DOI:
10.1039/C8RA10434D
(Paper)
RSC Adv., 2019,
9, 7706-7717
Significantly enhanced dielectric constant and energy storage properties in polyimide/reduced BaTiO3 composite films with excellent thermal stability
Received
20th December 2018
, Accepted 26th February 2019
First published on 7th March 2019
Abstract
In this work, reduced BaTiO3 (rBT) particles with a large number of defects sintered in a reducing atmosphere (95N2/5H2) were introduced into polyimide (PI) matrix without using any modifier or surfactant components. The rBT/PI composite films fabricated by an in situ polymerization method showed significantly enhanced dielectric constant and energy storage density. The dielectric constant of the rBT/PI composite with 30 wt% rBT reached up to 31.6, while maintaining lower loss (tg
δ = 0.031@1000 kHz) compared to pure PI (εr = 4.1). Its energy storage density (9.7 J cm−3 at 2628 kV cm−1) was enhanced by more than 400% over that of pure PI (1.9 J cm−3 at 3251 kV cm−1), and was greater than the energy density of the best commercial biaxially-oriented-polypropylenes (BOPP) (1.2 J cm−3 at 6400 kV cm−1). The energy storage efficiency was around 90% due to the linear dielectric performance of rBT/PI composite films. The improved dielectric constant and energy storage density could be attributed to the combined effect of the interface interaction between two phases and the surface defects of rBT induced by the reducing atmosphere. Therefore, rBT/PI composite films with high dielectric constant, energy storage density and storage efficiency may have potential applications in the preparation of embedded capacitors.
1 Introduction
Polymer materials with high dielectric constant play critical roles in the modern information and electronic industry as embedded capacitors and charge-storage devices because they are light weight, multifunction-integrated and miniaturization-friendly.1–5 Pure polymer materials have many merits including excellent flexibility, low-temperature processing, high electric breakdown strength, and so on.6 However, their low dielectric constant (typically less than 10) impedes their practical applications in capacitors.7 A promising strategy to enhance the dielectric constant of polymer materials is to incorporate ferroelectric materials with high dielectric constant (such as titanium dioxide (TiO2),8,9 BaTiO3,10,11 Pb(Zr,Ti)O3,12,13 BaSrTiO3,14,15 K0.5Na0.5NbO3 (ref. 16 and 17) and CaCu3Ti4O12 (ref. 18 and 19)) into a polymer matrix to form composites.20–23 This approach has been extensively studied for various polymer matrices including poly(vinylidene fluoride) (PVDF), polymethylmethacrylate (PMMA),24 polyimides25 and epoxy resins.26 The dielectric constant of ferroelectric/polymer composite system can be improved by a few times compared to the pure polymer when a high content of ferroelectric particles is incorporated (>50 vol%). Unfortunately, the breakdown strength and energy storage density of these composites are low.27–29 Therefore, it is still a challenge to find an effective way to achieve both high dielectric constant and breakdown strength.
Among the many polymers, polyimides (PI) are widely used as packaging materials, insulating layers, circuit boards and interlayer dielectrics due to their high tensile strength, superior mechanical properties, high glass transition temperature, good resistance to solvents and excellent thermal stability.30–33 PI is now considered to be a promising candidate for polymer composite dielectrics with good temperature stability. For example, Li et al. reported that titanium oxide/PI composites exhibited dielectric constant (εr) of 10.6 and low dielectric loss of <0.03 with 10 wt% high-aspect-ratio titanium oxide nanowires.34 The dielectric properties for some recently reported BT/PI composites are shown in Fig. 1. From these reported results, it can be seen that it is difficult to simultaneously achieve high dielectric constant and low loss (low dielectric breakdown strength) in PI-based composites. In addition to the dielectric properties at room temperature, it is necessary to systematically investigate the thermal stability of PI composites for dielectric capacitors in practical application.
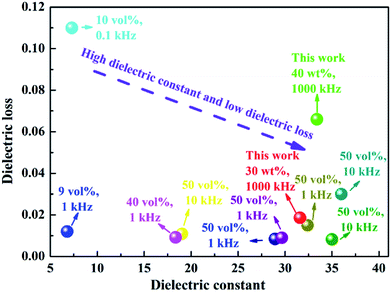 |
| Fig. 1 The dielectric constant and loss of BT/PI composite materials reported in literature.36–43 | |
Compared to BaTiO3 ceramics fabricated in air, BaTiO3 materials sintered in reducing atmosphere exhibit excellent dielectric properties due to their semiconducting properties.35 In this work, reduced BaTiO3 (rBT) particles were introduced into PI matrix to form rBT/PI composite films by in situ polymerization. Notably, the composites were obtained through simply mixing the precursor solution (PAA) and rBT suspension without using any modifier or surfactant components. The dielectric and energy storage properties of rBT/PI composite films were systematically studied. Significantly increased dielectric constant and energy storage density were realized in the as-prepared composite films.
2 Experiments
2.1. Materials
BaTiO3 (BT, 99.9%), BaCO3 (99.8%) and TiO2 (99.8%) were purchased from Alfa Aesar (China) Chemicals Co., Ltd. 4,4′-Diaminodiphenyl ether (ODA), pyromellitic anhydride (PMDA) and N,N-dimethylformamide (DMF, SP grade) were purchased from Aladdin, Shanghai, China. Absolute alcohol (AR grade) was purchased from Tianjin Reagents Co. Ltd. All the reagents were used as received without further purification. Deionized water was prepared in our laboratory.
2.2. Preparation of reduced BaTiO3 (rBT)
rBaTiO3 powder was prepared by a solid-state reaction described by the following equation: |
BaCO3 + TiO2 → BaTiO3 + CO2
| (1) |
High purity metal oxides or carbonates (BaCO3, TiO2) were used as the raw materials in this work. These powders were weighed and ball-milled in a polyethylene bottle with ethyl alcohol and zirconia balls for 24 h, and then dried in an oven at 60 °C for 6 hours. The resulting powder was calcined at 1000 °C for 4 h in air. The calcined powder was ball-milled once in ethyl alcohol for 24 h, and then dried in an oven at 60 °C. Finally, the reduced BT powder was prepared by heat treatment at 1250 °C for 2 h in a reducing atmosphere of N2 and H2 (95/5).
2.3. Preparation of rBT/PI composite films
The rBT/PI composites were prepared by in situ polymerization. First, ODA was dispersed into DMF solvent, and stirred until ODA was completely dissolved in DMF. Then, PMDA was added slowly to ensure complete dissolution, and stirred for 12 h. The as-prepared rBT powder was added into DMF solvent with the contents of 0 wt%, 5 wt%, 10 wt%, 20 wt%, 30 wt%, 40 wt% and 50 wt%, to form a series of suspensions. The suspensions were ultrasonicated for 1 h and then stirred for 12 h. Subsequently, the two solutions were mixed together, ultrasonicated for 1 h and then stirred it for 12 h. Finally, the rBT/PI composite films were prepared via solution casting method on the ITO substrate. The films were subsequently vacuum-dried at 80 °C for 2 h to volatilize the solvent, and then dried at 100 °C/2 h, 120 °C/2 h, 150 °C/1 h, 200 °C/1 h, 250 °C/1 h and 300 °C/1 h to convert completely into rBT/PI composite films. The detailed experimental procedure is described in Fig. 2.
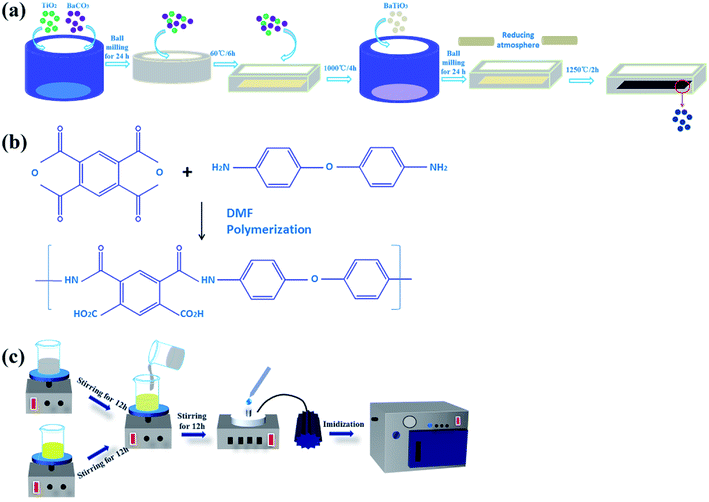 |
| Fig. 2 The preparation process of (a) rBT powder samples, (b) PAA solution (the precursor of PI), and (c) rBT/PI composite films. | |
2.4. Characterization of structure and dielectric properties
The surface and cross-section morphology of the samples were examined by field emission scanning electron microscope (FESEM; JEOL, JSM-6701F) equipped with energy dispersive spectroscopy (EDS, OXFORD). Phase structure of samples was analyzed by an X-ray diffractometer using Cu-Kα radiation (D8 Advanced, Bruker, Germany). Thermal gravimetric analyzer (TGA; TA, STA 449C) was used to perform the thermal analysis of composite films from room temperature to 800 °C with a heating rate of 10 °C min−1 under Ar flow. Bonding energy of elements in BT was measured using X-ray photoelectron spectroscopy (XPS; Kratos, Axis Supra) with Al Kα radiation (hν = 1486.6 eV). Both sides of composite films were sputtered with gold (1 mm diameter and 60 nm thick) as electrodes for measurement of electrical properties. A TH2828S LCR meter was used to measure dielectric properties of composites from frequency 0.1 kHz to 1000 kHz at room temperature. The electric breakdown strength (Eb) was measured using a high-voltage tester (ET2671A, China) at room temperature. During breakdown strength measurements, at least 8 specimens were selected for calculating the average Eb. The polarization–electric (P–E) field loops for rBT/PI composites were measured using a Premier II ferroelectric test system (Radiant Technologies, Inc. Albuquerque, NM).
3 Results and discussion
3.1. Structure characterization
X-ray diffraction (XRD) patterns of BT and rBT powders are shown in Fig. 3(a). The refined scanning (2θ = 40–50°) patterns are also shown in Fig. 3(b). The reduced BaTiO3 had similar XRD pattern as pure BaTiO3 phase. All samples belonged to typical perovskite structure, and no secondary phases were detected. The rBT exhibited a tendency to transform from tetragonal phase to cubic phase, which can be seen from the (002) and (200) peaks. These two peaks gradually overlapped at about 2θ ≈ 45°. Moreover, BT powder sintered under reducing atmosphere exhibited gray color while BT powder sintered in air was white, as shown in the inset of Fig. 3(a). According to many reported results, the blue color of rBaTiO3 powder was attributed to the presence of Ti3+ formed from Ti4+, which may be related to the following two mechanisms: (1) a direct donor-doping process: 2Ti4+ + H2 → 2H+ + 2Ti3+; (2) the loss of oxygen during heat treatment in an atmosphere with low oxygen partial pressure: O2+ → 1/2O2 + 2e−.44–47
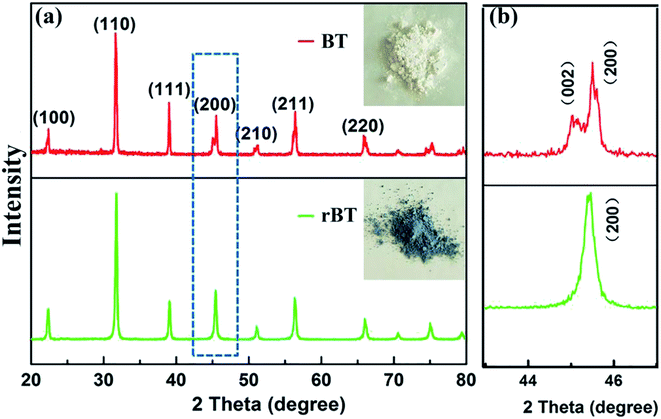 |
| Fig. 3 (a) XRD patterns of BT and rBT, the insets are photographs of BT and rBT powders, and (b) the refined peaks near 45 for BT and rBT. | |
The transition of Ti4+ to Ti3+ and the existence of oxygen vacancies can be further confirmed by XPS analysis, as shown in Fig. 4(b)–(e). The observed XPS spectra of BaTiO3 and rBaTiO3 were consistent with the reported data in literature.48,49 The Ti2p peak of BaTiO3 was split into 4 peaks, which were located at 465.0 eV and 459.8 eV corresponding to Ti2p3/2 and Ti2p3/2 peaks of Ti4+, and 463.9 eV and 458.26 eV corresponding to Ti2p1/2 and Ti2p1/2 peaks of Ti3+, respectively.50 The Ti2p peak of rBaTiO3 can also be deconvoluted into 4 peaks, two of which were located at 464.4 eV and 459.3 eV consistent with the Ti2p3/2 peaks of Ti4+, and the other two peaks were located at 463.5 eV and 458.1 eV, corresponding to the Ti2p1/2 peaks of Ti3+. The ratio of Ti3+/Ti4+ increased from 1.4 to 3.0. The O1s signal displayed two components at 531.6/531.4 eV and 529.4/529.4 eV, which were assigned to lattice O and absorbed O, respectively. The ratio of lattice O/absorbed O decreased from 6.1 to 1.5. The surface area and ratios under the peaks of the BaTiO3 and rBaTiO3 ceramics are listed in Table 1. The area of Ti3+ and absorbed O of rBaTiO3 increased significantly compared to that of BaTiO3 (as shown in the Fig. 4(b)–(e) and Table 1), suggesting that most Ti4+ ions were reduced to Ti3+ ions and the oxygen vacancies increased under the reducing atmosphere (N2/H2).51 According to the XPS survey spectra of BT and rBT powders, the elemental concentration were determined by a Thermo Avantage software. The Ba, Ti, O, and C atomic percentages for BT and rBT powders (BT/rBT) are about 8.85%/7.65% (Ba3d5), 8.72%/8.33% (Ti2p), 45.54%/40.29% (O1s), and 36.89%/34.94% (C1s), respectively. It is found that Ba/Ti ratios is close to 1, which is in agreement with BaTiO3 molecular formula, whereas rBT show a difference of Ti/O ratios, suggesting that there exist many O vacancies.
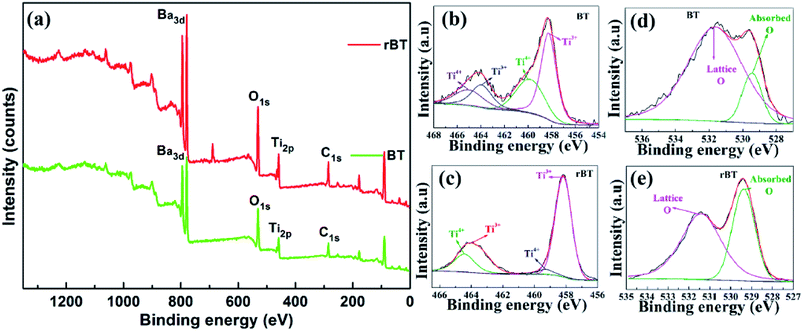 |
| Fig. 4 (a) XPS spectra of BaTiO3 and reduced BaTiO3 powders, (b) and (c) Ti2p and (d), (e) O1s XPS spectra of BaTiO3 and reduced BaTiO3, respectively. | |
Table 1 Fitting parameters of the Ti2p and O1s XPS spectra of rBaTiO3 and BaTiO3 powders
Peak |
Position (eV) |
Area |
FWHM (eV) |
Ti3+ (BT/rBT) |
458.255/458.170 |
6920.090/15 538.830 |
1.541/1.221 |
Ti4+ (BT/rBT) |
459.830/459.300 |
4229.967/1138.511 |
2.785/1.199 |
Ti3+ (BT/rBT) |
463.945/463.488 |
2449.244/4327.734 |
2.060/1.749 |
Ti4+ (BT/rBT) |
465.020/464.433 |
2240.286/4191.682 |
2.889/1.526 |
Lattice O (BT/rBT) |
531.637/531.415 |
30 332.440/32 142.790 |
3.875/2.271 |
Absorbed O (BT/rBT) |
529.444/529.375 |
4984.089/21 128.310 |
1.353/1.264 |
Fig. 5 shows XRD patterns of the fabricated rBT/PI composite films. With increase in mass fractions of rBaTiO3 particles, all composite samples presented a typical polycrystalline perovskite structure of rBaTiO3 particles, characterized by (100), (110), (111), (200), (211) and (211) peaks as compared to rBaTiO3 particles.52 Moreover, the relative intensities of rBT diffraction peaks gradually increased with rBaTiO3 concentrations. The amorphous structure of pure PI was clearly observed by the broad peak at around 2θ = 18°, which was due to the accumulation of PI polymer chains. However, the XRD pattern of polyimide in rBT/PI composite was different from that of pure polyimide. The peak intensities of PI slowly decreased, which was attributed to the high content of rBaTiO3 fillers in the composites. This result suggested that the crystallinity of the pure PI was affected by rBT particles.
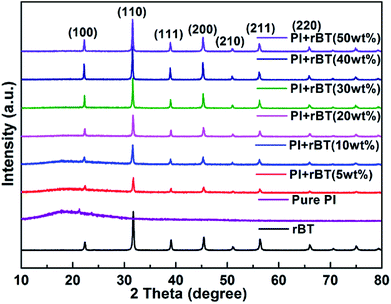 |
| Fig. 5 XRD patterns of the rBT/PI composites with different mass fractions of 0, 5, 10, 20, 30, 40 and 50 wt%. | |
Fig. 6(a) shows the SEM images of the rBaTiO3 particles. The rBaTiO3 particles exhibit plate-like shape, whose particle sizes about 200–500 nm (length or width). The fractured cross-sections of pure PI and rBT/PI composites with different filler fractions are presented in Fig. 6(b)–(h). The fabricated rBT/PI composite films were approximately 7 μm to 14 μm in thickness. Under SEM observation, rBT particles showed no obvious aggregation and were homogeneously dispersed in the PI matrix even when the filler content was up to about 50 wt%. The homogeneous dispersion of the rBT particles contributed to the good dielectric properties of rBT/PI composites.53
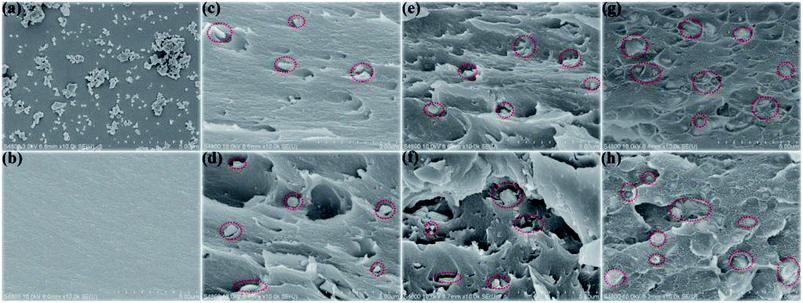 |
| Fig. 6 Scanning electron micrographs of the rBaTiO3 particles, (a) the fractured cross section of pure PI (b) and rBT/PI composites: (c) 5 wt% rBT; (d) 10 wt% rBT; (e) 20 wt% rBT; (f) 30 wt% rBT; (g) 40 wt% rBT; (h) 50 wt% rBT. | |
The thermal stability of pure PI and rBT/PI composites was investigated by TG and DSC, and the curves are shown in Fig. 7. In Fig. 7(a), the TG curves of the rBT/PI composites showed a similar trend as pure PI in the temperature range from 20 to 800 °C, indicating that the rBT powders had no influence on the degradation mechanism of PI matrix.54 Pure PI and rBT/PI composites started to degrade at 510 °C, which may be mainly due to the decomposition of the PI network.55 The values of weight loss rate of composites decreased with the increase in rBT loading, ranging from 31.6% (x = 0 wt%), 30.0% (x = 5 wt%), 28.2% (x = 10 wt%), 26.3% (x = 20 wt%), 22.9% (x = 30 wt%), 21.8% (x = 40 wt%), to 22.5% (x = 50 wt%). Overall, the rBT/PI composites had better thermal stability compared to pure PI, which was ascribed to the homogeneous distribution of rBT particles in the PI matrix.56 The rBT particles acted as barriers in the composites. Consequently, the volatile by-products formed during the pyrolysis could not escape.57 As shown in Fig. 7(b), the crystallization temperature of pure PI was about 621.5 °C. With increasing rBT contents, the crystallization temperature shifted to higher temperature, for example, 653.2 °C (x = 5 wt%), 683.9 °C (x = 10 wt%), 640.7 °C (x = 20 wt%), 673.4 °C (x = 30 wt%), 659.8 °C (x = 40 wt%), 632.9 °C (x = 50 wt%), respectively. The crystallization temperature of rBT/PI composite films rose with increasing rBT content, indicating that the crystallization process was promoted in the polymer matrix through the introduction of rBT powders.58
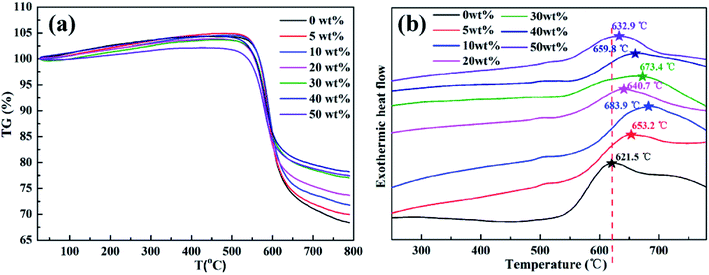 |
| Fig. 7 (a) TG and (b) DSC curves of pure PI and rBT/PI composites with different contents of fillers (0 wt%, 5 wt%, 10 wt%, 20 wt%, 30 wt%, 40 wt% and 50 wt%). | |
3.2. Dielectric properties of the rBT/PI composite films
The frequency dependence of dielectric constant and dielectric loss for rBT/PI composites with various mass fractions is illustrated in Fig. 8. The dielectric constant and dielectric loss of rBT/PI composites exhibited a decreasing trend with increase in frequency. This could be due to the response characteristics of different molecule groups and different chemical structures in different frequency ranges.59 Especially, the dielectric loss was relatively high in the low frequency range. The production of dielectric loss can be ascribed to the accumulation of many free charges at the internal interfaces between rBT and PI matrix. The interface polarization increases with the accumulation of free charges under the applied electric field.60 In the low frequency range, the charges have enough time to accumulate on the interfaces between rBT and PI matrix, which leads to high dielectric loss. In the high frequency range, the interfacial polarization cannot respond to the change in frequency, and thus, the dielectric constant and loss would decrease.61 In the insets of Fig. 8(a) and (b), the dielectric constant and dielectric loss of composite samples changed significantly with different rBT fillers. When the content of rBT increased up to 40 wt%, the dielectric constant reached its maximum of about 33.4 at 1000 kHz, which is considerably higher than that of pure PI (εr = 4.1). Subsequently, the dielectric constant sharply decreased to 23.9 with 50 wt% of rBT content. Correspondingly, the dielectric loss of samples was lower (tg
δ < 0.031) when the rBT content was below 30 wt%. It was found that the rBT/PI composite with the loading of 30 wt% was the best candidate (εr = 31.6, tg
δ = 0.031@1000 kHz) among all the tested composites.
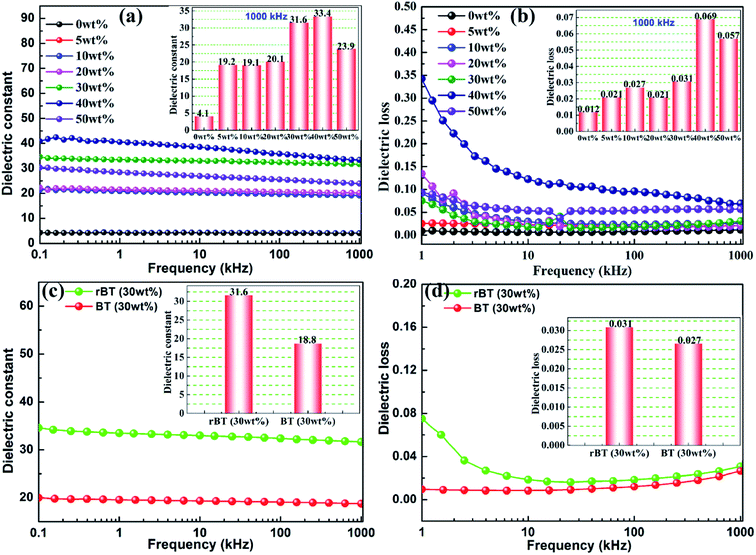 |
| Fig. 8 Frequency dependence of dielectric constant (a) and loss (b) of rBT/PI composites with different rBaTiO3 contents, and frequency dependence of dielectric constant (c) and (d) loss of rBT/PI (30 wt%) and BT/PI (30 wt%) composites. The insets are the dielectric constant and loss values corresponding to the fixed composition and measured frequency (1000 kHz). | |
The rBT/PI composite sample with 30 wt% was selected for comparison with the corresponding non-reduced composite filled with BaTiO3 particles. Dependence of dielectric constant and dielectric loss on frequencies for rBT/PI and BT/PI composites is shown in Fig. 8(c) and (d). The dielectric constant of rBT/PI composite film (εr = 31.6) was evidently higher than the BT/PI composite (εr = 18.8) at 1000 kHz, while maintaining a relatively lower loss (tg
δ = 0.031) compared to that of BT/PI composite (tg
δ = 0.027).
Fig. 9 shows the effect of temperature on the dielectric properties of rBT/PI composites. The dependence of dielectric constant and dielectric loss on temperature ranging from 25 to 370 °C at 1000 kHz was investigated. The dielectric constant of the rBT/PI composites showed no significant fluctuations over the entire temperature range. With increase in temperature, the dielectric constant increased slightly. This may be due to the high temperature resistance of PI. The dielectric loss of rBT/PI composites increased sharply with increase in temperature from 25 to 370 °C when rBT concentration was above 40 wt%. At lower content of rBT, the dielectric loss maintained a lower value over a wide temperature range (tg
δ < 0.08). Generally, the statistical thermal motion of dipole and the charge distribution decide the dielectric properties of the composites.62 In Fig. 9(a) and (b), the dielectric constant of composites, measured at 350 °C, gradually increased with rBT content, and reached its maximum of about 40.2. Dielectric loss showed a lower value (<0.147) when rBT concentration was below 40 wt% than at high concentrations of rBT.
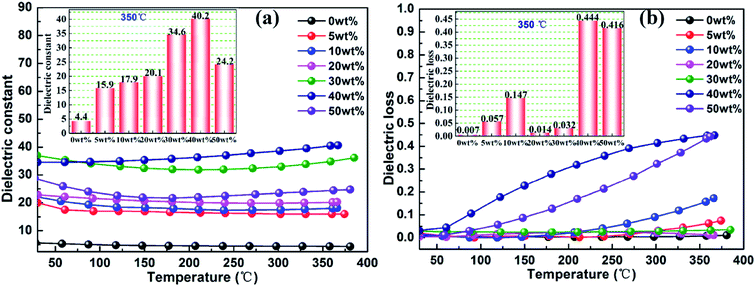 |
| Fig. 9 Temperature dependence of dielectric constant (a) and loss (b) of rBT/PI composites with different rBT concentrations, the insets are the curves of dielectric constant and loss vs. rBT concentration at 350 °C and 1000 kHz. | |
Dielectric breakdown strength (Eb) of composite materials is a crucial parameter to realize capacitor applications. Fig. 10(a) shows the average breakdown strength of rBT/PI composites with different rBT contents. The detailed Eb values at room temperature are listed in Table 2. Clearly, the Eb values gradually decreased with increasing rBT content, as shown in Fig. 10(b), ranging from 3251 kV cm−1 (x = 0 wt%), 3115 (x = 5 wt%), 3064 kV cm−1 (x = 10 wt%), 2810 kV cm−1 (x = 20 wt%), to 2628 kV cm−1 (x = 30 wt%), respectively. With further increase in rBT content, the Eb values reduced significantly from 2179 kV cm−1 (x = 40 wt%) to 1406 kV cm−1 (x = 50 wt%).
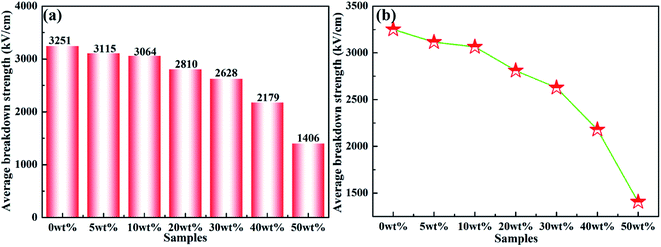 |
| Fig. 10 (a) and (b) Average breakdown strength of rBT/PI composites filled with different rBT contents. | |
Table 2 Dielectric and energy storage properties of rBT/PI composite films
Samples |
Dielectric constant/loss (1000 kHz) |
Dielectric constant/loss (350 °C) |
Average breakdown strength (kV cm−1) |
Energy storage density (J cm−3) |
Sample thickness (μm) |
0 wt% |
4.1/0.012 |
4.4/0.007 |
3251 |
1.9 |
7 |
5 wt% |
19.2/0.021 |
15.9/0.057 |
3115 |
8.2 |
10 |
10 wt% |
19.1/0.027 |
17.9/0.147 |
3064 |
7.9 |
7 |
20 wt% |
20.1/0.021 |
20.1/0.014 |
2810 |
7.0 |
8 |
30 wt% |
31.6/0.031 |
34.6/0.032 |
2628 |
9.7 |
14 |
40 wt% |
33.4/0.031 |
40.2/0.444 |
2179 |
7.0 |
8 |
50 wt% |
23.9/0.057 |
33.2/0.042 |
1406 |
2.1 |
14 |
The polarization–electric field (P–E) curve for a representative composite sample (x = 30 wt%) is presented in Fig. 11(a). It can be seen from the curve that at the electric field of 500 kV cm−1, the maximum polarization reached 1.616 μC cm−2, and the remanent polarization (Pr) remained at a very low value, almost close to zero. A large energy-storage efficiency of about 90% (energy loss = 10%) was achieved in the composite film. P–E curves at higher electric fields (>500 kV cm−1) are not provided due to limitation of instruments. Similar trend was also observed in other composite samples (not shown here). According to the P–E loop, it was evident that the rBT/PI composite film possessed linear dielectric performance. Therefore, its energy storage density (Ue) was calculated using the following formula:
where
εr and
ε0 are the relative dielectric constant and vacuum permittivity, respectively.
Eb is the dielectric breakdown strength. The calculated results of energy storage density for different samples are shown in
Fig. 12(b) and
Table 2. Based on the overall consideration of
Eb and
εr, a high energy density of 9.7 J cm
−3 was achieved at 2628 kV cm
−1 in rBT/PI composite filled with 30 wt% rBT particles. The energy density of the rBT/PI composites was enhanced by more than 400% over that of pure PI (1.9 J cm
−3 at 3251 kV cm
−1). Moreover, the energy density of rBT/PI composites was greater than the energy density of BOPP (1.2 J cm
−3 at 6400 kV cm
−1).
63,64 Therefore, such marked enhancement of energy storage density (
Ue) was a result of introducing rBT particles in the polymer matrix to form the corresponding composite films. Moreover, another favorable property of rBT/PI composites was their ultrahigh energy storage efficiency. These results indicate that rBaTiO
3 can effectively improve the dielectric constant and energy storage density of PI-based composites.
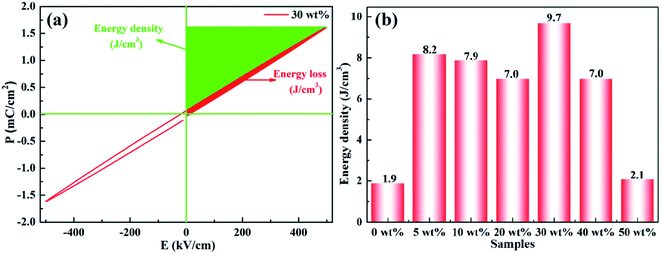 |
| Fig. 11 (a) Room temperature P–E loops of rBT/PI composites with 20 wt% rBT, (b) energy storage density of rBT/PI composites filled with different rBT contents. | |
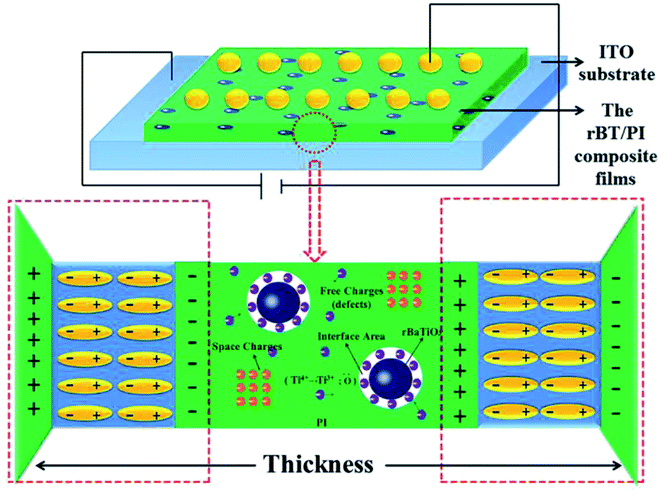 |
| Fig. 12 Schematic model of polarization mechanism for rBT/PI composite films. | |
The above results can be explained according to the proposed polarization mechanism occurring in rBT/PI composites, as shown in Fig. 12. As discussed earlier, there are numerous defects inside the reduced BaTiO3, which are caused by lattice defects including a large number of oxygen vacancies and reduced Ti3+ ions. When rBT particles are introduced into PI to form composites, many space-charge polarization dipoles occur on the interface between rBT particles and PI due to a concentration gradient, which then contribute to the dielectric constant of composites.65,66 As shown in Fig. 8(a), a significant enhancement in dielectric constant was clearly observed at about 30 wt% rBT content. Moreover, the presence of these defects in rBT would facilitate the interface interaction between ceramic particles and polymer, which play an important role in dielectric loss and dielectric breakdown strength properties of composites.67,68 In this work, –COOH chains in PI matrix likely reacted with surface –OH groups of BT to form ester group. The existence of defects in rBT enabled the two phases to bond tightly to each other. These two factors were beneficial for the higher dielectric breakdown strength of rBT/PI composites at a certain content of rBT. However, the increase in rBT content not only enlarged the distance between rBT particles, but also extended the internal stress between the two phases. This may lead to the appearance of microcracking, and consequently lower the breakdown strength. Therefore, when the rBT content was increased up to 40 wt%, the dielectric breakdown strength of rBT/PI composite films decreased significantly.
4 Conclusions
In summary, reduced BaTiO3 (rBT) particles obtained by heating under reducing atmosphere were introduced into PI polymer matrix to form composite films by in situ polymerization method. It was found that the rBT with surface defects played an important role in enhancing dielectric and energy storage properties of PI-based composites. A significant increase in dielectric constant (εr = 31.6@1000 kHz) was realized for the composite sample with 30 wt% rBT, while maintaining a relatively low dielectric loss (tg
δ = 0.031) and high breakdown strength (2628 kV cm−1). The measured energy density for the sample with 30 wt% rBT was as high as 9.7 J cm−3, which was much higher than that of pure PI (1.9 J cm−3). These results suggest that the rBT/PI composites could have potential applications in embedded capacitors.
Conflicts of interest
There are no conflicts of interest to declare.
Acknowledgements
This work was supported by the Natural Science Foundation of China (No. 51462028), the Natural Science Foundation of Inner Mongolia (No. 2016MS0208), Program for Young Talents of Science and Technology in Universities of Inner Mongolia Autonomous Region (NJYT-17-A10), and Program for Innovative Research Team in Universities of Inner Mongolia Autonomous Region (NMGIRT-A1605).
Notes and references
- Z. M. Dang, J. K. Yuan, J. W. Zha, T. Zhou, S. T. Li and G. H. Hu, Fundamentals, processes and applications of high-permittivity polymerematrix composites, Prog. Mater. Sci., 2012, 57(4), 660–723 CrossRef CAS.
- D. Zhang, W. Liu, R. Guo, K. Zhou and H. Luo, High discharge energy density at low electric field using an aligned titanium dioxide/lead zirconate titanate nanowire array, Adv. Sci, 2018, 5(2), 1700512 CrossRef PubMed.
- C. Wu, X. Huang, X. Wu, L. Xie, K. Yang and P. Jiang, Graphene oxide-encapsulated carbon nanotube hybrids for high dielectric performance nanocomposites with enhanced energy storage density, Nanoscale, 2013, 5(9), 3847–3855 RSC.
- H. Luo, D. Zhang, C. Jiang, X. Yuan, C. Chen and K. Zhou, Improved dielectric properties and energy storage density of poly (vinylidene fluoride-co-hexafluoropropylene) nanocomposite with hydantoin epoxy resin coated BaTiO3, ACS Appl. Mater. Interfaces, 2015, 7(15), 8061–8069 CrossRef CAS PubMed.
- B. G. Kim, Y. S. Kim, Y. H. Kim, H. Kim, Y. J. Hong, H. M. Jung and J. C. Won, Nano-scale insulation effect of polypyrrole/polyimide core-shell nanoparticles for dielectric composites, Compos. Sci. Technol., 2016, 129(6), 153–159 CrossRef CAS.
- L. Zhang and Z. Cheng, Development of polymer-based 0-3 composites with high dielectric constant, J. Adv. Dielectr., 2011, 1(4), 389–406 CrossRef CAS.
- A. F. Baldwin, R. Ma, A. Mannodi-Kanakkithodi, T. D. Huan, C. Wang and M. Tefferi, Poly (dimethyltin glutarate) as a prospective material for high dielectric applications, Adv. Mater., 2015, 27(2), 346–351 CrossRef CAS PubMed.
- J. Borges, D. Costa, E. Antunes, C. Lopes, M. S. Rodrigues, M. Apreutesei and L. Cunha, Biological behaviour of thin films consisting of Au nanoparticles dispersed in a TiO2 dielectric matrix, Vacuum, 2015, 122, 360–368 CrossRef CAS.
- H. X. Tang and H. A. Sodano, High energy density nanocomposite capacitors using non-ferroelectric nanowires, Appl. Phys. Lett., 2013, 102(6), 063901 CrossRef.
- H. Luo, Z. Wu, X. Zhou, Z. Yan, K. Zhou and D. Zhang, Enhanced performance of P (VDF-HFP) composites using two-dimensional BaTiO3 platelets and graphene hybrids, Compos. Sci. Technol., 2018, 160, 237–244 CrossRef CAS.
- J. Fu, Y. Hou, M. Zheng, Q. Wei, M. Zhu and H. Yan, Improving dielectric properties of PVDF composites by employing surface modified strong polarized BaTiO3 particles derived by molten salt method, ACS Appl. Mater. Interfaces, 2015, 7(44), 24480–24491 CrossRef CAS PubMed.
- A. K. Zak, W. C. Gan, W. H. A. Majid, M. Darroudi and T. S. Velayutham, Experimental and theoretical dielectric studies of PVDF/PZT nanocomposite thin films, Ceram. Int., 2011, 37(5), 1653–1660 CrossRef CAS.
- H. Tang, Y. Lin and H. A. Sodano, Enhanced energy storage in nanocomposite capacitors through aligned PZT nanowires by uniaxial strain assembly, Adv. Energy Mater., 2012, 2(4), 469–476 CrossRef CAS.
- L. Zhang, P. Wu, Y. Li, Z. Cheng and J. C. Brewer, Preparation process and dielectric properties of Ba0.5Sr0.5TiO3-P(VDF-CTFE) nanocomposites, Composites, Part B, 2014, 56, 284–289 CrossRef CAS.
- J. Shi, H. Fan, X. Liu, Y. Ma and Q. Li, Bi deficiencies induced high permittivity in lead-free BNBT-BST high-temperature dielectrics, J. Alloys Compd., 2015, 627(5), 463–467 CrossRef CAS.
- Z. Liu, H. Fan, S. Lei, X. Ren and C. Long, Duplex structure in K0.5Na0.5NbO3-SrZrO3 ceramics with temperature-stable
dielectric properties, J. Eur. Ceram. Soc., 2017, 37(1), 115–122 CrossRef CAS.
- J. Lin, G. Chen, W. Yang, H. Li and Q. Lei, New potassium sodium niobate/poly(-vinylidene fluoride) functional composite films with high dielectric permittivity, J. Polym. Res., 2016, 23(8), 1–7 Search PubMed.
- J. Li, K. Wu, R. Jia, L. Hou, L. Gao and S. Li, Towards enhanced varistor property and lower dielectric loss of CaCu3Ti4O12 based ceramics, Mater. Des., 2016, 92, 546–551 CrossRef CAS.
- W. Yang, S. Yu, R. Sun and R. Du, Nano and microsize effect of CCTO fillers on the dielectric behavior of CCTO/PVDF composites, Acta Mater., 2011, 59(14), 5593–5602 CrossRef CAS.
- H. Kim, J. Johnson, L. A. Chavez, C. A. G. Rosales, T. L. B. Tseng and Y. Lin, Enhanced dielectric properties of three phase dielectric MWCNTs/BaTiO3/PVDF nanocomposites for energy storage using fused deposition modeling 3D printing, Ceram. Int., 2018, 44(8), 9037–9044 CrossRef CAS.
- S. Wang, J. Sun, L. Tong, Y. Guo, H. Wang and C. Wang, Superior dielectric properties in Na0.35%Ba99.65%Ti99.65%Nb0.35%O3/PVDF composites, Mater. Lett., 2018, 211, 114–117 CrossRef CAS.
- H. Tang, Z. Zhou, C. C. Bowland and H. A. Sodano, Synthesis of calcium coppertitanate (CaCu3Ti4O12) nanowires with insulating SiO2, barrier for low loss high dielectric constant nanocomposites, Nano Energy, 2015, 17, 302–307 CrossRef CAS.
- Y. Yang, Z. Li, W. Ji, C. Sun, H. Deng and Q. Fu, Enhanced dielectric properties through using mixed fillers consisting of nano-barium titanate/nickel hydroxide for polyvinylidene fluoride based composites, Composites, Part A, 2018, 104, 24–31 CrossRef CAS.
- E. Y. Shin, H. J. Cho, S. Jung, C. Yang and Y. Y. Noh, A High-k Fluorinated P (VDF-TrFE)-g-PMMA Gate Dielectric for High-Performance Flexible Field-Effect Transistors, Adv. Funct. Mater., 2018, 28(4), 1704780 CrossRef.
- H. Feng, X. Fang, X. Liu, Q. Pei, Z. K. Cui, S. Deng and Q. Zhuang, Reduced polyaniline decorated reduced graphene oxide/polyimide nanocomposite films with enhanced dielectric properties and thermostability, Composites, Part A, 2018, 109, 578–584 CrossRef CAS.
- Y. Kobayashi, A. Kurosawa, D. Nagao and M. Konno, Fabrication of barium titanate nanoparticles-epoxy resin composite films and their dielectric properties, Polym. Compos., 2010, 31(7), 1179–1183 CAS.
- V. K. Prateek and R. K. Gupta, Recent progress on ferroelectric polymer-based nanocomposites for high energy density capacitors: synthesis, dielectric properties, and future aspects, Chem. Rev., 2016, 116(7), 4260–4317 CrossRef CAS PubMed.
- Z. M. Dang, J. K. Yuan, J. W. Zha, T. Zhou, S. T. Li and G. H. Hu, Fundamentals, processes and applications of high-permittivity polymer-matrix composites, Prog. Mater. Sci., 2012, 57(4), 660–723 CrossRef CAS.
- G. Wang, X. Huang and P. Jiang, Tailoring dielectric properties and energy density of ferroelectric polymer nanocomposites by high-k nanowires, ACS Appl. Mater. Interfaces, 2015, 7(32), 18017–18027 CrossRef CAS PubMed.
- S. Yue, B. Wan, H. Li, Y. Liu and Q. Zhang, Enhanced Dielectric and Energy Storage Properties of the (200)-oriented Plate-like Na0.5Bi0.5TiO3/Polyimide Composite Materials, Int. J. Electrochem. Sci., 2019, 14, 2049–2062 CrossRef.
- H. Y. Lu, C. Y. Chou, J. H. Wu, J. J. Lin and G. S. Liou, Highly transparent and flexible polyimide-AgNW hybrid electrodes with excellent thermal stability for electrochromic applications and defogging devices, J. Mater. Chem. C, 2015, 3(15), 3629–3635 RSC.
- X. F. Lei, Y. Chen, H. P. Zhang, X. J. Li, P. Yao and Q. Y. Zhang, Space survivable polyimides with excellent optical transparency and self-healing properties derived from hyperbranched polysiloxane, ACS Appl. Mater. Interfaces, 2013, 5(20), 10207–10220 CrossRef CAS PubMed.
- G. He, J. Zhou, K. Tan and H. Li, Preparation, morphology and properties of acylchloride-grafted multiwall carbon nanotubes/fluorinated polyimide composites, Compos. Sci. Technol., 2011, 71(16), 1914–1920 CrossRef CAS.
- Y. Li, C. Yang, N. Li, J. Yin, Y. Feng, Y. Liu and X. Liu, Microstructure and electrical properties of polyimide-based composites reinforced by high-aspect-ratio titanium oxide nanowires, Surf. Coat. Technol., 2019, 361, 425–431 CrossRef CAS; Z. M. Dang, Y. Q. Lin, H. P. Xu, C. Y. Shi, S. T. Li and J. Bai, Fabrication and dielectric characterization of advanced BaTiO3/polyimide nanocomposite films with high thermal stability, Adv. Funct. Mater., 2008, 18(10), 1509–1517 CrossRef.
- H. Q. Sun, X. S. Wang and X. Yao, Structure and electric properties of Sm doped BaTiO3 ceramics, Ferroelectrics, 2010, 1(404), 99–104 CrossRef.
- S. H. Choi, I. D. Kim, J. M. Hong, K. H. Park and S. G. Oh, Effect of the dispersibility of BaTiO3 nanoparticles in BaTiO3/polyimide composites on the dielectric properties, Mater. Lett., 2007, 61(11–12), 2478–2481 CrossRef CAS.
- S. H. Xie, B. K. Zhu, X. Z. Wei, Z. K. Xu and Y. Y. Xu, Polyimide/BaTiO3 composites with controllable dielectric properties, Composites, Part A, 2005, 36(8), 1152–1157 CrossRef.
- B. H. Fan, J. W. Zha, D. R. Wang, J. Zhao, Z. F. Zhang and Z. M. Dang, Preparation and dielectric behaviors of thermoplastic and thermosetting polymer nanocomposite films containing BaTiO3 nanoparticles with different diameters, Compos. Sci. Technol., 2013, 80, 66–72 CrossRef CAS.
- M. Wang, W. L. Li, Y. Feng, Y. F. Hou, T. D. Zhang, W. D. Fei and J. H. Yin, Effect of BaTiO3 nanowires on dielectric properties and energy storage density of polyimide composite films, Ceram. Int., 2015, 41(10), 13582–13588 CrossRef CAS.
- W. Sun, X. Lu, J. Jiang, X. Zhang, P. Hu, M. Li and Y. Shen, Dielectric and energy storage performances of polyimide/BaTiO3 nanocomposites at elevated temperatures, J. Appl. Phys., 2017, 121(24), 244101 CrossRef.
- Y. Ding, Q. Wu, D. Zhao, W. Ye, M. Hanif and H. Hou, Flexible PI/BaTiO3 dielectric nanocomposite fabricated by combining electrospinning and electrospraying, Eur. Polym. J., 2013, 49(9), 2567–2571 CrossRef CAS.
- W. Xu, Y. Ding, S. Jiang, W. Ye, X. Liao and H. Hou, High permittivity nanocomposites fabricated from electrospun polyimide/BaTiO3 hybrid nanofibers, Polym. Compos., 2016, 37(3), 794–801 CrossRef CAS.
- Y. H. Wu, J. W. Zha, Z. Q. Yao, F. Sun, R. K. Li and Z. M. Dang, Thermally stable polyimide nanocomposite films from electrospun BaTiO3 fibers for high-density energy storage capacitors, RSC Adv., 2015, 5(56), 44749–44755 RSC.
- D. Makovec, Z. Samardzaija and D. Kolar, Solid solubility of cerium in BaTiO3, J. Solid State Chem., 1996, 123(1), 30–38 CrossRef CAS.
- N. Maso, H. Beltran, E. Cordoncillo, A. A. Flores, P. Escribano, D. C. Sinclair and A. R. West, Synthesis and electrical properties of Nb-doped BaTiO3, J. Mater. Chem., 2006, 16(30), 3114–3119 RSC.
- H. Beltran, E. Cordoncillo and P. Escribano, Oxygen loss,
semiconductivity and positive temperature coefficient of resistance behavior in undoped cation-stoichiometric BaTiO3 ceramics, J. Appl. Phys., 2005, 98(9), 94–102 CrossRef.
- Y. X. Xu, Electroceramics Material, Tianjin University Press, Tianjin, 1993, pp. 183–186 (in Chinese) Search PubMed.
- Q. W. Zhang, J. W. Zhai, Q. Ben, X. Yu and X. Yao, Enhanced microwave dielectric properties of Ba0.4Sr0.6TiO3 ceramics doping by metal Fe powders, J. Appl. Phys., 2012, 112(10), 104104 CrossRef.
- S. Nayak, B. Sahoo, T. K. Chaki and D. Khastgir, Facile preparation of uniform barium titanate (BaTiO3) multipods with high permittivity: impedance and temperature dependent dielectric behavior, RSC Adv., 2014, 4(3), 1212–1224 RSC.
- J. L. Jou, C. M. Lei, Y. W. Xu and W. C. V. Yeh, The higher energy components in Ti2p Xps spectrum of Ga doped barium titanate, Chin. J. Phys., 2012, 50(6), 926–931 CAS.
- Y. Yang, X. Wang, C. Sun and L. Li, Structure study of single crystal BaTiO3 nanotube arrays produced by the hydrothermal method, Nanotechnology, 2009, 20(5), 055709 CrossRef PubMed.
- X. Liu, H. Yang, F. Yan, Y. Qin, Y. Lin and T. Wang, Enhanced energy storage properties of BaTiO3-Bi0.5Na0.5TiO3 lead-free ceramics modified by SrY0.5Nb0.5O3, J. Alloys Compd., 2019, 778, 97–104 CrossRef CAS.
- Z. M. Dang, J. K. Yuan, S. H. Yao and R. J. Liao, Flexible nanodielectric materials with high permittivity for power energy storage, Adv. Mater., 2013, 25(44), 6334–6365 CrossRef CAS PubMed.
- W. Gao, B. Zhou, Y. Liu, X. Ma, Y. Liu and Z. Wang, The influence of surface modification on the structure and properties of a zinc oxide-filled poly(-ethylene terephthalate), Polym. Int., 2013, 62(3), 432–438 CrossRef CAS.
- Z. W. Ouyang, E. C. Chen and T. M. Wu, Enhanced piezoelectric and mechanical properties of electroactive polyvinylidene fluoride/iron oxide composites, Mater. Chem. Phys., 2015, 149(50), 172–178 CrossRef.
- L. J. Fan, W. Wu, X. Y. Huang, J. L. He and P. K. Jiang, Hydrangea-like zinc oxide superstructures for ferroelectric polymer composites with high thermal conductivity and high dielectric constant, Compos. Sci. Technol., 2015, 107(11), 67–74 Search PubMed.
- S. H. Liu, J. W. Zhai, J. W. Wang, S. X. Xue and W. Q. Zhang, Enhanced energy storage density in poly(vinylidene fluoride) nanocomposites by a small loading of suface-hydroxylated Ba0.6Sr0.4TiO3 nanofibers, ACS Appl. Mater. Interfaces, 2014, 6(3), 1533–1540 CrossRef CAS PubMed.
- S. S. Guan, H. Li, S. Zhao and L. Guo, Novel three-component nanocomposites with high dielectric permittivity and low dielectric loss co-filled by carboxyl-functionalized multi-walled nanotube and BaTiO3, Compos. Sci. Technol., 2018, 158(12), 79–85 CrossRef CAS.
- Z. M. Dang, L. Wang, Y. Yin, Q. Zhang and Q. Q. Lei, Giant dielectric permittivities in functionalized carbon-nanotube/electroactive-polymer nanocomposites, Adv. Mater., 2010, 19(6), 852–857 CrossRef.
- M. Tian, Q. Ma, X. L. Li, L. Q. Zhang, T. Nishic and N. Y. Ning, High performance dielectric composites by latex compounding of graphene oxide-encapsulated carbon nanosphere hybrids with XNBR, J. Mater. Chem. A, 2014, 2(29), 11144–11154 RSC.
- P. Mishra and P. Kumar, Dielectric properties of 0.25 (BZT-BCT)-0.75 [(1-x)PVDFxCCTO] (x = 0.02, 0.04, 0.06, 0.08 and 0.1) composites for embedded capacitor applications, Compos. Sci. Technol., 2013, 88(14), 26–32 CrossRef CAS.
- G. X. Hu, F. Gao, J. Kong, S. J. Yang, Q. Q. Zhang and Z. T. Liu, Preparation and dielectric properties of poly(vinylidene fluoride)/Ba0.6Sr0.4TiO3 composites, J. Alloys Compd., 2015, 619(15), 686–692 CrossRef CAS.
- X. Zhang, Y. Shen, Q. H. Zhang, L. Gu, Y. H. Hu, J. W. Du, Y. H. Lin and C. W. Nan, Ultrahigh energy density of polymer nanocomposites containing BaTiO3@TiO2 nanofibers by atomic-scale interface engineering, Adv. Mater., 2015, 27(5), 819–824 CrossRef CAS PubMed.
- C. Zou, Q. Zhang, S. Zhang, D. Kushner, X. Zhou, R. Bernard and R. J. Orchard, PEN/Si3N4 bilayer film for dc bus capacitors in power converters in hybrid electric vehicles, J. Vac. Sci. Technol., B: Nanotechnol. Microelectron.: Mater., Process., Meas., Phenom., 2011, 29, 061401 Search PubMed.
- X. L. Dou, X. L. Liu, Y. Zhang, H. Feng, J. F. Chen and S. Du, Improved dielectric strength of barium titanate-polyvinylidene fluoride nanocomposite, Appl. Phys. Lett., 2009, 95(13), 132904 CrossRef.
- H. Luo, C. Ma, X. Zhou, S. Chen and D. Zhang, Interfacial design in dielectric nanocomposite using liquid-crystalline polymers, Macromolecules, 2017, 50(13), 5132–5137 CrossRef CAS.
- X. Zhang, J. Jiang, Z. Shen, Z. Dan, M. Li, Y. Lin and Y. Shen, Polymer nanocomposites with ultrahigh energy density and high discharge efficiency by modulating their nanostructures in three dimensions, Adv. Mater., 2018, 30(16), 1707269 CrossRef PubMed.
- Z. Pan, L. Yao, J. Zhai, X. Yao and H. Chen, Interfacial coupling effect in organic/inorganic nanocomposites with high energy density, Adv. Mater., 2018, 30(17), 1705662 CrossRef PubMed.
|
This journal is © The Royal Society of Chemistry 2019 |
Click here to see how this site uses Cookies. View our privacy policy here.