DOI:
10.1039/D0NH00268B
(Communication)
Nanoscale Horiz., 2020,
5, 1226-1232
An intelligent film actuator with multi-level deformation behaviour†
Received
6th May 2020
, Accepted 10th June 2020
First published on 11th June 2020
Abstract
Smart materials with simply reversible deformation or reconfigurability have shown great potential in artificial muscles, robots, controlled displays, etc. However, the combination of reversible and reconfigured functions in responsive materials, which can endow them with mature and complex actuation performance similar to that of living things, is still a great challenge. In this regard, we report an intelligent graphene oxide (GO)/polyvinylidene fluoride (PVDF) film with reconfigured structures resulting from inner plastic deformation after treatment at elevated temperature (40–80 °C), which simultaneously expresses basically and secondarily reversible deformation ability of its original and reconfigured states in response to external stimuli (e.g. IR light and moisture), respectively. As a result, this film achieves unique multi-level actuation behaviour by combining reversible and reconfigured functions. Based on this, an “Artificial Pupil” with two switchable light penetration modes under the different reconfigured states was designed and developed. Furthermore, many special and reconfigured 3D structures (e.g. cubic boxes, pyramids) have been well explored, which is promising for applications in future materials engineering and biomimetic devices.
New concepts
Smart materials which can reversibly modulate their shapes under multiple stimuli have attracted massive attention, showing great potential in artificial muscles, soft robots, etc. However, most of these actuators collapse into their original configurations after removal of the external stimulus. Also, other actuators with reconfigurability can hardly demonstrate reversible actuation behavior of their reconfigured structures. In this study, we demonstrated an intelligent graphene oxide (GO)/polyvinylidene fluoride (PVDF) bilayer film with multi-level deformation ability of its original and reconfigured structures resulting from inner plastic deformation under elevated temperature treatment (40–80 °C). This bilayer film exhibited basically reversible actuation performance under multiple stimuli, including IR light, temperature and moisture. In its reconfigured structures after elevated temperature and cooling treatment, this smart film still showed secondarily reversible deformation ability under thermal stimulus. As a result, this film achieved unique multi-level actuation behaviour combining reversible and reconfigurable functions. Based on this, complex 3D structures (e.g. cubic boxes, pyramids) and an “artificial pupil” with two light penetration modes were explored in depth and showed promise for applications in biomimetic devices and future smart materials.
|
Introduction
Responsive actuators that can actively modulate their shapes under electrical,1–3 humid,4–6 light7–10 or thermal11–13 stimuli like living things have attracted widespread and continuing attention in artificial muscles,14–17 valves,18 cell capture and release,19 soft robots,20–22etc. Reversible actuators, which exhibit excellent deformation ability, are the main subject of study; however, the established morphologies of these actuators always collapse into their original configurations after the disappearance of the external stimulus.9,10,23–28 Recently, some polymer-based films were reported that can be reconfigured and locked into special three-dimensional (3D) structures after external stimulus treatment due to their advantageous elastic-plastic transformation properties.29–32 However, most of these actuators with reconfigured structures will lose their reversible deformation ability, unlike living things, which can maintain their highly reversible shape-change behaviors even in complex 3D states.29 Therefore, as key characteristics, achieving favorable and controllable reversible deformation ability as well as reconfigured 3D structures for actuators have remained great challenges to date.
Intelligent film actuators based on graphene and polymer composite materials have been well explored due to their excellent stability and deformation ability under multiple stimuli.33–45 In this study, we explored an intelligent film with reconfigured structures that also expresses basically and secondarily reversible deformation ability of its original and reconfigured states, respectively (Fig. 1), achieving multi-level and sophisticated actuation behaviour. This film is composed of a responsive graphene oxide (GO) layer and polyvinylidene fluoride (PVDF) layer; these can easily change shape from flat to bent states reversibly when triggered by a mild thermal stimulus (Tm < 37 °C) (Fig. 1a and b). In addition, elevated temperature Te (40–80 °C) and cooling treatment of this film will cause the elastic-plastic transition of the PVDF layer and fix the whole film into as-designed reconfigured structures (e.g. folding structures) (Fig. 1a and c). More impressively, this reconfigured film exhibits a secondarily reversible deformation (Fig. 1c and d) triggered by Tm towards a sophisticated shape representation (e.g. a “wave” state). Furthermore, the reconfigured film can be further recovered to the original structure with Te thermal treatment and by applying external force again. In addition to an “artificial pupil” that demonstrates various smart light penetration modes under different reconfigured states, many special and reconfigured 3D structures (e.g. cubic boxes, pyramids) have been well explored, which is promising for applications in future intelligent and biomimetic devices.
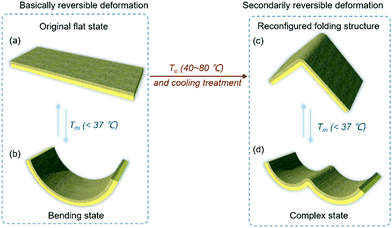 |
| Fig. 1 Schematic of the reconfigurable film with sophisticated multi-level actuation ability. (a and b) Basically reversible deformation of this bilayer film from the original flat state to the bending state under thermal stimulus (<37 °C); (c and d) secondarily reversible deformation of the reconfigured folding film into the complex state under thermal stimulus (<37 °C). The reconfigured folding structure was formed by applying Te (40–80 °C) thermal treatment on the central part of the original film and subsequent cooling treatment. | |
Experimental section
Materials and instruments
All the solvents were of analytical grade and were used as obtained without further purification. Polyvinylidene fluoride was purchased from Alfa Aesar. The graphite power was bought from Qingdao Huatai Lubricant Sealing S&T Co. Ltd (Qingdao, China). Other reagents were obtained from Beijing Chemical Reagent Co. (Beijing, China). Scanning electron microscopy (SEM) images were taken using a field-emission scanning electron microscope (Sirion-200, Japan). Water contact angles were measured using an OCA 15 Plus Contact Angle Meter (Eastern-Dataphy Inc., Beijing, China). Differential scanning calorimetry (DSC) experiments were performed at a heating rate of 20 °C min−1 using a Q2000 DSC (TA Instruments LLC). The storage moduli of the samples were determined using a DMA Q800 (TA Instruments LLC). The coefficients of thermal expansion (CTE) were determined using a TA Instruments TMA Q400. Fourier transform infrared (FTIR) spectroscopy was performed using a UATR 2 infrared spectrometer (PerkinElmer, USA). A high-power laser (24 W, 355 nm) was used to tailor the film into designed structures. IR light was provided by a 200 W infrared lamp. The mechanical analysis was measured by a model 3342 Instron universal testing machine. Both sides of the bilayer film were stuck onto the stretching clamps, and the tearing stress was tested to measure the binding strength between two layers.
GO dispersions and PVDF solutions
An aqueous solution of GO was prepared from 12,000 mesh graphite powder by following a modified Hummers’ method reported previously.46,47 The GO solution was freeze dried to form a lyophilized GO gel. The lyophilized GO gel was then dispersed in DMF under intense ultrasound, forming a GO dispersion with a concentration of 10 mg mL−1. The PVDF solution was prepared by adding 10 g PVDF particles to 100 mL DMF, followed by heating at 150 °C for 3 h under vigorous stirring. PVDFn was formed by simply mixing a DMF solution of GO and a DMF solution of PVDF.
GO/PVDFn bilayer films
First, the PVDFn (n% = mass ratio of GO to PVDF in the PVDFn layer) solution described above was blade-coated on a glass slide. Next, this glass slide was transferred onto a hotplate (60 °C) to evaporate DMF; then, the dry PVDFn film was formed. After being cooled to room temperature, the GO aqueous solution was blade-coated onto the PVDFn film, and the bilayer film of GO/PVDFn was successfully fabricated. For the partial bilayer film, a polyethylene terephthalate (PET) mask template carved by a laser was placed on the PVDFn film. The size and dimensions of the mask can be precisely designed. Then, the aqueous solution of GO was dropped on the PVDFn film covered by the PET mask at room temperature, forming the GO/PVDFn partial bilayer film at the carved-out places of the PET mask. The thickness of the GO layer can be tuned by controlling the thickness of the PET template.
Actuation tests
The RH was controlled using saturated aqueous solutions of CH3COOK, MgCl2, K2CO3, NaBr, NaCl, KCl and K2SO4. The IR light power density was controlled by the distance between the actuator and the infrared lamp. The temperature was precisely regulated by electric heating of the hotplate. The curvature (κ, cm−1) was calculated by the equation below (1-1):where θ is the degree of the bending angle and L is the length of the actuator (cm).
Results and discussion
Chemical structures of the GO/PVDFn films
As shown in Fig. 2a, the bilayer film was prepared by a simple blade-coating method. The PVDF layer was firstly constructed on a flat substrate by blade-coating a solution of PVDF in N,N-dimethyl formamide (DMF) and then drying at 60 °C, followed by deposition of a GO layer. It should be noted that the GO layer could be easily detached from the surface of the PVDF layer because PVDF and GO exhibited opposite hydrophilicities, which heavily restricts the practical applications of this bilayer film. Thus, we firstly modified the PVDF layer with a certain proportion of GO sheets to enhance the adhesion of the two layers. The digital photographs of pure PVDF, modified PVDFn and the corresponding bilayer films are illustrated in Fig. 2b. The addition of GO to PVDF changed the color of the PVDF film from transparent to brown and increased the hydrophilicity of the PVDF layer because of the abundant oxygen-containing functional groups of GO. The contact angle of the PVDFn film decreased from 86.0° to 81.6° with increasing n from 0 to 20 (Fig. S1, ESI†). As shown in Fig. 2c, the band at 1720 cm−1 of PVDF10 in the Fourier transform infrared (FTIR) spectrum was attributed to the carbonyl group of GO, exemplifying the successful addition of GO to the PVDF layer. From the scanning electron microscopy (SEM) images, the addition of GO also increased the roughness of the PVDFn layer (Fig. S2a and b, ESI†). The energy dispersive spectroscope (EDS) mapping image for O element also indicated the uniform distribution of GO in the PVDF10 film (Fig. S2c, ESI†). As a result, the obtained GO/PVDF10 bilayer film exhibited a high binding strength of 187 kPa between the GO layer and PVDF10 layer, about 37 times that of the GO/PVDF0 bilayer film between the GO layer and PVDF0 layer (Fig. S3, ESI†). The enhanced binding strength may be caused by strong interactions between the inner GO sheets, which endowed the bilayer film with stability and availability for further processing (e.g. laser cutting) towards application in devices (Fig. S4, ESI†). Otherwise, the GO and PVDF layers were easily detached by heat generated by the laser, and the bilayer actuator was damaged. In this study, all the PVDFn layers of the bilayer films used during the tests were composed of 10% GO unless specified. From the cross-sectional scanning electron microscopy (SEM) images, the upper layer of the GO layer bound tightly to the underlayer of PVDF10, and the total thickness of this bilayer film was about 8 μm (Fig. 2d). Overall, we successfully fabricated a GO/PVDF10 film with a strongly bonded bilayer structure, which was the basic film used for further applications.
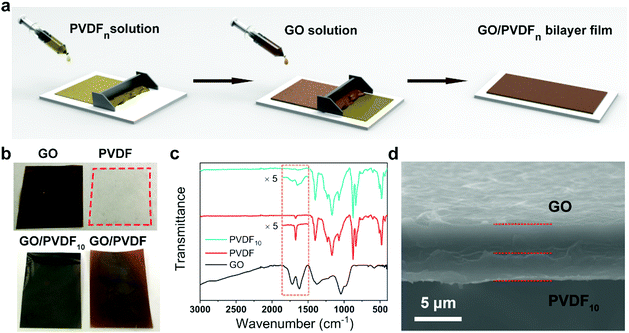 |
| Fig. 2 (a) Schematic of the fabrication process of the GO/PVDFn bilayer actuator. First, the DMF solution of PVDFn was blade coated onto a glass slide and heated to 60 °C to form the PVDFn film. Then, GO aqueous solution was coated onto the PVDFn film, and the bilayer film was obtained. (b) Digital photographs of the GO, PVDF, GO/PVDF10 and GO/PVDF films. (c) FTIR spectra of the GO, PVDF and PVDF10 films. (d) Cross-section scanning electron microscope (SEM) image of a GO/PVDF10 film (scale bar = 5 μm). The total thickness of this bilayer film is 8 μm. | |
Basically reversible actuation of GO/PVDFn films
GO contains abundant oxygen groups, and the adsorption or desorption of water molecules between the interlayers of GO sheets can induce significant volume expansion or contraction of the GO assemblies.48 Based on this, GO exhibited uniform shrinkage performance with increasing temperature due to desorption of water molecules, accompanied with an average negative CTE of −16.4 × 10−6 °C−1 (Fig. 3a). In contrast, PVDF10 showed large thermal expansion behaviour, with an average positive CTE (98.1 × 10−6 °C−1), as calculated from Fig. 3a. Thus, due to its asymmetric structures, the GO/PVDF10 bilayer film can bend towards the GO side under thermal stimulus, derived from the synergistic effect of these two layers. As indicated in Fig. 3b and c, when the temperature increased from 25 °C to 37 °C, the whole film spontaneously bent to the GO side because the GO layer experienced volume contraction while the PVDF10 layer exhibited volume expansion. In addition, the curvature of the GO/PVDF10 film increased linearly with temperature, and the average curvature variation was about 0.417 cm−1 °C−1 (Δcurvature/ΔT). This bilayer film formed a three-quarters circle under 37 °C, and the response time was within 2 s; this indicates the ultrasensitive actuation behaviour of the GO/PVDF10 film. When the temperature returned from 37 °C to 25 °C, this GO/PVDF10 film recovered to the original straight state within 5 s. After alternating the temperature between 25 °C and 35 °C 500 times, the actuation curvature of the actuator was nearly unchanged, exemplifying the excellent reversible deformation stability of the GO/PVDF10 bilayer film under Tm.
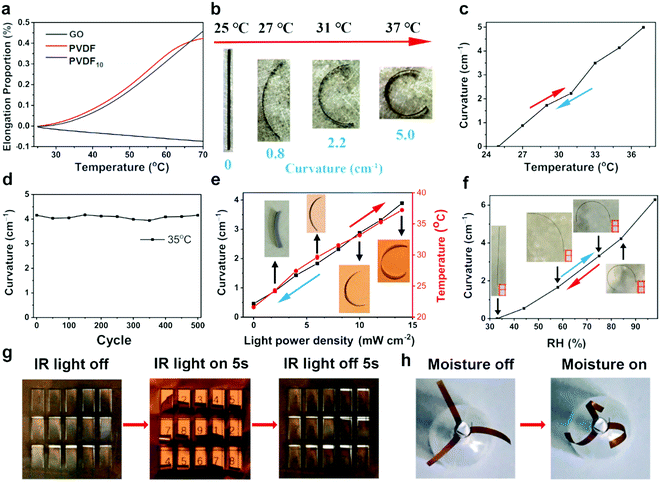 |
| Fig. 3 Reversible actuation of the GO/PVDF10 bilayer film. (a) The elongation proportions of the GO, PVDF and PVDF10 films. (b) Digital photographs and (c) curvatures of the GO/PVDF10 actuator at different temperatures. (d) Cyclic tests of the GO/PVDF10 actuator between 35 °C and 25 °C at the RH of 18.8%. (e) Temperatures and curvatures of the GO/PVDF10 actuator upon irradiation under IR light with different light power densities (RH = 20%). (f) The curvatures of the GO/PVDF10 actuator at different RHs. (g) The IR light-controlled password display formed by engraving 15 individual rectangle-shaped micro-actuators (10 × 3 mm) on the GO/PVDF10 bilayer film. (h) An anticlockwise spiral flower using three GO/PVDF10 strip-petals (10 × 1 mm) can be activated by moisture. | |
In addition to its thermal-responsive actuation, benefiting from its brown appearance due to the incorporation of GO into the transparent PVDF, this GO/PVDF10 film can absorb infrared (IR) light and convert the light energy into thermal energy, which allows the reversible actuation to be remotely controlled by IR light. As shown in Fig. 3e, the temperature and curvatures of the GO/PVDF10 actuator increased linearly with the power density of the light. Due to the synergistic effect of the GO and PVDF10 layers under thermal effects, GO/PVDF10 bent to the GO side, with the largest curvature of 3.89 cm−1 at an IR light intensity of 14 mW cm−2. After the removal of IR light, the GO/PVDF10 actuator could recover to the original flat state, indicating reversible actuation behaviour of this bilayer film. Furthermore, the GO/PVDF10 film can not only respond to heat and light, but also to moisture (Fig. 3f). With increasing relative humidity (RH), GO with abundant oxygen-containing groups adsorbs water molecules into its interlayers and shows large volume expansion (Fig. S5, ESI†). However, the PVDF layer is relatively inert to moisture changes. Therefore, the GO/PVDF10 actuator bent to the PVDF10 side under high RH (80%), with the largest curvature of 6.3 cm−1. The bending direction of the GO/PVDF10 actuator triggered by high RH is opposite to that under thermal or IR stimulus, and the bending direction can be controlled easily by alternating the external stimuli (Fig. S5, ESI†). The above results exemplify that the GO/PVDF10 film demonstrates basically reversible deformation ability under thermal, light or moisture stimulus.
Based on the reversible actuation, this GO/PVDF10 film can be easily constructed into many smart devices. As a demonstration, an IR-light remotely controlled password display was established by engraving 15 individual rectangle-shape micro-actuators (10 × 3 mm) on the GO/PVDF10 film. When IR light (14 mW cm−2) was turned on, the micro-actuators curled, and the passwords covered by the film were revealed (Fig. 3g) within only 5 seconds. Similarly, after the IR light was turned off, these micro-actuators returned to their original state, and all the passwords were concealed. Furthermore, an artificially IR-triggered flower bloomed by curvature of 8 GO/PVDF10 strip-petals to the outside when the IR light was turned on (Fig. S6, ESI†). The strip-petals closed after the light was turned off. This IR light-triggered behaviour of our actuator was similar to that of some sunflowers in nature, which open after the sun rises and close after the sun goes down. The GO/PVDF10 film strip-petals can also be controlled by moisture, and the blooming direction can be adjusted by tuning the fixed angle of the strips. As shown in Fig. 3h, we further developed an anticlockwise spiral flower using three GO/PVDF10 strip-petals. This flower showed open or spirally closed states in dry or wet environments, respectively.
Secondarily reversible actuation of the GO/PVDFn films
In addition to its basic reversible deformation, this GO/PVDF10 film can be reconfigured into fixed structures by elevated temperature Te (40–80 °C) and natural cooling treatment. As shown in Fig. 4a, when the whole film was heated to 50 °C and then cooled to room temperature, the structure of the GO/PVDF10 film was transformed into a reconfigured state of oppositely bending (o-bending) to the PVDF10 side (Fig. 4a). Unlike the reversible shape change under Tm stimulus (<37 °C), this reconfigured bending state of the GO/PVDF10 film was fixed, and the structure was locked at room temperature after releasing the external stimulation. In this structural reconfiguration of the GO/PVDF10 film, the storage modulus of the PVDF10 layer decreased and PVDF10 demonstrated plastic deformation, mainly at high temperatures (Te: 40–80 °C) (Fig. 4b). Meanwhile, shrinkage of the GO layer occurred with increasing temperature. As a result, the plastic PVDF10 layer could be forced to shrink due to the stress caused by the GO layer, and the GO layer played a shaping role in the whole film towards uniform shrinkage and the final flat state (Fig. S7, ESI†). During natural cooling (from Te to 25 °C), the PVDF10 layer recovered its storage modulus gradually and shrank because of its positive CTE. However, the GO layer expanded continuously as the temperature decreased. In consequence, the whole film bent to the PVDF10 side, resulting in the reconfigured and o-bending behaviour of the GO/PVDF10 film (Fig. S7, ESI†). In addition, the differential scanning calorimeter (DSC) curves of PVDF10 showed that there was no crystal phase transition of PVDF10 below 120 °C, indicating that the reconfigurable phenomenon was not caused by crystal phase transition (Fig. 4c). Therefore, the elastic-plastic transition properties of PVDF10 and the negative CTE of GO promoted reconfigurability of the GO/PVDF10 film to the o-bending state. This GO/PVDF10 film can also be returned to the initial straight state at room temperature with the assistance of external forces and upon being overheated to Te, which can restore the PVDF10 layer to the original state by elastic-plastic transition. Moreover, the curvature of the o-bending GO/PVDF10 film is tunable by controlling the elevated temperature Te (Fig. 4d). For instance, the GO/PVDF10 film bent to the PVDF10 side with a curvature of 5.5 cm−1 at Te = 40 °C. When Te = 80 °C, the curvature of the o-bending GO/PVDF10 film was ∼14 cm−1. Similarly, upon Te treatment on part of the GO/PVDF10 film followed by cooling at room temperature, the GO/PVDF10 film showed partial o-bending behaviour and was reconfigured into an as-designed folding structure (Fig. 4e).
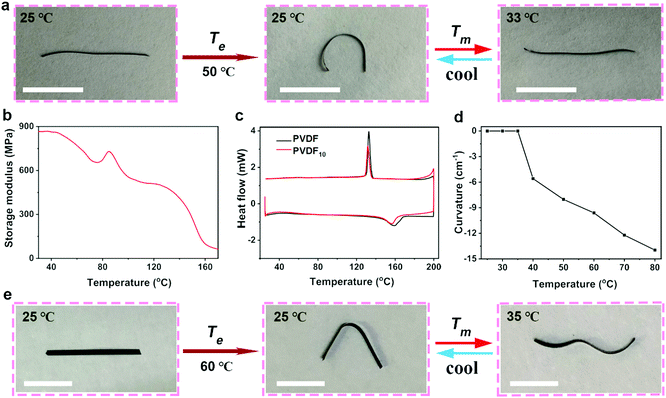 |
| Fig. 4 (a) The reconfigured bending-state of GO/PVDF10 (Te = 50 °C) and its secondarily reversible deformation (33 °C). The size of this bilayer actuator is 10 × 1 mm. Scale bar: 5 mm. (b) The storage modulus of the PVDF10 film at different temperatures. (c) DSC curves of the PVDF and PVDF10 films. (d) Curvature of the GO/PVDF10 actuator after being heated to different temperature and cooling to room temperature. (e) The reconfigured folding-state GO/PVDF10 film (Te = 60 °C) and secondarily reversible deformation under 35 °C. The size of this bilayer actuator is 10 × 1 mm. Scale bar: 5 mm. | |
More importantly, the reconfigured and o-bending state GO/PVDF10 showed second-level reversible deformation ability by Tm stimulation (Fig. 4a and e), which is unique compared with other reversible or reconfigured films with only a single function. As shown in Fig. 4a, at the stimulus Tm (33 °C), the GO layer shrank and the PVDF10 layer expanded so that the o-bending state GO/PVDF10 film changed into a second-straight state. This state was different from the originally straight state at room temperature; as the temperature decreased, the second-straight GO/PVDF10 film reversibly changed its deformation into the o-bending state again (Fig. S7, ESI†). Similarly, the reconfigured folding GO/PVDF10 film showed a reversible second-level and sophisticated “wave” deformation under Tm (Fig. 4e) because of the asymmetric effect between GO and the PVDF10 layer. As a result, the GO/PVDF10 film achieved multi-levelly reversible actuation ability with reconfigured deformation behaviour.
Reconfigured three-dimensional structures
Due to its outstanding reconfigurable behavior, 2D films of GO/PVDF10 can construct fixed and complex 3D structures at room temperature. As shown in Fig. 5a, by constructing GO/PVDF10 structures as hinges on the crisscross PVDF10 film, the bilayer part could be reconfigured, and the whole film formed a cube after treatment with Te (60 °C) and cooling. The angles of the GO/PVDF10 hinges can also be controlled precisely by tuning the width of the GO layer and evaluated temperature Te (Fig. S8, ESI†). As a result, a designed triangular pyramid with 60-degree angles between two sides can be obtained by constructing a GO/PVDF10 bilayer structure with hinges within a triangle PVDF10 film and higher Te (70 °C) treatment. Further, a smart “artificial pupil” that demonstrated two switchable light penetration modes was developed. As shown in Fig. 5b, in the first mode, the 12 GO/PVDF10 valves opened by IR stimulus with an increscent light-passing area. In dark conditions, this “artificial pupil” closed and rested. Benefiting from the reconfigurability and secondary deformation ability of GO/PVDF10, this “artificial pupil” could be reconfigured into the second mode after Te and cooling treatment, in which 12 GO/PVDF10 valves opened with the reduction of IR intensity and returned to the closed state under strong irradiation. Also, these two modes are freely switchable by reconfiguring the GO/PVDF10 valve structures, showing promising multimodal deformations. Furthermore, the 3D “artificial pupil” showed almost no difference after 20 actuation cycles under two light penetration modes, demonstrating the favorable durability of this GO/PVDF10 film in 3D structures.
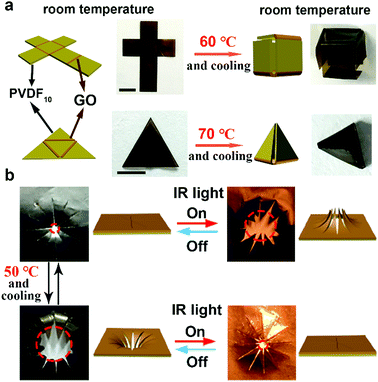 |
| Fig. 5 (a) Representative examples of the reconfigured 3D structures by GO/PVDF10 hinges after Te heating and cooling. The width of the GO layer was 1.5 mm. Scale bar: 5 mm. (b) Two switchable light penetration modes of a smart and reconfigured “artificial pupil” prepared from the GO/PVDF10 film (6 × 6 mm). | |
Conclusions
In conclusion, an intelligent bilayer film with multi-level deformation behaviour under multiple stimuli, including temperature, moisture and IR light, was prepared by compositing the GO layer and PVDF10 layer. The reconfigured behaviour of this intelligent film resulted from plastic deformation of the PVDF10 layer under Te treatment (40–80 °C). Notably, the GO/PVDF10 bilayer actuator in both the original and reconfigured states exhibited reversible and sensitive actuation performance, with excellent stability and durability under multiple stimuli (<37 °C), exemplifying multi-level deformation ability and a combination of reversible and reconfigured functions. Based on this, many complex and special 3D structures at room temperature were designed and fabricated using the GO/PVDF10 bilayer film. Furthermore, this bilayer film was devised to exploit a smart “artificial pupil” with two switchable light penetration modes; thus, it is highly attractive for potential applications in biomimetic devices, etc.
Conflicts of interest
There are no conflicts to declare.
Acknowledgements
This work was supported by the National Science Foundation of China (No. 21805160, 51673026 and 21674056), National Key R&D Program of China (2016YFA0200200 and 2017YFB1104300), Tsinghua University Initiative Scientific Research Program (2019Z08QCX08), and Tsinghua-Foshan Innovation Special Fund (2018THFS0412), NSFC-MAECI (51861135202) and NSFC-STINT (21911530143). This work is also supported by a grant from the Institute for Guo Qiang (2019GQG1025), Tsinghua University.
References
- R. Pelrine, R. Kornbluh, Q. B. Pei and J. Joseph, Science, 2000, 287, 836 CrossRef CAS PubMed.
- J. Kim, J.-H. Jeon, H.-J. Kim, H. Lim and I.-K. Oh, ACS Nano, 2014, 8, 2986 CrossRef CAS PubMed.
- B. Xue, M. Qin, T. Wang, J. Wu, D. Luo, Q. Jiang, Y. Li, Y. Cao and W. Wang, Adv. Funct. Mater., 2016, 26, 9053 CrossRef CAS.
- G. Xu, J. Chen, M. Zhang and G. Shi, Sens. Actuators, B, 2017, 242, 418 CrossRef CAS.
- Y. Qiu, M. Wang, W. Zhang, Y. Liu, Y. V. Li and K. Pan, Nanoscale, 2018, 10, 14060 RSC.
- P. Zhou, L. Chen, L. Yao, M. Weng and W. Zhang, Nanoscale, 2018, 10, 8422 RSC.
- M. Yamada, M. Kondo, J. Mamiya, Y. Yu, M. Kinoshita, C. J. Barrett and T. Ikeda, Angew. Chem., Int. Ed., 2008, 47, 4986 CrossRef CAS PubMed.
- Y. Tai, G. Lubineau and Z. Yang, Adv. Mater., 2016, 28, 4665 CrossRef CAS PubMed.
- Z. Wang, K. Li, Q. He and S. Cai, Adv. Mater., 2019, 31, 1806849 CrossRef.
- Y. L. Zhang, Y. Q. Liu, D. D. Han, J. N. Ma, D. Wang, X. B. Li and H. B. Sun, Adv. Mater., 2019, 31, 1901585 CrossRef PubMed.
- M. Beregoi, A. Evanghelidis, V. C. Diculescu, H. Iovu and I. Enculescu, ACS Appl. Mater. Interfaces, 2017, 9, 38068 CrossRef CAS PubMed.
- A. Baumann, A. Sanchez-Ferrer, L. Jacomine, P. Martinoty, V. Le Houerou, F. Ziebert and I. M. Kulic, Nat. Mater., 2018, 17, 523 CrossRef CAS PubMed.
- H. Tian, Z. Wang, Y. Chen, J. Shao, T. Gao and S. Cai, ACS Appl. Mater. Interfaces, 2018, 10, 8307 CrossRef CAS PubMed.
- S. M. Mirvakili and I. W. Hunter, Adv. Mater., 2018, 30, 201704407 CrossRef.
- M. Rajagopalan and I. K. Oh, ACS Nano, 2011, 5, 2248 CrossRef CAS PubMed.
- K.-Y. Chun, S. H. Kim, M. K. Shin, C. H. Kwon, J. Park, Y. T. Kim, G. M. Spinks, M. D. Lima, C. S. Haines, R. H. Baughman and S. J. Kim, Nat. Commun., 2014, 5, 3322 CrossRef PubMed.
- E. Acome, S. K. Mitchell, T. G. Morrissey, M. B. Emmett, C. Benjamin, M. King, M. Radakovitz and C. Keplinger, Science, 2018, 359, 61 CrossRef CAS PubMed.
- E. Lee, H. Lee, S. I. Yoo and J. Yoon, ACS Appl. Mater. Interfaces, 2014, 6, 16949 CrossRef CAS PubMed.
- W. Li, J. Wang, J. Ren and X. Qu, Adv. Mater., 2013, 25, 6737 CrossRef CAS PubMed.
- C. Lekakou, Y. Elsayed, T. Geng and C. M. Saaj, Adv. Eng. Mater., 2015, 17, 1180 CrossRef CAS.
- L. Hines, K. Petersen, G. Z. Lum and M. Sitti, Adv.
Mater., 2017, 29, 1603483 CrossRef.
- A. Mourran, H. Zhang, R. Vinokur and M. Möller, Adv. Mater., 2017, 29, 201604825 CrossRef.
- W. Xu, Z. Qin, C. T. Chen, H. R. Kwag, Q. Ma, A. Sarkar, M. J. Buehler and D. H. Gracias, Sci. Adv., 2017, 3, 1701084 CrossRef.
- C. J. Wang, K. Sim, J. Chen, H. Kim, Z. Y. Rao, Y. H. Li, W. Q. Chen, J. Z. Song, R. Verduzco and C. J. Yu, Adv. Mater., 2018, 30, 9 Search PubMed.
- L. D. Zhang, P. Naumov, X. M. Du, Z. G. Hu and J. Wang, Adv. Mater., 2017, 29, 8 Search PubMed.
- J. H. Na, A. A. Evans, J. Bae, M. C. Chiappelli, C. D. Santangelo, R. J. Lang, T. C. Hull and R. C. Hayward, Adv. Mater., 2015, 27, 79 CrossRef CAS PubMed.
- J. Zheng, P. Xiao, X. Le, W. Lu, P. Theato, C. Ma, B. Du, J. Zhang, Y. Huang and T. Chen, J. Mater. Chem. C, 2018, 6, 1320 RSC.
- Z. Tang, Z. Gao, S. Jia, F. Wang and Y. Wang, Adv. Sci., 2017, 4, 1600437 CrossRef.
- Y. Yang, E. M. Terentjev, Y. Wei and Y. Ji, Nat. Commun., 2018, 9, 1906 CrossRef PubMed.
- X. Wang, X. Guo, J. Ye, N. Zheng, P. Kohli, D. Choi, Y. Zhang, Z. Xie, Q. Zhang, H. Luan, K. Nan, B. H. Kim, Y. Xu, X. Shan, W. Bai, R. Sun, Z. Wang, H. Jang, F. Zhang, Y. Ma, Z. Xu, X. Feng, T. Xie, Y. Huang, Y. Zhang and J. A. Rogers, Adv. Mater., 2019, 31, 1805615 CrossRef PubMed.
- M. Lahikainen, H. Zeng and A. Priimagi, Nat. Commun., 2018, 9, 4148 CrossRef PubMed.
- Z. Qian and D. S. Ginger, J. Am. Chem. Soc., 2017, 139, 5266 CrossRef CAS PubMed.
- J. J. Liang, Y. F. Xu, Y. Huang, L. Zhang, Y. Wang, Y. F. Ma, F. F. Li, T. Y. Guo and Y. S. Chen, J. Phys. Chem. C, 2009, 113, 9921 CrossRef CAS.
- Y. Huang, J. Liang and Y. Chen, J. Mater. Chem., 2012, 22, 3671 RSC.
- J. Liu, Z. Wang, X. J. Xie, H. H. Cheng, Y. Zhao and L. T. Qu, J. Mater. Chem., 2012, 22, 4015 RSC.
- J. Kim, J. H. Jeon, H. J. Kim, H. Lim and I. K. Oh, ACS Nano, 2014, 8, 2986 CrossRef CAS PubMed.
- A. R. Liu, W. J. Yuan and G. Q. Shi, Thin Solid Films, 2012, 520, 6307 CrossRef CAS.
- J. J. Liang, L. Huang, N. Li, Y. Huang, Y. P. Wu, S. L. Fang, J. Y. Oh, M. Kozlov, Y. F. Ma, F. F. Li, R. Baughman and Y. S. Chen, ACS Nano, 2012, 6, 4508 CrossRef CAS PubMed.
- Y. Hu, T. Lan, G. Wu, Z. C. Zhu and W. Chen, Nanoscale, 2014, 6, 12703 RSC.
- X. W. Yu, H. H. Cheng, M. Zhang, Y. Zhao, L. T. Qu and G. Q. Shi, Nat. Rev. Mater., 2017, 2, 13 Search PubMed.
- H. H. Cheng, Y. X. Huang, G. Q. Shi, L. Jiang and L. T. Qu, Acc. Chem. Res., 2017, 50, 1663 CrossRef CAS PubMed.
- H. H. Cheng, Y. X. Huang, Q. L. Cheng, G. Q. Shi, L. Jiang and L. T. Qu, Adv. Funct. Mater., 2017, 27, 8 Search PubMed.
- X. J. Xie, L. T. Qu, C. Zhou, Y. Li, J. Zhu, H. Bai, G. Q. Shi and L. M. Dai, ACS Nano, 2010, 4, 6050 CrossRef CAS PubMed.
- G. C. Xu, J. Chen, M. Zhang and G. Q. Shi, Sens. Actuators, B, 2017, 242, 418 CrossRef CAS.
- G. C. Xu, M. Zhang, Q. Q. Zhou, H. W. Chen, T. T. Gao, C. Li and G. Q. Shi, Nanoscale, 2017, 9, 17465 RSC.
- J. Chen, B. Yao, C. Li and G. Shi, Carbon, 2013, 64, 225 CrossRef CAS.
- J. Chen, Y. Li, L. Huang, C. Li and G. Shi, Carbon, 2015, 81, 826 CrossRef CAS.
- J. Zhu, C. M. Andres, J. Xu, A. Ramamoorthy, T. Tsotsis and N. A. Kotov, ACS Nano, 2012, 6, 8357 CrossRef CAS PubMed.
Footnotes |
† Electronic supplementary information (ESI) available: Fig. S1–S8. See DOI: 10.1039/d0nh00268b |
‡ Authors contribute to this paper equally. |
|
This journal is © The Royal Society of Chemistry 2020 |
Click here to see how this site uses Cookies. View our privacy policy here.