DOI:
10.1039/C9ME00166B
(Review Article)
Mol. Syst. Des. Eng., 2020,
5, 419-432
Interfacial solar evaporation for water production: from structure design to reliable performance
Received
28th November 2019
, Accepted 20th January 2020
First published on 20th January 2020
Abstract
Interfacial solar evaporation has emerged as a convenient and efficient strategy for harvesting solar energy, and shows promising application in the fields of water purification, desalination, and atmospheric water harvesting. During the last decade, advanced photothermal materials as well as innovative structural design for preparing high-performance solar evaporators have been widely reported. In this review article, we firstly conclude the basic principle of design and fabrication of current solar evaporators. In the second section, we aim to propose some existing issues that hamper the reliable performance of solar evaporation systems, including the floating stability, anti-scaling ability, heat management, integrated system design, etc. Finally, the prospect of future development of such solar evaporation systems is proposed. This review article is focused on the key problems for real-world application of solar steam generation at air/water interfaces, and could stimulate new thinking about evaporator design and serve as an instruction for future investigations.
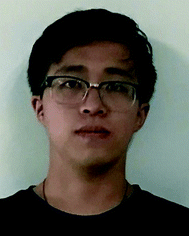 Haoyu Bai | Mr. Haoyu Bai is currently a postgraduate student at the School of Chemical Engineering and Technology, Tianjin University, China. In 2019, he received his bachelor's degree in Molecular Science and Engineering, which was jointly developed by Tianjin University and Nankai University. He joined Prof. Cao's lab in 2017, and his current research interests include fluid manipulation with bio-inspired interfaces. |
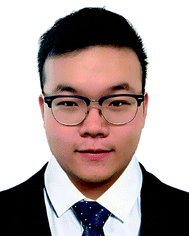 Tianhong Zhao | Mr. Tianhong Zhao is currently a research assistant at the School of Chemical Engineering and Technology, Tianjin University, China. He graduated from Tianjin University in 2019, and then joined Prof. Cao's lab. His current research interests focus on responsive materials for liquid transport. |
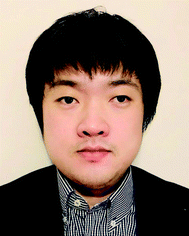 Moyuan Cao | Dr. Moyuan Cao is currently an Associate Professor at the School of Chemical Engineering and Technology, Tianjin University, China. He received his B. Eng. degree (2010) and M. Sc. degree (2013) in Macromolecular Science and Engineering from Zhejiang University, China. In 2016, he received his PhD degree in Materials Science under the supervision of Prof. Lei Jiang at Beihang University. He is also a member of the State Key Laboratory of Chemical Engineering (Tianjin). He has published over 40 academic papers with an h-index of 22. His present scientific interests are focused on the design of fluid manipulating interfaces with smart functions, including (1) self-propelled fluid delivery, (2) underwater microbubble control, and (3) hydrophilic/hydrophobic cooperative Janus interfaces. |
Design, System, Application
Photothermal materials are designed to float on water surfaces for enhanced interfacial solar steam generation. The total system of this interfacial solar evaporator is based on efficient solar harvesting, steam generation, vapor condensation, and water collection. The corresponding system is able to reduce and then solve the water crisis around world, especially for the people living in seaside areas and on ships. This review aims to point out some key problems for real-world application of solar evaporation systems, and could stimulate new thinking about system optimization and serve as an instruction for future investigations in this field.
|
1. Introduction
Solar energy has been considered as the best answer to the global energy crisis.1 Therefore, numerous research studies have been focused on the harvesting of solar energy for human beings such as the use of solar cells,2–4 photocatalysis,5,6etc. In nature, the most direct method for harnessing solar radiation depends on the water–vapor conversion, including the transpiration of plants7 and the evaporation of surface water.8 Driven by solar irradiation, salty seawater can be vaporized into atmospheric water, and the desalinated water can be recycled as rain and dew.9 This kind of solar evaporation process happens every day; however, the efficiency of water production is restricted by the light absorption of water and the specific weather. In general, light can penetrate the sea surface and heat the total water a few meters thick.10 To our best knowledge, the evaporation process only occurs at the air/water interface, indicating that this kind of natural heat process could be inefficient. If the solar irradiation can be remarkably localized at the interface for heating a thin layer of surface water, the actual efficiency of solar evaporation will be largely enhanced (Fig. 1).
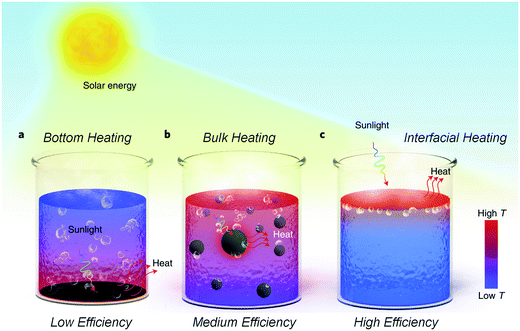 |
| Fig. 1 Different strategies for liquid heating using photothermal materials.10 (a) Bottom heating, (b) bulk heating with suspended particles, and (c) interfacial heating with floatable substrates. | |
The development of advanced materials offers great opportunities to optimize the current system of solar-driven water purification.11 In order to improve the performance of solar-assisted water production, more than 1000 papers have been published to report this interfacial solar steam generation by describing versatile materials and different designs.12 With respect to the materials selection, scientists have focused on photothermal materials with high efficiency and a broad absorption spectrum,13–15 such as metallic nanomaterials,16–18 carbon-based substrates,19,20 conductive polymers,21etc. The light-to-heat conversion of these materials relies on the photon capture and electronic transitions via the surface plasma resonance or the specific valence band structures. On the other hand, the rational design of an evaporator structure can further enhance the efficiency of steam generation through the concentration of light and the restriction of heat loss.22 As a result, efficient photothermal materials and well-structured evaporating interfaces cooperatively contribute to the promising solar evaporation process. Compared with the other technologies for water production, the solar evaporation process exhibits obvious advantages such as low cost, energy independence, high adaptability, etc. Nowadays, reverse osmosis and electrodialysis have been applied in drinking water production for both industrial and household usage. However, the cost of membranes and equipment could hamper their application in underdeveloped countries. Furthermore, these modern processes should be powered by electricity, which is inferior to the solar evaporation.
A number of review articles have already presented the design, fabrication, and performance of solar evaporators, especially in the materials preparation and the working principle.23–26 Detailed discussion and introduction of photothermal materials and their application in solar evaporation can be found in other reviews.27,28 In this review, from the view of solving real-world issues, we focus on some key factors for designing reliable evaporators, including light localization, anti-scaling, long-term stability, cost performance, etc. We aim to provide valuable information on how to achieve the practical application of solar evaporation. In the first section, two types of interfacial solar evaporators are briefly introduced for better understanding of the process. In the second section, the major problems that hamper the practical application of evaporators are discussed, and the potential solution in previous reports is displayed. In the last section, the prospect of future solar evaporators and the possible developing direction of solar steam generation are proposed. We envision that this review can reveal important points for improving the current systems of solar evaporation as well as stimulating new ideas in this field.
2. Typical structures of interfacial solar evaporators
The structure of solar evaporators strongly influences their performance and function by manipulating the location of the photothermal interface. The most direct method for heating the air–water interface depends on the floating light-absorbing substrates, namely the direct contact mode (Fig. 2a). The floating particle or sheet can concentrate the heat at the air–water interface, promoting an improved evaporation efficiency. In this type of evaporator, the evaporation process occurs at the original air–water interface, which means that the evaporating interface and the water surface are at the same height. In comparison, for the better concentration of solar radiation, the evaporating interface can be separated from the original water surface. In the indirect contact mode (Fig. 2b), liquid can be lifted to a higher interface for vaporizing through a water pumping process. One of the advantages of this mode is that the downward heat transfer can be largely resisted, resulting in an ultrahigh efficiency of steam generation. The detailed examples and the pros and cons are discussed in the following section.
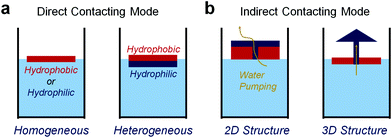 |
| Fig. 2 The classification of current solar evaporators. (a) Direct contact mode with homogeneous or heterogeneous structures. (b) Indirect contact mode with 2D or 3D hierarchical structures. | |
2.1. Direct contact mode
Aquatic plants are able to harvest sunlight by floating on the water surface. Inspired by these natural examples, the most convenient method for localizing the solar energy is to use a floatable object with effective light absorption. In 2011, Prof. Huanting Wang's group reported that hydrophobic carbon microspheres can float on the water surface and accelerate the water evaporation.29 After the solar evaporation, the recycling of the carbon microspheres is based on magneto-controllability. This pioneering work demonstrated the effectiveness of interfacial solar evaporation via floatable particles. Another typical evaporator in direct contact mode is a float monolith with considerable water channels. In 2014, Prof. Gang Chen's group reported that a carbon foam-based sheet with a porous structure largely enhances the water steam generation (Fig. 3a).30 After absorbing solar radiation, the thermal energy will be confined to the water/foam interface for rapid steam generation. This pioneering work demonstrated a new way to generate steam with a photothermal floatable sheet. For membrane-like two-dimensional substrates, Liu et al. fabricated an efficient evaporation system inspired by modern plants (Fig. 3b).31 They used an air-laid paper-supported gold nanoparticle film to localize plasmonic heating near the water surface without increasing the temperature of bulk water. Benefitting from its high productivity with minimum extra installation cost, this design could have potential value for commercial evaporation systems.
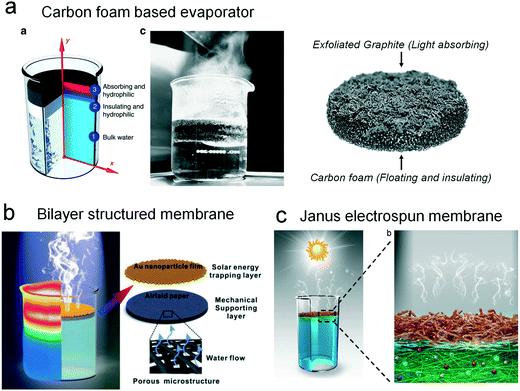 |
| Fig. 3 Typical evaporators in direct contact mode. (a) Carbon foam-based solar steam generator.30 (b) Janus evaporator that is composed of gold nanoparticles and air-laid paper.31 (c) Salt rejecting evaporator with a hydrophobic/hydrophilic binary structure.32 | |
2.2. Indirect contact mode
Although the direct contact evaporators show an obvious function of localizing the solar irradiation, the efficiency of light-to-steam conversion may not be satisfactory due to the inevitable heat loss. In most reports, the actual efficiency of an evaporator in the direct contact mode might not be satisfactory. The major disadvantage of the direct contact mode can be attributed to the heat dissipation, i.e., the heat transfer from the water surface to the bulk water. To lower the undesired heat loss, indirect contact evaporators are developed. In this mode, the evaporating interface is separated from the bulk water, which maximally resists the downward heat transfer.33 In addition, the water pumping process should be incorporated into the system, and the selected light-absorbing substrates ought to be hydrophilic enough.34 During the evaporation process, the bulk water was spontaneously lifted to the evaporating surface through the capillary effect, and then the pumped water layer can be efficiently vaporized.35 In 2016, Li et al. reported a direct assembly of a graphene oxide-based photothermal film, water pumping fabrics, and a polystyrene foam (Fig. 4).36 Compared with direct contact evaporators, the downward heat loss of this assembly was significantly suppressed by the floatable foam. The resulting evaporation efficiency was increased from 30% to 80% by using this innovative design. Li et al. displayed a 3D-printed carbon-based evaporator with all-in-one water production.37 The bulk water was efficiently lifted to a higher surface through the capillary effect of the side wall. The separation of bulk water and the evaporating interface largely reduced the desired heat transfer. Therefore, the final photothermal conversion efficiency reached 85.6%. Hydrophilic materials can also achieve the separation of the evaporating interface via wicking. Prof. Guihua Yu's group reported that an ultra-high efficiency of solar evaporation (94%) can be realized by using a hierarchical porous structured hydrogel.38 The downward heat transfer is strongly suppressed by the confined water, resulting in the improved steam generation.
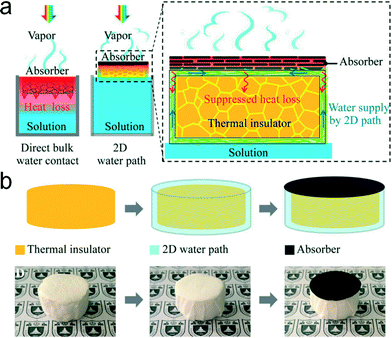 |
| Fig. 4 Typical evaporator in indirect contact mode.36 (a) The comparison and the mechanism of the interfacial solar evaporator. The heat loss is strongly suppressed by the insulator, and water can be continuously pumped to the evaporating interface through the 2D path. (b) The rapid fabrication of the evaporator in indirect contact mode. | |
Most of the previous evaporators can be classified into two kinds, i.e., direct and indirect contact modes. In brief comparison, evaporators in direct contact mode possess a simplified structure and a compact volume. In contrast, evaporators in indirect contact mode always give a higher efficiency of solar utilization, originating from the optimized heat localization. After the informative introduction of the evaporator design, the major challenges of real-world application of solar evaporators will be discussed in the next section.
3. Key challenges for the reliable performance of solar evaporation
3.1. The interfacial localization of the evaporator
The interfacial heating process can be recognized as the indispensable and decisive factor for the enhancement of the evaporation rate. Therefore, the first principle for designing a solar evaporator is to localize the energy at the interface. Floating objects with light absorbing ability are able to harvest solar energy and elevate the surface temperature itself.39 After the heat transfer from the floating object to the water surface, the evaporation can be accelerated. To this end, the reliable floatability of solar evaporators is highly desired. Hydrophobic and superhydrophobic materials possess remarkable interfacial floatability due to their superior water repellency.40–42 In nature, aquatic plants, such as lotus and water lily, can float in pools via surface hydrophobicity.43,44 In 2015, our group demonstrated that a superhydrophobic black gauze can float on the water surface and enhance the water evaporation under irradiation (Fig. 5a).45 Although the light-to-heat conversion of this work might not be ideal, the utilization of a floatable superhydrophobic sheet with self-cleaning ability can give a nice answer to interfacial heat localization. Zhang et al. reported a self-healing membrane which was based on polypyrrole-coated stainless steel mesh.46 The deposited polypyrrole that is a valid photothermal material possesses prominent self-healing ability and hydrophobicity. Due to its promising hydrophobicity, this sheet is capable of localizing sunlight at the water–air interface, and the solar energy was allowed to heat the interfacial water directly. Aside from film-shape materials, Hu et al. further reported that graphene oxide-based aerogels can achieve highly efficient solar steam generation under one-sun solar radiation (Fig. 5b).47 This is the first time to apply graphene oxide-based aerogels in the field of solar steam generation. Due to their low density and porous structure, the reported aerogels are capable of floating on the top surface of the bulk water, resulting in a high light-to-heat conversion. This work offered free-floating aerogels with high desalination performance and prominent solar spectrum absorption and they were expected to provide a wide range of applications.
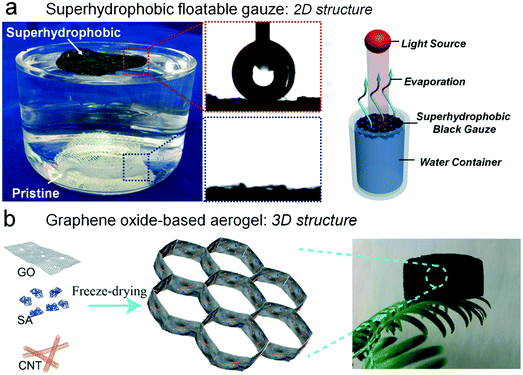 |
| Fig. 5 Intrinsically floatable solar evaporators. (a) The carbon black-based, self-cleaning, superhydrophobic gauze for efficient solar evaporation at the air–water interface.45 (b) The graphene oxide-based aerogel with ultralow density for solar steam generation.47 | |
Another type of floating principle is to use an external floater that is integrated with light absorbing materials. In 2017, Wang et al. came up to a paper-based reduced graphene oxide composite membrane which tremendously increased the absorption efficiency as compared with graphene oxide (Fig. 6a).48 The silicone floater underneath the paper-based absorber plays an important role in the interfacial localization. Owing to the silicone floater, the new structure could completely block the downward heat loss to the bulk water. This is mostly why the evaporation efficiency is promoted substantially. Benefiting from the low price of the paper-based materials, this evaporator can meet a wide requirement of reliable devices in solar steam generation. Gao et al. brought up a bifunctional structure solar evaporator (Fig. 6b),49 similar to the one above. The evaporator was assembled with two parts: for the top layer, they designed a carbon black/polyacrylonitrile composite nanofiber layer to collect sunlight and deliver water. For the bottom layer, hydrophobic polyvinylidene fluoride nanofibers were used to support the floating light absorber and keep the evaporating interface away from the bulk water. The whole device has a wide heat-absorption ability and stability. This cost-efficient evaporator has great promise in the large-scale application of solar steam generation.
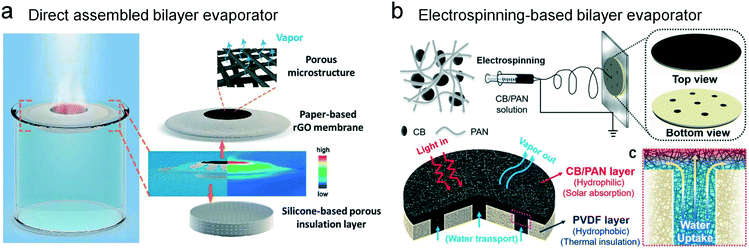 |
| Fig. 6 Integrated solar evaporators with an external floating apparatus. (a) The silicone-based insulation layer as a supporting substrate for the graphene membrane.48 (b) The PVDF substrate acting as the floater to support the electrospun light-absorbing fabric.49 (c) The water channel. | |
Besides, a number of solar evaporation systems are built on the integrated device with controllable water input/output instead of the device floating on the water surface.50 For this type of evaporator, the interfacial localization of heat could be convenient; however, the cost-performance and the large-scale application of such a system should be carefully considered.
3.2. The anti-scaling ability and the salt-rejection ability
Toward the desalination of seawater and the purification of industrial wastewater, the salt-rejection ability is one of the most important properties of the evaporating surface. During the rapid steam generation, the nucleation and crystallization of salt on the evaporator is inevitable. Therefore, two strategies have been developed to reduce the salt accumulation. One is to withdraw the salt on the surface of the solar evaporator (salt re-dissolving mode), and the other is to prevent the salt from interacting with the light-harvesting surface (salt rejecting mode). For the salt re-dissolving mode, the evaporating interface is commonly hydrophilic or even superhydrophilic. The salt on the hydrophilic surface can be firstly wetted by pumped water, and then the saturated salt solution could be drained from the water channel of the evaporating surface.51 In contrast, the salt rejecting mode depends on the hydrophobic light harvesting surface that can minimize the interaction between the salty water and the light harvesting surface.
As a typical salt rejecting evaporator, the hydrophobic light-absorbing layer can be considered indispensable for this superior repellency of salty water.52 It has been reported that a Janus film composed of a hydrophobic carbon black-based upper layer and a polyacrylonide-based lower layer can effectively prevent the salt accumulation on the light-absorbing surface during the seawater desalination.32 Recently, exciting results have been reported by Xu et al., i.e., a water lily-inspired solar evaporator can treat high-salinity brine (10 wt%) and wastewater containing heavy metal ions (30 wt%) (Fig. 7a).53 Inspired by water lily's outstanding transpiration modes, the hierarchical hydrophobic evaporating interface and the efficient water/brine delivering channels are the key factors to avoid salt crystallization on the upper surface. This system is a promising way to achieve direct and large-scale production of drinking water from brine water, seawater, and even saturated solutions, and opens an advanced way to the adaptive water treatment.
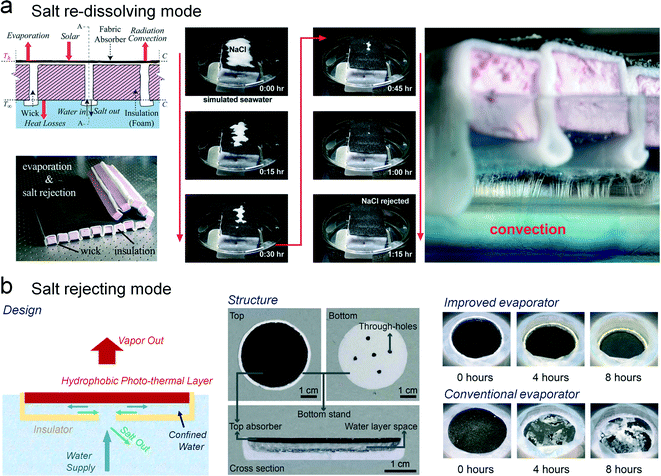 |
| Fig. 7 The anti-scaling mechanism of solar evaporators. (a) The salt rejecting mode: the top layer of the evaporator is highly hydrophobic, resulting in the complete rejection of liquid attachment. Therefore, the crystallization process can only occur at the back side of the evaporating interface, promoting a salt-free light-harvesting surface.53 (b) The salt re-dissolving mode: the fibrous evaporating surface and the water channel are highly wetted. The salt crystals on the top of the evaporator can be gradually dissolved and transferred from the top to the bottom, indicating an effective salt removing process.54 | |
Another type of anti-scaling mode is the salt re-dissolving mode, which depends on a highly wetted liquid channel for salt transport. The significant demonstration of the salt re-dissolving process was performed by Ni et al. via a cotton-based water channel (Fig. 7b).54 The external salt crystals on the top of the light-absorbing layer can be rapidly removed in 60 minutes, and the re-dissolving process was clearly observed at the bottom of the evaporator. This result indicates that the reliable performance of salt removal can be realized in real-world solar evaporation, i.e., the accumulated salt crystals can be cleaned and the evaporating interface can be refreshed in the dark. Zhou et al. reported a hydrogel-based antifouling solar evaporator with similar salt-re-dissolving ability.55 On the basis of an equilibrium between the salty brine and salt in the hydrogel-based material, the crystallized salt can be simultaneously dissolved. Despite the outstanding salt rejection, the hydrogel with capillary and osmotic swelling effects could enhance the water transport from the water bulk to the evaporating surface by the water channel of the hydrogel. In addition, by taking advantage of highly efficient rGO sunlight absorbers, this hydrogel-based solar steam generator exhibits a high evaporation efficiency and a reliable anti-scaling ability.
Considering the potential contamination of the evaporator, a contactless heating process could be highly promising for reliable solar evaporation. Recently, a novel contactless mode of water heating is proposed on the basis of blackbody radiation, which can be attributed to a completely new mode of a solar evaporator (Fig. 8a).56 The proposed contactless solar evaporation structure completely segregates the heat apparatus from the water surface. The solar energy is absorbed by the evaporator directly and the heated evaporator re-radiates infrared photons to heat water beneath. The infrared photons could only penetrate less than 100 μm depth of water, so we can approximately recognize that only the surface of bulk water was heated (Fig. 8b). Building on the advanced thermal conduction mode, the whole device set has a good performance against contamination owing to the non-contact radiation transfer from the device to the water surface. This work created a new strategy to develop a completely salt-free interface, which would inspire other researchers who suffer from evaporator scaling issues.
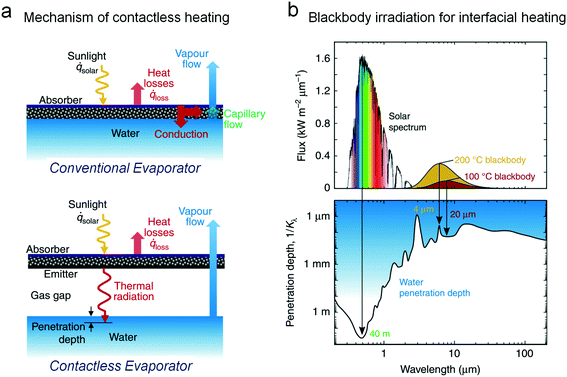 |
| Fig. 8 The contactless evaporator for complete salt rejection.56 (a) The mechanism of contactless heating on the basis of blackbody radiation. Unlike the conventional evaporator, the heat transfer between the light absorbing materials and the water surface depends on the thermal radiation. (b) The spectra and the interfacial heating process of the blackbody irradiation. The 100 °C and 200 °C blackbody can merely heat the water with a depth of 20 μm and 4 μm respectively, indicating the available interfacial heating process. | |
3.3. The heat management and utilization of the evaporator
Although the material innovation of solar evaporators has bloomed in the recent decade, the structure optimization of solar evaporators is the primary issue for improving their actual efficiency. After solar radiation is collected at the air–water interface, the next requirement should be the lowering of heat dissipation and the acceleration of water evaporation.57,58 In general, the heat dissipation in solar evaporation can be divided into radiation, convection, and conduction toward air or bulk water (Fig. 9).
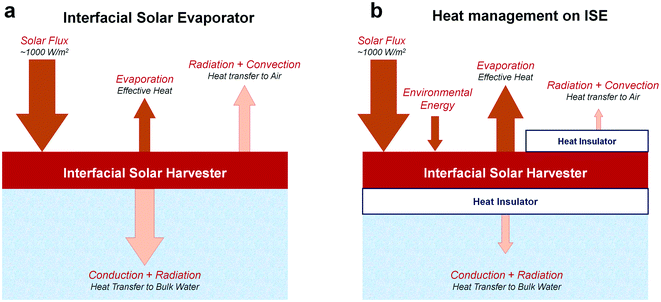 |
| Fig. 9 The heat transfer during the interfacial solar evaporation (ISE). (a) The conventional evaporator and (b) the novel evaporation system with precise heat management. | |
Inspired by the stoma, Ni et al. reported a floating device with a precisely designed heat managing system (Fig. 10a).59 Building on the dual structures with heat resistance, the outlet temperature of solar-generated vapor can reach 100 °C, indicating a powerful strategy for producing high temperature vapor using solar evaporation. In this system, the heat transfer to air, viz. radiation and convection, and the heat transfer to water, viz. conduction and radiation, are largely restricted. Nearly all the heat was focused on the stoma for high-temperature steam generation. In 2018, Shi et al. proposed a new approach to manage the thermal radiation heat loss.60 Through a creative 3D cup-like structure, the diffuse reflection and the thermal reflection could be recycled and used, leading to the efficiency of solar steam generation having been increased approximately to 100%. This work is focused on the reduction of reflections, proving a valid method to optimize the energy utilization. It could be a promising way in practical usage in seawater desalination, and this work may inspire further researchers to take 3D photothermal structures into consideration.
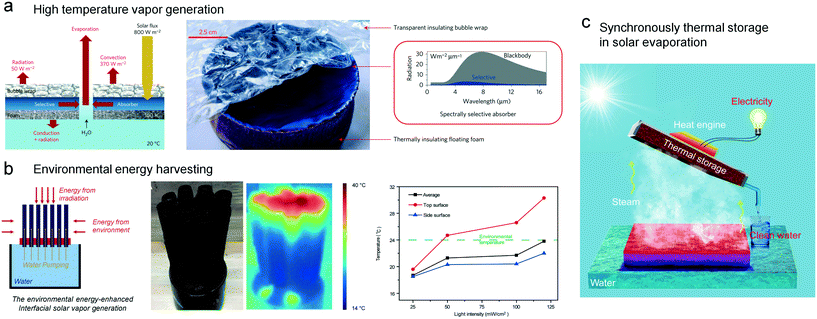 |
| Fig. 10 Innovative solar evaporators with heat managing design. (a) The evaporator with multi-level high insulation for high temperature vapor generation.59 (b) Smart design for harvesting environmental energy through a wetted side wall. (c) Harnessing the heat of vapor by the water collector for electricity generation.66 | |
Heat managing design can also endow the evaporators with the ability to harvest environmental energy. In 2018, Li et al. invented an energy-enhanced interfacial solar vapor generator to optimize the existing energy generation method (Fig. 10b).61 The authors assembled cylindrical vapor generators to collect the environmental energy as well as the solar energy, so that the efficiency of the energy conversion was above 100%. The top layer of the evaporator is capable of collecting solar radiation using light-absorbing materials, and the side wall with a high water content can slowly release vapor that is powered by environmental energy.
Aside from the reduction of potential energy loss, gathering the energy from the evaporated steam can be a novel strategy to improve the energy utilization via heat management, such as power generation.62–64 Chang et al. put forward a new vision of solar-thermal energy harvesting.65 In a sealed chamber, the solar energy was transformed into thermal energy by a paper-supported gold nanoparticle thin film. Then the transformed thermal energy heats water to hot vapors, and then the hot vapors diffuse to the other side of the chamber, to condense and release the absorbed thermal energy. This excellent work achieved an efficient process which rapidly transforms solar energy into thermal energy. And it's able to transfer the collected thermal energy to a specified target with the help of hot vapors. Later, in 2018, Li et al. reported a fancy way to store and recycle the solar steam energy with outstanding thermal management (Fig. 10c).66 In this work, the authors can realize generation of clean water and electricity simultaneously. Combining steam stimulation, energy storage and electricity generation, this work provided a promising way to use the extra thermal energy from hot vapors, which demonstrates an innovative way to integrate solar steam generation with electricity generation.
3.4. The long-term stability of the evaporator
The current research in this field mainly focused on the light-to-heat conversion and the heat management during the evaporation process. As a result, systematical evaluation on the chemical and physical stability of evaporators is still insufficient. To our best knowledge, solar irradiation can effectively degrade a branch of polymeric materials through photo-oxidation as well as carbon-based materials. Meanwhile, the corrosion of metal-based evaporators cannot be neglected when the evaporator is soaked in salty or contaminated water for a long period.67,68 For example, in our experiment, a Cu(OH)2 nanoneedle-based superhydrophilic surface may gradually dissolve in the water in a week, indicating the potential danger of water pollution. To enhance stability, in 2019, Huang et al. reported a coupled tunable photothermal material for highly effective evaporation.69 Commercial carbon fiber material possessing high stability and inexpensive cost is selected as the available solar energy harvester. The designed evaporator exhibits strong strength owing to its carbon fiber structure and it may be used on a large scale in real-world application. Investigations which focus on long-term stability are relatively insufficient, and further research should consider the reactivity and photostability of materials as important factors for designing solar evaporators.
3.5. The cost performance and the scalable fabrication of the evaporator
Advanced photothermal materials significantly increase the efficiency of the light harvesting interface, and meanwhile the cost of these materials should be elevated. Not only the experiment materials but also the tedious fabrication can hamper the wide application of solar evaporation. For example, gold nanoparticles show a promising performance in steam generation, however, the use of this noble metal should be re-evaluated in practical application. The freeze drying process can be applied to prepare aerogels with a well-defined porous structure, which might not be easy to scale up. Therefore, many researchers have tried to make low-price materials instead of cost-inefficient substrates. We have briefly summarized some cost-efficient materials in Fig. 11, and the common and stable materials should be a wise choice for the construction of reliable solar evaporators.
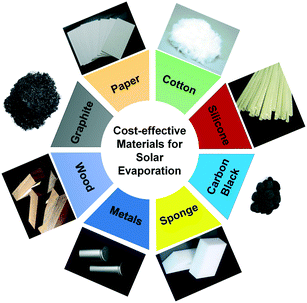 |
| Fig. 11 The cost-efficient materials that are used in solar evaporation, including low price photothermal materials (carbon black and graphite), cellulose-based hydrophilic substrates (paper and cotton), and effective floating supports (wood and sponge). | |
Commercial fabric has been recognized as a good choice for realizing enhanced evaporation, especially cotton with intrinsic hydrophilicity. Wu et al. reported a facile preparation of light-absorbing cotton via carbonization (Fig. 12a).70 After further treatment with dopamine, the as-prepared material exhibits a typical wicking effect for water pumping. Owing to the elevation of the evaporating interface, the temperature of the light-absorbing surface can reach 74 °C with a solar efficiency of 88.8%, proving the high performance of this oil lamp inspired device (Fig. 12b).
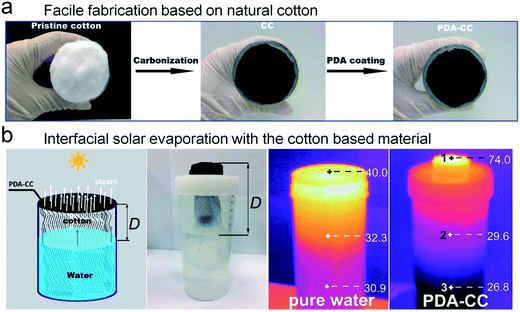 |
| Fig. 12 Low-cost cotton based solar evaporator. (a) The rapid fabrication of light absorbing cotton. (b) The oil lamp inspired solar evaporator exhibits an obvious interfacial heating ability.70 | |
Prof. Liangbin Hu's group reported a series of novel solar steam generators made of natural wood.71 The top layer of the wood was coated with graphite to receive the solar energy, and the water was transported to the top layer based on the wood lumens (Fig. 13a). Due to the well-arranged water channels in the wood lumens, the efficiency of water transport was promising (Fig. 13b). Besides, the thermal energy was concentrated on the vapor generating surface owing to the anisotropic thermal conductivity and the thin graphite layer. The anisotropic structure decreases the conductive heat loss, because the preferred thermal transport direction and the liquid transport direction are decoupled. Importantly, the selection of natural wood can largely reduce the cost of the solar evaporator, and can also provide a possible method for fabricating such evaporators on a large scale (Fig. 13c).
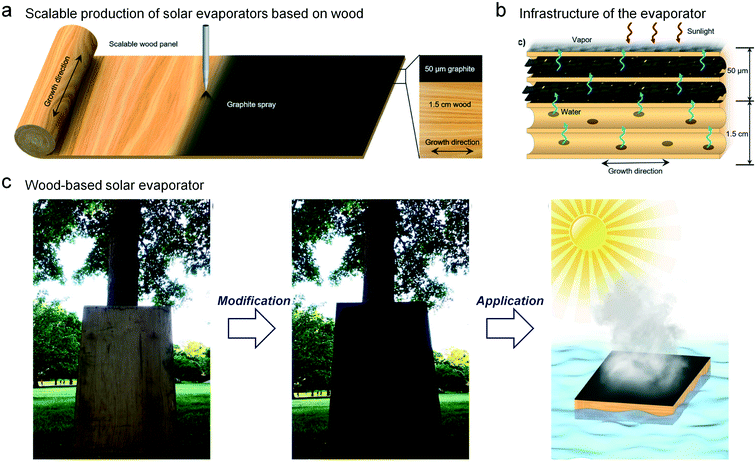 |
| Fig. 13 Low-cost and scalable wood-based solar evaporator.71 (a) The fabrication of the wood-based light-absorbing material via a graphite spraying method. The thickness of the light-absorbing layer is 50 μm and that of the insulating layer is about 1.5 cm. (b) The water can transfer to the evaporation interface through the wood lumens. (c) The demonstration of scalable fabrication and the application of the wood-based floatable evaporator. | |
3.6. The integration of the solar evaporator and the water collecting surface: water collection
During the last decade, the investigation in the solar evaporation largely focused on the water evaporating surface. As another important aspect of water purification, the efficient collection of water steam and the integrated system of water production still remain a challenge. Most of the reports merely show a transparent plastic cap for collecting the evaporated water without considering the collection efficiency and the heat exchange. Furthermore, the actual question in the water production using solar evaporation should be deeply discussed, such as liquid delivery, water storage, energy utilization efficiency, etc. All of these are based on the interdisciplinary study between science and engineering, including chemical engineering, processing simulation, thermodynamic study, etc. Only when the reliable system and the technological process are set up, the practical value of solar evaporation can be confirmed. The previous water collection apparatus commonly relies on the transparent collector such as glass and low-density polyethylene. The generated vapor spontaneously condenses on the film and the collected water flows along the collecting surface to the container. These water collectors are very simple and easy-to-fabricate, however, the efficiency and the reliable performance should be considered. Taking inspiration from the industrial process, Xue et al. presented a compact membrane distillation system with a multi-layer structure for optimized solar-assisted water purification (Fig. 14a).72 The authors introduced an integrated device that is composed of a hydrophilic light-absorbing layer, a hydrophobic support, and a condenser. More importantly, this device can facilely achieve a multi-level assembly with well-defined heat utilization, and the solar efficiency of a two-level device is up to 72% with an outstanding reliability (Fig. 14b). The rational design of the integrative system for solar evaporation should simplify the process and then enhance the efficiency of solar-assisted water production.
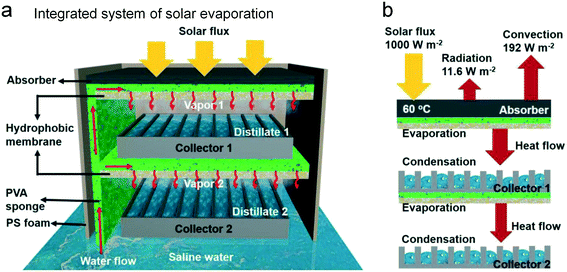 |
| Fig. 14 The multi-level water production device with integrated evaporation and collection design.72 (a) The illustration of this solar assisted water production including saline water pumping, vapor generation, and vapor condensation. (b) The heat utilization of this integrated device. The heat flow from the solar irradiation can continuously generate the vapor at different levels. | |
Beyond that, combining high efficiency water collecting interfaces with a promising solar evaporation system is also a good way to optimize the current integrated systems. During the last decade, a number of publications have demonstrated efficient fog/vapor harvesting interfaces,73–75 which can be directly incorporated into solar evaporation systems. For example, Prof. Shi's group reported a leaf vein-inspired fog water collector possessing continuous water delivery capability.76 The collected water can be transferred actively, providing potential applications in solar steam collection. We envision that the recent progress in fog/vapor collecting interfaces should stimulate new ideas in water production in solar evaporation and enhance the actual performance of the integrated systems.
4. Perspective and prospect
Interfacial solar evaporation is one of the most direct methods for harnessing solar energy. The current investigation mainly focuses on the fabrication of high-performance light-absorbing materials and the design of novel structures for maximizing the energy utility. In the application of such evaporators, the reliable performance and the durability of carriers should be taken into consideration. For example, the mechanical properties and the anti-corrosion ability of the solar evaporator should not be ignored in the actual sea environment. While the evaporator stably floats on the sea surface, the potential damage from fishes and ships may deteriorate its application duration. Corrosion, bio-fouling, wave impact, and oil contamination also influence the effectiveness of solar evaporators. Furthermore, the photostability of materials should be promising, because the photothermal conversion process is always accompanied by photodegradation and photo-oxidation. Therefore, the selected substrates, both the light-absorbing materials and the carriers, should be stable against the irradiation. The future development of solar evaporators ought to notice their reliability and durability for achieving better performance and actual value in water production.
As mentioned in section 3.6, the integrated system involving steam generation and water collection is highly desired for the application of solar evaporation. The basic investigation can merely focus on the light-to-heat conversion and the water evaporation; however, for the practical application of this technique, the well-designed system and the controllable process should be set up. The advanced water producing process based on solar evaporation may include steam generation, vapor condensation, water collection and delivery, liquid storage, etc. In an ideal model, the large sheet of a solar evaporator floating on the sea surface can continuously produce clean water for the people living in seaside areas or on ships (Fig. 15). For massive water production, the effective area of light absorption should be as large as possible, which should require efficient water harvesting and delivery. Therefore, the vapor condensing interfaces and the water delivering pathway should be rationally designed and incorporated. A pumpless liquid delivery process and an ultrathin vapor condenser could be a better choice for future solar evaporators.77,78
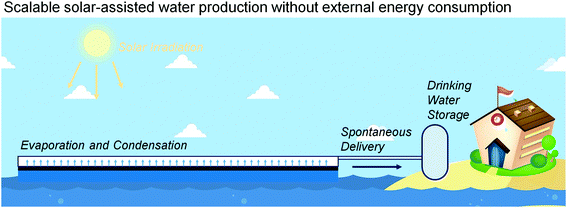 |
| Fig. 15 The prospect of an interfacial solar evaporator for drinking water supply in seaside areas. The total process of water production will be solely driven by solar energy without using any expensive and toxic materials. | |
For the scalable fabrication and the wide application of evaporators, the cost performance is a decisive factor for judging their actual value. To date, the most common evaluation of the light-to-heat conversion depends on the evaporation rate per unit area. However, in future studies, the cost performance may be introduced by using the evaporation rate per unit cost. We do not question the innovative studies based on noble metals or advanced materials, but we would like to recommend a cost evaluation in future studies on solar evaporation.
Solar evaporation also exhibits exciting function when being integrated with novel materials and designs. For harvesting water in a relatively dry environment, Prof. Evelyn Wang's and Prof. Yaghi's groups integrate a metal–organic framework with temperature sensitive water uptake into a solar evaporation system.79 The reported MOF can absorb water vapor by using its porous structure during night-time, and solar irradiation can be applied to evaporate the absorbed water in the MOF for clean water production during daytime. By employing this smart design, the novel solar-assisted water harvesting device is able to collect drinking water in a dry environment with a relative humidity of 20%. This innovative design for collecting atmospheric water in a dry environment can also be achieved by using an inexpensive desiccant such as CaCl2 and a hydrophilic ionic liquid.80–82 The core concept of this process is that the desiccant absorbs water in the cold state and releases water through solar evaporation. Compared with previous work on solar-assisted desalination, the water harvesting in low humidity offers a great opportunity to solve the water crisis in harsh environments.
Interfacial solar evaporation, or solar steam generation, is a typical system for solar-assisted water production. One of the advantages of solar evaporation is that the ideal process does not require any energy input, demonstrating an economic and energy-independent water purifying technique. Moreover, the current designs and systems of solar evaporation are relatively simple and inexpensive as compared with the existing technology. It seems that the fabrication and the set-up of the evaporating interface can be available. Therefore, the reliable performance of such solar evaporators is the first challenge toward the real-world applications. The cost-performance, the environmental impact, and the integrated systems of solar evaporation should also be investigated to develop a rational platform for reliable solar-assisted water production. Besides, the rational design of the molecular structure of photothermal materials should further promote the performance and the reliability of the solar evaporation systems. We envision that the interfacial solar evaporation can meet the requirement of low-cost water purification and open a new way to solve the global water crisis, especially for the people living in underdeveloped areas.
Conflicts of interest
There are no conflicts to declare.
Acknowledgements
This work was supported by the National Natural Science Foundation (21805204), the Tianjin Natural Science Foundation (19JCQNJC05100), and the Young Elite Scientists Sponsorship Program by Tianjin (TJSQNTJ-2018-17).
References
- N. S. Lewis and D. G. Nocera, Proc. Natl. Acad. Sci. U. S. A., 2007, 104, 20142–20142 CAS.
- M. A. Green, Prog. Photovoltaics, 2009, 17, 183–189 CAS.
- M. Z. Liu, M. B. Johnston and H. J. Snaith, Nature, 2013, 501, 395–398 CrossRef CAS PubMed.
- H. Benten, T. Nishida, D. Mori, H. J. Xu, H. Ohkita and S. Ito, Energy Environ. Sci., 2016, 9, 135–140 RSC.
- A. Fujishima, X. T. Zhang and D. A. Tryk, Surf. Sci. Rep., 2008, 63, 515–582 CrossRef CAS.
- K. Hashimoto, H. Irie and A. Fujishima, Jpn. J. Appl. Phys., Part 1, 2005, 44, 8269–8285 CrossRef CAS.
- T. D. Wheeler and A. D. Stroock, Nature, 2008, 455, 208–212 CrossRef CAS PubMed.
- I. W. Eames, N. J. Marr and H. Sabir, Int. J. Heat Mass Transfer, 1997, 40, 2963–2973 CrossRef CAS.
- A. E. Kabeel, Energy, 2009, 34, 1504–1509 CrossRef.
- P. Tao, G. Ni, C. Y. Song, W. Shang, J. B. Wu, J. Zhu, G. Chen and T. Deng, Nat. Energy, 2018, 3, 1031–1041 CrossRef.
- S. V. Boriskina, A. Raza, T. J. Zhang, P. Wang, L. Zhou and J. Zhu, MRS Bull., 2019, 44, 59–66 CrossRef.
- S. S. Cao, Q. S. Jiang, X. H. Wu, D. Ghim, H. G. Derami, P. I. Chou, Y. S. Jun and S. Singamaneni, J. Mater. Chem. A, 2019, 7, 24092–24123 RSC.
- X. Wu, G. Y. Chen, G. Owens, D. Chu and H. Xu, Mater. Today Energy, 2019, 12, 277–296 CrossRef.
- P. Wang, Environ. Sci.: Nano, 2018, 5, 1078–1089 RSC.
- D. Li, D. Han, S. N. Qu, L. Liu, P. T. Jing, D. Zhou, W. Y. Ji, X. Y. Wang, T. F. Zhang and D. Z. Shen, Light: Sci. Appl., 2016, 5, e16120 CrossRef CAS PubMed.
- O. Neumann, A. S. Urban, J. Day, S. Lal, P. Nordlander and N. J. Halas, ACS Nano, 2013, 7, 42–49 CrossRef CAS PubMed.
- Z. H. Wang, Y. M. Liu, P. Tao, Q. C. Shen, N. Yi, F. Y. Zhang, Q. L. Liu, C. Y. Song, D. Zhang, W. Shang and T. Deng, Small, 2014, 10, 3234–3239 CrossRef CAS PubMed.
- M. M. Ye, J. Jia, Z. J. Wu, C. X. Qian, R. Chen, P. G. O'Brien, W. Sun, Y. C. Dong and G. A. Ozin, Adv. Energy Mater., 2017, 7, 1601811 CrossRef.
- V. D. Dao and H. S. Choi, Global Challenges, 2018, 2, 1700094 CrossRef PubMed.
- Y. C. Wang, L. B. Zhang and P. Wang, ACS Sustainable Chem. Eng., 2016, 4, 1223–1230 CrossRef CAS.
- Y. Shi, C. L. Zhang, R. Y. Li, S. F. Zhuo, Y. Jin, L. Shi, S. Hong, J. Chang, C. S. Ong and P. Wang, Environ. Sci. Technol., 2018, 52, 11822–11830 CrossRef CAS PubMed.
- L. L. Zhu, M. M. Gao, C. K. N. Peh and G. W. Ho, Nano Energy, 2019, 57, 507–518 CrossRef CAS.
- H. D. Liu, Z. Huang, K. Liu, X. J. Hu and J. Zhou, Adv. Energy Mater., 2019, 9, 1900310 CrossRef.
- C. J. Chen, Y. D. Kuang and L. B. Hu, Joule, 2019, 3, 683–718 CrossRef CAS.
- T. Arunkumar, Y. L. Ao, Z. F. Luo, L. Zhang, J. Li, D. Denkenberger and J. Q. Wang, Renewable Sustainable Energy Rev., 2019, 115, 109409 CrossRef.
- J. H. Zhou, Y. F. Gu, P. F. Liu, P. F. Wang, L. Miao, J. Liu, A. Y. Wei, X. J. Mu, J. L. Li and J. Zhu, Adv. Funct. Mater., 2019, 29, 1903255 CrossRef CAS.
- L. L. Zhu, M. M. Gao, C. K. N. Peh and G. W. Ho, Mater. Horiz., 2018, 5, 323–343 RSC.
- M. M. Gao, L. L. Zhu, C. K. Peh and G. W. Ho, Energy Environ. Sci., 2019, 12, 841–864 RSC.
- Y. Zeng, J. F. Yao, B. A. Horri, K. Wang, Y. Z. Wu, D. Li and H. T. Wang, Energy Environ. Sci., 2011, 4, 4074–4078 RSC.
- H. Ghasemi, G. Ni, A. M. Marconnet, J. Loomis, S. Yerci, N. Miljkovic and G. Chen, Nat. Commun., 2014, 5, 4449 CrossRef CAS PubMed.
- Y. M. Liu, S. T. Yu, R. Feng, A. Bernard, Y. Liu, Y. Zhang, H. Z. Duan, W. Shang, P. Tao, C. Y. Song and T. Deng, Adv. Mater., 2015, 27, 2768–2774 CrossRef CAS PubMed.
- W. C. Xu, X. Z. Hu, S. D. Zhuang, Y. X. Wang, X. Q. Li, L. Zhou, S. N. Zhu and J. Zhu, Adv. Energy Mater., 2018, 8, 1702884 CrossRef.
- N. Xu, X. Z. Hu, W. C. Xu, X. Q. Li, L. Zhou, S. N. Zhu and J. Zhu, Adv. Mater., 2017, 29, 1606762 CrossRef PubMed.
- J. Drelich, E. Chibowski, D. D. Meng and K. Terpilowski, Soft Matter, 2011, 7, 9804–9828 RSC.
- S. H. Hong, Y. Shi, R. Y. Li, C. L. Zhang, Y. Jin and P. Wang, ACS Appl. Mater. Interfaces, 2018, 10, 28517–28524 CrossRef CAS PubMed.
- X. Q. Li, W. C. Xu, M. Y. Tang, L. Zhou, B. Zhu, S. N. Zhu and J. Zhu, Proc. Natl. Acad. Sci. U. S. A., 2016, 113, 13953–13958 CrossRef CAS PubMed.
- Y. J. Li, T. T. Gao, Z. Yang, C. J. Chen, W. Luo, J. W. Song, E. Hitz, C. Jia, Y. B. Zhou, B. Y. Liu, B. Yang and L. B. Hu, Adv. Mater., 2017, 29, 1700981 CrossRef PubMed.
- F. Zhao, X. Y. Zhou, Y. Shi, X. Qian, M. Alexander, X. P. Zhao, S. Mendez, R. G. Yang, L. T. Qu and G. H. Yu, Nat. Nanotechnol., 2018, 13, 489–495 CrossRef CAS PubMed.
- Y. Ito, Y. Tanabe, J. H. Han, T. Fujita, K. Tanigaki and M. W. Chen, Adv. Mater., 2015, 27, 4302–4307 CrossRef CAS PubMed.
- J. T. Korhonen, M. Kettunen, R. H. A. Ras and O. Ikkala, ACS Appl. Mater. Interfaces, 2011, 3, 1813–1816 CrossRef CAS PubMed.
- H. Jin, M. Kettunen, A. Laiho, H. Pynnonen, J. Paltakari, A. Marmur, O. Ikkala and R. H. A. Ras, Langmuir, 2011, 27, 1930–1934 CrossRef CAS PubMed.
- Z. Li, M. Cao, P. Li, Y. Zhao, H. Bai, Y. Wu and L. Jiang, Matter, 2019, 1, 661–673 CrossRef.
- Y. Y. Zhao, C. M. Yu, H. Lan, M. Y. Cao and L. Jiang, Adv. Funct. Mater., 2017, 27, 1701466 CrossRef.
- H. Liu, Y. D. Wang, J. Y. Huang, Z. Chen, G. Q. Chen and Y. K. Lai, Adv. Funct. Mater., 2018, 28, 1707415 CrossRef.
- Y. M. Liu, J. W. Chen, D. W. Guo, M. Y. Cao and L. Jiang, ACS Appl. Mater. Interfaces, 2015, 7, 13645–13652 CrossRef CAS PubMed.
- L. B. Zhang, B. Tang, J. B. Wu, R. Y. Li and P. Wang, Adv. Mater., 2015, 27, 4889–4894 CrossRef CAS PubMed.
- X. Z. Hu, W. C. Xu, L. Zhou, Y. L. Tan, Y. Wang, S. N. Zhu and J. Zhu, Adv. Mater., 2017, 29, 1604031 CrossRef PubMed.
- Z. Z. Wang, Q. X. Ye, X. B. Liang, J. L. Xu, C. Chang, C. Y. Song, W. Shang, J. B. Wu, P. Tao and T. Deng, J. Mater. Chem. A, 2017, 5, 16359–16368 RSC.
- T. T. Gao, Y. J. Li, C. J. Chen, Z. Yang, Y. D. Kuang, C. Jia, J. W. Song, E. M. Hitz, B. Y. Liu, H. Huang, J. Y. Yu, B. Yang and L. B. Hu, Small Methods, 2019, 3, 1800176 CrossRef.
- C. Zhang, H. Q. Liang, Z. K. Xu and Z. K. Wang, Adv. Sci., 2019, 6, 1900883 CrossRef CAS PubMed.
- S. M. He, C. J. Chen, Y. D. Kuang, R. Y. Mi, Y. Liu, Y. Pei, W. Q. Kong, W. T. Gan, H. Xie, E. Hitz, C. Jia, X. Chen, A. Gong, J. M. Liao, J. Li, Z. J. Ren, B. Yang, S. Das and L. B. Hu, Energy Environ. Sci., 2019, 12, 1558–1567 RSC.
- V. Kashyap, A. Al-Bayati, S. M. Sajadi, P. Irajizad, S. H. Wang and H. Ghasemi, J. Mater. Chem. A, 2017, 5, 15227–15234 RSC.
- N. Xu, J. L. Li, Y. Wang, C. Fang, X. Q. Li, Y. X. Wang, L. Zhou, B. Zhu, Z. Wu, S. N. Zhu and J. Zhu, Sci. Adv., 2019, 5, eaaw7013 CrossRef PubMed.
- G. Ni, S. H. Zandavi, S. M. Javid, S. V. Boriskina, T. A. Cooper and G. Chen, Energy Environ. Sci., 2018, 11, 1510–1519 RSC.
- X. Y. Zhou, F. Zhao, Y. H. Guo, Y. Zhang and G. H. Yu, Energy Environ. Sci., 2018, 11, 1985–1992 RSC.
- T. A. Cooper, S. H. Zandavi, G. W. Ni, Y. Tsurimaki, Y. Huang, S. V. Boriskina and G. Chen, Nat. Commun., 2018, 9, 5086 CrossRef CAS PubMed.
- S. T. Yu, Y. Zhang, H. Z. Duan, Y. M. Liu, X. J. Quan, P. Tao, W. Shang, J. B. Wu, C. Y. Song and T. Deng, Sci. Rep., 2015, 5, 13600 CrossRef PubMed.
- Y. N. Luo, B. W. Fu, Q. C. Shen, W. Hao, J. L. Xu, M. D. Min, Y. M. Liu, S. An, C. Y. Song, P. Tao, J. B. Wu, W. Shang and T. Deng, ACS Appl. Mater. Interfaces, 2019, 11, 7584–7590 CrossRef CAS PubMed.
- G. Ni, G. Li, S. V. Boriskina, H. X. Li, W. L. Yang, T. J. Zhang and G. Chen, Nat. Energy, 2016, 1, 16126 CrossRef CAS.
- Y. Shi, R. Y. Li, Y. Jin, S. F. Zhuo, L. Shi, J. Chang, S. Hong, K. C. Ng and P. Wang, Joule, 2018, 2, 1171–1186 CrossRef CAS.
- X. Q. Li, J. L. Li, J. Y. Lu, N. Xu, C. L. Chen, X. Z. Min, B. Zhu, H. X. Li, L. Zhou, S. N. Zhu, T. J. Zhang and J. Zhu, Joule, 2018, 2, 1331–1338 CrossRef CAS.
- M. M. Gao, C. K. Peh, H. T. Phan, L. L. Zhu and G. W. Ho, Adv. Energy Mater., 2018, 8, 1800711 CrossRef.
- L. L. Zhu, T. P. Ding, M. M. Gao, C. K. N. Peh and G. W. Ho, Adv. Energy Mater., 2019, 9, 1900250 CrossRef.
- L. L. Zhu, M. M. Gao, C. K. N. Peh, X. Q. Wang and G. W. Ho, Adv. Energy Mater., 2018, 8, 1702149 CrossRef.
- C. Chang, C. Yang, Y. M. Liu, P. Tao, C. Y. Song, W. Shang, J. B. Wu and T. Deng, ACS Appl. Mater. Interfaces, 2016, 8, 23412–23418 CrossRef CAS PubMed.
- X. Q. Li, X. Z. Min, J. L. Li, N. Xu, P. C. Zhu, B. Bin Zhu, S. N. Zhu and J. Zhu, Joule, 2018, 2, 2477–2484 CrossRef.
- T. Liu, Y. S. Yin, S. G. Chen, X. T. Chang and S. Cheng, Electrochim. Acta, 2007, 52, 3709–3713 CrossRef CAS.
- F. Z. Zhang, L. L. Zhao, H. Y. Chen, S. L. Xu, D. G. Evans and X. Duan, Angew. Chem., Int. Ed., 2008, 47, 2466–2469 CrossRef CAS PubMed.
- J. Huang, Y. R. He, Y. W. Hu and X. Z. Wang, Sol. Energy Mater. Sol. Cells, 2019, 203, 110156 CrossRef CAS.
- X. Wu, L. M. Wu, J. Tan, G. Y. Chen, G. Owens and H. L. Xu, J. Mater. Chem. A, 2018, 6, 12267–12274 RSC.
- T. Li, H. Liu, X. P. Zhao, G. Chen, J. Q. Dai, G. Pastel, C. Jia, C. J. Chen, E. Hitz, D. Siddhartha, R. G. Yang and L. B. Hu, Adv. Funct. Mater., 2018, 28, 1707134 CrossRef.
- G. Xue, Q. Chen, S. Lin, J. Duan, P. Yang, K. Liu, J. Li and J. Zhou, Global Challenges, 2018, 2, 1800001 CrossRef PubMed.
- M. Y. Cao, J. S. Xiao, C. M. Yu, K. Li and L. Jiang, Small, 2015, 11, 4379–4384 CrossRef CAS PubMed.
- P. Li, M. Y. Cao, H. Y. Bai, T. O. H. Zhao, Y. Z. Ning, X. S. Wang, K. S. Liu and L. Jiang, Adv. Funct. Mater., 2019, 29, 1904446 CrossRef CAS.
- Y. H. Jiang, S. Savarirayan, Y. H. Yao and K. C. Park, Appl. Phys. Lett., 2019, 114, 083701 CrossRef.
- J. B. Lin, X. H. Tan, T. L. Shi, Z. R. Tang and G. L. Liao, ACS Appl. Mater. Interfaces, 2018, 10, 44815–44824 CrossRef CAS PubMed.
- H. Geng, H. Y. Bai, Y. Y. Fan, S. Y. Wang, T. Ba, C. M. Yu, M. Y. Cao and L. Jiang, Mater. Horiz., 2018, 5, 303–308 RSC.
- H. Y. Bai, C. H. Zhang, Z. Y. Long, H. Geng, T. Ba, Y. Y. Fan, C. M. Yu, K. Li, M. Y. Cao and L. Jiang, J. Mater. Chem. A, 2018, 6, 20966–20972 RSC.
- H. Kim, S. Yang, S. R. Rao, S. Narayanan, E. A. Kapustin, H. Furukawa, A. S. Umans, O. M. Yaghi and E. N. Wang, Science, 2017, 356, 430–432 CrossRef CAS PubMed.
- R. Y. Li, Y. Shi, L. Shi, M. Alsaedi and P. Wang, Environ. Sci. Technol., 2018, 52, 5398–5406 CrossRef CAS PubMed.
- X. Y. Wang, X. Q. Li, G. L. Liu, J. L. Li, X. Z. Hu, N. Xu, W. Zhao, B. Zhu and J. Zhu, Angew. Chem., Int. Ed., 2019, 58, 12054–12058 CrossRef CAS PubMed.
- H. S. Qi, T. Q. Wei, W. Zhao, B. Zhu, G. L. Liu, P. P. Wang, Z. H. Lin, X. Y. Wang, X. Q. Li, X. W. Zhang and J. Zhu, Adv. Mater., 2019, 31, 1903378 CrossRef CAS PubMed.
|
This journal is © The Royal Society of Chemistry 2020 |
Click here to see how this site uses Cookies. View our privacy policy here.