DOI:
10.1039/C8RA08516A
(Paper)
RSC Adv., 2019,
9, 878-883
Facile solvothermal preparation of Fe3O4–Ag nanocomposite with excellent catalytic performance
Received
15th October 2018
, Accepted 21st November 2018
First published on 8th January 2019
Abstract
Functional nanocomposites demonstrate excellent comprehensive properties and outstanding characteristics for numerous applications. Magnetic nanocomposites are an important type of composite materials, due to their applications in optics, medicine and catalysis. In this report, a new Fe3O4-loaded silver (Fe3O4–Ag) nanocomposite has been successfully synthesized via a simple solvothermal method and in situ growth of silver nanowires. The silver nanowires were prepared via the reduction of silver vanadate with the addition of uniformly dispersed Fe3O4 nanoparticles. Structural and morphological characterizations of the obtained Fe3O4–Ag nanocomposite were carried out using many characterization methods. As a new composite catalyst, the synthesized magnetic Fe3O4–Ag nanocomposite displayed a high utilization rate of catalytically active sites in catalytic reaction medium and showed good separation and recovery using an external magnetic field. The facile preparation and good catalytic performance of this Fe3O4–Ag nanocomposite material demonstrate its potential applications in catalytic treatment and composite materials.
1. Introduction
In recent years, the pollution of water by phenol and aniline compounds has attracted widespread attention worldwide. Among these compounds, 4-nitrophenol (4-NP) belongs to a class of highly toxic compounds, which are difficult to degrade and most difficult to treat. At the same time, 2-nitroaniline (2-NA) has strong water solubility, and can easily penetrate into the soil. The polluted soil then causes pollution of surface water, groundwater and river water. Thus, nitroaniline substances have been listed as key environmental pollutants in many countries. In order to efficiently degrade 2-NA and 4-NP, various nanomaterial catalysts, such as CuO,1 Ag/KCC-1,2 and CuPd,3 have been successfully developed. In particular, among these materials, magnetic nanoparticles have shown great potential in the degradation and catalysis of organic pollutants. Fe3O4 has aroused great research interest in the field of magnetic materials and its wide applications are well established4 in fields such as magnetic resonance imaging (MRI),5 spintronics,6,7 lithium ion batteries,8 catalysis,9 targeted drug delivery10,11 and environmental remediation.12–14 Metal nanoparticles also have many applications, in fields such as catalysis, electronics, optics, optoelectronics, sensing and data storage. Because of their unique properties,15–26 metal nanoparticles represent an important class of components. Ag nanoparticles exhibit many original chemical, physical and catalytic properties as good metal conductors.27 In recent years, self-assembled Ag composite materials have attracted the increasing attention of a large number of scientific researchers, including those in fields such as high-performance nanofilms,28 biosensors,29 electroless copper plating30 and catalytic materials.31–33 Thus, in the present work, Ag nanoparticles were speculated to form a magnetic nanocomposite with Fe3O4 particles, which could be expected not only to show good catalytic performance, but also reduce the loss of Ag nanoparticles and increase reusability.
In this work, Fe3O4 nanoparticles with uniform and controllable sizes were prepared using a modified solvothermal method. Then a uniform Fe3O4–Ag nanocomposite was successfully prepared and characterized by a series of morphological and spectral characterization techniques. The obtained Fe3O4–Ag composite was used as a new catalyst for catalytic reduction reactions of 4-NP and 2-NA, demonstrating good catalytic ability and excellent reusability.
2. Materials and methods
2.1 Materials
Ferric chloride hexahydrate (FeCl3·6H2O) and polyethylene glycol (PEG, Mw ∼6000 g mol−1) were purchased from Aladdin Reagent (Shanghai, China). Ethanol (C2H5OH, analytical reagent) was provided by Sinopharm Chemical Reagent Co., Ltd (Beijing, China). Ethylene glycol (C2H6O2), silver vanadate, and oleylamine were purchased from Alfa Aesar (Beijing, China). Sodium borohydride (NaBH4), sodium hydroxide (NaOH), 4-nitrophenol (4-NP, 99%) and 2-nitroaniline (2-NA, 99%) were obtained from Alfa Aesar (Beijing, China). Ultra-pure water was obtained using a Milli-Q Millipore filter system (Millipore Co., Bedford, MA, USA) with a resistivity of 18.2 MΩ cm−1. All chemicals were used without further purification.
2.2 Fabrication of Fe3O4–Ag nanocomposite
The synthesis of the Fe3O4–Ag nanocomposite was obtained according to the following procedure. Briefly, 1.35 g of ferric chloride hexahydrate (FeCl3·6H2O) was put into 30 mL of ethylene glycol (C2H6O2) to form a dispersed solution. Then 1.0 g of polyethylene glycol (PEG) and 0.8 g of sodium hydroxide (NaOH) were added to the above solution. The above mixed solution was stirred for 30 minutes and transferred into a Teflon-lined stainless-steel autoclave (∼100 mL) for next reaction, which took place for 8 h under a temperature of 180 °C. After completion of the reaction, the black precipitate (i.e., Fe3O4 nanoparticles) was collected using a magnetic block, and washed with deionized water and ethanol repeatedly, followed by drying at 60 °C in a vacuum oven.34 0.635 g of silver vanadate powder and 10 mL of oleylamine were transferred into a 50 mL flask filled with nitrogen gas for a repeated 3 times at room temperature. Then the reaction system was magnetically stirred for 24 hours until the liquid turned from transparent to bright yellow. After this, 2.5 mL of the silver vanadate/oleylamine mixed solution was dropwise added to 40 mL of the Fe3O4 suspension solution (1 mg mL−1) in n-hexane. Then the reaction was continued for 2 h at 70 °C under strong nitrogen agitation and mechanical stirring. The final product was magnetically separated and washed 3 times with ethanol.35
2.3 Catalytic performance test
In order to investigate the catalytic performance of the obtained Fe3O4–Ag nanocomposite, we selected 4-NP and 2-NA as model molecules to characterize the process.36–45 In the catalytic experiments, fresh NaBH4 (20 mL, 0.01 M) solution was added to 2-NA or 4-NP solution (2 mL, 5 mM) at room temperature. NaBH4 was used as a reducing agent for this catalytic reduction reaction. The Fe3O4–Ag composite (10 mg) was added into ethanol (10 mL) to form a stable suspension solution. Then the obtained Fe3O4–Ag composite suspension (300 μL, 1.0 mg mL−1) was added to the 2-NA or 4-NP solution to catalyze the reduction reaction. The progress of this catalytic reaction was monitored using UV-vis spectroscopy at room temperature. For the next recycling experiment, the used F3O4–Ag composite was recovered by magnetic separation, and was then washed with deionized water and ethanol thoroughly several times. The catalytic process was repeated for 8 consecutive cycles using the same solid powder with new fresh 4-NP/2-NA and NaBH4 aqueous solutions.
2.4 Characterization
The prepared nanocomposite material was treated to remove water with a freeze dryer at −48 °C for 48 h using a FD-1C-50 instrument (Beijing Boyikang Experimental Instrument Co., Ltd., China). The morphologies were characterized using transmission electron microscopy with an accelerating voltage of 20 kV (TEM, HT7700, Hitachi High-Technologies Corporation, Japan). The structure of the Fe3O4–Ag composite was investigated using a field-emission scanning electron microscope (SEM, S-4800II, Hitachi, Japan) with an accelerating voltage of 5–15 kV. X-ray diffraction (XRD) characterization was performed using a Rigaku D/max 2550PC diffractometer (SMART LAB, Rigaku, Japan). The XRD patterns were obtained using Cu Kα X-ray radiation with an incident wavelength of 0.1542 nm and current of 200 mA under a voltage of 40 kV. The magnetic properties of the products were characterized using a vibrating sample magnetometer (VSM) of the Physical Property Measurement System (PPMS, Quantum design Model 6000) magnetometer (MPMS-XL, Quantum Design Inc. San Diego, CA, USA) at 300 K. HRTEM photographs were obtained using an FEI Tecnai F20 electron microscope operating at 200 kV (FEI Trading (Shanghai) Co., Ltd, China). X-ray photoelectron spectroscopy (XPS) was performed using a Bragg diffraction setup (SMART LAB, Rigaku, Japan) with an Al Kα X-ray source.
3. Results and discussion
3.1 Characterization of Fe3O4–Ag nanocomposite
Fig. 1 demonstrates the schematic synthesis process of the Fe3O4–Ag nanocomposite. Firstly, magnetic Fe3O4 nanoparticles with well-defined geometries were synthesized using a modified solvothermal method.46–48 It was found that the initial geometry of the Fe3O4 nanoparticles changed with the addition of an initial mass of NaOH.34 After that, the multifaceted geometry of the Fe3O4 nanoparticles was covered with in situ grown silver nanowires. In the process of oleylamine reducing silver vanadate, Ag nanowire crystals grew in situ in the presence of the Fe3O4 nanoparticles under strong mechanical agitation. Then, the scheme illustrates the catalytic reaction of the Fe3O4–Ag nanocomposite with the substrates 4-NP and 2-NA. More specifically, 4-NP was reacted with fresh NaBH4 solution to obtain the product 4-aminophenol (abbreviated as 4-AP). Similarly, in the presence of the Fe3O4–Ag nanocomposite, the reduction process showed the conversion of the reactant 2-nitroaniline to o-phenylenediamine (abbreviated as OPD).49
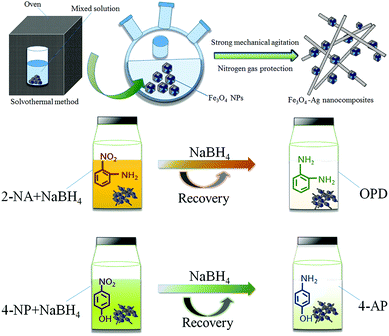 |
| Fig. 1 Schematic illustration of the preparation and catalytic performances of the obtained Fe3O4–Ag nanocomposite. | |
SEM and TEM images in Fig. 2 illustrate the morphology of the initial multifaceted geometry of the Fe3O4 nanoparticles and Fe3O4–Ag nanocomposite. From Fig. 2a and b, it can be seen that the prepared Fe3O4 nanoparticles did not have a smooth spherical surface, when compared with common magnetic particles, but instead exhibited an obvious angular multifaceted geometry. As shown in Fig. 2c and d, organized silver nanowires appeared after reduction by oleylamine.50 The obtained silver nanowires seemed uniform with an average diameter of approximately 40–60 nm with Fe3O4 nanoparticles anchored on the surface.
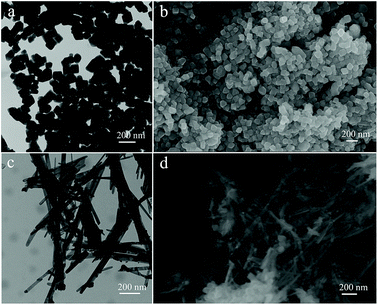 |
| Fig. 2 TEM and SEM images of the prepared Fe3O4 nanoparticles (a and b) and Fe3O4–Ag nanocomposite (c and d). | |
In addition, as shown in Fig. 3, the element mapping results show that the prepared Fe3O4–Ag nanocomposite was mainly composed of elements including Ag, O, and Fe. These elemental maps further verify that the Fe3O4 nanoparticles were surrounded by Ag nanowires and that Ag nanowires were dispersed homogeneously. To gain more information about the microstructure of the Ag nanowire crystals, high-resolution transmission electron microscopic (HRTEM) analysis was necessary. As shown in Fig. 4a, the obtained Ag nanowire crystal showed a clear crystalline structure and distinct lattice fringe. The interplanar spacing was easily resolved with a value of 0.238 nm, corresponding to the Ag (111) crystal plane. In addition, Fig. 4b demonstrates the XRD pattern of the original Fe3O4 nanoparticles compared with that of the Fe3O4–Ag nanocomposite. It can be seen from the XRD data that the pattern of the Fe3O4 nanoparticles demonstrates characteristic diffraction peaks at 2θ values of 30.1°, 35.4°, 43.0°, 53.4°, 57.1° and 62.2°, which corresponded to the (220), (222), (400), (422), (511) and (440) crystals planes, respectively. These results are in good agreement with the standard card (PDF#88-0315).51 In previous reports, many similar test results for the diffraction peaks of Fe3O4 NPs have been described explicitly.52–54 As for the pattern of the Fe3O4–Ag nanocomposite, obvious diffraction peaks could be observed and indexed to the (111), (200), (220) and (311) planes of pure face-centered cubic (fcc) silver crystals.55
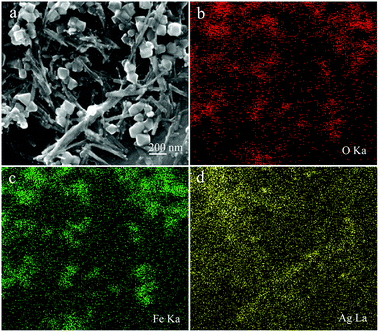 |
| Fig. 3 SEM image (a) and O/Fe/Ag (b, c, and d) elemental mapping of the obtained Fe3O4–Ag nanocomposite. | |
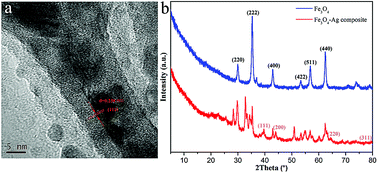 |
| Fig. 4 HRTEM image of Ag nanowires (a) and XRD patterns of the Fe3O4–Ag nanocomposite (b). | |
Fig. 5 demonstrates the magnetization hysteresis loops of the as-prepared Fe3O4 nanoparticles and Fe3O4–Ag nanocomposite at room temperature. The saturation magnetization of the prepared Fe3O4 nanoparticles was 83.0 emu g−1, which is more than the values reported for other pure Fe3O4 nanocrystals.56–59 In addition, the saturation magnetization value of the Fe3O4–Ag nanocomposite was 63.2 emu g−1. These results indicate the successful preparation of the Fe3O4–Ag nanocomposite with a coating of Ag nanowires. X-ray photoelectron spectroscopy (XPS) was used to study the surface composition and elemental states in the composite.60–68 As depicted in Fig. 6a, the wide scan of the XPS spectrum showed characteristic peaks of C1s, O1s, Ag3d and Fe2p from the as-prepared Fe3O4–Ag nanocomposite. From the deconvolution of Ag peaks in Fig. 6b, two peaks appeared in the Ag(3d) binding energy region. One, located at a binding energy of 368.1 eV, is assigned to the Ag(3d5/2) and the other located at 374.1 eV corresponds to Ag(3d3/2) with a distance of 6 eV, which may correspond to the 3d5/2 and 3d3/2 lines of metallic silver, respectively. Compared with the main Ag0 (71%) component, the Ag+ (7%) and Ag2+ (22%) content seemed very small, indicating the successful anchoring of the Ag metal onto the obtained composite.
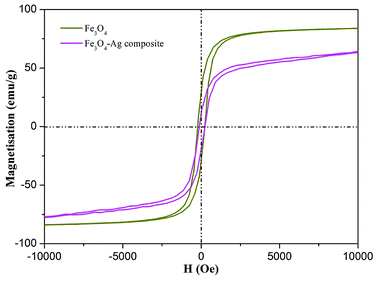 |
| Fig. 5 Magnetization hysteresis loops of as-prepared Fe3O4 nanoparticles and Fe3O4–Ag nanocomposite. | |
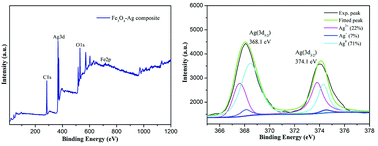 |
| Fig. 6 XPS profiles of the Fe3O4–Ag nanocomposite (a) and the deconvolution of Ag peaks (b). | |
3.2 Catalytic performance
Next, reduction reactions of 4-NP and 2-NA with NaBH4 solution were used to assess the catalytic activity of the as-obtained Fe3O4–Ag nanocomposite. NaBH4 provided negative hydrogen ions to attack 4-NP. As shown in Fig. 7, with the process of the classic reduction reaction, the peak of 4-NP at 402 nm decreased gradually, indicating the formation of 4-AP. It can be observed that a period of 70 min was required to finish the reaction. As for the catalytic reduction of 2-NA, after adding the aqueous NaBH4 solution fully, no significant changes in the 2-NA solution were observed in the characteristic absorption peak at 415 nm, as shown in Fig. 7b. However, after adding the Fe3O4–Ag composite as a catalyst, the absorption peak of 2-NA was significantly reduced, while the system solution changed from bright yellow to pale yellow to colorless simultaneously after only 11 minutes. Fig. 7e and f depict the linear relationship between ln(Ct/C0) and time (t), in which C0 represents the initial concentration, and Ct represents the concentrations of 4-NP at time t. The pseudo-first-order reaction rate constant (k) was fitted and calculated with the values 0.022 and 0.24 min−1 for the reduction reactions of 4-NP and 2-NA, respectively.
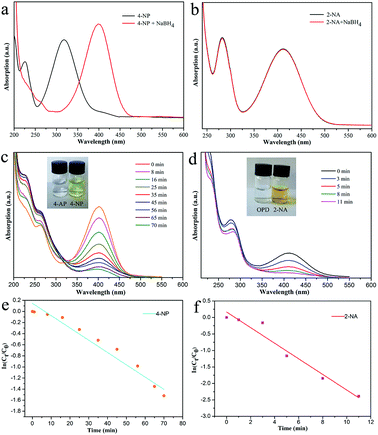 |
| Fig. 7 The spectra of 4-NP and 2-NA with the addition of NaBH4 (a and b). Curves of the catalytic reduction of 4-NP (c) and 2-NA (d). Plots of ln(Ct/C0) versus time for 4-NP (e) and 2-NA (f). Pictures (insets in (c) and (d)) represent the solutions before/after the catalytic reaction. | |
For heterogeneous materials to be used in practical applications, their level of reusability and activity in cycling experiments are critical factors. Therefore, in this work, the reusability of the as-prepared Fe3O4–Ag catalyst was investigated via reduction reactions of 4-NP and 2-NA with fresh NaBH4 solution. The activity of the catalyst was calculated based on the reduction in the reaction rate relative to the initial rate per use. After the catalytic reductions of 4-NP and 2-NA, the Fe3O4–Ag composite catalyst could be easily recovered magnetically from the mixed solution and washed with deionized water and ethanol for the next cycle test. Fig. 8 shows the reusability test of the Fe3O4–Ag composite over eight successive cycles. The material exhibited a stable catalytic conversion of more than 92%, demonstrating its wide applications in material catalysis and composite design. In addition, as shown in Fig. 9, the morphological and elemental mapping results of the Fe3O4–Ag nanocomposite after eight consecutive cycles demonstrate a stable and high dispersion state, highlighting its great potential and high capacity as a new catalyst.
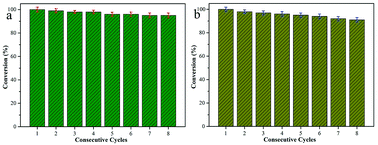 |
| Fig. 8 Reusability test of the present Fe3O4–Ag nanocomposite as a catalyst for the reduction of 4-NP (a) and 2-NA (b) for eight consecutive cycles. | |
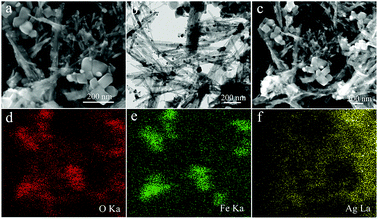 |
| Fig. 9 SEM (a) and TEM (b) images with O/Fe/Ag elemental mapping (d, e, and f) of the Fe3O4–Ag nanocomposite after eight consecutive cycles of catalytic reactions. | |
4. Conclusions
In summary, we have successfully synthesized a Fe3O4–Ag nanocomposite material via a solvothermal method. A series of characterization techniques revealed that Ag nanowires were successfully anchored onto Fe3O4 nanoparticles. The synthesized Fe3O4–Ag composite showed excellent catalytic activity for the reduction of 4-NP and 2-NA in the presence of NaBH4. It is interesting to note that the as-synthesized Fe3O4–Ag composite catalyst demonstrated good reusability even after eight cycles at room temperature. Thus, the as-prepared composite catalyst, with superior catalytic ability, convenient magnetic separation capability and excellent reusability, is expected to have great potential as a magnetic functional composite for various advanced catalytic applications.
Conflicts of interest
There are no conflicts to declare.
Acknowledgements
We greatly appreciate the financial supports of National Natural Science Foundation of China (No. 21872119, 21473153, and 51771162), Support Program for the Top Young Talents of Hebei Province, China Postdoctoral Science Foundation (No. 2015M580214), Research Program of the College Science & Technology of Hebei Province (No. ZD2018091), and Scientific and Technological Research and Development Program of Qinhuangdao City (No. 201701B004).
Notes and references
- W. Che, Y. Ni, Y. Zhang and Y. Ma, J. Phys. Chem. Solids, 2015, 77, 1–7 CrossRef CAS.
- Z. Dong, X. Le, X. Li, W. Zhang and C. Dong, Appl. Catal., B, 2014, 158–159, 129–135 CrossRef CAS.
- H. Saikia, B. J. Borah, Y. Yamada and P. Bharali, J. Colloid Interface Sci., 2017, 486, 46–57 CrossRef CAS PubMed.
- R. Guo, T. Jiao, R. Li, Y. Chen, W. Guo, L. Zhang, J. Zhou, Q. Zhang and Q. Peng, ACS Sustainable Chem. Eng., 2018, 6, 1279–1288 CrossRef CAS.
- S. Xuan, F. Wang and J. M. Y. Lai, ACS Appl. Mater. Interfaces, 2011, 3, 237–244 CrossRef CAS PubMed.
- D. Zhang, Z. Liu, S. Han, C. Li and B. Lei, Nano Lett., 2004, 4, 2151–2155 CrossRef CAS.
- Y. Zhan, R. Zhao, Y. Lei, F. Meng and J. Zhong, J. Magn. Magn. Mater., 2011, 323, 1006–1010 CrossRef CAS.
- J. S. Xu and Y. J. Zhu, ACS Appl. Mater. Interfaces, 2012, 4, 4752–4757 CrossRef CAS PubMed.
- A. H. Lu, W. Schmidt, N. Matoussevitch, H. Boennemann and B. Spliethoff, Angew. Chem., Int. Ed., 2004, 43, 4303–4306 CrossRef CAS PubMed.
- Y. Zhu, Y. Fang and S. Kaskel, J. Phys. Chem. C, 2010, 114, 16382–16388 CrossRef CAS.
- Y. Chen, H. Chen, D. Zeng, Y. Tian and F. Chen, ACS Nano, 2010, 4, 6001–6013 CrossRef CAS PubMed.
- S. Linley, T. Leshuk and F. X. Gu, ACS Appl. Mater. Interfaces, 2013, 5, 2540–2548 CrossRef CAS PubMed.
- Y. Liu, Y. Wang, S. Zhou, S. Lou and L. Yuan, ACS Appl. Mater. Interfaces, 2012, 4, 4913–4920 CrossRef CAS PubMed.
- Q. Cheng, F. Qu, N. B. Li and H. Q. Luo, Anal. Chim. Acta, 2012, 715, 113–119 CrossRef CAS PubMed.
- Y. Sun and C. Lei, Angew. Chem., Int. Ed., 2010, 48, 6824–6827 CrossRef PubMed.
- S. Xie, N. Lu, Z. Xie, J. Wang and M. J. Kim, Angew. Chem., Int. Ed., 2012, 124, 10412–10416 CrossRef.
- Y. Li and W. J. Shen, Sci. China: Chem., 2012, 55, 2485–2496 CrossRef CAS.
- N. Tian, Z. Y. Zhou, S. G. Sun, Y. Ding and Z. L. Wang, Science, 2007, 38, 732–735 CrossRef PubMed.
- A. R. Tao, S. Habas and P. Yang, Small, 2010, 4, 310–325 CrossRef.
- S. Yang, Z. Peng and H. Yang, Adv. Funct. Mater., 2008, 18, 2745–2753 CrossRef CAS.
- J. Jiu, T. Sugahara, M. Nogi and K. Suganuma, J. Nanopart. Res., 2013, 15, 1–13 CrossRef.
- A. Manivannan, G. Glaspell and M. S. Seehra, J. Appl. Phys., 2003, 94, 6994–6996 CrossRef CAS.
- B. H. Hong, S. C. Bae, C. W. Lee, S. Jeong and K. S. Kim, Science, 2001, 294, 348–351 CrossRef CAS PubMed.
- X. Zhang, M. A. Young, O. Lyandres and R. P. Van Duyne, J. Am. Chem. Soc., 2005, 127, 4484–4489 CrossRef CAS.
- J. L. West and N. J. Halas, Annu. Rev. Biomed. Eng., 2003, 5, 285–292 CrossRef CAS PubMed.
- C. J. Murphy, A. M. Gole, J. W. Stone, P. N. Sisco and A. M. Alkilany, Acc. Chem. Res., 2008, 40, 1721–1730 CrossRef PubMed.
- K. Li, T. Jiao, R. Xing, G. Zou, J. Zhou, L. Zhang and Q. Peng, Sci. China Mater., 2018, 61, 728–736 CrossRef.
- H. Gao, Y. Li, C. Li, F. Ma, Z. Song and K. Xu, RSC Adv., 2016, 6, 30998–31004 RSC.
- L. Wang, A. Shen, X. Li, Y. Zeng, X. Zhou, R. M. Richards and J. Hu, RSC Adv., 2014, 4, 34294–34302 RSC.
- J. Hu, S. Wu, Q. Cao and W. Zhang, RSC Adv., 2016, 6, 81767–81773 RSC.
- Q. Wang, X. Zhao, X. K. Zhang, Y. I. Lee and H. G. Liu, RSC Adv., 2015, 5, 69339–69347 RSC.
- A. Barrera, F. Tzompantzi, J. Campa-Molina, J. E. Casillas, R. Pérez-Hernández, S. Ulloa-Godinez, C. Velasquez and J. Arenas-Alatorre, RSC Adv., 2018, 8, 3108–3119 RSC.
- P. Gnanaprakasam and T. Selvaraju, RSC Adv., 2014, 4, 24518–24525 RSC.
- T. Jiao, Y. Liu, Y. Wu, Q. Zhang, X. Yan, F. Gao, A. J. P. Bauer, J. Liu, T. Zeng and B. Li, Sci. Rep., 2015, 5, 12451 CrossRef CAS PubMed.
- Y. Liu, C. Hou, T. Jiao, J. Song, X. Zhang, R. Xing, J. Zhou, L. Zhang and Q. Peng, Nanomaterials, 2018, 8, 35 CrossRef.
- W. Guo, Q. Wang, G. Wang, M. Yang and W. Dong, Chem.–Asian J., 2013, 8, 1160–1167 CrossRef CAS PubMed.
- W. Guo, J. Jiao, K. Tian and Y. Tang, RSC Adv., 2015, 5, 102210–102218 RSC.
- M. Liang, R. Su, W. Qi, Y. Yu and L. Wang, J. Mater. Sci., 2014, 49, 1639–1647 CrossRef CAS.
- W. Guo, Q. Wang, Y. Luan, G. Wang and W. Dong, Chem.–Asian J., 2015, 10, 701–708 CrossRef CAS PubMed.
- S. Peng, F. Gao, D. Zeng, C. Peng and Y. Chen, Cellulose, 2018, 25, 1–12 CrossRef.
- Z. Sun, H. Li, G. Cui, Y. Tian and S. Yan, Appl. Surf. Sci., 2016, 360, 252–262 CrossRef CAS.
- Q. Du, L. Tan, B. Li, T. Liu and J. Ren, RSC Adv., 2014, 4, 56057–56062 RSC.
- Y. Liu, Y. Y. Zhang, Q. W. Kou, Y. Chen and D. L. Han, RSC Adv., 2018, 8, 2209–2218 RSC.
- U. Kurtan, E. Onuş, Md. Amir and A. Baykal, J. Inorg. Organomet. Polym., 2015, 25, 1120–1128 CrossRef CAS.
- S. Huo, P. Duan, T. Jiao, Q. Peng and M. Liu, Angew. Chem., Int. Ed., 2017, 56, 12174–12178 CrossRef CAS PubMed.
- Q. Han, Z. Wang, J. Xia, S. Chen and X. Zhang, Talanta, 2012, 101, 388–395 CrossRef CAS PubMed.
- X. Du, P. Guo, H. Song and X. Chen, Electrochim. Acta, 2010, 55, 4812–4819 CrossRef CAS.
- X. Zhao, T. Jiao, R. Xing, H. Huang and J. Hu, RSC Adv., 2017, 7, 49923–49930 RSC.
- H. Shi, C. Zhou and C. Zhang, Res. Chem. Intermed., 2015, 41, 1–13 CrossRef.
- H. Wang, J. Deng, Y. Chen, F. Xu and Z. Wei, Nano Res., 2016, 9, 1–9 CrossRef CAS.
- L. Sun, X. Hong, P. Zou, X. Chu and Y. Liu, J. Alloys Compd., 2012, 535, 91–94 CrossRef CAS.
- X. Zhou, Y. Shi, L. Ren, S. Bao and Y. Han, J. Solid State Chem., 2012, 196, 138–144 CrossRef CAS.
- G. Basina, G. Mountrichas, E. Devlin, N. Boukos and D. Niarchos, J. Nanosci. Nanotechnol., 2009, 9, 4753–4759 CrossRef CAS.
- D. Chen, X. Qiao, X. Qiu, J. Chen and R. Jiang, J. Colloid Interface Sci., 2010, 344, 286–291 CrossRef CAS PubMed.
- P. Hervés, M. Pérez-Lorenzo, L. M. Liz-Marzán, J. Dzubiella and Y. Lu, Chem. Soc. Rev., 2012, 41, 5577–5587 RSC.
- J. Zhou, Y. Liu, T. Jiao, R. Xing, Z. Yang, J. Fan, J. Liu, B. Li and Q. Peng, Colloids Surf., A, 2018, 538, 7–13 CrossRef CAS.
- J. Zhou, F. Gao, T. Jiao, R. Xing, L. Zhang, Q. Zhang and Q. Peng, Colloids Surf., A, 2018, 545, 60–67 CrossRef CAS.
- X. Luo, K. Ma, T. Jiao, R. Xing, L. Zhang, J. Zhou and B. Li, Nanoscale Res. Lett., 2017, 12, 99 CrossRef PubMed.
- K. Chen, J. Li, L. Zhang, R. Xing, T. Jiao, F. Gao and Q. Peng, Nanotechnology, 2018, 29, 445603 CrossRef PubMed.
- R. Xing, K. Liu, T. Jiao, N. Zhang, K. Ma, R. Zhang, Q. Zou, G. Ma and X. Yan, Adv. Mater., 2016, 28, 3669–3676 CrossRef CAS PubMed.
- H. Guo, T. Jiao, Q. Zhang, W. Guo, Q. Peng and X. Yan, Nanoscale Res. Lett., 2015, 10, 272 CrossRef PubMed.
- R. Xing, W. Wang, T. Jiao, K. Ma, Q. Zhang, W. Hong, H. Qiu, J. Zhou, L. Zhang and Q. Peng, ACS Sustainable Chem. Eng., 2017, 5, 4948–4956 CrossRef CAS.
- X. Zhao, K. Ma, T. Jiao, R. Xing, X. Ma, J. Hu, H. Huang, L. Zhang and X. Yan, Sci. Rep., 2017, 7, 44076 CrossRef PubMed.
- J. Song, R. Xing, T. Jiao, Q. Peng, C. Yuan, H. Möhwald and X. Yan, ACS Appl. Mater. Interfaces, 2018, 10, 2368–2376 CrossRef CAS PubMed.
- X. Huang, T. Jiao, Q. Liu, L. Zhang, J. Zhou, B. Li and Q. Peng, Sci. China Mater., 2019, 62, 423–436 Search PubMed.
- C. Wang, S. Sun, L. Zhang, J. Yin, T. Jiao, L. Zhang, Y. Xu, J. Zhou and Q. Peng, Colloids Surf., A, 2019, 561, 283–291 CrossRef CAS.
- S. Sun, C. Wang, S. Han, T. Jiao, R. Wang, J. Yin, Q. Li, Y. Wang, L. Geng, X. Yu and Q. Peng, Colloids Surf., A, 2019, 564, 1–9 CrossRef CAS.
- Y. Xu, B. Ren, R. Wang, L. Zhang, T. Jiao and Z. Liu, Nanomaterials, 2019, 9, 10 CrossRef PubMed.
|
This journal is © The Royal Society of Chemistry 2019 |
Click here to see how this site uses Cookies. View our privacy policy here.