DOI:
10.1039/C9RA02720C
(Paper)
RSC Adv., 2019,
9, 18853-18862
Life cycle assessment of emerging Ni–Co hydroxide charge storage electrodes: impact of graphene oxide and synthesis route†
Received
11th April 2019
, Accepted 18th May 2019
First published on 17th June 2019
Abstract
Decoupling energy supply from fossil fuels through electrification and sustainable energy management requires efficient and environmentally low-impact energy storage technologies. Potential candidates are charge storage electrodes that combine nickel and cobalt hydroxides with reduced graphene oxide (rGO) designed to achieve high-energy, high-power density and long cycling lifetimes. An early eco-efficiency analysis of these electrodes seeks to examine the impacts of materials and processes used in the synthesis, specifically while focusing on the use of rGO. The emerging electrodes synthesized by means of electrodeposition, are further compared with electrodes obtained by an alternative synthesis route involving co-precipitation. Life cycle assessment (LCA) method was applied to compare a baseline nickel–cobalt hydroxide electrode (NCED), the focal electrode integrating rGO (NCED-rGO), and the benchmark co-precipitated electrode (NCCP), for delivering the charge of 1000 mA h. Contribution analysis reveals that the main environmental hotspots in the synthesis of the NCED-rGO are the use of electricity for potentiostat, ethanol for cleaning, and rGO. Results of comparison show significantly better performance of NCED-rGO in comparison to NCED across all impact categories, suggesting that improved functionalities by addition of rGO outweigh added impacts of the use of material itself. NCED-rGO is more impactful than NCCP except for the indicators of cumulative energy demand, climate change, and fossil depletion. To produce a functional equivalent for the three electrodes, total cumulative energy use was estimated to be 78 W h for NCED, 25 W h for NCED-rGO, and 35 W h for NCCP. Sensitivity analysis explores the significance of rGO efficiency uptake on the relative comparison with NCCP, and potential impact of rGO on the category of freshwater ecotoxicity given absence of removal from the process effluent. Scenario analysis further shows relative performance of the electrodes at the range of alternative functional parameters of current density and lifetime. Lastly, the environmental performance of NCED-rGO electrodes is discussed in regard to technology readiness level and opportunities for design improvements.
Introduction
Energy storage technologies are considered essential in the pursuit of sustainable energy use, especially their foreseen role in decarbonizing the transportation sector and the expansion of renewable energy infrastructure. To meet increasingly diversified demand of these and other applications, efforts in materials science have been directed on developing energy storage systems with improved functionality and low environmental impacts. Desired properties are expected for storage systems with high-energy density, high-power density and long cycling lifetimes of their integrating electrodes.1–3
The state-of-art electrodes could be developed by combining metal oxides and hydroxides with carbon-based materials,4–7 which are currently pursued in positive electrodes for batteries and hybrid-supercapacitors based on nickel and cobalt (Ni–Co) hydroxides fabricated by means of potentiostatic electrodeposition.8 Enhanced electrochemical performance of the Ni–Co hydroxide electrodes has been observed with the addition of reduced graphene oxide (rGO). The addition of rGO improves the capacity of the electrodes and acts as a conductive matrix that accommodates strain in the charge–discharge process leading to longer lifetimes.8 Conveniently, the reduction of GO to rGO is facilitated through the process of electrodeposition itself, avoiding the energy-intensive step of chemical reduction or other analogous routes, which would otherwise be necessary.
Considering their emerging nature, quantification of the environmental impacts of novel electrodes has not been previously attempted. Such an early inclusion of environmental performance consideration in the design of emerging electrodes could ensure that the of potential impacts in electrode synthesis are known and can be minimized in the future design and process optimization. Several studies, that constitute closest available literature, include analysis of several emerging cathode composites that only loosely resemble some of the materials used for the fabrication of novel electrodes.9,10 Similarly, lack of science-based environmental impact analysis applies to the exploration of a new trend of combining metal-hydroxides with carbon-based materials such as rGO.
To address these gaps, the present study employs the life cycle assessment (LCA) method to establish resource, ecosystem and human health impacts in the synthesis of emerging electrodes, implications of addition of rGO to metal hydroxide matrix, and performance of electrodes as they are compared with existing alternatives. The analysis identifies how impacts of the electrodes can be improved, and what functional application leads to optimized environmental performance with the aim to support these electrodes to take a positive role in sustainable energy management.
Materials and methods
The LCA study is carried out through four phases pertaining to requirements and recommendations of the International Standards Association, including (i) goal and scope, (ii) life cycle inventory, (iii) life cycle impact assessment, and (iv) life cycle interpretation.11,12
The goal and scope phase, detailed in the current material and methods section, outlines the study purpose, the boundaries of the modeled product systems (i.e., electrodes), the function and functional unit used as a reference for comparison, and select impact category indicators used for characterization of environmental impacts.
Goal and scope
Goal definition.
The goal of this study is to identify environmental hotspots in the synthesis of Ni–Co electrodes integrating rGO, and determine if the addition of rGO improves eco-efficiency when compared with baseline electrodeposited Ni–Co hydroxide electrode and Ni–Co hydroxide electrodes obtained through co-precipitation (an alternative fabrication route).
Given this goal, the analysis aims to improve and determine the eco-efficient status of the rGO integrating electrode and, as a broader objective, shed light on environmental implications of newly adopted practice in the materials science of combining carbon-based materials and metal hydroxides and oxides. The findings of this study are meant to contribute to the material design and to support future research on energy storage materials.
Function and functional unit.
The function of the electrode is defined by its ability to store energy over its effective lifetime, characterized by two parameters: (1) the electrode's capacity, representing an ability of the material to store charge given applied current, and (2) the number of charge–discharge cycles that can be carried out before capacity reduces due to structural degradation, chemical parasitic transformations or other ageing phenomena that occur during cycling. Capacity fade is commonly tolerated up to 20–30%, or in other words, when 70–80% of the initial electrode capacity is maintained.13–15 Parameters of capacity and lifetime are integrated to derive functional unit (FU) using following equation:
where Ci is the capacity of the material after i charge–discharge cycles in mA h g−1 (electrode's capacity after the first cycle), n is the total number of cycles at a given point during the charge–discharge cycling test, nEOL is the number of cycles to reach end-of-life capacity fade, and X is the mass of electrode's active layer, expressed in grams. Using the equation for FU, the electrodes and their corresponding quantities are compared at a functional equivalent for delivering the charge current of 1000 mA h at the current density of 1 A g–1 over the lifetime of the electrodes defined by the capacity fade of 20%.
Product systems: NCED and NCED-rGO.
The charge storage electrodes investigated in this study are nickel–cobalt hydroxides deposited on top of conductive stainless-steel substrate. The two electrodes are synthesized by means of potentiostatic electrodeposition. First product system is the baseline electrode NCED (Ni–Co-electrodeposited), with chemical formulae α-Ni0.33Co0.66(OH)2·(CO32−,2NO3−)0.66(H2O)0.5 and second, the analogous composite in which reduced graphene oxide is added: NCED-rGO, with chemical formulae α-Ni0.33Co0.66(OH)2·(CO32−,2NO3−)0.66(H2O)0.5/rGO. Derivation of the formulae is available in ESI, Table S1.†
Synthesis of the two electrodes and their characterization has been depicted in Fig. 1 and detailed elsewhere.8 The NCED electrode was prepared by applying a 10 seconds pulsed potential between −0.9 V and −1.2 V to the working electrode (stainless steel AISI 304) and using a counter electrode of platinum submerged in an aqueous electrolyte containing nickel and cobalt nitrate hexahydrates with a concentration of 3 mM and 6 mM respectively, and a saturated calomel electrode as the reference electrode. The deposition rate was approximately 1.5 μg per cm2 per minute, assuming linearity,16 which can be manipulated to achieve different layer thicknesses. The electrodeposited electrode material was subsequently washed with water and ethanol to remove impurities and to facilitate drying. The NCED-rGO electrode was prepared similarly, with the exception of the substitution of the aqueous electrolyte by a graphene oxide (GO) aqueous suspension at the concentration of 1 g l−1 and subsequent addition to electrodeposition bath along with the nickel and cobalt salts. Prior to its addition, GO was ultrasonicated for 30 min to ensure stable dispersion of GO flakes.
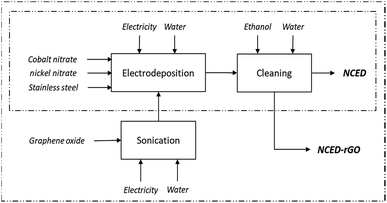 |
| Fig. 1 Process flowchart for the synthesis of NCED and NCED-rGO. | |
Electrochemical properties have been measured at several current densities including 1 A g−1, 4 A g−1 and 10 A g−1 and after reaching capacity fade of 20% and 30%. The cycling stability and the consequent evaluation of capacity fade was assessed at the current density of 10 A g−1 by applying continuous charge–discharge during 5000 cycles in the 0.45 V to −0.2 V potential range. Cycling stability was assumed to be equivalent for other current densities, as similar degradation phenomena occur.
At the applied current density of 1 A g−1, the capacity of NCED electrode is 30 mA h g−1 and NCED-rGO is 96 mA h g−1. For NCED the capacity fade of a 20% is reached after 972 cycles, and NCED-rGO after 1676 cycles.
Product system: NCCP.
More mature and resource-optimized Ni–Co hydroxide electrode involving the synthesis of active material by co-precipitation followed by physical deposition onto a stainless-steel substrate was used as a benchmark for comparison with NCGOED-rGO electrode. The material, noted here as NCCP (Ni–Co co-precipitated), with chemical formulae α-Ni0.33Co0.66(OH)2·(CO32−,2NO3−)0.66(H2O)0.5, is prepared in several process steps as depicted in Fig. 2, and detailed elsewhere.17,18 Co-precipitation is carried out in 2 M sodium hydroxide solution, containing 1.5 ml of hydrogen peroxide, that is slowly added to a solution containing 5 g of nickel nitrate hexahydrate and 10 g of cobalt nitrate hexahydrate (1
:
2 molar ratio). The mixture is stirred for 48 h and washed under centrifugation (4000 rpm, 10 minutes) six times with water and two with ethanol to reach stable pH. The precipitate is dried in the oven for 24 h at 40 °C. The material, in powder form, is then mixed with polytetrafluoroethylene (PTFE) and carbon black (at 80
:
5
:
15 mass ratio, respectively), using ethanol as solvent, and pressure-printed on a stainless-steel grid to produce the electrode. The capacity of this electrode is 121 mA h g−1 at a current density of 1 A g−1, and reaches a capacity fade of 20% after 1006 charge–discharge cycles.
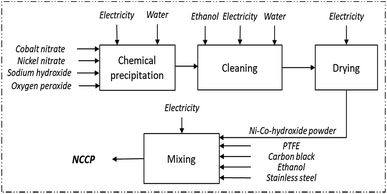 |
| Fig. 2 Process flowchart for the synthesis of NCCP. | |
System boundaries.
Cradle-to-product gate analysis was carried out. Boundaries of the analyzed product system include the production and manufacture of the electrodes, and do not quantify impacts arising in the use and disposal of the electrodes, which could have been modeled only in consideration to the entire energy-storage device. Cut-off criteria also apply to capital goods such as laboratory equipment, machinery, buildings and transportation vehicles used to carry out the processes and manage materials. Impacts of capital goods are assumed to be negligible considering low use of abrasive chemicals and high temperatures. In either case, these impacts would be almost identical for the two electrodeposited electrodes that employ similar processing steps. Capital goods also include the counter and reference electrodes that are used in electrodeposition, since they are not consumed in the process and could be reused without losses and deterioration.
Wastewater effluents from potentiostat, co-precipitation and washing stages are excluded for the baseline comparison and only potential toxicity impacts of GO to the freshwater systems quantified and investigated as a separate scenario. The small amounts of cobalt and nickel present in the effluent, in similar concentrations for all three electrodes, are assumed to be treated on site and precipitated prior to disposal to the sewage system or landfill. The literature suggests a high degree of removal of cobalt (up to 90%) and nickel (up to 80%) from the effluents.19,20 The reagents that would be potentially used to precipitate these pollutants are assumed to be small and uncertain, as electrolytic effluent is mixed with the wastewater from other experiments before it is treated. GO in effluent could be precipitated to a large degree using adsorption,21 floc-flotation,22 coagulation,23,24 or photo-degradation.25 However, if the specific type of treatment is not applied to the process effluent before its disposal to the conventional sewage system, the portion of GO could be eventually left untreated and enter natural water systems. GO in freshwater is associated with toxicity-related effects.26
Classification and characterization of environmental impacts is carried out using the indicator of cumulative energy demand and nine impact assessment categories of ReCiPe Midpoint (H) method including: climate change, ionizing radiation, metal depletion, fossil depletion, water depletion, terrestrial ecotoxicity, freshwater ecotoxicity, marine ecotoxicity, and human toxicity.27 GO impacts to freshwater ecotoxicity was investigated using USEtox method,28 as needed characterization factors and reference units of toxicity impacts were developed specifically for this method. Toxicity impacts in USEtox are expressed in comparative toxic units (CTUs), which correspond to the unit of potentially affected fraction of species (PAF) integrated over time (days) and volume (cubic meters) per unit mass (kilogramme) of a chemical emitted (PAF m3 day kg–1) whereas toxicity with ReCiPe is expressed in kg 1,4-dichlorobenzene (1,4-DB) equivalents.29 The modeling was carried out using OpenLCA v1.5 software. Direct material inputs in the synthesis of the electrodes are either observed experimentally, upscaled in reference to industrial practice or optimal use of laboratory equipment. Value assumptions are based on the literature, direct measurements, and expert opinion. Synthesis of the electrodes is modeled as a foreground system while impact-profiles of reagent materials are sourced from the Ecoinvent v3.3 database. Input quantities, related assumptions, and background data sources for each material in the foreground system are described in a subsequent LCI section. Input quantities of each material are shown per 1 g of active material. Material inputs per quantity of active materials corresponding to the functional unit and naming of background data sourced from the Ecoinvent database are provided in ESI, Tables S2 and S3.† Background datasets of electricity inputs and transportation were selected for an average European context, while for all chemicals an average global production was assumed.
In addition to sensitivity analysis applied to system boundaries to investigate potential toxicity effect of GO, a sensitivity analysis is also carried out to address the inventory assumption related to an efficiency rate of GO use in the manufacture of NCED-rGO. An increased GO uptake of 80% was considered for this upscaled scenario. Upscaled NCED-rGO is compared with NCCP only.
Scenario analysis was further carried out to compare electrodes in consideration to different operational parameters of applied current density and electrodes' lifetimes. In comparison to the baseline scenario, in which electrodes are compared at 1 A g−1 current density and capacity fade of 20%, a comparison was also carried out at current densities of 4 A g−1 and 10 A g−1 and a capacity fade of 30%. In total, five scenarios are investigated. Performance values of the electrodes (capacity and number of charge–discharge cycles) at these alternative current densities and capacity fade criteria are detailed in ESI, Table S4.†
Results
The results section encompasses the remaining three phases in LCA: the inventory, impact assessment, and interpretation phase. The inventory phase details data sources, assumptions and quantities for all the materials and energy inputs, which are then classified and characterized among environmental impact categories, in the subsequent impact assessment phase. In interpretation phase, main findings and modeling assumptions related to functional unit and GO use, are investigated through scenario and sensitivity analysis.
Life cycle inventory
Cobalt and nickel nitrates.
The quantities of cobalt and nickel nitrate salts used during the fabrication of electrodeposited electrodes (NCED and NCED-rGO) are calculated assuming an uptake efficiency of 95%. These are upscaled efficiencies readily achieved in industrial settings. Cobalt and nickel nitrate salts are modeled as obtained in direct oxidation from metallic cobalt in reaction with nitric acid.30 0.83 g of nickel-nitrate-hexahydrate and 1.661 g of cobalt-nitrate-hexahydrate were required to produce 1 g of active material for fabrication of NCED, and 0.79 g and 1.58 g for fabrication of NCED-rGO electrode, respectively.
Use efficiency of cobalt in nickel salts in co-precipitation was calculated to be 83%. 0.76 g of nickel-nitrate-hexahydrate and 1.54 g of cobalt-nitrate-hexahydrate are required to produce 1 g of active material for NCCP.
Graphene oxide solution.
Inputs of GO for fabrication of NCED-rGO had to be established on the basis of limited knowledge of GO behavior during electrodeposition, specifically, the efficiency of GO-use in electrodeposition and the concentration of the GO in the final electrode. It is approximated that rGO constitutes 5% of the NCED-rGO electrode which comes as an additional mass in electrodeposition in comparison to NCED, holding all other process material-inputs equal. This assumption is supported by the slight difference in weight between two materials. However precise measurement is difficult due to the possible presence of surface pollutants, non-homogeneous nature of the dispersion and limitations of the techniques currently used to quantify weight percentage (i.e., energy dispersive X-ray spectroscopy and X-ray photoelectron spectroscopy).
GO is used in excess in laboratory practice and only around 1% is utilized in the preparation of electrode. However, unlike the metal salts, the electrodeposition of GO is an emerging practice and the efficiency rates of deposition could not be emulated from existing industry practices and current scientific literature. Although, considering the non-ionic mechanism of GO deposition, and low reactivity of rGO, it is likely that this efficiency would be lower than for metals. Consequently, we made a conservative assumption in which GO use-efficiency is set at 5% for the default comparison, and uptake of 80% has been investigated as a potential scale-up scenario. Use efficiency will, among other, depend if the electrodeposition of GO can be established as a continuous and semi-continuous production, as opposed to batch-scale production carried out in a laboratory.
The inventory for the production of GO was adapted from comparative LCA study of different GO production routes,31 based on Bangal variant of the Hummer's method.32 1 g of GO or 1000 ml of 1% GO solution was assumed per 1 g of active electrode material.
Electricity use for sonication of GO was assumed for 110 W sonicator working for 30 min mixing 1 l solution of GO, equaling use of energy to 55 W h per 1 g of GO.
Stainless steel substrate.
A stainless steel AINSI 304 is used as a substrate for all electrodes, given its low electrochemical signal and chemical stability, which are needed to evaluate the electrochemical response of the active material. The stainless-steel foil, with a thickness of 3 mm, is applied as a substrate and is used to deposit 0.05 g of active material per 1 cm2 of active electrode material. 3.2 g of stainless steel is required per 1 g of active material.
Transport of materials.
Transportation of materials and process chemicals is assumed for average European transportation following the recommendation of Frischknecht et al. (2007). Accordingly, the distances of 600 km by train and 200 km by a 32 t lorry are taken for all the chemicals and 200 km by train and 100 km by 32 t lorry for stainless steel.33
Electricity use.
Potentiostat electricity is calculated for constant use of 75 W Gamry Interface 1000™ potentiostat, depositing an area of 100 cm2 steel substrate, at −1.2 V which can allow deposition rates of 0.15 mg and 0.1575 mg of active material per min per cm2 for NCED and NCED-rGO, respectively. Energy consumption was measured empirically resulting in energy use of 317 W h for 1 g of active material for both NCED and NCED-rGO.
In co-precipitation, electricity was measured for 2280 W Sigma 4–16 K centrifuge operating for a total of 80 min at 4000 rpm. Electricity for drying was indicated for Mermert oven 5800 W, for 24 h at 40 °C and measured empirically. The energy for printing the mixture on a steel substrate is assumed at 5 t cm−2. Per gram of active material, the energy requirement for centrifuge was measured to be 15.15 W h, for drying 106.8 W h and the energy for printing was calculated to be 2.72 W h.
Cleaning agents, electrolyte and effluent treatment.
Use of ethanol and water for washing and drying of electrodeposited electrodes corresponds to an experimental procedure. 3 ml of ethanol and 9 ml of water are estimated for cleaning 1 cm2 surface area of the electrode. For deposition of 1 g of active material, we estimate 62 ml of ethanol and 200 ml of water for NCED, and NCED-rGO.
Cleaning in co-precipitation was carried out under centrifugation using 602 ml of ethanol and 230 ml of water per gram of active material.
Additional chemicals for the synthesis of NCCP.
In addition to Ni–Co precipitation, fabrication of NCCP comprises additional mixing and pressing step that involves use of additional materials including polytetrafluoroethylene, carbon black, hydrogen peroxide, ethanol and sodium hydroxides. The inventory for production of polytetrafluoroethylene (PTFE) used as a binder is obtained from Jungbluth et al.34 0.05 g of PTFE is used per gram of active material. Quantities of other reagents include 0.15 g of carbon black, 0.2 ml of hydrogen peroxide, 250 ml of ethanol, and 0.5 g of sodium hydroxide, for which background data was obtained from the Ecoinvent.
Life cycle impact assessment (LCIA)
Contribution analysis of NCED-rGO.
The relative contribution of the main processes and materials in the synthesis of NCED-rGO to environmental impact categories are shown in Fig. 3. Application of GO and electricity for potentiostat appear to be the major contributors to the environmental impact categories. Impacts of GO application are generated from electricity for sonication and GO manufacture, and are mostly equally shared among each other for impact categories, with the exception of metal depletion category that is affected solely due to GO manufacture. Potential impacts of electricity are particularly high in the category of ionizing radiation due to use of nuclear electricity in Europe. Impacts of cleaning are the third most significant, with the particular contribution to the category of terrestrial ecotoxicity, fossil depletion and cumulative energy use. Consumption of distilled water for cleaning and potentiostat is the major contributor to impacts of terrestrial ecotoxicity (45%) mostly due to impacts of road transportation. Ethylene in production of ethanol is responsible to high impacts of ethanol especially to category of fossil depletion (35%). Stainless steel substrate has high impact on marine and freshwater ecotoxicity and resource categories including water and metal depletion, due to use of ferrochromium and ferronickel used for alloying. Impacts of nickel and cobalt nitrates which are relatively low when compared to other reagents, contribute to toxicity categories and metal depletion. Impacts of transportation of foreground materials are negligible.
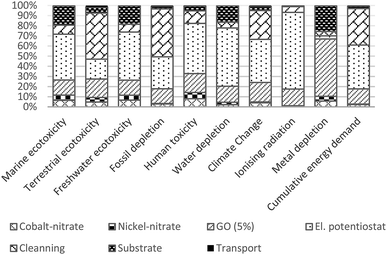 |
| Fig. 3 Environmental impact contributions of direct material use and emissions in the synthesis of NCED-rGO electrode. | |
Comparison with NCED and NCCP.
Normalized comparison between three electrodes is given in Fig. 4 and 5, and absolute values detailed in ESI, Table S5.† In comparison to NCED, NCED-rGO electrode appears to have the lowest impacts in all investigated categories. Hence, it appears that significant improvement in electrochemical properties considerably outweighs added impacts from GO production. On average across all the impact categories, NCED-rGO generates 70% less impacts than NCED to reach the same discharge current.
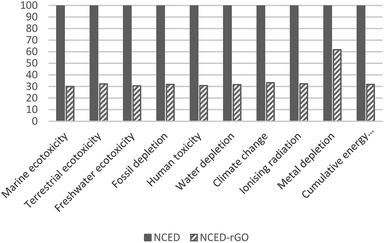 |
| Fig. 4 Normalized comparison between NCED and NCED-rGO. | |
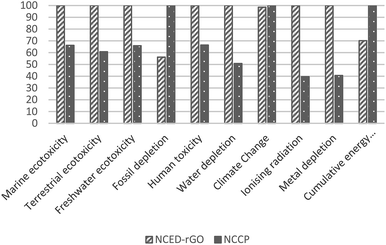 |
| Fig. 5 Normalized comparison between NCED-rGO and NCCP. | |
The superior performance of NCED-rGO is not confirmed in reference to NCCP electrode. NCCP is better in most of the impact categories with on average 40% lower impacts. The exceptions are categories of fossil depletion, climate change and cumulative energy use that are driven by considerably higher use of ethanol and electricity in fabrication of NCCP.
Interpretation
The potential impact of GO-rich effluent on freshwater ecotoxicity.
Under the scenario that GO from effluent is not adequately treated, freshwater ecotoxicity impacts of NCED-rGO electrode would increase by 37% for default scenario. As impacts of GO manufacture are 45% of total 15% that GO application adds to the net impacts in that category (remaining 55% are impact of electricity for sonication), the total impacts to category of freshwater ecotoxicity would increase by 4% if GO would not be removed from the effluent before wastewater discharge. Absolute values of three electrodes and hypothetical scenario for NCED-rGO including impacts of GO to freshwater are given per FU in Table 1.
Table 1 Relative comparison between electrodes for freshwater ecotoxicity including the scenario of untreated GO effluent (NCED-rGO + eff-GO). Unit CTUe [PAF m3 day kg–1] applies to all the values
|
Freshwater ecotoxicity |
NCED |
7.68 × 10−2 |
NCED-rGO |
2.12 × 10−2 |
NCCP |
1.77 × 10−2 |
NED-rGO + eff-GO |
2.63 × 10−2 |
Influence of increased rGO uptake on the relative comparison with NCCP.
At more efficient GO use (uptake of 80%) two electrodes are comparable with clear preference for NCED-rGO in additional categories of terrestrial ecotoxicity and fossil depletion. The comparison of upscaled scenario for NCED-rGO with NCCP electrode is given in Fig. 6. GO use is one of the main environmental hotspots in the fabrication of NCED-rGO with 20% of the contribution in all impact categories and 70% of the impacts in metal depletion category. Consequently, the significant influence of GO to toxicity categories results in notable shift in these categories at upscaled use. More detailed contribution analysis further reveals that impacts due to GO use for the categories of human toxicity, marine and freshwater ecotoxicity are equally divided between production of GO and electricity use for sonication whereas the categories of terrestrial ecotoxicity and metal depletion are dominated by GO production.
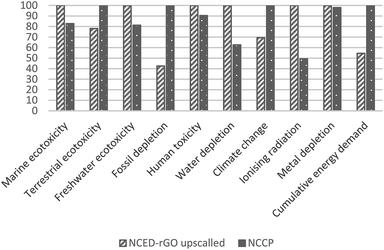 |
| Fig. 6 Normalized comparison between upscaled scenario for NCED-rGO and NCCP. | |
Effect of capacity fade and current density on relative performance of NCED-rGO electrode.
The relative performance between NCED, NCCP and NCED-rGO electrode varies at different current densities and allowances for capacity fade. Table 2 shows relative performance of each NCED and NCCP in comparison with NCED-rGO electrode for baseline scenario corresponding to parameters taken for FU (S-0), and additional scenarios (S-1, S-2, S-3, S-4, and S-5). Absolute values for electrode are given in ESI Table S6(a–c).† It appears that NCED-rGO performs best for current density of 1 A g−1 considered for the baseline comparison, while it would entail slightly better performance at capacity fade of 30%. Overall, it compares similarly with NCED across additional scenarios. The preference for NCCP increases at higher current densities. Thus, the least favorable application of NCED-rGO appears at the current density of 10 A g−1.
Table 2 Relative impacts of NCED-rGO in comparison with NCED, and NCCP at different operational parameters of current density and capacity fade. Scenario abbreviation refer to combination of current density (CD) and capacity fade (CF): S-0 – CD 1 A g−1, CF 20% (baseline); S-1 – CD 4 A g−1, CF 20%; S-2 – CD 10 A g−1, CF 20%; S-3 – CD 1 A g−1, CF 30%; S-4 – CD 4 A g−1, CF 30%; S-5 – CD 10 A g−1, CF 30%. Impacts of NCED-rGO are lower for percentage values preceded by the minus sign and are higher for positive values
|
Relative difference in comparison with NCED |
Relative difference in comparison with NCCP |
S-0 |
S-1 |
S-2 |
S-3 |
S-4 |
S-5 |
S-0 |
S-1 |
S-2 |
S-3 |
S-4 |
S-5 |
Marine ecotoxicity |
−70% |
−60% |
−70% |
−76% |
−66% |
−73% |
34% |
61% |
62% |
29% |
56% |
59% |
Terrestrial ecotoxicity |
−68% |
−58% |
−68% |
−75% |
−64% |
−72% |
39% |
63% |
21% |
34% |
45% |
49% |
Freshwater ecotoxicity |
−69% |
−61% |
−71% |
−76% |
−67% |
−74% |
34% |
61% |
18% |
30% |
57% |
60% |
Fossil depletion |
−68% |
−59% |
−68% |
−75% |
−64% |
−72% |
−44% |
−7% |
0% |
−51% |
−22% |
−16% |
Human toxicity |
−69% |
−60% |
−69% |
−76% |
−65% |
−73% |
34% |
60% |
19% |
30% |
56% |
59% |
Water depletion |
−68% |
−59% |
−68% |
−75% |
−64% |
−72% |
49% |
69% |
23% |
43% |
65% |
67% |
Climate change |
−67% |
−57% |
−67% |
−74% |
−63% |
−71% |
−1% |
39% |
14% |
−14% |
26% |
31% |
Ionising radiation |
−68% |
−58% |
−68% |
−75% |
−64% |
−72% |
60% |
76% |
25% |
56% |
71% |
73% |
Metal depletion |
−38% |
−20% |
−39% |
−52% |
−31% |
−46% |
59% |
75% |
47% |
56% |
73% |
75% |
Cumulative energy demand |
−68% |
−59% |
−68% |
−75% |
−64% |
−72% |
−30% |
14% |
20% |
−39% |
−2% |
5% |
Discussion
Opportunities and priorities for NCED-rGO design improvements
Results pinpointed several material and process hotspots that should be prioritized when considering future electrode design and process upscaling, and while seeking improvements in specific impact categories. Although, this is not universally observed,35 the use of process reagents and energy that are modeled at the scale of laboratory equipment is expected to decrease with process optimization.36,37 The impacts of materials that already assume industrial-scale efficiency could be further mitigated by identifying more eco-efficient substitutes or pursuing their recovery at the end-of-life. Here we discuss how impacts of some of the materials can be mitigated.
The impacts of the stainless-steel substrate is relative to required active material thickness and a requirement for the thickness of the substrate itself, thus of concern if the aim is to create electrodes with relatively thin deposits. To reduce impacts of the substrate, the stainless-steel could be compared with adequate alternatives which could include both metallic and non-metallic substrates,38,39 or stainless-steel substrate used in a way that it could be recycled at end-of-life of the electrode.40
The impacts of cobalt and nickel nitrates appear small but their share is likely to increase relative to a contribution to other electrode constituents since their use is already modeled at high efficiency. Reduction of impacts of cobalt and nickel salts can be targeted by manipulating their concentration taking their similar electrochemical properties in order to target reduction of specific impact categories. Relative to cobalt nitrate, nickel nitrate induces greater impacts in toxicity categories, while climate change and metal depletion categories are more impacted by cobalt nitrate. Such substitution is only appropriate under the condition that the functionality of the electrode is maintained.
The impacts of GO could be mitigated with more efficient uptake of GO in the deposition process, and by using GO from more eco-efficient synthesis route. Increasing uptake would mean that less GO would be required to produce NCED-rGO electrode. Impacts of GO that are shown to be on average 20% would reduce to the low of 3–4% if GO would be utilized at the efficiency of 80%. Therefore, any efforts directed to better understand and improve GO deposition could significantly improve environmental impacts. For example, researchers and industry could examine the effect of increased deposition times and investigate if electrodeposition involving GO could be established as a continuous production.
The impacts of GO appears to vary significantly depending on its manufacturing production route. Hence, sourcing or manufacturing of GO needs to be carefully selected and optimized if impacts of integrating electrode are to be minimized. The fabrication method adopted in the present study is based on chemical oxidation route,32 which rates favorably in comparison to approach by chemical vapor deposition and other variants of the Hummer's method.31 For example, the procedure initially considered, as described in Zaaba et al. (2017), was three times more impactful in comparison to chemical oxidation route we used for our model.31,41 Although, the authors report that impacts of adopted synthesis route could be potentially further reduced (by approximately 50%) if energy is used more efficiently, and hydrochloric acid is recovered and reused.31
Usefulness and limitations in view of emerging nature and technological maturity
LCA of emerging technologies is often regarded as exploratory because findings are directional rather than definitive.42 In like manner, the findings of this study need to be interpreted in view of an emerging nature of studied electrodes, particularly the aspects of a less known functional requirement of the electrodes in comparison to the whole energy storage product, and technology readiness level (TRL).
Technical requirements of novel electrodes as emerging and component-level technology are not explicit which makes any estimate of operational conditions used as a functional proxy for LCA analysis limited in its ability to comprehensively describe the technology. Therefore, the assumed values of current density and cycling stability used for the functional unit represent just one of the scenarios under which the electrodes could be applied. To address this limitation, it was important to encompass other functional setups, either by investigating multiple functional units or, as pursued here, by additionally exploring different scenarios to reflect on other likely alternatives. Amount of charge current based on electrodes' inherent capacity and cyclability correspond to applied current density which ultimately correlate with the power requirements of the final device, and is a critical parameter in applications such as memory back-up applications or auxiliary power sources in small appliances such as laptops or mobile phones.43
Furthermore, our findings have to reflect on technology's TRL which affects the potentials of estimated impacts to decrease with increased technological maturity and upscaling. This is particularly relevant for comparison between technologies at different TRLs as their potential to optimize use of materials may not adequately reflect their competitiveness at the point of analysis.37 In the current study, NCED-rGO appears at TRL level of four and NCCP at the level of five, which will likely make NCED-rGO more competitive as material develops. While comparing technologies at significantly different TRLs is not optimal,44 it is important to realize potential benefits to research and innovation of providing a certain benchmark to the development of new technology. Furthermore, different potentials of materials to undergo changes with increased scales means that the current relative contribution of different reagents, as shown in Fig. 3, could further change. These potentials need to be considered when interpreting current results and prioritizing resource strategies to reduce the impacts of the electrodes.
With uncertainties pertaining to assessment of emerging technology, especially in regard to data, the primary aim of our study was to aid the design of the electrode and accommodate fair comparison among competing electrodes of similar TRLs. Despite data and other limitations commonly claimed for assessment of emerging technologies,45,46 incorporating eco-efficiency considerations to early-stage research has great potential to steer product design across more environmentally plausible lines.42,47 Specifically, analysis at an early stage can navigate most convenient application of technology at which technological and environmental performance are maximized, which should ultimately be the goal in materials engineering for energy storage. LCA can assist this process by selecting the most benign and convenient material while maintaining technical requisites.
In our study, we established that under favorable operational conditions, NCED-rGO has clear potential to be eco-efficient. Particularly, as such observation comes in addition to some of the other practical aspects inherent to electrodeposition fabrication method itself, that could add a positive impact on the environment. Electrodeposition enables morphology-controlled deposition enabling adhesion on various conductive substrates without the need of binders thus conferring certain flexibility to the technique (i.e., material thickness, surface geometry), involves few process steps required to produce the final electrode including the absence of thermal treatment of pressurized systems, and can be scaled to various capacities with ease.48 These aspects result in shorter deposition times, safer working conditions and more durable use of process equipment, that could also positively affect environmental performance, but could not be captured in the present analysis. Nonetheless, this work reflects the need to increase capacity response and rate capability of electrodeposited Ni–Co hydroxide to produce more competitive results for this fabrication technique and NCED-rGO electrodes to be the most compelling choice. To this aim, strategies such as creating 3D hierarchical structures to optimize morphology may be undertaken.
This work may be extended to other synthesis techniques such as chemical vapor deposition or sol–gel synthesis among others, or compare Ni–Co hydroxide electrodes with other commonly used material for charge storage electrodes, such as manganese oxide or lithium-based electrodes. Extending LCA studies to other early-stage electrode material development could lead to environmentally-informed decisions in future research for energy storage.
Conclusions
The present study identifies the main environmental hotspots in the synthesis of NCED-rGO electrode and its environmental performance relative to baseline NCED electrode and benchmark NCCP electrode. The analysis aims to support further design and optimization of this electrode while giving a broader perspective on potentials of using rGO, and offering insight how this electrode performs in reference to current alternatives. The cradle-to-gate analysis was based on two functional parameters denoting capacity and lifetime, which are examined at different operational parameters of applied currents and criteria for end-of-life.
The findings suggest that the most dominant impacts in the fabrication of NCED-rGO come from electricity and cleaning, followed by GO, steel substrate and use of cobalt and nickel nitrates. Use of GO has shown to be advantageously applied to nickel–cobalt hydroxide electrodes as improved functionality of NCED-rGO electrode over NCED considerably outweighs added impacts from GO use. In comparison with the benchmark NCCP electrode, NCED-rGO is most competitive at 1 A g–1 current density and 30% capacity fade.
We argue that the findings of this study need to be interpreted in view of the emerging nature of these technologies. Potential impacts of the electrodes need to be interpreted in view of changing potentials for upscaling of reagent materials while comparative results need to be interpreted in view of technology readiness level of comparing electrodes and the functional requirement of energy storage applications. The study recommends several process and material management strategies for further optimization of NCED-rGO.
Conflicts of interest
There are no conflicts to declare.
Acknowledgements
Authors acknowledge funding support of IDS-FunMat and Erasmus + grant, CQE project and Fundação para a Ciência e Tecnologia (FCT) for the funding under the contracts M-ERA.NET/0004/2014 and UID/QUI/00100/2013t.
Notes and references
- J. H. Chae, X. Zhou and G. Z. Chen, From electrochemical capacitors to supercapatteries, Green, 2012, 2, 41–54 CAS.
- B. E. Conway, Transition from “supercapacitor” to “battery” behavior in electrochemical energy storage, J. Electrochem. Soc., 1991, 138, 1539–1548 CrossRef CAS.
-
C. J. Rydh, Environmental assessment of battery systems: critical issues for established and emerging technologies, Chalmers University of Technology, 2003 Search PubMed.
- Y. Wang, Y. Song and Y. Xia, Electrochemical capacitors: mechanism, materials, systems, characterization and applications, Chem. Soc. Rev., 2016, 45, 5925–5950 RSC.
- P. Prioteasa,
et al., Electrodeposition of Polypyrrole on Carbon Nanotubes/Si in the Presence of Fe Catalyst for Application in Supercapacitors, Rev. Chim., 2015, 66, 820–824 CAS.
- P. Simon and Y. Gogotsi, Materials for electrochemical capacitors, Nat. Mater., 2008, 7, 845 CrossRef CAS PubMed.
- T. Nguyen, M. Boudard, M. J. Carmezim and M. F. Montemor, NixCo1-x (OH)2 nanosheets on carbon nanofoam paper as high areal capacity electrodes for hybrid supercapacitors, Energy, 2017, 126, 208–216 CrossRef CAS.
- A. Adán-Más, R. G. Duarte, T. M. Silva, L. Guerlou-Demourgues and M. F. G. Montemor, Enhancement of the Ni-Co hydroxide response as energy storage material by electrochemically reduced graphene oxide, Electrochim. Acta, 2017, 240, 323–340 CrossRef.
- Y. Deng, L. Ma, T. Li, J. Li and C. Yuan, Life Cycle Assessment of Silicon-Nanotube-Based Lithium Ion Battery for Electric Vehicles, ACS Sustainable Chem. Eng., 2018, 7, 599–610 CrossRef.
- J. Peters, D. Buchholz, S. Passerini and M. Weil, Life cycle assessment of sodium-ion batteries, Energy Environ. Sci., 2016, 9, 1744–1751 RSC.
-
ISO-14044, Environmental Management—Life Cycle Assessment—requirements and guidelines, Int. Organ. Stand., 2006 Search PubMed.
-
ISO-14040, Environmental management-Life cycle assessment-Principles and framework, Int. Organ. Stand., 2006 Search PubMed.
- S. Saxena, C. Le Floch, J. MacDonald and S. Moura, Quantifying EV battery end-of-life through analysis of travel needs with vehicle powertrain models, J. Power Sources, 2015, 282, 265–276 CrossRef CAS.
- R. Chaari, O. Briat, J.-Y. Delétage, E. Woirgard and J.-M. Vinassa, How supercapacitors reach end of life criteria during calendar life and power cycling tests, Microelectron. Reliab., 2011, 51, 1976–1979 CrossRef.
- D. B. Murray and J. G. Hayes, Cycle testing of supercapacitors for long-life robust applications, IEEE Trans. Power Electron., 2015, 30, 2505–2516 Search PubMed.
- C. C. Streinz, A. P. Hartman, S. Motupally and J. W. Weidner, The effect of current and nickel nitrate concentration on the deposition of nickel hydroxide films, J. Electrochem. Soc., 1995, 142, 1084–1089 CrossRef CAS.
- C. Faure, C. Delmas, M. Fouassier and P. Willmann, Preparation and characterization of cobalt-substituted α-nickel hydroxides stable in KOH medium Part I. α′-hydroxide with an ordered packing, J. Power Sources, 1991, 35, 249–261 CrossRef CAS.
- C. Faure, C. Delmas and P. Willmann, Preparation and characterization of cobalt-substituted α-nickel hydroxide stable in KOH medium Part II. α-Hydroxide with a turbostratic structure, J. Power Sources, 1991, 35, 263–277 CrossRef CAS.
- F. Fu and Q. Wang, Removal of heavy metal ions from wastewaters: a review, J. Environ. Manage., 2011, 92, 407–418 CrossRef CAS PubMed.
- T. A. Kurniawan, G. Y. S. Chan, W.-H. Lo and S. Babel, Physico–chemical treatment techniques for wastewater laden with heavy metals, Chem. Eng. J., 2006, 118, 83–98 CrossRef CAS.
- J. Sun,
et al., The influential factors towards graphene oxides removal by activated carbons: Activated functional groups vs. BET surface area, J. Mol. Liq., 2018, 271, 142–150 CrossRef CAS.
- P. Chen and H. Li, Separation and Purification Technology
Removal of graphene oxide from water by floc-flotation, Sep. Purif. Technol., 2018, 202, 27–33 CrossRef CAS.
- J. Wang,
et al., Performances and mechanisms of Mg/Al and Ca/Al layered double hydroxides for graphene oxide removal from aqueous solution, Chem. Eng. J., 2016, 297, 106–115 CrossRef CAS.
- L. Duan,
et al., Removal of graphene oxide nanomaterials from aqueous media via coagulation: Effects of water chemistry and natural organic matter, Chemosphere, 2017, 168, 1051–1057 CrossRef CAS PubMed.
- C. Zhang, T. Li, Y. Yuan and J. Xu, An efficient and environment-friendly method of removing graphene oxide in wastewater and its degradation mechanisms, Chemosphere, 2016, 153, 531–540 CrossRef CAS PubMed.
- L. Ou, B. Song, H. Liang, J. Liu, X. Feng, B. Deng, T. Sun and L. Shao, Toxicity of graphene-family nanoparticles: a general review of the origins and mechanisms, Part. Fibre Toxicol., 2016, 13(1), 57 CrossRef PubMed.
-
M. J. Goedkoop, et al., A life cycle impact assessment method which comprises harmonised category indicators at the midpoint and the endpoint level, Report I: Characterisation, Leiden Univ., Leiden, Netherlands, 2008, accessed May 25, 2017 Search PubMed.
- R. K. Rosenbaum,
et al., USEtox—the UNEP-SETAC toxicity model: recommended characterisation factors for human toxicity and freshwater ecotoxicity in life cycle impact assessment, Int. J. Life Cycle Assess., 2008, 13, 532 CrossRef CAS.
- Y. Deng,
et al., Deriving characterization factors on freshwater ecotoxicity of graphene oxide nanomaterial for life cycle impact assessment, Int. J. Life Cycle Assess., 2017, 22, 222–236 CrossRef CAS.
-
M. Grayson, R. E. Kirk and D. F. OthmerKirk-Othmer encyclopedia of chemical technology – Chlorocarbons and Chlorohydrocarbons to Combustion Science, J. Wiley, 1996 Search PubMed.
- M. Cossutta, J. McKechnie and S. J. Pickering, A comparative LCA of different graphene production routes, Green Chem., 2017, 19, 5874–5884 RSC.
- W. Chen, L. Yan and P. R. Bangal, Preparation of graphene by the rapid and mild thermal reduction of graphene oxide induced by microwaves, Carbon, 2010, 48, 1146–1152 CrossRef CAS.
-
R. Frischknecht, et al., Overview and methodology, Ecoinvent Rep.vol. 1, 2007 Search PubMed.
-
N. Jungbluth, M. Stucki, K. Flury, R. Frischknecht and S. Büsser, Life cycle inventories of photovoltaics, ESU-services Ltd., Uster, CH, 2012, retrieved from http://www.esu-services Search PubMed.
- R. Arvidsson and S. Molander, Prospective Life Cycle Assessment of Epitaxial Graphene Production at Different Manufacturing Scales and Maturity, J. Ind. Ecol., 2017, 21, 1153–1164 CrossRef CAS.
- T. G. Gutowski,
et al., Thermodynamic analysis of resources used in manufacturing processes, Environ. Sci. Technol., 2009, 43, 1584–1590 CrossRef CAS PubMed.
- S. Gavankar, S. Suh and A. A. Keller, The role of scale and technology maturity in life cycle assessment of emerging technologies: a case study on carbon nanotubes, J. Ind. Ecol., 2015, 19, 51–60 CrossRef CAS.
- D. P. Dubal,
et al., Supercapacitors based on flexible substrates: an overview, Energy Technol., 2014, 2, 325–341 CrossRef.
- M. Wu, J. Gao, S. Zhang and A. Chen, Comparative studies of nickel oxide films on different substrates for electrochemical supercapacitors, J. Power Sources, 2006, 159, 365–369 CrossRef CAS.
- R. Frischknecht, LCI modelling approaches applied on recycling of materials in view of environmental sustainability, risk perception and eco-efficiency, Int. J. Life Cycle Assess., 2010, 15, 666–671 CrossRef CAS.
- N. I. Zaaba,
et al., Synthesis of graphene oxide using modified hummers method: solvent influence, Procedia Eng., 2017, 184, 469–477 CrossRef CAS.
- M. Villares, A. Işıldar, C. van der Giesen and J. Guinée, Does ex ante application enhance the usefulness of LCA? A case study on an emerging technology for metal recovery from e-waste, Int. J. Life Cycle Assess., 2017, 22, 1618–1633 CrossRef.
- M. Endo, T. Takeda, Y. J. Kim, K. Koshiba and K. Ishii, High power electric double layer capacitor (EDLC's); from operating principle to pore size control in advanced activated carbons, Carbon Lett., 2001, 1, 117–128 Search PubMed.
- S. Troy,
et al., Life Cycle Assessment and resource analysis of all-solid-state batteries, Appl. Energy, 2016, 169, 757–767 CrossRef.
- A. C. Hetherington, A. L. Borrion, O. G. Griffiths and M. C. McManus, Use of LCA as a development tool within early research: challenges and issues across different sectors, Int. J. Life Cycle Assess., 2014, 19, 130–143 CrossRef.
-
B. A. Wender and T. P. Seager, Towards prospective life cycle assessment: Single wall carbon nanotubes for lithium-ion batteries, in Sustainable Systems and Technology (ISSST) 2011 IEEE International Symposium on 1–4, IEEE, 2011 Search PubMed.
- B. A. Wender,
et al., Anticipatory life-cycle assessment for responsible research and innovation, J. Responsible Innov., 2014, 1, 200–207 CrossRef.
- W. Schwarzacher, Electrodeposition: a technology for the future, Electrochem. Soc. Interface, 2006, 15, 32–33 CAS.
Footnote |
† Electronic supplementary information (ESI) available. See DOI: 10.1039/c9ra02720c |
|
This journal is © The Royal Society of Chemistry 2019 |
Click here to see how this site uses Cookies. View our privacy policy here.