mater., 2018, 189, 448–459 CrossRef CAS PubMed
. - F. I. El-Dib, M. H. Hussein, H. H. Hefni, G. Eshaq and A. E. ElMetwally, J. Appl. Polym. Sci., 2014, 131, 41078 CrossRef
. - K. Das, D. Ray, N. Bandyopadhyay, A. Gupta, S. Sengupta, S. Sahoo, A. Mohanty and M. Misra, Ind. Eng. Chem. Res., 2010, 49, 2176–2185 CrossRef CAS
. - E. Jasiukaitytė-Grojzdek, M. Kunaver, D. Kukanja and D. Moderc, Int. J. Adhes. Adhes., 2013, 46, 56–61 CrossRef
. - V. Kovačević, S. Lučić, D. Hace, A. Glasnović, I. Šmit and M. Bravar, J. Adhes., 1994, 47, 201–215 CrossRef
. - Z. Z. Gao and F. Liao, Adv.Mater. Res., 2011, 181, 287–292 Search PubMed
. - L. Chen, Z. Xiong, Q. Li, Z.-u. Din and H. Xiong, Int. J. Biol. Macromol., 2019, 140, 1026–1036 CrossRef CAS PubMed
. - R. S. Gurney, A. Morse, E. Siband, D. Dupin, S. P. Armes and J. L. Keddie, J. Colloid Interface Sci., 2015, 448, 8–16 CrossRef CAS PubMed
. - Z. Ophir, A. Buchman, F. Flashner, I. Liran, H. Simons and H. Dodiuk, J. Adhes. Sci. Technol., 1995, 9, 159–175 CrossRef CAS
. - S. D. Desai, J. V. Patel and V. K. Sinha, Int. J. Adhes. Adhes., 2003, 23, 393–399 CrossRef CAS
. - J. Hu, K. Peng, J. Guo, D. Shan, G. B. Kim, Q. Li, E. Gerhard, L. Zhu, W. Tu and W. Lv, ACS Appl. Mater. Interfaces, 2016, 8, 17499–17510 CrossRef CAS PubMed
. - J. R. Lakowicz, Principles of fluorescence spectroscopy, Springer Science & Business Media, 2013 Search PubMed
. - X. Miao, T. Liu, C. Zhang, X. Geng, Y. Meng and X. Li, Phys. Chem. Chem. Phys., 2016, 18, 4295–4299 RSC
. - A. A. M. Prabhu, S. Siva, R. Sankaranarayanan and N. Rajendiran, J. Fluoresc., 2010, 20, 43–54 CrossRef CAS PubMed
. - P. D. McFadden, K. Frederick, L. A. Argüello, Y. Zhang, P. Vandiver, N. Odegaard and D. A. Loy, ACS Appl. Mater. Interfaces, 2017, 9, 10061–10068 CrossRef CAS PubMed
. - B. De, B. Voit and N. Karak, ACS Appl. Mater. Interfaces, 2013, 5, 10027–10034 CrossRef CAS PubMed
.
Footnote |
† Electronic supplementary information (ESI) available: Dispersions of P(VP-Acr) and P(Acn-Acr) in various solvent systems, gel permeation chromatography data of P(VP-Acr), P(Acn-Acr), and P(VP-Acn-Acr), designing of paper and wood samples for adhesive strength test and statistical analysis of the mechanical test data. See DOI: 10.1039/d0ra03782f |
|
This journal is © The Royal Society of Chemistry 2020 |
Click here to see how this site uses Cookies. View our privacy policy here.