DOI:
10.1039/C9RA10624C
(Paper)
RSC Adv., 2020,
10, 9341-9346
An electroless-plating-like solution approach for the preparation of PS@TiO2@Ag core–shell spheres
Received
17th December 2019
, Accepted 17th February 2020
First published on 4th March 2020
Abstract
PS@TiO2@Ag spheres with triple-level core–shell nanostructures were prepared via a versatile coating procedure based on an electroless-plating-like solution deposition (EPLSD) method. A peroxo-titanium-complex (PTC) aqueous solution was used as the precursor to react with an aniline monomer in the EPLSD preparation. Aniline plays an important role in the TiO2 layer anchoring process through the swollen effects of the PS cores. As extended, peroxo-metal-complex (PMC) with the d0 configuration can be introduced onto PS spheres to form varieties of PS@metal oxide core–shell structures by this method under mild conditions. Ag layers were then modified onto the PS@TiO2 spheres via the photocatalytic method. By the extraction of the PS cores, hollow TiO2 and TiO2@Ag spheres could be obtained. The photochemical degradation of methylene blue (MB) under UV light irradiation was performed on the composite nanostructures.
1. Introduction
Core–shell nanostructures are effective sources for the construction of many numerous advanced materials.1,2 Most of the shell materials can be substituted by inexpensive core species to reduce the consumption of the expensive shell materials. Among the core–shell nanostructures, titania (TiO2)–polystyrene (PS) composites are good templates to generate inorganic-coated polymer encapsulation, hollow spheres, or composite nanomaterials.3–5 Titania is very attractive owing to its high chemical and thermal stability, and excellent electronic and optical properties.6,7 The construction of TiO2 with core–shell structures is a promising strategy to tune its properties without its obvious side effects. Moreover, PS substrates can be easily prepared with narrow size distribution over a wide size range, which is an ideal substrate for TiO2 loading. A large number of synthetic strategies for core–shell materials based on TiO2–PS have been developed, which are mainly divided into two categories: top–down8,9 and bottom–up methods.10,11 Among these, the sol–gel method is highly versatile and does not require complicated operations and expensive instruments. Based on this method, great efforts have been made to develop titania shell coating procedures using aqueous solution media.12,13
However, the uniform deposition of crystalline TiO2 as thin layer shells in core–shell structures via a simple one-pot procedure is still a big challenge, which may be due to the low electronic negativity and high coordination numbers of titanium. Therefore, it is difficult to control the reaction kinetics of the heterogeneous nucleation for the shell TiO2 growth on the cores since the condensation and hydrolysis of titania precursors are rapid to control the coating processes via a sol–gel method.11 In this case, inhibitor agents are often used to slow down the rate of the condensation and hydrolysis of titania precursors.14 In addition, crystalline metal oxides (e.g., TiO2) formed by sol–gel routes typically require annealing steps at high temperatures, which may result in the destruction of the formed core–shell structures.
In practical applications, TiO2 suffers from poor visibility and IR absorption due to the large band gap (∼3.0 eV), which limits its efficiency for photocatalysis and energy conversion. The doping of metal species may modify the photochemical properties of TiO2. Hence, combining the TiO2–PS core–shell nanostructures with modified metals may generate new types of composites with enhanced photochemical activity, which can be used in photocatalysis, photothermal therapy, energy storage, or solar energy conversion. More importantly, metal or metal oxide-assisted TiO2 photocatalytic degradation is considered as an efficient method for the removal of organic wastes.15 This type of photocatalyst with hollow or porous structures can lower the diffusion resistance of reactants, thus boosting their diffusion as well as trapping the incident light for a long time to achieve high efficiency for photon utilization.
Herein, we have developed a versatile method to synthesize monodispersed PS@TiO2@Ag core–shell structures using the electroless-plating-like solution deposition (EPLSD) strategy, as shown in Scheme 1.16,17 Electroless plating is a non-galvanic method for simultaneous redox reactions between metal ions in aqueous solutions to form metal films at room temperature. In this preparation, PS cores are swollen-treated by aniline for the further modification of TiO2 shells. It is a novel strategy to prepare multi-level core–shell nanostructures where the in situ crystallization of oxides occurs at low temperatures. For example, other types of peroxo-metal-complex precursors using metal oxides with d0 configurations, such as peroxo-molybdenum-complex (PMC) or peroxo-vanadium-complex (PVC) can be used to replace peroxo-titanium-complex (PTC), forming the PS@MoO3@Ag or PS@V2O5@Ag nanocomposite structures. Moreover, the anchored Ag nanoparticles onto the metal oxide layer may also replace other metal shells by using other metal salt solutions, such as HAuCl4 or Cu(NO3)2 to form Au- or Cu-modified layers. In addition, hollow metal oxide spheres or metal(1) oxide@metal(2) spheres can further be obtained by the chemical extraction of the PS cores. The unique nanostructure can increase the surface area and provide more active sites for better electrolyte infiltration. Moreover, the void space in hollow nanostructures can serve as soft mediums for the adsorption of ions and shorten the ion transportation route.18 This method towards preparing multi-level PS@metal(1) oxide@metal(2) nanocomposites provides an alternative for the titania-based core–shell nanostructures, which is highly different from the Stöber-related coating procedure. In comparison with our previous studies, it is the first time that we construct the multi-layer structures via a one-pot procedure by the EPLSD method, where the in situ crystallization of metal oxides occurs at a low temperature.
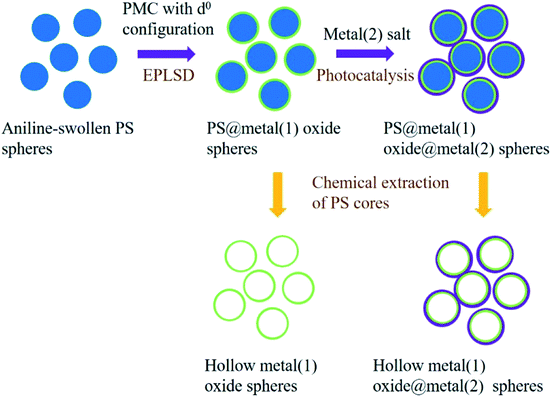 |
| Scheme 1 Illustration of the preparation of PS@metal(1) oxide@metal(2) nanocomposite with core–shell structures, and their relative hollow spheres. | |
2. Experimental
The synthesis procedure is illustrated in Scheme 1. First, PS spheres were prepared by a polymerization method via emulsifier-free emulsion. 180 mL of water and 9 g of styrene were added into a four-necked round flask (250 mL) and heated up to 70 °C. Before introducing the initiator, the mixture solution was purged with nitrogen to eliminate the inhibiting effects of oxygen, and then AIBA (2,2′-azobis[2-methylpropionamidine] dihydrochloride) dissolved in pure water (0.18 g 15 mL−1) was added into the solution. The polymerization was performed under nitrogen atmosphere protection with mechanical stirring for 24 h before cooling to room temperature, and the PS spheres were obtained.
Moreover, the peroxo-titanium-complex (PTC) precursor solution was prepared through TiCl4 which in turn was treated with ammonia to form titanic acid precipitates. The precipitate was dissolved in 30 wt% H2O2 solution, followed by diluting to M [Ti] = 0.125 mol L−1 to prepare the PTC precursor solution. Similarly, other peroxo-metal-complex (PMC, with d0-configured metals) precursor solutions can be prepared similar to the PTC precursor solution.
The PS@TiO2 nanostructures were prepared via the anchoring of the PTC precursor onto the aniline swollen-treated PS spheres. Aniline was added into water (15 mL) at 0 °C through an ultrasonic treatment for 15 min, followed by the introduction of the as-prepared PS (1.2 g). The mixture was stirred for 30 min at 0 °C to anchor aniline molecules onto the PS seed surface through a swelling process. Then, the dispersion of the PS particles swollen with aniline was transferred into a three-necked round bottom flask placed in an ice bath, and the PTC aqueous solution was then added into the dispersion with a PTC/aniline molar ratio of a 2
:
1. Then, the TiO2 shell was formed on the PS core surface at 80 °C via the EPLSD process for 30 min. Similarly, other types of metal (with the d0 configuration) oxide shells via the EPLSD process can be obtained with their corresponding precursors (PMC). Finally, Ag nanocrystals (NCs) were modified onto the PS@TiO2 spheres using the AgNO3 solution by a UV photocatalytic (254 nm ultraviolet irradiation) method to form the PS@TiO2@Ag core–shell nanostructures.
The surface morphologies of the samples were examined via field-emission scanning electron microscopy (FE-SEM, JSM-7500F, JEOL, Japan). X-ray diffraction (XRD) experiments were performed using an XD-2 diffractometer (Purkinje General Instrument Co. Ltd.) with Cu Kα radiation at 36 kV and 30 mA. The transmission electron microscopy (TEM, Tecnai G2 F20, FEI, USA) was performed at an operating voltage at 100 kV to observe the microstructure of the samples. Energy dispersive X-ray spectroscopy (EDS) analysis was performed to characterize the element type and content.
The photocatalytic performance towards the methylene blue (MB) degradation was performed under UV irradiation (365 nm) in an aqueous solution (20 mg mL−1, 50 mL) using the composites as the photocatalysts (0.1 mg mL−1). The suspension was magnetically stirred at room temperature. At last, 3 mL of the solution was taken out as the sample. After centrifugation to remove the solid residues, the sample was analyzed via UV-vis spectroscopy. After each degradation experiment, the nanocomposites were separated and soaked in HCl solution (1 M, 50 mL) for 1 h, rinsed and dried under UV irradiation, and then were reused for the next test.
3. Results and discussion
3.1. PTC effect
It is difficult for the TiO2 shells to grow on bare PS substrate without proper pretreatments.19,20 In this preparation, PTC with d0-configured titanium is employed as the titania precursor instead of the widely used tetrabutyltitanate (TBOT).15 Another difference from other preparations is the use of aniline to swell the PS spheres. By controlling the redox reaction between the PTC precursor and aniline that is swollen into PS cores, preferential heterogeneous nucleation and growth of crystalline TiO2 shells on the core surface can be easily realized without an additional calcination process.21 The role of aniline on surface modification is very important in the preparation process.
The nanosized charge-stabilized PS seed latex was readily formed in the emulsifier-free emulsion polymerization and could be further used without any post-treatment. Upon mixing the yellow oil droplets of aniline with the as-prepared PS cores, the added aniline monomer was distributed between the organic species and aqueous phase. Aniline is an ideal solvent for PS, but its aqueous solubility is limited. Therefore, aniline molecules are absorbed into the PS beads after a certain period of stirring with ultrasonic assistance, forming aniline-swollen PS particles that are highly dispersed. As shown in Fig. 1(a), the as-prepared PS cores have a diameter of around 380 nm. After the treatment of the PS spheres with aniline, the PTC solution was subsequently added into the solution of aniline-swollen PS spheres at 80 °C for 30 min through the EPLSD procedure, forming the PS@TiO2 core–shell nanostructure. As shown in Fig. 1(b), the as-prepared PS@TiO2 composite spheres have the same spherical shape but rougher surface in comparison with the PS seed spheres. High-resolution TEM (HRTEM) image (Fig. 1(c)) reveals that a well-crystallized TiO2 shell with a 4 nm thickness was formed on the sphere surface. The (101) facet of anatase TiO2 with a 0.35 nm spacing was identified. As shown in Fig. 1(d), only a small amount of TiO2 nanoparticles obtained through the heterogeneous nucleation growth are randomly distributed on the untreated PS spherical surface instead of the aniline-swollen PS in the EPLSD process, revealing that the aniline treatment is a key factor in the EPLSD preparation. As reported in our previous study, the EPLSD procedure is highly dependent on a redox reaction between PTC and aniline, in which PTC is reduced to TiO2, and the aniline is polymerized to polyaniline as oxide. Therefore, the TiO2-shell coating can be formed on aniline-swollen PS spheres via the EPLSD process, while bare PS species can hardly anchor the TiO2 nanoparticles obtained via the decomposition of PTC precursors.
 |
| Fig. 1 TEM images of (a) PS cores, (b) PS@TiO2 spheres prepared by PTC coating on aniline swollen PS cores, (c) HRTEM analysis on the PS@TiO2 particle surface, (d) effect of PTC coating on untreated PS cores. | |
3.2. SEM and XRD characterizations
In our previous studies, by using the EPLSD method, flexible films modified by metal oxides were successfully fabricated,17,21 and polyaniline/titania nanocomposites with porous networks were obtained.16 In this study, we extended the EPLSD method to construct multi-layer spheres with different types of materials. Through SEM observation, the obtained PS spheres have a narrow size distribution, as shown in Fig. 2(a). Their average diameter is about 380 nm. After covering with TiO2 layers, the sphere surface turned from smooth to rough, as compared in Fig. 2(a) and (b). The in situ UV photocatalytic deposition of Ag nanoparticles on the titania layer to generate the PS@TiO2@Ag nanostructure is based on the charge transfer (CT) from TiO2 to the adsorbed metal particles.22,23 After the further deposition of Ag layers onto the PS@TiO2 surface, a rather rough surface on the Ag-modified spheres is observed (Fig. 2(c)), which may be caused by a different photocatalytic redox efficiency on different anatase facets.24,25 The element analysis revealed the presence of C, N, O, and Ti elements in the PS@TiO2 (Fig. 2(d)), and the presence of C, N, O, Ti, and Ag elements in the PS@TiO2@Ag (Fig. 2(d)) material, which confirms that the shell species are successfully uploaded onto the previous cores. The chemical components in the core–shell nanostructures were further characterized via X-ray diffraction (XRD), as shown in Fig. 2(f), which confirms the presence of anatase TiO2 formed in the crystalline phase (JCPDS: 02-0406). In addition, three types of PS@TiO2@metal (Au, Ag, and Cu) nanocomposites prepared by the EPLSD method were measured for comparison. The diffraction peaks are identified as TiO2 (101) 25.5°, Ag (111) 38.1°, Au (111) 38.3°, and Cu (200) 50.1°, respectively.
 |
| Fig. 2 SEM images of (a) PS spheres, (b) PS@TiO2 spheres, (c) PS@TiO2@Ag spheres; and EDS of (d) PS@TiO2 spheres, (e) PS@TiO2@Ag spheres; and (f) XRD patterns of PS@TiO2@metal (Au, Ag, Cu) nanocomposites. | |
3.3. TiO2 layer effect
It is well known that the charge transfer (CT) from TiO2 to the adsorbed molecules can be used for the photocatalytic deposition of metal nanocrystals (NCs) on titania.26 Fig. 3(a) indicates that the sphere surface was successfully decorated with Ag NCs. The PS@TiO2@Ag core–shell spheres have a slightly rough surface, as shown in Fig. 3(b), which is different from that of the PS@TiO2 spheres. The HRTEM image (Fig. 3(c)) on the sphere surface shows the crystalline structure and the distance between two adjacent lattice planes is about 0.23 nm, which is in agreement with the lattice spacing of the Ag (111) facets. The average thickness of the Ag layers is estimated to about 4 nm. As compared, if only the PS spheres are used as the cores without TiO2 layers, only a few Ag nanoparticles (NPs) are separately absorbed onto the PS surface (Fig. 3(d)) in the photocatalytic deposition process, indicating that the TiO2 intermediate layer plays an important role in the metal layer modification.
 |
| Fig. 3 TEM images of (a) PS@TiO2@Ag spheres, (b) magnified TEM image of an individual PS@TiO2@Ag sphere at the surface, (c) HRTEM image for the surface layer analysis, (d) TEM image of the effects of the photocatalytic deposition of Ag NCs on PS spheres without TiO2 layers. | |
3.4. Hollow spheres
Hollow structures provide high cycling performance, specific active area, and superior rate capability.27 The PS core extraction was performed to obtain hollow TiO2 and hollow TiO2@Ag nanostructures. TEM images which are shown in Fig. 4(a) and (b) demonstrate the TiO2 and TiO2@Ag residues as hollow spheres after immersing the PS@TiO2 and PS@TiO2@Ag spheres in tetrahydrofuran overnight, respectively. After the extraction treatment, the remained shells are clearly seen. Some Ag NCs with lager size are clearly seen on the surface of the hollow TiO2@Ag spheres (indicated by the arrows in Fig. 4(b)). The average size of the Ag NCs is about 2–4 nm evaluated from the observation.
 |
| Fig. 4 (a) Remaining TiO2 and (b) TiO2@Ag residue spheres after the tetrahydrofuran extraction of the PS cores from the composite spheres. | |
3.5. Degradation test
The multi-layer phase of this kind of nanocomposite is a highly desirable structure for high-performance photocatalysis. MB in an aqueous solution was used as a model target to test the photocatalytic activity of the nanocomposites, and the results are compared in Fig. 5(a). It was found that about 86.1% and 88.2% of MB could be degraded after 120 min on the hollow TiO2@Ag and PS@TiO2@Ag spheres, respectively, suggesting a better photocatalytic property of the core–shell nanostructure due to the synergic effects of TiO2 and Ag shells. Ag NCs compacted with the TiO2 layers could enhance their practical potential in harsh environments. It is considered that Ag NCs confined in a core–shell hollow TiO2 photocatalyst may exhibit photocatalytic activity under solar light irradiation.15 In addition, the multiple light reflection and scattering from the mixing phases of Ag and TiO2 are other crucial factors of the photocatalytic activity.28,29 The influence of Ag in the nanocomposites on the photocatalytic degradation was also evaluated. As shown in Fig. 5(a), the photoactivity of the PS@TiO2 sphere alone is not ideal in comparison with that of Ag-modified ones. Moreover, the stability of the composites was examined in the degradation for five repeated cycles, and the results indicated favorable stability of this core–shell nanostructure (Fig. 5(b)). In comparison with the TiO2 single shell, this kind of composite photocatalyst can use the anchored Ag layer as the electron transfer channel and reservoir, thus improving the lifetime of the photogenerated charge pairs. Further progress on this kind of hollow spheres is currently under investigation for optimally photocatalytic applications.
 |
| Fig. 5 (a) Photocatalytic degradation of MB in an aqueous solution under UV light (365 nm) on PS spheres, PS@TiO2 spheres, PS@TiO2@Ag nanocomposites, and hollow TiO2@Ag spheres; (b) cycling test for MB degradation on hollow TiO2@Ag and PS@TiO2@Ag nanocomposites (blue triangle: PS@TiO2@Ag, red circle: hollow TiO2@Ag). | |
4. Conclusions
A facile method to prepare PS@TiO2@Ag core–shell nanostructures using an EPLSD strategy has been developed. By the careful regulation of the redox reaction between the PTC precursors and aniline, the heterogeneous nucleation and growth of crystalline TiO2 shells on the PS cores could be achieved under mild conditions. Other types of metal oxide shells for core–shell nanostructures via the EPLSD process could be obtained with their corresponding PMC precursors. Furthermore, PS@metal(1) oxide@metal(2) composite spheres could be alternatively obtained via the photocatalytic deposition of metal(2) NC layers onto PS@metal(1) oxide previously prepared by PMC precursors and PS cores based on the CT mechanism. Moreover, hollow TiO2 or TiO2@Ag nanocomposite spheres were obtained by the chemical extraction of the PS cores. The photocatalytic degradation of MB by the PS@TiO2@Ag spheres and hollow TiO2@Ag demonstrates the desirable photoactivity of the nanostructures. Our study overcomes the disadvantages of numerous TiO2-based photocatalysts for unideal degradation efficiency.
Conflicts of interest
The authors declare no competing financial interest.
Acknowledgements
We acknowledge the Basic Research Funding for Breeding Project of Sichuan University (2019-21), the Fundamental Research Funds for the Central Universities (20826041C4202), and the funding from Science & Technology Department of Sichuan Province (2017JY0270). We thank Engineer Yi He's operation on the SEM imaging and Dr Jiqiu Wen's help of XRD measurements from Analytical & Testing Center of Sichuan University.
Notes and references
- O. D. Velev, T. A. Jede, R. F. Lobo and A. M. Lenhoff, Nature, 1997, 389, 447–448 CrossRef CAS.
- H. Y. Hu, Y. Lin and Y. H. Hu, Chem. Eng. J., 2019, 375, 122029 CrossRef CAS.
- J. Shao, W. C. Sheng, M. S. Wang, S. J. Li, J. R. Chen, Y. Zhang and S. S. Cao, Appl. Catal., B, 2017, 209, 311–319 CrossRef CAS.
- J. Q. Zhang and L. Zhang, ACS Appl. Nano Mater., 2019, 2, 6368–6377 CrossRef CAS.
- F. Z. Shi, Y. G. Li, H. Z. Wang and Q. H. Zhang, Appl. Catal., B, 2012, 123–124, 127–133 CrossRef CAS.
- X. B. Chen and S. S. Mao, Chem. Rev., 2007, 107, 2891–2959 CrossRef CAS PubMed.
- D. B. Luo, B. S. Liu, A. Fujishima and K. Nakata, ACS Appl. Nano Mater., 2019, 2, 3943–3950 CrossRef CAS.
- H. Li, R. M. Vilar and Y. M. Wang, J. Mater. Sci., 1997, 32, 5545–5550 CrossRef.
- A. C. Dodd, Powder Technol., 2009, 196, 30–35 CrossRef CAS.
- R. G. Chaudhuri and S. Paria, Chem. Rev., 2012, 112, 2373–2433 CrossRef PubMed.
- Y. Bao, Q. L. Kang, C. Liu and J. Z. Ma, Mater. Lett., 2018, 214, 272–275 CrossRef CAS.
- W. Li, J. P. Yang, Z. X. Wu, J. X. Wang, B. Li, S. S. Feng, Y. H. Deng, F. Zhang and D. Y. Zhao, J. Am. Chem. Soc., 2012, 134, 11864–11867 CrossRef CAS PubMed.
- J. S. Chen, C. P. Chen, J. Liu, R. Xu, S. Z. Qiao and X. W. Lou, Chem. Commun., 2011, 47, 2631–2633 RSC.
- Z. L. He, W. X. Que and Y. C. He, Mater. Lett., 2013, 94, 136–139 CrossRef CAS.
- S. D. Zhao, J. R. Chen, Y. F. Liu, Y. Jiang, C. G. Jiang, Z. L. Yin and Y. G. Xiao, Chem. Eng. J., 2019, 367, 249–259 CrossRef CAS.
- Y. Z. Li, Y. Yu, L. Z. Wu and J. F. Zhi, Appl. Surf. Sci., 2013, 273, 135–143 CrossRef CAS.
- L. Z. Wu, Y. Yu, X. Y. Han, Y. Zhang, Y. Zhang, Y. Z. Li and J. F. Zhi, J. Mater. Chem. C, 2014, 2, 2266–2271 RSC.
- Y. Zhang, Y. Zhao, S. S. Cao, Z. L. Yin, L. Cheng and L. M. Wu, ACS Appl. Mater. Interfaces, 2017, 9, 29982–29991 CrossRef CAS PubMed.
- A. Dutschke, C. Diegelmann and P. Löbmann, Chem. Mater., 2003, 15, 3501–3506 CrossRef CAS.
- L. Z. Wu, Y. Yu, L. Song and J. F. Zhi, J. Colloid Interface Sci., 2015, 446, 213–217 CrossRef CAS PubMed.
- L. Z. Wu, Y. Yu and J. F. Zhi, RSC Adv., 2015, 5, 10159–10164 RSC.
- L. B. Yang, X. Jiang, W. D. Ruan, B. Zhao, W. Q. Xu and J. R. Lombardi, J. Phys. Chem. C, 2008, 112, 20095–20098 CrossRef CAS.
- M. Liu, L. Y. Piao, L. Zhao, S. T. Ju, Z. J. Yan, T. He, C. L. Zhou and W. J. Wang, Chem. Commun., 2010, 46, 1664–1666 RSC.
- L. C. Liu, X. R. Gu, Z. Y. Ji, W. X. Zou, C. J. Tang, F. Gao and L. Dong, J. Phys. Chem. C, 2013, 117, 18578–18587 CrossRef CAS.
- D. W. Li, L. J. Pan, S. Li, K. Liu, S. F. Wu and W. Peng, J. Phys. Chem. C, 2013, 117, 6861–6871 CrossRef CAS.
- K. Tanaka, K. Harada and S. Murata, Sol. Energy, 1985, 36, 159–161 CrossRef.
- Z. Y. Wang, L. Zhou and X. W. Lou, Adv. Mater., 2012, 24, 1903–1911 CrossRef CAS PubMed.
- P. A. Gross, S. N. Pronkin, T. Cottineau, N. Keller, V. Keller and E. R. Savinova, Catal. Today, 2012, 189, 93–100 CrossRef CAS.
- A. Takai and P. V. Kamat, ACS Nano, 2011, 5, 7369–7376 CrossRef CAS PubMed.
Footnote |
† The authors contributed equally to this work. |
|
This journal is © The Royal Society of Chemistry 2020 |
Click here to see how this site uses Cookies. View our privacy policy here.