DOI:
10.1039/C9RA09854B
(Paper)
RSC Adv., 2020,
10, 9309-9317
The effect of solvents on the thermal degradation products of two Amadori derivatives†
Received
25th November 2019
, Accepted 26th February 2020
First published on 4th March 2020
Abstract
To enrich the flavor additives of the Maillard reaction, two Amadori analogs, N-(1-deoxy-D-fructosyl-1-yl)-L-phenylalanine ester (Derivative 1) and di-O-isopropylidene-2,3:4,5-β-D-fructopyranosyl phenylalanine ester (Derivative 2), were chemically synthesized starting from D-fructose. The samples were reacted at 120 and 180 °C for 2 h, and the effects of solvents (water and ethanol) on their degradation products were studied. The analyses of thermogravimetry (TG), derivative thermogravimetry (DTG), differential scanning calorimetry (DSC), and gas chromatography-mass spectrometry (GC/MS) were used to investigate the thermal behavior and degradation products of the samples. TG–DTG curves show that the Tp values of the samples corresponding to the largest mass-loss rates are 132 and 275 °C, respectively. The degradation products of Derivative 1 are mainly phenyl acetaldehyde and phenylalanine ethyl ester in water and ethyl benzoate and benzaldehyde diethyl acetal in ethanol. For Derivative 2, the major degradation products both in water and ethanol are phenylalanine ethyl ester and diacetonefructose, but the products have different relative contents affected by solvent media. The products of the pyrolysis of the samples at 350 °C were analyzed and compared with the degradation compounds obtained in solvent. These results show that organic solvents can greatly influence the degradation pathway and products. Finally, possible mechanisms of the degradation processes are proposed.
1. Introduction
The Amadori compounds, produced in the initial stage of the Maillard reaction, are ubiquitous during the manufacture and storage of food such as bread, cakes, potatoes, meat, coffee, and tobacco.1–4 The degradation products of Amadori compounds include volatile aromas, which directly influence the organoleptic and nutritional qualities of foodstuffs.5–7 Mills et al.8 and Huyghues-Despointes et al.9 studied the pyrolysis of 1-L-proline-1-deoxy-D-fructose at various temperatures and reported the generation of compounds such as dihydrofuran, dihydropyrones, and pyrrolidines with bready aromas. Additionally, Shigematsu et al.,10 Vernin et al.11 and Mao et al.12–14 reported the formation of volatile aroma compounds via the thermal degradation of 1-L-alanine-1-deoxy-D-fructose, 1-L-valine-1-deoxy-D-fructose, 1-L-methionine-1-deoxy-D-fructose, 1-L-glutamic acid-1-deoxy-D-fructose, 1-L-phenylalanine-1-deoxy-D-fructose, 1-L-leucine-1-deoxy-D-fructose, etc. Since the degradation products of Amadori compounds play a major role in the flavors of food, factors influencing the degradation processes were investigated. Davidek et al.15 studied the effects of phosphate ions on the degradation products of 1-L-glycine-1-deoxy-D-fructose, and the results showed that the addition of phosphate ions could accelerate the degradation processes. Shu et al.16 reported that at a pH of 8.5, the major products formed from the degradation of glucosamine were pyrazine and methylpyrazine. Hofmann et al.17 reported that the formation of phenylacetaldehyde was favored during the degradation of 1-L-phenylalanine-1-deoxy-D-fructose catalyzed by ambient oxygen. However, the effect of organic solvents such as ethanol on the generated degradation products from Amadori derivatives has not yet been studied.
In the present paper, two compounds were chemically synthesized, N-(1-deoxy-D-fructosyl-1-yl)-L-phenylalanine ester (Derivative 1) and di-O-isopropylidene-2,3:4,5-β-D-fructopyranosyl phenylalanine ester (Derivative 2) (Fig. 1), starting from D-fructose.18,19 In Derivative 2, the hydroxyl groups on the pyranose ring are protected by acetal groups to disfavor the isomerization of the sugar moiety. The two derivatives were analyzed by TG, DTG, and DSC, and they were pyrolyzed. The effects of the solvent media on the thermal degradation products were then assessed by GC/MS. The results show that the solvent can influence the degradation of products to a certain extent.
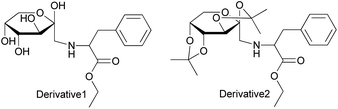 |
| Fig. 1 Chemical structures of Derivative 1 and Derivative 2. | |
2. Materials and methods
2.1 Materials
Methanol, dimethylformamide, dichloromethane, acetone, ethyl acetate, trifluoroacetic acid, and petroleum ether were purchased from Tianjin Kermel Chemical Reagent Co., Ltd (China). The above reagents were of analytical grade. Deionized water (filtered through a 0.22 μm membrane filter, >18.2 MΩ cm) was purified using a Milli-Q system from Millipore. Silica gel was purchased from Qingdao Haiyang Chemical Reagent Co., Ltd (China). Phenylalanine ethyl ester, di-O-isopropylidene-2,3:4,5-β-D-fructose and di-O-isopropylidene-2,3:4,5-β-D-fructopyranosyl trifluoromethanesulfonate were synthesized according to ref. 18 and 19, respectively.
2.2 Structure identification
1H NMR and 13C NMR spectra data were recorded on a Brucker 400 MHz spectrometer. Each sample was dissolved in CDCl3 or CD3OD containing tetramethylsilane (TMS) as the internal reference. HRMS data were obtained using an Agilent 1290LC-6540 Accurate Q-TOF mass spectrometer.
2.3 Preparation of Derivative 2
Di-O-isopropylidene-2,3:4,5-β-D-fructopyranosyl trifluoromethanesulfonate (736.70 mg, 1.88 mmol) and phenylalanine ethyl ester (544.27 mg, 2.82 mmol) were mixed in dimethylformamide (30 mL) and then heated at 120 °C for 6 h. The progress of the reaction was monitored by thin-layer chromatography (TLC) with petroleum ether–ethyl acetate (3
:
1, v
:
v). When the starting materials were consumed, the solvent was evaporated under reduced pressure. The crude residue was purified on a silica gel column with petroleum ether–ethyl acetate (3
:
1, v
:
v) to give the target compound as a yellow oil (342.20 mg, 41.85%). 1H NMR (400 MHz, CDCl3 containing 0.03% TMS, 25 °C): δ: 7.28–7.15 (m, 5H, Ar), 4.58 (dd, J = 7.9 Hz, J = 2.6 Hz, 1H, CH), 4.38 (d, J = 2.6 Hz, 1H, CH), 4.22 (dd, J = 7.9 Hz, J = 1.0 Hz, 1H, CH), 4.06 (q, J = 7.2 Hz, 2H, CH2), 3.81 (dd, 2J = 64.6 Hz, 3J = 12.9 Hz, 2H, CH2), 3.66 (t, J = 6.8 Hz, 1H, CH), 2.97 (m, 2H, CH2), 2.84 (s, 2H, CH2), 1.51 (s, 3H, CH3), 1.46 (s, 3H, CH3), 1.38 (s, 3H, CH3), 1.34 (s, 3H, CH3), 1.13 (t, J = 7.2 Hz, 3H, CH3). 13C NMR (100 MHz, CDCl3, 25 °C): δ: 174.21 (CO), 137.19 (C, Ar), 129.27 (C, Ar), 128.36 (C, Ar), 126.64 (C, Ar), 108.91 (C), 108.15 (C), 103.48 (C), 71.12 (CH), 71.07 (CH), 70.40 (CH), 63.23 (CH2), 61.24 (CH2), 60.46 (CH), 52.94 (CH2), 39.26 (CH2), 26.55 (CH3), 25.89 (CH3), 25.56 (CH3), 24.06 (CH3), 14.11 (CH3). HRMS ESI-TOF: m/z = 458.2154 [M + Na]+ (calcd for C23H33NO7Na, 458.2155).
2.4 Preparation of Derivative 1
Derivative 1 was prepared through the hydrolysis of Derivative 2. The reaction procedure is described below. Derivative 2 (119.10 mg, 0.27 mmol) was stirred in 3.97 mL of trifluoroacetic acid–water (v
:
v 9
:
1) for 1 h at room temperature. Then, the solvent was removed on a rotary evaporator at 45 °C. The crude residue was purified on a silica gel column with ethyl acetate to give the target compound as a white oil (65.67 mg, 68.44%). 1H NMR (400 MHz, MeOD, 25 °C): δ: 7.33–7.30 (m, 2H, Ar), 7.28–7.22 (m, 3H, Ar), 4.20–4.15 (m, 1H, CH), 4.11 (q, J = 7.1 Hz, 2H, CH2), 3.98–3.95 (m, 1H, CH), 3.87 (m, 1H, CH), 3.81–3.77 (m, 1H, CH), 3.69–3.63 (m, 2H, CH2), 3.28–3.08 (m, 2H, CH2), 3.15 (s, 2H, CH2), 1.10 (t, J = 7.1 Hz, 3H, CH3). 13C NMR (100 MHz, MeOD, 25 °C): pyranose form δ: 171.47 (CO), 136.36 (C, Ar), 130.49 (C, Ar), 130.06 (C, Ar), 128.83 (C, Ar), 97.26 (C), 71.46 (CH), 71.25 (CH), 70.81 (CH), 64.93 (CH), 63.23 (CH2), 63.14 (CH2), 53.56 (CH2), 37.81 (CH2), 14.22 (CH3). Furanose form δ: 170.21 (CO), 135.66 (C, Ar), 130.44 (C, Ar), 129.87 (C, Ar), 128.54 (C, Ar), 103.20 (C), 84.54 (CH), 84.32 (CH), 84.10 (CH), 77.62 (CH), 62.61 (CH2), 52.82 (CH2), 51.79 (CH2), 37.18 (CH2), 14.22 (CH3). HRMS ESI-TOF: m/z = 356.1708 [M + H]+ (calcd for C17H26NO7, 356.1709).
2.5 Thermal degradation process20
The thermal degradation of each sample (5 mg) was conducted at 120 °C or 180 °C for 120 min in water (5 mL) or ethanol (5 mL) utilizing sealed 48 mL Synthware glass vials (bought from Beijing Synthware Glass Instrument Co., Ltd.) in oil baths. The reactions were immediately stopped by cooling under a stream of cold water. Solvents were evaporated from the reaction mixtures, and the residues were redissolved in methanol for GC/MS analysis.
2.6 Thermal analysis21
TG, DTG, and DSC analyses were conducted using a simultaneous thermal analyzer (NETZSCH STA 449 F3, Germany). The mass of each sample loaded into the alumina crucible for each run was approximately 5 mg. The tests were carried out under an argon atmosphere at a flow rate of 60 mL min−1. Thermal degradation was monitored from 30 to 900 °C at a constant heating rate of 10 °C min−1. The TG, DTG and DSC curves of the samples were simultaneously determined.
2.7 Pyrolysis-GC/MS and GC/MS analyses22
Pyrolysis-GC/MS analysis was conducted on a combined CDS Pyroprobe 5000 and Agilent 7890/5975 GC/MS system. The pyroprobe was heated at a rate of 5 °C ms−1 from an initial temperature of 50 °C to a final temperature of 350 °C, which was then held for 15 s. The sample mass was approximately 1 mg. The pyrolysis was conducted in air. The corresponding pyrolysis pressure was 1.03 × 106 Pa, and it was higher than the pressure of the GC column. The final pyrolysis products were directly carried into the GC/MS column. Details of the GC/MS analysis conditions are shown below. A DB-5MS fused silica capillary column (50 m × 250 μm id × 0.25 μm df) was used. The injector temperature was 250 °C. The initial oven temperature was 50 °C, and this was held for 2 min; the oven was then heated to 250 °C at a rate of 5 °C min−1, and held at 250 °C for 5 min. The helium carrier gas flow rate remained at 1 mL min−1, and the split ratio was 50
:
1. The EI energy was 70 eV, and the transfer line temperature was 280 °C. The ion source temperature was 230 °C. The quadrupole temperature was 150 °C. The EI-MS scan range was 30–400 amu, and the solvent delay time was 3.6 min. Qualitative analysis of the compound was achieved with the NIST mass spectral search program for the NIST/EPA/NIH mass spectral library version 2.2 (NIST2014, Gaithersburg, USA). Quantitative analysis was based on the area normalization method, which was used to calculate the relative content of each component. All experiments were performed in duplicate, and the quantitative data were expressed by the average values.
3. Results and discussion
3.1 TG–DTG analysis
The TG curve (%) and the DTG curve (DTG, % min−1) of Derivative 1 are presented in Fig. 2. Three stages of thermal degradation were observed. The initial stage, occurring between 103 and 193 °C (Table 1), was the main degradation stage, and approximately 31.3% of the total mass was lost. In this stage, the highest mass-loss rate appeared at a Tp of 132 °C, and at this point, approximately 11.6% of the initial mass of the sample had been lost. The second stage occurred between 217 and 279 °C (Table 1), and the maximum decomposition rate was at 254 °C. Approximately 14.1% of the initial mass of the sample was lost during this stage. From 284 to 900 °C, the sample exhibited a slow mass-loss process with a mass loss of 30.3%. According to the molecular structure of Derivative 1, the benzyl and carbonyl groups are relatively stable, while the C–OH and C–COO–CH2CH3 moieties are unstable groups. The two major mass-loss processes are likely induced by dehydration, de-esterification, and decarboxylation.13 Upon temperature elevation, C–N bonds are broken as are other chemical bonds.
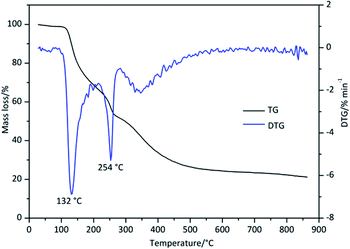 |
| Fig. 2 TG and DTG curves of Derivative 1. | |
Table 1 Thermal analysis data for Derivative 1 and Derivative 2
Sample name |
DSC |
TG–DTG |
Tonset/°C |
Tpeak/°C |
Tend/°C |
ΔH/kJ mol−1 |
Tp/°C |
Trange/°C |
Derivative 1 (peak 1) |
110 |
132 |
146 |
25 |
132 |
103–193 |
Derivative 1 (peak 2) |
247 |
255 |
272 |
−13 |
254 |
217–279 |
Derivative 2 |
81 |
226 |
351 |
−852 |
275 |
160–341 |
Fig. 3 shows the mass loss and mass-loss rates of Derivative 2 with increasing temperature. The curve reveals that the main degradation stage occurred between 160 and 341 °C (Table 1), and in this stage, approximately 98.3% of the total mass was lost. In this stage, the highest mass-loss rate appeared at a Tp of 275 °C, and at this point, approximately 53.0% of the initial mass had been lost. TG–DTG analysis indicates that Derivative 1 and Derivative 2 have good stability at room temperature, and the temperature corresponding to the highest mass-loss rate of Derivative 1 is lower than that of Derivative 2 (Table 1). These phenomena suggest that Derivative 1, with unprotective hydroxyl groups, is more susceptible to thermal degradation.
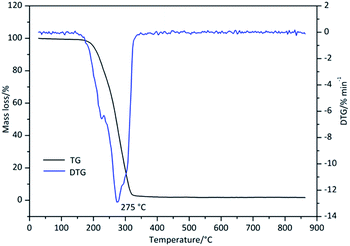 |
| Fig. 3 TG and DTG curves of Derivative 2. | |
3.2 DSC analysis
The DSC curves of Derivative 1 and Derivative 2 are shown in Fig. 4 and 5, respectively. In Fig. 4, the Tpeak values of Derivative 1 are at 132 and 255 °C. The former peak with the onset temperature (Tonset) of 110 °C corresponds to the first mass-loss process displayed in TG–DTG curves, showing an endothermic degradation. The latter peak with Tonset of 247 °C illustrates an exothermic degradation consistent with the second stage shown in TG–DTG curves. On the other hand, the DSC curve of Derivative 2 displays one main exothermic peak with a Tpeak of 226 °C (Fig. 5). These results suggest that the degradation processes in Derivative 1 are more complex than that in Derivative 2. The onset temperature (Tonset), end temperatures (Tend) and thermal enthalpy change (ΔH) of the samples in the DSC curves are detected by the apparatus and summarized in Table 1. In general, the DSC data are corresponding to that of TG–DTG results.
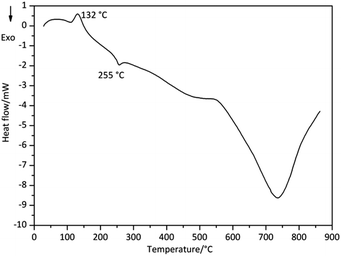 |
| Fig. 4 DSC curve of Derivative 1. | |
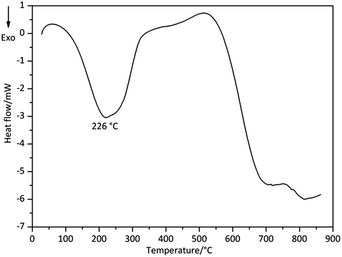 |
| Fig. 5 DSC curve of Derivative 2. | |
3.3 Pyrolysis-GC/MS analysis (degradation without solvents)
TG–DTG and DSC analyses helped elucidate the relationship between temperature change and mass loss (or enthalpy change) in the samples, but these data are not sufficient to identify the molecular structure of the degradation products. To further understand the influence of solvent on the decomposition process, online pyrolysis-GC/MS experiments (degradation without solvents) were conducted at 350 °C in air for Derivative 1 and Derivative 2. The pyrolysis conditions were set based on the degradation temperatures of Derivative 1 and Derivative 2 shown in the TG–DTG curves.
Table 2 lists the main components released from Derivative 1 and Derivative 2 under the pyrolysis conditions. The main pyrolysis products of Derivative 1 are ethyl-3-phenylpropionate, ethyl cinnamate and tetrahydrofuran-3,4-diol. Heterocyclic aroma-active compounds such as 2-formyl furan are dehydration and oxidation products of pyranoses, while phenyl derivatives are obtained from phenylalanine ester. For the pyrolysis of Derivative 2, the products are mainly phenethyl acetate, phenylalanine ethyl ester, and diacetonefructose. Flavor compounds such as phenylmethanol, benzaldehyde, ethyl benzoate, ethyl-3-phenylpropionate and ethyl cinnamate are also formed. Comparing the products between Derivative 1 and Derivative 2, the number of furan or hydrofuran compounds from Derivative 2 is lower than that from Derivative 1, indicating that the protection of the hydroxyl groups notably restricted the degradation of the pyranose ring.
Table 2 Pyrolysis products of Derivative 1 and Derivative 2 at 350 °Ca
No. |
RT min−1 |
Products |
Structure |
Match (%) |
Relative content (%) |
Derivative 1 |
Derivative 2 |
“—” means that the compound was not detected. The table shows only the main degradation products. |
1 |
8.33 |
Tetrahydrofuran-3,4-diol |
 |
85 |
2.60 |
— |
2 |
10.45 |
Toluene |
 |
80 |
0.29 |
— |
3 |
12.25 |
2-Formyl furan |
 |
87 |
0.69 |
— |
4 |
13.53 |
Benzaldehyde |
 |
87 |
0.49 |
0.21 |
5 |
14.09 |
Styrene |
 |
89 |
0.70 |
— |
6 |
15.69 |
Phenylmethanol |
 |
87 |
— |
0.14 |
7 |
19.91 |
Ethyl benzoate |
 |
85 |
— |
0.18 |
8 |
21.32 |
Phenethyl acetate |
 |
95 |
1.32 |
55.84 |
9 |
24.94 |
Ethyl-3-phenylpropionate |
 |
90 |
38.84 |
0.84 |
10 |
28.04 |
Ethyl cinnamate |
 |
80 |
4.84 |
0.83 |
11 |
28.33 |
1-(2-Furyl)-1,2-butanediol |
 |
85 |
— |
0.64 |
12 |
29.13 |
Phenylalanine ethyl ester |
 |
91 |
— |
2.86 |
13 |
31.30 |
Diacetonefructose |
 |
92 |
— |
4.62 |
3.4 Thermal degradation in water and ethanol
To investigate the thermal degradation processes and the distribution of the degradation products obtained in the solvent, Derivative 1 and Derivative 2 were heated at 120 °C and 180 °C in water and ethanol. After evaporating the solvents, the thermal degradation products were analyzed by GC/MS.
Table 3 shows the distribution of degradation products for Derivative 1 and Derivative 2 when the samples were heated at 120 °C and 180 °C in aqueous medium. Derivative 1 releases three compounds, 5-(dimethoxymethyl)-2-furanmethanol (0.71%), ethyl-3-phenylpropionate (0.95%) and phenylalanine ethyl ester (93.38%), at 120 °C. Upon heating to 180 °C, the relative content of phenylalanine ethyl ester drastically decreased to 38.88%, and this was accompanied by the formation of phenylacetaldehyde (3.85%). As expected, the main degradation products of Derivative 2 in water are phenylalanine ethyl ester (5.10%) and diacetonefructose (84.80%). The relative contents of these two compounds at 180 °C are lower than that at 120 °C because of the formation of a compound derived from diacetonefructose. Besides, fewer degradation products (3 and 4 compounds from Derivative 1, 2 and 3 compounds from Derivative 2 at 120 and 180 °C respectively) are detected relative to what is seen after pyrolysis (8 compounds from Derivative 1 and 9 compounds from Derivative 2). The lower degradation temperature and the solvent medium are responsible for these results.
Table 3 Degradation products of Derivative 1 and Derivative 2 in water at 120 and 180 °Ca
No. |
RT min−1 |
Products |
Structure |
Match (%) |
Relative content (%) |
Derivative 1 (120 °C) |
Derivative 1 (180 °C) |
Derivative 2 (120 °C) |
Derivative 2 (180 °C) |
“—” means that the compound was not detected. The table shows only the main degradation products. |
1 |
16.52 |
Phenylacetaldehyde |
 |
88 |
— |
3.85 |
— |
— |
2 |
23.93 |
5-(Dimethoxymethyl)-2-furanmethanol |
 |
87 |
0.71 |
2.79 |
— |
— |
3 |
24.94 |
Ethyl-3-phenylpropionate |
 |
90 |
0.95 |
— |
— |
— |
4 |
27.42 |
Methyl-2-amino-3-phenylpropanoate |
 |
89 |
— |
2.53 |
— |
— |
5 |
28.65 |
2,3:4,5-Bis-O-(1-methylethylidene)-β-D-arabino-hexos-2-ulo-2,6-pyranose |
 |
88 |
— |
— |
— |
11.03 |
6 |
29.13 |
Phenylalanine ethyl ester |
 |
89 |
93.38 |
38.88 |
5.10 |
4.23 |
7 |
31.30 |
Diacetonefructose |
 |
91 |
— |
— |
84.80 |
70.56 |
Table 4 displays the degradation products released from Derivative 1 and Derivative 2 when the compounds were heated to 120 °C and 180 °C in ethanol. Benzaldehyde diethyl acetal, ethyl benzoate, phenylalanine ethyl ester, and ethyl-3-phenylpropionate are the main degradation products from Derivative 1 at 120 °C, and their relative contents are 36.53%, 6.70%, 5.86%, and 5.72%, respectively. At 180 °C, the relative contents of ethyl benzoate (4.52%) and ethyl-3-phenylpropionate (5.11%) becomes lower, and this is accompanied by a slight increase in the contents of benzaldehyde diethyl acetal (37.67%) and ethyl cinnamate (3.62%). Additionally, flavor compounds benzaldehyde, phenylmethanol, and ethyl phenylacetate are formed during thermal degradation in ethanol. It is worth noting that the distribution of products in ethanol is distinct from that in water, indicating that the reaction media can influence the degradation processes. For Derivative 2, the degradation products are phenylalanine ethyl ester and diacetonefructose with relative contents of 6.75% and 76.86% at 120 °C and 14.10% and 69.98% at 180 °C, respectively. The relative content of phenylalanine ethyl ester from ethanol is higher while the amount of diacetonefructose is lower relative to their levels from water, suggesting that changing the degradation medium is one method to control the degradation products.
Table 4 Products of the degradation of Derivative 1 and Derivative 2 in ethanol at 120 and 180 °Ca
No. |
RT min−1 |
Products |
Structure |
Match (%) |
Relative content (%) |
Derivative 1 (120 °C) |
Derivative 1 (180 °C) |
Derivative 2 (120 °C) |
Derivative 2 (180 °C) |
“—” means that the compound was not detected. The table shows only the main degradation products. |
1 |
13.53 |
Benzaldehyde |
 |
90 |
1.99 |
— |
— |
— |
2 |
14.19 |
Diethyl oxalate |
 |
91 |
0.31 |
— |
— |
— |
3 |
15.69 |
Phenylmethanol |
 |
87 |
0.44 |
— |
— |
— |
4 |
16.97 |
1,1,3-Triethoxypropane |
 |
89 |
0.36 |
0.99 |
— |
— |
5 |
19.91 |
Ethyl benzoate |
 |
90 |
6.70 |
4.52 |
— |
— |
6 |
20.08 |
2-Methoxy-2-phenylacetic acid |
 |
87 |
10.02 |
— |
— |
— |
7 |
21.71 |
Benzaldehyde diethyl acetal |
 |
92 |
36.53 |
37.67 |
— |
— |
8 |
22.16 |
Ethyl phenylacetate |
 |
84 |
1.14 |
2.13 |
— |
— |
9 |
23.93 |
5-(Dimethoxymethyl)-2-furanmethanol |
 |
85 |
0.43 |
— |
— |
— |
10 |
24.39 |
(2,2-Diethoxyethyl)benzene |
 |
82 |
2.25 |
1.76 |
— |
— |
11 |
24.94 |
Ethyl-3-phenylpropionate |
 |
90 |
5.72 |
5.11 |
— |
— |
12 |
28.04 |
Ethyl cinnamate |
 |
88 |
1.84 |
3.62 |
— |
— |
13 |
28.65 |
2,3:4,5-Bis-O-(1-methylethylidene)-β-D-arabino-hexos-2-ulo-2,6-pyranose |
 |
87 |
— |
— |
— |
4.30 |
14 |
29.13 |
Phenylalanine ethyl ester |
 |
89 |
5.86 |
— |
6.75 |
14.10 |
15 |
31.30 |
Diacetonefructose |
 |
91 |
— |
— |
76.86 |
69.98 |
3.5 Mechanism of thermal degradation
Based on the degradation products formed in water and ethanol, possible degradation pathways of the two samples are proposed (Scheme 1). For Derivative 1 in water, the degradation processes essentially follow the rules of 1-L-phenylalanine-1-deoxy-D-fructose. The acyclic form of Derivative 1 undergoes cyclization and dehydration followed by the elimination of the amino groups, producing 5-hydroxymethyl-2-furfural (HMF) and phenylalanine ethyl ester. The research of Yaylayan et al.23 and Gottschalk et al.24 has proven this. 5-(Dimethoxymethyl)-2-furanmethanol is likely formed through the condensation of HMF with methanol (Scheme 1). For the degradation of phenylalanine ethyl ester, ethyl cinnamate is produced by the deamination of phenylalanine ethyl ester, and the hydrogenation of this compound generates ethyl-3-phenylpropionate.25 Additionally, the formation of phenylacetaldehyde occurs through the Strecker degradation of phenylalanine interacting with α-dicarbonyl compounds (Scheme 1).26 The degradation product with largest relative contents in water is phenylalanine ethyl ester (93.38% at 120 °C and 38.88% at 180 °C), which is one of the reactants of Derivative 1.
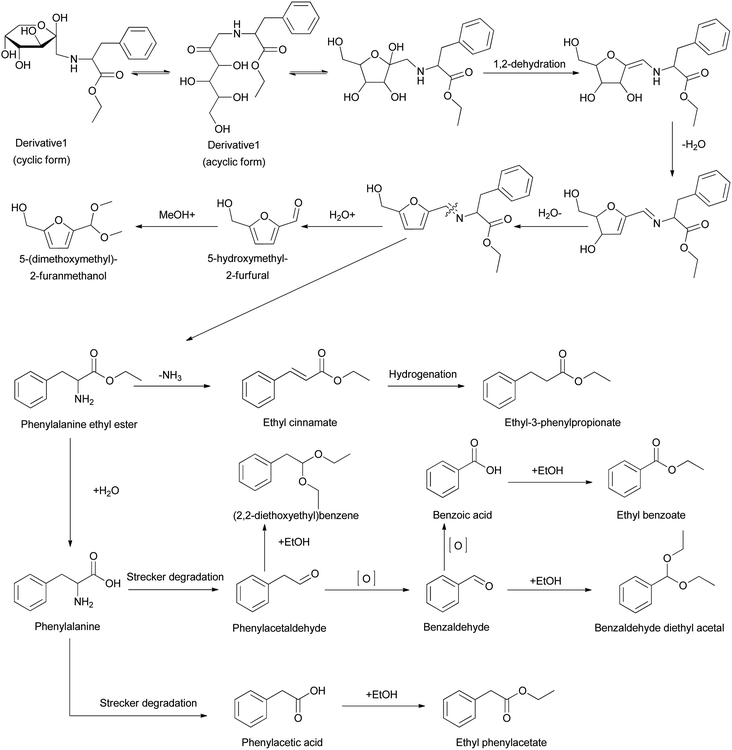 |
| Scheme 1 Proposed degradation mechanisms of Derivative 1 in water and ethanol. | |
For the degradation process in ethanol, more degradation products, especially the compounds containing ethyl group, are generated than that produced in water. The content of phenylalanine ethyl ester is greatly reduced. Instead, the aldol condensation reactions between aldehyde compounds and ethanol generate the acetol compounds, that is, benzaldehyde for benzaldehyde diethyl acetal and phenylacetaldehyde for (2,2-diethoxyethyl)benzene (Scheme 1). Here, benzaldehyde could be formed by the free radical-initiated oxidative cleavage of the carbon–carbon double bond of the enolized phenylacetaldehyde.27,28 Other ethyl group-containing compounds are also formed. For instance, ethyl phenylacetate and ethyl benzoate are produced through the esterification of ethanol and corresponding acids (Scheme 1).29
In the pyrolysis process in air, the degradation mechanism is of complexity. For example, furfural is generated, which is consistent with previous reports.30,31 A possible mechanism is initiated by the oxidation of the C1 or C6 carbon atoms of the glucose moieties, producing aldopentose.32 Other compounds such as toluene and styrene are likely caused by the initial benzylic cleavage followed by the generation of reactive radicals.25
For Derivative 2, the hydrolysis of the C–N bonds in the junction generates the final products, phenylalanine ethyl ester, and diacetonefructose (Scheme S2†). Both elevating the temperature and changing the reaction media could influence the decomposition processes. Specifically, the degradation products in water and ethanol are similar while the relative contents of each compound are different. When pyrolysed in air at 350 °C, abundant phenyl group-containing compounds are generated from phenylalanine ethyl ester (Scheme S2†). Among them, phenethyl acetate with the largest relative content (55.84%) is likely formed from the esterification of acetic acid and phenyl ethanol. Here, acetic acid is reported to generate via the hydrolytic β-dicarbonyl cleavages from 1-deoxy-2,4-hexodiulose,33 one possible intermediate during the pyrolysis process. For phenyl ethanol, it is formed from the hydrogenation of phenylacetaldehyde34 which is a Strecker degradation product of phenylalanine.
4. Conclusions
The thermal behavior and degradation products of Derivative 1 and Derivative 2 were investigated by TG–DTG, DSC, pyrolysis-GC/MS, and GC/MS analysis. TG analysis indicated that Derivative 1 and Derivative 2 have good stability at room temperature, and the Tp values corresponding to the largest mass losses are 132 and 275 °C, respectively. DSC curves demonstrated that the Tpeak values are 132 and 255 °C for Derivative 1 and 226 °C for Derivative 2. Pyrolysis-GC/MS analysis showed that characteristic aroma compounds are produced during the degradation of these samples. Further degradation processes of Derivative 1 in water generate new flavor compounds such as phenylacetaldehyde, whereas the reactions in ethanol produce compounds such as phenylacetaldehyde diethyl acetal through the aldol condensation between phenylacetaldehyde and ethanol. The number and content of degradation products from Derivative 2 are also affected by solvent media. These results show that the degradation media can influence the degradation processes by reacting with the Amadori intermediates. The synthesis of other Amadori derivatives and the effects of organic solvents on their degradation products are under investigation.
Conflicts of interest
There are no conflicts to declare.
Acknowledgements
This research was funded by the Key Science and Technology Program of Science and the Technology Department of Henan Province (No. 132102210042) and the program of Henan Agricultural University (No. 30500569). We would also like to thank Dr Zhiyong Wu from Henan Agricultural University and Dr Yuntao Wang from the Zhengzhou University of Light Industry for data analysis and language modification.
References
- M. N. Lund and C. A. Ray, J. Agric. Food Chem., 2017, 65, 4537–4552 CrossRef CAS.
- C. Rannou, D. Laroque, E. Renault, C. Prost and T. Sérot, Food Res. Int., 2016, 90, 154–176 CrossRef CAS PubMed.
- A. D. Troise and V. Fogliano, Trends Food Sci. Technol., 2013, 33, 63–74 CrossRef CAS.
- V. V. Mossine and T. P. Mawhinney, Adv. Carbohydr. Chem. Biochem., 2010, 64, 291–402 CrossRef CAS PubMed.
- K. Aalaei, M. Rayner and I. Sjöholm, Crit. Rev. Food Sci. Nutr., 2019, 59, 1829–1839 CrossRef CAS PubMed.
- R. Jeantet, T. Croguennec, P. Schuck and G. Brulé, Handbook of Food Science and Technology 1: Food Alteration and Food Quality, Wiley, Hoboken, 2016, pp. 133–157 Search PubMed.
- D. A. Baines, S. Bishara, J. K. Parker and D. S. Mottram, ACS Symp. Ser., 2010, 1024, 63–69 CrossRef.
- F. D. Mills and J. E. Hodge, Carbohydr. Res., 1976, 51, 9–21 CrossRef CAS.
- A. Huyghues-Despointes, V. A. Yaylayan and A. Keyhani, J. Agric. Food Chem., 1994, 42, 2519–2524 CrossRef CAS.
- H. Shigematsu, S. Shibata, T. Kurata, H. Kato and M. Fujimaki, Agric. Biol. Chem., 1977, 41, 2377–2385 CAS.
- G. Vernin, J. Metzger, C. Boniface, M.-H. Murello, A. Siouffi, J.-L. Larice and C. Párkányi, Carbohydr. Res., 1992, 230, 15–29 CrossRef CAS.
- D. Mao, S. Li, D. Mou, G. Peng, X. Bai, C. Jia and J. Yang, Acta Tab. Sin., 2014, 20, 18–29 CAS.
- Y. Ou, H. Ju, C. Jia and D. Mao, Tob. Sci. Technol., 2011, 4, 41–46 Search PubMed.
- D. Mao, H. Ju, D. Mou and X. Bai, Acta Tab. Sin., 2010, 16, 1–9 CAS.
- T. Davidek, N. Clety, S. Aubin and I. Blank, J. Agric. Food Chem., 2002, 50, 5472–5479 CrossRef CAS.
- C.-K. Shu, J. Agric. Food Chem., 1998, 46, 1129–1131 CrossRef CAS.
- T. Hofmann and P. Schieberle, J. Agric. Food Chem., 2000, 48, 4301–4305 CrossRef CAS PubMed.
- D. Wang, Y. Liang, P. Gong and Y. Zhao, Chin. J. Med. Chem., 2002, 12, 94–96 CAS.
- D. Xenakis, N. Moll and B. Gross, Synthesis, 1983, 7, 541–543 CrossRef.
- G. Lu, T.-H. Yu and C.-T. Ho, J. Agric. Food Chem., 1997, 45, 233–236 CrossRef CAS.
- M. Lai, X. Ji, T. Tao, Y. Shan, P. Liu and M. Zhao, J. Therm. Anal. Calorim., 2017, 128, 1627–1638 CrossRef CAS.
- S. Zeng, S. Sun, S. Liu, J. Hu and B. He, J. Therm. Anal. Calorim., 2014, 115, 1049–1056 CrossRef CAS.
- V. A. Yaylayan and P. Sporns, Food Chem., 1987, 26, 283–305 CrossRef CAS.
- A. Gottschalk, Biochem. J., 1952, 52, 455–460 CrossRef CAS PubMed.
- S. Wang, B. Liu and Q. Su, J. Anal. Appl. Pyrolysis, 2004, 71, 393–403 CrossRef CAS.
- V. A. Yaylayan, Food Sci. Technol. Res., 2003, 9, 1–6 CrossRef CAS.
- F. L. Chu and V. A. Yaylayan, J. Agric. Food Chem., 2008, 56, 10697–10704 CrossRef CAS PubMed.
- P. C. Wietstock, T. Kunz and F.-J. Methner, J. Agric. Food Chem., 2016, 64, 8035–8044 CrossRef CAS PubMed.
- T. Hofmann, P. Münch and P. Schieberle, J. Agric. Food Chem., 2000, 48, 434–440 CrossRef CAS.
- Y. Zhang and C.-T. Ho, J. Agric. Food Chem., 1991, 39, 760–763 CrossRef CAS.
- J. Chen and C.-T. Ho, J. Agric. Food Chem., 1998, 46, 1518–1522 CrossRef CAS.
- V. A. Yaylayan and A. Keyhani, J. Agric. Food Chem., 2000, 48, 2415–2419 CrossRef CAS PubMed.
- T. Davidek, S. Devaud, F. Robert and I. Blank, J. Agric. Food Chem., 2006, 54, 6667–6676 CrossRef CAS PubMed.
- S. Zöchling and M. Murkovic, Food Chem., 2002, 79, 125–134 CrossRef.
Footnote |
† Electronic supplementary information (ESI) available: Including 1H NMR and 13C NMR spectra and TLC results of Derivative 1 and Derivative 2 (Fig. S1–S5, Scheme S1), all the total ion chromatograms (TICs) from the solvent-phase and pyrolytic degradations of Derivative 1 and Derivative 2 at different temperatures (Fig. S6–S15), mass spectra of degradation compounds extracted from the TICs (Fig. S16–S38), and the proposed degradation mechanisms of Derivative 2 (Scheme S2). See DOI: 10.1039/c9ra09854b |
|
This journal is © The Royal Society of Chemistry 2020 |
Click here to see how this site uses Cookies. View our privacy policy here.