DOI:
10.1039/C8RA08624A
(Paper)
RSC Adv., 2018,
8, 41131-41142
Preparation of hierarchical HZSM-5 zeolites with combined desilication with NaAlO2/tetrapropylammonium hydroxide and acid modification for converting methanol to propylene
Received
17th October 2018
, Accepted 27th November 2018
First published on 7th December 2018
Abstract
In the present work, mesoporosity is introduced into highly siliceous HZSM-5 zeolites (SiO2/Al2O3 = 400) by a two-step path including desilication using NaAlO2 and TPAOH (tetrapropylammonium hydroxide) mixtures, followed by acid washing treatment. The physicochemical properties of conventional microporous HZSM-5 and all treated samples were characterized by ICP-OES, XRD, FE-SEM, BET and NH3-TPD methods. The catalytic performance of the HZSM-5 samples was determined in methanol to propylene conversion reaction at 460 °C and methanol WHSV of 0.9 h−1 using feed containing 50 wt% methanol in water. The results showed that the porosity of the desilicated samples has been mainly blocked by sodium aluminate derived deposits and silicon-containing debris. After a subsequent acid washing step with hydrochloric acid, the blocking species were removed which resulted in improving the mesoporosity generated in the desilication step. It was found that alkaline-acid treatment in a NaAlO2/TPAOH solution with TPAOH/(NaAlO2 + TPAOH) = 0.4 followed by acid washing, leads to the formation of narrow and uniform mesoporosity without severely destroying the crystal structure. Also, it exhibits higher selectivities to propylene (37.7 vs. 30.7%) and total butylenes (21.2 vs. 16.1%), propylene to ethylene ratio (4.0 vs. 2.7), as well as total light olefins (68.4 vs. 57.9%) compared to the parent catalyst, while its selectivities to C1–C4 alkanes (9.6 vs. 13.7%) and heavy hydrocarbons (13.8 vs. 28.4%) are relatively lower. The lifetime of the optimum alkaline-acid treated sample (640 h) showed a significant increase compared to that of the parent catalyst (425 h). The results exhibited that desilication process leads to a considerable mesoporosity development, while acid washing treatment mostly influences on the catalyst acidity. Therefore, the combination of the alkaline-acid treatment leads to hierarchical HZSM-5 catalyst formation with tailored pore architecture and surface acidic properties.
1. Introduction
Propylene is one of the key components for the production of propylene oxide, polypropylene, acrylic acid, acrylonitrile, and isopropyl alcohol in the petrochemical industry.1 It is mainly produced as a byproduct of steam cracking of hydrocarbons and fluid catalytic cracking units which have high energy consumption and lead to greenhouse gas emission.2 Increasing oil prices, shortage of petroleum resources, and consumption demands for propylene, lead to considerable attention toward new processes with high propylene to ethylene ratios.3 The methanol to propylene (MTP) process based on acidic catalysts is a promising way to produce light olefins with high propylene yield, since methanol can be easily synthesized by steam reforming of natural gas or coal gasification.4,5
Chang and Silvestri6 proposed a reaction path for methanol conversion to hydrocarbons reaction over ZSM-5 catalyst as follows:
|
 | (1) |
At first, methanol dehydrates to dimethyl ether (DME), which reacts further to produce ethylene and propylene. Dimethyl ether formation is directly related to weak acid sites and strong acid sites which are favor for secondary reactions as well as MTO reaction. Butanes, higher olefins, alkanes, C5+ heavy hydrocarbons, and aromatics are usually produced as by-products in the MTO process. It is well established that the products distributions in the MTO process strongly depend on the catalyst properties and operating conditions.7,8
ZSM-5 is a common catalyst for converting methanol to propylene due to high resistance against coke deposition, high acidic activity, and excellent shape selectivity. However, the relatively small micropores of this catalyst considerably lead to mass transfer limitation.9,10 Therefore, ZSM-5 modification with good performance in MTP reaction still remains a great challenge in the catalyst science.
Introducing an additional mesopore network besides the intrinsic micropore system, which referred to hierarchical ZSM-5, can be a promising method to overcome fast deactivation and develop a catalyst with high stability for the MTP reaction. This leads to decrease in inner diffusion paths, increase in catalyst external surface area, increase in accessibility and mass transfer of molecules to/from the active sites.11,12
A wide variety of strategies have been developed to generate the hierarchical porous ZSM-5, such as direct synthesis in the presence of various hard or soft templates and post treatment approaches such as desilication and dealumination, which are presented in the reviews of Serrano et al.13, Möller and Bein,14 and Čejka and Mintova.15
Among all the approaches, desilication of ZSM-5 in an alkaline medium (typically NaOH), seems to be a promising route due to its simplicity operations, versatility, and efficiency. According to the literatures,16,17 the mesoporosity formation by NaOH operates in the optimum ratio of Si/Al of 25–50 and majority of studies have been done in this ratio, while desilication studies of highly siliceous ZSM-5 have been less frequent.
Sadowska et al.,18,19 investigated the influence of alkaline treatments with NaOH and NaOH/TBAOH mixtures on the physicochemical properties and catalytic performance of two different ratio of ZSM-5 (Si/Al = 164 and 31.5) zeolite in cracking reaction. The results showed that the mixture of NaOH and TBAOH as an alkaline agent, leads to form mesoporous ZSM-5 with smaller diameter and narrower pore size distribution with higher accessibility to active sites of catalyst respect to the case of using NaOH alone. Ahmadpour and Taghizadeh10 studied the MTP reaction over desilicated ZSM-5 (Si/Al = 175) samples by different ratio of NaOH/TPAOH mixtures. They found that NaOH/TPAOH solution with 0.4 ratio of TPAOH in the mixture shows higher propylene selectivity (%47.2) and longer catalyst life time (80 h) compared to the parent one (%35.7 propylene selectivity and 43 h life time). Fathi et al.20 desilicated ZSM-5 (Si/Al = 15) zeolite by alkaline treatment (CaCO3, Na2CO3 and NaOH solution) at 75 °C for 3 h and catalytically tested for the methanol to gasoline reaction. The results showed that desilicated sample by NaOH produced mesoporous structure more than other desilicated samples. They also showed that the alkaline treated sample by Na2CO3 solution provided the highest C5+ selectivity (43%) and the longest catalytic lifetime (4 h). Caicedo-Realpe and Pérez-Ramírez21 prepared mesopore ZSM-5 zeolites (Si/Al = 15, 25, and 40) by desilication and subsequent acid washing treatment. They studied the effect of different conditions of desilication and acid washing parameters with respect to concentration, temperature, and time on the mesoporosity formation. The results showed that after desilication, the external surface area of the hierarchical increased 3 to 4 times higher than in the parent one, while crystallinity and acidity of the desilicated samples were largely preserved. The results showed that acid washing treatment after desilication process removed the blocking species and regained the native microporosity. Groen et al.22 investigated mesoporosity development and acidity adjustment by sequential desilication–dealumination of ZSM-5 zeolites (Si/Al = 15, 35 and 200). Desilication and dealumination were done by 0.2 M NaOH solution at 65 °C for 30 min and steam treatment at 600 °C for 5 h, respectively. They showed that appropriate modification of structure and acidity can be obtained using alkaline treatment followed by steaming. Ding et al.23 introduced mesoporosity in highly siliceous ZSM-5 zeolite (SiO2/Al2O3 = 417) by alkaline treatment using mixtures of NaOH and TEAOH (tetraethylammonium hydroxide). A subsequent phosphorus modification was carried out to stabilize the acidity properties and porosity of the desilicated samples. The catalytic performance of the phosphorus modified mesoporous ZSM-5 catalysts in catalytic hydrocarbons cracking reaction showed higher conversion in the bulky molecule cracking reaction compared to the parent one.
To the best of our knowledge, the catalytic performance of a highly siliceous mesoporous HZSM-5 catalyst prepared by desilication with different ratios of NaAlO2/TPAOH mixtures in MTP reaction have not been previously investigated. This work focuses on using different alkaline solutions of NaAlO2/TPAOH mixtures in mesoporosity formation over HZSM-5 zeolite. A conventional microporous HZSM-5 catalyst was used to compare the effect of mesoporosity in the MTP reaction using a fixed-bed flow reactor under the same operating conditions. Also, the physicochemical properties of these catalysts were characterized by ICP-OES, XRD, FE-SEM, BET and NH3-TPD methods.
2. Experimental
2.1 Materials
All the chemical reagents were the analytical grade and used without further purification. Silicic acid (SiO2·xH2O, ≥99 wt%), ammonium nitrate (NH4NO3, 99 wt%), sulfuric acid (H2SO4, 98 wt%), sodium hydroxide (NaOH, 99.6 wt%), hydrochloric acid (HCl, 37 wt%), and tetrapropylammonium hydroxide (TPAOH, 40 wt% aqueous solution) were purchased from Merck Company (Germany) while sodium aluminate (NaAlO2, Al2O3 wt% = 55) was purchased from Riedel de Haen (Germany).
2.2 Catalysts synthesis
2.2.1 Parent zeolite synthesis. High silica H-ZSM-5 catalyst (nominal Si/Al ratio of 200) was synthesized by the hydrothermal method using silicic acid and sodium aluminate as Si and Al sources, respectively. The gel composition of 20SiO2
:
0.05Al2O3
:
1TPAOH
:
1.5Na2O
:
200H2O was used for the reaction mixture. The synthesis procedure to prepare the gel is as bellow. At first sodium aluminate was added to NaOH aqueous solution and mixed for 30 min. Then TPAOH was drop-wise added to the mixture for 30 min (solution A). Simultaneously, silicic acid added slowly to NaOH aqueous solution and mixed for 30 min (solution B). Solution A was added dropwise to solution B during 120 min under vigorous stirring and then concentrated H2SO4 was added to the mixture to adjust gel pH. The crystallization was carried out at 187 °C under autogenously pressure for 48 h without stirring in stainless-steel Teflon-lined autoclave. The solid product was recovered by filtration and then was washed with deionized water several times until the pH value of the decanted water reached to neutral. After that, it was dried overnight at 105 °C. Finally, the catalyst sample was calcined to remove the organic template in a muffle furnace under air flow at 530 °C for 12 h at a heating rate of 3 °C min−1. Ion exchange of as-synthesized Na-ZSM-5 sample was carried out four times with 1.0 M NH4NO3 solution for 10 h at 90 °C under continuous agitation. The sample was then washed and dried at 105 °C for 12 h, followed by calcination at 530 °C for 12 h (at heating rate of 3 °C min−1) to obtain the H-form of the zeolite. The resulting powder was formed by tableting and then catalyst with a mesh size in the range of 16–25 was made by crushing and sieving for catalytic evaluation in the reactor. This sample was denoted as parent.
2.2.2 Alkaline treatment. Desilication treatments on the parent catalyst were carried out in the alkaline solution of NaAlO2, and NaAlO2/TPAOH mixture in different ratios. The alkaline samples were named as DeSi-NaAlO2-TPA-R which R is the molar ratio of the TPAOH/(NaAlO2 + TPAOH) which varied from 0 to 0.6. The concentration of each solution was 0.2 M. 300 ml of the alkaline solution were heated to 65 °C in the flax under reflux, after then, 30 g of the parent catalyst were added to the heated solution and stirred vigorously for 30 min. Then, the suspension was cooled down immediately in ice bath. After that, it was filtered, and then washed with deionized water until neutral pH. The filtrated cake was dried at 105 °C for 12 h and converted into the H-form following the procedure described for the parent catalyst.
2.2.3 Acid treatment. After alkaline treatment, acid washing step was used to remove silicate debris and alkali ions which deposited on the zeolite pores and to modify the porosity of desilicated samples in the presence of NaAlO2. Acid washing treatment as an extraction step was performed by contacting the HZSM-5 desilicated samples with an aqueous solution of hydrochloric acid (3.0 M) at 80 °C for 3 h with ratio of 10 cm3 HCl solution/1 g of desilicated sample. Afterwards, the suspension washed several times with deionized water, dried at 105 °C for 12 h, followed by calcination at 530 °C for 12 h with heating rate of 3 °C min−1. After acid washing, the samples were denoted as DeSi-NaAlO2-TPA-R-AW which R is the molar ratio of the TPAOH/(NaAlO2 + TPAOH) varying from 0 to 0.6 and AW refer to acid washing step.
2.3 Catalyst characterization techniques
The molar ratio of Si/Al in the parent and all alkaline treated samples before and after acid washing step were determined by the ICP OES method using a Perkin Elmer Optima 2000 DV spectrometer. Powder X-ray diffraction (XRD) analysis was used to recognize the type of crystalline phase and crystallinity of samples. Patterns were recorded on a Philips PW1730 diffractometer (Philips Analytical, Almelo, The Netherlands) using Cu Kα radiation (λ = 1.5406 Å ) over a 2θ range of 5° to 50° with a step size of 0.05° and a step time of 1 s at room temperature. The crystal size and morphology of HZSM-5 catalysts were determined by field-emission scanning electron microscopy (FE-SEM) on MIRA3 TESCAN, USA instrument, operating at 15 kV. The textural properties of all samples including the specific surface areas and pore diameters were determined using N2 adsorption–desorption isotherms at 77 K on NOVA2000 QuantaChrome, USA instrument. Before measuring, the samples were evacuated at 300 °C under N2 flow for 3 h. The Brunauer–Emmett–Teller (BET) equation was used to calculate the specific surface area using adsorption data at p/p0 = 0.05–0.25. Micropore volume and micropore surface area were determined by t-plot curve at thickness range between 3.5 and 5.4 Å. The pore size distribution was obtained from adsorption isotherm using Barrett–Joyner–Halenda (BJH) method. Mesopore volume was calculated by using difference between the total pore volume (p/p0 = 0.99) and micropore volume. The surface acidity of the catalysts was determined by temperature-programmed desorption of ammonia (NH3-TPD) with an online thermal conductivity detector (TCD) using a conventional flow apparatus (BELCAT-A, BEL Japan, Inc.). 35 mg of the sample was preheated under helium flow at 300 °C for 2 h with a heating rate of 10 °C min−1. After cooling to 60 °C, the sample was saturated with NH3 in the micro reactor for 1 h. To remove the physically adsorbed NH3 on the catalyst surface; helium was passed over the sample for 30 min. The temperature ranges of ammonia desorption was 35 to 850 °C.
2.4 Catalytic performance tests
The performance of the samples for conversion of methanol to propylene (MTP) reaction was investigated in a fixed-bed continuous flow reactor (L = 60 cm, I.D. = 11 mm, S.S. 316) at 460 °C under atmospheric pressure. The reactor was heated by a temperature-controlled three-zone furnace and a K-type thermocouple probe was placed coaxially in the center of the catalyst bed to measure and monitor the reaction temperature. A schematic flow diagram of the lab scale set-up has been shown in Fig. 1. In each run, 4 g of the catalyst was loaded in the center section of the reactor and a liquid mixture containing 50 wt% methanol in water with methanol WHSV of 0.9 h−1 was injected to catalyst bed with a WellChrom K-120 HPLC pump. Prior to the MTP reaction, the sample was activated at 300 °C for 2 h under N2 flow with a heating rate of 3 °C min−1. Then, the N2 gas flow was stopped and the mixture of methanol and water was pumped from the feed tank to the preheater. The reactor outlet stream was cooled to 6 °C in a refrigerating bath and then the gas and liquid products were separated. In order to prevent heavy components condensation, the transfer line from the reactor outlet to the refrigerating bath was externally heated and maintained at 170 °C. On-line analysis of the gas phase was carried out using a micro-GC (Varian CP-4900) equipped with a TCD detector. Four channels of this instrument were used to separate the products [(CH4, C2–C5 olefin/paraffins, DME, C6-cut) and (H2, CO and CO2)]. The separated aqueous parts of the liquid products were analyzed using Varian CP-3800 gas chromatograph equipped with FID and TCD detectors in which a CP-Wax 52 CB column was used to separate the components (methanol and water). The organic part was also analyzed using Varian CP-3800 gas chromatograph equipped with a FID detector in which a PONA column was used to separate the components (C6–C16 hydrocarbons).
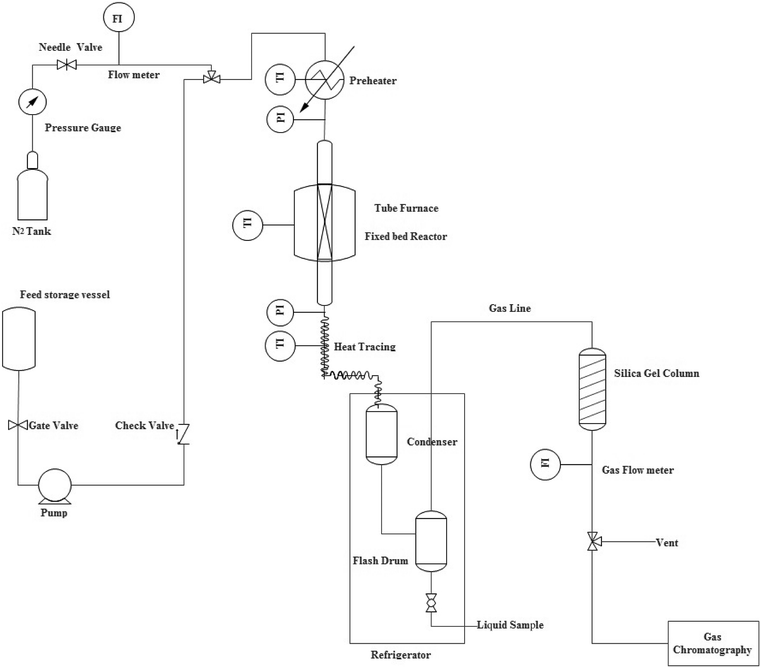 |
| Fig. 1 Schematic flow diagram of the experimental setup for the catalytic activity tests. | |
The methanol conversion and selectivity of products were evaluated using eqn (1) and (2), respectively.
|
 | (2) |
|
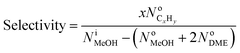 | (3) |
where
N is the number of moles. Superscripts i, o, and x represent components at the inlet of reactor, components at the outlet of reactor, and the number of carbon atoms, respectively.
3. Results and discussion
3.1 Catalysts characterization
3.1.1 Chemical composition. The amount of Si/Al molar ratio for the parent and all the alkaline treated samples before and after acid washing step, have been listed in Table 1. According to the literature,10,16 alkaline treatment over ZSM-5, results in both silicon and aluminum dissolution from the zeolite framework. However, due to easier hydrolysis of Si–OH–Si than Si–OH–Al bond in the presence of Al(OH)4− attack, the dissolution of silicon is more favorable than aluminum from the zeolite framework in alkaline treatment.24,25 As listed in Table 1, more reduction in Si/Al molar ratio is observed for the alkaline treated sample with pure NaAlO2 compared to the desilicated samples in the presence of TPAOH. At low Si/Al ratios, aluminum acts as a pore directing agent and prevents the framework from base attack, while in highly siliceous ZSM-5 (nominal Si/Al ratio of 200), because of low concentration of aluminum on the zeolite framework, uncontrolled excessive silicon extraction occurred, which resulted in massive zeolite dissolution. Less reduction in Si/Al ratio for the alkaline treated samples in the presence of TPAOH is related to its high adsorption affinity towards the zeolite surface, which protects zeolite against dissolution.26,27 However, the molar ratio of Si/Al for all the alkaline treated samples is very low compared to the parent one, which is related to the Al2O3 deposits present in the sodium aluminate treated samples.21 It can be seen from Table 1 that after acid washing step with concentrated hydrochloric acid, the Si/Al molar ratio of all the alkaline-acid treated catalysts is very close to that of the parent one. These results confirmed that a preferential elimination of alumina deposits and siliceous species occurred during the acid washing step.
Table 1 Chemical composition and textural properties of the parent, all desilicated HZSM-5 samples before and after acid washing
Sample |
Si/Ala |
SBETb (m2 g−1) |
SMicroc (m2 g−1) |
SExtd (m2 g−1) |
VTotale (cm3 g−1) |
VMicrof (cm3 g−1) |
VMesog (cm3 g−1) |
HFh |
Determined by inductively coupled plasma-optical emission spectroscopy (ICP-OES). Total surface areas were obtained by the BET method using adsorption data in P/P0 ranging from 0.05 to 0.25. Measured by t-plot method using adsorption data in P/P0 ranging from 0.19 to 0.39. External surface area, measured by t-plot method using adsorption data in P/P0 ranging from 0.19 to 0.39. Total pore volumes were estimated from the adsorbed amount at P/P0 = 0.99. Measured by t-plot method using adsorption data in P/P0 ranging from 0.19 to 0.39. VMeso = Vads,p/p0=0.99 − VMicro. The hierarchical factor, defined as (VMicro/VTotal) × (SExt/SBET). |
Parent |
183 |
398.8 |
368.7 |
30.1 |
0.202 |
0.137 |
0.065 |
0.051 |
DeSi-NaAlO2 |
44 |
350.9 |
280.3 |
70.6 |
0.174 |
0.117 |
0.057 |
0.135 |
DeSi-NaAlO2-TPA0.2 |
72 |
351.8 |
229.3 |
119.4 |
0.186 |
0.119 |
0.067 |
0.217 |
DeSi-NaAlO2-TPA0.4 |
84 |
360.7 |
238.2 |
122.5 |
0.198 |
0.124 |
0.074 |
0.212 |
DeSi-NaAlO2-TPA0.6 |
58 |
339.1 |
255.1 |
84 |
0.191 |
0.121 |
0.07 |
0.157 |
DeSi-NaAlO2-AW |
155 |
367.7 |
244.8 |
122.9 |
0.225 |
0.121 |
0.104 |
0.180 |
DeSi-NaAlO2-TPA0.2-AW |
176 |
375.1 |
231.9 |
143.2 |
0.231 |
0.124 |
0.107 |
0.205 |
DeSi-NaAlO2-TPA0.4-AW |
162 |
383.1 |
214.5 |
168.6 |
0.235 |
0.127 |
0.108 |
0.238 |
DeSi-NaAlO2-TPA0.6-AW |
170 |
357 |
221.4 |
135.6 |
0.228 |
0.121 |
0.107 |
0.201 |
3.1.2 XRD analysis. Fig. 2 shows XRD patterns of the parent zeolite and all desilicated samples prepared with mixture of NaAlO2/TPAOH at different ratios after acid washing step. The comparison between the XRD patterns of the alkaline-acid treated samples with those of the parent zeolite showed two main peaks at 2θ = 7–10° and three peaks at 2θ = 23–25°, which can be attributed to the preservation of the MFI lattice structure during alkaline-acid treatment without any additional phases formation. A slight decrease in the peak intensity related to the desilicated samples is associated with partial extraction of Si and Al from zeolite framework during alkaline-acid treatment. This event confirmed that the hierarchical samples crystallinity has not destroyed.
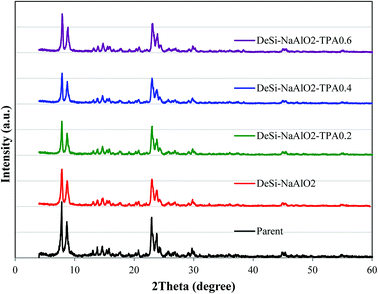 |
| Fig. 2 The XRD patterns of the parent and all desilicated HZSM-5 samples after acid washing. | |
3.1.3 Nitrogen adsorption/desorption analysis. Nitrogen adsorption–desorption isotherms and corresponding BJH pore size distribution curves of the parent and all the hierarchical HZSM-5 samples prepared by two-step path of alkaline-acid treatment with different ratios of the NaAlO2/TPAOH mixtures have been shown in Fig. 3a and b, respectively. The nitrogen isotherm of the parent catalyst shows isotherm type I without any recognizable hysteresis loop and with a high uptake at relative pressures (p/p0 < 0.2), confirming its microporous structure without considerable mesoporosity.24,28 This result was verified by the BJH curve of the sample (Fig. 3b) which does not indicate any clear peak at mesoporous range (2–50 nm). Moreover, as presented in Table 1, the parent catalyst has relatively low contribution of mesoporosity (SExt of 30.1 m2 g−1 and VMeso of 0.065 cm3 g−1) compared to its total BET surface area (398.8 m2 g−1) and total pore volume (0.202 cm3 g−1). As can be seen in Fig. 3a, all the alkaline-acid treatment HZSM-5 samples exhibit both types I and VI behavior with a pronounced type H3 hysteresis at high relative pressures (P/P0 > 0.4). This event indicates a porous system coupling micro and mesoporosity, confirming by the t-plot results listed in Table 1. The alkaline-acid treated HZSM-5 samples verify the generation of the narrow and uniform mesopore size distribution centered at ca. 3 nm (Fig. 3b). While pore size distribution curves of the sample desilicated by pure NaAlO2 show a narrow peak at 3 nm and a broad peak at around 9 nm. On the other words, the affinity of TPA+ cations to the catalyst surface, as a pore growth moderator, can avoid the formation of large pores and excessive silicon extraction from the zeolite framework during desilication process.29,30 As can be seen, there is no considerable difference in BJH pore size distributions for the samples treated with NaAlO2/TPAOH mixtures at different ratios of both bases. As listed in Table 1, for all desilicated samples, the total BET surface areas have been decreased compared to the parent catalyst. This reduction for the alkaline treated sample with pure NaAlO2 is much higher than other desilicated samples. These results are related to the catalyst framework destruction due to silicon extraction during desilication process.
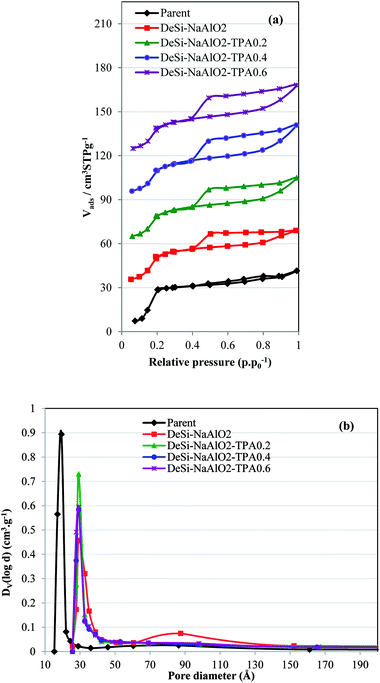 |
| Fig. 3 (a) N2 adsorption/desorption isotherms of the parent, all desilicated HZSM-5 samples after acid washing (b) BJH pore size distributions derived from the adsorption branch of the isotherms of the samples. | |
Moreover, because of pore blockage caused by NaAlO2-derived deposits, the total pore volume and micropore volume of the all desilicated samples are decreased.21 While the micropore volume decreased, the external surface area for all treated samples increased. As presented in Table 1, after acid washing step and removing silicate debris and sodium aluminate deposits, a considerable increase of total surface area and total pore volume observed for the all samples. The significant increase in external surface area (more than 4 times) and mesopore volume with a slight drop in micropore volume (∼max. 10%) observed for all the desilicated samples in the presence of TPAOH, compared to the parent one. While for the desilicated sample by pure NaAlO2, the external surface area enhance twice in comparison by the parent catalyst. Among these samples with different ratios, DeSi-NaAlO2-TPA0.4-AW (ratio = 0.4) illustrated the largest mesopore surface area (168.6 m2 g−1), and the lowest micropore volume reduction (0.127 cm3 g−1). It can be concluded that the alkaline treatment by different rations of NaAlO2/TPAOH solution is absolutely responsible for the mesoporosity formation in the parent zeolite, while the acid washing treatment step removes the pore blocking deposits which had been accumulated in the catalyst pores in the first step treatment.
3.1.4 FE-SEM analysis. Fig. 4 shows the surface morphology before and after acid washing step for the parent and all the desilicated samples. As shown in Fig. 4a, a relatively spherical aggregate shaped morphology observes for the parent catalyst. The crystal size of the sample is large with quite clear and smooth surface which confirms low presence of mesopores in the structure. As can be clearly seen in the FE-SEM micrographs of the alkaline treated sample with pure NaAlO2 (Fig. 4b) and the treated sample with NaAlO2/TPAOH solution with TPAOH/(NaAlO2 + TPAOH) = 0.4 (Fig. 4d), the pore porosity of the samples has been mainly blocked by sodium aluminate-derived deposits and silicon-containing debris. In addition, after desilication process, the external surface area of the parent catalyst becomes rough and rugged. Even though, as can be seen in Fig. 4c and e, after acid washing step with hydrochloric acid, the blocking species were removed which result in improving the intracrystalline mesoporosity generated in the desilication step. These results are confirmed by the t-plot results listed in Table 1. Similar observations have been obtained by other researchers on mesoporous zeolites after dealumination.22,31
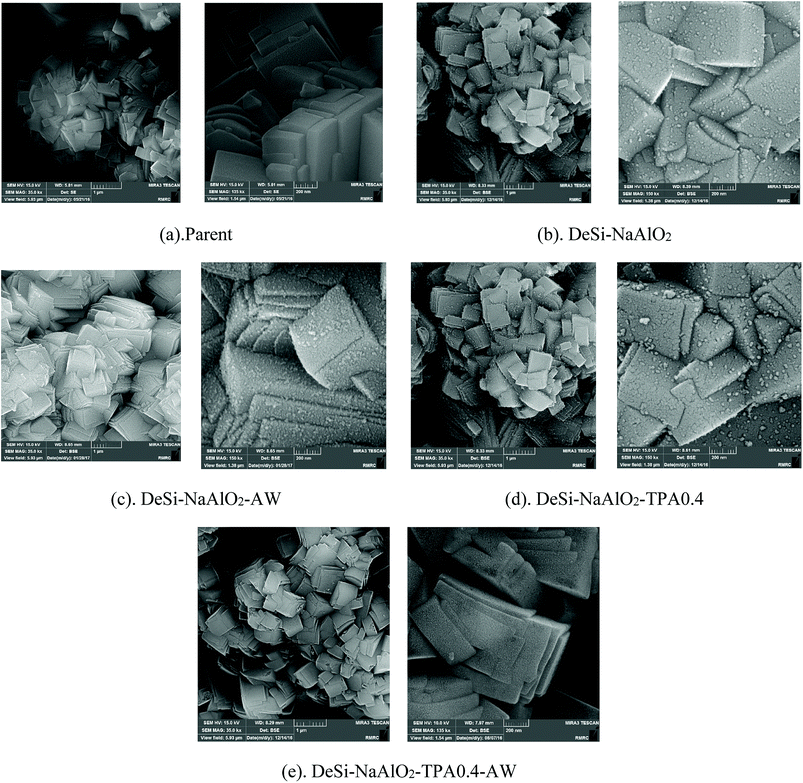 |
| Fig. 4 FE-SEM images of the (a) parent, (b) DeSi-NaAlO2, (c) DeSi-NaAlO2-AW, (d) DeSi-NaAlO2-TPA0.4, and (e) DeSi-NaAlO2-TPA0.4-AW. | |
3.1.5 NH3-TPD analysis. The acidity changes including surface concentration and strength of the acid sites in the parent catalyst and all treated samples were studied by the NH3-TPD method. Fig. 5 presents the NH3-TPD patterns of the parent zeolite and all desilicated samples before and after acid washing treatment. The NH3-TPD results including the amount of acid sites along with maximum desorption temperature which was calculated by desorption peak area and desorption peak temperature, respectively have been listed in Table 2. As shown in Fig. 5a, in comparison with the parent catalyst, total acid amount for the desilicated samples with pure NaAlO2 and different ratios of mixture of NaAlO2 and TPAOH solution increases remarkably respect to the parent catalyst. It can be explained by the fact that for desilicated samples in the presence of sodium aluminate, aluminate ions and Al2O3 deposited on the acid sites of zeolite surface are responsible for increasing the total acidity of the zeolite. As depicted in the figure, all treated samples present similar NH3-TPD patterns with three desorption peaks which the lower temperature peak (TP1) at around 165–195 °C and the higher temperature peak (TP2) at around 350–390 °C, are related to ammonia desorption from weak/moderate and moderate/strong acid sites, respectively. After desilication process with NaAlO2/TPAOH mixtures, weak and strong acid sites show a shift to lower temperatures respect to the parent one. This means that all the desilicated samples have lower acidic strength than the parent one because of aluminum atoms extraction from the zeolite framework and more mesoporosity of the desilicated samples. It is generally accepted that alkaline treatment over ZSM-5, results in both silicon and aluminum dissolution from the zeolite framework. Groen et al.16 investigated the role of aluminum for mesoporosity development of ZSM-5 zeolite in desilication by alkaline treatment. They showed that after alkaline treatment, both Al and Si were leached from the framework, but the concentration of Al was more than two orders lower than that of Si, which confirmed that in alkaline treatment Si dissolution was favored over that of Al. Some parts of aluminum species extracted during alkaline treatment have been reinserted into the zeolite surface from the alkaline solution. This phenomenon has been previously reported by other researchers based on 27Al MAS NMR and FTIR measurements.32,33 Verboekend and Pérez-Ramírez27 reported that extracted aluminum species from the zeolite in alkaline solutions can be partially inserted into the zeolite surface, which leads to increase both Brønsted and Lewis acid sites. You et al.34 showed that after desilication by alkaline treatment, the amount of framework aluminum decreased owing to extra framework aluminum formation. So it can be concluded that the generation of extra framework aluminum species is an inherent characteristic of desilication by alkaline solution. After acid washing treatment with concentrated hydrochloric acid, by removing the Al2O3 deposits and extra framework aluminum which reinserted to the zeolite surface at first step, the amount of total acidity decreased mostly even lower than the parent one (see Fig. 5b and Table 2). This is in line with previous studies which have been obtained similar observations on mesoporous zeolites after dealumination.21,22
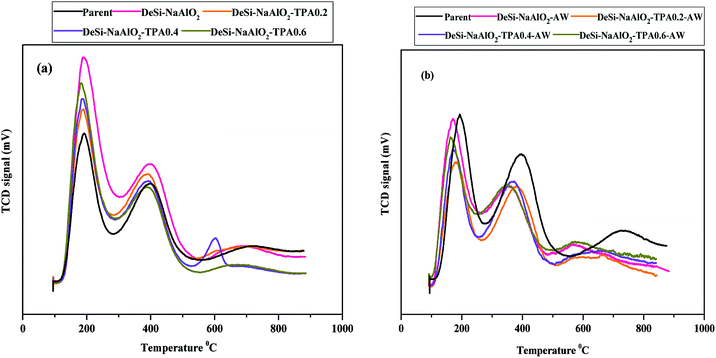 |
| Fig. 5 NH3-TPD profiles of the parent, all desilicated HZSM-5 samples (a) before acid washing (b) after acid washing. | |
Table 2 NH3-TPD data for the parent, all desilicated HZSM-5 samples before and after acid washing
Catalyst name |
Characteristic |
Acidity (mmol NH3 g−1) |
Peak temperature (°C) |
Weak |
Medium |
Strong |
Total |
Low temp. peak (TP1) |
High temp. peak (TP2) |
Parent |
0.083 |
0.139 |
0.114 |
0.336 |
191 |
391 |
DeSi-NaAlO2 |
0.185 |
0.421 |
0.204 |
0.810 |
186 |
396 |
DeSi-NaAlO2-TPA0.2 |
0.172 |
0.301 |
0.260 |
0.733 |
189 |
387 |
DeSi-NaAlO2-TPA0.4 |
0.182 |
0.322 |
0.219 |
0.723 |
187 |
397 |
DeSi-NaAlO2-TPA0.6 |
0.195 |
0.378 |
0.218 |
0.791 |
184 |
387 |
DeSi-NaAlO2-AW |
0.065 |
0.127 |
0.133 |
0.356 |
168 |
357 |
DeSi-NaAlO2-TPA0.2-AW |
0.05 |
0.094 |
0.091 |
0.235 |
167 |
366 |
DeSi-NaAlO2-TPA0.4-AW |
0.055 |
0.1 |
0.107 |
0.262 |
162 |
347 |
DeSi-NaAlO2-TPA0.6-AW |
0.048 |
0.085 |
0.115 |
0.248 |
176 |
379 |
According to easier hydrolysis of Si–OH–Si bond than Si–OH–Al bond in the presence of Al(OH)4− attack in alkaline solution, the amount of Si–OH groups (known as weak acid sites) on the external surface of the zeolite increase which is expected to have a good performance in MTP reaction.24,35 It is generally accepted that methanol to DME conversion, alkylation and methylation reactions were carried out by weak acid sites. They can also prevent many side reactions such as hydrogen transfer reactions in MTP process. But the strong acid sites have been known as main acid sites for olefin production in MTH reaction.7,36,37 Therefore, in order to improve catalyst stability and propylene selectivity in MTP reaction, it is necessary to adjust the concentration amount of weak and strong acid sites.
3.2 Catalytic performance
In order to investigate the effect of mesoporosity formation associated with alkaline-acid treatment using different ratios of the NaAlO2/TPAOH mixtures followed by acid washing, all the treated samples and the parent one were tested in the conversion of methanol to propylene reaction under similar operational conditions (T = 460 °C, P = 1 atm, feed: 50% wt methanol in water, WHSV = 0.9 h−1). Table 3 represents full description of the average product distributions in MTP reaction over the parent and all the treated samples in steady state conditions (time on stream of 48 h) when methanol conversion is above 99%. Parent catalyst in MTP reaction shows a catalytic performance with propylene selectivity of 30.7% and a total light olefins (C
2–C
4) selectivity of 57.9% along with 13.7% selectivity to C1–C4 saturated hydrocarbons and a lot of heavy hydrocarbons formation (28.4%).
Table 3 Product distribution of MTP reaction over the parent, all desilicated HZSM-5 samples before and after acid washing measured at steady state conditions (reaction condition: T = 460 °C, P = 1 atm, WHSV = 0.9 h−1, feed: 50 wt% methanol in water, time on stream of 48 h.)
Sample |
Conversion (%) |
Selectivity (%) |
C1–C4a |
C 2 |
C 3 |
Total C 4 |
(C 2–C 4) |
C 3/C 2 |
C5+b |
C4-HTI |
C1–C4 saturated hydrocarbons. C5 and higher hydrocarbons. |
Parent |
99.9 |
13.7 |
11.1 |
30.7 |
16.1 |
57.9 |
2.7 |
28.4 |
0.33 |
DeSi-NaAlO2 |
99.9 |
17.6 |
12.6 |
21.4 |
13.4 |
47.4 |
1.7 |
36.5 |
0.40 |
DeSi-NaAlO2-TPA0.2 |
99.7 |
16.4 |
11.4 |
23.3 |
14.2 |
48.9 |
2.0 |
34.6 |
0.36 |
DeSi-NaAlO2-TPA0.4 |
99.8 |
15.1 |
11.7 |
26.8 |
15.3 |
53.8 |
2.3 |
32.4 |
0.35 |
DeSi-NaAlO2-TPA0.6 |
99.9 |
16.1 |
12.1 |
25.2 |
13.8 |
51.1 |
2.1 |
35.5 |
0.38 |
DeSi-NaAlO2-AW |
99.7 |
11.4 |
10.7 |
33.7 |
17.6 |
62.0 |
3.15 |
21.8 |
0.29 |
DeSi-NaAlO2-TPA0.2-AW |
99.8 |
10.8 |
10.1 |
35.8 |
19.1 |
65.0 |
3.54 |
15.1 |
0.22 |
DeSi-NaAlO2-TPA0.4-AW |
99.8 |
9.6 |
9.4 |
37.7 |
21.2 |
68.3 |
4.01 |
13.8 |
0.17 |
DeSi-NaAlO2-TPA0.6-AW |
99.7 |
10.1 |
10.6 |
34.3 |
19.4 |
64.3 |
3.22 |
16.6 |
0.19 |
It can be clearly seen from the Table 3 that all the alkaline treated samples before acid washing represent higher heavy hydrocarbons selectivity and lower light olefins selectivity as well as lower propylene to ethylene ratio compared to the parent one, which these results are not appropriate for MTP process. As listed in Table 3, propylene and total light olefins selectivity decrease from 30.7 and 57.9% for the parent catalyst to 21.4 and 47.4% for the desilicated sample with pure sodium aluminate, respectively. Among all the desilicated samples with different ratio of NaAlO2 and TPAOH, the DeSi-NaAlO2-TPA0.4 sample represents better catalytic performance in terms of higher propylene selectivity (26.8%), higher light olefins selectivity (53.8%), and lower heavy hydrocarbon formation (32.4%). However, there is no improvement in the catalytic performance of this sample and other desilicated samples compared to the parent one.
These reactor test results show that only mesoporosity creation in the parent catalyst is not sufficient for improving the catalyst performance in MTP reaction. As discussed in BET and FE-SEM results, for all the desilicated samples pore blockage is caused by sodium aluminate-derived deposits. Moreover, precipitation of aluminate ions on the acid sites of the catalyst surface results in appearing Al2O3 after calcination step, which is responsible for huge acidity of the desilicated samples.21 It is generally believed that the catalyst with high acidity on the zeolite surface converts more light olefins to higher olefins, paraffins, and heavy hydrocarbons, which leads to low selectivity of light olefins, more coke formation and short catalytic lifetime. So, it is necessary to adjust the acidity of the desilicated samples to obtain better catalytic performance in MTP process. Our experimental results of the catalytic performance of the desilicated catalysts before acid washing are in consistent with BET, FE-SEM and NH3-TPD analysis.
As listed in Table 3, all the alkaline-acid treated samples exhibit higher propylene and butylene selectivity and lower selectivity to ethylene, C1–C4 saturated hydrocarbons and C5+ heavy hydrocarbons compared to the parent catalyst due to their high external surface area and mesopore volume.
According to Table 3, for alkaline-acid treated samples in the presence of TPAOH, propylene and butylene selectivity increase from (35.8 and 19.1%) to (37.7 and 21.3%), respectively by increasing TPAOH/(NaAlO2 + TPAOH) ratio from 0.2 to 0.4. But a more increase in the ratio (DeSi-NaAlO2-TPA0.6-AW sample) leads to decrease in propylene selectivity to 34.3% which is not beneficial. It can be clearly seen from the different ratios of the NaAlO2/TPAOH mixtures, the DeSi-NaAlO2-TPA0.4-AW compared to the parent catalyst exhibits higher selectivities to propylene (37.7 vs. 30.7%) and total butylenes (21.3 vs. 16.1%), as well as total light olefins (68.4 vs. 57.9%), while its selectivities to C1–C4 alkanes (9.6 vs. 13.7%) and heavy hydrocarbons (13.8% vs. 28.4%) are relatively lower. The catalytic performance of this sample is probably due to higher external surface area and mesopore volume compared to the other ratios of NaAlO2/TPAOH mixtures, which leads to a shorter diffusion path length. Therefore, a shorten residence time of heavy hydrocarbon products in the crystal pores of this sample before diffusing out to the gas phase results in less heavy hydrocarbons products (C5+) and less saturated hydrocarbons (C1–C4) selectivities in this sample. In this study, C4 Hydrogen Transfer Index (C4-HTI) was also used to evaluate the catalytic performance of the parent and all the alkaline-acid treated samples in MTP reaction. This parameter is defined as a ratio between the yields of butane (n-C4 and i-C4) and the total yield of C4 hydrocarbons (n-C4, i-C4 and total C
4) which announce the progress of the hydrogen transfer reactions over the ZSM-5 catalysts.38 Therefore, a high value of C4-HTI indicates extensive aromatization and cyclization reactions along with high alkane generation.39 As listed in the final column of the Table 3, for all the alkaline-acid treated samples C4-HTI is lower than the parent one. This parameter for the DeSi-NaAlO2-TPA0.4-AW sample is 0.17 which is less than the other alkaline-acid treated samples and less than half of the parent catalyst (0.33). This trend can be expected by the NH3-TPD results for this sample due to their high weak and medium acid sites which result in reducing the hydrogen transfer reactions in the MTP reaction.
In order to quantitative estimate of the catalyst stability, the catalyst life time is considered as the time on stream after which the methanol/DME conversion drops below 90% which is indicated by the dashed line in Fig. 6. The reactor test results over the parent catalyst showed that the methanol/DME conversion remained approximately 100% up to 250 h on stream and then dropped slowly to 90% after 425 h on stream. It should be noted the similar long life time has been recently reported by Yaripour et al.7 According to literature,22,40 it is expected that improving mesoporosity and acid modifications over microporous ZSM-5 catalyst surface results in better catalytic performance and longer life time.
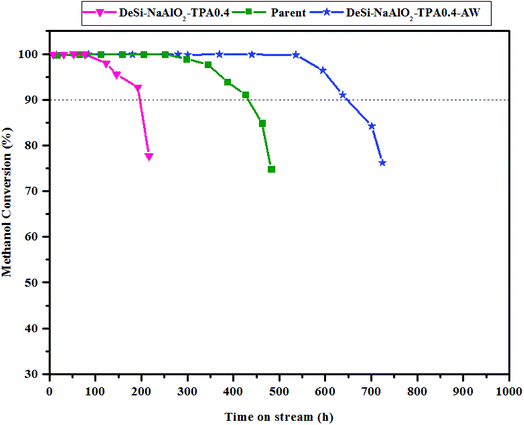 |
| Fig. 6 Conversion of methanol as a function of time on stream over the parent and optimum ratio of NaAlO2/TPAOH before and after acid washing step. | |
As it was expected from the product distribution data over the alkaline treated samples (see Table 3), the catalyst life time value in MTP reaction was obtained 192 h for DeSi-NaAlO2-TPA0.4 sample, which is lower than 425 h for the parent one. As shown in Fig. 6, the initial activity of the DeSi-NaAlO2-TPA0.4-AW catalyst is similar to that of the parent one, but methanol conversion remains constant at approximately 100% for 520 h on stream. The methanol conversion of the DeSi-NaAlO2-TPA0.4-AW sample falls below 90% after 640 h on stream. The catalytic lifetime of this catalyst is nearly 1.5 times higher than that of the parent one. These results confirmed that after alkaline-acid treatment over the microporous ZSM-5 catalyst, the stability was noticeably improved. A comparison of MTP reactor test results of the DeSi-NaAlO2-TPA0.4-AW catalyst with those of other reported mesoporous ZSM-5 catalysts have been presented in Table 4. As presented in this table, this catalyst shows long life time and good catalytic performance in terms of high propylene and total light olefins selectivity compared to literature. Although the numerical value of our catalyst lifetime is higher than the reported values in the table, but since the operating conditions of the tests presented in the table are not the same, therefore we cannot claim that our catalyst shows a better performance compared to other catalyst in the same conditions. On the other hand, the comparison in view of stability has more credibility for references 5,10,41,42 because the reactor tests has been performed under the same operating conditions with the current research.
Table 4 Comparison of MTP reactor test results of the optimum alkaline-acid treated catalyst with literature
Preparation method |
Si/Al |
MeOH : water |
WHSV (h−1) |
Selectivity |
P/E |
Lifetimea |
Application |
Ref. |
Ethylene |
Propylene |
C2 –C4![[double bond, length as m-dash]](https://www.rsc.org/images/entities/char_e001.gif) |
The catalyst life time is considered as the time on stream after which the methanol/DME conversion drops below 90%. |
Dealumination |
200 |
1 : 1 |
0.9 |
4 |
40 |
42.9 |
11.2 |
384 h |
MTP |
5 |
Desilication |
175 |
1 : 1 |
1 |
10.3 |
44.4 |
80.8 |
4.3 |
80 h |
MTP |
10 |
Desilication |
76 |
1 : 1 |
1 |
4.1 |
42.2 |
67.7 |
10.1 |
100 h |
MTP |
11 |
Desilication |
200 |
1 : 1 |
0.9 |
8 |
43 |
__ |
5.4 |
75 h |
MTO |
41 |
Soft template |
175 |
1 : 1 |
1 |
11.6 |
40.6 |
73.9 |
3.5 |
83 h |
MTP |
42 |
Dealumination |
175 |
1 : 1 |
6 |
12.5 |
38.0 |
72.6 |
3.0 |
75 h |
MTP |
43 |
Fluoride medium route |
23 |
Pure MeOH |
1.8 |
7 |
36 |
66 |
5.1 |
— |
MTP |
44 |
Hard template |
45 |
__ |
20 |
17 |
28 |
45 |
1.6 |
10 h |
MTH |
45 |
Dealumination |
27 |
__ |
6.65 |
25 |
37 |
__ |
1.5 |
— |
MTH |
46 |
Seed-induced |
100 |
1 : 1 |
2 |
14 |
36 |
74 |
2.6 |
190 h |
MTP |
47 |
DeSi-NaAlO2-TPA0.4-AW |
200 |
1 : 1 |
0.9 |
9.4 |
37.7 |
68.3 |
4.0 |
640 h |
MTP |
This study |
4. Conclusion
A two-step route comprising alkaline treatment in different ratios of NaAlO2 and TPAOH, followed by acid washing was successfully developed to introduce mesoporosity in highly siliceous HZSM-5 zeolites. The porosity of the alkaline treated samples which is mostly blocked by Al2O3 and silica debris significantly improved after acid washing treatment. The characterization results confirm that the acid washing step after desilication of HZSM-5 catalyst leads to a reduction in the acid sites strength without harshly destructing the crystal structure and its intrinsic acidity. Moreover, the hierarchical catalysts prepared by alkaline-acid treatment have the Si/Al ratio very similar to that of the parent one. The catalytic performance of the alkaline treated samples did not show any improve in propylene and light olefins selectivity, due to pore blockage and huge acidity while after acid washing step, a considerable increase in light olefins selectivity and life time was achieved. Alkaline-acid treated sample with TPAOH/(NaAlO2 + TPAOH) ratio of 0.4, represents the highest propylene and light olefins selectivities (37.7 and 68.4%, respectively), as well as the lowest selectivity to heavy hydrocarbons (13.8%), among all the alkaline-treated samples. Moreover, the lifetime of this catalyst (640 h) showed a significant increase compared to the parent one (425 h). The lower strength of its acid sites and higher mesoporosity may be the reasons for better catalytic performance of DeSi-NaAlO2-TPA0.4-AW catalyst in MTP reaction.
Conflicts of interest
There are no conflicts to declare.
Acknowledgements
The authors gratefully acknowledge Tarbiat Modares University (Tehran, Iran) and the Petrochemical Research and Technology Company (Tehran, Iran) for their financial supports of the research.
References
- M. Khanmohammadi, S. Amani, A. B. Garmarudi and A. Niaei, Chin. J. Catal., 2016, 37, 325–339 CrossRef.
- F. Gorzin and F. Yaripour, Res. Chem. Intermed., 2018, 1–25 Search PubMed.
- H. M. Torres Galvis and K. P. de Jong, ACS Catal., 2013, 3, 2130–2149 CrossRef CAS.
- F. Yaripour, Z. Shariatinia, S. Sahebdelfar and A. Irandoukht, J. Nat. Gas Sci. Eng., 2015, 22, 260–269 CrossRef CAS.
- M. Rostamizadeh and F. Yaripour, J. Taiwan Inst. Chem. Eng., 2017, 71, 454–463 CrossRef CAS.
- C. D. Chang and A. J. Silvestri, J. Catal., 1977, 47, 249–259 CrossRef CAS.
- F. Yaripour, Z. Shariatinia, S. Sahebdelfar and A. Irandoukht, Microporous Mesoporous Mater., 2015, 203, 41–53 CrossRef CAS.
- Y.-Q. Zhuang, X. Gao, Y.-p. Zhu and Z.-h. Luo, Powder Technol., 2012, 221, 419–430 CrossRef CAS.
- Z. Hu, H. Zhang, L. Wang, H. Zhang, Y. Zhang, H. Xu, W. Shen and Y. Tang, Catal. Sci. Technol., 2014, 4, 2891–2895 RSC.
- J. Ahmadpour and M. Taghizadeh, C. R. Chim., 2015, 18, 834–847 CrossRef CAS.
- C. Mei, P. Wen, Z. Liu, H. Liu, Y. Wang, W. Yang, Z. Xie, W. Hua and Z. Gao, J. Catal., 2008, 258, 243–249 CrossRef CAS.
- Z. Xie, Z. Liu, Y. Wang, Q. Yang, L. Xu and W. Ding, Int. J. Mol. Sci., 2010, 11, 2152–2187 CrossRef CAS PubMed.
- D. Serrano and P. Pizarro, Chem. Soc. Rev., 2013, 42, 4004–4035 RSC.
- K. Möller and T. Bein, Chem. Soc. Rev., 2013, 42, 3689–3707 RSC.
- J. Čejka and S. Mintova, Catal. Rev., 2007, 49, 457–509 CrossRef.
- J. C. Groen, L. A. A. Peffer, J. A. Moulijn and J. Pérez-Ramírez, Chem.–Eur. J., 2005, 11, 4983–4994 CrossRef CAS PubMed.
- D. a. J. P.-R. Verboekend, Catal. Sci. Technol., 2011, 1(6), 879–890 RSC.
- F. Schmidt, M. R. Lohe, B. Büchner, F. Giordanino, F. Bonino and S. Kaskel, Microporous Mesoporous Mater., 2013, 165, 148–157 CrossRef CAS.
- K. Sadowska, A. Wach, Z. Olejniczak, P. Kuśtrowski and J. Datka, Microporous Mesoporous Mater., 2013, 167, 82–88 CrossRef CAS.
- S. Fathi, M. Sohrabi and C. Falamaki, Fuel, 2014, 116, 529–537 CrossRef CAS.
- R. Caicedo-Realpe and J. Pérez-Ramírez, Microporous Mesoporous Mater., 2010, 128, 91–100 CrossRef CAS.
- J. C. Groen, J. A. Moulijn and J. Pérez-Ramírez, Microporous Mesoporous Mater., 2005, 87, 153–161 CrossRef CAS.
- J. Ding, M. Wang, L. Peng, N. Xue, Y. Wang and M.-Y. He, Appl. Catal., A, 2015, 503, 147–155 CrossRef CAS.
- M.-L. Gou, R. Wang, Q. Qiao and X. Yang, Microporous Mesoporous Mater., 2015, 206, 170–176 CrossRef CAS.
- A. Čižmek, B. Subotić, R. Aiello, F. Crea, A. Nastro and C. Tuoto, Microporous Mater., 1995, 4, 159–168 CrossRef.
- D. Verboekend and J. Pérez-Ramírez, Catal. Sci. Technol., 2011, 1, 879–890 RSC.
- D. Verboekend and J. Pérez-Ramírez, Chem.–Eur. J., 2011, 17, 1137–1147 CrossRef CAS PubMed.
- T. Fu, J. Chang, J. Shao and Z. Li, J. Energy Chem., 2017, 26, 139–146 CrossRef.
- K. Sadowska, K. Góra-Marek, M. Drozdek, P. Kuśtrowski, J. Datka, J. Martinez Triguero and F. Rey, Microporous Mesoporous Mater., 2013, 168, 195–205 CrossRef CAS.
- S. Abelló, A. Bonilla and J. Pérez-Ramírez, Appl. Catal., A, 2009, 364, 191–198 CrossRef.
- F. Jin, Y. Cui, Z. Rui and Y. Li, J. Mater. Res., 2010, 25, 272–282 CrossRef CAS.
- G. Lietz, K. Schnabel, C. Peuker, T. Gross, W. Storek and J. Volter, J. Catal., 1994, 148, 562–568 CrossRef CAS.
- M. Ogura, S.-y. Shinomiya, J. Tateno, Y. Nara, M. Nomura, E. Kikuchi and M. Matsukata, Appl. Catal., A, 2001, 219, 33–43 CrossRef CAS.
- S. J. You and E. D. Park, Microporous Mesoporous Mater., 2014, 186, 121–129 CrossRef CAS.
- A. Čižmek, B. Subotić, R. Aiello, F. Crea, A. Nastro and C. Tuoto, Microporous Mater., 1995, 4, 159–168 CrossRef.
- S. M. Campbell, X.-Z. Jiang and R. F. Howe, Microporous Mesoporous Mater., 1999, 29, 91–108 CrossRef CAS.
- M. Rostamizadeh and A. Taeb, Synth. React. Inorg., Met.-Org., Nano-Met. Chem., 2016, 46, 665–671 CrossRef CAS.
- S. Teketel, W. Skistad, S. Benard, U. Olsbye, K. P. Lillerud, P. Beato and S. Svelle, ACS Catal., 2012, 2, 26–37 CrossRef CAS.
- M. Bjørgen, F. Joensen, M. S. Holm, U. Olsbye, K.-P. Lillerud and S. Svelle, Appl. Catal., A, 2008, 345, 43–50 CrossRef.
- M. H. Ahmed, O. Muraza, M. Yoshioka and T. Yokoi, Microporous Mesoporous Mater., 2017, 241, 79–88 CrossRef CAS.
- M. Rostamizadeh, F. Yaripour and H. Hazrati, Polyolefins J., 2018, 5, 59–70 Search PubMed.
- J. Ahmadpour and M. Taghizadeh, J. Nat. Gas Sci. Eng., 2015, 23, 184–194 CrossRef CAS.
- S. Zhang, Y. Gong, L. Zhang, Y. Liu, T. Dou, J. Xu and F. Deng, Fuel Process. Technol., 2015, 129, 130–138 CrossRef CAS.
- F. L. Bleken, S. Chavan, U. Olsbye, M. Boltz, F. Ocampo and B. Louis, Appl. Catal., A, 2012, 447, 178–185 CrossRef.
- P. Sazama, B. Wichterlova, J. Dedecek, Z. Tvaruzkova, Z. Musilova, L. Palumbo, S. Sklenak and O. Gonsiorova, Microporous Mesoporous Mater., 2011, 143, 87–96 CrossRef.
- S. M. Almutairi, B. Mezari, E. A. Pidko, P. C. Magusin and E. J. Hensen, J. Catal., 2013, 307, 194–203 CrossRef CAS.
- H. Chen, Y. Wang, F. Meng, C. Sun, H. Li, Z. Wang, F. Gao, X. Wang and S. Wang, Microporous Mesoporous Mater., 2017, 244, 301–309 CrossRef CAS.
|
This journal is © The Royal Society of Chemistry 2018 |
Click here to see how this site uses Cookies. View our privacy policy here.