DOI:
10.1039/C9RA05343C
(Paper)
RSC Adv., 2019,
9, 31979-31987
Electrochemical fabrication of FeSx films with high catalytic activity for oxygen evolution
Received
12th July 2019
, Accepted 28th September 2019
First published on 9th October 2019
Abstract
Electrochemical decomposition of water to produce oxygen (O2) and hydrogen (H2) through an anodic oxygen evolution reaction (OER) and a cathodic hydrogen evolution reaction (HER) is a promising green method for sustainable energy supply. Here, we demonstrate that cauliflower-like S-doped iron microsphere films are materials that can efficiently decompose water as an electrocatalyst for the oxygen evolution reaction. FeSx films are prepared by a simple one-step electrodeposition method and directly grow on copper foam from a deep eutectic solvent, ethaline (mixture of choline chloride and ethylene glycol), as a durable and highly efficient catalyst for the OER in 1.0 M KOH. The prepared FeSx/CF, as an oxygen-evolving anode, shows remarkable catalytic performance toward the OER with a moderate Tafel slope of 105 mV dec−1, and require an overpotential of only 340 mV to drive a geometrical catalytic current density of 10 mA cm−2. In addition, this catalyst also demonstrates strong long-term electrochemical durability. This study provides a simple synthesis route for practical applications of limited transition metal nano catalysts.
1. Introduction
Over the past decades, as the world's population has grown and living standards have changed, energy has gained widespread attention as a fundamental driver.1,2 In recent years, researchers have attempted to achieve sustainable development by developing new energy sources and utilizing renewable energy sources. Solar energy, wind energy, tidal energy, geothermal energy and other energy sources are expected to play an important role in the future development of human society. Affected by regional differences and intermittent supply, however, they are difficult to use on a large scale.3 To solve the energy and environmental problems, efficient and green energy conversion and storage devices, such as fuel cells,4 metal-air batteries5 and electrolytic water,6 have recently received widespread attention. Among them, electrolytic water is an energy conversion device that converts electric energy into hydrogen energy.7 The electrolytic water reaction is carried out in an electrolytic cell. Under the action of direct current and catalyst, the water generates hydrogen and oxygen through electrochemical reaction on the electrode.8 The cathode reacts with hydrogen evolution catalyst to produce hydrogen (HER), and the anode reacts with oxygen evolution catalyst to produce oxygen (OER). The oxygen release reaction has a slow kinetics (High Overpotential). Therefore, OER can be performed in any medium, at room temperature (293 K), OER has a thermodynamic potential of 1.23 V vs. RHE.9 However, in order to accelerate the catalytic reaction, a potential higher than the thermodynamic potential must be applied, which will lead to the consumption of excess energy and reduce the conversion frequency.10–15 This extra potential (also called an overpotential) η mainly have intrinsic reactive activation barrier and some other resistances, such as solution resistance and contact resistance.16 Therefore, it is urgent to develop OER catalysts with high catalytic performance and cost performance.
In recent years, although most non-expensive HER and OER electrocatalysts are based on crystalline compounds, an increasing number of amorphous materials have become more effective electrocatalysts than their crystalline counterparts, mainly including amorphous metal sulfides (e.g., MoSx and CoSx) for HER17–20 and amorphous metal oxides (e.g., MOx, M = Fe, Co, and Ni) for OER.21–25 Although some progress has been made in the study of strategies and catalytic properties for the synthesis of amorphous catalytic materials, fine design of microstructure of new amorphous materials and a deep understanding of their catalytic mechanism are necessary, which it is hoped that the newly developed materials will be efficient for HER and OER. To this end, we prepared a copper based material, which is composed of a high conductivity carrier with high surface area and a large amount of activity. We prepared cauliflower-like FeSx microsphere films using choline chloride (ChCl)–ethylene glycol (EG)-based deep eutectic solvent (ethaline) as high-performance OER catalyst using a simple potentiostatic electrodeposition method, with no template required.17,26–28 Compared with water molecular solutions, the solvent properties of ethaline can provide a favorable chemical environment for producing nanostructured materials with high catalytic activity.29
In this paper, we report a simple and efficient method for preparing self-supporting FeSx microsphere films grown directly on copper foam (labeled as FeSx/CF), which is a highly durable and efficient catalyst for OER in alkaline media. The system without precious metal has unprecedented electrocatalytic activity of water oxidation and low potential stability under various conditions.30
2. Experimental section
2.1 Chemicals and materials
Laboratory equipment and chemicals include ethylene glycol (EG, 99%), choline chloride (ChCl, 99%), ferric chloride hexahydrate (FeCl3·6H2O, 98%), thiourea (CH4N2S, 99%), potassium hydroxide (KOH, 95%) are purchased from Aladdin Ltd. (Shanghai, China) and used as received. The deep eutectic solvent ethaline is synthesized by stirring the EG and ChCl together with a molar ratio of 1
:
2 at 353 K until a homogeneous liquid mixture is obtained.31
2.2 Electrochemical preparation of FeSx/CF films
The CHI760D electrochemical workstation is the main equipment. 400 mM FeCl3·6H2O and 10 mM thiourea are weighed and placed in 40 ml eutectic solvent and stirred at 333 K. The FeSx/CF electrodeposition is carried out in a standard three-electrode system, and s-doped iron films are prepared by one-step potentiostatic deposition. Among them, copper foam (the thickness of 1 mm, purity > 99.99%, 2.3 cm2) is used as the working electrode, silver wire and platinum column are used as the reference electrode and the counter electrode, respectively. Before each deposition, the copper foam is ultrasonically cleaned in 1% HCl for 10 min, then in anhydrous ethanol for 10 min, ished with distilled water, and finally dried. The electrodeposition is carried out at a fixed potential of −0.95 V vs. Ag wire with various charge densities. After deposition, the samples are ished with anhydrous ethanol and deionized water successively and dried with air for further characterization.
2.3 Characterization
The morphology and element composition of the deposited samples are characterized by field emission scanning electron microscopy (SEM, Nove NanoSEM 450) equipped with energy dispersive X-ray (EDS) system. X-ray diffraction (XRD) patterns are recorded on a D/max 2200 X-ray diffractometer (XRD, Cu Kα radiation). X-ray photoelectron spectroscopy (XPS) analysis was detected on a PHI 5500 X-ray photoelectron spectroscope.
2.4 Electrochemical test
Electrocatalytic experiments are performed using linear sweep voltammetry (LSV), cyclic voltammetry (CV), and electrochemical impedance spectroscopy (EIS) and chronoamperometry. All measurements are performed at ambient temperature in a CHI760D electrochemical workstation with a 50 mL electrolyte (1.0 M KOH). This experiment FeSx/CF, Hg/HgO and platinum column are respectively used as the working electrode, reference electrode and counter electrode. All the deposited samples were activated prior to any measurements as reported previously. All potentials, measured against a Hg/HgO electrode, are converted to the potential versus the reversible hydrogen electrode (RHE) according to E (vs.RHE) = E (vs. Hg/HgO) + 0.096 + 0.0591 pH. LSV is measured at the scanning rate of 5 mV s−1 in 1.0 M KOH. Electrochemical impedance spectroscopy measurements are performed at 0.75 V (vs. RHE) at the same configuration from 100
000 KHz to 0.1 Hz. Electrochemical two-layer capacitances are measured to determine the surface activity areas of the deposited products. For each sample, CV curves in the non-faraday voltage range (0.62–0.72 V vs. RHE) at various scan rates ranges from 5 to 200 mV−1. The rough stability of the electrocatalyst prepared for FeSx/CF is measured for 6000 scans by continuous cycle operation (1.0 to 1.7 V vs. RHE for the OER, 100 mV−1). The timing-current diagram is measured to assess the durability of the catalyst at 1.50 V in 1.0 M KOH solution.
3. Results and discussion
Under the condition of 293 K, the voltage of electrolysis at constant potential is −0.95 V (vs. Ag wire), and the electrodeposition times are 35 min, 45 min, 55 min and 65 min, respectively. The electrochemical activity for oxygen evolution reaction (OER) was measured by linear sweep voltammetry (LSV) with catalysts obtained at different deposition times. All electrochemical tests were carried out in a solution of 1 M KOH electrolyte, and the LSV shows a scanning rate of 5 mV s−1. After the electrodeposition of the copper foam (CF), it is obvious that the fuchsia CF turns black. Fig. 1 shows the polarization curve of electrocatalytic water oxidation of catalyst FeSx/CF prepared at different electrodeposition times. Comparison of the LSV diagram in Fig. 1 shows that catalyst FeSx/CF in 1 M KOH solution for electrocatalytic OER, produced by the catalytic current density, increased with the increase of electrodeposition time, and show the trend of initial increase followed by a decrease. When the electrodeposition time increased from 35 min to 45 min, the electrocatalytic activity for OER increased gradually. When the electrodeposition time increased from 45 min to 65 min, electrocatalytic activity for OER gradually decreased. Therefore, it was confirmed that at electrodeposition time of 45 min, the catalytic current density is the maximum at the same voltage as when the obtained catalyst conducts electrocatalytic OER in 1 M KOH solution. In other words, the electrodeposition time of 45 min is the optimal electrodeposition time.
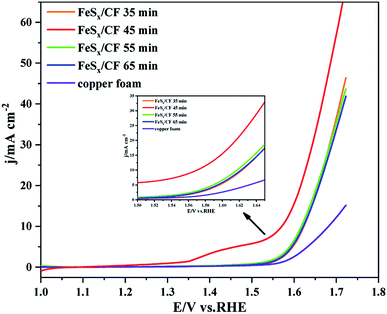 |
| Fig. 1 Electrocatalytic water oxidation polarization curves of the FeSx/CF electrodes fabricated with different electrodeposition time to create the surface FeSx species. | |
In this experiment, X-ray diffractometer (XRD) was used to analyse catalyst FeSx/CF prepared with an electrodeposition time of 45 min. Fig. 2a presents the XRD patterns of pure Fe (blue line) and FeSx (red line). Except for the strong signal from the Cu substrate, the XRD pattern for the as-prepared Fe/CF (blue line) matches well with the face-centred cubic Fe phase (PDF#06–0696). Diffraction peaks of iron and copper also exist in the samples with added thiourea (red line). This indicates that the deposit containing thiourea in solution is amorphous. In contrast, the S-doped product shows a shift of the diffraction peaks towards lower angles compared with the pure Fe sample (inset in Fig. 2a).
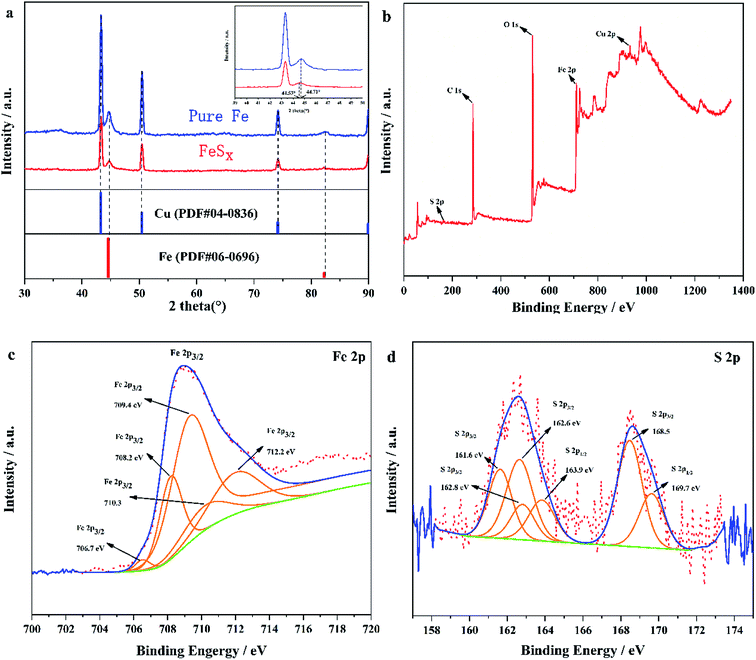 |
| Fig. 2 (a) XRD pattern of the sample only consisting of FeSx/CF. Comparison XPS surveys of FeSx/CF (b) full survey, (c) Fe 2p and (d) S 2p. | |
The chemical compositions and surface states of the as-prepared sample were further identified by XPS, as shown in Fig. 2b–d. In the XPS survey, peaks in the full XPS spectrum indicate the existence of Cu, Fe, O, and C elements. The presence of O and C comes from surface attack of the deposited sample and trace solvent residues. XPS spectra of the Fe 2p and S 2p regions of the as-deposited sample are shown in Fig. 2c and d. The Fe 2p levels are split into 2p3/2 and 2p1/2 doublets owing to the spin–orbit coupling32–34 (we only analyze Fe 2p3/2 in Fig. 2c). As seen from the XPS image, Fe 2p3/2 identified five splitting peaks, and the corresponding binding energies and combined states were 706.7 eV (FeS2),35 708.2 eV (Fe3O4),36 709.4 eV (FeO),37 710.3 eV (FeS),38 and 712.2 eV (FeS),38 respectively. The two peaks at 708.2 eV and 709.4 eV were attributed to the oxidation of the sample surface. As oxidation is easy when FeS2 encounters oxygen, and it can be seen from the XPS spectrum of S that SO42− ions exist at the binding energy 168.5 eV (Fig. 2d). In the iron picture, the binding energy 712.2 eV is attributed to the partial oxidation of FeS2 to FeSO4.38 In the S 2p region (Fig. 2d), the two groups of peak at 161.6 eV, 162.8 eV; and 162.6 eV, 163.9 eV belong to S 2p3/2 and S 2p1/2 respectively, which are related to the binding energy of S2− and S22− ligands. The other peak at 168.3 eV is the binding energy of Fe–O–S, which is caused by surface oxidation in air.39,40 Thus, it suggests that S doped enter into Fe. These results indicate that the FeSx obtained by electrodeposition has poor crystal form and may even be amorphous. It also means that the FeSx films in FeSx/CF may consists of small clusters in which Fe is in the FeS and FeS2 states. The ratio of the atomic radius of Fe (atomic radius 117 pm) and S (atomic radius 104 pm)41,42 is greater than 0.59, which further proves that S is doped into the lattice of Fe to form interstitial compounds. The interstitial compound can be called FeSx.
Fig. 3a shows that the whole surface of the CF is bright and smooth. Fig. 3b shows that the whole surface of the CF is uniformly covered with cauliflower-like FeSx microsphere films (inset in Fig. 3b). The associated high magnification SEM image (Fig. 3c and d) clearly shows that the cauliflower-like FeSx microsphere films is made up of many nanosheets. Meanwhile, samples of the catalyst FeSx/CF with electrodeposition time of 45 min were characterized by element mapping analysis in SEM. In the element distribution diagrams of SEM, Fe and S are shown in Fig. 3c–e. It can be seen from Fig. 3d and e that Fe and S elements are evenly distributed on the entire sample surface.
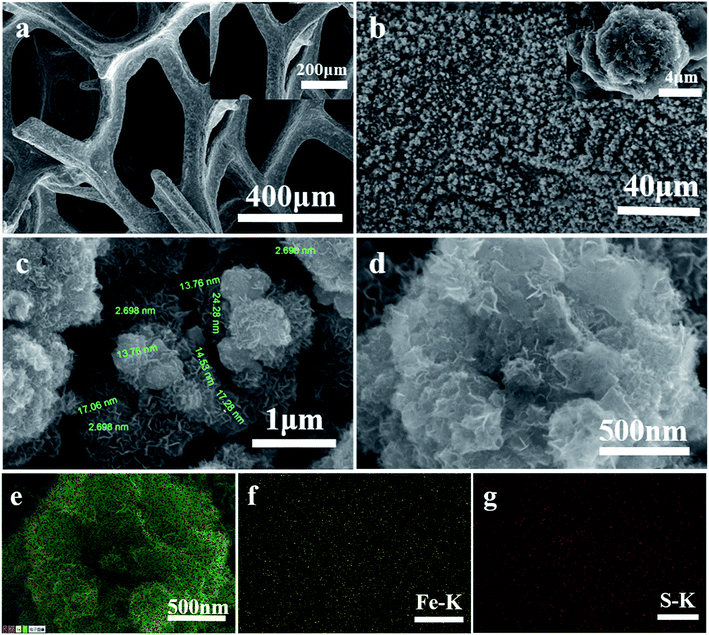 |
| Fig. 3 (a) SEM image of copper foam surface. (b–d) The associated high magnification SEM image clearly shows that cauliflower-like FeSx microsphere films is made up of many nanosheets. (e–g) The corresponding element mapping images of Fe and S, the scale bars are all 500 nm. | |
The electrocatalytic activity of the prepared FeSx/CF OER was assessed in 1.0 M KOH by steady-state LSV with a scan rate 5 mV s−1. For comparison with the FeSx/CF catalyst, pure Fe was deposited onto CF electrode by measurement of electrochemical properties. Fig. 4a shows the polarization curve compensation of these catalysts without iR. As expected, FeSx/CF shows excellent OER activity, whereas the deposited Fe/CF exhibits poor OER activity and greater starting potential. The FeSx/CF enables OER with high catalytic activity and relatively low starting potential (1.57 V). When the current density reaches 10 mA cm−2, the overpotential of the sample in 1 M KOH solution was 340 mV. This overpotential compares favourably with the behaviour of Cu-based OER electrocatalysts, except FeSx/CF composites such as Fe(OH)3
:
Cu(OH)2/CF (∼365 mV),43 Co–CoO@3DHPG (∼410 mV),44 FeNx/carbon (∼320 mV),45 NiS/NC (∼371 mV),46 and 2D CuO nanosheet bundles (∼350 mV),47etc. A more detailed comparison is given in Table 1. Fig. 4b shows the Tafel slopes for FeSx/CF and deposited Fe/CF. The Tafel plots are fitted with the formula: η = b
log
j + a (where j is the current density and b is the Tafel slope). The Tafel slope of catalyst FeSx/CF (105 mV dec−1) is higher than that of deposited Fe/CF (167 mV dec−1), implying more favorable catalytic kinetics on FeSx/CF.
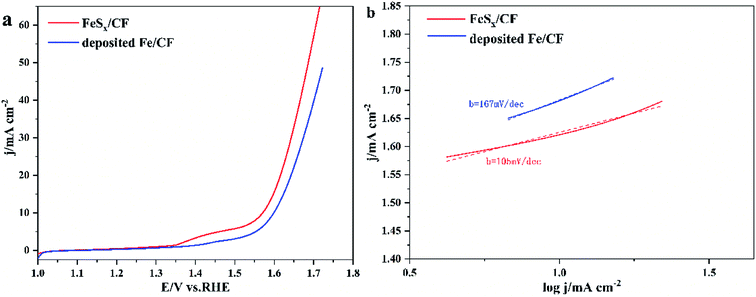 |
| Fig. 4 (a) The polarization curves of FeSx/CF and deposited Fe/CF with scanning rate of 5 mV s−1. (b) Corresponding Tafel plots with linear fitting. | |
Table 1 Comparison of OER performance for FeSx/CF and deposited Fe/CF with other nonnoble-metal OER catalysts under alkaline conditions
Catalyst |
j (mA cm−2) |
η (mV) |
Electrolyte |
Ref. |
FeSx/CF |
10 |
340 |
1 M KOH |
This work |
Deposited Fe/CF |
10 |
369 |
1 M KOH |
This work |
Fe(OH)3 : Cu(OH)2/CF |
10 |
365 |
1 M KOH |
43
|
Co–CoO@3DHPG |
10 |
410 |
1 M KOH |
44
|
FeNx/carbon |
10 |
360 |
1 M KOH |
45
|
NiS/NC |
10 |
371 |
1 M KOH |
46
|
2D CuO nanosheet bundles |
10 |
350 |
1 M KOH |
47
|
Electrochemical impedance spectroscopy (EIS) data (Fig. 5a) reveal that FeSx/CF, with a much smaller semicircle radius compared with deposited Fe/CF, manifests the high conductivity of the as-prepared electrode, and lower polarization resistance (Rct). Accordingly, FeSx/CF has faster charge transfer and OER kinetics. These result show that the electrode dynamics mainly controls the charge transfer process, and the electrochemical system is approximated by the modified Randles circuit, as shown in the inset of Fig. 4a. The potential dependencies of the obtained data include solution resistance (Rs), charge-transfer resistance (Rct), and constant-phase element related to the double-layer capacitance (CPE).48
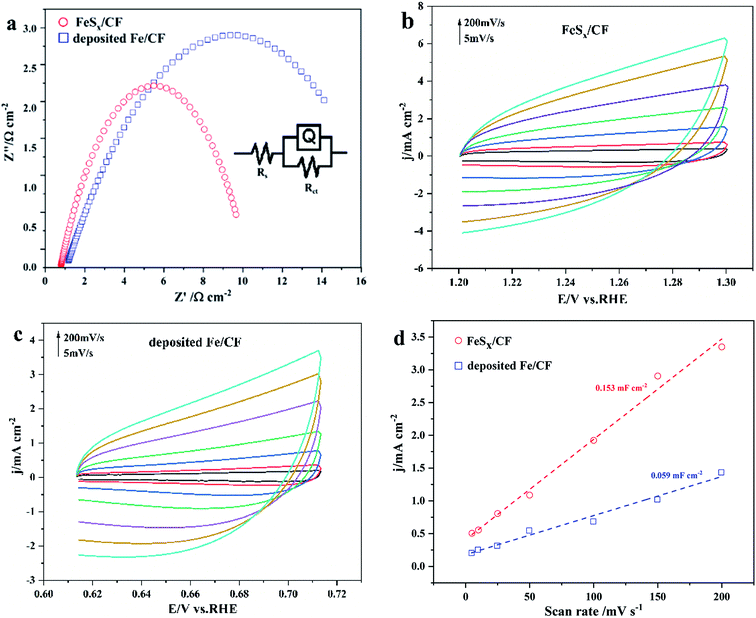 |
| Fig. 5 (a) Nyquist plots of FeSx/CF and deposited Fe/CF at 0.75 V (vs. RHE). (b and c) CV curves of FeSx/CF and deposited Fe/CF catalyst in non-faraday voltage range (0.62–0.72 V vs. RHE). (d) The relationship between charging current density difference (ja − jc) and scanning rate is shown in the figure. The slope in the figure is twice that of Cdl. | |
The contribution of S-doping to the catalytic activity of these electrodes was evaluated, considering that the electrocatalytic activity for OER is highly dependent on their electrochemically active surface area (ECSA) and reaction active sites. CVs of catalyst FeSx/CF and deposited Fe/CF samples were recorded at different scanning rates from 5 to 200 mV s−1 in the faradaic silent region (Fig. 5b and c). From the measured capacitances (Fig. 5d), the Cdl of porous FeSx/CF and deposited Fe/CF are 0.153 mF cm−2 and 0.059 mF cm−2, respectively, suggesting a much larger ECSA of the FeSx/CF electrode, which is consistent with the LSV and EIS results. The findings suggest that the large ECSA generated by the structural characteristics of FeSx/CF plays a crucial role in its high catalytic activity. The rough nanosheet structure not only leads to more effective exposure of catalytic activity sites, but also promotes rapid electron transfer and ion diffusion, thereby improving OER catalytic activity.
In order to obtain the stability of FeSx/CF, CV scans were performed at 1.0 and 1.7 V vs. RHE for 6000 consecutive cycles with a scanning rate of 100 mV s−1. The FeSx/CF catalyst remained stable after thousands of cycles (Fig. 6a). To further prove stability, Fig. 6b shows a multistep chronopotentiometric curve for FeSx/CF with current density ranging from 10 to 60 mA cm−2 (5 mA cm−2 per 500 s), and the deposited Fe/CF with current density ranging from 10 to 50 mA cm−2 (5 mA cm−2 per 500 s). In the range of 1.60–1.74 V, all steps remained unchanged for 500 s, which means that the FeSx/CF electrode has higher conductivity, better mechanical strength, and better mass transfer than the Fe/CF electrode. For long-term electrolysis at a constant current density of 10 mA cm−2 (Fig. 6c), the FeSx/CF exhibits strong electrochemical stability, maintaining its original OER activity for at least 24 h with negligible degradation. These results show that the FeSx/CF electrode has a great potential in practical alkaline water electrolysis applications.
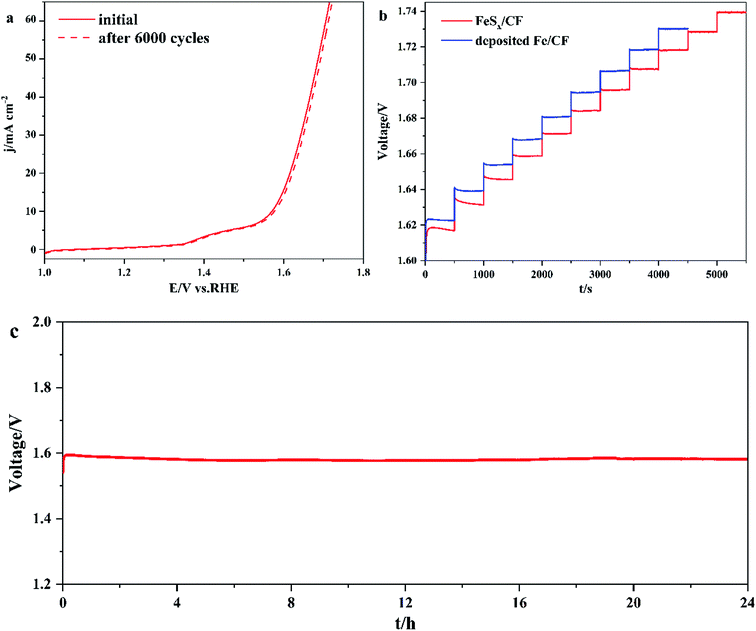 |
| Fig. 6 (a) At the scanning rate of 100 mV s−1, the polarization curve of FeSx/CF before and after 6000 voltage sweeps between 1.0 V and 1.7 V vs. RHE. (b) Multistep chronopotentiometric curve for FeSx/CF with current density ranging from 10 to 60 mA cm−2, and the deposited Fe/CF with current density ranging from 10 to 50 mA cm−2, without iR compensation. (c) Chronopotential curve recorded at constant current density of 10 mA cm−2. | |
4. Conclusion
In summary, FeSx films is successfully prepared on copper foam by a simple electrodeposition method. The as prepared FeSx/CF catalyst shows excellent electrocatalytic activity, durability and low overpotential. It is expected that FeSx/CF hold great promise for developing a cheap electrode material for electrocatalytic OER. Notably, this electrode material has great potential for large-scale and low-cost oxygen production through water decomposition. Besides, the proposed simple electrodeposition method can use to prepare other transition metal based nanomaterials for application of electrochemical oxygen generation.
Conflicts of interest
There are no conflicts to declare.
Acknowledgements
Authors gratefully acknowledge the financial supports of the National Natural Science Foundation of China (Project No. 51874154); the Key Project of Yunnan Province Applied Basic Research Plan of China (Project No. 2014FA024); the Specialized Research Fund for the Doctoral Program of the Ministry of Education of China (Project No. 20125314110011).
References
- B. Gates, The energy research imperative, Science, 2011, 334(6058), 877 CrossRef CAS.
- S. Chu and A. Majumdar, Opportunities and challenges for a sustainable energy future, Nature, 2012, 488(7411), 294–303 CrossRef CAS.
- Y.-G. Guo, J.-S. Hu and L.-J. Wan, Nanostructured Materials for Electrochemical Energy Conversion and Storage Devices, Adv. Mater., 2008, 20(15), 2878–2887 CrossRef CAS.
- O. Z. Sharaf and M. F. Orhan, An overview of fuel cell technology: Fundamentals and applications, Renewable Sustainable Energy Rev., 2014, 32, 810–853 CrossRef CAS.
- K. F. Blurton and A. F. Sammells, Metal/air batteries: their status and potential—a review, J. Power Sources, 1979, 4(4), 263–279 CrossRef CAS.
- M. D. Symes and L. Cronin, Decoupling hydrogen and oxygen evolution during electrolytic water splitting using an electron-coupled-proton buffer, Nat. Chem., 2013, 5(5), 403 CrossRef CAS.
-
M. Tanaka, Y. Nishiki, N. Hayamizu and N. Sakurai, Apparatus for producing electrolytic water, US Pat., 6,235,186, 2001-5-22.
- B. Conway, Electrochemical proton transfer and cathodic hydrogen evolution, Sci. Prog., 1987,(1933-), 479–509 CAS.
- J.-L. Tao and Y.-Q. Xiong, Hydrogen production from the decomposition of ethanol aqueous solution using glow discharge plasma electrolysis, Acta Phys.-Chim. Sin., 2013, 29(1), 205–211 CAS.
- X. Sun, Y. Guo, C. Wu and Y. Xie, The hydric effect in inorganic nanomaterials for nanoelectronics and energy applications, Adv. Mater., 2015, 27(26), 3850–3867 CrossRef CAS.
- W. Lu, T. Liu, L. Xie, C. Tang, D. Liu, S. Hao, F. Qu, G. Du, Y. Ma and A. M. Asiri, In Situ Derived Co B Nanoarray: A High-Efficiency and Durable 3D Bifunctional Electrocatalyst for Overall Alkaline Water Splitting, Small, 2017, 13(32), 1700805 CrossRef.
- W. Zhu, R. Zhang, F. Qu, A. M. Asiri and X. Sun, Design and application of foams for electrocatalysis, ChemCatChem, 2017, 9(10), 1721–1743 CrossRef CAS.
- X. Ren, R. Ge, Y. Zhang, D. Liu, D. Wu, X. Sun, B. Du and Q. Wei, Cobalt–borate nanowire array as a high-performance catalyst for oxygen evolution reaction in near-neutral media, J. Mater. Chem. A, 2017, 5(16), 7291–7294 RSC.
- Q. Liu, L. Xie, Z. Liu, G. Du, A. M. Asiri and X. Sun, A Zn-doped Ni3S2 nanosheet array as a high-performance electrochemical water oxidation catalyst in alkaline solution, Chem. Commun., 2017, 53(92), 12446–12449 RSC.
- R. Xu, R. Wu, Y. Shi, J. Zhang and B. Zhang, Ni3Se2 nanoforest/Ni foam as a hydrophilic, metallic, and self-supported bifunctional electrocatalyst for both H2 and O2 generations, Nano Energy, 2016, 24, 103–110 CrossRef CAS.
- L. Han, S. Dong and E. Wang, Transition-Metal (Co, Ni, and Fe)-Based Electrocatalysts for the Water Oxidation Reaction, Adv. Mater., 2016, 28(42), 9266–9291 CrossRef CAS.
- M. Gao, C. Yang, Q. Zhang, Y. Yu, Y. Hua, Y. Li and P. Dong, Electrochemical fabrication of porous Ni-Cu alloy nanosheets with high catalytic activity for hydrogen evolution, Electrochim. Acta, 2016, 215, 609–616 CrossRef CAS.
- Y. Liu, Q. Li, R. Si, G. D. Li, W. Li, D. P. Liu, D. Wang, L. Sun, Y. Zhang and X. Zou, Coupling Sub-Nanometric Copper Clusters with Quasi-Amorphous Cobalt Sulfide Yields Efficient and Robust Electrocatalysts for Water Splitting Reaction, Adv. Mater., 2017, 29(13), 1606200 CrossRef.
- P. D. Tran, T. V. Tran, M. Orio, S. Torelli, Q. D. Truong, K. Nayuki, Y. Sasaki, S. Y. Chiam, R. Yi and I. Honma, Coordination polymer structure and revisited hydrogen evolution catalytic mechanism for amorphous molybdenum sulfide, Nat. Mater., 2016, 15(6), 640 CrossRef CAS.
- J. Staszak-Jirkovský, C. D. Malliakas, P. P. Lopes, N. Danilovic, S. S. Kota, K.-C. Chang, B. Genorio, D. Strmcnik, V. R. Stamenkovic and M. G. Kanatzidis, Design of active and stable Co–Mo–Sx chalcogels as pH-universal catalysts for the hydrogen evolution reaction, Nat. Mater., 2016, 15(2), 197 CrossRef.
- C. L. Farrow, D. K. Bediako, Y. Surendranath, D. G. Nocera and S. J. Billinge, Intermediate-range structure of self-assembled cobalt-based oxygen-evolving catalyst, J. Am. Chem. Soc., 2013, 135(17), 6403–6406 CrossRef CAS.
- X. L. Hu, S. Piccinin, A. Laio and S. Fabris, Atomistic structure of cobalt-phosphate nanoparticles for catalytic water oxidation, ACS Nano, 2012, 6(12), 10497–10504 CrossRef CAS.
- D. A. Salvatore, K. E. Dettelbach, J. R. Hudkins and C. P. Berlinguette, Near-infrared–driven decomposition of metal precursors yields amorphous electrocatalytic films, Sci. Adv., 2015, 1(2), e1400215 CrossRef.
- R. D. Smith, M. S. Prévot, R. D. Fagan, Z. Zhang, P. A. Sedach, M. K. J. Siu, S. Trudel and C. P. Berlinguette, Photochemical route for accessing amorphous metal oxide materials for water oxidation catalysis, Science, 2013, 340(6128), 60–63 CrossRef CAS.
- J. Zhu, F. Lambert, C. Policar, F. Mavré and B. Limoges, Fast magnetically driven electrodeposition of amorphous metal oxide water oxidation catalysts from carbon-coated metallic nanoparticles, J. Mater. Chem. A, 2015, 3(31), 16190–16197 RSC.
- M. Gao, C. Yang, Q. Zhang, J. Zeng, X. Li, Y. Hua, C. Xu and P. Dong, Facile electrochemical preparation of self-supported porous Ni–Mo alloy microsphere films as efficient bifunctional electrocatalysts for water splitting, J. Mater. Chem. A, 2017, 5(12), 5797–5805 RSC.
- C. Yang, Q. Zhang and A. P. Abbott, Facile fabrication of nickel nanostructures on a copper-based template via a galvanic replacement reaction in a deep eutectic solvent, Electrochem. Commun., 2016, 70, 60–64 CrossRef CAS.
- J. Zeng, M. Gao, Q. Zhang, C. Yang, X. Li, W. Yang, Y. Hua, C. Xu and Y. Li, Facile electrodeposition of cauliflower-like S-doped nickel microsphere films as highly active catalysts for electrochemical hydrogen evolution, J. Mater. Chem. A, 2017, 5(29), 15056–15064 RSC.
- D. V. Wagle, H. Zhao and G. A. Baker, Deep eutectic solvents: sustainable media for nanoscale and functional materials, Acc. Chem. Res., 2014, 47(8), 2299–2308 CrossRef CAS.
- T. N. Huan, G. Rousse, S. Zanna, I. T. Lucas, X. Xu, N. Menguy, V. Mougel and M. Fontecave, A dendritic nanostructured copper oxide electrocatalyst for the oxygen evolution reaction, Angew. Chem., Int. Ed., 2017, 56(17), 4792–4796 CrossRef CAS.
- A. P. Abbott, G. Capper, D. L. Davies, K. J. McKenzie and S. U. Obi, Solubility of metal oxides in deep eutectic solvents based on choline chloride, J. Chem. Eng. Data, 2006, 51(4), 1280–1282 CrossRef CAS.
- N. Cheng, Q. Liu, A. M. Asiri, W. Xing and X. Sun, A Fe-doped Ni3S2 particle film as a high-efficiency robust oxygen evolution electrode with very high current density, J. Mater. Chem. A, 2015, 3(46), 23207–23212 RSC.
- M. Sun, X.-R. Ru and L.-F. Zhai, In-situ fabrication of supported iron oxides from synthetic acid mine drainage: high catalytic activities and good stabilities towards electro-Fenton reaction, Appl. Catal., B, 2015, 165, 103–110 CrossRef CAS.
- Y. Qiu, J. Yu, W. Wu, J. Yin and X. Bai, Fe–N/C nanofiber electrocatalysts with improved activity and stability for oxygen reduction in alkaline and acid solutions, J. Solid State Electrochem., 2013, 17(3), 565–573 CrossRef CAS.
- S. Nakamura and A. Yamamoto, Electrodeposition of pyrite (FeS2) thin films for photovoltaic cells, Sol. Energy Mater. Sol. Cells, 2001, 65(1–4), 79–85 CrossRef CAS.
- D. Wilson and M. Langell, XPS analysis of oleylamine/oleic acid capped Fe3O4 nanoparticles as a function of temperature, Appl. Surf. Sci., 2014, 303, 6–13 CrossRef CAS.
- K. Prince, M. Matteucci, K. Kuepper, S. Chiuzbaian, S. Bartkowski and M. Neumann, Core-level spectroscopic study of FeO and FeS2, Phys. Rev. B, 2005, 71(8), 085102 CrossRef.
- M. Descostes, F. Mercier, N. Thromat, C. Beaucaire and M. Gautier-Soyer, Use of XPS in the determination of chemical environment and oxidation state of iron and sulfur samples: constitution of a data basis in binding energies for Fe and S reference compounds and applications to the evidence of surface species of an oxidized pyrite in a carbonate medium, Appl. Surf. Sci., 2000, 165(4), 288–302 CrossRef CAS.
- H. Khani and D. O. Wipf, Iron oxide nanosheets and pulse-electrodeposited Ni–Co–S nanoflake arrays for high-performance charge storage, ACS Appl. Mater. Interfaces, 2017, 9(8), 6967–6978 CrossRef CAS.
- N. Yang, C. Tang, K. Wang, G. Du, A. M. Asiri and X. Sun, Iron-doped nickel disulfide nanoarray: A highly efficient and stable electrocatalyst for water splitting, Nano Res., 2016, 9(11), 3346–3354 CrossRef CAS.
-
D. K. Lonsdale, International tables for X-ray crystallography, Kynoch Press, 1968 Search PubMed.
- O. Senkov and D. Miracle, Effect of the atomic size distribution on glass forming ability of amorphous metallic alloys, Mater. Res. Bull., 2001, 36(12), 2183–2198 CrossRef CAS.
- C.-C. Hou, C.-J. Wang, Q.-Q. Chen, X.-J. Lv, W.-F. Fu and Y. Chen, Rapid synthesis of ultralong Fe(OH)3
:
Cu(OH)2 core–shell nanowires self-supported on copper foam as a highly efficient 3D electrode for water oxidation, Chem. Commun., 2016, 52(100), 14470–14473 RSC.
- N. Ullah, W. Zhao, X. Lu, C. J. Oluigbo, S. A. Shah, M. Zhang, J. Xie and Y. Xu, In situ growth of M-MO (M = Ni, Co) in 3D graphene as a competent bifunctional electrocatalyst for OER and HER, Electrochim. Acta, 2019, 298, 163–171 CrossRef CAS.
- J. Ding, P. Wang, S. Ji, H. Wang, V. Linkov and R. Wang, N-doped mesoporous FeNx/carbon as ORR and OER bifunctional electrocatalyst for rechargeable zinc-air batteries, Electrochim. Acta, 2019, 296, 653–661 CrossRef CAS.
- J. Ding, S. Ji, H. Wang, H. Gai, F. Liu, V. Linkov and R. Wang, Mesoporous nickel-sulfide/nickel/N-doped carbon as HER and OER bifunctional electrocatalyst for water electrolysis, Int. J. Hydrogen Energy, 2019, 44(5), 2832–2840 CrossRef CAS.
- S. M. Pawar, B. S. Pawar, B. Hou, J. Kim, A. T. A. Ahmed, H. S. Chavan, Y. Jo, S. Cho, A. I. Inamdar and J. L. Gunjakar, Self-assembled two-dimensional copper oxide nanosheet bundles as an efficient oxygen evolution reaction (OER) electrocatalyst for water splitting applications, J. Mater. Chem. A, 2017, 5(25), 12747–12751 RSC.
- C. C. McCrory, S. Jung, J. C. Peters and T. F. Jaramillo, Benchmarking heterogeneous electrocatalysts for the oxygen evolution reaction, J. Am. Chem. Soc., 2013, 135(45), 16977–16987 CrossRef CAS.
|
This journal is © The Royal Society of Chemistry 2019 |
Click here to see how this site uses Cookies. View our privacy policy here.