DOI:
10.1039/C9RA06359E
(Paper)
RSC Adv., 2019,
9, 31728-31734
TiO2 nanocrystals with the {001} and {101} facets co-exposed with MIL-100(Fe): an egg-like composite nanomaterial for efficient visible light-driven photocatalysis†
Received
14th August 2019
, Accepted 16th September 2019
First published on 7th October 2019
1. Introduction
Nowadays, environmental pollution caused by organic dyes in wastewater is becoming more serious.1–5 The design and self-assembly of novel, efficient, and highly stable photocatalysts are critical to solving the current environmental energy problems.6–9 TiO2 has been widely used for water decomposition and the photocatalytic degradation of organic pollutants because of its chemical stability, strong oxidizing power, non-toxicity and low-cost.2–5,10 Large-scale commercial applications are still difficult in research at present. Moreover, the adsorption capacity of TiO2 is poor, the specific surface area is small, and the rapid recombination of photoexcited electron–hole pairs is also a factor that causes its low photocatalytic efficiency.11,12 Researchers have used many methods to improve and enhance the photocatalytic performance of TiO2. For instance, precious metal loading, quantum dot doping, semiconductor recombination, and different heterojunction structures improve the photocatalytic properties of materials to some extent.13–15 In particular, the synergistic effect of the {001} and {101} crystal facets of anatase TiO2 and the crystal face heterojunction theory have proven that the photocatalytic properties of the facet-controlled TiO2 material are improved.14–17,44–46 However, high-efficiency TiO2-based photocatalytic materials have been rarely reported thus far.
Metal-organic frameworks (MOFs) are bridged by metal ions or metal clusters with organic ligands containing O or N, forming 1D, 2D or 3D coordination porous crystal materials, which together possess the advantages of organic and inorganic compounds.18–21 An ideal carrier is a solid matrix with a large specific surface area.22 The advantages of MOFs as photocatalysts are their diversity, ideal ordered structure and high surface area, and they have considerable application potential in adsorption and catalysis.20–25 Notably, several MOF species, such as MIL-101(Fe),26–28 NH2-UiO-66 (ref. 29–32) and NH2-MIL-125(Ti),33–36 and various MOF-semiconductor composites, such as TiO2@MIL-101,37–39 CsPbBr3 dots/UiO-66(NH2),40 ZnIn2S4@NH2-MIL-125(Ti)41 and Fe3O4@MIL-100(Fe),42 are widely studied in the photocatalytic degradation of pollutants. The sandwich-like TiO2NS@MIL-100(Fe) nanocomposite obtained by the self-assembly of TiO2NS on porous MIL-100(Fe) not only has a porous channel to adsorb organic molecules, but the interface of the composite also provides a platform for photoexcited electrons. Consequently, the photoelectron–hole separation increased, the photocatalytic performance of the material was enhanced, and the adsorption performance was also improved.43 The MIL-100(Fe)/P25 composite photocatalyst was formed by a process in which MIL-100(Fe) was grown on the TiO2 surface, and several Ti atoms were replaced by Fe atoms, thereby resulting in a change in the electron density distribution and defect levels.4 In the photocatalytic process, the excited electrons were trapped at the defect level, which considerably suppressed the recombination of the charge carriers and increased the number of charge carriers, thereby improving the photocatalytic efficiency. When special TiO2@MIL-101 core–shell nanocomposites were used as adsorbents and catalysts, the adsorption capacity was outstanding and good catalytic performance was also exhibited.37
Herein, an egg-like TiO2/MIL-100(Fe) composite nanomaterial was successfully synthesized, for the first time, via a facile two-pot hydrothermal method, and anatase TiO2 had the {001} and {101} facets co-exposed. The synthesised TiO2/MIL-100(Fe) composite could efficiently photocatalyse the organic dye methylene blue (MB) under visible light (λ = 664 nm). The outstanding photocatalytic properties of the composite can be attributed to the introduction of facet-controlled TiO2 in porous MIL-100(Fe) with a high surface area. At the same time, the increased surface area and average pore size of the TiO2/MIL-100(Fe) composite effectively improved its photocatalytic properties, which was different from those reported in previous studies. Amongst these composites, the 30% TiO2/MIL-100(Fe) composite exhibited the most complete egg-like morphology and had high photocatalytic performance. The efficiency of MB degradation could reach 99.02% in 30 min, and the kinetic rate was 0.158 min−1, which is 2.1 and 4.3 times those of pure TiO2 (0.036 min−1) and MIL-100(Fe) (0.077 min−1), respectively.
2. Experimental details
2.1 Synthesis of MIL-100(Fe)
The MIL-100(Fe) was synthesized via a simple hydrothermal method.43,47 FeCl3·6H2O (18 mmol), H3BTC (12 mmol) and Na2CO3 (25 mmol) were added into Milli-Q water (36 mL) and stirred well. Then, the mixture was poured into a 100 mL Teflon-lined steel autoclave at 160 °C for 12 h. After naturally cooling to room temperature, the light orange solid was recovered by centrifugation. In order to remove the unreacted H3BTC, which was present both inside and outside the pores of the material, the reaction product was purified by consequent washing with hot Milli-Q water and hot ethanol several times. After centrifugation, the product was finally dried overnight at 60 °C. To prevent any experimental error, the synthesis of each material was repeated several times, and the samples were subjected to the same characterization techniques.
2.2 Synthesis of the {001} and {101} co-exposed TiO2/MIL-100(Fe) composite
The synthesis method of the {001} and {101} co-exposed TiO2/MIL-100(Fe) egg-like composite was similar to the above method for MIL-100(Fe). The only difference was that {001} and {101} co-exposed TiO2 (1.8, 3.6, 5.4, and 7.2 mmol) was added to the reaction precursor during the synthesis process. The purification process was adopted from the above method.
2.3 Characterization
X-ray powder diffraction analysis (XRD) was performed on a German Bruker D8 type. The experimental conditions were Cu Kα radiation, the tube pressure and tube flow were 35 kV and 30 mA, respectively, and the scanning range was 2θ = 5–70°. Scanning Electron Microscopy (SEM) was performed using the model MAIA 3 XMH. The transmission electron microscope (TEM) model JEM-2100F with an acceleration voltage of 200 kV and produced by the Japanese Electronics Society was employed. The UV-Vis-DRS model UV-2600 produced by Shimadzu Corporation of Japan was used with BaSO4 as the standard reference with a scanning wavelength range of 200–800 nm and a scan step size of 1 nm. X-ray photoelectron spectroscopy (XPS) was conducted on an EXCALAB210 produced by the American Thermoelectric Corporation. The UV-Vis spectrophotometer (model UVmini-1240) manufactured by Shimadzu Corporation of Japan was used for measuring the absorbance of methylene blue solution in the wavelength range of 200–800 nm.
2.4 Evaluation of photocatalytic activity
The photocatalytic performance of the TiO2/MIL-100(Fe) photocatalyst was evaluated by the photodegradation of methylene blue dye (MB). 5 mg of TiO2/MIL-100(Fe) photocatalyst was mixed with 100 mL of MB aqueous solution (10 ppm). A xenon lamp was used as the analog light source, and the dark adsorption experiment was performed for 1 h before the light was turned on, and the adsorption–desorption equilibrium was achieved between the photocatalyst and the contaminant. 3 mL of the suspension was centrifuged at 8000 rpm for 5 min, and the supernatant was taken for the measurement of absorbance at λ = 664 nm using a UV-visible spectrophotometer (UV-2550, Shimadzu).
3. Results and discussion
3.1 Structural and morphological characterization
The XRD patterns of bare TiO2 nanoparticles, MIL-100(Fe) and TiO2/MIL-100(Fe) with different molar ratios of components 100 (Fig. 1) depicted characteristic structures. All the peaks of pure TiO2 at 25.28°, 37.80°, 48.05°, 53.89° and 55.06° corresponded to the (101), (004), (200), (105) and (211) crystal facets of anatase TiO2. They depicted the characteristic tetragonal structure of anatase TiO2 (JCPDS card no. 21-1272). The characteristic peak of MIL-100(Fe) was consistent with those in the previous reports.43,47 After the simple hydrothermal TiO2 modification on MIL-100(Fe), the XRD patterns of the TiO2/MIL-100(Fe) composites with different molar ratios contained unique peaks for both TiO2 and MIL-100(Fe) (e.g. 2θ = 11.0°, 25.2°, 37.8°, 48.0°, and 53.8°). With the increase in added TiO2, the unique peak of TiO2/MIL-100(Fe) at 25.28° was evident, thereby corresponding to the {101} crystal plane of anatase TiO2. This result demonstrated the successful modification of TiO2 on the MIL-100(Fe) materials. The XRD pattern of the TiO2/MIL-100(Fe) material also retained the characteristic peak of MIL-100(Fe), indicating that the composite retained the typical crystal structure of MIL-100(Fe).
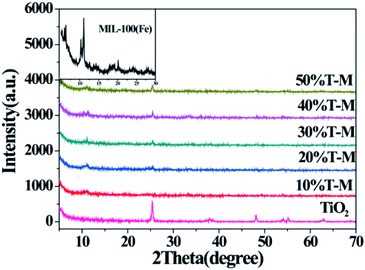 |
| Fig. 1 XRD patterns of {001} and {101} co-exposed TiO2 and 10–50% TiO2/MIL-100(Fe) composites; the inset is the enlarged XRD pattern of MIL-100(Fe) in the region of 2θ = 5–30°. | |
The BET results indicated the porous nature of MIL-100(Fe) and the 30% TiO2/MIL-100(Fe) composite. Fig. 2 shows the specific surface area and pore size distribution curves of the MIL-100(Fe) and 30% TiO2/MIL-100(Fe) materials. According to the BDDT classification, both samples belonged to type II isotherm, which also indicated that all the materials prepared had porous structures. Surprisingly, with the addition of TiO2, the specific surface area did not decrease and the pore size increased slightly, which is in agreement with the XRD results. According to previous reports, the average specific surface area of pure P25 is 53 m2 g−1.4 The average specific surface area of the 30% TiO2/MIL-100(Fe) composite was 460.56 m2 g−1. The porous 30% TiO2/MIL-100(Fe) composite with high specific surface area and large pore size can adsorb additional organic molecules when used as a photocatalyst and accelerate the photogenerated carrier separation, thereby improving the photocatalytic performance of the material (Table 1).
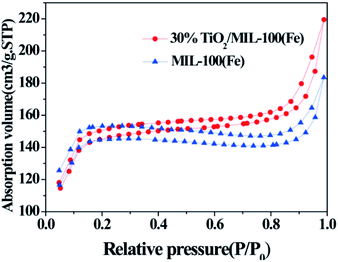 |
| Fig. 2 N2 adsorption–desorption isotherms of {001} and {101} co-exposed TiO2 and the 30% TiO2/MIL-100(Fe) composite. | |
Table 1 BET surface area of the {001} and {101} co-exposed TiO2 and 30% TiO2/MIL-100(Fe) composite
Samples |
BET surface area (m2 g−1) |
Pore volume (cm3 g−1) |
Pore size (nm) |
MIL-100(Fe) |
431.9545 |
0.2380 |
5.7786 |
30% TiO2/MIL-100(Fe) |
460.5602 |
0.2809 |
6.0852 |
The SEM and TEM images illustrated the influence of MIL-100(Fe) introduction on the morphological characteristics of the {001} and {101} co-exposed TiO2 samples (Fig. 3, S1 and S2†). TiO2 with co-exposed of {001} and {101} facets was successfully loaded on the surface of MIL-100(Fe), and the egg-like TiO2/MIL-100(Fe) was established well (Fig. 3(a)–(d), S1(a), (b) and S2†). Evident lattice fringes could be observed by HRTEM (Fig. 3(d)). The lattice fringe was 0.354 nm in size, corresponding to the {101} crystal plane of TiO2, and d = 0.235 nm corresponded to the {001} facet of TiO2. The crystal faces demonstrated the co-exposure of the {001} and {101} facets of TiO2 in the TiO2/MIL-100(Fe) composites. The element distribution maps further showed that the Fe and Ti elements were uniformly distributed on the TiO2/MIL-100(Fe) samples, thereby indicating that TiO2 was uniformly distributed on the MIL-100(Fe) carrier, which is consistent with the SEM results. The appearance of the characteristic peaks of Fe, Ti and O on the EDS map further demonstrated the successful preparation of TiO2/MIL-100(Fe) composites. TiO2 was also a factor in accelerating the photogenerated electron–hole pair separation due to the synergistic effect of the crystal plane between the {001} and {101} facets, which further explains the efficient photocatalytic performance of the {001} and {101} co-exposed TiO2/MIL-100(Fe) composites.
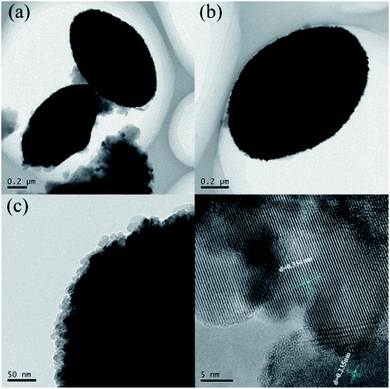 |
| Fig. 3 TEM images of the 30% {001} and {101} co-exposed TiO2/MIL-100(Fe) composite. (a and b) Different perspectives, (c) edge position, (d) lattice spacing. | |
The chemical composition and binding status of neat TiO2 and TiO2@30%MIL-100(Fe) were measured by XPS. The survey spectrum (Fig. 4(a)) showed the presence of Ti, Fe, O and C. The high resolution XPS spectrum of O 1s consisted of three component peaks at 531.4 eV, 530.4 eV and 528.8 eV (Fig. S3(a)†). The characteristic binding energy peaks at 458.8 eV and 464.5 eV corresponded to Ti 2p3/2 and Ti 2p1/2 of Ti atoms, which belong to Ti4+ in a tetragonal structure (Fig. S3(b)†).14 An additional peak appeared at 458.1 eV in the presence of the Fe–O–Ti bond. The Fe–O–Ti bond is formed during the growth of TiO2/MIL-100(Fe), in which some of the Ti atoms are replaced by Fe atoms. As shown in Fig. 4(b), the peaks of Fe 2p3/2 and Fe 2p1/2 were observed at 711.9 eV and 724.8 eV, respectively, thereby indicating that the Fe element in TiO2/MIL-100(Fe) existed in the form of Fe3+.47
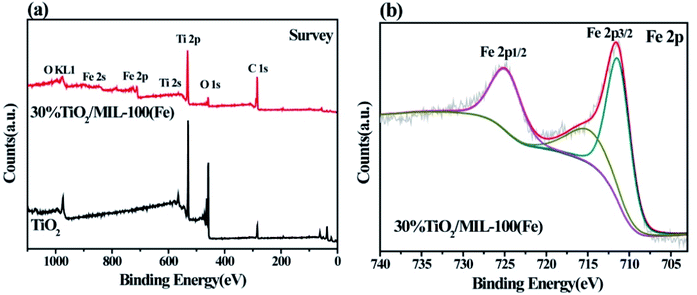 |
| Fig. 4 XPS pattern measurements of neat TiO2 and 30% TiO2/MIL-100(Fe): (a) survey and (b) Fe 2p binding energy spectra. | |
In order to further explore the factors affecting the photocatalytic activity of TiO2/MIL-100(Fe), UV-visible absorption spectroscopy was performed for TiO2, MIL-100(Fe) and the TiO2/MIL-100(Fe) composites with different molar ratios. The as-prepared TiO2 had an absorption wavelength of approximately 400 nm and belonged to the intrinsic absorption band (Fig. 5). In addition, MIL-100(Fe), as a carrier, also played an important role in the light absorption properties of the TiO2/MIL-100(Fe) composites. MIL-100(Fe) and 10–50% TiO2/MIL-100(Fe) composites had two absorption edges at 500 nm and 650 nm.
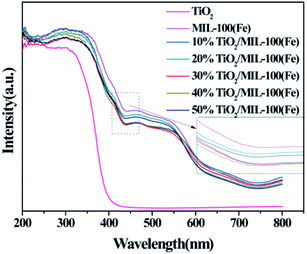 |
| Fig. 5 UV-vis DRS spectra of TiO2, MIL-100(Fe) and TiO2/MIL-100(Fe) composites. | |
3.2 Photocatalytic activities
The photocatalytic properties of TiO2, MIL-100(Fe) and the TiO2/MIL-100(Fe) materials with different molar ratios of TiO2 were investigated by the adsorption degradation of the organic dye MB under visible light. As shown in Fig. 6(a), MIL-100(Fe) and the TiO2/MIL-100(Fe) materials with different molar ratios of TiO2 had significant improvement compared with the photocatalyst and pure TiO2. With the addition of TiO2, the photocatalytic MB degradation efficiency of the TiO2/MIL-100(Fe) composites were significantly higher than that of MIL-100(Fe). The order of degradation efficiency was as follows: 30% T/M > 40% T/M > 20% T/M > 50% T/M > 10% T/M > MIL-100(Fe) > TiO2. The 30% TiO2/MIL-100(Fe) composite containing {001} and {101} facet co-exposed TiO2 exhibited the best photocatalytic performance with a degradation efficiency of 99.02% in 30 min. According to the photocatalytic experimental data, a quasi-first-order kinetic equation and the degradation rate constants for MB degradation and adsorption were obtained according to −ln(C/C0) = kt,16,17 as shown in Fig. 6(b), (c) and (d). The degradation rate of 30% TiO2/MIL-100(Fe) was the highest at 0.158 min−1, which was 2.1 and 4.4 folds higher than that of MIL-100(Fe) (0.077 min−1) and TiO2 (0.036 min−1), respectively (Fig. 6(b)–(d)). This result was observed because the rapid electron transfer between TiO2 with co-exposed {001} and {101} facets and MIL-100(Fe) allowed the photogenerated electron–hole pairs to be efficiently separated. The MB adsorption kinetics equation (Fig. 6(c)–(d)) showed that the adsorption rates of MIL-100(Fe) and TiO2/MIL-100(Fe) composites did not significantly improve, which is consistent with the BET results. Pure MIL-100(Fe) had the highest adsorption kinetics rate of 1.4 × 10−2 min−1. The adsorption capacity of pure TiO2 was low, and the adsorption amount of MB was approximately 1.9%. Combining TiO2 and MIL-100(Fe) increased the adsorption kinetics rate of the TiO2/MIL-100(Fe) complex because the high specific surface area and large pore size facilitated the capture of organic molecules and provided reaction sites. The interface channel also improved the adsorption capacity of the composite. At the same time, the synergy between the co-exposed {001} and {101} crystal facets of TiO2 could also effectively promote photocarrier separation and further improve the photocatalytic efficiency.
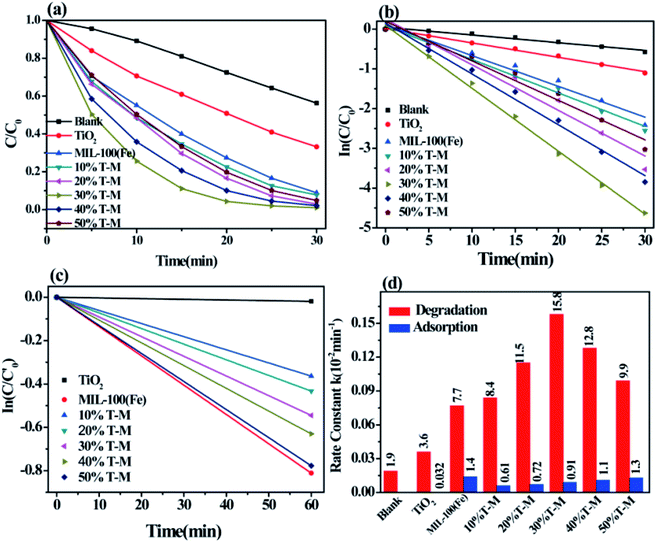 |
| Fig. 6 (a) Control experiments for the photodegradation of MB with respect to different photocatalysts; (b) kinetics of MB degradation as a function of photocatalysts; (c) kinetics of MB adsorption as a function of photocatalysts; (d) catalytic rate constants of MB degradation and adsorption. is the initial concentration of MB before dark adsorption, and C0 is the concentration of MB before illumination. Reaction conditions: 5 mg photocatalyst, 100 mL of 10 mg L−1 MB aqueous solution. | |
The photodegradation cycle of the 30% {001} and {101} facet co-exposed TiO2/MIL-100(Fe) composite was tested four times with MB to evaluate the reusability of the material. In each photodegradation experiment, the suspension was treated in the dark for 1 h to establish an adsorption–desorption equilibrium. The absorbance of MB from 4 cycles of photodegradation showed that the 30% TiO2/MIL-100(Fe) composite maintained good adsorption and catalytic properties and had good stability (Fig. 7). Only 5 mg of the photocatalyst was slightly damaged by centrifugation and washing, thereby resulting in a slight decrease in the photocatalytic performance and adsorption performance.
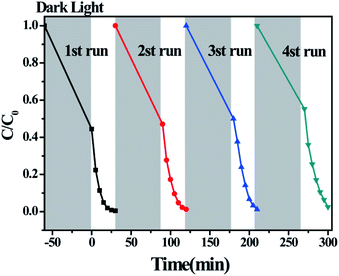 |
| Fig. 7 Photocatalytic degradation of MB by 30% TiO2/MIL-100(Fe) over four consecutive cycles. | |
According to the above results, the possible photocatalytic degradation mechanism of MB by the {001} and {101} facet co-exposed TiO2/MIL-100(Fe) complexes was proposed (Fig. 8). Due to the charge transfer occurring between an inorganic semiconductor and the MOF, photogenerated electron–hole pair recombination can be substantially suppressed. Under visible light, photoexcited electrons (e−) are transferred from the valence band to the conduction band on TiO2, thereby forming holes (h+) on the valence band.10 The photoexcited electrons (e−) are then transferred from the conduction band of TiO2 to the conduction band of MIL-100(Fe) by the interactions between the TiO2 and MIL-100(Fe) interfaces. This phenomenon also effectively suppresses the recombination of the photogenerated electron–hole pairs, thereby further improving the photocatalytic efficiency of the material. The photogenerated hole (e−) in the valence band of TiO2 oxidises MB or directly reacts with OH− in H2O to form a hydroxyl radical (·OH). The photogenerated electrons in the MIL-100(Fe) and TiO2 conduction bands react with O molecules to form superoxide radicals (·O2−).4,43 The MB molecules adsorbed on the surface of the composite are photodegraded by ·O2− and ·OH into CO2, H2O and other products. The TiO2/MIL-100(Fe) composite with a larger pore size and specific surface area can effectively adsorb a certain amount of dye molecules and become the base of further photocatalytic reactions. The synergistic effect between the total exposure of the {001} and {101} TiO2 crystal planes effectively improved the separation efficiency of the photogenerated electron–hole pairs. The special egg-like structure of the material had a larger pore size and specific surface area, which provided an effective channel for photoelectron electron–hole pair separation and a favourable place for the photocatalytic reaction. The interfacial effect of TiO2 and MIL-100(Fe) also increased the photocatalytic efficiency.
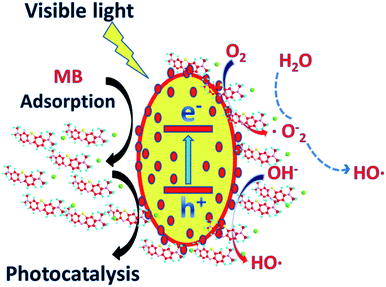 |
| Fig. 8 Proposed mechanism for the photocatalytic degradation of MB by the {001} and {101} facet co-exposed TiO2/MIL-100(Fe) composite. | |
4. Conclusion
In summary, the photocatalytic {001} and {101} facet co-exposed TiO2/MIL-100(Fe) composite material was successfully prepared via a simple two-step hydrothermal method. A TiO2/MIL-100(Fe) composite with 30% {001} and {101} facet co-exposed TiO2 that maintained a complete egg-like morphology was prepared for the first time. The material had a higher specific surface area and pore diameter than pure MIL-100(Fe) under the same preparation conditions and exhibited excellent performance in the photocatalytic degradation of the organic dye MB. The efficiency of 30% TiO2/MIL-100(Fe) in the photocatalytic degradation of MB in 30 min was as high as 99.02%. Photocatalytic experiments with 4 cycles showed that the reduction in the photocatalytic activity of the prepared composites was insignificant and it had good stability. The excellent performance in the photocatalysis was attributed to the synergistic effect between the {001} and {101} planes of TiO2 and the interfacial effect between TiO2 and MIL-100(Fe), and the egg-like morphology increased the specific surface area and pore size of the composite, which provided a channel for electron transfer to occur at the interface. To further improve solar energy utilisation, we will continue to conduct research on semiconductors and MOF composites.
Conflicts of interest
There are no conflicts to declare.
Acknowledgements
This work was supported by the National Natural Science Foundation of China (Grant no. 21671026) and Hunan Collaborative Innovation Center of Environmental and Energy Photocatalysis. The authors are also grateful to the aid provided by the Science and Technology Innovative Research Team in Higher Educational Institutions of Hunan Province.
Notes and references
- Z. Zou, J. Ye, K. Sayama and H. Arakawa, Nature, 2001, 414, 625 CrossRef CAS.
- C. B. D. Marien, T. Cottineau, D. Robert and P. Drogui, Appl. Catal., B, 2016, 194, 1 CrossRef CAS.
- F. Cao, J. Xiong, F. Wu, Q. Liu, Z. Shi, Y. Yu, X. Wang and L. Liang, ACS Appl. Mater. Interfaces, 2016, 8, 12239 CrossRef CAS.
- H.-Q. Xu, J. Hu, D. Wang, Z. Li, Q. Zhang, Y. Luo, S.-H. Yu and H.-L. Jiang, J. Am. Chem. Soc., 2015, 137, 13440 CrossRef CAS.
- X. Zeng, L. Huang, C. Wang, J. Wang, J. Li and X. Luo, ACS Appl. Mater. Interfaces, 2016, 8, 20274 CrossRef CAS.
- P. Tan, A. Zhu, L. Qiao, W. Zeng, H. Cui and J. Pan, J. Colloid Interface Sci., 2019, 533, 452–462 CrossRef CAS.
- F. Yao, T. Jiao, J. Yin, L. Zhang, L. Zhang, J. Zhou and Q. Peng, Nanoscale Res. Lett., 2019, 14, 78 CrossRef.
- Y. He, R. Wang, T. Jiao, X. Yan, M. Wang, L. Zhang, Z. Bai and Q. Zhang, ACS Sustainable Chem. Eng., 2019, 7, 10888–10899 CrossRef CAS.
- P. Tan, A. Zhu, Y. Liu, Y. Ma, W. Liu, H. Cui and J. Pan, Inorg. Chem. Front., 2018, 5, 679–686 RSC.
- H. Xiang, H. Fang, D. J. Gosztola, J. Zhang, P. Jena and W.-N. Wang, ACS Appl. Mater. Interfaces, 2019, 11, 12516 CrossRef.
- G. Xiang, T. Li, J. Zhuang and X. Wang, Chem. Commun., 2010, 46, 6801 RSC.
- A. Mercedes, E. Carbonell, B. Ferrer, F. X. Llabrési Xamena and H. Garcia, Chem.–Eur. J., 2007, 13, 5106 CrossRef.
- W. Zeng, B. Yuan, S. Cao, Y. Ma, Y. Liu, A. Zhu and P. Tan, ACS Appl. Mater. Interfaces, 2018, 10, 21328–21334 CrossRef CAS.
- L. Liu, Y. Jiang, H. Zhao, J. Chen, J. Cheng, K. Yang and Y. Li, ACS Catal., 2016, 6, 1097 CrossRef CAS.
- J. Ma, H. Wu, Y. Liu and H. He, J. Phys. Chem. C, 2014, 118, 7434 CrossRef CAS.
- J. Yu, J. Low, W. Xiao, P. Zhou and M. Jaroniec, J. Am. Chem. Soc., 2014, 136, 8839 CrossRef CAS PubMed.
- J. Liu, D. Olds, R. Peng, Y. Lei, S. F. Guo, S. Qian, J. Keum, B. S. Guiton, Z. Wu and K. Page, Chem. Mater., 2017, 29, 5591 CrossRef CAS.
- S. L. James, Chem. Soc. Rev., 2003, 32, 276 RSC.
- R. J. Drout, L. Robison and O. K. Farha, Coord. Chem. Rev., 2019, 381, 151 CrossRef CAS.
- T. Islamoglu, D. Ray, L. Peng, M. B. Majewski, I. Akpinar, X. Zhang, C. J. Cramer, L. Gagliardi and O. K. Farha, Inorg. Chem., 2018, 57, 13246 CrossRef CAS.
- L. Shi, T. Wang, H. Zhang, K. Chang, X. Meng, H. Liu and J. Ye, Adv. Sci., 2015, 2, 1500006 CrossRef.
- C. Wang, J. Yin, S. Han, T. Jiao, Z. Bai, J. Zhou, L. Zhang and Q. Peng, Catalysts, 2019, 9, 559 CrossRef CAS.
- R. Liang, R. Chen, F. Jing, N. Qin and L. Wu, Dalton Trans., 2015, 44, 18227 RSC.
- K. Guesh, A. D. C. Clarice, Á. Mayoral, M. Díaz-García, I. Díaz and M. Sanchez-Sanchez, Cryst. Growth Des., 2017, 17, 1806 CrossRef CAS.
- N. Stock and S. Biswas, Chem. Rev., 2011, 112, 933 CrossRef.
- J. W. Shin, M. Kim, J. Cirera, S. Chen, G. J. Halder, T. A. Yersak, F. Paesani, S. M. Cohen and Y. S. Meng, J. Mater. Chem. A, 2015, 3, 4738 RSC.
- D. Wang and Z. Li, Catal. Sci. Technol., 2015, 5, 1623 RSC.
- Z. Zhang, X. Li, B. Liu, Q. Zhao and G. Chen, RSC Adv., 2016, 6, 4289 RSC.
- D. Sun, Y. Fu, W. Liu, L. Ye, D. Wang, L. Yang, X. Fu and Z. Li, Chem.–Eur. J., 2013, 19, 14279 CrossRef CAS.
- L. Shen, R. Liang, M. Luo, F. Jing and L. Wu, Phys. Chem. Chem. Phys., 2015, 17, 117 RSC.
- S. J. Garibay and S. M. Cohen, Chem. Commun., 2010, 46, 7700 RSC.
- D. Sun and Z. Li, J. Phys. Chem. C, 2016, 120, 19744 CrossRef CAS.
- D. Sun, L. Ye and Z. Li, Appl. Catal., B, 2015, 164, 428 CrossRef CAS.
- D. Sun, W. Liu, Y. Fu, Z. Fang, F. Sun, X. Fu, Y. Zhang and Z. Li, Chem.–Eur. J., 2014, 20, 4780 CrossRef CAS.
- S.-N. Kim, J. Kim, H.-Y. Kim, H.-Y. Cho and W.-S. Ahn, Catal. Today, 2013, 204, 85 CrossRef CAS.
- C. H. Hendon, D. Tiana, M. Fontecave, C. Sanchez, L. D'arras, C. Sassoye, L. Rozes, C. Mellot-Draznieks and A. Walsh, J. Am. Chem. Soc., 2013, 135, 10942 CrossRef CAS.
- H. Sheng, D. Chen, N. Li, Q. Xu, H. Li, J. He and J. Lu, Chem. Mater., 2017, 29, 5612 CrossRef CAS.
- N. Chang, H. Zhang, M.-S. Shi, L. Jia, W. Shao and H.-T. Wang, Mater. Lett., 2017, 200, 55 CrossRef CAS.
- D. Tilgner, M. Friedrich, J. Hermannsdörfer and R. Kempe, ChemCatChem, 2015, 7, 3916 CrossRef CAS.
- S. Wan, M. Ou, Z. Qin and X. Wang, Chem. Eng. J., 2019, 358, 1287 CrossRef CAS.
- H. Liu, J. Zhang and D. Ao, Appl. Catal., B, 2018, 221, 433 CrossRef CAS.
- C.-F. Zhanga, L.-G. Qiu, K. Fei, Y.-J. Zhua, Y.-P. Yuana, G.-S. Xua and X. Jianga, J. Mater. Chem. A, 2013, 1, 14329 RSC.
- X. Liu, R. Dang, W. Dong, X. Huang, T. Jia, H. Gao and G. Wang, Appl. Catal., B, 2017, 209, 506 CrossRef CAS.
- J. Pan, G. Liu, G. Q. Lu and H.-M. Cheng, Angew. Chem., Int. Ed., 2011, 50, 2133 CrossRef CAS.
- Z. Zheng, B. Huang, J. Lu, X. Qin, X. Zhang and Y. Dai, Chem.–Eur. J., 2011, 17, 15032 CrossRef CAS PubMed.
- H. G. Yang, G. Liu, S. Z. Qiao, C. H. Sun, Y. G. Jin, S. C. Smith, J. Zou, H. M. Cheng and G. Q. Lu, J. Am. Chem. Soc., 2009, 131, 4078 CrossRef CAS.
- Y. Fang, W. Jia, G. Zeng, F. Jia, S. Zhang, Z. Peng and H. Zhang, Chem. Eng. J., 2018, 337, 532 CrossRef CAS.
Footnote |
† Electronic supplementary information (ESI) available. See DOI: 10.1039/c9ra06359e |
|
This journal is © The Royal Society of Chemistry 2019 |
Click here to see how this site uses Cookies. View our privacy policy here.