DOI:
10.1039/C8RA04401E
(Paper)
RSC Adv., 2018,
8, 24458-24463
Excellent binding effect of L-methionine for immobilizing silver nanoparticles onto cotton fabrics to improve the antibacterial durability against washing
Received
23rd May 2018
, Accepted 28th June 2018
First published on 6th July 2018
Abstract
Silver nanoparticles (Ag NPs) have outstanding antimicrobial effects, but their weak adhesive force onto cotton fiber surfaces often causes undesired silver loss from antibacterial fabrics, diminishing antibacterial durability, and even leading to environmental and health risks. To improve adhesion of the Ag NPs, various strategies have been tried, but achieving long-term antibacterial effectiveness still remains challenging. Here, L-methionine is proposed as a binder reagent because it has low toxicity towards mammalian cells and has a methyl group to enhance its coordination ability. The antibacterial cotton fabric was fabricated via a very simple pad-dry-cure process: after dipping a cotton fabric in an L-methionine solution followed with heating for esterification, Ag NPs are formed via the reaction of silver nitrate with sodium borohydride. The resulting cotton fabric exhibits an excellent antibacterial property and laundering durability. Its bacterial reduction rates (BR) against both S. aureus and E. coli remained over 97% even after 90 consecutive laundering cycles. Moreover, the modification causes insignificant damage to cotton's characteristics, such as tensile breaking strength, water absorptivity, and vapor permeability.
1 Introduction
Cotton fabric has suitable flexibility, water absorptivity, and air permeability for wearable textiles; therefore its wear comfortability has been well-received by customers.1–3 To extend its market share, various efforts have been made to endow cotton textiles with additional functions,4–6 and such exploration has gradually concentrated on a few areas, for example, antibacterial effects,7,8 UV-protection,9,10 hydrophobic coating,11,12 flame retardance,13–15 and wear-resistance.16 Among these functions, the antibacterial effect has received more significant attention because the bacterial problem of cotton textiles often seriously troubles users. The temperature, moisture, and nutrients in the cotton textiles generally meet the requirements for the growth and reproduction of a multitude of bacteria and fungi,17 and the microorganisms living on cotton fabrics often produce terrible odours, and cause colour degradation and even serious risks to human health.18,19 Therefore, a wide range of researchers have been putting efforts into antimicrobial cotton textiles, and numerous successful antibacterial cotton products have been applied in textile commodities including underwear, socks, curtains, and medical textile supplies. However, washing durability is still a practical challenge for most of the antimicrobial products,20–24 especially for the cotton fabrics modified using silver nanoparticles (Ag NPs).25
Ag NPs have strong antimicrobial effect,26–30 but they were suspected to have potential risks on the environment and human health.31,32 Moreover, the absence of covalent bonds between Ag NPs and cotton fibers makes the Ag NPs easy to split form the fiber surface during washing process. In this respect, various approaches have been investigated to enhance the adhesive force of Ag NPs onto cotton fabrics. As a result, it was reported that several ways, including polymer binders,33,34 composite nanoparticles,35,36 and surface modifications of cotton fiber37 are effective on improving the antibacterial durability. Generally, these methods can give cotton fabrics with a certain degree of durability, for example, keeping more than 90% of the original antibacterial efficiency after 20–50 washing cycles.38–40 However, achieving a satisfactory antibacterial durability with a minor dosage of Ag NPs still remains challenging. We have demonstrated that L-cysteine has an excellent effect on binding Ag NPs onto cotton fiber surface recently.41 Basing on the finding, we further pay attention to a similar amino acid, L-methionine, because it is one of the essential amino acids for human body and it has low toxicity towards mammalian cells as L-cysteine, but the electron donating effect of the methyl group may induce a stronger affinity with Ag NPs than L-cysteine does. The reducing agent used in this experiment is sodium borohydride, and its reduction product is sodium borate, which can be used as cleaning agents and cosmetics. It is unharmful to human being, and has little environmental risk.
In the present work, L-methionine is covalently linked onto cotton fiber surface via an esterification reaction with the hydroxyl groups of cellulose using a facile finishing pad-dry-cure process. Then Ag NPs are synthesized and immobilized on the modified surface by the enhanced adhesive force of the L-methionine moieties. These reactions are monitored using a variety of analytical tools, including field emission scanning electron microscopy (FE-SEM), Fourier transform infrared spectroscopy (FTIR), X-ray diffraction (XRD), and X-ray photoelectron spectroscopy (XPS). Moreover, antibacterial effect and antibacterial durability of the finished fabrics are evaluated. As a result, L-methionine gives cotton fabrics with excellent laundering durability but without significant damages on cotton natures such as water absorptivity and vapor permeability. To our best knowledge, this is the first time to apply L-methionine as a binder to immobilize Ag NPs onto cotton fabrics, which offers outstanding antibacterial durability against washing.
2 Materials and methods
2.1 Materials
Cotton fabrics (abbreviated as Cot, warp density 60 stick per cm, weft density 30 stick per cm, thickness 0.42 mm, square meter quality 120 g m−2, specific area 35.2 m2 g−1) were purchased from Shaoxing Qidong Textile Co., Ltd. (China). Before chemical modification, the cotton (30 mm × 30 mm) fabrics were cleaned as previous literature.3 L-Methionine and other reagents were purchased from shanghai Aladdin Co., Ltd (China) and used without further purification.
2.2 Surface modification
As shown in Scheme 1, a cotton fabric (30 mm × 30 mm) was immersed in an aqueous solution of L-methionine (100 mL, 1.0 wt%) for 30 min, squeezed using a roller to a wet pick up of 90 ± 2 wt%, heated at 180 °C for 5 min, rinsed with deionized water (100 mL × 3 times) to remove unreacted L-methionine molecules, and dried at 100 °C for 30 min to obtain the modified fabric (Me-Cot). The Me-Cot fabric was soaked in a solution of silver nitrate (100 mL, 0.046 mol L−1), heated at 100 °C for 30 min, further soaked in a solution of sodium borohydride (100 mL, 0.095 mol L−1), rinsed with deionized water (100 mL × 3 times), and dried at 100 °C for 30 min to obtain the final cotton fabric sample (Ag-Me-Cot).
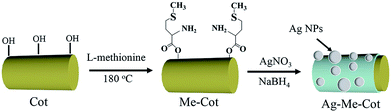 |
| Scheme 1 Scheme of grafting L-methionine and forming Ag NPs on cotton fabric. | |
2.3 Characterizations
FTIR measurements were performed on a Nicolet Avatar 370 spectrometer (Nicolet Company, Madison, USA) with an attenuated total reflection (ATR) accessory. XRD analyses were obtained using an X-ray diffractometer (ARL XTRA, Switzerland) with Cu K radiation (λ = 1.5418 Å) operating at 40 kV, 60 mA, and the detailed protocol was described in our previous report.3 XPS analysis was performed by an AXIS multifunctional X-ray photoelectron spectrometer (ULTRA DLD, Shimadzu Ltd., Japan) at a power of 450 W. Surface morphology of the modified cotton fabrics was investigated using a FE-SEM set (Ultra-55, Zeiss, Germany). Size distribution of the Ag NPs on fiber surface was calculated by measuring 200 bright points in the SEM images. The silver content in the finished cotton fabrics was measured by using inductively coupled plasma mass spectrometry (ICP-MS, Agilent 7500a, Australia).
Escherichia coli (E. coli, ATCC 1555) and Staphylococcus aureus (S. aureus, ATCC 547) were used as the model microorganisms, and the detailed protocol was described in our previous report.42
Laundering durability was evaluated by monitoring the antimicrobial ability of the cotton fabric sample periodically after every stringent washing process.42 For one laundering cycle, the cotton fabric (15 mm × 15 mm) was washed with 50 mL of an aqueous solution of sodium dodecanesulphonate (2.0%, w/w) in a beaker (diameter, 50 mm) with stirring (300 rpm, magnetic stirrer, 9 mm × 25 mm) at 25 °C.
As our previous work,42 water absorptivity was measured by weighting the difference of the cotton samples after soaking in deionized water and hanging out, water vapor permeability was evaluated by using the ASTM E-96 (open cup test) method,43 tensile strength tests were carried out on an electronic fabric tensile tester (YG065, China) at a constant rate of 20 cm min−1.
3 Results and discussion
3.1 Preparation and characterization of the Ag-Me-Cot cotton fabric
Pad-dry-cure process was used to graft L-methionine on the surface of cotton fibers and in situ-synthesize Ag NPs on the modified surface (Scheme 1). Pad-dry-cure method is a very usual technique can be found in almost all dyeing and finishing factories. To perform reactions on fabrics, it generally contains four successive steps: dipping fabric in a functional solution, squeezing to control the wet weight, drying and curing to promote the reaction rate. The reaction conditions (such as heating at 180 °C for more than 2 min) for esterification with the hydroxyl groups of cotton fabric have been well established.44,45
Fig. 1 compares the ATR-FTIR spectra of Cot (a), Me-Cot (b) and Ag-Me-Cot (c). Both Me-Cot and Ag-Me-Cot exhibit new peaks at 1725 cm−1 after the modification process. The peak is associable to the asymmetric stretching of COOH groups and COOR groups, implying that the esterification reactions occurred between the L-methionine and the hydroxyl groups of cellulose on cotton surface.46 Additionally, by comparing the spectra of Cot and Me-Cot, the attenuation observed on the peak around 3340 cm−1 (for –OH) and appearance of new peaks around 1567 cm−1 (for –NH2) further suggest the introduction of L-methionine onto the fabric surface.
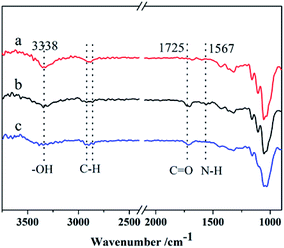 |
| Fig. 1 ATR-FTIR spectra of the Cot (a), Me-Cot fabric (b), and Ag-Me-Cot fabric (c). | |
Fig. 2 shows the XRD spectra of Cot (a) and Ag-Me-Cot (b). The peaks appearing at 2θ = 39, 45, 65, and 78 are assigned to the Ag (111), (200), (220), and (311) planes, respectively. As reported before,7,8,46,47 they are typical XRD peaks of Ag NPs having a pure crystalline structure. Moreover, by applying the Debye–Scherrer equation,48 the average size of the Ag NPs loaded on the fabric is calculated as 83.4 nm.
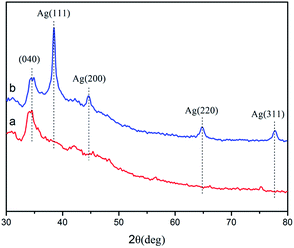 |
| Fig. 2 XRD patterns of the Cot (a), and Ag-Me-Cot fabric (b). | |
Fig. 3a and b show the wide-range XPS spectra of Cot and Ag-Me-Cot fabric samples. Cot displays C 1s and O 1s signals, but Ag-Me-Cot has additional S 2p and Ag 3d signals. The high resolution XPS C 1s spectra of Cot and Ag-Me-Cot are deconvoluted in Fig. 3c and d, respectively. The C 1s peak for Cot can be decomposed to two peaks with binding energy of 284 eV (C–C) and 286 eV (C–OH). Whereas in the case of Ag-Me-Cot fabric, the C 1s peak compose of new peaks at 287.2 eV and 288.8 eV, which are assignable to C–S and C
O bonds,49 respectively. Fig. 3e shows the Ag 3d XPS spectra of Ag-Me-Cot, and the peaks at 368.0 eV and 374.0 eV can be attributed to Ag0. The 6.0 eV slitting between the two peaks, Ag (3d5/2) and Ag (3d3/2), indicates the existence form of metallic silver on the fabric surface.50 Moreover, it is very obvious that these peaks can be further decomposed to two peaks with a 1.6 eV slitting of binding energy. Because Ag+ shows lower binding energy than Ag0,51,52 the attribution of the split peaks to silver ion can be disconfirmed. The positive shifts of 1.6 eV suggest the existence of small Ag NPs on the cotton fiber surface. Typically, 0.5–2.0 eV shifts have been observed previously for small nanoparticles compared to peaks of bulk crystals.53 The coordination bonds of Ag atoms with L-methionine binder is verified by the S 2p spectra shown in Fig. 3f. By comparing with the modified cotton before loading Ag NPs, the new peak appeared at 161.2 eV is attributable to the highly de-electronated state of S elements.54 These XPS results suggest that the L-methionine molecules have been covalently linked on the fiber surface by ester groups, and there are coordination bonds between the Ag NPs and the S atoms of L-methionine.
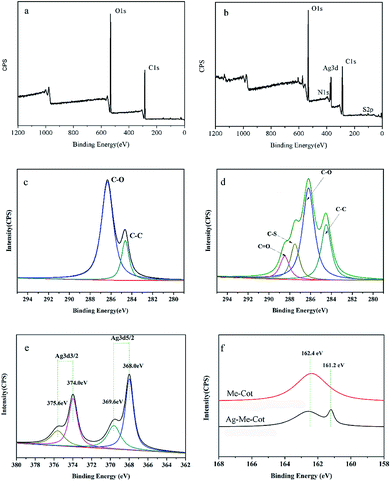 |
| Fig. 3 XPS spectra of the cotton fabrics. Wide-range and high resolution C 1s XPS spectra of Cot (a and c) and Ag-Me-Cot fabric (b and d); high resolution Ag 3d XPS spectrum of Ag-Me-Cot fabric (e) and high resolution S 2p XPS spectra of Me-Cot and Ag-Me-Cot fabrics (f). | |
Fig. 4 shows the SEM images of the cotton fabric surfaces. Cot surface is clean and smooth (Fig. 4a), but the modified cotton surfaces are rough (Fig. 4b–d). The fiber surface of Me-Cot seems covered by a layer of material (Fig. 4b), and the fiber surfaces of Ag-Me-Cot before and after washing (Fig. 4c and d) have numerous particles (Ag NPs).
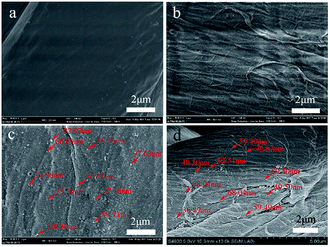 |
| Fig. 4 SEM images of the fiber surfaces. (a) Cot fiber, (b) Me-Cot, (c) Ag-Me-Cot, and (d) Ag-Me-Cot after 90 washing cycles. | |
These SEM results indicate that a lot of Ag NPs were remained on the Ag-Me-Cot surfaces even after 90 laundering cycles. The diagrams of the size distribution (calculated via the statistical analyses) of the Ag NPs are given in Fig. 5a and b, indicating that the Ag NPs loaded on the fiber surface of Ag-Me-Cot became smaller by the washing action. Moreover, the size range of the Ag NPs became more narrow (ranged from 10 to 110 nm, with an average diameter of 47.75 nm, following a normal distribution) after washed for 90 laundering cycles when compared with the Ag-Me-Cot fabric before washing (ranged from 10 to 170 nm, with an average diameter of 84.13 nm, following a positive skewed distribution). This result means that larger Ag NPs are easier to loss from the modified cotton fabrics.
 |
| Fig. 5 Size distribution of the Ag NPs loaded on the cotton fabrics. (a) Ag-Me-Cot and (b) Ag-Me-Cot after 90 washing cycles. | |
To further examine the quantities of Ag NPs on the cotton surface, ICP-MS technique was carried out on the cotton fabrics. As shown in Table 1, after 90 laundering tests, the silver content of the Ag-Me-Cot fabric was reduced by 10.2%, which in good agreement with the size reduction of the Ag NPs. These results suggest that larger Ag particles are more easily washed off from the fiber surface.
Table 1 ICP-MS analysis results of the silver content and the antibacterial effect of the cotton fabrics
Sample |
Ag (mg kg−1) |
Remaining rates of Ag (%) |
Bacterial reduction rate (%) |
E. coli |
S. aureus |
After washed for 90 laundering tests. |
Ag-Me-Cot |
250 |
— |
99.0 ± 1.0 |
99.0 ± 1.0 |
Ag-Me-Cot washeda |
220 |
89.80 |
99.0 ± 1.0 |
98.0 ± 1.0 |
3.2 Antibacterial efficacy and laundering durability
Fig. 6 shows the optical images of inhibition zones towards E. coli and S. aureus. Cot and Me-Cot fabric have no obvious bacteriostatic effect as the diameters of their inhibition zones are constant at 1.00 cm. However, in case of Ag-Me-Cot fabric, the antibacterial diameters towards E. coli and S. aureus reached to 1.74 cm (Fig. 6Ec) and 1.70 cm (Fig. 6Sc), respectively. This indicates that the bacteriostatic effect is caused by the loading of the Ag NPs.
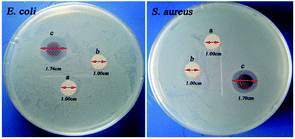 |
| Fig. 6 The optical images of the inhibition zone tests. (a) Cot, (b) Me-Cot, and (c) Ag-Me-Cot. | |
Fig. 7 shows the antimicrobial durability of the modified cotton fabrics. Although it was washed by a certain number of laundering cycles, its BR rates for both bacteria are kept at 100%. Even after 90 washing cycles, as shown in Fig. 7, the BR rates are remained over 97.7%. In other reports,7,55–57 the general durability level is that a modified cotton fabric maintains 90% BR value after 10–50 laundering cycles. Therefore, the antimicrobial results demonstrated here have significant improvement on washing durability by comparing with previous reports.
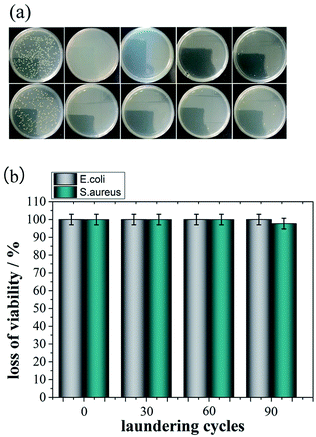 |
| Fig. 7 Antibacterial durability of Ag-Me-Cot fabric. (a) The optical images of the ager plates after the colony-forming tests, and (b) the BR rates against washing cycles. | |
As shown in the Table 1, the loss quantity of the Ag NPs (0.11%, 0.33 mg kg−1 per once laundering) is better than that reported in previous works. In addition, the silver content is about 250 mg kg−1 cotton fabric, which is far smaller than that reported early before.58–60 The improvement on immobilization of Ag NPs can be contributed to the linking effect of L-methionine.
In our earlier study, it was reported that 97.6% BR value and 10% silver loss after 50 laundering cycles can be achieved by the linking effect of L-cysteine.41 In the present work, almost same BR level (higher than 98%) and 10% silver loss are kept even until 90 consecutive laundering cycles were finished. Thus, we conclude that the outstanding antibacterial durability with fewer silver loading achieved in the present work can be contributed to the stronger affinity of L-methionine, which has an additional electron donating effect of the methyl group.
3.3 Influences on the intrinsic cotton natures
Significant damages on cotton natures are generally unacceptable. As shown in the Table 2, Ag-Me-Cot shows good vapor permeability, water absorbability, and tensile breaking strength, which very closed to that of Cot. These results indicate that the desired cotton natures are largely preserved after grating L-methionine binder and forming Ag NPs on cotton fabrics.
Table 2 Important natures of the cotton fabrics
Cotton sample |
Ventilation property (g m−2 d−1) |
Water absorption (%) |
Tensile strength (MPa) |
Cot |
1560 ± 9.0 |
246.0 ± 22.0 |
17.5 ± 0.2 |
Ag-Me-Cot |
1520 ± 13.0 |
238.0 ± 14.0 |
22.6 ± 0.3 |
4 Conclusions
L-Methionine can improve adhesive force of Ag NPs onto fiber surface of cotton. The binding effect of L-methionine gives cotton fabrics with a remarkable antibacterial durability that can keep the BR rate more than 97% even after 90 stringent laundering cycles. It is notable that such good antibacterial durability is obtained by a small amount of silver loading. The high washing durability is contributable to the coordination bonds between Ag NPs and the L-methionine moieties that grafted on the cotton fiber surface. Importantly, our finishing method does not significantly damage cotton natures such as tensile breaking strength, water absorptivity, and vapor permeability. It is believed that the finishing method has great potential for practical applications in biomedical textiles.
Conflicts of interest
The authors have no conflicts to declare.
Acknowledgements
This work was financially supported by the Natural Science Foundation of China (51573167) and Public Welfare Technology Application Research Project of Zhejiang Province (2017C31035 and 2017C33154).
Notes and references
- D. Saravanan, N. S. Vasanthi and T. Ramachandran, Carbohydr. Polym., 2009, 76, 1–7 CrossRef.
- Q. Xu, L. Xie, H. Diao, F. Li, Y. Zhang, F. Fu and X. Liu, Carbohydr. Polym., 2017, 177, 187–193 CrossRef PubMed.
- A. C. Baker, Agric. Hist., 2015, 89, 119–121 Search PubMed.
- B. Cortese, D. Caschera, G. Padeletti, G. M. Ingo and G. Gigli, Surf. Innovations, 2013, 1, 140–156 CrossRef.
- A. K. Yetisen, Q. Hang, A. Manbachi, H. Butt, M. R. Dokmeci, J. P. Hinestroza, M. Skorobogatiy, A. Khademhosseini and S. H. Yun, ACS Nano, 2016, 10, 3042–3068 CrossRef PubMed.
- H. E. Emam, N. H. Saleh, K. S. Nagy and M. K. Zahran, Int. J. Biol. Macromol., 2016, 84, 308–318 CrossRef PubMed.
- Y. Gao and R. Cranston, Text. Res. J., 2010, 60, 60–72 Search PubMed.
- M. M. G. Fouda, E. S. Abdel-Halim and S. S. Al-Deyab, Carbohydr. Polym., 2013, 92, 943–954 CrossRef PubMed.
- S. Muzaffar, I. A. Bhatti, M. Zuber, H. N. Bhatti and M. Shahid, Int. J. Biol. Macromol., 2017, 94, 51–60 CrossRef PubMed.
- O. K. Alebeid and T. Zhao, J. Text. Inst., 2017, 108, 2027–2039 CrossRef.
- G. H. Xi, W. C. Fan, L. Wang, X. D. Liu and T. Endo, J. Polym. Sci., Part A: Polym. Chem., 2015, 53, 1862–1871 CrossRef.
- L. Wang, G. H. Xi, S. J. Wan, C. H. Zhao and X. D. Liu, Cellulose, 2014, 21, 2983–2994 CrossRef.
- T. Liang, Z. Jiang, C. Wang and J. Liu, J. Appl. Polym. Sci., 2017, 134, 45114–45119 CrossRef.
- H. Yan, L. Zhao, Z. Fang and H. Wang, J. Appl. Polym. Sci., 2017, 134, 45556 CrossRef.
- Z. W. Yang, Y. Y. Zhang, F. Y. Fu and X. D. Liu, RSC Adv., 2017, 7, 53871–53877 RSC.
- W. Fan, Y. Zhu, G. Xi, M. Huang and X. D. Liu, J. Appl. Polym. Sci., 2016, 133, 43024–43030 Search PubMed.
- Y. Zhang, Q. Xu, F. Fu and X. D. Liu, Cellulose, 2016, 23, 2791–2808 CrossRef.
- X. Dai, Z. Fan, Y. Lu and P. C. Ray, ACS Appl. Mater. Interfaces, 2013, 5, 11348–11354 CrossRef PubMed.
- C. M. Courtney, S. M. Goodman, J. A. McDaniel, N. E. Madinger, A. Chatterjee and P. Nagpal, Nat. Mater., 2016, 15, 529–534 CrossRef PubMed.
- M. Salat, P. Petkova, J. Hoyo, I. Perelshtein, A. Gedanken and T. Tzanov, Carbohydr. Polym., 2018, 189, 198–203 CrossRef PubMed.
- J. Lin, X. Chen, C. Chen, J. Hu, C. Zhou, X. Cai, W. Wang, C. Zheng, P. Zhang and J. Cheng, ACS Appl. Mater. Interfaces, 2018, 10, 6124–6136 CrossRef PubMed.
- L. Li, X. Chi, F. Gai, H. Zhou, F. Zhang and Z. Zhao, J. Appl. Polym. Sci., 2017, 134, 45323 CrossRef.
- G. Luo, G. Xi, X. Wang, D. Qin, Y. Zhang, F. Fu and X. Liu, J. Appl. Polym. Sci., 2017, 134, 44897–44903 Search PubMed.
- G. Xi, Y. Xiu, L. Wang and X. Liu, J. Appl. Polym. Sci., 2015, 132, 41824–41830 CrossRef.
- G. Sun, J. Chem. Educ., 2005, 82, 5 CrossRef.
- D. A. Mosselhy, H. Granbohm, U. Hynonen, Y. Ge, A. Palva, K. Nordstrom and S. P. Hannula, Nanomaterials, 2017, 7, 7090261–7090279 CrossRef PubMed.
- T. T. T. Vi, S. Rajesh Kumar, B. Rout, C. H. Liu, C. B. Wong, C. W. Chang, C. H. Chen, D. W. Chen and S. J. Lue, Nanomaterials, 2018, 8, 8030162–8030177 CrossRef PubMed.
- S. Gomez-Grana, M. Perez-Ameneiro, X. Vecino, I. Pastoriza-Santos, J. Perez-Juste, J. M. Cruz and A. B. Moldes, Nanomaterials, 2017, 7, 7060139–7060153 CrossRef PubMed.
- F. Tanvir, A. Yaqub, S. Tanvir and W. A. Anderson, Nanomaterials, 2017, 7, 7100296–7100310 CrossRef PubMed.
- M. C. Sportelli, R. A. Picca, F. Paladini, A. Mangone, L. C. Giannossa, C. D. Franco, A. L. Gallo, A. Valentini, A. Sannino, M. Pollini and N. Cioffi, Nanomaterials, 2017, 7, 7080203–7080218 CrossRef PubMed.
- S. León-Silva, F. Fernández-Luqueño and F. López-Valdez, Water, Air, Soil Pollut., 2016, 227, 305–325 CrossRef.
- Y. Li, Y. Zhang and B. Yan, Int. J. Mol. Sci., 2014, 15, 3671–3697 CrossRef PubMed.
- H. Xu, X. Shi, H. Ma, Y. Lv, L. Zhang and Z. Mao, Appl. Surf. Sci., 2011, 257, 6799–6803 CrossRef.
- D. Zhang, L. Chen, C. Zang, Y. Chen and H. Lin, Carbohydr. Polym., 2013, 92, 2088–2094 CrossRef PubMed.
- W. Zhu, M. Kuang, S. Wei, T. Duan, Y. Wang, D. Zhou, L. Ma, D. Fang, J. Zhou and W. Yang, J. Exp. Nanosci., 2015, 11, 471–479 CrossRef.
- Y. Di, Q. Li and X. Zhuang, J. Eng. Fibers Fabr., 2012, 7, 24–29 Search PubMed.
- M. K. Zahran, H. B. Ahmed and M. H. El-Rafie, Carbohydr. Polym., 2014, 108, 145–152 CrossRef PubMed.
- M. Montazer, F. Alimohammadi, A. Shamei and M. K. Rahimi, Colloids Surf., B, 2012, 89, 196–202 CrossRef PubMed.
- M. Gouda, A. Aljaafari, Y. Al-Fayz and W. E. Boraie, J. Nanomater., 2015, 16, 1–9 Search PubMed.
- L. M. Liu and B. Deng, Sci. Rep., 2014, 4, 5920–5929 CrossRef PubMed.
- Q. Xu, J. Gu, Y. Zhao, X. Ke and X. D. Liu, Fibers Polym., 2017, 18, 2204–2211 CrossRef.
- Q. B. Xu, Y. H. Wu, Y. Y. Zhang, F. Y. Fu and X. D. Liu, Fibers Polym., 2016, 17, 1782–1789 CrossRef.
- Q. Xu, X. Ke, L. Shen, N. Ge, Y. Zhang, F. Fu and X. D. Liu, Int. J. Biol. Macromol., 2018, 111, 796–803 CrossRef PubMed.
- H. Qi, Y. Huang, B. Ji, G. Sun, F. L. Qing, C. Y. Hu and K. L. Yan, Carbohydr. Polym., 2016, 135, 86–93 CrossRef PubMed.
- C. Schramm, B. Rinderer and R. Tessadri, Carbohydr. Polym., 2014, 105, 81–89 CrossRef PubMed.
- Q. Xu, X. Ke, D. Cai, Y. Zhang, F. Fu, T. Endo and X. D. Liu, Cellulose, 2018, 25, 2129–2141 CrossRef.
- V. Prysiazhnyi, A. Kramar, B. Dojcinovic, A. Zekic, B. M. Obradovic, M. M. Kuraica and M. Kostic, Cellulose, 2013, 20, 315–325 CrossRef.
- M. Zhang, J. Pang, W. Bao, W. Zhang, H. Gao, C. Wang, J. Shi and J. Li, Appl. Surf. Sci., 2017, 419, 16–23 CrossRef.
- J. Wang, G. Xi, G. Luo and X. D. Liu, Cellulose, 2016, 23, 915–927 CrossRef.
- W.-G. Kwak, M. H. Oh and M.-S. Gong, Carbohydr. Polym., 2015, 115, 317–324 CrossRef PubMed.
- X.-Y. Gao, S.-Y. Wang, J. Li, Y.-X. Zheng, R.-J. Zhang, P. Zhou, Y.-M. Yang and L.-Y. Chen, Thin Solid Films, 2004, 455–456, 438–442 CrossRef.
- D. Wang, Y. Duan, Q. Luo, X. Li and L. Bao, Desalination, 2011, 270, 174–180 CrossRef.
- I. Lopez-Salido, D. C. Lim and Y. D. Kim, Surf. Sci., 2005, 588, 6–18 CrossRef.
- F. Porcaro, L. Carlini, A. Ugolini, D. Visaggio, P. Visca, I. Fratoddi, I. Venditti, C. Meneghini, L. Simonelli, C. Marini, W. Olszewski, N. Ramanan, I. Luisetto and C. Battocchio, Materials, 2016, 9, 1–15 CrossRef PubMed.
- A. Hebeish, A. El-Shafei, S. Sharaf and S. Zaghloul, Carbohydr. Polym., 2011, 84, 605–613 CrossRef.
- N. A. Ibrahim, B. M. Eid, T. M. Elmaaty and E. A. Elaziz, Carbohydr. Polym., 2013, 94, 612–618 CrossRef PubMed.
- X. Yue, H. Lin, T. Yan, D. Zhang, H. Lin and Y. Chen, Fibers Polym., 2014, 15, 716–722 CrossRef.
- T. Jiang, L. Liu and J. Yao, Fibers Polym., 2011, 12, 620–625 CrossRef.
- H. Liu, Y.-Y. Lee, T. B. Norsten and K. Chong, J. Ind. Text., 2013, 44, 198–210 CrossRef.
- D. Klemenčič, B. Tomšič, F. Kovač, M. Žerjav, A. Simončič and B. Simončič, J. Mater. Sci., 2014, 49, 3785–3794 CrossRef.
|
This journal is © The Royal Society of Chemistry 2018 |
Click here to see how this site uses Cookies. View our privacy policy here.