DOI:
10.1039/C9RA10618A
(Paper)
RSC Adv., 2020,
10, 6452-6459
Catalysis with magnetically retrievable and recyclable nanoparticles layered with Pd(0) for C–C/C–O coupling in water†
Received
17th December 2019
, Accepted 27th January 2020
First published on 11th February 2020
Abstract
Nanoparticles layered with palladium(0) were prepared from nano-sized magnetic Fe3O4 by coating it with silica and then reacting sequentially with phenylselenyl chloride under an N2 atmosphere and palladium(II) chloride in water. The resulting Fe3O4@SiO2@SePh@Pd(0) NPs are magnetically retrievable and the first example of NPs in which the outermost layer of Pd(0) is mainly held by selenium. The weight percentage of Pd in the NPs was found to be 1.96 by ICP-AES. The NPs were authenticated via TEM, SEM-EDX, XPS, and powder XRD and found to be efficient as catalysts for the C–O and C–C (Suzuki–Miyaura) coupling reactions of ArBr/Cl in water. The oxidation state of Pd in the NPs having size distribution from ∼12 to 18 nm was inferred as zero by XPS. They can be recycled more than seven times. The main features of the proposed protocols are their mild reaction conditions, simplicity, and efficiency as the catalyst can be separated easily from the reaction mixture by an external magnet and reused for a new reaction cycle. The optimum loading (in mol% of Pd) was found to be 0.1–1.0 and 0.01–1.0 for O-arylation and Suzuki–Miyaura coupling, respectively. For ArCl, the required amount of NPs was more as compared to that needed for ArBr. The nature of catalysis is largely heterogeneous.
Introduction
NPs having a magnetic core can be easily separated from the reaction mixture by using an external magnet. This makes materials like Fe3O4 a promising support for nano-catalysts as easy separation improves their reusability.1 Nano-catalysts have a high specific surface area-to-volume ratio. Thus, more reactant molecules undergo association with the catalyst, enhancing the catalytic efficiency.2 However, the high surface energy of a nano-catalyst can make it unstable and sometimes it causes agglomeration. On supporting the catalytic species on magnetic nanoparticles, agglomeration is prevented along with the significant advantage of recyclability, resulting from easy separation.3,4 Magnetically separable nano-catalysts have been designed successfully by the grafting methodology and used in metal-catalyzed organic reactions,5 organo-catalysis and enzymatic catalysis.6 Fe3O4 is a robust, low-cost, chemically stable, and readily available material of low toxicity. Therefore, it is suitable for designing magnetically retrievable NPs. The easy functionalization of Fe3O4 makes it a better alternative to other heterogeneous supports, viz., silica, graphene, and alumina. After completion of the reaction, the magnetic NPs can be easily removed from the mixture with the help of an external magnet.7,8 The functionalization of magnetic Fe3O4 with diverse functional groups, chemical entities, metal complexes, and NPs has led to efficient catalytic systems for a wide range of organic reactions.5,6,9 The metal complexes of organochalcogen ligands have emerged as promising single-source precursors for the synthesis of metal chalcogenide NPs and catalysts for various chemical transformations.10 Metal chalcogenide NPs supported on solids have been found to be efficient for catalyzing the organic reactions.11 Ru(OH)x NPs supported on selenium–silica coated Fe3O4 have been reported recently as efficient catalysts for amide synthesis.12 Encouraged by the catalytic potential of these metal chalcogenides, we have designed Fe3O4@SiO2@SePh@Pd(0) and investigated its catalytic activities for the C–C (Suzuki–Miyaura) and C–O coupling reactions. The NPs catalyze the reactions efficiently in water. The magnetic nanoparticles also often show a strong tendency to agglomerate as a result of self-interactions and hence, suitable protecting agents are used for stabilizing them. Therefore, Fe3O4 is coated with SiO2 in the present case.13
Diaryl ether linkage is an important component of various polymers, agrochemicals, and pharmaceuticals.14 Several antibiotics and biologically active natural products like thyroxine (a mammalian hormone) have diaryl ether linkage.15 Palladium17 and copper16 are among the important metal catalysts for the O-arylation reaction. The research groups of Hartwig and Buchwald have contributed immensely in this area.18 In most of the cases, a ligand is used with a metal salt to catalyze the reaction. There is also a report on a ligand-free catalytic system.19 However, recyclable catalytic systems applicable under mild reaction conditions in water are rarely reported.13
Suzuki–Miyaura coupling is an important C–C coupling reaction,20 affording biaryls, building blocks of natural products,21 agrochemicals, and pharmaceutical ingredients. The palladium complexes of phosphines,22,23 carbenes,24 palladacycles,25 and organochalcogen ligands26 are reported as efficient homogeneous catalysts for this coupling. Several of the catalytic systems known for this coupling reaction are air- and moisture-sensitive and for a good yield, an inert atmosphere is a necessity.27 Heterogeneous catalytic systems are also known28–30 for the coupling reactions as well as other organic transformations. Among them, some are air- and moisture-sensitive and require an inert atmosphere.29b Furthermore, with most of the catalysts reported for coupling and other organic reactions, an organic solvent is necessary to achieve a good yield.29e,30 Water, being environment-friendly, economical, non-toxic, non-flammable, cheap, and readily available,31 is of enormous interest as a solvent for catalytic reactions. Many reactions in an aqueous medium reported in the literature were performed at a high temperature and/or in the presence of a co-solvent to get a good yield of the product.30g–k Herein, we report the Fe3O4@SiO2@SePh@Pd(0) nanoparticle (NP)-catalyzed Suzuki–Miyaura coupling and O-arylation of phenol in pure water at a moderate temperature of 80 °C.
Results and discussion
The preparation of Fe3O4@SiO2@SePh@Pd(0) NPs is summarized in Scheme 1. Fe3O4 prepared using a recently reported protocol12 was coated with silica and treated in an aqueous medium under an N2 atmosphere with phenylselenyl chloride and PdCl2 successively. Magnetic Fe3O4@SiO2@SePh@Pd(0) NPs were separated using an external magnet, washed with water followed by Et2O, and dried in vacuo at 60 °C for 2 h. Neither Fe3O4@SiO2@SePh@Pd(0) NPs nor their precursor was found to be soluble in water or the organic solvent. The weight percentage of Pd in Fe3O4@SiO2@SePh@Pd(0) NPs was determined to be 1.96% with ICP-AES. TEM, SEM-EDX, and powder X-ray diffraction (PXRD) (Fig. 1) were used to authenticate the NPs as Fe3O4@SiO2@SePh@Pd(0). They appeared to have irregular cubic morphology.
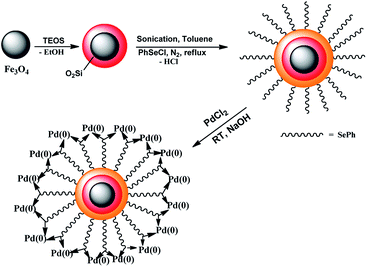 |
| Scheme 1 The synthesis of Fe3O4@SiO2@SePh@Pd(0) NPs. | |
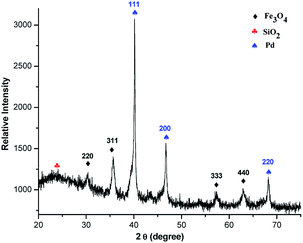 |
| Fig. 1 PXRD of Fe3O4@SiO2@SePh@Pd(0) NPs. | |
Powder XRD and XPS of Fe3O4@SiO2@SePh@Pd(0) NPs
The PXRD pattern12 of Fe3O4 exhibits peaks (hkl) at 220, 311, 333, and 440. They can be well indexed to the cubic phase of Fe3O4 and are in good agreement with the literature results (JCPDS 82-1533). The silica-coated NPs (Fe3O4@SiO2) show a broader PXRD pattern12 at 2θ = 20 to 29° (JCPDS 83-2470) due to their non-crystalline nature. Their peaks (hkl) at 220, 311, 333, and 440 correspond to the Fe3O4 core. After the immobilization of selenium-containing species (SePh) onto Fe3O4@SiO2, additional peaks due to Se appear in the PXRD pattern of Fe3O4@SiO2@SePh along with the peaks of Fe3O4@SiO2.12 On layering Fe3O4@SiO2@SePh with Pd, the dispersity of Se increases as it becomes a part of the metal's coordination sphere. Thus, peaks corresponding to Se were not detected in the PXRD pattern of Fe3O4@SiO2@SePh@Pd(0) (Fig. 1). Palladium coordinated with Se and the binding of Pd with selenium donor sites was expected to be strong. The PXRD pattern of Fe3O4@SiO2@SePh@Pd(0) exhibits peaks (hkl) at 111, 200, and 220, corresponding to Pd(0) NPs (JCPDS 87-0643). No peak indicating any impurity was noticed, thereby authenticating the purity of Fe3O4@SiO2@SePh@Pd(0) NPs.
The zero oxidation state of Pd in Fe3O4@SiO2@SePh@Pd(0) was established by the X-ray photoelectron spectra, as shown in Fig. 2. The binding energies of the 3d5/2 and 3d3/2 states of Pd were found to be 335.8 and 341.2 eV, respectively, which were consistent with its zero oxidation state, thereby indicating the complete reduction of Pd(II) to Pd(0).32
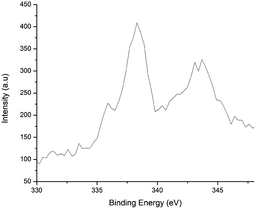 |
| Fig. 2 The XPS spectra of Fe3O4@SiO2@SePh@Pd(0) NPs. | |
TEM and SEM-EDX of Fe3O4@SiO2@SePh@Pd(0) NPs
The transmission electron microscopy (TEM) images of Fe3O4@SiO2@SePh@Pd(0) NPs are shown in Fig. 3. The SEM-EDX spectrum (Fig. S2 in the ESI†) supports the presence of iron, oxygen, silicon, selenium, carbon, and palladium in Fe3O4@SiO2@SePh@Pd(0) NPs. The size distribution of these NPs was found to be approximately ∼12–18 nm (Fig. S1 in ESI†).
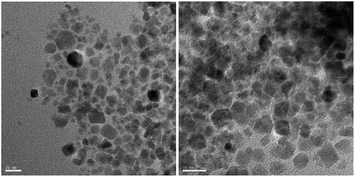 |
| Fig. 3 The TEM images of Fe3O4@SiO2@SePh@Pd(0) NPs at 20 nm scale bar. | |
Catalytic applications
O-Arylation of phenol. The Fe3O4@SiO2@SePh@Pd(0) NPs were explored to catalyze the C–O coupling reaction of phenol with several aryl halides in water. The conditions for the coupling reaction were optimized for the reaction of 4-bromobenzaldehyde with phenol (Table 1). In the absence of the catalyst as well as a base, the conversion to the coupled product was negligible (Table 1, entries 7 and 8). The reaction was investigated with different quantities of the catalyst (0.01 to 0.5 mol%). The best results were achieved with 0.1 mol% catalyst loading. On increasing the quantity of the catalyst, significant improvement was not observed in the yield of the product. However, on lowering the catalyst amount to 0.01 mol%, the yield of the product decreased (Table 1, entry 9). Among the bases tested, namely, K2CO3, Cs2CO3, Et3N, K3PO4, and NaOH, optimum results were obtained with NaOH (Table 1, entry 5). The performance of a range of solvents, viz., DMF, EtOH, DMSO, and toluene was tested and compared to that of water. All these alternatives to water did not show better results (Table 1, entries 10–13).
Table 1 Screening of reaction conditions for O-arylationa
Entry no. |
Catalyst (mol%) |
Base |
Solvent |
Time (h) |
Yieldb (%) |
Reaction conditions: 4-bromobenzaldehyde (1 mmol), phenol (1.1 mmol), solvent (5 mL), base (1.5 mmol), bath temp. (80 °C). Isolated yield. |
1 |
0.5 |
K2CO3 |
Water |
3 |
83 |
2 |
0.5 |
Cs2CO3 |
Water |
3 |
78 |
3 |
0.5 |
Et3N |
Water |
3 |
10 |
4 |
0.5 |
K3PO4 |
Water |
3 |
45 |
5 |
0.5 |
NaOH |
Water |
3 |
94 |
6 |
0.1 |
NaOH |
Water |
3 |
93 |
7 |
0.5 |
— |
Water |
12 |
— |
8 |
— |
NaOH |
Water |
12 |
— |
9 |
0.01 |
NaOH |
Water |
3 |
76 |
10 |
0.1 |
NaOH |
DMF |
3 |
79 |
11 |
0.1 |
NaOH |
EtOH |
3 |
92 |
12 |
0.1 |
NaOH |
DMSO |
3 |
88 |
13 |
0.1 |
NaOH |
Toluene |
3 |
46 |
The scope of the present protocol was explored using a range of aryl halides. The results (Table 2) showed that the present catalyst was capable of coupling aryl chlorides, bromides, and iodides with phenol. The yield was good even in the case of less activated substrates in a short time (2–6 h) compared to many literature results.29a–29f The present NPs also showed good catalytic activity for heteroaryl halides. The electron-withdrawing and releasing substituents on haloarene had a significant effect on the yield of the coupled product (Table 2). The reaction of deactivated aryl halides with phenol gave a good yield, but it was less in comparison to those of activated aryl halides. The position of a substituent on the ring of aromatic halide also affected the yield of the coupled product; the substituent at a position ortho to the halo group gave a lower yield in comparison to that for the substrates having a substituent at the para position (Table 2, entries 1, 4–6).
Table 2 Fe3O4@SiO2@SePh@Pd(0)-catalyzed O-arylation of phenola,b
Reaction conditions: aryl halide (1 mmol), phenol (1.1 mmol), catalyst (0.1 mol%), time 3 h, water (5 mL), NaOH (1.5 mmol), and bath temp. 80 °C. Isolated yield. Catalyst 1 mol% and reaction time 6 h. Catalyst 0.01 mol% and reaction time 2 h. |
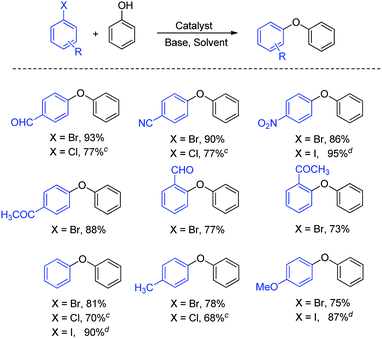 |
Some of the previously reported heterogeneous catalytic systems reported for the O-arylation of phenol, viz, (i) Fe3O4@SiO2@PPh2@Pd(0) (ref. 29a) (ii) maghemite-copper nanocomposites (ref. 29b) (iii) NiFe2O4 (ref. 29c) (iv) CNT@α-Fe2O3@CuO (ref. 29d) (v) Pd–ZnFe2O4 (ref. 29e) and (vi) CuFe2O3 (ref. 29f) were compared with the present catalyst (Table S1 (ESI†)). The comparison revealed that the present protocol with Fe3O4@SiO2@SePh@Pd(0) NPs was better in efficiency than those reported earlier. The medium of the reaction was water (a major advantage), with the scope and the reaction time being comparable (Table 2).
Suzuki–Miyaura coupling. The magnetically retrievable catalyst was also explored for the Suzuki–Miyaura coupling of aryl halides. The reaction of 4-bromobenzaldehyde with phenylboronic acid was chosen as the model reaction. In the absence of the catalyst and a base, no conversion was observed. K2CO3 as a base and water as a solvent were found to give the best combination for the reaction (Table 3). Under the optimized conditions (3 h, 0.1 mol% of the catalyst, 80 °C), nearly quantitative conversion of 4-bromobenzaldehyde to the coupled product was observed (isolated yield: 94%). On lowering the loading of the catalyst to 0.01 mol%, the yield of the product decreased (Table 3, entry 9). Similar to the O-arylation of phenol, the catalyst Fe3O4@SiO2@SePh@Pd(0) successfully converted several aryl halides to biaryls with very good yields in 1.5–6 h (Table 4).
Table 3 Screening of reaction conditions for Suzuki–Miyaura reactiona
Entry no. |
Catalyst (mol%) |
Base |
Solvent |
Time (h) |
Yieldb (%) |
Reaction conditions: 4-bromobenzaldehyde (1 mmol), phenylboronic acid (1.2 mmol), solvent (5 mL), and base (1.5 mmol), bath temp. (80 °C). Isolated yield. |
1 |
0.5 |
K2CO3 |
Water |
3 |
95 |
2 |
0.1 |
K2CO3 |
Water |
3 |
94 |
3 |
0.1 |
Cs2CO3 |
Water |
3 |
90 |
4 |
0.5 |
Et3N |
Water |
3 |
34 |
5 |
0.5 |
K3PO4 |
Water |
3 |
86 |
6 |
0.5 |
NaOH |
Water |
3 |
68 |
7 |
0.5 |
— |
Water |
12 |
— |
8 |
— |
K2CO3 |
Water |
12 |
— |
9 |
0.01 |
K2CO3 |
Water |
3 |
81 |
10 |
0.1 |
NaOH |
DMF |
3 |
77 |
11 |
0.1 |
NaOH |
DMF + water |
3 |
92 |
12 |
0.1 |
NaOH |
EtOH |
3 |
91 |
13 |
0.1 |
NaOH |
EtOH + water |
3 |
94 |
14 |
0.1 |
NaOH |
DMSO |
3 |
74 |
15 |
0.1 |
NaOH |
Toluene |
3 |
36 |
Table 4 Fe3O4@SiO2@SePh@Pd(0)-catalyzed Suzuki–Miyaura coupling reactiona,b
Reaction conditions: aryl halide (1 mmol), phenylboronic acid (1.2 mmol), catalyst (0.1 mol%), time 3 h, water (5 mL), K2CO3 (1.5 mmol), and bath temp. (80 °C). Isolated yield. Catalyst 1 mol% and reaction time 6 h. Catalyst 0.01 mol% and reaction time 2 h. |
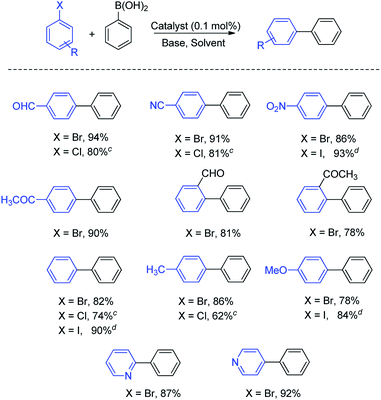 |
The effect on the yield of the coupled product due to the nature and position of the substituent present on the benzene ring of aryl halides may be inferred from Table 4. The presence of electron-withdrawing groups gave a somewhat better yield than the electron-donating ones. The aryl halides having a substituent at the para position gave a better yield of the coupled product compared to ortho-substituted derivatives (Table 4, entries 1, 4–6). The coupling of heteroaromatic halides was also efficiently catalyzed by Fe3O4@SiO2@SePh@Pd(0).
In summary, the magnetically separable Fe3O4@SiO2@SePh@Pd(0) NPs result in good catalytic conversion with low catalyst loading (0.01–1 mol%) in an aqueous medium without any co-solvent/additive. The comparison of the present catalyst for Suzuki–Miyaura coupling with the previously reported ones, viz., (i) HMMS (hollow magnetic mesoporous spheres)-NH2–Pd,30a (ii) Pd@Mag-MSN,30b (iii) Pd–CoFe2O4 MNPs,30c (iv) silica-supported palladium catalyst,30d (v) iron oxide-supported palladium NHC complex,30e (vi) NiFe2O4–(dopamine)–Pd,30f (vii) Pd/C-cetyltrimethylammonium bromide (CTAB),30g (viii) layered double hydroxide (LDH)-supported nanopalladium,30h (ix) Pd-polyoxomatalate nanoparticles,30i (x) Pd/C30j (xi) mercaptopropyl-modified mesoporous silica-supported palladium catalyst30k (xii) Pd–PPh2–SiO2@Fe3O4,30l (xiii) magnetic nanoparticle-supported (β-oxoiminato)-(phosphanyl) palladium complex,30m and (xiv) Pd–Fe3O4 heterodimer nanocrystals30n made in Table S2 (ESI†) reveals that its catalytic efficiency is better than that of most of the related heterogeneous Pd-based catalysts.
The time profiles of both C–O and Suzuki–Miyaura coupling reactions of 4-bromobenzaldehyde (1 mmol) shown in Fig. 4 indicate that on increasing the reaction time from 3 to 5 h, there is almost no increment in the yield of the coupled product, and 78–82% of the reaction is completed in 2 h. The catalysis of both the coupling reactions with nano-sized Fe3O4, Fe3O4@SiO2, and Fe3O4@SiO2@SePh was attempted. No coupled product was formed even after 6 h (Table 5, entries 1–3). When the C–O coupling and SMC reactions were carried out using PdCl2 as the catalyst under the present optimum conditions, the resulting yields were 18 and 27%, respectively (Table 5, entry 4). The yield was maximum for both the coupling reactions (Table 5, entry 5) when Fe3O4@SiO2@SePh@Pd(0) NPs were used as the catalyst.
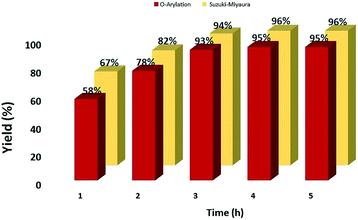 |
| Fig. 4 Time profiles of Suzuki–Miyaura and C–O coupling of 4-bromobenzaldehyde (1 mmol); catalyst, (0.1 mol%); phenyl boronic acid (for SMC), phenol (for C–O coupling), (1.2 mmol); K2CO3 (for SMC), NaOH (for C–O coupling) (1.5 mmol); water 5 mL; bath temperature, 80 °C; isolated yield in %. | |
Table 5 Fe3O4@SiO2@SePh@Pd(0) NPs and their precursor as catalystsa
Entry |
Catalyst |
Time (h) |
Yieldd % (for C–O) |
Yieldd % (for SMC) |
Reaction conditions: 4-bromobenzaldehyde (1 mmol); catalyst, (30 mg); phenyl boronic acid (for SMC), phenol (for C–O coupling), (1.2 mmol); K2CO3 (for SMC), NaOH (for C–O coupling) (1.5 mmol); water, 5 mL; temperature, 80 °C. 1 mol%. 100 °C. Isolated yield. |
1 |
Fe3O4 |
6 |
0 |
0 |
2 |
Fe3O4@SiO2 |
6 |
0 |
0 |
3 |
Fe3O4@SiO2@SePh |
6 |
0 |
0 |
4b |
PdCl2 |
3 |
18 |
27 |
5 |
Fe3O4@SiO2@SePh@Pd(0) NPs |
3 |
93 |
94 |
6c |
Fe3O4@SiO2@SePh@Pd(0) NPs |
3 |
93 |
94 |
The recyclability of the catalyst was studied by carrying out the reaction between 4-bromobenzaldehyde and phenol/phenylboronic under optimum conditions, as described in the experimental section; the results are shown in Fig. 5.
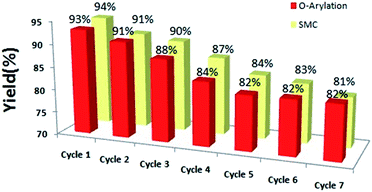 |
| Fig. 5 Recycling experiments. | |
Thus, the present catalyst is reusable for at least more than 7 times but with a small loss in the yield.
The catalyst was re-analyzed with TEM, SEM-EDX, and ICP-AES after the recycling experiment. The TEM image (Fig. 6) indicates some agglomeration in the nanoparticles, which is probably responsible for the decrease in the catalytic activity with the decrease in its surface area. The SEM-EDX (Fig. S3 in ESI†) result revealed that the catalyst composition remained almost the same after the catalytic reaction. The palladium content of the catalyst was determined with ICP-AES before and after the seven reaction cycles; it was found to be 1.96% in the beginning and 1.91% after the seventh reaction cycle. The small amount of leaching is due to the strong binding of Pd with selenium and indicates the good stability of the present catalyst. A hot filtration test was conducted for O-arylation as well as SMC carried out under optimum conditions to establish the role of Pd leaching, if any, on the catalytic reaction. Both the reactions did not proceed after the removal of the catalyst as the yield remained at the same level, indicating its heterogeneous nature.28
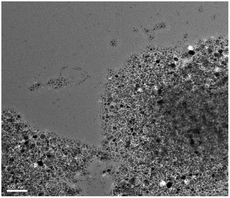 |
| Fig. 6 The TEM image of recycled Fe3O4@SiO2@SePh@Pd(0) NPs at 100 nm scale bar. | |
Conclusions
A magnetically retrievable palladium nano-catalyst [Fe3O4@SiO2@SePh@Pd(0)] was designed and authenticated with PXRD, SEM-EDX, ICP-AES, XPS, and TEM. It catalyzed the O-arylation of phenol with aryl halides and Suzuki–Miyaura coupling under mild reaction conditions in water. The optimum loading (in mol% of Pd) was found to be 0.1–1.0 and 0.01–1.0 for arylation and SMC, respectively. For ArCl, the required amount of NPs was more as compared to that needed for ArBr. The nature of catalysis was heterogeneous, as revealed by hot filtration. The recyclability of the catalyst was good. The comparison with other relevant catalytic systems indicated that it was superior to them.
Experimental
Physical measurement
1H and 13C{1H} NMR spectra were recorded using a Bruker Spectrospin DPX 300 NMR spectrometer at 300.13 and 75.47 MHz, respectively. The chemical shifts were reported in ppm relative to the internal standard (tetramethylsilane) for the 1H and 13C{1H} NMR spectra. All the reactions were carried out in glassware dried in an oven. Powder X-ray diffraction (PXRD) studies were carried out using a Bruker D8 Advance diffractometer using Ni-filtered Cu-Kα radiation at a scan speed of 1 s and a scan step of 0.05°. Transmission electron microscopy (TEM) studies were carried out using a JEOL JEM 200CX TEM instrument operated at 200 kV. The specimens for these studies were prepared by dispersing the powdered sample in ethanol by ultrasonic treatment. A few drops of the resulting homogenized slurry were put on a porous carbon film supported on a copper grid and dried in air. The elemental composition of the NPs was studied with a Carl ZEISS EVO5O scanning electron microscope (SEM) and the associated EDX system Model QuanTax 200, which is based on the SDD technology and provides an energy resolution of 127 eV under Mn-Kα radiation. The sample was mounted on a circular metallic sample holder with a sticky carbon tape. X-ray photoelectron spectroscopic (XPS) studies were carried out on Specs instrument equipped with an Mg K-radiation source (E = 1253.60 eV) and hemispherical analyzer. The estimation of palladium in the nanoparticles was carried out using ICP-AES (DRE, PS-3000UV, Leeman Labs, Inc. USA).
Chemicals and reagents
FeCl3·6H2O, urea, FeSO4·7H2O, tetraethylorthosilicate (TEOS), PdCl2, phenylselenyl chloride, phenol, aryl halides, phenyl boronic acid, KOH, and K2CO3 obtained from Sigma-Aldrich (USA) were used as received. The solvents (toluene, acetone, ethyl acetate, and ethanol) of AR grade were dried and distilled before use according to standard procedures.33 Fe3O4@SiO2@SePh was synthesized according to a previously reported method.12
Synthesis of Fe3O4@SiO2@SePh@Pd(0) NPs34
An aqueous solution of PdCl2 (1 mmol in 60 mL H2O) was added to Fe3O4@SiO2@SePh NPs (2 g) dispersed in water, and the mixture was stirred for 30 min. The aqueous solution of sodium hydroxide (1 M) was added dropwise to the mixture until its pH reached ∼12. The resulting mixture was stirred for 20 h with refluxing. The product was separated magnetically, washed 5–6 times with water followed by ethanol, and dried in vacuo for 2 h. The weight percentage of Pd in the catalyst was found to be 1.96% with ICP-AES.
Procedure for Suzuki–Miyaura coupling (SMC)
A round bottom flask of 50 mL was charged with aryl halide (1 mmol), phenylboronic acid (1.2 mmol), K2CO3 (1.5 mmol) catalyst (0.01–1.0 mol%), and deionized water (5 mL). The mixture was stirred at 80 °C. The reaction was monitored with TLC. When the conversion of aryl halide reached maximum, the reaction mixture was cooled to room temperature and extracted with diethyl ether (20 mL). The extract was dried over anhydrous Na2SO4. Its solvent was evaporated with a rotary evaporator, and the residue was purified through a column of silica gel with CHCl3/hexane as an eluent. All coupling products were analyzed with 1H NMR spectroscopy.
Procedure for C–O coupling
Aryl halide (1 mmol), phenol (1.1 mmol), NaOH (1.5 mmol), catalyst (0.01–1.0 mol%), and deionized water (5 mL) were mixed in a round bottom flask of 50 mL and stirred at 80 °C. The reaction was monitored with TLC. On approaching the completion of the reaction, the mixture was cooled to room temperature. It was extracted with ethyl acetate (20 mL). The extract was dried with anhydrous Na2SO4. The solvent of the extract was evaporated with a rotary evaporator, and the residue was purified through a column of silica gel with ethyl acetate/hexane as the eluent. All coupling products were analysed with 1H NMR spectroscopy.
Recyclability
4-Bromobenzaldehyde was used to check recyclability. 4-Bromobenzaldehyde (1 mmol), catalyst (0.1 mol%), phenol (1.1 mmol), NaOH (1.5 mmol) [for C–O coupling]/phenylboronic acid (1.2 mmol), K2CO3 (1.5 mmol) [for SMC], and deionized water (5 mL) were mixed in a round bottom flask of 50 mL and stirred at 80 °C. The reaction was monitored with TLC. After completion of the C–C/C–O coupling reaction, the catalyst (Fe3O4@SiO2@SePh@Pd(0) NPs) was separated with an external magnet. It was washed with H2O, dried in vacuo and reused for a new reaction cycle of 4-bromobenzaldehyde.
Hot filtration experiment
4-Bromobenzaldehyde (1 mmol), phenol/phenylboronic acid (1.2 mmol), NaOH/K2CO3 (1.5 mmol), and catalyst (0.1 mol%) were mixed with deionized water (5 mL). The mixture was stirred at 80 °C. The reaction was stopped after 1 h, and the catalyst was separated using an external magnet. The clear reaction mixture was divided into two equal parts and each part was taken separately in a 50 mL round bottom flask. The separated NPs were added to one of them. Thereafter, the reactions in both the flasks were allowed to proceed for another 3 h, and the product/conversion was analyzed with 1H NMR spectroscopy.
Conflicts of interest
There are no conflicts to declare.
Acknowledgements
Authors thank to Council of Scientific and Industrial Research (CSIR), New Delhi, India for the financial support and SRF to AS. Nano-mission, Department of Science and Technology (India) is acknowledged for research project. HJ thanks University Grants Commission (India) for JRF/SRF.
Notes and references
-
(a) E. Rafiee and S. Eavani, Green Chem., 2011, 13, 2116 RSC;
(b) C. Ó. Dálaigh, S. A. Corr, Y. Gun’ko and S. J. Connon, Angew. Chem., Int. Ed., 2007, 46, 4329 CrossRef PubMed;
(c) D. M. Lai, L. Deng, J. Li, B. Liao, Q. X. Guo and Y. Fu, ChemSusChem, 2011, 4, 55 CrossRef CAS PubMed;
(d) Y. Zhang and C. G. Xia, Appl. Catal., A, 2009, 366, 141 CrossRef CAS;
(e) X. X. Zheng, S. Z. Luo, L. Zhang and J. P. Cheng, Green Chem., 2009, 11, 455 RSC.
- V. Polshettiwar and R. S. Varma, Green Chem., 2010, 12, 743 RSC.
-
(a) A.-H. Lu, E. L. Salabas and F. Schüth, Angew. Chem., Int. Ed., 2007, 46, 1222 CrossRef CAS PubMed;
(b) Y. Zhu, L. P. Stubbs, F. Ho, R. Liu, C. P. Ship, J. A. Maguire and N. S. Hosmane, ChemCatChem, 2010, 2, 365 CrossRef CAS.
- V. Polshettiwar and R. S. Varma, Org. Biomol. Chem., 2009, 7, 37 RSC.
-
(a) R. Abu-Reziq, H. Alper, D. S. Wang and M. L. Post, J. Am. Chem. Soc., 2006, 128, 5279 CrossRef CAS PubMed;
(b) G. Chouhan, D. S. Wang and H. Alper, Chem. Commun., 2007, 4809 RSC;
(c) T. Hara, T. Kaneta, K. Mori, T. Mitsudome, T. Mizugaki, K. Ebitani and K. Kaneda, Green Chem., 2007, 9, 1246 RSC;
(d) M. J. Jin and D. H. Lee, Angew. Chem., Int. Ed., 2010, 49, 1119 CrossRef CAS PubMed;
(e) H. Q. Yang, Y. Wang, Y. Qin, Y. Chong, Q. Yang, G. Li, L. Zhang and W. Li, Green Chem., 2011, 13, 1352 RSC;
(f) S. E. Garca-Garrido, J. Francos, V. Cadierno, J.-M. Basset and V. Polshettiwar, ChemSusChem, 2011, 4, 104 CrossRef PubMed.
-
(a) X. Wang, P. P. Dou, P. Zhao, C. M. Zhao, Y. Ding and P. Xu, ChemSusChem, 2009, 2, 947 CrossRef CAS PubMed;
(b) J. Lee, Y. Lee, J. K. Youn, H. B. Na, T. Yu, H. Kim, S. M. Lee, Y. M. Koo, J. H. Kwak, H. G. Park, H. N. Chang, M. Hwang, J. G. Park, J. Kim and T. Hyeon, Small, 2008, 4, 143 CrossRef CAS PubMed.
-
(a) S. Wu, A. Sun, F. Zhai, J. Wang, W. Xu, Q. Zhang and A. A. Volinsky, Mater. Lett., 2011, 65, 1882 CrossRef CAS;
(b) K. S. Lee, M. H. Woo, H. S. Kim, E. Y. Lee and I. S. Lee, Chem. Commun., 2009, 3780 RSC;
(c) V. Polshettiwar and Á. Molnár, Tetrahedron, 2007, 63, 6949 CrossRef CAS;
(d) L. M. Rossi, I. M. Nangoi and N. J. S. Costa, Inorg. Chem., 2009, 48, 4640 CrossRef CAS PubMed.
-
(a) S. B. Kim, C. Cai, J. Kim, S. Sun and D. A. Sweigart, Organometallics, 2009, 28, 5341 CrossRef CAS;
(b) H. Zhang and G. Zhu, Appl. Surf. Sci., 2012, 258, 4952 CrossRef CAS;
(c) M. Ma, Q. Zhang, D. Yin, J. Dou, H. Zhang and H. Xu, Catal. Commun., 2012, 17, 168 CrossRef CAS;
(d) N. Koukabi, E. Kolvari, A. Khazaei, M. A. Zolfigol, B. Shirmardi-Shaghasemi and H. R. Khavasi, Chem. Commun., 2011, 47, 9230 RSC.
-
(a) S. Qu, H. Yang, D. Ren, S. Kan, G. Zou, D. Li and M. Li, J. Colloid Interface Sci., 1999, 215, 190 CrossRef CAS PubMed;
(b) V. Polshettiwar, R. Luque, A. Fihri, H. Zhu, M. Bouhrara and J.-M. Basset, Chem. Rev., 2011, 111, 3036 CrossRef CAS PubMed.
-
(a) K. N. Sharma, H. Joshi, A. K. Sharma, O. Prakash and A. K. Singh, Chem. Commun., 2013, 49, 9344 RSC;
(b) H. Joshi, K. N. Sharma, V. V. Singh, P. Singh and A. K. Singh, Dalton Trans., 2013, 42, 2366 RSC;
(c) O. Prakash, K. N. Sharma, H. Joshi, P. L. Gupta and A. K. Singh, Dalton Trans., 2013, 42, 8736 RSC;
(d) O. Prakash, H. Joshi, U. Kumar, A. K. Sharma and A. K. Singh, Dalton Trans., 2015, 44, 1962 RSC;
(e) O. Prakash, H. Joshi, K. N. Sharma, P. L. Gupta and A. K. Singh, Organometallics, 2014, 33, 3804 CrossRef CAS;
(f) O. Prakash, K. N. Sharma, H. Joshi, P. L. Gupta and A. K. Singh, Organometallics, 2014, 33, 2535 CrossRef CAS;
(g) A. K. Sharma, H. Joshi, K. N. Sharma, P. L. Gupta and A. K. Singh, Organometallics, 2014, 33, 3629 CrossRef CAS;
(h) O. Prakash, K. N. Sharma, H. Joshi, P. L. Gupta and A. K. Singh, Organometallics, 2014, 33, 983 CrossRef CAS.
-
(a) H. Joshi, K. N. Sharma, A. K. Sharma, O. Prakash and A. K. Singh, Chem. Commun., 2013, 49, 7483 RSC;
(b) H. Joshi, K. N. Sharma, A. K. Sharma and A. K. Singh, Nanoscale, 2014, 6, 4588 RSC.
- H. Joshi, K. N. Sharma, A. K. Sharma, O. Prakash, A. Kumar and A. K. Singh, Dalton Trans., 2014, 43, 12365 RSC.
- R. K. Sharma, S. Dutta, S. Sharma, R. Zboril, R. S. Varma and M. B. Gawande, Green Chem., 2016, 18, 3184 RSC.
-
(a) F. Theil, Angew. Chem., Int. Ed., 1999, 38, 2345 CrossRef CAS;
(b) J. S. Sawyer, Tetrahedron, 2000, 56, 5045 CrossRef;
(c) A. W. Thomas and S. V. Ley, Angew. Chem., Int. Ed., 2003, 42, 5400 CrossRef PubMed.
-
(a) E. S. Tan, M. Miyakawa, J. R. Bunzow, D. K. Grandy and T. S. Scanlan, J. Med. Chem., 2007, 50, 2787 CrossRef CAS PubMed;
(b) K. C. Nicolaou, C. N. C. Boddy, S. Brase and N. Winssinger, Angew. Chem., Int. Ed., 1999, 38, 2097 CAS.
-
(a) N. Xia and M. Taillefer, Chem.–Eur. J., 2008, 14, 6037 CrossRef CAS PubMed;
(b) G. C. H. Chiang and T. Olsson, Org. Lett., 2004, 6, 3079 CrossRef CAS;
(c) X. Lv and W. Bao, J. Org. Chem., 2007, 72, 3863 CrossRef CAS PubMed;
(d) D. Maiti, Chem. Commun., 2011, 47, 8340 RSC;
(e) D. Ma and Q. Cai, Org. Lett., 2003, 5, 3799 CrossRef CAS PubMed.
-
(a) B. Schlummer and U. Scholz, Adv. Synth. Catal., 2004, 346, 1599 CrossRef CAS;
(b) S. Gowrisankar, A. G. Sergeev, P. Anbarasan, A. Spannenberg, H. Neumann and M. Beller, J. Am. Chem. Soc., 2010, 132, 11592 CrossRef CAS PubMed;
(c) T. Hu, T. Schulz, C. Torborg, X. Chen, J. Wang, M. Beller and J. Huang, Chem. Commun., 2009, 7330 RSC;
(d) A. Dumrath, X. F. Wu, H. Neumann, A. Spannenberg, R. Jackstell and M. Beller, Angew. Chem., Int. Ed., 2010, 49, 8988 CrossRef CAS.
-
(a) G. Nordmann and S. L. Buchwald, J. Am. Chem. Soc., 2003, 125, 4978 CrossRef CAS PubMed;
(b) X. Wu, B. P. Fors and S. L. Buchwald, Angew. Chem., Int. Ed., 2011, 50, 9943 CrossRef CAS PubMed;
(c) R. A. Altman and S. L. Buchwald, Org. Lett., 2007, 9, 643 CrossRef CAS;
(d) L. Salvi, N. R. Davis, S. Z. Ali and S. L. Buchwald, Org. Lett., 2012, 14, 170 CrossRef CAS PubMed;
(e) G. Mann, C. Incarvito, A. L. Rheingold and J. F. Hartwig, J. Am. Chem. Soc., 1999, 121, 3224 CrossRef CAS;
(f) Q. Shelby, N. Kataoka, G. Mann and J. Hartwig, J. Am. Chem. Soc., 2000, 122, 10718 CrossRef CAS;
(g) N. Kataoka, Q. Shelby, J. P. Stambuli and J. F. Hartwig, J. Org. Chem., 2002, 67, 5553 CrossRef CAS PubMed.
- J. Zhang, J. Chen, M. Liu, X. Zheng, J. Ding and H. Wu, Green Chem., 2012, 14, 912 RSC.
-
(a) N. Miyaura and A. Suzuki, in Advances in Metal-Organic Chemistry, ed. L. S.Liebeskind, JAI, London, 1998, vol. 6, p. 187 Search PubMed;
(b) S. Kotha, K. Lahiri and D. Kashinath, Tetrahedron, 2002, 58, 9633 CrossRef CAS.
-
(a) T. J. Colacot, Platinum Met. Rev., 2011, 55, 84 CrossRef;
(b) A. Suzuki, Angew. Chem., Int. Ed., 2011, 50, 6722 (Angew. Chem., 2011, 123, 6854) CrossRef CAS PubMed;
(c) A. Suzuki and Y. Yamamoto, Chem. Lett., 2011, 40, 894 CrossRef CAS;
(d) A. Suzuki, J. Organomet. Chem., 1999, 576, 147 CrossRef CAS.
-
(a) J. P. Wolfe and S. L. Buchwald, Angew. Chem., Int. Ed., 1999, 38, 2413 (Angew. Chem., 1999, 111, 2570) CrossRef CAS;
(b) A. F. Littke, C. Dai and G. C. Fu, J. Am. Chem. Soc., 2000, 122, 4020 CrossRef CAS;
(c) X. Bei, H. W. Turner, W. H. Weinberg and A. S. Guram, J. Org. Chem., 1999, 64, 6797 CrossRef CAS PubMed.
-
(a) R. B. Bedford and C. S. J. Cazin, Chem. Commun., 2001, 1540 RSC;
(b) R. B. Bedford, S. L. Hazelwood and M. E. Limmert, Chem. Commun., 2002, 2610 RSC;
(c) J. Ma, X. Cui, L. Gao and Y. Wu, Inorg. Chem. Commun., 2007, 10, 762 CrossRef CAS;
(d) J. P. Wolfe, R. A. Singer, B. H. Yang and S. L. Buchwald, J. Am. Chem. Soc., 1999, 121, 9550 CrossRef CAS.
-
(a) C. Fleckenstein, S. Roy, S. Leuthaeusser and H. Plenio, Chem. Commun., 2007, 2870 RSC;
(b) C. Zhang and M. L. Trudell, Tetrahedron Lett., 2000, 41, 595 CrossRef CAS;
(c) K. N. Sharma, H. Joshi, A. K. Sharma, O. Prakash and A. K. Singh, Organometallics, 2013, 32, 2443 CrossRef CAS.
-
(a) Z. Xiong, N. Wang, M. Dai, A. Li, J. Chen and Z. Yang, Org. Lett., 2004, 6, 3337 CrossRef CAS PubMed;
(b) S. M. Nobre and A. L. Monteiro, J. Mol. Catal. A: Chem., 2009, 313, 65 CrossRef CAS;
(c) H. Joshi, O. Prakash, A. K. Sharma, K. N. Sharma and A. K. Singh, Eur. J. Inorg. Chem., 2015, 1542 CrossRef CAS.
-
(a) K. N. Sharma, H. Joshi, V. V. Singh, P. Singh and A. K. Singh, Dalton Trans., 2013, 42, 3908 RSC;
(b) O. Prakash, H. Joshi, K. N. Sharma, A. K. Sharma and A. K. Singh, Eur. J. Inorg. Chem., 2015, 520 CrossRef CAS.
- G. C. Fortman and S. P. Nolan, Chem. Soc. Rev., 2011, 40, 5151 RSC.
- L. Yin and J. Liebscher, Chem. Rev., 2007, 107, 133 CrossRef CAS PubMed.
-
(a) M. A. Zolfigol, V. Khakyzadeh, A. R. Moosavi-Zare, A. Rostami, A. Zare, N. Iranpoor, M. H. Beyzavieand and R. Luque, Green Chem., 2013, 15, 2132 RSC;
(b) R. K. Sharma, R. Gaur, M. Yadav, A. K. Rathi, J. Pechousek, M. Petr, R. Zboril and M. B. Gawande, ChemCatChem, 2015, 7, 3495 CrossRef CAS;
(c) S. Paul, K. Pradhan, S. Ghosh, S. K. De and A. R. Das, Adv. Synth. Catal., 2014, 356, 1301 CrossRef CAS;
(d) D. Saberi, M. Sheykhan, K. Niknamc and A. Heydari, Catal. Sci. Technol., 2013, 3, 2025 RSC;
(e) A. S. Singh, S. S. Shendageand and J. M. Nagarkar, Tetrahedron Lett., 2013, 54, 6319 CrossRef CAS;
(f) R. Zhang, J. Liu, S. Wang, J. Niu, C. Xia and W. Sun, ChemCatChem, 2011, 3, 146 CrossRef CAS.
-
(a) P. Wang, F. Zhang, Y. Long, R. Li and J. Ma, Catal. Sci. Technol., 2013, 3, 1618 RSC;
(b) S. Shylesh, L. Wang, S. Demeshko and W. R. Thiel, ChemCatChem, 2010, 2, 1543 CrossRef CAS;
(c) K. K. Senapati, S. Roy, C. Borgohain and P. Phukan, J. Mol. Catal. A: Chem., 2012, 352, 128 CrossRef CAS;
(d) S. Paul and J. H. Clark, Green Chem., 2003, 5, 635 RSC;
(e) P. D. Stevens, G. Li, J. Fan, M. Yen and Y. Gao, Chem. Commun., 2005, 4435 RSC;
(f) B. Baruwati, D. Guin and S. V. Manorama, Org. Lett., 2007, 9, 5377 CrossRef CAS PubMed;
(g) A. Arcadi, G. Cerichelli, M. Chiarini, M. Correa and D. Zorzan, Eur. J. Org. Chem., 2003, 4080 CrossRef CAS;
(h) B. M. Choudary, S. Madhi, N. S. Chowdari, M. L. Kantam and B. Sreedhar, J. Am. Chem. Soc., 2002, 124, 14127 CrossRef CAS PubMed;
(i) V. Kogan, Z. Aizenshtat, R. Popovitz-Biro and R. Neumann, Org. Lett., 2002, 4, 3529 CrossRef CAS PubMed;
(j) C. R. LeBlond, A. T. Andrews, Y. K. Sun and J. R. Sowa, Org. Lett., 2001, 3, 1555 CrossRef CAS;
(k) C. M. Crudden, M. Sateesh and R. Lews, J. Am. Chem. Soc., 2005, 127, 10045 CrossRef CAS PubMed;
(l) F. Zhang, M. Chen, X. Wu, W. Wang and H. Li, J. Mater. Chem. A, 2014, 2, 484 RSC;
(m) M. J. Jin and D. H. Lee, Angew. Chem., Int. Ed., 2010, 49, 1119 CrossRef CAS PubMed;
(n) Y. Jang, J. Chung, S. Kim, S. W. Jun, B. H. Kim, D. W. Lee, B. M. Kim and T. Hyeon, Phys. Chem. Chem. Phys., 2011, 13, 2512 RSC.
-
(a) C. I. Herrerias, C. X. Yao, Z. Li and C. J. Li, Chem. Rev., 2007, 107, 2546 CrossRef CAS PubMed;
(b) U. M. Lindstrom, Chem. Rev., 2002, 102, 2751 CrossRef PubMed;
(c) S. Minakata and M. Komatsu, Chem. Rev., 2009, 109, 711 CrossRef CAS PubMed.
- S. Zhou, M. Johnsonand and J. G. C. Veinot, Chem. Commun., 2010, 46, 2411 RSC.
- B. S. Furniss, A. J. Hannaford, P. W. G. Smith and A. R. Tatchell, Vogel's Textbook of Practical Organic Chemistry, 5th edn, ELBS, Longman Group, Harlow, UK, 1989 Search PubMed.
- J. Liu, X. Peng, W. Sun, Y. Zhao and C. Xia, Org. Lett., 2008, 10, 3933 CrossRef CAS PubMed.
Footnotes |
† Electronic supplementary information (ESI) available: Size distribution curve of NPs, SEM-EDX image. See DOI: 10.1039/c9ra10618a |
‡ Present address: Department of Chemistry, School of Chemical Sciences and Pharmacy, Central University of Rajasthan, NH-8, Bandarsindri, Ajmer, Rajasthan 305817, India. |
|
This journal is © The Royal Society of Chemistry 2020 |
Click here to see how this site uses Cookies. View our privacy policy here.