DOI:
10.1039/C8RA05065A
(Paper)
RSC Adv., 2018,
8, 24780-24786
Microwave absorption properties of lightweight and flexible carbon fiber/magnetic particle composites
Received
13th June 2018
, Accepted 2nd July 2018
First published on 10th July 2018
Abstract
Hybridized-carbon-based materials with magnetic metals and oxides have attracted much attention because of their enhanced electromagnetic wave loss. In this study, magnetic particles were coated on the surface of carbon fibers by carbonizing in a nitrogen atmosphere. The morphology, structure, thermolysis, and wave-absorption performance of the carbon fiber/magnetic particle composite were determined. Results show that the in situ-formed magnetic particles (such as Fe3O4, NiFe2O4, CoFe2O4, and Ni3Fe) are uniformly dispersed along the carbon-based fibers, which exhibit different wave absorption. The absorption of the carbon fiber/magnetic particle composite can be controlled by adjusting the species and concentration of the magnetic particle coating, which provides a new and effective way of endowing the magnetic-particle-coated carbon fibers with good microwave absorption properties.
Introduction
Radar-absorbing materials (RAMs) are used to cover the surface of targets in order to reduce target detection by radar, i.e., to reduce the radar signature (radar echo). In addition, RAMs can reduce the impact of electromagnetic pollution. Therefore, RAMs are of great importance, both in civilian and military fields, and have attracted great attention globally. To date, many studies have been carried out on new high-performance electromagnetic absorbers with light materials, wide absorption bands, and low cost. Carbon materials, such as carbon fibers (CFs), reduced graphene oxide (RGO), and carbon nanotubes (CNTs), which are a typical subject of research, have proved effective as RAMs.1–5 Carbon fibers, which are suitable substrate materials owing to their low density, high strength, and excellent electrical properties, are used to prepare carbon fiber nonwovens and other absorbing materials.1,6 Carbon fibers are also combined with other polymers, such as polyaniline and epoxy resin, to obtain absorbing materials in order to improve their microwave-absorbing capacity.7,8
However, carbon materials are a type of electromagnetic-wave-absorbing materials that exhibit dielectric loss. When a pure carbonaceous material is used, the absorbing property of the material is9,10 affected by its low magnetic loss and high reflection coefficient. To mitigate this defect, researchers have used electroplating, co-precipitation, or coating on the surface of carbon materials to load magnetic particles such as carbonyl-iron, Fe3O4, Ni, and Fe–Co in order to enhance the absorption properties of the material.11–14 It is worth noting that magnetic materials based on Fe, Co, and Ni with better soft magnetic properties are coated on CFs, RGO, and CNTs, and other carbon materials, which can effectively combine their advantages, reduce the disadvantages of dielectric loss and magnetic loss in these materials, thus providing a lightweight and wide-absorption-band-absorbing composite material.15–18
However, electroplating, chemical plating, and reduction are usually adopted to prepare magnetic coatings on carbon fibers. The drawbacks of these methods are time consumption, low yield, and uncertain quality, and effect on the coat of the internal fiber.
In this study, for the first time, core (CFs)–shell (magnetic particle) hybrids with light and soft were prepared via a simple, low-pollution, high-temperature one-step molding process. The magnetic and microwave absorption properties of the CF/magnetic particle composites were then investigated.
Experimental
Preparation of CF/magnetic particle composite
The preparation process is schematically illustrated in Fig. 1. Polyacrylonitrile (PAN)-based pre-oxidative felt (fiber diameter of 1.5 dtex) was obtained from Nantong Sen Carbon Fiber Co., Ltd. Prior to impregnation, the felts were cleaned at 60 °C for 30 min in ethanol. A metal salt solution (different proportions of FeCl3, CoSO4·7H2O, and NiSO4·6H2O) was employed for the impregnation of PAN-based pre-oxidative felts. After drying, the PAN-based pre-oxidative fibers containing metal salts were heat-treated at 650 °C for 60 min in N2. CF/FeCoNi, CF/FeCo, CF/FeNi, and CF/CoNi were prepared according to different ratios of the impregnating solution [n(Fe)
:
n(Co)
:
n(Ni)], of 2
:
2
:
1, 2
:
2
:
0, 2
:
0
:
1, and 0
:
2
:
1, and the concentration of the total metal ions was 0.625 mol L−1. CF/FeCoNi was prepared under different concentrations (0.625 × 0 mol L−1, 0.625 × 0.5 mol L−1, 0.625 × 1 mol L−1, 0.625 × 1.5 mol L−1, 0.625 × 2 mol L−1, and 0.625 × 2.5 mol L−1).
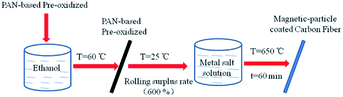 |
| Fig. 1 Preparation process for magnetic-particle-coated carbon fiber. | |
Characterization
Phase structure analysis of the prepared CF/magnetic particle was performed using X-ray diffraction (XRD, Rigaku D/max-2500PC, with CuKα). A scanning electron microscopy (SEM, Scios DualBeam) system equipped with energy dispersive spectroscopy (EDS) apparatus was used for morphology observation and elemental analysis, respectively. The formation mechanism was analyzed using thermogravimetry/differential scanning calorimetry (TG/DSC, Netzsch 214 Polyma) at a heating rate of 5 °C min−1 from 30 to 800 °C in argon atmosphere. The reflection coefficient (RC) of the CF/magnetic particle composite was determined in the frequency ranges of 5.85–8.2 GHz, 8.2–12.4 GHz, 12–18 GHz, and 18–26 GHz by the NRL-arc method. A metal sheet (180 mm × 180 mm) and CF/magnetic particle composite with the same dimensions were successively placed on the sample platform. Two horn antennas were used to send and receive the electromagnetic wave normally with the sheet.
Results and discussion
Phase composition and morphology
The PAN-based pre-oxidized felt after impregnation with metal salts was treated for 60 min at 650 °C in N2. The interaction between the fiber and metal salt produces complex particles. The XRD patterns of the pure carbon powders (Fig. 2a) show only one extremely broad diffraction peak, which is attributed to the crystallographic (0 0 2) plane of graphite in the turbostratic carbon structure.19 In the CF/magnetic particle composite, this peak broadens and shifts slightly towards high 2θ. The strong diffraction peaks with a small full-width at half maximum indicate good crystallization of the sample. In Fig. 2a, we can observe CF/FeCoNi contained by Fe3O4 (JCPDS 75-1609), NiFe2O4 (JCPDS 74-2081), CoFe2O4 (JCPDS 79-1744), Ni3Fe (JCPDS 88-1715), and other magnetic particles; it also includes (Co, Ni, Fe)9S8 (JCPDS 30-0444) and other non-magnetic particles. The magnetic properties of these magnetic particles appearing in the XRD pattern clearly exhibit magnetic loss. In reality, they are also applied to magnetic loss composites.13,15,17 When we change the concentration of the impregnated solution, the position of the characteristic peak in the XRD diagram does not change; only the Ni3Fe characteristic peak becomes stronger. Therefore, we can conclude that the level of concentration does not affect the change in the final magnetic particle type. However, when only two types of metal salts are prepared with the impregnation solution, the particles generated are different from CF/FeCoNi, and there are different phases in the same substance. When there are only two types of metal salts in the solution, we find that CF/FeCo is coated by particles such as Fe3O4 (JCPDS 75-0499), CoFe2O4 (JCPDS 22-1086), CoxSy (JCPDS 75-1561, and JCPDS 25-2023); CF/FeNi is coated by particles such as Fe3O4 (JCPDS 86-2267), NiFe2O4 (JCPDS 86-2267), and Ni3S2 (JCPDS 44-1418). CF/CoNi is coated by particles such as CoO (JCPDS 75-0533), Co (JCPDS 15-0806), and Ni3S2 (JCPDS 30-0863). The particles of these coatings, most of which are nonmagnetic particles, also include magnetic particles. Therefore, we can consider that the magnetic particles coated on the CF/FeCoNi surface are of different types and contents compared to other samples.
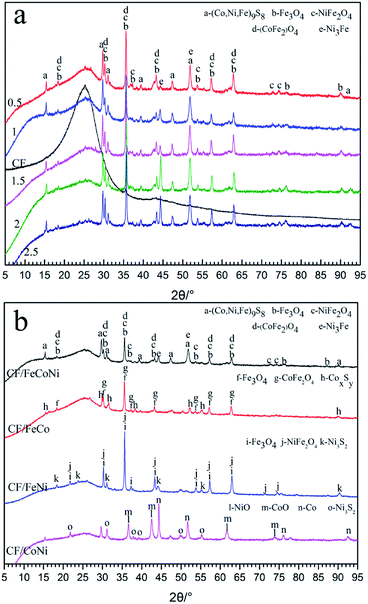 |
| Fig. 2 XRD patterns (a and b) of CF/FeCoNi prepared at 0.5, 1, 1.5, 2, and 2.5 times concentrations; CF/FeCoNi (1 times), CF/FeCo, CF/FeNi, CF/CoNi. | |
The surface morphology of CF/FeCoNi will also be different when the concentration of the impregnation solution changes. We can see in Fig. 3 that when the concentration of the impregnation solution increases, the number of particles contained in the prepared samples increases. Fig. 3a shows that the surface of the CF (the concentration is 0 times) is smooth and there is no particle coated. When the concentration is 0.5 times (Fig. 3b), there is a certain gap between the particles on the surface of the fiber. When the concentration is greater than 1 times, the magnified image (Fig. 3d–f) reveals a typical plate-like coating; the particle coating on the fiber surface is uniform and tight, and with the increase in concentration, the number of larger particles on the surface of the carbon fiber increases gradually. The increase in the magnetic particle content on the surface of the fiber will affect the electromagnetic wave absorption property of the material.15 Further, many gaps can be seen between the fibers in the fiber felt, which helps the incident wave to enter the material; the incident wave is reflected in the material many times and produces loss, and there is the improvement in the absorbing property of the material. Fig. 3g shows that CF/FeCoNi (1 times) can be attracted by magnets, which further demonstrates that the fiber surface contains many magnetic particles. In addition, as shown in Fig. 3h, CF/FeCoNi can be bent, which indicates that the material has certain flexibility.
 |
| Fig. 3 SEM images of CF/FeCoNi prepared at (a) 0, (b) 0.5, (c) 1, (d) 1.5, (e) 2, and (f) 2.5 times concentration; (g) magnetic and (h) bending properties of CF/FeCoNi prepared at 1 times concentration. | |
Fig. 4 shows the surface topographic map of CF/FeCo, CF/FeNi, and CF/CoNi obtained from the PAN-based pre-oxidized felt after immersion in the solution with only two salts. We can find that although the concentration of metal ions in the impregnated solution is the same, the distribution of the particles on the surface of the fiber is different, and the particles exhibit a larger aggregation trend, which leads to the larger gap between the particles on the surface of the fiber. It is more obvious that the particles in CF/CoNi are massive, and cannot be uniformly loaded onto the fiber surface. When the impregnated solution contains three metal elements (FeCl3, CoSO4·7H2O, and NiSO4·6H2O), they can form more uniform particles on the fiber surface. The reasons can be further studied.
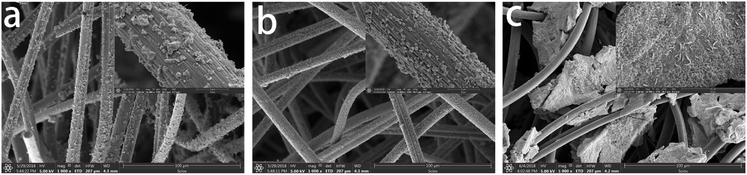 |
| Fig. 4 SEM images of (a) CF/FeCo, (b) CF/FeNi, and (c) CF/CoNi. | |
The EDS spectra of CF, CF/FeCo, CF/FeNi, and CF/CoNi (Fig. 3a, 4a–c) are shown in Fig. 5. Upon immersion in the metal salt solution and treatment at high temperature, there are corresponding C, N, O, S, Cl, Fe, Co, Ni, and other elements on the surface of the fiber. The results show that the surface of the PAN-based pre-oxidative fibers can adsorb metal salts that dissolve in the solution; metal salts undergo thermal degradation after high-temperature treatment and form new particles on the surface of the fibers. Fig. 2 and 3 show that the surface of the CF/FeCoNi fiber contains magnetic particles such as Fe3O4, NiFe2O4, CoFe2O4, and Ni3Fe, and their distribution on the surface of the fiber. We can see the EDS surface scan in Fig. 6(c–e); the Fe, Co, and Ni atoms are uniformly dispersed in the fiber on the surface, and the distribution maps are almost overlapped, which proves that the three metal elements are combined after a series of reactions to generate the magnetic particles; this also agrees with the XRD (Fig. 2a) results.
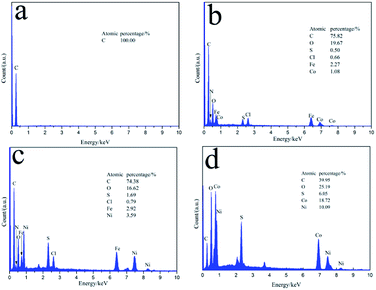 |
| Fig. 5 EDS spectra of (a) CF, (b) CF/FeCo, (c) CF/FeNi, and (d) CF/CoNi. | |
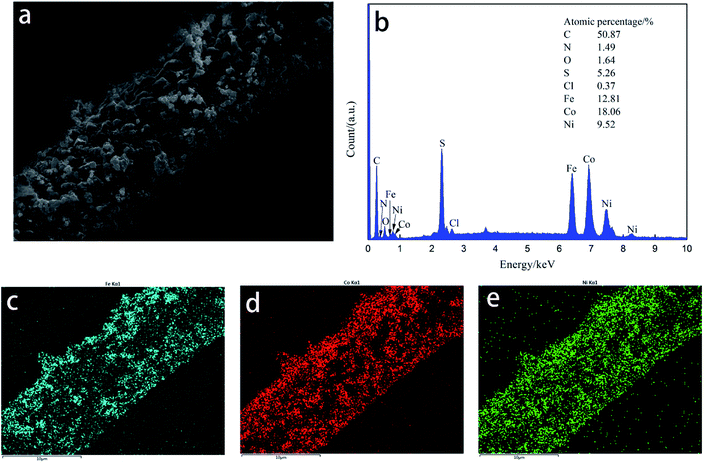 |
| Fig. 6 SEM map scanning topography of CF/FeCoNi neutron absorber composites. | |
Formation mechanisms of CF/magnetic particle composite
To analyze the reactions involved in carbonization and understand the formation mechanism of the CF/magnetic particle composite, TG/DSC analyses were performed. Fig. 7 displays the TG curves of pristine CF, and PAN-based pre-oxidized/FeCl3/CoSO4·7H2O/NiSO4·6H2O (PAN/metal salt) at a heating rate of 5 °C min−1. There is a proportional weight loss below 100 °C in the TG curves, which is mainly due to the evaporation of moisture. The TG analysis of pristine CF shows one obvious weight loss at 418 °C, which is mainly ascribed to the fast degradation of the PAN-based pre-oxidized fiber, and Fig. 7b shows five weight losses at 138, 380, 505, 607, and 775 °C, which are attributed to the release of crystal water and the degradation of fiber and melt salt (FeCl3, CoSO4·7H2O, and NiSO4·6H2O), respectively.
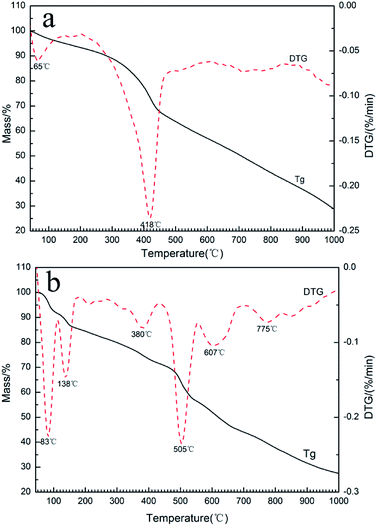 |
| Fig. 7 TG and DTG curves of PAN-based pre-oxidized fiber and PAN/metal salt. | |
However, during the carbonization of PAN/metal salt, the position of the above weight loss peaks slightly changes (see the differential thermal gravimetry (DTG) part of the TG curve), which indicates that the degradation process of PAN-based pre-oxidized fiber and metal salt varies with the interaction between them in the composite fibers.20 It has been reported that the heating of transition metal salts in an inert atmosphere (namely CO and H2) leads to an abnormal decomposition.21,22 This further illustrates a series of reactions such as thermal decomposition and thermal reduction of FeCl3, CoSO4·7H2O, and NiSO4·6H2O in the presence of C and at certain temperatures (main reaction processes, such as (1)–(10)). The existence of a series of magnetic particles, such as Fe–Ni, Fe3O4, Fe–Co–O, and Fe–Ni–O, and the formation of Fe–Co–Ni, Fe–Co, etc. may not reflect the corresponding characteristic peaks in the XRD because of the existence of the amorphous state. The possibility of magnetic particle formation is further confirmed.
|
 | (1) |
|
 | (2) |
|
 | (3) |
|
 | (4) |
|
 | (5) |
|
 | (6) |
|
 | (7) |
|
 | (8) |
|
 | (9) |
|
 | (10) |
Electromagnetic wave absorption properties
Fig. 8 shows the RC of CF and CF/FeCoNi, as a function of frequency, by the NRL-arc method. It shows the influence of concentration on wave absorption; the electromagnetic loss of CF/FeCoNi prepared at low concentration is excellent. It can be seen that the RC of the CF at 5.85–26 GHz was >−2 dB. After coating with magnetic particles, the RC at 5.85–26 GHz was greatly reduced. Magnetic particles, being magnetic loss materials, play a key role in the absorption of electromagnetic waves, and are synergistic with the dielectric loss of carbon fibers, showing excellent wave absorbing properties.4 When the concentration is 0.5 (0.3125 mol L−1), the RC is <−10 dB (90% of the attenuation), and could reach up to 12.2 GHz (from 13.8 to 26 GHz) (Fig. 8). When the concentration is 1 (0.625 mol L−1), the RC is <−10 dB, and could reach up to 7.4 GHz (from 8.7 to 16.1 GHz), and realizes a minimal RC of −30.62 dB at 15.38 GHz, and an RC better than low concentration (0.5 times) from 5.85 to 15.12 GHz is found. With the increase in the concentration of the solution, the wave absorption of the sample is affected by the concentration of the solution. When the concentration of the impregnated solution is greater than 1 times, the RC of CF/FeCoNi from 5.85 to 26 GHz is >−10 dB. This can be explained as the magnetic particle load of the CF surface being able to increase the electromagnetic wave loss,12–14 but as the concentration increases, the density of the magnetic particles on the surface of the carbon fiber increases, and the particle size also increases gradually (Fig. 3). All these factors will affect the synergistic effect between the CF (dielectric loss material) and magnetic particles, resulting in wave-absorbing properties, the mechanism of which warrants further study. The NRL-arc method has multiple bell mouths corresponding to different band frequencies; therefore, there is a certain error in the data at the band junction.
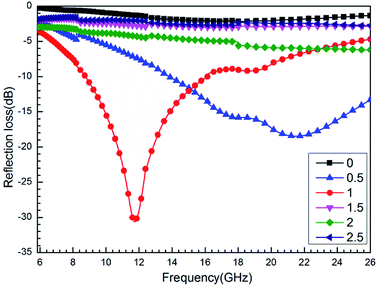 |
| Fig. 8 Reflection loss curves of CF/FeCoNi prepared at 0, 0.5, 1, 1.5, 2, and 2.5 times concentrations. | |
The presence of iron, cobalt, and nickel can affect the microwave absorbing properties of the sample (Fig. 9). When n(Fe)
:
n(Co)
:
n(Ni) = 2
:
2
:
1 (0.625 mol L−1), the RC of the sample from 5.85 to 16.41 GHz is better than that of the other; it has a minimum RC of −30.62 dB at 11.74 GHz, whereas the effective bandwidth of RC <−10 dB can reach up to 7.4 GHz (from 8.7 to 16.1 GHz). When the frequency band is higher than 16.41 GHz, the RC of CF/FeCo and CF/FeNi is better; this is attributed to the type of particles on the surface of the sample being different. Different magnetic materials show different magnetic loss performance. When the carbon fiber is combined with the dielectric loss material, different wave absorption properties manifest different wavelengths.23–27 We also found that the addition of Fe could make the CF/magnetic particle composite exhibit better microwave absorption. Through XRD and SEM analysis, we found that the addition of Fe compounds produced more magnetic particles (Fig. 2a) and promoted the uniform distribution of the particles on the surface of the fiber (Fig. 4), Therefore, the RCs of the samples were enhanced. In addition, although the magnetic particles are not found in the CF/CoNi sample, the particles coated on the CF improve the reflection properties of the electromagnetic waves on the surface of the CF, and make the wave-absorbing performance better than that of the CF.10
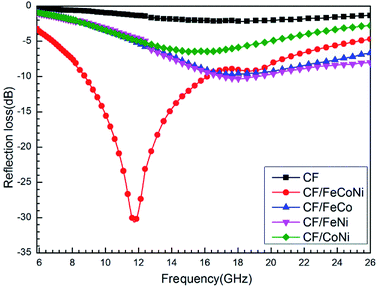 |
| Fig. 9 Reflection loss curves of CF, CF/FeCoNi, CF/FeCo, CF/FeNi, and CF/CoNi. | |
Conclusions
In summary, a CF/magnetic particle composite was successfully synthesized by the carbonization of an as-impregnated PAN-based pre-oxidized fiber/metal salt, in which the formed magnetic particle can be well dispersed on the surface of CFs. Unlike pristine carbon material, the CF/magnetic particle composite can retain the soft fiber felt structure after carbonization under nitrogen atmosphere. The composites exhibit excellent electromagnetic wave absorption capabilities and wide absorption bandwidths at a lower concentration (0.0625 mol L−1, n(Fe)
:
n(Co)
:
n(Ni) = 2
:
2
:
1). The minimum RC of the composite containing the CF/magnetic particle composite can reach up to −30.62 dB at 11.74 GHz due to the enhanced dielectric loss from the magnetic Fe3O4, NiFe2O4, CoFe2O4, and Ni3Fe particles and lightweight carbon-based fibers. Moreover, an effective bandwidth (RC below −10 dB) of 7.4 GHz can be achieved in a wide frequency range from 8.7 to 16.1 GHz. These results indicate that the preparation of light soft core (carbon fibers)–shell (magnetic particle) hybrid materials via a high-temperature one-step molding process can be considered a promising technique to obtain strong and lightweight electromagnetic wave-absorbing materials in a wide frequency range.
Conflicts of interest
There are no conflicts to declare.
Acknowledgements
This study was supported by the National Key Research and Development Program of China (2016YFB0303100), and the National Science Foundation for Young Scientists of China (Grant No. 51503105).
Notes and references
- H. Zhu, P. Chen and R. Wu, et al., Microwave absorption properties of carbon fibre containing nonwovens, Indian J. Fibre Text. Res., 2007, 32, 391–398 Search PubMed.
- B. Wen, X. X. Wang and W. Q. Cao, et al., Reduced graphene oxides: the thinnest and most lightweight materials with highly efficient microwave attenuation performances of the carbon world, Nanoscale, 2014, 6(11), 5754–5761 RSC.
- H. Sun, R. Che and X. You, et al., Crossstacking aligned carbon-nanotube films to tune microwave absorption frequencies and increase absorption intensities, Adv. Mater., 2014, 26(48), 8120–8125 CrossRef PubMed.
- Y. Qing, D. Min and Y. Zhou, et al., Graphene nanosheet - and flake carbonyl iron particle-filled epoxy–silicone composites as thin–thickness and wide-bandwidth microwave absorber, Carbon, 2015, 86, 98–107 CrossRef.
- Y. Qing, W. Zhou and F. Luo, et al., Epoxy-silicone filled with multi-walled carbon nanotubes and carbonyl iron particles as a microwave absorber, Carbon, 2010, 48(14), 4074–4080 CrossRef.
- S. Xia, B. Yao and Q. Chen, et al., Composites with Koch fractal activated carbon fiber felt screens for strong microwave absorption, Composites, Part B, 2016, 105, 1–7 CrossRef.
- B. Cheng, J. Wang and F. Zhang, et al., Preparation of silver/carbon fiber/polyaniline microwave absorption composite and its application in epoxy resin, Polym. Bull., 2017, 28, 1–13 Search PubMed.
- Liu, R. Tao and P. Luo, et al., Preparation and microwave absorbing property of carbon fiber/polyurethane radar absorbing coating, RSC Adv., 2017, 7(73), 46060–46068 RSC.
- M. Arjmand, Electrical conductivity, electromagnetic interference shielding and dielectric properties of multi-walled carbon nanotube polymer composites, University of Calgary, 2014 Search PubMed.
- J. Qiu and T. Qiu, Fabrication and microwave absorption properties of magnetite nanoparticle-carbon nanotube-hollow carbon fiber composites, Carbon, 2015, 81(1), 20–28 CrossRef.
- Y. C. Qing, W. C. Zhou and S. Jia, et al., Electromagnetic and microwave absorption properties of carbonyl iron and carbon fiber filled epoxy/silicone resin coatings, Appl. Phys. A: Mater. Sci. Process., 2010, 100(4), 1177–1181 CrossRef.
- X. Chen, X. Wang and L. Li, et al., Preparation and microwave absorbing properties of nickel-coated carbon fiber with polyaniline via in situ polymerization, J. Mater. Sci.: Mater. Electron., 2016, 27(6), 5607–5612 CrossRef.
- Z. Zeyang, L. Xiangxuan and Z. Haifeng, et al., Electromagnetic and microwave absorption properties of carbon fibers coated with carbonyl iron, J. Mater. Sci.: Mater. Electron., 2015, 26(9), 6518e25 Search PubMed.
- M. Choi, S. Lee and J. Kim, Clustering effect on the frequency-dependent magnetic properties of Fe-Co micro hollow fiber composites, IEEE Trans. Magn., 2017, 1 Search PubMed.
- Y. Wan, J. Xiao and C. Li, et al., Microwave absorption properties of FeCo-coated carbon fibers with varying morphologies, J. Magn. Magn. Mater., 2016, 399, 252–259 CrossRef.
- X. Huang, J. Zhang and W. Rao, et al., Tunable electromagnetic properties and enhanced microwave absorption ability of flaky graphite/cobalt zinc ferrite composites, J. Alloys Compd., 2016, 662, 409–414 CrossRef.
- Y. Rao, W. Chen and Z. Cao, Synthesis and Microwave Absorbing Properties of FeCoNi Alloy Particles/Graphite Flaky Composites, J. Inorg. Mater., 2010, 25(4), 406–410 CrossRef.
- M. Ning, J. Li and B. Kuang, et al., One-Step Fabrication of N-doped CNTs Encapsulating M nanoparticles (M = Fe, Co, Ni) for Efficient Microwave Absorption, Appl. Surf. Sci., 2018, 447(31), 244–253 CrossRef.
- Z. Zhou, C. Lai and L. Zhang, et al., Development of carbon nanofibers from aligned electrospun polyacrylonitrile nanofiber bundles and characterization of their microstructural, electrical, and mechanical properties, Polymer, 2009, 50(13), 2999–3006 CrossRef.
- C. Sun, Y. Guo and X. Xu, et al., In situ preparation of carbon/Fe3C composite nanofibers with excellent electromagnetic wave absorption properties, Composites, Part A, 2017, 92, 33–41 CrossRef.
- T. Wanjun and C. Donghua, Mechanism of thermal decomposition of cobalt acetate tetrahydrate, Chem. Pap., 2007, 61(4), 329–332 Search PubMed.
- J. C. De Jesus, I. González and A. Quevedo, et al., Thermal decomposition of nickel acetate tetrahydrate: an integrated study by TGA, QMS and XPS techniques, J. Mol. Catal. A: Chem., 2005, 228(1), 283–291 CrossRef.
- K. Osouli-Bostanabad, H. Aghajani, E. Hosseinzade and H. Maleki-Ghaleh, et al., Microwave Absorption of Nano-Fe3O4 Deposited Electrophoretically on Carbon Fiber, Mater. Manuf. Processes, 2015, 31(10), 1351–1356 CrossRef.
- W. Gan, L. Gao and W. Zhang, et al., Fabrication of microwave absorbing CoFe2O4 coatings with robust superhydrophobicity on natural wood surfaces, Ceram. Int., 2016, 42(11), 13199–13206 CrossRef.
- H. Hosseini and H. Mahdavi, Nanocomposite based on epoxy and MWCNTs modified with NiFe2O4 nanoparticles as efficient microwave absorbing material, Appl. Organomet. Chem., 2018, 32(4), e4294 CrossRef.
- L. I. U. Min, X. I. A. N. G. Jun and W. U. Zhi-Peng, et al., Facile Preparation and Microwave Absorption Properties of Fe-Co-Ni Alloy Nanoparticle Embedded-Carbon Nanofibers, Chin. J. Inorg. Chem., 2017, 1, 57–65 Search PubMed.
- J. Shim, J. Kim and S. H. Han, et al., Nanocrystalline Fe–Co–Ni–B thin film with high permeability and high-frequency characteristics, J. Magn. Magn. Mater., 2005, 290–291(s290–291), 205–208 CrossRef.
|
This journal is © The Royal Society of Chemistry 2018 |
Click here to see how this site uses Cookies. View our privacy policy here.