DOI:
10.1039/C9TA00769E
(Paper)
J. Mater. Chem. A, 2019,
7, 10723-10728
Realizing facile regeneration of spent NaBH4 with Mg–Al alloy†
Received
21st January 2019
, Accepted 28th March 2019
First published on 28th March 2019
Abstract
The regeneration of sodium borohydride (NaBH4) is crucial to form a closed cycle after it either supplies hydrogen energy via a hydrolysis process or provides energy through electron transfer at the anode of direct borohydride fuel cells (DBFCs). In both of these cases, the spent fuels are NaB(OH)4 from NaBO2 aqueous solution. However, the current regeneration process from (NaB(OH)4)·xH2O to form NaBH4 by reduction reaction and calcination at high temperature with metal hydrides as reducing agents is very expensive. In this work, we developed a simple regeneration process via ball milling with Mg–Al alloys as the reducing agent for NaB(OH)4 under an argon atmosphere. Under optimized conditions, a high yield of about 72% of NaBH4 could be obtained. Mechanistic study showed that all the hydrogen atoms from NaB(OH)4 remain in NaBH4 and no additional hydrogen sources are needed for the reduction process. The inexpensive Mg–Al alloy works as a reducing agent transforming the H+ to H− in NaBH4. This approach demonstrates a ∼20-fold cost reduction compared with the method using metal hydrides. This opens the door to the commercial implementation of simple ball milling processes for the regeneration of spent NaBH4 from NaB(OH)4 with cheap reducing agents.
1. Introduction
Fuel cells provide a promising alternative technology for electrical power generation from renewable energy carriers, for instance, hydrogen energy.1 However, currently the fuel supply is still one of the biggest hindrances for worldwide application of mobile fuel cell technologies.2,3 Hydrogen supply via hydrolysis of sodium borohydride (NaBH4)4 or direct borohydride fuel cells (DBFCs) both have great potential as possible solutions.5 However, both of these technologies suffer from the high cost of NaBH4 as well as difficulties in the regeneration of the spent fuel.6,7 Therefore, a high-efficiency and low-cost approach for a simple regeneration process for spent NaBH4 is highly desirable. This could be the key step and enabling technology for further distribution of NaBH4-powered fuel cell applications.
The spent fuel from NaBH4 hydrolysis is confirmed by the following hydrolysis reaction:
| NaBH4 + (2 + x)H2O → NaBO2·xH2O + 4H2 + heat | (1) |
where
x is the hydration factor.
8 However, it should be noted that the spent fuel is normally hydrated sodium metaborate (NaBO
2) or its aqueous solution after the hydrolysis.
9 The actual formulae of NaBO
2·2H
2O and NaBO
2·4H
2O are NaB(OH)
4 and NaB(OH)
4·2H
2O, respectively, according to the chemical structures.
10 In DBFCs, NaBH
4 is oxidized at the anode according to the following reaction:
| BH4− + 8OH− → BO2− + 6H2O + 8e−, E0 = −1.24 V vs. SHE | (2) |
The spent fuel from the anode reaction is B(OH)4− and H2O, which are also generated as an aqueous solution of NaBO2.7,11 From the NaBO2 aqueous solution, NaB(OH)4·2H2O or NaB(OH)4 can be obtained via drying at temperatures of <54 °C or 54–110 °C, respectively, while dehydrated NaBO2 can be formed after treatment at temperatures >350 °C.12 Over the past few decades, a great deal of effort has been made toward dehydrated NaBO2 reduction. With a calcination treatment at 550 °C, MgH2 reduced the dehydrated NaBO2 to NaBH4 under hydrogen pressure.13 Ball milling with metal hydrides at near room temperature can also achieve the reduction under an argon atmosphere with a NaBH4 yield of over 70%.14–16 However, the synthesis of metal hydrides at high temperature could be one important factor in the energy consumption and cost. Without the use of metal hydrides, high-temperature annealing treatment under hydrogen pressure for Mg,13,17 Mg and Si13 or transition metals (Fe, Co or Ni)18,19 mixed with dehydrated NaBO2 is another reduction technique. However, this high-temperature dehydration of NaBO2 is also energy consuming and additional hydrogen supply is needed, which increases the costs of the regeneration process (hydrogen from renewable sources, like water splitting, or unsustainably from fossil fuels). Direct reduction of hydrated NaBO2 with Mg by annealing at 3 MPa hydrogen pressure may be an option, but the yield is only 12.3% of NaBH4.20 Therefore, an innovative low-cost and high-efficiency approach for NaBH4 regeneration is of great importance and is urgently required.
Herein, instead of only Mg, we introduce aluminum (Al) to the reduction process of hydrated NaBO2 because it can offer more electrons than Mg but with similar reducibility, which may further decrease the cost and increase the yield of the process. In addition, Mg and Al are relatively soft metals, making the ball milling process less efficient. Thus, magnesium aluminum alloy (Mg17Al12) was chosen as a reducing agent in this work. The alloy was used to react with hydrated NaBO2via ball milling under an argon atmosphere in order to regenerate NaBH4. During the ball milling process, oxide layers on the alloy will be destroyed and fresh surfaces will be produced continuously. This will increase the overall kinetics of the regeneration process.
In this process, the Mg17Al12 alloy offers a high NaBH4 yield and a low cost, while the hydrated NaBO2 provides a self-sufficient hydrogen source with no need for any additional hydrogen input. Furthermore, the unnecessity of drying at high temperature (>350 °C) may greatly reduce energy consumption during the regeneration process. Therefore, this approach for regeneration of NaBH4 may be a very promising solution for future energy supply technologies.
2. Experimental
2.1 Chemicals
Mg17Al12 was purchased from Aike Reagent (China), while NaB(OH)4 was obtained by drying (NaB(OH)4)·2H2O (>99%, Sigma-Aldrich) for 12 h. Ethylenediamine (≥99%) was purchased from Sigma-Aldrich. The chemicals for quantification, potassium iodate (KIO3, AR grade), H2SO4 (98%), NaOH (≥99%), starch indicator (≥99%), and sodium thiosulfate solution (Na2S2O3, 1 M, AR grade) were purchased from Aladdin, and potassium iodide (KI, ≥99%) was purchased from TCI. The Mg17Al12 and the generated NaB(OH)4 were stored and handled in an argon-filled glove box (Mikrouna, China). The oxygen and water concentrations in the glove box were always below 1 ppm.
2.2 NaBH4 regeneration
For a typical experiment, a total 1 g of Mg17Al12 and NaB(OH)4 with different mole ratios and 50 g of steel balls (ball to powder ratio of 50
:
1, 4 steel balls of 10 mm and 68 steel balls of 6 mm) were mixed and loaded in the milling vial in the glove box. Then, the ball milling reactions were carried out in a shaker mill (QM-3C, Nanjing, China) at 1200 cycles per min (cpm).
2.3 Purification and quantification
20 mL of ethylenediamine was used to extract NaBH4 from the ball milled products. The turbid solution was then filtered via a polytetrafluoroethylene filter. The clear NaBH4 solution was dried using a freeze dryer (Martin Christ, Alpha 1-2LD Plus, Germany) to obtain NaBH4 as a white powder and the waste solvent (ethylenediamine) was collected in the cold trap. The purified NaBH4 was quantified by the iodate method.21 The yield of NaBH4 was calculated according to the following equation: |  | (3) |
2.4 Hydrolysis process
The hydrolysis test was conducted using the hydrolysis apparatus introduced here.22 In each hydrolysis experiment, 0.1 g of NaBH4 was used to react with 0.225 mL of a 5 wt% aqueous solution of CoCl2 at room temperature and the hydrogen generation curves were automatically collected.
2.5 Characterization
The phase composition was measured by X-ray diffractometer (XRD, Rigaku MiniFlex 600) with Cu Kα radiation (λ = 1.5406 Å) at 45 kV and 40 mA. Because both the raw materials and milling products are air sensitive, liquid paraffin was used to protect the XRD samples from the air. The chemical bonds of the products were measured by Fourier-transform infrared spectroscopy (FTIR, IS50, Nicolet) in transmission mode. Potassium bromide (KBr) pellets for FTIR measurements were prepared in the glove box with a sample to KBr ratio of 1
:
99. The ball milling products were also characterized by solid-state 11B magic-angle spinning nuclear magnetic resonance (MAS NMR) spectroscopy (AVANCE III HD 400, Bruker). Scanning electron microscopy (SEM; Supra-40, Zeiss) was used to characterize the morphology of the NaBH4.
3. Results and discussion
3.1 NaBH4 synthesis
For the NaBH4 regeneration, a mixture of Mg17Al12 alloy and NaB(OH)4 in a molar ratio of 4
:
35 was mechanochemically treated with a ball to powder ratio of 50
:
1 at 1200 cpm under an argon atmosphere. The XRD curves of the raw materials are shown in Fig. S1.†Fig. 1a shows the XRD curves of the generated NaBH4 after milling depending on the milling time. It can be seen that the raw materials (Mg17Al12 and (NaB(OH)4)) lose their intensity gradually with increasing milling time. The (200) diffraction peak of NaBH4 at around 28.9° in the XRD pattern confirms the generation of NaBH4 after 2 hours of milling. With the further increase of the milling time, the diffraction peak of NaBH4 becomes stronger after 5 h of milling but the intensity decrease after 10 h of milling, which may result from the combination effect of amorphization and NaBH4 generation during ball milling. After 20 h of milling, the (111) and (220) diffraction peaks of NaBH4 appear at around 25.1° and 41.4° with the sharper (200) diffraction peak at 28.9° because of the crystallization.23
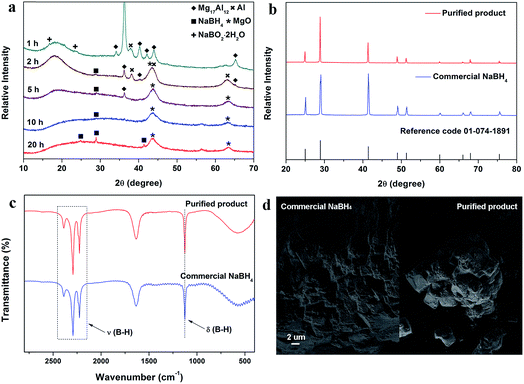 |
| Fig. 1 (a) XRD patterns of the 5, 7.5, 10 and 20 h ball milled products of Mg17Al12 and NaB(OH)4 mixtures (in a 4 : 35 molar ratio). (b) XRD patterns of the purified product (red line) and commercial NaBH4 (blue line). (c) FTIR spectra of the purified product (red line) and the commercial NaBH4 (blue line). (d) SEM images of the commercial NaBH4 (left) and the purified product (right). | |
To remove the byproducts from the powder after 5 h of milling and obtain high-purity NaBH4, the ball milling products were further purified. Fig. 1b presents the XRD curved for the purified NaBH4 product and the commercial material. As compared to the curve from commercial NaBH4, the similar diffraction pattern of the purified NaBH4 and the sharp (111), (200), (220), (311), (222), (400), (331) and (420) diffraction peaks14,15 indicate the successful generation of high-purity NaBH4 phase. No other reflections can be detected from the XRD pattern. From the FTIR spectra of these two samples shown in Fig. 1c, the bonds of the purified NaBH4 were further analyzed. The stretching (2200–2400 cm−1) and bending (1125 cm−1) vibrations of B–H appear in the spectrum of the purified NaBH4,14,16 which are similar to the vibrations of commercial NaBH4. Therefore, we may conclude that the regenerated NaBH4 with a similar crystal structure and bonding features to the commercial NaBH4 was regenerated by the reaction between Mg17Al12 and NaB(OH)4via ball milling. This method not only avoids the high-temperature process at 350 °C for NaB(OH)4 reduction, but also realizes the complete H supply for the regenerated NaBH4 from the [OH]− group of NaB(OH)4. Fig. 1d shows the SEM images of the purified and the commercial NaBH4. The grain-like surface structure of the purified NaBH4 is quite similar to that of the commercial NaBH4, which indicates that the regenerated NaBH4 has a similar surface morphology to that of the commercial NaBH4.
3.2 Yield
Fig. 2a presents the yields of high-purity NaBH4 prepared from the raw materials Mg17Al12 and NaB(OH)4 in molar ratios of 4
:
35 and 4
:
17 depending on the milling time. Quantification of the pure NaBH4 was done with the iodate method. For the 4
:
35 ratio, the NaBH4 yield after 5 h of milling was 20% and the yields increased with the milling time. After 20 h of milling, the yield reached 37%. As known from previous studies, the relation of NaB(OH)4 to the reduction compound has an important influence on the NaBH4 yield.24–26 It was further optimized by varying the molar ratio of Mg17Al12 and NaB(OH)4 (raw materials ratio). Fig. 2b shows the NaBH4 yields depending for the raw materials ratio range from 4
:
35 to 4.5
:
17 after 10 and 20 h of ball milling. For both of the milling durations, the NaBH4 yield first increases then decreases with increasing raw materials ratio. However, the highest yield after 10 h of ball milling was 54% with the raw materials ratio of 3.5
:
17, while for 20 h of milling the yield was 72% when the raw materials ratio was 4
:
17. It should be noted that the highest NaBH4 yield in this work of 72% is higher than the yield of the Mg and NaB(OH)4 system in our previous study27 and also approaches the yields from other reports of NaBH4 regeneration via MgH2 and NaBO2.14–16 The yields for the shorter milling times of the products with a raw materials ratio of 4
:
17 are presented in Fig. 2a. The yields for 5 h (5%) and 7.5 h (9%) milling times are lower than that with the 4
:
35 raw materials molar ratio, and the diffraction peaks of NaBH4 cannot be found in the XRD results (Fig. S2†). Diffraction peaks for NaBH4 appear in the pattern of the product after 5 h of ball milling, while the peak for NaBH4 appears in the pattern of the product with the 4
:
35 raw materials ratio only after 2 h of ball milling (Fig. 1a). Strong crystallization of NaBH4 happens when the ball milling time is increased to 20 h. The diffraction peaks for NaBH4 in the product with the raw materials ratio of 4
:
17 are much sharper (Fig. S2†).
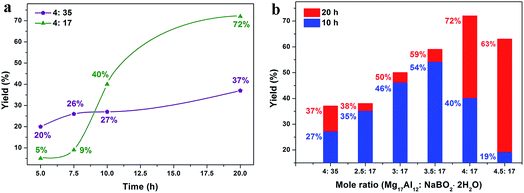 |
| Fig. 2 (a) Yields of the ball milled products of Mg17Al12 and NaB(OH)4 mixtures (in 4 : 35 and 4 : 17 molar ratios) for different milling times. (b) Yields of the 10 and 20 h ball milled products of Mg17Al12 and NaB(OH)4 mixtures with different mole ratios. | |
3.3 Reaction mechanism
To clarify the reaction mechanism between Mg17Al12 alloy and NaB(OH)4, the products obtained with different milling times were also investigated and characterized by FTIR, as shown in Fig. 3a. According to the XRD patterns in Fig. 1a, the (111) diffraction peak of Al at 38.4° and the (200) diffraction peak of MgO at 42.9° imply the generation of Al and MgO after 1 and 2 h of milling. After 1 h of milling, the formation of NaBH4 could be verified by the appearance of B–H vibrations in the FTIR spectrum in Fig. 3a and the [BH4]− resonance from Fig. 3b. According to the NMR spectra (Fig. 3b), [B(OH)4]− is gradually reduced to [BH4]− in this process. Therefore, the first step of the regeneration process can be described by the following reaction: | Mg17Al12 + NaB(OH)4 → MgO + Al + NaBH4 | (4) |
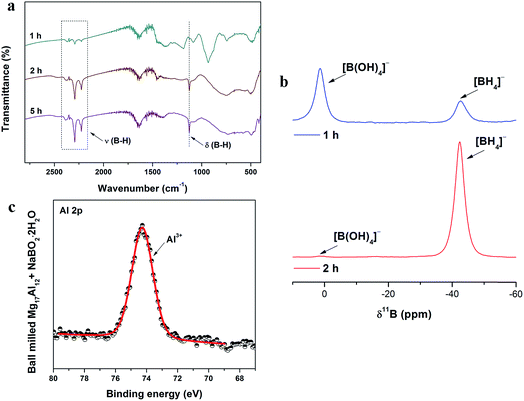 |
| Fig. 3 (a) FTIR spectra of the 1, 2 and 5 h ball milled products of Mg17Al12 and NaB(OH)4 mixtures (in a molar ratio of 4 : 35). (b) 11B NMR spectra of the 1 and 2 h ball milled products of Mg17Al12 and NaB(OH)4 mixtures (in a 4 : 35 molar ratio). (c) XPS spectra of Al 2p of the 1 h ball milled products of Mg17Al12 and NaB(OH)4 mixtures (in a 4 : 35 molar ratio). | |
The diffraction peaks of Al then disappear after 5 h of milling, which indicates that Al may become amorphous or work as a reducing agent and react with NaB(OH)4 during the ball milling. Because Al was generated after 1 h of milling and could react with NaB(OH)4, to further confirm the reaction, the product was characterized by XPS and the results are shown in Fig. 3c, which may provide more evidence. The only peak that appears at 74.30 eV in the spectrum is indexed to Al3+, while the peak belonging to Al0 in Mg17Al12 can be found in the spectrum for Mg17Al12 (Fig. S3†) milled with the same parameters. This evidence indicates that Al reacts with NaB(OH)4 in this reaction. To further unveil the reaction mechanism, pure Al-metal and NaB(OH)4 in a molar ratio of 24
:
9 were ball milled for 5 h with the same other milling parameters. Only diffraction peaks from Al-metal were found in the XRD pattern (Fig. S4a†) while on the other hand B–H vibrations appeared in the FTIR spectrum (Fig. S4b†). This demonstrates that even Al-metal can react with NaB(OH)4 producing NaBH4. Considering that Mg transfers to MgO in this system, it can be assumed that the byproduct is Al2O3 but not Al(OH)3, which may be amorphous so that its diffraction peaks cannot be observed in the XRD patterns. Therefore, the reaction of the second step is described as:
| Al + NaB(OH)4 → Al2O3 + NaBH4 | (5) |
Fig. 3b shows the solid-state 11B MAS NMR spectra of boron compounds produced during ball milling with different milling times. When the milling time changes from 1 to 2 h, the intensity of the [B(OH)4]− resonance decreases sharply, while the intensity of the [BH4]− resonance increases, indicating the conversion from [B(OH)4]− to [BH4]−. Owing to the self-supplied H from the [OH]− group in the raw material of NaB(OH)4, and the avoidance of high-temperature dehydration in this system, the cost of the regenerated NaBH4 is significantly reduced, benefitting from the use of the Mg17Al12 alloy. From calculations for the price of the raw materials, the expected cost of this process is ∼20 fold lower than the method using MgH2 and dehydrated NaBO2 as raw materials (Table S1†). An approximately 25% reduction in the cost of the raw materials is also achieved compared with the commercial method.
3.4 Hydrolysis
The generation of hydrogen from NaBH4via hydrolysis was also examined to confirm its properties. Here, a low-cost and effective non-noble metal catalyst, cobalt chloride (CoCl2),28 was used in the hydrolysis process. According to the hydrogen generation curves in Fig. 4a, the regenerated NaBH4 shows fast hydrogen generation kinetics, although with a little lower final hydrogen generation content than that of the commercial NaBH4. Nevertheless, around 2215 mL g−1 hydrogen can be generated within 10 min, with a conversion rate of about 86%. After the hydrolysis, the byproduct was collected and placed in ambient condition for 48 h before XRD measurement. In the XRD pattern (Fig. 4b), the low intensity diffraction peaks located at 22.0°, 25.2° and 33.2° are indexed to the (101), (111) and (211) of Na2ClB(OH)4, while other peaks are similar to those of NaB(OH)4. We can conclude here that the NaB(OH)4 is the main phase of the byproduct, which can be regenerated by the above method.
 |
| Fig. 4 (a) Hydrolysis curves of the purified product (red line) and commercial NaBH4 (blue line). (b) XRD pattern of the hydrolysis byproduct of the purified product. | |
4. Conclusion
In summary, NaB(OH)4 can be successfully reduced with Mg17Al12 alloy via ball milling to realize a very easy regeneration process for spent NaBH4. Using the inexpensive Mg17Al12 alloy, a H−-anion in the regenerated NaBH4 is directly transferred from the [OH]− group to H−. The yield in NaBH4 reaches 72%, which results from the reducibility of Mg and also Al-metal. During the reduction process, firstly the Mg17Al12 alloy reacts with NaB(OH)4 and generates NaBH4, MgO and Al-metal. Afterwards, the Al-metal reacts with residual NaB(OH)4 and produces NaBH4 and Al2O3. Since both metals of the cheap Mg17Al12 alloy can act as reducing agents, the commercial cost of this regeneration method is further reduced by a factor of ∼20 compared to regeneration methods using metal hydrides as the reducing agent. This new method holds promise for use as a commercial regeneration process and could open the door for broad applications of energy supply from NaBH4.
Conflicts of interest
There are no conflicts to declare.
Acknowledgements
This work was supported by the Foundation for Innovative Research Groups of the National Natural Science Foundation of China (No. NSFC51621001) and National Natural Science Foundation of China Projects (No. 51431001 and 51771075). Author Ouyang also thanks Guangdong Province Universities and Colleges Pearl River Scholar Funded Scheme (2014). Shao acknowledges Macao Science and Technology Development Fund (FDCT) for project 118/2016/A3.
References
- U. Eberle, B. Muller and R. von Helmolt, Energy Environ. Sci., 2012, 5, 8780–8798 RSC.
- S. Guo, J. Sun, Z. Zhang, A. Sheng, M. Gao, Z. Wang, B. Zhao and W. Ding, J. Mater. Chem. A, 2017, 5, 15879–15890 RSC.
- S. Park, J. M. Vohs and R. J. Gorte, Nature, 2000, 404, 265 CrossRef CAS PubMed.
- D. M. F. Santos and C. A. C. Sequeira, Renewable Sustainable Energy Rev., 2011, 15, 3980–4001 CrossRef CAS.
- G. Rostamikia and M. J. Janik, Energy Environ. Sci., 2010, 3, 1262–1274 RSC.
- U. B. Demirci, O. Akdim and P. Miele, Int. J. Hydrogen Energy, 2009, 34, 2638–2645 CrossRef CAS.
- I. Merino-Jiménez, C. Ponce de León, A. A. Shah and F. C. Walsh, J. Power Sources, 2012, 219, 339–357 CrossRef.
- A. Marchionni, M. Bevilacqua, J. Filippi, M. G. Folliero, M. Innocenti, A. Lavacchi, H. A. Miller, M. V. Pagliaro and F. Vizza, J. Power Sources, 2015, 299, 391–397 CrossRef CAS.
- M. A. Budroni, S. Garroni, G. Mulas and M. Rustici, J. Phys. Chem. C, 2017, 121, 4891–4898 CrossRef CAS.
- L. J. Csetenyi, F. P. Glasser and R. A. Howie, Acta Crystallogr., Sect. C: Cryst. Struct. Commun., 1993, 49, 1039–1041 CrossRef.
- Z. P. Li, B. H. Liu, K. Arai and S. Suda, J. Alloys Compd., 2005, 404–406, 648–652 CrossRef CAS.
- A. M. Beaird, P. Li, H. S. Marsh, W. A. Al-Saidi, J. K. Johnson, M. A. Matthews and C. T. Williams, Ind. Eng. Chem. Res., 2011, 50, 7746–7752 CrossRef CAS.
- Y. Kojima and T. Haga, Int. J. Hydrogen Energy, 2003, 28, 989–993 CrossRef CAS.
- C.-L. Hsueh, C.-H. Liu, B.-H. Chen, C.-Y. Chen, Y.-C. Kuo, K.-J. Hwang and J.-R. Ku, Int. J. Hydrogen Energy, 2009, 34, 1717–1725 CrossRef CAS.
- L. Kong, X. Cui, H. Jin, J. Wu, H. Du and T. Xiong, Energy Fuels, 2009, 23, 5049–5054 CrossRef CAS.
- Ç. Çakanyıldırım and M. Gürü, Renewable Energy, 2010, 35, 1895–1899 CrossRef.
- Z. P. Li, B. H. Liu, J. K. Zhu, N. Morigasaki and S. Suda, J. Alloys Compd., 2007, 437, 311–316 CrossRef CAS.
- B. Liu, Int. J. Hydrogen Energy, 2008, 33, 1323–1328 CrossRef CAS.
- B. H. Liu, Z. P. Li and S. Suda, J. Alloys Compd., 2009, 474, 321–325 CrossRef CAS.
- B. H. Liu, Z. P. Li and J. K. Zhu, J. Alloys Compd., 2009, 476, L16–L20 CrossRef CAS.
- D. A. Lyttle, E. H. Jensen and W. A. Struck, Anal. Chem., 1952, 24, 1843–1844 CrossRef CAS.
- L. Ouyang, M. Ma, M. Huang, R. Duan, H. Wang, L. Sun and M. Zhu, Energies, 2015, 8, 4237 CrossRef CAS.
- C. Suryanarayana, Prog. Mater. Sci., 2001, 46, 1–184 CrossRef CAS.
- H. Zhong, L. Z. Ouyang, J. S. Ye, J. W. Liu, H. Wang, X. D. Yao and M. Zhu, Energy Storage Mater., 2017, 7, 222–228 CrossRef.
- W. Chen, L. Z. Ouyang, J. W. Liu, X. D. Yao, H. Wang, Z. W. Liu and M. Zhu, J. Power Sources, 2017, 359, 400–407 CrossRef CAS.
- H. Zhong, L. Ouyang, J. Liu, C. Peng, X. Zhu, W. Zhu, F. Fang and M. Zhu, J. Power Sources, 2018, 390, 71–77 CrossRef CAS.
- L. Ouyang, W. Chen, J. Liu, M. Felderhoff, H. Wang and M. Zhu, Adv. Energy Mater., 2017, 1700299 CrossRef.
- H.-B. Dai, G.-L. Ma, X.-D. Kang and P. Wang, Catal. Today, 2011, 170, 50–55 CrossRef CAS.
Footnote |
† Electronic supplementary information (ESI) available: XRD analysis of the raw materials; XRD analysis of the ball milled products; XPS analysis of the ball milled raw material; cost calculation of raw materials for NaBH4 produced by different approaches. See DOI: 10.1039/c9ta00769e |
|
This journal is © The Royal Society of Chemistry 2019 |
Click here to see how this site uses Cookies. View our privacy policy here.