DOI:
10.1039/C8RA05947K
(Paper)
RSC Adv., 2018,
8, 30860-30867
Potassium iodide–polyethylene glycol catalyzed cycloaddition reaction of epoxidized soybean oil fatty acid methyl esters with CO2†
Received
12th July 2018
, Accepted 17th August 2018
First published on 3rd September 2018
Abstract
Nowadays, the clean production of bio-based products and fixation of carbon dioxide (CO2) are highly desirable. In this work, carbonated fatty acid methyl esters have been successfully prepared in 99% yield by cycloaddition of CO2 with bio-based epoxidized methyl soyates. This was accomplished with a simple and cheap catalyst system of polyethylene glycol 400 (PEG-400) and potassium iodide (KI) under solvent-free conditions. Experimental parameters such as the molar ratio of polyethylene glycol to metal halide, catalyst loading, reaction temperature, reaction time and CO2 pressure were systematically evaluated. The PEG-400 and KI co-catalysts (4 mol%) could significantly promote the cycloaddition of CO2 with internal epoxides (epoxidized methyl soyates) to produce carbonated fatty acid methyl esters. FT-IR and NMR analyses were used to confirm the product, and 99% yield of the five-membered cyclic carbonated methyl soyates was obtained at 120 °C with 3.0 MPa pressure of CO2 for 20 h. This method provides a cleaner approach for the production of bio-based products.
1. Introduction
Carbon dioxide (CO2) is a major component of greenhouse gases and is produced by the combustion of fossil fuels, the fermentation of sugar and the respiration of all living organisms.1 Moreover, CO2 is considered as an abundant, low-cost, non-toxic and renewable C1 resource. Therefore, the applications of CO2 have rapidly become a subject of interest in the academic and industrial sectors.2 In the past two decades, the utilization of CO2 transformation has mainly focused on the following areas: (a) reacting with hydrogen to produce methanol, hydrocarbons and their derivatives,3–5 (b) reacting with ammonia to form urea,6 (c) cycloaddition with epoxides to form carbonates or polycarbonates.7,8
In recent years, the cycloaddition reaction of CO2 has become one of the hot fields in catalysis (e.g. heterogeneous catalysts)9–11 for its production of value-added organic chemicals (e.g. cyclic carbonates) from the renewable C1 building block. Cyclic carbonates are one of the special fine chemical products. Because of their advantages of high boiling points, excellent biodegradability and solubility, cyclic carbonates can be widely used as one of the main raw material for polycarbonates12 and in other plastic industries such as non-isocyanate polyurethanes.13 Five-membered cyclic carbonates, as a member of the cyclic carbonates, are often used as electrolyte solvents in lithium-ion batteries,14 plasticizers,15 environment friendly aprotic polar organic solvents,16 fuel additives,17 starting materials and intermediates in the manufacture of fine chemicals.18
The cycloaddition reaction of CO2 to epoxides depends on the type of catalyst used. Therefore, the biggest challenge is the development of efficient catalysts to promote the cycloaddition reaction under moderate reaction conditions. Over the past decades, a lot of researchers have focused on the development of efficient homogeneous catalysts19 and heterogeneous catalysts (e.g. metal–organic frameworks)10 for these reactions. Due to their high catalytic activity, homogeneous catalysts, such as quaternary ammonium salts (e.g. TBAB),20,21 metal complexes,22 ionic liquids,23 organocatalysts24 and crown ether complexes25 have received significant attention. However, it is still very desirable to explore simple and efficient catalyst systems for this important transformation.
Polyethylene glycols (PEGs) are well known as inexpensive, thermally stable, toxicologically innocuous, environmentally benign media to chemical, pharmaceutical and food industries,26 and are commercially available on large scales for economical prices. In particular, they are also used as phase transfer catalysts (PTC) in some cases and reports indicate that CO2 can weakly interact with ether linkage of PEGs, which leads to the improvement of CO2 adsorption rates.27 Furthermore, the hydroxyl moieties of PEGs should benefit the cyclic-carbonate formation by substrate activation through hydrogen bonding.28 Metal halides (e.g. ZnBr2) are also effective catalysts for catalytic cycloaddition reaction of epoxides and CO2. However, there is virtually no catalytic activity when only these metal halides are used. Therefore, coordination of additives or phase transfer catalysts is usually required.29–34
In line with the development of green and sustainable chemistry, it is of great importance to prepare value-added products from bio-based epoxides.35,36 Carbonated methyl soyates (CMS), which were prepared through the cycloaddition of CO2 with epoxidized soybean oil fatty acid methyl esters, represent a useful and sustainable chemical intermediate. Soybean oil fatty acid methyl esters (methyl soyate) are one of the typical vegetable oil fatty acid methyl esters prepared from soybean oil. Due to the steric hindrance of the epoxide groups in methyl soyate, efficient catalysts for the preparation of carbonated methyl soyates are limited.24,30,37 In the present work, we explored the catalytic performance of cheap and green PEGs and KI for cycloaddition of CO2 with epoxidized methyl soyates (EMS) to produce carbonated methyl soyates (CMS) (Scheme 1). Particularly, the role of PEGs in this cycloaddition reaction was investigated. The CMS product was identified by both FT-IR and NMR analysis.
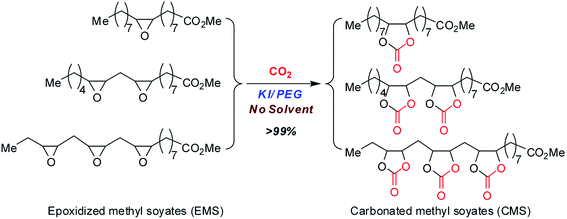 |
| Scheme 1 Cycloaddition of CO2 with EMS. | |
2. Results and discussion
2.1. Catalyst screening for the carbonation of EMS
PEG-400-embedded-KBr (i.e. [K+{PEG}Br−]) has been reported as an efficient catalyst for the cycloaddition of terminal epoxides (e.g. styrene oxide) with CO2, and [K+{PEG}Br−] exhibited higher efficiency than the mixture of PEG-400 and KBr in the study.29 Considering the simple preparation, low cost and sustainability of this catalyst, we embarked our investigation on the cycloaddition of EMS with CO2 using [K+{PEG}Br−] as the catalyst (Scheme 2). We conducted the cycloaddition of EMS with CO2 (10 atm) at 120 °C. However, the results indicated that no carbonation of EMS occurred in the presence of [K+{PEG}Br−]. This may be because [K+{PEG}Br−] is not suitable for substrates with larger steric hindrance (e.g. EMS). Herein, we revisited the combination of PEG and metal halides to develop an efficient cycloaddition catalyst system for the bio-based EMS.
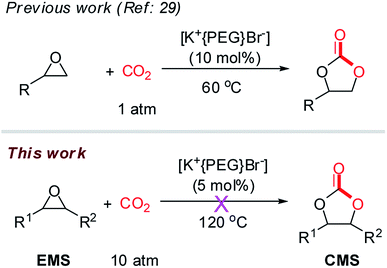 |
| Scheme 2 Cycloaddition catalyzed by [K+{PEG}Br−] complex. | |
The reaction conditions for the initial screening were as follows: 120 °C, 1.0 MPa pressure of CO2, reaction time of 18 h under solvent-free condition (Table 1). It is noteworthy that no cycloaddition product was observed using only KI as the metal halide (Table 1, entry 1). Poly(ethylene glycol)s (PEGs) are of particular interest because their properties can be tuned by their size and their large-scale commercial availability at low costs.30 PEG can be used as phase transfer catalysts (PTC) and green solvent in most cases.38 In general, when the commonly used potassium iodide (KI) in combination with PTC (1
:
1, mol mol−1) was used as the co-catalyst system for the cycloaddition reaction of EMS, the yields of CMS significantly improved with the increase in molecular weight of the PEGs (Table 1, entries 2–11). When ethylene glycol or triethylene glycol (MW = 150) were used as the PTC (Table 1, entries 2 and 3), the yields of CMSs were less than 5% and 10%, respectively. Cycloaddition using tetraethylene glycol (MW = 194) or PEG-200 as the PTC resulted in CMS yields of 52% and 55%, respectively (Table 1, entries 4 and 5). Subsequently, the yields of CMSs increased (74–79%) with larger molecular weight PEGs (PEG-400, PEG-600, PEG-800, PEG-1000, PEG-2000 and PEG-4000) (Table 1, entries 6–11). This is probably because the solubility of these PEGs is not limited with the substrates at the reaction temperature of 120 °C.
Table 1 Catalyst screening for the carbonation of EMSa
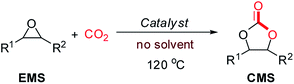
|
Entry |
Metal salt |
PTC |
Yield (%) |
Reaction conditions: reaction temperature: 120 °C; reaction time: 18 h; CO2 pressure: 1.0 MPa; stirring speed: 400 rpm; catalyst loading: 5 mol%; PTC concentration: 5 mol%; EMS: 5.0 g. |
1 |
KI |
— |
0 |
2 |
KI |
Ethylene glycol |
<5 |
3 |
KI |
Triethylene glycol |
10 |
4 |
KI |
Tetraethylene glycol |
52 |
5 |
KI |
PEG-200 |
55 |
6 |
KI |
PEG-400 |
79 |
7 |
KI |
PEG-600 |
78 |
8 |
KI |
PEG-800 |
78 |
9 |
KI |
PEG-1000 |
74 |
10 |
KI |
PEG-2000 |
74 |
11 |
KI |
PEG-4000 |
78 |
12 |
NaI |
PEG-400 |
65 |
13 |
CaI2 |
PEG-400 |
0 |
14 |
ZnI2 |
PEG-400 |
0 |
15 |
KBr |
PEG-400 |
0 |
For comparison, we also explored the cycloaddition reaction of EMSs and CO2 catalyzed by other metal iodides (e.g. NaI, CaI2) (Table 1, entries 12–14). The yield of CMSs catalyzed by sodium iodide (NaI) in cooperation with PEG-400 was 65%. However, NaI was less attractive due to the low catalytic activity compared with that of KI. Calcium iodide (CaI2) or zinc iodide (ZnI2) showed no activity for this reaction under the same reaction conditions (120 °C, 1.0 MPa pressure of CO2) in combination with PEG-400. This might be due to the higher dissociation energy needed by CaI2 and ZnI2 to form Ca2+, Zn2+ and I−,39 in this case. Finally, the combination of potassium bromide (KBr) and PEG-400 for the cycloaddition reaction of EMS and CO2 was investigated (Table 1, entry 15). The results showed that KBr had no activity for this cycloaddition reaction similar to the [K+{PEG}Br−] complex (Scheme 2). Considering PEG-400 as the most commonly used PEG, KI in cooperation with PEG-400 was selected as the optimum catalyst system to explore the cycloaddition reaction of EMS with CO2 in the following experiments.
2.2. Effect of the molar ratio of KI to PEG-400
In the catalyst screening experiments, the amount of metal halide and PTC were both 5 mol%. We hypothesized that the molar ratio of metal halide (e.g. KI) to PTC had an impact on the cycloaddition reaction of EMS and CO2 to prepare CMS. Therefore, the effect of molar ratio of KI to PEG-400 (5
:
1, 5
:
3, 5
:
5, 5
:
8 and 5
:
10) on the cycloaddition reaction of EMS with CO2 was investigated (Fig. 1).
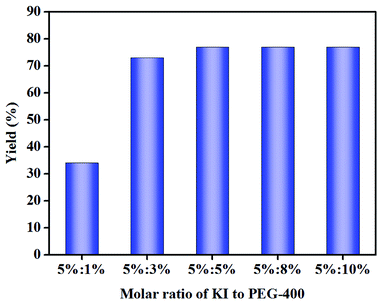 |
| Fig. 1 The effect of molar ratio of KI to PEG-400 on cycloaddition reaction. (Reaction conditions: reaction temperature: 120 °C; CO2 pressure: 1.0 MPa; reaction time: 18 h; stirring speed: 400 rpm; EMS: 5.0 g.) | |
Yields of CMS increased as the molar amount of PEG-400 increased from 1 mol% to 5 mol%, producing CMS in 79% yield. Subsequently, the molar amount of PEG-400 was increased to 8–10 mol% in order to investigate the PTC effect, and it was observed that the yield of CMS remained constant. We proposed that one molecule of KI salt reacts with one unit of PEG-400 in situ to afford the [K+{PEG}I−] complex (Scheme 3),29 which may act as the true catalyst for such a cycloaddition reaction. On the other hand, PEG-400 can coordinate with the K+ from KI, which reduces the interaction between K+ and I− to increase the nucleophilicity of I−, thus enhancing the catalytic activity of KI. It can be seen that the highest yield was achieved for the molar ratio of KI to PEG-400 of 1
:
1. Therefore, the combination of KI/PEG-400 (1
:
1, mol mol−1) was selected for the following optimization experiments.
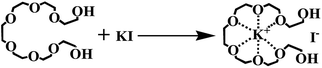 |
| Scheme 3 Proposed formation of [K+{PEG}I−] complex. | |
2.3. Effect of other reaction parameters on the yield of CMS
The effect of other reaction parameters (e.g. catalyst concentration, reaction temperature, reaction time and CO2 pressure) on the yield of CMS were systematically investigated (Fig. 2). The catalyst concentration is one of the most important factors affecting the yield of CMS. Therefore, a suitable concentration of the catalyst is required. A set of experiments on the catalyst concentration were performed and the results are shown in Fig. 2a. The results indicate that the yields of CMS increased with the increase in catalyst concentration and a high yield of CMS (85%) was obtained at 8 mol% KI/PEG-400. Increasing the catalyst concentration further (10 mol%) led to an almost constant yield under the used reaction conditions. Therefore, the optimum catalyst concentration of 8 mol% was used in the following experiments.
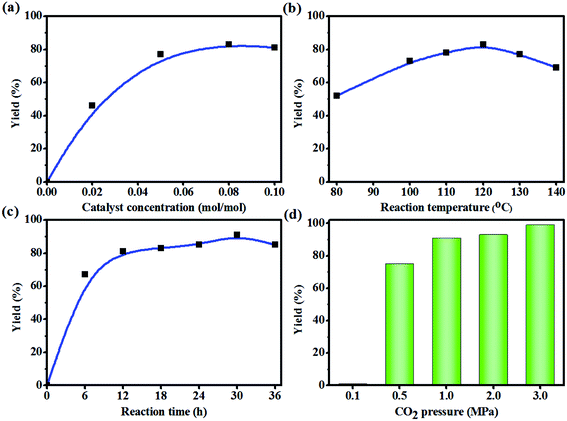 |
| Fig. 2 Effects of (a) catalyst concentration, (b) reaction temperature, (c) reaction time, (d) CO2 pressure on the yield of CMS. (Reaction conditions: (a) 120 °C, 1.0 MPa, 18 h; (b) catalyst concentration 8 mol%, 1.0 MPa, 18 h; (c) catalyst concentration 8 mol%, 120 °C, 1.0 MPa; (d) catalyst concentration 8 mol%, 120 °C, 30 h.) | |
The reaction temperature is another important parameter that affects the cycloaddition reaction. The oxirane groups are located in the middle of the molecular chain of the EMS, which results in a larger steric hindrance. So a relatively higher reaction temperature was employed. Experiments were conducted at different temperatures (80–140 °C) to investigate the effect of temperature on the yield of CMS (Fig. 2b). It is evident that the yield of CMS increased with the increase in temperature (80–120 °C). However, higher temperatures (>130 °C) led to possible side-reactions, such as epoxy ring opening reaction. Therefore, an operating temperature of 120 °C was selected for the subsequent investigations.
Fig. 2c displays the influence of reaction time on the CMS yield. It was noted that the CMS yield increased with prolongation of the reaction time. In detail, the CMS yields increased rapidly with the increase in reaction time until it reached 12 h. With further prolonging the reaction time, the yields of carbonated methyl soyates increased slowly and reached a maximum (91%) with a reaction time of 30 h. This phenomenon was probably due to the increased steric hindrance caused by the formation of cyclic carbonate groups from two or three oxirane groups located in the same molecular chain (Scheme 4). Besides, the absorption rate of CO2 increased in the following order: carbonated vegetable oils < epoxidized vegetable oils.40 In other words, the concentration of CO2 in the reaction system declined rapidly with increasing yields of CMS. Thus, 30 h was selected as the optimal reaction time.
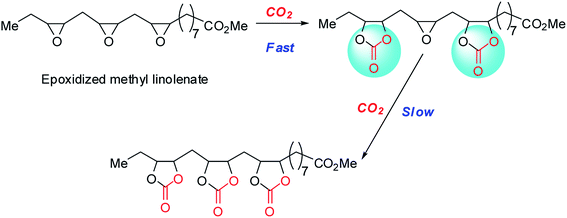 |
| Scheme 4 Stepwise reaction for the carbonation of epoxidized methyl linolenate. | |
In terms of gas–liquid two-phase reactions, the CO2 pressure also plays an important role on the cycloaddition reaction. As shown in Fig. 2d, the CMS yields were significantly affected by CO2 pressure. Notably, nearly no reaction was detected under 0.1 MPa CO2 pressure. The CMS yields increased when the pressure of CO2 increased from 0.1 MPa to 3.0 MPa. In general, the yields of the cycloaddition reaction were increased with increase in CO2 pressure. The reason for this phenomenon may be that EMS contains about 6% of epoxidized methyl linolenate, and the cycloaddition of epoxidized methyl linolenate with CO2 is challenging due to the three epoxides groups incorporated on the same backbone (Scheme 4). In addition, the solubility of CO2 in CMS is lower than that in the starting material, i.e. EMS. Therefore, 3.0 MPa was chosen as the optimum pressure of CO2 and the yield of CMS reached 99%.
2.4. Reaction mechanism
Both the mixture of KBr and PEG (Table 1, entry 15) and the [K+{PEG}Br−] complex (Scheme 2) showed no catalytic activity for this cycloaddition reaction. Therefore, we could conclude that iodide anion (I−) in the metal halides (e.g. KI) is crucial for the cycloaddition reaction of EMS with CO2. Also, we propose that the KI salt reacted with PEG-400 in situ to afford the [K+{PEG}I−] complex, which could act as the true catalyst for such cycloaddition reactions (Scheme 5). Based on the procedure described by Kumar et al.,29 [K+{PEG}I−] was prepared as a yellow viscous oil, which was identified by UV-spectra (Fig. S1, ESI†). As the complex [K+{PEG}I−] was formed, the absorbance peak of the host (PEG-400) at 235 nm gradually reduced and a clear absorbance peak was observed at 265 nm. [K+{PEG}I−] was then used as the catalyst in the cycloaddition reaction (Table 2). To our surprise, using PEG-400-embedded-KI (i.e. [K+{PEG}I−]) as the catalyst in the cycloaddition reaction produced only 44% yield of CMS (Table 2, entry 2), which indicates that the [K+{PEG}I−] complex shows less efficiency than the combination of KI and PEG-400. The combination of [K+{PEG}I−] and PEG-400 still showed less efficiency in the cycloaddition reaction (Table 2, entries 3 and 4). To our delight, good yields of CMSs (77–81%) were obtained when the combination of [K+{PEG}I−] (5 mol%) and KI (3–5 mol%) was used as the catalyst (Table 2, entries 5 and 6). Undoubtedly, free KI was crucial for this cycloaddition reaction involving epoxidized methyl soyates (EMS) as the internal epoxides. The larger molecule [K+{PEG}I−] might have hampered the nucleophilic attack between an iodide anion (I−) and the internal epoxides with larger steric hindrance (EMS) (Scheme 5). In fact, some insoluble white powder (KI) was observed after the cycloaddition reaction using KI and PEG-400 as the co-catalyst (KI/PEG-400) (Fig. S2 in ESI†). In the UV-vis spectra of KI/PEG mixtures, the absorbance peaks of the complex [K+{PEG}I−] (at 235 nm) and KI (at 360 nm) were both observed (Fig. S3 in ESI†). Therefore, the in situ generation of PEG-400-embedded-KI (i.e. [K+{PEG}I−]) as the sole catalyst in the cycloaddition reaction was ruled out.
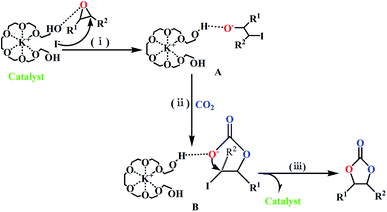 |
| Scheme 5 Proposed mechanism through the generation of [K+{PEG}I−]. | |
Table 2 Control experiments for the carbonation of EMSa
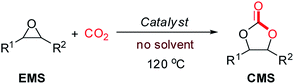
|
Entry |
Catalyst |
Yield (%) |
Reaction conditions were the same as Table 1 (120 °C, 18 h, CO2 1.0 MPa, EMS: 5.0 g). |
1 |
KI (5 mol%)/PEG-400 (5 mol%) |
80 |
2 |
[K+{PEG}I−] (5 mol%) |
44 |
3 |
[K+{PEG}I−] (5 mol%)/PEG-400 (3 mol%) |
44 |
4 |
[K+{PEG}I−] (5 mol%)/PEG-400 (5 mol%) |
44 |
5 |
[K+{PEG}I−] (5 mol%)/KI (3 mol%) |
77 |
6 |
[K+{PEG}I−] (5 mol%)/KI (5 mol%) |
81 |
2.5. Carbonation at the CO2 pressure of 3.0 MPa
It was found in above experiments that the yield of CMS reached 99% under the following conditions: catalyst concentration of 8 mol%, reaction time of 30 h at 120 °C with CO2 pressure of 3.0 MPa. Thus the CO2 pressure has a significant effect on the CMS yield, and a higher CO2 pressure would increase the reaction rate of the substrate with steric hindrance, which may decrease the catalyst loading or reaction time. Because of this, the influence of catalyst concentration and reaction times on the yield of CMS under 3.0 MPa CO2 pressure was explored (Table 3). The yield of CMS changed with the decrease in the catalyst concentration (Table 3, entries 1–3). It can be seen that a 99% yield of CMS could be obtained when the amount of catalyst (KI/PEG-400) was 4 mol%, under CO2 pressure of 3.0 MPa and with a reaction time of 30 h. Subsequently, the reaction time was also optimized (Table 3, entries 4 and 5). The experimental results proved that the reaction time could be shortened to 20 h without affecting the outcome. However, using a significantly shorter reaction time (10 h) led to a lower yield (85%). Therefore, 99% yield of CMS could be obtained in the presence of 4 mol% catalyst (KI/PEG-400) with a 3.0 MPa CO2 pressure and a reaction time of 20 h.
Table 3 Optimization at the CO2 pressure of 3.0 MPaa
Entry |
Catalyst concentration (mol%) |
Time (h) |
Yield (%) |
Reaction conditions: reaction temperature: 120 °C, CO2 pressure: 3.0 MPa. |
1 |
8 |
30 |
99 |
2 |
4 |
30 |
99 |
3 |
2 |
30 |
93 |
4 |
4 |
20 |
99 |
5 |
4 |
10 |
85 |
6 |
3 |
20 |
93 |
2.6. Characterization of carbonation product
The structural features of the product of CMS were characterized by FT-IR, 1H-NMR and 13C-NMR. First, we could clearly observe that the substrate before and after the cycloaddition reaction changed based on the FT-IR spectroscopy analysis (Fig. 3). The FT-IR spectra clearly showed the generation of a new bond at 1801 cm−1 (C
O stretching), associated with the five-membered cyclic carbonate formation, which was different from the original carbonyl bond of the epoxidized methyl soyate backbone at 1730 cm−1 (C
O stretching). The carbonyl groups (1730 cm−1) of the ester bond present in both the raw material (EMS) and the final product (CMS) showed no change.
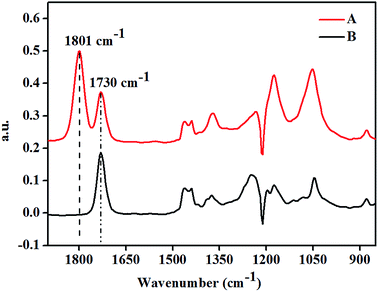 |
| Fig. 3 FT-IR spectra after (A) and before (B) the cycloaddition reaction. | |
Subsequently, 1H-NMR was utilized to further determine the cycloaddition reaction of EMS with CO2. The 1H-NMR spectra of the starting material-EMS and CMS clearly indicate the occurrence of the cycloaddition reaction of EMS with CO2, which is shown in Fig. 4. The 1H-NMR signals of the epoxide moiety (2.85–3.15 ppm) disappeared, while new 1H-NMR signals associated with the carbonate moiety emerged between 4.20–4.95 ppm.
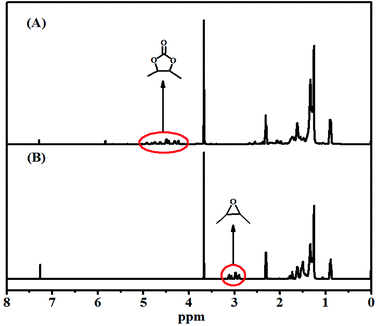 |
| Fig. 4 1H-NMR spectra after (A) and before (B) the cycloaddition reaction. | |
Finally, the cycloaddition product was also identified by 13C-NMR spectroscopy (Fig. 5). The 13C-NMR spectra was obtained for CMS under the following reaction conditions: reaction temperature of 120 °C, catalyst concentration of 4 mol%, 3.0 MPa pressure of CO2 and reaction time of 20 h. A new peak appeared at 154 ppm, which was associated with the carbonate moiety in the five-membered cyclic group in the final product (CMS).
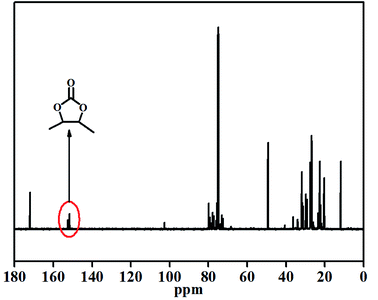 |
| Fig. 5 13C-NMR spectra of carbonated methyl soyates (CMS). | |
3. Conclusions
In this work, bio-based carbonated methyl soyates (CMS) were prepared by the cycloaddition of CO2 with epoxidized methyl soyates in excellent yield using green and cheap polyethylene glycol 400 (PEG-400) and potassium iodide (KI) as co-catalyst system (4 mol%) at 120 °C and 3.0 MPa pressure of CO2 for 20 h. PEG-400 possesses the characteristics of being environment friendly, cheap, green, able to capture CO2 and biodegradable compared to those of the other phase transfer catalysts (PTC). The effect of the catalyst system on cycloaddition reaction of epoxidized methyl soyates and CO2 was explored systematically, which demonstrated that the use of PEG-400 and KI could significantly promote the cycloaddition reaction of CO2 with epoxidized methyl soyates, and the yield of carbonated methyl soyates (CMS) was up to 99%. In addition, the combination of PEG-400 and KI will provide a potential method to catalyze the cycloaddition reaction of CO2 and internal epoxides with larger steric hindrance to produce five-membered cyclic carbonated compounds without any solvents.
Conflicts of interest
The authors declare no competing financial interest.
Acknowledgements
This work was supported by the China Postdoctoral Science Foundation funded project (No. 2017M622364, 2018T110730), the Henan Postdoctoral Science Foundation and Project of Henan University of Technology Excellent Young Teachers (No. 2014003).
References
- Q. Liu, L. P. Wu, R. Jackstell and M. Beller, Using carbon dioxide as a building block in organic synthesis, Nat. Commun., 2015, 6, 5933 CrossRef PubMed.
- J. Klankermayer and W. Leitner, Love at second sight for CO2 and H2 in organic synthesis, Science, 2015, 350, 629–630 CrossRef PubMed.
- X. Z. Lim, How to make the most of carbon dioxide, Nature, 2015, 526, 628–630 CrossRef PubMed.
- M. F. Kuehnel, D. W. Wakerley, K. L. Orchard and E. Reisner, Photocatalytic formic acid conversion on CdS nanocrystals with controllable selectivity for H2 or CO, Angew. Chem., Int. Ed., 2015, 54, 9627–9631 CrossRef PubMed.
- S. Moret, P. J. Dyson and G. Laurenczy, Direct synthesis of formic acid from carbon dioxide by hydrogenation in acidic media, Nat. Commun., 2014, 5, 4017 CrossRef PubMed.
- M. Marchegiani, M. Nodari, F. Tansini, C. Massera, R. Mancuso, B. Gabriele, M. Costa and N. Della Ca, Urea derivatives from carbon dioxide and amines by guanidine catalysis: easy access to imidazolidin-2-ones under solvent-free conditions, J. CO2 Util., 2017, 21, 553–561 CrossRef.
- Y. Liu, W. M. Ren, W. P. Zhang, R. R. Zhao and X. B. Lu, Crystalline CO2-based polycarbonates prepared from racemic catalyst through intramolecularly interlocked assembly, Nat. Commun., 2015, 6, 8594 CrossRef PubMed.
- C. Maeda, T. Taniguchi, K. Ogawa and T. Ema, Bifunctional catalysts based on m-phenylene-bridged porphyrin dimer and trimer platforms: synthesis of cyclic carbonates from carbon dioxide and epoxides, Angew. Chem., Int. Ed., 2015, 54, 134–138 CrossRef PubMed.
- X. D. Lang and L. N. He, Green catalytic process for cyclic carbonate synthesis from carbon dioxide under mild conditions, Chem. Rec., 2016, 16, 1337–1352 CrossRef PubMed.
- J. Liang, Y. B. Huang and R. Cao, Metal-organic frameworks and porous organic polymers for sustainable fixation of carbon dioxide into cyclic carbonates, Coord. Chem. Rev., 2017 DOI:10.1016/j.ccr.2017.11.013.
- Z. D. Chang, X. Jing, C. He, X. Liu and C. Y. Duan, Silver clusters as robust nodes and π-activation sites for the construction of heterogeneous catalysts for the cycloaddition of propargylamines, ACS Catal., 2018, 8, 1384–1391 CrossRef.
- A. A. G. Shaikh and S. Sivaram, Organic carbonates, Chem. Rev., 1996, 96, 951–976 CrossRef PubMed.
- B. Schäffner, F. Schäffner, S. P. Verevkin and A. Börner, Organic carbonates as solvents in synthesis and catalysis, Chem. Rev., 2010, 110, 4554–4581 CrossRef PubMed.
- O. Crowther, D. Keeny, D. M. Moureau, B. Meyer, M. Salomon and M. Hendrickson, Electrolyte optimization for the primary lithium metal air battery using an oxygen selective membrane, J. Power Sources, 2012, 202, 347–351 CrossRef.
- P. Ziosi, T. Tabanelli, G. Fornasari, S. Cocchi, F. Cavani and P. Righi, Carbonates as reactants for the production of fine chemicals: the synthesis of 2-phenoxyethanol, Catal. Sci. Technol., 2014, 4, 4386–4395 RSC.
- D. C. Webster, Cyclic carbonate functional polymers and their applications, Prog. Org. Coat., 2003, 47, 77–86 CrossRef.
- J. A. Kenar, G. Knothe, R. O. Dunn, T. W. Ryan and A. Matheaus, Physical properties of oleochemical carbonates, J. Am. Oil Chem. Soc., 2005, 82, 201–205 CrossRef.
- N. V. Maksimchuk, I. D. Ivanchikova, A. B. Ayupov and O. A. Kholdeeva, One-step solvent-free synthesis of cyclic carbonates by oxidative carboxylation of styrenes over a recyclable Ti-containing catalyst, Appl. Catal., B, 2016, 181, 363–370 CrossRef.
- T. Sakakura and K. Kohno, The synthesis of organic carbonates from carbon dioxide, Chem. Commun., 2009, 11, 1312–1330 RSC.
- Z. R. Li, Y. H. Zhao, S. R. Yan, X. K. Wang, M. Q. Kang, J. W. Wang and H. W. Xiang, Catalytic synthesis of carbonated soybean oil, Catal. Lett., 2008, 123, 246–251 CrossRef.
- C. A. Montoya, A. B. Paninho, P. M. Felix, M. E. Zakrzewska, J. Vital, V. Najdanovic-Visak and A. V. M. Nunes, Styrene carbonate synthesis from CO2 using tetrabutylammonium bromide as a non-supported heterogeneous catalyst phase, J. Supercrit. Fluids, 2015, 100, 155–159 CrossRef.
- J. A. Castroosma, K. J. Lamb and M. North, Cr(salophen) complex catalyzed cyclic carbonate synthesis at ambient temperature and pressure, ACS Catal., 2016, 6, 5012–5025 CrossRef.
- F. D. Bobbink and P. J. Dyson, Synthesis of carbonates and related compounds incorporating CO2 using ionic liquid-type catalysts: state-of-the-art and beyond, J. Catal., 2016, 343, 52–61 CrossRef.
- H. Büttner, J. Steinbauer, C. Wulf, M. Dindaroglu, H. G. Schmalz and T. Werner, Organocatalyzed synthesis of oleochemical carbonates from CO2 and renewables, ChemSusChem, 2017, 10, 1076–1079 CrossRef PubMed.
- W. Desens and T. Werner, Convergent activation concept for CO2 fixation in carbonates, Adv. Synth. Catal., 2016, 358, 622–630 CrossRef.
- Y. Du, J. Q. Wang, J. Y. Chen, F. Cai, J. S. Tian, D. L. Kong and L. N. He, A Poly(ethylene glycol)-supported quaternary ammonium salt for highly efficient and environmentally friendly chemical fixation of CO2 with epoxides under supercritical conditions, Tetrahedron Lett., 2006, 47, 1271–1275 CrossRef.
- J. Steinbauer and T. Werner, Poly(ethylene glycol)s as ligands in calcium-catalyzed cyclic carbonate synthesis, ChemSusChem, 2017, 10, 3025–3029 CrossRef PubMed.
- S. Kaneko and S. Shirakawa, Potassium iodide-tetraethylene glycol complex as a practical catalyst for CO2 fixation reactions with epoxides under mild conditions, ACS Sustainable Chem. Eng., 2017, 5, 2836–2840 CrossRef.
- S. Kumar and S. L. Jain, Polyethylene glycol wrapped potassium bromide assisted chemical fixation of carbon dioxide, Ind. Eng. Chem. Res., 2014, 53, 541–546 CrossRef.
- B. Schäffner, M. Blug, D. Kruse, M. Polyakov, A. Köckritz, A. Martin, P. Rajagopalan, U. Bentrup, A. Brückner, S. Jung, D. Agar, B. Rüngeler, A. Pfennig, K. Müller, W. Arlt, B. Woldt, M. Graß and S. Buchholz, Synthesis and application of carbonated fatty acid esters from carbon dioxide including a life cycle analysis, ChemSusChem, 2014, 7, 1133–1139 CrossRef PubMed.
- J. Tharun, G. Mathai, A. C. Kathalikkattil, R. Roshan, J. Y. Kwak and D. W. Park, Microwave-assisted synthesis of cyclic carbonates by a formic acid/KI catalytic system, Green Chem., 2013, 15, 1673–1677 RSC.
- M. E. Wilhelm, M. H. Anthofer, M. Cokoja, I. I. E. Markovits, W. A. Herrmann and F. E. Kühn, Cycloaddition of carbon dioxide and epoxides using pentaerythritol and halides as dual catalyst system, ChemSusChem, 2014, 7, 1357–1360 CrossRef PubMed.
- S. G. Liang, H. Z. Liu, T. Jiang, J. L. Song, G. Y. Yang and B. X. Han, Highly efficient synthesis of cyclic carbonates from CO2 and epoxides over cellulose/KI, Chem. Commun., 2011, 47, 2131–2133 RSC.
- J. L. Song, Z. F. Zhang, B. X. Han, S. Q. Hu, W. J. Li and Y. Xie, Synthesis of cyclic carbonates from epoxides and CO2 catalyzed by potassium halide in the presence of β-cyclodextrin, Green Chem., 2008, 10, 1337–1341 RSC.
- J. Martínez, J. Fernández-Baeza, L. F. Sánchez-Barba, J. A. Castro-Osma, A. Lara-Sánchez and A. Otero, An efficient and versatile catalyst for carbon dioxide fixation into cyclic carbonates, ChemSusChem, 2017, 10, 2886–2890 CrossRef PubMed.
- A. F. Guzman, D. A. Echeverri and L. A. Rios, Carbonation of epoxidized castor oil: a new bio-based building block for chemical industry, J. Chem. Technol. Biotechnol., 2017, 92, 1104–1110 CrossRef.
- N. Tenhumberg, H. Büttner, B. Schäffner, D. Kruse, M. Blumenstein and T. Werner, Cooperative catalyst system for the synthesis of oleochemical cyclic carbonates from CO2 and renewables, Green Chem., 2016, 18, 3775–3788 RSC.
- M. Vafaeezadeh and M. M. Hashemi, Polyethylene glycol (PEG) as a green solvent for carbon-carbon bond formation reactions, J. Mol. Liq., 2015, 207, 73–79 CrossRef.
- W. V. T. Madhushani, Y. M. C. D. Jayathilake, K. S. Perera and K. P. Vidanapathirana, Effect of cation size of iodide salt in the electrolyte on the performance of dye sensitised solar cells, J. Natl. Sci. Found. Sri Lanka, 2016, 44, 77–81 CrossRef.
- X. S. Cai, J. L. Zheng, J. Wärnå, T. Salmi, B. Taouk and S. Leveneur, Influence of gas-liquid mass transfer on kinetic modeling: carbonation of epoxidized vegetable oils, Chem. Eng. J., 2017, 313, 1168–1183 CrossRef.
Footnote |
† Electronic supplementary information (ESI) available. See DOI: 10.1039/c8ra05947k |
|
This journal is © The Royal Society of Chemistry 2018 |
Click here to see how this site uses Cookies. View our privacy policy here.