DOI:
10.1039/C8RA07359G
(Paper)
RSC Adv., 2018,
8, 34380-34387
Co-production of fully renewable medium chain α-olefins and bio-oil via hydrothermal liquefaction of biomass containing polyhydroxyalkanoic acid
Received
4th September 2018
, Accepted 27th September 2018
First published on 8th October 2018
Abstract
Medium chain-length linear α-olefins (mcl-LAO) are versatile precursors to commodity products such as synthetic lubricants and biodegradable detergents, and have been traditionally produced from ethylene oligomerization and Fischer–Tropsch synthesis. Medium chain-length polyhydroxyalkanoic acid (mcl-PHA) can be produced by some microorganisms as an energy storage. In this study, Pseudomonas putida biomass that contained mcl-PHA was used in HTL at 300 °C for 30 min, and up to 65 mol% of mcl-PHA was converted into mcl-LAO. The yield and quality of the bio-oil co-produced in the HTL was remarkably improved with the biomass rich in mcl-PHA. Experiments with extracted mcl-PHA revealed the degradation mechanism of mcl-PHA in HTL. Overall, this work demonstrates a novel process to co-produce mcl-LAO and bio-oil from renewable biomass.
Introduction
Due to their terminal functionality, linear α-olefins (LAO) are extremely versatile and valuable precursors to produce many commodity chemicals. The short chain (C2–4) LAO can be used as feedstock to produce polyethylene, polypropylene and acrylonitrile. Medium chain-length LAO (mcl-LAO) are of particular interest because they can be used as “drop-in” fuels that are compatible with the existing engine systems and transportation infrastructure.1 mcl-LAO are also widely used as co-monomers (C5–C8) in polymer production, and to produce poly α-olefins (PAO) as base stocks for synthetic lubricants for automotive and industrial applications. Long chain-length LAO can be converted into valuable fatty alcohols to produce biodegradable detergents,2 and environmentally friendly drilling fluid base stocks. The global LAO market size was valued at USD 8.26 billion in 2016 and is expected to grow at a compound annual growth rate (CAGR) of 4.8% for the next 10 years.3
Petroleum derived feedstocks have been traditionally used for LAO production, mainly via Fischer–Tropsch synthesis or catalytic oligomerization of ethylene to produce a mixture of largely linear products of C4–C20+ with even carbon number chain length. The processes require non-renewable resource and are energy intensive. With increasing energy demand and growing concern about carbon emissions, there has been increasing global interest in producing fuels and chemicals through sustainable approaches, such as from renewable biomass.
Hydrothermal liquefaction (HTL) is a thermal process operating under subcritical water environment that converts wet biomass into four phases: an oil phase (bio-oil), a solid phase (biochar), a gas phase (largely CO2), and an aqueous phase (containing substantial amounts of water soluble organics and inorganics). Water is usually the only solvent in this process. HTL bypasses the energy intensive step of drying biomass, simplifies downstream processing and reduces cost. Therefore, HTL has been widely applied in microbial biomass conversion and upgrading.4 Recently, chemical assisted liquefaction has also been employed to produce value-added bio-derived products at high yields.5,6 Here we developed a novel approach to produce renewable mcl-LAO based on the early studies that propylene can be produced from polyhydroxybutyric acid (PHB) as a thermal degradation product, where the hydroxybutyrate units undergo an intramolecular β-elimination to produce crotonic acid, which is then converted into propylene via decarboxylation.7 A recent research also reported propylene production from cyanobacterial biomass rich in PHB via HTL,8 consistent with these thermochemical reactions. We hypothesized that mcl-LAO could be produced from medium chain-length polyhydroxyalkanoic acid (mcl-PHA) via a similar series of reactions. The work described here demonstrates that renewable mcl-LAO can be co-produced with bio-oil in a non-catalytic HTL process from the bacterium Pseudomonas putida biomass rich in mcl-PHA.
Materials and methods
Chemicals
1-Undecene and 1-tridecene were purchased from Alfa Aesar (MA, USA). PHB, benzoic acid, 1-heptene, 1-nonene, benzoic acid and 3-hydroxybutyric acid were purchased from Sigma-Aldrich (MO, USA). Methyl ester of 3-hydroxyoctanoic acid (3-OH C8), 3-hydroxydecanoic acid (3-OH C10), 3-hydroxydodecanoic acid (3-OH C12) and 3-hydoxytetradecanoic acid (3-OH C14) were purchased from Matreya LLC (PA, USA). All solvents and reagents were either of HPLC grade or analytical reagent grade.
Cultivation of Pseudomonas putida
P. putida KT2440 was grown as published by Sun et al.9 The inoculum was grown in a 500 mL shake flask with 100 mL growth medium supplemented with 10 g L−1 glucose, pH 6.8 and incubated in a shaking incubator at 31 °C with 200 rpm. The shake flask medium contained per liter: 4.7 g (NH4)2SO4, 0.8 g MgSO4·7H2O, 12 g Na2HPO4·7H2O, 2.7 g KH2PO4, 10 g glucose and 1 g nutrient broth (DIFCO, USA, 231000). After 12 hours growth the inoculum culture was transferred into a BioFlow 3000 fermenter with 4 L growth media containing 10 g L−1 glucose with initial OD (600 nm) of 0.15. The fermentation medium was similar to shake flask medium except the Na2HPO4 concentration was increased to 18 g L−1, the KH2PO4 concentration was increased to 4.05 g L−1, and the medium was supplemented with 8 mL of trace minerals solution as described by Sun et al.9 The pH was controlled at 6.8 using NH4OH (14%) for first 11 hours to build biomass then it was controlled by KOH (4N) afterwards to induce PHA production. Oxygen was kept at ≥40% saturation using 0.5–1 L min−1 air flow and by variable agitation. At 10 h 3.5 mL of antifoam (Sigma SE 204, 15%) was added to the fermenter to prevent foaming. After 10.5 h fermentation 1.8 L of broth was withdrawn to harvest the first batch of biomass. This volume was replaced with 2 L of fermentation medium without (NH4)2SO4 to continue the fermentation. From 11 h glucose feed (600 g L−1 glucose and 10 g L−1 MgSO4·7H2O) was started at the rate of 5 mL h−1. The feeding rate was increased to 25 mL h−1 at 24 h. The second batch of biomass was harvested at 30 h by withdrawing 2 L of broth, and that volume was replaced with 1 L of fermentation medium without (NH4)2SO4. At 47 h 150 mL of glucose feed was added. At 49 h all the biomass was harvested by centrifuging at 10
000 rpm (Sorvall Lynx 6000). Biomass samples for HTL studies were frozen and stored at −20 °C. Biomass samples for PHA extraction were lyophilized before solvent extraction.
Extraction of mcl-PHA
PHA was extracted from freeze-dried P. putida biomass powder using dichloromethane (DCM) three times (biomass to DCM = 1
:
15, w/v) for 4 hours at room temperature.10 The solution was filtered through a glass fiber filter to remove cell debris. The mcl-PHA resin was obtained by removing solvent using rotary evaporation. Then the resin was dissolved in DCM (resin to DCM = 1
:
10, w/v). The solution was added dropwise into a cold methanol solution (DCM/methanol = 1
:
10, v/v)10,11 and kept at 4 °C for 2 hours. The solvent was decanted to obtain precipitated resin. The residual solvent was removed by evaporation in a vacuum oven at 40 °C overnight.
HTL process
HTL reactors were made with 316 stainless steel with 4 in. length of 1/2 in. O.D. tube with a wall thickness of 0.065 in. A cap is placed on one end, and the other end is fitted with an 18 in. length of 1/8 in. O.D. tube, with a wall thickness of 0.028 in., connected to a high-pressure valve. In a typical experiment 5 mL of biomass slurry (20 wt% DCW) was loaded into a reactor.12 The slurry loading was selected such that 95% of the reactor volume will be occupied by liquid at reaction conditions. The air in the headspace of the reactor was replaced with helium by repeated cycles of evacuation and charging with helium. A 140 psi of helium was remained serving as an internal standard for the quantification of gas yields.
HTL reactions were carried out by placing the reactors vertically in a fluidized sand bath, and the temperature was maintained at 300 °C for 30 min. After the reaction, the reactors were removed from the sand bath and immersed in a cold-water bath for about 30 min to quench the reaction. The reactors were placed in ambient temperature for up to 3 hours to allow the liquid and gas phase to equilibrate. The gas phase was collected into air bags for analysis. The gas bags were directly hooked up to and analyzed by an Agilent 490 micro-GC with Molecular Sieve 5A, PoraPLOT Q, CP-Sil 5CB, and CP-Wax 52CB columns for He, N2, H2, CO, CO2, and C1–C4 hydrocarbons.13
HTL product recovery
The mixture in the reactor was transferred to a separatory funnel and the reactor was rinsed with DCM and DI water to ensure complete transfer. The funnel was shaken vigorously to extract bio-oil into the DCM phase. Then the phases were allowed to separate under gravity. The DCM and aqueous phase were sequentially filtered to remove biochar. The obtained DCM phase was transferred into a 10 mL volumetric flask to make up to 10 mL using DCM. One microliter of DCM phase was injected into a GC for analysis. Then an aliquot of DCM phase was transferred into a pre-weighted tube. The DCM was evaporated under a nitrogen flow for 2 hours. Then the obtained bio-oil was evaporated in a vacuum oven under 40 °C for 2 hours to get a gravimetric yield. An aliquot of aqueous phase was freeze-dried to get the dry weight for aqueous phase yield. The general HTL product recovery scheme is illustrated in Fig. 1.
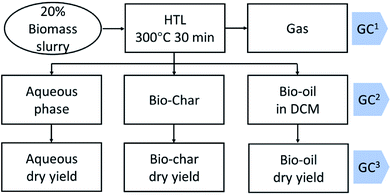 |
| Fig. 1 Small scale HTL experiment setting up (the gas phase was analyzed by GC1; the bio-oil in dichloromethane (DCM) was analyzed by GC2; after DCM evaporation the bio-oil was analyzed by GC3). | |
Compositional analysis of biomass
The composition of biomass was analyzed using protocols described previously.14 Ash content was quantified by burning weighted samples in a muffle furnace.15 Carbohydrate content was quantified by hydrolyzing the biomass with sulfuric acid and analyzing on a Thermo Scientific Dionex ICS 5000 system equipped with pulsed amperometric detection (PAD). Fatty acids were converted into fatty acid methyl esters (FAMEs) and analyzed by gas chromatography-flame ionization detection (GC-FID) on an Agilent 7890. Carbon, hydrogen and nitrogen are determined by an external laboratory (Hazen Labs, Golden, CO) on a Flash EA 1112 Series Elemental Analyzer. The technique is the classical Dumas method, with thermal conductivity detection. The method is described in ASTM D5373 (coal) and ASTM D5291 (petroleum products). Briefly, weighed samples are combusted in oxygen at 1000 °C. The combustion products are swept by a helium carrier gas through combustion catalysts, scrubbers and a reduced copper tube. All gases are then separated on a chromatography column and measured by thermal conductivity detection (TCD) detection. Oxygen was assumed to account for the bulk of the remaining sample mass balance. Higher heating value (HHV; MJ kg−1) was estimated using Dulong's formula.16 |
HHV = 0.3383C + 1.422(H–O/8)
| (1) |
PHA analysis
PHA content was analyzed by a modified methylation derivation method.17 Briefly, 10 mg sample, 1 mg of benzoic acid internal standard and 1 mL of derivatization agent BF3/MeOH were sequentially fed into a silanized glass vial. The vial was sealed and heated at 80 °C for 20 hours. The contents in the vial was transferred into a 10 mL volumetric flask and made up to 10 mL with DCM. Then the solution was transferred into a 20 mL glass vial and mixed with 3 mL of water to wash out acid. The DCM phase was transferred to another vial with anhydrous Na2SO4 and Na2CO3. One microliter of solution was injected into GC for analysis.17
GC analysis
One microliter of sample in DCM was injected into a gas chromatography-flame ionization detection/mass spectra (GC-FID/MS) on an Agilent 7890 A GC equipped with a polyarc (Activated Research Company, MN, USA) FID detector. The inlet temperature was 260 °C. Oven temperature started at 50 °C, hold for 2 min, ramped at 10 °C min−1 to 120 °C, hold for 1 min, ramped at 10 °C min−1 to 220 °C, hold for 1 min, ramped at 25 °C min−1 to 300 °C, and hold for 2 min. The injected compounds were separated by an Agilent HP-5MS column (30 m × 0.25 mm i.d. × 0.25 μm film thickness) and detected by the FID and MS, respectively. Peaks were identified by NIST11 library. Quantification of the compounds was based on a 5-point calibration curve obtained from FID.
Results and discussion
Production of propylene from PHB via HTL
It has been reported that PHB can be converted into propylene under HTL condition.8 We conducted experiments with pure PHB at 300 °C for 30 min in our HTL setting and confirmed the propylene product in the gas phase after the experiment. Up to 43 mol% of hydroxybutyrate units was converted into propylene. Recently, bio-derived propane has garnered increased attention for its potential to reduce greenhouse gas footprint.18 Propane can be produced from propylene via catalytic hydrogenation. We tested for in situ production of propane by conducting HTL of PHB in the presence of hydrogen. In this experiment we purged 750 psi of hydrogen instead of He into the reactor with PHB and performed HTL at 300 °C for 30 min. Propane was indeed detected in the gas phase after the reaction, indicating the feasibility to produce a fully renewable propane by this approach. However, the propane yield was low (1.2 mol%), presumably because there was no catalyst for the hydrogenation and the condition was not optimal for hydrogenation. We think that a higher propane yield can be achieved by applying a hydrogenation catalyst either in the HTL process, or in a sequential downstream upgrading step. Since propylene is a gas under HTL process, the catalyst can be placed in the head space in the reactor to avoid being fouled by other compounds (liquid or solid phase) in the HTL. Alternatively, the propylene can also be easily separated from liquid phase after HTL to be upgraded through a downstream catalytic bed.19,20 Further studies will be needed to test these ideas.
Based on the high propylene yield from PHB in HTL process we hypothesized that mcl-LAO can be produced from mcl-PHA via the similar pathway. mcl-PHA is naturally produced by some microbes and could be a renewable feedstock. Since there is no commercially available mcl-PHA, we decided to produce mcl-PHA using P. putida fermentation.
Production of mcl-PHA using P. putida
P. putida is known for its capacity to accumulate high amounts of mcl-PHA when grown on glucose9 or other carbon sources including lignin17 under nitrogen deplete conditions. Here we fed the P. putida with glucose for biomass production and mcl-PHA accumulation. Biomass was built up in the initial phase of growth by maintaining a high ammonia concentration through the use of NH4OH to control pH. In the second phase of the fermentation, nitrogen was depleted from the medium by replacing NH4OH with KOH for pH control (Fig. 2). Biomass was harvested at three different growth stages (early stage with nitrogen replete condition, middle stage at the beginning of nitrogen depletion, and late stage with nitrogen depleted) and mcl-PHA content was analyzed, confirming that the mcl-PHA content increased by nitrogen depletion strategy (Fig. 2).
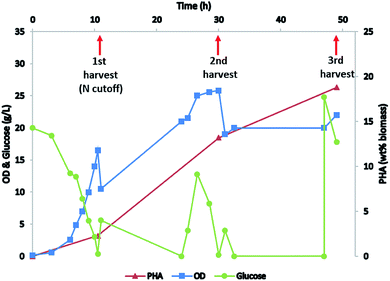 |
| Fig. 2 Cultivation of P. putida to accumulate mcl-PHA. | |
HTL of biomass to co-produce mcl-LAO and bio-oil.
The total PHA in the early stage was 2.3% DCW, and it increased to 18.6% at the end of the fermentation, with 3-hydroxydecanoic acid as the dominant monomer (Table 1). During the fermentation, carbon and hydrogen content increased, while nitrogen content decreased, due to the nitrogen depletion. The total higher heating value (HHV) of the biomass increased from 17.0 to 20.9 indicating an increase in energy content of the biomass with the accumulation of PHA. The total carbohydrate and fatty acid content declined slightly with nitrogen depletion.
Table 1 Summarizes the composition of the biomassa
Harvested biomass |
Total PHA % |
3-OH C8% |
3-OH C10% |
3-OH C12% |
FAME % |
Carbohydrates % |
Ash % |
Nitrogen % |
Carbon % |
Hydrogen % |
Oxygen % |
HHV MJ kg−1 |
3-OH C8: 3-hydroxyoctanoic acid; 3-OH C10: 3-hydroxydecanoic acid; 3-OH C12: 3-hydroxydodecanoic acid. |
1st harvest |
2.3 |
0.0 |
1.5 |
0.8 |
4.1 |
12.7 |
14.0 |
11.1 |
43.0 |
6.6 |
39.3 |
17.0 |
2nd harvest |
13.3 |
3.2 |
8.9 |
1.2 |
2.8 |
13.4 |
10.8 |
7.0 |
45.2 |
6.9 |
40.9 |
17.8 |
3rd harvest |
18.6 |
4.9 |
12.2 |
1.5 |
2.1 |
10.9 |
9.1 |
5.7 |
49.8 |
7.4 |
37.0 |
20.9 |
The 3rd harvest biomass listed in Table 1 was used for HTL to evaluate if mcl-LAO and bio-oil could be co-produced. We followed the classic small scale HTL sample preparation process, in which bio-oil was recovered by DCM rinsing/extraction and solvent evaporation (Fig. 1). An aliquot of bio-oil sample was dissolved in DCM and analyzed by GC (Fig. 1, GC3), but no mcl-LAO was found (Fig. 3, green chromatograph). We speculated that the volatile mcl-LAO products might be lost during DCM evaporation, which is a method that has been routinely applied in the classic small scale HTL sample preparation.4,21 Then, we analyzed the DCM solution before the evaporation (Fig. 1. GC2) and found considerable amounts of volatile compounds (Fig. 3, blue chromatography), confirming our concern that volatile compounds could be lost during solvent evaporation. Thus, solvent evaporation in a small scale HTL study can lead to underestimation of bio-oil yield and failure to identify potentially valuable volatile compounds. In principle, solvent extraction is not necessary at pilot scale or larger, because the produced bio-oil can be separated spontaneously from aqueous phase under gravimetric settling.22 We believe this is a potential issue that has been overlooked for traditional small scale HTL experiments, and that published bio-oil yields may be artifactually low and opportunities for exploitation of volatile products may have been missed by others.
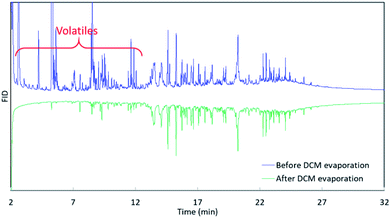 |
| Fig. 3 GC analysis of collected bio-oil before and after solvent evaporation. | |
In this case, we identified and quantified volatile olefin products, such as 1-heptene, 1-nonene and 1-undecene, by analyzing DCM solution before evaporation. These mcl-LAO with odd carbon chain numbers (n − 1) are believed to arise from the Cn 3-hydroxyalkanoic acids units via decarboxylation (Table 2). In contrast to the traditional olefin process, such as ethylene oligomerization, in which only even number LAOs can be produced, LAOs with odd carbon numbers can be produced by PHA degradation. These odd carbon LAOs will not necessarily serve as direct replacements for petrochemical LAOs but their properties may allow the development of novel applications.
Table 2 mcl-LAO yields after HTL of P. putida biomass and extracted PHAa
3-Hydroxyalkanoic acid |
Produced mcl-LAO |
mcl-LAO yield (% of biomass/material) |
1st harvest |
3rd harvest |
Extracted PHA |
Alkene yields are based on the AFDW of starting materials. |
3-Hydroxyoctanoic (C8) |
1-Heptene (C7) |
0.0 |
1.5 |
4.7 |
3-Hydroxydecanoic (C10) |
1-Nonene (C9) |
0.4 |
6.1 |
24.6 |
3-Hydroxydodecanoic (C12) |
1-Undecene (C11) |
0.2 |
0.8 |
2.4 |
Then, we used the 1st harvest biomass (with minimum mcl-PHA) and extracted PHA for HTL under the same conditions and the LAO yields were summarized in Table 2. For the 1st harvest biomass the mcl-LAO yield was very low, corresponding to the low mcl-PHA content (2.3%) in that batch of biomass. The mcl-LAO yield from extracted PHA was the highest among the three experiments. These results support our hypothesis that mcl-PHA can be the precursor for mcl-LAO production.
Besides the production of mcl-LAO, bio-oil, aqueous phase, bio-char and gas were produced via the HTL process. The yields of these fractions were summarized in Table 3. The bio-oil yield was significantly higher for the 3rd harvest biomass that was rich in mcl-PHA, while the yields of non-volatile aqueous phase and char were significantly lower for this biomass, indicating a higher conversion efficiency from biomass to bio-oil. The carbon and nitrogen analysis on the aqueous phase showed that the aqueous phase contained about 50% of the total nitrogen from the starting biomass for both materials. The aqueous phase generated from the 1st harvest biomass and 3rd harvest biomass contained 24% and 15% of the total carbon from the starting materials, respectively. During HTL carbohydrate will generate hydroxymethylfurfural, acetic acid, etc., while protein will be degraded into amino acid, peptides and other derivatives.23 Most of these water-soluble degradation products will end in the aqueous phase.4 Since the carbohydrate and FAME contents for 1st harvest and 3rd harvest were similar (Table 1), the remarkable increase of bio-oil yield in 3rd biomass is very likely due to the presence of mcl-PHA. In the gas phase, the dominant compound was carbon dioxide, with trace amount of hydrogen and methane. The 3rd harvest biomass generated much more carbon dioxide, as expected from decarboxylation of alkenoic acids.
Table 3 HTL results for P. putida biomassa
|
Bio-oil yield% |
Aqueous yield% |
Char yield% |
Gas yield% |
mcl-LAO yield% |
Bio-oil, aqueous phase (non-volatile), gas and alkene yields are based on AFDW. |
1st harvest |
23.4 ± 2.1 |
45.6 ± 4.0 |
10.7 ± 1.5 |
4.8 ± 3.5 |
0.8 ± 0.1 |
3rd harvest |
32.6 ± 1.3 |
28.1 ± 3.5 |
7.4 ± 1.0 |
10.2 ± 1.9 |
8.3 ± 0.2 |
The carbon, hydrogen and nitrogen contents in the obtained bio-oil samples are shown in Table 4. Bio-oil derived from the 3rd harvest biomass contained higher levels of carbon and hydrogen resulting in a higher heating value (HHV), while the nitrogen content was reduced by 31% compared to the 1st harvest. Thus the quantity and quality of bio-oil were both improved by increasing mcl-PHA content in the biomass. HTL has been recognized as a composition-independent process to convert biomass into bio-oil. However, recent studies have demonstrated that the composition of biomass can significantly affect the bio-oil yield and quality.21 Increasing bio-oil yield and quality by tuning up the composition of biomass might be a promising approach to further drive down biofuel cost.
Table 4 Carbon, hydrogen and nitrogen analysis on bio-oil products
Bio-oil samples |
Nitrogen % |
Carbon % |
Hydrogen % |
Oxygen % |
HHV MJ kg−1 |
1st harvest (N replete) |
8.6 |
71.9 |
9.3 |
10.2 |
35.7 |
3rd harvest (N deplete) |
5.9 |
73.6 |
10.0 |
10.5 |
37.3 |
PHA is a promising biopolymer,24 and a feedstock for biofuel production.17 Previously, both processes involve biomass dehydration and solvent extraction of the PHA from the biomass. The extracted PHA in the latter process requires thermal-degradation to produce unsaturated fatty acids (such as decenoic acid), which can be converted into hydrocarbon biofuels via catalytic upgrading.17 However, dehydration of microbial biomass for extraction is energy-intensive,25 extraction requires solvent recycling and can complicate downstream processing, and noble metal catalysts may not be economical for biofuel production. In this experiment, we applied HTL as an alternative approach to integrate downstream processes, demonstrating co-production of bio-oil and mcl-LAO in one step. The produced mcl-LAO can be easily separated from the bio-oil, due to the high volatility of these compounds. Moreover, the yield and quality of bio-oil was remarkably improved with the presence of mcl-PHA in the starting biomass. As such, the production of value-added mcl-LAO in addition to high-quality bio-oil via a simple and integrated pathway could help drive the economics.
GC-MS analysis of bio-oil derived from mcl-PHA rich biomass
Bio-oil produced from HTL process usually consists of many compounds. The result of GC-MS analysis on the bio-oil obtained from 3rd harvest biomass is summarized in Table 5. Alkenes with odd carbon number, such as heptene, nonene, and undecene are the major compounds that can be detected by GC-MS. 3-Decenoic acid, 2-decenoic acid and γ-decalactone could be derived from 3-hydroxydecanoic acid unit in the mcl-PHA, but we were concerned about the complexity of interactions among various compounds in the starting biomass therefore decided to extract PHA from the biomass to get a clearer picture on the fate of the mcl-PHA in the HTL.
Table 5 GC-MS analysis of bio-oil derived from mcl-PHA rich biomass before solvent evaporationa
No. |
RT (min) |
Compound |
M+(m/z) |
Formula |
Relative concentration (area %) |
Only identified compounds are shown in this table. Relative concentration was determined by area of each compounds using a polyarc FID. |
1 |
2.61 |
Heptene |
98 |
C7H14 |
13.4 |
2 |
3.05 |
1,3-Diazine |
80 |
C4H4N2 |
1.1 |
3 |
4.21 |
Methylpyrazine |
94 |
C5H6N2 |
2.1 |
4 |
5.35 |
Nonene |
126 |
C9H18 |
49.1 |
5 |
5.60 |
2,6-Dimethyl pyrazine |
108 |
C6H8N2 |
2.4 |
6 |
7.09 |
2-Ethyl-5-methyl pyrazine |
122 |
C7H10N2 |
0.7 |
7 |
7.57 |
N-Isobutylacetamide |
115 |
C6H13NO |
0.5 |
8 |
8.45 |
1,4-Undecadiene |
152 |
C11H20 |
1.3 |
9 |
8.54 |
Undecene |
156 |
C11H20 |
6.7 |
10 |
9.03 |
(Z)-Cycloundecene |
152 |
C11H20 |
0.8 |
11 |
9.35 |
1-Hexylcyclopentene |
152 |
C11H20 |
0.9 |
12 |
9.52 |
2,9-Undecadiene |
152 |
C11H20 |
0.6 |
13 |
9.83 |
1-Acetylpyrrolidine |
113 |
C6H11NO |
0.6 |
14 |
11.64 |
Cycloundecene |
152 |
C11H20 |
1.0 |
15 |
11.87 |
1-Tridecene |
182 |
C13H26 |
0.9 |
16 |
13.59 |
3-Decenoic acid |
170 |
C10H18O2 |
3.2 |
17 |
14.20 |
trans-2-Decenoic acid |
170 |
C10H18O2 |
3.1 |
18 |
14.62 |
γ-Decalactone |
170 |
C10H18O2 |
2.1 |
19 |
15.26 |
4-Hexylphenol |
178 |
C12H18O |
0.8 |
20 |
15.30 |
N-(2-phenylethyl)acetamide |
163 |
C10H13 |
1.0 |
21 |
16.67 |
Azacyclotridecan-2-one |
197 |
C12H23NO |
0.7 |
22 |
20.26 |
Hexadecanoic acid |
256 |
C16H32O2 |
5.6 |
23 |
22.03 |
Oleic acid |
282 |
C18H34O2 |
0.8 |
24 |
22.28 |
Hexadecanamide |
255 |
C16H33NO |
0.7 |
Thermal degradation of mcl-PHA in HTL
Extracted mcl-PHA resin, water, and deuterated toluene (internal standard) were fed into tube reactors for HTL at 300 °C in a sand bath. The reactors were quenched with ice water at 5, 10, 15 or 30 min, respectively. Then the contents were extracted by DCM into a volumetric flask for GC analysis. Since the 3-hydroxydecanoic acid was the major compound (66%) in the extracted mcl-PHA resin, we tracked the fate of this compound and its derivatives during the process to illustrate the thermal degradation mechanism of mcl-PHA in HTL.
In this HTL process 5 major derivatives that are related to 3-hydroxydecanoic acid were identified and quantified, and they are 1-nonene, nonene isomers (2-nonene, 3-nonene, etc.), 3-decenoic acid, 2-decenoic acid and decalactone. As shown in Fig. 4, the concentration of 2-decenoic acid and 3-decenoic acid decreased, while the yield of 1-nonene, nonene isomers and decalactone increased during the HTL process. A final yield for 1-nonene of 69 mol% was observed at 300 °C after 30 min. The final yield for 3-decenoic acid and 2-decenoic acid was 11 mol% and 18 mol%.
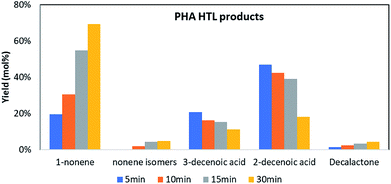 |
| Fig. 4 PHA thermal degradation products in HTL process. | |
Based on a previous report, in which PHB thermal degradation was studied by experimental and density functional theory (DFT) analysis,26 we propose here a similar mcl-PHA thermal degradation pathway (Fig. 5): During the HTL process, the depolymerization of mcl-PHA took place initially by an intramolecular β-elimination to produce 2-decenoic acid, which was then converted into 3-decenoic acid via isomerization, followed by decarboxylation to produce 1-nonene as the final product. Other reaction pathways (such as hydrolysis of mcl-PHA to form 3-hydroxyfatty acid, followed by dehydration of 3-hydroxyfatty acid to produce unsaturated fatty acids) might also take place simultaneously.
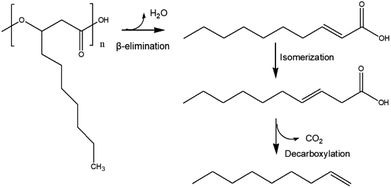 |
| Fig. 5 Proposed mcl-PHA degradation pathway. | |
In this study we have demonstrated that the mcl-PHA can be converted directly into mcl-LAO via HTL, and the residue alkenoic acids can be collected into the bio-oil phase after the HTL. The residue alkenoic acid can be converted into drop-in hydrocarbon biofuel via catalytic upgrading. This study provides a simplified and integrated process that has potential to reduce the cost of biofuel production.
Unlike the HTL bio-oil from other feedstocks, the bio-oil produced from mcl-PHA biomass had a pleasant smell. We believe that the fragrance can be attributed to γ-decalactone and γ-octalactone that were identified in the bio-oil. γ-decalactone is an aroma compound present naturally in many fruits and fermented products. It is particularly important in the formulation of peach, apricot, and strawberry flavors.27 Many synthetic γ-lactones have been utilized as artificial flavors. γ-lactones are also versatile platform molecule that can be used for the production of liquid fuels and chemicals.28,29 γ-lactones can serve as precursors for biopolymers via ring-opening polymerization,30 offering a novel route for renewable biopolymers.31 γ-lactone products have been produced from microbial processes,32,33 but the low productivity remains a hurdle to overcome. This research provides an alternative approach to produce γ-lactone from biomass via a scalable thermal chemical pathway.
Besides these major compounds, other derivatives such as dienes, alcohols and aldehydes were also detected after the HTL of mcl-PHA (data not shown), indicating other unknown reaction mechanisms. The thermal degradation of mcl-PHA in HTL process comprises of a series of complex pathways, which might be able to be controlled by catalysts and reaction kinetics to produce preferred chemicals.
Conclusions
In this study we have demonstrated co-production of mcl-LAO and bio-oil from biomass via non-catalytic HTL. Up to 65 mol% of mcl-PHA was converted into mcl-LAO. Co-products and reaction intermediates such as unsaturated fatty acids, olefin isomers and lactones, were also identified. This process represents a simpler and more energy efficient route to produce mcl-LAO, and possibly also long chain LAO from corresponding PHA in biomass, and could contribute to lower cost biofuels.
Conflicts of interest
There are no conflicts to declare.
Acknowledgements
We would like to thank Ali Mohagheghi and Ryan Spiller for P. putida fermentation; Kellene McKinney, Stuart Black, William Michener, Susan Habas and Stefanie Van Wychen for technical assistance; Ron Chance and Bo Wang for valuable discussions. This work was authored by Alliance for Sustainable Energy, LLC, the manager and operator of the National Renewable Energy Laboratory for the U.S. Department of Energy (DOE) under Contract No. DE-AC36-08-GO28308. Funding provided by US Department of Energy, BioEnergy Technologies Office. The views expressed in the article do not necessarily represent the views of the DOE or the U.S. Government. The U.S. Government retains and the publisher, by accepting the article for publication, acknowledges that the U.S. Government retains a nonexclusive, paid-up, irrevocable, worldwide license to publish or reproduce the published form of this work, or allow others to do so, for U.S. Government purposes.
Notes and references
- R. M. Lennen and B. F. Pfleger, Curr. Opin. Biotechnol., 2013, 24, 1044–1053 CrossRef CAS PubMed.
- M. E. Dry, Catal. Today, 2002, 71, 227–241 CrossRef CAS.
- Grand View Research, Alpha Olefin Market Analysis By Product, (1-Butene, 1-Hexene, 1-Octene, 1-Decene, 1-Dodecene), By Application (Polyethylene, Detergent Alcohol, Synthetic Lubricants), By Region, And Segment Forecasts, 2018 – 2025, https://www.grandviewresearch.com/industry-analysis/alpha-olefins-market.
- C. Miao, M. Chakraborty, T. Dong, X. Yu, Z. Chi and S. Chen, Bioresour. Technol., 2014, 164, 106–112 CrossRef CAS PubMed.
- Y. Pierson, X. Chen, F. D. Bobbink, J. Zhang and N. Yan, ACS Sustainable Chem. Eng., 2014, 2, 2081–2089 CrossRef CAS.
- J. Zhang and N. Yan, Green Chem., 2016, 18, 5050–5058 RSC.
- J. M. Clark, M. R. Nimlos and D. J. Robichaud, J. Phys. Chem. A, 2015, 119, 501–516 CrossRef CAS PubMed.
- J. Wagner, R. Bransgrove, T. A. Beacham, M. J. Allen, K. Meixner, B. Drosg, V. P. Ting and C. J. Chuck, Bioresour. Technol., 2016, 207, 166–174 CrossRef CAS PubMed.
- Z. Sun, J. A. Ramsay, M. Guay and B. A. Ramsay, Appl. Microbiol. Biotechnol., 2006, 71, 423–431 CrossRef CAS PubMed.
- B. Wampfler, T. Ramsauer, S. Rezzonico, R. Hischier, R. Köhling, L. Thöny-Meyer and M. Zinn, Biomacromolecules, 2010, 11, 2716–2723 CrossRef CAS PubMed.
- G. N. Huijberts, G. Eggink, P. de Waard, G. W. Huisman and B. Witholt, Appl. Environ. Microbiol., 1992, 58, 536–544 CAS.
- P. Duan and P. E. Savage, Ind. Eng. Chem. Res., 2011, 52–61 CrossRef CAS.
- K. Iisa, R. J. French, K. A. Orton, A. Dutta and J. A. Schaidle, Fuel, 2017, 207, 413–422 CrossRef CAS.
- T. Dong, E. P. Knoshaug, R. Davis, L. M. L. Laurens, S. Van Wychen, P. T. Pienkos and N. Nagle, Algal Res., 2015, 19, 316–323 CrossRef.
- S. Van Wychen and L. M. L. Laurens, Determination of Total Solids and Ash in Algal Biomas – Laboratory Analytical Procedure (LAP), Golden, CO, 2013 Search PubMed.
- P. Biller and a. B. Ross, Bioresour. Technol., 2011, 102, 215–225 CrossRef CAS PubMed.
- J. G. Linger, D. R. Vardon, M. T. Guarnieri, E. M. Karp, G. B. Hunsinger, M. A. Franden, C. W. Johnson, G. Chupka, T. J. Strathmann, P. T. Pienkos and G. T. Beckham, Proc. Natl. Acad. Sci. U. S. A., 2014, 111, 12013–12018 CrossRef CAS PubMed.
- E. Johnson, Biofuels, Bioprod. Biorefin., 2017, 11, 887–896 CrossRef CAS.
- A. M. Argo, J. F. Odzak, F. S. Lai and B. C. Gates, Nature, 2002, 415, 623–626 CrossRef CAS PubMed.
- J. Camacho-bunquin, P. Aich, M. Ferrandon, A. Bean, U. Das, F. Dogan, L. A. Curtiss, J. T. Miller, C. L. Marshall, A. S. Hock and P. C. Stair, J. Catal., 2017, 345, 170–182 CrossRef CAS.
- S. Leow, J. R. Witter, D. R. Vardon, B. K. Sharma, J. S. Guest and T. J. Strathmann, Green Chem., 2015, 17, 3584–3599 RSC.
- D. C. Elliott, T. R. Hart, A. J. Schmidt, G. G. Neuenschwander, L. J. Rotness, M. V. Olarte, A. H. Zacher, K. O. Albrecht, R. T. Hallen and J. E. Holladay, Algal Res., 2013, 2, 445–454 CrossRef.
- A. Teymouri, K. J. Adams, T. Dong and S. Kumar, Fuel, 2018, 224, 23–31 CrossRef CAS.
- J. Choi and S. Y. Lee, Appl. Microbiol. Biotechnol., 1999, 51, 13–21 CrossRef CAS.
- T. Dong, E. P. Knoshaug, P. T. Pienkos and L. M. L. Laurens, Appl. Energy, 2016, 177, 879–895 CrossRef CAS.
- J. M. Clark, H. M. Pilath, A. Mittal, W. E. Michener, D. J. Robichaud and D. K. Johnson, J. Phys. Chem. A, 2016, 120, 332–345 CrossRef CAS PubMed.
- J. An, Y. Joo and D. Oh, Appl. Environ. Microbiol., 2013, 79, 2636–2641 CrossRef CAS PubMed.
- X. Tang, X. Zeng, Z. Li, L. Hu, Y. Sun and S. Liu, Renewable Sustainable Energy Rev., 2014, 40, 608–620 CrossRef CAS.
- D. Wang, S. H. Hakim, D. M. Alonso and J. A. Dumesic, Chem. Commun., 2013, 49, 7040–7042 RSC.
- M. Chalid, H. J. Heeres and A. A. Broekhuis, J. Appl. Polym. Sci., 2011, 123, 3556–3564 CrossRef.
- M. Hong and E. Y. Chen, Nat. Chem., 2016, 8, 42–49 CrossRef CAS PubMed.
- G. Feron, L. Dufosse, E. V. A. Pierard, P. Bonnarme, J. L. E. Quere, H. Spinnler and L. De Recherches, Appl. Environ. Microbiol., 1996, 62, 2826–2831 CAS.
- M. Mota and J. A. Teixeira, Biotechnol. Lett., 2005, 1617–1621 Search PubMed.
|
This journal is © The Royal Society of Chemistry 2018 |
Click here to see how this site uses Cookies. View our privacy policy here.