DOI:
10.1039/C8RA02472C
(Paper)
RSC Adv., 2018,
8, 17151-17158
A novel green process for tannic acid hydrolysis using an internally sulfonated hollow polystyrene sphere as catalyst
Received
21st March 2018
, Accepted 27th April 2018
First published on 10th May 2018
Abstract
A polystyrene-hollow sphere catalyst was prepared by treating polystyrene-encapsulated calcium carbonate particles with concentrated hydrochloric acid. This catalyst was characterized using TGA, FT-IR, optical microscope, SEM-EDX and XPS. Evidences from SEM-EDX and XPS analyses indicated that the sulfonate groups were on the inner surface of the polystyrene hollow sphere. The polystyrene hollow spheres were used as catalyst in the hydrolysis of tannic acid. Reaction conditions including the reaction temperature and time, loading of catalyst, ratio of tannic acid to H2O and number of recycles were optimized. A high yield of gallic acid was obtained as the reaction performed under the following conditions: a temperature of 80 °C, a molar ratio of tannic acid to H2O of 1
:
3, and a catalyst loading of 7% w/w (based on the mass of tannic acid). This catalyst showed excellent catalytic performance, easy separation, high stability and good reusability. This work provides a new strategy for the controllable synthesis of polystyrene hollow structures with sulfonic groups on the inner surface and an excellent and prospective catalyst for the production of gallic acid through hydrolysis of tannic acid.
Introduction
Gallic acid is an important chemical that has various properties, such as anti-fungal, anti-viral, antioxidant, and anti-cancer activities (Fiuza et al., 2004; Zaheer et al., 2010).1–3 It is widely used in organic synthesis, pharmaceutics, food etc.4–6 Gallic acid is mainly produced by the hydrolysis of tannic acid, a specific form of tannin obtained from Chinese gall. There are a few typical catalysts used for hydrolysis of tannic acid including inorganic bases,7 inorganic acids,8 enzymes, and sulfonic ionic resins.9 In the cases using inorganic bases and acids as catalysts, a lot of wastewater is produced, which is difficult to be treated. In addition, corrosion of the equipment and tedious purification are also faced in typical production process. In the case using enzyme9–12 as catalyst, shortages including high cost of tannase, deactivation of enzyme and non-recyclable, low efficiency limit the application of the enzymatic method for gallic acid production in industry. Strongly acidic ion exchange resins could be useful in the sulfonic catalyzed hydrolysis of tannic acid, but commercialized ionic exchange resins still cannot improve the efficiency of tannic acid hydrolysis due to following reasons: the absence of specific affinity between the reactant molecules and the ion exchange resins; the lower diffusion and concentration of reactant inside the resin cavities because of the large size of tannic molecules and relative higher cross-link density of ionic resins. Thus, environmentally friendly catalysts with high efficiency are need for the industrial production of gallic acid from tannic acid. In fact, there are a number of previous studies where sulfonated solid acids were prepared and used in biomass-related reactions.13–16
In this paper, a polystyrene hollow sphere with sulfonic groups on the inner surface was prepared to improve the diffusion of reactants, and the structure of the polystyrene hollow sphere was characterized. In addition, its catalytic performance was tested for the hydrolysis of tannic acid.
Experimental section
Materials
Light calcium carbonate (2 μm < d < 5 μm) was purchased from Zhangjiajie Hengliang New Material Technology Co., Ltd. (Hunan Province, China). Analytical grade styrene and divinylbenzene were purchased from Shanghai Yongda Chemical Reagent Co., Ltd. (Shanghai, China). Analytical grade vinyl benzenesulfonic acid was purchased from Shanghai Aladdin Reagent Co., Ltd. (Shanghai, China). Benzoyl peroxide (BPO), methyl alcohol, phosphoric acid, AgNO3, NaOH and NaCl were purchased from Tianjin Chemical Reagent Co., Ltd. (Tianjin, China). Tannic acid (>95%) was purchased from Zhangjiajie JiuRui Biological Technology Co., Ltd. (Hunan Province, China). Distilled water was used throughout this experiment. All chemicals were used without further purification.
Synthesis of internally sulfonated polystyrene hollow sphere
50 g of light calcium carbonate was added into 100 mL of ethyl alcohol in a three-necked flask equipped with a mechanical stir. This mixture was homogenized for 30 min at 80 °C at a speed of 2000 rpm. Then 3.5 g of vinyl benzenesulfonic acid was added. The mixture continued to be stirred at a speed of 400 rpm at 80 °C for 2 h. Subsequently, 0.105 g of styrene, 0.105 g of divinyl benzene, and 0.07 g of BPO were added independently. After 2 h, this suspended mixture was cooled to room temperature, and the resulted solid particles were separated and collected by centrifugation. Then, they were washed with ethyl alcohol, and subsequently dried at 80 °C under vacuum for 12 h to obtain the polystyrene-coated calcium carbonate. The internally sulfonated polystyrene hollow spheres were obtained by removing calcium carbonate from polystyrene-coated calcium carbonate using hydrochloric acid (36% w/w). This polystyrene hollow spheres were further treated by repeatedly washing using distilled water until no hydrogen chloride was detected by AgNO3 solution test. After being dried at 40 °C under vacuum for 12 h, 4.8 g of polystyrene hollow sphere with catalytic property was obtained. The scheme for the preparation of sulfonated polystyrene hollow sphere is shown in Fig. 1.
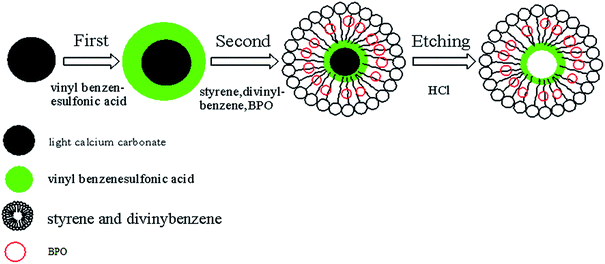 |
| Fig. 1 The scheme for the preparation of sulfonated polystyrene hollow sphere. | |
Characterization
Thermogravimetric analysis (TGA) was performed on a Netzsch STA409PC instrument (Bavaria, Germany) under a flowing nitrogen atmosphere at a scan rate of 20 °C min−1 from room temperature to 1000 °C using α-Al2O3 as the standard material. TGA results reported were the average of a minimum of three determinations. Temperatures were reproducible to ±3 °C, and the error bars on the fraction of nonvolatile material were ±1%. Fourier-transform infrared (FT-IR) spectra of the samples were obtained using a WQF-200 spectrometer (Rayleigh, China) over a frequency range of 400–4000 cm−1. The samples were mixed with KBr and pressed in the form of pellets for FT-IR analysis. Optical microscopic images of the samples were obtained using a N-180M microscope (Shanghai, China). The scanning electron microscopy (SEM) was performed on a FEI Nova NanoSEM 450 instrument (Hillsboro, America), and analyses were carried out on a Nova NanoSEM 450 equipped with an energy-dispersive X-ray analyzer. XPS measurements were carried out on a Shimadzu ESCA-3200 (Tokyo, Japan) using Al Kα radiation. The catalyst was titrated with aqueous NaOH solution to determine the amount of catalytic –SO3H group in it. In a typical procedure, 20 mg of the sample was suspended in 10 mL of 2 mol L−1 aqueous NaCl solution for 24 h at room temperature, then this suspension was filtrated, and the resulting solution was titrated with 0.05 mol L−1 aqueous NaOH solution.12 The amount of catalytic –SO3H group was calculated from the amount of NaOH used in the above titration reaction. The samples were quantitatively analyzed by HPLC with UV detector. The HPLC column was Phenomenex C18 (5 μm, 250 mm × 4.6 mm ID). The mobile phase was a mixture of methyl alcohol, phosphoric acid and H2O in a volume ratio of 15
:
0.5
:
100 at a flow rate of 0.5 mL min−1. The temperature of column was 30 °C and the wavelength was 280 nm.
The yield of gallic acid was calculated by the following equation:
where
Y is yield of gallic acid;
mGA is mass of gallic acid (determined by HPLC);
mTA is mass of tannic acid;
wTA is mass percentage of gallic acid to tannic acid after complete hydrolysis.
wTA was experimentally obtained as 80.3%.
Catalytic performance
The polystyrene hollow spheres were used as catalyst in the hydrolysis of tannic acid. In a typical reaction, 200 g of tannic acid and 600 mL of H2O were added in a three-necked flask equipped with magnetic stirring bars and water-separation apparatus. After being stirred for 30 min, 7% w/w of catalyst (based on the mass of tannic acid) was added. The reaction temperature and time were set at 80 °C and 6 h, respectively. Then, the solution was cooled down. Reaction process was monitored using HPLC. The reaction temperature and time, the amount of polystyrene hollow sphere, the concentration of tannic acid, and the recycling of catalyst were optimized and evaluated.
Results and discussion
Characterization of catalysts
TGA analysis. In this experiment, the thermal stability of polystyrene hollow sphere was evaluated using TGA, and the experimental results were shown in Fig. 2.
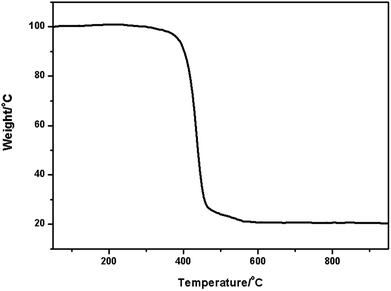 |
| Fig. 2 Typical TGA curve of polystyrene hollow sphere. | |
TGA analysis information includes the 5% weight loss temperature (T5%), the initial degradation temperature, the 50% weight loss temperature (T50%), the degradation temperature, and the char content (residual weight percent at 950 °C).13 Fig. 2 indicates that the samples began to lose weight at 300 °C, which is due to the thermal degradation of polystyrene hollow sphere. It is evident that the prepared polystyrene hollow sphere is thermally stable below 300 °C, which would be the upper limit temperature of the hydrolysis of tannic acid.
Optical microscopic analysis. Optical microscope was used to obtain the particle sizes of light calcium carbonate, polystyrene-coated calcium carbonate, and polystyrene hollow sphere. The images are shown in Fig. 4.
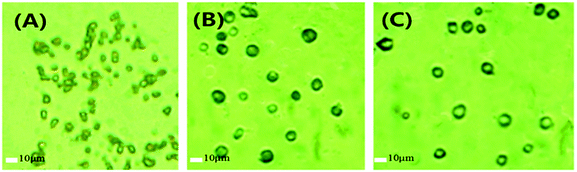 |
| Fig. 4 The optical microscopic images of (A) light calcium carbonate, (B) polystyrene-coated calcium carbonate, and (C) polystyrene hollow sphere. | |
Light calcium carbonates have irregular shapes and the particle sizes are in the range of 2–5 μm (Fig. 4A). The light calcium carbonate was coated with polystyrene to obtain polystyrene-coated calcium carbonate. The polystyrene-coated calcium carbonate has smooth surface and the sizes increase to be in the range of 5–10 μm (Fig. 4B). Polystyrene-coated calcium carbonate was treated with hydrochloric acid solution to obtain polystyrene hollow sphere. Polystyrene-coated calcium carbonate and polystyrene hollow sphere have no significant difference in particle size and shape. The prepared polystyrene hollow sphere has a smooth surface with a size of 5–10 μm (Fig. 4C). From the perspective of catalyst, the size of polystyrene hollow sphere meets the size requirement of a high-performance catalyst.
SEM-EDX and XPS analyses. SEM-EDX and XPS analyses were performed on the polystyrene hollow sphere to determine the position of –SO3H groups. SEM-EDX is an X-ray technique used to reveal the elemental composition of materials. SEM-EDX analysis results consist of spectra showing peaks corresponding to the elements making up the true composition of the analyzed sample.19 SEM-EDX analysis of the polystyrene hollow sphere are shown in Fig. 5. There is no evidence for the presence of S element on the outer surface of polystyrene hollow sphere.
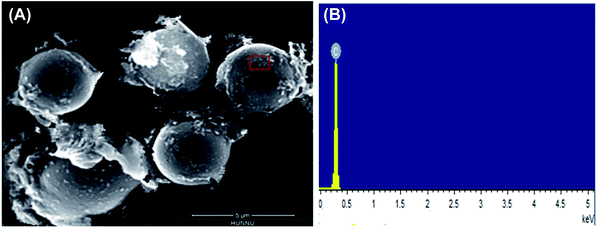 |
| Fig. 5 SEM image (A) and EDX analysis results (B) of polystyrene hollow sphere. Red box in (A) denotes the region analyzed by EDX (B). | |
This polystyrene hollow sphere was also characterized by XPS to determine the elementary composition and valence state.
As shown in Fig. 6, the peak at binding energy of 1196.7 eV was assigned to C1s, confirming that the catalyst was composed of C. There is no peak at the binding energy of S, indicating no sulfonic group on the interior of the polystyrene hollow sphere.20 We magnified the XPS spectra near the positions where peaks of S occur, but the peaks of S were still not found (see the following Fig. 7). Both XPS and SEM-EDX analysis results demonstrate that there is no element S present on the outer surface of the polystyrene hollow sphere. Considering the IR analysis results, we inferred that SO3H groups should be on the inner surface of the polystyrene hollow sphere.
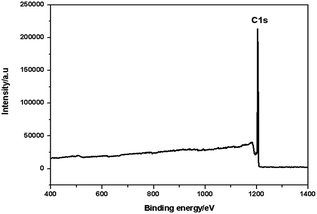 |
| Fig. 6 XPS spectra of polystyrene hollow sphere. | |
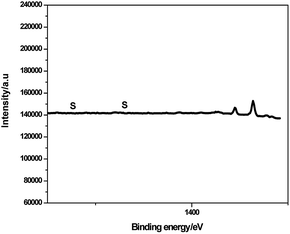 |
| Fig. 7 XPS spectra of polystyrene hollow sphere (magnified the XPS spectra near the positions where peaks of S occur). | |
Application in the hydrolysis of tannic acid. Weighed amounts of tannic acid and H2O (in a molar ratio of 1
:
3), as well as polystyrene hollow sphere (7% w/w, based on the mass of tannic acid) were added to a 500 mL three-necked round bottomed glass flask equipped with a water-cooled condenser and a magnetic stirrer. The temperature of the reaction mixture was controlled using a temperature controller with an accuracy of ±0.5 °C. The hydrolysis reaction of tannic acid (Fig. 8) was allowed to proceed for 0.5–6 h with vigorous stirring at the designed temperature. Then, the solution was cooled down. Subsequently, the amount of tannic acid in the reaction mixture was determined by HPLC.
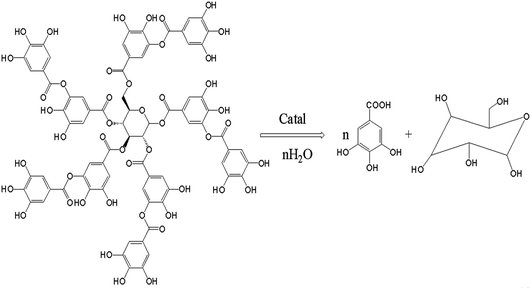 |
| Fig. 8 Hydrolysis of tannic acid using polystyrene hollow sphere as catalyst. | |
The influences of (A) reaction time, (B) reaction temperature, (C) molar ratio of reactants, (D) loading of polystyrene hollow sphere and (E) number of recycles on the tannic acid hydrolysis were evaluated (Fig. 9).
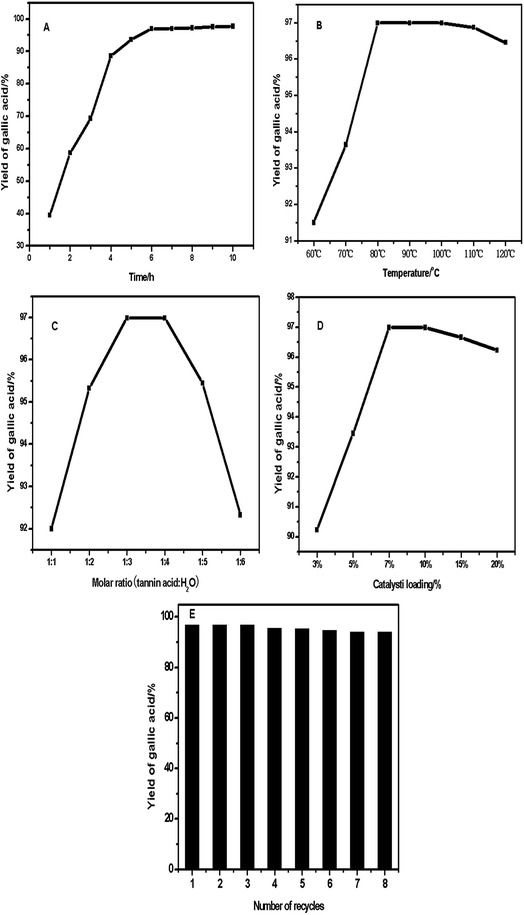 |
| Fig. 9 Yield of gallic acid using polystyrene hollow sphere as catalyst (A) yield vs. reaction time; (B) yield vs. reaction temperature; (C) yield vs. molar ratio of reactants; (D) yield vs. catalyst loadings; (E) yield vs. number of recycles. | |
Fig. 9A shows the time course of yield of gallic acid at 80 °C, molar ratio of tannic acid to H2O of 1
:
3, and polystyrene hollow sphere loading of 7% w/w (based on the mass of tannic acid). At first, the yield of gallic acid increased with the reaction time and reached 96.99% at 6 h of reaction. With further extension of reaction time, the yield remained almost unchanged and the yield at 10 h increased little compared with that at 6 h.
Fig. 9B shows the effect of reaction temperature on the yield of gallic acid. Reaction temperature was set in the range of 60–120 °C, while other reaction conditions were set as follows: molar ratio of tannic acid to H2O of 1
:
3, reaction time of 6 h and polystyrene hollow sphere loading of 7% w/w. At 60 °C, the yield of gallic acid was 91.5%. As the temperature increased from 60 to 80 °C, the hydrolysis rate and the yield of gallic acid increased rapidly and significantly. As the temperature further increased from 110 to 120 °C, the yield of gallic acid slightly decreased. This indicates that gallic acid might be converted to pyrogallic acid or other by-products. Fig. 9C shows the effect of the molar ratio of tannic acid to H2O on the hydrolysis reaction. The molar ratio ranged from 1
:
1 to 1
:
6, at a reaction temperature of 80 °C, a reaction time of 6 h, polystyrene hollow sphere loading of 7% w/w. Fig. 8C indicates that the yield of gallic acid increases first and then decreases as the molar ratio changes from 1
:
1 to 1
:
6. The optimum molar ratio was found to be 1
:
3 in order to obtain the maximum yield of gallic acid. In the reaction system, water serves as both solvent and reactant. At first, with the increase in water content, more tannic acids are dissolved into water and the viscosity of the reaction system decreases, which is conducive to dispersion of reactants and enhancement of mass transfer. As a result, the yield of gallic acid increases. However, with further increase in water content, the concentration of tannic acid decreases, which results in decrease in yield of gallic acid. Fig. 9D shows the effect of polystyrene hollow sphere loading on the yield of tannic acid. The polystyryl hollow sphere loading was set at 3%, 5%, 7%, 10%, 15% and 20% w/w (based on the mass of tannic acid), respectively. Other reaction conditions included reaction temperature of 80 °C, reaction time of 6 h, and molar ratio of tannic to H2O of 1
:
3. All loadings of polystyrene hollow sphere could ensure a yield no lower than 90.5% (Fig. 9D). All above experimental results indicate a high catalytic performance of polystyrene hollow sphere.21 Note that the yield of gallic acid decreases when the polystyryl hollow sphere loading is above about 10%. This might be related to the calcium ions in polystyrene hollow sphere. As the polystyrene hollow sphere loading increases, the amount of calcium ions also increases. Gallic acid produced by hydrolysis of tannic acid might react with calcium ions to form by-products, thus affecting the yield of gallic acid. Considering both the reaction rate and the cost of polystyrene hollow sphere, 7% w/w was taken as the optimum polystyrene hollow sphere loading and used in most of the hydrolysis experiments.
Fig. 9E shows the effect of the number of recycle times on the activity and stability of polystyrene hollow sphere. After each cycle, the polystyrene hollow spheres were separated from the reaction mixture by decantation and then washed with water, followed by drying before the next run. Other reaction conditions included a reaction temperature of 80 °C, a reaction time of 6 h, a molar ratio of tannic acid to H2O of 1
:
3, and polystyrene hollow sphere loading of 7% w/w.22–25 The experimental results indicate that the catalyst is stable enough to be recycled for many times. However, it is worth noting that the yield rate decreases slightly after the catalyst has been reused for 8 times. In order to find the reason for this trend, we performed XPS and SEM-EDX analyses of this catalyst before and after use (Fig. 10 and 11). Fig. 10 suggests that the intensity of the peak assigned to S decreases after the catalyst has been reused for 8 times. Fig. 11 shows that the peak corresponding to S shrinks after the catalyst has been reused for 8 times. It is thus inferred that the content of sulfonic groups in the catalyst decreases as the number of recycle times increases. This can lead to the degradation of the performance of catalyst and therefore decrease in the yield of gallic acid.
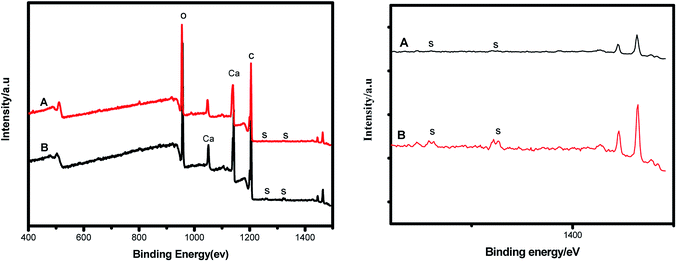 |
| Fig. 10 XPS spectra of polystyrene hollow sphere (A), reused for 8 times; (B), not used. | |
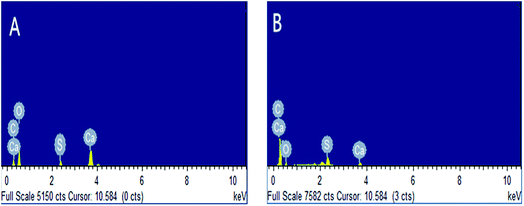 |
| Fig. 11 SEM-EDX analysis results of polystyrene hollow sphere (A), reused for 8 times; (B), not used. | |
The hydrolysis of tannic acids in the presence of four different catalysts including polystyrene hollow sphere, amberlite XAD-16, BC-SO3H, PRPC-SO3H were conducted to assess their catalytic activities under reaction conditions including a temperature of 80 °C, molar ratio of tannic acid to H2O of 1
:
3, and polystyrene hollow sphere loading of 7% w/w (based on the mass of tannic acid). The experimental data are listed in Table 1.
Table 1 Experimental results on the synthesis of hydrolysis of tannic acid is catalyzed by polystyryl hollow sphere and other common catalystsa
Catalysts (SO3H/mmol g−1) |
Conversion rate/% |
Yields |
1 h |
2 h |
3 h |
4 h |
5 h |
6 h |
(1) polystyrene hollow spheres; (2) amberlite XAD-16; (3) BC-SO3H; (4) PRPC-SO3H. |
1 (1.24 mmol g−1) |
90.90 |
93.84 |
94.90 |
96.92 |
99.92 |
99.85 |
98.9 |
2 (1.24 mmol g−1) |
74.70 |
84.29 |
91.97 |
92.00 |
93.07 |
93.14 |
94.0 |
3 (1.24 mmol g−1) |
80.45 |
83.87 |
97.12 |
97.87 |
97.71 |
97.20 |
97.0 |
4 (1.24 mmol g−1) |
84.56 |
85.73 |
87.26 |
86.29 |
87.98 |
87.54 |
87.6 |
The comparison experimental results indicate that the polystyrene hollow sphere has the highest performance as a catalyst for hydrolysis of tannic acid under the same reaction conditions with the same amount of sulfonic groups. The excellent catalytic performance of polystyrene hollow sphere might be attributed to its porous hollow structure, which is conducive to enhancing mass transfer.
Conclusions
This study provides a new strategy for the controllable synthesis of hollow structures with sulfonic groups on the inner surface. And this polystyrene hollow sphere has high performance as a green catalyst in the hydrolysis of tannic acid to obtain gallic acid. This polystyrene hollow sphere prepared in this study might be used as an excellent and prospective catalyst for the hydrolysis of high-molecule weight nature chemicals.
Conflicts of interest
There are no conflicts to declare.
Acknowledgements
This work was supported by the Xiaoxiang Scholar Sponsorship of Hunan Normal University and the National Natural Science Foundation of China (No. 21606082).
References
- S. Kambourakis, K. M. Draths and J. W. Frost, Synthesis of Gallic Acid and Pyrogallol from Glucose: Replacing Natural Product Isolation with Microbial Catalysis, J. Am. Chem. Soc., 2000, 9042–9043 CrossRef CAS.
- H. Wang, H. Tang and J. Wilson, et al., Total Acid Number Determination of Biodiesel and Biodiesel Blends, J. Am. Oil Chem. Soc., 2008, 85(11), 1083–1086 CrossRef CAS.
- J. Zhao, I. A. Khan and F. R. Fronczek, Gallic acid, Acta Crystallographica, 2011, 67(67), 316–317 Search PubMed.
- C. M. González, J. R. Aguilera and A. P. Zaderenko, Synthesis of Tannic acid and Gallic acid nanostructures with biomedical applications, Biosaia, 2017 Search PubMed.
- A. M. Chacón, A. B. Fuentes and A. P. Zaderenko Partida, Synthesis and Characterization of a Gallic Acid Metal Organic Framework for Antitumoral Therapy, Biosaia, 2016 Search PubMed.
- K. P. Sharma, P. J. John and P. Goswami, et al., Enzymatic synthesis of gallic acid from tannic acid with an inducible hydrolase of Enterobacter spp, Biocatal. Biotransform., 2017, 1–8 Search PubMed.
- J. Yao, G. S. Guo and G. H. Ren, et al., Production, characterization and applications of tannase, J. Mol. Catal. B: Enzym., 2014, 101(2), 137–147 CrossRef CAS.
- J. Fu, Y. Zhang and X. Lu, A Greener Process for Gallic Acid Production from Tannic Acid Hydrolysis with Hydrochloric Acid, Asian J. Chem., 2015, 27(9), 3328–3332 CrossRef CAS.
- P. F. Siril, N. R. Shiju and D. R. Brown, et al., Optimising catalytic properties of supported sulfonic acid catalysts, Appl. Catal., A, 2009, 364(1), 95–100 CrossRef CAS.
- F. Lara-Victoriano, F. Veana and F. D. Hernndez-Castillo, et al., Variability among strains of Aspergillus section Nigri with capacity to degrade tannic acid isolated from extreme environments, Arch. Microbiol., 2017, 199(1), 77–84 CrossRef CAS PubMed.
- J. A. Curiel, L. Betancor and R. B. De l, et al., Hydrolysis of tannic acid catalyzed by immobilized-stabilized derivatives of Tannase from Lactobacillus plantarum, J. Agric. Food Chem., 2010, 58(10), 6403–6409 CrossRef CAS PubMed.
- M. Gielen, M. Biesemans and V. D. De, et al., Purification and characterization of tannase from Paecilomyces variotii: Hydrolysis of tannic acid using immobilized tannase, Appl. Microbiol. Biotechnol., 2006, 70(4), 444–450 CrossRef PubMed.
- E. L. S. Ngee, Y. Gao and C. Xi, et al., Sulfated Mesoporous Niobium Oxide Catalyzed 5-Hydroxymethylfurfural Formation from Sugars, Ind. Eng. Chem. Res., 2014, 53(37), 14225–14233 CrossRef CAS.
- Y. Peng, Z. Hu and Y. Gao, et al., Synthesis of a Sulfonated Two-Dimensional Covalent Organic Framework as an Efficient Solid Acid Catalyst for Biobased Chemical Conversion, Chemsuschem, 2015, 8(19), 3208–3212 CrossRef CAS PubMed.
- Z. Hu and Y. Peng, et al., Direct Synthesis of Hierarchically Porous Metal–Organic Frameworks with High Stability and Strong Brønsted Acidity: The Decisive Role of Hafnium in Efficient and Selective Fructose Dehydration, Chem. Mater., 2016, 28, 2659–2667 CrossRef CAS.
- Y. Wang, S. De and N. Yan, Rational control of nano-scale metal-catalysts for biomass conversion, Chem. Commun., 2016, 52, 6210–6224 RSC.
- S. Chen, J. Li and Y. Zhu, et al., Increasing the efficiency of intumescent flame retardant polypropylene catalyzed by polyoxometalate based ionic liquid, J. Mater. Chem. A, 2013, 1(48), 15242–15246 CAS.
- B. Erdem and A. Kara, Sulfonic acid functionalized poly (ethylene glycol dimethacrylate-1-vinyl-1,2,4-triazole) as an efficient catalyst for the synthesis of methyl propionate, React. Funct. Polym., 2011, 71(2), 219–224 CrossRef CAS.
- A. Amoozadeh and S. Rahmani, Nano-WO 3 -supported sulfonic acid: New, efficient and high reusable heterogeneous nano catalyst, J. Mol. Catal. A: Chem., 2015, 396, 96–107 CrossRef CAS.
- P. Gogoi, A. K. Dutta and P. Sarma, et al., Development of Brönsted–Lewis acidic solid catalytic system of 3-methyl-1-sulfonic acid imidazolium transition metal chlorides for the preparation of bis (indolyl)methanes, Appl. Catal., A, 2015, 492, 133–139 CrossRef CAS.
- X. Liu, J. Xiao, H. Ding, W. Zhong, Q. Xu, S. Su and D. Lin, Chem. Eng. J., 2015, 283, 1315–1321 CrossRef.
- S. Zhang, Q. Fan and H. Gao, et al., Formation of Fe3O4@MnO2 ball-in-ball hollow spheres as a high performance catalyst for enhanced catalytic performances, J. Mater. Chem. A, 2015, 4(4), 1414–1422 Search PubMed.
- F. Adam and C. W. Kueh, Heterogeneous para -phenylamino sulfonic acid ligand functionalized on MCM-41 derived from rice husk ash: Selective mono-alkylated products of tert -butylation of phenol, Appl. Catal., A, 2015, 489(3), 162–170 CrossRef CAS.
- P. Neubert, I. Meier and T. Gaide, et al., First telomerisation of piperylene with morpholine using palladium–carbene catalysts, Catal. Commun., 2016, 77, 70–74 CrossRef CAS.
- S. P. Chopade and M. S. Man, Reaction of ethanol and formaldehyde: use of versatile cation-exchange resins as catalyst in batch reactors and reactive distillation columns, React. Funct. Polym., 1997, 32(1), 53–65 CrossRef CAS.
|
This journal is © The Royal Society of Chemistry 2018 |
Click here to see how this site uses Cookies. View our privacy policy here.