DOI:
10.1039/C9RA05045K
(Paper)
RSC Adv., 2019,
9, 21587-21590
Association of liquid-assisted grinding with aging accelerates the inherently slow slipping-on of a dibenzo-24-crown-8 over the N-hydroxysuccinimide ester of an ammonium-containing thread†
Received
3rd July 2019
, Accepted 5th July 2019
First published on 11th July 2019
Abstract
Solvent-free and solvent-less slipping-on of the dibenzo-24-crown-8 (DB24C8) over the N-hydroxysuccinimide end of an ammonium-containing thread has been studied and compared to the same reaction operated in solution. Slippage proved to be possible in solvent-free conditions, but the fastest slippage was obtained under heating when preliminary Liquid-Assisted Grinding (LAG) conditions were applied to the reactants followed by aging under an atmosphere of acetonitrile.
The recently awarded 2016 Nobel Prize in chemistry1 has put a light on molecular machines.2 Some of these machines benefit from their interlocked molecular architecture3 so that the relative displacement of one interlaced element among others becomes possible and controllable. Hence, the straightforward synthesis of interlocked molecules is appealing in order to access novel molecular machines. Using the slippage strategy,4 we recently reported the preparation of an insulated and storable, albeit activated, N-hydroxysuccinimide (NHS) ester-containing [2]rotaxane building block (Scheme 1 and entry 1 of Table 1).5 This compound is a valuable activated building block for post-interlocking elongation of the encircled axle using bulky amino compounds.6 As the mechanism of such aminolysis reactions preserves the mechanical bond, it allowed the efficient and straightforward preparation of more sophisticated interlocked compounds such as [2] and [3]rotaxane molecular shuttles.5,6 Improving the access to the NHS ester-containing [2]rotaxane building block 2 is therefore of real interest. This is particularly justified since in acetonitrile solution, the slipping-on of the DB24C8 (3 equiv.) over the NHS extremity of an ammonium-containing thread (at a concentration of 3 × 10−2 M) is very slow and necessitates heating (13 days and 333 K, respectively). In this paper, we wondered if this slipping-on process could be possible, nay improved, by drastically reducing the amount of solvent. Since solvent-free/solvent-less conditions are highly prone to induce mass transfer limitations, utilisation of ball-milling was envisaged. Indeed it was previously shown that ball-milling could improve the speed of inherently slow reactions.7 A few examples of solvent-free/solvent-less synthesis of rotaxanes have been reported to date,8 and to the best of our knowledge, only three of these examples are related to slippage process through a co-melting process9 or an immediate solvent evaporation method.10 Herein, different experimental procedures were considered to yield the activated [2]rotaxane 2: solvent-free grinding,11 Liquid-Assisted Grinding (LAG),12 and aging by heating with or without an acetonitrile atmosphere.13 LAG is defined as the use of small amounts of a non-reactive liquid during grinding.14 It has been shown by us and by other research groups to have a considerable effect on the course of reactions run under mechanical forces.15 Besides, aging is the action of letting the reaction take place in the absence of any mechanical agitation. This reactivity is based on the inherent mobility of molecules and can be accelerated by the presence of vapours and/or a slight heating in the presence, or not, of a catalyst.16 Both LAG and aging are processes that are using generally much lower quantities of solvents compared to traditional solvent-based syntheses, and therefore are generally qualified as “solvent-less” processes. The results of these slipping-on experiments are shown in Fig. 1 and Table 1 and compared to that realized anteriorly in acetonitrile.
 |
| Scheme 1 Slippage process of the NHS ester-containing molecular axle 1 by the DB24C8. | |
Table 1 Experimental conditions relative to the slippage of thread 1
Entry |
Procedure |
Preliminary grinding |
LAG |
Aging under an atm. of |
T (K) |
t (h) |
Conversion in 2 (%) |
1 |
In solution |
No |
No |
— |
333 |
312 |
72 |
2 |
Solvent-free |
No |
No |
— |
298 |
505 |
3 |
3 |
Solvent-less |
Yes |
Yes |
— |
298 |
1 |
5 |
4 |
Solvent-free |
No |
No |
Ar |
333 |
504 |
5 |
5 |
Solvent-free |
Yes |
No |
Ar |
333 |
504 |
10 |
6 |
Solvent-less |
Yes |
Yes |
Ar |
333 |
504 |
10 |
7 |
Solvent-less |
No |
No |
MeCN |
333 |
72 |
58 |
8 |
Solvent-less |
Yes |
Yes |
MeCN |
333 |
149 |
89 |
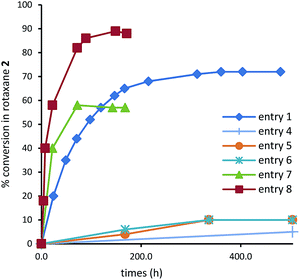 |
| Fig. 1 Kinetics comparison of the slipping-on relative to the formation of rotaxane 2 from 1. Corresponding experimental procedures are given in Table 1. Conversion ratio of rotaxane 2 was calculated from subsequent 1H NMR analysis of the mixture. For sake of clarity, curves corresponding to entries 2 and 3 were omitted. | |
In acetonitrile solution at 333 K,17 the reaction proceeded slowly (312 h – 13 days – to reach the equilibrium, corresponding to a conversion of 72%) because of the bulkiness of the NHS ester with respect to the size of the inner diameter of the DB24C8 (entry 1, Table 1 and Fig. 1). The slippage was then attempted at room temperature under solvent-free conditions: after 1 equiv. of thread 1 have been mixed with a spatula for few minutes with 3 equiv. of DB24C8 then let reacting without any mixing under ambient conditions for 505 hours (21 days) (entry 2, Table 1), only 3% of [2]rotaxane 2 was obtained! By comparison, if Liquid-Assisted Grinding (LAG) was applied to the same ratio of reactants with acetonitrile as the liquid grinding assistant (0.2 μL mg−1) (entry 3, Table 1), a slightly larger amount of [2]rotaxane 2 was obtained (5%), however in a much shorter time (1 h).
This result could be explained by the reduction of the particle size induced by ball-milling, while the small amount of acetonitrile might have helped in the homogenization of the reaction mixture. Although favouring the reaction, reaching complete conversion by using a ball-mill would imply very long milling time. Therefore, ball-milling was used thereafter for preliminary grinding as a plus to homogenize and most probably to reduce the particle size of the reactants mixture, while other approaches were envisaged to reach complete conversion.
Heating the mixture of solids was first considered to evaluate the contribution of the temperature factor on the efficacy of the slippage reaction in the absence of solvent. We thus reproduced the experimental conditions of entry 2 albeit at 333 K under an Ar atmosphere (entry 4, Table 1 and Fig. 1).18 No significant improvement was noticed for the conversion yield in [2]rotaxane 2 nor for the time to reach the equilibrium of the reaction. Adding to this experiment a preliminary 1 h grinding period in the vibrating ball-mill afforded a slight improvement probably due to the more intimate mixing of the reactants (entry 5, Table 1 and Fig. 1). The same ratio of rotaxane 2 was observed if 0.2 μL of acetonitrile (per mg of reactants) is added to the ball-mill as a liquid-grinding assistant (entry 6, Table 1, Fig. 1). For all these solvent-free/solvent-less experiments that were carried out at 333 K, the time to reach the equilibrium of the slippage reaction proved to be much longer than that realized in solution (entries 1 and 4–6, Fig. 1). However, it became lower if the solid mixture was heated at 333 K under an acetonitrile atmosphere (entries 7–8, Table 1, Fig. 1). This procedure, called “aging”, has been recently described by other groups as a valuable, low-energy demanding and solvent-less alternative to classical synthesis in solution.19 In the absence of preliminary grinding, 58% of rotaxane 2 could be obtained after 72 h under an acetonitrile atmosphere (entry 7, Table 1). Even though the equilibration time was lowered, the yield of rotaxane 2 seemed capped, probably due to the lack of homogenization of the solids mixture. Preceding the heating by a liquid-assisted grinding solved this problem (entry 8, Table 1). In this case, the ratio of rotaxane 2 increased to 89% and the time to reach the equilibrium was the fastest (about 149 h).20 By directly comparing with the reaction operated in solution (entry 1), the ratio of rotaxane 2 was higher (89% vs. 72%) and most of all, the time to reach the equilibrium was more than twice lower (149 h vs. 312 h).
In conclusion, slippage process of thread 1 by the DB24C8 was proved possible in the absence of solvent although producing [2]rotaxane 2 in very low yields (3–10%). In the absence of any acetonitrile atmosphere, the rate of the rotaxane formation was much slower than in solution and preliminary grinding did not afford significant improvement. On the opposite, the ratio of rotaxane as well as the time to reach the equilibrium of its formation could be tremendously enhanced when combining preliminary grinding with heating at 333 K under an acetonitrile atmosphere. Noteworthy, the aging-based solvent-less slippage, which occurred in the presence of a 216 times lesser quantity of acetonitrile than in solution, resulted in a time to reach the equilibrium more than twice shorter and an improved yield ratio of 24%. It demonstrates that combining ball-milling with accelerated aging is an easy and efficient protocol that should be envisaged to facilitate the inherently slow formation of other sophisticated interlocked molecules.
Conflicts of interest
There are no conflicts to declare.
Notes and references
- The 2016 Nobel Prize in chemistry was awarded to J.-P. Sauvage, J. F. Stoddart and B. L. Feringa for the design and synthesis of molecular machines, see:
(a) J.-P. Sauvage, Angew. Chem., Int. Ed., 2017, 56, 11080–11093 CrossRef CAS;
(b) J. F. Stoddart, Angew. Chem., Int. Ed., 2017, 56, 11094–11125 CrossRef CAS;
(c) B. L. Feringa, Angew. Chem., Int. Ed., 2017, 56, 11060–11078 CrossRef CAS.
-
(a) E. R. Kay, D. A. Leigh and F. Zerbetto, Angew. Chem., Int. Ed., 2007, 46, 72–191 CrossRef CAS;
(b) J. –P. Sauvage, J. –P. Collin, S. Durot, J. Frey, V. Heitz, A. Sour and C. Tock, C. R. Chim., 2010, 13, 315–328 CrossRef CAS;
(c) A. Coskun, M. Banaszak, R. D. Astumian, J. F. Stoddart and B. A. Grzybowski, Chem. Soc. Rev., 2012, 41, 19–30 RSC;
(d) C. Pezzato, C. Cheng, J. F. Stoddart and R. D. Astumian, Chem. Soc. Rev., 2017, 46, 5491–5507 RSC;
(e) S. Erbas-Cakmak, D. A. Leigh, C. T. McTernan and A. L. Nussbaumer, Chem. Rev., 2015, 115, 10081–10206 CrossRef CAS.
- C. Bruns and J. F. Stoddart, The Nature of the Mechanical Bond: From Molecules to Machines, John Wiley & Sons Inc., Hoboken, NJ, 2017 Search PubMed.
-
(a) P. R. Ashton, I. Baxter, M. C. T. Fyfe, F. M. Raymo, N. Spencer, J. F. Stoddart, A. J. P. White and D. J. Williams, J. Am. Chem. Soc., 1998, 120, 2297–2307 CrossRef CAS;
(b) Y. Tokunaga, N. Wakamatsu, A. Ohbayashi, K. Akasaka, S. Saeki, T. Hisada, T. Goda and Y. Shimomura, Tetrahedron Lett., 2006, 47, 2679–2682 CrossRef CAS;
(c) F. M. Raymo, K. N. Houk and J. F. Stoddart, J. Am. Chem. Soc., 1998, 120, 9318–9322 CrossRef CAS;
(d) F. M. Raymo and J. F. Stoddart, Pure Appl. Chem., 1997, 69, 1987–1997 CAS;
(e) M. Händel, M. Plevoets, S. Gestermann and F. Vögtle, Angew. Chem., Int. Ed., 1997, 36, 1199–1201 CrossRef;
(f) S.-Y. Hsueh, C.-C. Lai, Y.-H. Liu, Y. Wang, S.-M. Peng and C.-C. Hsu, Org. Lett., 2007, 9, 4523–4526 CrossRef CAS;
(g) J.-J. Lee, A. G. White, J. M. Baumes and B. D. Smith, Chem. Commun., 2010, 46, 1068–1069 RSC;
(h) A. J. McConnell and P. D. Beer, Chem.–Eur. J., 2011, 17, 2724–2733 CrossRef CAS;
(i) P. R. Ashton, M. Belohradsky, D. Philp and J. F. Stoddart, J. Chem. Soc., Chem. Commun., 1993, 1269–1274 RSC;
(j) M. Asakawa, P. R. Ashton, R. Ballardini, V. Balzani, M. Belohradsky, M. T. Gandolfi, O. Kocian, L. Prodi, F. M. Raymo, J. F. Stoddart and M. Venturi, J. Am. Chem. Soc., 1997, 119, 302–310 CrossRef CAS;
(k) M. A. Bolla, J. Tiburcio and S. J. Loeb, Tetrahedron, 2008, 64, 8423–8427 CrossRef CAS;
(l) P. Linnartz, S. Bitter and C. A. Schalley, Eur. J. Org. Chem., 2003, 4819–4829 CrossRef CAS;
(m) H. W. Gibson, N. Yamaguchi, Z. Niu, J. W. Jones, C. Slebodnick, A. L. Rheingold and L. N. Zakharov, J. Polym. Sci., Part A: Polym. Chem., 2010, 48, 975–985 CrossRef CAS;
(n) X. H. Huang, S. Y. Huang, B. Q. Zhai, Y. Zhang, Y. N. Xu and Q. C. Wang, Tetrahedron Lett., 2012, 53, 6414–6417 CrossRef CAS;
(o) Z. Qian, X. Huang and Q. Wang, Dyes Pigm., 2017, 145, 365–370 CrossRef CAS;
(p) A. C. Smith and D. H. Macartney, J. Org. Chem., 1998, 63, 9243–9251 CrossRef CAS;
(q) D. B. Amabilino, P. R. Ashton, M. Bglohradsky, F. M. Raymo and J. F. Stoddart, J. Chem. Soc., Chem. Commun., 1995, 747–750 RSC;
(r) S. H. Chiu, S. J. Rowan, S. J. Cantrill, P. T. Glink, R. L. Garrell and J. F. Stoddart, Org. Lett., 2000, 2, 3631–3634 CrossRef CAS;
(s) J. O. Jeppesen, J. Becher and J. F. Stoddart, Org. Lett., 2002, 4, 557–560 CrossRef CAS;
(t) A. C. Catalán and J. Tiburcio, Chem. Commun., 2016, 52, 9526–9529 RSC.
- T. Legigan, B. Riss-Yaw, C. Clavel and F. Coutrot, Chem.–Eur. J., 2016, 22, 8835–8847 CrossRef CAS PubMed.
- B. Riss-Yaw, J. Morin, C. Clavel and F. Coutrot, Molecules, 2017, 22, 2017 CrossRef.
-
(a) T.-X. Métro, E. Colacino, J. Martinez and F. Lamaty, in Ball Milling, Towards Green Synthesis: Applications, Projects, Challenges, The Royal Society of Chemistry, 2015, pp. 114–150 Search PubMed;
(b) J. L. Howard, Q. Cao and D. L. Browne, Chem. Sci., 2018, 9, 3080–3094 RSC;
(c) J. Anderson and J. Mack, Green Chem., 2018, 20, 1435–1443 RSC;
(d) D. Tan and T. Friščić, Eur. J. Org. Chem., 2018, 2018, 18 CrossRef CAS;
(e) D. Tan and F. Garcia, Chem. Soc. Rev., 2019, 48, 2274–2292 RSC;
(f) G. Kaupp, CrystEngComm, 2009, 11, 388–403 RSC.
-
(a) A. Inthasot, T. –Y. Tai and S. H. Chiu, J. Chin. Chem. Soc., 2019, 66, 134–145 CrossRef CAS;
(b) T. Friščić, Chem. Soc. Rev., 2012, 41, 3493–3510 RSC;
(c) M. Holler, T. Stoerkler, A. Louis, F. Fischer and J.-F. Nierengarten, Eur. J. Org. Chem., 2019, 3401–3405 CrossRef CAS;
(d) A. Bose and P. Mal, Beilstein J. Org. Chem., 2019, 15, 881–900 CrossRef CAS PubMed.
-
(a) M. Händel, M. Plevoets, S. Gestermann and F. Vogtle, Angew. Chem., Int. Ed. Engl., 1997, 36, 1199–1201 CrossRef;
(b) A. Affeld, G. M. Hübner, C. Seel and C. Schalley, Eur. J. Org. Chem., 2001, 2877–2890 CrossRef CAS.
- A. Orita, J. Okano, G. Uehara, L. Jiang and J. Otera, Bull. Chem. Soc. Jpn., 2007, 8, 1617–1623 CrossRef.
- Retsch® MM200 or MM400 high speed vibrating ball mill (operated at 25 Hz, 1 stainless steel ball with a diameter of 10 mm in a 10 mL stainless steel reactor) was used for grinding the solids mixture..
- LAG was realized through the addition of 0.2 μL of acetonitrile per mg of mixture of DB24C8 and 1..
- To create an atmosphere of acetonitrile, 0.1 mL of acetonitrile was added to a 100 mL stoppered round-bottom flask. In this flask was disposed uncapped vials containing 5 mg of the solids mixture. The round-bottom flask was disposed in an oven at 333 K..
- For more information regarding Liquid-Assisted Grinding (LAG), see: T. Friščić, S. L. Childs, S. A. A. Rizvi and W. Jones, CrystEngComm, 2009, 11, 418–426 RSC.
-
(a) T. Stolar, S. Lukin, M. Tireli, I. Sović, B. Karadeniz, I. Kereković, G. Matijašić, M. Gretić, Z. Katančić, I. Dejanović, M. d. Michiel, I. Halasz and K. Užarević, ACS Sustainable Chem. Eng., 2019, 7, 7102–7110 CrossRef CAS;
(b) D. Hasa, E. Miniussi and W. Jones, Cryst. Growth Des., 2016, 16, 4582–4588 CrossRef CAS;
(c) N. Tumanova, N. Tumanov, K. Robeyns, F. Fischer, L. Fusaro, F. Morelle, V. Ban, G. Hautier, Y. Filinchuk, J. Wouters, T. Leyssens and F. Emmerling, Cryst. Growth Des., 2018, 18, 954–961 CrossRef CAS;
(d) Y. Yeboue, B. Gallard, N. Le Moigne, M. Jean, F. Lamaty, J. Martinez and T.-X. Métro, ACS Sustainable Chem. Eng., 2018, 6, 16001–16004 CrossRef CAS.
-
(a) M. J. Cliffe, C. Mottillo, R. S. Stein, D.-K. Bučar and T. Friščić, Chem. Sci., 2012, 3, 2495–2500 RSC;
(b) X. Lim, Nature, 2015, 524, 20–21 CrossRef CAS PubMed;
(c) T. Di Nardo, C. A. Hadad, A. Nguyen Van Nhien and A. H. Moores, Green Chem., 2019, 21, 3276–3285 RSC.
- [1] = 3 × 10−2 M; [DB24C8] = 9 × 10−2 M..
- The solids were mixed with a spatula before being heated..
-
(a) X. Lim, Nature, 2015, 524, 20 CrossRef CAS;
(b) M. J. Cliffe, C. Mottillo, R. S. Stein, D.-K. Bučar and T. Friščić, Chem. Sci., 2012, 3, 2495 RSC;
(c) T. Di Nardo, C. A. Hadad, A. Nguyen Van Nhien and A. H. Moores, Green Chem., 2019, 21, 3276–3285 RSC.
- At the end of the aging procedure (entries 7 and 8, Table 1), the sample keeps a slightly pasty solid appearance. The quantity of acetonitrile which has been absorbed by the solid mixture has been quantified. For each vial, it corresponds to 4.1 μl of acetonitrile, that is 216 times less than the quantity used for slippage in solution (entry 1, Table 1)..
Footnote |
† Electronic supplementary information (ESI) available. See DOI: 10.1039/c9ra05045k |
|
This journal is © The Royal Society of Chemistry 2019 |
Click here to see how this site uses Cookies. View our privacy policy here.