DOI:
10.1039/C9RA07939D
(Paper)
RSC Adv., 2019,
9, 33997-34003
Boosting the hydrogen evolution activity of a Co–N–C electrocatalyst by codoping with Al†
Received
30th September 2019
, Accepted 16th October 2019
First published on 23rd October 2019
Abstract
Co, Al and N tri-doped graphene (CANG) was successfully fabricated via annealing N-doped graphene with Co and Al precursors. The material was characterized by scaning electron microscopy (SEM), transmission electron microscopy (TEM), X-ray diffraction (XRD), Raman spectroscopy, physical adsorption, and X-ray photoelectron spectroscopy (XPS). It was found that the as-prepared CANG features a robust three-dimensional hierarchically porous structure. The contents of Co and Al can achieve the maximum value of 2.18 at% and 0.51 at% at the annealing temperature of 950 °C. Upon using the electrocatalyst for the hydrogen evolution reaction (HER), the CANG exhibited remarkable electrocatalytic performance in both acidic (η10 = 105 mV) and alkaline media (η10 = 270 mV), and outperforms Co,N-codoped graphene and Al,N-codoped graphene, respectively. In combination with the density functional theory (DFT) calculations, it was revealed that the introduction of the Al heteroatom can decrease the absolute value of hydrogen adsorption free energy (ΔG(H*)) of Co–N–C catalysts, thus greatly enhancing the HER activity. This discovery will provide new guidance to the design of advanced and inexpensive carbon materials for fuel cell, water-splitting and other electrochemical devices.
1. Introduction
The use of renewable energy such as wind and solar energy has become more and more attractive because of the ever-increasingly serious environmental pollution and the shortage of fossil fuel. Wind and solar energies can theoretically meet the major share of human demands, however, they are intrinsically intermittent.1,2 Hydrogen is an interesting energy carrier for the storage of wind and solar energies by electrolytic or photo water splitting. Among them, electrochemical water-splitting is a preferred method for fast and large-scale hydrogen-production.3–5 As a cathodic reaction in electrochemical water-splitting, the hydrogen evolution reaction (HER) is the pivotal process for electrolysers, and mostly depends on electrocatalysts to reduce hydrogen from water energy-efficiently and economically. Currently, Pt-based materials are the state-of-the-art electrocatalysts for HER, but the high price, scarcity and instability as well as poisoning challenges the feasibility of Pt for industrial application.6–8 Therefore, the development of active and inexpensive electrocatalysts for the HER is highly desirable. Up to now, several classes of catalysts derived from earth-abundant elements such as transition metal carbides,9,10 nitrides,11,12 phosphide,13,14 chalcogenides,15 and selenides16 have gained much attention, however, their inferior activity and corrosion in acid or alkaline media make them impractical for commercialization.
In recent years, carbon materials have been extensively studied as electrocatalysts, with their high electro-conductivity, low price, abundant supply, and good resistance to acid and alkaline.17 The pure carbon merely shows extremely weak electrocatalytic activity. Heteroatom-doping is generally an efficient way to promote the electrocatalytic performance of carbon.18,19 Particularly, transitional (i.e., Fe, Co, Ni, Mo, Cu, etc.) and nitrogen codoped carbon (Me–N–C) materials have shown their promising future in energy-related reactions such as oxygen reduction reaction (ORR),20,21 oxygen evolution reaction (OER),22 and HER.23,24 The carbon matrix can facilitate the transportation of electrons, while the nitrogen dopant can induce structural defects that strengthen the interaction with metal atoms to activate reactants. Among them, Co- and N- codoped carbon materials (i.e., graphene, carbon nanotube, and active carbon) have shown their great potentials in electrocatalyzing HER.25,26 It has been known that CoCxNy moiety is the active site and plays critical role in catalysing HER.27 Albeit great progress has been achieved on Co–N–C catalysts in recent years, they still suffer from the ordinary HER activity. Certainly, the HER activity of Co–N–C catalysts can be improved by loading active nano-catalysts (i.e., Co–CoO,28 Co3C,29 Ni2P30) on them, but the improvement by this way is usually quite limited. Very recently, it was discovered that doping a tertiary heteroatom such as sulfur31 or phosphorous32 is a more effective strategy to promote the HER activity of Co–N–C catalysts, which offers the possibility of enhancing their HER performance by tuning the structure of active centre.
In our previous works, we have proposed an Al,N-codoped three-dimensional (3D) graphene (ANG)33 and a Co,N-codoped 3D graphene (CNG).34 Of the two materials, ANG expressed super electrocatalytic ORR performance, unfortunately, poor HER activity.33 In contrast, CNG showed the good HER activity, however, poor ORR performance.34 Here, we were inspired to fabricate Co, Al, and N tri-doped 3D graphene (CANG) to create a bi-functional electrocatalyst with balanced ORR and HER performance, unexpectedly, the CANG exhibited the remarkable HER performance superior to CNG and ANG in both acid and alkaline medium. In combination with density functional theory (DFT) calculation, it was confirmed that the introduction of Al heteroatom can greatly improve the intrinsic HER activity of Co–N–C catalyst.
2. Experimental
2.1 Chemical reagents
Natural graphite powder (325 meshes) was purchased from Qingdao Graphite Co., Ltd. (Qingdao, China). Cobalt nitrate was purchased from Shanghai Qiangshun Chemical Reagent Co., Ltd. Aluminum iso-propoxide was purchased from Shanghai Runjie Chemical Reagent Co., Ltd. Formaldehyde aqueous solution (35 wt%), melamine, vitriol, phosphoric acid, and potassium permanganate were obtained from Aladdin Chemical Reagent Co., Ltd. (Shanghai, China). All other reagents not mentioned were of analytical grade and used as received.
2.2 Fabrication materials
2.2.1 Preparation of NG. Firstly, graphite flakes (1.0 g) and KMnO4 (6.0 g) were added into a mixture of 120 mL concentrated H2SO4 and 13.3 mL H3PO4, producing a slight exotherm to 35 °C. The mixture was then heated at 50 °C for 12 h. The mixture was cooled to room temperature and poured into ice water (150 mL) with 30% H2O2 (10 mL), and then sifted through a polyester fibre. The filtrate was centrifuged (4000 rpm for 4 h), and the supernatant was decanted away. The remained solid was then washed in succession with 200 mL of water, 200 mL of 30% HCl, and 200 mL of ethanol. The solid was vacuum-dried overnight at room temperature, resulting 1.8 g GO. Secondly, 150 mg GO was dispersed in 15 mL water to produce a concentrated GO suspension, which was then mixed with 1 mL formaldehyde solution (37 wt%) and 0.35 g melamine. The dispersion was transferred into an autoclave and hydrothermally treated at 180 °C for 12 h. The obtained composite hydrogel was dried at 80 °C for 24 h in an oven. The dry aerogel was subsequently calcined at 750 °C for 5 h in N2 atmosphere, resulting in the eventual NG product.
2.2.2 Preparation of CANG, ANG and CNG. For the preparation of CANG, 0.04 g of NG, 0.04 g of Co(NO3)2 and 0.04 g of aluminium isopropanol were dispersed in mixed solution of 10 mL H2SO4 and 10 mL H2O. Then magnetic stirred the mixture for three hours. The obtained composite hydrogel was dried at 80 °C for 24 h in an oven. The dry aerogel was subsequently annealed at 950 °C for 3 h in Ar atmosphere, and leached by acid (1 M H2SO4, 80 °C) and alkali (1 M KOH, 80 °C) until it lost magnetism completely. The final product was denoted as CANG. For the preparation of CNG and ANG, the fabricating process is same as that of CANG, except that the precursors what they used is Co(NO3)2 or aluminium isopropanol, respectively.
2.2.3 Electrochemical measurements. The electrochemical measurements were conducted on an electrochemical cell with conventional three-electrode system. The commercial glass carbon electrode (GCE) with the diameter of 5 mm was used as the working electrode. The current densities were normalized by the geometric surface area of the GCE. The graphite rod electrode and the saturated calomel electrode (SCE) served as the counter electrode and the reference electrode, respectively. The working electrodes were fabricated by the following procedure: the suspensions (catalysts in water, 2.0 mg mL−1, 10 μL) of the as-prepared materials were drop coated onto a glassy carbon disk with the diameter of 3 mm (mass loading ∼0.28 mg cm−2) and dried at room temperature in air for 6 h. Then 5 μL Nafion solution (0.02 wt%) were cast on the electrode surface to adhere the materials on electrodes. The potential versus saturated calomel electrode were converted into the potential versus reversible hydrogen electrode (RHE) according Evs. RHE = Evs. SCE + EθSCE + 0.059 pH.The calibration test was conducted in a 0.25 M H2SO4 solution containing 10 mM CuSO4 with saturated N2 during the whole test. The electrode was first cycled between 0.23 and 0.7 V in 0.25 M H2SO4 with scan speed of 10 mV s−1 for many scans as the background. Then the solution was changed into 0.25 M H2SO4 and 10 mM CuSO4 with scan speed of 10 mV s−1. And the electrochemical active area (ECSA) was calculated after 20 times CV scan using the following formula:
|
 | (1) |
The Mmetal is the loading of Co on the working electrode, and QCu is the average charge calculated from area under the voltragram of the Cu-upd CV curve.
Afterwards, the HER turnover frequency (TOF) is defined as:
|
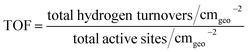 | (2) |
The upper hydrogen turnovers per geometric electrode area can be calculated by the hydrogen evolution current density under a constant overpotential:
|
 | (3) |
The total active sites per geometric electrode area can be calculated through the pre-calculated ECSA above.
Electrocatalytic performance measurements were conducted in a three-electrode cell using an Ag/AgCl electrode (calibrated and converted to a reverse hydrogen electrode, RHE) as the reference electrode, graphite rod electrode as the counter electrode, and the sample modified glassy carbon electrode as the working electrode.
The chronopotentiometry (i–t) and cycled LSV were tested in the 0.5 M H2SO4 solution saturated with N2. The constant potential technique used for i–t test, the potential with a current density of 10 mA cm−2 was selected, and the speed was set to 1600 rpm min−1. The test time was 20
000 seconds. For the cycle stability, the test was the LSV curve experienced 20
000 cycles.
For the cyclic voltammetry (CV) test, an O2 flow was maintained over the electrolyte during the recording of CVs. Before data were recorded, the working electrode was cycled at least 5 times at a scan rate of 10 mV s−1. For comparison, CV measurements were also carried out in N2-saturated KOH solution. For RDE measurement, the working electrode was scanned at a rate of 10 mV s−1 with various rotating speed from 400 to 2400 rpm.
SCN− tests were conducted in the solution of 0.5 M H2SO4 containing 10 mmol KSCN.
3. Results and discussion
3.1 The fabrication and characterization of CANG
As illustrated in Fig. 1, the CANG was prepared by a heat-treating process of 3D N-doped graphene (NG) with Al and Co precursors. The NG was firstly prepared through the method reported by us previously.35 It had been proved that the NG possesses robust 3D structure and abundant nitrogen heteroatom (∼8 at%) as well as hierarchical pore. Al and Co was secondly doped into graphene by a post heat-treatment of isopropyl aluminium and cobalt nitrate with NG.
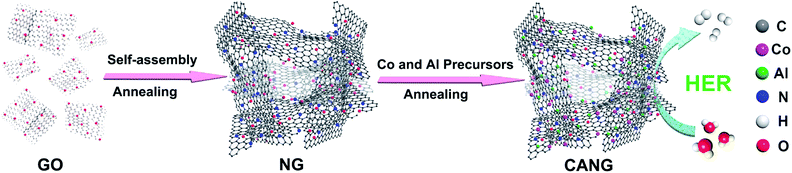 |
| Fig. 1 Schematic illustration of the fabricating process of CANG. | |
The morphologies of CANG were firstly characterized with scan electron microscope (SEM) and transmission electron microscope (TEM), as shown in Fig. 2. SEM images clearly show the well-defined 3D interconnected network constructed by the partially overlapping graphene sheets, and continuous macroporous architecture with the pore size ranged from sub-micrometer to several micrometers (Fig. 2a and b), which is identical to our previously reported CNG and ANG.33,34 TEM images further validated the 3D structure connected by graphene units (Fig. 2c). The wall of the CANG is thin and transparent, which consists of only few layers of graphene sheets (Fig. 2d). Both TEM and SEM images display the very clean surface almost free of any particles, suggesting that the residues of Al and Co precursors were removed entirely. The high angle annular dark field (HAADF)-scanning transmission electron microscopy (STEM) image reconfirms the 3D foam-like and porous structure (Fig. 2e). Both the elemental mapping analysis of CANG by STEM (Fig. 2f) and energy dispersive X-ray spectroscopy (EDX) (Fig. S1, ESI†) elucidates the presence of C, N, Co, and Al element. Moreover, the distribution of Al and Co is as homogeneous as those of C and N, implying that Al and Co have been successfully doped into the carbon matrix of graphene.
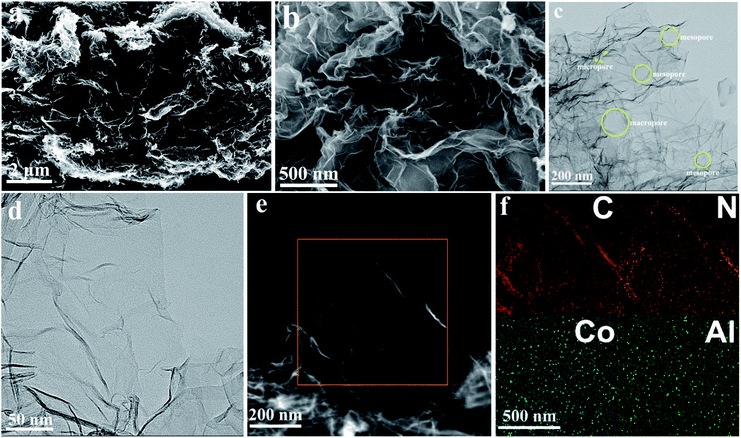 |
| Fig. 2 The SEM (a and b), TEM (c and d), HAADF-STEM images (e), and the corresponding elemental mapping (f) of CANG. | |
The structure and composition of the CANG were further examined by X-ray diffraction (XRD), Raman spectroscopy, physical adsorption, and X-ray photoelectron spectroscopy (XPS), moreover, compared with those of CNG and ANG. As seen from Fig. 3a, their XRD patterns exhibit the two identical broad diffraction peaks of C (002) and C (100), respectively. The XRD pattern of CANG is free of Al- and Co-related crystalline diffraction peaks, further validating the clean surface of the graphene sheet. All of their Raman spectra exhibit the two peaks positioned at 1350 cm−1 and 1594 cm−1, which are assigned to the D and G band peaks of graphene,36 respectively (Fig. 3b). As is known, the G band results from the in-plane vibration of sp2-hybridized C, and the D band stems from the edge or the defect of graphene.37 The ratio of their intensity at the fitted D band to G band (ID/IG) (Fig. S2†) can reflect the structural integrity of graphene. As shown in Fig. 2b, CANG delivers the slightly higher ID/IG value (1.95) than those of CNG (1.9) and ANG (1.88), indicating that CANG features the slightly more defects than CNG and ANG, due most likely to the introduction of double metal heteroatoms. The nitrogen adsorption–desorption isotherm reveals that CANG has a BET surface area of 253 m2 g−1 (Fig. 3c), which is close to that of ANG (257 m2 g−1) and CNG (189 m2 g−1), respectively. The pore-size distribution curves indicate that they possess the basically identical pore structure (Fig. S3, ESI†), and the mesopore contributes most of the surface area. Their chemical compositions were further estimated by XPS, shown in Fig. S4a, ESI.† It can be found that CANG displays the Al and Co peaks besides C, N, and O, evidencing the successful doping of Al and Co. The amounts of Al and Co in CANG are 0.51 at% and 2.18 at%, respectively, very close to those in CNG and ANG.33,34 The Al 2p and Co 2p fine XPS of CANG showed the pronounced Al 2p3/2, Co 2p1/2, and Co 2p3/2 peaks (Fig. S4b and c, ESI†). Particularly, the high resolution N1s XPS of CANG can be deconvoluted into the clear Co–N and Al–N peaks besides the conventional pyridinic, pyrrolic and graphitic N (Fig. 3d), however, those of CNG and ANG merely show the individual Co–N peak and Al–N peak (Fig. S5, ESI†), implying the possible existence of Co–N–Al structure in CANG.
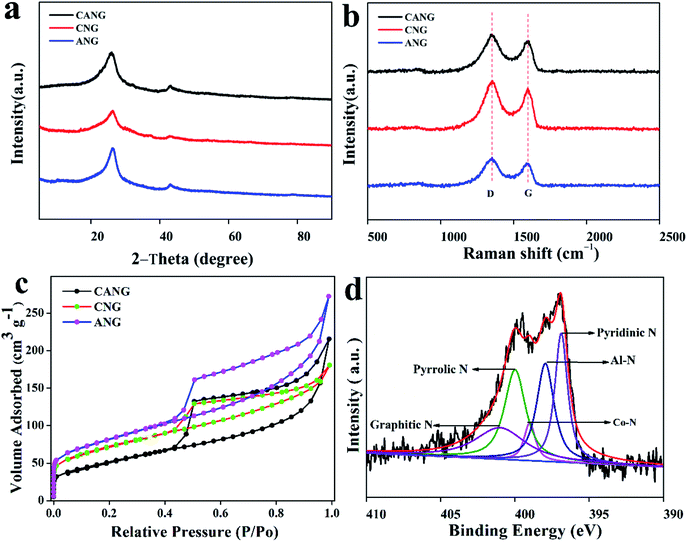 |
| Fig. 3 (a) XRD patterns, (b) Raman spectroscopy, (c) N2-adsorption isotherm of and N 1s XPS (d) characterization of CANG. | |
3.2 The electrocatalytic HER performance of CANG
The electrocatalytic performance of CANG for HER was firstly assessed in an acid media (0.5 M H2SO4) using a three-electrode electrochemical cell. The mass loading of catalysts on working electrode maintained at 0.28 mg cm−2 (geometrical area). The potentials against SCE were referenced to reversible hydrogen electrode (RHE). For comparison, the electrocatalytic HER performance of CNG and ANG were also measured, and benchmark to the commercial Pt/C catalyst (20 wt%). The HER activity of a catalyst is generally evaluated by the overpotential (η10) needed to achieve the current density of 10 mA cm−2 from the linear sweep voltammetry (LSV) curves. As seen from Fig. 4a, the η10 of CANG is only 105 mV, which is much smaller than those of CNG (173 mV) and ANG (362 mV), respectively. The Tafel plot is a powerful metric to assess the HER performance as well as an indicator of reaction pathway. The CANG gives the Tafel slope of 81.5 mV dec−1 (Fig. 4b), much smaller than those of CNG (100 mV dec−1) and ANG (181 mV dec−1) as well. The Tafel slope ranges between 40 and 120 mV dec−1, indicating that CANG catalyses the HER through the Volmer–Heyrovsky mechanism, which involves the fast release of a proton followed by a rate-limiting step of electrochemical recombination with an extra proton.27 The ECSA and TOF were further used to evaluate the intrinsic activity of the catalysts, as shown in Fig. S6, ESI.† CANG displays the ECSA of 48 m2 g−1 and the TOF of 0.3 s−1, which are several times to those of CNG (21 m2 g−1, 0.05 s−1) and ANG (10.7 m2 g−1, 0.02 s−1), respectively. The electrochemical impedance spectroscopy (EIS) discloses that CANG holds the lowest charge-transfer resistance (Fig. S7, ESI†). All the above electrochemical parameters demonstrated the same result that CANG bears significantly better HER activity than CNG and ANG in acid condition. Specially, to achieve the high current density of 100 mA cm−2, the overpotential (η100) needed by CANG (197 mV) is very close to that of Pt/C (153 mV). As is known that the half reaction (OER) on the counter electrode of HER is more efficient in alkaline condition.38–40 Therefore, the electrocatalytic HER activity of CANG in alkaline media (1 M KOH) was also considered (Fig. 4c and d). Similarly, CANG exhibits the smallest η10 (270 mV) and Tafel slope (120 mV dec−1) among the three catalysts, elucidating the best HER activity of CANG in alkaline condition as well. In both acidic and alkaline electrolyte, the HER activity of CNG is higher than that of ANG, which implies that Co heteroatom plays the more vital role than Al in electrocatalyzing HER, however, the introduction of Al can greatly boost the HER activity of CNG. Although slightly inferior to Pt/C, CANG still shows the better HER activity than most of the Co–N–C catalysts reported in literature (Tab. S1, ESI†). The electrochemical stability tests were evaluated by the LSV plot experienced 20
000 CV cycles and i–t curve (Fig. S8, ESI†). It can be seen that, CANG displays the excellent cyclic stability in both acidic (Fig. S8a and b†) and alkaline media (Fig. S8c and d†). Unfortunately, in neutral media (1 M phosphate buffer solution), CANG shows the same poor HER activity (Fig. S9, ESI†) as CNG and ANG. The ORR performance of CANG was considered as well (Fig. S10, ESI†). As compared with that of ANG, CANG bespeaks the degraded ORR activity, signifying that the introduction of Co can't improve the ORR activity of ANG.
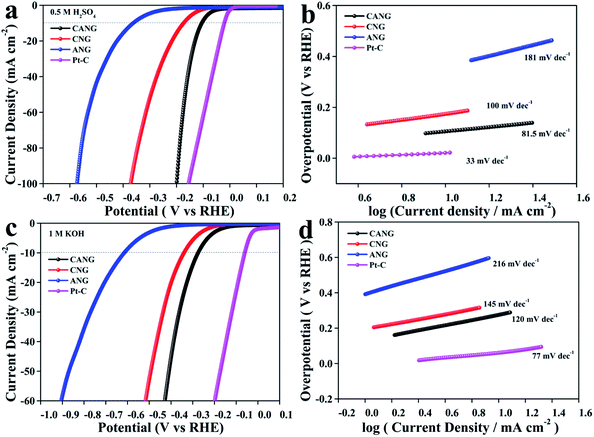 |
| Fig. 4 Electrocatalytic HER activity of CANG in acidic (a and b) and alkaline (c and d) electrolyte. (a and c) LSV curves, (b and d) Tafel plots. Catalysts loading: 0.28 mg cm−2, scan rate: 10 mV s−1. | |
To further understand the nature of active site of CANG, thiocyanate ions (SCN−) test was performed. SCN− is well known to poison the metal active centre in acidic condition.41 As shown in Fig. S11, ESI,† after introducing SCN− into the electrolyte, the η10 of CANG and CNG increases by 30 mV and 40 mV, respectively, however, that of ANG nearly keeps unchanged. This result evidences that the metal active centre in CANG is Co. In addition, the HER activity of CANG fabricated at various annealing temperatures were investigated (Fig. S12, ESI†). The contents of Co, Al and N in these CANG materials were determined by XPS (Tab. S2, ESI†). It was found that, the content of Co delivers the best relevance with their HER activities, further confirming the Co active centre in CANG. Admittedly, Al is not the active centre of CANG, however, it can greatly enhance the HER activity of Co active centre (Co–N–C). Based on these facts, it is inferred that the Co–N–Al structure is possibly the active centre of CANG.
3.3 The DFT calculation
DFT calculation was finally carried out to uncover the mechanism of Al-boosting the HER activity of CNG. The Co–N–C, Al–N–C and Co–N–Al structure were choose as the active centres of CNG, ANG and CANG, respectively. Their structural models can be found in Fig. S12, ESI.† The HER activity is evaluated by a three-state diagram involving H+ (initial state), H* (intermediate state), and ½H2 (final state). The Gibbs free energy of adsorption under room temperature and 1.23 V electric-potential was derived based on Norskov's scheme.42 Theoretically, an ideal HER electrocatalyst should feature a moderate free energy for H adsorption (ΔG(H*)) and desorption simultaneously.27 Their free energy diagrams were shown in Fig. 5. Clearly, ANG shows the highest positive |ΔG(H*)| (0.4 eV), representing the lowest HER activity, which results from the strong hydrogen adsorption on N atom. CNG displays the relatively low |ΔG(H*)| of 0.2 eV, due to the moderate hydrogen adsorption on Co atom. Interestingly, CANG manifests the lowest |ΔG(H*)| of 0.11 eV, which is very close to that of Pt (0.09 eV), hinting its remarkable potentials in electrocatalyzing HER. The introduction of Al enables the |ΔG(H*)| of Co–N–C to decrease from 0.2 eV to 0.11 eV, which may be the intrinsic reason of Al-boosting the HER activity of Co–N–C.
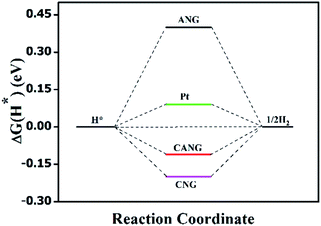 |
| Fig. 5 Free energy diagrams of HER for active centre of Pt, CNG, ANG, and CANG by DFT calculations. | |
4. Conclusions
In summary, we proposed for the first time a Co, Al, and N tridoped graphene with robust 3D hierarchically porous structure. As an electrocatalyst for HER, this material exhibited outstanding HER activity in both acidic (η10 = 105 mV) and alkaline (η10 = 270 mV) electrolyte. Very interestingly, it was found that the introduction of Al heteroatom can notably promote the HER performance of Co–N–C catalyst. The principle developed here, Al-boosting the HER activity of Co–N–C catalysts, will provide new guidance to design advanced carbon materials with inexpensive metals for fuel cell, water-splitting and other electrochemical devices.
Conflicts of interest
There are no conflicts to declare.
Acknowledgements
This work is financially supported by the Natural Science Foundation of Jiangsu Province, China (BK20161191), the Project of Jiangsu Key Laboratory of Advanced Catalytic Materials and Technology, the Advanced Catalysis and Green Manufacturing Collaborative Innovation Centre of Jiangsu Province, and Natural Science Foundation of China (21775013).
Notes and references
- I. Roger, M. A. Shipman and M. D. Symes, Nat. Rev. Chem., 2017, 1, 0003 CrossRef CAS.
- F. Díaz-González, A. Sumper, O. Gomis Bellmunt and R. Villafáfila Robles, Renewable Sustainable Energy Rev., 2012, 16, 2154 CrossRef.
- Y. J. Sa, S. Park, G. Y. Jung, T. J. Shin, H. Y. Jeong, S. K. Kwak and S. H. Joo, ACS Catal., 2019, 9, 83 CrossRef CAS.
- Y. Jiao, Y. Zheng, M. T. Jaroniec and S. Z. Qiao, Chem. Soc. Rev., 2015, 44, 2060 RSC.
- Y. Zheng, Y. Jiao, M. Jaroniec and S. Z. Qiao, Angew. Chem., 2015, 54, 52 CrossRef CAS.
- C. Tang, L. F. Gan, R. Zhang, W. B. Lu, X. E. Jiang, A. M. Asiri, X. P. Sun, J. Wang and L. Chen, Nano Lett., 2016, 16, 6617 CrossRef CAS.
- E. Skulason, G. S. Karlberg, J. Rossmeisl, T. Bligaard, J. Greeley, H. Jonsson and J. K. Norskov, Phys. Chem. Chem. Phys., 2007, 9, 3241 RSC.
- S. A. Grigoriev, P. Millet and V. N. Fateev, J. Power Sources, 2008, 177, 281 CrossRef CAS.
- Q. Gao, W. Zhang, Z. Shi, L. Yang and Y. Tang, Adv. Mater., 2018, 30, 1802880 Search PubMed.
- L. Pan, Y. Li, S. Yang, P. Liu, M. Yu and H. Yang, Chem. Commun., 2014, 50, 13135 RSC.
- Y. Zhu, G. Chen, Y. Zhong, W. Zhou and Z. Shao, Adv. Sci., 2017, 5, 1700603 CrossRef PubMed.
- W. Chen, J. T. Muckerman and E. Fujita, Chem. Commun., 2013, 49, 8896 RSC.
- P. Xiao, W. Chen and X. Wang, Adv. Energy Mater., 2015, 5, 1500985 CrossRef.
- Y. Li, F. Chu, Y. Bu, Y. Kong, Y. Tao, X. Zhou, H. Yu, J. Yu, L. Tang and Y. Qin, Chem. Commun., 2019, 55, 7828 RSC.
- Y. Guo, T. Park, J. W. Yi, J. Henzie, J. Kim, Z. Wang, B. Jiang, Y. Bando, Y. Sugahara, J. Tang and Y. Yamauchi, Adv. Mater., 2019, 31, 1807134 CrossRef.
- C. Xia, H. Liang, J. Zhu, U. Schwingenschlögl and H. N. Alshareef, Adv. Energy Mater., 2017, 7, 1602089 CrossRef.
- W. Cui, Q. Liu, N. Cheng, A. M. Asiri and X. Sun, Chem. Commun., 2014, 50, 9340 RSC.
- X. Wang, G. Sun, P. Routh, D. H. Kim, W. Huang and P. Chen, Chem. Soc. Rev., 2014, 43, 7067 RSC.
- H. Liu, Y. Liu and D. Zhu, J. Mater. Chem. A, 2011, 21, 3335 RSC.
- U. Martinez, S. K. Babu, E. F. Holby, H. T. Chung, X. Yin and P. Zelenay, Adv. Mater., 2019, 31, 1806545 CrossRef.
- M. Zhang, Q. Dai, H. Zheng, M. Chen and L. Dai, Adv. Mater., 2018, 30, 1705431 CrossRef.
- S. Chao and M. Gen, Int. J. Hydrogen Energy, 2016, 41, 12995 CrossRef CAS.
- A. Morozan, V. Goellner, Y. Nedellec, J. Hannauer and F. Jaouen, J. Electrochem. Soc., 2015, 162, H719 CrossRef CAS.
- L. Zhang, W. Liu, Y. Dou, Z. Du and M. Shao, J. Phys. Chem. C, 2016, 120, 29047 CrossRef CAS.
- C. Deng, K. H. Wu, J. Scott, S. Zhu, X. Zheng, R. Amal and D. W. Wang, ACS Appl. Mater. Interfaces, 2019, 11, 9925 CrossRef CAS.
- Z. Zhang, S. Yang, M. Dou, J. Ji and F. Wang, Int. J. Hydrogen Energy, 2017, 42, 4193 CrossRef CAS.
- Z. Wang, X. Hao, Z. Jiang, X. Sun, D. Xu, J. Wang, H. Xia, F. Meng and X. Zhang, J. Am. Chem. Soc., 2015, 137, 15070 CrossRef CAS PubMed.
- H. Jin, J. Wang, D. Su, Z. Wei, Z. Pang and Y. Wang, J. Am. Chem. Soc., 2015, 137, 2688 CrossRef CAS.
- X. Ma, X. He and T. Asefa, Electrochim. Acta, 2017, 257, 40 CrossRef CAS.
- T. Sun, J. Dong, Y. Huang, W. Ran, J. Chen and L. Xu, J. Mater. Chem. A, 2018, 6, 12751 RSC.
- S. Wang, Y. Qin, Y. Liu, F. Chu, Y. Kong and Y. Tao, J. Electrochem. Soc., 2017, 164, F1110 CrossRef CAS.
- S. Li, H. Li, S. Huang, Q. He and L. Hou, Energy Technol., 2019, 7, 1800757 CrossRef.
- Y. Qin, H. H. Wu, L. Zhang, X. Zhou, Y. Bu, W. Zhang, F. Chu, Y. Li, Y. Kong, Q. Zhang, D. Ding, Y. Tao, Y. Li, M. Liu and X. C. Zeng, ACS Catal., 2019, 9, 610 CrossRef CAS.
- S. Wang, L. Zhang, Y. Qin, D. Ding, Y. Bu, F. Chu, Y. Kong and M. Liu, J. Power Sources, 2017, 363, 260 CrossRef CAS.
- Y. Qin, J. Yuan, J. Li, D. Chen, Y. Kong, F. Chu, Y. Tao and M. Liu, Adv. Mater., 2015, 27, 5171 CrossRef CAS.
- S. Li, C. Cheng, H. W. Liang, X. Feng and A. Thomas, Adv. Mater., 2017, 29, 1700707 CrossRef.
- Z. Liu, K. Parvez, R. Li, R. Dong, X. Feng and K. Müllen, Adv. Mater., 2015, 27, 669 CrossRef CAS.
- J. Jin, X. Liu, Y. Jiao, A. Vasileff, Y. Zheng and S. Qiao, Nano Energy, 2018, 53, 690 CrossRef.
- Y. Luo, X. Li, X. Zou, F. Kang, H. M. Cheng and B. Liu, ACS Nano, 2018, 12, 4565 CrossRef CAS.
- D. Hou, S. Zhu, H. Tian, H. Wei, X. Feng and Y. Mai, ACS Appl. Mater. Interfaces, 2018, 10, 40800 CrossRef CAS.
- H. W. Liang, S. Brüller, R. Dong, J. Zhang, X. Feng and K. Müllen, Nat. Commun., 2015, 6, 7992 CrossRef CAS.
- J. K. Nørskov, T. Bligaard, A. Logadottir, J. R. Kitchin, J. G. Chen, S. Pandelov and U. Stimming, J. Electrochem. Soc., 2005, 152, J23 CrossRef.
Footnote |
† Electronic supplementary information (ESI) available: The Experimental section, the XPS survey and the ORR activity of CANG, the EIS and comparison of electrochemical performance of CANG with those Co–N–C catalysts reported in literature. See DOI: 10.1039/c9ra07939d |
|
This journal is © The Royal Society of Chemistry 2019 |
Click here to see how this site uses Cookies. View our privacy policy here.