DOI:
10.1039/C9RA07351E
(Paper)
RSC Adv., 2019,
9, 34581-34588
Hydrogenation of alkyl-anthraquinone over hydrophobically functionalized Pd/SBA-15 catalysts
Received
12th September 2019
, Accepted 17th October 2019
First published on 28th October 2019
Abstract
Organosilane-functionalized mesoporous silica SBA-15 was prepared by the co-condensation method and then applied as a support of Pd catalysts for hydrogenation of 2-alkyl-anthraquinone (AQ, alkyl = ethyl, tert-butyl and amyl). The as-prepared Pd catalysts were characterized by X-ray diffraction, Fourier transform infrared spectroscopy, thermogravimetric analysis, N2 adsorption–desorption, zeta potential, water contact angles measurement and transmission electron microscopy. By extending the pre-hydrolysis time of the silica source, the content of functional groups in the catalysts slightly increases. However, there is an initial increase in zeta potential and water contact angles up to a maximum at 2 h, followed by a decrease as the pre-hydrolysis time was further prolonged. The hydrophobicity created by organic functionalization has positive effects on AQ hydrogenation. The catalyst with the highest hydrophobicity exhibits the highest catalytic activity, with increments of 33.3%, 60.0% and 150.0% for hydrogenation of ethyl-, tert-butyl- and amyl-anthraquinone compared with the unfunctionalized one.
1 Introduction
Hydrogen peroxide (H2O2) is a green oxidant in line with ecological requirements and has been widely used in many domains.1–3 The worldwide consumption of hydrogen peroxide tends to raise yearly and annual production of hydrogen peroxide reached 6 million tons in 2016 (based on 100% H2O2).4,5 At present, the anthraquinone process is almost the only industrial production method of hydrogen peroxide.6 It involves four main processes: hydrogenation of a 2-alkyl-anthraquinone (AQ), such as 2-ethyl-anthraquinone (EAQ) and 2-amyl-anthraquinone (AAQ) in a nonpolar–polar mixed solvent (working solution), oxidation of produced 2-alkyl-anthrahydroquinone (AQH2), extraction of hydrogen peroxide with water from the working solution and regeneration of the working solution. There are two routes of side reactions in hydrogenation of AQ: hydrogenation of the aromatic ring and carbonyl hydrolysis of AQH2.7 Among the by-products formed via deep hydrogenation reactions, 2-alkyl-tetrahydro-anthraquinone is active and others are identified as degradation products because they cannot be further oxidized to produce H2O2.8
Supported Pd-based catalysts have been widely employed in hydrogenation of AQ.9,10 Surface area and pore size, acidity/basicity and hydrophilicity/hydrophobicity of support are demonstrated to be the crucial parameters affecting the catalytic performance. Tang et al. prepared an Al2O3 support by extrusion method with pseudoboehmite as precursor and found the Pd catalyst on it to be highly effective for EAQ hydrogenation due to the higher surface area and ordered pore structure.11 Chen et al. reported that large-diametered uniform mesopore of SBA-15 was conducive to the hydrogenation of EAQ.12 The similar result that catalytic activity of EAQ hydrogenation remarkably increased with expanding the pore size of Pd/SBA-15 was also observed by Yuan and Wang et al.13,14 Li et al. proposed that the large-pored catalyst was beneficial to the diffusion of both EAQ and EAQH2, restraining the occurrence of deep hydrogenation.15 Hong et al. drew the same conclusion by performing hydrogenation of EAQ over anodic alumina oxide supported Pd catalyst with different pore sizes.16
Kosydar et al.17 and Chen et al.18 reported that alkali-modification of Al2O3 support could resulted in significant suppression of deep hydrogenation reactions. Drelinkiewicz et al. proposed that the Pd catalyst on SiO2 support was more durable and could suppress the formation of degradation products compared with that on Al2O3.19 Feng et al. considered that acid sites in Al2O3–SiO2 support could facilitate the adsorption of EAQ molecules and thus improve the hydrogenation activity.20 Yuan et al. found the selectivity of EAQ hydrogenation over Pd/SBA-15 to be significantly promoted by incorporating Mg into SBA-15 and the rate of EAQ hydrogenation to be accelerated by incorporating Al into SBA-15.13 Li et al. observed the addition of MgO into Pd/SiO2/cordierite monolith catalyst to be favourable to the catalytic activity of EAQ hydrogenation and attributed it to the facilitated activation and adsorption of C
O group.21
Polymer supports are attended by researchers as well. Bombi et al. prepared resin supported Pd catalyst and achieved high activity but ordinary selectivity.22 Biffis et al. designed suitable tailor-made resin supported Pd catalyst and improved the selectivity to EAQH2 due to the lipophilic micro-environments around Pd particles.23 Drelinkiewicz et al. employed polyaniline (PANI) coated SiO2 as the support of Pd catalysts, and showed them to be high activity and selectivity for EAQ hydrogenation.24 In previous work, the Pd catalysts were prepared on SBA-15 post-grafted with alkyltriethoxysilane and evaluated using hydrogenation of EAQ. It was found that the catalytic activity increased with the content of carbon in the catalysts.25 But it is difficult to further increase grafting amount due to the limitation of silanol groups available.26
The co-condensation of silica source and organotrialkoxysilane is another common approach of organic functionalization of SBA-15, by which the higher functionalization degree can be achieved.27 3-Aminopropyl-triethoxysilane (APTES) is the most commonly used functional reagent. Chong et al. prepared APTES functionalized SBA-15 with ordered structure and uniform pore size distribution.26 Niu et al. found that 3-aminopropyl functionalized SBA-15 could control the delivery of baicalin more efficiently than pure SBA-15.28 Other organic functionalization agents are also used for the functionalization of SBA-15 by the co-condensation method. Barczak et al. reported the synthesis of functionalized SBA-15 by the condensation of 2-(2-pyridyl)ethyltrimethoxysilane (PETS) and tetraethyl orthosilicate (TEOS).29 Pt catalyst supported on 3-mercaptopropyletrimethoxysilane (MPTMS) functionalized SBA-15 was prepared by Khan et al. and applied to the decomposition of sulfuric acid in Sulfur–Iodine cycle.30 Zhu et al. used aldehyde functionalized SBA-15 as ammonia sensor, which exhibited excellent sensitivity, response speed and reversibility.31
In this work, hydrophobically functionalized SBA-15 was synthesized by the co-condensation method with propyl-triethoxysilane (PTES) as modification agent and supported Pd catalyst was prepared on the as-synthesized SBA-15. The influences of pre-hydrolysis time of silica source on the content and distribution of organosilane in the catalysts and thereby on physicochemical properties and catalytic performance of catalysts were investigated. The hydrogenation of AQ (2-alkyl-anthraquinone, alkyl = ethyl, tert-butyl and amyl) was selected for performance test of catalysts.
2 Experimental
2.1 Preparation
2.1.1 SBA-15 supports. Functionalized SBA-15 was synthesized by the co-condensation method. In a typical synthesis, 2 g triblock copolymer (Pluronic P123, Sigma-Aldrich, Mw = 5800) was dissolved in 75 mL HCl solution with a concentration of 1.6 mol L−1 and stirred at 40 °C for 1 h. Then, tetraethyl orthosilicate (TEOS, 98%, Tianjin Kermel Chemical Reagent Corporation, China) was dropped and stirred for a certain time (pre-hydrolysis time, t = 0.5, 1, 2 and 4 h). After that, propyl-triethoxysilane (PTES, AR, Aladdin Bio-Chem Technology Co., Ltd., Shanghai) was added and stirred at 40 °C for 24 h. The mixture thus obtained was transferred into a Teflon-lined stainless-steel autoclave and heated at 100 °C for 48 h. The solid product was obtained by filtration and then refluxed with ethanol (GR, Real Lead Chemical Co., Ltd., China) for 24 h to remove P123. Finally, the solid sample was recovered by filtration, washed with distilled water and dried at 110 °C overnight, yielding functionalized SBA-15.For comparison, a conventional SBA-15 was also synthesized using the same procedures and conditions as those mentioned-above, without the addition of PTES. And a calcination procedure at 550 °C for 6 h in air replaced the extraction with ethanol to remove P123.
2.1.2 Pd catalysts. Pd was loaded by the incipient wetness impregnation method with the Pd loading of 1 wt%. Pd(OAc)2 (≥99.0%, Macklin Biochemical Co., Ltd., Shanghai) was used as Pd source for the supports of functionalized SBA-15. 42 mg Pd(OAc)2 was dissolved in 4.6 mL acetone. Then the solution was added into 2.0 g dried PTES functionalized SBA-15. After impregnating for 2 h, the sample was dried at 110 °C for 12 h, calcined in the air at 300 °C for 4 h and reduced by H2 at 250 °C for 1 h. The resultant catalysts are denoted as Pd/P-X where X (0.5, 1, 2 and 4) means the pre-hydrolysis time of TEOS.For conventionally synthesized SBA-15 support, Pd(NO3)2·2H2O (≥99.0%, Macklin Biochemical Co., Ltd., Shanghai) was used as Pd source25 and the resulting catalyst is denoted as Pd/SN.
2.2 Characterization
Powder X-ray diffraction (XRD) patterns were recorded on a Philips X′Pert MPD diffractometer (Cu-Kα radiation). Fourier transform infrared (FTIR) spectra were obtained on a FTIR Bruker Equinox Vertex 70 spectrometer using a KBr wafer (60 mg with 1
:
50 in the mass ratio of sample to KBr and 0.63 cm in a diameter for each measured catalyst) in an in situ cell at a residual pressure of 10−4 mbar. Prior to measurement, the powder sample was dried in a vacuum drying oven at 50 °C for 12 h. Elemental analysis was performed on an Elementar Vario EL elemental analyzer with high sensitivity thermal conductivity detector (TCD) in the mode of CHN. Thermogravimetric analysis (TGA) was recorded on a TQ500 Thermal analyzer from TA instrument under air atmosphere from room temperature to 700 °C with the heating rate of 10 °C min−1. Nitrogen adsorption–desorption measurements were carried out at liquid nitrogen temperature on an APSP 2020 volumetric adsorption analyzer, samples were pre-degassed at 200 °C to remove water and other physical adsorbed species. Zeta potential was measured by a Malvern Nano ZS laser granulometer with a 4 mW and 633 nm He–Ne laser. Water contact angles were measured on a Powereach JC2000D2M Drop Shape Analyzer. The TEM images were obtained using a JEOL JEM-2100F transmission electron microscopy.
2.3 Hydrogenation test
AQ hydrogenation was carried out in a batch reactor with the volume of 100 mL. Firstly, dried AQ (2-ethyl-anthraquinone, EAQ, ≥99.0%, Wuhan Fude Chemical Co., Ltd., China; 2-tert-butyl-anthraquinone, TBAQ, >98.0%, TCI Tokyo Chemical Industry Co., Ltd., Japan; 2-amyl-anthraquinone, AAQ, ≥99.0%, Shanghai Ruisi Chemical Co., Ltd., China) was dissolved in a mixture solvent of 1,3,5-trimethylbenzene (TMB, 97%, Aladdin Industrial Corporation, China) and trioctyl phosphate (TOP, 98%, TCI Tokyo Chemical Industry Co., Ltd., Japan) with the volume ratio of 1
:
1, yielding a working solution with the AQ concentration of 0.38 mol L−1. Then, 0.2 g reduced catalyst and 30 mL working solution were added into the reactor. N2 was fed to replace air and the reactor was heated to 60 °C in a water bath. Finally, H2 was fed into the reactor. When the pressure reached 0.3 MPa, the mechanical agitation was turned on and the reaction was started. H2 consumption was measured by a mass flowmeter. After the reaction finished, the hydrogenated working solution was completely oxidized with O2 at room temperature and atmospheric pressure and then hydrogen peroxide was extracted with deionized water for 4 times. H2O2 in the water phase was determined by titration with KMnO4 solution. The raffinate was analyzed by a gas chromatography (Bruker 456-GC) with DB-17 column (60 m × 0.32 mm × 0.25 μm) and FID detector.
3 Results and discussion
3.1 Characterization of catalysts
3.1.1 XRD characterization. The small angle XRD patterns of catalysts are shown in Fig. 1(a). All catalysts have three distinct characteristic peaks at 0.9°, 1.4° and 1.7° which can be indexed to the (100), (110) and (200) reflections associated with the highly ordered hexagonal symmetry of SBA-15 structure.32 With extending the pre-hydrolysis time of TEOS from 0.5 to 2 h, the intensity of diffraction peak (100) gradually increases, indicating increased long-range order. Among them, the peak intensity of Pd/P-2 (the pre-hydrolysis time is 2 h) is very close to that of Pd/SN. But, with further extension of the pre-hydrolysis time to 4 h, the intensity of diffraction peak (100) slightly decreases. This is in agreement with the observation by Wang et al. on methylaminopropyl functionalized SBA-15 silica synthesized by co-condensation of MAPTMS and TEOS.33
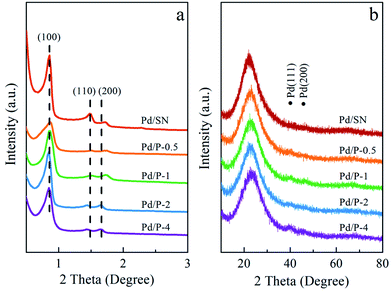 |
| Fig. 1 (a) Small angle and (b) wide angle XRD patterns of catalysts. | |
The wide angle XRD patterns are shown in Fig. 1(b). The diffraction peak at 2θ = 22° corresponds to amorphous silica.34 In addition, two extremely weak diffraction peaks are observed at 2θ = 40.1° and 46.5°, indexed to (111) and (200) reflections of palladium lattice.35 Among all catalysts, the signals of Pd0 in Pd/P-0.5 can almost not be observed, which are similar to those in Pd/SN. This may be due to the slightly higher dispersion of Pd particles in Pd/P-0.5 and Pd/SN than in others.36
3.1.2 FTIR measurement. Fig. 2 depicts the FTIR spectra of catalysts. There are four adsorption bands at 465 cm−1, 800 cm−1, 950 cm−1 and 1100 cm−1, corresponding to the O–Si–O deformation, SiO4 tetrahedron ring, Si–OH stretching and Si–O–Si asymmetrical stretching existed in typical SBA-15.37 The decreased intensities of Si–O–Si asymmetrical stretching bands for Pd/P-Xs might be ascribed to the co-condensation of PTES and Si–OH. This is in agreement with the results of small angle XRD patterns, in which (100) diffraction peaks decrease for Pd/P-Xs. The bands at 3400 cm−1 and 1600 cm−1 are assigned to the stretching and bending vibrations of physically adsorbed water, respectively.38,39 For Pd/P-Xs, the intensities of these two bands significantly weaken, indicating the decrease in hydrophilicity. The extremely weak bands appeared in the region of 2800–3000 cm−1 could be assigned to symmetric stretching vibration of CH2 (2935 cm−1) and CH3 (2975 cm−1), asymmetric stretching vibration of CH2 (2858 cm−1) and CH3 (2886 cm−1),40 indicating the presence of alkyl chain.41 The intensity of CH2 and CH3 bands increase with prolonging the pre-hydrolysis time, implying the incremental amount of alkyl chains.
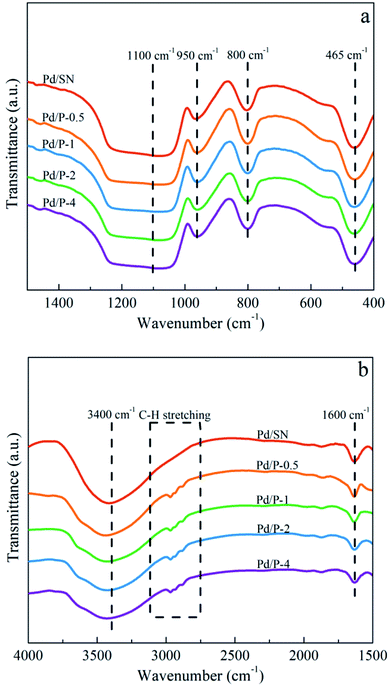 |
| Fig. 2 FTIR spectra in (a) 400–1500 cm−1 and (b) 1500–4000 cm−1 of catalysts. | |
3.1.3 Elemental analysis and thermogravimetric analysis. The carbon content of Pd/P-Xs obtained by elemental analysis (mcEA in Table 1) increases with prolonging the pre-hydrolysis time, and reaches a maximum of 3.50% at 4 h (Pd/P-4). Fig. 3 shows the TGA curves of catalysts. The weight loss at low-temperature (below 200 °C) could be assigned to physically adsorbed water. The low-temperature weight loss of Pd/P-Xs (0.07–0.29%) is lower than that of Pd/SN (0.63%), being ascribed to the lower hydrophilicity of Pd/P-Xs than Pd/SN. All the catalysts (including Pd/SN) also exhibit a weight loss at high-temperature (above 200 °C). The high-temperature weight loss of Pd/SN (1.57%, mL in Table 1) is lower than that consistent with mcEA. This indicates that the weight loss in the high temperature is mainly caused by the decomposition of alkyl chains.
Table 1 Physicochemical properties of catalysts
Catalysts |
mcEAa (%) |
mLb (%) |
mcGAc (%) |
SBETd (m2 g−1) |
VPe (cm3 g−1) |
dPf (nm) |
twall/a0g (nm) |
DPdh (nm) |
Carbon content of catalysts determined by elemental analysis. Weight loss at 200–700 °C determined by thermogravimetric analysis. Difference in mL between Pd/P-Xs and Pd/SN. Specific surface area calculated by BET method. Total pore volume obtained at 0.9 in the relative pressure of P/P0. Pore size calculated from the desorption branch by BJH method. Pore wall thickness (twall = a0 − dP)/crystal cell parameter. Average size of Pd particles estimated from TEM images. |
Pd/P-0.5 |
2.87 |
4.20 |
2.63 |
789 |
1.02 |
5.6 |
6.1/11.7 |
4.3 |
Pd/P-1 |
3.01 |
4.65 |
3.08 |
813 |
1.09 |
6.5 |
5.4/11.9 |
4.6 |
Pd/P-2 |
3.28 |
4.94 |
3.37 |
829 |
1.15 |
6.6 |
5.4/12.0 |
4.6 |
Pd/P-4 |
3.50 |
5.10 |
3.53 |
822 |
1.12 |
6.4 |
5.6/12.0 |
4.7 |
Pd/SN |
— |
1.57 |
— |
497 |
1.05 |
8.0 |
3.8/11.8 |
4.4 |
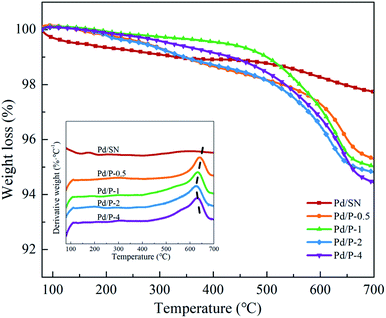 |
| Fig. 3 TGA curves of catalysts (inset: DTG curves of catalysts). | |
As shown in the DTG curves of catalysts, the maximum peak temperature in the range of high temperature slightly decreases with extending the pre-hydrolysis time from 0.5 to 2 h and achieves the lowest value at 2 h. Then, it rises slightly as the pre-hydrolysis time further extended to 4 h. It can be explained by the different distribution of organic groups. The decomposition temperature of the organic groups distributed on the outer surface of SBA-15 should be relatively low. At the early stage of synthesis, a small amount of TEOS is hydrolyzed and formed silanol groups are not yet self-assembly around the P123 micelles. The functional groups could be dispersed homogeneously in the mixture of TEOS and P123, which is similar to the description by Kecht et al. in their studies on selective functionalization of CMS materials.42 Hence, the functional groups added at 0.5 h would co-condense with silanol groups around P123 and a small part of functional groups may penetrate into P123 micelles, resulting in more distribution on the pore wall and inside pores of SBA-15 as shown in Scheme 1. With any extension of TEOS pre-hydrolysis time longer than 0.5 h (1 h and 2 h), the amount of hydrolyzed TEOS increases and silanol groups gradually condense around P123, which makes more functional groups gradually distributed on the outer surface. At 4 h, the compact structure between P123 and silica forms, which compels functional groups to concentrate on the channel opening. The change in distribution of functional groups in SBA-15 with the pre-hydrolysis time of TEOS is in good agreement with that of the pore size of Pd/P-Xs (Table 1).
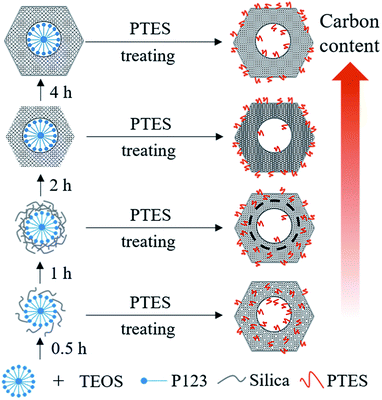 |
| Scheme 1 Schematic diagram for co-condensation of PTES and TEOS. | |
3.1.4 N2 adsorption–desorption. The N2 adsorption–desorption isotherms and pore size distributions of catalysts are displayed in Fig. 4. The calculated textural properties are listed in Table 1. As shown in Fig. 4(a), the isotherms are all of type IV with obvious H1 hysteresis loops at high relative pressure, indicating the presence of uniformly ordered cylindrical mesopores.43 The pore size of Pd/P-Xs (5.6–6.6 nm) is smaller than that of Pd/SN (8.0 nm), with the opposite variation in the pore wall thickness due to the existence of organic groups. Among Pd/P-Xs, Pd/P-2 gives the largest pore size, although its carbon content is close to Pd/P-4 having the highest carbon content.
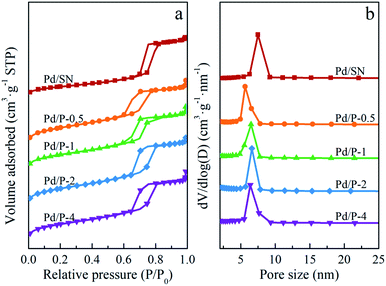 |
| Fig. 4 (a) Nitrogen adsorption–desorption isotherms and (b) pore size distributions of catalysts. | |
3.1.5 Zeta potential and water contact angle. The zeta potential and water contact angles of catalysts are shown in Fig. 5. The unfunctionalized catalyst has the lowest zeta potential (−3.39 mV) and water contact angle (13°) due to the highest hydrophilicity. Both the zeta potential and water contact angles of functionalized catalysts increase compared with Pd/SN, indicating the improvement of hydrophobicity.44 As shown in Fig. 5, zeta potential and water contact angles do not monotonously vary with the carbon content, instead the maximum values of zeta potential and water contact angles appear at 3.28%. This could be ascribed to the difference in the distribution of organic groups, which is greatly affected by the pre-hydrolysis time. Rosenholm reported that the zeta potential is sensitive only to functional groups on the outer surface of porous material.45 In comparison, functionalization groups trends to distribute on the outer surface of catalyst at the pre-hydrolysis time of 2 h.
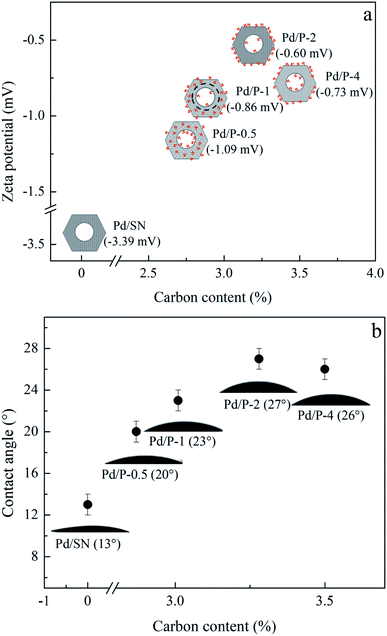 |
| Fig. 5 (a) Zeta potential and (b) water contact angles of catalysts. | |
3.1.6 TEM. Fig. 6 shows the TEM images of catalysts and the size distributions of Pd particles. It can be observed that all catalysts present a regular P6mm ordered mesoporous structure, which is consistent with the results of XRD and N2 adsorption–desorption.46 The average sizes of Pd particles in Pd/P-0.5 and Pd/SN are slightly smaller than those in Pd/P-1, Pd/P-2 and Pd/P-4 (4.3–4.4 nm vs. 4.6–4.7 nm, Table 1).
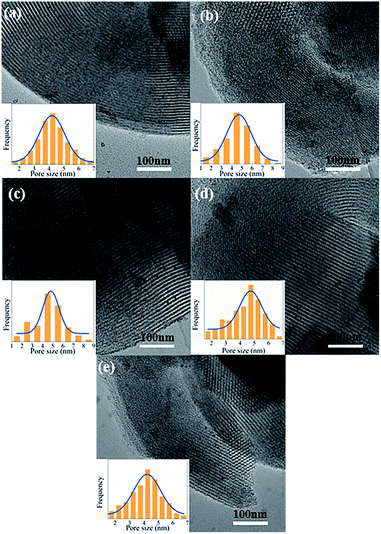 |
| Fig. 6 TEM images of (a) Pd/P-0.5, (b) Pd/P-1, (c) Pd/P-2, (d) Pd/P-4 and (e) Pd/SN (insets: size distributions of Pd particles). | |
3.2 Catalytic test
3.2.1 Hydrogenation of EAQ. The ratio of hydrogen consumption to the initial amount of EAQ (RHC, mol H2 per mol AQ) over functionalized Pd/P-Xs is delineated in Fig. 7(a). As can be seen in Fig. 7(a), RHC shows a linear increase with the reaction time at the initial stage. Thus, the activity of catalyst is described using the H2 initial consumption rate (r0, hydrogen consumption per unit reaction time and Pd mass in the linear region of RHC curve) as listed in Table 2. Pd/P-1 and Pd/P-2 give the higher RHC at the same reaction time and r0 than Pd/SN, but Pd/P-0.5 and Pd/P-4 give the opposite results. The high activity of Pd/P-2 and Pd/P-1 can be explained by combination of high hydrophobicity and relatively large pore diameter. The high hydrophobicity benefits the adsorption of EAQ molecules on the catalyst surface from the organic solution. And larger pore diameter could facilitate the diffusion of EAQ molecules to active sites.47,48 Although Pd/P-0.5 and Pd/P-4 have higher hydrophobicity than Pd/SN, the obviously small pore size of Pd/P-0.5 and Pd/P-4 limit the diffusion of EAQ molecules, rendering the lower activity than the latter. As for between Pd/P-0.5 and Pd/P-4, the smaller size of Pd particles in Pd/P-0.5 than Pd/P-4 is responsible for its relatively higher activity.16
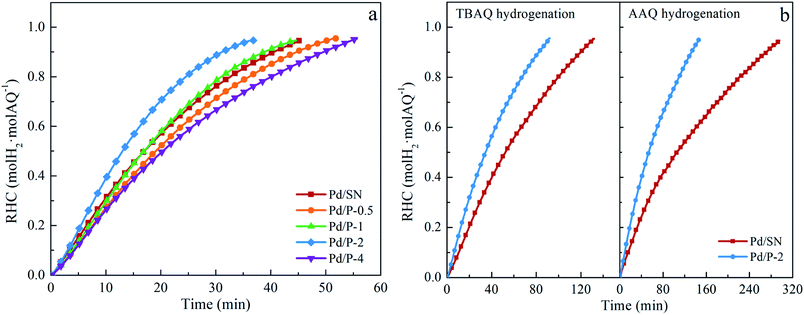 |
| Fig. 7 Ratio of hydrogen consumption to the initial amount of AQ (RHC) for (a) EAQ hydrogenation and (b) TBAQ and AAQ hydrogenation (reaction conditions: catalyst amount: 6.7 g L−1, concentration and volume of AQ solution: 0.38 mol L−1 and 30 mL, temperature: 60 °C, pressure: 0.3 MPa). | |
Table 2 Initial hydrogen consumption rate and selectivity of AQ hydrogenation
Catalysts |
Reactants |
r0a (mol H2 per g Pd per min) |
Sb, % |
AQH2 |
H4AQ |
EAN |
iso-H4EAQ |
Initial hydrogen consumption rate defined as hydrogen consumption per unit reaction time and Pd mass in the linear region of RHC curve (Fig. 7). Selectivity at RHC of about 0.95. |
Pd/P-0.5 |
EAQ |
0.14 |
94.9 |
3.6 |
1.3 |
0.2 |
Pd/P-1 |
EAQ |
0.16 |
95.1 |
3.5 |
1.2 |
0.2 |
Pd/P-2 |
EAQ |
0.20 |
95.3 |
3.4 |
1.1 |
0.2 |
Pd/P-4 |
EAQ |
0.13 |
94.6 |
3.8 |
1.4 |
0.2 |
Pd/SN |
EAQ |
0.15 |
94.3 |
4.1 |
1.4 |
0.2 |
Pd/P-2 |
TBAQ |
0.08 |
93.2 |
6.4 |
0.4 |
— |
Pd/SN |
TBAQ |
0.05 |
93.3 |
6.4 |
0.3 |
— |
Pd/P-2 |
AAQ |
0.05 |
92.9 |
6.7 |
0.4 |
— |
Pd/SN |
AAQ |
0.02 |
93.1 |
6.6 |
0.3 |
— |
The selectivity to target product 2-ethyl-anthrahydroquinone (EAQH2) and by-products detected including 2-ethyl-anthrone (EAN), 2-ethyl-5,6,7,8-tetrahydroanthraquinone (H4EAQ), and 2-ethyl-1,2,3,4-tetrahydroanthraquinone (iso-H4EAQ) at about 0.95 in RHC are shown in Table 2. Bombi et al.22 and Biffis et al.23 reported that the lipophilic catalysts could reduce the probability of deep hydrogenation, improving the selectivity. In this work, however, the selectivity to EAQH2 is very close (approximately 95%). This might be ascribed to the low polarity of EAQH2. Moreover, the hydrophobicity of Pd/P-Xs is much lower than that of lipophilic supports used in their work. Under this circumstance, the improvement effect of hydrophobicity created by organic functionalization on the selectivity is slight and it is easy to be neutralized by the negative effects of decreased pore size of functionalized catalysts on the selectivity.
3.2.2 Hydrogenation of TBAQ and AAQ. Fig. 7(b) and Table 2 show RHC, r0 and selectivity of the TBAQ and AAQ hydrogenation over Pd/SN and Pd/P-2. It is found that Pd/P-2 gives higher activity than Pd/SN, regardless of the reactants. Moreover, the positive effects of hydrophobicity on the rate of AQ hydrogenation enhance with the alkyl-chain length. To be specific, the initial hydrogenation rate of AAQ, TBAQ and EAQ increases by 150.0%, 60.0% and 33.3%, respectively. In addition, it can be observed that the rate of EAQ hydrogenation is more rapid than that of TBAQ, which is in its turn more rapid than that of AAQ. The results are accordant with those reported by Yuan et al.49For hydrogenation of TBAQ and AAQ, the by-products detected in this work are only corresponding H4AQ (2-tert-butyl- and 2-amyl-5,6,7,8-tetrahydroanthraquinone, H4TBAQ and H4AAQ) and AN (2-tert-butyl- and 2-amyl-anthrone, TBAN and AAN). As can be seen in Table 2, the selectivity to the target products and by-products over functionalized and unfunctionalized catalysts is very close, which is similar to the results of the EAQ hydrogenation. Moreover, the selectivity of TBAQ and AAQ hydrogenation is also very close.
4 Conclusions
PTES functionalized SBA-15 was synthesized by the co-condensation method and used as the support for preparation of Pd catalyst. The hydrophilicity/hydrophobicity and pore size of catalysts were shown to be greatly affected by the pre-hydrolysis time of TEOS. The organic functional groups in SBA-15 support synthesized at the pre-hydrolysis time of 2 h trend to distribute on its outer surface and the Pd catalyst prepared on it (Pd/P-2) has the highest hydrophobicity and largest pore size. The combination of the high hydrophobicity and largest pore size benefits the activity of catalyst. The highest initial hydrogen consumption rate for the EAQ hydrogenation (0.2 mol H2 per g Pd per min) was obtained over Pd/P-2.
The positive effect of support hydrophobicity on catalyst activity increases with the length of alkyl side chain in 2-alkyl-anthraquinone. The initial hydrogen consumption rate for the AAQ hydrogenation obtained over Pd/P-2 increased by 150.0% compared with that over the catalyst prepared on unfunctionalized SBA-15 support.
Conflicts of interest
There are no conflicts to declare.
Acknowledgements
This work is supported by financial support from the National Natural Science Foundation of China (21676184).
References
- R. Guan, X. Yuan, Z. Wu, L. Jiang, Y. Li and G. Zeng, Chem. Eng. J., 2018, 339, 519–530 CrossRef CAS.
- R. Ciriminna, L. Albanese, F. Meneguzzo and M. Pagliaro, ChemSusChem, 2016, 9, 3374–3381 CrossRef CAS.
- Y. Guo, C. Dai and Z. Lei, Chem. Eng. Process., 2019, 136, 211–225 CrossRef CAS.
- S. Yang, A. Verdaguer-Casadevall, L. Arnarson, L. Silvioli, V. Čolić, R. Frydendal, J. Rossmeisl, I. Chorkendorff and I. E. L. Stephens, ACS Catal., 2018, 8, 4064–4081 CrossRef CAS.
- H. Li, B. Zheng, Z. Pan, B. Zong and M. Qiao, Front. Chem. Sci. Eng., 2017, 12, 124–131 CrossRef.
- H. Yao, C. Shen, Y. Wang and G. Luo, RSC Adv., 2016, 6, 23942–23948 RSC.
- A. Drelinkiewicz and A. Waksmundzka-Góra, J. Mol. Catal. A: Chem., 2006, 246, 167–175 CrossRef CAS.
- R. Kosydar, A. Drelinkiewicz and J. P. Ganhy, Catal. Lett., 2010, 139, 105–113 CrossRef CAS.
- E. Yuan, C. Wu, X. Hou, M. Dou, G. Liu, G. Li and L. Wang, J. Catal., 2017, 347, 79–88 CrossRef CAS.
- R. E. Albers, M. Nyström, M. Siverström, A. Sellin, A.-C. Dellve, U. Andersson, W. Herrmann and T. Berglin, Catal. Today, 2001, 69, 247–252 CrossRef.
- P. Tang, Y. Chai, J. Feng, Y. Feng, Y. Li and D. Li, Appl. Catal., A, 2014, 469, 312–319 CrossRef CAS.
- X. Chen, S. Wang, J. Zhuang, M. Qiao, K. Fan and H. He, J. Catal., 2004, 227, 419–427 CrossRef CAS.
- E. Yuan, C. Wu, G. Liu, G. Li and L. Wang, J. Ind. Eng. Chem., 2018, 66, 158–167 CrossRef CAS.
- N. Wang, Q. Ma, E. Yuan and L. Wang, Trans. Tianjin Univ., 2019, 25, 595–602 CrossRef CAS.
- X. Li, H. Su, G. Ren and S. Wang, RSC Adv., 2015, 5, 100968–100977 RSC.
- R. Hong, J. Feng, Y. He and D. Li, Chem. Eng. Sci., 2015, 135, 274–284 CrossRef CAS.
- R. Kosydar, A. Drelinkiewicz, E. Lalik and J. Gurgul, Appl. Catal., A, 2011, 402, 121–131 CrossRef CAS.
- H. Chen, D. Huang, X. Su, J. Huang, X. Jing, M. Du, D. Sun, L. Jia and Q. Li, Chem. Eng. J., 2015, 262, 356–363 CrossRef CAS.
- A. P. A. Drelinkiewicz, R. Kangas and R. Laitinen, Catal. Lett., 2004, 94, 157–170 CrossRef CAS.
- J.-T. Feng, H.-Y. Wang, D. G. Evans, X. Duan and D.-Q. Li, Appl. Catal., A, 2010, 382, 240–245 CrossRef CAS.
- X. Li, H. Su, G. Ren and S. Wang, Appl. Catal., A, 2016, 517, 168–175 CrossRef CAS.
- G. Bombi, S. Lora, M. Zancato, A. A. D'Archivio, K. Jerabek and B. Corain, J. Mol. Catal. A: Chem., 2003, 194, 273–281 CrossRef CAS.
- A. Biffis, R. Ricoveri, S. Campestrini, M. Kralik, K. Jeroea¡bek and B. Corain, Chem.–Eur. J., 2002, 8, 2962–2967 CrossRef CAS.
- A. Drelinkiewicz, A. Waksmundzka-Góra, J. W. Sobczak and J. Stejskal, Appl. Catal., A, 2007, 333, 219–228 CrossRef CAS.
- Q. Ma, N. Wang, G. Liu and L. Wang, Microporous Mesoporous Mater., 2019, 279, 245–251 CrossRef CAS.
- A. S. M. Chong and X. S. Zhao, J. Phys. Chem. B, 2003, 107, 12650–12657 CrossRef CAS.
- D. Rath, S. Rana and K. M. Parida, RSC Adv., 2014, 4, 57111–57124 RSC.
- X. Niu, X. Zhou, Z. Lv, Y. Gao, J. Zhang and H. Wang, Mater. Res. Innovations, 2016, 20, 151–155 CrossRef CAS.
- M. Barczak, J. Solid State Chem., 2018, 258, 232–242 CrossRef CAS.
- H. A. Khan, A. Jaleel, P. Natarajan, S. Yoon and K.-D. Jung, Int. J. Hydrogen Energy, 2019 DOI:10.1016/j.ijhydene.2019.05.139.
- Y. Zhu, Z. Cheng, Q. Xiang, Y. Zhu and J. Xu, Sens. Actuators, B, 2018, 256, 888–895 CrossRef CAS.
- Z. Zhang, Y. Luo, Y. Guo, W. Shi, W. Wang, B. Zhang, R. Zhang, X. Bao, S. Wu and F. Cui, Chem. Eng. J., 2018, 344, 114–123 CrossRef CAS.
- X. Wang, Y.-H. Tseng, J. C. C. Chan and S. Cheng, Microporous Mesoporous Mater., 2005, 85, 241–251 CrossRef CAS.
- J. Sun, J. Zhang, H. Fu, H. Wan, Y. Wan, X. Qu, Z. Xu, D. Yin and S. Zheng, Appl. Catal., B, 2018, 229, 32–40 CrossRef CAS.
- F. Ulusal, E. Erünal and B. Güzel, J. Nanopart. Res., 2018, 20, 219 CrossRef.
- L. Li, L.-X. Zhang, J.-L. Shi, J.-N. Yan and J. Liang, Appl. Catal., A, 2005, 283, 85–89 CrossRef CAS.
- T. Ji, C. Ma, L. Brisbin, L. Mu, C. G. Robertson, Y. Dong and J. Zhu, Appl. Surf. Sci., 2017, 399, 565–572 CrossRef CAS.
- R. He, Z. Wang, L. Tan, Y. Zhong, W. Li, D. Xing, C. Wei and Y. Tang, Microporous Mesoporous Mater., 2018, 257, 212–221 CrossRef CAS.
- M. M. Abolghasemi, S. Hassani and M. Bamorowat, Microchim. Acta, 2015, 183, 889–895 CrossRef.
- J. Huang, M. Ye, Y. Qu, L. Chu, R. Chen, Q. He and D. Xu, J. Colloid Interface Sci., 2012, 385, 137–146 CrossRef CAS.
- H. Yang, F. Li, C. Shan, D. Han, Q. Zhang, L. Niu and A. Ivaska, J. Mater. Chem., 2009, 19, 4632–4638 RSC.
- J. Kecht, A. Schlossbauer and T. Bein, Chem. Mater., 2008, 20, 7207–7214 CrossRef CAS.
- T. Krajnovic, D. Maksimovic-Ivanic, S. Mijatovic, D. Draca, K. Wolf, D. Edeler, L. A. Wessjohann and G. N. Kaluderovic, Nanomaterials, 2018, 8, 322 CrossRef.
- Y. Xia, Z. Yang, R. Zhang, Y. Xing and X. Gui, Fuel, 2019, 239, 145–152 CrossRef CAS.
- J. M. Rosenholm and M. Lindén, Chem. Mater., 2007, 19, 5023–5034 CrossRef CAS.
- H. G. Hosseini, E. Doustkhah, M. V. Kirillova, S. Rostamnia, G. Mahmoudi and A. M. Kirillov, Appl. Catal., A, 2017, 548, 96–102 CrossRef CAS.
- X. Chen, J. Catal., 2003, 220, 254–257 CrossRef CAS.
- A. Drelinkiewicz, A. Waksmundzkagora, W. Makowski and J. Stejskal, Catal. Commun., 2005, 6, 347–356 CrossRef CAS.
- E. Yuan, X. Ren, L. Wang and W. Zhao, Front. Chem. Sci. Eng., 2017, 11, 177–184 CrossRef CAS.
|
This journal is © The Royal Society of Chemistry 2019 |
Click here to see how this site uses Cookies. View our privacy policy here.