DOI:
10.1039/C9RA02052G
(Paper)
RSC Adv., 2019,
9, 18641-18651
Synthesis of a novel magnetic Caragana korshinskii biochar/Mg–Al layered double hydroxide composite and its strong adsorption of phosphate in aqueous solutions†
Received
17th March 2019
, Accepted 5th June 2019
First published on 13th June 2019
Abstract
Phosphate pollution of aquatic ecosystems is of great concern and requires the development of high-performance materials for effective pollution treatment. To realize efficient phosphate removal from aqueous solution, an easily separable magnetic (Fe3O4) Caragana korshinskii biochar/Mg–Al layered double hydroxide composite (denoted as FCB/MAC) was synthesized via two-step electro-assisted modification for the first time. Subsequently, the physical and chemical properties of FCB/MAC were characterized. Furthermore, the sorption mechanism for phosphate removal was investigated in detail. The results indicated that Fe3O4 and the Mg–Al layered double hydroxide were successfully embedded in the biochar matrix. Moreover, FCB/MAC exhibited a high phosphate adsorption capacity and excellent magnetic properties for easy recovery. The maximum phosphate sorption capacity of FCB/MAC was 252.88 mg g−1, which is much higher than the capacities of most magnetic phosphate adsorbents. In addition, the adsorption kinetics and isotherms indicated that phosphate adsorption by FCB/MAC was controlled by the pseudo-second-order kinetic model and the Langmuir–Freundlich isotherm model. The phosphate adsorption mechanism involves anion exchange, electrostatic attraction, and ligand exchange. After five adsorption–desorption cycles, the phosphate adsorption capacity of FCB/MAC was 25.71 mg g−1 with 51.43% removal efficiency and high recyclability. Thus, the composite prepared in this study is a promising adsorbent for phosphate removal from aqueous solution, and this work provides an excellent reference for constructing novel biochar-based phosphate adsorbents.
1. Introduction
Phosphate, as a basic nutrient, is vital for the growth of aquatic organisms. However, the excessive emission of phosphate into runoff systems has been confirmed to cause eutrophication, which can result in serious water quality deterioration and aquatic ecosystem collapse. Furthermore, phosphate pollution not only could increase the cost of water treatment and decrease the recreational value of waterways but also lead to the formation of algal blooms, which is harmful to human health owing to the production of cyanotoxins.1 Therefore, there is an immediate need to remove excess phosphates from aquatic ecosystems.
Biochar, a pyrogenic black carbon, is mainly produced from various carbon-rich biomass and waste sources by thermal decomposition processes under moderate temperatures and oxygen-limited environments.2 Owing to its wide environmental applications and excellent physicochemical properties, such as high surface porosity and numerous surface functional groups, biochar has been recognized as an promising adsorbent for the removal of various contaminants in solution.3 However, the net negative surface charge of biochar seriously limits its adsorption affinity towards anions such as phosphate.4,5 For example, the phosphate adsorption capacities of biochar from corn cobs, garden wood waste, and wood chips are 0.036, 0.132, and 0.296 mg g−1, respectively.6 In addition, difficulties in separating and recycling biochar from phosphate solutions have seriously restricted its application in wastewater remediation. Therefore, methods for simultaneously improving the phosphate adsorption capacity and recovery efficiency of biochar are essential.
With the aim of improving the phosphate adsorption capacity and recycling performance of biochar, some composites, such as MgFe2O4- and La/Fe3O4-modified biochar composites, have been produced by grafting iron and another metal onto biochar.7–11 However, the phosphate adsorption capacities of these metal-modified biochar composites were still low. However, the formation of magnetic layered double hydroxides (LDHs) on the surface of biochar can greatly improve the adsorption capacity because LDHs are cationic clays with large anion sorption capacities. LDHs consist of positively charged metal hydroxide layers and are generally described as [M1–x2+Mx3+(OH)2][An−]x/n·yH2O, where M2+ is a divalent cation (Mg2+, Cu2+, Zn2+, etc.), M3+ is a trivalent cation (Fe3+, Al3+, Cr3+, etc.), and An− is an interlayer anion (CO32−, NO3−, Cl−, OH−, etc.). In general, the x value ranges between 0.17 and 0.33.12 LDH composites have exhibited excellent abilities to adsorb pollutants.13–17 However, LDHs may have limited capabilities for removing anion contaminants owing to their tight layer stacking. Therefore, composite materials were prepared by introducing biochar onto the LDH frame, which can increase efficiency and reduce costs.
The methods for modifying biochar include microwave irradiation,18 hydrothermal coprecipitation,19,20 and electro-assisted modification.21 However, microwave irradiation is complex, and hydrothermal coprecipitation is time consuming when more than two chemicals are utilized. Furthermore, the general electro-assisted modification method gives products that are unstable. However, the electro-assisted modification method could provide some advantages, as it is simple to operate, rapid, and allows upgrading of the properties of modified biochar via the generation of crystalline structures. Therefore, there is an urgent need for an improved electro-assisted modification method.
In this study, the general electro-assisted modification method was optimized to facilitate both obtaining a biochar with magnetic properties and producing an LDH on the biochar surface. A novel strategy of fabricating magnetite (Fe3O4) and a Mg–Al LDH via a two-step electro-assisted modification process was developed. Magnetic Fe3O4 and the Mg–Al LDH were introduced to Caragana korshinskii biochar during the synthesis process to obtain a magnetic (Fe3O4) C. korshinskii biochar/Mg–Al LDH composite (denoted as FCB/MAC). The surface morphology, chemical composition, and magnetic properties of FCB/MAC were characterized. In addition, a series of batch experiments were carried out to investigate the effects of various parameters (initial pH, coexisting anions, contact time, and initial phosphate concentration) on the phosphate adsorption performance of FCB/MAC and elucidate the phosphate adsorption mechanism. Furthermore, the phosphate desorption behavior and recyclability of phosphate-loaded FCB/MAC were also evaluated.
2. Materials and methods
2.1. Materials
As a biochar precursor, C. korshinskii was collected from Shanghuang Village, Guyuan City, Ningxia Hui Autonomous Region, China. Owing to the low utilization rate of C. korshinskii (<40%), there is a high abundance of most C. korshinskii resources. All chemicals were of AR grade and were purchased from Sinopharm Chemical Reagent Co., Ltd. (China). All experimental solutions were prepared using deionized (DI) water. Iron and aluminum electrodes were purchased from Goodfellow Cambridge Ltd. (UK).
2.2. Adsorbent preparation
2.2.1. Biochar production. The C. korshinskii raw materials were washed and dried in a vacuum oven for 24 h. Then, the dry raw materials were cut into pieces smaller than 2 mm. The C. korshinskii pieces were pyrolyzed in a box-type atmosphere furnace (GF11Q-8, Nanjing Boyuntong Instrument Technology Co., Ltd., China) at 600 °C for 2 h with a heating rate of 10 °C min−1 under a constant N2 flow. A three-stage temperature-programmed thermal cracking method was used, with a uniform heating time of 1 h and a cooling time of 1 h. After the sample was cooled to room temperature, the biochar material was broken into powder using an agate mortar and pestle, and then sieved to a particle size of less than 0.1 mm.
2.2.2. Synthesis of Fe3O4 magnetic biochar. Magnetic C. korshinskii biochar was prepared using an electro-assisted modification procedure similar to a previously reported method.21 In brief, 3.0 g of biochar was dipped in 500 mL of a NaCl electrolyte (1.0 g L−1). For electro-assisted modification of the biochar, a current density (123.91 mA cm−2) was applied for 5 min using a power supply (FTS12-100 Programmable DC Power Supply, Faithtech Co., China) and iron electrodes (each electrode had dimensions of Φ 10 × 150 mm), which were placed perpendicularly in the electrolyte. The effective surface area and distance of each electrode were 32.20 cm2 and 6 cm, respectively. After the electro-assisted modification process, the precipitates were collected using a magnet, washed with DI water three times, and finally dried at 60 °C under a N2 environment.
2.2.3. Synthesis of FCB/MAC. First, 3.0 g of Fe3O4 magnetic biochar was dipped in 500 mL of a MgCl2 electrolyte (5.0 g L−1). A current density (123.91 mA cm−2) was applied for 5 min using a power supply and aluminum electrodes. The obtained compound was aged for 24 h at 80 °C and the solution pH was adjusted to 9.0 with 0.5 M solutions of H2SO4 and NaOH. Then, the precipitates were collected through centrifugation, washed with DI water, and oven-dried at 60 °C under a N2 environment.
2.3. Characterization
To investigate the surface morphology and structure of the modified biochar, scanning electron microscopy (FE-SEM, JEOL 7800F, Japan) was employed. Furthermore, the element contents were characterized by energy-dispersive X-ray spectroscopy (EDS). X-ray diffraction (XRD) analysis was performed to identify any crystalline structures in the biochar samples using a computer-controlled X-ray diffractometer (XRD-6100, Shimadzu, Japan). The BET surface area and total pore volume of the biochar samples were obtained using N2 sorption on an ASAP 2020 Plus HD88 instrument (Micromeritics Inc., USA). The surface elemental composition was examined by X-ray photoelectron spectroscopy (XPS, ESCALab Xi+, Thermo Scientific, USA). The magnetization curve of the product was measured using a MPMS-SQUID-094 vibrating sample magnetometer (VSM, Quantum Design, USA) with an applied field between −10
000 and 10
000 Oe at 298 K. Fourier transform infrared (FT-IR) spectra were recorded in the range of 4000–400 cm−1 using a FT-IR spectrometer (Nicolet iS50, Thermo Scientific, USA). Inductively coupled plasma mass spectrometry (ICP-MS, NexlON 350D, PerkinElmer, USA) was used to detect the leaching concentrations of Fe, Mg, and Al from the adsorbent. The zeta potential was analyzed using a zeta potential analyzer (Zetasizer Nano ZSE, Malvin, UK).
2.4. Phosphate adsorption experiments
Adsorption experiments were performed to determine the phosphate adsorption capacity of FCB/MAC. Specifically, a stock solution of 500 mgP L−1 was prepared by dissolving 2.195 g of KH2PO4 in 1.0 L DI water. Then, the stock solution was diluted to prepare phosphate solutions with various phosphate concentrations. First, the effect of pH on phosphate adsorption was investigated in the pH range 3.0–11.0 with an interval of 1.0. The pH values of the solutions were adjusted by adding 0.1 M HCl or NaOH. Then, 0.05 g of adsorbent was added to 50 mL of each phosphate solution (50 mgP L−1), and the reaction vessels were agitated using a shaker operating at 120 rpm at a constant temperature of 25 ± 1 °C for 12 h. The samples were immediately filtered using a syringe filter (0.45 μm syringe filter, PP filter media, Whatman, UK). The concentration of phosphate remaining in each solution was measured using a spectrophotometer (UV-2600, Shimadzu, Japan) at a wavelength of 880 nm according to a standard method. The adsorption amount of phosphate and the removal efficiency (%) were calculated using the following equations: |
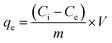 | (1) |
|
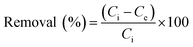 | (2) |
Here, qe is the amount of adsorbed phosphate per unit weight of adsorbent (mg g−1), m is the mass of the adsorbent (g), V is the volume of the phosphate solution (L), and Ci and Ce are the initial and equilibrium concentrations of phosphate (mg L−1), respectively.
The adsorption kinetics of phosphate on FCB/MAC were evaluated by preparing a series of solutions consisting of 0.25 g of FCB/MAC and 250 mL of phosphate solution (pH 3.0, 50 mgP L−1) in plastic bottles. The mixtures were fixed in the thermostatic oscillator at 120 rpm and 25 ± 1 °C, and 5 mL of the samples were removed from the mixtures at predetermined time intervals (5, 15, 30, 60, 120, 240, 360, 480, 600, and 720 min). The samples were immediately filtered using a nylon membrane syringe filter with a 0.45 μm pore size. Adsorption equilibrium isotherms were obtained at 25 ± 1 °C using 0.05 g of FCB/MAC in 50 mL of phosphate solutions (pH 3.0, 5–500 mgP L−1) in polyethylene centrifuge tubes. After mixing for 12 h (sufficient to reach adsorption equilibrium), the mixtures were filtered. The amount of phosphate adsorbed on FCB/MAC under each condition was calculated using eqn (1), and the experimental results were analyzed using three kinetic models (pseudo-first-order, pseudo-second-order, and intraparticle diffusion) and five isotherm models (Langmuir, Freundlich, Langmuir–Freundlich, Redlich–Peterson, and Temkin). The expressions of the employed models are listed in Table S1.†
The effects of coexisting anions on phosphate adsorption were evaluated by mixing 0.05 g of FCB/MAC with 50 mL of phosphate solutions (pH 3.0, 50 mgP L−1) containing equal concentrations of coexisting anions (Cl−, F−, NO3−, SO42−, and their mixture). A solution without coexisting anions was prepared as a blank. The mixtures were fixed in the thermostatic oscillator at 120 rpm and 25 ± 1 °C. After equilibration for 12 h, each mixture was filtered and the phosphate concentration was analyzed.
2.5. Phosphate desorption and reusability tests
To evaluate the recyclability of FCB/MAC, the exhausted adsorbent was collected from the solution using an ordinary magnet after the adsorption equilibrium was reached under the following conditions: adsorbent dosage = 0.05 g, initial phosphate concentration = 50 mg L−1, solution pH = 3.0, working volume = 50 mL, and contact time = 12 h. Then, the collected adsorbent was immersed in NaOH solutions with different concentrations (0.005, 0.01, 0.05, 0.1, and 0.5 M) and the mixtures were stirred at 120 rpm for 12 h to desorb phosphate from the adsorbent. Finally, the desorbed phosphate concentrations were measured and the desorption efficiency (%) was calculated using the following equation: |
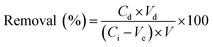 | (3) |
where Cd and Vd are the desorbed phosphate concentration (mg L−1) and the volume of solution (L) during the desorption test, respectively. In this study, each recyclability test consisted of five adsorption–desorption cycles.
3. Results and discussion
3.1. General characteristics of FCB/MAC
The physicochemical properties of the prepared biochar samples are presented in Table 1. Compared with raw biochar, the C and O contents of FCB/MAC decreased after Fe3O4 and Mg–Al LDH introduction, and the BET surface area and total pore volume of the biochar composite also decreased. In addition, the doping contents of Fe, Mg, and Al in FCB/MAC were 9.23, 18.97, and 7.09 wt%, respectively, and the atomic ratio between Mg and Al was approximately 3. Thus, the presence of magnetic Fe3O4 and the Mg–Al LDH were confirmed indirectly. The XRD pattern displayed sharp and symmetric principal diffraction peaks at low 2θ angles, in good agreement with those of clay minerals containing an LDH and synthetic well-crystallized hydrotalcite-like compounds (Fig. 1a). The diffraction peaks observed at 2θ = 11.3° (003), 23.0° (006), 35.6° (009), and 61.2° (110) corresponded to the characteristic peaks of a Mg–Al LDH (JCPDS no. 50-1684). The interlayer spacing of the (003) plane (d003) was 0.7834 nm and d006 was 0.3912 nm, which is consistent with the values reported in the literature.22–24 The peaks at 2θ = 30.1° (220), 43.1° (400), 53.5° (422), 57.0° (511), and 74.1° (533) were consistent with the characteristic peaks of Fe3O4 (JCPDS no. 19-0629). The sharpness and intensity of the peaks indicated that FCB/MAC had a highly crystalline structure. Thus, the XRD analysis confirmed the successful synthesis of FCB/MAC, which is in good agreement with the subsequent FT-IR spectral analysis.
Table 1 Physiochemical properties of the prepared biochar materials
Material |
C (wt%) |
O (wt%) |
Cl (wt%) |
Fe (wt%) |
Mg (wt%) |
Al (wt%) |
Surface area (m2 g−1) |
Total pore volume (cm3 g−1) |
Saturated magnetization (emu g−1) |
Raw biochar |
58.43 |
26.67 |
13.68 |
— |
1.22 |
— |
133.49 |
0.09 |
— |
FCB/MAC |
36.52 |
17.96 |
10.23 |
9.23 |
18.97 |
7.09 |
27.01 |
0.03 |
32.90 |
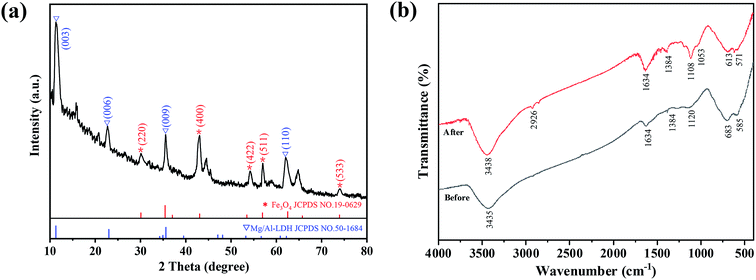 |
| Fig. 1 (a) XRD pattern, (b) FT-IR spectra data for FBC/MAC before and after phosphate adsorption. | |
FT-IR spectroscopy was used to further identify specific functional groups in FCB/MAC (Fig. 1b). The broad bands at 3435 and 1634 cm−1 are attributed to the stretching vibrations of OH groups in the brucite-like layer and the bending vibrations of water molecules in the interlayer, respectively. The band at 1384 cm−1 is assigned to the vibration mode of CO23−, which suggested that CO23− was successfully introduced into the interlayer of the Mg–Al LDH by the absorption of CO2 during the preparation procedure.25,26 Moreover, the bands between 500 and 700 cm−1 are attributed to the characteristic lattice vibrations of MgO and Al2O3. Therefore, the FT-IR spectral analysis confirmed the presence of intercalated CO32− and water molecules in the LDH interlayer.
To determine the magnetism of FCB/MAC, the magnetic-field-dependent behavior was measured using a VSM at room temperature. As shown in Table 1, the specific saturation magnetization (Ms) of FCB/MAC was 32.9 emu g−1, which is lower than the reported value of bulk Fe3O4, i.e., 92 emu g−1.27 The reduction of the Ms value of FCB/MAC is mainly attributable to the smaller size of Fe3O4 nanoparticles and the relatively low amount of Fe3O4 loaded on FCB/MAC. The magnetic remanence (Mr) of FCB/MAC was almost zero. This small Mr value indicates that FCB/MAC exhibited superparamagnetic behavior. Interestingly, the magnetic nanocomposites suspended in aqueous solution could be easily collected and separated by a nearby permanent magnet (inset digital picture, Fig. S1†).
The comprehensive elemental composition and electronic states of FCB/MAC were investigated using XPS (Fig. 2). The XPS spectra of FCB/MAC revealed that iron, magnesium, aluminum, carbon, oxygen, and chlorine were the predominant elements. The photoelectron lines at binding energy (EB) values of approximately 711.0, 1303.3, 74.5, 284.1, 531.8, and 200.5 eV were attributed to Fe 2p, Mg 1s, Al 2p, C 1s, O 1s, and Cl 2p, respectively (Fig. 2a). Furthermore, a P 2p peak with a binding energy of 133.6 eV was clearly observed for phosphate-loaded FCB/MAC, which demonstrated the successful adsorption of phosphate on FCB/MAC. The XPS analysis further confirmed the presence of magnetite on the surface of FCB/MAC. In the Fe 2p spectrum (Fig. 2b), the peaks at 710.8 and 724.4 eV were attributed to Fe 2p3/2 and Fe 2p1/2, respectively.28,29 The spin–orbital splitting of the Fe 2p peak was broad owing to the small chemical shift between Fe2+ and Fe3+, both of which are present in Fe3O4.30 The absence of a satellite peak at approximately 719 eV, a characteristic of Fe2O3, was indicative of the formation of a Fe3O4 phase in FCB/MAC, in good agreement with the XRD results.31
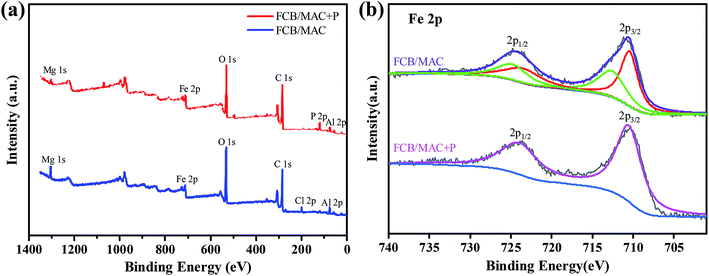 |
| Fig. 2 The XPS spectra of FCB/MAC before and after adsorption: (a) wide spectrum, (b) Fe 2p. | |
The morphological and structural features of biochar (Fig. 3a) and FCB/MAC (Fig. 3b) were characterized by SEM. The biochar surface was relatively smooth with some cracks and pores. After the two-step electro-assisted modification process, some thin layered flocculent materials and small particles were dispersed on the surface of FCB/MAC, which were presumably the Mg–Al LDH and magnetic Fe3O4 particles. SEM-EDS elemental mapping further confirmed the presence of Fe3O4 and the Mg–Al LDH on the biochar surface, as shown in Fig. 3c, as O, Cl, Fe, Mg, and Al were clearly distributed on the FCB/MAC surface.
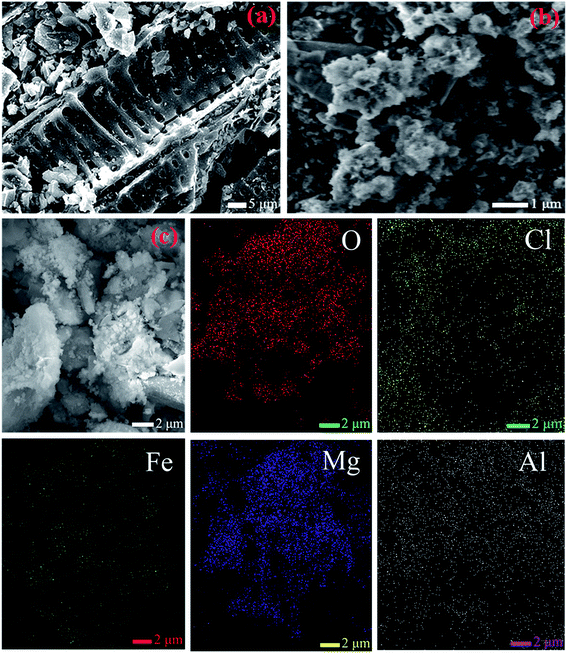 |
| Fig. 3 SEM images of (a) raw biochar, (b) FCB/MAC and (c) the selected area of FCB/MAC for EDS analysis and EDS elemental mapping spectra of O, Cl, Fe, Mg and Al. | |
3.2. Effect of pH on phosphate adsorption
Generally, pH is considered an important parameter that influences the adsorption properties at water–adsorbent interfaces. The phosphate adsorption capacities of FCB/MAC and the final solution pH (the pH of the solution after adsorption equilibrium) within the pH range 3.0–11.0 are shown in Fig. S2a.† It was clearly found that the adsorption of phosphate on FCB/MAC was highly dependent on the solution pH and the maximum adsorption amount of phosphate gradually decreased with the increase of the solution pH value from 3 to 11. Therefore, the ideal pH value was chosen as 3. Furthermore, to determine whether any dissolution of Fe, Mg, and Al from FCB/MAC occurred during utilization, 0.05 g of FCB/MAC was immersed in 50 mL of DI water at pH 3.0 or 11.0 for 12 h. The ICP-MS results showed that no Fe, Mg, or Al could be detected in the supernatant, indicating that these elements were strongly bound in the biochar matrix. Thus, FCB/MAC exhibited excellent stability in both acidic and basic solutions.32
When the solution pH is lower than the point of zero charge (pHpzc), the surface of the adsorbent is protonated and becomes more positively charged with decreases in pH, which would promote the adsorption of phosphate anions. However, at pH values higher than the pHpzc, phosphate adsorption on the adsorbent would be inhibited owing to increased electrostatic repulsion between the adsorbent and phosphate ions. Moreover, with further increases in the solution pH, the hydroxyl ions would complete with phosphate species for the adsorption sites on the adsorbent surface, which would further reduce phosphate adsorption.10,11 To clarify the influence of pH on phosphate adsorption, the zeta potential values of FCB/MAC were measured at different pH values. As shown in Fig. S2b,† the pHpzc of FCB/MAC is approximately 8.21. Therefore, within the pH range 3.0–7.0, FCB/MAC was protonated and positively charged, which would promote the adsorption of phosphate species H2PO4− or HPO42− via electrostatic attraction, leading to a higher amount of adsorbed phosphate. However, when the pH was further increased, FCB/MAC was deprotonated and became negatively charged, which would decrease the phosphate adsorption capacity.33 Overall, these results indicated that electrostatic attraction plays an important role in the phosphate adsorption behavior of FCB/MAC.
3.3. Effect of coexisting anions on phosphate adsorption
To investigate the effect of coexisting anions on the phosphate adsorption, adsorption experiments were conducted using phosphate solutions (pH 3, 50 mgP L−1) with equal concentrations of competing anions (Fig. 4). It was obvious that the presence of Cl−, NO3−, and SO42− had a negligible influence on phosphate adsorption, as the amount of phosphate adsorbed by FCB/MAC was only reduced by 0.8, 1.3, and 0.7 mg g−1, respectively. These anions had an insignificant effect on the phosphate adsorption process because of the strong and stable interactions between the LDH and phosphate, including electrostatic attraction, anion exchange, and the formation of inner-sphere complexes with metal hydroxides.34,35 Compared with Cl−, NO3−, and SO42−, F− had a more negative influence on phosphate adsorption, with the amount of phosphate adsorbed reduced by 3.9 and 5.7 mg g−1 for F− and an anion mixture, respectively. The inhibition of phosphate adsorption by F− is likely due to strong competition between phosphate and F− for the binding sites on the adsorbent surface. Similar results have been previously observed for other adsorbents.32 However, overall, coexisting anions have little influence on phosphate adsorption on FCB/MAC. Thus, the selectivity of this adsorbent for phosphate is high, which is important for practical applications.
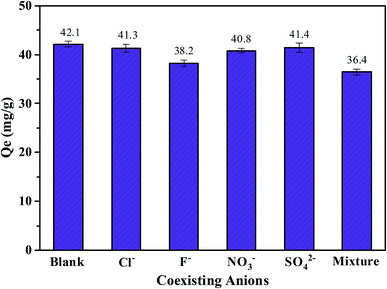 |
| Fig. 4 Effect of coexisting anions on the phosphate adsorption by FCB/MAC. Adsorption conditions: initial phosphate concentration, 50 mg L−1; solution pH, 3.0; temperature, 25 °C; FCB/MAC dosage, 0.05 g; working volume, 50 mL; contact time, 12 h. | |
3.4. Adsorption kinetics
The amounts of phosphate adsorbed on FCB/MAC as a function of contact time are shown in Fig. 5a. Clearly, phosphate adsorption on FCB/MAC occurred rapidly, reaching a phosphate adsorption capacity of 40.1 mg g−1 after 2 h, which is approximately 80% of the equilibrium adsorption capacity. The initial rapid adsorption process could be attributed to electrostatic attraction, which led to the fast transportation of phosphate from the solution onto the surface of the adsorbent. The subsequent slow adsorption process indicated that ion exchange and ligand exchange were the dominant mechanisms of phosphate adsorption.1,36
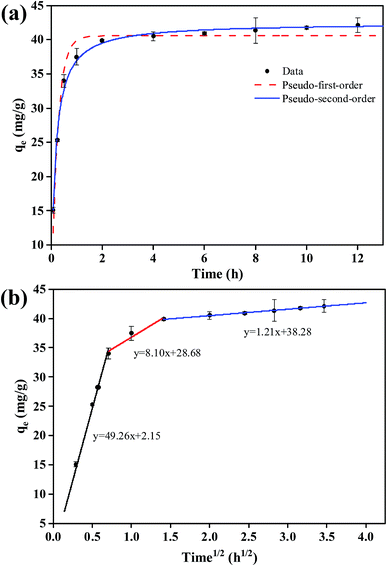 |
| Fig. 5 Kinetics of phosphate adsorption on FCB/MAC: (a) experimental data and fitting for pseudo-first-order and pseudo-second-order models and (b) intraparticle diffusion model. Adsorption conditions: initial phosphate concentration, 50 mg L−1; solution pH, 3.0; temperature, 25 °C; FCB/MAC dosage, 0.25 g; working volume, 250 mL; contact time, 12 h. | |
The kinetic data for phosphate adsorption were analyzed using pseudo-first-order, pseudo-second-order, and intraparticle diffusion models. The fitting curves for the pseudo-first-order and pseudo-second-order models are presented in Fig. 5a and the kinetic parameters obtained using these two kinetic models are summarized in Table 2. It was found that the correlation coefficient (R2) of the pseudo-second-order kinetic model was higher than that of the pseudo-first-order kinetic model, suggesting that the phosphate adsorption process was better described by the pseudo-second-order kinetic model.
Table 2 Best-fit parameter values from model simulations of phosphate adsorption kinetics and isotherms
|
Parameter 1 |
Parameter 2 |
Parameter 3 |
R2 |
Adsorption kinetics |
Pseudo-first-order |
k1 = 4.1160 (h−1) |
qe = 40.5612 (mg g−1) |
|
R2 = 0.9615 |
Pseudo-second-order |
k2 = 0.1569 (g mg−1 h−1) |
qe = 42.4511 (mg g−1) |
|
R2 = 0.9932 |
Intraparticle diffusion |
ki1 = 49.2608 (mg g−1 h1/2) |
C1 = 2.1493 (mg g−1) |
|
R2 (ki1) = 0.9785 |
ki2 = 8.1021 (mg g−1 h1/2) |
C2 = 28.6793 (mg g−1) |
|
R2 (ki2) = 0.9149 |
ki3 = 1.0951 (mg g−1 h1/2) |
C3 = 38.2825 (mg g−1) |
|
R2 (ki3) = 0.9967 |
![[thin space (1/6-em)]](https://www.rsc.org/images/entities/char_2009.gif) |
Adsorption isotherms |
Langmuir |
KL = 0.0464 (L mg−1) |
Qm = 248.6390 (mg g−1) |
|
R2 = 0.9916 |
Freundlich |
KF = 49.4181 (mg g−1) |
1/n = 0.2921 |
|
R2 = 0.8948 |
Langmuir–Freundlich |
KLF = 0.0537 (L mg−1) |
Qm = 252.8803 (mg g−1) |
1/n = 0.9368 |
R2 = 0.9925 |
Redlich–Peterson |
KR = 12.1571 (L mg−1) |
a = 0.0375 (L mg−1) |
1/n = 0.9566 |
R2 = 0.9924 |
Temkin |
b = 0.0964 (J g mg−1) |
a = 1.8360 (L mg−1) |
|
R2 = 0.9173 |
More importantly, as clearly shown in Fig. 5b, the adsorption kinetics (plots of qe versus t1/2) exhibited multilinearity. The first region is sharper and quicker, which can be ascribed to the presence of many available adsorption sites in the adsorbent and a relativity high concentration of phosphate in the solution.37 Then, the second region represents phosphate molecules diffusing into the pores of the adsorbent, suggesting that intraparticle diffusion is the rate-limiting step of this stage. Finally, the third region can be attributed to the equilibrium stage, where intraparticle diffusion becomes slow owing to the low phosphate concentration in the solution.38 In addition, the multilinear plots indicate that two or more steps (multistep adsorption) occur during the phosphate adsorption process on FCB/MAC. The kinetic parameters obtained from the kinetic models (Table 2) show that the intraparticle diffusion model fits the experimental data well (R2 = 0.99). This finding indicates that intraparticle diffusion is involved in the adsorption process but other mechanisms also play an important role. Therefore, the kinetic and intraparticle diffusion analyses confirmed that the overall behavior of the phosphate adsorption process on FCB/MAC is likely controlled by multiple parallel processes, involving rapid external surface adsorption and diffusion into the interior of the prepared biochar.39
3.5. Adsorption isotherms
The adsorption isotherms for phosphate adsorption on FCB/MAC are presented in Fig. 6. As shown, with an increase of the initial phosphate concentration, the adsorption capacity of FCB/MAC gradually increases. The related parameters calculated from the five models are listed in Table 2. Clearly, almost all the isotherm models reproduced the adsorption data well, except the Freundlich equation. However, the Langmuir–Freundlich (highest R2 value of 0.9925) and Redlich–Peterson models matched the experimental data better than the other models, suggesting that the interaction between phosphate and FCB/MAC could be affected by both the Langmuir and Freundlich processes. This result is consistent with the kinetics study and suggests that the adsorption of phosphate on FCB/MAC is controlled by multiple processes, involving simultaneous physical and chemical adsorption.40,41
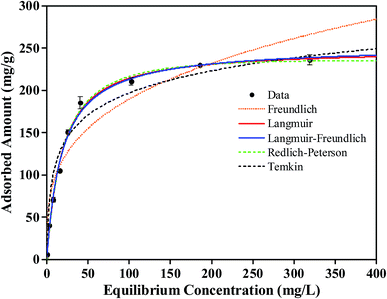 |
| Fig. 6 Adsorption isotherm data and modeling for phosphate on the FCB/MAC. Symbols are experimental data, and lines are model results. Adsorption conditions: initial phosphate concentration range, 5–500 mg L−1; solution pH, 3.0; temperature, 25 °C; FCB/MAC dosage, 0.05 g; working volume, 50 mL; contact time, 12 h. | |
Herein, the adsorption of phosphate on FCB/MAC occurs by ion exchange with both the intercalated anions of the Mg–Al LDH and ligand exchange reactions with the surface groups. Typically, there are three steps during the phosphate adsorption process on the Mg–Al LDH: (1) external mass transfer between the external surface of the Mg–Al LDH and the surrounding fluid phase; (2) intraparticle transport within the LDH; and (3) chemisorption.42 It has been suggested that lower molecular weight phosphates can easily enter the mesoporous Mg–Al LDH and undergo ligand exchange reactions with the surface groups.43 The synergistic interactions of the Mg–Al LDH with phosphate lead to the highly efficient adsorption of phosphate on FCB/MAC. Notably, the theoretical maximum adsorption capacity (qm) of FCB/MAC was calculated to be 252.88 mg g−1 at 25 ± 1 °C using the Langmuir–Freundlich isotherm, which far exceeds the adsorption capacity of a pure Fe3O4@Mg–Al LDH, as reported by Yan et al.44 These results clearly indicated that FCB/MAC is a promising adsorbent for phosphate adsorption. The significant increase of phosphate adsorption achieved by grafting an LDH on a Fe3O4 magnetic biochar compared with magnetic biochars modified with single metals suggested that the combination of metal modification and the positively charged Mg–Al LDH provides considerably enhanced anion adsorption. For comparison, Table 3 lists the phosphate adsorption capacities of other adsorbents, such as magnetite-particle-grafted orange peel biochar (1.24 mg g−1),7 MgO-impregnated magnetic biochar (121.25 mg g−1),8 La(OH)3-modified magnetic pineapple biochar (101.16 mg g−1),9 and MgFe2O4/biochar magnetic composite (159.24 mg g−1).10 Obviously, FCB/MAC is a better phosphate adsorbent than these previously reported systems.
Table 3 Comparison of phosphate adsorption capacities with other reported adsorbentsa
Adsorbent |
IC (mg L−1) |
pH |
t (h) |
RT (°C) |
Isotherm |
AM |
AC (mg g−1) |
References |
IC, initial concentration; RT, removal temperature; L–F, Langmuir–Freundlich model; D–R, Dubinin–Radushkevich model; L, Langmuir model; F, Freundlich model; S, Sips model; AM, adsorption mechanisms; IC, inner-sphere complexation; AE, anion exchange; EA, electrostatic attraction; LE, ligand exchange; AC, adsorption capacity; NR, no report. |
Magnetite particles grafted orange peel biochar |
0–12 |
NR |
24 |
25 |
L |
NR |
1.24 |
7 |
MgO-impregnated magnetic biochar |
5–500 |
4.0 |
12 |
23 |
L |
EA and IC |
121.25 |
8 |
La(OH)3-modified magnetic pineapple biochar |
100–400 |
NR |
24 |
30 |
L |
EA, LE and IC |
101.16 |
9 |
MgFe2O4/biochar magnetic composites |
2–163 |
3.0 |
12 |
20 |
S |
IC |
159.24 |
10 |
La/Fe3O4-biochar |
75 |
6.1 |
15 |
25 |
D-R |
EA and IC |
25.00 |
16 |
Ce/Fe3O4-biochar |
75 |
6.1 |
15 |
25 |
F |
EA and IC |
18.75 |
|
Ferric oxides loaded cotton stalks biochar |
7 |
NR |
24 |
25 |
NR |
AE and EA |
0.31 |
47 |
Fe3O4@Mg–Al layered double hydroxide |
13 |
3.0 |
1 |
25 |
L |
AE, LE and EA |
10.30 |
44 |
FCB/MAC |
5–500 |
3.0 |
12 |
25 |
L-F |
AE, EA, and LE |
252.88 |
This study |
3.6. XPS analysis
To further explore the sorption mechanism of phosphate on the FCB/MAC adsorbent, the adsorbent before and after phosphate adsorption was subjected to XPS analysis. Fig. 7 shows the P 2p, O 1s, Mg 1s, and Al 2p XPS spectra. Based on the binding energies of various phosphorus species, the P 2p XPS spectra (Fig. 7a) could be divided into two peaks corresponding to M–P (phosphorus bonded to metal) and M–O–P (phosphorus bonded to metal oxide), indicating a strong affinity between phosphate and FCB/MAC. For the pristine adsorbent, the O 1s XPS spectrum (Fig. 7b) could be fitted to three peaks, namely, O2− at 529.5 eV, OH− at 530.4 eV, and CO32− at 531.4 eV.16,45,46 After phosphate adsorption, the area ratio of O2− decreased from 26.40% to 26.05%, likely owing to the group exchange of M–O (oxygen bonded to metal) with phosphate. The area ratio of CO32− also decreased from 37.89% to 31.5%, likely owing to the exchange of phosphate with CO32−. Furthermore, the area ratio of OH− increased from 35.71% to 42.45%, corresponding to the one or two P–OH groups contributed by different H2PO4−/HPO42− species.17 Thus, it is believed that the metal hydroxyl sites are capable of ligand exchange with the target phosphates. The Mg 1s and Al 2p XPS spectra of FCB/MAC are displayed in Fig. 7c and d, respectively. The binding energy of Mg 1s changed from 1304.3 to 1303.6 eV, whereas that of Al 2p changed from 74.9 to 75.7 eV, illustrating that the Mg and Al metal hydroxides participated in the adsorption process.16 Furthermore, the Fe 2p XPS spectra (Fig. 2b) of FCB/MAC before and after adsorption were similar, indicating that the iron oxide did not participate in the adsorption process. These analyses are consistent with anion exchange and ligand exchange being involved in the phosphate adsorption process.
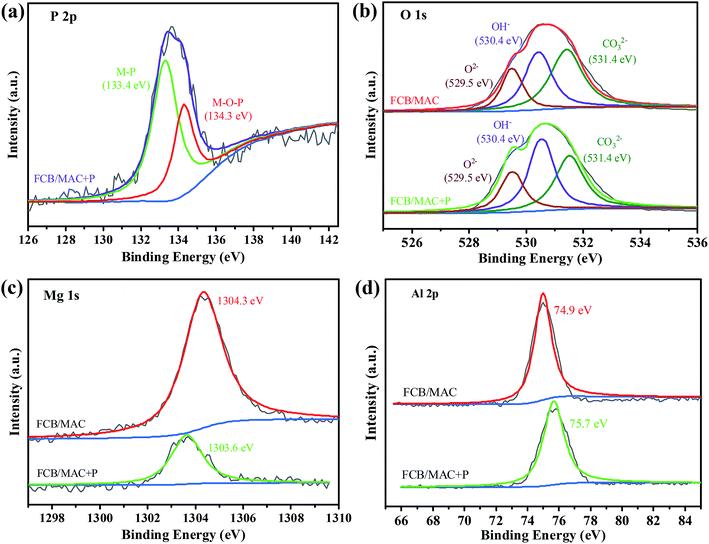 |
| Fig. 7 (a) The XPS spectra of P 2p. The XPS analysis of the O 1s (b), Mg 1s (c), Al 2p (d) before and after phosphate adsorption. | |
3.7. Adsorbent regeneration and phosphate readsorption
The stability and the recyclability of an adsorbent are vital for its industrial application. As mentioned in Section 3.2, the phosphate adsorption capacity of FCB/MAC decreased drastically as the solution pH increased. This result indicated that alkaline conditions (pH > pHpzc) can facilitate the desorption of phosphate from exhausted adsorbents. Thus, the desorption of phosphate from phosphate-loaded FCB/MAC was performed at different NaOH concentrations (0.005–0.5 M), and the results are shown in Fig. 8a. The desorption efficiency increased gradually from 19.95% to 81.76% with the increase of the NaOH concentration from 0.005 to 0.1 M. However, further increases in the NaOH concentration had no significant effect on the desorption efficiency. Therefore, 0.1 M NaOH was chosen as the optimal condition for the regeneration process. As shown in Fig. 8b, even though the phosphate adsorption performance of FCB/MAC gradually decreased with subsequent adsorption–desorption cycles, a certain adsorption capacity (approximately 25.71 mg g−1 with 51.43% removal efficiency) was still maintained after five cycles, which is better than the performance other magnetic adsorbents. Thus, the recyclability test demonstrated that FCB/MAC could be effectively separated without any weight loss using a magnetic field and easily reused by applying a NaOH solution as an eluent for efficient phosphate removal. Subsequently, as a suggestion for recycling of the exhausted material, the exhausted FCB/MAC can be acidified to obtain the raw biochar. The raw biochar can again be subjected to the two-step electro-assisted modification process to produce FCB/MAC, thus achieving recycling of the exhausted material.
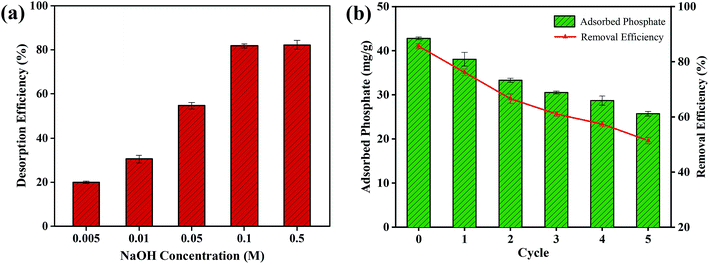 |
| Fig. 8 (a) Desorption performance at different NaOH concentrations. (b) Cyclic stability of FCB/MAC regenerated by 0.1 M NaOH. | |
4. Conclusions
FCB/MAC was successfully prepared by a two-step electro-assisted modification process for the first time. This process enriches the technology that is available for modifying biochar. FCB/MAC provides an ideal combination of the adsorption features of biochar with the magnetic properties of Fe3O4 and the adsorption properties of Mg–Al LDH. FCB/MAC showed a higher phosphate adsorption capacity (252.88 mg g−1) than most previously reported adsorbents. Furthermore, FCB/MAC showed good selectivity, as the presence of coexisting anions, including Cl−, F−, NO3−, and SO42−, had little influence on the removal of phosphate. The adsorption kinetics of phosphate were well represented by the pseudo-second-order and intraparticle diffusion models and the adsorption isotherms were fitted best by the Langmuir–Freundlich model. The phosphate adsorption mechanism involved electrostatic attraction, ligand exchange with surface groups, and anion exchange with the interlayer anions of FCB/MAC. Phosphate-loaded FCB/MAC exhibited excellent magnetic recovery and phosphate desorption. Therefore, FCB/MAC is an optimal reusable hybrid adsorbent and has considerable potential for phosphate removal in practical applications.
Conflicts of interest
There are no conflicts to declare.
Acknowledgements
This work was supported by the National Key Research and Development Plan of China (2016YFC0501702, 2017YFC0504504), the National Natural Science Foundation of China (41571225), and Science and technology Service Network Initiative of the Chinese Academy of Sciences (KFJ-STS-ZDTP-012). We also thank the instrument analysis center of Xi'an Jiaotong University (XJTU, China).
References
- J. Lalley, C. Han, X. Li, D. D. Dionysiou and M. N. Nadagouda, Chem. Eng. J., 2016, 284, 1386–1396 CrossRef CAS.
- M. I. Inyang, B. Gao, Y. Yao, Y. Xue, A. Zimmerman, A. Mosa, P. Pullammanappallil, Y. S. OK and X. Cao, Crit. Rev. Environ. Sci. Technol., 2016, 46, 406–433 CrossRef CAS.
- S. B. Liu, X. F. Tan, Y. G. Liu, Y. L. Gu, G. M. Zeng, X. J. Hu, H. Wang, L. Zhou, L. H. Jiang and B. B. Zhao, RSC Adv., 2016, 6, 5871–5880 RSC.
- Y. Yao, B. Gao, J. Chen, M. Zhang, M. Inyang, Y. Li, A. Alva and L. Yang, Bioresour. Technol., 2013, 138, 8–13 CrossRef CAS PubMed.
- S. Wan, S. Wang, Y. Li and B. Gao, J. Ind. Eng. Chem., 2017, 47, 246–253 CrossRef CAS.
- B. Micháleková-Richveisová, V. Frišták, M. Pipíška, L. Ďuriška, E. Moreno-Jimenez and G. Soja, Environ. Sci. Pollut. Res., 2016, 24, 463–475 CrossRef PubMed.
- B. Chen, Z. Chen and S. Lv, Bioresour. Technol., 2011, 102, 716–723 CrossRef CAS PubMed.
- R. Li, J. J. Wang, B. Zhou, M. K. Awasthi, A. Ali, Z. Zhang, A. H. Lahori and A. Mahar, Bioresour. Technol., 2016, 215, 209–214 CrossRef CAS PubMed.
- T. Liao, T. Li, X. Su, X. Yu, H. Song, Y. Zhu and Y. Zhang, Bioresour. Technol., 2018, 263, 207–213 CrossRef CAS PubMed.
- K. W. Jung, S. Lee and Y. J. Lee, Bioresour. Technol., 2017, 245, 751–759 CrossRef CAS PubMed.
- L. Wang, J. Wang, C. He, W. Lyu, W. Zhang, W. Yan and L. Yang, Colloids Surf., A, 2019, 561, 236–243 CrossRef CAS.
- M. K. R. Reddy, Z. P. Xu, G. Q. Lu and C. J. Diniz da Costa, Ind. Eng. Chem. Res., 2006, 45, 7504–7509 CrossRef.
- K. H. Goh, T. T. Lim and Z. Dong, Water Res., 2008, 42, 0–1368 CrossRef CAS PubMed.
- H. Pang, Y. Wu, S. Huang, C. Ding, S. Li, X. Wang, S. Yu, Z. Chen, G. Song and X. Wang, Inorg. Chem. Front., 2018, 5, 2657 RSC.
- S. Yu, Y. Liu, Y. Ai, X. Wang, R. Zhang, Z. Chen, Z. Chen, G. Zhao and X. Wang, Environ. Pollut., 2018, 242, 1–11 CrossRef CAS PubMed.
- S. Yu, X. Wang, Y. Liu, Z. Chen, Y. Wu, Y. Liu, H. Pang, G. Song, J. Chen and X. Wang, Chem. Eng. J., 2019, 365, 51–59 CrossRef CAS.
- Q. Zhang, J. Teng, G. Zou, Q. Peng, Q. Du, T. Jiao and J. Xiang, Nanoscale, 2016, 8, 7085 RSC.
- G. Gollavelli, C. C. Chang and Y. C. Ling, ACS Sustainable Chem. Eng., 2013, 1, 462–472 CrossRef CAS.
- S. Nethaji, A. Sivasamy and A. B. Mandal, Bioresour. Technol., 2013, 134, 94–100 CrossRef CAS PubMed.
- S. Yu, L. Yin, H. Pang, Y. Wu, X. Wang, P. Zhang, B. Hu, Z. Chen and X. Wang, Chem. Eng. J., 2018, 352, 360–370 CrossRef CAS.
- K. W. Jung, M. J. Hwang, T. U. Jeong and K. H. Ahn, Bioresour. Technol., 2015, 191, 342–345 CrossRef CAS PubMed.
- F. Cavani, F. Trifiro and A. Vaccari, Catal. Today, 1991, 11, 173–301 CrossRef CAS.
- Y. Chen, F. Li, S. Zhou, J. Wei, Y. Dai and Y. Chen, J. Solid State Chem., 2010, 183, 2222–2226 CrossRef CAS.
- S. Özgümüş, M. K. Gök, A. Bal and G. Güçlü, Chem. Eng. J., 2013, 223, 277–286 CrossRef.
- Y. Li, B. Gao, T. Wu, D. Sun, X. Li, B. Wang and F. Lu, Water Res., 2009, 43, 3067–3075 CrossRef CAS PubMed.
- L. Li, R. Li, S. Gai, F. He and P. Yang, J. Mater. Chem. A, 2014, 2, 8758–8765 RSC.
- X. Peng, Z. Luan and H. Zhang, Chemosphere, 2006, 63, 300–306 CrossRef CAS PubMed.
- F. R. Costa, A. Leuteritz, U. Wagenknecht, M. A. D. Landwehr, D. Jehnichen, L. Haeussler and G. Heinrich, Appl. Clay Sci., 2009, 44, 7–14 CrossRef CAS.
- X. Lu, Y. Yu, L. Chen, H. Mao, H. Gao, J. Wang and W. Yen, Nanotechnology, 2005, 16, 1660–1665 CrossRef CAS.
- S. Shanmugam, T. Nakanishi and T. Osaka, J. Electrochem. Soc., 2009, 156, K121–K127 CrossRef CAS.
- D. Zhang, Z. Liu, S. Han, C. Li, B. Lei, M. P. Stewart, J. M. Tour and C. Zhou, Nano Lett., 2004, 4, 2151–2155 CrossRef CAS.
- R. Li, J. J. Wang, B. Zhou, M. K. Awasthi, A. Ali, Z. Zhang, L. A. Gaston, A. H. Lahori and A. Mahar, Sci. Total Environ., 2016, 559, 121–129 CrossRef CAS PubMed.
- B. Wu, L. Fang, J. D. Fortner, X. Guan and I. M. C. Lo, Water Res., 2017, 126, 179–188 CrossRef CAS PubMed.
- F. Hu, M. Wang, X. Peng, F. Qiu, T. Zhang, H. Dai, Z. Liu and Z. Cao, Colloids Surf., A, 2018, 555, 314–323 CrossRef CAS.
- J. Lu, H. Liu, X. Zhao, W. Jefferson, F. Cheng and J. Qu, Colloids Surf., A, 2014, 455, 11–18 CrossRef CAS.
- J. Lü, H. Liu, R. Liu, X. Zhao, L. Sun and J. Qu, Powder Technol., 2013, 233, 146–154 CrossRef.
- M. Ghaedi, A. Hassanzadeh and S. N. Kokhdan, J. Chem. Eng. Data, 2011, 56, 2511–2520 CrossRef CAS.
- S. Karaca, A. Gürses, M. Ejder and M. Açikyildiz, J. Colloid Interface Sci., 2004, 277, 257–263 CrossRef CAS PubMed.
- G. Crini, H. N. Peindy, F. Gimbert and C. Robert, Sep. Purif. Technol., 2007, 53, 97–110 CrossRef CAS.
- C. Fang, T. Zhang, P. Li, R. F. Jiang and Y. C. Wang, Int. J. Environ. Res. Public Health, 2014, 11, 9217–9237 CrossRef PubMed.
- Y. Yao, B. Gao, M. Inyang, A. R. Zimmerman, X. Cao, P. Pullammanappallil and L. Yang, J. Hazard. Mater., 2011, 190, 501–507 CrossRef CAS PubMed.
- M. S. Gasser, H. T. Mohsen and H. F. Aly, Colloids Surf., A, 2008, 331, 195–201 CrossRef CAS.
- Z. P. Xu and G. Q. Lu, Chem. Mater., 2005, 17, 1055–1062 CrossRef CAS.
- L. G. Yan, K. Yang, R. R. Shan, T. Yan, J. Wei, S. J. Yu, H. Q. Yu and B. Du, J. Colloid Interface Sci., 2015, 448, 508–516 CrossRef CAS PubMed.
- J. Chen, Y. Song, D. Shan and E. Han, Corros. Sci., 2012, 63, 148–158 CrossRef CAS.
- Q. Zhang, S. Bolisetty, Y. Cao, S. Handschin, J. Adamcik, Q. Peng and R. Mezzenga, Angew. Chem., Int. Ed., 2019, 58, 6012–6016 CrossRef CAS PubMed.
- J. Ren, N. Li, L. Li, J. K. An, L. Zhao and N. Q. Ren, Bioresour. Technol., 2015, 178, 119–125 CrossRef CAS PubMed.
Footnote |
† Electronic supplementary information (ESI) available. See DOI: 10.1039/c9ra02052g |
|
This journal is © The Royal Society of Chemistry 2019 |
Click here to see how this site uses Cookies. View our privacy policy here.