DOI:
10.1039/C7RA11430C
(Paper)
RSC Adv., 2018,
8, 1385-1391
A novel study on preparation of H2TiO3–lithium adsorbent with titanyl sulfate as titanium source by inorganic precipitation–peptization method
Received
16th October 2017
, Accepted 18th December 2017
First published on 3rd January 2018
Abstract
A peroxy lithium titanate sol was prepared with low-cost and easily available titanyl sulfate as the titanium source, lithium acetate as the lithium source, and aquae hydrogenii dioxidi as the complexing agent using an inorganic precipitation–peptization method. The sol system was aged, centrifugal-washed, dried and calcined to obtain a pure precursor, Li2TiO3, followed by pickling with hydrochloric acid to obtain the H2TiO3–lithium adsorbent. The effects of aging time and calcination temperature on the target product were investigated. The results indicate that the sol-system is stable, which is beneficial for loading on a suitable carrier, such as ceramic foams. Centrifugal-washing, instead of vacuum filtration-washing, is conducive to product formation. The most suitable aging time of precursor sol is 24 h and the appropriate calcination temperature is 750 °C. The lithium drawn-out ratio of samples synthesized in this condition reaches 89.50% after pickling with 0.2 M hydrochloric acid for 8 h at 70 °C. Moreover, the Li+ uptake of the adsorbent (adsorption capacity) reaches 29.96 mg g−1 and 33.35 mg g−1 when the adsorption time is 1 h and 8 h, respectively.
1 Introduction
Lithium plays an increasingly important role in energy, air conditioning, metallurgy aerospace, etc.1 With the development of electronic information technology, numerous studies on efficient chemical batteries,2–5 particularly lithium ion batteries, have been reported. The demand for lithium cannot be met if it is only extracted from solid ore; thus, there is an urgent need to develop methods to extract lithium from liquid ore, such as sea and salt-lake brine, which contain an abundance of lithium. However, traditional precipitation, calcination leaching, carbonization, solvent extraction and salting methods4–7 are not suitable for lithium extraction from sea and salt-lake brine that contain low lithium concentrations. The use of lithium ionic-sieves,1,8,9 which is a new approach to address the above-mentioned problems, have increasingly attracted the attention of researchers because of their various remarkable advantages, such as their reduced dissolution rate and stable structure.
The most frequently used titanium–lithium ionic-sieve precursors are Li2TiO3 and Li4Ti5O12. To prepare them, several synthetic techniques, including solid-state reaction, hydrolysis route, sol–gel process and molten-salt microwave-assisted, have been reported.1,8,10–22 However, it is difficult to use powdery Li2TiO3 in engineering because it suffers from the separation of small solid particles from liquid, washing and regeneration. Ceramic foams are currently widely used in filters, catalyst support, construction, bone scaffold materials, etc.23–25 due to their high permeability, porosity and specific surface. To solve the problems mentioned above, loading Li2TiO3 on ceramic foams can help realize adsorption, elution and regeneration in an ion exchange column.
In our previous studies,26,27 Li2TiO3 was prepared and loaded on ceramic foams via the sol–gel process. However, tetrabutyl titanate, which was employed as a titanium source, is expensive and readily hydrolysed; thus, it is not suitable for industrial applications. Therefore, it is urgent to consider the use of cheap and easily available raw materials. In order to effectively load Li2TiO3 on the matrix, a stable sol system with good dispersity is absolutely necessary. For an inorganic substance, the precipitation–peptization approach is an effective way to achieve this purpose. Generally, in this process, the inorganic substance is first hydrolyzed to obtain the fresh precipitate by controlling pH, followed by filtering, washing and beating the filter cake in deionized water to obtain a uniform suspension. Then, the peptizing agent is added to obtain the stable sol-like mixture. Numerous studies on the preparation of the stable sol-like mixture are available in the literature. Anatase TiO2 colloids, derived from the peptization of TiO2 precipitates with trifluoroacetic acid, was prepared by Yuan et al.28 Li et al. obtained a VO2 sol in air under room temperature using vanadium sulfate as a vanadium source, ammonia as a precipitating agent, and hydrogen peroxide as an initiating agent via inorganic precipitation–peptization method.29 ZnS phosphor sols doped with copper ion were synthesized by the peptization process of sulfide–citrate complex precipitates.30 Furthermore, LaPO4–ZrO2 nanocomposites were also successfully developed with a wet chemical synthetic approach involving precipitation–peptization mechanisms.31 However, to the best of our knowledge, reports regarding the preparation of Li2TiO3 by the precipitation–peptization method are rare.
In this study, a stable sol-like system was prepared with lithium acetate as the lithium source, cheap and easily available titanyl sulfate as the titanium source, and aquae hydrogenii dioxidi as the complexing and peptizing agent,29 which is helpful for loading on a suitable carrier.
2 Experimental
2.1 Preparation of lithium titanate sol
All chemicals were used without any further purification. Titanyl sulfate (CP, Tianjin Guangfu Fine Chemical Research Institution, China) was accurately weighed (8.8 g) and a known volume of deionized water (200 mL, RO pure water), which was obtained from an ultra-pure water machine (UKP-1-100L, Sichuan Youpu Ultra-pure Technology Co., Ltd., China) was added. The mixture was treated in a water bath at 60 °C by continuous stirring to prepare a transparent solution (0.2 mol L−1). Lithium acetate (CP, Shandong Siya Chemical Reagent Co., Ltd., China) was accurately weighed (6.6 g) and the same volume of deionized water (200 mL) was added. The mixture was also treated at 60 °C by uninterrupted stirring to obtain a transparent solution. Concentrated ammonia (10 mL, AR, Chengdu Jinshan Chemical Reagent Co., Ltd., China) was added into the titanyl sulfate solution, which was cooled in advance slowly (about one drop per second) under strong magnetic stirring to produce a white precipitate, during which the pH of the system was regulated at 8–9. Then, the precipitate containing slurry was centrifugal-washed, and similar steps were repeated until sulfate ions were undetectable in the filtrate. The sediment that was eventually centrifuged was diluted with deionized water to obtain a white paste, followed by continuous stirring at room temperature. Then, the CH3COOLi solution, which was cooled in advance, was slowly poured onto the white paste (about one dropper every ten seconds using a glass dropper with a rubber head) with continuous stirring to ensure even mixing, achieving a Li/Ti molar ratio of 2
:
1. Finally, under uninterrupted stirring, 30% H2O2 (22 mL, AR, Chengdu Jinshan Chemical Reagent Co., Ltd., China) solution was slowly poured into the above mixture (about one drop per second) to adjust the Ti4+
:
H2O2 molar ratio to 1
:
4 to peptize the precipitate.
2.2 Preparation and adsorption performance of H2TiO3–lithium ion adsorbent
The precursor sol was aged and then dried in an oven at 80 °C to obtain dry gel, followed by calcination in a muffle at different temperatures (550, 600, 700, 750 and 800 °C) to obtain lithium titanate. The prepared Li2TiO3 was treated with 0.2 mol L−1 hydrochloric acid (AR, Chengdu Jinshan Chemical Reagent Co., Ltd., China) at 70 °C for 8 h in a water bath with a solid to liquid ratio of 5 g/500 mL. In the pickling process, the system was gently stirred at regular intervals to ensure even concentration of ions in solution, during which a few liquid samples were taken for later detection. After pickling, the mixture was filtered to obtain the sediment, followed by washing 2–3 times with distilled water. Then, the precipitate was placed on a surface plate, followed by drying in an oven at 80 °C to obtain the H2TiO3–lithium ion adsorbent. Finally, the adsorbent was used to adsorb Li+ from lithium hydroxide (AR, Chengdu Kelong Chemical Reagent Co., Ltd., China) solution with a Li+ concentration of 1.6 g L−1 at 25 °C and a solid to liquid ratio of 2 g/100 mL.
2.3 Characterization
The crystalline phases of the samples were investigated by an X-ray diffractometer (DX-2700, Dangdong Haoyuan Instrument Co., Ltd., China) using Cu Kα radiation at a scanning rate of 0.05° s−1 and a working voltage/current of 40 kV/40 mA. The viscosity of colloidal sol was measured by a digital viscometer (NDJ-5S, Shanghai Bonsi Instrument Science and Technology Co. Ltd., China). The concentration of Li+ in solution was determined by ICP-AES (IRIS Advantage, Thermo Fisher Scientific, USA).
3 Results and discussion
3.1 Performance of the precursor sol
It was found that the prepared sol changes from opaque yellow to transparent deep yellow, and eventually becomes translucent light yellow with aging (Fig. 1). The sol system is stable after aging for 24 h, and laser permeability is the best at this time as shown in Fig. 2a. In comparison, the laser cannot pass through sol aged for 48 h as shown in Fig. 2b. However, precipitation and the layered phenomenon are not observed, which is primarily related with the zeta potential of the sol system. Colloidal sol particles are negatively charged, and they can stably exist in sol via mutual exclusion. Thus, the sol system is relatively stable.
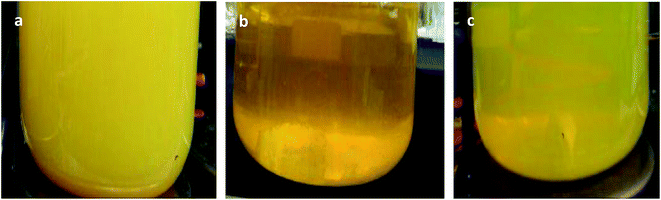 |
| Fig. 1 Comparison of precursor sol aging (a) before aging, (b) aged for 12 h, and (c) aged for 24 h. | |
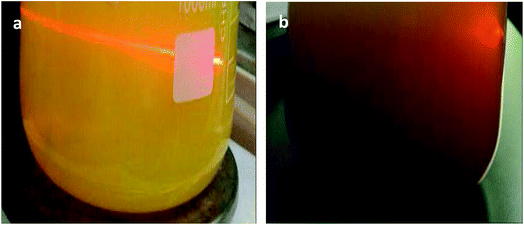 |
| Fig. 2 Laser transmittance of precursor sol (a) aged for 24 h, and (b) aged for 48 h. | |
3.2 Viscosity testing
The viscosities of the prepared sol system aged for different times were measured by a rotary viscometer, and then calculated according to eqn (1). Table 1 shows the variation of sol viscosity with a Ti4+ concentration of 0.1 mol L−1.In eqn (1), η, k, and α are the viscosity, constant, and instrument reading, respectively.
Table 1 Variation of sol viscosity with aging time
Time/h |
2 |
16 |
24 |
40 |
48 |
64 |
Viscosity/mPa s |
2.13 |
2.96 |
3.39 |
5.35 |
10.4 |
324.5 |
It can be observed from Table 1 that viscosity increases from 2.13 to 10.4 mPa s upon aging from 2 to 48 h, and it further increases drastically to 324.5 mPa s upon aging from 48 to 64 h. However, the system does not transform to a gel-state. An appropriate concentration of Ti4+, aging time and viscosity of the sol system are very important to ensure effective loading of sol on ceramic foams. However, sol-systems with high viscosities are not suitable for making membranes. Therefore, a system aged for 24 h is most suited for use as a precursor sol for loading on ceramic foams because it does not form a gel-state and it also has the appropriate viscosity.
3.3 XRD analysis
As shown in Fig. 3, the diffraction peaks of the samples correspond to lithium titanate, and they are indexed to the monoclinic β-Li2TiO3 family (ICDD PDF #033-0831) according to the C2/c (no. 15) space group. It is clear that the Li2TiO3 crystalline phase can be obtained after treating at 550 °C; however, the diffraction peaks are relatively low and broad. With the increase of calcination temperature, the diffraction peaks of Li2TiO3 become strong and sharp, implying improved crystallinity and increased grain size. When the temperature rises to 750 °C, the diffraction peaks of (002) and (−131) increase significantly. When it further increases to 850 °C, the diffraction peaks further strengthen, particularly for the crystal surfaces of (002) and (−131). It is worth mentioning that the diffraction peaks obtained in this study matches quite well with the standard card of Li2TiO3 (ICDD PDF #033-0831). However, in an earlier study reported by Yao et al.,32 the diffraction peak of the crystal surface (002), which is the strongest peak in the standard card, is quite low even after calcination at 850 °C. This is attributed to the different washing methods: centrifugal-washing in this study versus vacuum filtration-washing in their study. It is difficult to completely remove the sulfate ions via vacuum filtration-washing, and the residual sulfate ions in the filter cake have a significant effect on the crystallization orientation of lithium titanate. The titanium loss is relatively large in the pickling process when the diffraction peak intensity is not sufficiently high (550–700 °C). In contrast, an intensity that is too strong (800–850 °C) is not conducive to the subsequent lithium ion extraction. Taking into consideration the crystallization of Li2TiO3 and the subsequent picking process, a calcination temperature of 750 °C is the most suitable, which is in good accordance with our previous study.33
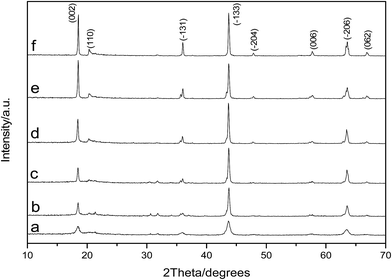 |
| Fig. 3 XRD patterns of Li2TiO3 powders calcined at various temperatures (a) 550 °C, (b) 650 °C, (c) 700 °C, (d) 750 °C, (e) 800 °C, and (f) 850 °C. | |
In addition, the XRD data of the precursor Li2TiO3 prepared by calcination at different temperatures were treated with MDI Jade 6 (Fig. 4); the obtained cell parameters are listed in Table 2. It can be observed from Table 2 that the cell parameters of the samples obtained at different calcination temperatures are all close to those detailed in the standard card (Li2TiO3, ICDD PDF #033-0381), indicating the excellent formation of Li2TiO3. However, there is still a slight difference between them. Taking a comprehensive consideration of a, b, c and β, the values obtained for the sample calcined at 750 °C is the closest to the standard card of Li2TiO3, which illustrates once again that Li2TiO3 precursor calcined at this temperature is optimal.
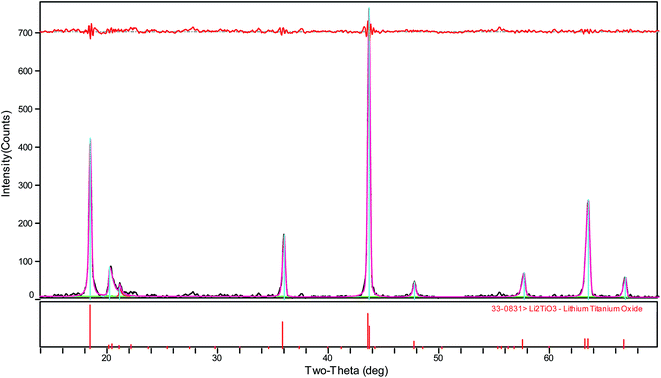 |
| Fig. 4 Processing chart of the cell parameters of Li2TiO3. | |
Table 2 The cell parameters of Li2TiO3 prepared in this work and that of Li2TiO3 from the standard card
Calcination temperatures |
a/Å |
b/Å |
c/Å |
β/° |
550 °C |
5.057 |
8.814 |
9.747 |
99.82 |
650 °C |
5.122 |
8.774 |
9.765 |
101.07 |
700 °C |
5.113 |
8.765 |
9.759 |
100.89 |
750 °C |
5.061 |
8.771 |
9.731 |
99.91 |
800 °C |
5.073 |
8.768 |
9.718 |
99.84 |
850 °C |
5.058 |
8.772 |
9.724 |
99.89 |
ICDD PDF #033-0831 |
5.069 |
8.799 |
9.759 |
100.2 |
The XRD patterns of the specimens before and after acid-treatment were also investigated as shown in Fig. 5. It can be clearly observed that the diffraction peaks change markedly after pickling. The intensities of the diffraction peaks at 2θ of 43.6° and 63.5°, which are assigned to the crystal planes (−133) and (−206), respectively, apparently decrease after acid-modification. However, the diffraction peaks of (−133) and (−206) have not completely disappeared. This behavior is similar to that observed in our previous study,26 but different from the observation in another study reported by our group.33 This is because for a perfect structure of Li2TiO3, in the (−133) lattice plane, two titanium ions together with one lithium ion in the 4e Wyckoff sites are present in an ordered arrangement in the slab.34 Once the insertion of lithium ions into the cell of anatase TiO2 takes place, the basic structure of the (−133) lattice plane is formed.34 Formation of Li2TiO3 can be considered as the introduction of the specific target ion Li+ into the lattice of TiO2, followed by recrystallization processed by high temperature calcination to fix Li+ in the lattice with Li+ in the state of an ionic bond. Adsorbent preparation can be regarded as the extraction of the objective Li+ with hydrochloric acid from the lattice, accompanied by the entrance of H+, ensuring the electrically neutral solution. The exchange sites vacated by Li+ due to extraction are quite narrow. However, they have special selectivity for accepting Li+ because of the memory effect. Other ions cannot occupy the sites until both the following aspects are met: the first is a similar ionic radius; the second is an approximate energy of dehydration. Thus, the as-synthesized adsorbent has a selective adsorption performance to Li+.35
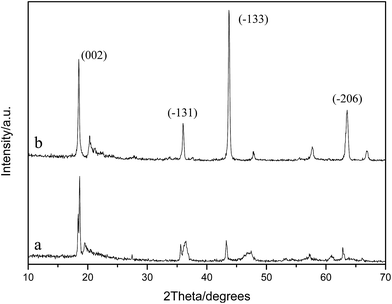 |
| Fig. 5 XRD patterns of Li2TiO3 before and after acid treatment (a) after pickling, and (b) before pickling. | |
As we know, Li+ is easily combined with ionic bonds, while H+ generally forms covalent compounds. Therefore, in the pickling process, with Li+ extracted from the lattice, H+ enters simultaneously, maintaining the electrical neutrality of the solution. However, hydrogen ions do not always replace lithium ions in situ, and the combination state of H+ in the lithium adsorbent is different from that of Li+ in the initial Li2TiO3 precursor. H+ exists in the lithium adsorbent via electrostatic attraction, while Li+ exists in the initial Li2TiO3 precursor through ionic bonding. As a result, the diffraction peak of (−133) decreases apparently or even disappears completely after pickling. In this study, the diffraction peak decreases sharply after pickling, indicating that a predominant proportion of Li+ has been extracted. However, it can be observed in Fig. 5 that this diffraction peak has not completely disappeared, which is due to the following calculated lithium ion drawn-out rate of 89.50%. There are still some lithium ions that are not extracted by hydrochloric acid from Li2TiO3. Moreover, it can also be observed that the intensities of the diffraction peaks of (−131) and (002) slightly decrease. In addition, after acid treatment, the corresponding diffraction peaks of the (−131) and (002) crystal faces shift slightly toward high diffraction angles, indicating that the hydrogen ions exchange with lithium ions when Li2TiO3 is treated with hydrochloric acid, and the crystal interplanar spacing narrows after acid-treatment.8
3.4 Composition and adsorption performance of H2TiO3–lithium ion adsorbent
The composition of lithium adsorbent, H2TiO3, was analyzed and a suitable formula is given as LixHyTiO3 (x + y = 2, 0 ≤ x < 2, y > 0). The crystal structure of Li2TiO3 can be better described by the formula Li[Li1/3Ti2/3]O2 in relation to its layered structure. The structure can be represented as a cubic close packing of oxygen atoms with metal atoms placed in octahedral voids.1 Li and Ti form two types of layers in the Li2TiO3 structure: one (Li) layer is occupied only by Li atoms, the other (LiTi2) layer is occupied by 1/3 of Li and 2/3 of Ti.1 Furthermore, Li+ in the (Li) layer constitutes 75% of the total number of lithium ions in the Li2TiO3 structure, while the remaining 25% are located in the (LiTi2) layers.36 The activity of Li+ at (LiTi2) layers is different from that at (Li) layers. During the pickling process, lithium ions in the (Li) layers are first exchanged to form H[Li1/3Ti2/3]O2, followed by further exchange of Li+ in the (LiTi2) layers to form the fully exchanged phase H[H1/3Ti2/3]O2.37 With the change in the Li+ drawn-out ratio, the values of x and y will change, while the sum of x and y would be equal to 2. Therefore, a suitable formula to describe the composition of lithium adsorbent should be LixHyTiO3 (x + y = 2, 0 ≤ x < 2, y > 0).
Furthermore, the adsorption of Li+ by the obtained lithium adsorbent was also carried out, and the result shows that the Li+ uptake of the adsorbent (adsorption capacity) reaches 29.96 mg g−1 and 33.35 mg g−1 when the adsorption time is 1 h and 8 h, respectively. It can be observed that the lithium ion adsorbent prepared by the method described in this study also shows excellent adsorptivity. In addition, the adsorption capacity at 1 h reaches 89.8% of that at 8 h, which indicates that the adsorption of Li+ by the adsorbent prepared by this method is quite fast. This performance is favorable for the rapid extraction of lithium from brine.
4 Conclusion
A stable peroxide lithium titanate sol was prepared by the inorganic precipitation–peptization method with titanyl sulfate as the titanium source, which is helpful for loading of Li2TiO3 on a suitable carrier to solve its engineering application problem derived from the separation of small solid particles from liquid, washing and regeneration. Compared with vacuum filtration-washing, centrifugal-washing assists in the formation of Li2TiO3, the suitable aging time of the sol is 24 h, and the appropriate calcination temperature is 750 °C. The lithium drawn-out ratio of samples runs up to 89.50% after pickling with hydrochloric acid for 8 h, and the Li+ uptake of the adsorbent reaches 33.35 mg g−1.
Conflicts of interest
There are no conflicts to declare.
Acknowledgements
This work was funded by the Basic Theory Research Project of Neijiang Normal University (No. 15JC10), the Key Project of Natural Science of Sichuan Provincial Education Department (No. 16ZA0309), the Doctoral Research Start-up Funding of Neijiang Normal University (No. 0015B16), and the Open Fund of Key Laboratory of Sichuan Provincial College (No. KF17002).
References
- R. Chitrakar, Y. Makita, K. Ooi and A. Sonoda, Lithium recovery from salt lake brine by H2TiO3, Dalton Trans., 2014, 43, 8933–8939 RSC.
- Y. Li, J. Song and J. Yang, A review on structure model and energy system design of lithium-ion battery in renewable energy vehicle, Renewable Sustainable Energy Rev., 2014, 37, 627–633 CrossRef.
- A. Sonoca and J. Jeswieta, A review of lithium supply and demand and a preliminary investigation of a room temperature method to recycle lithium ion batteries to recover lithium and other materials, Proc. CIRP, 2014, 15, 289–293 CrossRef.
- C. Tan, J. Cao, A. M. Khattak, F. Cai, B. Jiang, G. Yang and S. Hu, High-performance tin oxide-nitrogen doped graphene aerogel hybrids as anode materials for lithium-ion batteries, J. Power Sources, 2014, 270, 28–33 CrossRef CAS.
- B. Xia, C. Chen, Y. Tian, W. Sun, Z. Xu and W. Zheng, A novel method for state of charge estimation of lithium-ion batteries using a nonlinear observer, J. Power Sources, 2014, 270, 359–366 CrossRef CAS.
- A. H. Hamzaoui, H. Hammi and A. M'nif, Operating conditions for lithium recovery from natural brines, Russ. J. Inorg. Chem., 2007, 52, 1859–1863 CrossRef.
- S. W. Van Ginkel, Y. Tang and B. E. Rittmann, Impact of precipitation on the treatment of real ion-exchange brine using the H2-based membrane biofilm reactor, Water Sci. Technol., 2011, 63, 1453–1458 CrossRef CAS PubMed.
- X. C. Shi, Z. B. Zhang, D. F. Zhou, L. F. Zhang, B. Z. Chen and L. L. Yu, Synthesis of Li+ adsorbent (H2TiO3) and its adsorption properties, Trans. Nonferrous Met. Soc. China, 2013, 23, 253–259 CrossRef CAS.
- L. Tian, M. Wei and M. Han, Adsorption behavior of Li+ onto nano-lithium ion sieve from hybrid magnesium/lithium manganese oxide, Chem. Eng. J., 2010, 156, 134–140 CrossRef CAS.
- C. Xu, Y. J. Li, L. Li, X. Y. Wang, Q. Han, M. M. Ren and W. Q. Ye, Effect of Cl− on the properties of Li2TiO3 ceramic powders synthesized by in situ hydrolysis, Ceram. Int., 2014, 40, 7213–7218 CrossRef CAS.
- X. W. Wu, Z. Y. Wen, X. X. Xu, Z. H. Gu and X. H. Xu, Optimization of a wet chemistry method for fabrication of Li2TiO3 pebbles, J. Nucl. Mater., 2008, 373, 206–211 CrossRef CAS.
- X. W. Wu, Z. Y. Wen, B. Lin and X. G. Xu, Sol–gel synthesis and sintering of nano-size Li2TiO3 powder, Mater. Lett., 2008, 62, 837–839 CrossRef CAS.
- A. Sinha, S. R. Nair and P. K. Sinha, Single step synthesis of Li2TiO3 powder, J. Nucl. Mater., 2010, 399, 162–166 CrossRef CAS.
- R. Ramaraghavulu, S. Buddhudu and G. Bhaskar Kumar, Analysis of structural and thermal properties of Li2TiO3 ceramic powders, Ceram. Int., 2011, 37, 1245–1249 CrossRef CAS.
- Y. J. Li, C. Xu, X. Y. Wang, L. Li and L. Kong, Synthesis of Li2TiO3 ceramic breeder powders by in situ hydrolysis and its characterization, Mater. Lett., 2012, 89, 25–27 CrossRef CAS.
- S. J. Lee, Y. H. Park and M. W. Yu, Fabrication of Li2TiO3 pebbles by a freeze drying process, Fusion Eng. Des., 2013, 88, 3091–3094 CrossRef CAS.
- D. Q. Dong, F. B. Zhang, G. L. Zhang and Y. F. Liu, Synthesis of Li4Ti5O12 and its exchange kinetics with Li+, Acta Phys.-Chim. Sin., 2007, 23, 950–954 CAS.
- A. Deptuła, M. Brykała, W. Łada, T. Olczak, B. Sartowska, A. G. Chmielewski, D. Wawszczak and C. Alvani, Preparation of spherical particles of Li2TiO3 (with diameters below 100 μm) by sol–gel process, Fusion Eng. Des., 2009, 84, 681–684 CrossRef.
- A. Laumann, K. T. Fehr, M. Wachsmann, M. Holzapfel and B. B. Iversen, Metastable formation of low temperature cubic Li2TiO3 under hydrothermal conditions—Its stability and structural properties, Solid State Ionics, 2010, 181, 1525–1529 CrossRef CAS.
- T. Plachy, M. Mrlik, Z. Kozakova, P. Suly, M. Sedlacik, V. Pavlinek and I. Kuritka, The electrorheological behavior of suspensions based on molten-salt synthesized lithium titanate nanoparticles and their core–shell titanate/urea analogues, ACS Appl. Mater. Interfaces, 2015, 7, 3725–3731 CAS.
- Y. Shen, M. Søndergaard, M. Christensen, S. Birgisson and B. B. Iversen, Solid state formation mechanism of Li4Ti5O12 from an anatase TiO2 source, Chem. Mater., 2014, 26, 3679–3686 CrossRef CAS.
- Z.-Y. Ji, F.-J. Yang, Y.-Y. Zhao, J. Liu, N. Wang and J.-S. Yuan, Preparation of titanium-base lithium ionic sieve with sodium persulfate as eluent and its performance, Chem. Eng. J., 2017, 328, 768–775 CrossRef CAS.
- P. Ciambelli, V. Palma and E. Palo, Comparison of ceramic honeycomb monolith and foam as Ni catalyst carrier for methane autothermal reforming, Catal. Today, 2010, 155, 92–100 CrossRef CAS.
- S. Zuercher, K. Pabst and G. Schaub, Ceramic foams as structured catalyst inserts in gas-particle filters for gas reactions—Effect of backmixing, Appl. Catal., A, 2009, 357, 85–92 CrossRef CAS.
- F. K. Juillerat, R. Engeli, I. Jerjen, P. N. Sturzenegger, F. Borcard, L. Juillerat-Jeanneret, S. Gerber-Lemaire, L. J. Gauckler and U. T. Gonzenbach, Synthesis of bone-like structured foams, J. Eur. Ceram. Soc., 2013, 33, 1497–1505 CrossRef.
- L. Zhang, D. Zhou, G. He, Q. Yao, F. Wang and J. Zhou, Synthesis of H2TiO3–lithium adsorbent loaded on ceramic foams, Mater. Lett., 2015, 145, 351–354 CrossRef CAS.
- L. Zhang, D. Zhou, Q. Yao and J. Zhou, Preparation of H2TiO3–lithium adsorbent by the sol–gel process and its adsorption performance, Appl. Surf. Sci., 2016, 368, 82–87 CrossRef CAS.
- S. J. Yuan, Y. G. Li, Q. H. Zhang and H. Z. Wang, Anatase TiO2 colloids derived from the peptization of TiO2 precipitates with CF3COOH and their photocatalytic activities, Adv. Mater. Res., 2012, 465, 44–50 CrossRef CAS.
- Y. Li, P. Jiang, W. Xiang, F. Ran and W. Cao, A novel inorganic precipitation–peptization method for VO2 sol and VO2 nanoparticles preparation: synthesis, characterization and mechanism, J. Colloid Interface Sci., 2016, 462, 42–47 CrossRef CAS PubMed.
- N. Uekawa, M. Ouchi, C. M. Wen, T. Matsumoto and T. Kojima, Synthesis of copper ion doped ZnS phosphor sols by peptization process of sulfide–citrate complex precipitates, J. Ceram. Soc. Jpn., 2015, 123, 924–928 CrossRef CAS.
- K. Shijina, S. Sankar, M. Midhun, M. Firozkhan, B. N. Nair, K. G. Warriera and U. N. S. Hareesh, Very low thermal conductivity in lanthanum phosphate–zirconia ceramic nanocomposites processed using a precipitation–peptization synthetic approach, New J. Chem., 2016, 40, 5333–5337 RSC.
- Q. Yao, J. Zhou, L. Zhang, S. Yang and D. Zhou, Study on H2TiO3–lithium exchanger synthesized by precipitation–peptization method, Iron, Steel, Vanadium, Titanium, 2017, 38, 38–44 Search PubMed.
- L. Zhang, D. Zhou, G. He, F. Wang and J. Zhou, Effect of crystal phases of titanium dioxide on adsorption performance of H2TiO3–lithium adsorbent, Mater. Lett., 2014, 135, 206–209 CrossRef CAS.
- C. L. Yu, K. Yanagisawa, S. Kamiya, T. Kozawa and T. Ueda, Monoclinic Li2TiO3 nano-particles via hydrothermal reaction: Processing and structure, Ceram. Int., 2014, 40, 1901–1908 CrossRef CAS.
- D. Tang, D. Zhou, J. Zhou, P. Zhang, L. Zhang and Y. Xia, Preparation of H2TiO3–lithium adsorbent using low-grade titanium slag, Hydrometallurgy, 2015, 157, 90–96 CrossRef CAS.
- M. Vijayakumar, S. Kerisit, Z. Yang, G. L. Graff, J. Liu, J. A. Sears, S. D. Burton, K. M. Rosso and J. Hu, Combined 6,7Li NMR and molecular dynamics study of Li diffusion in Li2TiO3, J. Phys. Chem. C, 2009, 113, 20108–20116 CAS.
- T. A. Denisova, L. G. Maksimova, E. V. Polyakov, N. A. Zhuravlev, S. A. Kovyazina, O. N. Leonidova, D. F. Khabibulin and E. I. Yur'eva, Metatitanic acid: Synthesis and properties, Russ. J. Inorg. Chem., 2006, 51, 691–699 CrossRef.
|
This journal is © The Royal Society of Chemistry 2018 |
Click here to see how this site uses Cookies. View our privacy policy here.