DOI:
10.1039/C9RA06195A
(Paper)
RSC Adv., 2019,
9, 30575-30580
Synthesis of porous carbon via a waste tire leavening strategy for adsorptive desulfurization
Received
9th August 2019
, Accepted 11th September 2019
First published on 26th September 2019
Abstract
Adsorptive desulfurization is an effective technology for removing harmful sulfur under mild conditions. Carbon materials have many advantages and are often used in adsorption desulfurization research, but until now have been synthesized using complicated methods and have shown limited adsorption capacity. Using an NaHCO3-assisted leavening method, waste tires were in the current work used as raw materials to produce hierarchically porous carbon that exhibits a high specific surface area and abundant oxygen-containing functional groups. In contrast to the sulfur removal by the carbon material prepared using a commonly used method, the as-prepared carbon material shows excellent adsorption performance, and was able to achieve an ultra-deep desulfurization of pentanethiol, specifically removing up to 99.7% of the sulfur from a model fuel with an initial sulfur concentration of 28 ppm. Therefore, we have provided a simple method for synthesizing adsorbents with high adsorption performance, and we expect these adsorbents to be used for industrial adsorptive desulfurization.
1. Introduction
To reduce the impact of pollutants on the environment,1,2 increasing attention has been paid to the standards for the emission of sulfides in the formulation of fuels.3–5 Recently, sulfide emissions have been limited by these standards to be less than 10 ppm.6,7 For a long time, the hydrodesulfurization process,8–14 as a cornerstone of the chemical industry, has been applied in removing harmful sulfur from oil.9 However, the hydrogen sulfide generated in the hydrodesulfurization process reacts with olefins to form a small amount of mercaptan, and sometimes the hydrotreatment needs to be repeated, resulting in increased costs. Therefore, non-hydrodesulfurization techniques for removing the mercaptan produced after the hydrodesulfurization process15 have been studied in order to greatly reduce costs. Such studied non-hydrodesulfurization of mercaptans has included photocatalytic oxidative desulfurization,16,17 oxidative desulfurization,18,19 adsorption and photocatalytic oxidation desulfurization,20 adsorptive desulfurization,21 and so on. Of these desulfurization processes, adsorptive desulfurization has been particularly widely studied22,23 because of its low energy consumption and effective removal capacity.24
So far, the main adsorbents used for removing mercaptans have included zeolite,25,26 activated carbons,27–31 nanoporous graphene,21 and boron nitride,32 among others. Of these different types of adsorbents, activated carbon has shown some particularly excellent properties such as high adsorption capacity,33,34 high specific surface area35,36 and easy regeneration. The raw materials that have been recently reported to be used for the synthesis of activated carbon have included sewage sludge, biochar, waste rubber tires, wood, lignocellulosic biomass, and animal bones.37 Rubber tires are essential for our daily transportation, and since they readily wear out, many waste tires become available every year all over the world. However, waste tires are non-biodegradable materials,37 and hence pose environmental problems. These problems, however, could be solved by recycling and reusing the tires. A previously reported method for preparing activated carbon materials from waste tires37–44 involves carbonizing the raw materials at about 500 °C, and subjecting the resulting sample to a physical activation process and then an HNO3 and NaOH chemical activation (Table 1). In addition, metals and metal oxides have been added to the activated carbon material to further enhance the adsorption performance.39,42 Therefore, in order to avoid the introduction of metals and to simplify the synthesis step, further investigations of the synthesis method have become extremely important. The “leavening” method has been reported to be advantageous for increasing the specific surface area of carbon materials.45,46
Table 1 The adsorption performance of activated carbon materials from waste tires
Entry |
Adsorbent |
Initial concentration |
Adsorption capacity (mg S per g adsorbent) or sulfur removal |
Ref. |
1 |
Acidic and basic treatments of activated C |
T (51 ppm), BT (50 ppm) DBT (52 ppm) |
0.18(T), 0.50(BT), 1.20(DBT) |
38
|
2 |
Ce/Fe-loaded rubber tire-derived activated C |
T (52 ppm), BT (50 ppm) DBT (51 ppm) |
7.78(T), 7.23(BT), 16.63(DBT) |
37
|
3 |
Rubber tire-derived C |
DBT (50 ppm) |
8.60 |
40
|
4 |
Nickel/rubber tire-derived activated C |
DBT (59 ppm) |
96.00% |
39
|
5 |
Nanocomposite of rubber tire-derived activated C and manganese oxide |
T (50 ppm), BT (52 ppm) DBT (53 ppm) |
4.50(T), 5.70(BT), 11.40(DBT) |
41
|
6 |
Cobalt and molybdenum nanoparticles loaded on rubber tire-derived activated C |
50 ppm each |
2.20(T), 2.32(BT), 2.72(DBT), 3.68(MBT), 3.64(MDBT), 3.72(DMDBT) |
42
|
7 |
Waste tires to activated C |
DBT (150 ppm) |
1.22 |
43
|
8 |
Porous C from waste tire leavening |
Pentanethiol (30 ppm S) |
99.70% |
This work |
Herein, to develop a green and sustainable synthetic process starting with waste tires as raw materials, we deployed the leavening method and obtained carbon materials displaying high specific surface areas and abundant surface functional groups. The obtained adsorbent was investigated in the desulfurization of pentanethiol and butanethiol. As expected, the carbon material prepared using the leavening method demonstrated a much enhanced adsorptive desulfurization ability compared to general carbon materials. This result suggests the significance here of randomly opened macropores, high specific surface area and abundant oxygen-containing functional groups of the as-prepared carbon materials. Moreover, this carbon material when optimized achieves very extensive desulfurization at a low concentration of sulfur, indicating promising application prospects for this material.
2. Experimental
2.1. Materials
KOH (AR grade) was purchased from Chengdu Kelong Chemical Reagent Factory. NaHCO3 (AR grade) was obtained from Sinopharm Chemical Reagent Co. Pentanethiol (>99.5%) was purchased from TCI (Shanghai) Development Co., Ltd. and butanethiol (>99%) was purchased from Aladdin.
2.2. Preparation of the carbon materials
First, 5.05 g of waste rubber tire particles and 10.2 g of KOH were ground and mixed, and then transferred into 50 mL of distilled water and stirred at 60 °C. The purpose of this process was to remove the surface impurities of the waste tires. The obtained sample was filtered, washed and dried. Then, the resulting black solid was mixed with NaHCO3 in mass ratios of 1
:
1, 1
:
1.5 and 1
:
2, respectively. Finally, the obtained mixture was calcined at 800 °C for 2 h under a nitrogen atmosphere. The prepared materials were marked as C-1, C-1.5 and C-2 (Fig. 1a).
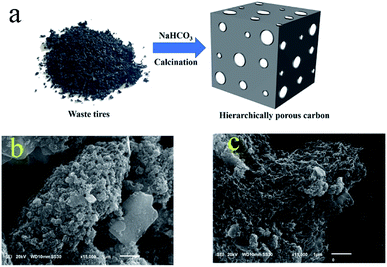 |
| Fig. 1 (a) Schematic of the synthesis of porous carbon. (b and c) SEM images of C and C-1.5. | |
Similar to the above process, the carbon material was also pre-treated and then calcined, but the calcination process was carried out without NaHCO3 and marked as C.
2.3. Characterization of the materials
Scanning electron microscopy (SEM) measurements were carried out using a JSM-6010 PLUS/LA scanning electron microscope. Surface areas of the obtained materials were determined using the Brunauer–Emmett–Teller (BET) method based on N2 adsorption–desorption isotherms collected on a TriStar II 2020 surface area and porosity analyser (Micromeritics Instrument Corporation). Fourier-transform infrared (FT-IR) spectra were acquired using a Nicolet FTIR spectrophotometer (Nexus 470). Raman spectra (Thermo Scientific DXR) were acquired to further characterize the properties of the materials.
2.4. Adsorption experiments
Model fuels with different initial sulfur concentrations (15, 28, 38, and 48 ppm) were each prepared by dissolving an appropriate amount of pentanethiol in n-octane. A similar method was used to prepare a butanethiol model fuel containing 27 ppm S. The adsorption process involved adding 0.1 g of adsorbent and 20 mL of model fuel to a 50 mL conical flask and stirring this mixture at a certain temperature. A gas chromatography-flame photometric detector was used to determine the residual sulfur concentration.
The equilibrium adsorption capacity (qe) values of the sulfur compounds were determined using the equation
The equation
| Sulfur removal (%) = (1 − Ct/C0) × 100% | (2) |
was also used. In these equations,
qe,
C0,
Ct,
Ce,
V and
m represent the equilibrium adsorption capacity (mg S per g adsorbent), initial sulfur content (ppm), sulfur content (ppm) at
t min, equilibrium sulfur content (ppm), volume of the model fuel (L) and mass of the adsorbent (g), respectively.
3. Results and discussion
3.1. Characterization of the carbon materials
The morphologies of the as-prepared carbon materials were investigated using a scanning electron microscope (SEM).47–50 As shown in Fig. 1b, the bulk carbon material obtained by directly calcining waste tires was observed in SEM images to display a rough surface. When NaHCO3 was mixed with the waste tire and calcined, the obtained carbon material showed many randomly open macropores (Fig. 1c). The presence of macropores was beneficial to increase the specific surface area of the carbon material and expose more interior atoms. These properties contributed to the exposure of the adsorption sites and hence to the promotion of the adsorption performance;51 moreover, the macropores facilitated mass transfer,52 that is, the adsorbents could easily contact the sulfides. Therefore, the carbon material prepared by the “leavening” method may be more favorable for adsorptive desulfurization.
The specific surface areas and pore size distributions of the carbon materials were characterized by acquiring their N2 adsorption–desorption isotherms (Fig. 2).53 These isotherms each showed a typical II type curve with an H3 hysteresis loop, indicating the presence of micropores and mesopores in the carbon material. Based on the BET method and quenched solid-state functional theory (QSDFT), the specific surface areas and pore size distributions of the carbon materials were obtained. The specific surface area of C-1.5 (99.3 m2 g−1) was about three times that of C (32.8 m2 g−1). This case was distinguished by the addition of NaHCO3 having generated a large amount of gas (CO2) during the calcination process and the activator having reacted with carbon intermediates,46 resulting in the production of carbon material containing many pores and surface functional groups. The characterization result was consistent with the above-described SEM results. Moreover, according to the literature, a high specific surface area is beneficial for enhancing adsorption performance and macropores and mesopores contribute to mass transfer,54 so the carbon material prepared using the leavening method was expected to have the potential to display excellent adsorption performance.
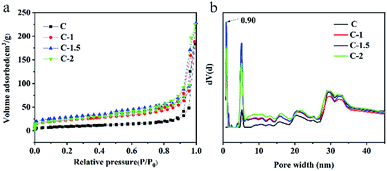 |
| Fig. 2 (a) N2 adsorption–desorption isotherms and (b) the pore size distribution of C, C-1, C-1.5, and C-2. | |
To gain further insight into the surface chemical functional groups of the carbon materials, FT-IR spectra were acquired.55–58 As shown in Fig. 3, bands corresponding to a C–OH stretching mode and bending mode were found at 3417 and 1620 cm−1.59 Additionally, a band was observed at about 1031 cm−1 and was attributed to the infrared vibration of the C–O bond.60 A band was also observed at about 1428 cm−1 and may have been due to the asymmetric bending vibration of C–H.57 These results illustrate that many oxygen atoms are incorporated in the carbon materials prepared using the leavening method.
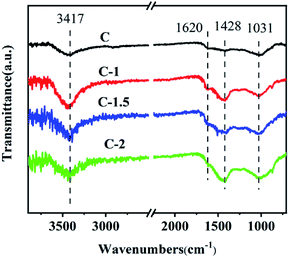 |
| Fig. 3 FT-IR spectra of C, C-1, C-1.5 and C-2. | |
Raman spectroscopy is the most direct and non-destructive technique used to characterize the structure of carbon materials. Usually, it is employed to characterize the defects, disorder and doping of carbon materials. As shown in Fig. 4, D and G bands are located at about 1340 and 1600 cm−1.61 It is generally believed that the G band represents the in-plane vibration of the sp2 carbon atom; and the D band indicates carbon defects.62,63 The ratios of the intensity of the D band to that of the G band (Id/Ig) of C, C-1, C-1.5 and C-2 were found to be 3.02, 2.47, 1.64 and 2.26, respectively. C-1.5 with the lowest value of Id/Ig indicates that it has the fewest structural defects.
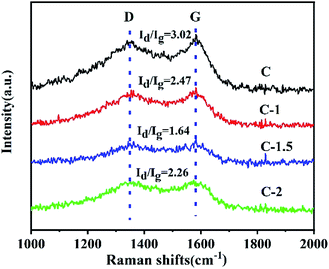 |
| Fig. 4 Raman spectra of C, C-1, C-1.5 and C-2. | |
3.2. Adsorption experiments
Next, the adsorption performances of various carbon materials, including the carbon material prepared using the NaHCO3-assisted leavening method, were determined. The results are given in Fig. 5. C-1.5 removed the most sulfur from pentanethiol, achieving a relatively high adsorption ability. In contrast, when using the same experimental conditions, C showed a relatively poor adsorption ability, with only 23.8% of the sulfur having been removed. The percentages of sulfur removed from pentanethiol by the tested carbon materials followed the trend C-1.5 (99.7%) > C-1 (98.6%) > C-2 (79.9%) > C (23.8%). The excellent performances of the porous adsorbents may be ascribed to the Lewis acid–base derived from oxygen-containing functional groups in the porous carbon materials, strong van der Waals interactions, hierarchically porous structure and high specific surface areas.
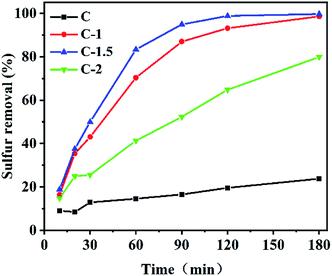 |
| Fig. 5 The percentages of sulfur removed from pentanethiol by various carbon materials. Experimental conditions: 28 ppm initial sulfur concentration, T = 25 °C, V (fuel) = 20 mL, m (adsorbent) = 0.1 g, shaker agitation speed of 150 rpm and atmospheric pressure. | |
Based on the above structural characterization and experimental results, a mechanism for the adsorption was derived. The strong Lewis acid S atoms in a pentanethiol molecule interacted with a pair of electrons from oxygen atoms in the carbon materials.31 The presence of macropores and mesopores contributed to the increased specific surface area of the carbon material, exposed more interior atoms, and facilitated mass transfer so that the adsorbents could easily contact the sulfides.
C-1.5 also removed a very high percentage (98.5%) of sulfur at 303 K, but slightly less so than the 99.7% removal at 298 K (Fig. 6). This small difference can be attributed to the exothermic nature of the adsorption process64–67
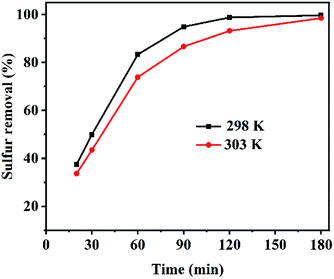 |
| Fig. 6 Effect of temperature on the adsorption of pentanethiol by C-1.5. Experimental conditions: 28 ppm initial sulfur concentration, V (fuel) = 20 mL, m (adsorbent) = 0.1 g, shaker agitation speed of 150 rpm and atmospheric pressure. | |
Concerning the industrial application prospects of C-1.5, the influence of the initial concentration of sulfur on the adsorption performance was considered.68 As shown in Fig. 7, C-1.5 displayed equilibrium adsorption capacities of 3.0, 5.6, 7.6, and 9.6 mg S per g adsorbent for the model fuels containing initial sulfur concentrations of 15, 28, 38, and 48 ppm, respectively.
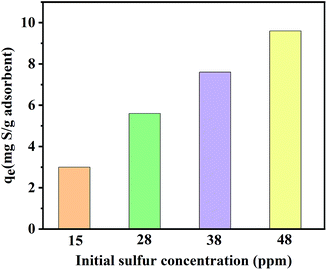 |
| Fig. 7 Effect of the initial sulfur concentration on the adsorption of pentanethiol by C-1.5. Experimental conditions: T = 25 °C, V (fuel) = 20 mL, m (adsorbent) = 0.1 g, shaker agitation speed of 150 rpm, atmospheric pressure and contact time of 180 minutes. | |
It is worth noting that the sulfur removal of the adsorbent for this concentration range was above 97%. This set of results indicates an obvious industrial application value of this material for the removal of low concentrations of sulfide.
To further explore the adsorption ability of the carbon materials for different thiols, butanethiol as well as pentanethiol were used as adsorbates, and the adsorption results are shown in Fig. 8. Most significantly, when C was used as the adsorbent, the percentages of sulfur removed from pentanethiol and butanethiol were 23.8% and 63%, respectively, values much lower than the respective 99.7% and 96.3% values when C-1.5 was used as the adsorbent. As expected, the carbon material synthesized by the leavening method exhibited efficient adsorption.
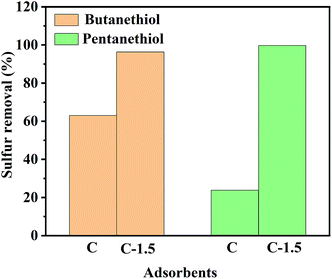 |
| Fig. 8 The sulfur removal (%) of C and C-1.5 for pentanethiol and butanethiol. Experimental conditions: 28 ppm initial sulfur concentration of pentanethiol, 27 ppm initial sulfur concentration of butanethiol, T = 25 °C, V (fuel) = 20 mL, m (adsorbent) = 0.1 g, shaker agitation speed of 150 rpm, atmospheric pressure and contact time of 180 min. | |
4. Conclusions
We have developed a “leavening” method to treat used tires. This method was used to turn waste tires into a high-added-value product. The process was found to be efficient, mild, and facile, and may be generally applied to prepare porous carbon materials from other carbon sources. Benefiting from the randomly opened macropores, high specific surface area and abundant oxygen-containing functional groups, the resulting carbon materials exhibited an outstanding adsorptive desulfurization ability, showing a removal of 99.7% of sulfur from pentanethiol, and achieving such a nearly complete desulfurization using mild conditions. The outstanding performance was attributed to macropores and mesopores facilitating mass transfer and the strong Lewis acid S atoms in the pentanethiol molecules interacting with pairs of electrons from oxygen atoms in the carbon materials. Hence, this study may provide the impetus to prepare highly efficient adsorbents for the industrial production of clean fuels.
Conflicts of interest
There are no conflicts to declare.
Acknowledgements
This work was financially supported by the National Key R&D Program of China (No. 2017YFB0306504), the National Natural Science Foundation of China (No. 21722604, 21606113, 21576122, 21878133).
Notes and references
- K. X. Lee, G. Tsilomelekis and J. A. Valla, Appl. Catal., B, 2018, 234, 130–142 CrossRef CAS.
- X. Ren, Z. Liu, L. Dong, G. Miao, N. Liao, Z. Li and J. Xiao, AIChE J., 2018, 64, 2146–2159 CrossRef CAS.
- L. Sun, T. Su, J. Xu, D. Hao, W. Liao, Y. Zhao, W. Ren, C. Deng and H. Lu, Green Chem., 2019, 21, 2629–2634 RSC.
- P. Wu, Y. Wu, L. Chen, J. He, M. Hua, F. Zhu, X. Chu, J. Xiong, M. He, W. Zhu and H. Li, Chem. Eng. J., 2020, 380, 122526 CrossRef CAS.
- W. Zhu, C. Wang, H. Li, P. Wu, S. Xun, W. Jiang, Z. Chen, Z. Zhao and H. Li, Green Chem., 2015, 17, 2464–2472 RSC.
- L. Li, Y. Lu, H. Meng and C. Li, Fuel, 2019, 253, 802–810 CrossRef CAS.
- R. Ghubayra, C. Nuttall, S. Hodgkiss, M. Craven, E. F. Kozhevnikova and I. V. Kozhevnikov, Appl. Catal., B, 2019, 253, 309–316 CrossRef CAS.
- W. Zhou, Q. Wei, Y. Zhou, M. Liu, S. Ding and Q. Yang, Appl. Catal., B, 2018, 238, 212–224 CrossRef CAS.
- R. V. Mom, J. N. Louwen, J. W. M. Frenken and I. M. N. Groot, Nat. Commun., 2019, 10, 2546 CrossRef.
- Y. Sun and R. Prins, Angew. Chem., Int. Ed., 2008, 47, 8478–8481 CrossRef CAS PubMed.
- H. Li, W. Zhu, S. Zhu, J. Xia, Y. Chang, W. Jiang, M. Zhang, Y. Zhou and H. Li, AIChE J., 2016, 62, 2087–2100 CrossRef CAS.
- T. Klimova, M. Calderon and J. Ramirez, Appl. Catal., A, 2003, 240, 29–40 CrossRef CAS.
- S. A. AL-Hammadi, A. M. Al-Amer and T. A. Saleh, Chem. Eng. J., 2018, 345, 242–251 CrossRef CAS.
- T. A. Saleh, S. A. AL-Hammadi, I. M. Abdullahi and M. Mustaqeem, J. Mol. Liq., 2018, 272, 715–721 CrossRef CAS.
- B. R. Fox, B. L. Brinich, J. L. Male, R. L. Hubbard, M. N. Siddiqui, T. A. Saleh and D. R. Tyler, Fuel, 2015, 156, 142–147 CrossRef CAS.
- X. Li, M. Hou, F. Li and H. Chua, Ind. Eng. Chem. Res., 2006, 45, 487–494 CrossRef CAS.
- M. H. Habibi, S. Tangestaninejad and B. Yadollahi, Appl. Catal., B, 2001, 33, 57–63 CrossRef CAS.
- R. Zavoianu, A. Cruceanu, O. D. Pavel, E. Angelescu, A. P. S. Dias and R. Birjega, React. Kinet., Mech. Catal., 2012, 105, 145–162 CrossRef CAS.
- D. W. Scott, D. L. Myers, H. Hill and O. Omadoko, Fuel, 2019, 242, 573–579 CrossRef CAS.
- J. He, J. Zhao and Y. Lan, J. Fuel Chem. Technol., 2009, 37, 485–488 CrossRef CAS.
- S. S. Meshkat, O. Tavakoli, A. Rashidi and M. D. Esrafili, Ecotoxicol. Environ. Saf., 2018, 165, 533–539 CrossRef CAS.
- P. Tan, D. Xue, J. Zhu, Y. Jiang, Q. He, Z. Hou, X. Liu and L. Sun, AIChE J., 2018, 64, 3786–3793 CrossRef CAS.
- P. Tan, Y. Jiang, L. Sun, X. Liu, K. AlBahily, U. Ravon and A. Vinu, J. Mater. Chem. A, 2018, 6, 23978–24012 RSC.
- J. Xiong, H. Li, L. Yang, J. Luo, Y. Chao, J. Pang and W. Zhu, AIChE J., 2017, 63, 3463–3469 CrossRef CAS.
- F. Seyedeyn-Azad, A. H. Ghandy, S. F. Aghamiri and R. Khaleghian-Moghadam, Fuel Process. Technol., 2009, 90, 1459–1463 CrossRef CAS.
- R. Barzamini, C. Falamaki and R. Mahmoudi, Fuel, 2014, 130, 46–53 CrossRef CAS.
- S. Bashkova, A. Bagreev and T. J. Bandosz, Environ. Sci. Technol., 2002, 36, 2777–2782 CrossRef CAS.
- H. Tamai, H. Nagoya and T. Shiono, J. Colloid Interface Sci., 2006, 300, 814–817 CrossRef CAS.
- S. W. Lee, W. M. A. W. Daud and M. G. Lee, J. Ind. Eng. Chem., 2010, 16, 973–977 CrossRef CAS.
- D. J. Kim and J. E. Yie, J. Colloid Interface Sci., 2005, 283, 311–315 CrossRef CAS.
- S. S. Meshkat, A. Rashidi and O. Tavakoli, J. Nat. Gas Sci. Eng., 2018, 55, 288–297 CrossRef CAS.
- Z. Moghadaszadeh, M. R. Toosi and M. R. Zardoost, J. Mol. Model., 2019, 25, 138 CrossRef.
- Y. Shi, X. Zhang and G. Liu, ACS Sustainable Chem. Eng., 2015, 3, 2237–2246 CrossRef CAS.
- Y. Shi, G. Liu, L. Wang and X. Zhang, Chem. Eng. J., 2015, 259, 771–778 CrossRef CAS.
- J. H. Kim, X. Ma, A. Zhou and C. Song, Catal. Today, 2006, 111, 74–83 CrossRef CAS.
- X. Li, H. Zhu, C. Liu, P. Yuan, Z. Lin, J. Yang, Y. Yue, Z. Bai, T. Wang and X. Bao, Ind. Eng. Chem. Res., 2018, 57, 15020–15030 CrossRef CAS.
- G. I. Danmaliki and T. A. Saleh, Chem. Eng. J., 2017, 307, 914–927 CrossRef CAS.
- T. A. Saleh and G. I. Danmaliki, J. Taiwan Inst. Chem. Eng., 2016, 60, 460–468 CrossRef CAS.
- G. I. Danmaliki, T. A. Saleh and A. A. Shamsuddeen, Chem. Eng. J., 2017, 313, 993–1003 CrossRef CAS.
- T. A. Saleh and G. I. Danmaliki, Process Saf. Environ. Prot., 2016, 102, 9–19 CrossRef CAS.
- T. A. Saleh, K. O. Sulaiman, S. A. Al-Hammadi, H. Dafalla and G. I. Danmaliki, J. Cleaner Prod., 2017, 154, 401–412 CrossRef CAS.
- T. A. Saleh, S. A. Al-Hammadi, A. Tanimu and K. Alhooshani, J. Colloid Interface Sci., 2018, 513, 779–787 CrossRef CAS PubMed.
- G. I. Danmaliki and T. A. Saleh, J. Cleaner Prod., 2016, 117, 50–55 CrossRef CAS.
- M. Hofman and R. Pietrzak, Chem. Eng. J., 2011, 170, 202–208 CrossRef CAS.
- M. Tang, J. Deng, M. Li, X. Li, H. Li, Z. Chen and Y. Wang, Green Chem., 2016, 18, 6082–6090 RSC.
- J. Deng, T. Xiong, F. Xu, M. Li, C. Han, Y. Gong, H. Wang and Y. Wang, Green Chem., 2015, 17, 4053–4060 RSC.
- C. Wang, Z. Chen, X. Yao, Y. Chao, S. Xun, J. Xiong, L. Fan, W. Zhu and H. Li, Fuel, 2018, 230, 104–112 CrossRef CAS.
- T. A. Saleh, Environ. Sci. Pollut. Res., 2015, 22, 16721–16731 CrossRef CAS.
- T. A. Saleh, J. Water Supply: Res. Technol.--AQUA, 2015, 64, 892–903 CrossRef.
- T. A. Saleh, Desalin. Water Treat., 2016, 57, 10730–10744 CrossRef CAS.
- J. Xiong, J. Luo, L. Yang, J. Pang, W. Zhu and H. Li, J. Ind. Eng. Chem., 2018, 64, 383–389 CrossRef CAS.
- X. Chen, M. Zhang, Y. Wei, H. Li, J. Liu, Q. Zhang, W. Zhu and H. Li, Inorg. Chem. Front., 2018, 5, 2478–2485 RSC.
- S. Xun, W. Jiang, T. Guo, M. He, R. Ma, M. Zhang, W. Zhu and H. Li, J. Colloid Interface Sci., 2019, 534, 239–247 CrossRef CAS.
- L. Lu, J. He, P. Wu, Y. Wu, Y. Chao, H. Li, D. Tao, L. Fan, H. Li and W. Zhu, Green Chem., 2018, 20, 4453–4460 RSC.
- L. Fan, L. Yang, X. Y. Ni, J. Han, R. Guo and C. F. Zhang, Carbon, 2016, 107, 629–637 CrossRef CAS.
- T. A. Saleh, Appl. Surf. Sci., 2011, 257, 7746–7751 CrossRef CAS.
- T. A. Saleh, J. Cleaner Prod., 2018, 172, 2123–2132 CrossRef CAS.
- T. A. Saleh, S. A. AL-Hammadi and A. M. Al-Amer, Process Saf. Environ. Prot., 2019, 121, 165–174 CrossRef CAS.
- J. Romanos, M. Beckner, T. Rash, L. Firlej, B. Kuchta, P. Yu, G. Suppes, C. Wexler and P. Pfeifer, Nanotechnology, 2012, 23, 015401 CrossRef CAS.
- C. Troca-Torrado, M. Alexandre-Franco, C. Fernandez-Gonzalez, M. Alfaro-Dominguez and V. Gomez-Serrano, Fuel Process. Technol., 2011, 92, 206–212 CrossRef CAS.
- C. Yang, H. Noguchi, K. Murata, M. Yudasaka, A. Hashimoto, S. Iijima and K. Kaneko, Adv. Mater., 2005, 17, 866–870 CrossRef CAS.
- M. Wang, Y. Lai, L. Fang, J. Li, F. Qin, K. Zhang and H. Lu, Int. J. Hydrogen Energy, 2015, 40, 16230–16237 CrossRef CAS.
- F. Pan, Z. Cao, Q. Zhao, H. Liang and J. Zhang, J. Power Sources, 2014, 272, 8–15 CrossRef CAS.
- J. Xiong, L. Yang, Y. H. Chao, J. Y. Pang, M. Zhang, W. S. Zhu and H. M. Li, ACS Sustainable Chem. Eng., 2016, 4, 4457–4464 CrossRef CAS.
- J. Xiong, L. Yang, Y. Chao, J. Pang, P. Wu, M. Zhang, W. Zhu and H. Li, Green Chem., 2016, 18, 3040–3047 RSC.
- J. Xiong, W. Zhu, H. Li, L. Yang, Y. Chao, P. Wu, S. Xun, W. Jiang, M. Zhang and H. Li, J. Mater. Chem. A, 2015, 3, 12738–12747 RSC.
- J. Luo, Y. Chao, Z. Tang, M. Hua, X. Li, Y. Wei, H. Ji, J. Xiong, W. Zhu and H. Li, Ind. Eng. Chem. Res., 2019, 58, 13303–13312 CrossRef CAS.
- J. Xiong, W. Zhu, H. Li, W. Ding, Y. Chao, P. Wu, S. Xun, M. Zhang and H. Li, Green Chem., 2015, 17, 1647–1656 RSC.
|
This journal is © The Royal Society of Chemistry 2019 |
Click here to see how this site uses Cookies. View our privacy policy here.