DOI:
10.1039/D0RA00794C
(Paper)
RSC Adv., 2020,
10, 10188-10196
Tetrahydropyrazolopyridines as antifriction and antiwear agents: experimental and DFT calculations†
Received
26th January 2020
, Accepted 2nd March 2020
First published on 10th March 2020
Abstract
Some tetrahydropyrazolopyridines (THPP-H) with the methoxy (THPP-OMe) and methyl (THPP-Me) substituents were synthesized by a one-pot multi-component reaction. NMR spectroscopy (1H and 13C) was used to authenticate the synthesis. According to the results of tribological tests ASTM D4172, and ASTM D5183 on a four-ball tester in paraffin oil (PO) at a concentration of 0.25% w/v, their relative tribo-activity along with a reference additive, zinc dialkyldithiophosphate (ZDDP) could be figured out as mentioned below-THPP-OMe > THPP-Me > THPP-H > ZDDP. The calculation of frictional power loss from the coefficient of friction data of the tested additives supports the given order. As is apparent from AFM and SEM micrographs of the wear scar surface for plain oil with and without different tetrahydropyrazopyridines, surface evenness endorses the above trend. Proof for strong adsorption of the synthesized additives is provided by EDX analysis of the steel ball surface after performing the tribological test, where nitrogen and oxygen are vividly seen as heteroatoms. XPS studies reveal the composition of the in situ formed tribofilm. The moieties containing carbon bonded to oxygen/nitrogen as decomposed products of the additive together with oxides of iron in +II or +III oxidation states are perceptible in the tribofilm, the tribofilm interferes with the proximity of the surfaces keeping them far apart. Consequently, friction and wear are remarkably reduced. Findings from Density Functional Theory (DFT) calculations are in full agreement with the results obtained from tribological experiments.
1. Introduction
Friction and wear together have been immanent adversaries to mechanical systems. Lubrication stands as the only remedial measure to safeguard such systems.1–5 Sundry lubricant systems with numerous types of additives, therefore, have been fabricated to address this issue. Among them, heterocyclic organic compounds,6 nanomaterials,7,8 inorganic lamellar structures9 and metal complexes10 find paramount significance. Zinc dialkyldithiophosphates (ZDDP) have been employed, very often, as multifaceted antiwear additives.11,12 However, their incessant use is prohibited because of their susceptibility to attenuating the efficacy of exhaust emission catalytic converters, thus enhancing air pollution.13 From an environmental perspective, various standards have been put forth to control sulphated ash, sulphur and phosphorus (SAPS) contents in an additive.14
Nanolubricants15,16 are well appreciated for their dexterous antiwear behavior but their agglomeration poses a great problem for the stability of their dispersions. In contrast, the use of conventional organic compounds is everlasting owing to their comparatively higher solubility in base oils. From the viewpoint of adsorption over the metal/alloy surface, heterocyclic compounds containing heteroatoms specifically, nitrogen and oxygen are categorically advocated for their friction/wear lowering disposition. The lone pair of electrons at heteroatoms and the aromatic ring electrons are basically involved in the process of adsorption.17–20 A comprehensive literature survey reveals that several groups of workers have chosen to investigate the tribological efficiency of different types of heterocyclic compounds. Kamano et al. have patented several pyridines, pyridazines, pyrazines, pyrimidines, pyrroles, pyrazoles, imidazoles as antiwear agents.21 Friction and wear-reducing behavior of indole, indazole and benzotriazole in liquid paraffin oil have been reported by Zhongyi and co-workers.22 Tribological properties of the benzimidazoles23 and tetrazole derivatives24 have been investigated in liquid paraffin oil. The antiwear and antifriction properties of imidazoline derivatives25 in water–glycol mixture and triazine in poly-alpha olefin base oil26 have been studied. Desanker et al. have tested the performance of alkyl-substituted cyclen derivative (commercial Group III lubricating oil) as friction modifier using pin-on-disk tribometry tests.27 Several ionic liquids such as di[bis(2-hydroxyethyl)ammonium]succinate,28 1-acetyl-3-hexylbenzotriazolium benzoate/sorbate,29 poly-alkylimidazoliumbis(trifluoromethylsulfonyl) imide,30 alkylimidazolium diethyl phosphates,31 bis(imidazolium)/bis(ammonium)-di[bis(salicylato)borate]32 are reported as effective antiwear agents. Quinoline derivatives33 in polyethylene glycol (PEG) and Schiff bases of 4-aminoantipyrene with substituted benzaldehyde34 in paraffin oil have been reported as excellent tribological additives from our laboratory. There is always an urge to develop more and more superior antiwear additives of different types. This instigated us to synthesize substituted tetrahydropyrazopyridines, having two pyrazoles and a pyridine ring arranged in a specific fashion and evaluate their tribological behavior in paraffin oil on a four-ball tribo-tester. The tribo-activity is directly related to the number of adsorption centres accessible to the metal surface. The adsorption of substituted tetrahydropyrazopyridines on the steel surface is anticipated to occur primarily through the nitrogen atoms, provided these are competent enough to approach the surface. The inherent properties of the substituents at the pyridine ring may facilitate adsorption by enhancing electron density at these nitrogen atoms. For a deep insight into electronic environments around adsorption centres, Density Functional Theory calculations were also performed. These calculations have been used to validate the observed tribological results.
2. Experimental section
2.1. Chemicals
AR grade chemicals were utilized throughout the investigation.
2.2. Synthesis of tetrahydropyrazolopyridine derivatives
2.0 mmol hydrazine hydrate and 2.1 mmol ethyl acetoacetate in ethanol (5 mL) were taken in a round bottom flask. The reactants were stirred for half an hour at 30 °C and 1.0 mmol aldehyde and 4.0 mmol ammonium acetate were successively added. The prepared reaction mixture was refluxed for 4–8 h and then cooled to normal temperature. The distilled water (10 mL) was added, and the mixture was stirred for 30 min.35 The resulting product was filtered, washed with distilled water followed by acetone and dried under vacuum (Scheme 1).
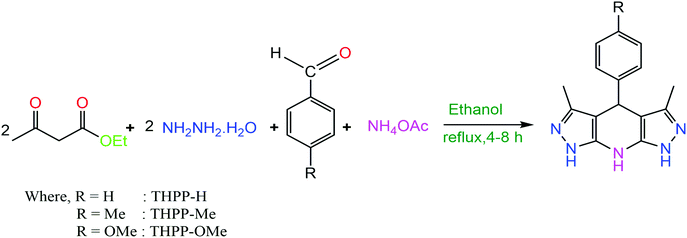 |
| Scheme 1 Synthesis of tetrahydropyrazolopyridine derivatives. | |
NMR spectroscopy was used to characterize the synthesized product. The 1H and 13C NMR spectra of the prepared additives have been provided in the ESI (ESI-1 Fig. S1–S6†). The IUPAC names, abbreviations, structures and characterization of the tetrahydropyrazolopyridines are given in (Table 1).
Table 1 Molecular structures, IUPAC names, abbreviations and characterizations of the tetrahydropyrazolopyridine derivatives (THPP-H, THPP-Me, THPP-OMe)
S. no. |
Structure |
IUPAC name and abbreviation |
Characterization |
1 |
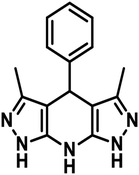 |
3,5-Dimethyl-4-phenyl-1,4,7,8-tetrahydrodipyrazolo[3,4-b:4′,3′-e]pyridine, (THPP-H) |
Melting point 240–242 °C |
1H NMR (500 MHz, DMSO) 7.52–7.50 (2H, d), 7.15–7.13 (1H, d), 6.94 (2H, s), 4.62 (1H, s), 1.80 (6H, s). 13C NMR (126 MHz, DMSO) δ 161.92, 143.71, 140.46, 128.24, 127.97, 125.93, 104.45, 32.81, 10.88. |
2 |
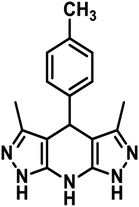 |
3,5-Dimethyl-4-(4-methylphenyl)-1,4,7,8-tetrahydrodipyrazolo[3,4-b:4′,3′-e]pyridine, (THPP-Me) |
Melting point 242–244 °C |
1H NMR (500 MHz, DMSO) δ 7.22–7.21 (2H, d) 7.06–7.03 (2H, d), 4.93 (1H, s), 2.11 (3H, s), 1.80 (6H, s).13C NMR (126 MHz, DMSO) δ 159.92, 140.93, 137.36, 134.87, 129.34, 127.75, 125.04, 124.52, 102.20, 30.50, 18.63, 9.88. |
3 |
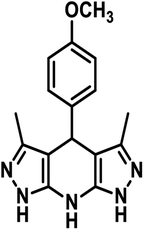 |
3,5-Dimethyl-4-(4-methoxyphenyl)-1,4,7,8-tetrahydrodipyrazolo[3,4-b:4′,3′-e]pyridine, (THPP-OMe) |
Melting point 185–186 °C |
1H NMR (500 MHz, DMSO) δ 7.04–7.02 (2H, d), 6.78–6.76 (2H, d), 4.75 (1H, s), 3.68 (3H, s), 2.07 (6H, s).13C NMR (126 MHz, DMSO) δ 160.71, 156.81, 139.42, 134.80, 128.00, 112.75, 103.91, 54.43, 31.55, 9.96. |
2.3. Tribological analysis
2.3.1. Preparation of admixtures. Tetrahydropyrazolopyridine blends in paraffin oil (base oil) with concentrations (0.00, 0.125, 0.25, 0.50, 0.75 and 1.0% w/v) were made by stirring at 40–50 °C for 1–2 hour followed by 1 h sonication at room temperature. The optimized concentration of the additives was identified as 0.25% w/v. All tribological tests, therefore, were conducted at the concentration, 0.25% w/v.Tribological testing procedures and surface analysis adopted in the present investigation were the same as reported from our laboratory5–8 and are provided as the ESI (ESI-2†).
2.4. Computational details
DFT computations were performed with the help of B3LYP. Full geometry of the additives was optimized with the standard B3LYP/321G+* basis set applying Gaussian 03, revision C. 01.36
3. Results and discussion
3.1. Antiwear studies
The antiwear tests of paraffin oil (PO) with or without synthesized tetrahydropyrazolopyridine derivatives were performed with the help of a four-ball tester. At first, the concentration of the additive was optimized. Fig. 1 displays the deviation in the mean wear scar diameter (MWD) against the concentration of the synthesized additives (0.00 to 1.0% w/v) in base lube at 392 N load for 60 minutes.
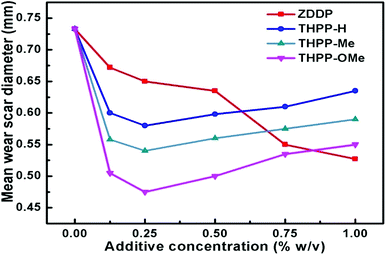 |
| Fig. 1 Deviation in mean wear scar diameter with the concentration of different tetrahydropyrazolopyridine additives in PO at 392 N applied load for 60 min test. | |
It is obvious from Fig. 1 that as compared to plain paraffin oil, the MWD decreases for its blends with tetrahydropyrazolopyridines at all the investigated concentrations up to 0.25% w/v. Beyond 0.25% w/v, there is a sluggish hike in MWD in every case up to 1% w/v. Although the additives are triboactive at all the tested concentrations, 0.25% w/v is considered as the optimum concentration for testing. It is important to point out here that in case of the commercial additive ZDDP, the MWD is much higher at 0.25% w/v and the minimum value is obtained at four times higher concentration, 1% w/v.
Fig. 2 exhibits how COF varies with time for paraffin oil and its admixtures with various tetrahydropyrazolopyridines for the optimized concentration (0.25% w/v) at load 392 N and 60 min duration.
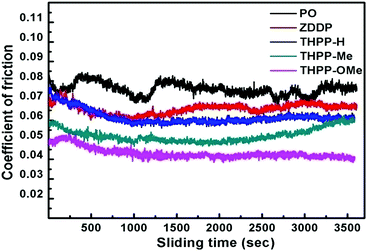 |
| Fig. 2 Variation of the coefficient of friction with sliding time in the presence of different tetrahydropyrazolopyridine additives (0.25% w/v) in PO: load, 392 N; sliding speed, 1200 rpm; temperature, 75 °C; test duration, 60 min. | |
As per figure, the highest diminution in the coefficient of friction values is noted for THPP-OMe followed by THPP-Me and finally THPP-H.
Fig. 3 displays magnitude of reduction in MWD and COF data simultaneously for base oil with or without the synthesized additives. The MWD for base oil (0.733 mm) undergoes about 21, 26 and 35% reduction in the presence of THPP-H, THPP-Me and THPP-OMe respectively. However, there is only an 11% reduction in MWD for the standard additive zinc dialkyldithiophosphate (ZDDP). The observed data indicate the highest antiwear performance for the THPP-OMe derivative. Similarly, reduction in values of the coefficient of friction (COF) of base oil (0.0948) is observable in its blends with ZDDP (11%), THPP-H (13%), THPP-Me (26%) and THPP-OMe (40%) supporting the maximum antifriction performance again for THPP-OMe additive.
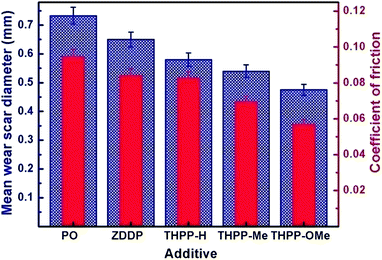 |
| Fig. 3 Variation of mean wear scar diameter and coefficient of friction in the presence of tetrahydropyrazolopyridine additives in PO: load, 392 N; sliding speed, 1200 rpm; temperature, 75 °C; test duration, 60 min; concentration of additives, 0.25% w/v. | |
Fig. 4 displays the relation between frictional torque and time at succeeding loads beginning from 98 N experimental load. For the base lube, frictional torque increases slowly up to 1078 N load and thereafter increases abruptly due to failure of the tribofilm.
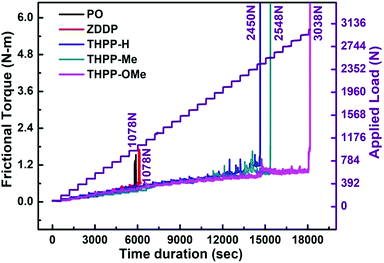 |
| Fig. 4 Alteration of frictional torque with stepwise loading and time for different tetrahydropyrazolopyridine additives: sliding speed, 600 rpm; temperature, 75 °C; concentration of additives, 0.25% w/v. | |
Thus, base oil alone can sustain the load only up to 1078 N. It is noticeable that for ZDDP 0.25% w/v concentration is not compatible with increasing the load-bearing capacity of base lube. On the other hand, for the synthesized additives a sharp increase in frictional torque is noted at much higher loads, THPP-H (2450 N), THPP-Me (2548 N) and THPP-OMe (3038 N). Thus, the developed tribochemical film is much stronger to bear the load when THPP-OMe is applied as an additive.
The frictional power loss (P)37 for different tetrahydropyrazolopyridine additives, collected in Table 2 has been calculated using the given eqn (1). The details are given in (ESI-3†).
|
P = 2.07 × μ × 10−3 (W)
| (1) |
where,
μ = coefficient of friction
Table 2 Loss of frictional power measured for different additives at the concentration, 0.25% (w/v) in PO
S. no. |
Additives |
Power consumption (MJ) |
Reduction in power consumption |
% reduction in power consumption |
1 |
PO |
0.7064 |
____ |
____ |
2 |
ZDDP |
0.6296 |
0.0768 |
10.87 |
3 |
THPP-H |
0.6183 |
0.0881 |
12.47 |
4 |
THPP-Me |
0.5200 |
0.1864 |
26.39 |
5 |
THPP-OMe |
0.4264 |
0.2800 |
39.64 |
The PO shows highest power consumption (0.7064 MJ) as compared to the other additives, ZDDP (0.6296 MJ), THPP-H (0.6183 MJ), THPP-Me (0.5200 MJ) and THPP-OMe (0.4264 MJ). The highest percentage reduction in P was observed in case of THPP-OMe additive, 39.64%. Consequently, among all the tested additives, THPP-OMe additive saves substantial energy.
3.2. Surface examination of the wear scar
The worn surface has been examined by SEM and AFM (contact mode) after tribological test ASTM D4172. The SEM images of worn surface on steel ball in the presence of blank lubricant and its blends with tetrahydropyrazolopyridines (0.25% w/v) are shown in Fig. 5. The size of wear scar and its smoothness are directly related to the relative tribological performance of the synthesized additives. Thus, severely damaged wear scar surface for plain paraffin oil while substantially smoothened surface in case of THPP-OMe may be arguably discussed.
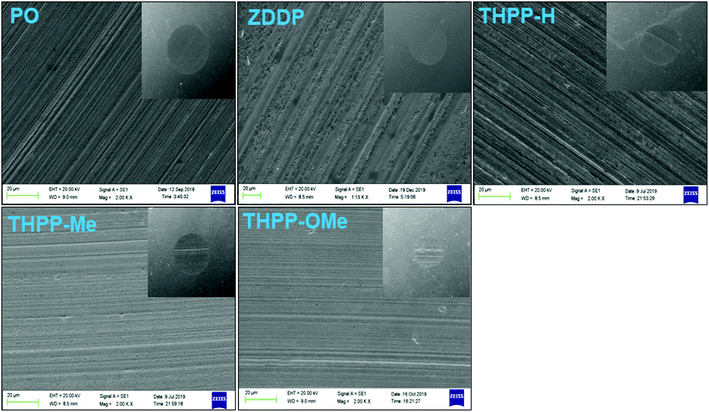 |
| Fig. 5 SEM images (inset: full view of wear scar at 100×, wear scar surface at 2.00k× magnification) of the worn steel surface lubricated with PO with or without tetrahydropyrazolopyridine additives (0.25% w/v) for 60 min test at 392 N applied load. | |
The AFM of the worn surface was performed after the antiwear test. The obtained data for surface roughness variables of wear scars on steel ball are displayed in Fig. 6 together with their 3D AFM figures.
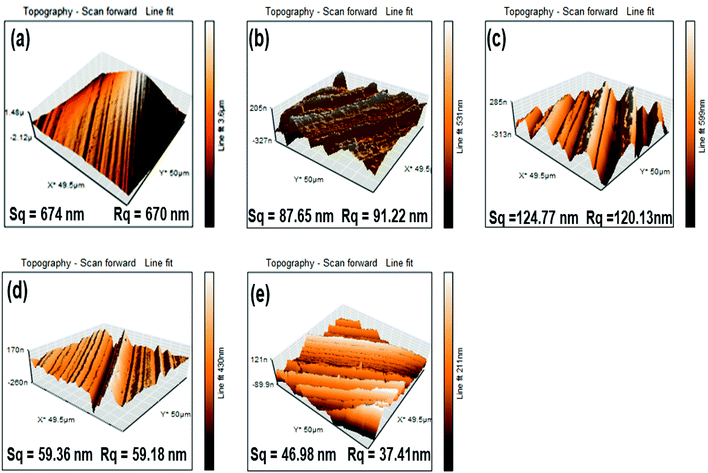 |
| Fig. 6 3D AFM images of the wear scar surface in the presence of PO with or without different tetrahydropyrazolopyridine additives (0.25% w/v) for 60 min test duration at 392 N applied load (a) PO, (b) ZDDP, (c) THPP-H, (d) THPP-Me and (e) THPP-OMe. | |
The roughness parameters, root mean square area (Sq) and root mean square line roughness (Rq) were found to be very high (Sq = 674 nm, Rq = 670 nm) for the blank oil. A huge reduction in these values is marked in the presence of additives THPP-OMe (Sq = 46.98 nm, Rq = 37.41 nm), THPP-Me (Sq = 59.36 nm, Rq = 59.18 nm), THPP-H (Sq = 124.77 nm, Rq = 120.13 nm). The above-mentioned values of Sq and Rq validate the order of activity obtained from tribological data.
3.3. Energy dispersive X-ray spectroscopy (EDX)
The EDX analysis of wear scar in the presence of plain oil and its admixtures with tetrahydrohydopyrazolopyridines has been performed after the antiwear test for elemental characterization of the tribofilm. Fig. 7 shows the EDX spectra of base lube and its admixture with THPP-OMe. Presence of nitrogen as the heteroatom can be easily seen in Fig. 7(b), emphasizing its contribution during the development of tribofilm.
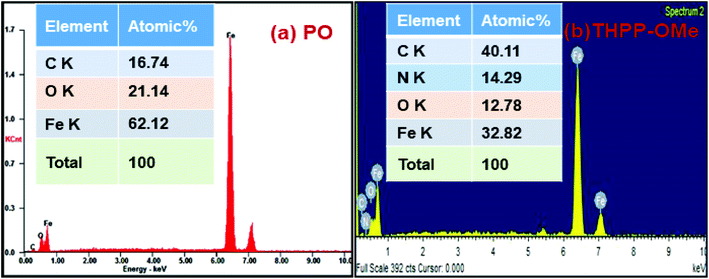 |
| Fig. 7 EDX spectra of worn surface lubricated with (a) PO and (b) THPP-OMe. | |
3.4. X-ray photoelectron spectroscopy (XPS)
The deconvoluted XPS spectra of C 1s, N 1s, O 1s and Fe 2p of the tribofilm formed on the wear scar surface in the presence of THPP-OMe after following ASTM D4172 standards are displayed in Fig. 8. The core-level spectrum of C 1s, Fig. 8(a) exhibits two peaks at 284.5, 285.1 eV binding energies corresponding to C–C/C
C, C–O/C–N bonds respectively.8,38,39 Fig. 8(b) shows core-level spectrum of O 1s indicating three peaks with binding energies 529.8, 532.1 and 533.5 eV which could be correlated with Fe–O/Fe2O3, C–O, C–O–C moieties respectively.40–42 The N 1s spectrum is illustrated in Fig. 8(c). The presence of only one peak identified at 399.9 eV could be accorded with –N
C/–N–C– group.10 The binding energies of Fe 2p at 710.8 eV (Fig. 8(d)) and O 1s at 529.8 eV (Fig. 8(b)) together indicate the formation of iron oxides FeO and Fe2O3 confirming oxidation of steel surface iron during rubbing process.43 Thus, it may be inferred that the additive adsorbed on the steel surface through heteroatoms has decomposed under tribo conditions to form a complex tribofilm along with the mixture of FeO/Fe2O3 and rendered active participation in exceeding lubricating behavior.
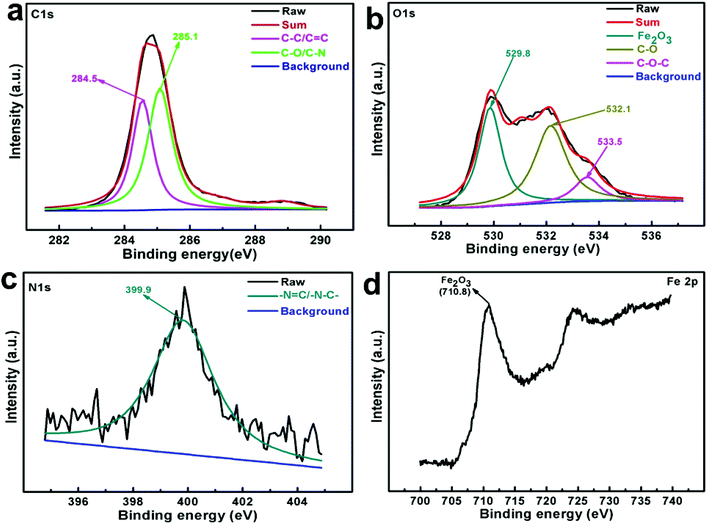 |
| Fig. 8 XPS spectra of tribochemical film formed on worn steel surface lubricated with the THPP-OMe additive (0.25% w/v) at 392 N applied load for 60 min test duration in PO. (a) C 1s (b) O 1s (c) N 1s and (d) Fe 2p. | |
3.5. Tribochemistry and proposed mechanism for triboaction
Based on tribological tests, it may be established that tertahyrdopyrazolopyridine formulations prove to be extremely tribologically active. The AFM and SEM results corroborate the experimental data for the relative activity of different additives. The energy dispersive X-ray analysis provides sufficient evidence in support of heteroatoms present on the tribo-surface. A thin chemical film is formed under the tribo-test condition because of additive decomposition and interaction of the decomposed products with the mating surfaces. The tenacious film keeps the proximal surfaces away from each other and therefore, friction and wear are greatly reduced.
3.6. DFT calculations
The DFT calculations have been conducted to observe the effect of various substituents on the inherent framework of tetrahydropyrazolopyridine towards antiwear lubricating properties. An endeavour has been made to correlate the test results with the molecular structures of the synthesized additives. Fig. 9 displays the optimized structures of the synthesized tetrahydropyrazolopyridine additives THPP-OMe, THPP-Me, THPP-H. At first, the additive molecules tend to undergo physical or chemical adsorption on the steel ball surface via their polar ends followed by their chemical interaction at the surface. Frontier Molecular Orbital (FMO) theory, may be ensued to give the mechanism of tribological behavior. The quantum chemical variables like total energy, the energy of highest occupied and lowest unoccupied molecular orbitals (EHOMO and ELUMO) and their energy gap (ΔE = ELUMO − EHOMO) are given in Table 3. These variables have been used to justify the reactivity of the additive molecules.
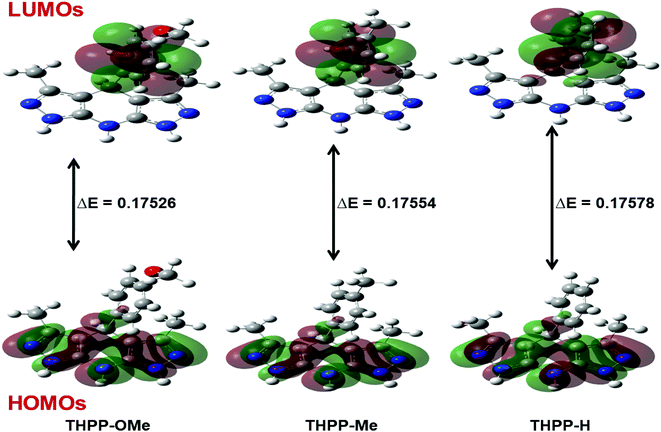 |
| Fig. 9 Frontier Molecular Orbitals (HOMO and LUMO) of different tetrahydropyrazolopyridine additives with their ΔE values. | |
Table 3 Quantum chemical parameters of tetrahydropyrazolopyridine antiwear additives by B3LYP/3-21G +*
S. no. |
Additives |
Total energy (a.u.) |
EHOMO (Hartree–Fock) |
ELUMO (Hartree–Fock) |
ΔE (Hartree–Fock) |
I |
A |
χ |
γ |
σ |
1 |
Fe5 (ref. 45) |
|
−0.18651 |
−0.06420 |
0.12231 |
0.18651 |
0.06420 |
0.12535 |
0.06115 |
16.35322 |
2 |
THPP-OMe |
−963.67 |
−0.20469 |
−0.02943 |
0.17526 |
0.20469 |
0.02943 |
0.11706 |
0.08763 |
11.41162 |
3 |
THPP-Me |
−888.86 |
−0.20413 |
−0.02859 |
0.17554 |
0.20413 |
0.02859 |
0.11636 |
0.08777 |
11.39341 |
4 |
THPP-H |
−849.75 |
−0.20529 |
−0.02951 |
0.17578 |
0.20529 |
0.02951 |
0.11740 |
0.08789 |
11.37786 |
In accordance with the Hartree–Fock theorem,44 the energies of frontier molecular orbitals are shown by:
where
I and
A correspond to the ionization potential and the electron affinity respectively and are depicted in
Table 3.
The absolute electronegativity (χ) is given as:
The global hardness (γ) is equal to:
When metal (iron) and additive come in close proximity to each other, electron flows from lower χ (additive) to higher χ (iron) values until chemical potentials become equal.
The global softness (σ) is defined as:
Global softness (σ) gives information about the reactivity of a compound.
Based on the hardness–softness concept, it may be stated that the highest value for ΔE corresponds to highest stability index showing hard or inert behavior in a chemical reaction; on the other hand, its lowest value designates the lowest stability index accompanied with soft or easily polarized behavior. The soft additive with the smallest energy gap ΔE is anticipated to show the maximum capability of adsorption and accordingly, it would be the most tribologically active additive. It is apparent from Table 3 that additive (THPP-OMe) is having the lowest value for γ and the highest for σ. Based on these parameters, the ascending order of tribological performance of the synthesized additives may be expressed as:
THPP-H < THPP-Me < THPP-OMe |
3.7. Structure–activity relationship
The tribological data achieved for different tetrahydropyrazolopyridines may be correlated with their corresponding structures. Structurally, a tetrahydropyrazolopyridine moiety has a pyridine ring fused with two pyrazole rings on either side. It may get adsorbed on the steel ball surface via nitrogens of the pyrazoles and the pyridine ring. All the nitrogens being present in a delocalized system are engaged in surface adsorption. The relative performance of different additives is guided by the nature of substituents attached to the benzene ring at the 4th position of the pyridine group. As discussed above, the best activity is displayed by methoxy analogue (THPP-OMe) followed by methyl (THPP-Me) and then (THPP-H). The observed order reflects that the electron density on the fused rings has decreased accordingly. The +R effect of methoxy group and +I effect of the methyl group have been instrumental in increasing the electron-donating tendency of the corresponding tetrahydropyrazolopyridines.
4. Conclusions
(1) The tetrahydropyrazolopyridine additives were synthesized and characterized by NMR spectroscopy.
(2) The studied additives having zero SAPs contents show very high tribological activity at all the tested concentrations. The maximum activity is observed at a very low concentration, 0.25% w/v.
(3) Based on antiwear and load ramp tests at 0.25% w/v concentration, the activity of various additives could be established as:
ZDDP < THPP-H < THPP-Me < THPP-OMe |
(4) Morphological investigations of the wear scar surface authenticate the relative tribological activity.
(5) The DFT calculations verify the experimentally found data.
(6) The EDX analysis of the wear scar surface shows the presence of heteroatoms, nitrogen and oxygen confirming adsorption of different additives on the steel surface.
(7) XPS spectra of the wear scar surface confirm that tribochemical film is made up of decomposed products of the additive along with iron oxides.
Conflicts of interest
There is no conflict of interest.
Acknowledgements
One of the authors, Kavita acknowledge to Council of Scientific & Industrial Research (CSIR), India for financial support. Authors are grateful to the Incharge of Central Instrument Facility Centre (CIFC) – IIT (BHU), Varanasi for NMR and SEM with EDX services.
Notes and references
- S. C. Tung and M. L. McMillan, Tribol. Int., 2004, 37, 517–536 CrossRef CAS.
- S. M. Hsu, Tribol. Int., 2004, 37, 553–559 CrossRef CAS.
- M. D. Bermúdez, A. E. Jiménez, J. Sanes and F. J. Carrión, Molecules, 2009, 14, 2888–2908 CrossRef PubMed.
- M. K. A. Ali, H. Xianjun, L. Mai, C. Bicheng, R. F. Turkson and C. Qingping, Wear, 2016, 364, 270–281 CrossRef.
- B. Kumar, J. Kuntail, D. K. Verma, R. B. Rastogi and I. Sinha, J. Mol. Liq., 2019, 289, 111171 CrossRef.
- Kalyani, V. Jaiswal, R. B. Rastogi and D. Kumar, RSC Adv., 2014, 4, 30500–30510 RSC.
- Kalyani, R. B. Rastogi and D. Kumar, ACS Sustainable Chem. Eng., 2016, 4, 3420–3428 CrossRef CAS.
- D. K. Verma, B. Kumar, Kavita and R. B. Rastogi, ACS Appl. Mater. Interfaces, 2018, 11, 2418–2430 CrossRef PubMed.
- J. Wu, X. Huang, K. Berglund, X. Lu, X. Feng, R. Larsson and Y. Shi, Compos. Sci. Technol., 2018, 162, 86–92 CrossRef CAS.
- V. Jaiswal, S. R. Gupta, R. B. Rastogi, R. Kumar and V. P. Singh, J. Mater. Chem. A, 2015, 3, 5092–5109 RSC.
- B. H. Kim, J. C. Jiang and P. B. Aswath, Wear, 2011, 270, 181–194 CrossRef CAS.
- A. M. Barnes, K. D. Bartle and V. R. A. Thibon, Tribol. Int., 2001, 34, 389–395 CrossRef CAS.
- P. Njiwa, C. Minfray, T. Le Mogne, B. Vacher, J. M. Martin, S. Matsui and M. Mishina, Tribol. Lett., 2011, 44, 19–30 CrossRef CAS.
- H. Spikes, Lubr. Sci., 2008, 20, 103–136 CrossRef CAS.
- M. K. A. Ali, H. Xianjun, L. Mai, C. Qingping, R. F. Turkson and C. Bicheng, Tribol. Int., 2016, 103, 540–554 CrossRef CAS.
- H. Xie, B. Jiang, J. He, X. Xia and F. Pan, Tribol. Int., 2016, 93, 63–70 CrossRef CAS.
- F. U. Shah, S. Glavatskih and O. N. Antzutkin, ACS Appl. Mater. Interfaces, 2009, 1, 2835–2842 CrossRef CAS PubMed.
- B. Bhushan, J. N. Israelachvili and U. Landman, Nature, 1995, 374, 607 CrossRef CAS.
- S. V. Didziulis, Langmuir, 1995, 11, 917–930 CrossRef CAS.
- J. Lara, T. Blunt, P. V. Kotvis, A. Riga and W. T. Tysoe, J. Phys. Chem. B, 1998, 102, 1703–1709 CrossRef CAS.
- H. Kamano and H. Koshima, US Pat., 8,841,242 B2, 2014.
- Z. He, W. Rao, T. Ren, W. Liu and Q. Xue, Tribol. Lett., 2002, 13, 87–93 CrossRef CAS.
- X. Xu, Y. Wan and L. Cao, Wear, 2000, 241, 41–46 CrossRef CAS.
- J. Li, T. Ren, H. Liu, D. Wang and W. Liu, Wear, 2000, 246, 130–133 CrossRef CAS.
- L. Xiong, Z. He, S. Han, J. Tang, Y. Wu and X. Zeng, Tribol. Int., 2016, 104, 98–108 CrossRef CAS.
- G. Yang, J. Zhang, S. Zhang, L. Yu, P. Zhang and B. Zhu, Tribol. Int., 2013, 62, 163–170 CrossRef CAS.
- M. Desanker, X. He, J. Lu, P. Liu, D. B. Pickens, M. Delferro, T. J. Marks, Y. W. Chung and Q. J. Wang, ACS Appl. Mater. Interfaces, 2017, 9, 9118–9125 CrossRef CAS PubMed.
- M. D. Avilés, F. J. Carrión-Vilches, J. Sanes and M. D. Bermúdez, Tribol. Lett., 2019, 67, 26 CrossRef.
- P. S. Bakshi, R. Gusain, M. Dhawaria, S. K. Suman and O. P. Khatri, RSC Adv., 2016, 6, 46567–46572 RSC.
- J. Wu, L. Mu, X. Feng, X. Lu, R. Larsson and Y. Shi, Adv. Mater. Interfaces, 2019, 6, 1–8 CAS.
- L. Zhang, D. Feng and B. Xu, Tribol. Lett., 2009, 34, 95–101 CrossRef.
- R. Gusain, P. Gupta, S. Saran and O. P. Khatri, ACS Appl. Mater. Interfaces, 2014, 6, 15318–15328 CrossRef CAS PubMed.
- D. K. Verma, Kalyani, V. Jaiswal and R. B. Rastogi, Tribol. Trans., 2019, 62, 283–294 CrossRef CAS.
- V. Jaiswal, Kalyani, R. B. Rastogi and R. Kumar, J. Mater. Chem. A, 2014, 2, 10424–10434 RSC.
- M. Dabiri, P. Salehi, M. Koohshari, Z. Hajizadeh and D. I. MaGee, Arkivoc, 2014, 204–214 Search PubMed.
- S. Dapprich, A. D. Daniels, M. C. Strain, O. Farkas, D. K. Malick, A. D. Rabuck, K. Raghavachari, J. B. Foresman, J. V. Qrtiz, Q. Cui and A. G. Baboul, Gaussian 03, revision C.01, Gaussian. Inc., Wallingford, CT., 2004 Search PubMed.
- S. S. Rawat, A. P. Harsha, S. Das and A. P. Deepak, Tribol. Trans., 2019, 1–11 Search PubMed.
- B. Kumar, D. K. Verma, A. K. Singh, Kavita, N. Shukla and R. B. Rastogi, Compos. Interfaces, 2019, 1–18 Search PubMed.
- F. Sordello, G. Zeb, K. Hu, P. Calza, C. Minero, T. Szkopek and M. Cerruti, Nanoscale, 2014, 6, 6710–6719 RSC.
- G. Yang, Z. Zhang, G. Li, J. Zhang, L. Yu and P. Zhang, J. Tribol., 2011, 133, 1–7 CrossRef.
- G. Yang, J. Zhao, L. Cui, S. Song, S. Zhang, L. Yu and P. Zhang, RSC Adv., 2017, 7, 7944–7953 RSC.
- V. Kumar, D. Bano, D. K. Singh, S. Mohan, V. K. Singh and S. H. Hasan, ACS Sustainable Chem. Eng., 2018, 6, 7662–7675 CrossRef CAS.
- J. Zhou, Z. Wu, Z. Zhang, W. Liu and H. Dang, Wear, 2001, 249, 333–337 CrossRef CAS.
- P. Mourya, P. Singh, A. K. Tewari, R. B. Rastogi and M. M. Singh, Corros. Sci., 2015, 95, 71–87 CrossRef CAS.
- W. Huang, Y. Tan, B. Chen, J. Dong and X. Wang, Tribol. Int., 2003, 36, 163–168 CrossRef CAS.
Footnotes |
† Electronic supplementary information (ESI) available. See DOI: 10.1039/d0ra00794c |
‡ These authors contributed equally to this work. |
|
This journal is © The Royal Society of Chemistry 2020 |
Click here to see how this site uses Cookies. View our privacy policy here.