DOI:
10.1039/C8RA09517E
(Paper)
RSC Adv., 2019,
9, 3661-3668
Efficient synthesis of C15 fuel precursor by heterogeneously catalyzed aldol-condensation of furfural with cyclopentanone†
Received
19th November 2018
, Accepted 21st January 2019
First published on 28th January 2019
Abstract
The aldol-condensation reaction of biomass-derived furfural and cyclopentanone coupled with hydrogenation/hydrodeoxygenation is a promising route for the production of renewable high-quality diesel or jet fuel. In this paper, we focus on the heterogeneously catalyzed aldol condensation of furfural with cyclopentanone, in order to maximize the yield of 2,5-bis(2-furylmethylidene)cyclopentan-1-one (F2C, a C15 fuel precursor). Experiments were conducted over a series of solid-base catalysts and it was found that potassium fluoride impregnated alumina shown the highest catalytic efficiency. We further investigated the effect of different parameters on the performance of KF/γ-Al2O3, including KF loading amount, solvent, reaction time and temperature. Over KF/γ-Al2O3 with a 33% KF loading amount, the aldol reaction achieved an F2C molar yield up to 95.4% at 333 K within 2 h. Under the nearly optimal condition, the separated solid product is almost F2C with a purity of 100%, providing a high-quality biofuel precursor for the next processing step.
Introduction
Given current concerns about increased fuel demand, declining petroleum resources and the underlying greenhouse effect, it is imperative to exploit sustainable and environment-friendly energy sources for the production of alternative fuels. In this respect, plant biomass is the only current sustainable source of organic carbon, which can be used directly for fuel production.1 In addition, developing fuels from biomass resources can mitigate global warming to some extent, because CO2 released during combustion can be utilized for biomass growth in the next cycle.2,3 Lignocellulose has been considered as the most promising biomass feedstock for the production of renewable fuels with the advantages of abundant reserves, low cost and fast growing. In recent decades, various processing technologies for lignocellulose conversion into a fuel were developed, some of which have been moved to practical application.
General approaches for the conversion of lignocellulosic biomass to liquid fuels include: (i) thermochemical based routes through the combination of gasification and Fischer–Tropsch synthesis to obtain gasoline or diesel, or the pyrolysis/liquefaction processing to get bio-oils,4–8 (ii) hydrolysis based routes using biochemical or catalytic pathways to obtain various platform compounds such as sugars, polyols, furfurals, levulinic acid and γ-valerolactone, as upgradeable intermediates to be converted to transportation fuels range hydrocarbons by different aqueous-phase catalytical strategies.9–14 Although hydrolysis pathways are relatively expensive and complex, especially the step of isolation of carbohydrates from lignocellulose feedstocks, the biomass-derived platform molecules can be processed selectively to yield hydrocarbons with targeted molecular weights and structures.2 Typically, however, lignocellulosic biomass-derived platform compounds has short carbon-chain length (C5 or C6), thus C–C chain formation step acts as an indispensable part in the production of high-quality liquid fuels from these platform molecules. Recent studies have shown that reactions like aldol condensation, hydroalkylation/alkylation, oligomerization, ketonization, Diels–Alder, Guerbet, and acylation are viable approaches to increase carbon-chain length or carbon atom numbers.15,16
Furfural, a great potential fuel intermediate due to its chemical activity, has been produced on industrial scale by hydrolysis/dehydration of polysaccharides.17,18 Beginning with the work of Huber et al.,19 the combination of aldol condensation and dehydration/hydrogenation using furfural and ketones as feedstocks for the synthesis of diesel or jet fuel range alkanes was proposed and developed over different homogeneous or solid base catalysts. Lewis acid zeolite was also used in the condensation of furfural with acetone and exhibited shape selectivity for the aldol products.20 Furthermore, methyl isobutyl ketone, 2-pentanone, 2-heptanone and 3-pentanone were successively applied to the aldol condensation with furfural, generating linear or singly branched alkanes after the later hydrogenation/hydrodeoxygenation.21–24 Aldol condensation plays an important role in this fuel synthesis strategy, by which the carbon-chain length of platform molecules can increase. In our view, the choice of the second reactant in the furfural aldol condensation is a crucial step, which almost determines the structure of final products and fuel quality.
Very recently, the utilization of cyclopentanone as second reactant in furfural aldol condensation for the synthesis of C15 fuel precursor was firstly reported.25 Under either higher reaction temperatures (353–373 K) and lower concentration of NaOH or lower temperatures (313 K) and higher concentration of NaOH, more than 95% yield of fuel precursor, 2,5-bis(2-furylmethylidene)cyclopentan-1-one (F2C), can be obtained in less than 2 hours. With a view to match the green chemistry principles, J. Cueto et al. investigated the feasibility of heterogeneously catalyzed furfural–cyclopentanone cross-condensation using Mg–Zr mixed oxide, yielding up to 60% desired F2C within 4 hours.26,27 Similarly, solid acid catalysts were also studied and Nafion resin exhibited the best performance with 73.86% conversion of furfural and 37.48% selectivity of the C15 product.28 As compared to aforementioned ketone compounds, using cyclopentanone as the second reactant for furfural aldol condensation has some vital advantages. Firstly, as shown in Scheme 1, the obtained final products would have longer carbon chain and contain a cyclic ring, which contribute to a higher density and lower freezing point liquid fuel. In addition, cyclopentanone can be cost-effectively produced through the selectively hydrogenation of furfural,29 thus the final fuel product can be entirely considered to be renewable. However, the development of more efficient heterogeneous catalyst is critical to improve this route for higher yield of C15 fuel precursor while going with the green chemistry principles.
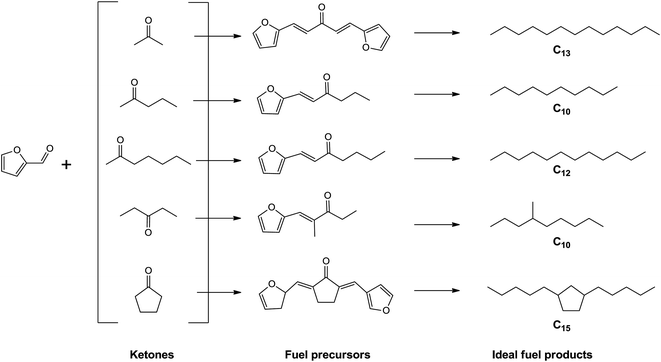 |
| Scheme 1 Comparison of the obtained fuel products using different ketones as second reactants. | |
To that end, we investigated a series of solid base catalysts for furfural–cyclopentanone cross-condensation and found that KF/γ-Al2O3 exhibited great performance under mild condition, achieving a high yield of F2C similarly to using NaOH as catalyst. The effects of KF loading, reaction temperature, reaction time and different solvent on the conversion of furfural and yield of F2C were also studied. Finally, the catalyst stability and reusability of KF/γ-Al2O3 in the aldol condensation of furfural with cyclopentanone was explored and discussed. According to the results, it is believed that the KF/γ-Al2O3 can completely replace NaOH to efficiently catalyse the aldol condensation of furfural with cyclopentanone in this promising biofuel processing route.
Experimental
Materials
Analytical reagents, including furfural, dichloromethane, tetrahydrofuran, methyl alcohol, ethyl alcohol, sodium hydroxide, sodium carbonate, aluminium nitrate nonahydrate, magnesium nitrate hexahydrate, cobaltous nitrate hexahydrate, ziconyl nitrate, calcium oxide, magnesium oxide, gamma aluminum oxide and potassium fluoride dihydrate were purchased from Sinopharm Chemical Reagent Co., Ltd. Cyclopentanone (99%) was purchased from Shanghai Aladdin Bio-Chem Technology Co., Ltd. F2C standard was prepared according to the report,30 and verified by nuclear magnetic resonance (NMR). Furfural was directly used without any preliminary treatment considering the same experimental result.25
Preparation of catalysts
The CaO and MgO were calcined for 4 h in a tube furnace under N2 flow at 873 K and 823 K, respectively.
Magnesia-zirconia (MgO–ZrO2) catalyst was synthesized using the sol–gel technique described by Ordóñez et al.31 The catalyst was prepared by dissolving 50.9 g of magnesium nitrate hexahydrate and 4.04 g of ziconyl nitrate in 1 L of deionized water. The mixture was stirred at room temperature, and a NaOH water solution was added until the pH was equal to 10. The gel was aged for 72 h, filtered and washed with deionized water until pH 7. It was dried at 393 K during 24 h and, finally, it was calcined in air flow at 10 K min−1 until 873 K, and hold at this temperature for 3 h.
Mg–Al hydrotalcite (MgAl-HT) with Mg/Al ratio of 3 was synthesized by co-precipitation at low super-saturation conditions (constant pH) according to the literature.32 The material was prepared by mixing 1 mol mL−1 solutions of magnesium nitrate hexahydrate and aluminium nitrate nonahydrate in 3/1 molar ratio. A volume of 150 mL of this solution was added drop wise to 100 mL of sodium carbonate 0.2 mol mL−1 under sonication at 298 K. The pH was kept at 10 by adding appropriate volumes of 1.6 mol mL−1 NaOH solution. After that, the precipitate was separated by high-speed centrifugation, washed in deionized water in order to remove the alkali metals and the nitrate ions until pH 7, and dried in oven at 373 K for 24 h. The resulting hydrotalcites were calcined in air flow at 723 K for 7 h to obtain the mixed oxides.
The KF/γ-Al2O3 catalysts with different KF loading were prepared through incipient wetness impregnation method. Firstly, the support gamma alumina was calcined in a muffle oven at 823 K for 2 h, in order to evacuate the adsorbed impurities from air. Then the alumina support was impregnated with a certain concentration of KF·2H2O aqueous solution for 48 h. Finally, it was dried absolutely using a freeze drier and calcined in a muffle furnace at 623 K for 2 h before being used.
Co–Al hydrotalcite (CoAl-HT) with Co/Al ratio of 1.5 was prepared by co-precipitation method using cobaltous nitrate hexahydrate and aluminium nitrate nonahydrate as precursors according to the literature.32 An aqueous solution (100 mL) containing 0.027 mol cobaltous nitrate hexahydrate and 0.018 mol aluminium nitrate nonahydrate and a basic solution (100 mL) containing 0.13 mol NaOH and 0.065 mol Na2CO3 were added dropwise into 250 mL of deionized water at room temperature under vigorous stirring to maintain the pH around 10. Then the mixture was aged at 353 K for 24 h under magnetic stirring. After filtering and washing to neutral, the resulting CoAl-HT precursor was dried, then calcined at 573 K for 4 h.
Aldol condensation
The reactions at the temperatures under the solvent boiling point were carried out in a 250 mL three-neck glass reactor equipped with a reflux condenser and a magnetic stirrer. 40 mL ethanol was firstly added into the reactor as solvent and preheated to the targeted temperatures 293, 313 or 333 K controlled by an oil bath. Typically, 1.92 g furfural, 0.84 g cyclopentanone and 0.2 g catalyst were then added into the reactor with a vigorous stirring, and the reaction started. The experiments at 353 and 373 K were performed in a 100 mL stainless steel reactor with a temperature control system. After a certain reaction time, the reactor was quickly cooled down to ambient temperature with water and the resulting mixture was filtered and washed by deionized water several times until no solid product was separated from the filtrate. The product could almost precipitated from the liquid phase because of the insolubility of F2C in water. The total volume of the filtrate was measured and a small amount was collected as a sample. The residue was dissolved in adequate dichloromethane and the spent catalyst was filtered out. The final solid product was obtained after vacuum evaporation of the dichloromethane solution.
Analytical procedure
Nitrogen physical adsorption of the catalysts were conducted by the Quantachrome Autosorb-IQ2 at 77 K. Before the tests, each sample was evacuated at 523 K for 10 h.
Temperature-programmed desorption of carbon dioxide (CO2-TPD), which was used to determine the base strength of the catalysts, was carried out by the Quantachrome Automated Chemisorption Flow Analyzer with a TCD detector. Before each test, 30 mg sample was placed in a U-type quartz tube, flushed by helium flow at 393 K for 50 min and cooled down to 353 K. After the saturated adsorption of CO2, the sample was kept at 353 K in helium flow for 60 min to remove physically adsorbed CO2. The desorption of CO2 was conducted from 353 to 1023 K at a heating rate of 15 K min−1. The base site amount was determined by CO2 impulse adsorption of the catalyst, calibrated with a certainty volume of pure CO2.
X-ray diffraction (XRD) patterns were recorded with a Bruker D8 ADVANCE X-ray diffractometer. The X-ray tube uses Cu as target and released Kα radiation when accelerated at 30 mA and 40 kV.
The concentrations of unreacted reactants in the filtrate and the purity of isolated solid products were determined by Agilent 1260 HPLC, equipped with a ZORBAX Eclipse Plus C18 column (4.6 × 250 mm, 5 μm) and a diode array detector (DAD). Spectral signals were collected from 200 to 500 nm, and the wavelengths of chromatograph were set at 270, 290 and 400 nm for furfural, cyclopentanone and F2C respectively. In isocratic elution mode, a mixture of methanol and water (1
:
1 v/v) was used as mobile phase at the flow-rate of 0.3 mL min−1. All samples were dissolved in the mobile phase with a certain concentration before the tests.
The structural characterization of the isolated product was performed by 1H NMR analysis using a 600 MHz NMR spectrometer (Bruker AVANCE III HD). Before the measurements, the solid sample was dissolved in CDCl3 which containing tetramethylsilane (TMS) as an internal standard, and then filtrated using 0.45 μm membrane.
The conversion of furfural, selectivity and yield of F2C were calculated according to the following formulae:
Results and discussion
Performance of different solid bases
The F2C product is formed from the condensation of one molecule of cyclopentanone and two molecule of furfural, so a constant molar ratio (furfural/cyclopentanone molar ratio 2
:
1) is used in each reaction. The results of furfural–cyclopentanone cross-condensation reactions over different solid-base catalysts are shown in Fig. 1. Among them, KF/γ-Al2O3 with a 20% weight potassium fluoride loading exhibited significantly higher performance than other solid bases, achieving 76% conversion of furfural, 51% yield and 68% selectivity of F2C at 333 K within 2 hours. The activity sequence of different catalysts is KF/Al2O3 > CaO > MgAl-hydrotalcite (MgAl-HT) > CoAl-hydrotalcite (CoAl-HT) > MgO > MgO–ZrO2. Evident consumptions of furfural were also observed in the CaO, MgAl-HT, CoAl-HT, MgO and MgO–ZrO2 catalyzed reactions, whereas the corresponding selectivities of F2C were quite low, yielding the desired product F2C less than 10%. Specifically, MgO–ZrO2, which provided best behavior for acetone–furfural aldol condensation in previous study,33 was rather inactive for F2C production in this reaction which conducted in alcohol solvent system. None of any self-condensation product of cyclopentanone was detected in these reactions, even if MgAl-HT was proved to be active for the self-condensation of cyclopentanone.34 This might be explained by the quicker reaction of furfural with the carbanion formed by cyclopentanone owing to the smaller steric hindrance.35 The low selectivities of the desired F2C are mainly attributed to another product, 2-bis(2-furylmethylidene)cyclopentan-1-one (FC), formed by the condensation of a molecular of furfural and cyclopentanone. Taking account of the aim of this work (to maximum the yield of C15 and guarantee a good quality fuel precursor that will be hydrodeoxygenated to dialkylcyclopentane type of diesel or jet fuels), the FC content in the product mixture should be limited as soon as possible.
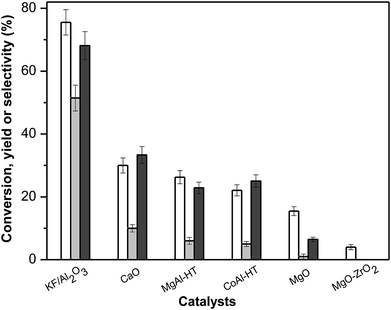 |
| Fig. 1 Conversions of furfural (white bar), yields (grey bar) and selectivities (black bar) of F2C over different solid-base catalysts. Reaction conditions: 333 K, 2 h; 1.92 g furfural, 0.84 g cyclopentanone (furfural/cyclopentanone mole ratio 2 : 1), 40 mL methanol and 0.2 g catalyst were used in each reaction; the KF loading of KF/γ-Al2O3 was 20 wt%. | |
N2 physical adsorption and CO2-TPD tests of these solid-base catalysts were carried out and the results are shown in Table 1 and Fig. 2. It was found that there is an obvious relevance of base strength to catalytical activity in these aldol reactions while the specific surface area and base site amount have little to do with the results. As a traditional base catalyst, CaO has strong base sites and the CO2 desorption peak locates at a high temperature of 868 K. By comparison, KF/γ-Al2O3 prepared in this work has stronger base sites, in that a sharp CO2 desorption peak centered at 913 K was detected, explaining its great performance in the aldol condensation of furfural and cyclopentanone. The low activities of MgAl-HT, CoAl-HT, MgO and MgO–ZrO2 were attributed to fairly weaker basicity, for their CO2 desorption peaks were observed at the temperatures of less than 765 K. The strong base sites on the surface of KF-impregnated alumina are formed from the interaction of KF and Al2O3 during the catalyst preparation, because KF and Al2O3 are both inactive in the reaction when being used alone in separate experiments. It is uncontroversial that KF is a neutral salt and the Al2O3 is a amphoteric oxide, and neither of them could provide strong base site. The XRD patterns of the catalyst and support given in Fig. 3 serve to illustrate the significant changes which take place upon preparation of the catalyst, and it is found that K3AlF6 but not KF is the main species containing F− ion in KF/γ-Al2O3. This result verify the occurrence of the reaction between KF and Al2O3 during the preparation as following scheme shows. Though the nature of the active sites on the catalyst is still a debatable problem in literature,36 it is no doubt that the combination of active fluoride anion as well as the hydroxide anion is accountable for the basicity of the solid surface.
12KF + Al2O3 + 3H2O → 6KOH + 2K3AlF6 |
Table 1 Specific BET surface areas (SBET), and the amounts of base sites on different solid base catalysts
Catalyst |
MgO |
MgO–ZrO2 |
KF/Al2O3 |
CoAl-HT |
MgAl-HT |
CaO |
SBET (m2 g−1) |
32 |
77 |
102 |
125 |
120 |
11 |
Base site amount (mmol g−1) |
0.09 |
0.16 |
0.05 |
0.13 |
0.21 |
0.14 |
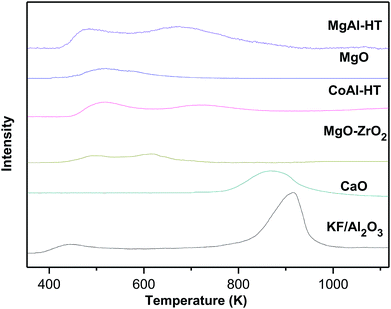 |
| Fig. 2 CO2-TPD curves of different solid-base catalysts. | |
 |
| Fig. 3 XRD patterns of γ-Al2O3 and KF/γ-Al2O3. | |
Regard to the reaction mechanism of the aldol condensation of furfural with cyclopentanone in the catalytical process, the first step of the reaction is the α-proton abstraction from cyclopentanone when this molecule was adsorbed on a strong-strength base site (B−) of KF/γ-Al2O3. Then the formed carbanion subsequently attacks the carbonyl group of furfural molecule and β-hydroxy ketone intermediate is expected to be formed. However, this material was never observed among the reaction products under the reaction conditions of this work. It is assumed that the β-hydroxy ketone could rapidly dehydrated to monomeric FC on acid sites (A−), which were probably provided by Al2O3 support. Finally, in the same form, F2C is obtained by the initial abstraction of the α-proton from FC, forming a carbanion that consecutively attacks the carbonyl group of another adsorbed furfural molecule. This mechanism is depicted in Scheme 2.
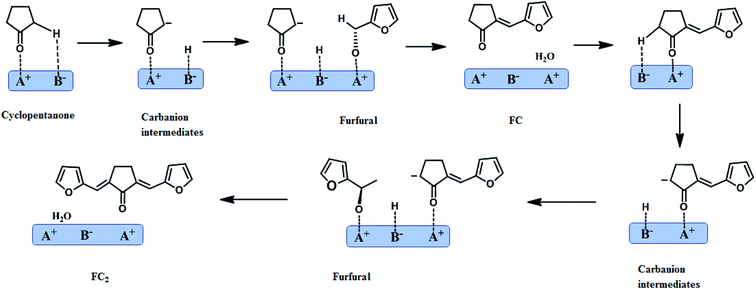 |
| Scheme 2 Proposed pathway for the furfural–cyclopentanone aldol condensation over KF/γ-Al2O3. | |
Effect of KF loading amount on the performance of KF/γ-Al2O3
Noticing the distinctive activity of KF/γ-Al2O3 for the heterogeneously catalyzed furfural–cyclopentanone aldol condensation under the relatively mild condition, we tried to further improve the performance of this catalyst through loading more KF amount on the catalyst. A series of KF/γ-Al2O3 catalysts with different potassium fluoride loading amount were prepared by incipient wetness impregnation, and then used in the aldol condensation of furfural and cyclopentanone. As shown in Fig. 4, the results suggested that the increase of KF loading amount from 20% to 33% contributes to a significant rise of both furfural conversion and F2C yield due to a concomitantly remarkable increase of surface active sites. Specifically, an expected high yield of F2C product was obtained up to 95.4% over the 33 wt% KF/γ-Al2O3, whose activity is almost comparable to that of sodium hydroxide.22 But higher KF content is unnecessary and even adverse, for the slightly decreased performances of 36 wt% and 40 wt% KF/γ-Al2O3 catalysts were observed in the experiments. With the increase of KF content, the activity site amount on the catalyst surface gradually reach saturated and then keep constant, whereas the specific surface areas are still on the decline as shown in Table 2. Although specific surface area of the catalyst is not a leading factor, an excessively low specific area would inevitably have a negative impact on the catalyst performance (e.g., insufficient adsorption of reactants on catalyst surface). The XRD patterns of KF/γ-Al2O3 with different KF loading are shown in Fig. S3.† As the KF content grew, the characteristic peaks of K3AlF6 phase was gradually enhanced and then keep constant, which is consistent with the changing trend of base sites amount. This result corroborate that the active base sites on the catalyst surface originate from the interaction of KF and Al2O3. The obtained yellow solid product over 33 wt% KF/γ-Al2O3 was analyzed by 1H NMR and HPLC and the results are shown in Fig. S1 and S2,† respectively. No signal of the monomer FC was detected as well as other byproduct, which indicates that this alumina-supported KF is highly selective and the product has almost 100% purity of the targeted F2C.
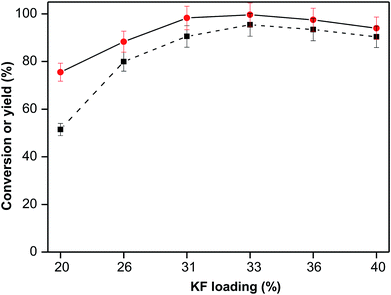 |
| Fig. 4 Conversions of furfural ( ) and yields of F2C ( ) over different loading amount KF/γ-Al2O3. Reaction conditions: 333 K, 2 h; 1.92 g furfural, 0.84 g cyclopentanone (furfural/cyclopentanone molar ratio 2 : 1), 0.2 g catalyst and 40 mL ethanol were used in each reaction. | |
Table 2 SBET and base site amounts of the support and different loading KF/γ-Al2O3
Catalysts or support |
γ-Al2O3 |
γ-Al2O3 with different KF loading (wt%) |
20 |
26 |
31 |
33 |
36 |
40 |
SBET (m2 g−1) |
153 |
102 |
87 |
66 |
59 |
41 |
23 |
Base site amount (mmol g−1) |
— |
0.05 |
0.07 |
0.11 |
0.12 |
0.12 |
0.11 |
Effect of reaction conditions on the aldol condensation over KF/γ-Al2O3
In order to discern the optimum reaction conditions, the influence of various parameters (i.e., solvent, reaction temperature and time) was investigated.
A set of experiments were carried out to evaluate the effect of different solvents including methanol, ethanol, propanol, butanol, water and THF, and the results are described in Table 3. The aldol condensation of furfural with cyclopentanone conducted in methanol yielded product F2C nearly 90%, slightly lower than that in ethanol solvent. This can be explained by the fairly lower solubility of F2C in methanol (Table 3), which would have a bad influence on its transfer rate from catalyst surface to liquid phase. With a higher solubility in propanol and butanol, F2C's yields from the reactions conducted in these two solvents are higher than that in ethanol. It is suggested that a longer carbon chain length of alcohol solvent is beneficial to the aldol condensation of furfural and cyclopentanone over KF/γ-Al2O3. This can be explained by the lower polarity of alcohol solvent with a longer carbon-chain length. Unexpectedly, few of the desired product was detected in the aqueous phase reaction, implying that the KF/γ-Al2O3 catalyst was almost inactive for the reaction in water. The F2C product is practically in-soluble in water at ambient temperature, which might be the reason for the bad catalytical performance. At initial stage of the reaction, the adduct formed and deposited inside the catalyst, inhibiting the further adsorption of reactants on the active sites. The reaction conducted in THF obtained a yield of F2C more than 98%. That is not only because THF can dissolve the product very well, but also it is aprotic solvent which can promote aldol reaction. Among these solvents, anyhow, ethanol is considered as the most appropriate one in the KF/γ-Al2O3 catalyzed aldol condensation of furfural with cyclopentanone, because it is believed to be a cost-effective and green solvent.
Table 3 Solubility of F2C in various solvents at 298 K and effect of solvent on the aldol condensation. Reaction conditions: 333 K, 2 h; 1.92 g furfural, 0.84 g cyclopentanone (furfural/cyclopentanone molar ratio 2
:
1), 0.2 g 33 wt% KF/γ-Al2O3 and 40 mL solvent were used in each reaction
Solvent |
Solubility of F2C, g/100 g |
Conversion of furfural, % |
Yield of F2C, % |
Ref. 25. |
Methanol |
0.40a |
92.9 |
89.7 |
Ethanol |
1.02 |
99.6 |
95.4 |
Propanol |
1.42 |
99.9 |
96 |
Butanol |
1.65 |
99.9 |
96.4 |
Water |
0.01a |
<1 |
0 |
THF |
4.06a |
100 |
98.1 |
Fig. 5 presents the results of aldol condensation of furfural with cyclopentanone at different reaction temperatures. It was found that the reaction at ambient temperature (293 K) was still going fast, yielding more than 90% F2C product within 2 h. The conversion of furfural rose to almost 100% when the reaction temperature reached to 333 K. Meanwhile, the yield of F2C kept increasing at the temperature from 293 to 353 K, but then decreased at higher temperature of 373 K. This result is related to the fact that side reactions are more likely to take place at high reaction temperature.
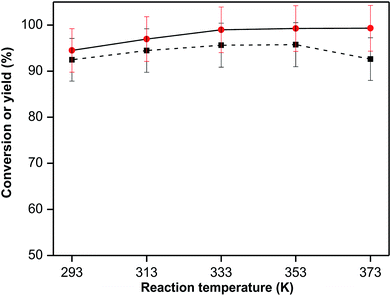 |
| Fig. 5 Furfural conversions ( ) and F2C yields ( ) over 33 wt% KF/γ-Al2O3 at different reaction temperatures. Reaction conditions: 2 h; 1.92 g furfural, 0.84 g cyclopentanone (furfural/cyclopentanone molar ratio 2 : 1), 0.2 g catalyst and 40 mL methanol were used in each reaction. | |
Fig. 6 shows the yield of F2C over KF/γ-Al2O3 as a function of reaction time at 333 K. F2C yield reached nearly 25% and 70% at reaction time of 1 min and 10 min respectively, indicating a remarkably high initial reaction rate. Later, the yield of F2C continued to increase at relatively slow rate until 2 h reaction time and then remained constant.
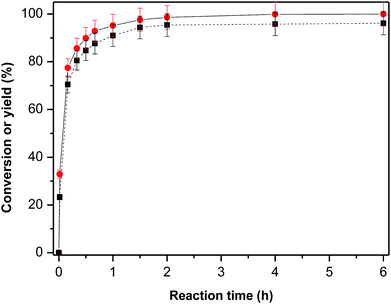 |
| Fig. 6 Furfural conversion ( ) and F2C yield ( ) over 33 wt% KF/γ-Al2O3 as a function of reaction time. Reaction conditions: 333 K; 1.92 g furfural, 0.84 g cyclopentanone (furfural/cyclopentanone molar ratio 2 : 1), 0.2 g catalyst and 40 mL methanol were used in each reaction. | |
Catalyst stability
As another important criterion of practical catalyst, the reusability and stability of KF/γ-Al2O3 in the aldol condensation of furfural with cyclopentanone was investigated. In order to eliminate the impact of residues, the spent catalyst was completely washed with dichloromethane, dried at 353 K for 2 h and calcined under air flow at 623 K for 4 h. Then the catalyst was recycled four times and the results are illustrated in Fig. 7. The performance of the recycled catalysts slightly declined with the cycle number increasing, but a F2C yield higher than 80% was still obtained within 2 hours over the catalyst which had being used for four times. However, such a decreased performance of spent catalyst can not really influence the final yield of the desired product, for a longer reaction time can achieve ideal F2C yield. Significantly, the selectivity of the targeted product F2C had very little change among the catalyst recycle reactions, which means the solid product keeps a high purity as a good fuel precursor. Moreover, we also explored the possible influence of leaching material from the catalyst surface into the liquid reaction mixture which may lead to both the deactivation of catalyst and the presence of undesired homogeneous contribution of aldol condensation reactions. A separate experiment was carried out, in which the solid catalyst of an ongoing reaction was filtrated out and immediately keep the reaction going in the filtrate under the same condition. No evident change of reactant or product concentration was detected during the another 6 h reaction time. It is suggested that the homogeneous contribution of aldol condensation reactions can be ignored. Chemical analysis (ICP) of K+, F− and Al3+ in the reaction medium after reaction reveals that the KF/γ-Al2O3 is quite stable to lixiviation: about 0.2% of Al and 0.5% of KF lixiviated to the liquid during the reaction. Comparing the CO2-TPD curves of the fresh and reused catalysts as shown in Fig. S4,† it was also found that the distribution and strength of base sites on KF/γ-Al2O3 surface changed very little after reused for four times. Overall, KF/γ-Al2O3 exhibited great stability and reusability in the aldol condensation of furfural and cyclopentanone. We believe it has a very bright application prospect as a solid base catalyst for the aldol condensation of furanic aldehydes and ketones in the high-density biofuel processing field.
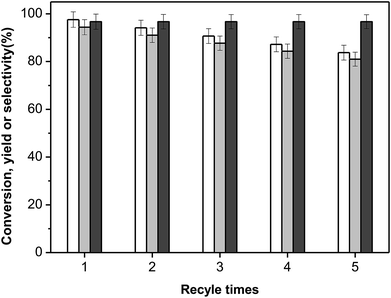 |
| Fig. 7 Conversions of furfural (white bar), yields (grey bar) and selectivities (black bar) of F2C over recycled 33 wt% KF/γ-Al2O3. Reaction conditions: 333 K, 2 h; 1.92 g furfural, 0.84 g cyclopentanone (furfural/cyclopentanone molar ratio 2 : 1), 0.2 g catalyst and 40 mL methanol were used in each reaction. | |
Conclusion
In this work, heterogeneously catalyzed aldol condensation of furfural with cyclopentanone was investigated over a series of solid base catalysts, aiming to maximum the yield of F2C (a high-quality diesel or jet fuel precursor). It has been demonstrated that potassium fluoride impregnated alumina is highly active in this reaction among the tested candidates. Because the prepared KF/γ-Al2O3 has strong base sites formed from the interaction of the salt and support, and the catalytical performance in the aldol condensation largely depends on the base strength. KF loading amount of the catalyst has a significant effect on the reaction, and 33 wt% of KF/γ-Al2O3 has the best catalytical efficiency which almost similar to previously used hydroxide sodium, yielding more than 95% target product within 2 h at the reaction temperature of 333 K. It means that the previously used homogeneous catalyst (NaOH), which has technical, economic and environmental disadvantages, can be completely replaced by heterogeneous KF/γ-Al2O3 in this fuel processing strategy. Significantly, the separated solid product under near optimal condition has almost 100% purity, which is very favorable to obtain high-quality fuel after subsequent hydrogenation/hydrodeoxygenation step.
Conflicts of interest
There are no conflicts to declare.
Acknowledgements
This work was supported by the Fundamental Research Funds for the Central Universities [Grant numbers 2017XKZD10].
References
- G. W. Huber, S. Iborra and A. Corma, Chem. Rev., 2006, 106, 4044–4098 CrossRef CAS PubMed.
- D. M. Alonso, J. Q. Bond and J. A. Dumesic, Green Chem., 2010, 12, 1493–1513 RSC.
- Y. P. Zhang, J. Ind. Microbiol. Biotechnol., 2008, 35, 367–375 CrossRef CAS PubMed.
- D. C. Elliott, D. Beckman, A. V. Bridgwater, J. P. Diebold, S. B. Gevert and Y. Solantausta, Energy Fuels, 1991, 5, 399–410 CrossRef CAS.
- R. R. Soares, D. A. Simonetti and J. A. Dumesic, Angew. Chem., Int. Ed., 2006, 45, 3982–3985 CrossRef CAS PubMed.
- D. A. Simonetti, J. Rass-Hansen, E. L. Kunkes, R. R. Soares and J. A. Dumesic, Green Chem., 2007, 9, 1073–1083 RSC.
- D. J. Hayes, Catal. Today, 2009, 145, 138–151 CrossRef CAS.
- T. R. Carlson, G. A. Tompsett, W. C. Conner and G. W. Huber, Top. Catal., 2009, 52, 241–252 CrossRef CAS.
- S. G. Allen, D. Schulman, J. Lichwa, M. J. Antal, M. Laser and L. R. Lynd, Ind. Eng. Chem. Res., 2001, 40, 2934–2941 CrossRef CAS.
- T. A. Lloyd and C. E. Wyman, Bioresour. Technol., 2005, 96, 1967–1977 CrossRef CAS PubMed.
- G. W. Huber, J. N. Chheda, C. J. Barrett and J. A. Dumesic, Science, 2005, 308, 1446–1450 CrossRef CAS PubMed.
- G. W. Huber and J. A. Dumesic, Catal. Today, 2006, 11, 119–132 CrossRef.
- G. W. Huber, R. D. Cortright and J. A. Dumesic, Angew. Chem., Int. Ed., 2004, 43, 1549–1551 CrossRef CAS PubMed.
- R. R. Davda, J. W. Shabaker, G. W. Huber, R. D. Cortright and J. A. Dumesic, Appl. Catal., B, 2005, 56, 171–186 CrossRef CAS.
- H. Li, A. Riisager, S. Saravanamurugan, A. Pandey, R. S. Sangwan, S. Yang and R. Luque, ACS Catal., 2018, 8, 148–187 CrossRef CAS.
- A. Bohre, S. Dutta, B. Saha and M. M. Abu-Omar, ACS Sustainable Chem. Eng., 2015, 3, 1263–1277 CrossRef CAS.
- R. Karinen, K. Vilonen and M. Niemelä, ChemSusChem, 2011, 4, 1002–1016 CrossRef CAS PubMed.
- C. M. Cai, T. Zhang, R. Kumar and C. E. Wyman, J. Appl. Chem. Biotechnol., 2014, 89, 2–10 CrossRef CAS.
- G. W. Huber, J. N. Chheda, C. J. Barrett and J. A. Dumesic, Science, 2005, 308, 1446–1450 CrossRef CAS PubMed.
- M. X. Su, W. Z. Li, T. W. Zhang, H. S. Xin, S. Li, W. Fan and L. L. Ma, Catal. Sci. Technol., 2017, 7, 3555–3561 RSC.
- N. Li, G. Y. Li, W. T. Wang, A. Q. Wang, X. D. Wang, Y. Cong and T. Zhang, ChemSusChem, 2013, 6, 1149–1152 CrossRef PubMed.
- J. F. Yang, N. Li, S. S. Li, W. T. Wang, L. Li, A. Q. Wang, X. D. Wang, Y. Cong and T. Zhang, Green Chem., 2014, 16, 4879–4884 RSC.
- F. Chen, N. Li, S. S. Li, J. F. Yang, F. Liu, W. T. Wang, A. Q. Wang, Y. Cong and T. Zhang, Catal. Commun., 2015, 59, 229–232 CrossRef CAS.
- T. Shen, C. Zhu, C. Tang, Z. Cao, L. Wang and K. Guo, RSC Adv., 2016, 6, 62974–62980 RSC.
- M. Hronec, K. Fulajtárova, T. Liptaj, M. Štolcová, N. Prónayová and T. Soták, Biomass Bioenergy, 2014, 6, 291–299 CrossRef.
- J. Cueto, L. Faba, E. Díaz and S. Ordóñez, ChemCatChem, 2017, 9, 1765–1770 CrossRef CAS.
- J. Cueto, L. Faba, E. Díaz and S. Ordóñez, J. Chem. Technol. Biotechnol., 2018, 93, 1563–1571 CrossRef CAS.
- W. Wang, X. H. Ji, H. G. Ge, Z. Z. Li, G. H. Tian, X. Z. Shao and Q. Zhang, RSC Adv., 2017, 7, 16901–16907 RSC.
- Y. Zhang, G. Fan, L. Yang and F. Li, Appl. Catal., A, 2018, 561, 117–126 CrossRef CAS.
- S. Y. Ma and Z. B. Zheng, Acta Crystallogr., Sect. E: Struct. Rep. Online, 2009, 65, 3084 CrossRef PubMed.
- L. Faba, E. Díaz and S. Ordóñez, Catal. Today, 2011, 164, 451–456 CrossRef CAS.
- W. J. Xu, H. Liu, J. W. Ren, H. H. Liu, Y. C. Ma, Y. Q. Wang and G. Z. Lu, Microporous Mesoporous Mater., 2011, 142, 251–257 CrossRef CAS.
- L. Faba, E. Díaz and S. Ordóñez, Appl. Catal., B, 2012, 113, 201–211 CrossRef.
- J. F. Yang, N. Li, G. Y. Li, W. T. Wang, A. Q. Wang, X. D. Wang, Y. Cong and T. Zhang, Chem. Commun., 2014, 50, 2572–2574 RSC.
- Q. Deng, J. S. Xu, P. J. Han, L. Pan, L. Wang, X. W. Zhang and J. J. Zou, Fuel Process. Technol., 2016, 148, 361–366 CrossRef CAS.
- B. Basudeb, D. Pralay and D. Sajal, Curr. Org. Chem., 2008, 12, 141–158 Search PubMed.
Footnote |
† Electronic supplementary information (ESI) available. See DOI: 10.1039/c8ra09517e |
|
This journal is © The Royal Society of Chemistry 2019 |
Click here to see how this site uses Cookies. View our privacy policy here.