DOI:
10.1039/D0GC01484B
(Tutorial Review)
Green Chem., 2020,
22, 4411-4425
Applications of xylochemistry from laboratory to industrial scale
Received
29th April 2020
, Accepted 8th June 2020
First published on 29th June 2020
Abstract
Xylochemicals and their utilisation in total synthesis and industrial applications are highlighted in this review. This class of chemicals consists of bio-based molecules or building blocks derived from renewable feedstocks like plant-biomass, lignocellulose as well as waste-streams. The advantages over petroleum-based chemicals are presented with the aid of specific examples ranging from the total synthesis of natural products, relevant industrial applications to the exploitation of CO2 as a C1 feedstock. This review contributes to the trend of a “greener” and a more sustainable chemistry.
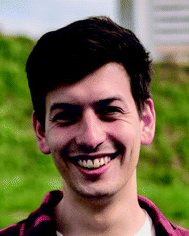 Jonathan Groß | Jonathan Groß obtained his Bachelor's (2017) and Master's degree (2018) in Chemistry from the Johannes Gutenberg-University Mainz studying natural product synthesis and the valorization of renewable resources for the synthesis of functional materials. He is currently a graduate student in the group of Professor Till Opatz since 2019. In 2016/7, he spent six months with Professor Doug Stephan at the University of Toronto, Canada, researching on new frustrated Lewis-pairs for the activation of small molecules. His research interests are green chemistry and using computational chemistry for structure elucidation. |
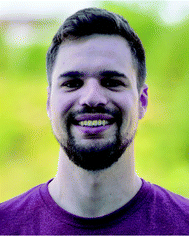 Jonas Kühlborn | Jonas Kühlborn obtained his Bachelor's (2014) and Master's degree (2016) in Biomedical Chemistry from the Johannes Gutenberg-University Mainz studying natural product synthesis and the valorization of renewable resources for the synthesis of functional materials. He is currently a graduate student in the group of Professor Till Opatz since 2016. In 2018, he spent four months with Professor Charles de Koning at the University of the Witwatersrand, Johannesburg, researching on the utilization of cashew nut shell liquid for organic synthesis. His research interests are green chemistry and total synthesis based on biomass-derived molecules. |
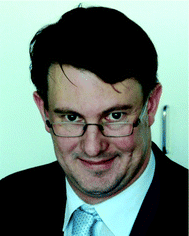 Till Opatz | Till Opatz is currently a Professor of Organic Chemistry at the Department of Chemistry, Johannes Gutenberg-University, Mainz, Germany. After receiving his diploma in 1997 with Professor Johann Mulzer at the Goethe-University Frankfurt, he obtained his doctorate with Professor Horst Kunz at the Johannes Gutenberg-University Mainz in 2001. After a postdoctoral stay with Professor Rob Liskamp at the University of Utrecht (Netherlands), he completed his Habilitation in 2006 at Johannes Gutenberg-University Mainz. In 2007, he was appointed associate and later full Professor at the University of Hamburg and returned to Mainz in 2010. His research interests are method development, natural products, and sustainable chemistry. |
1. Introduction
Xylochemicals are synthetically valuable organic building blocks derived from renewable lignocellulose or other fractions of woody biomass and therefore theoretically CO2-neutral.1,2 Apart from an often useful degree of oxygenation, some xylochemicals also retain stereochemical information, which can be exploited for subsequent synthetic purposes.3 In contrast, petroleum-based chemicals have lost the majority of the formerly contained heteroatoms during the process of kerogenesis4 so that desired functionalities need to be reinstalled in often resource-intensive sequences.5,6
Lignocellulose is the most abundantly available type of biomass on planet earth. More precisely, agricultural waste products such as corn stover or rice husks, wood-waste streams e.g. wood processing residues like stalks and wood chips or municipal plant waste as well as switchgrass as ground cover for soil conversion, constitute promising renewable feedstocks for biofuels and platform chemicals.3,7,8 Food supply chain waste streams (e.g. apple pomace,9 brewer's spent grain10 or waste frying oil11) are also abundant, readily available, and still contain valuable and functionalized compounds like antioxidants, carbohydrates or phenolics, which can be exploited for the production of chemicals.12–15
In the context of renewable feedstocks, a major benefit for the chemical industry was the switch from first to second generation biofuels. First generation fuels rely mainly on alcohols (bioethanol) and oils (biodiesel) which are available through well understood technologies for processing food crops, while for the second generation biofuels, non-edible feedstocks such as lignocellulose biomass or algae crops are utilised.8,16 The limited or absent interference with the food and feed industry solved the so-called food versus fuel debate and the ethical problems associated with it.17–19
There are several approaches to produce platform chemicals or synthesis gas from biomass which have already been well-presented in the current literature (including both biorefinery concepts as well as chemical processes).13,20–23 For these procedures, the pre-treatment of biomass proved crucial to achieve an efficient conversion or processing due to the complex structure of lignocellulose. A suitable pre-processing is highly dependent on the source of feedstock and can be performed biologically, chemically, thermally or mechanically (detailed information can be found in the cited literature).13,24,25
Prominent examples of xylochemical platform chemicals are vanillin (1),26–28 the sugar alcohols sorbitol (2), xylitol (3) and mannitol (4)29 or furfural (5).30 These compounds can be upgraded to more advanced platform chemicals like levulinic acid (6),31–33 succinic acid (7),34,35 furan-2,5-dicarboxylic acid (8),36,37 itaconic acid (9),36 5-(chloromethyl)furfural (10, CMF),38 5-(hydroxymethyl)furfural (11, HMF)39–42 or γ-valerolactone (12) (Fig. 1).43 For further examples of biomass conversion into value-added products, the reader is referred to the existing literature.44–49
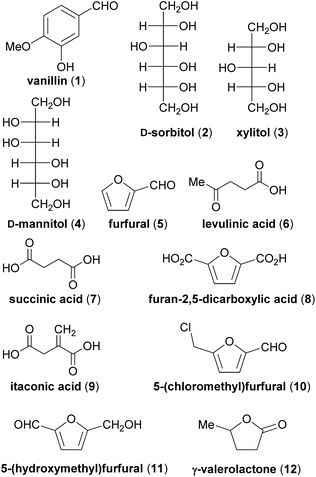 |
| Fig. 1 Examples of xylochemical platform chemicals. | |
The mentioned waste streams and raw materials result in platform chemicals, all carbon atoms of which are wood-based and hence renewable on a short timescale.1 With these xylochemical platform chemicals (or xylochemicals), the synthesis of functional materials as well as natural products50 can be the basis of processes with an improved carbon footprint and ideally with little or even no input of fossil carbon. While the complete re-engineering of process cascades for the sake of environmental production and to avoid the increasing costs of fossil fuels is one option, xylochemical routes to valuable intermediates already integrated in today's value chains might be a more convenient first step towards a sustainable chemical economy.51
In the present review, selected examples of the synthesis of natural products as well as of functional materials are presented to illustrate the application of the above-mentioned options for eco-friendly synthesis.
2. Examples of xylochemistry
2.1. Total synthesis of natural products
2.1.1. (–)-Thebaine.
Opatz, Waldvogel and Schäfer et al. have developed an enantioselective total synthesis of (–)-thebaine ((–)-13) via a regioselective intramolecular anodic coupling of a laudanosine derivative 14 in an undivided constant-current setup (Scheme 1).52,53 The desired 4a-2′-coupling was achieved with a 3′,4′,5′-trioxygenated laudanosine derivative 14 possessing an unsymmetrical substitution pattern which was synthesised from the three xylochemicals methanol, homoveratrylamine (15), and methyl gallate (16).54–56
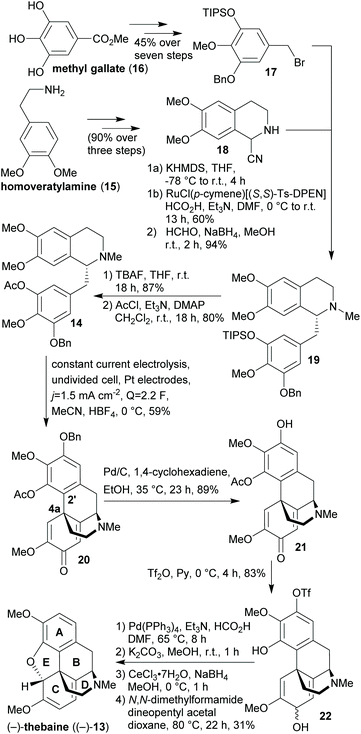 |
| Scheme 1 Total synthesis of (–)-thebaine ((–)-13) from xylochemicals (DPEN = diphenylethylene diamine, TBAF = tetrabutylammonium fluoride). | |
The electrochemical approach is a sustainable alternative to the conventional approach of using partly toxic or harmful stoichiometric oxidants such as VOCl3,57 thallium tris(trifluoroacetate),58 manganese dioxide59 or potassium ferricyanide60,61 for the aryl–aryl coupling of reticuline-type scaffolds. Every carbon and oxygen atom in (–)-thebaine ((–)-13) can be derived from woody biomass in the present synthesis. Furthermore, tetrahydroisoquinoline 18 was prepared in three steps from 15 according to known procedures without chromatographic purification.62–64 The iodomethane required for the O-methylation of methyl gallate (16) can be obtained by reacting methanol (“wood spirit”) with hydrogen iodide.65 For the conversion of homoveratrylamine (15) into 6,7-dimethoxy-3,4-dihydroisoquinoline (not shown), formic acid is required which is accessible via a biorefinery process.23 Formaldehyde, which is employed in the reductive alkylation reaction leading to 19, can e.g. be obtained by the rapid pyrolysis of milled wood lignin.66 Unfavourable aspects in the light of “green” chemistry are the switching and the general use of protecting groups as well as the use of several undesired solvents and reagents. Moreover, the majority of the chemicals employed in the synthesis are conventional and hence petrochemistry-based. In a very similar sequence, the same group managed to synthesise (–)-oxycodone (not shown)67 while its “non-natural” enantiomer (+)-oxycodone (not shown) was prepared by the Hudlický lab in an enzyme-catalysed approach, in which all carbon atoms are derivable from renewable resources and employing several “green” solvents. Yet, petrochemistry-derived protecting groups as well as toxic reagents were used in the latter synthesis, too.68
2.1.2. Ilicifoline B.
In 2015, Opatz et al. published the first total synthesis of ilicifoline B (23), a dimeric berberine-type alkaloid first isolated from Berberis ilicifolia (Scheme 2).1,2,69 All of the carbon atoms in the product were derived from sustainable sources. The oxygenation pattern of the starting aromatic residues was preserved throughout the sequence.1,2 The starting materials, ferulic acid (24) and veratrole (25), are available from wood or other types of biomass.70,71 The employed reagents, dimethyl sulfate for the O-methylation of the phenolic hydroxy group of 16, and formaldehyde for the double bromomethylation of veratrole (25), can be directly obtained from methanol.66,72,73 The authors used the solvents MeOH, H2O, EtOH and toluene, which are classified as benign according to the principles of “green” chemistry.74 Moreover, toluene is available through hydrodeoxygenation of lignin75 while ethanol can be prepared by fermentation from sugars available by catalytic hydrolysis of cellulose and hemicelluloses.8 Yet, the use of undesired solvents such as dichloromethane should generally be avoided. Also, a switch to a non-toxic cyanide source (e.g. potassium ferricyanide)76,77 would have been welcome.
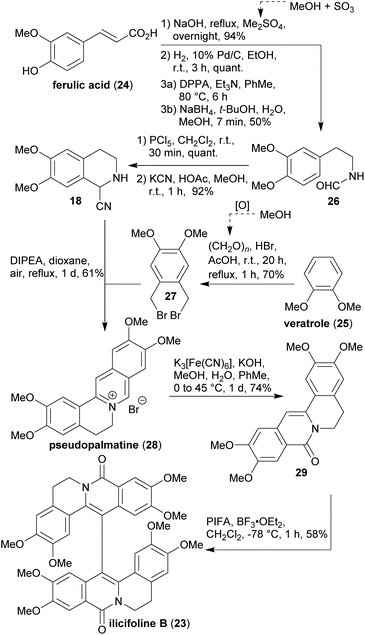 |
| Scheme 2 Total synthesis of ilicifoline B (23) (DPPA = diphenyl phosphoryl azide, PIFA = [bis(trifluoroacetoxy)iodo]benzene). | |
2.1.3. Aminophenoxazinones.
Veratraldehyde (30) was also utilised by Opatz et al. as a building block in their xylochemical synthesis of 2-aminophenoxazinone-type natural products.78 Aldehyde 30 can either be isolated directly from woody biomass79,80 or be obtained by O-methylation of vanillin (1) with dimethyl sulfate81 (xylochemical, vide supra).73 The conventional oxidative synthesis of these interesting compounds from o-aminophenols requires the stoichiometric use of strong oxidants which generally lead to decreased yields due to the lack of selectivity. The authors therefore opted for a “greener” method with higher selectivity for the oxidation of the 2-aminophenol starting materials 31–36 to avoid the formation of undesired products. This should allow a selective cross coupling when two different o-aminophenols were deployed. A combination of the mild, eco-friendly oxidant H2O2 with the electron rich 4,5-dimethoxy-2-aminophenol (31) was found to provide optimum results. The latter could be synthesised from 30
82 and was reacted with various less electron rich o-aminophenols 31–36 which are also derivable from renewable sources to produce the respective natural products or intermediates 37–39 (Table 1). The only “waste” products of this method are methanol and water.
Table 1 Results and conditions of the key oxidative coupling in the synthesis of 2-aminophenoxazinone natural products by Opatz et al.
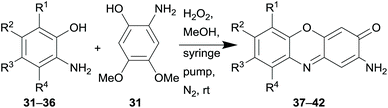
|
# |
Starting material |
R1 |
R2 |
R3 |
R4 |
Product, % |
1 |
31
|
H |
OMe |
OMe |
H |
37, 98 |
2 |
32
|
H |
H |
H |
H |
38, 100 |
3 |
33
|
H |
H |
CO2Me |
H |
39, 66 |
4 |
34
|
OH |
H |
H |
H |
40, 14 |
5 |
35
|
H |
H |
H |
OH |
41, 76 |
6 |
36
|
H |
H |
CH2OTHP |
H |
42, 91 |
With this method, the natural products peristrophine (37), questiomycin A (38), maroxazinone (39) as well as 2-amino-6-hydroxy-3H-phenoxazin-3-one (40) could be synthesised in generally high overall yields. The hydroxy derivative 41 served as an intermediate for the synthesis of chandrananimycin A (43), which was obtained by acetylation and subsequent ester cleavage (Scheme 3A). Exfoliazone (44), viridobrunnine A (45) and venezueline E (46) were synthesised from 42 by N-acetylation, deprotection and esterification (Scheme 3B). Since aminophenoxazinones are known for their biological activities and particularly for their cytotoxicity, the synthesised natural products were subjected to an MTT viability assay with HeLa cells in which they showed promisingly low IC50 values from 8.87 to 23.65 μM.
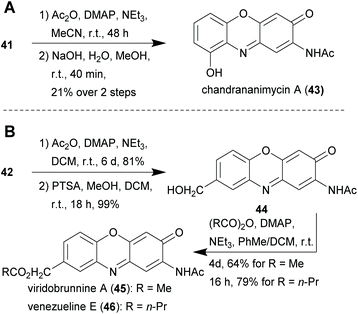 |
| Scheme 3 Synthesis of chandrananimycin A (43) from 41 (A) as well as exfoliazone (44), viridobrunnine A (45) and venezueline E (46) from 42 (B). | |
2.2. Dyes
The production of dyestuffs was one of the key driving forces for industrial scale synthetic organic chemistry and began with Perkin's synthesis of mauveine.83 The structure elucidation and first total synthesis of indigo by von Baeyer84–86 in the second half of the 19th century is another highly important milestone. On the other hand, the advent of synthetic dyestuffs boosted the use of fossil carbon sources like coal tar and later petroleum by the chemical industry. With increasing production volumes, petrochemical starting materials became indispensable for the manufacturing of most chemical products.87,88
The increasing depletion of these resources challenges today's scientists to develop new routes to known dyestuffs based on renewable starting materials and to search for novel dyes that can be produced in a more sustainable fashion as potential substitutes for the materials currently in use. In search for a xylochemical approach, the Opatz lab investigated the synthesis of the indigo derivatives 5,5′,6,6′-tetramethoxyindigo (47) and 5,5′,6,6′-tetrahydroxyindigo (48).89
In a three step sequence, 47 was synthesised starting from veratraldehyde (30)79 and nitromethane (available from methanol)90 in 69% yield without the use of an organic solvent at ambient temperature (Scheme 4). This short and eco-friendly approach furthermore bears the advantage that the reductive cyclization in the last step of the synthesis of 47 directly yields a solution of the (reduced) leuko-form suitable for vat dyeing of any natural fabric without prior isolation of the dyestuff itself. Furthermore, all carbon atoms incorporated in the product were obtained from renewable starting materials.
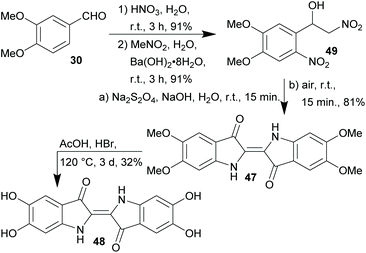 |
| Scheme 4 Synthesis of indigo-type dyes by Opatz et al. | |
The group of Mascal presented a sustainable synthesis of butenolide colorants based on bio-derived starting materials.91 For this approach, they utilised the carbohydrate-derived, versatile renewable platform molecule 5-(chloromethyl)furfural (10, CMF) as well as the related angelica lactone (50, AL) which can also be prepared from CMF (10).38 Condensation of lactone 49 with aldehyde 10 or with 2,5-diformylfuran (51, DFF) or vanillin (1) in 1,4-dioxane with Mn2O3 as a catalyst gave the butenolide dyes 52–54 in high yields of 87%, 82% and 85%, respectively (Table 2, entries 1a, 4 and 5). While DFF (51) is also accessible from carbohydrates,92 vanillin (1) is a prime example of a lignin-derivable starting material and numerous methods for its preparation through lignin depolymerisation have been developed.28,93–95 Although 1,4-dioxane is a less favourable solvent in terms of sustainability,96 the superiority of these conditions in terms of chemical yield might justify its use. Other solvents caused side reactions which decreased the yields significantly or led to different products. The yield of 52 dropped to 22% in water with BaCO3 due to predominant hydrolysis of AL 50 (Table 2, entry 1b), whereas the reaction of 50 with 51 in water without any additive produced the mono-condensation product 55 in only 28% yield (Table 2, entry 3). Switching the solvent to ethanol gave the respective ethyl ether 56 through chloride displacement in 85% yield (Table 2, entry 2).
Table 2 Synthesised butenolide dyes 52–56 and conditions by Mascal et al.
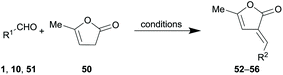
|
# |
R1 |
Conditions |
R2 |
1 |
|
(a) 1,4-Dioxane, H2O, Mn2O3, reflux, 2 h |
|
(b) H2O, BaCO3, reflux, no 49 |
2 |
|
EtOH, Mn2O3, reflux, 1.5 h |
|
3 |
|
H2O, 80 °C, 1 h |
|
4 |
|
1,4-Dioxane, Mn2O3, reflux, 2 h |
|
5 |
|
1,4-Dioxane, Mn2O3, reflux, 14 h |
|
Both approaches to sustainable colorants not only relied exclusively on starting materials from renewable resources but also were devoid of extensive purification operations which are usually cost- as well as material-intensive and increase the environmental burden of a given process.97 All intermediates and products could instead be separated by simple extraction or filtration.
2.3. Polymers
While the valorisation of lignin for applications in polymer chemistry (composites, carbon nanofibers or dispersing agents) is a highly active research field,98–101 several pure bulk chemicals obtained from lignocellulose have also been successfully applied for future polymer production (vide infra).37,102
2.3.1. Polyamides.
A rather unusual but also one of the longest known xylochemicals, 4-propylcyclohexanol (57),103 was used by Opatz et al. for the synthesis of polyamides as xylochemical counterparts of nylon-6 and nylon-6,6 (its monomer lactic acid (64) can be obtained via fermentation of pure carbohydrates, corn or sugar beets).89,104 Polyamides currently belong to the most popular chemical consumer products but are also tightly linked to classical petrochemistry. Therefore, there is an urgent need for eco-friendly alternatives.105–109 The xylochemical approach regarding the starting materials of Opatz et al. was complemented using sustainable methods and solvents throughout the syntheses (Scheme 5).
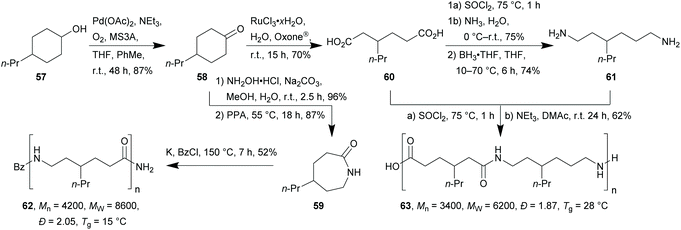 |
| Scheme 5 Synthesis of polyamides 62 and 63 from xylochemical 57 by Opatz et al. | |
The key intermediate for the synthesis of the monomers for both types of polyamides was 4-propylcyclohexanone (58), which was synthesised by Pd-catalysed aerial oxidation of 57 in 87% yield. From there on, the respective ε-lactam 59 was synthesised through oxime formation and Beckmann rearrangement with neat polyphosphoric acid in 84% over two steps. The monomers for the dipropyl analogue of nylon-6,6 polyamide, diacid 60 and diamine 61, were synthesised by catalytic oxidative C–C-bond cleavage of 58, subsequent conversion to the diamide followed by reduction of the latter to yield 61. For the implementation of this step on a laboratory scale, the unfavourable borane–THF complex was used as the stoichiometric reducing agent. As an ecologically more acceptable alternative the Ru/triphos hydrogenation reaction developed by Beller et al. could be employed.110
Polymerisation of the respective monomers by means of an anionic ring opening polymerisation for 59 and polycondensation in the case of 60/61 led to xylochemical, propyl-functionalised versions of nylon-6 and nylon-6,6 with reasonable dispersity in moderate yields of 52% and 62%, respectively. Both resulting polymers show unusually low glass transition temperatures (Tg) of 15 °C in case of polylactam 62 and 28 °C for A2B2-type polyamide 63.
2.3.2. Polylactic acid.
Polylactic acid (PLA) is currently the most promising polymer available from renewable resources.111,112 Its monomer lactic acid (64) can be obtained via fermentation of carbohydrates, corn or sugar beets.104
Biodegradation is not an inherent property of polymers, just because their monomers can be obtained from biomass. PLA however shows excellent biodegradability and decomposes only to H2O, CO2 and humus.113,114 PLA finds application in biomedical-devices, coatings, 3D printing, fibres and packagings.113,115,116
Lactide (65), the dimeric self-condensation product of lactic acid (64), can also be used as a building block for polymerisations. Its ring-opening polymerisation (ROP) is one of the most promising synthetic methods (Scheme 6).117,118
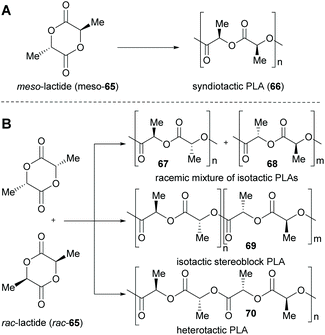 |
| Scheme 6 Polymerisation of meso-65 (A) and rac-65 (B) to different PLA structures 66–70. | |
Dependent on the relative configuration of the starting material (i.e. whether the meso lactide or the racemic mixture of (R,R)- and (S,S)-lactide is used), a variety of PLA structures (atactic, isotactic, heterotactic and syndiotactic) can be obtained, (A and B), which differ in their materials properties.119–121 Companies (e.g. NatureWorks LLC) are already producing biobased polylactide polymers on an industrial scale (nameplate capacity of 150
000 t per year)122 and have performed life cycle assessments as well as ecoprofile investigations.123,124 Furthermore, industry is currently assessing new technologies to use microorganisms to convert CO2 and methane into lactic acid.125,126
2.3.3. CO2 as C1-feedstock.
CO2 is a cheap, nontoxic, and extremely abundant C1 feedstock.127,128 Since it acts as greenhouse gas and is believed to be a major contributor to the recent change of the global climate, the utilisation of CO2 for synthetic purposes is highly desirable. The fixation and valorisation of CO2 has triggered many research initiatives and has resulted in numerous examples in the literature (Scheme 7A–C).129–131 Yet, the overall CO2-balance including the consumed energy ultimately needs to be taken into account.
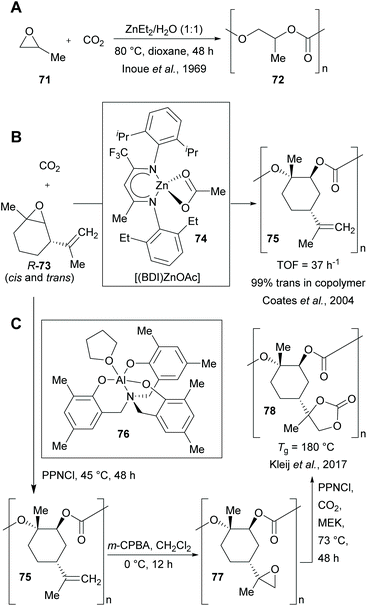 |
| Scheme 7 Copolymerisation of CO2 with propylene oxide (71, A) or (R)-limonene oxide ((R)-73) (B and C). ([(BDI)ZnOAc] (74) = β-diiminate zinc acetate complex, turnover frequency (TOF) = mol 73 (mol Zn)−1 h−1), PPNCl = (bis-triphenylphosphine iminium chloride). | |
The copolymerisation of CO2 and an epoxide (e.g. propylene oxide (71)) with organometallic catalysts (e.g. Et2Zn) at ambient temperature was discovered in the 1960s by Inoue et al.132 This opened up an alternative route to the phosgene process for the production of polycarbonates, which suffers from environmental and safety problems due to the involvement of the highly toxic and corrosive COCl2.133
In 2004, Coates et al. developed the alternating copolymerisation of CO2 with (R)-limonene oxide ((R)-73, mixture of cis- and trans-diastereomer) to give a highly regio- and stereoregular, biodegradable polycarbonate.134 Epoxide 73 is derived from limonene, the most common terpene (produced by >300 plant species) and major component of oils from citrus peels.135,136 The Kleij lab is also very active in the field of CO2/terpene epoxide copolymerization.137–139
2.3.4. Cyclic lactones.
Renewable, cyclic alternatives to methyl methacrylate (79, MMA, Scheme 8A) are vinylidene lactones like α-methylene-γ-butyrolactone (80, MBL, Scheme 8B) or its methyl derivate γ-methyl-α-methylene-γ-butyrolactone (81, MMBL, Scheme 8B).121,140 The former monomer is also known as tulipalin A due to its natural occurrence in tulips,141,142 while the latter monomer can be obtained from biomass derived levulinic acid (6) and formaldehyde.140
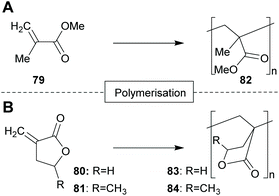 |
| Scheme 8 Polymerisation of MMA 79 (A) vs. MBL 80 and MMBL 81 (B). | |
PMMA (82)143 is widely used as a substitute for glass144 as well as for biomedical-,145 sensor-,146 or nanotechnology147 applications. PMBL (83) can be used for high temperature applications, due to its high thermal stability and the very high glass transition temperature.148 PMMBL (84) possess a higher glass transition temperature than PMMA (82) and exhibits excellent resistance to common organic solvents.149,150
Another emerging platform chemical available from renewable resources is succinic acid (7). It can be produced by micro-organisms via an anaerobic conversion under consumption of CO2.151 Untreated whey, wood hydrolysate or corn steep liquor can be used as the raw material for this process.152,153 Succinic acid (7) can either be transformed into commodity or fine chemicals,39,40,154 or serve as a building block for the synthesis of poly(esteramides), polyamides or polyesters.151,155,156
Its derivatives are also used in compositions for lubricants or as fuel additives.157–159
2.4. Oils and fatty acids
Another compound class suitable for the preparation of biodegradable polymers with industrial applications are fatty acids and plant oils, which can also be regarded as xylochemicals.160–162 Vegetable oils from soy, rapeseed, cotton, peanut, sunflower, ricinus, olive, and coconut as well as tall oil, a side stream from wood pulping, are important sources for renewable raw materials. They are widely used for the production of surfactants, paint formulations, flooring materials, cosmetic products, and lubricants.121,163–165 The mostly found fatty acids in the nature (stearic acid (85), palmitic acid (86), oleic acid (87), linoleic acid (88), linolenic acid (89) and ricinoleic acid (90)) are present as triglycerides in vegetable oils.163,165
Unsaturated fatty acids and vegetable oils can undergo various oxidation reactions like epoxidation-, bishydroxylation- or carbon–carbon-bond cleavage reactions.166,167 For the formation of C–C-bonds, pericyclic-,168 ionic-169 and radical170,171 reactions can be employed. Olefin metathesis reactions in lipids were first observed by a homogeneous WCl6/Me4Sn catalyst,172 but can more conveniently be performed with well-known ruthenium catalysts.173,174 This type of reaction was improved by Gooßen et al. by developing a bifunctional catalyst system consisting of a dimeric palladium(I) complex for a double-bond migration and a ruthenium complex for the olefin metathesis. With this system, fatty acids and esters can be transformed into olefin mixtures with controllable chain length distributions adjustable in their mean and span.175 These kinds of blends were tested as additives for biodiesel176 or as building blocks in polymerisation reactions177,178 and represent interesting recent examples of the integration of oleochemicals into the chemical value chain. The group of Biermann reported a protocol for the transesterification of calendula oil and tung oil with alcohols such as methanol, ethanol or isopropanol. The respective esters were then tested in coating formulations as reactive diluents for alkyd resins.179 Conventional diluents are volatile organic compounds (VOCs) which are added to lacquers or resins to reduce their viscosity and evaporate during the drying process. In contrast, reactive diluents participate in the cross-linking process and remain in the resin while influencing the viscosity as well as the physical properties after curing.180 The substitution of volatile organic solvents by reactive diluents is also reducing the emission of volatile substances into the atmosphere.181 Mixed canola oil esters using methanol, ethanol or a mixture of both were synthesized by Dalai et al. for the use as lubricity additives for diesel fuels in order to compensate for the reduced sulphur content required by the authorities.182
2.5. Surfactants
2.5.1. Cashew nut shell liquid.
Cashew nut shell liquid (CNSL) is a sustainable, nonedible feedstock, which is recently gaining attention and application in various areas. The annual production of cashew nuts in 2017 added up to 3.97 million metric tons and they can therefore be seen as a major agricultural product.183 Whereas the nut itself is the desired product for consumption, the shells usually end up as compostable waste or are incinerated for energy production. On the other hand, the cold ethanol extract of this waste product delivers the cashew nut shell liquid itself which stands out for its high content of up to 95% of pentadecyl(ene) substituted phenolics, namely anacardic acid (91), which makes up to 70%, cardanol (92) and cardol (93, Scheme 9A).184–187 These unique compounds found use in natural product synthesis,188 fuel research,189 polymer chemistry,190–192 and the synthesis of fine chemicals.193–195 Furthermore, the pentadecyl moiety is interesting for the design of functional materials where lipophilicity is desired.
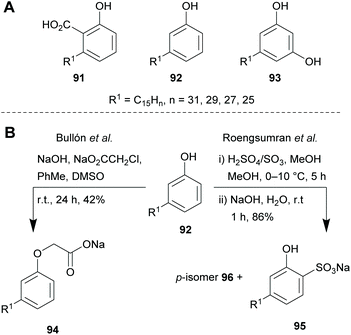 |
| Scheme 9 Constituents of CNSL (A) and syntheses of anionic surfactants 89 and 90 (B). | |
Based on this idea and the surface-activity of sodium anacardate already discovered in 1958,196 various surface-active compounds have been derived from cardanol (92). Five decades later, the groups of Bullón and Roengsumran synthesised anionic surfactants in the form of sodium 2-O-cardanyl acetate (94)197 and sodium cardanol sulfonate (95),198 respectively (Scheme 9B). The Gooßen group prepared a variety of 3-pentadecylcyclohexyl-substituted surfactants in the form of betaines, N-oxides and quaternary ammonium salts from technical CNSL in a straightforward, eco-friendly fashion (Scheme 10).199
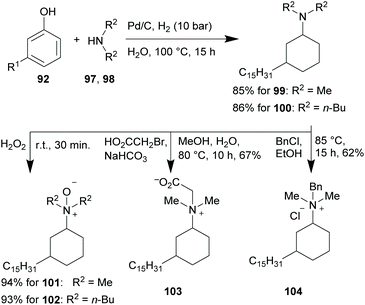 |
| Scheme 10 Synthesis of cyclohexyl based surfactants from cardanol (87) by Gooßen et al. | |
The respective cardanol-derived tertiary amine intermediates (99–100) were produced in a one-pot phenol hydrogenation to the corresponding cyclohexanone and a subsequent reductive amination sequence in aqueous solution. Moderate to high yields with an exceptionally low E-factor of 1.99 (4.84 with water included) in the case of 99 were achieved. The E-factor is specified as the mass ratio of the total waste produced and the product formed.200,201 The N-oxides 101 and 102 were synthesised in an equally green fashion by reacting 99 and 100 with aqueous hydrogen peroxide at ambient temperature in yields of 94% and 93%, respectively. Furthermore, 101 could also be synthesised in a two-step, one-pot sequence starting from 92 with a yield of 71%. Betaine 103 and quaternary ammonium salt 104 were produced by standard procedures from 99 with moderate yields of 67% and 62%, respectively.
2.5.2. Carbohydrates.
The group of Palkovits202 opted for the synthesis of anionic surfactants from the (hemi)cellulose-derivable dialcohols cyclopentanediol (105, CPD),203 2,5-bis(hydroxymethyl)furan (106, BHMF), 2,5-bis(hydroxymethyl)-tetrahydrofuran (107, BHMTHF)204 as well as fatty acid-based 1-dodecanol (108)205 and tetradec-1-ene (109).206–208 The key step of this approach was the acid-catalysed etherification of the diols with the respective fatty alcohol and olefin. Subsequently, the second hydroxy group was converted into a sulfate monoester by reaction with pyridine–SO3 (Scheme 11). Although the yields of the etherification step were low and high temperatures were necessary throughout the sequence, these novel surfactants were constructed entirely from starting materials derived from sustainable carbon sources. This step was conducted under catalytic conditions using either 5 mol% of sulfuric acid or 5 wt% of the cation exchanger Amberlyst® 15 or the zeolite beta H-BEA 150. Furthermore, the reactions could be performed in a favourable solvent or even in a solvent-free fashion.
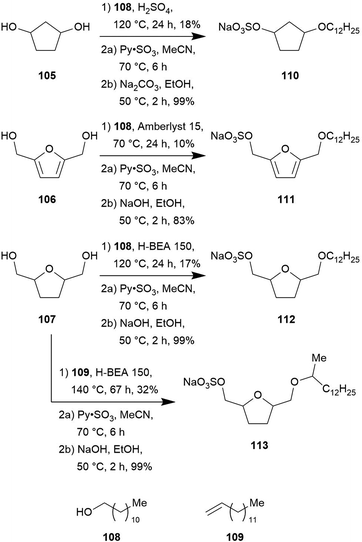 |
| Scheme 11 Synthesis of cellulose based surfactants by Palkovits et al. (Amberlyst® 15 and zeolite H-BEA 150 are commercially available catalysts). | |
The presented etherification approach is very eco-friendly as water is the only by-product.
Comparison of the surface-activity properties of the cardanol- and carbohydrate-derived surfactants with sodium dodecylbenzenesulfonate (SDBS, 114), one of the most widely used and potent surfactants proves the exceptional potential of these biomass-based compounds (Table 3). Their values for the critical micellar concentration (CMC) as well as for the surface tension at the CMC are highly similar.
Table 3 Surface-activity properties of cardanol derived surfactants and SDBS (109)
Compound |
CMC (μmol L−1) |
Surface tension at CMC (mN m−1) |
94
|
830 |
29.2 |
95
|
372 000 |
32.3 |
101
|
28 |
ca. 35 |
103
|
10 |
ca. 31 |
104
|
5 |
ca. 41 |
110
|
349 |
3.5 |
112
|
124 |
4.0 |
113
|
255 |
4.2 |
SDBS (114)212 |
2000 |
ca. 31 |
Zhou et al. used glucose or lactose (obtained from cheese whey, a by-product of the dairy industry) with canola oil to produce enzyme-catalysed sophorose lipids (up to 160 g L−1) as biosurfactants.209
2.6. UV-absorbers
The phenolic hydroxy group of the CNSL constituents not only allows synthetic modification but also serves as a hydrogen bond donor. This permits the synthesis of photostable organic UV-filters which rely on the excited state intramolecular proton transfer (ESIPT) mechanism, for which O–H⋯H and O–H⋯N hydrogen bonds play a crucial role.210,211 Since those compounds usually find application in lipophilic formulations like sunscreens, finishes, coatings or polymers, the nonpolar pentadecyl chain of the CNSL ingredients was assumed to be beneficial for the solubility in these formulations. The groups of de Koning and Opatz opted for the syntheses of cardanol (92) as well as anacardic acid (91) derived UV-absorbers as potential protectants.213,214
A variety of different compound classes exhibiting hydrogen–oxygen or hydrogen–nitrogen bonds like 2,2′-dihydroxybenzophenones 115–118, 3-hydroxyflavone 119, 1,8-dihydroxyxanthones 120, or s-triazines 121 were synthesised by simple transformations (Scheme 12). Throughout these syntheses, the saturated derivatives of the CNSL constituents were used in order to obtain pure single compounds. Besides 91 and 92 as biomass-derived starting materials, all other organic reagents were selected to be accessible from renewable resources to further improve the eco-friendliness in this approach. Benzophenones 115–117 were synthesised from anacardic acid (91), whereas the all other presented compounds were produced from the hydrogenation product of 92.
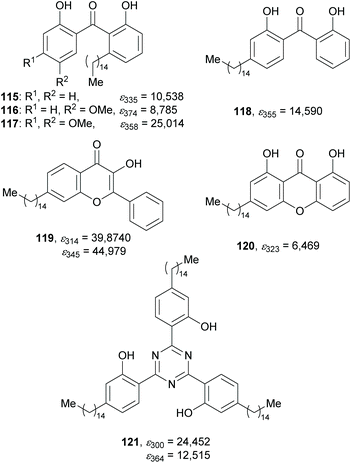 |
| Scheme 12 Examples of the synthesised UV-absorbing compounds by Opatz et al. and their respective ε values (in L mol−1 cm−1). | |
Comparison of the molar extinction coefficients (ε) of these compounds with the values of commercially available state-of-the-art UV-protectants like oxybenzone (OB, ε287 = 15
150 L mol−1 cm−1), 2-ethylhexyl 4-methoxycinnamate (OMC, ε356 = 39
470 L mol−1 cm−1) and avobenzone (ε310 = 31
670 L mol−1 cm−1)215 displays the potential of the CNSL-derived compounds as UV-filters. In particular, flavone 119 and s-triazine 121 show remarkable properties regarding the UV absorption spectra as well as the ε values which parallel those of commercial products. Building on these promising results, the implementation of a scalable synthesis could lead to a potential substitution of conventional UV-filters by these eco-friendly alternatives.
3. Conclusions
In addition to the conversion of lignin in the production of syngas216 or biofuels,217,218 technical grade lignin has found application as a replacement for chemically defined phenols and polyols in the manufacturing of resins, polyurethane foams, carbon fibres or additives in bitumen.219–222 However, the valorisation of lignin needs to be cost-competitive and is ideally integrated in high-value commercial applications.223,224 The catalysts employed in production and transformations of xylochemicals need to be improved with the aim of operating under mild conditions and possessing a long lifetime as well as a high selectivity while being tolerant towards the inevitable impurities contained. Furthermore, an efficient purification process (e.g. membrane processes such as organic solvent nanofiltration)225,226 as well as by-product and waste management are crucial to the sustainability of the whole process, while conventional methods of purification (e.g. chromatography and distillation) are material and energy inefficient and should be avoided.227,228
A main goal of this review was to showcase possible benefits of the use of xylochemicals and how they can be employed in total syntheses or the manufacturing of products with an industrial application. To this end, a variety of platform chemicals and the procedures to obtain them from woody biomass were presented.
These technical possibilities are particularly important in the light of increasing atmospheric CO2 levels and the depletion of formerly rich underground deposits of fossil carbon sources. There is a growing need to switch from fossil resources to renewable starting materials available from biomass which do not compete with agricultural food production. In some cases, the obtained materials and products can even provide superior properties relative to petroleum-based commodities, as in the case of biodegradable polymers or promising absorption characteristics as in the case of UV-absorbers. This scenario should provide a formidable challenge and motivation for today's chemists to develop renewable alternatives which ideally require no further replacement at any point. Future challenges lie instead in the exploitation of new renewable feedstocks for accessing additional platform chemicals and to broaden the product scope while maintaining a favourable ecological profile. Also, further side- or waste-streams should be reconsidered as possible raw materials in the light of new technologies and of the true cost of the use of fossil resources.
Conflicts of interest
There are no conflicts to declare.
Acknowledgements
We thank the members of the STANCE consortium (Sustainable Technology for a New Chemical Economy) for helpful discussions. Financial support from the German Federal Ministry of Education and Research (BMBF, grant no. 01DG17013) is gratefully acknowledged.
Notes and references
- D. Stubba, G. Lahm, M. Geffe, J. W. Runyon, A. J. Arduengo III and T. Opatz, Angew. Chem., Int. Ed., 2015, 54, 14187–14189 CrossRef CAS PubMed.
- D. Stubba, G. Lahm, M. Geffe, J. W. Runyon, A. J. Arduengo III and T. Opatz, Angew. Chem., 2015, 127, 14394–14396 CrossRef.
- L. Wu, T. Moteki, A. A. Gokhale, D. W. Flaherty and F. D. Toste, Chem, 2016, 1, 32–58 CrossRef CAS PubMed.
-
R. L. Braun and A. K. Burnham, Chemical reaction model for oil and gas generation from type 1 and type 2 kerogen, Lawrence Livermore National Lab., CA (United States), 1993 Search PubMed.
- R. A. Sheldon, Curr. Opin. Green Sustainable Chem., 2019, 18, 13–19 CrossRef.
- R. A. Sheldon and J. M. Woodley, Chem. Rev., 2018, 118, 801–838 CrossRef CAS PubMed.
- S. Chu and A. Majumdar, Nature, 2012, 488, 294–303 CrossRef CAS PubMed.
- D. M. Alonso, J. Q. Bond and J. A. Dumesic, Green Chem., 2010, 12, 1493–1513 RSC.
- I. Parmar and H. V. Rupasinghe, Bioresour. Technol., 2013, 130, 613–620 CrossRef CAS PubMed.
- R. Liguori, C. R. Soccol, L. Porto de Souza Vandenberghe, A. L. Woiciechowski and V. Faraco, Energies, 2015, 8, 2575–2586 CrossRef CAS.
- R. A. Verlinden, D. J. Hill, M. A. Kenward, C. D. Williams, Z. Piotrowska-Seget and I. K. Radecka, AMB Express, 2011, 1, 11 CrossRef PubMed.
- V. L. Budarin, P. S. Shuttleworth, J. R. Dodson, A. J. Hunt, B. Lanigan, R. Marriott, K. J. Milkowski, A. J. Wilson, S. W. Breeden and J. Fan, Energy Environ. Sci., 2011, 4, 471–479 RSC.
-
J. H. Clark and F. Deswarte, Introduction to chemicals from biomass, Wiley-VCH, 2014 Search PubMed.
- H. Alizadeh, F. Teymouri, T. I. Gilbert and B. E. Dale, Appl. Biochem. Biotechnol., 2005, 124, 1133–1141 CrossRef.
- R. Ravindran and A. K. Jaiswal, Trends Biotechnol., 2016, 34, 58–69 CrossRef CAS PubMed.
- O. M. Adeniyi, U. Azimov and A. Burluka, Renewable Sustainable Energy Rev., 2018, 90, 316–335 CrossRef.
-
S. Prasad and A. P. Ingle, in Sustainable Bioenergy, ed. M. Rai and A. P. Ingle, Elsevier, 2019, pp. 327–346 Search PubMed.
- A. Ajanovic, Energy, 2011, 36, 2070–2076 CrossRef.
- D. Graham-Rowe, Nature, 2011, 474, S6–S8 CrossRef CAS PubMed.
- B. Kamm, Angew. Chem., Int. Ed., 2007, 46, 5056–5058 CrossRef CAS PubMed.
- R. A. Sheldon, Green Chem., 2014, 16, 950–963 RSC.
- A. J. J. Straathof, Chem. Rev., 2014, 114, 1871–1908 CrossRef CAS PubMed.
-
D. J. Hayes, S. Fitzpatrick, M. H. Hayes and J. R. Ross, in Biorefineries–Industrial Processes and Product, Wiley-VCH, Weinheim, 2006, vol. 1, pp. 139–164 Search PubMed.
- V. Menon and M. Rao, Prog. Energy Combust. Sci., 2012, 38, 522–550 CrossRef CAS.
- K. Zhang, Z. Pei and D. Wang, Bioresour. Technol., 2016, 199, 21–33 CrossRef CAS PubMed.
-
F. Stecker, I. M. Malkowsky, A. Fischer, S. R. Waldvogel and C. Regenbrecht, US Pat, US20140034508, 2014 Search PubMed.
- D. Schmitt, C. Regenbrecht, M. Hartmer, F. Stecker and S. R. Waldvogel, Beilstein J. Org. Chem., 2015, 11, 473–480 CrossRef CAS PubMed.
- M. Zirbes and S. R. Waldvogel, Curr. Opin. Green Sustainable Chem., 2018, 14, 19–25 CrossRef.
- Y. Román-Leshkov, J. N. Chheda and J. A. Dumesic, Science, 2006, 312, 1933–1937 CrossRef PubMed.
-
K. J. Zeitsch, The chemistry and technology of furfural and its many by-products, Elsevier, 2000 Search PubMed.
-
S. W. Fitzpatrick, US Pat, US4897497A, 1990 Search PubMed.
-
S. W. Fitzpatrick, US Pat, US5608105A, 1997 Search PubMed.
-
P. Saling, P. Spicher, R. Schröder, M. Kaltschmitt, E. Dinjus, F. Seyfried, K. Hill, C. Estéves, A. Gozzo and M. Kunz, Sustainable solutions for modern economies, RCS Publishing, 2009 Search PubMed.
- J. Akhtar, A. Idris and R. Abd. Aziz, Appl. Microbiol. Biotechnol., 2014, 98, 987–1000 CrossRef CAS PubMed.
- H. Choudhary, S. Nishimura and K. Ebitani, Appl. Catal., A, 2013, 458, 55–62 CrossRef CAS.
-
F. Cherubini and A. H. Strømman, Chemicals from lignocellulosic biomass: opportunities, perspectives, and potential of biorefinery systems, Wiley-VCH, Weinheim, 2011 Search PubMed.
- M. Rose and R. Palkovits, Macromol. Rapid Commun., 2011, 32, 1299–1311 CrossRef CAS PubMed.
- M. Mascal and E. B. Nikitin, Green Chem., 2010, 12, 370–373 RSC.
-
T. Werpy and G. Petersen, Top value added chemicals from biomass: volume I–results of screening for potential candidates from sugars and synthesis gas, National Renewable Energy Lab., Golden, CO (US), 2004 Search PubMed.
-
B. Kamm, P. R. Gruber and M. Kamm, Biorefineries-industrial processes and products, Wiley-VCH, Weinheim, 2006 Search PubMed.
- X. Qi, M. Watanabe, T. M. Aida and R. L. Smith Jr., Green Chem., 2010, 12, 1855–1860 RSC.
- E. L. Kunkes, D. A. Simonetti, R. M. West, J. C. Serrano-Ruiz, C. A. Gärtner and J. A. Dumesic, Science, 2008, 322, 417 CrossRef CAS PubMed.
-
L. E. Manzer, EPO, EP1368333A1, 2003 Search PubMed.
- F. Jin and H. Enomoto, BioResources, 2009, 4, 704–713 CAS.
- P. L. Rivilli, G. I. Yranzo and J. D. Pérez, BioResources, 2011, 6, 2703–2710 CAS.
- A. Deneyer, T. Renders, J. Van Aelst, S. Van den Bosch, D. Gabriëls and B. F. Sels, Curr. Opin. Chem. Biol., 2015, 29, 40–48 CrossRef CAS PubMed.
- J. S. Luterbacher, D. Martin Alonso and J. A. Dumesic, Green Chem., 2014, 16, 4816–4838 RSC.
- J. C. Serrano-Ruiz, R. M. West and J. A. Dumesic, Annu. Rev. Chem. Biomol. Eng., 2010, 1, 79–100 CrossRef CAS PubMed.
- J. Q. Bond, D. Martin Alonso, R. M. West and J. A. Dumesic, Langmuir, 2010, 26, 16291–16298 CrossRef CAS PubMed.
- J. Kühlborn, J. Groß and T. Opatz, Nat. Prod. Rep., 2020, 37, 380–424 RSC.
- S. Van den Bosch, S.-F. Koelewijn, T. Renders, G. Van den Bossche, T. Vangeel, W. Schutyser and B. Sels, Top. Curr. Chem., 2018, 376, 36 CrossRef CAS PubMed.
- A. Lipp, D. Ferenc, C. Gütz, M. Geffe, N. Vierengel, D. Schollmeyer, H. J. Schäfer, S. R. Waldvogel and T. Opatz, Angew. Chem., Int. Ed., 2018, 57, 11055–11059 CrossRef CAS PubMed.
- A. Lipp, D. Ferenc, C. Gütz, M. Geffe, N. Vierengel, D. Schollmeyer, H. J. Schäfer, S. R. Waldvogel and T. Opatz, Angew. Chem., 2018, 130, 11221–11225 CrossRef.
- B. Pfundstein, S. K. El Desouky, W. E. Hull, R. Haubner, G. Erben and R. W. Owen, Phytochemistry, 2010, 71, 1132–1148 CrossRef CAS PubMed.
-
I. W. Southon and J. Buckingham, Dictionary of Alkaloids, with CD-ROM, CRC Press, 1989 Search PubMed.
- S. Ghosal and R. S. Srivastava, Phytochemistry, 1973, 12, 193–197 CrossRef CAS.
- M. A. Schwartz, Synth. Commun., 1973, 3, 33–35 CrossRef CAS.
- M. A. Schwartz and I. S. Mami, J. Am. Chem. Soc., 1975, 97, 1239–1240 CrossRef CAS PubMed.
- B. Franck, G. Dunkelmann and H. Lubs, Angew. Chem., Int. Ed. Engl., 1967, 6, 1075–1076 CrossRef CAS PubMed.
- D. H. R. Barton, D. S. Bhakuni, R. James and G. W. Kirby, J. Chem. Soc. C, 1967, 128–132 RSC.
- T. Kametani, T. Sugahara, H. Yagi and K. Fukumoto, Tetrahedron, 1969, 25, 3667–3673 CrossRef CAS.
- G. Lahm, J.-G. Deichmann, A. L. Rauen and T. Opatz, J. Org. Chem., 2015, 80, 2010–2016 CrossRef CAS PubMed.
- J. C. Orejarena Pacheco, G. Lahm and T. Opatz, J. Org. Chem., 2013, 78, 4985–4992 CrossRef CAS PubMed.
- J. C. Liermann and T. Opatz, J. Org. Chem., 2008, 73, 4526–4531 CrossRef CAS PubMed.
- S. M. Klein, C. Zhang and Y. L. Jiang, Tetrahedron Lett., 2008, 49, 2638–2641 CrossRef CAS.
- T. R. Nunn, J. B. Howard, J. P. Longwell and W. A. Peters, Ind. Eng. Chem. Process Des. Dev., 1985, 24, 844–852 CrossRef CAS.
- A. Lipp, M. Selt, D. Ferenc, D. Schollmeyer, S. R. Waldvogel and T. Opatz, Org. Lett., 2019, 21, 1828–1831 CrossRef CAS PubMed.
- M. A. A. Endoma-Arias, M. Makarova, H. E. Dela Paz and T. Hudlicky, Synthesis, 2019, 225–232 CAS.
- V. Fajardo, C. Cárcamo and B. Moreno, Heterocycles, 1996, 5, 949–951 CrossRef.
-
J. Rowe and A. Conner, General Technical Report FPL-United States, 1979 Search PubMed.
- T. Fedorova, S. Fedorov and V. Babkin, Russ. J. Bioorg. Chem., 2019, 45, 927–932 CrossRef CAS.
- M. Z. M. Salem and M. Böhm, BioResources, 2013, 8, 4775–4790 Search PubMed.
- J. Guyot and L. J. Simon, C. R. Hebd. Seances Acad. Sci., 1919, 169, 795–797 CAS.
- R. A. Sheldon, Chem. Soc. Rev., 2012, 41, 1437–1451 RSC.
- C.-J. Chen, W.-S. Lee and A. Bhan, Appl. Catal., A, 2016, 510, 42–48 CrossRef CAS.
- C. Grundke and T. Opatz, Green Chem., 2019, 21, 2362–2366 RSC.
- A. M. Nauth, N. Otto and T. Opatz, Adv. Synth. Catal., 2015, 357, 3424–3428 CrossRef CAS.
- J. Kühlborn, M. Konhäuser, J. Groß, P. R. Wich and T. Opatz, ACS Sustainable Chem. Eng., 2019, 4414–4419 CrossRef.
- M. Melián-Rodríguez, S. Saravanamurugan, S. Kegnæs and A. Riisager, Top. Catal., 2015, 58, 1036–1042 CrossRef.
- A. Rahimi, A. Azarpira, H. Kim, J. Ralph and S. S. Stahl, J. Am. Chem. Soc., 2013, 135, 6415–6418 CrossRef CAS PubMed.
- L. Gavara, T. Boisse, J.-P. Hénichart, A. Daïch, B. Rigo and P. Gautret, Tetrahedron, 2010, 66, 7544–7561 CrossRef CAS.
- D. Orphanos and A. Taurins, Can. J. Chem., 1966, 44, 1875–1879 CrossRef CAS.
- W. H. Perkin, Proc. R. Soc. London, 1862, 12, 713–715 Search PubMed.
- A. von Baeyer and V. Drewsen, Ber. Dtsch. Chem. Ges., 1882, 15, 2856–2864 CrossRef.
- A. von Baeyer and V. Drewsen, Ber. Dtsch. Chem. Ges., 1883, 16, 2205–2208 CrossRef.
- A. von Baeyer and A. Emmerling, Ber. Dtsch. Chem. Ges., 1870, 3, 514–517 CrossRef.
-
P. Rys and H. Zollinger, Farbstoffchemie: ein Leitfaden, Verlag Chemie, Weinheim, 3 edn, 1982 Search PubMed.
-
N. Welsch and C. C. Liebmann, Farben: Natur, Technik, Kunst, Spektrum Akademischer Verlag, Heidelberg, 3rd edn, 2012 Search PubMed.
- J. Kühlborn, A.-K. Danner, H. Frey, R. Iyer, A. J. Arduengo and T. Opatz, Green Chem., 2017, 19, 3780–3786 RSC.
-
J. Liu, Liquid Explosives, Springer, Berlin, Heidelberg, 2015 Search PubMed.
- J. Saska, Z. Li, A. L. Otsuki, J. Wei, J. C. Fettinger and M. Mascal, Angew. Chem., 2019, 58, 17293–17296 CrossRef CAS PubMed.
- Q. Girka, B. Estrine, N. Hoffmann, J. Le Bras, S. Marinković and J. Muzart, React. Chem. Eng., 2016, 1, 176–182 RSC.
- M. Zirbes, D. Schmitt, N. Beiser, D. Pitton, T. Hoffmann and S. R. Waldvogel, ChemElectroChem, 2019, 6, 155–161 CrossRef CAS.
- M. D. Kärkäs, B. S. Matsuura, T. M. Monos, G. Magallanes and C. R. J. Stephenson, Org. Biomol. Chem., 2016, 14, 1853–1914 RSC.
- M. Fache, B. Boutevin and S. Caillol, ACS Sustainable Chem. Eng., 2016, 4, 35–46 CrossRef CAS.
- F. P. Byrne, S. Jin, G. Paggiola, T. H. M. Petchey, J. H. Clark, T. J. Farmer, A. J. Hunt, C. Robert McElroy and J. Sherwood, Sustainable Chem. Processes, 2016, 4, 7 CrossRef.
- K. Galyan and J. Reilly, Curr. Opin. Green Sustainable Chem., 2018, 11, 76–80 CrossRef.
- A. J. Ragauskas, G. T. Beckham, M. J. Biddy, R. Chandra, F. Chen, M. F. Davis, B. H. Davison, R. A. Dixon, P. Gilna and M. Keller, Science, 2014, 344, 1246843 CrossRef PubMed.
- B. M. Upton and A. M. Kasko, Chem. Rev., 2016, 116, 2275–2306 CrossRef CAS PubMed.
- S. Sen, S. Patil and D. S. Argyropoulos, Green Chem., 2015, 17, 4862–4887 RSC.
- D. M. Alonso, S. H. Hakim, S. Zhou, W. Won, O. Hosseinaei, J. Tao, V. Garcia-Negron, A. H. Motagamwala, M. A. Mellmer and K. Huang, Sci. Adv., 2017, 3, e1603301 CrossRef PubMed.
- J. Artz and R. Palkovits, Curr. Opin. Green Sustainable Chem., 2018, 14, 14–18 CrossRef.
- E. E. Harris, J. D'Ianni and H. Adkins, J. Am. Chem. Soc., 1938, 60, 1467–1470 CrossRef CAS.
- H. Danner and R. Braun, Chem. Soc. Rev., 1999, 28, 395–405 RSC.
- Y. Jiang, D. Maniar, A. J. J. Woortman, G. O. R. Alberda van Ekenstein and K. Loos, Biomacromolecules, 2015, 16, 3674–3685 CrossRef CAS PubMed.
- M. Winnacker, M. Neumeier, X. Zhang, C. M. Papadakis and B. Rieger, Macromol. Rapid Commun., 2016, 37, 851–857 CrossRef CAS PubMed.
- M. Winnacker and B. Rieger, Macromol. Rapid Commun., 2016, 37, 1391–1413 CrossRef CAS PubMed.
- M. Winnacker and J. Sag, Chem. Commun., 2018, 54, 841–844 RSC.
- P. Zierdt, T. Theumer, G. Kulkarni, V. Däumlich, J. Klehm, U. Hirsch and A. Weber, Sustainable Mater. Technol., 2015, 6, 6–14 CrossRef CAS.
- J. R. Cabrero-Antonino, E. Alberico, K. Junge, H. Junge and M. Beller, Chem. Sci., 2016, 7, 3432–3442 RSC.
- M. Okada, Prog. Polym. Sci., 2002, 27, 87–133 CrossRef CAS.
- R. A. Gross and B. Kalra, Science, 2002, 297, 803–807 CrossRef CAS PubMed.
- R. E. Drumright, P. R. Gruber and D. E. Henton, Adv. Mater., 2000, 12, 1841–1846 CrossRef CAS.
- I. Vroman and L. Tighzert, Materials, 2009, 2, 307–344 CrossRef CAS.
- A. J. R. Lasprilla, G. A. R. Martinez, B. H. Lunelli, A. L. Jardini and R. M. Filho, Biotechnol. Adv., 2012, 30, 321–328 CrossRef CAS PubMed.
- K. Fukushima and Y. Kimura, Polym. Int., 2006, 55, 626–642 CrossRef CAS.
- C. M. Thomas, Chem. Soc. Rev., 2010, 39, 165–173 RSC.
- O. Dechy-Cabaret, B. Martin-Vaca and D. Bourissou, Chem. Rev., 2004, 104, 6147–6176 CrossRef CAS PubMed.
- Z. Zheng, G. Zhao, R. Fablet, M. Bouyahyi, C. M. Thomas, T. Roisnel, O. Casagrande Jr. and J.-F. Carpentier, New J. Chem., 2008, 32, 2279–2291 RSC.
- B. Lian, C. M. Thomas, O. L. Casagrande Jr., T. Roisnel and J.-F. Carpentier, Polyhedron, 2007, 26, 3817–3824 CrossRef CAS.
- M. J.-L. Tschan, E. Brulé, P. Haquette and C. M. Thomas, Polym. Chem., 2012, 3, 836–851 RSC.
- The manufacturing facility is located in Blair, Nebraska, USA.
- E. T. Vink, S. Davies and J. J. Kolstad, Ind. Biotechnol., 2010, 6, 212–224 CrossRef CAS.
- E. T. Vink and S. Davies, Ind. Biotechnol., 2015, 11, 167–180 CrossRef CAS.
-
R. M. Saville, S. Lee, D. D. REGITSKY, S. M. Resnick and J. Silverman, WIPO (PCT), WO2014205146A1, 2014 Search PubMed.
- NatureWorks, https://www.natureworksllc.com/News-and-Events/Press-Releases/2016/03-09-16-NatureWorks-Methane-to-Lactic-Acid-Fermentation-Lab and https://www.natureworksllc.com/What-is-Ingeo/Where-Ingeo-Comes-From, (accessed 20.04.2020).
- M. Scharfenberg, J. Hilf and H. Frey, Adv. Funct. Mater., 2018, 28, 1704302 CrossRef.
- C. J. Whiteoak, A. Nova, F. Maseras and A. W. Kleij, ChemSusChem, 2012, 5, 2032–2038 CrossRef CAS PubMed.
- M. Poliakoff, W. Leitner and E. S. Streng, Faraday Discuss., 2015, 183, 9–17 RSC.
- D. M. D'Alessandro, B. Smit and J. R. Long, Angew. Chem., Int. Ed., 2010, 49, 6058–6082 CrossRef PubMed.
- A. A. Olajire, Energy, 2010, 35, 2610–2628 CrossRef CAS.
- S. Inoue, H. Koinuma and T. Tsuruta, Macromol. Chem. Phys., 1969, 130, 210–220 CrossRef CAS.
- S. Fukuoka, I. Fukawa, T. Adachi, H. Fujita, N. Sugiyama and T. Sawa, Org. Process Res. Dev., 2019, 23, 145–169 CrossRef CAS.
- C. M. Byrne, S. D. Allen, E. B. Lobkovsky and G. W. Coates, J. Am. Chem. Soc., 2004, 126, 11404–11405 CrossRef CAS PubMed.
-
G. A. Burdock, Fenaroli's handbook of flavor ingredients, CRC press, 2016 Search PubMed.
- F. Parrino, A. Fidalgo, L. Palmisano, L. M. Ilharco, M. Pagliaro and R. Ciriminna, ACS Omega, 2018, 3, 4884–4890 CrossRef CAS PubMed.
- N. Kindermann, À. Cristòfol and A. W. Kleij, ACS Catal., 2017, 7, 3860–3863 CrossRef CAS.
- G. Fiorani, M. Stuck, C. Martín, M. M. Belmonte, E. Martin, E. C. Escudero-Adán and A. W. Kleij, ChemSusChem, 2016, 9, 1304–1311 CrossRef CAS PubMed.
-
J. E. Gómez and A. W. Kleij, in Adv. Organomet. Chem, ed. P. J. Pérez, Academic Press, 2019, vol. 71, pp. 175–226 Search PubMed.
- L. E. Manzer, Appl. Catal., A, 2004, 272, 249–256 CrossRef CAS.
- M. W. P. C. van Rossum, M. Alberda and L. H. W. van der Plas, Phytochemistry, 1998, 49, 723–729 CrossRef CAS.
- Y. Kato, H. Yoshida, K. Shoji, Y. Sato, N. Nakajima and S. Ogita, Tetrahedron Lett., 2009, 50, 4751–4753 CrossRef CAS.
- U. Ali, K. J. B. A. Karim and N. A. Buang, Polym. Rev., 2015, 55, 678–705 CrossRef CAS.
- M. M. Demir, M. Memesa, P. Castignolles and G. Wegner, Macromol. Rapid Commun., 2006, 27, 763–770 CrossRef CAS.
- Z. J. A. Amer, J. K. Ahmed and S. F. Abbas, Int. J. Eng. Technol., 2014, 4, 1–6 CrossRef.
- H. Lu, W. M. Huang, X. L. Wu, Y. C. Ge, F. Zhang, Y. Zhao and J. Geng, Smart Mater. Struct., 2014, 23, 067002 CrossRef.
- X. Wang, P. Wang, Y. Jiang, Q. Su and J. Zheng, Compos. Sci. Technol., 2014, 104, 1–8 CrossRef CAS.
- J. Mosnáček, J. A. Yoon, A. Juhari, K. Koynov and K. Matyjaszewski, Polymer, 2009, 50, 2087–2094 CrossRef.
- J. Suenaga, D. M. Sutherlin and J. K. Stille, Macromolecules, 1984, 17, 2913–2916 CrossRef CAS.
- G. M. Miyake, Y. Zhang and E. Y. X. Chen, Macromolecules, 2010, 43, 4902–4908 CrossRef CAS.
- I. Bechthold, K. Bretz, S. Kabasci, R. Kopitzky and A. Springer, Chem. Eng. Technol., 2008, 31, 647–654 CrossRef CAS.
- P. Lee, S. Lee, S. Hong, H. N. Chang and S. Park, Biotechnol. Lett., 2003, 25, 111–114 CrossRef CAS PubMed.
- P. C. Lee, W. G. Lee, S. Y. Lee, H. N. Chang and Y. K. Chang, Biotechnol. Bioprocess Eng., 2000, 5, 379–381 CrossRef CAS.
- C. Delhomme, D. Weuster-Botz and F. E. Kühn, Green Chem., 2009, 11, 13–26 RSC.
- C. Gioia, M. Vannini, P. Marchese, A. Minesso, R. Cavalieri, M. Colonna and A. Celli, Green Chem., 2014, 16, 1807–1815 RSC.
- I. Villuendas, J. J. Bou, A. Rodríguez-Galán and S. Muñoz-Guerra, Macromol. Chem. Phys., 2001, 202, 236–244 CrossRef CAS.
- A. Cukalovic and C. V. Stevens, Biofuels, Bioprod. Biorefin., 2008, 2, 505–529 CrossRef CAS.
-
G. Soula and P. Duteurtre, US Pat, US4199462A, 1978 Search PubMed.
-
R. H. Wollenberg and F. Plavac, US Pat, US4747850A, 1988 Search PubMed.
- Y. Lu and R. C. Larock, Biomacromolecules, 2006, 7, 2692–2700 CrossRef CAS PubMed.
- S. Matsumura and J. Takahashi, Macromol. Rapid Commun., 1986, 7, 369–373 CrossRef CAS.
- D. Teomim, A. Nyska and A. J. Domb, J. Biomed. Mater. Res., 1999, 45, 258–267 CrossRef CAS PubMed.
- U. Biermann, U. Bornscheuer, M. A. Meier, J. O. Metzger and H. J. Schäfer, Angew. Chem., Int. Ed., 2011, 50, 3854–3871 CrossRef CAS PubMed.
- U. Biermann and J. O. Metzger, Eur. J. Lipid Sci. Technol., 2008, 110, 805–811 CrossRef CAS.
- S. S. Gupta, T. P. Hilditch and J. P. Riley, J. Sci. Food Agric., 1951, 2, 245–251 CrossRef CAS.
- A. Köckritz and A. Martin, Eur. J. Lipid Sci. Technol., 2008, 110, 812–824 CrossRef.
-
G. Knothe, J. Kenar and F. Gunstone, The Lipid Handbook, CRC Press, Boca Raton, FL, 2007 Search PubMed.
- U. Biermann, W. Butte, T. Eren, D. Haase and J. O. Metzger, Eur. J. Org. Chem., 2007, 3859–3862 CrossRef CAS.
- U. Biermann and J. O. Metzger, J. Am. Chem. Soc., 2004, 126, 10319–10330 CrossRef CAS PubMed.
- J. G. O. Metzger and U. Riedner, Lipid/Fett, 1989, 91, 18–23 CrossRef CAS.
- G. B. Bantchev, J. A. Kenar, G. Biresaw and M. G. Han, J. Agric. Food Chem., 2009, 57, 1282–1290 CrossRef CAS PubMed.
- P. Van Dam, M. Mittelmeijer and C. Boelhouwer, J. Chem. Soc., Chem. Commun., 1972, 1221–1222 RSC.
- M. A. R. Meier, Macromol. Chem. Phys., 2009, 210, 1073–1079 CrossRef CAS.
- A. Rybak, P. A. Fokou and M. A. R. Meier, Eur. J. Lipid Sci. Technol., 2008, 110, 797–804 CrossRef CAS.
- D. M. Ohlmann, N. Tschauder, J.-P. Stockis, K. Gooßen, M. Dierker and L. J. Gooßen, J. Am. Chem. Soc., 2012, 134, 13716–13729 CrossRef CAS PubMed.
- R. E. Montenegro and M. A. R. Meier, Eur. J. Lipid Sci. Technol., 2012, 114, 55–62 CrossRef CAS.
- G. Heublein, H. Hartung, M. Helbig and D. Stadermann, J. Macromol. Sci., Chem., 1982, 17, 821–845 CrossRef.
- S. Huf, S. Krügener, T. Hirth, S. Rupp and S. Zibek, Eur. J. Lipid Sci. Technol., 2011, 113, 548–561 CrossRef CAS.
- U. Biermann, W. Butte, R. Holtgrefe, W. Feder and J. O. Metzger, Eur. J. Lipid Sci. Technol., 2010, 112, 103–109 CrossRef CAS.
- J. T. P. Derksen, F. Petrus Cuperus and P. Kolster, Prog. Org. Coat., 1996, 27, 45–53 CrossRef CAS.
- M. Eissen, J. O. Metzger, E. Schmidt and U. Schneidewind, Angew. Chem., Int. Ed., 2002, 41, 414–436 CrossRef CAS.
- M. G. Kulkarni, A. K. Dalai and N. N. Bakhshi, Bioresour. Technol., 2007, 98, 2027–2033 CrossRef CAS PubMed.
-
https://www.statista.com/statistics/967702/global-cashew-nut-production/
, (accessed March 23, 2020).
- J. Mgaya, G. B. Shombe, S. C. Masikane, S. Mlowe, E. B. Mubofu and N. Revaprasadu, Green Chem., 2019, 21, 1186–1201 RSC.
- E. B. Mubofu, Pure Appl. Chem., 2016, 88, 17–27 CAS.
- C. N. Subbarao, K. Krishna Prasad and V. Prasad, Pharm. Res. J., 2011, 6, 21–41 Search PubMed.
-
E. A. Taiwo, in Advances in Petrochemicals, Intech, Ile-Ife, 2015 Search PubMed.
- M. L. D. Santos and G. C. D. Magalhães, J. Braz. Chem. Soc., 1999, 10, 13–20 CrossRef.
- S. Kumar, P. Dinesha and M. A. Rosen, Energy Fuels, 2018, 32, 7237–7244 CrossRef CAS.
- M. C. Lubi and E. T. Thachil, Des. Monomers Polym., 2000, 3, 123–153 CrossRef CAS.
- A. S. Trita, L. C. Over, J. Pollini, S. Baader, S. Riegsinger, M. A. R. Meier and L. J. Gooßen, Green Chem., 2017, 19, 3051–3060 RSC.
- C. Voirin, S. Caillol, N. V. Sadavarte, B. V. Tawade, B. Boutevin and P. P. Wadgaonkar, Polym. Chem., 2014, 5, 3142–3162 RSC.
- L. Kisula, S. J. M. Mdachi, C. B. de Koning and Q. A. Mgani, Tanzania J. Sci., 2015, 41, 27–37 Search PubMed.
- J. E. Mgaya, E. B. Mubofu, Q. A. Mgani, D. B. Cordes, A. M. Slawin and D. J. Cole-Hamilton, Eur. J. Lipid Sci. Technol., 2015, 117, 190–199 CrossRef CAS.
- J. A. Mmongoyo, Q. A. Mgani, S. J. M. Mdachi, P. J. Pogorzelec and D. J. Cole-Hamilton, Eur. J. Lipid Sci. Technol., 2012, 114, 1183–1192 CrossRef CAS.
- A. K. Biswas and A. B. Roy, Nature, 1958, 182, 1299–1300 CrossRef CAS.
- C. Scorzza, J. Nieves, F. Vejar and J. Bullón, J. Surfactants Deterg., 2009, 13, 27 CrossRef.
- P. Peungjitton, P. Sangvanich, S. Pornpakakul, A. Petsom and S. Roengsumran, J. Surfactants Deterg., 2009, 12, 85–89 CrossRef CAS.
- V. Bragoni, R. K. Rit, R. Kirchmann, A. S. Trita and L. J. Gooßen, Green Chem., 2018, 20, 3210–3213 RSC.
- R. A. Sheldon, Chem. Ind., 1992, 903–906 CAS.
- R. A. Sheldon, Green Chem., 2007, 9, 1273–1283 RSC.
- L. Kipshagen, L. T. Vömel, M. A. Liauw, A. Klemmer, A. Schulz, C. Kropf, P. J. C. Hausoul and R. Palkovits, Green Chem., 2019, 21, 3882–3890 RSC.
- G. Li, N. Li, M. Zheng, S. Li, A. Wang, Y. Cong, X. Wang and T. Zhang, Green Chem., 2016, 18, 3607–3613 RSC.
- J. Ohyama, Y. Ohira and A. Satsuma, Catal. Sci. Technol., 2017, 7, 2947–2953 RSC.
-
K. Noweck and W. Grafahrend, in Ullmann's Encyclopedia of Industrial Chemistry, Wiley-VCH, Weinheim, 2006 Search PubMed.
- F. Krafft, Ber. Dtsch. Chem. Ges., 1883, 16, 3018–3024 CrossRef CAS.
-
S. Warwel, P. Bavaj and M. Rüsch, gen. Klaas and B. Wolff, in Perspektiven nachwachsender Rohstoffe in der Chemie, ed. H. Eierdanz, Wiley-VCH, Weinheim, 1996, pp. 119–135 Search PubMed.
- S. Warwel, F. Brüse, C. Demes, M. Kunz and M. Rüsch, gen. Klaas, Chemosphere, 2001, 43, 39–48 CrossRef CAS.
- Q.-H. Zhou and N. Kosaric, J. Am. Oil Chem. Soc., 1995, 72, 67–71 CrossRef CAS.
- A. Maliakal, G. Lem, N. J. Turro, R. Ravichandran, J. C. Suhadolnik, A. D. DeBellis, M. G. Wood and J. Lau, J. Phys. Chem. A, 2002, 106, 7680–7689 CrossRef CAS.
- P. F. McGarry, S. Jockusch, Y. Fujiwara, N. A. Kaprinidis and N. J. Turro, J. Phys. Chem. A, 1997, 101, 764–767 CrossRef CAS.
- G. Basu Ray, I. Chakraborty, S. Ghosh and S. P. Moulik, Colloid Polym. Sci., 2007, 285, 457–469 CrossRef CAS.
- K. J. Ngwira, J. Kühlborn, Q. A. Mgani, C. B. de Koning and T. Opatz, Eur. J. Org. Chem., 2019, 4778–4790 CrossRef CAS.
-
T. Opatz, J. Kühlborn, C. B. de Koning, K. J. Ngwira and Q. A. Mgani, South African provisional patent, ZA2019/01514, 2019 Search PubMed.
- H. M. Chawla, N. Pant, S. Kumar, S. Mrig, B. Srivastava, N. Kumar and D. S. Black, J. Photochem. Photobiol., B, 2011, 105, 25–33 CrossRef CAS PubMed.
- M. P. Pandey and C. S. Kim, Chem. Eng. Technol., 2011, 34, 29–41 CrossRef CAS.
- F. Chen and R. A. Dixon, Nat. Biotechnol., 2007, 25, 759–761 CrossRef CAS PubMed.
- J.-K. Weng, X. Li, N. D. Bonawitz and C. Chapple, Curr. Opin. Biotechnol., 2008, 19, 166–172 CrossRef CAS PubMed.
-
N. Smolarski, High-value opportunities for lignin: unlocking its potential, Frost & Sullivan, 2012, vol. 1 Search PubMed.
- R. Behling, S. Valange and G. Chatel, Green Chem., 2016, 18, 1839–1854 RSC.
- V. E. Tarabanko and N. Tarabanko, Int. J. Mol.
Sci., 2017, 18, 2421 CrossRef PubMed.
- L. Dessbesell, M. Paleologou, M. Leitch, R. Pulkki and C. Xu, Renewable Sustainable Energy Rev., 2020, 109768 CrossRef CAS.
- L. P. Dansereau, M. El-Halwagi, B. Mansoornejad and P. Stuart, Comput. Chem. Eng., 2014, 63, 34–50 CrossRef CAS.
- L. Dessbesell, C. Xu, R. Pulkki, M. Leitch and N. Mahmood, Can. J. For. Res., 2016, 47, 277–288 CrossRef.
- J. F. Kim, G. Székely, I. B. Valtcheva and A. G. Livingston, Green Chem., 2014, 16, 133–145 RSC.
- P. Vandezande, L. E. M. Gevers and I. F. J. Vankelecom, Chem. Soc. Rev., 2008, 37, 365–405 RSC.
- R. A. Sheldon, ACS Sustainable Chem. Eng., 2018, 6, 32–48 CrossRef CAS.
- J. F. Jenck, F. Agterberg and M. J. Droescher, Green Chem., 2004, 6, 544–556 RSC.
Footnote |
† These authors contributed equally. |
|
This journal is © The Royal Society of Chemistry 2020 |
Click here to see how this site uses Cookies. View our privacy policy here.