DOI:
10.1039/C8RA01154K
(Paper)
RSC Adv., 2018,
8, 23442-23450
Silicate silver/flower-like magnalium hydroxide composites for enhanced visible light photodegradation activities
Received
24th February 2018
, Accepted 10th June 2018
First published on 27th June 2018
Abstract
Flower-like magnalium layered composites (MgAl-LDH) were first fabricated by a hydrothermal method, and a series of AgSiOx/MgAl-LDH composites with different mole ratios was successfully prepared by loading AgSiOx on the MgAl-LDH surface. The photocatalytic activities of the composites for the degradation of methylene blue (MB) were investigated under visible light irradiation (xenon lamp). The prepared AgSiOx/MgAl-LDH composites were characterized by X-ray diffraction (XRD), scanning electron microscopy (SEM), transmission electron microscopy (TEM), UV-vis diffuse reflectance spectroscopy, thermogravimetric analysis (TG), and X-ray photoelectron spectroscopy (XPS). The results revealed that AgSiOx/MgAl-LDH (5
:
1) displayed a photocatalytic degradation efficiency of 99.7% in 30 min for MB. The photocatalytic degradation rate was higher than that of pure AgSiOx.
Introduction
The increase in demand for textiles, leather, and other industries has resulted in the generation of a large number of organic dye pollutants, which are difficult to treat because of their large volumes and high concentrations. Therefore, the disposal of dye wastewater in an environmentally friendly manner with high efficiency has become a matter of pressing concern.1–4 Among the multiple approaches for handling dye wastewater, photocatalytic technology can decompose organic matter into inorganic ions and water at normal temperature and pressure without secondary pollution.5,6 Hence, semiconductor photocatalysts have received significant attention since Fujishima et al.7 reported in 1972 that TiO2 electrodes can achieve photocatalytic splitting of water. However, the practical application of traditional semiconductor photocatalysts has been limited due to their wide band gaps, quick combination of photogenerated holes, and narrow absorption spectra.8,9 Thus, it is desirable to develop a highly efficient photocatalyst that is active in the visible light to improve the utilization of sunlight.
Silver silicate (AgSiOx) is a novel type of photocatalyst developed in recent years. There are three kinds of ligands in silver silicate, namely, AgO2, AgO3, and AgO4, which are favorable for the separation of photoelectrons and holes; the narrow band gap (1.58 eV) results in very strong photocatalytic activity in the entire visible light region (λ < 740 nm), and the photocatalytic degradation efficiency of methylene blue (MB) is much higher than those of Ag2O and Ag3PO4 under visible light.10 In addition, silver silicate can be combined with other materials such as Ag6Si2O7/WO3,11 Ag6Si2O7/α-Fe2O3,12 and Ag6Si2O7@RGO to improve the photocatalytic performance.13 However, the high cost of silver salts limits its application. Therefore, herein, to reduce the cost and enhance photocatalytic activity, we choose layered double hydroxides as a catalyst carrier.
Layered double hydroxides (LDHs) are a class of anionic clays or layered compounds. The general formula of LDHs can be represented by [M2+1−xM3+x(OH)2]x+(An−)n/x·yH2O, where M2+ and M3+ are the divalent and trivalent metal cations, respectively, and An− is an interlayer anion.14–16 LDHs have received much interest because of their special layered structures, stability, exchangeable ions in the interlayer, and large surface area, due to which they can be used as ideal candidates for the preparation of composites with catalysts or catalyst supports.17–21 In addition, LDHs can display unique optical properties through the introduction of functional anions or upon organo-modification, which can be potentially applied in the fields of fluorescence,22–24 detection,25 UV-blocking, and UV absorption materials.26,27
In particular, MgAl-LDH is the most typical representative of different kinds of hydrotalcites. However, MgAl-LDH alone shows very low photocatalytic activity under visible light irradiation. Fortunately, the layered structure of LDHs has been proven to be beneficial for inducing electron migration and inhibition of electron–hole pair recombination; additionally, the large number of hydroxyl groups on LDH laminates can generate more highly active ˙OH species, which are beneficial for improving the quantum efficiency of the photocatalytic reaction.28,29 A wide variety of semiconductor and MgAl-LDH composites such as TiO2/MgAl-LDH,30 SnO2/MgAl-LDH,31 and CeO2/MgAl-LDH32 has been reported for various photocatalytic applications.
Herein, a flower-like MgAl-LDH sample was prepared by a simple hydrothermal method. A series of AgSiOx/MgAl-LDH photocatalysts was synthesized in situ using a one-step approach. The composite structures were characterized by XRD, SEM, EDS, TEM, TG, and XPS. Finally, photodegradation tests and the mechanism of AgSiOx/MgAl-LDH photocatalysts were discussed.
Experimental section
Materials
Analytical grade Mg(NO3)2·6H2O, Al(NO3)3·9H2O, urea, Na2SiO3·9H2O, AgNO3, methylene blue (MB), hexadecyltrimethylammonium bromide (CTAB), trichloromethane, ethylenediaminetetraacetic acid disodium salt (EDTA-2Na), and tert-butanol were purchased and used without further purification.
Synthesis of MgAl–DS-LDH
Mg(NO3)2·6H2O (0.0016 mol), 0.0008 mol Al(NO3)3·9H2O, 0.0016 mol SDS, and 0.008 mol urea were dissolved in 960 mL deionized water. After magnetic stirring for 30 min, the solution was transferred to a 150 mL hydrothermal reactor and subsequently heated at 150 °C for 24 h. After cooling down to room temperature, the precipitate was filtered and washed thrice with ethanol and deionized water. Finally, the white products were dried in a vacuum oven at 80 °C for 8 h.
Synthesis of MgAl–CO32−-LDH
CTAB (0.15 mol L−1, 50 mL), 0.2 mol L−1 Na2CO3 (100 mL), 60 mL chloroform, and 2 g MgAl–DS-LDHs were mixed by magnetic stirring for 1 h. Then, the products were washed thrice with deionized water and ethanol and dried at 80 °C.
Synthesis of AgSiOx
A total of 150 mL of deionized AgNO3 solution (solution A) and 50 mL of deionized Na2SiO3·9H2O solution (solution B) was prepared with a concentration of 0.1 mol L−1. Under magnetic stirring, the solution B was added dropwise to the solution A using a constant pressure funnel. The mixture was further stirred for 2 h. The final reddish brown products were obtained by centrifuging and washing thrice with deionized water and ethanol; the products were then dried at room temperature (Fig. 1).
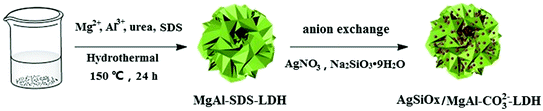 |
| Fig. 1 Schematic diagram of the process of the synthesis of AgSiOx/MgAl-LDH. | |
Synthesis of AgSiOx/MgAl-LDH
The AgSiOx/MgAl-LDH composites were prepared by in situ deposition. In a typical procedure, 0.5 g of MgAl–CO32−-LDH powder and a certain amount of AgNO3 solution (0.1 mol L−1) were added to 150 mL water. The solution mixture was magnetically stirred for 30 min and then, a certain amount of 0.1 mol L−1 Na2SiO3·9H2O solution was added dropwise. After two hours of reaction, the resultant product was separated by filtration, washed thrice with deionized water and ethanol, and dried at room temperature. Changing the amount of AgNO3 and Na2SiO3·9H2O solutions yielded composite materials with different mass ratios of AgSiOx and MgAl-LDH (3
:
1, 4
:
1, 5
:
1, 6
:
1, 10
:
1).
Characterization
Microstructures of the nanocomposites were observed with a Zeiss Supra 55 field-emission scanning electron microscope (SEM) and a JEOL JEM-3010 transmission electron microscope (TEM). X-ray diffraction (XRD) measurements were carried out on a Rigaku D/Max 2500 diffractometer with Cu Kα radiation (λ = 1.54 Å) at a generator voltage of 40 kV and a generator current of 40 mA. AgSiOx, MgAl-LDH, and AgSiOx/MgAl-LDH were characterized using a Thermo VG RSCAKAB 250X high-resolution X-ray photoelectron spectroscope (XPS). UV-vis diffuse reflectance spectra were recorded on a UV-vis spectrometer (UV-2450 Shimadzu). Thermogravimetric analysis (TG) was conducted using a STA449-type thermogravimetric analyzer under nitrogen flow; the heating rate was 20 °C min−1, and the gas flow velocity was 27 mL min−1.
Photocatalytic measurements
The photocatalytic experiments were carried out in a photocatalytic reaction chamber under a CEL-HXUV300 xenon lamp with a cutoff filter (λ > 420 nm), and the photocatalytic activities were evaluated by the degradation of MB. A total of 100 mg of photocatalyst was dispersed into 50 mL of MB (40 mg L−1) solution, and the mixture was stirred in the dark for 30 min to achieve adsorption equilibrium. The reaction temperature was maintained at 20 °C, and 5 mL of the solution mixture was taken out every 5 min and centrifuged (8000 rpm). The supernatant was tested using a UV-6100s Double BEAM spectrophotometer.
Results and discussion
XRD analysis
The XRD patterns of MgAl–DS-LDH, MgAl–CO32−-LDH, AgSiOx, and AgSiOx/MgAl-LDH (5
:
1) are shown in Fig. 2. As shown in Fig. 2b, AgSiOx retained the unique characteristic diffraction peak in accordance with the standard card (JCPDS no. 85-0281), and this was consistent with previously reported results,10 indicating the successful synthesis of AgSiOx. As shown in Fig. 2c, the pattern of MgAl–CO32−-LDH exhibited sharp and clear peaks at 11.71, 23.58, 39.67, 47.10, 47.10 and 47.10°, which corresponded to the basal reflections of (003), (006), (015), (018), (110), and (113). The structure of our compound matched with the standard structure of MgAl–CO32−-LDH (PDF#35-0964), suggesting the synthesis of MgAl–CO32−-LDHs.33 The XRD patterns (Fig. 2d) illustrate that C12H25SO3− anions were intercalated in MgAl-LDH, which was consistent with previously reported results.34 When the prepared AgSiOx was uniformly loaded on the MgAl-LDH surface, the XRD pattern (Fig. 2a) of the composites mainly exhibited the features of silver silicate; the diffraction peak signals of MgAl-LDH were obscured due to its small particles, high signals, and low crystallinity. However, MgAl-LDH as a carrier did not affect the structure of AgSiOx.
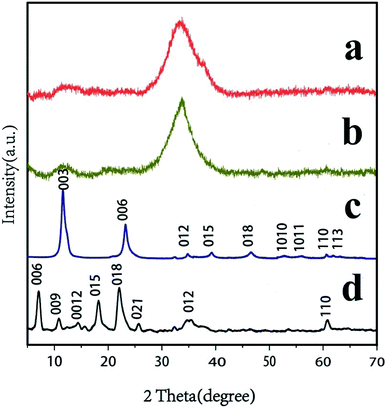 |
| Fig. 2 XRD patterns of (a) AgSiOx/MgAl-LDH (5 : 1); (b) AgSiOx; (c) MgAl–CO32−-LDH; and (d) MgAl–DS-LDH. | |
UV-vis analysis
The UV-visible spectra of AgSiOx/MgAl-LDH (5
:
1), AgSiOx, and MgAl-LDH were recorded, and the results are shown in Fig. 3. MgAl-LDH exhibited low absorption in the ultraviolet region and almost no absorption in the visible region. For silver silicate, apart from the ultraviolet region, it also exhibited strong absorption in the visible light region (λ > 420 nm), thus showing good photocatalytic efficiency in the visible light region. The absorptions of the composites and pure AgSiOx in the ultraviolet light region were similar. However, the absorption of the composite in the visible region of λ > 420 nm was much higher than those of pure AgSiOx and MgAl-LDH, indicating that MgAl-LDH could enhance the absorption in the visible light region as a carrier, which was beneficial for the enhancement of photocatalytic efficiency.
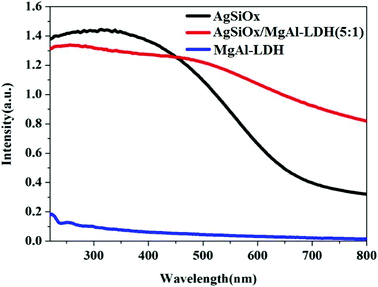 |
| Fig. 3 UV-vis spectra of AgSiOx, MgAl-LDH, and AgSiOx/MgAl-LDH (5 : 1). | |
TG analysis
As shown in Fig. 4, AgSiOx started exhibiting weight loss at 200 °C, with a mass loss of about 8.32%, which was mainly caused by the removal of physically adsorbed water. The thermal decomposition of MgAl-LDH mainly consisted of two stages: the first weight loss at temperatures below 250 °C was mainly due to the loss of physically adsorbed water and interlaminar water, corresponding to a mass loss of ∼13.65%. The second stage was seen in the temperature range of 250–550 °C. In this process, interlayer water, interlayer hydroxyl removal and interlayer anion decomposition, such as CO32− decomposition to release CO2, were mainly carried out, and the mass loss at this stage was about 25.79%.20,21,28,29 With the addition of AgSiOx, the weight loss ratio of the composite photocatalyst decreased, which also illustrated that the above-mentioned two materials have been effectively combined.
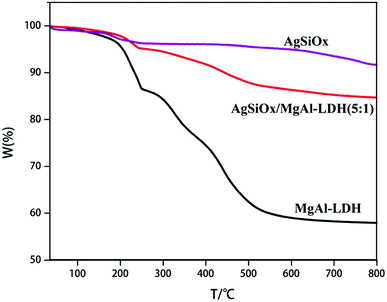 |
| Fig. 4 TG curves of AgSiOx, AgSiOx/MgAl-LDH (5 : 1), and MgAl-LDH. | |
SEM and TEM analysis
The SEM image of the prepared pure AgSiOx is displayed in Fig. 5a. The microscopic morphology of pure AgSiOx was a solid pellet of agglomerate. The prepared MgAl-LDH with spherical and flower-like structure is shown in Fig. 5b. During the formation of the flower-like MgAl-LDH sample, excessive surfactants formed micelles in the solution and imposed a bending force on the growth of LDH; thus, the LDH sheets grew along the curved micellar interface. Thus, a unique flower-like structure with a size of about 3–5 microns was formed,34 which was much larger than that of pure AgSiOx; it possessed high specific surface area and adsorption capacity, which are beneficial for the dispersal of AgSiOx and enriching of the pollutants.
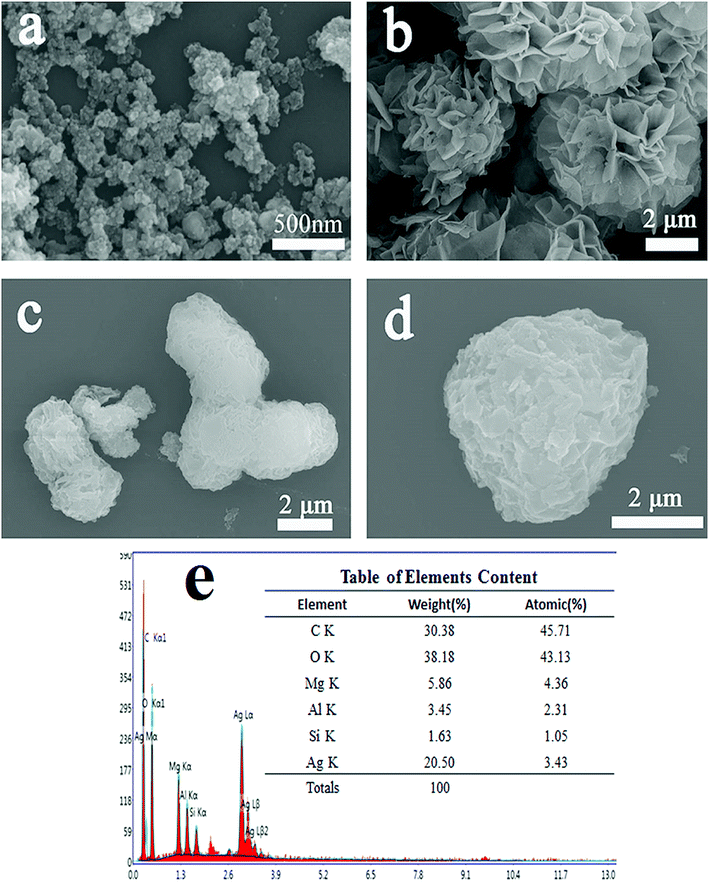 |
| Fig. 5 SEM images of (a) AgSiOx; (b) MgAl-LDH; (c and d) AgSiOx/MgAl-LDH (5 : 1); and (e) EDS of AgSiOx/MgAl-LDH (5 : 1). | |
The SEM images of the prepared AgSiOx/MgAl-LDH (5
:
1) composite are shown in Fig. 5c and d. We can clearly see that AgSiOx was uniformly and densely loaded on the surface of MgAl-LDH. The EDS spectrum of AgSiOx/MgAl-LDH (Fig. 5e) shows the presence of Mg, Al, O, Si, and Ag, with atomic percentages of 4.36%, 2.31%, 43.13%, 1.05% and 3.43%, respectively; these values indicated that the estimated atomic ratio of Mg to Al was ∼2
:
1 and Ag to Si was ∼3
:
1, which confirmed that the prepared samples are AgSiOx/MgAl-LDHs.
The TEM images of the prepared pure AgSiOx and AgSiOx/MgAl-LDH (5
:
1) composite are shown in Fig. 6. We can see that AgSiOx was composed of solid spherical particles with a size of 30–50 nm, and it could easily be aggregated. The TEM image of AgSiOx/MgAl-LDH (5
:
1) is shown in Fig. 6b, and it reveals that the AgSiOx particles were highly distributed on the MgAl-LDH surface or in the fractures, and the size of AgSiOx was smaller than that of pure AgSiOx; this indicated that MgAl-LDH can improve the dispersibility of AgSiOx.
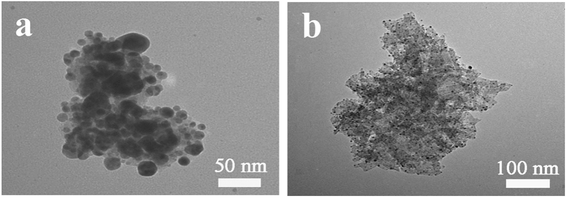 |
| Fig. 6 TEM images of (a) AgSiOx; (b) AgSiOx/MgAl-LDH (5 : 1). | |
XPS analysis
The full-scan XPS spectra of pure AgSiOx, MgAl-LDH, and AgSiOx/MgAl-LDH (5
:
1) materials are shown in Fig. 7a. The Al 2p and Mg 1s peaks were observed for MgAl-LDH; Ag 3d, Ag 3p, O 1s, and Si 2p peaks were seen for pure AgSiOx. All the above-mentioned characteristic peaks could be found for the AgSiOx/MgAl-LDH (5
:
1) composite. The high resolution XPS spectrum for the Ag 3d peak is shown in Fig. 7b. The peaks located at 374.4 and 368.3 eV correspond to Ag 3d3/2 and Ag 3d5/2, which were detected for AgSiOx and AgSiOx/MgAl-LDH. The XPS diffraction peaks of Si 2p for pure AgSiOx and AgSiOx/MgAl-LDH (5
:
1) are shown in Fig. 7c; the diffraction peaks resulted from Si 2p1/2, Si 2p3/2, and Ag 4s. The divided peaks were located at 102.3, 101.2, and 97.1 eV for Si 2p1/2, Si 2p3/2, and Ag 4s, respectively, and these observations were consistent with previously reported results.12 The XPS results further illustrated the successful preparation of the composite materials.
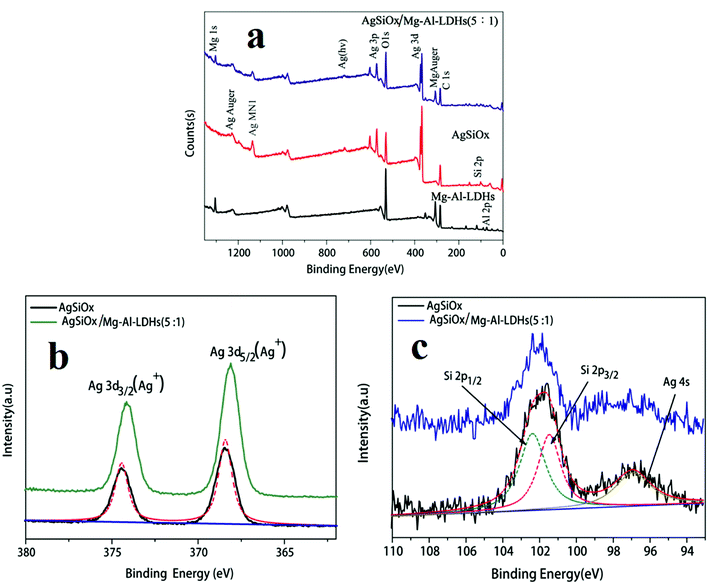 |
| Fig. 7 (a) The complete XPS spectra of pure AgSiOx, MgAl-LDH, AgSiOx/MgAl-LDH (5 : 1); (b) main peaks of Ag 3d5/2 and Ag 3d3/2 for pure AgSiOx and AgSiOx/MgAl-LDH (5 : 1); (c) main peaks of Si 2p3/2 and Si 2p5/2 for pure AgSiOx and AgSiOx/MgAl-LDH. | |
Photocatalytic performance
The performance of the samples for photodegradation of MB was studied in a photocatalytic reaction chamber under a CEL-HXUV300 xenon lamp with a cutoff filter (λ > 420 nm). As shown in Fig. 7a, all the samples except pure MgAl-LDH exhibited good performance. All the composites showed better degradation efficiency than pure AgSiOx, and AgSiOx/MgAl-LDH (5
:
1) showed the best performance under the experimental conditions. As shown in Fig. 7b, upon fitting the correlation data, the performance of the samples in the photodegradation process was found to be consistent with the first order reaction kinetics:
here, C0 is the concentration of MB at time t = 0 (as the light is turned on, after the period in the dark), Ct is the concentration of MB at photocatalytic reaction time t, and k is the decolorization rate constant. The MB decolorization rate constants under different conditions are shown in Table 1. The results demonstrated that the photocatalytic rate of AgSiOx/MgAl-LDH (5
:
1) was higher than that of pure silver, and the full UV-visible absorption spectra for MB photodegradation are shown in Fig. 8c.
Table 1 Decolorization rate constants of MB obtained for different photocatalysts
Samples |
k (min−1) |
AgSiOx/Mg–Al-LDHs (3 : 1) |
0.1159 |
AgSiOx/Mg–Al-LDHs (4 : 1) |
0.1007 |
AgSiOx/Mg–Al-LDHs (5 : 1) |
0.1367 |
AgSiOx/Mg–Al-LDHs (6 : 1) |
0.1094 |
AgSiOx/Mg–Al-LDHs (10 : 1) |
0.1138 |
AgSiOx |
0.0935 |
Mg–Al-LDHs |
— |
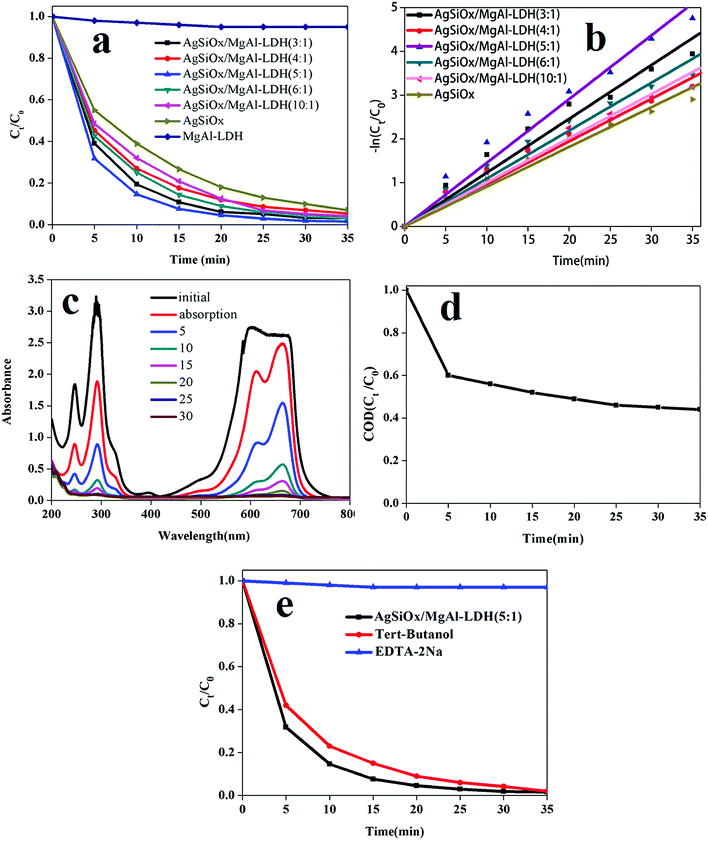 |
| Fig. 8 (a) Photocatalytic degradation curves; (b) curve of the fitting equation of photocatalytic degradation rate; (c) the UV-visible absorption spectra of MB during photodegradation process with AgSiOx/MgAl-LDH (5 : 1); (d) the curve of COD (Ct/C0) in the process of photodegradation of MB with AgSiOx/MgAl-LDH (5 : 1); (e) photodegradation of MB by AgSiOx/MgAl-LDH (5 : 1) with the addition of EDTA-2Na or tert-butanol. | |
To further explore the degradation of methylene blue, the CODGr (O2, mg L−1) values at different reaction times (t = 0–35 min, at 5 minutes intervals) were measured and shown in Fig. 8d. The experimental results showed that the AgSiOx/MgAl-LDH (5
:
1) catalyst exhibits good COD removal performance for methylene blue (56%) after 35 minutes.
To investigate the active species in the photocatalytic process, a photoinduced hole removal agent EDTA-2Na and hydroxyl scavenger tert-butanol were added to the reaction mixture. The addition of EDTA-2Na almost stopped the photocatalytic degradation process (Fig. 8e), whereas the addition of tert-butanol hardly changed the photocatalytic degradation process. The results illustrated that photogenerated holes were the main active species in the photocatalytic degradation process, which was consistent with previously reported results.13
To further evaluate the cyclic performance of AgSiOx/MgAl-LDH (5
:
1), it was repeatedly used for three cycles; the specific performance (Fig. 9) revealed good stability and reusability. It is easy to find a conclusion from the diagram of cycling runs that if we want to get the same photocatalytic degradation rate, we should extend the reaction time in the photocatalytic cycle test; this could be because some of the Ag+ ions are reduced to Ag0, which is frequently observed in most Ag-based compounds. Additionally, after each cycle test, a large amount of water is used to wash the samples, which can result in the loss of catalyst, leading to the decrease in photocatalytic efficiency (Fig. 10).
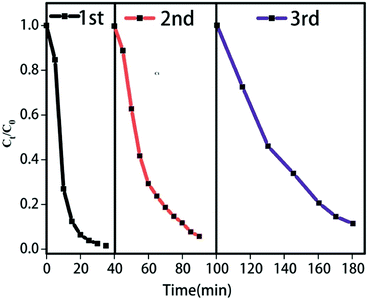 |
| Fig. 9 Cycling runs of AgSiOx/MgAl-LDH (5 : 1) composite for the degradation of MB. | |
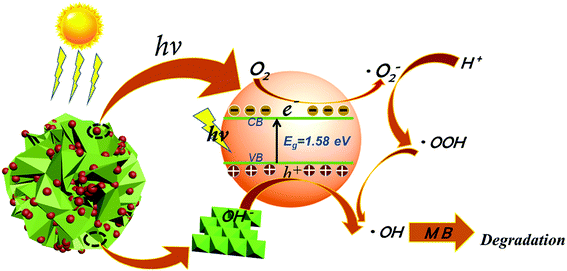 |
| Fig. 10 Proposed photocatalytic mechanism of AgSiOx/MgAl-LDH under visible light irradiation. | |
There have been many studies on the degradation mechanism of methylene blue.35,36 Based on the above-mentioned results, the following photocatalytic degradation mechanism was proposed. Under visible light irradiation, AgSiOx generated electron–hole pairs,11–13 and the holes reacted with abundant hydroxyl groups on the surface of LDH to generate hydroxyl radicals (˙OH) with strong oxidability.37–39 The excited electrons were captured by dissolved oxygen species in aqueous solution to form superoxide radicals (˙O2−).40,41 The reactive ˙O2− and ˙OH species with high activities degraded organic matter into inorganic small molecules.42,43 In addition, the particle size of AgSiOx was reduced to reveal more active sites, and the contact area with the target pollutants was increased, which was beneficial for the enhancement of photocatalytic efficiency. The photocatalytic decolorization reactions of MB can be written as follows:
|
AgSiOx/LDH/MB + hν → AgSiOx/LDH/MB*
| (1) |
|
AgSiOx/LDH/MB* → AgSiOx(eCB−)/LDH/MB+
| (2) |
|
AgSiOx(eCB−)/LDH + O2 → AgSiOx/LDH + ˙O2−
| (3) |
|
˙O2− + H+ → HOO˙ → ˙OH
| (4) |
|
˙OH + MB → degradation products
| (6) |
Conclusions
MgAl-LDH having a flower-like structure was prepared by a hydrothermal method, and a series of AgSiOx/MgAl-LDH composites with different mole ratios was successfully obtained by loading AgSiOx on the MgAl-LDH surface. The photocatalytic activities of these composites for the photodegradation of MB were investigated under visible light irradiation. The results showed that the photodegradation efficiency of MB by AgSiOx/MgAl-LDH (5
:
1) was nearly 99.7% in 30 min, and the photodegradation rate was higher than that of pure AgSiOx. Meanwhile, AgSiOx/MgAl-LDH (5
:
1) maintained good photocatalytic efficiency after 3 cycling experiments. The hydroxyl-rich structure and adsorption capacity of MgAl-LDH are important contributors for improving the photocatalytic ability.
Conflicts of interest
There are no conflicts to declare.
Acknowledgements
The authors gratefully acknowledge the financial support of the Science and Technology major projects of Guizhou province (Guizhou branch [2013]6017 and [2013]6004 and the High-level Talent Training Program in Guizhou Province (Talent (2016) 5658).
References
- J. H. Weisburger, Mutat. Res., Fundam. Mol. Mech. Mutagen., 2002, 506, 9 CrossRef PubMed.
- Q. Zhou, Bull. Environ. Contam. Toxicol., 2001, 66, 784 Search PubMed.
- A. S. González and S. S. artinez, Ultrason. Sonochem., 2008, 15, 1038 CrossRef PubMed.
- I. Arslan and I. A. Balcioglu, J. Chem. Technol. Biotechnol., 2001, 76, 53 CrossRef.
- Y. Y. Liu, G. Z. Wang, J. C. Dong, Y. An, B. B. Huang, X. Y. Qin, X. Y. Zhang and Y. Dai, J. Colloid Interface Sci., 2016, 469, 231 CrossRef PubMed.
- S. Y. Lee and S. J. Park, J. Ind. Eng. Chem., 2013, 19, 1761 CrossRef.
- A. Fujishima and K. Honda, Nature, 1972, 238, 37 CrossRef PubMed.
- Y. S. Li, Z. L. Tang, J. Y. Zhang and Z. T. Zhang, Appl. Catal., A, 2016, 522, 90 CrossRef.
- L. Han, P. Wang, C. Z. Zhu, Y. M. Zhai and S. J. Dong, Nanoscale, 2011, 3, 2931 RSC.
- Z. Z. Lou, B. B. Huang, Z. Y. Wang, X. C. Ma, R. Zhang, X. Y. Zhang, X. Y. Qin, Y. Dai and M. H. Whangbo, Chem. Mater., 2014, 26, 3873 CrossRef.
- Y. G. Hu, H. Zheng, T. Z. Xu, N. Xu and H. W. Ma, RSC Adv., 2016, 6, 103289 RSC.
- J. Liu, W. Wu, Q. Y. Tian, Z. G. Dai, Z. H. Wu, X. H. Xiao and C. Z. Jiang, Dalton Trans., 2016, 45, 12745 RSC.
- Y. Q. Jing, C. X. Gui, J. Qu, S. M. Hao, Q. Q. Wang and Z. Z. Yu, ACS Sustainable Chem. Eng., 2017, 5, 3641 CrossRef.
- M. Zubair, M. Daud, G. Mckay, F. Shehzad and M. A. Al-Harthi, Appl. Clay Sci., 2017, 143, 279 CrossRef.
- K. M. Parida and L. Mohapatra, Chem. Eng. J., 2012, 179, 131 CrossRef.
- W. Y. Shi, Y. Y. Lin, S. T. Zhang, R. Tian, R. Z. Liang, M. Wei, D. G. Evans and X. Duan, Phys. Chem. Chem. Phys., 2013, 15, 18217 RSC.
- L. Yao, D. Wei, D. Yan and C. Hu, Chem.–Asian J., 2015, 10, 630–636 CrossRef PubMed.
- R. Liang, R. Tian, Z. Liu, D. Yan and M. Wei, Chem.–Asian J., 2014, 9, 1161–1167 CrossRef PubMed.
- S. Nayak and K. M. Parida, Int. J. Hydrogen Energy, 2016, 41, 21166 CrossRef.
- Z. Li, M. Chen, Q. W. Zhang, J. Qu, Z. Q. Ai and Y. J. Li, Appl. Clay Sci., 2017, 144, 115 CrossRef.
- B. Luo, R. Song and D. W. Jing, Int. J. Hydrogen Energy, 2017, 42, 23427 CrossRef.
- Y. Zhao, H. Lin, M. Chen and D. Yan, Ind. Eng. Chem. Res., 2015, 53, 3140–3147 CrossRef.
- W. Li, D. Yan, R. Gao, J. Lu, M. Wei and X. Duan, J. Nanomater., 2013, 586462 Search PubMed.
- D. Yan, Y. Zhao, M. Wei, R. Liang, J. Lu, D. G. Evans and X. Duan, RSC Adv., 2013, 3, 4303 RSC.
- Gao and D. Yan, Chem. Commun., 2017, 53, 5408–5411 RSC.
- G. Wang, S. Xu, C. Xia, D. Yan, Y. Lin and M. Wei, RSC Adv., 2015, 5, 23708–23714 RSC.
- H. Zhang, J. Zhang, R. Yun, Z. Jiang, H. Liu and D. Yan, RSC Adv., 2016, 6, 34288–34296 RSC.
- J. Yoshimura, Y. Ebina, J. Kondo, K. Domen and A. Tanaka, J. Phys. Chem., 2002, 97, 1970 CrossRef.
- J. C. Sun, Y. B. Zhang, J. Cheng, H. Fan, J. Y. Zhu, X. Wang and S. Y. Ai, J. Mol. Catal. A: Chem., 2014, 382, 146 CrossRef.
- E. M. Seftel, M. Mertens and P. Cool, Appl. Catal., B, 2013, 134, 274–285 CrossRef.
- E. Dvininov, M. Ignat, P. Barvinschi, M. A. Smithers and E. Popovici, J. Hazard. Mater., 2010, 177, 150–158 CrossRef PubMed.
- J. S. Valente, Appl. Catal., B, 2011, 102, 276–285 CrossRef.
- Y. Yang, G. L. Fan and F. Li, Mater. Lett., 2014, 116, 203 CrossRef.
- B. Li and J. He, J. Phys. Chem. C, 2008, 112, 10909 CrossRef.
- R. Lu, X. Xu, J. Chang, Y. Zhu, S. Xu and F. Zhang, Appl. Catal., B, 2012, 111, 389–396 CrossRef.
- Y. Zhou, L. Shuai, X. Jiang, F. Jiao and J. Yu, Adv. Powder Technol., 2015, 26, 439–447 CrossRef.
- K. M. Parida, L. Mohapatra and N. Baliarsingh, J. Phys. Chem. C, 2012, 116, 22417 CrossRef.
- F. Cao, W. Shi, L. Zhao, S. Song, J. Yang, Y. Lei and H. Zhan, J. Phys. Chem. C, 2008, 112, 17095 CrossRef.
- N. Baliarsingh, K. M. Parida and G. C. Pradhan, Ind. Eng. Chem. Res., 2014, 53, 3834–3841 CrossRef.
- K. Parida, L. Mohapatra and N. Baliarsingh, J. Phys. Chem. C, 2017, 116, 22417–22424 CrossRef.
- Y. Zhu, R. Zhu, G. Zhu, M. Wang, Y. Chen, J. Zhu, Y. Xi and H. He, Appl. Surf. Sci., 2017, 433, 458–467 CrossRef.
- J. Wang, G. Ji, Y. Liu, M. A. Gondal and X. Chang, Catal. Commun., 2014, 46, 17–21 CrossRef.
- M. I. Shinger, A. M. Idris, S. Devaramani, D. D. Qin, H. Baballa, S. T. Zhang, D. Shan and X. Liu, J. Environ. Chem. Eng., 2017, 5, 1526–1535 CrossRef.
|
This journal is © The Royal Society of Chemistry 2018 |
Click here to see how this site uses Cookies. View our privacy policy here.