DOI:
10.1039/C9RA01968E
(Paper)
RSC Adv., 2019,
9, 15615-15628
A magnetically separable plate-like cadmium titanate–copper ferrite nanocomposite with enhanced visible-light photocatalytic degradation performance for organic contaminants
Received
14th March 2019
, Accepted 14th May 2019
First published on 17th May 2019
Abstract
A novel magnetic cadmium titanate–copper ferrite (CdTiO3/CuFe2O4) nanocomposite, in which spherical CuFe2O4 nanoparticles were loaded onto the surface of CdTiO3 nanoplates, was successfully synthesized via a sol–gel hydrothermal route at 180 °C. The structure, morphology, magnetic and optical properties of the as-prepared nanocomposite were respectively characterized by Fourier transform infrared (FT-IR) spectroscopy, X-ray diffraction (XRD), field emission scanning electron microscopy (FESEM), energy dispersive X-ray (EDX) spectroscopy, transmission electron microscopy (TEM), Brunauer–Emmett–Teller (BET) surface area analysis, UV-visible diffuse reflectance spectroscopy (DRS), vibrating sample magnetometry (VSM) and photoluminescence (PL) spectroscopy. The photocatalytic activity of this novel CdTiO3-based magnetic nanocomposite was investigated for the degradation of organic dye pollutants such as methylene blue (MB), rhodamine B (RhB), and methyl orange (MO) in the presence of H2O2 under visible light irradiation. The results showed that the photocatalyst completely degraded three dyes within 90–100 min. Compared with pure CdTiO3 and CuFe2O4, the heterogeneous CdTiO3/CuFe2O4 nanocomposite exhibited significantly enhanced photocatalytic efficiency. On the basis of the results of the OH trapping and photoluminescence (PL) experiments, the enhanced photocatalytic performance was mainly ascribed to the efficient separation of photo-induced electron–hole pairs and the formation of highly active hydroxyl radicals (OH) species in the CdTiO3/CuFe2O4 photocatalytic oxidation system. The PL measurements of the CdTiO3/CuFe2O4 nanocomposite also indicated an enhanced separation of photo-induced electron–hole pairs. Moreover, the nanocomposite could be easily separated and recycled from contaminant solution using a magnet without a decrease in their photocatalytic activity due to their good magnetic separation performance and excellent chemical stability. Based on these findings, CdTiO3/CuFe2O4 nanocomposite could be a promising visible-light-driven magnetic photocatalyst for converting solar energy to chemical energy for environmental remediation.
1. Introduction
Nowadays, the world energy crisis and environmental pollution have become main issues in the lives of humans.1,2 Organic dye effluents from the textile and dyeing industries are one of the largest groups of pollutants discharged into the environment without adequate treatment.3 Although conventional biological, physical, and chemical methods have been established for wastewater treatment, in these cases, the pollutant is only transferred from the liquid phase to the solid phase and further treatment is necessary to purify the resulting sludge.4–10 Additionally, pollutants with very low concentrations are still difficult to remove from wastewater.11 Advanced oxidation processes (AOPs) have been used to eliminate a wide range of organic contaminants from water and air.12 In this context, heterogeneous photocatalysis is considered one of the most potent AOPs because of its potential applications in the degradation of organic contaminants.13–16 Among the various AOPs, the semiconductor-based photocatalysis is an effective and low-cost strategy for the treatment of water pollutants and disinfection.17 In this method, organic compounds can be completely degraded to H2O and CO2 by photocatalysis and no secondary pollutants are generated.18,19
Metal oxide-based semiconductor photocatalysts have been extensively applied in the field of environmental remediation due to their unique physicochemical properties, nontoxicity, and excellent photocatalytic activity.20–24 In recent decades, titanium dioxide (TiO2) has attracted considerable attention due to its low-cost, nontoxicity, and chemical inertness.25 Nevertheless, its use is limited to UV light irradiation due to its wide band gap structure (3.2 eV).26,27 It is well known that UV light is just 4% of solar radiation, while visible light is about 43%. Therefore, the design and synthesis of highly efficient visible-light-driven photocatalysis is an important research focus.28–30
Over the past several years, titanium-based perovskite-type oxides with formula of MTiO3 (M = Ca2+, Ba2+, Sr2+, Pb2+, …) have been widely studied because of their ferroelectric, dielectric, piezoelectric, pyroelectric and photostrictive properties, which make these ceramics eligible to be defined as ‘smart’.31 They also showed interesting properties as non-linear optics and humidity sensors. Among this smart family, cadmium titanate (CdTiO3) is much less studied because it is not ferroelectric at room temperature. From a fundamental point of view, however, CdTiO3 represents an interesting system for the investigation of the nature of the ferroelectric and structural phase transitions.32–35 Cadmium titanate has also been used as a conductive material,36,37 optical fibers,38 and humidity sensing.39 In addition, like other titanium-based systems, there is the possibility that it may have unexplored potential for application in photocatalysis.40 However, little previous studies showed that the CdTiO3 with a wide band gap of 3.5 eV like TiO2 has no significant photocatalytic activity under visible light irradiation.22 Forming a heterostructure by combining CdTiO3 with a narrow band-gap semiconductor is an effective route to enhance the visible-light response and improve the charge separation efficiency.41
Nanostructured spinel-type ferrites (MFe2O4; M = Mn2+, Fe2+, Co2+, Ni2+, Cu2+, Zn2+, …) have been considered as a promising candidate for efficient photocatalysts because of their small band gaps (1.3–2.1 eV), high photochemical stability, low cost, easy synthesis and unique magnetic properties.42 For these reasons, the use of nanoscale spinel-type ferrites in the fabrication of magnetic photocatalyst nanocomposite is very beneficial.43–46 Thus, it is possible to improve the efficiency of photoinduced charge separation in CdTiO3 by coupling it with magnetic spinel-type CuFe2O4 nanoparticles, resulting in high photocatalytic performance. Furthermore, its magnetic nature makes composite magnetically separable from the reaction mixture in a convenient manner.
In the present study, a novel magnetic cadmium titanate-based photocatalyst (CdTiO3/CuFe2O4) composite was prepared by a facile sol–gel hydrothermal route. The composition, microstructure and optical properties of the synthesized nanocomposite were fully characterized by various physical techniques. The visible-light photocatalytic activity of CdTiO3/CuFe2O4 nanocomposite was evaluated based on the degradation of organic dyes in the presence of H2O2. The effects of various parameters (e.g. H2O2 quantity, the catalyst dosage, and initial dye concentration) on the degradation process were also investigated. Furthermore, the activity of CdTiO3/CuFe2O4 nanocomposite was compared with those of pure CdTiO3 and CuFe2O4 under similar conditions. Furthermore, a possible mechanism for solar-light photoactivity of the nanocomposite was proposed. To the best of our knowledge, there are no reports on the preparation and photocatalytic properties of magnetic CdTiO3-based hybrids in the degradation of aqueous organic pollutants under visible light.
2. Experimental
2.1. Materials
Cadmium acetate (Cd(CH3COO)2, 98%), tetrabutyl orthotitanate (Ti(C4H9O)4, 99%), iron(III) chloride hexahydrate (FeCl3·6H2O, 98%), copper(II) chloride dehydrate (CuCl2·2H2O, 98%), sodium acetate (CH3COONa, 98%), potassium hydroxide (KOH, 98%), glycerol (C3H8O3, 99%), ethanol (C2H5OH, 98%), acetic acid (CH3COOH), diethyl ether ((C2H5)2O), hydrogen peroxide (H2O2, 30%), methylene blue (MB, C16H18ClN3S, 98%), methyl orange (MO, C14H14N3NaO3S, 98%), and rhodamine B (RhB, C28H31ClN2O3, 98%) were purchased from Merck chemical company and used as received.
2.2. Characterization techniques
XRD patterns were measured on a XPertPro Panalytical X-ray diffractometer instrument with Cu Kα radiation (λ = 1.54056 Å) in the range 2θ = 10–80° with a scan speed of 10° min−1. Infrared spectra were recorded from Schimadzu FT-IR 160 spectrophotometer in transmission mode from 4000 to 400 cm−1 using KBr pellets. The morphology and elemental analysis of the CdTiO3/CuFe2O4 nanocomposite were observed by Field emission scanning electron microscopy-energy-dispersive X-ray spectroscopy (FESEM-EDX) on a Mira3 Tescan scanning electron microscope equipped with an energy-dispersive X-ray unit. Transmission electron microscopy (TEM) images were taken on EM10C electron microscope operating at n voltage of 100 kV. Magnetic measurements were employed using a vibrating sample magnetometer (VSM, Daneshpajoh Kashan Co, Iran) with a maximum magnetic field of 10 kOe at room temperature. The UV-vis diffuse reflectance spectra (DRS) were obtained on a Sinico S4100 spectrophotometer using BaSO4 powder as a standard. UV-Vis spectra of dye solutions were analyzed at room temperature using a Cary 100 UV-visible spectrophotometer. The Brunauer–Emmett–Teller (BET) analysis was performed to obtain a specific surface area of CdTiO3/CuFe2O4 nanocomposite by a PHS-1020 PHSCHINA instrument. The photoluminescence (PL) spectra were measured using a fluorescence spectrophotometer of the samples (F-4500, Hitachi) at an excitation wavelength of 330 nm. The loading amount of CuFe2O4 in the composite adsorbent and the concentrations of Cu and Fe metals in the filtrates and solutions after recovering photocatalyst were determined by inductively coupled plasma atomic emission spectrometer (PerkinElmer ICP-AES, USA).
2.3. Synthesis of CuFe2O4 nanoparticles
In a typical experiment, 0.54 g FeCl3·6H2O and 0.14 g CuCl2·2H2O were dissolved in 30 mL of 1
:
1 glycerol–water solution by magnetic stirring for 30 min. Then, 0.8 g NaCH3COO·3H2O was added into the mixed solution under vigorous stirring for 20 min. The mixture was then poured into a Teflon-lined stainless steel autoclave of 40 mL capacity. The autoclave was placed in an electric oven at a temperature of 200 °C for 12 h. After 12 h, the autoclave was allowed to cool to room temperature. The product was separated by and washed with deionized water 3 times before being dried at 60 °C overnight.
2.4. Synthesis of the CdTiO3/CuFe2O4 nanocomposite
In a typical procedure, cadmium acetate (1.5 mmol) was dissolved in distilled water (15 mL). Then, it was introduced into a prepared solution of tetrabutyl orthotitanate (1.5 mmol) which was dissolved in ethanol (15 mL). After stirring for 15 min, CH3COOH (0.3 mL) was added to the mixture to control the hydrolysis of tetrabutyl orthotitanate. To this mixture 0.2 g CuFe2O4 nanoparticles sonicated in 10 mL of deionized water was added. The mixture was stirred at room temperature for 5 h, afterward it was kept under magnetic stirring at 40 °C constantly. With the evaporation of water and CH3COOH, a light yellow transparent gelatin, as the unique starting source of this hydrothermal preparation, was prepared. Then sufficient amount of the gelatin was put into a 50 mL Teflon-lined stainless autoclave. The autoclave was filled with KOH (1 M) solution up to 80% of its total volume and maintained at 200 °C for 24 h, the resulting precipitates were filtered, washed with distilled water, ethanol and ether and then dried at ambient temperature. The ICP-AES results indicated that the loading amount of CuFe2O4 in the as-prepared CdTiO3/CuFe2O4 nanocomposite was estimated to be 38 wt%. For comparison, pure CdTiO3 powder was prepared by using current method in the absence of CuFe2O4.
2.5. Photocatalytic tests
The photocatalytic activities of the as-synthesized samples were evaluated by the degradation of MB dye aqueous solution under visible-light irradiation. All experiments were carried out in a cylindrical Pyrex cell with a 400 W high-pressure mercury lamp with a UV-cutoff filter as the visible-light irradiation source (λ ≥ 420 nm), and temperature was controlled by the circulating water. In a typical procedure, 30 mg of as-synthesized materials were dispersed into 30 mL of dyes aqueous solution and the suspensions were shaken for 30 min in the dark prior to visible-light illumination to obtain an adsorption–desorption equilibrium. After that, 0.5 mL of 30% H2O2 was added to the mixture, and then irradiated. 2 mL aliquot of the reaction solution was collected regularly at a certain time interval, and the photocatalyst was separated using an external magnet. The MB dye absorption intensity was measured at maximum absorbance wavelength of 664 nm via a UV-Vis spectrophotometer. The degradation efficiency of the MB was calculated using the following equation: |
Degradation efficiency (%) = 100 (C0 − Ct)/C0
| (1) |
whereas C0 and Ct are the initial concentration of dye and concentration after regular irradiation, respectively. Similar experiments were conducted to evaluate the effect of initial dye concentration (12.5, 25, 37.5, 50 mg L−1), catalyst dosage (10, 20, 30, 40, 50 mg) and amount of 30% H2O2 (0, 0.25, 0.5, 0.75, 1 mL) on the photocatalytic activity of CdTiO3/CuFe2O4 nanocomposite. To investigate the photocatalytic stability and reusability of the samples, the photocatalytic activity measurements mentioned above were repeated for 5 cycles using an aqueous MB solution (25 mg L−1). After each cycle, the spent photocatalyst was separated from the treated MB solution, washed with deionized water, dried in an oven, and used again for the next photodegradation cycle. Photocatalytic activity of the CdTiO3/CuFe2O4 was also evaluated by the degradation of RhB and MO aqueous solution in a same manner. To detect the active species generated in the photodegradation process, the scavengers isopropyl alcohol (IPA; 5 mmol L−1), and disodium ethylenediaminetetraacetate (Na2EDTA; 5 mmol L−1) were added into the solution of MB. The photocatalytic process was the same as that described in the above.
3. Results and discussion
3.1. FTIR analysis
FT-IR spectra of pure CuFe2O4, pristine CdTiO3 and CdTiO3/CuFe2O4 nanocomposite are shown in Fig. 1. In Fig. 1(a), a characteristic band at around 580 cm−1 corresponds to the stretching vibration of Fe–O bond, confirms the formation of magnetic CuFe2O4 nanoparticles.47 Fig. 1(b) indicates the FT-IR spectrum of pure CdTiO3 phase. Absorption peaks at 711, 526 and 426 cm−1 can be related to the stretching vibrations of O–Ti–O, Ti–O, Cd–O bands, respectively.48 These results provided that CdTiO3 was successfully synthesized. As shown in Fig. 1(c), the characteristic spectral bands verified the existence of the both CdTiO3 and CuFe2O4 in the CdTiO3/CuFe2O4 nanocomposite and two broad peak were also observed at about 2800–3700 cm−1 and 1400–1700 cm−1 due to the stretching vibration and deformation of the absorbed water molecules.49 The characteristic band of CuFe2O4 in the nanocomposite appeared as a shoulder at 582 cm−1 due to overlapping with the stretching band of CdTiO3 at 525 cm−1.
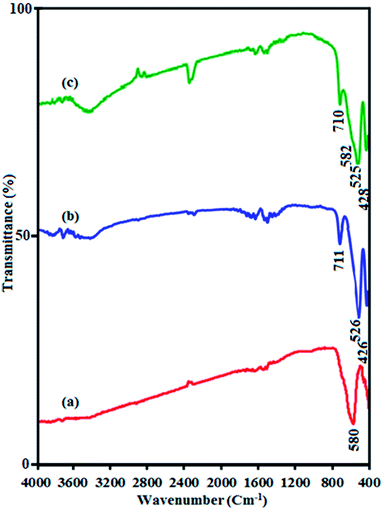 |
| Fig. 1 FT-IR spectra of (a) CuFe2O4, (b) CdTiO3 and (c) CdTiO3/CuFe2O4. | |
3.2. XRD analysis
Fig. 2 shows the XRD patterns of CuFe2O4, CdTiO3 and CdTiO3/CuFe2O4. The diffraction peaks of spinel-type CuFe2O4 nanoparticles at 35.4°, 43.3°, 53.6°, 57.1° and 62.7° in Fig. 2(a) are assigned to the (261), (400), (422), (511), and (440) planes (JCPDS card no. 25-0283), respectively.50 In addition, the diffraction peaks appeared at 17.9°, 20.4°, 22.9°, 31.1°, 34.1°, 53.7° and 59.3° can be indexed as (003), (101), (012), (104), (110), (116) and (214) diffraction planes of CdTiO3 phase (JCPDS, card no. 29–0277), respectively (Fig. 2(b)).51 It is obvious in Fig. 2(c) that the XRD pattern of nanocomposite sample exhibits diffraction peaks corresponding to both CuFe2O4 and CdTiO3 phases and no other impure peaks can be observed, indicating that this sample is composed of CuFe2O4 and CdTiO3 phases and the CdTiO3/CuFe2O4 composite has been successfully prepared. The diffraction peaks of 35.4 and 53.7 from CuFe2O4 overlapped with the peaks from CdTiO3, and the relative intensity of these peaks for CdTiO3/CuFe2O4 nanocomposite increased. The average size of the CuFe2O4 was found of about 20 nm using Debye–Scherrer equation:52 DXRD = 0.9λ/(β
cos
θ), where DXRD is the average crystalline size, λ is the wavelength of Cu Kα radiation, β is the full width at half maximum of the diffraction peak, and θ is the Bragg angle.
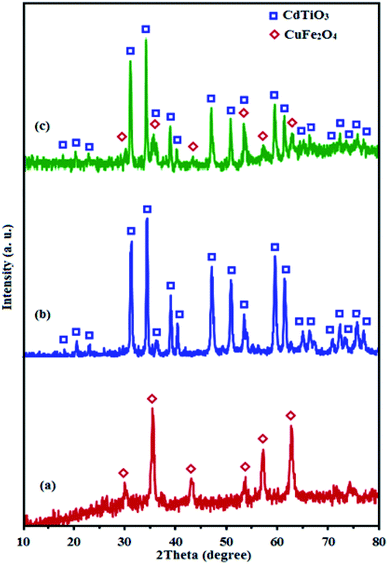 |
| Fig. 2 XRD patterns of (a) CuFe2O4, (b) CdTiO3 and (c) CdTiO3/CuFe2O4. | |
3.3. SEM and EDX analyses
The shape and morphology of the as-synthesized CdTiO3, CuFe2O4 and CdTiO3/CuFe2O4 samples were investigated by FE-SEM, and the results are shown in Fig. 3. The SEM images of CuFe2O4 sample in Fig. 3(a) show a large quantity of nearly uniform spherical nanoparticles with diameters 15–25 nm. The SEM images in Fig. 3(b) and (c) show that the bare CdTiO3 sample was formed from nanoplates with smooth surface which were loosely aggregated. The thickness and width of nanoplates are estimated to be about 50 nm and 250–650 nm, respectively. As can be observed, the porous structure was formed by self-assembly of these nanoplates. SEM images of the CdTiO3/CuFe2O4 nanocomposite are shown in Fig. 3(d)–(f). From the images, it is evident that the shape and morphology of CdTiO3/CuFe2O4 are similar to those of the pure CdTiO3, but a lot of sphere-like CuFe2O4 nanoparticles are homogeneously distributed over the surfaces of plate-like CdTiO3 nanostructures.
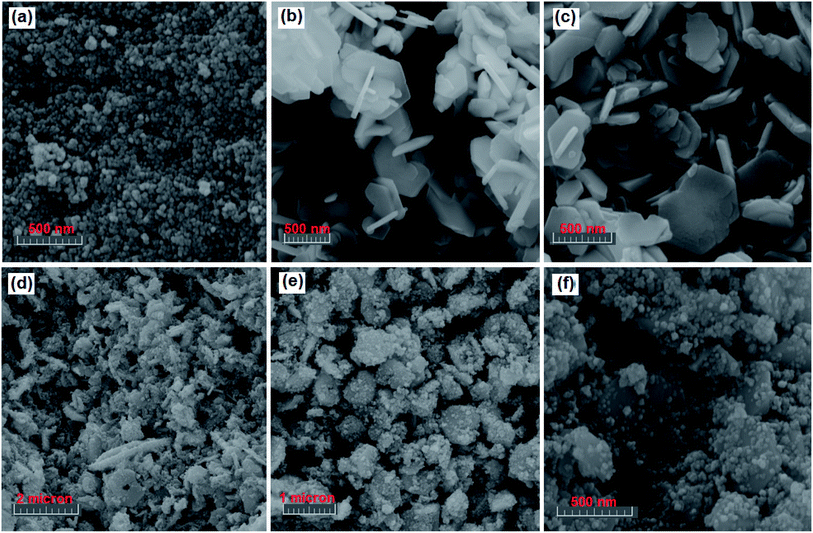 |
| Fig. 3 SEM images (a) CuFe2O4, (b and c) CdTiO3, and (d–f) CdTiO3/CuFe2O4. | |
The existence of elements in the nanocomposite was detected by EDX spectroscopy and the results are shown in Fig. 4. From EDX spectrum in Fig. 4(a), the Cd, Ti, Cu, Fe and O elements are clearly observed at their corresponding keV values. The distribution of elements present in the nanocomposite was also studied using EDX mapping analysis, and the results are shown in the Fig. 4(b). The corresponding elemental mappings show all elements are uniformly distributed over the nanocomposite, confirming the homogeneity of the nanocomposite sample. These results confirm that the obtained product was formed with high purity.
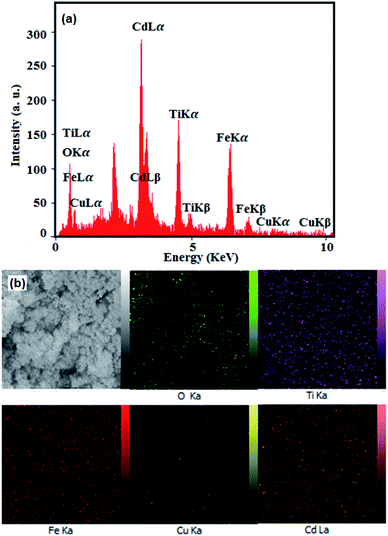 |
| Fig. 4 (a) EDX spectrum and (b) elemental mappings of the CdTiO3/CuFe2O4 nanocomposite. | |
3.4. TEM analysis
The size and microstructure of the as-prepared CdTiO3/CuFe2O4 sample were further investigated by TEM. The sample was sonicated in ethanol for 30 min and a drop of the suspension was dried on a carbon-coated microgrid for TEM measurements. The TEM images in Fig. 5 show that the nanocomposite was formed mainly from plate-like particles with a weak agglomeration. From the TEM images in Fig. 5(a) and (b), it is clear that the CdTiO3/CuFe2O4 contains a plate-like structure with the lengths of 250–650 nm and thicknesses of several nanometers. From images, it can be clearly seen that a lot of sphere-like CuFe2O4 nanoparticles were well deposited on CdTiO3 nanoplates. As evident from the images, the morphology of the CdTiO3/CuFe2O4 sample from TEM images agreed with the SEM results. After being loaded with CuFe2O4 nanoparticles, the plate-like structure of CdTiO3 is maintained but the distinct CuFe2O4 aggregates were attached to the edge and surface of the CdTiO3 sample. The synergistic interactions between CuFe2O4 and CdTiO3 led to decreased aggregation of the CuFe2O4 nanoparticles. The size of CuFe2O4 particles was calculated to be in the range of 15–25 nm from the measurements on the TEM micrographs which is in close agreement with the average size obtained from XRD analysis.
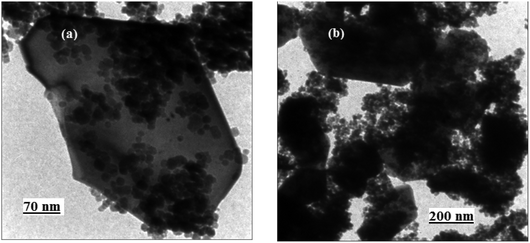 |
| Fig. 5 TEM images of the CdTiO3/CuFe2O4 nanocomposite. | |
3.5. BET surface area analysis
Fig. 6 presents the N2 adsorption–desorption isotherms of pure CuFe2O4, pristine CdTiO3 and CdTiO3/CuFe2O4 nanocomposite samples. As shown in Fig. 6(a) and (b), CdTiO3 and CdTiO3/CuFe2O4 composites display typical type IV isotherms with a H3 hysteresis loops according to the IUPAC classification, indicating the presence of large mesopores structures.53,54 The Brunauer–Emmett–Teller (BET) surface area values for CuFe2O4, CdTiO3 and CdTiO3/CuFe2O4 were calculated to be 43.512, 14.023 m2 g−1 and 13.514 m2 g−1, respectively (Table 1). Obviously, there are only small differences among the surface area values of CdTiO3 and CdTiO3/CuFe2O4 samples. It is well known that the surface area is an important factor for enhanced photocatalytic activity due to the increase of adsorption activity and reaction sites. However, the photocatalytic activity of pure CuFe2O4, pristine CdTiO3 are lower than that of CdTiO3/CuFe2O4 composite though their surface area and adsorption activity are the highest. The results indicate that there are other factors influencing the photocatalytic efficiency besides the specific surface area of one photocatalyst, including good visible light absorption properties, efficient charge transfer and the inhibition of electron–hole pairs recombination. It can be speculated that the different photocatalytic activity of the samples could not be determined by the BET surface areas in the process of dye degradation. Furthermore, we also calculated the pore size distributions by using the Barrett–Joyner–Halenda (BJH) method from the adsorption branches of the N2 isotherms (the insets of Fig. 6). The CdTiO3 and CdTiO3/CuFe2O4 heterojunction samples have a broad pore size distribution centered at about 47.22 and 19.99 nm, respectively which reveal the existence of nanopores. The presence of nanopores may serve as transport paths for organic pollutant molecules. As given in Table 1, the CdTiO3/CuFe2O4 heterojunction demonstrated a significant decrease pore volume and pore diameter compared with the pure CuFe2O4 and pristine CdTiO3 probably owing to the introduction of CuFe2O4 nanoparticles into the pores of the CdTiO3. The pores of CdTiO3/CuFe2O4 were further occupied by the CuFe2O4 nanoparticles which resulted in a further decrease in pore volume and surface area.
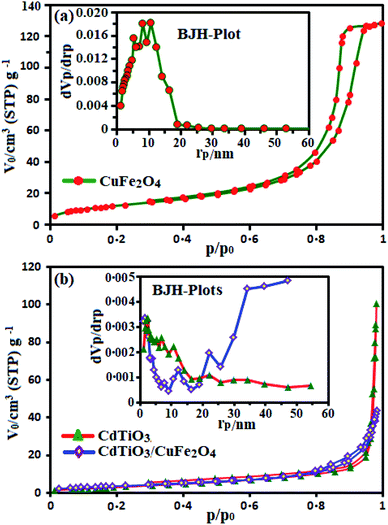 |
| Fig. 6 Nitrogen adsorption–desorption isotherms of (a) pure CuFe2O4 and (b) pristine CdTiO3 and CdTiO3/CuFe2O4 nanocomposite samples. The insets show pore size distribution curves. | |
Table 1 The textural properties of as-prepared samples
Sample |
BET surface area (SBET, m2 g−1) |
Total pore volume (Vp, cm3 g−1) |
Average pore diameter (rp, nm) |
CuFe2O4 |
43.512 |
0.199 |
10.65 |
CdTiO3 |
14.023 |
0.156 |
47.22 |
CdTiO3/CuFe2O4 |
13.514 |
0.068 |
19.99 |
3.6. Optical properties analysis
UV-vis diffuse reflectance spectra of the samples were measured and the results are shown in Fig. 7. The UV vis spectrum of pure CdTiO3 sample (curve (i) in Fig. 7(a)) shows a strong absorption band from the UV to the visible light region with a clear absorption edge at 460 nm. The UV vis spectrum of CuFe2O4 sample (curve (ii) in Fig. 7(a)) exhibits a broad absorption band in the visible range. However, after coupling CdTiO3 with CuFe2O4, the obtained composite exhibited a wide absorption band that covered the whole visible region (curve (iii) in Fig. 7(a)). The CdTiO3/CuFe2O4 had a significant red-shift toward the visible light region. Obviously, the visible light absorption of CdTiO3/CuFe2O4 heterojunction is better than that of CdTiO3, which possibly results good visible-light utilization. The band gap energy (Eg) of samples can be deducted from the formula:55 (αhν)2 = B(hν − Eg), where α, ν, and B are absorption coefficient, light frequency and proportionality constant, respectively. The (αhv)2 versus hv curves for CdTiO3, CuFe2O4 and CdTiO3/CuFe2O4 nanocomposites are shown in Fig. 7(b). The value of hv extrapolated to α = 0 gives the absorption band gap energy. From Fig. 7(b), curves (i)–(iii), the band gap energies were estimated to be 3.55, 1.55 and 2.20 eV for CdTiO3, CuFe2O4 and CdTiO3/CuFe2O4 nanocomposite samples, respectively, indicating that the introduction of CuFe2O4 decreased the Eg of CdTiO3. Furthermore, the decrease of Eg upon composite formation confirms electronic coupling between CdTiO3 and CuFe2O4. The visible light photocatalytic activity of CdTiO3/CuFe2O4 could be attributed to the existence of this broad band with the Eg of 2.20 eV. After the decoration of CuFe2O4 on the surface of CdTiO3, CdTiO3/CuFe2O4 heterojunction displays a broad photoabsorption from ultraviolet to visible light with an edge around 750 nm. This fact reveals that CdTiO3/CuFe2O4 heterojunction has a broad photoabsorption region, resulting in great potential as an excellent visible light driven photocatalyst.
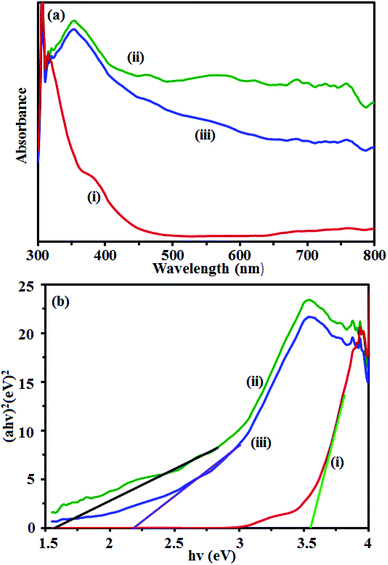 |
| Fig. 7 (a) UV-vis DRS and (b) band gap energies of: (i) CdTiO3, (ii) CuFe2O4 and (iii) CdTiO3/CuFe2O4 nanocomposite. | |
3.7 Magnetic properties analysis
Fig. 8 shows magnetization hysteresis curves of the CuFe2O4 and CdTiO3/CuFe2O4 nanocomposite at room-temperature. The samples exhibit zero coercivity (Hc = 0) and near-zero remanence magnetization (Mr ∼ 0) at room temperature, reflecting their superparamagnetic properties. However, because of the presence of diamagnetic CdTiO3, the saturation magnetization of CdTiO3/CuFe2O4 nanocomposite is reduced to 19.17 emu g−1 as compared with that of pure CuFe2O4 (55.03 emu g−1). The composite still exhibits superparamagnetic characteristics. As shown in the inset of Fig. 8, the CdTiO3/CuFe2O4 nanocomposite could be easily separated from the wastewater with a common magnet and quickly collected on the side of the glass vial in a short time, which indicates that CdTiO3/CuFe2O4 nanocomposite can be easily recycled from wastewater by external magnetic field and it can be readily re-dispersed back into the aqueous phase due to its zero coercivity.56 The facile separation and recovery of CdTiO3/CuFe2O4 composite is very favorable for its practical applications.
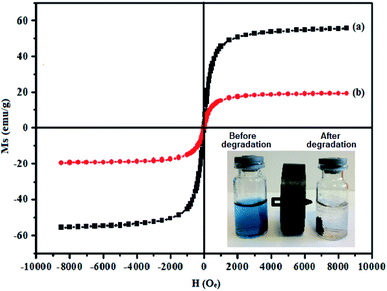 |
| Fig. 8 Room-temperature magnetic hysteresis loops of (a) pure CuFe2O4 and (b) CdTiO3/CuFe2O4 nanocomposite. The photo inset shows magnetic separation of the photocatalyst from aqueous dye solution before and after dye degradation using a magnet. | |
3.8. Photocatalytic performance
The photocatalytic activity of CdTiO3/CuFe2O4 nanocomposite was evaluated by H2O2-assisted degradation of organic dyes in aqueous solutions under visible light irradiation. As shown in Fig. 9(a), the intense absorption peak of MB dye at 664 gradually decreased in during the different reaction times and disappeared after 90 min. Also, color change of the MB solution from blue to almost colorless with increasing irradiation time indicated its complete degradation. The control experiments were carried out under different conditions. The results of MB dye degradation rate are shown in Fig. 9(b). Curve (I) in Fig. 9(b) shows that MB decomposition is negligible without the catalyst and H2O2 under visible light irradiation. CdTiO3/CuFe2O4 nanocomposite (without H2O2) under visible light irradiation degraded 23% of MB (curve (II)). The photodegradation efficiency of MB in the presence of H2O2 alone (without catalyst) was 21% (curve (III)). CdTiO3/H2O2 system removed only 18% of MB dye (curve (IV)) in 90 min whereas CuFe2O4/H2O2 system degraded MB dye about 61% at the same time (curve (V)). The degradation percentage of MB by CdTiO3/CuFe2O4 nanocomposite in the presence of H2O2 without visible light illumination (in the dark) was 72% (curve (VI)). Curve (VII) in Fig. 9(b) shows photocatalytic capability CdTiO3/CuFe2O4/H2O2 system under visible light irradiation that indicates the highest photocatalytic activity, 100% of MB was degraded in 90 min. Thus, it can be concluded that complete degradation of MB dye occurs when simultaneously CdTiO3/CuFe2O4 nanocomposite and H2O2 are present in the reaction solution under visible light irradiation. In order to study the photocatalytic degradation rate of MB under different conditions, a pseudo-first-order kinetic model was used (eqn (2)), and the results were displayed in Fig. 9(c).where, C0 and C are the MB concentrations before and after visible light irradiation, respectively, kapp is the pseudo-first-order rate constant and t is irradiation time. The slope of the line of ln(C/C0) vs. t is reaction rate constant (kapp). From Fig. 9(c), the kapp values for visible light irradiation alone, H2O2/vis, CuFe2O4/H2O2/vis, CdTiO3/H2O2/vis, CdTiO3/CuFe2O4/H2O2, CdTiO3/CuFe2O4/vis and CdTiO3/CuFe2O4/H2O2/vis were calculated to be 0, 0.0043, 0.0107, 0.005, 0.0165, 0.0024 and 0.049 min−1, respectively. The kinetic rate constant of CdTiO3/CuFe2O4 nanocomposite is much higher than those of other catalyst samples. Based on the above results, one can conclude that CdTiO3/CuFe2O4 nanocomposite is much more active than pristine CdTiO3 and pure CuFe2O4.
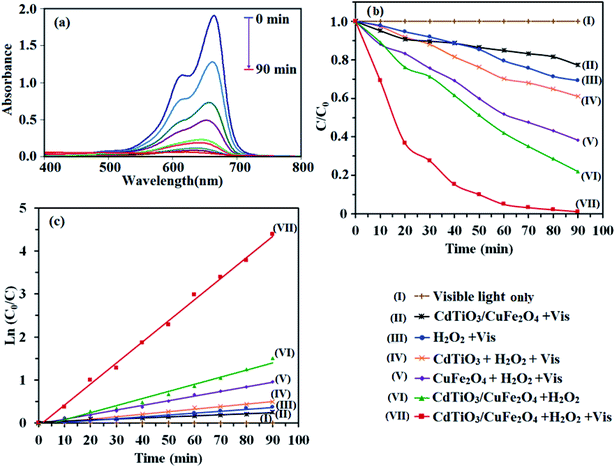 |
| Fig. 9 (a) Photocatalytic degradation of MB under different conditions. (b) Concentration changes of MB at 664 nm as a function of irradiation time. (c) Plot of ln(C0/C) against the irradiation time. Conditions: MB (25 mg L−1, 30 mL), H2O2 (0.15 M), catalyst (1 g L−1) and reaction time of 90 min. | |
3.8.1. Effect of H2O2 concentration. To investigate the influence of H2O2 concentration on MB degradation, a series of experiments were done with different amounts of H2O2, while the initial concentration of dye and other parameters were constant and the results are presented in Fig. 10(a). It is clear that the degradation rate of MB dye increased with increasing H2O2 amount. At higher concentration of H2O2, more ˙OH radicals were achieved. Therefore, the photodegradation activity was improved.57
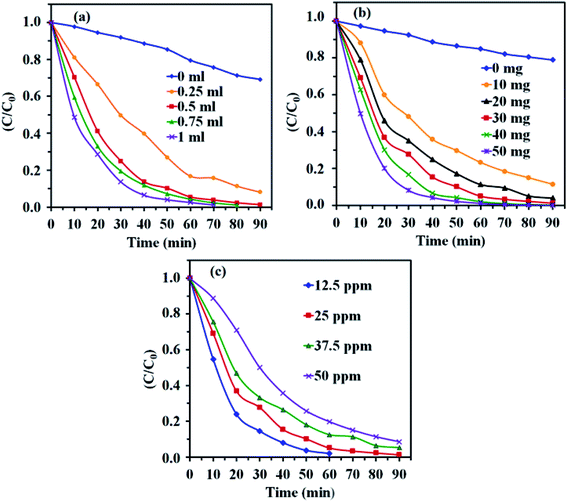 |
| Fig. 10 Effects of (a) H2O2 amount, (b) CdTiO3/CuFe2O4 dosage and (c) initial dye concentration on the photocatalytic degradation. Conditions: MB (25 mg L−1, 30 mL), H2O2 (0.15 M), catalyst (30 mg) and time = 90 min. | |
3.8.2. Effect of photocatalyst dosage. Fig. 10(b) shows the effect of photocatalyst amount on the MB degradation under visible light illumination. It can be clearly seen that with the increase of the catalyst amount from 10 to 50 mg, the degradation rate of MB dye in aqueous solution increased. This may be due to the increase in active sites resulting from higher amount of catalyst which generate more ˙OH radicals and facilitate the further and faster degradation of dye molecules.58
3.8.3. Effect of initial concentration of MB. Fig. 10(c) shows the effect of the initial MB concentration on its photocatalytic degradation percentage. For this purpose, different initial concentration of MB from 12.5 to 50 mg L−1 was studied under visible light irradiation. As shown in Fig. 10(c), a more time needed to achieve the suitable degradation at higher concentration of MB dye. At a constant catalyst dosage, amount of H2O2, and reaction time, the number of generated ˙OH radicals for the degradation the dye molecules remains constant with increasing dye initial concentration, resulting degradation efficiency decreases.59,60To study the scope of this method, the photocatalytic degradation of MO and RhB dyes was also evaluated. Accordingly, similar experiments were performed and the results are shown in Fig. 11. As shown in Fig. 11(a) and (b), the RhB and MO dyes were degraded completely in 90 and 100 min, respectively. The slower degradation of MO molecules can be related to its high redox potential. As compared in Fig. 11(c), this novel photocatalytic system exhibits excellent capacity for the degradation of MB, RhB and MO under visible light irradiation.
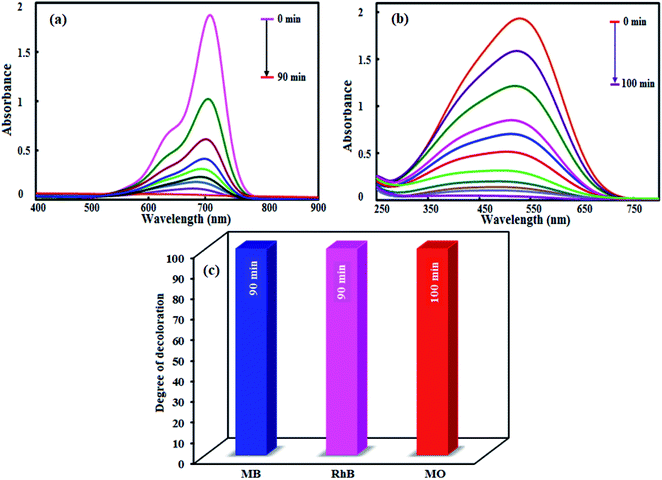 |
| Fig. 11 Photocatalytic degradation of (a) RhB and (b) MO. (c) Comparison of the photocatalytic degradation of MB, RhB and MO dyes. Conditions: [dye] = 25 mg L−1; [catalyst] = 0.1 g L−1; [H2O2] = 0.15 mol L−1 and reaction times of 90–100 min. | |
To check the effectiveness of our photocatalyst, the degradation efficiency of the present work was compared with some of the earlier reported photocatalysts61–80 and the results are presented in Table 2. It is clear that the earlier studies have utilized high power xenon and mercury lights for the degradation of low concentration of dyes (5–10 mg L−1) with more quantity of photocatalyst (50–300 mg) and longer times (100–300 min). From Table 2, it can be seen that our catalyst showed higher degradation efficiency for high concentration dye with less amount of photocatalyst in lesser time under mild conditions in visible light when contrasted with the other most reported works. These results affirmed that our photocatalyst is more superior and/or is better than that of those observed in the previous reports.
Table 2 Comparison of visible-light-driven photocatalytic performance of CdTiO3/CuFe2O4 nanocomposite with other reported nanomaterials
Photocatalyst |
Irradiation source |
Dyes |
[Dye] (mg L−1) |
Volume (mL)/catalyst (mg) |
Degradation(%)/time (min) |
Ref. |
CdTiO3/CuFe2O4 |
400 W Hg lamp (λ ≥ 420 nm) |
MB & RhB |
25 |
30/30 |
100/90 |
This work |
CdTiO3 |
UV lamp (λ ≥ 300 nm) |
R6G |
10 |
100/100 |
100/300 |
61 |
CuFe2O4/TiO2 |
250 W High pressure Hg lamp |
MB |
12 |
100/100 |
47/150 |
62 |
TiO2/PbTiO3 |
300 W High pressure Hg lamp (λ ≥ 420 nm) |
MB |
∼3.2 |
65/300 |
80/300 |
63 |
TiO2/Fe3O4 |
250 W High pressure Hg lamp (λ ≥ 300 nm) |
RhB |
10 |
60/200 |
96.3/80 |
64 |
ZnO/CdS |
Sun light |
RhB |
5 |
80/20 |
100/90 |
65 |
rGO/MoS2 |
SOL2/500S lamp (λ ≥ 295 nm) |
MB |
12.5 |
8.5/6.5 |
95/300 |
66 |
P25/CoFe2O4/graphene |
500 W Xenon lamp |
MB |
40 |
30/30 |
100/240 |
67 |
Graphene/TiO2/Fe3O4 |
300 W Hg lamp |
RhB |
5 |
50/10 |
100/25 |
68 |
g-C3N4/Fe3O4/BiOI |
50 W LED lamp (visible-light source) |
MB |
∼4 |
250/100 |
98/180 |
69 |
LaFeO3/GrO |
300 W Xe arc lamp (λ > 400 nm |
MB |
0.5 |
100/10 |
98/70 |
70 |
LaFeO3/g-C3N4 |
500 W Xe arc lamp (λ ≥ 420 nm) |
RhB |
15 |
100/20 |
85/160 |
71 |
Bi2S3/Bi2O2CO3 |
300 W Xe lamp (λ > 400 nm) |
RhB |
10 |
50/50 |
100/30 |
72 |
CdS/Bi2O2CO3 |
300 W Xe lamp (λ > 400 nm) |
MB |
10 |
50/40 |
67/90 |
73 |
CdS/ZnFe2O4 |
500 W Xe lamp (λ > 400 nm) |
RhB |
10 |
100/50 |
98/60 |
74 |
CuFe2O4/g-C3N4 |
300 W Tungsten light lamp (λ ≥ 400 nm) |
RhB |
10 |
100/50 |
90/150 |
75 |
Ag3PO4/GO/NiFe2O4 |
300 W Xe arc lamps (λ ≥ 400 nm) |
RhB |
10 |
100/20 |
98/30 |
76 |
SrTiO3/NiFe2O4 |
500 W Xe lamp(λ ≥ 400 nm) |
RhB |
20 |
100/100 |
100/120 |
77 |
Ag3PO4/MgFe2O4 |
300 W Xe arc lamp (λ ≥ 400 nm) |
RhB |
10 |
100/20 |
100/30 |
78 |
SrTiO3/TiO2 |
50 W High-pressure Hg lamp (UV, λ ≥ 313 nm) |
RhB |
10 |
100/10 |
100/60 |
79 |
MoS2/Fe3O4 |
500 W High-pressure xenon lamp (λ ≥ 420 nm) |
MB |
30 |
—/25 |
98/120 min |
80 |
3.9. Possible photocatalytic mechanism
The above results reveal that CdTiO3/CuFe2O4 nanocomposite exhibits a higher photocatalytic activity than those of pristine CdTiO3 and pure CuFe2O4. The enhanced photocatalytic activity of CdTiO3/CuFe2O4 can be attributed to the synergetic effects of strong visible-light absorption and p–n junction structure causing effective separation of photo generated holes and electrons. CuFe2O4 is a p-type semiconductor with a narrow band gap while CdTiO3 is an n-type semiconductor with a large band gap.81 The positions of the conduction band (CB) and valence band (VB) of n-type CdTiO3 and p-type CuFe2O4 can be computed using the atom's Mulliken electronegativity definition (eqn (3) and (4)):82where EVB is the VB potential, ECB is the CB potential, Ee is the energy of free electrons on the hydrogen scale (ca. 4.5 eV), Eg is the band gap energy and χ is the absolute electronegativity of the semiconductor. On the basis of the above equations, the EVB and ECB of n-CdTiO3 were calculated to be 1.08 eV and −2.47 eV, whereas the potentials for CuFe2O4 were estimated to be 0.27 eV and −1.28 eV, respectively.
According to the above results, the energy band schematic diagram for CuFe2O4 and CdTiO3 were illustrated in Fig. 12. The band gap of CdTiO3 is 3.55 eV and thus it cannot be excited under visible light irradiation. However, CuFe2O4 with the band gap of 1.55 eV can be easily excited to generate holes and electrons under visible light irradiation in its VB and CB, respectively. Before contact, the conduction band and Fermi level (Ef) position of CuFe2O4 is lower than those of CdTiO3. In the case of contact between p-type CuFe2O4 and n-type CdTiO3, the electrons will diffusion from CdTiO3 to CuFe2O4 due to the more negative CB of CdTiO3, which results in accumulation of negative charges in CuFe2O4 close to the junction.71,83 Meanwhile, a positive section in CdTiO3 near the junction will generate after the holes transfer from CuFe2O4 to CdTiO3. The Fermi energy level of CuFe2O4 is moved up, and simultaneously the Fermi level of CdTiO3 is moved down to form an equilibrium state, where the inner electric field is formed and the CB of CuFe2O4 is higher than that of CdTiO3. Under visible-light illumination, CuFe2O4 could be easily excited and induced the generation of photoelectrons and holes. According to the schematic diagram in Fig. 12, the excited electrons on the CB of the CuFe2O4 transfer to that of CdTiO3, and simultaneous the holes remain in the VB of CuFe2O4.84 The internal electric field can promote the migration of photogenerated carriers. Accordingly, the p–n junction formed in the CdTiO3/CuFe2O4 interface will be beneficial for separation of the photogenerated electron–hole pairs, and the recombination probability of electron–hole pairs can be consequently reduced.85 The separated electrons and holes are then free to initiate reactions with the dye molecules adsorbed on the photocatalyst surfaces. The photogenerated electrons will be used to active H2O2 to produce hydroxyl radicals (˙OH). Some of holes maybe directly involved in the oxidation of MB to produce unstable MB+ as a target of OH− attack. On the other hand, the produced hydroxyl radicals (˙OH) resulting from reaction of the electrons in CB with H2O2 were active enough to degrade MB to the innocent products CO2 and H2O, etc. (eqn (5)–(9)).86
|
CdTiO3/CuFe2O4 + hv → eCB− + hVB+
| (5) |
|
H2O2 + eCB− → ˙OH + OH−
| (6) |
|
MB + hVB+ → MB+ (unstable)
| (8) |
|
MB+ + ˙OH → CO2 + H2O + …
| (9) |
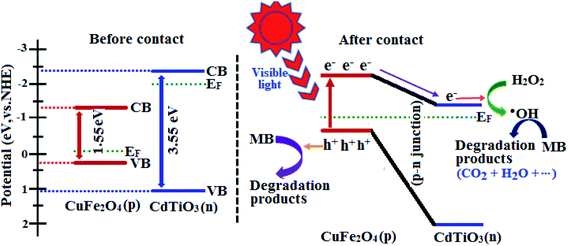 |
| Fig. 12 Schematic illustration of excitation and separation of photoinduced electron–hole pairs for CdTiO3/CuFe2O4 heterojunction under visible-light irradiation. | |
The separation of photoexcited carriers was further validated by their photoluminescence (PL) property. Fig. 13(a) exhibits the room-temperature PL spectra of pristine CdTiO3 and CdTiO3/CuFe2O4. The pristine CdTiO3 nanoparticles show the PL spectrum with high intensity, indicating high radiative recombination. Moreover, CdTiO3/CuFe2O4 heterojunction has a similar peak shape and peak position, but much lower PL intensity, suggesting that the sample possessed the high separation efficiency of photogenerated electrons and holes. The results indicated that the CdTiO3/CuFe2O4 heterojunction is favorable at suppressing radiative recombination. This led to better utilization of electron and hole pairs induced by light irradiation.
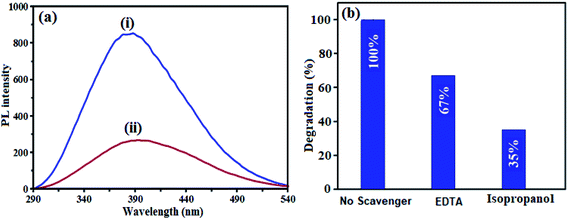 |
| Fig. 13 (a) PL spectra excited at 325 nm of (i) pure CdTiO3 and (ii) CdTiO3/CuFe2O4 samples and (b) the photocatalytic degradation of MB over the CdTiO3/CuFe2O4 in the presence of different scavengers under visible-light irradiation. | |
To further evaluate what kind of species plays a main role in the photo degradation process of dyes, in this reaction system, isopropanol and disodium ethylenediamine tetraacetate (EDTA) were used as be the scavengers of ˙OH radicals and holes (hVB+), respectively. As shown in Fig. 13(b), EDTA decreased the photodegradation rate slightly, demonstrating the minor role of holes (hVB+). In contrast, the photocatalytic degradation efficiency of MB decreases significantly in the presence of isopropanol, demonstrating that ˙OH radicals play a main role in the photocatalytic degradation of MB. According to these results, it can be concluded that ˙OH radicals are the major active species in the photocatalytic reaction, and holes were less involved.
3.10. Recyclability and stability tests
The reusability of photocatalysts is a noteworthy issue in practical applications, especially for the separation property and their stability. The CdTiO3/CuFe2O4 nanocomposite has magnetism due to the presence of CuFe2O4 nanoparticles. To confirm the magnetic properties of the CdTiO3/CuFe2O4, a separation experiment was conducted as follows. The inset of Fig. 4 showed that the CdTiO3/CuFe2O4 has magnetic properties that can solve the separation problem of photocatalysts via magnetic separation. The CdTiO3/CuFe2O4 was reused three times to test the stability of CdTiO3/CuFe2O4 nanocomposite on the photodegradation of MB. After each photocatalytic degradation experiment, the nanocomposite was separated from the dye solution by a permanent magnet, washed with distilled water, dried at 60 °C and used in a new cycle. As shown in Fig. 14(a), the recycled catalyst activity showed no significant change after three recycles. The amounts of Cu, Fe and Cd metals in the filtrate were also determined to be about less than 0.1% by ICP-AES analysis. In addition, XRD and FT-IR spectra of the fresh and recycled catalyst did not exhibit obvious differences even after three cycling runs (Fig. 14(b) and (c)). These findings confirm the composite has a good stability during the photocatalytic degradation of dyes.
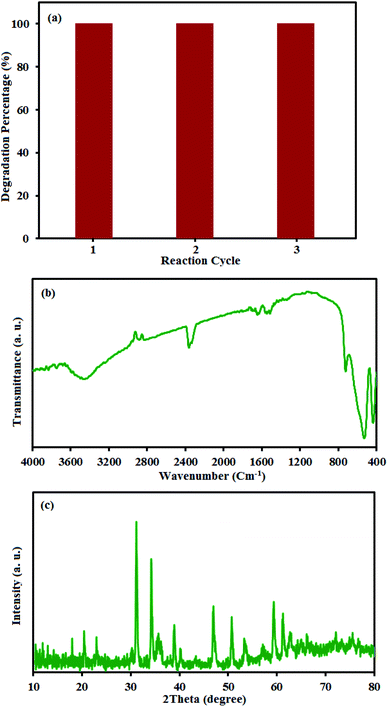 |
| Fig. 14 (a) Cycling runs of CdTiO3/CuFe2O4 in the photodegradation of MB. Each run of photocatalytic reactions lasted for 90 min. (b) XRD and (c) FT-IR of the recovered nanocomposite after the 3rd run. | |
4. Conclusion
In summary, a novel magnetically recyclable CdTiO3/CuFe2O4 nanocomposite was successfully constructed by attachment of spherical CuFe2O4 nanoparticles onto the surface of CdTiO3 nanoplates via a sol–gel hydrothermal process for the first time. The photocatalytic activity of CdTiO3/CuFe2O4 nanocomposite is significantly enhanced for removal of organic dyes under visible light irradiation. The enhanced photodegradation performance can be attributed to the promoted separation and inhibited recombination of electron–holes pairs in the heterostructures of CdTiO3/CuFe2O4 nanocomposites. Moreover, the excellent room temperature superparamagnetism and stability of CdTiO3/CuFe2O4 nanocomposites ensure the convenient magnetic separation. Since the unique CdTiO3/CuFe2O4 material with high activity and recyclable magnetic separation, it has potential applications in organic pollutant removal and environmental remediation.
Conflicts of interest
There are no conflicts of interest to declare.
Acknowledgements
The authors gratefully acknowledge the Lorestan University and Iran Nanotechnology Initiative Council (INIC) for their financial support.
References
- K. Ji, J. Deng, H. Zang, J. Han, H. Arandiyan and H. Dai, Appl. Catal., B, 2015, 165, 285–295 CrossRef CAS.
- S. Kansal, M. Singh and D. Sud, J. Hazard. Mater., 2007, 141, 581–590 CrossRef CAS PubMed.
- M. Saranya, R. Ramachandran, E. J. J. Samuel, S. K. Jeong and A. N. Grace, Powder Technol., 2015, 279, 209–220 CrossRef CAS.
- R. Jain and M. Shrivastava, J. Hazard. Mater., 2008, 152, 216–220 CrossRef CAS PubMed.
- H. Wang, X.-W. Zheng, J.-Q. Su, Y. Tian, X.-J. Xiong and T.-L. Zheng, J. Hazard. Mater., 2009, 171, 654–659 CrossRef CAS PubMed.
- K. Kumari and T. E. Abraham, Bioresour. Technol., 2007, 98, 1704–1710 CrossRef CAS PubMed.
- M. M. Pendergast and E. M. Hoek, Energy Environ. Sci., 2011, 4, 1946–1971 RSC.
- N. Harsha, K. S. Krishna, N. K. Renuka and S. Shukla, RSC Adv., 2015, 5, 30354–30362 RSC.
- K. Li, F. Chai, Y. Zhao and X. Guo, RSC Adv., 2015, 5, 94397–94404 RSC.
- K. Soutsas, V. Karayannis, I. Poulios, A. Riga, K. Ntampegliotis, X. Spiliotis and G. Papapolymerou, Desalination, 2010, 250, 345–350 CrossRef CAS.
- D. Xu, B. Cheng, S. Cao and J. Yu, Appl. Catal., B, 2015, 164, 380–388 CrossRef CAS.
- F. Z. Yehia, N. G. Kandile, A. M. Badawi and A. H. Mady, Clean: Soil, Air, Water, 2012, 40, 692–697 CAS.
- J. Ding, W. Yan, S. Sun, J. Bao and C. Gao, ACS Appl. Mater. Interfaces, 2014, 6, 12877–12884 CrossRef CAS PubMed.
- S. Farhadi and F. Siadatnasab, Desalin. Water Treat., 2017, 66, 299–308 CrossRef CAS.
- Y. Yao, L. Wang, L. Sun, S. Zhu, Z. Huang, Y. Mao, W. Lu and W. Chen, Chem. Eng. Sci., 2013, 101, 424–431 CrossRef CAS.
- Y. Yao, Y. Cai, F. Lu, F. Wei, X. Wang and S. Wang, J. Hazard. Mater., 2014, 270, 61–70 CrossRef CAS PubMed.
- Y. Yang, J. J. Pignatello, J. Ma and W. A. Mitch, Environ. Sci. Technol., 2014, 48, 2344–2351 CrossRef CAS PubMed.
- H. Tong, S. Ouyang, Y. Bi, N. Umezawa, M. Oshikiri and J. Ye, Adv. Mater., 2012, 24, 229–251 CrossRef CAS PubMed.
- S. Sepahvand and S. Farhadi, RSC Adv., 2018, 8, 10124–10140 RSC.
- F. L. Zhang, Z. Q. Cheng, L. Y. Cui, T. T. Duan, C. F. Zhang and L. J. Kang, RSC Adv., 2016, 6, 1844–1850 RSC.
- H. Y. Zhu, R. Jiang, Y. Q. Fu, R. R. Li, J. Yao and S. T. Jiang, Appl. Surf. Sci., 2016, 369, 1–10 CrossRef CAS.
- T. H. Yu, W. Y. Cheng, K. J. Chao and S. Y. Lu, Nanoscale, 2013, 5, 7356–7360 RSC.
- B. Chai, J. Li, Q. Xu and K. Dai, Mater. Lett., 2014, 120, 177–181 CrossRef CAS.
- S. Z. Zhao, Z. Q. Cheng, L. J. Kang, Y. Y. Zhang and X. D. Zhao, Mater. Lett., 2016, 182, 305–308 CrossRef CAS.
- K. Nakata and A. Fujishima, J. Photochem. Photobiol., C, 2012, 13, 169–189 CrossRef CAS.
- H. Li, T. X. Zhang, C. Pan, C. C. Pu, Y. Hu, X. Y. Hu, E. Z. Liu and J. Fan, Appl. Surf. Sci., 2017, 391, 303–310 CrossRef CAS.
- Y. Wang, J. Sunarsoc, B. Zhao, C. H. Ge and G. H. Chen, Ceram. Int., 2017, 43, 15769–15776 CrossRef CAS.
- M. Ge, Y. Y. Chen, M. L. Liu and M. Li, J. Environ. Chem. Eng., 2015, 3, 2809–2815 CrossRef CAS.
- K. Lakhera, A. Watts, H. Y. Hafeez and B. Neppolian, Catal. Today, 2018, 300, 58–70 CrossRef.
- Y. Xia, Z. He, J. Su, B. Tang, K. Hu, Y. Lu, S. Sun and X. Li, RSC Adv., 2018, 8, 4284–4294 RSC.
- Z.-Q. Song, S.-B. Wang, W. Yang, M. Li, H. Wang and H. Yan, Mater. Sci. Eng., B, 2004, 113, 121–124 CrossRef.
- R. Marandi, A. Sharif, M. Olya and R. Moradi, J. Basic Appl. Sci. Res., 2013, 3, 443–456 Search PubMed.
- C. Karunakaran and A. Vijayabalan, Mater. Sci. Semicond. Process., 2013, 16, 1992–1996 CrossRef CAS.
- B. Pant, H. R. Pant, N. A. Barakat, M. Park, T.-H. Han, B. H. Lim and H.-Y. Kim, Ceram. Int., 2014, 40, 1553–1559 CrossRef CAS.
- H. Wang, X. X. Zhang, A. P. Huang, H. Y. Xu, M. K. Zhu, B. Wang, H. Yan and M. Yoshimura, J. Cryst. Growth, 2002, 246, 150–154 CrossRef CAS.
- A. R. Phani and S. Santucci, J. Phys.: Condens. Matter, 2006, 18, 6965–6978 CrossRef CAS.
- S. A. Bakar, S. T. Hussain and M. Mazhar, New J. Chem., 2012, 36, 1844–1851 RSC.
- A. R. Phani, M. Passacantando and S. Santucci, J. Mater. Sci., 2000, 35, 5295–5299 CrossRef CAS.
- Z. Imran, S. S. Batool, H. Jamil, M. Usman, M. Israr-Qadir, S. H. Shah, S. Jamil-Rana, M. A. Rafiq, M. M. Hasan and M. Willander, Ceram. Int., 2013, 39, 457–462 CrossRef CAS.
- M. de Anda Reyes, G. T. Delgado, R. C. Pérez, J. M. Marín and O. Z. Angel, J. Photochem. Photobiol., A, 2012, 228, 22–27 CrossRef CAS.
- H. Wang, L. Zhang, Z. Chen, J. Hu, S. Li, Z. Wang, J. Liu and X. Wang, Chem. Soc. Rev., 2014, 43, 5234–5244 RSC.
- E. Casbeer, V. K. Sharma and X.-Z. Li, Sep. Purif. Technol., 2012, 87, 1–14 CrossRef CAS.
- S. Saadi, A. Bouguelia and M. Trari, Renewable Energy, 2006, 31, 2245–2256 CrossRef CAS.
- H. Yang, J. Yan, Z. Lu, X. Cheng and Y. Tang, J. Alloys Compd., 2009, 476, 715–719 CrossRef CAS.
- A. Kezzim, N. Nasrallah, A. Abdi and M. Trari, Energy Convers. Manage., 2011, 52, 2800–2806 CrossRef CAS.
- R. Cheng, X. Fan, M. Wang, M. Li, J. Tian and L. Zhang, RSC Adv., 2016, 6, 18990–18995 RSC.
- Y. Ding, L. Zhu, N. Wang and H. Tang, Appl. Catal., B, 2013, 129, 153–162 CrossRef CAS.
- S. Rus, P. Vlazan, S. Novaconi, P. Sfirloaga and I. Grozescu, J. Optoelectron. Adv. Mater., 2012, 14, 293–297 CAS.
- M. Salavati-Niasari, F. Soofivand, A. Sobhani-Nasab, M. Shakouri-Arani, M. Hamadanian and S. Bagheri, J. Mater. Sci.: Mater. Electron., 2017, 28, 14965–14973 CrossRef CAS.
- M. Zhu, D. Meng, C. Wang and G. Diao, ACS Appl. Mater. Interfaces, 2013, 5, 6030–6037 CrossRef CAS PubMed.
- M. S. Hassan, T. Amna and M. S. Khil, Ceram. Int., 2014, 40, 423–427 CrossRef.
- H. P. Klug and L. E. Alexander, X-ray diffraction procedures: for polycrystalline and amorphous materials, Wiley-VCH, 2nd edition, 1974 Search PubMed.
- L. Li, X. D. Huang, T. Y. Hu, J. X. Wang, W. Z. Zhang and J. Q. Zhang, New J. Chem., 2014, 38, 5293–5302 RSC.
- L. Y. Yang, G. P. Feng, T. X. Wang, J. M. Zhang and T. J. Lou, Mater. Lett., 2011, 65, 2601–2603 CrossRef CAS.
- T. I. Draskovic, M. Z. Yu and Y. Y. Wu, Inorg. Chem., 2015, 54, 5519–5526 CrossRef CAS PubMed.
- L. Zou, H. Wang, G. Yuan and X. Wang, ACS Appl. Nano Mater., 2018, 1, 831–838 CrossRef CAS.
- R. Liang, S. Luo, F. Jing, L. Shen, N. Qin and L. Wu, Appl. Catal., B, 2015, 176, 240–248 CrossRef.
- N. Ertugay and F. N. Acar, Appl. Surf. Sci., 2014, 318, 121–126 CrossRef CAS.
- Z. Frontistis and D. Mantzavinos, Ultrason. Sonochem., 2012, 19, 77–84 CrossRef CAS PubMed.
- R. Darvishi Cheshmeh Soltani, A. Khataee and M. Mashayekhi, Desalin. Water Treat., 2016, 57, 13494–13504 CrossRef CAS.
- Y. Yao, Y. Cai, F. Lu, J. Qin, F. Wei, C. Xu and S. Wang, Ind. Eng. Chem. Res., 2014, 53, 17294–17302 CrossRef CAS.
- H. A. Mourão, A. R. Malagutti and C. Ribeiro, Appl. Catal., A, 2010, 382, 284–292 CrossRef.
- L. Li, Y. Zhang, A. M. Schultz, X. Liu, P. A. Salvador and G. S. Rohrer, Catal. Sci. Technol., 2012, 2, 1945–1952 RSC.
- Y. Yao, F. Lu, Y. Zhu, F. Wei, X. Liu, C. Lian and S. Wang, J. Hazard. Mater., 2015, 297, 224–233 CrossRef CAS PubMed.
- S. Kandula and P. Jeevanandam, J. Nanopart. Res., 2014, 16, 2452 CrossRef.
- S. Cravanzola, F. Cesano, G. Magnacca, A. Zecchina and D. Scarano, RSC Adv., 2016, 6, 59001–59008 RSC.
- J. Sun, Y. Fu, P. Xiong, X. Sun, B. Xuc and X. Wang, RSC Adv., 2013, 3, 22490–22497 RSC.
- Y. Shi, K. Zhou, B. Wang, S. Jiang, X. Qian, Z. Gui, R. K. K. Yuen and Y. Hu, J. Mater. Chem. A, 2014, 2, 535–544 RSC.
- M. Mousavi and A. Habibi-Yangjeh, J. Colloid Interface Sci., 2016, 465, 83–92 CrossRef CAS PubMed.
- X. Ren, H. T. Yang, S. Gen, J. Zhou, T. Z. Yang, X. Q. Zhang, Z. H. Cheng and S. H. Sun, Nanoscale, 2016, 8, 752–756 RSC.
- Q. Liang, J. Jin, C. Liu, S. Xu and Z. Li, J. Alloys Compd., 2017, 709, 542–548 CrossRef CAS.
- N. Liang, J. Zai, M. Xu, Q. Zhu, X. Wei and X. Qian, J. Mater. Chem. A, 2014, 2, 4208–4216 RSC.
- Y. Ao, L. Xu, P. Wang, C. Wang, J. Hou and J. Qian, Dalton Trans., 2015, 44, 11321–11330 RSC.
- P. Xiong, J. Zhu and X. Wang, Ind. Eng. Chem. Res., 2013, 52, 17126–17133 CrossRef CAS.
- J. Y. Shen, Z. S. Cui, Z. W. Wu, J. X. Wang, Q. Ning and X. M. Lu, Mater. Res. Innovations, 2015, 19, 187–191 CrossRef.
- T. Zhou, G. Zhang, H. Yang, H. Zhang, R. Suo, Y. Xie and G. Liu, RSC Adv., 2018, 8, 28179–28188 RSC.
- Y. Xia, Z. He, Y. Lu, B. Tang, S. Sun, J. Su and X. Li, RSC Adv., 2018, 8, 5441–5450 RSC.
- T. Zhou, G. Zhang, P. Ma, X. Qiu, H. Zhang, H. Yang and G. Liu, J. Alloys Compd., 2018, 735, 1277–1290 CrossRef CAS.
- T. Cao, Y. Li, C. Wang, C. Shao and Y. Liu, Langmuir, 2011, 27, 2946–2952 CrossRef CAS PubMed.
- Q. Wang, S. Dong, D. Zhang, C. Yu, J. Lu, D. Wang and J. Sun, J. Mater. Sci., 2018, 53, 1135–1147 CrossRef CAS.
- S. Abu-Bakar, S. T. Hussain and M. Mazhar, New J. Chem., 2012, 36, 1844–1851 RSC.
- J. Theerthagiri, R. Senthil, A. Priya, J. Madhavan, R. Michael and M. Ashokkumar, RSC Adv., 2014, 4, 38222–38229 RSC.
- G. P. Dai, J. G. Yu and G. Liu, J. Phys. Chem. C, 2011, 115, 7339–7346 CrossRef CAS.
- D. L. Jiang, L. L. Chen, J. J. Zhu, M. Chen, W. D. Shi and J. M. Xie, Dalton Trans., 2013, 42, 15726–15734 RSC.
- W. J. Yin, L. J. Bai, Y. Z. Zhu, S. X. Zhong, L. H. Zhao, Z. Q. Li and S. Bai, ACS Appl. Mater. Interfaces, 2016, 8, 23133–23142 CrossRef CAS PubMed.
- F.-J. Zhang, M.-L. Chen, K. Zhang and W.-C. Oh, Bull. Korean Chem. Soc., 2010, 31, 133–139 CrossRef CAS.
|
This journal is © The Royal Society of Chemistry 2019 |
Click here to see how this site uses Cookies. View our privacy policy here.