DOI:
10.1039/D0RA01093F
(Paper)
RSC Adv., 2020,
10, 10606-10611
Highly-selective solvent-free catalytic isomerization of α-pinene to camphene over reusable titanate nanotubes
Received
5th February 2020
, Accepted 9th March 2020
First published on 12th March 2020
Abstract
Titanate nanotubes, prepared by the hydrothermal reconstitution and modification with hydrochloric acid, were tested as solid acid catalysts in the isomerization of α-pinene under solvent free conditions. The results showed that titanate nanotubes have better catalytic properties than titanium dioxide nanoparticles, and the camphene was the main product for α-pinene isomerization. The effects of several reaction variables, such as reaction temperature, catalyst dosage, and reaction time, on the conversion of α-pinene and the selectivity to camphene were examined. The highest conversion was up to 97.8% with selectivity to camphene of 78.5% under the mild reaction conditions, and the catalyst also showed outstanding reusability after four runs. It is proposed that appropriate surface acidic sites and opened nanotubular structures are mainly responsible for the excellent catalytic performance of titanate nanotubes materials.
Introduction
The production of high value-added chemicals from biomass has attracted a lot of attention.1 α-Pinene extracted from resin tapping, wood pulp papermaking and cellulose production is an inexpensive and important essential oil, which is widely used in the synthesis of various fine chemicals. Many research works indicated that α-pinene can be rearranged to give several isomeric products in the presence of an acid catalyst. Among several isomers, camphene is especially important substrate in the production of fragrance materials, acrylates, terpene-phenol resins and other chemical derivatives.2 Camphene is also a key intermediate from α-pinene for the production of isobornyl esters and camphor which are extensively used as mildew proofing and insecticidal agents in our daily life.
Camphene is generally obtained by the isomerization of α-pinene using acidic catalysts. In recent years, the use of heterogeneous catalyst is a shift toward green and environmental-friendly technologies. Various solid acid catalysts, such as zeolites,3,4 iron-modified zeolites,5 sulfated zirconia,6 modified layered aluminosilicates,7 Al-incorporated MCM-41,8 MSU-S mesoporous materials,9 W2O3/Al2O3,10 phosphotungstic heteropoly acids,11 Ti-SBA-15 (ref. 12 and 13), and ionic liquids12 have been employed for the isomerization of α-pinene. However, there is still a challenge to develop new catalysts which posse higher activity and selectivity to camphene during the α-pinene isomerization process.
In recent years, titanium dioxide nanoparticles (TNPs) were worked as efficient catalyst for the acceleration of various organic reactions including Knoevenagel condensations,13 Friedel–Crafts alkylation of indoles,14 the aldol condensation of furfural,15 Mannich synthesis of β-aminocarbonyls,16 and synthesis of tetrahydrobenzo[b]pyran derivatives,17 α-aminophosphonates18 and polyhydroquinoline derivatives.19 However, the weak acidity sites on the surface of TNPs are become a major drawback that limits the catalytic applications of TNPs in organic reactions. It has been reported that the reaction rate on titanium dioxide nanoparticles is low for the α-pinene isomerization to camphene.20 Surface modification of TiO2 materials with acidic groups is an efficient method to increase the catalytic activity.23,24 Besides, textural properties are usually a factor influencing the activity of acid catalysts. Among titanium dioxide materials, one dimensional titanate nanotubes (TNTs) have novel properties such as large surface area and tubular structure that increase the number of active sites.21 TNTs can be synthesized in large quantities via the hydrothermal treatment using commercial TiO2 powder. The main hollow tunnel structures are formed after the acid washing step that removing the Na+ ion to form Ti–OH bonds. This means that the surface acidity can be modified to tune the catalytic activity of TNTs during the acid washing process.
In the present work, titanate nanotubes were modified by different acids as solid catalysts to improve the isomerization of α-pinene to camphene (Scheme 1). Repetition reuses were conducted in order to suit the catalyst's potential application.
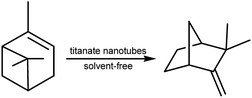 |
| Scheme 1 The isomerization of α-pinene over titanate nanotubes. | |
Experimental
Materials
TiO2 nanoparticles (anatase, >99.9%) and α-pinene were purchased from Aladdin and were used as received. Other chemical reagents, such as NaOH, HCl, H2SO4, HNO3, hexane, and ethanol were of analytical grade and used without further purification.
Preparation of catalyst
TNTs were synthesized by the hydrothermal method in NaOH solution using commercial TNPs as Ti source referring to the previous work with some modifications.22 3 g TNPs were uniformly dispersed in 120 mL of 10 mol L−1 NaOH aqueous solution, followed by hydrothermal treatment at 150 °C in a Teflon-lined autoclave for 24 h. The white powders were washed thoroughly with distilled water and 0.1 mol L−1 [H+] HCl aqueous solution. Then, the suspension was centrifugated and the solid sample was washed with distilled water until the pH of the rinsing solution close to 7, and subsequently dried overnight under vacuum at 60 °C, the product denoted as TNTs-Cl. Similarly, TNTs-SO4 and TNTs-NO3 were prepared with 0.1 mol L−1 H2SO4 and HNO3 aqueous solution during the acid washing process, respectively.
Characterization
Prior to measurement, all samples were dried under vacuum. Fourier transform infrared spectrum (FT-IR) was obtained by the KBr pellet technique on a Nicolet 370 infrared spectrophotometer in the range 400–4000 cm−1. The crystalline structure of TNTs was determined by X-ray diffraction (XRD) spectroscopy using Bruker diffractometer with Cu Kα wavelength (λ = 1.5418 Å) and diffraction angle (2θ) ranging from 10–90°. The microscopic morphology of TNTs was investigated by using transmission scanning microscopy (TEM, JEOL 2100, Japan) and scanning electron microscope (SEM, Carl Zeiss Sigma-HD, Germany). The N2 adsorption–desorption isotherms was recorded with an ASAP 2400 physisorption instrument made by Micromeritics Corporation (United States). Surface acidity of sample was determined from the adsorbed pyridine in hexane solution by ultraviolet spectrum (Shimadzu UV-1900, Japan).23
Catalytic testing
The isomerization reaction was carried out in a 5 mL round bottom flask equipped with a condenser. In a typical run, 0.050 g catalyst and 1.0 mL of α-pinene were added to the round bottomed flask and stirred for 5 min, and heated in a thermostatic oil bath at atmospheric pressure. Once the reaction finish, the products were taken, centrifugated and analyzed quantitatively by gas chromatography. The products of the isomerization were identified by GC-MS analyses.
Results and discussion
Catalytic performance of modified TNTs in isomerization
The catalytic performance of TNPs and different TNTs was evaluated in the isomerization of α-pinene under solvent free conditions, and the results have been summarized in Table 1. It was found that α-pinene conversion was almost zero for 6 h at 100 °C in the blank experiment (Table 1, Entry 1), and the similar result was obtained for reaction using the commercial TNPs (Table 1, Entry 2). However, when modified TNTs materials were used as catalyst, an increase on the conversion of α-pinene was observed (Table 1, Entry 3–5). It was found that the highest conversion of α-pinene was 42.8% with 64.8% highest camphene selectivity when catalyzed by TNTs-Cl for only 120 min (Table 1, Entry 5). From the adsorption of pyridine, the surface acidity of modified TNTs was quantified in Table 1. The amount of acidity on the sample surface is related to the kind of acid agent. This means that the acid catalytic sites can be modified by mineral acid in the washing step. The improvement on the catalytic performance of TNTs can be explained as TNTs has Lewis acids sites and Brønsted acid sites,24 and the strength distribution of acid sites are also adjusted by modifying the surface with different mineral acid. Lewis acid sites were mainly promoted when HCl was used in the washing step.24 Interestingly, we found that the major product after the reaction was camphene, thus suggesting the appropriate surface acidic sites of TNTs-Cl play a determinant role in the selective isomerization reaction for enlarging the four number ring of α-pinene to dicyclic camphene. The amount of acid sites of TNTs-NO3 and TNTs-SO4 are 0.46 and 0.58 mmol g−1, respectively. It is deduced that the stronger Brønsted acidic sites exist on the surface of TNTs-SO4 and TNTs-NO3, so more monocyclic isomers, such as limonene and terpinolene are formed from cracking the four number ring of α-pinene. The higher conversion of α-pinene was obtained after 6 h and is 77.7% with 76.2% of selectivity for camphene over TNTs-Cl (Table 1, Entry 6).
Table 1 Catalytic performance of modified TNTs in α-pinene isomerizationa
Entry |
Catalyst |
Acidity (mmol g−1) |
Time (min) |
Conversion (%) |
Selectivity (%) |
Reaction conditions: 1 mL α-pinene, 0.05 g catalyst, reaction temperature 100 °C. |
1 |
— |
|
360 |
— |
— |
2 |
TNPs |
— |
240 |
1.3 |
70.6 |
3 |
TNTs-NO3 |
0.46 |
120 |
15.2 |
52.3 |
4 |
TNTs-SO4 |
0.58 |
120 |
18.7 |
46.8 |
5 |
TNTs-Cl |
0.83 |
120 |
42.8 |
64.8 |
6 |
TNTs-Cl |
|
360 |
77.7 |
76.2 |
Catalyst characterization
Modified TNTs materials were identified by FT-IR analysis, and the corresponding FT-IR spectra are depicted in Fig. 1. The FT-IR spectra of the three samples were similar. For TNTs samples, the broad peak present at around 3214–3600 cm−1 can be assigned the surface –OH stretching vibrations. The peak at 1638 cm−1 arises from the O–H deformation vibration of H–O–H as well as Ti–OH bonds. The band at 1384 cm−1 can be attributed to the Ti–O–H deformation vibration.25 In addition, the peak around 477–486 cm−1 in the spectrum could be same to interpret as the crystal lattice vibration of TiO6 octahedra.26
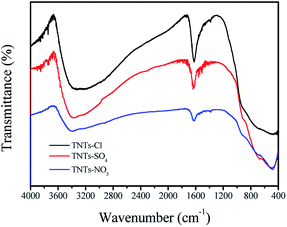 |
| Fig. 1 FT-IR spectra of modified TNTs. | |
The XRD patterns of the TNTs-Cl, TNTs-SO4 and TNT-NO3 samples were recorded, and the results are presented in Fig. 2. The peaks at 2θ = 10.8°, 24.5°, 28.6° and 48.5° which are still consistent with the characteristic diffraction signals of titanate nanotubes,30 the main structure is not changed by the acid agent. Furthermore, the XRD patterns of the TNTs-Cl and TNTs-SO4 showed a little change in the peaks.
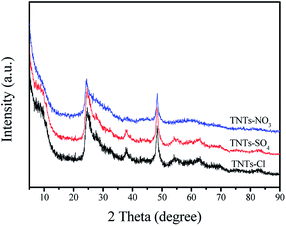 |
| Fig. 2 XRD patterns of modified TNTs. | |
TEM image of TNTs-Cl is shown in Fig. 3. It can be observed from Fig. 3a that the as-prepared titanium dioxide nanotubes are interlaced with each other, and nanotubes can be several micrometers in length. TNTs-Cl showed the nanotubes with openings at the ends. Titanium dioxide nanotubes have a hollow tubular structure with an internal diameter of about 9 nm, which is consistent with the reported literature. The morphology and structure of TNTs-Cl were further surveyed by SEM. It can be seen from the Fig. 3b that it is consistent with the above TEM observations.
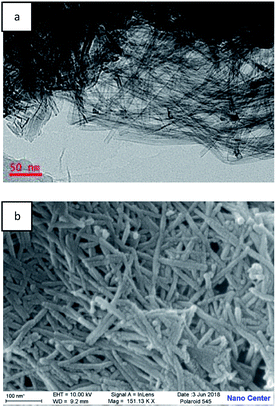 |
| Fig. 3 TEM image (a) and SEM photographs (b) of TNTs-Cl. | |
The textural property of TNTs-Cl was further investigated using N2 adsorption–desorption isotherms, and the results are present in Fig. 4. TNTs-Cl has the type IV isotherms based on IUPAC classification, which is characteristic of the mesoporous materials. TNPs are non porous materials. The surface area value of TNTs-Cl was calculated by BET method to be 295 m2 g−1. Besides, the pore volume of TNTs-Cl was 0.646 cm3 g−1. At the same time, the results of pore size distribution of TNTs-Cl by BJH method, which can support the observation of TEM image. It can be clearly seen that the hydrothermal reconstitution method and post-modification method can be used to transform nanoparticles into nanotubes, which increases the surface area of the material. The opened hollow structure can facilitate the contact of the substrate molecules with the active sites during the catalytic reaction process.
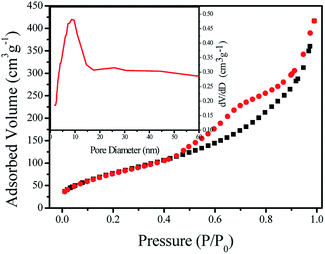 |
| Fig. 4 Nitrogen adsorption–desorption isotherms for TNTs-Cl. | |
Effect of isomerization condition
To check the variables such as reaction temperature, catalyst dosage, and reaction time effect on the results of the reaction, a series of single-factor experiment were performed using the best TNTs-Cl catalyst. Firstly, the conversion of α-pinene and the selectivity of camphene were investigated as a function of temperature at a catalyst amount of 0.05 g between 90 and 130 °C, and the results are presented in Fig. 5.
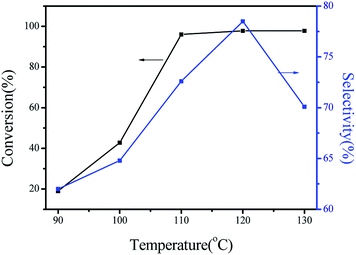 |
| Fig. 5 Effect of the temperature in the catalytic performance of TNTs-Cl. Reaction conditions: 1 mL α-pinene, 0.05 g TNTs-Cl, reaction time 120 min. | |
It can be seen that an increase of the reaction temperature caused a significant increase in the conversion of α-pinene. For the lower temperatures of 90 °C, the values of α-pinene conversion were quite low and were 19.0%. The higher conversion of α-pinene was obtained when the reaction temperature reached 100 °C. It was observed that a greater increase in the values of α-pinene conversion, which rose from 40.2% (100 °C) to 98.7% (110 °C). The highest selectivity of camphene was amounted to ca. 78.5% at 120 °C. The reaction temperature was further increased, while the selectivity of camphene was lowered. The result can be most probably explained by camphene transformed into monocyclic isomer products at relatively high temperature.
The effects of the catalyst dosage on the isomerization were further investigated, and the results are summarized in Fig. 6. It can be obviously seen that an increase in the catalyst amount resulted in the better catalytic performance in term of α-pinene conversion. However, camphene selectivity remarkably decreased with the catalyst amount increase. This may be caused by the large amount of acidic active centers available, thus leading to higher production of monocyclic products. This phenomenon is good agreement with results previously published.27
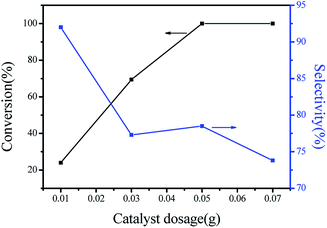 |
| Fig. 6 Effect of the catalyst dosage on the α-pinene conversion and camphene selectivity. Reaction conditions: 1 mL α-pinene, reaction time 120 min, reaction temperature 120 °C. | |
The effects of reaction time on the isomerization were investigated, and results are presented in Fig. 7. The conversion of α-pinene increased with reaction time. However, the reaction rate was very slow after 60 min as if pseudo-equilibrium was reached. The conversion of α-pinene remained 97.8% and the prolongation of the reaction time did not seem to increase obviously the system's activity. It is worth noting that camphene selectivity increases with the reaction time. After 90 min of reaction, camphene selectivity remained approximately unchanged, keeping at 78.5%.
 |
| Fig. 7 Effect of reaction time on the α-pinene conversion and camphene selectivity. Reaction conditions: 1 mL α-pinene, 0.05 g TNTs-Cl, reaction temperature 120 °C. | |
Catalyst stability
The stability of TNTs-Cl was also evaluated during the isomerization process. After each run, TNTs-Cl was easily removed from the reaction mixture by centrifugation. The catalyst was washed and centrifugated repeatedly with hexane and ethanol to remove the residues. Then, the catalyst was reused in the next run. Fig. 8 shows that the catalyst exhibits fairly outstanding stability. The conversion of α-pinene was maintained 94% with 71.4% camphene selectivity after four runs. While supplemental addition of 10% TNTs-Cl dosage for the mass lost in recovering, the conversion and selectivity in fifth are comparable to the first run. This indicates that the catalytic activity of TNTs-Cl catalyst was not much affected on recycling. The catalytic activities of various catalysts that have been studied in the previous literatures are summarized in Table 2. The catalysts with stronger acid sites, such as zeolites beta, H3PW12O40/SiO2, and sulfated ZrO2–SiO2 have been reported for the isomerization of α-pinene with low selectivity to camphene. The higher selectivity to camphene was achieved for 40Ga-41, sulfated zirconia, Fe3+-loaded clinoptilolite and Ti-SBA-15. It is worth noting that the catalytic performance of TNTs-Cl in the present work was better than that of other systems. These results indicate that TNTs-Cl worked as an acid catalyst exhibiting excellent catalytic performance in selective isomerization of α-pinene to camphene.
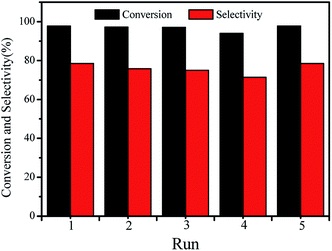 |
| Fig. 8 Recycling of TNTs-Cl for the isomerization of α-pinene. Reaction conditions: 1 mL α-pinene, reaction time 120 min, 0.05 g TNTs-Cl, reaction temperature 120 °C. | |
Table 2 Comparison of TNTs-Cl with reported catalyst
Catalyst |
Temp. (°C) |
Time (h) |
Cat./α-pinene (wt%) |
Conv. (%) |
Camphene sele. (%) |
Ref. |
Zeolites beta |
70 |
0.5 |
6 |
91.4 |
43.9 |
3 |
40Ga-41 |
80 |
1 |
3.5 |
61.0 |
65.0 |
27 |
H3PW12O40/SiO2 |
100 |
1 |
0.6 |
90.0 |
50.0 |
11 |
Sulfated zirconia |
120 |
2 |
1.5 |
88.2 |
67.4 |
28 |
W2O3/Al2O3 |
150 |
2 |
1 |
73.0 |
55.0 |
10 |
Sulfated ZrO2–SiO2 |
150 |
2 |
5 |
98.0 |
34.0 |
29 |
Illite clay |
140 |
1.6 |
1 |
85.0 |
54.3 |
7 |
Fe3+-loaded clinoptilolite |
155 |
8 |
17 |
93.7 |
65.6 |
2 |
[HO3S–(CH2)3–Net3]Cl–ZnCl2 |
140 |
4 |
— |
97.6 |
64.8 |
12 |
Ti-SBA-15 |
140 |
5 |
15 |
60.0 |
65.0 |
30 |
TNTs-Cl |
120 |
2 |
5.8 |
97.8 |
78.5 |
This work |
Conclusions
In conclusion, titanate nanotubes prepared by hydrothermal reconstitution and post-modification with HCl aqueous solution were studied in α-pinene isomerization showing high selectivity to camphene (78.5% at 97.8% α-pinene conversion). This catalyst exhibited outstanding catalytic performance and have an excellent stability over four runs. The study demonstrated that titanate nanotubes worked as an efficient solid acid catalyst for the green conversion of α-pinene into value-added chemicals. Further works on the relationships between the strength of acid sites and the catalytic performances of titanate nanotubes are underway.
Conflicts of interest
There are no conflicts to declare.
Acknowledgements
This work was supported by the National Natural Science Foundation of China (Grant No. 21776068, 21606082), the Key Scientific Research Fund of Hunan Provincial Education Department (Grant No. 19A035) and Collaborative Innovation Center of New Chemical Technologies for Environmental Benignity and Efficient Resource Utilization.
Notes and references
- L. T. Mika, E. Cséfalvay and . Németh, Chem. Rev., 2018, 118, 505–613 CrossRef CAS PubMed.
- M. Akgül, B. zyağcı and A. Karabakan, J. Ind. Eng. Chem., 2013, 19, 240–249 CrossRef.
- F. Tian, Y. Wu, Q. Shen, X. Li, Y. Chen and C. Meng, Microporous Mesoporous Mater., 2013, 173, 129–138 CrossRef CAS.
- X. Wang, L. Chen, D. Huang, J. Yue, Z. Luo and T. Zeng, Catal. Lett., 2018, 148, 3492–3501 CrossRef CAS.
- N. Kumar, P. Mäki-Arvela, S. F. Diáz, A. Aho, Y. Demidova, J. Linden, A. Shepidchenko, M. Tenhu, J. Salonen, P. Laukkanen, A. Lashkul, J. Dahl, I. Sinev, A.-R. Leino, K. Kordas, T. Salmi and D. Y. Murzin, Top. Catal., 2013, 56, 696–713 CrossRef CAS.
- A. I. M. Rabee, L. J. Durndell, N. E. Fouad, L. Frattini, M. A. Isaacs, A. F. Lee, G. A. H. Mekhemer, V. C. D. Santos, K. Wilson and M. I. Zaki, Mol. Catal., 2018, 458, 206–212 CrossRef CAS.
- A. Y. Sidorenko, A. Aho, J. Ganbaatar, D. Batsuren, D. B. Utenkova, G. M. Sen'kov, J. Wärnå, D. Y. Murzin and V. E. Agabekov, Mol. Catal., 2017, 443, 193–202 CrossRef CAS.
- J.-J. Zou, N. Chang, X. Zhang and L. Wang, ChemCatChem, 2012, 4, 1289–1297 CrossRef CAS.
- J. Wang, W. Hua, Y. Yue and Z. Gao, Bioresour. Technol., 2010, 101, 7224–7230 CrossRef CAS PubMed.
- F. Tzompantzi, M. Valverde, A. Pérez, J. L. Rico, A. Mantilla and R. Gómez, Top. Catal., 2010, 53, 1176–1178 CrossRef CAS.
- K. A. D. S. Rocha, P. A. Robles-Dutenhefner, I. V. Kozhevnikov and E. V. Gusevskaya, Appl. Catal., A, 2009, 352, 188–192 CrossRef CAS.
- Y. Liu, L. Li and C. X. Xie, Res. Chem. Intermed., 2016, 42, 559–569 CrossRef CAS.
- M. Hosseini-Sarvari, H. Sharghi and S. Etemad, Chin. J. Chem., 2007, 25, 1563–1567 CrossRef CAS.
- M. L. Kantam, S. Laha, J. Yadav and B. Sreedhar, Tetrahedron Lett., 2006, 47, 6213–6216 CrossRef CAS.
- D. Nguyen Thanh, O. Kikhtyanin, R. Ramos, M. Kothari, P. Ulbrich, T. Munshi and D. Kubička, Catal. Today, 2016, 277, 97–107 CrossRef CAS.
- M. Z. Kassaee, R. Mohammadi, H. Masrouri and F. Movahedi, Chin. Chem. Lett., 2011, 22, 1203–1206 CAS.
- P. L. Anandgaonker, S. Jadhav, S. T. Gaikwad and A. S. Rajbhoj, J. Cluster Sci., 2014, 25, 483–493 CrossRef CAS.
- M. Hosseini-Sarvari, Tetrahedron, 2008, 64, 5459–5466 CrossRef CAS.
- F. Shirini, S. V. Atghia and M. Alipour Khoshdel, Iran. J. Catal., 2011, 1, 93–97 CAS.
- M. Golets, S. Ajaikumar and J.-P. Mikkola, Chem. Rev., 2015, 115, 3141–3169 CrossRef CAS PubMed.
- M. Kitano, K. Nakajima, J. N. Kondo, S. Hayashi and M. Hara, J. Am. Chem. Soc., 2010, 132, 6622–6623 CrossRef CAS PubMed.
- S. Zhou, X. Liu, J. Lai, M. Zheng, W. Liu, Q. Xu and D. Yin, Chem. Eng. J., 2019, 361, 571–577 CrossRef CAS.
- J. Guo, D. Yin and J. Guo, J. Xiangtan. Nor. Univ., (Nat. Sci. Ed.), 2001, 23, 65–68 Search PubMed.
- B. Rajendra Prasad Reddy, P. Vasu Govardhana Reddy and B. N. Reddy, New J. Chem., 2015, 39, 9605–9610 RSC.
- W. Linghu, Y. Sun, H. Yang, K. Chang, G. Sheng, T. Hayat, N. S. Alharbi and J. Ma, J. Mol. Liq., 2017, 244, 146–153 CrossRef CAS.
- T. A. Silva, J. Diniz, L. Paixão, B. Vieira, B. Barrocas, C. D. Nunes and O. C. Monteiro, Solid State Sci., 2017, 63, 30–41 CrossRef CAS.
- R. Luque, J. M. Campelo, T. D. Conesa, D. Luna, J. M. Marinas and A. A. Romero, Microporous Mesoporous Mater., 2007, 103, 333–340 CrossRef CAS.
- N. A. Comelli, E. N. Ponzi and M. I. Ponzi, Chem. Eng. J., 2006, 117, 93–99 CrossRef CAS.
- K. B. Sidhpuria, B. Tyagi and R. V. Jasra, Catal. Lett., 2011, 141, 1164–1170 CrossRef CAS.
- A. Wróblewska, P. Miądlicki and E. Makuch, React. Kinet., Mech. Catal., 2016, 119, 641–654 CrossRef.
|
This journal is © The Royal Society of Chemistry 2020 |
Click here to see how this site uses Cookies. View our privacy policy here.