DOI:
10.1039/C8RA07863G
(Paper)
RSC Adv., 2018,
8, 39902-39912
Enhanced performance of chemical looping combustion of methane with Fe2O3/Al2O3/TiO2 oxygen carrier
Received
21st September 2018
, Accepted 20th November 2018
First published on 29th November 2018
Abstract
Iron-based oxygen carriers supported on alumina or alumina/titania were prepared and evaluated for chemical looping combustion of methane. The reduction conversion of Fe2O3/Al2O3 and Fe2O3/Al2O3/TiO2 particles was markedly increased with increasing inlet concentration and was slightly enhanced by elevated operating temperatures. According to the shrinking core model, the mass transfer coefficients (kg) of Fe2O3/Al2O3 and Fe2O3/Al2O3/TiO2 reduction with methane are found to be 0.07 and 0.12 mm s−1. Complete combustion of methane is almost achieved for experiments conducted with Fe2O3/Al2O3 and Fe2O3/Al2O3/TiO2 operated as the Fe2O3/CH4 molar ratio reached about 5.4 and 4.4, respectively. Carbon deposition during methane combustion was avoided by using Fe2O3/Al2O3/TiO2 as an oxygen carrier. More heat was generated for the combustion of methane by Fe2O3/Al2O3/TiO2 oxygen carriers because methane more fully reacted with the Fe2O3 contained in the Fe2O3/Al2O3/TiO2 oxygen carriers.
1 Introduction
Shale gas is an important natural gas resource, and distributed in many countries, such as China, Argentina, Algeria, U.S., Canada, Mexico, Australia, South Africa, and Russia etc.1 For U.S. dry natural gas production, shale gas as the largest contributor has rapidly grown by 40% from 9.7 trillion cubic feet in 2012 to 13.6 trillion cubic feet in 2015.2,3 Natural gas is one of the primary fuels composed of approximately 90% of methane, which is widely used as a fuel and chemical feedstock for the conversion of methane to generate a number of products, for instance, hydrogen, liquid fuels, chemicals, heat, and electricity.4 However, carbon dioxide (CO2) is also generated during a variety of methane conversion processes. CO2 is a major contributor to global warming and climate change. In order to combat global warming and mitigate the CO2 emissions, various carbon capture, storage, and utilization technologies have recently been developed.
Chemical looping process (CLP) is considered to be a novel alternative for fuel combustion to achieve efficient energy generation as well as inherent CO2 separation. A chemical looping system is typically comprised of a fuel reactor and an air reactor. Carbonaceous fuels are oxidized by metal oxides (oxygen carriers) in the fuel reactor to generate CO2 and H2O. The reduced oxygen carrier is subsequently oxidized and regenerated by air in the air reactor.
The performance of the oxygen carrier is crucial for CLP development and is greatly influenced by the characteristics of metal oxide and support material. Fe-based oxygen carriers are frequently applied for chemical looping combustion of gaseous fuel; however, sintering and attrition during continuous and high-temperature operations would decrease the reactivity of these oxygen carriers. Therefore, oxygen carriers of mixed metal oxide and support material are frequently employed for chemical looping operations to retard the sintering of oxygen carriers and to enhance their mechanical strength.5 Adánez et al.6 studied the CLC of methane in a thermogravimetric analyzer (TGA) using hematite as active phase and supported by various inert materials, and also reported that Fe2O3/Al2O3 and Fe2O3/ZrO2 oxygen carriers containing 40–80 wt% Fe2O3 sintered at above 1100 °C exhibited high reactivity with methane and delivered high crush strength. Johansson et al.7 utilized the Fe2O3 supported with MgAl2O4 as an oxygen carrier to investigate their reactivity properties on the CLC of methane in a fluidized bed reactor. The results indicated that 60 wt% Fe2O3/MgAl2O4 oxygen carriers sintered at 1100 °C demonstrated high reactivity regarding methane combustion. In addition, the crush strength of Fe2O3/MgAl2O4 particles ranged of 125 to 180 μm was determined to be about 1.8 N. Zafar et al.8 investigated Fe2O3 on the MgAl2O4 and SiO2 supports in a fluidized bed reactor for CLC application, and found that the Fe2O3/MgAl2O4 oxygen carriers showed high reactivity with methane during the Fe2O3 reduced to Fe3O4, whereas the poor reactivity with methane was observed during the Fe3O4 reduced to FeO. Besides, the unreactive iron silicate was formed at high temperature by using SiO2 as support. Corbella and Palacios9 revealed the methane conversion was reached about 90% for methane combustion with titania supported Fe2O3 oxygen carriers in a fixed bed reactor operated at 900 °C, and also reported that the low oxygen capacity was caused in the reduction stage because the interaction between iron-containing active phase and the support material lead to the formation of an irreducible phase FeTiO3. Li et al.10 indicated TiO2 as support can markedly lower the energy barrier for O2− migration within the dense solid phase, thus enhancing the O2− diffusivity.10 Qin et al.11 stated the vacancy defect is easy to form on the FeTiO3 surface because the vacancy formation energy of FeTiO3 is lower than Fe2O3 in the reduction stage. Consequently, the enhancing the porous surface structure formation on FeTiO3. However, Zhao and Shadman12 observed that phase separation of iron oxide phase and titania phase during the redox cycles. Iron oxide migrates to the surface of FeTiO3 during the oxidation, which could fracture the ilmenite particle. This mechanism might lower the particle strength.
In this study, alumina is selected as support to improve the mechanical strength of iron-based oxygen carrier, and titania is employed as another support to promote the reactivity. Based our previous research results, the components of the Fe2O3/Al2O3 and Fe2O3/Al2O3/TiO2 oxygen carriers were optimized to achieve the better reactivity during TGA tests and mechanical strength.13,14 The optimized composition of Fe2O3/Al2O3 and Fe2O3/Al2O3/TiO2 oxygen carriers were determined to be 60/40 and 70/20/10 in weight percentage. Alumina and alumina/titania supported Fe2O3 oxygen carriers (Fe2O3/Al2O3 and Fe2O3/Al2O3/TiO2) were fabricated to investigate their reactivity properties in a fixed bed reactor. The effect of operating temperature and inlet gas concentration on the combustion of CH4 with Fe2O3/Al2O3 and Fe2O3/Al2O3/TiO2 oxygen carriers in a fixed bed reactor was examined and analyzed by shrinking core model (SCM). Preliminarily kinetic study for CLC of methane with Fe2O3/Al2O3 and Fe2O3/Al2O3/TiO2 oxygen carriers are performed based on the experimental results from this study. Furthermore, the performance of the moving bed reactor using iron-based oxygen carriers was also discussed in this study. Fe2O3/Al2O3 and Fe2O3/Al2O3/TiO2 oxygen carriers were employed for chemical looping combustion of methane in a moving bed reactor (MBR) operated with the various CH4/Fe2O3 ratio. The methane conversion, carbon conversion, and oxygen carrier conversion for methane combustion by Fe2O3/Al2O3 and Fe2O3/Al2O3/TiO2 oxygen carriers were evaluated by the moving bed reactor. The crystalline phases of the reduced oxygen carrier after the moving bed operation were identified by X-ray diffraction (XRD). Heat analysis for chemical looping combustion of methane was employed to evaluate the heat balance of input and output processing capacities.
2 Experimental
2.1 Preparation of various iron-based oxygen carriers
Fe2O3/Al2O3 and Fe2O3/Al2O3/TiO2 particles were prepared to serve as oxygen carriers in this study. Fe2O3/Al2O3 oxygen carriers were formulated with 60 wt% hematite (99.9% Fe2O3, China Steel) and 40 wt% alumina (99% Al2O3, Chin Jung). Fe2O3/Al2O3/TiO2 were formulated with 70 wt% hematite, 20 wt% alumina and 10 wt% titania. Hematite, alumina and titania particles of roughly 1 μm were mixed in deionized water and dried at 80 °C for 6 hours to form a cake, and were then pulverized and screened for sizes between 1.2 and 1.4 mm. The Fe2O3/Al2O3 and Fe2O3/Al2O3/TiO2 particles were later sintered at 1300 °C and 1200 °C for 2 hours in a muffle furnace, respectively. The crush strength of prepared oxygen carriers was analyzed by a texture machine (TA.XT plus), and the attrition of prepared oxygen carriers was examined by an attrition analyzer following ASTM methods D4058-96. The true density, particle density and bulk density of prepared oxygen carriers were determined by eqn (1) and (2), respectively, similar defines and results were reported by previous researchers.15where ρt is the true density of the oxygen carrier without the pores which presented in the oxygen carrier; ρp is the particle density of the oxygen carrier including the pores, which was measured by the Archimedes method; is the bulk density of the oxygen carrier; ϕ is 49.13% and 59.60% as the porosity of prepared Fe2O3/Al2O3 and Fe2O3/Al2O3/TiO2, respectively; ε is the fraction of void contained in the packed Fe2O3/Al2O3 and Fe2O3/Al2O3/TiO2 oxygen carriers, which were determined to be 41.61% and 40.17%, respectively. The main physicochemical properties of these prepared iron-based oxygen carriers are shown in Table 1.
Table 1 Main physicochemical properties of the iron-based oxygen carriers
Parameters |
Unit |
Fe2O3/Al2O3 |
Fe2O3/Al2O3/TiO2 |
Fe2O3 fraction |
wt% |
60 |
70 |
Particle size |
mm |
1.2–1.4 |
1.2–1.4 |
True density, ρt |
kg m−3 |
4673 |
4795 |
Particle density, ρp |
kg m−3 |
2377 |
1937 |
Bulk density, ρb |
kg m−3 |
1388 |
1159 |
Porosity |
% |
49.13 |
59.60 |
Fraction void |
% |
41.61 |
40.17 |
Crushing strength |
N |
30.53 |
10.25 |
Attrition |
% |
4.01 |
16.83 |
Specific surface area, BET |
m2 g−1 |
0.61 |
0.64 |
A porosity of fresh oxygen carriers was measured by Archimedes method in water. The porosities of Fe2O3/Al2O3 and Fe2O3/Al2O3/TiO2 oxygen carriers were determined to be 49.13% and 59.60%, respectively. The physical properties of 60 wt% Fe2O3/Al2O3 oxygen carriers reported by De Vos et al.16 were similar to the results of this study that the porosity was obtained to be in the range of 49.10–59.70%.16 From the literature published by Breault et al.17 illustrated that the disappear of small grains due to the growth of larger grain promoted by high-temperature calcination, hence, the grain size and porosity become larger, while the specific surface area becomes smaller.17 Breault et al.17 also reported that as the calcination temperature is raised to 1000 °C, the specific surface area of hematite particles was dropped from 6.0 to 0.3 m2 g−1.17 A similar result was observed in this study, the specific surface area of Fe2O3/Al2O3 and Fe2O3/Al2O3/TiO2 oxygen carriers determined by BET analysis were 0.61 and 0.64 m2 g−1 at calcination temperatures of 1300 °C and 1100 °C, respectively.
2.2 Establishment of the fixed bed reactor system
A fixed-bed reactor system composed of a 25.4 mm ID SS310 reactor and with a PID-controlled heating element covering 200 mm of reactor length employed in this study is shown in Fig. 1. A plate with sixteen 0.25 mm apertures was located in the lower part of the reactor for supporting 40 g of prepared Fe2O3/Al2O3 particles or 30.2 g of prepared Fe2O3/Al2O3/TiO2 particles. The temperature of the loaded reactor was then increased from room temperature with a ramping rate of 10 °C min−1 and eventually kept at a specific operating temperature, ranging from 875 to 925 °C. For reduction experiments, methane was introducing into the reactor at a flow rate of 1 L min−1 at different concentrations, ranging from 5 to 20%. After reduction, N2 was introduced for sweeping reducing gas contained in the reactor. Air at a flow rate of 1 L min−1 was subsequently introduced for 30 minutes to oxidize the reduced oxygen carriers. The outlet stream from the reactor was passed through a cold trap to condense steam, and was consequently analyzed by a non-dispersive infrared sensor (NDIR, Molecular Analysis 6000i) and a gas chromatography equipped with a thermal conductivity detector (GC-TCD, China Chromatography 2000) to detect the concentrations of carbon dioxide, carbon monoxide, methane, hydrogen, and oxygen.
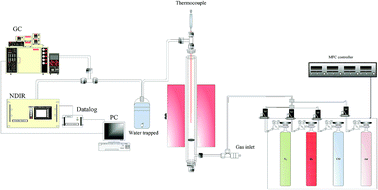 |
| Fig. 1 Schematic diagram of the fixed bed reactor system used in this study for CLP operation. | |
2.3 Establishment of the moving bed reactor system
Schematic diagram of the annular duel-tube moving bed reactor (ADMBR) employed in this study is shown in Fig. 2. The reactor was composed of a 76.20 mm ID SS310S outer tube covered with an electric heating element to provide isothermally atmosphere, and a 25.40 mm ID SS310S inner tube. Roughly 3.0 kg of prepared Fe2O3/Al2O3 oxygen carriers or 2.5 kg of prepared Fe2O3/Al2O3/TiO2 oxygen carriers were initially packed in the spacing between inner and outer tubes of the ADMBR. Fe2O3/Al2O3 and Fe2O3/Al2O3/TiO2 oxygen carriers were then continuously fed into the packed reactor by a screw conveyor at flow rate operated at 29.53 and 20.72 g min−1, respectively. Methane was fed into inner tube to serve as gaseous fuel, and N2 was also introduced into the inner tube at a flow rate of 2.2 L min−1. The fuel gas was then passing through the bottom of the inner tube for consequent combustion with Fe-based oxygen carriers fed into and moved through the moving bed reactor. The reduced oxygen carriers were collectively removed out of the fuel reactor by another screw conveyor. The outlet stream from the moving bed reactor was cooled by a cold trap to condense water vapour and was afterward analyzed by a gas chromatography equipped with a thermal conductivity detector (GC-TCD, China Chromatography 2000) to detect the concentration of H2 and a non-dispersive infrared sensor (NDIR, Molecular Analysis 6000i) to detect the concentration of CO2, CO, CH4, and O2. The phase transformation of prepared oxygen carriers during methane combustion was characterized by X-ray diffraction (XRD).
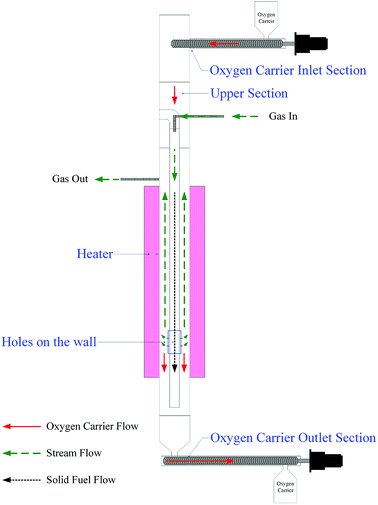 |
| Fig. 2 Schematic diagram of the moving bed reactor system used in this study for methane combustion. | |
3 Results and discussion
3.1 Methane combustion with iron-based oxygen carriers in a fixed bed reactor
Moving bed reactor (MBR) with counter-flow for solids and gases were proposed to enhance the utilization of available oxygen in the oxygen carriers.18 In order to estimate the influence of thermal and chemical effects only on the oxygen carrier reduction, a fixed bed reactor was used instead of moving beds. Indeed, the fixed bed allows avoiding any flow of the material, and the performance of the oxygen carrier in this kind of reactor may only be the consequence of chemical and thermal effects. The reactivity of prepared Fe2O3/Al2O3 and Fe2O3/Al2O3/TiO2 oxygen carriers were investigated and conducted in the fixed bed reactor operated at the temperature between 875 and 925 °C by feeding CH4/N2 gas mixtures containing 5 to 20 vol% CH4. The iron-based oxygen carriers are fully reduced for methane combustion as described by reaction (3).4,19,20 |
 | (3) |
Based on the mass balances of oxygen and hydrogen, the reduction conversion of iron-based oxygen carriers for methane combustion is determined as:
|
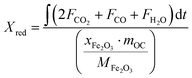 | (4) |
|
FH2O = 2FCH4,in − (2FCH4 + FH2)
| (5) |
where
FCH4,in is the inlet mole flow rate (mmol min
−1) of CH
4;
Fi is the outlet molar flow rate (mmol min
−1) of species i, i is denoted as CO
2, CO, H
2O, H
2, and CH
4;
mOC is the weight (g) of oxygen carriers packed in the reactor;
xFe2O3 is the fraction of Fe
2O
3 contained in the oxygen carriers;
MFe2O3 is 159.69 g mol
−1 as the molecular weight of Fe
2O
3.
Fig. 3 shows the effect of operating temperature on the reduction of iron-based oxygen carriers with methane. The reduction conversions of Fe
2O
3/Al
2O
3/TiO
2 oxygen carriers calculated for experiments conducted with constant operation time are significantly higher than that of Fe
2O
3/Al
2O
3 oxygen carriers and are increased with higher operating temperatures. For instance, more than 95% Fe
2O
3/Al
2O
3/TiO
2 is reduced by methane at about 84 minutes for experiments conducted at 925 °C, much higher than that for Fe
2O
3/Al
2O
3 reduction with methane.
Fig. 4 demonstrates the effect of inlet methane concentrations on the CLC of CH
4 by iron-based oxygen carriers. The conversions of Fe
2O
3/Al
2O
3 and Fe
2O
3/Al
2O
3/TiO
2 reduction are increased for experiments conducted with greater inlet methane concentrations, possibly because of the existence of more methane molecules. More methane molecules are more ready to react with Fe
2O
3 contained in the iron-based oxygen carriers to generate CO
2 and H
2O, as described by reaction
(3).
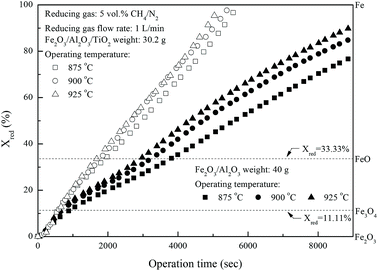 |
| Fig. 3 Effect of operating temperature on the reduction of Fe2O3/Al2O3 and Fe2O3/Al2O3/TiO2 with CH4 in the fixed bed. | |
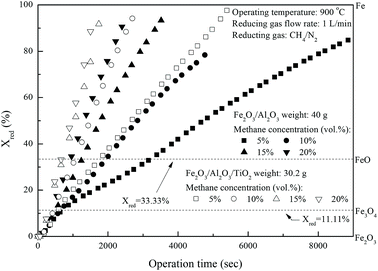 |
| Fig. 4 Effect of inlet CH4 concentrations on the reduction of Fe2O3/Al2O3 and Fe2O3/Al2O3/TiO2 with CH4 in the fixed bed. | |
In this study, the temporal behaviour of iron-based oxygen carrier reduction for methane combustion is described by a shrinking core model (SCM), as exercised by most researchers for the application of various oxygen carriers for chemical looping:21–23
|
 | (6) |
|
 | (7) |
|
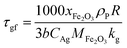 | (8) |
|
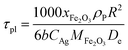 | (9) |
|
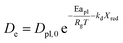 | (10) |
|
 | (11) |
where
R and
r are the radius (m) of the fresh particle and the unreacted core;
τgf and
τpl are the time (s) required for complete conversion of the oxygen carrier when the reaction is controlled by the gas-film diffusion and the product layer diffusion;
CAg is the inlet molar concentration (mol m
−3) of the gaseous fuel;
b is the stoichiometric coefficient of gaseous fuel combusted with Fe
2O
3, which is determined to be 4/3 by reaction
(3);
kg is the mass transfer coefficient (m s
−1) between gaseous fuel and oxygen carriers;
De is the effective diffusion coefficient (m
2 s
−1) of gaseous fuel in the product layer;
Dpl,0 (m
2 s
−1) and Ea
pl (kJ mol
−1) are the pre-exponential factor and activation energy for the product layer diffusion reaction;
kd,
kd,0 and Ea
d (kJ mol
−1) are the decay constant, pre-exponential factor and activation energy for the product layer diffusivity;
Rg is the ideal gas constant;
T (K) is the operation temperature.
The reduction kinetics of Fe2O3/Al2O3 and Fe2O3/Al2O3/TiO2 with methane are regressed and calculated by the shrinking core model (SCM), as described in eqn (6)–(11). After fitting the conversion curves, the kinetic parameters are summarized in Table 2. As listed in Table 2, the mass transfer coefficient (kg) of around 0.07 mm s−1 is calculated for the reduction of Fe2O3/Al2O3 with methane, while the kg of Fe2O3/Al2O3/TiO2 for methane combustion reached 0.12 mm s−1, indicating that the reaction rate of methane for Fe2O3/Al2O3/TiO2 reduction is faster than that for Fe2O3/Al2O3 reduction. Less Dpl,0 is obtained for experiments with Fe2O3/Al2O3 oxygen carriers than those with Fe2O3/Al2O3/TiO2 oxygen carriers, explicitly, demonstrating that the methane more easily diffusion through the product layer of Fe2O3/Al2O3/TiO2 oxygen carriers. Moreover, the influence of operating temperature on the oxygen carrier conversions for the reduction of Fe2O3/Al2O3 with methane are more than that for Fe2O3/Al2O3/TiO2 reduction with methane, as shown in Fig. 3, because high activation energy for the product layer diffusion reaction (Eapl) is obtained for Fe2O3/Al2O3 reduction with methane. Furthermore, the slop of the reduction conversion vs. time curves is observed to be altered for experiments conducted at the various operating temperature, which may be also attributed to the decay constant (kd) is dependent on the operating temperatures, similar to the results reported by previous researchers.23,24 For experiments conducted with operating temperature of 900 °C, the slop of the reduction conversion vs. time curves for Fe2O3/Al2O3 reduction is significantly changed with inlet methane concentration ranged from 5 to 20%, as shown in Fig. 4, possibly due to high kd,0 is obtained for Fe2O3/Al2O3 reduction with CH4.22
Table 2 Kinetics parameters for the reduction of iron-based oxygen carriers conducted with methane
Parameter |
Unit |
Fe2O3/Al2O3 |
Fe2O3/Al2O3/TiO2 |
kg |
mm s−1 |
0.07 |
0.12 |
Dpl,0 |
mm2 s−1 |
4.37 × 1020 |
1.03 × 1021 |
Eapl |
kJ mol−1 |
476.45 |
446.61 |
kd,0 |
— |
3.08 × 1032 |
7.88 × 1013 |
Ead |
kJ mol−1 |
736.19 |
305.41 |
In this study, the gas-film diffusion and the product layer diffusion were major reaction resistances contributed for Fe2O3/Al2O3 and Fe2O3/Al2O3/TiO2 reduction with methane in the fixed bed reactor. Cabello et al.22 studied that the kinetic study of 20 wt% Fe2O3/Al2O3 oxygen carrier for gaseous fuel combustion by chemical looping process, and also indicated that the reduction reactions are controlled by the chemical reaction in the grain surface and the diffusion through the product layer of FeAl2O4 around the grains. This can be attributed to the external diffusion resistance is eliminated by using a small mass of solid sample (50 mg).22 Comparing the results from the literature and this study, methane more easily diffusion through the product layer of 20 wt% Fe2O3/Al2O3 oxygen carriers, while less temperature effect on the reduction conversion was observed for experiments with both iron-based oxygen carriers. The reason is due to the Dpl,0 and Epl obtained here were significantly lower than that found in the literature.22 Additionally, the intensity of the reaction rate for reduction of both iron-based oxygen carriers with methane was significantly changed with various methane concentration probably due to higher kd,0 and higher Ed were obtained in this work.
3.2 Methane combustion with Fe2O3/Al2O3 oxygen carriers in the ADMBR
Chemical looping combustion of methane was conducted in the ADMBR at 900 °C by feeding Fe2O3/Al2O3 oxygen carriers at flow rate of 29.53 g min−1 and CH4 at flow rate from 328.4 to 985.3 mg min−1. The main components of outlet streams for the combustion of methane from the moving bed reactor operated at different inlet CH4 flow rates were determined to be CO2, CH4, H2 and slightly CO in this study, as illustrated in Fig. 5. Outlet gas stream containing about 96% CO2 and 4% CH4 are achieved for experiments conducted with CH4/Fe2O3 ratio ranged from 18.5 to 37.1 mg g−1. However, CO2 concentration of the outlet gas stream is rapidly reduced for experiments carried out with the CH4/Fe2O3 ratio more than 37.1 mg g−1. More CO and H2 are observed due to the occurrence of incomplete methane combustion and methane decomposition reaction, as depicted by reaction (12).19,20 Based on carbon and hydrogen balance calculation, the steam generation rate (FH2O) and carbon deposition rate (FC) for methane combustion are determined by eqn (5) and (13) and were also shown in Fig. 5. |
FC = FCH4,in − (FCH4 + FCO2 + FCO)
| (13) |
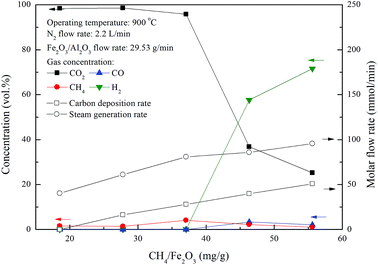 |
| Fig. 5 Effect of methane flow rates on the combustion of methane with Fe2O3/Al2O3 in the moving bed. | |
The carbon deposition rate and steam generation rate of methane combustion by Fe2O3/Al2O3 in the ADMBR are found to be increased for experiments conducted with greater CH4/Fe2O3 ratio. The increased in carbon deposition for experiments carried out at high CH4/Fe2O3 ratio may be ascribed to the presence of excessive methane, thus more methane molecules are decomposed to generate carbon and hydrogen. CO2 concentrations for CH4 combustion conducted with CH4/Fe2O3 ratio of 27.8 and 37.1 mg g−1 were determined to be about 98% and 96%, respectively, indicating that hydrogen generated by methane decomposition was completely combusted by Fe2O3/Al2O3. Moreover, hydrogen was detected in the outlet stream for experiments operated at CH4/Fe2O3 ratio more than 37.1 mg g−1, possibly due to more hydrogen generated by methane decomposition was higher than that consumed by Fe2O3/Al2O3 reduction reaction.
The carbonaceous gases (CO2, CO and CH4) and deposited carbon are generated by methane combustion and decomposition. Therefore, carbon conversion (XC) is the conversion of inlet methane to carbonaceous gases in the fuel reactor, as described as eqn (14). Based on the oxygen balance, the methane conversion (Xmethane) and oxygen carrier conversion (XOC) for CH4 combustion were determined by eqn (15) and (16).25,26
|
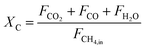 | (14) |
|
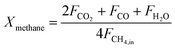 | (15) |
|
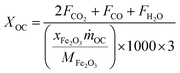 | (16) |
where
m˙OC is the mass flow rate (g min
−1) of the oxygen carriers in the ADMBR. As illustrated in
Fig. 6,
XC and
Xmethane are significantly decreased for experiments carried out with increasing CH
4/Fe
2O
3 ratio for the combustion of methane with Fe
2O
3/Al
2O
3 oxygen carriers in the ADMBR operated at 900 °C, indicating excessive methane is provided. Experimental results obtained in this study suggest that the complete combustion reaction between CH
4 and Fe
2O
3/Al
2O
3 oxygen carriers could be accomplished for experiment conducted with CH
4/Fe
2O
3 ratio of 18.5 mg g
−1. As also indicated in
Fig. 6, nearly 24.2% of the oxygen carrier conversion is achieved for the complete combustion of methane with Fe
2O
3/Al
2O
3 oxygen carriers, demonstrating the Fe
2O
3/Al
2O
3 oxygen carriers operated in a moving bed reactor is majorly reduced to Fe
3O
4 and FeO, similar to the results reported by previous study.
27 However, oxygen carrier conversion for CLC of methane is found to be slightly enhanced for experiments conducted with greater CH
4/Fe
2O
3 ratio, because more Fe
2O
3/Al
2O
3 oxygen carriers are considered to be reduced by fuel gases, such as CH
4, CO and H
2, which is generated by methane combustion and decomposition.
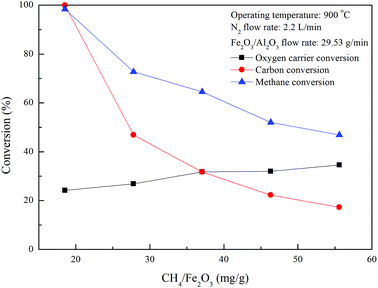 |
| Fig. 6 Effect of methane flow rates on fuel and oxygen carrier conversions for CLC of methane with Fe2O3/Al2O3. | |
3.3 Methane combustion with Fe2O3/Al2O3/TiO2 oxygen carriers in the ADMBR
Chemical looping combustion of methane by Fe2O3/Al2O3/TiO2 oxygen carriers for experiments conducted with various CH4/Fe2O3 ratio were examined in this study. The outlet gas streams for combustion experiments of methane were composed mainly of CO2, CH4, H2 and CO, as illustrated in Fig. 7. Outlet gas stream of nearly 100% CO2 is achieved for experiments conducted with CH4/Fe2O3 ratio of 22.6 mg g−1. However, CO2 concentration of the outlet gas stream for CLC of methane are found to be decreased for experiments carried out with CH4/Fe2O3 ratio more than 34.0 mg g−1, whereas H2 and CO concentrations are increased. Besides, methane concentration of the outlet gas stream for methane combustion with Fe2O3/Al2O3/TiO2 is enhanced for experiments conducted with CH4/Fe2O3 ratio ranged from 34.0 to 45.3 mg g−1. Subsequently, CH4 concentration of the outlet gas stream is reduced for experiments conducted with CH4/Fe2O3 ratio above 45.3 mg g−1, possibly due to the occurrence of methane reforming reaction, as depicted by reaction (17).28,29 Thus, less steam generation rate is observed for the combustion of methane with Fe2O3/Al2O3/TiO2 than that for methane combustion with Fe2O3/Al2O3, as illustrated in Fig. 7. |
CH4 + H2O → CO + 3H2
| (17) |
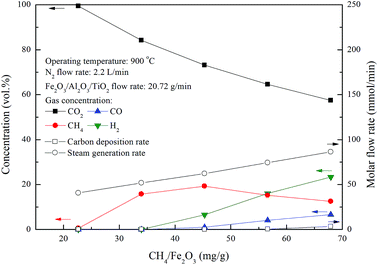 |
| Fig. 7 Effect of methane flow rates on the combustion of methane with Fe2O3/Al2O3/TiO2 in the moving bed. | |
As shown in Fig. 5 and 7, the carbon deposition rate for methane combustion with Fe2O3/Al2O3/TiO2 is noticeably lower than that for methane combustion with Fe2O3/Al2O3, indicating carbon deposition is significantly reduced as methane is combusted with Fe2O3/Al2O3/TiO2 oxygen carriers. Carbon deposition is impeded because the reactivity of Fe2O3/Al2O3/TiO2 oxygen carriers for methane combustion is higher than that of Fe2O3/Al2O3 oxygen carriers. Fig. 8 demonstrates that high carbon conversions (approximately 99%) are obtained for methane combustion conducted with CH4/Fe2O3 ratio ranged from 22.6 to 56.6 mg g−1, while the carbon conversion of methane combustion reached about 94.5% for experiments carried out with CH4/Fe2O3 ratio of 67.9 mg g−1, due to the insufficient oxygen carriers are provided to react with methane. Thus, methane molecules are slightly decomposed to generate carbon and hydrogen. As also illustrated in Fig. 8, methane is completely combusted by Fe2O3/Al2O3/TiO2 oxygen carriers for experiment conducted with CH4/Fe2O3 ratio of 22.6 mg g−1. However, as for experiment conducted with CH4/Fe2O3 ratio more than 22.6 mg g−1, the methane conversions are found to be decreased with increased with increasing CH4/Fe2O3 ratio. The decreased in methane conversion for experiments carried out at high CH4/Fe2O3 ratio may be ascribed to the occurrence of incomplete methane combustion and methane reforming reaction, thus more combustible gases are observed.
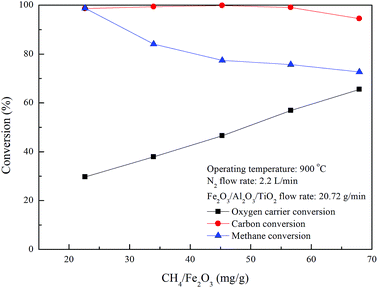 |
| Fig. 8 Effect of methane flow rates on fuel and oxygen carrier conversions for CLC of methane with Fe2O3/Al2O3/TiO2. | |
Oxygen carrier conversion of around 29.7% is achieved for the complete combustion of methane with Fe2O3/Al2O3/TiO2 oxygen carrier, while the oxygen carrier conversions are enhanced for experiment conducted with CH4/Fe2O3 ratio above 22.6 mg g−1, as shown in Fig. 8, further demonstrating increased CH4/Fe2O3 ratio to promote the Fe2O3/Al2O3/TiO2 reduction. Besides, Fe2O3/Al2O3 flowrate of around 29.53 g min−1 was provided for complete methane combustion, while the Fe2O3/Al2O3/TiO2 flow rate needed to about 20.72 g min−1 for the complete combustion of methane. Less oxygen carrier is demanded for the complete combustion of methane with Fe2O3/Al2O3/TiO2 than that for methane combustion with Fe2O3/Al2O3, possibly due to the methane is considered to be consumed more rapidly by Fe2O3/Al2O3/TiO2 reduction reaction than by Fe2O3/Al2O3 reduction reaction. Moreover, less oxygen carriers are required may also be ascribed to the higher Fe2O3 contained in the Fe2O3/Al2O3/TiO2 oxygen carrier. Abad et al.21 analyzed the design criteria for a CLC system and reported that the solid circulation rate was decreased with increasing the et al. oxide content for the combustion of fuel gases (H2, CO and CH4) with different metal oxides (CuO, NiO, and Fe2O3).
As listed in Table 3, the gas hourly space velocity (GHSV) of CH4/N2 mixture was increased with increasing inlet methane concentration. Higher GHSV means higher fuel/oxygen carrier ratios and shorter residence time. Therefore, the increase in the GHSV led to a decrease of methane and carbon conversion, whereas an increase of oxygen carrier conversion.
Table 3 The operating conditions of methane combustion with iron-based oxygen carriers in the moving bed reactora
FCH4,in mmol min−1 |
CCH4,in vol% |
GHSV h−1 |
Fe2O3/Al2O3 |
Fe2O3/Al2O3/TiO2 |
m˙OC g min−1 |
CH4/Fe2O3 mg g−1 |
m˙OC g min−1 |
CH4/Fe2O3 mg g−1 |
GHSV: gas hourly space velocity; FCH4,in: the inlet mole flow rate of methane; CCH4,in: the inlet concentration of methane; m˙OC: the mass flow rate of the oxygen carriers in the ADMBR. |
20.5 |
18.52 |
295.1 |
29.53 |
18.54 |
20.72 |
22.64 |
30.7 |
25.42 |
322.4 |
27.80 |
33.96 |
41 |
31.25 |
349.8 |
37.07 |
45.29 |
51.2 |
36.23 |
377.1 |
46.34 |
56.61 |
61.4 |
40.54 |
404.4 |
55.61 |
67.93 |
3.4 Performance evaluation and heat analysis for CH4 combustion
In order to differentiate the theoretical and actual Fe2O3 amount for the combustion of one mole of methane, a Fe2O3/CH4 molar ratio was determined for evaluating the demand of oxygen carrier. For moving bed operation, a five-stage RGibbs reactor model has been shown to accurately simulate the experimental results for syngas and natural gas conversion.30,31 The parameters for the ASPEN Plus® model have been proposed by Li et al.18 and Kathe et al.32 The maximum fuel and oxygen carrier conversions for chemical looping combustion of methane with Fe2O3 in the counter-current moving bed reducer operated at 900 °C and 1 atm could be obtained from ASPEN simulation under the thermodynamic equilibrium. Based on the stoichiometry calculation, 4/3 mole of Fe2O3 are consumed for 1 mole of methane combustion, indicating the minimum Fe2O3 to CH4 molar flow rate ratio is determined to be 1.33 for theoretically complete combustion of CH4. Experiments and ASPEN simulations to examine the effect of Fe2O3/CH4 molar ratio on the fuel and oxygen carrier conversions were conducted with various Fe2O3/CH4 molar ratio, and the results were shown in Fig. 9. The decrease in the oxygen carrier conversion is observed for ASPEN simulation carried out with Fe2O3/CH4 molar ratio more than 0.9, while complete conversion of methane is achieved as Fe2O3/CH4 molar ratio reached more than 2.6, similar to the results reported by previous study.25,32 For the complete methane combustion, higher Fe2O3/CH4 molar ratio is determined by ASPEN simulation than that by stoichiometry calculation, which may be attributed to the thermodynamic resistance, hence, Fe2O3 is not fully reduced to Fe for the complete combustion of methane.
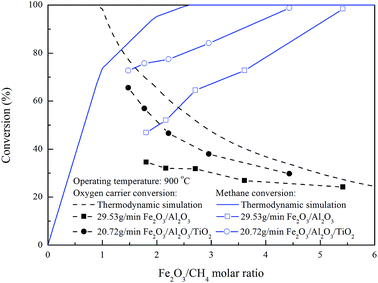 |
| Fig. 9 Effect of Fe2O3/CH4 molar ratio on fuel and oxygen carrier conversion for methane combustion in the moving bed. | |
Compared with the simulation result, the methane conversion for the combustion of methane with Fe2O3/Al2O3 and Fe2O3/Al2O3/TiO2 oxygen carriers are increased for experiments conducted with higher Fe2O3/CH4 molar ratio, and reached 98.4 and 98.8% as Fe2O3/CH4 molar ratio reached 5.4 and 4.4, as also shown in Fig. 9. More oxygen carriers are required for experiments conducted with Fe2O3/Al2O3 oxygen carriers than that with Fe2O3/Al2O3/TiO2 oxygen carriers, probably because lattice oxygen present in the Fe2O3/Al2O3/TiO2 oxygen carriers are more readily to react with combustible gas. Thus, the oxygen carrier conversions for the combustion of methane with Fe2O3/Al2O3/TiO2 oxygen carriers are higher than that for methane combustion with Fe2O3/Al2O3 oxygen carriers.
According to the XRD patterns illustrated in Fig. 10, the crystalline phases of freshly prepared Fe2O3/Al2O3 oxygen carriers are mainly Fe2O3 and Al2O3. The oxygen carriers moved through the ADMBR was also sampled, and characterized to be mostly Al2FeO4, indicating that the amount of oxygen utilization from F2O3 to FeO. Similar observation was reported by previous researchers.20,33 It has been reported that the crystal phase of Fe3C might be formation during ASPEN simulation of chemical looping combustion of methane.25 The formations of Fe3C and Fe were observed for experiment conducted with CH4/Fe2O3 ratio of 55.6 mg g−1 and Fe2O3/Al2O3 flow rate of 29.53 g min−1. Takenaka et al.34 analyzed the formation of filamentous carbon over supported Fe catalysts through methane decomposition, and also reported that Fe3C formation is favored at the mass fraction of Fe2O3 contained in the Fe2O3/Al2O3 was more than 38%. Additionally, Fe3C and Fe are the typical active species to be employed as catalyst for methane decomposition.34,35 Consequently, carbon deposition is also contributed by the Fe3C and Fe generated by the reaction between methane and Fe2O3/Al2O3 oxygen carrier. Subsequently, the reduced Fe2O3/Al2O3 oxygen carriers are completely oxidized by air in the air reactor to generate Fe2O3 and Al2O3, which are observed in the XRD pattern.
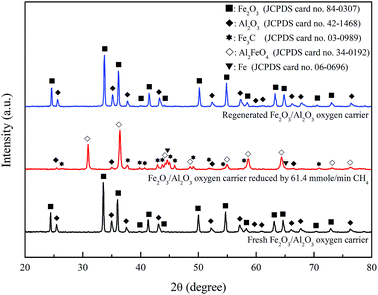 |
| Fig. 10 X-ray diffraction patterns of fresh, reduced and regenerated Fe2O3/Al2O3 oxygen carriers for methane combustion. | |
The fresh Fe2O3/Al2O3/TiO2 particles were characterized by XRD for phase identification as shown in Fig. 11. Fe2O3, Fe2TiO5 and Al2O3 are the major crystalline phases of fresh oxygen carriers. For experiment conducted with CH4/Fe2O3 ratio of 67.9 mg g−1 and Fe2O3/Al2O3/TiO2 flow rate of 20.72 g min−1, the reduced Fe2O3/Al2O3/TiO2 oxygen carriers were sampled from moving bed operation. The absence of Fe2O3, Fe2TiO5 and Al2O3 in the XRD pattern indicated that Fe2O3 and Fe2TiO5 is completely reduced. Hence, the crystalline phases of the reduced Fe2O3/Al2O3/TiO2 oxygen carriers are composed of Fe, Fe3O4, Al2FeO4 and FeTiO3, as illustrated in Fig. 11. In addition, Al2FeO4 and FeTiO3 generated during reduction might serve as support materials as well as oxygen carriers in practical operation by moving bed reactor for chemical looping process, similar to the results reported by previous study.13,36 For Fe2O3/Al2O3/TiO2 oxygen carriers sampled after regeneration, Fe2O3, Fe2TiO5 and Al2O3 are observed in the XRD pattern, demonstrating that Fe, Fe3O4, Al2FeO4 and FeTiO3 contained in the reduced Fe2O3/Al2O3/TiO2 oxygen carriers were completely oxidized to Fe2O3, Fe2TiO5 and Al2O3.
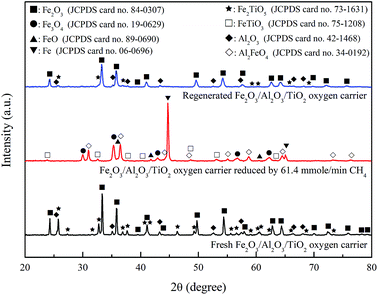 |
| Fig. 11 X-ray diffraction patterns of fresh, reduced and regenerated Fe2O3/Al2O3/TiO2 oxygen carriers for methane combustion. | |
The mechanism for reduction of Fe2O3/Al2O3 and Fe2O3/Al2O3/TiO2 oxygen carriers with methane are proposed as reactions (18)–(24) based on the experimental results from this study. Unfortunately, from the analysis of the fixed bed curves, the reduction conversion contributed by each reduction reactions were not possible to be separated because these reduction reactions may occur simultaneously. Therefore, as described by reaction (3), the overall reduction reaction of iron-based oxygen carrier for methane combustion is summarized and simplified by Integrated Rate of Reduction (IRoR) model, which has been widely used for evaluating the total reduction rate of iron ores.37
For Fe2O3/Al2O3 reduction:
|
4Fe2O3 + 8Al2O3 + CH4 ↔ 8Al2FeO4 + 2H2O + CO2
| (18) |
|
4Al2FeO4 + CH4 ↔ 4Fe + 4Al2O3 + 2H2O + CO2
| (19) |
|
3Fe + 2CO ↔ Fe3C + CO2
| (20) |
For Fe2O3/Al2O3/TiO2 reduction:
|
4Fe2O3 + 8Al2O3 + CH4 ↔ 8Al2FeO4 + 2H2O + CO2
| (18) |
|
4Al2FeO4 + CH4 ↔ 4Fe + 4Al2O3 + 2H2O + CO2
| (19) |
|
4Fe2TiO5 + 4TiO2 + CH4 ↔ 8FeTiO3 + 2H2O + CO2
| (21) |
|
12Fe2O3 + CH4 ↔ 8Fe3O4 + 2H2O + CO2
| (22) |
|
4Fe3O4 + CH4 ↔ 12FeO + 2H2O + CO2
| (23) |
|
4FeO + CH4 ↔ 4Fe + 2H2O + CO2
| (24) |
The input processing capacity (Qin) is the enthalpy of methane calculated as:
where
m˙OC and Δ
HFuel are the molar flow rate (mol s
−1) of methane and the higher heating value (kJ mol
−1), respectively. The heat balance analysis is determined by the following equation:
|
Qin = QC,out + QunC,out
| (26) |
where
QC,out and
QunC,out are the output processing capacity (W) for methane combustion and unburned, respectively. The output processing capacity for CLC and unburned is subsequently calculated by the following equations:
|
QC,out = ∑(Fj,in − Fj,out,C)ΔHrxn,j
| (27) |
|
QunC,out = ∑Fj,out,CΔHrxn,j
| (28) |
where
Fj,in is the inlet mole flow rate of species j;
Fj,out,C is the molar flow rate of species j generated by methane combustion; Δ
Hrxn,j is the enthalpy of species j; j is denoted as CO, CH
4, H
2 and C.
As shown in Fig. 12, 269 W and 270 W are released for methane combustion with Fe2O3/Al2O3 and Fe2O3/Al2O3/TiO2 oxygen carriers in the ADMBR, indicating that roughly 98% of Qin released for methane combustion using Fe2O3/Al2O3 and Fe2O3/Al2O3/TiO2 oxygen carriers in the ADMBR. Afterward, QC,out for methane combustions with Fe2O3/Al2O3/TiO2 oxygen carriers are increased for experiments conducted with higher CH4/Fe2O3 ratio, and reached 578 W as methane conversion reached 72.7%. However, QC,out for methane combustion with Fe2O3/Al2O3 oxygen carriers conducted with CH4/Fe2O3 ratio greater than 37.1 mg g−1, and reached 350 W as methane conversion reached less than 64.6%, as shown in Fig. 12. More heat is generated for combustion of methane by Fe2O3/Al2O3/TiO2 oxygen carriers, probably because methane is more fully to react with the Fe2O3 contained in the Fe2O3/Al2O3/TiO2 oxygen carriers. Moreover, less heat is generated for combustion of methane by Fe2O3/Al2O3 oxygen carriers because more carbon deposition is formed.
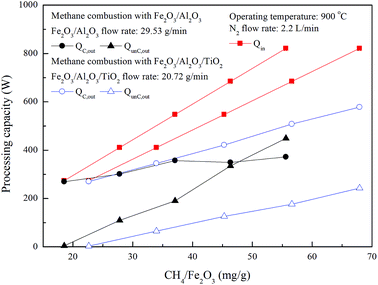 |
| Fig. 12 Effect of methane flow rate on processing capacity for methane combustion in the moving bed. | |
4 Conclusions
Fe2O3 supported with Al2O3 and Al2O3/TiO2 as oxygen carrier were investigated for CLC of methane. The reduction kinetic of Fe2O3/Al2O3 and Fe2O3/Al2O3/TiO2 with methane are agreeably described by a shrinking core model. The results indicated that the reduction rate of CH4 for Fe2O3/Al2O3/TiO2 reduction was faster than that for Fe2O3/Al2O3 reduction, also indicated that the methane more easily diffusion through the product layer of Fe2O3/Al2O3/TiO2 oxygen carriers. The activation energy for the product layer diffusion reaction (Eapl) estimated for CLP by employment of Fe2O3/Al2O3 and Fe2O3/Al2O3/TiO2 as oxygen carrier are about 476 and 447 kJ mol−1 for oxygen carrier reduction with methane, respectively. Approximately, methane is completely combusted for experiments conducted in the moving bed reactor with Fe2O3/Al2O3 and Fe2O3/Al2O3/TiO2 operated at Fe2O3/CH4 molar ratio reached about 5.4 and 4.4, respectively; in addition, the oxygen carrier conversions are respectively reached about 24.2% and 29.7%. Carbon deposition during methane combustion is noticeably avoided by using Fe2O3/Al2O3/TiO2 as oxygen carrier. According to the XRD characterization, Al2FeO4 is the major crystalline phase generated during CLC of methane with Fe2O3/Al2O3 oxygen carrier. The formations of Fe3C and Fe were observed for experiment conducted with CH4/Fe2O3 ratio of 67.9 mg g−1 and Fe2O3/Al2O3 flow rate of 29.53 g min−1, which would serve as catalyst for methane decomposition. For Fe2O3/Al2O3/TiO2 oxygen carriers sampled after reduction, Fe, Fe3O4, Al2FeO4 and FeTiO3 were identified by the XRD pattern, demonstrating Al2FeO4 and FeTiO3 generated during reduction might become support materials as well as oxygen carriers in practical operation by moving bed reactor for chemical looping process. Output processing capacity estimated for CLC by employment of Fe2O3/Al2O3 and Fe2O3/Al2O3/TiO2 as oxygen carrier are increased for experiments conducted with higher CH4/Fe2O3 ratio, and reached 350 W and 578 W as methane conversion reached around 64.6% and 72.7%, respectively. About 269 W and 270 W are released for complete methane combustion with Fe2O3/Al2O3 and Fe2O3/Al2O3/TiO2 oxygen carriers in the ADMBR, indicating that roughly 98% of Qin released for methane combustion using Fe2O3/Al2O3 and Fe2O3/Al2O3/TiO2 oxygen carriers in the ADMBR.
Conflicts of interest
There are no conflicts to declare.
Acknowledgements
This research was supported by Grant MOST 106-3113-E-007-002-from the National Science and Technology Program-Energy, Taiwan, and by Grant MOST 105-2622-E-011-019-CC2 and MOST 103-2221-E-011-002-MY3 from the Ministry of Science and Technology, Taiwan. The authors appreciated China Steel Corp. for providing hematite powders for the preparation of oxygen carriers.
References
- World Energy Council (WEC), World Energy Resources – Unconventional Gas, a Global Phenomenon, 2016 Search PubMed.
- U.S. Energy Information Administration (EIA), Annual Energy Outlook 2014 with Projections to 2040, 2014 Search PubMed.
- U.S. Energy Information Administration (EIA), Annual Energy Outlook 2016 with Projections to 2040, 2016 Search PubMed.
- L. S. Fan, Chemical Looping Systems for Fossil Energy Conversions, John Wiley & Sons, Inc., New York, 2010 Search PubMed.
- J. Adánez, A. Abad, F. Garcia-Labiano, P. Gayan and L. F. de Diego, Progress in Chemical-looping Combustion and Reforming Technologies, Prog. Energy Combust. Sci., 2012, 38, 215–282 CrossRef.
- J. Adánez, L. F. de Diego, F. García-Labiano, P. Gayán, A. Abad and J. M. Palacios, Selection of Oxygen Carriers for Chemical-looping Combustion, Energy Fuels, 2004, 18, 371–377 CrossRef.
- M. Johansson, T. Mattisson and A. Lyngfelt, Investigation of Fe2O3 with MgAl2O4 for Chemical-looping Combustion, Ind. Eng. Chem. Res., 2004, 43, 6978–6987 CrossRef CAS.
- Q. Zafar, T. Mattisson and B. Gevert, Redox Investigation of Some Oxides of Transition-state Metals Ni, Cu, Fe, and Supported on SiO2 and MgAl2O4, Energy Fuels, 2006, 20, 33–44 CrossRef.
- B. M. Corbella and J. M. Palacios, Titania-supported Iron Oxide as Oxygen Carrier for Chemical-looping Combustion of Methane, Fuel, 2007, 86, 113–122 CrossRef CAS.
- F. Li, S. Luo, Z. Sun, X. Bao and L. S. Fan, Role of Metal Oxide Support in Redox Reactions of Iron Oxide for Chemical Looping Applications: Experiments and Density Functional Theory Calculations, Energy Environ. Sci., 2011, 4, 3661–3667 RSC.
- L. Qin, Z. Cheng, J. A. Fan, D. Kopechek, D. Xu, N. Deshpande and L. S. Fan, Nanostructure Formation Mechanism and Ion Diffusion in Iron-titanium Composite Materials with Chemical Looping Redox Reactions, J. Mater. Chem. A, 2015, 3, 11302–11312 RSC.
- Y. Zhao and F. Shadman, Kinetics and Mechanism of Ilmenite Reduction with Carbon Monoxide, AIChE J, 1990, 36, 1433–1438 CrossRef CAS.
- P. C. Chiu, Y. Ku, Y. L. Wu, H. C. Wu, Y. L. Kuo and Y. H. Tseng, Characterization and Evaluation of Prepared Fe2O3/Al2O3 Oxygen Carriers for Chemical Looping Process, Aerosol Air Qual. Res., 2014, 14, 981–990 CrossRef.
- M. C. Lo, Composite Fe-Ti Based Oxygen Carrier for Chemical Looping Combustion and Hydrogen Generation, Master Thesis in Department of Chemical Engineering, National Taiwan University of Science and Technology, Taipei City, Taiwan, 2014 Search PubMed.
- P. Markström and A. Lyngfelt, Designing and Operating a Cold-flow Model of a 100 kW Chemical-looping Combustor, Powder Technol., 2012, 222, 182–192 CrossRef.
- Y. De Vos, M. Jacobs, P. Van Der Voort, I. Van Driessche, F. Snijkers and A. Verberckmoes, Optimization of Spray Dried Attrition-resistant Iron Based Oxygen Carriers for Chemical Looping Reforming, Chem. Eng. J., 2017, 309, 824–839 CrossRef CAS.
- R. W. Breault, C. S. Yarrington and J. M. Weber, The Effect of Thermal Treatment of Hematite Ore for Chemical Looping Combustion of Methane, J. Energy Resour. Technol., 2016, 138, 0422021–0422028 Search PubMed.
- F. Li, L. Zeng, L. G. Velazquez-Vargas, Z. Yoscovits and L. S. Fan, Syngas Chemical Looping Gasification Process: Bench-scale Studies and Reactor Simulations, AIChE J., 2010, 56, 2186–2199 CrossRef CAS.
- P. Cho, T. Mattisson and A. Lyngfelt, Carbon Formation on Nickel and Iron Oxide-containing Oxygen Carriers for Chemical-looping Combustion, Ind. Eng. Chem. Res., 2005, 44, 668–676 CrossRef CAS.
- Y. Ku, H. C. Wu, P. C. Chiu, Y. H. Tseng and Y. L. Kuo, Methane Combustion by Moving Bed Fuel Reactor with Fe2O3/Al2O3 Oxygen Carriers, Appl. Energy, 2014, 113, 1909–1915 CrossRef CAS.
- A. Abad, J. Adánez, F. García-Labiano, L. F. de Diego, P. Gayán and J. Celaya, Mapping of the Range of Operational Conditions for Cu-, Fe-, and Ni-based Oxygen Carriers in Chemical-looping Combustion, Chem. Eng. Sci., 2007, 65, 533–549 CrossRef.
- A. Cabello, A. Abad, F. García-Labiano, P. Gayán, L. F. de Diego and J. Adánez, Kinetic Determination of a Highly Reactive Impregnated Fe2O3/Al2O3 Oxygen Carrier for Use in Gas-fueled Chemical Looping Combustion, Chem. Eng. J., 2014, 258, 265–280 CrossRef CAS.
- A. Abad, F. García-Labiano, P. Gayán, L. F. de Diego and J. Adánez, Redox Kinetics of CaMg0.1Ti0.125Mn0.775O2.9−δ for Chemical Looping Combustion (CLC) and Chemical Looping with Oxygen Uncoupling (CLOU), Chem. Eng. J., 2015, 269, 67–81 CrossRef CAS.
- L. F. de Diego, A. Abad, A. Cabello, P. Gayán, F. García-Labiano and J. Adánez, Reduction and Oxidation Kinetics of a CaMn0.9Mg0.1O3−δ Oxygen Carrier for Chemical-looping Combustion, Ind. Eng. Chem. Res., 2014, 53, 87–103 CrossRef CAS.
- L. Zeng, A. Tong, M. Kathe, S. Bayham and L. S. Fan, Iron Oxide Looping for Natural Gas Conversion in a Countercurrent Moving Bed Reactor, Appl. Energy, 2015, 157, 338–347 CrossRef CAS.
- H. C. Wu and Y. Ku, Chemical Looping Gasification of Charcoal with Iron-based Oxygen Carriers in an Annular Dual-tube Moving Bed Reactor, Aerosol Air Qual. Res., 2016, 16, 1093–1103 CrossRef CAS.
- S. Luo, S. Bayham, L. Zeng, O. McGiveron, E. Chung, A. Majumder and L. S. Fan, Conversion of Metallurgical Coke and Coal Using a Coal Direct Chemical Looping (CDCL) Moving Bed Reactor, Appl. Energy, 2014, 118, 300–308 CrossRef CAS.
- P. C. Chiu and Y. Ku, Chemical Looping Process – a Novel Technology for Inherent CO2 Capture, Aerosol Air Qual. Res., 2012, 12, 1421–1432 CrossRef CAS.
- M. Kathe, C. Fryer, P. Sandvik, F. Kong, Y. Zhang, A. Empfield and L. S. Fan, Modularization Strategy for Syngas Generation in Chemical Looping Methane Reforming Systems with CO2 as Feedstock, AIChE J., 2017, 63, 3343–3360 CrossRef CAS.
- A. Tong, D. Sridhar, Z. Sun, H. R. Kim, L. Zeng, F. Wang, D. Wang, M. V. Kathe, S. Luo, Y. Sun and L. S. Fan, Continuous High Purity Hydrogen Generation from a Syngas Chemical Looping 25 kWth Sub-pilot Unit with 100% Carbon Capture, Fuel, 2013, 103, 495–505 CrossRef CAS.
- A. Tong, L. Zeng, M. V. Kathe, D. Sridhar and L. S. Fan, Application of the Moving-bed Chemical Looping Process for High Methane Conversion, Energy Fuels, 2013, 27, 4119–4128 CrossRef CAS.
- M. V. Kathe, A. Empfield, J. Na, E. Blair and L. S. Fan, Hydrogen Production from Natural Gas Using an Iron-based Chemical Looping Technology: Thermodynamic Simulations and Process System Analysis, Appl. Energy, 2016, 165, 183–201 CrossRef CAS.
- M. Ishida, K. Takeshita, K. Suzuki and T. Ohba, Application of Fe2O3–Al2O3 Composite Particles as Solid Looping Material of the Chemical-loop Combustor, Energy Fuels, 2005, 19, 2514–2518 CrossRef CAS.
- S. Takenaka, M. Serizawa and K. Otsuka, Formation of Filamentous Carbons Over Supported Fe Catalysts Through Methane Decomposition, J. Catal., 2004, 222, 520–531 CrossRef CAS.
- C. Emmenegger, J. M. Bonard, P. Mauron, P. Sudan, A. Lepora, B. Grobety, A. Züttel and L. Schlapbach, Synthesis of Carbon Nanotubes Over Fe Catalyst on Aluminum and Suggested Growth Mechanism, Carbon, 2003, 41, 539–547 CrossRef CAS.
- Y. Ku, Y. C. Liu, P. C. Chiu, Y. L. Kuo and Y. H. Tseng, Mechanism of Fe2TiO5 as Oxygen Carrier for Chemical Looping Process and Evaluation for Hydrogen Generation, Ceram. Int., 2014, 40, 4599–4605 CrossRef CAS.
- A. Abad, J. Adánez, A. Cuadrat, F. García-Labiano, P. Gayán and L. F. de Diego, Kinetics of Redox Reactions of Ilmenite for Chemical-looping Combustion, Chem. Eng. Sci., 2011, 66, 689–702 CrossRef CAS.
|
This journal is © The Royal Society of Chemistry 2018 |
Click here to see how this site uses Cookies. View our privacy policy here.