DOI:
10.1039/C9RA04568F
(Paper)
RSC Adv., 2019,
9, 28902-28907
Sulfonic-acid-functionalized carbon fiber from waste newspaper as a recyclable carbon based solid acid catalyst for the hydrolysis of cellulose
Received
18th June 2019
, Accepted 30th August 2019
First published on 13th September 2019
Abstract
Waste newspaper is one of the most common cellulosic materials. Therefore, effective utilization of this commonly available biomass resource to prepare high-value carbon-based solid acid catalysts is an interesting and meaningful task. In this study we propose a new route for waste newspaper valorization, in which sulfonic-acid-functionalized carbon fiber can be directly produced from waste newspaper as a recyclable carbon based solid acid catalyst (WCSA) for the hydrolysis of cellulose. The as-prepared sulfonic-acid-functionalized carbon fiber contained –SO3H, –COOH, and phenolic –OH groups and exhibited good catalytic activity for the hydrolysis of cellulose. WCSA prepared under sulfonation conditions at a temperature of 100 °C and for a duration of 10 h has a higher sulfonic acid content. A total reducing sugars (TRS) yield of 58.2% was obtained with a catalyst/microcrystalline cellulose (MCC) ratio of 4 at 150 °C using a reaction time of 6 h. The recycling performance of the WCSA catalyst indicated that the TRS remained almost stable for five cycles during the hydrolysis of cellulose.
1 Introduction
Efficient conversion of renewable biomass to useful chemicals and biofuels is one of the most popular topics in green and sustainable chemistry.1 Cellulose, a linear homopolymer composed of D-glucopyranose subunits linked by β-1,4-glycosidic bonds, is the most abundant organic molecule on Earth,2 effective methods of hydrolysis or depolymerization of cellulose seem to be an interesting entry point into the production of biofuels and biochemicals.3 Homogeneous acid hydrolysis of cellulose is a method that has been used for a long time; however, the method has some shortcomings such as reactor corrosion, poor catalyst recyclability, difficult product separation and treatment of the waste effluent.4 Enzymatic depolymerization of cellulose demonstrates a good selectively for the hydrolysis of cellulose to glucose, but it is slow, expensive and difficult to recover enzymes from the reaction mixture.5
In contrast to homogeneous acid catalysts (e.g., sulfuric acid) and enzymes which are highly active and selective but cannot be reused, solid acid catalysts are easy to handle on the large scale and can be reused multiple times. Among solid acid catalysts, carbon-based solid acids (CSA), such as amorphous carbons consisting of aromatic carbon sheets bearing active sites (SO3H, OH, and COOH groups), have attracted a great deal of attention owing to their favorable characteristics such as high acid densities, stability and recyclability, which are widely used in the hydrolysis of cellulose and its derived polysaccharides.6 During CSA catalytic hydrolysis of cellulose, phenolic OH groups bonded to CSA have the ability to absorb cellulose and rich-phenolic hydroxyl CSA derived from phenolic residues have improved this ability.7 The adsorption effect is affected by the size and morphology of the catalyst owing to the solid/solid interface effect between the CSA and the cellulose. Therefore, it is imperative to change the size and morphology of the CSA in order to enhance the interaction between the cellulose and catalyst. Guo et al. prepared a sulfonated carbonaceous solid acid catalyst with a spherical structure for catalytic hydrolysis of cellulose and procured total reducing sugars (TRS) at a yield of 68.9%. Ma et al. hydrolyzed cellulose into glucose with yields of 40.2% using a porous morphology lignin carbon-based solid acid.8 Pang et al. employed microcrystalline cellulose-derived carbon fragments with an elongated structure for the catalytic hydrolysis of cellulose and the glucose selectivity was found to be 48.5%.9 The catalysts used by those authors can be easily synthesized by the low temperature hydrothermal reaction of renewable hydrocarbon feedstocks, for example cellulose, lignin, and sugars.10
Waste newspaper is one of the most common cellulosic materials, millions of tons of waste newspapers are generated annually in China.11 Therefore, the effective utilization of this commonly available biomass resource to prepare high-value carbon-based solid acid catalysts is an interesting and meaningful task. In this work, we designed and synthesized a carbon fiber solid acid catalyst bearing –OH, –SO3H, and –COOH groups from the hydrothermal carbonization of waste newspaper under mild conditions and used it for the hydrolysis of cellulose in water. Cyclic experiments for the separated catalysts showed that the catalyst maintained its catalytic properties and could be reused. These solid acid catalysts based on waste newspaper prepared using hydrothermal carbonization provide a possible strategy for biomass conversion through renewable materials.
2 Materials and methods
2.1. Preparation of samples and reagents
Waste newspapers (WP) were obtained from Dalian Publishing House (Dalian, China). The composition, based on the dry substrate, was: 67.18 ± 0.04% cellulose; 9.88 ± 0.07% hemicelluloses; 5.36 ± 0.06% lignin; 12.72 ± 0.03% ash; 3.45 ± 0.02% moisture; and 1.41 ± 0.08% other additives. The composition was determined using the standard method described by National Renewable Energy Laboratory (NREL).12 Microcrystalline cellulose (MCC) was purchased from Merck. All other chemical reagents and deionized water were of laboratory grade and used as received.
2.2. Preparation of waste newspaper carbonaceous material with sulfonic acid (–SO3H) groups
The carbonaceous material was prepared by the hydrothermal carbonization of waste newspaper. Typically, the dried waste newspaper (3 g) and deionized water were mixed at a ratio of 1
:
6 (w/w), and the slurry was then added to a 100 mL polytetrafluoroethylene hydrothermal reaction vessel. The samples were carbonized at 240 °C for 4 h. After the carbonization treatment, the carbonized waste newspaper carbon fiber was filtered and then washed with 1 mol L−1 HCl for 1 h five times to remove the inorganic filler. Then the samples were vacuum dried at 80 °C overnight to produce the waste newspaper based carbonaceous material (WCM). Then, 1 g WCM was treated with concentrated sulfuric acid (∼20 mL H2SO4, 98%) at 60–140 °C under nitrogen for 6–14 h. Deionized water was added under stirring to remove the residual acids until the pH equaled 7 and it was then dried in an oven at 110 °C overnight. The functionalized WCM samples were then obtained and denoted as WCSA-sulfonation temperature (WCSA-60, -80, -100, -120, -140) and WCSA-sulfonation time (WCSA-6, -8, -10, -12, -14), respectively.
2.3. Catalyst characterization and analysis of the total reducing sugars
Scanning electron microscopy (SEM) was performed using a JSM-7800F scanning electron microscope produced by JEOL Co., Ltd. to characterize the apparent morphology of the sample. Fourier transform infrared spectrometry (FT-IR) analysis was carried out in a PerkinElmer Spectrum 100 spectrometer using KBr pellets. The wavenumber of the IR spectra was recorded from 4000 to 400 cm−1. The N2 adsorption–desorption isotherms were obtained using a 77 Kon Micromeritics ASAP 2020 physisorption analyzer. Then the pore size distribution was obtained from the description branch using the Barrett–Joyner–Halenda (BJH) formula. The crystal phase of the as-prepared products was characterized using an X-ray diffractometer (SHIMADZU XRD-7000S) with Cu-Kα radiation in the range (10–60°). The density of the –SO3H, –COOH and –OH groups of WCSA was determined using the Boehm titration with a slight modification. The method used was previously described in the literature by Lin et al.13
2.4. Catalytic activity of the hydrolysis of cellulose over a sulfonated carbon catalyst
For a typical run, the hydrolysis reaction was conducted by adding the WCSA catalyst (0.3 g) and MCC (0.1 g) into water (10 mL) at a reaction temperature of 130–170 °C and for a duration of 2–10 h in a 20 mL polytetrafluoroethylene tank with a stirring rate of 400 rpm. Recycling experiments were performed to determine the catalytic stability of the WCSA. At the end of each hydrolysis of cellulose cycle, the WCSA samples were recovered by centrifugation and washed with water and ethanol several times and dried at 80 °C for 12 h in a vacuum oven. After the hydrolysis of cellulose reaction, the TRS, such as glucose and fructose, were measured using the dinitrosalicylic (DNS) acid colorimetric method as described by Shimizu et al.14 Analysis of glucose in hydrolysates was performed using an ion chromatograph (Dionex ICS-5000, USA), which was equipped with a Capillary Reagent-Free IC System and a CarboPac 20 column.
3 Results and discussion
3.1. Structural characteristics of WCSA catalysts
Waste newspaper was prepared by hydrothermal carbonization and sulfonated to generate a sulfonated carbon catalyst (WCSA). A FT-IR spectrum (Fig. 1a) was used to determine the different effects on various groups in the waste newspapers, before and after sulfonation. The absorption peaks of the C
C double bonds (1608 cm−1) and –CH2 (1431 cm−1) were found on WCM and WCSA. The absorption bands at close to 1180 cm−1 (S
O symmetric stretching vibration), 1030 cm−1 (S–O stretching vibration) and 645 cm−1 (C–S stretching vibration) that were also found on WCSA indicate that WCM was functionalized with catalytic sites (–SO3H) on the surface.15 Similar characteristic peaks for sulfonate groups have been reported by Peng et al. and Li et al.15 The absorption peaks of the C
O double bonds (1700 cm−1), C–OH stretching and –OH bending vibrations (1000–1300 cm−1) were also found on WCSA, which confirm the existence of the –COOH and phenolic –OH groups.16 As a result, the adsorption peaks of the WCM and WCSA of the carbon were quite different. Again, this indicates that the WCM was successfully sulfonated by sulfuric acid which possessed hydroxyl groups for intermolecular dehydration.
 |
| Fig. 1 FT-IR spectra (a), XRD spectra (b), SEM images (c)–(e) and N2 adsorption–desorption isotherms and pore size distribution (f) for WP, before (WCM) and after (WCSA) sulfonation. | |
The X-ray diffractometry (XRD) patterns of WP, WCM and WCSA are shown in Fig. 1b, the two weak and broad peaks at 2θ = 20–30° and 40–50° are due to the carbon (002) and (100) reflections, respectively. These diffraction peaks indicate that WCSA is an amorphous carbon composed of aromatic carbon sheets oriented in a considerably random fashion. Structurally, the carbon framework of WCSA is approximately consistent with others reported in the literature.17
Fig. 1c–e shows the differences between the SEM images on the external surfaces of the WP, WCM and WCSA. SEM analysis reveals that the surface of WP was quite compact and smooth. After carbonization and sulfonic-acid-functionalization, the obtained WCM and WCSA materials formed fiber rods with a rough and loose surface and a diameter around 10–30 μm. There were no appreciable size and surface differences before and after sulfonation. During carbonization and sulfonic-acid-functionalization, the chemical bonds between the cellulose fibers were broken, this caused the fibers to become loose, and form a fiber rod structure. The rod-like structure provides the catalyst with more contact points with cellulose than the sheet structure. This rod-like structure may increase the adsorption between the catalyst and the cellulose fiber, thus improving the yield of the TRS from cellulose hydrolysis. Fig. 1f shows that the Brunauer–Emmett–Teller (BET) surface area of WCSA and WCM were much higher than that of WP, and the isotherms exhibited intermediate features between those of type I and II, which indicates that the porous network was composed of micropores and mesopores. In addition, the predominant pore size distribution exhibited was below 10 nm, which is associated with micropores with a narrow pore size distribution.
3.2. Effect of sulfonation parameters on the yield and structural characteristics of WCSA catalysts
The sulfonation temperature and time are important factors affecting the structure and activity of the carbon-derived catalyst.18 In this work, the effects of the sulfonation conditions on the catalyst yield (Table 1), structure (Fig. 2 and 3) and catalyst activity (Fig. 4) were investigated. The WCM yield obtained from the hydrothermally carbonized WP was 48.7 wt% (see Table 1). The yields of WCM after sulfonation are also listed in Table 1. It can be seen that, depending on the operational conditions, the yields of WCSA-n were in the 71–93 wt% range. The sulfonation conditions not only affect the yield of the products, but also affect the composition of the functional groups on the surface of the WCM. The amounts of –SO3H, –COOH and phenolic –OH groups bonded to the WCSA with different sulfonation temperatures and sulfonation times are also shown in Table 1. As shown in Table 1, increasing the sulfonation temperature has a positive effect on the –SO3H and phenolic –OH density for the WCSA catalyst, however, WCSA-140 had lower amounts of –SO3H and phenolic –OH than WCSA-100 because the high sulfonation temperature resulted in increased acid dehydration among the WCM, reducing the C–H and C–OH bonds which could be replaced by –SO3H groups. Meanwhile, the total acid density of all samples was slightly increased when the sulfonation temperature was raised from 60 to 100 °C, but they decreased rapidly when the temperature was increased further.
Table 1 Yield and acid density of WCM and sulfonated WCM prepared at different carbonization and sulfonation temperatures and timesa
Sample |
T/°C |
t/h |
Yield (%) |
Acid density (mmol g−1) |
–OH |
–COOH |
–SO3H |
Yield is expressed as: g WCM/100 g WP. Yield is expressed as: g WCSA-n/100 g WCM. |
WCM |
— |
— |
48.7a |
5.03 |
0.05 |
— |
WCSA-60 |
60 |
10 |
93.8b |
4.11 |
0.12 |
0.64 |
WCSA-80 |
80 |
10 |
91.2b |
3.98 |
0.15 |
1.10 |
WCSA-100 |
100 |
10 |
84.4b |
3.63 |
0.35 |
1.97 |
WCSA-120 |
120 |
10 |
80.5b |
3.59 |
0.23 |
1.76 |
WCSA-140 |
140 |
10 |
76.6b |
3.32 |
0.21 |
1.65 |
WCSA-160 |
160 |
10 |
71.2b |
2.77 |
0.14 |
1.20 |
WCSA-6 |
100 |
6 |
89.1a |
3.98 |
0.12 |
0.71 |
WCSA-8 |
100 |
8 |
87.2b |
3.86 |
0.25 |
0.91 |
WCSA-12 |
100 |
12 |
81.4b |
3.33 |
0.31 |
1.95 |
WCSA-14 |
100 |
14 |
80.8b |
3.05 |
0.34 |
1.87 |
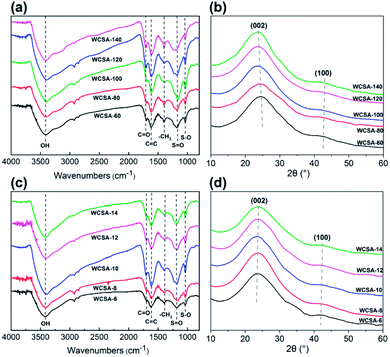 |
| Fig. 2 FTIR spectra and XRD patterns of sulfonated catalysts prepared under different conditions. (a) and (b) FTIR spectra and XRD patterns with sulfonation temperatures of 60–140 °C; (c) and (d) FTIR spectra and XRD patterns with sulfonation times of 6–14 h. | |
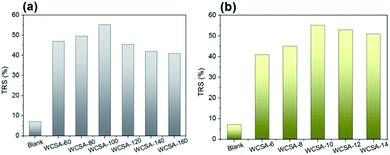 |
| Fig. 3 Effects of sulfonation (a) temperature and (b) time on the TRS yield from cellulose catalyzed using WCSA catalysts. Reaction conditions: cellulose (0.1 g), WCSA (0.3 g), and water (10 mL), 6 h, 150 °C. | |
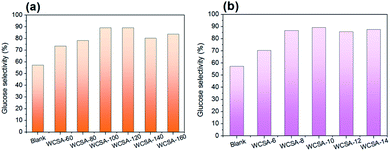 |
| Fig. 4 Effects of sulfonation (a) temperature and (b) time on glucose selectivity on the TRS yield. Reaction conditions: cellulose (0.1 g), WCSA (0.3 g), and water (10 mL), 6 h, 150 °C. | |
Moreover, it was also found that the density of –SO3H groups in the samples was slightly increased when the sulfonation time was raised from 6 to 10 h, but this remained almost stable upon increasing the time further, indicating that the –SO3H density did not change significantly with increasing sulfonation time.
The FT-IR and XRD patterns for WCSA prepared under different temperatures and times are shown in Fig. 2. Fig. 2a and c show that the absorption peak at 3600–3200 cm−1 is the OH stretching vibration absorption peak. The peak at 1600 cm−1, which represents the C
C double bond stretching vibration peak of the aromatic ring, indicates that the above described catalysts form a stable conjugated aromatic ring system. The two bands at 1038 and 1180 cm−1 in the WCSA catalysts can be assigned to the O
S
O symmetric stretching and –SO32− stretching modes in the –SO3H group of WCSA, this indicates that WCSA successfully introduced the sulfonic acid groups and that these groups were the active sites of WCSA. WCSA prepared under sulfonation conditions at a temperature of 100 °C and a time of 10 h exhibits the largest peak area, and we concluded that WCSA has a higher sulfonic acid content under these conditions. Therefore, the groups supported on WCSA mainly include –OH, –COOH and –SO3H.
Fig. 2b and d show the XRD test results for WCSA prepared under different sulfonation temperatures and times. The results obtained using the WCSA X-ray diffraction (XRD) pattern show a broad peak located at 2θ = 23°, which could be attributed to the characteristic peak of amorphous carbon (Fig. 2c). There are two characteristic peaks around 2θ = 30°, which are attributed to the carbon (002) peak, indicating that the degree of orientation of the aromatic ring space is similar to that of graphite. This indicates that WCSA is a type of polycyclic aromatic hydrocarbon which is non-directionally arranged in space and possesses a graphite-like amorphous carbon. The sulfonation process has little effect on the crystal form of the carbon materials.
The effects of the sulfonation conditions on the catalytic activity were investigated, as shown in Fig. 3. The blank represents a catalyst which has not been subjected to sulfonation, it is shown that the unsulfonated catalyst has a certain catalytic effect on cellulose hydrolysis, and the sulfonated catalyst causes a significant increase in the yield of the reducing sugars. The positive effects of the sulfonation process on the catalytic activity are shown, while different sulfonation conditions have different effects on the catalytic activity. As can be seen in Fig. 3a, the yield of the TRS during the hydrolysis of cellulose initially increased and then decreased with increasing sulfonation temperatures. When the sulfonation temperature was 100 °C (WCSA-100), the yield of TRS reached the highest value (56.7%). As shown in Fig. 3b, the yield of TRS remained almost stable at about 54% over the sulfonation time from 10 to 14 h, indicating that the catalytic activity did not change significantly with increasing sulfonation time. This was identical to the effect of the sulfonation time on the –SO3H and phenolic –OH density of the WCSA samples (Table 1). The hydrolysis of cellulose is the process of destroying β-1,4-glycosides bonds. It is reported that the OH groups in the CSA can adsorb cellulose through hydrogen bonding between the OH groups in the CSA and cellulose, so that the CSA can efficiently hydrolyze cellulose into glucose as well as sulfuric acid.19
As shown in Fig. 4, the effect of the sulfonation conditions on the glucose selectivity in TRS was investigated. The blank represents a catalyst which has not been subjected to sulfonation, it plays a minor role in the hydrolysis of cellulose to produce glucose. As can be seen from Fig. 4a, the yield of glucose in the TRS initially increases with the increase in the sulfonation temperature and then stabilizes. When the sulfonation temperature was 120 °C (WCSA-120), the glucose selectivity reached the highest value (89.2%). When the sulfonation temperature was 100 °C (WCSA-100), glucose selectivity reached 89.1%. As shown in Fig. 4b, the glucose selectivity remained almost stable at about 88% over the sulfonation time from 8 to 14 h, indicated that the catalytic activity did not change significantly with the increasing sulfonation time. This was identical to the effect of the sulfonation time on the –SO3H and phenolic –OH density of WCSA samples (Table 1).
3.3. Influence of reaction conditions on catalytic activity in the hydrolysis of cellulose
The effect of the hydrolysis reaction conditions on cellulose hydrolysis using the WCSA-100 catalyst is shown in Fig. 5. The different mass ratios of the catalyst and MCC employed were 2, 3, 4, 5 and 6 (Fig. 5A). When the mass ratio of the catalyst and MCC (catalyst/MCC) was increased to 5, the TRS yield increased to 58.2% at a temperature 150 °C and a reaction time of 6 h. It was proposed that a further increase in the ratio would probably enhance the hydrolysis of MCC to produce TRS, however, the TRS yield decreased slightly with a further increase in the catalyst/MCC ratio. A large ratio of catalyst/MCC is likely to provide excessive active sites in the reaction process, which not only enhances the hydrolysis of cellulose into TRS, but also enhances the depolymerization of TRS into small molecular derivatives, such as 5-hydroxymethyfurfural (5-HMF) and formic acid.20 The reaction temperature and time also had a significant effect on the TRS yield as shown in Fig. 5B and C. When the reaction time was 6 h, the maximum TRS yield of 56.7% was reached at 150 °C. When the temperature and time were increased to 170 °C and 10 h, respectively, the TRS yield was decreased to 29% and 46%, respectively. The possible reason for this may be that the high reaction temperature led to further side reactions, forming by-products such as formic acid and 5-HMF.21 It is known that water is an indispensable reactant in the cellulose hydrolysis reaction. Herein, the influence of the different mass ratios of water and MCC on the TRS yield was investigated, as shown in Fig. 5D. The TRS yield was 9% when the mass ratio of the liquid and MCC was 50. When the mass ratio was increased from 50 to 200, the TRS yield sharply increased from 9% to 56.7%. When the ratio of the liquid and MCC was higher than 200, the TRS yield quickly decreased. The possible reason for this may be that too much water in the reaction system could not only reduce the contact probability between the active sites of the catalyst and MCC, but it may also affect the activity of the WCSA catalyst owing to the hydration of the –SO3H groups in the catalyst.22
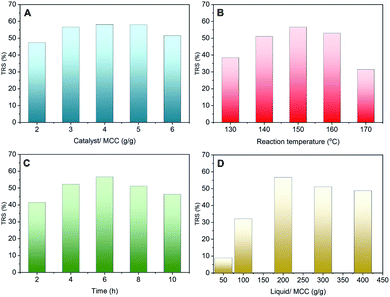 |
| Fig. 5 Effects of reaction conditions on the yield of WCSA-100 catalyst hydrolyzed cellulose. (A) Effect of catalyst dosage on the yield of reducing sugars; (B) effect of reaction temperature on the yield of reducing sugars; (C) effect of reaction time on the yield of reducing sugars; and (D) effect of solvent dosage on the yield of reducing sugars. | |
3.4. Reusability of WCSA
The recycling performance of the waste newspaper-derived solid acid catalyst was also investigated using the hydrolysis of MCC. Between each cycle of the reaction, water was employed as a washing solvent to recovery the catalyst. The effect of catalyst recycling on cellulose hydrolysis using the WCSA-100 catalyst is shown in Fig. 6. The TRS remained almost stable for five cycles for the hydrolysis of cellulose. When the catalyst (WCSA-100) was used for the first time, the yield of TRS reached the highest value (58.2%). The yield of TRS decreased to 55.2% in the fifth catalyst cycle. The yield reduced further after recycling five times, indicating that the catalyst displays a good stability in terms of the catalytic activity. Moreover, as shown in Table 2, the –SO3H, –COOH and phenolic –OH groups could still be identified. This illustrates that the groups chemically bonded onto WCSA do not exhibit the leaching problems that occur in most carbon based-solid catalysts. Thus, the catalyst has excellent stability and good repeatability.
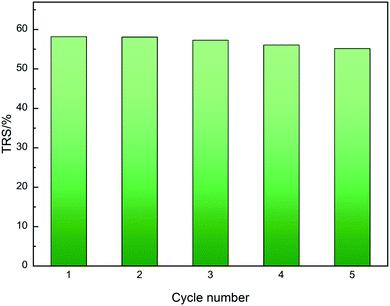 |
| Fig. 6 Reusability of WCSA catalysts for the hydrolysis of cellulose. Reaction conditions: cellulose (0.1 g), WCSA-100 (0.4 g), water (10 mL), reaction temperature 150 °C, and time 6 h per cycle. | |
Table 2 Acid density of WCM and sulfonated WCM prepared using the prescribed carbonization and sulfonation temperatures and times
Sample |
Acid density (mmol g−1) |
–OH |
–COOH |
–SO3H |
Fresh |
3.63 |
0.35 |
1.97 |
5th run |
3.33 |
0.29 |
1.94 |
4 Conclusions
In this work we proposed a new route for waste newspaper valorization, in which sulfonic-acid-functionalized carbon fiber can be directly produced from waste newspaper as a recyclable carbon based solid acid catalyst for the hydrolysis of cellulose. The prepared WCSA contained –SO3H, –COOH, and phenolic –OH groups and exhibited good catalytic activity for the hydrolysis of cellulose. WCSA prepared under sulfonation conditions at a temperature of 100 °C and with a reaction time of 10 h has a higher sulfonic acid content. A TRS yield of 58.2% was obtained with a catalyst/MCC ratio of 4 at 150 °C with a 6 h reaction time. Meanwhile, the recycling performance of the WCSA catalyst indicated that the TRS remained almost stable for five cycles during the hydrolysis of cellulose.
Conflicts of interest
There are no conflicts to declare.
Acknowledgements
This research was funded by the National Key Research and Development Program of China (No. 2017YFB0307900), the State Key Laboratory of Pulp and Paper Engineering (No. 201803), and the Liaoning Provincial Department of Education science and technology research projects (No. 2017J002).
References
- H. Guo, Y. Lian, L. Yan, X. Qi and R. L. Smith, Green Chem., 2013, 15, 2167–2168 RSC.
- B. R. Caes, R. E. Teixeira, K. G. Knapp and R. T. Raines, ACS Sustainable Chem. Eng., 2015, 3, 2591–2605 CrossRef CAS.
- R. Rinaldi and F. Schuth, ChemSusChem, 2009, 2, 1096–1107 CrossRef CAS.
- Y. B. Huang and Y. Fu, Green Chem., 2013, 15, 1095–1111 RSC.
- Z. Qiu, G. M. Aita and M. S. Walker, Bioresour. Technol., 2012, 117, 251–256 CrossRef CAS.
- S. Shen, B. Cai, C. Wang, H. Li, G. Dai and H. Qin, Appl. Catal., A, 2014, 473, 70–74 CrossRef CAS.
- M. Hara, Top. Catal., 2010, 53, 805–810 CrossRef CAS.
- Z. H. Ma, R. M. Gong, Y. Han, X. Wang, G. W. Sun, Y. Li and J. H. Zhou, Tappi J., 2019, 18, 67–71 CAS.
- Q. Pang, L. Wang, H. Yang, L. Jia, X. Pan and C. Qiu, RSC Adv., 2014, 4, 41212–41218 RSC.
- P. Asawaworarit, P. Daorattanachai, W. Laosiripojana, C. Sakdaronnarong, A. Shotipruk and N. Laosiripojana, Chem. Eng. J., 2019, 356, 461–471 CrossRef CAS.
- I. F. Nata, M. D. Putra, C. Irawan and C.-K. Lee, J. Environ. Chem. Eng., 2017, 5, 2171–2175 CrossRef CAS.
- G. Xia, J. Wan, J. Zhang, X. Zhang, L. Xu, J. Wu, J. He and J. Zhang, Carbohydr. Polym., 2016, 151, 223–229 CrossRef CAS.
- Q. Lin, C. Zhang, X. Wang, B. Cheng, N. Mai and J. Ren, Catal. Today, 2019, 319, 31–40 CrossRef CAS.
- K.-i. Shimizu, H. Furukawa, N. Kobayashi, Y. Itaya and A. Satsuma, Green Chem., 2009, 11, 1627–1632 RSC.
- X. Peng, S. Shen, C. Wang, T. Li, Y. Li, S. Yuan and X. Wen, Mol. Catal., 2017, 442, 133–139 CrossRef CAS.
- X. Li, Y. Jiang, L. Shuai, L. Wang, L. Meng and X. Mu, J. Mater. Chem., 2012, 22, 1283–1289 RSC.
- G. Chen and B. Fang, Bioresour. Technol., 2011, 102, 2635–2640 CrossRef CAS.
- Q. Shu, J. Gao, Z. Nawaz, Y. Liao, D. Wang and J. Wang, Appl. Energy, 2010, 87, 2589–2596 CrossRef CAS.
- M. Li, D. Chen and X. Zhu, Chin. J. Catal., 2013, 34, 1674–1682 CrossRef CAS.
- F. Shen, T. Guo, C. Bai, M. Qiu and X. Qi, Fuel Process. Technol., 2018, 169, 244–247 CrossRef CAS.
- S. Suganuma, K. Nakajima, M. Kitano, D. Yamaguchi, H. Kato, S. Hayashi and M. Hara, J. Am. Chem. Soc., 2008, 130, 12787–12793 CrossRef CAS.
- A. Sluiter, B. Hames, R. Ruiz, C. Scarlata, J. Sluiter, D. Templeton and D. Crocker, Laboratory Analytical Procedure, 2008, 1617, 1–16 Search PubMed.
|
This journal is © The Royal Society of Chemistry 2019 |
Click here to see how this site uses Cookies. View our privacy policy here.