DOI:
10.1039/D0RA00668H
(Paper)
RSC Adv., 2020,
10, 13855-13865
Promotion effect of urchin-like MnOx@PrOx hollow core–shell structure catalysts for the low-temperature selective catalytic reduction of NO with NH3
Received
21st January 2020
, Accepted 2nd March 2020
First published on 6th April 2020
Abstract
A MnOx@PrOx catalyst with a hollow urchin-like core–shell structure was prepared using a sacrificial templating method and was used for the low-temperature selective catalytic reduction of NO with NH3. The structural properties of the catalyst were characterized by FE-SEM, TEM, XRD, BET, XPS, H2-TPR and NH3-TPD analyses, and the performance of the low-temperature NH3-SCR was also tested. The results show that the catalyst with a molar ratio of Pr/Mn = 0.3 exhibited the highest NO conversion at nearly 99% at 120 °C and NO conversion greater than 90% over the temperature range of 100–240 °C. Also, the MnOx@PrOx catalyst presented desirable SO2 and H2O resistance in 100 ppm SO2 and 10 vol% H2O at the space velocity of 40
000 h−1 and a testing time of 3 h test at 160 °C. The excellent low-temperature catalytic activity of the catalyst could ultimately be attributed to high concentrations of Mn4+ and adsorbed oxygen species on the catalyst surface, suitable Lewis acidic surface properties, and good reducing ability. Additionally, the enhanced SO2 and H2O resistance of the catalyst was primarily ascribed to its unique core–shell structure which prevented the MnOx core from being sulfated.
1 Introduction
The selective catalytic reduction of NO with NH3 (NH3-SCR) is considered to be the most effective and widely applied technology for eliminating NOx from stationary sources.1–3 Low-temperature NH3-SCR, which can be placed downstream of a desulfurization tower and electrostatic precipitation in a power generation system, has gained increasing attention in recent years due to improved SCR economics.4 Abundant investigations have been carried out, and have made great progress in low-temperature NH3-SCR catalysts. Many developments have been made on low-temperature NH3-SCR catalysts. Among the various catalyst systems, Cu-based,5,6 Ce-based,7 Fe-based,8,9 Zr-based,10 Mn-contained catalysts have stimulated great interest because of their oxidation–reduction properties, environmentally friendly features and excellent low-temperature activities, however a disadvantage is easy deactivation in the presence of SO2 in the exhaust gas.
Many strategies have been proposed to overcome this problem. One strategy includes adding other metal elements modification and is considered as one of the most promising and effective methods. Wang et al.11 reported that the co-doping with Fe and Co can effectively improve the SO2 resistance of a Mn–Ce/TiO2 catalyst because the introduction of Fe and Co can prevent SO2 diffusion to the inner layer of the catalyst. Chang et al.12 proposed that the SO2 resistance of MnOx–CeO2 could be enhanced by Sn doping since it creates more Lewis acid sites on the surface for the SO2-containing SCR reaction. Xie et al.13 demonstrated that the addition of Cr reduced the SO2 adsorption strength on the surface of a MnCrOx/sepiolite catalyst, thereby increasing the anti-SO2 poisoning of the catalyst.
Among the potential additives, rare earth oxides (REOs) have been proven to possess high catalytic activity originating from their oxygen vacancies and strong surface acidities.14–18 Yan et al.18 synthesized RE-doped Mn/ASC for the low-temperature NH3-SCR of NO and found that the addition of RE enhanced the catalytic activity. In addition, DRIFTS result confirm that Ce doping provides more active Brønsted acid sites. Yu et al.19 studied the de-NOx catalytic activity and SO2 resistance of Ce/Pr-MnOx/SAPO-34 and proposed that compared with Ce, the Pr doping on the MnOx/SAPO-34 contained more oxygen vacancies, exhibited a superior low-temperature NH3-SCR activity, and inhibited the formation of ammonia sulfate on the catalyst surface, which protected the active Mn sites.
Some researchers contend that the morphology and structure of the composite oxide catalysts had an impact on their resistance to SO2 poisoning in the low-temperature SCR process.20–24 Generally, compared with irregular particles, catalysts with a well-designed structure typically exhibit higher functionality due to the size, shape, and interfacial effects. Therefore, considerable research has been focused on preparing SCR catalysts with a specific structure, such as hierarchical porous structures, hollow structures or a core–shell structure. In particular, core–shell structured catalysts have attracted much attention due to their unique mechanical and structural properties for the low-temperature NH3-SCR. For instance, a MnOx@TiO2 core–shell nanorod catalyst was prepared by a novel two-step method, which exhibited outstanding SCR performance due to possessed abundant mesopores and a core–shell structure. These features protect the catalytic active sites from SO2 and H2O poisoning.2 Han et al. designed a meso-TiO2@Fe2O3@Al2O3 core–shell material using experimental and density functional theory methods and found that the strong SO2 tolerance was attributed to the mesoporous-TiO2 shell, and it effectively prevented the deposition of FeSO4 and NH4HSO4.25 Ma et al. synthesized a hollow structured CeO2–MnOx hybrid materials with a multi-shelled structure by using carbon spheres as the hard template. This hybrid material displayed superior activity and stability over traditional CeO2–MnOx particles, most likely attributed to the special multi-shelled structure and abundant surface active species.26 Hence, the controlled fabrication of well-structured composites is of great significance for low-temperature NH3-SCR catalysts, and the core shape, elements and shell thicknesses are key factors. The hollow, core–shell composite structure catalyst, with special isolated chambers and controllable shell structures, would be prepared according to the structural characteristics of the hollow structure and core–shell structure. To the best of our knowledge, there are a limited number of reports about the hollow, core–shell structured Mn–Pr binary oxides as catalysts for low-temperature NH3-SCR.
In this paper, a hollow MnOx@PrOx core–shell structure catalyst for the low-temperature NH3-SCR reaction was prepared using carbon spheres both as hard template and as reducing agent. The obtained catalysts were then characterized by SEM, TEM, XRD, XPS, NH3-TPD and H2-TPR analysis, and the NH3-SCR reaction performance was tested to determine the physicochemical properties and structure–performance relationships.
2 Experimental
2.1 Catalyst preparation
Carbon spheres were prepared according to a typical hydro-thermal method.27 Typically, a 60 mL solution containing 0.5 g glucose was hydrothermally treated at 180 °C for 24 h and then cooled to room temperature naturally. After suction, filtering and washing with deionized water and absolute ethanol, the dark brown sample was dried in a vacuum oven at 80 °C for 12 h, and the templates were obtained.
The chemical process to synthesize the hollow MnOx@PrOx was carried out in two steps. The CSs@MnOx was first synthesized with the following procedure. A desired amount of CSs was placed into deionized water, and then KMnO4 was added with unceasingly stirring for 30 min. Thereafter, the mixture solution was transferred into an autoclave and maintained at 160 °C for 12 h. Until cooling to room temperature naturally, the obtained suspension was centrifuged and washed with water and absolute ethanol repeatedly. Finally, the CSs@MnOx was obtained by drying at 80 °C for 12 h.
Second, the hollow MnOx@PrOx was synthesized by a chemical precipitation method. Certain amounts of CSs@MnOx, Pr(NO3)3·6H2O, and NaOH were respectively dissolved in deionized water with the molar ratios of Pr/Mn of 0.3 and Pr(NO3)3·6H2O/NaOH of 0.5. Thereafter, the Pr(NO3)3·6H2O and NaOH solutions were added dropwise into above solution simultaneously and heated to 85 °C under stirring for 3 h. Finally, the hollow MnOx@PrOx was collected, washed to neutral, dried at 80 °C for 12 h and calcined at 400 °C in air for 3 h. The hollow MnOx could be obtained by the roasting treatment of CSs@MnOx. The hollow MnOx–PrOx catalyst without a core–shell structure was prepared through a similar method for hollow MnOx, and the only difference was that KMnO4 and Pr(NO3)3·6H2O were added together.
2.2 NH3-SCR activity test
The NH3-SCR activity of the solid catalyst was carried out in a fixed-bed quartz continuous flow reactor. The feed gas was composed of 0.08% NO, 0.08% NH3, 100 ppm SO2 (when added), 10 vol% H2O (when added), 5.0 vol% O2, and the balanced gas was Ar. The total flow rate was 600 mL min−1, corresponding to a gas hourly space velocity (GHSV) of 40
000 h−1. The NO, NO2 and NOx concentrations were measured using an NO–NO2–NOx analyzer (Thermal Scientific, model 42i-HL), and the concentration of N2 was monitored using a gas chromatograph (GC9560, Shanghai Huaai) with a TCD and 5 A columns. The NO removal efficiency and the N2 selectivity were obtained by the following equations: |
 | (1) |
|
 | (2) |
2.3 Catalyst characterization
Field emission scanning electron microscopy (FE-SEM) with an energy dispersive spectroscopy (EDS) was used to analyze the surface morphology and elemental composition of the catalysts using a ZEISS Merlin instrument. The micro-structural characterization by transmission electron microscopy (TEM) and high-resolution TEM (HRTEM) were carried out on JEM-2100 HT. Elemental mapping was conducted using an Inca Energy 200 TEM system. X-ray diffraction (XRD) was determined using a D8 Advance (Bruker) X-ray diffraction instrument with Cu Kα radiation (λ = 1.5406 Å). X-ray photo-electron spectroscopy (XPS) analyses were carried out on an ESCALAB 250 spectrometer (Thermo Fisher Scientific, USA) equipped with Al Kα X-ray radiation (1486.7 eV). H2-TPR (10% H2/Ar gas flow: 30 mL min−1 and a heating rate of 10 °C min−1) and NH3-TPD (N2 flow: 30 mL min−1 and a heating rate of 10 °C min−1) analysis were performed using a Micromeritics Auto ChemII 2920 instrument.
3 Results and discussion
3.1 Catalytic performance for the low-temperature NH3-SCR
The NH3-SCR catalytic performance of the hollow PrOx, hollow MnOx, hollow MnOx@PrOx and hollow MnOx–PrOx were shown in Fig. 1a. It could be seen from Fig. 1a that the NO conversion of the MnOx-containing samples increased with increasing reaction temperature and then decreased, exhibiting different activated temperature windows. Comparatively, the hollow PrOx catalyst basically had no catalytic activity at low temperature, when the reaction temperature greater than 160 °C, and the NO conversion rate began to gradually increase and reached the maximum conversion rate about 45% at 220 °C. Comparing the four catalysts, the hollow MnOx@PrOx catalyst exhibited superior low-temperature catalytic activity, achieving 97.1% of NO conversion at 100 °C, while the hollow PrOx, hollow MnOx and hollow MnOx–PrOx were only 21.3%, 59.5%, and 72.4%, respectively. In addition, the hollow MnOx@PrOx catalyst displayed more than 90% NO conversion over a wider temperature range of 100–240 °C, while the other catalysts had narrow temperature windows. N2 selectivity tests (Fig. 2a) and stability tests (Fig. 2b) were also performed and the hollow MnOx@PrOx consistently exhibited excellent catalytic activity, high N2 selectivity and high stability. In the whole reaction temperature range of 80–240 °C, N2 selectivity was above 95%, and NO conversion was maintained at 97% over the 24 h stability test at 160 °C. It could be deduced that the core–shell structure promotes the synergistic effect between the MnOx core and PrOx shell, and enhanced catalytic activity.
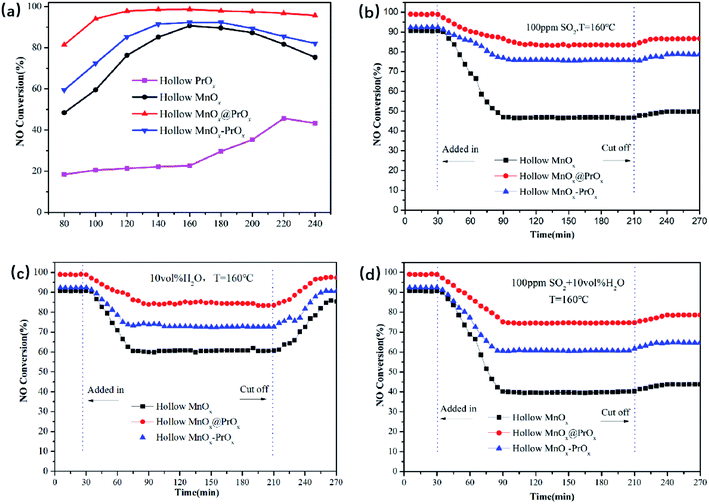 |
| Fig. 1 NO conversion (a); SO2 (b); H2O (c); SO2 + H2O (d) tolerance test of catalysts. | |
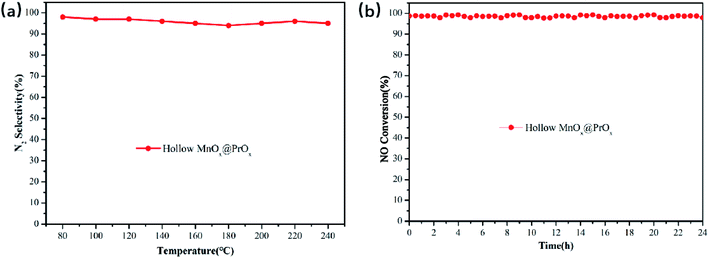 |
| Fig. 2 N2 selectivity (a) and stability test (b) of hollow MnOx@PrOx. | |
The effects of SO2 and H2O on the low-temperature SCR activity of catalysts are shown in Fig. 1(b–d). Fig. 1b shows the NO conversion for the hollow MnOx, hollow MnOx@PrOx and hollow MnOx–PrOx catalysts when 100 ppm SO2 was added at 160 °C. NO conversion decreased upon the addition of SO2. The hollow MnOx@PrOx exhibited superior resistance to SO2 poisoning, and the NO conversion was maintained at over 83.4% after a 3 h test, while the NO conversion of hollow MnOx–PrOx decreased from 92.3% to 75.5%. And the hollow MnOx catalyst exhibited a more obvious poisoning and the NO conversion decreased from 90.7% to 46.3%. Furthermore, when SO2 steam was cut off, the NO conversion for the catalysts could be partly restored to 86.6%, 78.7% and 49.7%, respectively. As displayed in Fig. 1c, the H2O resistance of the catalysts was tested using 10 vol% H2O at 160 °C. A decrease in NO conversion from 90.6% to less than 60% for the hollow MnOx catalyst was detected. In addition, the NO conversions of hollow MnOx@PrOx and hollow MnOx–PrOx declined as well but still remained at around 84% and 73%, respectively, for the next three hours. Additionally, it is worth noting that the NO conversion with the catalysts almost recovered to its original level when H2O was completely removed, indicating that the inhibitory effect of H2O are reversible. According to the results shown in Fig. 1d, when 100 ppm SO2 and 10 vol% H2O were both introduced into the reaction system, the NO conversions of the catalysts were lower than in the presence of either SO2 or H2O alone. This was especially seen using the hollow MnOx catalyst, which exhibited relatively faster deactivation with NO conversion decreasing sharply from 90.5% to 39.4% within one hour. By comparison, the coexistence of SO2 and H2O only resulted in a 20% decrease in NO conversion for the hollow MnOx@PrOx and a 32% decrease for hollow MnOx–PrOx, indicating that the introduction of Pr element could not only significantly increase the low-temperature activity of the catalysts but also enhance the SO2 and H2O resistance of the catalysts. The excellent poisoning resistance of the hollow MnOx@PrOx catalyst could be attributed to the protective effect of the PrOx shell, which could first react with SO2 and restrain the formation of manganese sulfate. Compared with other catalytic systems,28–30 the poisoning resistance of the hollow MnOx@PrOx catalyst was relatively better than the other tested catalysts.
3.2 Structural characterization of catalysts
3.2.1 FE-SEM and TEM analysis. The morphology of the synthesized catalysts was characterized by FE-SEM (Fig. 3). Fig. 3a shows the uniform and smooth carbon spheres (CSs), which served as both the sacrificial templates and as reducing agents. After the oxidation–reduction reaction between the KMnO4 solution and CSs, MnOx particles were grown in situ on the CSs surface (Fig. 3b), and maintained their spherical structure. As shown in Fig. 3c, the hollow MnOx@PrOx catalyst was comprised of uniform spheres that were fully coated by the 1D nanosheets, and exhibited an urchin-like structure. The morphology of the hollow MnOx–PrOx was wrinkled when accompanied with combustion of CSs during calcination but almost retained its original morphology (Fig. 3d).
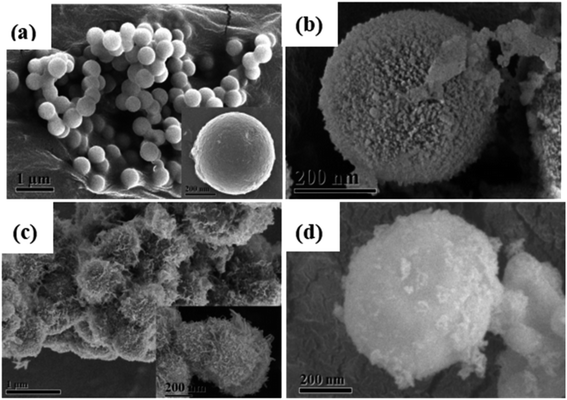 |
| Fig. 3 Low and high-magnification FE-SEM images of CSs (a); hollow MnOx (b); hollow MnOx@PrOx (c) and hollow MnOx–PrOx (d). | |
The structural information of the catalysts were further investigated by TEM and HRTEM (Fig. 4). Fig. 4a and d revealed that the hollow MnOx@PrOx catalyst exhibited an apparent interface between the hollow core and shell, indicating the typical features of a hollow core–shell architecture. The hollow core was about 40 nm in thickness with a 400 nm cavity and the nanosheet shell layer was about 60 nm in thickness. In addition, the TEM images of the hollow MnOx (Fig. 4c and f) and hollow MnOx–PrOx (Fig. 4g and h) displayed visibly hollow structures with shell layers of about 40 nm and 100 nm in thickness, respectively. The TEM images were in agreement with the FE-SEM images, and the d-spacing value was determined from the HR-TEM images and identified in the corresponding crystals. As shown in Fig. 4b and e, the highly crystalline lattice fringes with an inter-fringe spacing of 0.69 nm and 0.27 nm corresponded to the (110) plane of α-MnO2 (ref. 31) and the (222) plane of Mn2O3.32 Lattice fringes with a spacing of 0.28 nm, 0.38 nm and 0.31 nm were indexed to the Pr2O3 (402), (202) planes33,34 and the PrO2 (111) plane,35 respectively, indicating that the hollow MnOx nanospheres were coated by a shell of PrOx nanosheets. However, a hollow mixed oxide was observed in the hollow MnOx–PrOx (Fig. 4i). Ma et al.26 suggested that the homogeneous elemental distribution was favorable to the synergistic effects between elements, indicating that there existed intimate interactions between MnOx and PrOx.
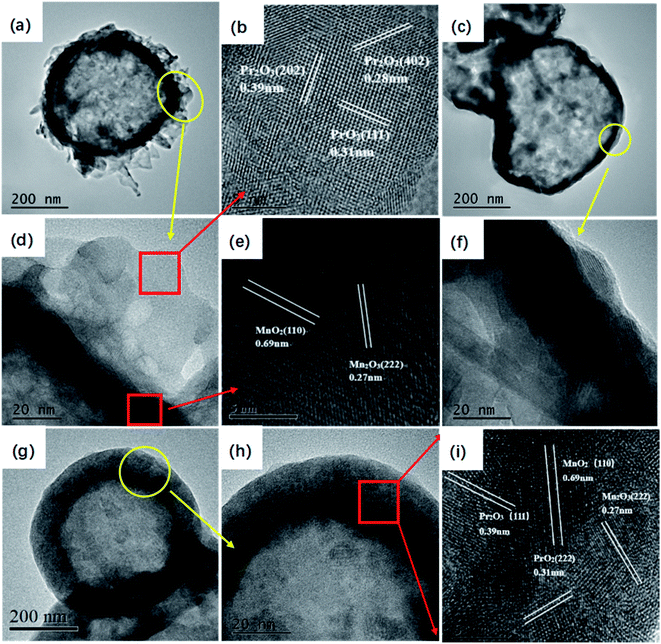 |
| Fig. 4 TEM and FE-TEM images with different magnifications of hollow MnOx@PrOx (a, b, d and e) and hollow MnOx (c and f) and hollow MnOx–PrOx (g–i). | |
The composition and distribution of the corresponding elements in the hollow MnOx@PrOx were evaluated by EDS and elemental mapping. EDS analysis in Fig. 5a shows that the hollow MnOx@PrOx was composed of Mn, Pr and O. In addition, the elemental map in Fig. 5b further revealed that each type of atom was uniformly distributed within the entire structure. The Pr species were located in the external layer of the hollow urchin-shaped structure, and the Mn species were observed in the interior layer. Also, the distribution range of the Pr was found to be the same as Mn, demonstrating that the PrOx uniformly covered the MnOx core. Based on the results above, it is reasonable to deduce that the core–shell structure catalyst could not only provide a relatively enclosed micro-environment to expose abundant active sites and enhance mass transfer, but the PrOx shell also protected the MnOx core from being poisoned. This contributed to an excellent SO2/H2O-tolerance of the hollow MnOx@PrOx catalyst.
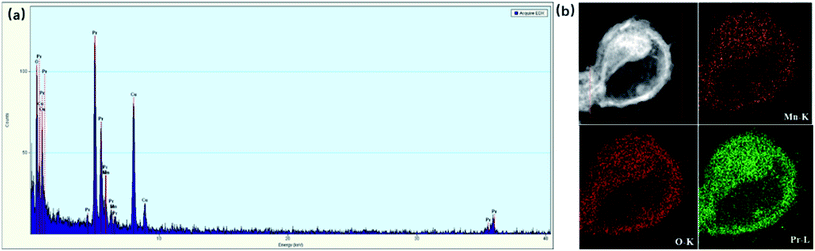 |
| Fig. 5 EDS spectra (a) and HAADF-STEM images (b) of an individual hollow MnOx@PrOx, and its element mapping of O, Mn and Pr. | |
3.2.2 XRD and BET analysis. XRD tests were carried out to determine the component and crystal phase structures of the catalysts. The crystalline structure of the active component plays an important role in its catalytic performance. Fig. 6 exhibits the typical XRD pattern of the catalysts including CSs, hollow MnOx and hollow MnOx@PrOx. For the CSs templates, only a distinct diffraction peak at 24° was detected, which was associated with the carbon material.36 Interestingly, no characteristic peaks of CSs were observed in the hollow MnOx, hollow MnOx@PrOx, or hollow MnOx–PrOx, suggesting that the sacrificial template of CSs was completely eliminated by heating at 400 °C. With regard to the hollow MnOx, the peaks at 2θ = 12.8°, 18.1°, 28.8°, 37.5°, 41.9°, 49.8°, 56.4°, 60.3°, and 69.7° were attributed to MnO2,37 while the peaks at 2θ = 32.9°, 55.2°, and 65.8° were assigned to Mn2O3.38 This phenomenon demonstrated the coexistence of different Mn species in the catalyst and that MnO2 was the main phase. After adding the Pr species, characteristic peaks at 2θ = 28.6°, 47.6° and 22.8°, 31.1°, 45.6° were observed for the hollow MnOx@PrOx and hollow MnOx–PrOx, which were related to the (110), (220) planes of PrO2 and the (202), (402), (503) planes of Pr2O3, respectively. The XRD results were also in agreement with the HRTEM images. Also, the diffraction peaks of both catalysts shifted slightly to higher angles, which was attributed to that the manganese ions (Mn4+ = 53 Å, Mn3+ = 64.5 Å, Mn2+ = 83 Å) being partly diffused into the PrOx (Pr4+ = 85 Å, Pr3+ = 99 Å) lattice during the heating process, which led to lattice shrinkage.29,30,39–41 Additionally, as compared with the hollow MnOx, the characteristic XRD peaks of the MnO2 and Mn2O3 were weaker and wider, which revealed that smaller mixed oxide particles with a lower degree of crystallization were formed. According to some reports,40,42,43 the decrease in crystallization degree led to increase of surface adsorbed oxygen, thus contributing to an improved SCR performance. The BET-specific surface areas of the catalysts were measured and are summarized in Table 1. It was reported that with a larger specific surface area and pore volume of the catalyst, the exposure of active sites increased and more reactants were absorbed on the surfaces.39 As can be seen from Table 1, after introducing Pr, the surface area and pore volume increased as follows: hollow MnOx@PrOx (195.31 m3 g−1, 0.36 cm3 g−1) > hollow MnOx–PrOx (185.39 m3 g−1, 0.31 cm3 g−1) > hollow MnOx (136.70 m3 g−1, 0.24 cm3 g−1). This indicated that more reactants were adsorbed on the core–shell structure hollow MnOx@PrOx catalyst leading to an increase in the SCR reactions.
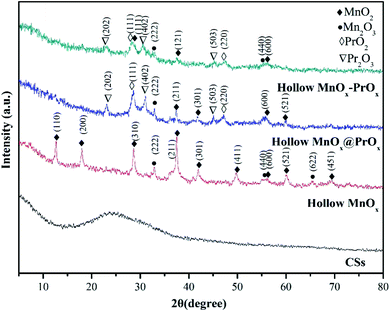 |
| Fig. 6 XRD patterns of CSs, hollow MnOx, hollow MnOx@PrOx and hollow MnOx–PrOx. | |
Table 1 BET surface area and surface atomic composition of the catalysts
Sample |
Surface atomic concentration (%) |
XMn/% |
XO/% |
XPr/% |
BET (m2 g−1) |
Pore volume (cm3 g−1) |
Mn |
O |
Pr |
Mn4+ |
Mn3+ |
Mn2+ |
Oα |
Oβ |
Pr4+ |
Pr3+ |
Hollow MnOx |
39.47 |
60.53 |
— |
49.01 |
37.02 |
13.97 |
83.05 |
16.95 |
— |
— |
136.70 |
0.24 |
Hollow MnOx@PrOx |
12.62 |
54.19 |
33.19 |
58.27 |
33.24 |
8.49 |
29.7 |
70.3 |
60.4 |
39.6 |
195.31 |
0.36 |
Hollow MnOx–PrOx |
34.58 |
50.19 |
15.23 |
51.1 |
37.3 |
11.6 |
57.36 |
42.64 |
66.4 |
33.6 |
185.39 |
0.31 |
3.2.3 XPS analysis. The surface properties of the catalysts also play an important role in the NH3-SCR reaction. Hence, the surface atom concentrations and states of the catalysts were determined by XPS (Fig. 7 and Table 1). The XPS spectrum of Mn 2p3/2 is shown in Fig. 7a and could be divided into three peaks: Mn2+ (640.2–640.8 eV), Mn3+ (641.2–641.5 eV) and Mn4+ (642.5–643.0 eV).44,45 The spectra of the hollow MnOx@PrOx and the hollow MnOx–PrOx were slightly shifted to lower binding energies. Similar results have been obtained by Ma et al.26 and Chang et al.,46 demonstrating that the chemical environment of Mn was different from the hollow MnOx, suggesting that there was an interaction between the MnOx species and the PrOx species given in the following reactions: |
Mn2O3 + 2PrO2 → 2MnO2 + Pr2O3;
| (2) |
|
Pr2O3 + 1/2O2 → 2PrO2.
| (3) |
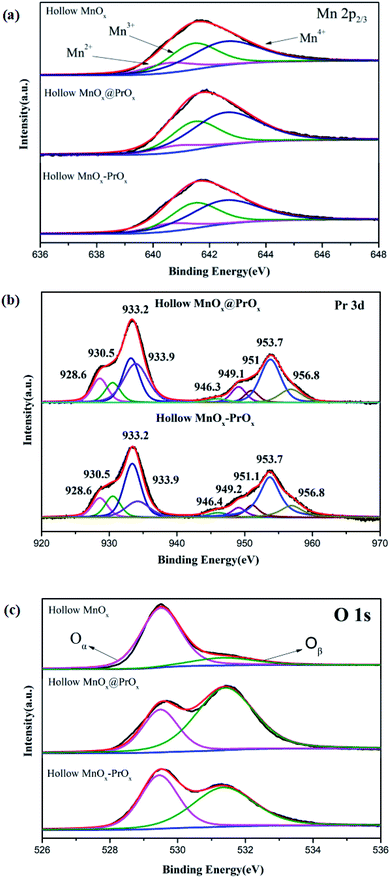 |
| Fig. 7 XPS spectra of Mn 2p2/3 (a), Pr 3d (b) and O 1s (c) of the catalysts. | |
As listed in Table 1, among the three catalysts, the hollow MnOx@PrOx possessed the highest surface molar concentration of Mn4+ (58.3%), indicating that the PrOx shell might have enriched the surface concentration of the Mn4+ species. It was confirmed that the Mn4+ species and their oxidation–reduction processes were in favor of the low-temperature NH3-SCR reaction.44,47–49 As a result, with more Mn4+ species, the low-temperature catalytic activity of the catalyst was enhanced. Furthermore, it was worth noting that the concentrations of Mn significantly decreased after the coating with a PrOx shell, which suggested that most of the Mn species were covered by PrOx. In other words, PrOx mainly deposited on the surface of catalyst, and the results were consistent with TEM.
The XPS spectrum of the Pr 3d reported in Fig. 7b shows two sets of spin–orbit multiples that were observed at binding energies of ca. 953.5 and 933.9 eV, which represented the 3d3/2 and 3d5/2 electrons of Pr, respectively.50 According to He et al.,51 the signals at ca. 928.6, 933.2, 946.3, and 951.1 eV were assigned to Pr3+, and the signals at ca. 930.5, 933.9, 949.2, 953.7, and 956.8 eV to Pr4+. The characteristic features of Pr4+ at 966–968 eV could not be resolved in the figure. As reported in other studies,52,53 this unique peak of Pr4+ usually appears after oxidation treatment (O2) of PrOx within the XPS reactor chamber. The Pr4+ ions were unstable and lose electrons easily, which facilitated the process of oxygen storage and release between Pr4+ and Pr3+ (2PrO2 → Pr2O3 + O*; Pr2O3 + 1/2O2 → 2PrO2).51,54 That is, the existence of Pr3+ in the PrOx implied the formation of an oxygen vacancy and the ratios of Pr3+/(Pr3+ + Pr4+) (39.6%) in the hollow MnOx@PrOx were higher than in the hollow MnOx–PrOx (33.6%). Therefore, it could be inferred that more oxygen vacancies were present in the hollow MnOx@PrOx than in the hollow MnOx–PrOx.
The O 1s XPS spectrum for the catalysts were also shown in Fig. 7c. The sub-band at 531.3–532.2 eV was attributed to the surface-adsorbed oxygen species (Oβ), and the sub-band at 529.2–530.0 eV was attributed to the lattice oxygen species (Oα).41 It is well known that Oβ is more active than Oα, therefore the higher mobility of the Oβ led to better performance in the oxidation reaction. An increase in the Oβ content promoted the oxidation of NO to NO2 and further enhanced the low-temperature NH3-SCR reaction through a fast pathway (4NH3 + 2NO + 2NO2 → 4N2 + 6H2O).55,56 From Table 1, the ratio of Oβ/(Oα + Oβ) in the hollow MnOx@PrOx (70.3%) was the highest of the three catalysts, which agrees with the XRD analysis, and could also explain the excellent low-temperature SCR activity of the hollow MnOx@PrOx catalyst.
3.2.4 NH3-TPD analysis. NH3-TPD was carried out to evaluate the amount of the acid sites and the acid strength of the prepared catalysts (Fig. 8 and Table 2). The TPD profile of the catalysts presented two broad desorption peaks in the temperature ranges of 100–300 °C and 400–700 °C. It was generally believed that the desorption peaks before 400 °C were ascribed to the weak adsorption of the NH3 at the Brønsted acid sites, while the desorption peaks above 400 °C were ascribed to the strong adsorption of the NH3 at the Lewis acid sites.57 Moreover, the positions of the desorption peaks were related to the acid strength and the areas of desorption peaks were related to the amount of acid sites.3 As shown in Fig. 8, all catalysts exhibited less Brønsted acid sites but much more Lewis acid sites. In addition, in the higher temperature range, the hollow MnOx@PrOx catalyst possessed the largest desorption area and the lowest desorption temperature at the Lewis acid sites, indicating that there was a sufficient number of Lewis acid sites with suitable acid strength on its surface. Studies show that the appropriate acid strength and number of sites are conducive to the adsorption-activation of NH3 on the catalyst surface.58 Moreover, the total number of acid sites for the catalysts were roughly calculated from the NH3-TPD, which was listed in Table 2. The acid strength sequence of the catalysts was: hollow MnOx@PrOx > hollow MnOx–PrOx > hollow MnOx. Based on the results, it was concluded that the hollow MnOx@PrOx catalyst contained a highly effective specific surface area due to its architecture, more acid sites could be exposed, and the catalyst exhibited enhanced adsorption ability of NH3, giving the same results as the BET analysis.
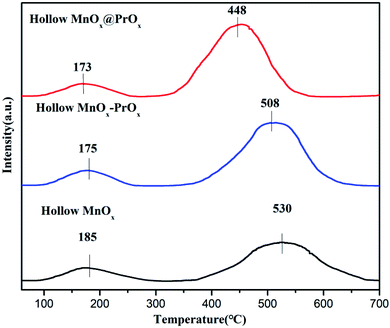 |
| Fig. 8 NH3-TPD profiles of the catalysts. | |
Table 2 The surface acidic properties of the catalysts
Sample |
Peak temperature (°C) |
Acid amount (mmol g−1) |
Total acid amount (mmol g−1) |
TI |
TII |
SI |
SII |
Hollow MnOx@PrOx |
173 |
448 |
0.141 |
1.345 |
1.486 |
Hollow MnOx–PrOx |
175 |
508 |
0.13 |
1.047 |
1.177 |
Hollow MnOx |
185 |
530 |
0.123 |
0.726 |
0.849 |
3.2.5 H2-TPR analysis. The H2-TPR test was performed to better understand the redox properties of the catalysts and the results were shown in Fig. 9. It was seen that the hollow MnOx exhibited two reduction peaks located at 356 and 488 °C, corresponding to the consecutive reduction processes of MnO2–Mn2O3 or Mn3O4–MnO.59–63 Three reduction peaks were observed for the hollow MnOx@PrOx and hollow MnOx–PrOx with the two peaks at higher temperatures coming from the conversion of Pr4+ to Pr3+, or the reduction reaction between Mn4+/Mn3+ and Pr4+/Pr3+.64 Specifically, the first two peaks were notably shifted to lower temperatures for both catalysts, indicating that the reduction capacity of the catalysts were improved and easier to reduce at low temperatures. In addition, the total consumption of H2 for the hollow MnOx@PrOx remarkably increased over the hollow MnOx, as illustrated in Table 3. This implied that the addition of PrOx generated more reducing agents on the catalyst surface, which is consistent with the XPS results showing a higher reducing ability. The increased reducibility of the hollow MnOx@PrOx over the hollow MnOx–PrOx catalysts further proved that the special core–shell structure of the catalyst was the main reason for the excellent reducibility.
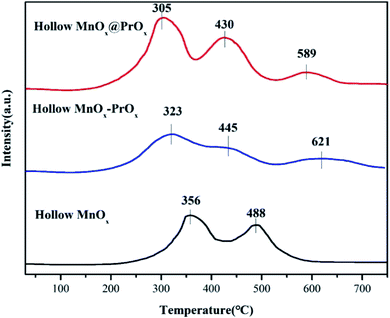 |
| Fig. 9 H2-TPR profiles of the catalysts. | |
Table 3 The reducibility of the catalysts
Sample |
Peak temperature (°C) |
H2 consumption (mmol g−1) |
Total H2 consumption (mmol g−1) |
TI |
TII |
TIII |
SI |
SII |
SIII |
Hollow MnOx@PrOx |
305 |
430 |
589 |
0.875 |
0.375 |
0.0838 |
1.3338 |
Hollow MnOx–PrOx |
323 |
445 |
621 |
0.6788 |
0.211 |
0.086 |
0.9758 |
Hollow MnOx |
356 |
488 |
— |
0.629 |
0.202 |
— |
0.831 |
4 Conclusion
In summary, we have successfully fabricated a hollow MnOx@PrOx core–shell nanohybrid as a high-performance low-temperature NH3-SCR de-NOx catalyst by using a facile two-step method. The hollow MnOx@PrOx nanohybrid displayed excellent low-temperature NH3-SCR activity with a maximum NO conversion of 99% at 120 °C with a space velocity of 40
000 h−1. It also maintained a NO conversion above 90% within the broad temperature window of 100–240 °C. This favorable catalytic behavior was mainly due to the abundant content of Mn4+ and Oβ species, uniform distribution of Mn and Pr species, and intimate interaction between MnOx and PrOx which brought about plentiful Lewis acid sites and excellent reducibility. Besides the excellent catalytic activity, the hollow MnOx@PrOx catalyst consistently exhibited superior SO2 and H2O tolerance, which could be attributed to the special core–shell structure of the catalyst. The protection from the PrOx shell minimized the exposure of the hollow MnOx core surface active sites to SO2 or H2O, resulting in high stability and an improved anti-poisoning performance.
Conflicts of interest
There are no conflicts to declare.
Acknowledgements
The project is financially supported by the National Natural Science Foundation of China (NSFC-51478191).
References
- T. Ryu, N. H. Ahn, S. Seo, J. Cho, H. Kim, D. Jo, G. T. Park, P. S. Kim, C. H. Kim, E. L. Bruce, P. A. Wright, I. S. Nam and S. B. Hong, Fully Copper-Exchanged High-Silica LTA Zeolites as Unrivaled Hydrothermally Stable NH3-SCR Catalysts, Angew. Chem., Int. Ed. Engl., 2017, 56, 3256–3260 CrossRef PubMed.
- Z. Sheng, D. Ma, D. Yu, X. Xiao, B. Huang, L. Yang and S. Wang, Synthesis of novel MnOx@TiO2 core-shell nanorod catalyst for low-temperature NH3-selective catalytic reduction of NOx with enhanced SO2 tolerance, Chin. J. Catal., 2018, 39, 821–830 CrossRef.
- B. Thirupathi and P. G. Smirniotis, Nickel-doped Mn/TiO2 as an efficient catalyst for the low-temperature SCR of NO with NH3: catalytic evaluation and characterizations, J. Catal., 2012, 288, 74–83 CrossRef.
- S. Li, B. Huang and C. Yu, A CeO2-MnOx core-shell catalyst for low-temperature NH3-SCR of NO, Catal. Commun., 2017, 98, 47–51 CrossRef.
- Y. Cao, D. Fan, L. Sun, M. Yang, L. Cao, T. Sun, S. Xu, P. Tian and Z. Liu, The self-protection effect of reactant gas on the moisture stability of CuSAPO-34 catalyst for NH3-SCR, Chem. Eng. J., 2019, 374, 832–839 CrossRef.
- H. I. Hamoud, V. Valtchev and M. Daturi, Selective catalytic reduction of NOx over Cu- and Fe-exchanged zeolites and their mechanical mixture, Appl. Catal., B, 2019, 250, 419–428 CrossRef.
- D. Wang, Y. Peng, Q. Yang, F. Hu, J. Li and J. Crittenden, NH3-SCR performance of WO3 blanketed CeO2 with different morphology: balance of surface reducibility and acidity, Catal. Today, 2019, 332, 42–48 CrossRef.
- L. Peng, Z. Li, J. Cui, C. Geng, Y. Kang, C. Zhang and C. Yang, N-doped graphene/CoFe2O4 catalysts for the selective catalytic reduction of NOx by NH3, RSC Adv., 2019, 9, 15791 RSC.
- N. Zhu, Z. Lian, Y. Zhang, W. Shan and H. He, Improvement of low-temperature catalytic activity over hierarchical Fe-beta catalysts for selective catalytic reduction of NO with NH3, Chin. Chem. Lett., 2019, 30, 867–870 CrossRef.
- S. Liu, H. Wang, Y. Wei, R. Zhang and S. Royer, Morphology-Oriented ZrO2-Supported Vanadium Oxide for the NH3-SCR Process: Importance of Structural and Textural Properties, ACS Appl. Mater. Interfaces, 2019, 11, 22240–22254 CrossRef PubMed.
- F. Wang, B. Shen, S. Zhu and Z. Wang, Promotion of Fe and Co doped Mn-Ce/TiO2 catalysts for low temperature NH3-SCR with SO2 tolerance, Fuel, 2019, 249, 54–60 CrossRef.
- H. Chang, J. Li, X. Chen, L. Ma, S. Yang, J. W. Schwank and J. Hao, Effect of Sn on MnOx–CeO2 catalyst for SCR of NOx by ammonia: enhancement of activity and remarkable resistance to SO2, Catal. Commun., 2012, 27, 54–57 CrossRef.
- A. Xie, Y. Tang, X. Huang, X. Jin, P. Gu, S. Luo, C. Yao and X. Li, Three-dimensional nanoflower MnCrO/sepiolite catalyst with increased SO2 resistance for NH3-SCR at low temperature, Chem. Eng. J., 2019, 370, 897–905 CrossRef.
- U. Hennings and R. Reimert, Investigation of the structure and the redox behavior of gadolinium doped ceria to select a suitable composition for use as catalyst support in the steam reforming of natural gas, Appl. Catal., A, 2007, 325, 41–49 CrossRef.
- B. Jiang, B. Deng, Z. Zhang, Z. Wu, X. Tang, S. Yao and H. Lu, Effect of Zr Addition on the Low-Temperature SCR Activity and SO2 Tolerance of Fe–Mn/Ti Catalysts, J. Phys. Chem. C, 2014, 118, 14866–14875 CrossRef.
- P. Maitarad, J. Han, D. Zhang, L. Shi, S. Namuangruk and T. Rungrotmongkol, Structure–Activity Relationships of NiO on CeO2 Nanorods for the Selective Catalytic Reduction of NO with NH3: Experimental and DFT Studies, J. Phys. Chem. C, 2014, 118, 9612–9620 CrossRef.
- L. Xiangwen, Z. Kebin, W. Lei, W. Baoyi and L. Yadong, Oxygen vacancy clusters promoting reducibility and activity of ceria nanorods, J. Am. Chem. Soc., 2009, 131, 3140–3141 CrossRef.
- Z. Yan, Y. Qu, L. Liu, X. Ge, J. Yang, L. Wei, T. Yang and X. Wang, Promotional effect of rare earth-doped manganese oxides supported on activated semi-coke for selective catalytic reduction of NO with NH3, Environ. Sci. Pollut. Res. Int., 2017, 24, 24473–24484 CrossRef.
- C. Yu, B. Huang, L. Dong, F. Chen, Y. Yang, Y. Fan, Y. Yang, X. Liu and X. Wang, Effect of Pr/Ce addition on the catalytic performance and SO2 resistance of highly dispersed MnOx/SAPO-34 catalyst for NH3-SCR at low temperature, Chem. Eng. J., 2017, 316, 1059–1068 CrossRef.
- R.-t. Guo, Q.-l. Chen, H.-l. Ding, Q.-s. Wang, W.-g. Pan, N.-z. Yang and C.-z. Lu, Preparation and characterization of CeOx@MnOx core–shell structure catalyst for catalytic oxidation of NO, Catal. Commun., 2015, 69, 165–169 CrossRef.
- X. W. Lou, L. A. Archer and Z. Yang, Hollow Micro-/Nanostructures: Synthesis and Applications, Adv. Mater., 2008, 20, 3987–4019 CrossRef.
- J. Yu, F. Guo, Y. Wang, J. Zhu, Y. Liu, F. Su, S. Gao and G. Xu, Sulfur poisoning resistant mesoporous Mn-base catalyst for low-temperature SCR of NO with NH3, Appl. Catal., B, 2010, 95, 160–168 CrossRef.
- S. Zhan, M. Qiu, S. Yang, D. Zhu, H. Yu and Y. Li, Facile preparation of MnO2 doped Fe2O3 hollow nanofibers for low temperature SCR of NO with NH3, J. Mater. Chem. A, 2014, 2, 20486–20493 RSC.
- L. Zhang, L. Shi, L. Huang, J. Zhang, R. Gao and D. Zhang, Rational Design of High-Performance DeNOx Catalysts Based on MnxCo3−xO4 Nanocages Derived from Metal–Organic Frameworks, ACS Catal., 2014, 4, 1753–1763 CrossRef.
- L. Han, M. Gao, J. Y. Hasegawa, S. Li, Y. Shen, H. Li, L. Shi and D. Zhang, SO2-Tolerant Selective Catalytic Reduction of NOx over Meso-TiO2@Fe2O3@Al2O3 Metal-Based Monolith Catalysts, Environ. Sci. Technol., 2019, 53, 6462–6473 CrossRef.
- K. Ma, W. Zou, L. Zhang, L. Li, S. Yu, C. Tang, F. Gao and L. Dong, Construction of hybrid multi-shell hollow structured CeO2–MnOx materials for selective catalytic reduction of NO with NH3, RSC Adv., 2017, 7, 5989–5999 RSC.
- X. Sun and Y. Li, Colloidal carbon spheres and their core/shell structures with noble-metal nanoparticles, Angew. Chem., Int. Ed. Engl., 2004, 43, 597–601 CrossRef.
- W. Li, C. Zhang, X. Li, P. Tan, A. Zhou, Q. Fang and G. Chen, Ho-modified Mn-Ce/TiO2 for low-temperature SCR of NO with NH3: evaluation and characterization, Chin. J. Catal., 2018, 39, 1653–1663 CrossRef.
- X. Yao, J. Cao, L. Chen, K. Kang, Y. Chen, M. Tian and F. Yang, Doping effect of cations (Zr4+, Al3+, and Si4+) on MnO/CeO2 nano-rod catalyst for NH3-SCR reaction at low temperature, Chin. J. Catal., 2019, 40, 733–743 CrossRef.
- X. Yao, L. Chen, J. Cao, Y. Chen, M. Tian, F. Yang, J. Sun, C. Tang and L. Dong, Enhancing the deNO performance of MnO/CeO2-ZrO2 nanorod catalyst for low-temperature NH3-SCR by TiO2 modification, Chem. Eng. J., 2019, 369, 46–56 CrossRef.
- S. Liang, F. Teng, G. Bulgan, R. Zong and Y. Zhu, Effect of Phase Structure of MnO2 Nanorod Catalyst on the Activity for CO Oxidation, J. Phys. Chem. C, 2010, 112, 5307–5315 CrossRef.
- J. Xu, Y. Sun, M. Lu, L. Wang, J. Zhang, J. Qian and E. J. Kim, Fabrication of porous Mn2O3 microsheet arrays on nickel foam as high-rate electrodes for supercapacitors, J. Alloys Compd., 2017, 717, 108–115 CrossRef.
- M. F. Gazulla, M. J. Ventura, C. Andreu, J. Gilabert, M. Orduña and M. Rodrigo, Praseodymium oxides. Complete characterization by determining oxygen content, Microchem. J., 2019, 148, 291–298 CrossRef.
- P. Monica and M. Kakihana, Praseodymium oxide formation by thermal decomposition of a praseodymium complex, Solid State Ionics, 2001, 141–142, 265–272 Search PubMed.
- B. Mutharani, P. Ranganathan, S. M. Chen and P. Sireesha, Ultrasound-induced radicals initiated the formation of inorganic-organic Pr2O3/polystyrene hybrid composite for electro-oxidative determination of chemotherapeutic drug methotrexate, Ultrason. Sonochem., 2019, 56, 410–421 CrossRef.
- H. Wang, Z. Zhang, C. Dong, G. Chen, Y. Wang and H. Guan, Carbon spheres@MnO2 core-shell nanocomposites with enhanced dielectric properties for electromagnetic shielding, Sci. Rep., 2017, 7, 15841 CrossRef.
- K. Lei, L. Cong, X. Fu, F. Cheng and J. Chen, Stirring-assisted hydrothermal synthesis of ultralong α-MnO2 nanowires for oxygen reduction reaction, Inorg. Chem. Front., 2016, 3, 928–933 RSC.
- Y.-C. Zhang, J.-T. Li, Z.-G. Wu, L. Huang and S.-G. Sun, Synthesis of hierarchical spindle-like Mn2O3 for lithium ion batteries with enhanced lithium storage properties, J. Alloys Compd., 2017, 721, 229–235 CrossRef.
- T. Du, H. Qu, Q. Liu, Q. Zhong and W. Ma, Synthesis, activity and hydrophobicity of Fe-ZSM-5@silicalite-1 for NH3-SCR, Chem. Eng. J., 2015, 262, 1199–1207 CrossRef.
- B. Shen, F. Wang and T. Liu, Homogeneous MnO–CeO2 pellets prepared by a one-step hydrolysis process for low-temperature NH3-SCR, Powder Technol., 2014, 253, 152–157 CrossRef.
- J. Wang, Z. Yan, L. Liu, Y. Zhang, Z. Zhang and X. Wang, Low-temperature SCR of NO with NH3 over activated semi-coke composite-supported rare earth oxides, Appl. Surf. Sci., 2014, 309, 1–10 CrossRef.
- F. Gao, X. Tang, H. Yi, J. Li, S. Zhao, J. Wang, C. Chu and C. Li, Promotional mechanisms of activity and SO2 tolerance of Co- or Ni-doped MnOx-CeO2 catalysts for SCR of NOx with NH3 at low temperature, Chem. Eng. J., 2017, 317, 20–31 CrossRef.
- Z. Liu, Y. Yi, S. Zhang, T. Zhu, J. Zhu and J. Wang, Selective catalytic reduction of NOx with NH3 over Mn-Ce mixed oxide catalyst at low temperatures, Catal. Today, 2013, 216, 76–81 CrossRef.
- Y. Su, B. Fan, L. Wang, Y. Liu, B. Huang, M. Fu, L. Chen and D. Ye, MnOx supported on carbon nanotubes by different methods for the SCR of NO with NH3, Catal. Today, 2013, 201, 115–121 CrossRef.
- L. Wang, B. Huang, Y. Su, G. Zhou, K. Wang, H. Luo and D. Ye, Manganese oxides supported on multi-walled carbon nanotubes for selective catalytic reduction of NO with NH3: catalytic activity and characterization, Chem. Eng. J., 2012, 192, 232–241 CrossRef CAS.
- H. Chang, T. Zhang, H. Dang, X. Chen, Y. You, J. W. Schwank and J. Li, Fe2O3@SiTi core–shell catalyst for the selective catalytic reduction of NOx with NH3: activity improvement and HCl tolerance, Catal. Sci. Technol., 2018, 8, 3313–3320 RSC.
- Y. Chao, L. X. H. BiChun and W. YouMing, Structural Properties and Low-Temperature SCR Activity of Zirconium-Modified MnOx/MWCNTs Catalysts, Acta Phys.-Chim. Sin., 2014, 30, 1895–1920 Search PubMed.
- X. Du, C. Li, L. Zhao, J. Zhang, L. Gao, J. Sheng, Y. Yi, J. Chen and G. Zeng, Promotional removal of HCHO from simulated flue gas over Mn-Fe oxides modified activated coke, Appl. Catal., B, 2018, 232, 37–48 CrossRef CAS.
- B. Zhao, H. Yi, X. Tang, Q. Li, D. Liu and F. Gao, Using CuO-MnOx/AC-H as catalyst for simultaneous removal of Hg degrees and NO from coal-fired flue gas, J. Hazard. Mater., 2019, 364, 700–709 CrossRef CAS.
- F. Liu, H. He, Y. Ding and C. Zhang, Effect of manganese substitution on the structure and activity of iron titanate catalyst for the selective catalytic reduction of NO with NH3, Appl. Catal., B, 2009, 93, 194–204 CrossRef CAS.
- H. He, H. X. Dai, K. W. Wong and C. T. Au, RE0.6Zr0.4−xYxO2 (RE = Ce, Pr; x = 0, 0.05) solid solutions: an investigation on defective structure, oxygen mobility, oxygen storage capacity, and redox properties, Appl. Catal., A, 2003, 251, 61–74 CrossRef CAS.
- C. K. Narula, L. P. Haack, W. Chun, H.-W. Jen and G. W. Graham, Single-Phase PrOy-ZrO2 Materials and Their Oxygen Storage Capacity: A Comparison with Single-Phase CeO2-ZrO2, PrOy-CeO2, and PrOy-CeO2-ZrO2 Materials, J. Phys. Chem. B, 1999, 103, 3634–3639 CrossRef CAS.
- E. Poggio-Fraccari, G. Baronetti and F. Mariño, Pr3+ surface fraction in CePr mixed oxides determined by XPS analysis, J. Electron Spectrosc. Relat. Phenom., 2018, 222, 1–4 CrossRef CAS.
- Z. Song, W. Liu, H. Nishiguchi, A. Takami, K. Nagaoka and Y. Takita, The Pr promotion effect on oxygen storage capacity of Ce–Pr oxides studied using a TAP reactor, Appl. Catal., A, 2007, 329, 86–92 CrossRef CAS.
- X. Lu, C. Song, S. Jia, Z. Tong, X. Tang and Y. Teng, Low-temperature selective catalytic reduction of NOx with NH3 over cerium and manganese oxides supported on TiO2–graphene, Chem. Eng. J., 2015, 260, 776–784 CrossRef CAS.
- L. Zhang, D. Zhang, J. Zhang, S. Cai, C. Fang, L. Huang, H. Li, R. Gao and L. Shi, Design of meso-TiO2@MnO(x)-CeO(x)/CNTs with a core-shell structure as DeNO(x) catalysts: promotion of activity, stability and SO2-tolerance, Nanoscale, 2013, 5, 9821–9829 RSC.
- Z. Fan, J.-W. Shi, C. Gao, G. Gao, B. Wang, Y. Wang, C. He and C. Niu, Gd-modified MnOx for the selective catalytic reduction of NO by NH3: the promoting effect of Gd on the catalytic performance and sulfur resistance, Chem. Eng. J., 2018, 348, 820–830 CrossRef CAS.
- Z. Ma, X. Wu, Y. Feng, Z. Si and D. Weng, Effects of WO3 doping on stability and N2O escape of MnOx–CeO2 mixed oxides
as a low-temperature SCR catalyst, Catal. Commun., 2015, 69, 188–192 CrossRef CAS.
- M. Richter, A. Trunschke, U. Bentrup, K. W. Brzezinka, E. Schreier, M. Schneider, M. M. Pohl and R. Fricke, Selective Catalytic Reduction of Nitric Oxide by Ammonia over Egg-Shell MnOx/NaY Composite Catalysts, J. Catal., 2002, 206, 98–113 CrossRef CAS.
- P. M. Sreekanth and P. G. Smirniotis, Selective Reduction of NO with CO Over Titania Supported Transition Metal Oxide Catalysts, Catal. Lett., 2007, 122, 37–42 CrossRef.
- X. Tang, Y. Li, X. Huang, Y. Xu, H. Zhu, J. Wang and W. Shen, MnOx–CeO2 mixed oxide catalysts for complete oxidation of formaldehyde: effect of preparation method and calcination temperature, Appl. Catal., B, 2006, 62, 265–273 CrossRef CAS.
- B. Thirupathi and P. G. Smirniotis, Effect of Nickel as Dopant in Mn/TiO2 Catalysts for the Low-Temperature Selective Reduction of NO with NH3, Catal. Lett., 2011, 141, 1399–1404 CrossRef CAS.
- J. Trawczyński, B. Bielak and W. Miśta, Oxidation of ethanol over supported manganese catalysts—effect of the carrier, Appl. Catal., B, 2005, 55, 277–285 CrossRef.
- V. Frizon, J.-M. Bassat, M. Pollet, E. Durand, J. Hernandez, K. Pajot, P. Vernoux and A. Demourgues, Tuning the Pr Valence State To Design High Oxygen Mobility, Redox and Transport Properties in the CeO2–ZrO2–PrOx Phase Diagram, J. Phys. Chem. C, 2019, 123, 6351–6362 CrossRef CAS.
|
This journal is © The Royal Society of Chemistry 2020 |
Click here to see how this site uses Cookies. View our privacy policy here.