DOI:
10.1039/C7RA12865G
(Paper)
RSC Adv., 2018,
8, 5034-5041
Flame-retardant effect and mechanism of melamine phosphate on silicone thermoplastic elastomer
Received
29th November 2017
, Accepted 22nd January 2018
First published on 29th January 2018
Abstract
Different from the traditional silicone materials, which are not easily ignited, silicone thermoplastic elastomer (Si-TPE) has poor flame retardant properties due to the existence of the hard segments in its molecular chains. In this paper, melamine phosphate (MP), a kind of halogen free flame retardant, was adopted to improve the flame retardancy of Si-TPE. The results showed that MP played the role of flame retardant in both gas and condensed phases due to its nitrogen–phosphorus-containing structure. Inert gases, including nitrogen, steam and ammonia which were released by the degradation of melamine during burning, could take away the heat and dilute the oxygen in the gas phase, and further working with the phosphoric acid, which was generated in the condensed phase, to form a denser and firmer char layer. In this way, Si-TPE/MP composite with good flame retardancy was obtained. Interestingly, MP had little influence on the thermal processability of Si-TPE, even at 28 wt% content, ascribing to its two opposite effects on Si-TPE, but enhanced the comprehensive mechanical properties of Si-TPE with suitable loadings, e.g. when the MP content was 28 wt%, the composite reached UL94-V0 rating, and its tensile strength and Young's modulus were 3.5 MPa and 37.7 MPa, respectively.
1. Introduction
Silicone thermoplastic elastomer (Si-TPE) is a kind of synthetic polymer consisting of a segmented structure of alternating soft blocks (organic silicon segments) that act as the elastic portion and hard blocks (plastic polymer segments) that act as the thermally reversible cross-linking sites.1–3 This special structure endows Si-TPE with not only the usual properties of silicone elastomers, e.g. high and low temperature resistance, weather resistance, superior corrosion resistance, low surface tension, small viscosity and temperature coefficient, non-toxicity and good biocompatibility,4–9 but also the possibility of being thermally processed via traditional plastic processing methods without chemical crosslinking, as well as controllable mechanical properties.10,11
The formation of the char barrier (Si–O, Si–C) at high temperature is absolutely essential for the flame retardant properties of a silicone material,12 but the introduction of the hard blocks disturbs the regularity of Si-TPE molecular chains, and decreases the proportion of silicone elements in it, contrarily resulting in its worse flame retardancy and narrow applications.13 To improve the flame retardancy of a silicone material, various methods, mainly based on inorganic flame retardants, have been adopted.12,14–16 However, these inorganic flame retardants, e.g. Fe2O3, red phosphorus and platinum, are commonly incompatible with the matrix, causing poor processability and mechanical properties as well as the dissatisfied flame retardancy of the matrix. In recent years, researchers have transferred their attentions to the organic flame retardants, e.g. melamine, pentaerythritol, graphite, etc.,4,17,18 but the large additive content of organic flame retardants is usually required to achieve the good flame retardancy, which not only deteriorates the processability and mechanical properties of the materials, but also increases the cost.
Melamine phosphate (MP), a typical halogen-free phosphorus flame retardant, is the reaction product of melamine and phosphoric acid, thus combining the flame retardancy of both melamine and phosphoric acid. When burning, MP can release phosphorus acids to carbonize and construct a stable and dense charring barrier in the condensed phase to decrease the flammability of a material,19 and nitrogen, bonded to the triazine rings in MP, can also pass to the gaseous phase,20 further insulating the material from fire. It has been reported that phosphorous and silicone have synergistic flame retardancy,21–24 so MP has been widely used in some silicone contained materials to improve their flame retardancy. For example, Li et al.25 adopted MP to promote the flame retardancy of α,ω-dihydroxy polydimethylsiloxane, and found that MP could accelerate the thermal decomposition of this silicone rubber to form oxygen and heat insulated barrier, thus effectively improving its limiting oxygen index.
In our previous work,26 a novel Si-TPE consisting of urea groups and the branched organic polysiloxane was developed. This Si-TPE had quite good thermal processability and high mechanical properties, but deteriorated flame retardancy due to the existence of urea groups. Here, to improve the flame retardancy of this novel Si-TPE, MP was adopted, and the effects of MP content on the melt fluidity, molecular structure, combusting process, char morphologies as well as mechanical properties of Si-TPE were systematically studied, which would surely extend the application fields of this novel Si-TPE.
2. Experimental
2.1 Materials
Silicone thermoplastic elastomer (Si-TPE) (Fig. 1a) was self-prepared in our laboratory. Melamine phosphate (MP) (Fig. 1b) was bought from Hefei Jinghui Company, China.
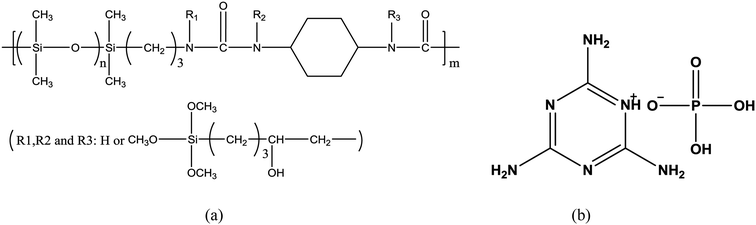 |
| Fig. 1 Chemical structures of Si-TPE (a) and MP (b). | |
2.2 Sample preparation
Flame retardant Si-TPE was prepared as follows: Si-TPE particles and MP powders were mixed in a high-speed mixer after being dried in a vacuum drying oven at 120 °C for 8 hours. The mass percentage of MP in the mixture was about 9 wt%, 16 wt%, 23 wt%, 28 wt% and 33 wt% respectively. Then, the mixture was extruded on a TSSJ-25/33 co-rotating twin-screw extruder (Chenguang Research Institute of Chemical Industry, China) at the temperature of 140–165 °C with a rotation rate of 60 rpm, then was granulated and dried again. The specimens for combustion and mechanical property tests were obtained by injecting the granulates on an injection molding machine (MA1200-SMS-A, Haitian Plastics Machinery Ltd., China) at the temperature of 140–165 °C and a screw speed of 40 rpm.
2.3 Characterization
2.3.1 Rheological property. The rheological behavior of Si-TPE was measured by a Advanced Capillary Rheometer (Rosand RH2000, Malvern Instruments Ltd., UK). The capillary diameter was 1.2 mm, the ratio of length to diameter (L/D) was 16, the test temperature was 165 °C, and the shear speed was in the range of 50 to 5000 s−1.
2.3.2 Interaction. The interactions between Si-TPE and MP were tested on a Nicolet 6700 IR spectrometer (Thermo Scientific company, USA) in the reflectance mode from 4000 cm−1 to 600 cm−1 at 4 cm−1 resolution and 32 scans at room temperature. Before test, the films were put into an oven at 80 °C for 12 h to completely remove the water.
2.3.3 Flammability. The UL-94 vertical burning test was performed on an HK-HVRA vertical burning tester (Zhuhai Huake Testing Equipment Co., Ltd., China) with bar dimensions of 125 × 13 × 1.6 mm3 according to ASTM D3801-10. The limited oxygen index (LOI) was tested by a Dynisco LOI instrument with the sample dimensions of 125 × 10 × 4 mm3 according to ASTM D 2863-97. Micro-scale combustion calorimeter (MCC), FAA type (Fire Testing Technology Co., Ltd., UK), was used to measure the heat release rate (HRR), the total heat release (THR), and the peak value of heat release rate (PHRR) of the specimens with a heating rate of 1 °C s−1 in the temperature range of 80–800 °C.
2.3.4 Thermal stability. TG and DTG curves were performed on a TA Q50 thermal analyzer (TA instrument Co., Ltd., USA) under a nitrogen atmosphere with a flow rate of 50 ml min−1 from 20 °C to 700 °C at a heating rate of 10 °C min−1.
2.3.5 Morphologies. The dispersion of MP in Si-TPE and the morphology of the char after burning were observed by a scanning electronic microscope (JSM-5900LV, JEOL Ltd., Tokyo, Japan) with a conductive gold coating and an accelerating voltage of 10 kV.
2.3.6 Mechanical properties. The tensile strength, Young's modulus and elongation at break of the specimens were tested at room temperature with a speed of 100 mm min−1 on a Reger universal testing machine (RGM-4010, Shenzhen Reger Instrument Co. Ltd, China). The average values were obtained by calculating over fives specimens for each group.
3. Result and discussion
3.1 Thermal processability
High-pressure capillary rheometer was utilized to evaluate the thermal processability of Si-TPE/MP composites, and the results were showed in Fig. 2. Apparently, the shear viscosity of each sample decreased with the increase of the shear rate, indicating that both Si-TPE and Si-TPE/MP composites belonged to the pseudoplastic fluid and presented the shear-thinning behaviors. The addition of MP changed the movement of Si-TPE molecular chains, thus influencing the melt fluidity of the composites. However, this influence was quite complex, making the melt viscosity first increased and then decreased with the increase of MP content.
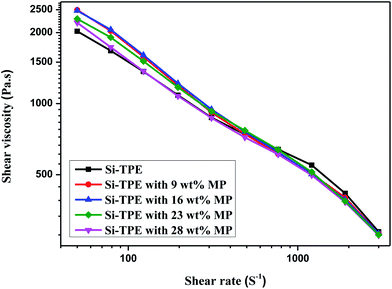 |
| Fig. 2 Rheological behaviors of Si-TPE with different MP content. | |
MP has two opposite influences on the melt viscosity of Si-TPE. Firstly, the existence of MP particles in the interspaces of Si-TPE molecular network could increase the internal rotation resistance of Si-TPE molecules, thus limiting the chain movement and leading to the increase of the shear viscosity. Secondly, the polar groups on the surface of MP particles could form certain hydrogen bonding with Si-TPE, thus weakening the originally strong hydrogen bonding among the hard segments of Si-TPE, and resulting in the decrease of the melt viscosity. At low MP content (<16 wt%), the interactions between MP and Si-TPE were not enough, so the former influence played the main role, making the shear viscosity of Si-TPE/MP constantly increased with MP content. While at higher MP content (>16 wt%), the hydrogen bonding between MP and Si-TPE was strong enough, and the later influence played the dominant role, contrarily leading to the decrease of the shear viscosity of Si-TPE/MP.
On the whole, the incorporation of MP changed the melt viscosity of Si-TPE in a narrow range, i.e. Si-TPE/MP still had good thermal processability compared with pure Si-TPE.
3.2 Interactions
FTIR spectra of MP and Si-TPE with different MP content were shown in Fig. 3. The N–H stretching vibration peak of the hard segments in Si-TPE appeared at 3349 cm−1, while the –NH2 and –NH3+ stretching vibration peaks of MP appeared at about 3393 cm−1 and 3156 cm−1 respectively. The addition of MP increased the N–H content in system and enhanced the intensity of its corresponding stretching and bending vibration peaks, simultaneously influenced the hydrogen bonding among the hard segments of Si-TPE, which was reflected in the FTIR spectra by that both the stretching and bending vibration peaks of N–H moving to higher wavenumbers, i.e. respectively from 3349 cm−1 and 1627 cm−1 of pure Si-TPE to 3368 cm−1 and 1639 cm−1 of Si-TPE with 28 wt% MP. All above changes confirmed the destruction and reformation of the hydrogen bonding in Si-TPE/MP system, ascribing to the partial interactions formed between the acid or/and amide group in MP (P–OH, –NH2) and the urea group (NH–C
O) in hard segments of Si-TPE, which weakened the original hydrogen bonding in Si-TPE and caused the heterogeneity of the electron density of N–H, thus increasing its vibration frequency and making its vibration peaks gradually moved to high wavenumbers. It should be noted that the formation of –NH3+ came from the interactions between –NH2 and P–OH of MP, so its wavenumbers accessed to that of pure MP with the increase of MP content.
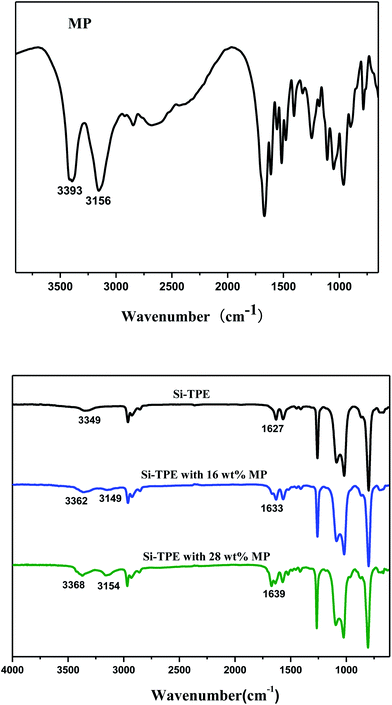 |
| Fig. 3 FTIR spectra of MP and Si-TPE with different MP content. | |
3.3 Flame retardancy
The flame retardancy of Si-TPE/MP composite was evaluated by vertical burning and limiting oxygen index tests, and the results were shown in Table 1. It could be seen from table that Si-TPE had poor flame retardancy due to the introduction of the flammable hard segments. The total self-extinction time after 10 s ignition of Si-TPE was about 50 s, and its limiting oxygen index LOI value was only 21%, approximately the oxygen concentration in air. With the addition of MP, the flame retardancy of Si-TPE was obviously improved, i.e. the total self-extinction time after 10 s ignition gradually reduced and the LOI value increased. When MP content was above 23 wt%, Si-TPE/MP composite could not be ignited, the LOI value reached 28%, and the result of vertical burning rating came to V0 level.
Table 1 Vertical burning level and limiting oxygen index of Si-TPE with different MP content
MP content (wt%) |
Total self-extinction time after 10 s ignition (s) |
Molten droplet |
UL94 rating |
LOI (%) |
0 |
>50 |
Yes |
NR |
21 |
9 |
<20 |
Yes |
V2 |
23 |
16 |
<10 |
Yes |
V2 |
24 |
23 |
0 |
No |
V0 |
25 |
28 |
0 |
No |
V0 |
28 |
33 |
<10 |
Yes |
V2 |
27 |
Fig. 4 showed the combustion process of Si-TPE and Si-TPE/MP composite. Obviously, Si-TPE was easily ignited and broken up with the development of combustion process. This might be attributed to the introduction of the hard segments that hindered the formation of the stable and continuous char layer, and thus causing the inner structure exposed to oxygen and the material continued burning without any barrier. The burning part formed a narrow neck and rapidly fell down by gravity, igniting the cotton. While for Si-TPE/MP composite, the incorporation of MP apparently improved the flame retardancy of the composite, reflecting in Fig. 4 by the decrease of the molten droplets and the formation of the carbon layer. This carbon layer was hard, compact and persistent, so could block the combustible medium during the following burning process, making inner material unburned.
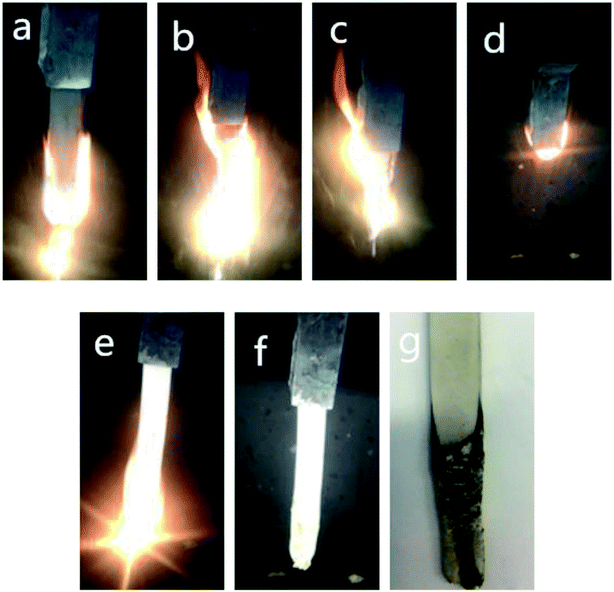 |
| Fig. 4 Combusting photos of pure Si-TPE (a–d) and Si-TPE/MP (28 wt%, e–g). | |
It should be noted that when MP content was above 28 wt%, the flame retardancy of Si-TPE/MP composite contrarily decreased, i.e. the sample could be ignited after 10 s ignition and the droplet came up again, simultaneously, the vertical burning level dropped to V2. As known, MP played a major role in the formation of the compact char layer, which could reduce the amount of volatile fuel, on the surface of a material. Within proper content, e.g. 23 wt%, MP could disperse uniformly in Si-TPE matrix, without big aggregations (Fig. 5), thus endowing Si-TPE with good flame retardancy by sufficiently reacting with the matrix and accelerating the formation of the uniformly compact char layer. However, the big aggregations appeared when MP content reached 33 wt%, deteriorating the good dispersion of MP in Si-TPE matrix and leading to the formation of the less uniform char layer during pyrolysis, even with some small holes (Fig. 7), thus weakening the barrier capability of the char layer on fire, and making the molten droplet generated again once being ignited, the LOI value decreased to 27%, and the UL94 rating depressed to V2 level.
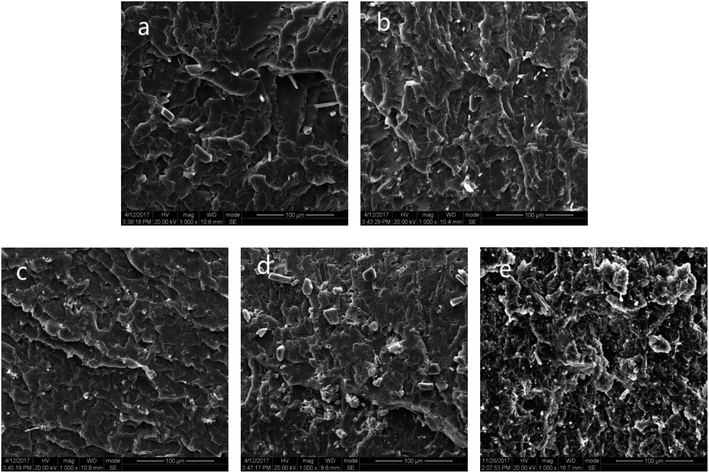 |
| Fig. 5 SEM morphologies of Si-TPE with different MP content. (MP content: (a) 9 wt%, (b) 16 wt%, (c) 23 wt%, (d) 28 wt%, (e) 33 wt%). | |
3.4 Flame retardant mechanism
To confirm the flame retardant mechanism of MP on Si-TPE, TG and DTG measurements were adopted, as shown in Fig. 6. As could be seen, Si-TPE presented two stages of rapid decomposition, i.e., from 320 °C to 380 °C, nearly 30% mass loss for dehydration and scission reactions; from 520 °C to 620 °C, thorough decomposition during pyrolysis, and after the first decomposition stage, Si-TPE showed a quite slow decomposition ascribing to the oxidation action that made Si-TPE material further crosslinked.27 Compared with Si-TPE, the initial decomposition of Si-TPE/MP was obviously accelerated and only one decomposition stage was observed, indicating the worsening thermal stability of Si-TPE/MP composite and the changed decomposition mechanism, possibly due to the catalytic degradation of the released acid source and polyphosphate compounds from MP.28 MP experienced the condensation reactions, chain scission and crosslinking reactions at the temperature below 300 °C, producing polyphosphate compounds,29,30 which could react with Si-TPE matrix to enhance the formation of the char layers, leading to the increase of the carbon residues in the composite after pyrolysis. The enhanced char layers could play a role of protection on the surface of the composite during the further combustion, so improved the flame retardancy of the composite. The more the MP content, the more the polyphosphate compounds would be produced, resulting in the earlier decomposition of the composite and the more the carbon residues after burning. Moreover, the released inert gas, e.g. nitrogen, steam, melamine and ammonia, from the further decomposition of MP and its condensation products, could take away part heat and diluted the oxygen, helping to the improvement of the flame retardancy of the halogen-free Si-TPE/MP composite. However, when MP content reached 33 wt%, the specimen contrarily presented the similar thermal degradation behaviours as pure Si-TPE again (Fig. 6B). This might be due to the poor dispersion and enlarged aggregations of MP in Si-TPE, which possibly led to the irregularity of carbonization degree on the surface and the imperfect barrier. The deficient areas could not prevent the invading of the flame into the interior material, surely resulting in the poor fire resistance of the material. Only proper MP content could achieve the best dispersion and exert the best flame retardant effect.
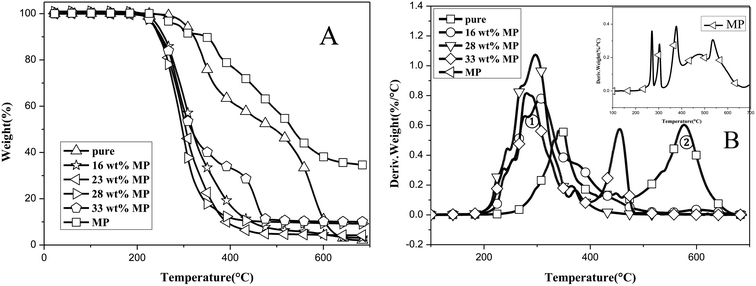 |
| Fig. 6 TG (A) and DTG (B) curves of Si-TPE with different MP content. | |
To further confirm the char morphology of the burned material, SEM photos of Si-TPE and Si-TPE/MP composites after complete burning were shown in Fig. 7. Apparently, the char layer of pure Si-TPE was quite loose and coarse, with large holes in it. While Si-TPE with 28 wt% MP presented a dense and flat char layer, almost without holes. This perfect char morphology could effectively retard the continuous burning of Si-TPE. However, when MP content reached 33 wt%, this perfect structure of the char layer was destroyed, with the appearance of many small holes, which would expose the interior material and worsen the flame retardancy of Si-TPE.
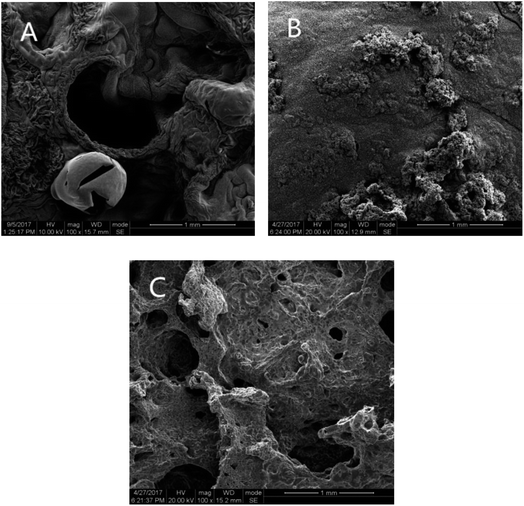 |
| Fig. 7 SEM photos of the char of Si-TPE with different MP content. (MP content: (A) 0 wt%, (B) 28 wt%, (C) 33 wt%). | |
Micro-scale combustion calorimeter (MCC) is a quantitative test method to evaluate the combustion behaviors of a material in fire situation. Table 2 listed the total heat release (THR) of Si-TPE with different MP content. Clearly, the addition of MP decreased the total heat release and heat release rate of Si-TPE, e.g. the THR values dropped from 24.7 kJ g−1 for pure Si-TPE to 17.4 kJ g−1 for that with 28% MP, the decrease was about 29.5%, showing that MP had the good carbonization properties and remarkable retarding heat release effect on Si-TPE/MP composites. With the high quality char layer formed on the material surface ascribing to the carbonation action of acid source decomposed by MP, heat, oxygen, fire and volatiles could be greatly held back.
Table 2 The total heat release of MCC of Si-TPE with different MP content
MP content (wt%) |
0 |
9 |
16 |
23 |
28 |
33 |
THR (kJ g−1) |
24.7 |
21.7 |
19.5 |
18.7 |
17.4 |
20.2 |
Fig. 8 showed the MCC curves of Si-TPE and Si-TPE with 28 wt% MP. Compared with Si-TPE, the first and second exothermic peaks of Si-TPE/MP composite respectively dropped by 17 kJ g−1 (about 13.0%) and 16 kJ g−1 (about 17.2%), and both appeared in advance, identifying the catalytic effect of MP on the decomposition of Si-TPE, and the formation of the denser char layer. Catalysis and carbonation endowed the composite with two-step decomposition (decomposed around 320 °C, and formed the stable char layer at about 400 °C), which was different from that of pure Si-TPE (decomposed at about 370 °C, and later continuously decomposed at 650 °C for the flimsy barrier). In addition, acid source could induce the further decomposition of non-flammable gas.31 Nitrogen and other non-flammable gas could carry part of heat and cover the surface of the Si-TPE after decomposition, thus preventing the further combustion.
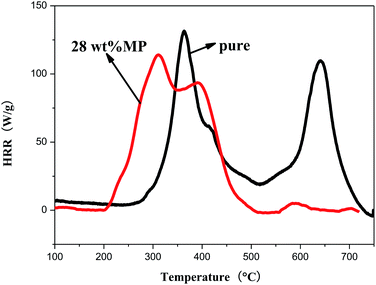 |
| Fig. 8 MCC curves of Si-TPE and Si-TPE with 28 wt% MP. | |
3.5 Mechanical properties
Fig. 9 showed the mechanical properties of Si-TPE/MP composites. It could be seen that with the addition of MP, the tensile strength of Si-TPE first increased, and then decreased. When MP content was below 9 wt%, micron-sized MP could disperse well in Si-TPE matrix, and almost no agglomerations appeared (Fig. 5a), thus improving the tensile strength of the composite. With the further increase of MP content, the aggregation of MP particles occurred (Fig. 5c and d), and the more the MP content, the larger the size of the aggregates formed for the electrostatic force of MP particles, resulting in the worse dispersion of MP in Si-TPE matrix, and the decrease of the tensile strength. But ascribing to the good interactions between MP and Si-TPE, the changes of tensile strength of all the composites were quite small, only in the range of 3.3 MPa to 4.0 MPa. While the Young's modulus of Si-TPE/MP composites continued increasing when MP content was lower than 28 wt%, confirming the enhancement of MP on Si-TPE. The decrease of the Young's modulus of the composite with 33 wt% MP might be due to the worsening dispersion of MP particles. Even though, the Young's modulus of the composite was still higher than that of pure Si-TPE. Under the co-effects of the dispersion of MP in Si-TPE and the interactions between MP and Si-TPE, the elongation of the composites only had a slight decrease with the increase of MP content.
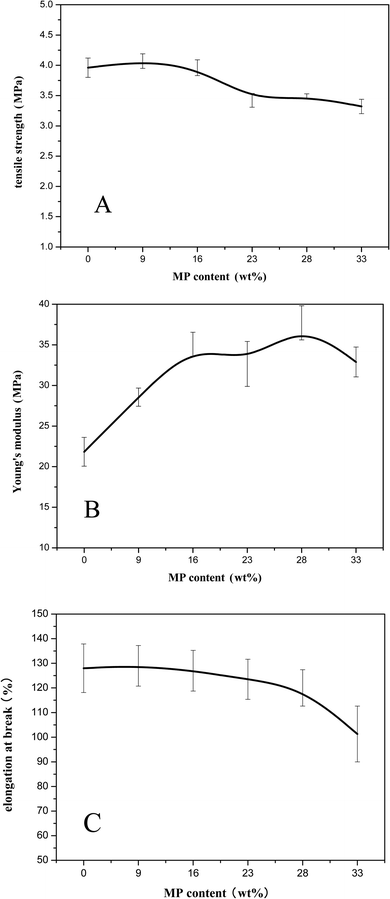 |
| Fig. 9 Tensile strength (A), Young's modulus (B) and elongation at break (C) of Si-TPE with different MP content. | |
4. Conclusions
MP was adopted to improve the flame retardancy of our self-prepared silicone thermoplastic elastomer. In Si-TPE/MP system, MP remarkably catalyzed the chain decomposition, then formed the unique char layers by its condensation products (phosphorous) and the interactions with the silicone in Si-TPE matrix, thus insulating the oxygen and heat, and endowing Si-TPE with excellent flame retardant properties, associating with inert gas released by MP. Additionally, the adoption of MP increased the mechanical properties of Si-TPE ascribing to the enhancement of MP on Si-TPE. When MP content was 28 wt%, the composite with good comprehensive properties was obtained, i.e. mechanical properties including the tensile strength and elongation at break maintained in a stable range and the Young's modulus increased a lot, and UL94 rating reached V0 value, LOI values increased to 28%. The introduction of MP was an efficient approach for the preparation of Si-TPE with high performance, and showed promise for the future commercial applications.
Conflicts of interest
There are no conflicts of interest to declare.
Acknowledgements
This work was supported by Science and Technology Planning Project of Sichuan Province (2016GZ0369) and Cheng Du Gui Bao Science & Technology Co., Ltd, Chengdu, China.
References
- A. S. Fawcett and M. A. Brook, Macromolecules, 2014, 47, 1656–1663 CrossRef CAS.
- J. E. Puskas and Y. Chen, Biomacromolecules, 2004, 5, 1141–1154 CrossRef CAS PubMed.
- V. Tanrattanakul and P. Bunkaew, eXPRESS Polym. Lett., 2014, 8, 387–396 CrossRef CAS.
- C. Jiao, J. Zhuo and X. Chen, Plast., Rubber Compos., 2013, 42, 374–378 CrossRef CAS.
- J. A. Jofre-Reche, Appl. Polym. Sci., 2011, 103, 2782–2787 Search PubMed.
- J. E. Puskas and Y. H. Chen, Biomacromolecules, 2004, 5, 1141–1154 CrossRef CAS PubMed.
- S. C. Shit and P. Shah, Natl. Acad. Sci. Lett., 2013, 36, 355–365 CrossRef CAS.
- F. Yan, X. Zhang, F. Liu, X. Li and Z. Zhang, Composites, Part B, 2015, 75, 47–52 CrossRef CAS.
- B. S. J. Heiner and M. Persson, Polym. Test., 2003, 22, 253–257 CrossRef.
- M. S. U. Khan, Z. Akhter, T. Naz, A. S. Bhatti, H. M. Siddiqi, M. Siddiq and A. Khan, Polym. Int., 2013, 62, 319–334 CrossRef.
- K. R. Strudwick, R. C. Wallis and R. D. Bridges, EP 0404895 A4, 1991.
- J. H. Wang, C. T. Ji, Y. T. Van, D. Zhao and L. Y. Shi, Polym. Degrad. Stab., 2015, 121, 149–156 CrossRef CAS.
- L. Hong and X. Hu, J. Macromol. Sci., Part B: Phys., 2016, 55, 175–187 CrossRef CAS.
- X. Chen, M. Li, J. Zhuo, C. Ma and C. Jiao, J. Therm. Anal. Calorim., 2016, 123, 439–448 CrossRef CAS.
- J. S. Young and B. K. Kim, Trans. Electr. Electron. Mater., 2006, 7, 283–292 CrossRef.
- J. L. Zhuo, J. Dong, C. M. Jiao and X. L. Chen, Plast., Rubber Compos., 2013, 42, 239–243 CrossRef CAS.
- J. C. Liu, M. J. Xu and B. Li, Chem. Res. Chin. Univ., 2015, 36, 1228–1235 CAS.
- N. Wang, G. Xu, Y. Wu, J. Zhang, L. Hu, H. Luan and Q. Fang, J. Therm. Anal. Calorim., 2016, 123, 1239–1251 CrossRef CAS.
- H. Liao, Y. Liu, J. Jiang, Y. Liu and Q. Wang, J. Appl. Polym. Sci., 2017, 134, 44369 Search PubMed.
- B. Cichy, D. Luczkowska, M. Nowak and M. Wladyka-Przybylak, Ind. Eng. Chem. Res., 2003, 42, 2897–2905 CrossRef CAS.
- X. P. Hu, Y. L. Li and Y. Z. Wang, Macromol. Mater. Eng., 2004, 289, 208–212 CrossRef CAS.
- Y.-y. Ren, L. Chen, Z.-y. Zhang, X.-l. Wang, X.-s. Yang, X.-j. Kong and L. Yang, Polym. Degrad. Stab., 2014, 109, 285–292 CrossRef CAS.
- C. S. Wu, Y. L. Liu and Y. S. Chiu, Polymer, 2002, 43, 4277–4284 CrossRef CAS.
- H.-q. Yin, D.-d. Yuan and X.-f. Cai, J. Therm. Anal. Calorim., 2013, 111, 499–506 CrossRef CAS.
- W. A.-y. Li Xing-jian, Z. Yi-heng and S. Dao-xing, China Elastomerics, 2012, 22, 9–14 Search PubMed.
- Q. Huang, H. Lu, B. Deng and L. Li, Mater. Res. Express, 2017, 4 Search PubMed.
- G. Camino, S. M. Lomakin and M. Lazzari, Polymer, 2001, 42, 2395–2402 CrossRef CAS.
- H. Yang, L. Song, Q. Tai, X. Wang, B. Yu, Y. Yuan, Y. Hu and R. K. K. Yuen, Polym. Degrad. Stab., 2014, 105, 248–256 CrossRef CAS.
- D. Guo, S. Bai and Q. Wang, J. Cell. Plast., 2014, 51 Search PubMed.
- X. Chen, J. Yu, S. Guo, Z. Luo and M. He, J. Macromol. Sci., Part A: Pure Appl.Chem., 2008, 45, 712–720 CrossRef CAS.
- W. Xu and G. Wang, Fire Mater., 2016, 40, 826–835 CrossRef CAS.
|
This journal is © The Royal Society of Chemistry 2018 |
Click here to see how this site uses Cookies. View our privacy policy here.