Synthesis of high-density and low-freezing-point jet fuel using lignocellulose-derived isophorone and furanic aldehydes†
Received
28th April 2018
, Accepted 28th June 2018
First published on 30th June 2018
Abstract
Biofuels synthesized from lignocellulose-derived platform chemicals are very attractive for sustainable development. Here we reported a new and facile route to synthesize multi-substituted cycloalkanes with a high density and low freezing point using isophorone and furanic aldehydes (furfural and 5-hydroxymethylfurfural), by solvent-free aldol condensation, followed by hydrodeoxygenation. Catalysts were screened and NaOH showed good performance. The reaction conditions including catalyst dosage, isophorone/furanic aldehyde ratio, temperature and solvent were optimized, and finally the yields of 70.0% for isophorone/furfural and 72.8% for isophorone/5-hydroxymethylfurfural were obtained. Pt/HZSM-5 was prepared as the bifunctional catalyst for hydrodeoxygenation of the condensed product. The resultant multi-substituted cyclohexanes derived from isophorone/furfural and isophorone/5-hydroxymethylfurfural have a density of 0.813 g mL−1 and 0.846 g mL−1 respectively and both have a freezing point lower than −75 °C, and are very promising as stand-alone fuels or additives of other biofuels.
1. Introduction
High-density jet fuels have higher density than conventional jet fuels, and thus can provide more propulsion energy to extend the flight distance and flight speed and increase the payload of volume-limited aerospace vehicles like military missiles and spacecrafts.1,2 High-density jet fuels are generally composed of cycloalkanes to afford high density, like currently used JP-10, RJ-7 and RJ-5,3 which are generally synthesized using feedstocks derived from petroleum. As a response to the increasing concern on CO2 emission and depletion of fossil energy, production of jet fuels or jet fuel range hydrocarbons from biomass-derived feedstocks has attracted increasing attention.4,5 So far much work has been done on the synthesis of jet fuel range straight and branched paraffins using lignocellulose-derived platform chemicals including γ-valerolactone,6 furanic aldehyde,7,8 2-methylfuran,9,10 methyl isobutyl ketone,11,12etc. Nonetheless, these hydrocarbons have relatively low density compared with petroleum derived hydrocarbons and cannot be used as stand-alone fuels.13 To get higher density, cyclic hydrocarbons such as branched monocycloalkanes and polycycloalkanes have been synthesized by C–C coupling reactions like alkylation,14–17 aldol condensation,18–22 Diels–Alder addition,23 Michael addition,24 oligomerization,25–27 and Robinson annulation,28 followed by hydrodeoxygenation. For example, cyclic molecules have been synthesized by reductive coupling/pinacol rearrangement of cyclic ketones (cyclopentanone and cyclohexanone),29 dehydration/oligomerization/rearrangement of cyclopentanol,27 and alkylation of phenols (phenol, anisole, and guaiacol) with benzyl ether or benzyl alcohols.15,30
Another important requirement for jet fuel is the low-temperature properties, especially the freezing point and viscosity. A desirable jet fuel must have a low freezing point and low-temperature viscosity because aerospace vehicles often work at very low temperature like high altitude or cold weather. Although polycycloalkane biofuels have relatively high density, their freezing point and viscosity are relatively high. Notably, branched cycloalkanes have shown excellent low-temperature properties. For example, a mixture of pentylcyclohexanes synthesized using aromatic oxygenates and furfuryl alcohol, or 2-methylfuran and cyclohexane, as a feedstock shows a relatively high density (0.804 g mL−1) and very low freezing point (−80 °C).16,17 And multi-substituted cycloalkane synthesized using mesityl oxide and 2-methylfuran as a feedstock has higher density (0.82 g mL−1) and a little higher but acceptable freezing point (−56 °C),14 but this synthesis requires a complex procedure including alkylation, hydrolysis, intramolecular aldol condensation and hydrodeoxygenation. With these considerations, here we aimed to synthesize jet fuel range hydrocarbons with the structure of multi-substituted cyclohexane to get both high density and excellent low-temperature properties by a simple synthetic procedure using easily obtained biomass-derived platform chemicals as feedstocks.
Furanic aldehydes including furfural and 5-hydroxymethylfurfural are important chemicals which can be produced on an industrial scale by the hydrolysis–dehydration of hemicellulose or cellulose.5 Isophorone is the cyclic trimer condensate of acetone from the acetone–butanol–ethanol fermentation of lignocellulose.31 Considering its multi-substituted cyclic structure, isophorone should be a good building brick to synthesize methyl-substituted cyclohexane. Meanwhile furanic aldehydes are ideal units to further introduce branched chains. Therefore in this work, we presented a new and facile route to synthesize multi-substituted cycloalkanes using isophorone and furanic aldehydes as feedstocks, by solvent-free aldol condensation followed by hydrodeoxygenation. Such hydrocarbons have both a high density and low freezing point, and are promising as renewable high-density fuels or fuel additives to improve the density and reduce the freezing point of other biofuels.
2. Experimental section
2.1 Chemicals
Furfural (99%) and isophorone (97%) were obtained from Aladdin Co., China. 5-Hydroxymethylfurfural (5-HMF, 98%) was supplied by Beijing Ouhe Technology Co., Ltd. All the chemicals used in this work were not further purified, and the base catalysts were all analytical reagents. Pd/C (5 wt%) was obtained from Shaanxi Rock New Materials Co., Ltd. Palladium dichloride (PdCl2) was supplied by Tianjin Guangfu Fine Chemical Research Institute. Chloroplatinic acid (H2PtCl6·6H2O, 99.95%) was supplied by Beijing HWRK Chem Co., Ltd. HZSM-5 (SiO2/Al2O3 = 27) and Hβ (SiO2/Al2O3 = 25) were purchased from Nankai Catalysts Company.
2.2 Catalyst preparation
Bifunctional hydrodeoxygenation catalysts were synthesized using the incipient wetness impregnation method. The supports (HZSM-5, Hβ) were immersed in an aqueous solution of H2PtCl6·6H2O or PdCl2 and kept overnight at room temperature to achieve sufficient impregnation. Then they were dried at 120 °C for 12 h and calcined at 580 °C for 3 h, and the catalysts were then reduced using hydrogen at 350 °C for 4 h.
2.3 Aldol condensation
Aldol condensation was carried out in a round-bottom flask with a reflux condenser and mechanical agitation. Typically, 70 mmol isophorone and 70 mmol furanic aldehyde were heated to a defined temperature (from 10 °C to 90 °C) and then a defined amount of catalyst (from 6.30 mmol to 15.75 mmol) was added. During the reaction the liquid mixture was sampled regularly and the catalyst was removed from the organic phase by washing. The sampled mixture was dissolved in dichloromethane for analysis. The organic mixture was analyzed qualitatively using an Agilent 6890/5975 GC-MS equipped with an HP-5 capillary column (30 m × 0.5 mm) and analyzed quantitatively by gas chromatography (Agilent 7820A).
The conversion and selectivity were calculated as follows:
2.4 Hydrodeoxygenation reaction
The liquid condensed products were purified by washing before the hydrodeoxygenation reaction. Hydrodeoxygenation was carried out in a 100 mL batch autoclave (EasyChem E100). The reactor was loaded with 1 g condensed product, 50 mL H2O and a defined amount of catalyst, purged with H2 3 times and then heated to 200 °C at 6 MPa of H2. After hydrodeoxygenation, the organic phase was extracted from water with ethyl acetate, analyzed qualitatively using an Agilent 6890/5975 GC-MS equipped with an HP-5 capillary column (30 m × 0.5 mm) and analyzed quantitatively by gas chromatography (Agilent 7820A). Finally, the biofuels were obtained by vacuum distillation. The yield was calculated as follows (C14 for isophorone/furfural and C15 for isophorone/5-HMF):
2.5 Measurements of fuel properties
The density was measured using a Mettler Toledo DE40 density meter according to ASTM D4052. The freezing point was measured according to ASTM D2386, and the kinematic viscosity was determined using a capillary viscometer according to ASTM D445. The net heat of combustion was measured using the IKA-C6000 isoperibol Package 2/10 Calorimeter according to ASTM D240-02.
3. Results and discussion
3.1 Aldol condensation of isophorone and furfural
The aldol condensation of isophorone and furfural under the catalysis of alkali hydroxides produces mono-condensed 6-(2-furanylmethylene)-3,5,5-trimethyl-2-cyclohexen-1-one (IF, mass spectra in Fig. S1†) as the major product, along with a small amount of di-condensed 2,6-bis(2-furanylmethylene)-3,5,5-trimethyl-3-cyclohexen-1-one (FIF, mass spectra in Fig. S2†) as the byproduct, as shown in Scheme 1. The aldol condensation is triggered by the proton abstraction from the α-carbon of isophorone, and then the formed carbanion attacks the carbonyl group of furfural to form β-hydroxy ketone that is finally dehydrated to a mono-condensed product (IF).32,33 Similarly, FIF is formed by the further cross-condensation of IF with furfural. Fig. 1 presents the product distribution in the aldol condensation of isophorone and furfural. The conversion of both reactants increases with the increase of reaction time. Since the formation of FIF requires two furfural molecules while the IF only needs one furfural molecule, the formation of FIF is more difficult than IF. Especially at a longer reaction time, the concentration of the feedstock (especially furfural) decreases to a very low level, which suppresses the formation of FIF. As one can see the selectivity of IF increases slightly but that of FIF decreases after 2 hours. Besides, neither 2-furanic acid nor furfuryl alcohol is present in detectable amounts, suggesting that the Cannizzaro disproportion of furfural does not occur under these conditions although it is a base-catalyzed reaction.34 Also the self-condensation of isophorone is not seen because it is hard to take place under basic catalysis.35 Therefore in this work we can consider the selectivity of IF and FIF only.
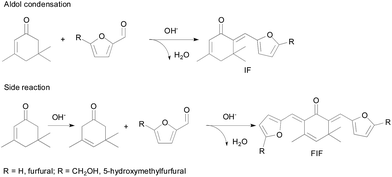 |
| Scheme 1 Aldol condensation of isophorone and furanic aldehydes. | |
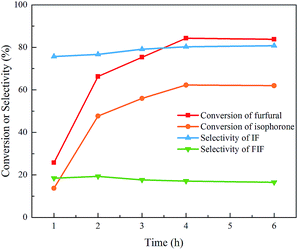 |
| Fig. 1 Product distribution in the aldol condensation of isophorone and furfural. Reaction conditions: 70 mmol isophorone, 70 mmol furfural, 30 °C, 9.45 mmol NaOH. | |
Since the generation of the carbanion is the first step for the base-catalyzed aldol condensation and the basicity of the catalyst may have a strong influence on the reaction,21 several catalysts including KOH, NaOH, Ba(OH)2 and Ca(OH)2 were tested in this work. As shown in Fig. 2, among the tested catalysts KOH shows the highest activity due to the strongest basicity, but the selectivity of IF is not the highest. It is because the strong basicity of KOH promotes the isomerization of isophorone to β-isophorone and then the β-isophorone condenses with furfural to form di-condensed FIF. NaOH exhibits a little lower conversion but the selectivity of IF is the highest, because the basicity is not so strong as KOH. Ba(OH)2 shows very low activity and Ca(OH)2 is nearly inactive even with prolonged time and higher temperature, indicating that the basicity is not strong enough to generate carbanion species. Overall NaOH shows the best performance to produce IF, so its dosage is further optimized to improve the reaction. As shown in Fig. 3, the conversion of both furfural and isophorone gradually increases when more catalyst is added, but the effect is limited when the dosage of NaOH exceeds 12.60 mmol. The selectivity of IF goes up first with the increase of NaOH dosage and then goes down when the dosage of NaOH exceeds 9.45 mmol, but overall the effect of catalyst dosage is not so obvious as compared with the conversion.
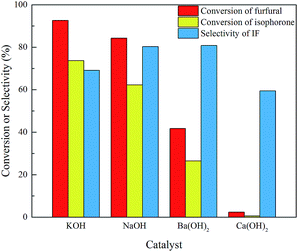 |
| Fig. 2 Activity of different catalysts on the aldol condensation of isophorone and furfural. Reaction conditions: 70 mmol isophorone, 70 mmol furfural, 9.45 mmol catalyst, 30 °C and 4 h for NaOH (KOH), 90 °C and 24 h for Ba(OH)2 (Ca(OH)2). | |
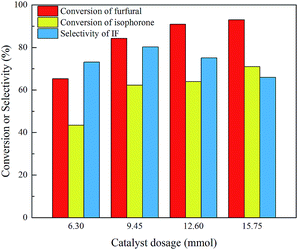 |
| Fig. 3 Effect of NaOH dosage on the aldol condensation of isophorone and furfural. Reaction conditions: 70 mmol isophorone, 70 mmol furfural, 30 °C, 4 h. | |
Furthermore, the effect of temperature and molar ratio of the feedstock on the aldol condensation of isophorone and furfural was investigated. As shown in Fig. 4, with the temperature increasing from 10 °C to 70 °C, the conversion of furfural and isophorone rises from 39.0% and 21.5% to 99.6% and 76.5%, respectively. However, the selectivity of IF keeps nearly unchanged as the temperature increases. The conversion of furfural and isophorone and the selectivity of IF can reach 99.6%, 76.5% and 84.2% within 4 h at 70 °C, respectively. Since the by-product (FIF) is generated from di-condensation between two furfural molecules with one isophorone molecule, it is expected that reducing the concentration of furfural in the feedstock could inhibit the side reaction. Unfortunately, as shown in Fig. 5, the selectivity of the mono-condensation product does not change with the ratio of furfural/isophorone. The reason may be that the formation of FIF requires two α-H in the ring of isophorone to condense with two furfural molecules at the same time, and isophorone has to be isomerized β-isophorone first to produce FIF.36 In this case, it is the basicity of the catalyst, rather than the molar ratio or temperature, that determines the isomerization of isophorone to β-isophorone and thus the formation of FIF.
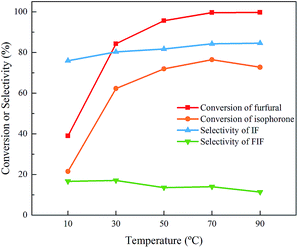 |
| Fig. 4 Effect of temperature on the aldol condensation of isophorone and furfural. Reaction conditions: 70 mmol isophorone, 70 mmol furfural, 4 h, 9.45 mmol NaOH. | |
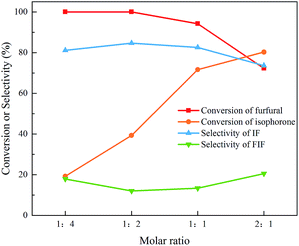 |
| Fig. 5 Effect of furfural/isophorone ratio on the aldol condensation of isophorone and furfural. Reaction conditions: 70 mmol isophorone, 70 °C, 0.5 h, 9.45 mmol NaOH. | |
Subsequently, we studied the effect of solvent on this reaction, as shown in Fig. 6. It is found that adding strong polar solvents like DMF slightly promotes the conversion of the feedstock and the selectivity of IF. In water, the selectivity of IF is also slightly promoted, however, the conversion of furfural and isophorone decreases obviously because the presence of water (the product of aldol condensation) suppresses the reaction equilibrium.21 Although the organic alcohols (methanol and ethanol) accelerate the reaction, the selectivity of IF becomes extremely low due to the formation of considerable FIF. Low reaction activity is observed in the presence of THF and hexane solvents due to the insolubility of the catalyst. Overall the use of solvent cannot improve the reaction significantly but increases the cost, so a solvent-free reaction is used in this work, and under the optimal reaction conditions (9.45 mmol NaOH, 70 °C, 0.5 h), the conversion of furfural and isophorone and the selectivity of IF can reach 99.6%, 76.5% and 84.2%, respectively.
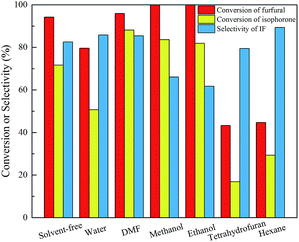 |
| Fig. 6 Effect of solvent on the aldol condensation of isophorone and furfural. Reaction conditions: 70 mmol isophorone, 70 mmol furfural, 70 °C, 0.5 h, 9.45 mmol NaOH, 15 mL solvent. | |
3.2 Aldol condensation of isophorone and 5-hydroxymethylfurfural
We further explored the aldol condensation of isophorone and 5-HMF. In this reaction, 6-(5-hydroxymethyl-2-furylmethylidene)-3,5,5-trimethyl-2-cyclohexen-1-one (mass spectra in Fig. S3†) is the mono-condensed product, and the selectivity can approach over 90% under optimized reaction conditions. In comparison with furfural, 5-HMF is more promising because it can be easily produced using glucose and fructose which is more abundant lignocellulose, moreover a longer carbon chain can be obtained that may increase the density of the final product. Similar to the reaction of isophorone and furfural, NaOH shows good activity and selectivity in this reaction, and the conversion of the feedstock increases with the increase of both catalyst dosage and temperature, see Table 1. But a higher selectivity of the mono-condensed product (93%) can be approached because the hydroxymethyl group in 5-HMF brings about steric hindrance that makes the di-condensation reaction difficult to occur. Also water is unfavorable for the condensation. Under optimized conditions (9.45 mmol NaOH, 50 °C, 2 h), the conversion of 5-HMF, isophorone and the selectivity of IF can reach 100%, 68.6% and 93.0%, respectively.
Table 1 Results of aldol condensation of isophorone and 5-HMFa
Run |
Temperature (°C) |
NaOH (mmol) |
Conversion of isophorone (%) |
Conversion of 5-HMF (%) |
Selectivity of IF(%) |
Reaction conditions: 70 mmol isophorone, 70 mmol 5-HMF, 2 h.
10 mL H2O was added.
|
1 |
30 |
6.30 |
55.8 |
100 |
89.6 |
2 |
30 |
9.45 |
57.5 |
85.5 |
91.3 |
3 |
30 |
12.60 |
67.0 |
100 |
86.1 |
4 |
30 |
15.75 |
74.4 |
97.5 |
92.8 |
5 |
50 |
9.45 |
68.6 |
100 |
93.0 |
6b |
50 |
9.45 |
55.7 |
90.0 |
97.0 |
7 |
70 |
9.45 |
88.2 |
98.8 |
85.9 |
3.3 Hydrodeoxygenation of the mono-condensed product
The mono-condensed products of furfural (or 5-HMF) and isophorone were further hydrodeoxygenated to C14–C15 multi-substituted cyclohexane in the aqueous phase, as shown in Scheme 2. Based on the GC-MS analysis, the predominant product is 1,1,5-trimethyl-2-pentyl-cyclohexane (mass spectra in Fig. S4†) and 1,1,5-trimethyl-2-hexyl-cyclohexane (mass spectra in Fig. S5†), respectively. The major side-reaction is the cracking of chains on the C6 ring, which produces small molecular alkanes and C12–C13 naphthenes. As suggested in the literature, hydrogenation of the carbonyl in IFs produces alcohols, which undergo dehydration to alkenes on the acid site and then a fast C
C hydrogenation will happen.37,38 Meanwhile, the furan ring in the IFs can be effectively hydrolyzed and deoxygenated in the presence of acid.39 Therefore this process requires a catalyst with both deoxygenation and hydrogenation functions.
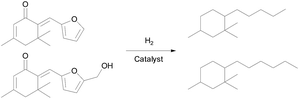 |
| Scheme 2 Hydrodeoxygenation of the mono-condensed product. | |
A series of catalysts were prepared and tested in the HDO of IFs, as shown in Table 2. First, a physical mixture of commercial Pd/C and HZSM-5 was tested, unfortunately the yield is very low because most of the products are incomplete HDO compounds. This indicates that the synergy of deoxygenation and hydrogenation is not strong enough. To enhance the synergy we loaded Pd on HZSM-5 and obtained an obviously higher HDO yield. This can be rationalized because the loading provides more intimate proximity between the metal and the acid sites, which will greatly increase the possibility of dehydration on acid sites followed by hydrogenation on metal sites.40
Table 2 Results for hydrodeoxygenation of the isophorone/furfural aldol condensation producta
Catalyst |
Yield of C14 (%) |
Reaction conditions: 1 g condensed product, 200 °C, 12 h, 50 mL H2O, 6 MPa H2.
The reaction was conducted for 40 h.
|
Pd/C(0.5 g) + HZSM-5 (5 g) |
12.3 |
0.5 wt% Pd/HZSM-5 (5 g) |
44.9 |
0.5 wt% Pt/HZSM-5 (5 g) |
68.1 |
1 wt% Pt/HZSM-5 (5 g) |
77.9 |
2 wt% Pt/HZSM-5 (5 g) |
82.7 |
2 wt% Pt/HZSM-5 (1 g) |
45.8 |
2 wt% Pt/HZSM-5 (1 g)b |
71.0 |
5 wt% Pt/HZSM-5 (5 g) |
79.4 |
5 wt% Pt/Hβ (5 g) |
74.4 |
To further promote the HDO reaction we prepared Pt/HZSM-5 because it is reported that Pt is more active than Pd in the hydrogenation of α,β-unsaturated aldehydes.41 It can be seen that the yield increases from 44.9% for 0.5 wt% Pd/HZSM-5 to 68.1% for 0.5 wt% Pt/HZSM-5. In addition, both HZSM-5 and Hβ zeolite supports perform well in the HDO. Among the prepared catalysts, 2 wt% Pt/HZSM-5 shows the highest yield (82.7%) in the HDO of the isophorone/furfural aldol condensation product, and a further increase in the loading of metal (5 wt%) does not promote the HDO performance, probably due to the formation of larger Pt particles. Moreover, a lower amount of HDO catalyst shows acceptable activity (45.8% yield of C14), and a better result can be obtained with prolonged time (40 h, 71.0% yield of C14). Finally 2 wt% Pt/HZSM-5 was chosen as the catalyst in the subsequent HDO of the isophorone/5-HMF condensed product, resulting in 85.4% yield of C14 + C15.
3.4 Properties of the obtained biofuels
After hydrodeoxygenation and vacuum distillation, the isophorone/furfural-derived biofuel (C14) contains 1,1,5-trimethyl-2-pentyl-cyclohexane and its isomers (95.4%), 1,1,5-trimethyl-2-butyl-cyclohexane (1.5%), and 1,1,5-trimethyl-2,4-dipentyl-cyclohexane (1.3%), and the isophorone/5-HMF-derived biofuel (C15) contains 1,1,5-trimethyl-2-hexyl-cyclohexane and isomers (64.2%), 1,1,5-trimethyl-2-pentyl-cyclohexane and its isomers (29.1%), and 1,1,5-trimethyl-2-butyl-cyclohexane (3.6%). The properties of the obtained hydrocarbons were assessed using ASTM methods, as shown in Table 3. Notably, the density of these hydrocarbons (0.813 g mL−1 for C14 and 0.846 g mL−1 for C15) is higher than that of pentylcyclohexane (0.804 g mL−1). This result indicates the presence of methyl groups and/or longer chain groups can increase the density. Moreover, the C14 and C15 biofuels have a very low freezing point (<−75 °C), although their viscosity increases to some degree. Overall they show very good low-temperature properties. Therefore the hydrocarbons synthesized here show good potential as high-density biofuels or fuel additives.
Table 3 Properties of hydrocarbons synthesized using isophorone and furanic aldehydes
Molecular structure |
|
|
|
Feedstock |
Furfural and isophorone |
5-HMF and isophorone |
Aromatic oxygenates and furfural alcohol |
Density at 20 °C (g mL−1) |
0.813 |
0.846 |
0.804 |
Freezing point (°C) |
<−75 |
<−75 |
<−80 |
Kinematic viscosity (mm2 s−1) |
3.4 (25 °C) |
5.3 (25 °C) |
2.0 (25 °C) |
26.1 (−30 °C) |
68.7 (−30 °C) |
7.5 (−30 °C) |
Heating value (MJ kg−1) |
43.0 |
42.9 |
43.3 |
Ref. |
This work |
This work |
16
|
4. Conclusions
We have developed a facile way to synthesize multi-substituted cyclohexanes via aldol condensation of isophorone and furanic aldehydes, followed by hydrodeoxygenation. NaOH shows excellent performance in the aldol condensation with the conversion of 76.5%/99.6% for isophorone/furfural and 68.6%/100% for isophorone/5-HMF under optimized conditions. The yield of the mono-condensed product reaches 70.0% and 72.8% for isophorone/furfural and isophorone/5-HMF, and is determined by the basicity of the catalyst and almost unchanged with the molar ratio of the feedstock or reaction temperature. After hydrodeoxygenation, the obtained hydrocarbons derived from isophorone/furfural and isophorone/5-HMF have a density of 0.813 g mL−1 and 0.846 g mL−1 (20 °C) and a freezing point less than −75 °C, and have good potential as high-density biofuels or additives of other biofuels.
Conflicts of interest
There are no conflicts to declare.
Acknowledgements
This work was supported by the National Natural Science Foundation of China (U1462119 and 21476168) and the Tianjin Municipal Natural Science Foundation (16JCQNJC05200).
References
- M. G. Sibi, B. Singh, R. Kumar, C. Pendem and A. K. Sinha, Green Chem., 2012, 14, 976–983 RSC.
- X. Zhang, L. Pan, L. Wang and J.-J. Zou, Chem. Eng. Sci., 2018, 180, 95–125 CrossRef.
- H. S. Chung, C. S. H. Chen, R. A. Kremer, J. R. Boulton and G. W. Burdette, Energy Fuels, 1999, 13, 641–649 CrossRef.
- G. W. Huber, S. Iborra and A. Corma, Chem. Rev., 2006, 106, 4044–4098 CrossRef PubMed.
- A. Corma, S. Iborra and A. Velty, Chem. Rev., 2007, 107, 2411–2502 CrossRef PubMed.
- J. Q. Bond, D. M. Alonso, D. Wang, R. M. West and J. A. Dumesic, Science, 2010, 327, 1110–1114 CrossRef PubMed.
- R. Xing, A. V. Subrahmanyam, H. Olcay, W. Qi, G. P. van Walsum, H. Pendse and G. W. Huber, Green Chem., 2010, 12, 1933–1946 RSC.
- J. Yang, N. Li, S. Li, W. Wang, L. Li, A. Wang, X. Wang, Y. Cong and T. Zhang, Green Chem., 2014, 16, 4879–4884 RSC.
- A. Corma, O. de la Torre, M. Renz and N. Villandier, Angew. Chem., Int. Ed., 2011, 50, 2375–2378 CrossRef PubMed.
- A. Corma, O. de la Torre and M. Renz, Energy Environ. Sci., 2012, 5, 6328–6344 RSC.
- J. Yang, N. Li, G. Li, W. Wang, A. Wang, X. Wang, Y. Cong and T. Zhang, ChemSusChem, 2013, 6, 1149–1152 CrossRef PubMed.
- B. Pholjaroen, N. Li, J. Yang, G. Li, W. Wang, A. Wang, Y. Cong, X. Wang and T. Zhang, Ind. Eng. Chem. Res., 2014, 53, 13618–13625 CrossRef.
- B. G. Harvey and R. L. Quintana, Energy Environ. Sci., 2010, 3, 352–357 RSC.
- S. Li, N. Li, W. Wang, L. Li, A. Wang, X. Wang and T. Zhang, Sci. Rep., 2016, 6, 32379 CrossRef PubMed.
- G. Nie, X. Zhang, P. Han, J. Xie, L. Pan, L. Wang and J.-J. Zou, Chem. Eng. Sci., 2017, 158, 64–69 CrossRef.
- P. Han, G. Nie, J. Xie, X.-T.-F. E, L. Pan, X. Zhang and J.-J. Zou, Fuel Process. Technol., 2017, 163, 45–50 CrossRef.
- Q. Deng, P. Han, J. Xu, J.-J. Zou, L. Wang and X. Zhang, Chem. Eng. Sci., 2015, 138, 239–243 CrossRef.
- J. Yang, N. Li, G. Li, W. Wang, A. Wang, X. Wang, Y. Cong and T. Zhang, Chem. Commun., 2014, 50, 2572–2574 RSC.
- Q. Deng, G. Nie, L. Pan, J.-J. Zou, X. Zhang and L. Wang, Green Chem., 2015, 17, 4473–4481 RSC.
- Q. Deng, J. Xu, P. Han, L. Pan, L. Wang, X. Zhang and J.-J. Zou, Fuel Process. Technol., 2016, 148, 361–366 CrossRef.
- W. Wang, N. Li, G. Li, S. Li, W. Wang, A. Wang, Y. Cong, X. Wang and T. Zhang, ACS Sustainable Chem. Eng., 2017, 5, 1812–1817 CrossRef.
- X. Sheng, N. Li, G. Li, W. Wang, J. Yang, Y. Cong, A. Wang, X. Wang and T. Zhang, Sci. Rep., 2015, 5, 9565 CrossRef PubMed.
- F. Chen, N. Li, S. Li, G. Li, A. Wang, Y. Cong, X. Wang and T. Zhang, Green Chem., 2016, 18, 5751–5755 RSC.
- Y. Wang, Y. Jing, Q. Xia and X. Liu, ChemSusChem, 2017, 10, 4817–4823 CrossRef PubMed.
- J.-J. Zou, N. Chang, X. Zhang and L. Wang, ChemCatChem, 2012, 4, 1289–1297 CrossRef.
- G. Nie, J.-J. Zou, R. Feng, X. Zhang and L. Wang, Catal. Today, 2014, 234, 271–277 CrossRef.
- F. Chen, N. Li, X. Yang, L. Li, G. Li, S. Li, W. Wang, Y. Hu, A. Wang and Y. Cong, ACS Sustainable Chem. Eng., 2016, 4, 6160–6166 CrossRef.
- Y. Jing, Q. Xia, J. Xie, X. Liu, Y. Guo, J.-J. Zou and Y. Wang, ACS Catal., 2018, 8, 3280–3285 CrossRef.
- J. Xie, X. Zhang, L. Pan, G. Nie, X.-T.-F. E, Q. Liu, P. Wang, Y. Li and J. J. Zou, Chem. Commun., 2017, 53, 10303–10305 RSC.
- G. Nie, X. Zhang, L. Pan, P. Han, J. Xie, Z. Li, J. Xie and J.-J. Zou, Chem. Eng. Sci., 2017, 173, 91–97 CrossRef.
- C. P. Kelkar and A. A. Schutz, Appl. Clay Sci., 1998, 13, 417–432 CrossRef.
- M. Hronec, K. Fulajtárova, T. Liptaj, M. Štolcová, N. Prónayová and T. Soták, Biomass Bioenergy, 2014, 63, 291–299 CrossRef.
- I. Sádaba, M. Ojeda, R. Mariscal, J. L. G. Fierro and M. L. Granados, Appl. Catal., B, 2011, 101, 638–648 CrossRef.
- S. Subbiah, S. P. Simeonov, J. M. S. S. Esperança, L. P. N. Rebelo and C. A. M. Afonso, Green Chem., 2013, 15, 2849–2853 RSC.
- W. Wang, Y. Liu, N. Li, G. Li, W. Wang, A. Wang, X. Wang and T. Zhang, Sci. Rep., 2017, 7, 6111 CrossRef PubMed.
-
S. Krill, S. Kretz, H.-j. Hasselbach, K. Huthmacher, R. Hahn and H. Schmitt, US pat. 6265617, 2001.
- C. Zhao, Y. Kou, A. A. Lemonidou, X. Li and J. A. Lercher, Angew. Chem., Int. Ed., 2009, 48, 3987–3990 CrossRef PubMed.
- F. Anaya, L. Zhang, Q. Tan and D. E. Resasco, J. Catal., 2015, 328, 173–185 CrossRef.
- M. J. Climent, A. Corma and S. Iborra, Green Chem., 2014, 16, 516–547 RSC.
- C. Zhao, D. M. Camaioni and J. A. Lercher, J. Catal., 2012, 288, 92–103 CrossRef.
- P. Gallezot and D. Richard, Catal. Rev., 1998, 40, 81–126 CrossRef.
Footnote |
† Electronic supplementary information (ESI) available. See DOI: 10.1039/c8se00197a |
|
This journal is © The Royal Society of Chemistry 2018 |
Click here to see how this site uses Cookies. View our privacy policy here.