DOI:
10.1039/D0RA02376K
(Paper)
RSC Adv., 2020,
10, 25918-25928
Development of quantitative 13C NMR characterization and simulation of C, H, and O content for pyrolysis oils based on 13C NMR analysis†
Received
14th March 2020
, Accepted 13th June 2020
First published on 9th July 2020
Abstract
Bio-oil is a valuable liquid product obtained from pyrolysis of biomass and it contains tens of hundreds of compounds, which brings about difficulties for characterization with various analytical methods. 13C NMR has advantages over other detection methods as it can characterize the entire composition of bio-oil and distinguish different types of carbon. But various shortcomings limit the application of 13C NMR. This study was carried out to develop a quantitative 13C NMR method to determine different functional groups in pyrolysis bio-oils with short NMR time and good accuracy, and propose a simulation of C, H, and O content for pyrolysis oils based on 13C NMR analysis. In order to solve long-term NMR problems, relax reagent has been added and the results show that it is an effective way to shorten the NMR time. Moreover, the aging problem is not obvious in the short-term NMR test, so the effect of aging on the test results can be neglected. Three types of substances with different oxygen content have been employed to verify the feasibility of the C, H, and O calculation methods and the result errors of all elements are small, which shows it is reliable for the simulation data of C, H and O content.
1. Introduction
Pyrolysis is a process in which a substance isolated from air is heated to a certain temperature to form solid, liquid and gaseous products1 and a series of physical changes and chemical reactions take place. Among the various conversion technologies for the utilization of biomass resources2,3 that are under study, pyrolysis as a thermochemical conversion process has been reported4,5 as one of the feasible approaches of producing precursors of biofuels, known as pyrolysis bio-oil.6–8 Pyrolysis technology of biomass can transform biomass, which is low in energy density and tough to process by general means, into a high calorific value substance at a low cost. During the pyrolysis process, the volume of biomass is greatly reduced, and biomass is converted into bio-oil that is easy to transport and store. Bio-oil, which can be used for the precursors of biofuels, is a kind of dark-brown, polar and viscous liquid with a high moisture content and a very low nitrogen and sulfur contents. The composition of bio-oil is extremely complex since it consists of various kinds of organic substances derived from the thermal decomposition of cellulose, hemicellulose and lignin. Bio-oil is mainly used in the production of combustion heating, electric power, fuels9 and chemicals. Moreover, high value-added chemicals can also be extracted10 from bio-oils, and the potential value of certain compounds11 in bio-oil is much higher than that of the recovered oil even if the recovery amount is very small. However, on account of the complex ingredient of pyrolysis oil, subsequent upgrading is indispensable for the research of development in the future.12 Simultaneously, the in-depth and quantitative characterization of pyrolysis oil is in urgent need.13
But traditional analysis strategies have difficulties in characterization of bio-oil, since the various undesirable properties and extreme complexity nature of bio-oil bring a great barrier to usual analysis methods, such as GPC, GC-MS and FT-IR. Individual components are usually detected by GC-MS, however, due to the poor volatility of some components in bio-oil, only a small part of bio-oil can be analysed by GC. Moreover, the ability to provide detailed information and insight into the whole portion of bio-oil for spectroscopic technique, e.g., FT-IR, is limited because of the complexity for bio-oil. Owing to the complicated components, characterization of the whole portion of bio-oil will provide insight into the following chemical upgrading process, which is a challenging but crucial undertaking.
Nuclear magnetic resonance (NMR) has the ability to analyse the whole portion of bio-oil and has some advantages over traditional methods as it can characterize different functional groups in the bio-oil and provide quantitative results.14–16 Sundry NMR researches17–19 have been used to better comprehend the structures and compositions of thermally converted bio-oils. In organic synthesis, NMR technology with wide applications can not only analyse the structure and determine the configuration of reactants or products, but also study the charge distribution, positioning effect in synthesis reactions and discuss the reaction mechanism.20–22
13C NMR is one of the most commonly used NMR methods to characterize different functional groups in the organic compounds or mixtures. Compared with 1H NMR, although 13C NMR takes a relatively long testing time, it can get more information about functional groups of bio-oil owing to less spectral overlap and broader chemical shift range of 13C NMR, which means 13C NMR has more advantages over 1H NMR.23 It also has been developed to identify more than 15 different functional groups in the pyrolysis oils.10,24,25 Besides, the Distortionless Enhancement by Polarization Transfer (DEPT) spectra of 13C NMR could be able to tell the differences from various carbons including primary, secondary, tertiary and quaternary carbons.13 Shahrzad Hosseinnezhad et al.10,26 detailed the bio-oil obtained from the slow pyrolysis of wood pallet, corn stover, miscanthus and swine manure through 13C NMR to provide more information about various functional groups and successfully confirmed the conversion of carbohydrates during thermal conversion process. Xiaoxiang Jiang et al.10,27 observed the changes for different peaks in specific regions with 13C NMR experiments to investigate the thermal stability of bio-oil and bio-diesel blends. Comparison of 13C NMR spectra has been made between extracted fractions of bio-oil and the unfractionated crude bio-oil, which indicated the extraction process divided the crude bio-oil into two parts.28 Great efforts have been made to characterize bio-oil using 13C NMR method in order to fully understand the composition of this complex mixture. But one of the drawbacks of 13C NMR is long NMR test time, which will take >20 h for a quantitative 13C NMR test. Relax reagent will be needed for saving the NMR time. Moreover, the produced pyrolysis oils always have limitations in applications due to several undesirable properties including poor volatility, corrosiveness, cold flow problems and relatively high molecular weight, oxygen content, acidity, and viscosity.29–31 But the most challenging one is the aging process, during which molecular weight, oxygen content, acidity and viscosity will increase.32,33 Aging problems in the NMR process can cause inaccurate measurement results, which should be avoided. Therefore, it is essential to test the aging process for the bio-oil in 13C NMR solvent to measure the effects of aging problem.
Elemental analysis is also a chemical analysis method for studying the composition of elements in organic compounds. By using the traditional elemental analyser, the carbon, hydrogen and nitrogen contents in the sample can be quickly and quantitatively obtained. However, since there is no simple qualitative method for the determination of oxygen, the oxygen content of the sample is used to obtain by mass difference. Rohan Stanger et al. introduced a new thermal characterization method—Dynamic Elemental Thermal Analysis (DETA) and demonstrated it as a means of calculating the intrinsic pyrolysis yields (i.e. char, tar, gas), analysing elemental compositions and estimating thermal properties.34 Accordingly, based on the employment of quantitative 13C NMR, DEPT 90 and DEPT 135 means for determining different functional groups in pyrolysis oils, a novel method of simulation of C, H and O contents by 13C NMR is very valuable, during which the oxygen content can be directly calculated.
This report details the results of experiments with model compounds mixtures and duplicated tests that demonstrate the accuracy and precision of the quantitative 13C NMR method measuring different functional groups in bio-oil and the C, H, O contents calculation method for bio-oil. Chromium acetylacetonate (Cr(acac)3) was chosen as the relax reagent and the influences of different concentrations of relax reagent on NMR time have been examined to find the most suitable concentration. Moreover, the comparison of the quantitative NMR results between long NMR time without relax reagent and short NMR time with relax reagent for various bio-oil samples has been provided to inspect the accuracy of the quantitative 13C NMR method with relax reagent. In order to examine the effect of aging on quantitative 13C NMR test results, the aging experiments for 3 different types of bio-oil with the use of 5 mg ml−1 Cr(acac)3 were conducted. The accuracy of C, H, O calculation method was tested with three different types of substances with different oxygen contents. This study will built up a new standard quantitative 13C NMR method with good precision and short NMR time, and develop a novel approach of simulation of C, H and O contents based on quantitative 13C NMR results, which few studies discussed before.
2. Experimental section
The experiment first developed a quantitative 13C NMR methodology by testing bio-oil samples under various NMR conditions, and checked the aging process for three different kinds of bio-oil under the optimized NMR condition. The bio-oil samples used in this investigation were produced from four different kinds of raw materials, which can be classified into two groups: single biomass (oak wood and cottonwood) and the mixture of biomass and coal (the mixture of saw powder and GBW11110 and the mixture of cottonwood and GBW11110). Oak wood was obtained in Georgia, USA. Cottonwood and saw powder were collected in Sipailou Campus, Southeast University, Nanjing, China. GBW11100, a type of standard coal, was produced in Shandong Metallurgical Research Institute, Jinan, China.
Later, the experiment, examining the accuracy for the simulation of C, H and O contents for pyrolysis oils based on 13C NMR analysis, was divided into three parts according to different oxygen contents of different samples including oxygen-free mixtures, oxygen-deficient compounds and oxygen-rich raw tars (all experiments for the calculation of C, H, O contents of bio-oil were performed on dry basis of bio-oil). Two standard mixtures obtained from AccuStandard Inc. (USA) containing Stock Sim Dis Paraffin Solution/#1 ASTM-P-0050 (standard #1) and Hydrocarbon Test Mixture/#2 D-5443-93-HTM (standard #2) were chosen as oxygen-free mixtures. The contents for various components in these two standards have been summarized in Tables S1 and S2.† Oxygen-deficient compounds were obtained from 8 products from industrial fluid catalytic cracking units and the vapours were produced by the pyrolysis of two types of oak wood. Detailed descriptions of each feed mixture are shown in Table S3.† Six kinds of oxygen-rich pyrolysis oils were prepared for test, including the bio-oils obtained from the pyrolysis of bituminous coal under N2 (NSC(N2)) or CO2 (NSC(CO2)) atmosphere at 773 K, platanus sawdust under N2 (PS(N2)) or CO2 (PS(CO2)) atmosphere at 773 K and two types of oak wood (OW1, OW2) under N2 atmosphere at 773 K. All liquid products in this section were examined by using developed standard method before.
2.1 Preparation of pyrolysis oils
All pyrolysis experiments were processed in the tube furnace under N2 or CO2 atmosphere, which is discussed previously.35,36 The flow rate of carrier gas was 500 ml min−1 and ventilation was required for 10 minutes before pyrolysis to ensure the pyrolysis gas environment. Around 10 g feedstock was placed in two quartz sample boats, positioned in the middle of pyrolysis equipment, at 773 K with heating rate of 100 K min−1, 20 min char residence time and 3 min gas residence. Condensing tube was connected to the quartz tube and the condensed pyrolysis oil was collected at the outlet of the condensing tube.
2.2 NMR methods
Bio-oils (∼250 μl) were dissolved in dimethyl sulfoxide-d6 (DMSO-d6, Adamas, 99.8 atom% D) (250 μl) with different concentrations (0, 1 or 5 mg ml−1) of Cr(acac)3 (Aldrich, 99.99% trace metals basis), which was chosen as relax reagent. A AVANCE III HD 600 MHz NMR spectrometer (Bruker Inc., Zurich, Switzerland) was used to record NMR spectral data reported in this study at room temperature. An inverse gated decoupling pulse sequence (zgig) and 90° pulse angle were chosen as the NMR parameters used in quantitative 13C NMR. Different pulse delays have been examined for different samples. During DEPT experiments, selection angle parameter of 90° was set for DEPT 90 and selection angle parameter of 135° was applied for DEPT 135. DEPT 90 spectrum only shows the upward peaks for tertiary carbons. Downward peaks for secondary carbons and upward peaks for primary and tertiary carbons are presented on DEPT 135 spectrum. Therefore, according to DEPT 90 and DEPT 135, different kinds of carbons can be distinguished on the 13C NMR spectrum.
Inversion-recovery method was employed to measure the T1, which was calculated with Bruker's TopSpin software.
The integrations for different functional groups of pyrolysis oil have been conducted by using assignment ranges listed in Table S4.† The results for different functional groups in the whole portion of bio-oils can be reported as carbon % (mol or wt).
2.3 Elemental analysis of pyrolysis oils
EURO EA3000 elemental analyser (Euro Vector Inc., Pavia, Italy) was used to explore the constituents of tar which utilized combustion to obtain hydrogen, carbon, sulfur, nitrogen contents and confirm the oxygen content by mass difference. The water content of bio-oil was obtained by Moisture Analyser (HE53/02, METTLER TOLEDO). According to the measured moisture content of bio-oil and the C, H, O content of bio-oil measured by traditional methods, the C, H, O content based on dry basis can be obtained, which can later compare with the C, H, O content obtained by NMR methods.
3. Results and discussion
3.1 Quantitative characterization of pyrolysis oils by NMR
Measurement for relaxation delay time (T1). T1 is a very important parameter for quantitative 13C NMR. The pulse delays (d1) should be set as five times of T1 to provide quantitative result. For a normal bio-oil, the T1 could be as long as 10 s, which will require a >50 s pulse delay and a lot of NMR time (>20 h). Relax reagent will be needed for saving the NMR time. The influences for concentrations of relax reagent on the T1 of bio-oil calculated by Bruker's TopSpin software have been examined and the results have been shown in Table S5.†37 After adding 1 mg ml−1 Cr(acac)3 the longest T1 decreased to 2.2 s, which will require at least 2.2 s × 5 = 11 s pulse delay. After adding 5 mg ml−1 Cr(acac)3 the longest T1 decreased to 0.46 s, which will only require a 0.46 s × 5 = 2.3 s pulse delay. Although high concentration relax reagent can decrease T1, it will also reduce the resolution of the spectrum, which indicates concentrations greater than 5 mg ml−1 will affect the accuracy of the results. Therefore, adding 5 mg ml−1 Cr(acac)3 was proved to be an appropriate way to shorten NMR time.
Optimization of NMR test conditions. To find the optimal NMR conditions, 7 pyrolysis bio-oil samples produced from oak wood were tested under different NMR conditions, in which various concentrations of Cr(acac)3 and numbers of scans were set. The quantitative 13C NMR result for pyrolysis oil sample without relax reagent, for which pulse delay was set as 60 s (Fig. S1† and Table 1), was chosen as the control sample. After adding 1 mg ml−1 Cr(acac)3, quantitative 13C NMR result for pyrolysis oil sample with pulse delay set as 15 s was examined (Fig. S2† and Table 1). The pulse delay (d1) decreased rapidly from 60 s to 15 s with 1 mg ml−1 Cr(acac)3 as it calculated by software, which indicated NMR time was greatly reduced compared with the NMR time for pyrolysis oil without relax reagent, and the differences between these two NMR results were <5.5%, showing small errors between these two samples. Moreover, this result proved the correctness of the calculation that relax reagent could greatly reduce NMR time. The pyrolysis oil sample with 5 mg ml−1 relax reagent and 15 s pulse delay was also tested (Fig. S3† and Table 1) and the results were very close to those of the control group as the biggest difference is 2.2%. The results of samples with different concentrations of Cr(acac)3 proved that the use of relax reagent would not only reduce test time but also provide precise results. Moreover, examinations have been taken for three quantitative 13C NMR tests for pyrolysis oil sample with 5 mg ml−1 relax reagent and shorter pulse delay (3 s) and the results are provided in Fig. S4† and Table 1. Averages and standard deviations for the condition performed in triplicate were calculated to compare with other values at other conditions. The averages show that the bio-oil was composed of 15.2% carbonyl, 9.1% aromatic C–O, 2.1% aromatic C–C, 12.5% aromatic C–H, 29.6% levoglucosan, 45.0% aliphatic C–O, 3.3% methoxyl, 12.8% aliphatic C–C, 6.2% methyl-aromatic and 0.7% methyl-aromatic′. The maximum standard deviation was 1.9 for levoglucosan, which indicated that the three measurements were very stable and accurate. The errors between average calculation results and the results under base condition (0 mg ml−1) were <5.0%. Although these three NMR tests only took 1.5 h NMR time, the accuracy of the results was comparable to that of the result taken more than 20 h NMR time. All results of quantitative 13C NMR for bio-oil samples with 0, 1, and 5 mg ml−1 Cr(acac)3 have been examined and summarized in Table 1. Although there are some differences between different bio-oil samples, which may be from the sampling of bio-oil, all of the carbon mol% for different functional groups in different pyrolysis oil samples are close to each other. The influence from numbers of scans also has been examined and the results have been shown in Fig. S5† and Table 1. When compared different spectrums in Fig. S5,† it seems that 1k scans are enough for most of the peaks since the largest difference is 1.8%, and the integration results are also comparable with long time scan (>8 h NMR time). All NMR results indicate the optimized experimental condition will be the use of 5 mg ml−1 Cr(acac)3, 3 s pulse delay and 1k scans, which only requires 1.5 h NMR time.
Table 1 Quantitative 13C NMR for bio-oil samples produced from oak wood with 0, 1, 5 mg ml−1 relax reagent and different pulse delay (d1), the results shown as carbon mol%
Functional groups |
Integration |
0 mg ml−1, d1 = 60 s |
1 mg ml−1, d1 = 15 s |
5 mg ml−1, d1 = 15 s |
5 mg ml−1, d1 = 3 s |
5 mg ml−1, d1 = 3 s |
5 mg ml−1, d1 = 3 s |
5 mg ml−1, d1a = 3 s |
This experiment used 8k scans and other experiments used 1k scan. |
 |
16.2 |
14.7 |
14.0 |
14.8 |
15.6 |
15.3 |
13.8 |
 |
7.7 |
7.0 |
9.3 |
9.2 |
8.6 |
9.5 |
10.2 |
 |
3.0 |
3.0 |
3.4 |
2.0 |
2.4 |
1.8 |
3.9 |
 |
12.6 |
12.8 |
13.1 |
13.4 |
13.1 |
10.9 |
13.3 |
 |
30.4 |
28.8 |
28.8 |
30.9 |
27.0 |
31.0 |
28.8 |
 |
40.0 |
45.5 |
40.7 |
44.6 |
44.6 |
45.9 |
43.8 |
 |
3.3 |
3.4 |
2.8 |
3.3 |
3.1 |
3.6 |
4.0 |
 |
17.2 |
13.7 |
16.7 |
12.8 |
12.6 |
12.9 |
11.0 |
 |
7.3 |
6.3 |
6.6 |
6.9 |
5.1 |
6.5 |
5.1 |
 |
1.0 |
0.8 |
0.8 |
0.6 |
0.6 |
0.8 |
0.5 |
Aging process for bio-oil under optimal condition. Bio-oil is an unstable organic mixture owing to aging problems, which brings about changes in physicochemical properties. It is necessary to examine the aging process during the 13C NMR test since long NMR time will cause aging problems.To test the aging process for the bio-oil in quantitative 13C NMR solvent, 48 hour in situ aging tests for three bio-oil samples with 5 mg ml−1 relax reagent have been examined. To make sure the bio-oil is “fresh”, these bio-oil samples were prepared just before the aging test, therefore, due to the sampling, there are some differences between these samples, which has been discussed previously. For the pyrolysis oil produced from oak wood, samples were tested every 8 h (Fig. S6,† 1 and Table S6†). The results of 8 hour aging test showed that levoglucosan (43%) and aliphatic C–O (31.4%) still took the most part of the whole portion after 8 h aging process, and other components of the sample stayed constant compared with the “fresh” bio-oil (Table 1). And the results for the bio-oil produced from oak wood after 16, 24, 32, 40 and 48 h aging process also showed that there were very limited differences (<3%) for different functional groups before and after aging process, which indicated that the aging process for this bio-oil in 13C NMR solvent was very slow and aging would not affect test result. The limited differences may be due to the processing of different spectrums. To verify if the aging process is also slow in other types of bio-oil with relax reagent, two additional aging tests for bio-oil produced from cottonwood and bio-oil produced from the mixture of cottonwood and coal were examined (every 12 h). Fig. S7,† 2 and Table S7† showed the quantitative 13C NMR results for the bio-oil produced from cottonwood. Different from the oak wood bio-oil, the composition of cottonwood bio-oil changed a lot versus time, especially for carbonyl, aromatic C–C and aromatic C–H, which suggested aging problem occurred in this bio-oil. With the aid of acids, aldehydes were active compounds in bio-oil, and aldehydes could react with other compounds in bio-oil via condensation reaction such as aldol condensation reaction, during which the number of C
O bonds would decrease.38,39 Instable organic peroxides, present in pyrolysis bio-oil, could produce radicals, which would later cause the condensation reaction to form new aromatic C–C bonds.40 But in the first few hours, the change of bio-oil was small. Therefore, short-term testing helps to get accurate results. And the quantitative 13C results for the bio-oil produced from the mixture of cottonwood and coal are presented in Fig. S8,† 3 and Table S8,† which show complex composition different from the other two types of bio-oil. After 48 hour aging process, the change of the composition was obvious as well. These aging tests for different kinds of bio-oil indicated that aging process during the quantitative 13C NMR process with 5 mg ml−1 relax reagent also existed. But after adding 5 mg ml−1 relax reagent, it will only take 1.5 h for a quantitative 13C NMR test. Short testing time can reduce the error for quantitative 13C NMR results and the results are relatively accurate. Therefore, the quantitative 13C NMR test for bio-oil developed in this study is valuable and necessary.
 |
| Fig. 1 Comparison of changes in contents of different functional groups during 48 hour aging process for bio-oil sample produced from oak wood with 5 mg ml−1 relax reagent. | |
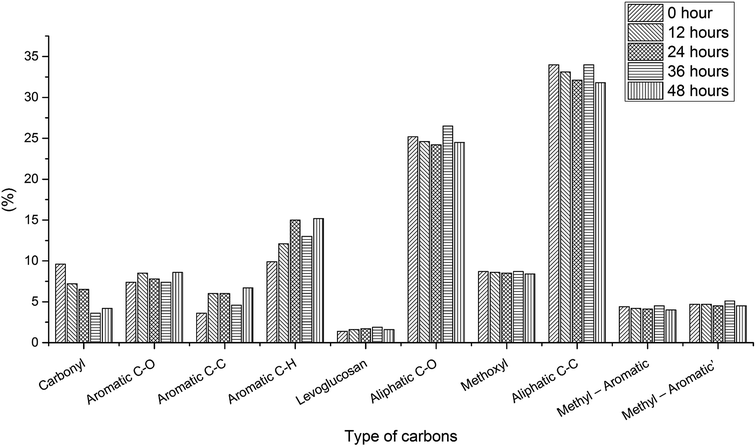 |
| Fig. 2 Comparison of changes in contents of different functional groups during 48 hour aging process for bio-oil sample produced from cottonwood with 5 mg ml−1 relax reagent. | |
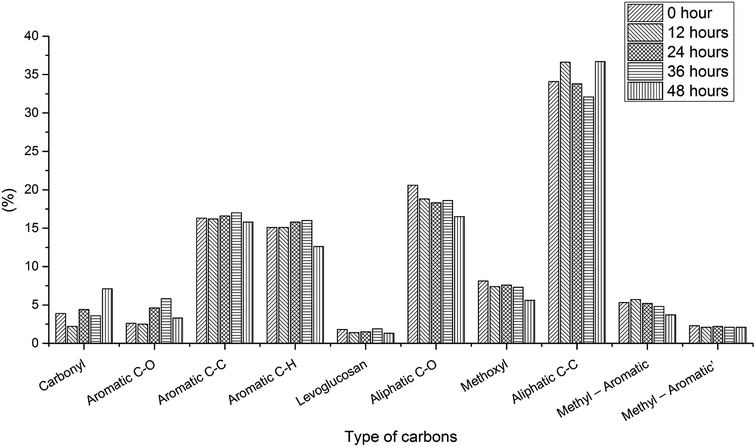 |
| Fig. 3 Comparison of changes in contents of different functional groups during 48 hour aging process for bio-oil sample produced from the mixture of cottonwood and coal with 5 mg ml−1 relax reagent. | |
3.2 C, H, O contents simulation based on 13C NMR
Oxygen-free mixtures. The evaluations for quantitative 13C NMR of standard #1 and standard #2 are listed in Tables 2 and 3. Two oxygen-free mixtures were employed to verify the feasibility of determining the C, H and O contents based on NMR data, which can be calculated as follows: |
mtotal = MCmC + MCHmCH + MCH2mCH2 + MCH3mCH3
| (1) |
|
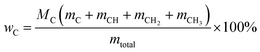 | (2) |
|
 | (3) |
(M: the molar mass; m: the contents of different types of carbons in Tables 2 and 3).
Table 2 Evaluations for quantitative 13C NMR of standard #1
Calculation methods |
Different types of carbons (carbon mol%) |
C |
CH |
CH2 |
CH3 |
Based on the concentrations listed in Table S1 |
0 |
0 |
82.35 |
17.65 |
Based on NMR data |
0 |
0 |
82.79 |
17.21 |
Calculation methods |
C, H, O contents (wt%) |
C |
H |
O |
Based on the concentrations listed in Table S1 |
84.7 |
15.3 |
0.0 |
Based on NMR data |
84.6 |
15.4 |
0.0 |
Table 3 Evaluations for quantitative 13C NMR of standard #2
Calculation methods |
Functional groups (carbon mol%) |
Aliphatic carbons |
Aromatic carbons |
Double bonds |
Based on the concentrations listed in Table S2 |
73.0 |
26.3 |
0.7 |
Based on NMR data |
71.2 |
28.0 |
0.8 |
Calculation methods |
Different types of carbons (carbon mol%) |
C |
CH |
CH2 |
CH3 |
Based on the concentrations listed in Table S2 |
9.7 |
20.0 |
41.3 |
29.0 |
Based on NMR data |
9.2 |
18.7 |
41.8 |
30.3 |
Calculation methods |
C, H, O contents (wt%) |
C |
H |
O |
Based on the concentrations listed in Table S2 |
86.9 |
13.1 |
0.0 |
Based on NMR data |
86.7 |
13.3 |
0.0 |
The standard substance of ASTM-P-0050 consists of saturated alkanes from pentane to eicosane. The comparison of results based on concentrations and NMR data was employed to verify the feasibility of NMR method. It could be seen that the difference of carbon or hydrogen content is only 0.1%, which shows precision of the developed 13C NMR method and correctness of this C, H, O simulation method.
The standard substance of D-5443-93-HTM is composed of saturated alkanes and unsaturated hydrocarbons such as alkenes and aromatics. The final results showed that the error of elemental content measured based on concentrations and NMR data was only 0.2%. These two standard mixtures were also examined by Ben37 using quantitative 13C NMR method, and the precision of the quantitative 13C NMR method has been proved. Therefore, both of these two evaluations for the 13C NMR of complex mixtures approve that the NMR method used in this report could provide quantitative results. The simulated C, H and O contents are also reliable based on the evaluations for oxygen-free mixtures.
Oxygen-deficient compounds. Quantitative 13C NMR results for 8 products obtained from industrial fluid catalytic cracking units have been summarized in Table 4 to verify the feasibility of determining the C, H, O contents based on NMR data for oxygen-deficient compounds. The results indicated that the feed of pyrolysis vapours with kerosene would produce more aliphatic carbons, and the feed of pyrolysis vapours with vacuum gas oil would produce more condensed aromatic carbons. The contents for the C
O bonds were very low, which indicated that the catalysts used in industrial fluid catalytic cracking units were good for the decarboxylation. Based on the 13C NMR results, some simulations have been done for the C, H and O contents for the oxygen-deficient samples, which can be calculated as follows: |
mtotal = MCmC + MCHmCH + MCH2mCH2 + MCH3mCH3 + MCOmCO
| (5) |
|
 | (6) |
|
 | (3) |
|
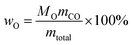 | (7) |
(M: the molar mass; m: the contents of different types of carbons in Table 4).
Table 4 Quantitative 13C NMR results for oxygen-deficient products
Sample |
Different types of carbons (carbon mol%) |
Aliphatic carbons |
Aromatic carbons (overlap with some double bond carbons) |
Terminal double bond carbons |
C O |
C |
CH |
CH2 |
CH3 |
C |
CH |
CH2 |
KO105 |
0.0 |
7.3 |
52.8 |
26.0 |
5.2 |
8.7 |
0.0 |
0.0 |
VO105 |
0.0 |
1.9 |
29.6 |
30.8 |
13.4 |
24.1 |
0.1 |
0.1 |
KO110 |
0.0 |
7.0 |
50.9 |
26.5 |
5.3 |
10.2 |
0.0 |
0.1 |
VO110 |
0.0 |
3.9 |
34.3 |
28.4 |
10.2 |
22.5 |
0.1 |
0.6 |
KO205 |
0.0 |
6.7 |
49.5 |
25.2 |
6.6 |
11.9 |
0.0 |
0.1 |
VO205 |
0.0 |
1.9 |
26.6 |
32.0 |
13.3 |
25.9 |
0.3 |
0.0 |
KO210 |
0.0 |
7.8 |
44.3 |
28.8 |
6.9 |
12.1 |
0.0 |
0.1 |
VO210 |
0.0 |
3.0 |
29.9 |
29.7 |
11.4 |
25.9 |
0.1 |
0.0 |
The simulated results were also compared with the normal C, H, N analysis results, which were exhibited in Table 5. Obviously, the contents of carbon and hydrogen were around 86% and 13%, as well as the amount of oxygen was extremely small, less than 1%. As shown in Fig. S9,† the maximum absolute error and relative error of carbon content were 1.1% and 1.3%, which fully reflected the accuracy of using NMR method to determine carbon content. Similarly, the maximum absolute error of hydrogen was 0.9% while the maximum relative error was 7.4% due to the small percentage of hydrogen. The gap of oxygen content between the results based on NMR data and figures obtained by elemental analysis was also narrow. It is not hard to find that though there is a small amount of oxygen in the sample oil, the determination of C, H and O contents by quantitative 13C NMR analysis is still very accurate. As a result, for all the simulated results based on 13C NMR are comparable with the C, H, N analysis results, which indicated that such simulation is a very reliable method to provide C, H and O contents for oxygen-deficient compounds.
Table 5 Comparison of simulated C, H, O contents based on NMR and based on C, H, N test
Sample |
C (wt%) |
H (wt%) |
O (wt%) |
By NMR |
By CHN |
By NMR |
By CHN |
By NMR |
By CHN |
KO105 |
85.7 |
85.4 |
14.3 |
14.5 |
0.0 |
0.1 |
VO105 |
87.0 |
86.6 |
12.9 |
13.2 |
0.1 |
0.2 |
KO110 |
85.7 |
86.5 |
14.2 |
13.4 |
0.1 |
0.1 |
VO110 |
86.3 |
87.4 |
13.0 |
12.1 |
0.7 |
0.5 |
KO205 |
86.0 |
86.6 |
13.9 |
13.3 |
0.1 |
0.1 |
VO205 |
87.1 |
87.7 |
12.9 |
12.2 |
0.0 |
0.1 |
KO210 |
85.9 |
86.4 |
14.0 |
13.5 |
0.1 |
0.1 |
VO210 |
87.1 |
87.4 |
12.9 |
12.5 |
0.0 |
0.1 |
Oxygen-rich pyrolysis oils. Six pyrolysis oil samples have been tested to verify the feasibility of determining the C, H and O contents of oxygen-rich pyrolysis oils based on NMR data in this report. The quantitative 13C NMR results for these six samples have been examined and shown in Table 6. It could be seen that the compositions of biomass and coal pyrolysis oils under different atmospheres were significantly different. For the pyrolysis oil of bituminous coal, CO2 increased the number of aromatic compounds and decreased aliphatic compounds in the liquid product. In contrast to the pyrolysis of NSC, the amount of aromatic substances in the tar of PS pyrolysis became smaller while aliphatic structure contents increased. The sample OW1 had more levoglucosan, aliphatic C–O bonds and methyl-aromatic bonds than the sample OW2. However, there were more aromatic bonds in the sample OW2, which indicated that sample OW2 contained more “lignin” part of pyrolysis components than the sample OW1, while sample OW1 contained more “carbohydrates” part of pyrolysis components.
Table 6 Quantitative 13C NMR for the samples of pyrolysis oil, the results shown as carbon mol%a
Functional groups |
NSC(N2) |
NSC(CO2) |
PS(N2) |
PS(CO2) |
OW1 |
OW2 |
The first four columns of data are from the article.41 |
 |
3.5 |
8.7 |
2.4 |
6.3 |
9.2 |
6.9 |
 |
0.9 |
1.3 |
1.7 |
5.0 |
16.2 |
20.7 |
 |
6.0 |
14.2 |
27.9 |
17.9 |
10.7 |
11.8 |
 |
17.6 |
12.4 |
17.3 |
9.8 |
24.1 |
28.2 |
 |
 |
4.0 |
3.2 |
0.2 |
0.2 |
7.0 |
6.7 |
General (including levoglucosan) |
28.5 |
28.8 |
3.3 |
4.0 |
8.7 |
7.5 |
 |
11.6 |
12.5 |
14.7 |
16.5 |
2.0 |
2.8 |
 |
General (including two methyl-Ar) |
32.0 |
22.1 |
32.7 |
40.6 |
29.2 |
22.0 |
 |
3.1 |
3.0 |
4.3 |
2.3 |
7.9 |
6.6 |
 |
0.9 |
1.1 |
1.2 |
1.0 |
4.4 |
3.9 |
To further investigate the pyrolysis oils by the 13C NMR, two additional tests have been done for each liquid sample – DEPT 90 and DEPT 135 (as shown in Fig. S10†), which could be able to tell the differences from different carbons (primary, secondary, tertiary and quaternary carbons). The results have been shown in Table 7, seven more different types of functional groups could be detected by this method. The results showed that there were much more ketones than the aldehydes in the bio-oils. Some possible overlaps between aromatic C–H and C–C bonds have also been observed. There were less primary alcohol/ethers than the secondary alcohol/ethers. For all the samples, there were much less secondary and tertiary aliphatic carbons than primary carbons.
Table 7 Detailed analysis for the pyrolysis oil samples, the results shown as carbon mol%a
Functional groups |
NSC(N2) |
NSC(CO2) |
PS(N2) |
PS(CO2) |
OW1 |
OW2 |
The first four columns of data are from the ref. 41. |
 |
R or R′ C |
3.1 |
7.7 |
2.3 |
5.2 |
9.0 |
6.9 |
R or R′ H |
0.4 |
1.0 |
0.1 |
1.1 |
0.2 |
0.2 |
 |
Ar–O–R |
0.9 |
1.2 |
1.7 |
4.1 |
16.2 |
20.7 |
Possible overlap with aromatic C–H |
0.1 |
0.1 |
0.0 |
0.9 |
0.0 |
0.0 |
 |
Ar–C–R |
5.3 |
12.2 |
20.2 |
13.2 |
6.9 |
7.5 |
Possible overlap with aromatic C–H |
0.6 |
2.1 |
7.8 |
4.8 |
3.8 |
4.3 |
 |
17.6 |
12.4 |
17.3 |
9.8 |
24.1 |
28.2 |
 |
H = 1 |
20.7 |
23.9 |
2.3 |
3.4 |
5.1 |
5.4 |
H = 2 |
7.8 |
4.8 |
1.0 |
0.7 |
3.6 |
2.1 |
 |
11.6 |
12.5 |
14.7 |
16.5 |
2.0 |
2.8 |
 |
H = 1 |
1.1 |
0.9 |
5.7 |
6.7 |
0.0 |
0.0 |
H = 2 |
2.8 |
1.9 |
7.8 |
10.5 |
9.8 |
6.3 |
H = 3 |
28.1 |
19.4 |
19.2 |
23.3 |
19.4 |
15.7 |
To explore the application of 13C NMR analysis, some simulations of C, H and O contents have been done for each sample. Table 8 listed all the proposed tentative C, H and O contents for each functional groups based on the results in Table 7. Although, there may have some overlaps for the C–O bonds, the proposed C, H and O contents could represent the elemental ratios for each functional group very well. Based on the proposed elemental ratios for each functional group and the content for these functional groups listed in Table 7, the simulated C, H and O contents for each sample have been shown in Table 9, which can be calculated as follows:
|
 | (9) |
|
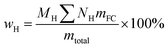 | (10) |
|
 | (11) |
(FG: functional groups;
MFG: the molar mass calculated by the results in
Table 8;
mFG: the carbon contents of functional groups in
Table 7;
MC,
MH,
MO: the molar mass of C, H, O;
NC,
NH,
NO: the number of C, H, O in
Table 8).
Table 8 Proposed tentative C, H and O contents for each functional group in the pyrolysis oils
Functional groups |
C |
H |
O |
 |
R or R′ C |
1 |
0 |
1 |
R or R′ H |
1 |
1 |
1 |
 |
Ar–O–R |
1 |
0 |
0 |
Possible overlap with aromatic C–H |
1 |
1 |
0 |
 |
Ar–C–R |
1 |
0 |
0 |
Possible overlap with aromatic C–H |
1 |
1 |
0 |
 |
1 |
1 |
0 |
 |
H = 1 |
1 |
1 |
1 |
H = 2 |
1 |
2 |
1 |
 |
1 |
3 |
1 |
 |
H = 1 |
1 |
1 |
0 |
H = 2 |
1 |
2 |
0 |
H = 3 |
1 |
3 |
0 |
Table 9 Comparison of simulated C, H, O contents based on NMR and based on C, H, N testa
Sample |
C (wt%) |
H (wt%) |
O (wt%) |
By NMR |
By CHN |
By NMR |
By CHN |
By NMR |
By CHN |
The first four columns of data are from the ref. 41. |
NSC(N2) |
57.8 |
55.8 |
8.7 |
8.5 |
33.5 |
35.4 |
NSC(CO2) |
55.9 |
58.4 |
7.0 |
7.2 |
37.2 |
34.0 |
PS(N2) |
71.5 |
71.1 |
9.1 |
9.3 |
19.4 |
18.0 |
PS(CO2) |
66.8 |
67.0 |
9.4 |
9.0 |
23.9 |
22.6 |
OW1 |
73.1 |
69.8 |
7.6 |
7.3 |
19.4 |
21.1 |
OW2 |
75.5 |
71.9 |
6.9 |
7.4 |
17.5 |
19.2 |
The results of calculation based on NMR data were also compared with the normal C, H, O analysis results, which were exhibited in Table 9. Different from the first two kinds of experimental samples, this type of pyrolysis oils contained a large amount of oxygen and even a small amount of nitrogen, which would affect the determination of C, H and O contents by NMR simulation. As shown in Fig. S11,† the maximum absolute error and relative error of carbon were 3.6% and 5%, which indicated that NMR simulation was quite accurate for the determination of carbon elements in oxygen-rich pyrolysis oils. It was equally precise for hydrogen content whose maximum absolute error and relative error were 0.5% and 6.8%. Due to the low oxygen content of the samples in the two experiments above, it was not clear whether the determination of oxygen in elemental analysis by NMR method was up to standard. However, the research about oxygen-rich pyrolysis oils solved the puzzle. The maximum absolute error and relative error of carbon were 3.6% and 9.4%, which proved that the calculation based on NMR data could meet the requirement of determining oxygen content. On the whole, the preliminary comparison indicated that this developed simulation of C, H and O contents based on the 13C NMR analysis for oxygen-rich pyrolysis oils is very reliable.
Accuracy and limitations. From the above, it can be confirmed that a developed simulation of C, H, O contents based on the 13C NMR analysis for pyrolysis oils is reliable. It can predict the C content with an absolute accuracy of 4%, the H content with an absolute accuracy of 1.5% and the O content with an absolute accuracy of 2%. Since this method still has some errors, this method is suitable for magnitude analysis but cannot be used to determine differences between oils from similar conditions. For example, for NSC(N2) and NSC(CO2) oils, the traditional C, H and O analysis suggests that the N2 sample has a higher O content, but the NMR method predicts the opposite. A similar difference in the relative magnitudes for the O contents of OW1 and OW2 samples is evident.Because the method still has some limitations, the error analysis seems to be an indispensable choice. Firstly, the instrument performance and the mode of operation have an impact on the experimental results. Therefore, accurate instrumentation and professional operation can effectively reduce the error impact on the experimental data and improve the correctness of the data. Secondly, the pyrolysis oil can not contain water as an inorganic substance because the 13C NMR spectrum is unable to detect the functional group therein. The more water content, the less accurate the simulation results. If there will be some water in the pyrolysis oil samples, the C, H and O contents based on the C, H, N tests need to be further adjusted by the water contents. Finally, “impurity” elements (such as nitrogen and sulfur) other than carbon, hydrogen and oxygen can also affect the experimental results. If the proportion of these elements in the pyrolysis oils is too large, the error of C, H and O contents measured based on NMR data will be equally large. Therefore, it is more accurate to simulate the C, H and O contents of pyrolysis oils by selecting pyrolysis oils with few “impurity” elements.
4. Conclusion
We demonstrated accuracy and precision of using quantitative 13C NMR to characterize bio-oil. The developed method was found to be accurate and can provide very valuable information for different functional groups in the bio-oil. The influences for concentrations of relax reagent on the T1 of bio-oil have been examined and discussed. The use of 5 mg ml−1 Cr(acac)3 can decrease the T1 by 95%. It can be found that, by using this developed quantitative 13C NMR method, the testing time of 13C NMR can be greatly reduced and the aging process of bio-oil during 13C NMR experiment is negligible due to the short NMR process, suggesting that this method can significantly improve the efficiency of the experiment while ensuring the accuracy. 13C NMR and DEPT 90 and 135 could further investigate the bio-oil, 15 + 7 different functional groups could be analysed by this method. A simulation of C, H and O contents for the bio-oil based on the 13C NMR has been proposed, and it can directly calculate the O content of bio-oil, which few studies focus on. Compared with traditional C, H, O contents calculation method, the absolute error in calculating C content using this method is 4%, the absolute error in calculating H content is 1.5%, and the absolute error in calculating O content is 2%, indicating that this new developed method is reliable to calculate C, H, O contents of bio-oil. Considering that there are more than three elements in bio-oil, more researches on elemental analysis, for example, simulation of N and S contents for pyrolysis oil, need to be carried out in the future study.
Conflicts of interest
There are no conflicts to declare.
Acknowledgements
The authors would like to acknowledge the financial support from National Science Foundation of China [51706044] and the Natural Science Foundation of the Jiangsu of China [BK20170666]. And a portion of work was supported by the U.S. Department of Energy under contract no. DE-AC36-08GO28308 with the National Renewable Energy Laboratory. Funding was provided by U.S. DOE Office of Energy Efficiency and Renewable Energy Bioenergy Technologies Office.
Notes and references
- N. H. Leibbrandt, J. H. Knoetze and J. F. Görgens, Biomass Bioenergy, 2011, 35, 2117–2126 CrossRef CAS.
- D. Chen, K. Cen, X. Jing, J. Gao, C. Li and Z. Ma, Bioresour. Technol., 2017, 233, 150–158 CrossRef CAS PubMed.
- A. Jain, R. Balasubramanian and M. P. Srinivasan, Chem. Eng. J., 2016, 283, 789–805 CrossRef CAS.
- R. P. Anex, A. Aden, F. K. Kazi, J. Fortman, R. M. Swanson, M. M. Wright, J. A. Satrio, R. C. Brown, D. E. Daugaard, A. Platon, G. Kothandaraman, D. D. Hsu and A. Dutta, Fuel, 2010, 89, S29–S35 CrossRef CAS.
- A. V. Bridgwater, Biomass Bioenergy, 2012, 38, 68–94 CrossRef CAS.
- H. Ben and J. R. Ferrell III, RSC Adv., 2016, 6, 17567–17573 RSC.
- A. V. Bridgwater, D. Meier and D. Radlein, Org. Geochem., 1999, 30, 1479–1493 CrossRef CAS.
- S. Yaman, Energy Convers. Manage., 2004, 45, 651–671 CrossRef CAS.
- E. Su, P. You and D. Wei, Bioresour. Technol., 2009, 100, 5813–5817 CrossRef CAS PubMed.
- X. Zhang, H. Lei, S. Chen and J. Wu, Green Chem., 2016, 18, 4145–4169 RSC.
- A. Aho, A. Tokarev, P. Backman, N. Kumar, K. Eränen, M. Hupa, B. Holmbom, T. Salmi and D. Y. Murzin, Top. Catal., 2011, 54, 941–948 CrossRef CAS.
- D. A. Ruddy, J. A. Schaidle, J. R. I. Ferrell, J. Wang, L. Moens and J. E. Hensley, Green Chem., 2014, 16, 454–490 RSC.
- G. D. Strahan, C. A. Mullen and A. A. Boateng, Energy Fuels, 2011, 25, 5452–5461 CrossRef CAS.
- N. Hao, H. Ben, C. G. Yoo, S. Adhikari and A. J. Ragauskas, Energy Fuels, 2016, 30, 6863–6880 CrossRef CAS.
- Q. Wang, D. Cui, P. Wang, J. Bai, Z. Wang and B. Liu, Fuel, 2018, 211, 341–352 CrossRef CAS.
- W. Qing, J. Chunxia, G. Jianxin and G. Wenxue, Energy Fuels, 2015, 30, 2478–2491 CrossRef.
- P. C. Tarves, C. A. Mullen and A. A. Boateng, ACS Sustainable Chem. Eng., 2015, 4, 930–936 CrossRef.
- H. Ben and A. J. Ragauskas, Energy Fuels, 2011, 25, 5791–5801 CrossRef CAS.
- F. Huang, S. Pan, Y. Pu, H. Ben and A. J. Ragauskas, RSC Adv., 2014, 4, 17743 RSC.
- D. P. Gallegos, K. Munn, D. M. Smith and D. L. Stermer, J. Colloid Interface Sci., 1987, 119, 127–140 CrossRef CAS.
- I. Ohtani, T. Kusumi, Y. Kashman and H. Kakisawa, J. Am. Chem. Soc., 1991, 113, 4092–4096 CrossRef CAS.
- D. J. Crockford, E. Holmes, J. C. Lindon, R. S. Plumb, S. Zirah, S. J. Bruce, P. Rainville, C. L. Stumpf and J. K. Nicholson, Anal. Chem., 2006, 78, 363–371 CrossRef CAS PubMed.
- E. D. Christensen, G. M. Chupka, J. Luecke, T. Smurthwaite, T. L. Alleman, K. Iisa, J. A. Franz, D. C. Elliott and R. L. McCormick, Energy Fuels, 2011, 25, 5462–5471 CrossRef CAS.
- H. Ben and A. J. Ragauskas, ChemSusChem, 2012, 5, 1687–1693 CrossRef CAS PubMed.
- H. Ben and A. J. Ragauskas, Energy Fuels, 2011, 25, 5791–5801 CrossRef CAS.
- S. Hosseinnezhad, E. H. Fini, B. K. Sharma, M. Basti and B. Kunwar, RSC Adv., 2015, 5, 75519–75527 RSC.
- X. Jiang, Z. Zhong, N. Ellis and Q. Wang, Chem. Eng. Technol., 2011, 34, 727–736 CrossRef CAS.
- A. S. Alwehaibi, D. J. Macquarrie and M. S. Stark, Green Chem., 2016, 18, 2762–2774 RSC.
- Y. Wang, S. Wang, F. Leng, J. Chen, L. Zhu and Z. Luo, Sep. Purif. Technol., 2015, 152, 123–132 CrossRef CAS.
- H. Ben, F. Huang, L. Li and A. J. Ragauskas, RSC Adv., 2015, 5, 74821–74827 RSC.
- S. No, Renewable Sustainable Energy Rev., 2014, 40, 1108–1125 CrossRef CAS.
- J. Joseph, M. J. Rasmussen, J. P. Fecteau, S. Kim, H. Lee, K. A. Tracy, B. L. Jensen, B. G. Frederick and E. A. Stemmler, Energy Fuels, 2016, 30, 4825–4840 CrossRef CAS.
- H. Jo, D. Verma and J. Kim, Fuel, 2018, 232, 610–619 CrossRef CAS.
- R. Stanger, T. Wall, J. Lucas and M. Mahoney, Fuel, 2013, 108, 656–667 CrossRef CAS.
- Y. Luo, H. Ben, Z. Wu, K. Nie, G. Han and W. Jiang, Polymers, 2019, 11, 1370 CrossRef CAS PubMed.
- H. Ben, F. Wu, Z. Wu, G. Han, W. Jiang and A. J. Ragauskas, Polymers, 2019, 11, 1387 CrossRef CAS PubMed.
- H. Ben, Z. Wu, G. Han, W. Jiang and A. Ragauskas, Polymers, 2019, 11, 324 CrossRef PubMed.
- S. K. R. Patil, J. Heltzel and C. R. F. Lund, Energy Fuels, 2012, 26, 5281–5293 CrossRef CAS.
- E. Alsbou and B. Helleur, Energy Fuels, 2014, 28, 3224–3235 CrossRef CAS.
- H. Ben and A. J. Ragauskas, ChemSusChem, 2012, 5, 1687–1693 CrossRef CAS.
- Y. Luo, H. Ben, Z. Wu, K. Nie, G. Han and W. Jiang, Polymers, 2019, 11, 1370 CrossRef CAS PubMed.
Footnote |
† Electronic supplementary information (ESI) available. See DOI: 10.1039/d0ra02376k |
|
This journal is © The Royal Society of Chemistry 2020 |
Click here to see how this site uses Cookies. View our privacy policy here.