DOI:
10.1039/C7NJ02523H
(Paper)
New J. Chem., 2018,
42, 103-110
Morphology-controlled fabrication of biomorphic alumina-based hierarchical LDH compounds for propane dehydrogenation reaction
Received
12th July 2017
, Accepted 2nd October 2017
First published on 27th November 2017
Abstract
A new material, MgAl-LDHs/Al2O3 fiber (abbreviated as MAF), was prepared using the classical hydrothermal method with a modification in this paper. The influence of different pH values on the structure and catalytic performance of catalysts for propane dehydrogenation was studied. The as-prepared materials were characterized by XRD, SEM, TEM, SAED, N2-physisorption, NH3-TPD, and TPO. Experimental results show that the pH value of the solution directly controlled the vertical growth of LDH sheets on Al2O3 fibers. After the suitable growth of LDH sheets, the dispersed state of active metal Pt was improved and the sizes were stabilized successfully at high temperature. Due to the effect of these LDH sheets, the BET surface and the regular pore system of the PtSn/15MAF catalysts were enhanced compared with the PtSn/CPMA catalysts. Finally, the propane dehydrogenation performance indicates that, when the pH was equal to 8.5, the catalysts (PtSn/15MAF) showed the highest conversion, selectivity and stability.
1. Introduction
Hierarchically structured layered double hydroxides (LDHs) are attracting significant attention owing to their high surface areas, large pore volumes, variable morphologies and microstructures.1 These structural features make them promising candidates for a variety of applications such as bioseparation, catalysis, pollution control, chemical sensing and biomedicine.2–7 As catalysts, layered double hydroxide (LDH) materials have been developed for various catalytic reactions such as green aqueous media, the conversion of benzaldehyde (XBA), highly efficient NOx capture, and catalytic soot combustion.8–10 So far, Cai et al. have successfully prepared porous Ni–Mn oxide nanosheets in situ formed on nickel foam as 3D hierarchical monolith de-NOx catalysts.11 Li et al. have also prepared 3D flower-like NiMnFe mixed oxides by in situ synthesis of monolith catalysts for selective catalytic reduction of NO with NH3.12 Besides, Du et al. reported coke- and sintering-resistant monolithic catalysts derived from in situ supported hydrotalcite-like films on Al wires for dry reformation of methane.13 The interesting properties of hierarchical LDHs may result from the synergism and coupling effect of micro- to nanostructures.
Al2O3, particularly with nanoscale pores, is extensively adopted as a catalyst support, owing to its distinct chemical properties.14,15 Furthermore, the structure and morphology of Al2O3 can be easily controlled by adjusting the preparation conditions. Notably, hierarchically structured LDHs have been prepared using an in situ crystallization method successfully, which involves direct growth of LDH crystallites on an Al2O3 substrate.16–18 The substrates provide inspiration for designing and fabricating hierarchical LDHs with tuneable morphology and structure. The controlled preparation of hierarchical LDHs seems to be directly obtained by controlling the morphology and structure of the substrates. By applying the in situ synthesis technique, Zhang and his co-workers19 have successfully synthesized porous LDHs based on crystal growth on the surface of Al2O3. Although there have been extensive studies on LDH materials, the preparation of hierarchically porous LDHs is still complicated and extremely challenging.20,21 In this work, we take advantage of the structures of biological materials and design a novel route to fabricate high performance MgAl-LDHs/Al2O3 fiber composites, which will have promising applications in catalysis. The Al2O3 fibers could not only enhance the dispersity of MgAl-LDHs on the support, but also increase the specific surface area of the catalysts to improve the reactivity. In this route, hollow Al2O3 fibers were obtained by copying the structures of cotton fibers; the hierarchically porous MgAl-LDHs/Al2O3 composites can be obtained by crystal growth on the surface of the microtube walls of the Al2O3 fibers. The structure, morphology and composition of the composites can be controlled by tuning the preparation conditions.22 It is well known that various synthesis conditions such as identity of the precursor, preparation methods, preparation temperature, molar ratios of metals, and preparation pH values have significant effects on the structural properties of support materials.23 For hierarchically structured LDHs based on Al2O3 fibers, the positively charged hydroxide sheets and intercalated anions are orderly stacked based on the strong electrostatic interaction and hydrogen bonding, resulting in the small molecules being limited by the interlayer space of the LDHs, which could contribute to dispersion of the small molecules.
Recently, supported platinum–tin catalysts have been studied in depth since they show high activity and selectivity in the process.15,24–26 Based on these research studies, to achieve a high catalytic level, Xia et al.23,27 prepared a PtSn catalyst based on MgAl-LDHs, which has been verified to be an effective method to enhance the catalytic capacity to resist coke during the reaction. Besides, Zhang et al.28 also proposed that the presence of zinc in the PtSnK/ZSM-5 catalyst could strengthen the interactions between the Sn species and the support. So far, many kinds of materials have been used as catalyst supports in dehydrogenation of propane. Among them, Zhang et al. compared different supports (ZSM-5, γ-Al2O3, mesoporous alumina, SBA-15) of PtSn-based catalysts for propane dehydrogenation.24 They found that a relatively large surface area and uniform pore size distribution of the support are favorable for the dispersion of metallic particles. Besides, supports having wide pore size distribution, such as coke, could be more easily covered on the external surface of the support instead of the metallic surface.29–31 However, although great efforts have been made to improve the catalytic performances of PtSn catalysts, the reaction selectivity and stability are still unsatisfactory. So it is very necessary to identify the relationships of the support structure and catalytic performance by changing the micromorphology of the support.27,31–33
Herein, based on the above hypothesis, we report a novel propane dehydrogenation catalyst with a PtSn active component embedded in the interlayer of LDHs.18,20 The LDHs could serve as excellent supports and enhance the catalytic activity due to the strong interaction with PtSn.34,35 In addition, the synthesized Pt NPs could show higher diffusion because of the lattice-induced effect of the LDH sheets. Furthermore, growth of the Sn element can be restrained because of the spatial confinement effect of the laminates of the LDH sheets.
2. Experimental
2.1 Synthesis of the material
Preparation of a biomorphic Al2O3 fiber.
Biomorphic Al2O3 fibers were prepared based on structure replication of degreased cotton fibers. In a typical preparation, 10 mmol of Al(NO3)3·9H2O was dissolved in 100 mL of ethanol solution to prepare the alumina sol precursor. Then, 1.05 g of degreases cotton was immersed into the precursor sol for 3 h, followed by ultrasonic treatment for 1 h. The infiltrated cotton fibers were washed with distilled water to remove non-adsorbed metal ions. After drying at 80 °C for 12 h, the sample was calcined for 4 h to obtain cotton based Al2O3 fibers.19
Preparation of biomorphic MgAl-LDHs/Al2O3 fiber composites.
The biomorphic MgAl-LDHs/Al2O3 fiber composites were prepared based on the vertical growth of MgAl-LDH nanocrystals on the surfaces of Al2O3 fibers. The preparation of composites was carried out using a classical hydrothermal method with a modification. The detailed preparation process is described as follows: 6 mmol of MgSO4·7H2O and 5, 15, or 30 mmol of urea were dissolved in 75 mL of distilled water in a 100 mL autoclave Teflon vessel whose pH value was 7.7, 8.5 or 10.0, respectively. Then, 4.6 mmol of the as-prepared Al2O3 fiber was immersed in the above mixed solution. The growth temperature of MgAl-LDHs was maintained at 120 °C for 10 h. Finally, the products were collected and washed thoroughly with distilled water several times, and finally dried in a vacuum oven at 80 °C. According to the addition of different amounts of urea, the materials were named as 5MAF, 15MAF, and 30MAF, respectively.
Preparation of LDH compounds.
LDH compounds were prepared using the co-precipitation method. The detailed preparation process is described as follows: a solution composed of 6 mmol of MgSO4·7H2O and 9.2 mmol Al(NO3)3 was dissolved in a three mouth flask, then the urea solution (1 mol L−1) was added dropwise to the above solution up to pH = 8.5. The above solution was maintained at 120 °C under vigorous stirring for 10 h. Finally, the products were collected and washed thoroughly with distilled water several times, and finally dried in a vacuum oven at 80 °C. The compound was named as CPMA.
2.2 Preparation of the catalysts
PtSn/xMAF (x represents 5, 15, and 30 respectively) and PtSn/CPMA catalysts were prepared using a co-impregnation method on the support. 6 g xMAF and CPMA were impregnated in a solution mixture of 2.14 ml H2PtCl6 (Pt content: 14 mg ml−1), 3.0 ml SnCl4 (Sn content: 20 mg ml−1), 4.0 ml C2H5OH, 0.75 ml HCl (wt% = 10%) and 2.11 ml H2O at 80 °C for 4 h, respectively. After that, the prepared catalyst was dried at 80 °C for 3 h. The nominal composition of each sample was 0.25 wt% Pt, and 0.5 wt% Sn. Finally, the catalyst was calcined at 500 °C for 5 h, and reduced under H2 at 500 °C for 8 h.
2.3 Catalyst characterization
Powder X-ray diffraction (XRD) patterns of all the products were conducted on a Bruker D-8 Advance X-ray diffractometer with Cu Kα radiation, generated at 40 kV and a current of 30 mA. An angular range from 5° to 90° was recorded using step scanning and long counting times to determine the position of the peaks. The nitrogen adsorption–desorption isotherms were measured at −196 °C on a Micromeritics ASAP 2000 apparatus. The samples were evacuated under a vacuum of 5 × 10−3 Torr at 350 °C for 15 h. The data of the pore structure were analyzed by the BJH (Barrett–Joyner–Halenda) method using the Halsey equation for the multilayer thickness. Inductively coupled plasma (ICP) optical emission spectrometry was used for the determination of the metal content in each sample after the hydrothermal treatment. The measurements were performed using a JA1100 inductively coupled plasma quantometer, and the sample was dissolved in a mixture of HF and HNO3 acids before the measurement. The platinum dispersion was observed by Transmission electron microscopy (TEM). TEM experiments were conducted on a JEM-1230 microscope operated at 100 kV. The samples for the TEM measurements were suspended in ethanol and supported on a Cu grid. The crystal morphology of the different supports was investigated by SEM using S3400. Surface acidity was measured by NH3-TPD in a Tp-5000 apparatus at ambient pressure. The sample (150 mg) was preheated at 500 °C for 1 h and then cooled to room temperature under He flow. At this temperature, sufficient pulses of NH3 were injected until adsorption saturation. TPD was carried out from 100 °C to 500 °C with a heating rate of 10 °C min−1 and with helium (30 ml min−1) as the carrier gas. Temperature-programmed oxidation (TPO) was measured using the same apparatus as that for NH3-TPD. About 0.15 g of the sample was placed in a quartz reactor at room temperature, then heated up to 700 °C at a rate of 10 °C min−1 in a 5% O2/He mixture (30 ml min−1).
2.4 Catalyst reaction
Propane dehydrogenation was carried out in a quartz tubular micro-reactor. Reaction conditions for propane dehydrogenation were a reaction temperature of 590 °C, a pressure of 0.1 Mpa, a H2/C3 molar ratio of 0.25 and a weight hourly space velocity (WHSV) of propane of 3.0 h−1. The reaction products were analyzed using an online GC-14C gas chromatograph (Shimadzu Japan).
3. Results and discussion
3.1 Physicochemical properties of the materials
In this work, we designed PtSn/MgAl-LDHs/Al2O3 fiber (abbreviated as MAF) catalysts. The new material, MAF, was synthesized using the in situ crystal growth method with different amounts of urea, and then bimetallic PtSn catalysts supported by these materials were applied to the propane dehydrogenation (PDH) reaction. Various methods of characterization were employed to discuss the correlations between the catalytic properties and the performance of the MAF support structure. The XRD patterns of different samples are shown in Fig. 1. After deposition of degreased cotton in the Al-sol solution, the diffraction peak of the calcined sample (Fig. 1a) is similar to that of traditional Al2O3, indicating the formation of an amorphous alumina fiber. For the MAF sample (Fig. 1b), there are some new diffraction peaks that appear between 10° and 70°, corresponding to the basal reflections of (003), (006), (012), (015) and (018) of LDHs, due to the in situ growth of the LDH sheets on the Al2O3 fiber surface. The XRD patterns clearly certify that the MAF sample was synthesized successfully.
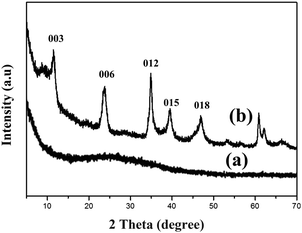 |
| Fig. 1 XRD patterns of (a) Al2O3 fiber and (b) MAF samples. | |
To better understand the MgAl-LDH structure in a series of xMAF materials, Fig. 2a–d represents the scanning electron micrographs of different samples. From Fig. 2a, it can be seen that the CPMA sample exhibits a typical two-double sheet structure, which is quite uniform with sheet sizes of 1–2 μm in width. As expected, after the growth of the MgAl-LDH sheets on the Al2O3 fiber surface, the morphological characteristics of the Al2O3 fiber surface are different. By comparison, for the samples, the nanosheets with larger sizes can also be obtained by either increasing the amount of urea to increase the rate of dissolution or decreasing the concentration of magnesium nitrate to decrease the rate of nucleation. Corresponding results (Fig. 2b–d and the corresponding insets) show that the size and thickness of the nanosheets also increased, which demonstrates that the pH value of the reaction solution could control the growth of MgAl-LDHs sheets on the Al2O3 fiber surface.36 It is not difficult to find that when the pH value is 10, the height of the LDH sheets grows up to ∼1.5 μm. According to the observation of SEM images, the fabrication of xMAF samples has been achieved successfully.
 |
| Fig. 2 SEM micrographs of different samples: (a) CPMA, (b) 5MAF, (c) 15MAF, and (d) 30MAF. The corresponding insets respresent the thickness of the LDH sheets. | |
Fig. 3(b–d) display the TEM images of (b) PtSn/5MAF, (c) PtSn/15MAF, and (d) PtSn/30MAF, and the insets at the bottom are the size distribution histograms of Pt NPs of the PtSn/xMAF samples. From the size distribution histograms, the Pt NPs exhibit an average particle diameter of around 1–3 nm. It can be inferred that, because of the lattice-induced effect of the MgAl-LDH sheets of the PtSn/xMAF samples which could control the dispersed state of the metallic active center effectively, the sizes of these Pt cubes would be stabilized successfully. The SEM image of PtSn/15MAF calcined at 600 °C is displayed in Fig. 3a. Compared to Fig. 2b, it is not difficult to find that the morphological characteristics of MgAl-LDH sheets growing on Al2O3 fiber (Fig. 3a) undergo great changes, which is because a portion of the MgAl-LDH sheets would transform into layered double oxide at 500 °C, corresponding to the XRD pattern of PtSn/15MAF samples in Fig. 4. Furthermore, from Fig. 3a, we could find that the MgAl-LDH sheets still remained in the vertical position of growth, which was due to the essential properties of xMAF supports. The SAED pattern obtained from the PtSn/15MAF sample (the inset of Fig. 3b at the top) demonstrated the existence of Pt NPs on the PtSn/xMAF samples again. The EDS mappings together with TEM demonstrated the uniform distribution of Pt and Sn elements, again.37 The above data clearly verified the successful synthesis of PtSn/xMAF propane dehydrogenation catalysts.
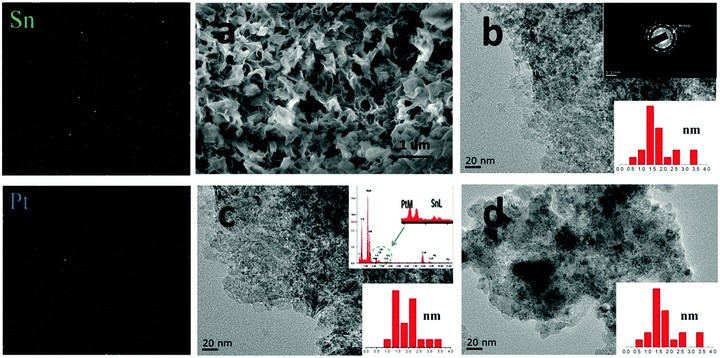 |
| Fig. 3 SEM image of (a) PtSn/15MAF calcined at 600 °C; TEM images of (b) PtSn/5MAF, (c) PtSn/15MAF, and (d) PtSn/30MAF. The corresponding insets are the SAED pattern and the size distribution histograms of Pt NPs, respectively. The EDS mappings obtained from the PtSn/15MAF sample represent the distribution of Pt and Sn elements. | |
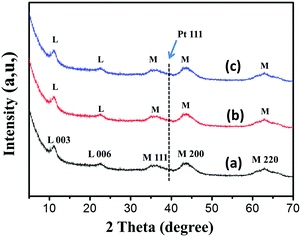 |
| Fig. 4 X-ray diffraction patterns of the as-synthesized (a) PtSn/3MAF, (b) PtSn/15MAF and (c) PtSn/30MAF samples. The diffraction peaks of MgAl-LDHs and MgO are marked as L and M, respectively. | |
The X-ray diffraction (XRD) patterns of the synthesized samples are shown in Fig. 4. Fig. 4a–c show the XRD patterns of the PtSn/xMAF catalysts, and the strong diffraction peaks at 2θ = 11.76 and 23.50 can be indexed to the (003) and (006) reflections, respectively, approaching the characteristic reflections of MAF, which clearly verifies that the MgAl-LDH sheets would still remain unchanged at 500 °C. The detected peaks at 35.50°, 43.25° and 64.30° are indexed to (111), (200) and (220) planes of MgO diffraction, which clearly demonstrates the existence of layered double oxide (MgO–Al2O3) after roasting at 500 °C. There are no obvious XRD peaks corresponding to Al2O3, indicating that the Al2O3 fibres are amorphous, which is in agreement with Fig. 1a. Because of the reduction reaction of Pt NPs mainly on the interior of the MgAl-LDH sheets and Al2O3 fibers, Pt diffraction was weak, which verifies that the structure of xMAF is thermally quite stable to prevent Pt NPs from sintering. According to the XRD pattern and the above work, it is clearly demonstrated that PtSn/xMAF catalysts have been prepared successfully.
The nitrogen adsorption–desorption isotherms of different samples are shown in Fig. 5(a). The PtSn/Al2O3 fiber sample exhibits a typical type IV adsorption isotherm with a H1 hysteresis loop as defined by IUPAC.14,15 The isotherm displays a sharp step with the increased relative pressure (P/P0) which is characteristic of capillary condensation of nitrogen with mesopores.38 In comparison, after growth of MgAl-LDHs sheets, the PtSn/xMAF samples exhibit type IV adsorption isotherms with a H3 hysteresis loop, demonstrating a disordered mesostructure. Compared with the former PtSn/Al2O3 fiber materials, we assume that these appeared adsorption isotherms in the PtSn/xMAF samples are related to the pore structure of MgAl-LDH sheets. In this case, because the Al2O3 fibers are surrounded by MgAl-LDH sheets, the PtSn/Al2O3 fiber structure correspondingly changes and is different from that of the PtSn/xMAF samples. In addition, the nitrogen adsorption–desorption isotherms of the PtSn/xMAF samples are almost the same as those of PtSn/CPMA, which is verified by the successful growth on the Al2O3 fibers again. In Fig. 5(b), the pore size distributions of different samples are observed. As expected, PtSn/xMAF displays two pore size distributions which might be the reason for the multiple constituents in the materials. The characterization data of different samples are listed in Table 1. As observed, the surface areas of PtSn/xMAF are highly decreased compared with PtSn/Al2O3 fibers, which could be related to the low surface area of MgAl-LDH sheets. However, for the PtSn/15MAF sample, it should be noted when the pH value is 8.5, the surface area of the PtSn/15MAF sample is increased significantly to 223 m2 g−1, which could be attributed to the orderly growth of MgAl-LDH sheets on the Al2O3 fiber surface. In other words, when the pH value is appropriate, the growth of MgAl-LDH sheets would not lead to pore channel blocking of the Al2O3 fibers, which suggests that PtSn/15MAF has great potential as a catalyst and vertical growth of the MgAl-LDH sheets.
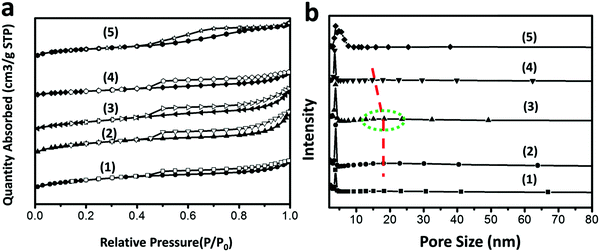 |
| Fig. 5 (a) N2 adsorption–desorption isotherms and (b) the corresponding pore size distribution as obtained from the desorption branch of the different samples: (1) PtSn/5MAF; (2) PtSn/15MAF; (3) PtSn/30MAF; (4) PtSn/CPMA; (5) PtSn/Al2O3 fibers. | |
Table 1 Characterization data of different samples
Sample |
S
BET (m2 g−1) |
S
ext (m2 g−1) |
S
micro (m2 g−1) |
V
p (cm3 g−1) |
D (nm) |
PtSn/5MAF |
179 |
178 |
1.0 |
0.77 |
3.84 |
PtSn/15MAF |
223 |
185 |
37.5 |
1.42 |
3.89 |
PtSn/30MAF |
176 |
175 |
1.0 |
1.27 |
3.84 |
PtSn/CPMA |
87 |
93 |
0 |
1.04 |
3.6 |
PtSn/Al2O3 fiber |
191 |
133 |
58 |
0.73 |
3.88 |
In order to find out the effects of the pH value on the acidity of different samples, NH3-TPD patterns of different samples were carried out and the result is shown in Fig. 6. As detected, two main NH3 desorption peaks are observed in PtSn/Al2O3 fibers, which can be assigned to weak (around 310 °C) and strong (around 510 °C) acid sites. In contrast, it is worth noting that the amount of ammonia desorption is decreased significantly in PtSn/CPMA, especially without any ammonia desorption at low temperature. This indicates that the growth of the MgAl-LDH sheet structure would result in serious blockage of interfaced strong acidic sites in the PtSn/xMAF samples. Meanwhile, the low temperature peaks of the PtSn/5MAF and PtSn/30MAF samples shift toward lower temperature compared with PtSn/Al2O3 fibers, which means that the weak acid sites of PtSn/5MAF and PtSn/30MAF become continuously weaker after growth of MgAl-LDH sheets. However, the low temperature peaks in the PtSn/15MAF samples are toward higher temperature compared with the other PtSn/xMAF samples. Furthermore, it is interesting to observe that the maximum of the low temperature peaks in the PtSn/15MAF samples is similar to that of the parent PtSn/Al2O3 fiber, which means that the growth of MgAl-LDHs sheets on the Al2O3 fiber would not destroy the essential attributes of the Al2O3 fibers. It is not difficult to find that, after the growth of MgAl-LDH sheets on the Al2O3 fiber, the samples present three peaks. Besides, the dium-strong acid sites of the samples are consistent with those of the PtSn/CPMA samples, which is caused by the performance of MgAl-LDHs. Therefore, the performance of the PtSn/15MAF catalyst would result from the interactions between the MgAl-LDH sheets and Al2O3 fibers.
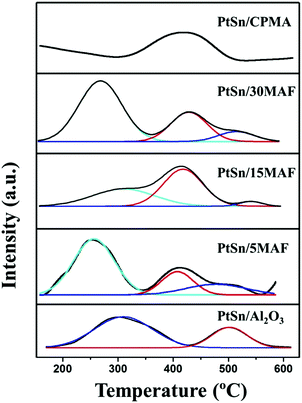 |
| Fig. 6 NH3-TPD patterns of different samples. | |
3.2 Characterization of the catalysts
As mentioned above, in our experiments, the as-prepared xMAF materials were used as the supports, and then PtSn/xMAF catalysts were obtained using the impregnation method. As listed in Table 2, the PtSn/xMAF catalysts display a higher value of platinum dispersion (DH2) than the PtSn/Al2O3 fiber catalyst, which is because the presence of MgAl-LDH sheets may help the adsorption of platinum anions with the interlayer of LDH sheets in the catalyst preparation, thus promoting the distribution of Pt particles. Zhang et al.39 discussed that an excess of Mg species may block the platinum leading to the decrease of metal dispersion, but, because of the characteristics of the vertical growth on the Al2O3 fiber surface, MgAl-LDH sheets could promote the distribution of Pt particles effectively, which would likely affect the properties of the surface of the active metal and the degree of metallic sintering. Such PtSn/xMAF catalysts would possess excellent thermal stability and catalytic activity, which is evidenced by some parameters listed in Table 2. As reported, in propane dehydrogenation reaction, the small Pt NPs would facilitate the desired dehydrogenation reaction, while the undesirable reaction would proceed on the large Pt NPs.40,41 In this case, the suitable growth content of MgAl-LDH sheets would help in suppression of the undesirable reaction and thus affect the catalytic performances in propane dehydrogenation. Further discussions will be presented in the catalytic performance section.
Table 2 Characterization data for different catalysts
Catalysts |
ICP results (wt%) |
D
H2
(%) |
Coke amountb (%) |
Pt |
Sn |
Calculated from the hydrogen chemisorption (HC) experiment.
Experimental value calculated from thermogravimetric (TG) analysis.
|
PtSn/5MAF |
0.48 |
0.84 |
28.6 |
15.6 |
PtSn/15MAF |
0.46 |
0.83 |
32.5 |
7.8 |
PtSn/30MAF |
0.47 |
0.85 |
29.8 |
17.6 |
PtSn/LDHs |
0.46 |
0.84 |
31.2 |
21.3 |
PtSn/Al2O3 fiber |
0.44 |
0.83 |
21.6 |
12.5 |
3.3 Catalytic performance
Fig. 7 shows the catalytic behaviors of different catalysts and the corresponding data are listed in Table 3. As can be seen from Fig. 7(A), the PtSn/CPMA catalyst exhibits the lowest initial reaction activity, and the propane conversion is decreased from 4.5% to 3.5% after reaction for 7 h. This decrease of conversion is related to the carbon deposits that are produced during the reaction, which prevents the active metal on the catalyst from contacting with the reactor gases. Meanwhile, propane conversion of the PtSn/CPMA catalyst is very low, which is likely to be attributed to the lower BET surface of MgAl-LDH sheets and the interlayer of MgAl-LDH sheets surrounding the Pt NPs. After the growth of MgAl-LDH sheets on the Al2O3 fiber, the catalytic activity increased drastically, especially for the PtSn/15MAF catalyst. The main reason is that the unique hierarchical architecture of the PtSn/15MAF not only could favor the diffusion and adsorption of reactant gas in the catalytic reaction, but also promote the distribution of Pt NPs effectively, which would enhance the catalytic activity tremendously.42,43 To further explain these findings, it should be noted that the catalysts are bifunctional and the two active centers of PtSn/xMAF (the metal particles and the acid sites) might work collaboratively: (de)hydrogenation and ring opening occur on the metal particles, whereas isomerization through C3+ carbenium ions occurs on the acid sites.44 Besides these, on the bimetallic PtSn catalyst, platinum is the only active metal and propene is formed on the metal only by dehydrogenation; the main cracking product (ethene) is mainly formed from cracking on the carrier and ethane is formed by hydrogenolysis of propane and by hydrogenation of ethane, with both reactions taking place on the metal.45 According to previous studies, Sn species exist in an oxidized form, which would be favorable for anchoring of Pt to Sn oxide. The Pt sites which anchor to the Sn oxide surface with a “sandwich structure” are the main reaction active sites of PtSn-catalysts. Meanwhile, the complex interplay between the hierarchical material and intrinsic LDH properties such as crystallinity could increase catalytic effectiveness.46 In this case, the equilibrium propane conversion of PtSn/xMAF is much higher than that of other catalysts. Besides, compared with PtSn/5MAF and PtSn/30MAF catalysts, the PtSn/15MAF catalyst shows higher catalytic activity and thermal stability, which further verifies that the pH value has an impact on propane conversion and selectivity. In combination with the result in Table 3, the deactivation parameter of PtSn/15MAF is lower (about 4.5%) in these catalysts, demonstrating the admirable catalytic stability of the PtSn/15MAF catalyst.
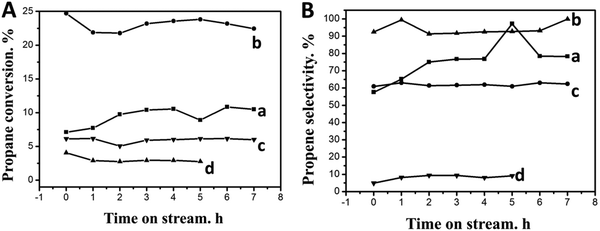 |
| Fig. 7 (A) Propane conversion and (B) propene selectivity of different catalysts for propane dehydrogenation: (a) PtSn/5MAF, (b) PtSn/15MAF, (c) PtSn/30MAF, and (d) PtSn/CPMA. | |
Table 3 Catalytic properties of different catalysts after conducting reaction for 7 h
Sample |
Propane conversion, % |
Propene selectivity, % |
Deactivation parameter, % |
0 h |
7 h |
0 h |
7 h |
PtSn/5MAF |
7.5 |
10.5 |
55.1 |
81.2 |
0 |
PtSn/15MAF |
24.7 |
23.5 |
92.5 |
99.5 |
4.9 |
PtSn/30MAF |
6.8 |
6.5 |
60.1 |
61.2 |
4.4 |
PtSn/LDHs |
4.5 |
3.5 |
5 |
10 |
22.2 |
Catalytic stability.
From the results of the catalytic tests, the reaction activity and stability of the PtSn/15MAF catalyst are superior to those of any other catalysts. Consequently, this catalyst is chosen for the stability test at a temperature of 590 °C. The propane conversion and selectivity to propylene as a function of reaction time are shown in Fig. 8. The result shows that the selectivity to propylene is higher than 99%, and the propane activity is still over 22% after the reaction for 112 h. In conclusion, these results demonstrate that PtSn/15MAF would be a better dehydrogenation catalyst which possesses high catalytic performance and stability.
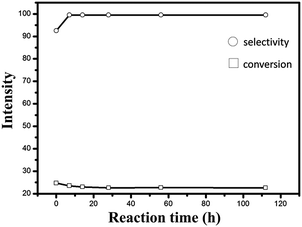 |
| Fig. 8 The reaction conversion and selectivity of the PtSn/15MAF catalyst for 112 h. | |
4. Conclusion
The article demonstrated that different pH values could affect the growth of MgAl-LDH sheets on the Al2O3 fiber, which would deeply modify the surface chemistry and the catalytic behavior of the PtSn-catalyst. The introduction of MgAl-LDH sheets not only modifies the BET surface of the catalysts, but also changes the structural characteristics of the Al2O3 fiber surface. When the pH is equal to 8.5, the catalytic activity and stability for propane dehydrogenation of PtSn/xMAF is found to be the best in these catalysts, which could be attributed to the improved dispersion of Pt NPs and the modified BET surface. Moreover, in combination with the MgAl-LDH sheets and Al2O3 fibers, the xMAF support could prevent the migration of Pt NPs and increase the contact area, which would promote the stability and selectivity of the catalysts. Upon these effects, it is reasonable to believe that PtSn/15MAF would be a great potential catalyst for propane dehydrogenation reaction. In future work, we will introduce some amount of metallic aid to the PtSn/15MAF catalysts to prepare a catalyst with the highest catalytic activity, selectivity and stability.
Conflicts of interest
There are no conflicts to declare.
Acknowledgements
The authors are grateful for the financial support from the National Natural Science Foundation of China (Grant No. 21676056, 51673040, 21376051 and 21306023), ‘‘Six Talents Pinnacle Program’’ of Jiangsu Province of China (JNHB-006), Natural Science Foundation of Jiangsu Province (Grant No. BK20131288), Fund Project for Transformation of Scientific and Technological Achievements of Jiangsu Province of China (Grant No. BA2014100), Qing Lan Project of Jiangsu Province (1107040167), The Fundamental Research Funds for the Central Universities (3207045421, 3207046302, 3207046409), and A Project Funded by the Priority Academic Program Development of Jiangsu Higher Education Institutions (PAPD) (1107047002).
References
- X. Guo, F. Zhang, D. G. Evans and X. Duan, Chem. Commun., 2010, 46, 5197–5210 RSC.
- X.-Y. Yu, T. Luo, Y. Jia, R.-X. Xu, C. Gao, Y.-X. Zhang, J.-H. Liu and X.-J. Huang, Nanoscale, 2012, 4, 3466–3474 RSC.
- M. Shao, F. Ning, J. Zhao, M. Wei, D. G. Evans and X. Duan, J. Am. Chem. Soc., 2011, 134, 1071–1077 CrossRef PubMed.
- Y. Zhao, M. Wei, J. Lu, Z. L. Wang and X. Duan, ACS Nano, 2009, 3, 4009–4016 CrossRef CAS PubMed.
- J. Zhao, Y. Xie, W. Yuan, D. Li, S. Liu, B. Zheng and W. Hou, J. Mater. Chem. B, 2013, 1, 1263–1269 RSC.
- Y. Li, Z.-Y. Fu and B.-L. Su, Adv. Funct. Mater., 2012, 22, 4634–4667 CrossRef CAS.
- T. Zhang, Y. Zhou, M. He, Y. Zhu, X. Bu and Y. Wang, Chem. Eng. J., 2013, 219, 278–285 CrossRef CAS.
- C. Li, M. Wei, D. G. Evans and X. Duan, Catal. Today, 2015, 247, 163–169 CrossRef CAS.
- X. Du, D. Zhang, R. Gao, L. Huang, L. Shi and J. Zhang, Chem. Commun., 2013, 49, 6770–6772 RSC.
- L. Dou, T. Fan and H. Zhang, Catal. Sci. Technol., 2015, 5, 5153–5167 CAS.
- S. Cai, D. Zhang, L. Shi, J. Xu, L. Zhang, L. Huang, H. Li and J. Zhang, Nanoscale, 2014, 6, 7346–7353 RSC.
- H. Li, D. Zhang, P. Maitarad, L. Shi, R. Gao, J. Zhang and W. Cao, Chem. Commun., 2012, 48, 10645–10647 RSC.
- X. Du, D. Zhang, L. Shi, R. Gao and J. Zhang, Nanoscale, 2013, 5, 2659–2663 RSC.
- G. Liu, L. Zeng, Z.-J. Zhao, H. Tian, T. Wu and J. Gong, ACS Catal., 2016, 6, 2158–2162 CrossRef CAS.
- S. Gómez-Quero, T. Tsoufis, P. Rudolf, M. Makkee, F. Kapteijn and G. Rothenberg, Catal. Sci. Technol., 2013, 3, 962–971 Search PubMed.
- T. Zhang, Y. Zhou, M. He, X. Bu, Y. Wang and C. Zhang, J. Eur. Ceram. Soc., 2015, 35, 1337–1341 CrossRef CAS.
- T. Zhang, Q. Li, H. Xiao, H. Lu and Y. Zhou, Ind. Eng. Chem. Res., 2012, 51, 11490–11498 CrossRef CAS.
- M. Filez, E. A. Redekop, H. Poelman, V. V. Galvita, M. Meledina, S. Turner, G. Van Tendeloo, C. Detavernier and G. B. Marin, Catal. Sci. Technol., 2016, 6, 1863–1869 CAS.
- T. Zhang, Y. Zhou, X. Bu, J. Xue, J. Hu, Y. Wang and M. Zhang, Microporous Mesoporous Mater., 2014, 188, 37–45 CrossRef CAS.
- S. A. Bocanegra, A. Guerrero-Ruiz, S. R. de Miguel and O. A. Scelza, Appl. Catal., A, 2004, 277, 11–22 CrossRef CAS.
- S. A. Bocanegra, S. R. de Miguel, A. A. Castro and O. A. Scelza, Catal. Lett., 2004, 96, 129–140 CrossRef CAS.
- T. Zhang, Y. Zhou, Y. Wang, X. Bu, H. Wang and M. Zhang, Appl. Clay Sci., 2015, 103, 67–70 CrossRef CAS.
- K. Xia, W.-Z. Lang, P.-P. Li, X. Yan and Y.-J. Guo, J. Catal., 2016, 338, 104–114 CrossRef CAS.
- Y. W. Zhang, Y. M. Zhou, J. J. Shi, S. J. Zhou, X. L. Sheng, Z. W. Zhang and S. M. Xiang, J. Mol. Catal. A: Chem., 2014, 381, 138–147 CrossRef CAS.
- Y. W. Zhang, Y. M. Zhou, H. Liu, L. Y. Bo and M. H. Tang, Fuel Process. Technol., 2009, 90, 1524–1531 CrossRef CAS.
- N.-l. Wang, J.-e. Qiu, Z.-w. Wu, J. Wu, K.-y. You and H.-a. Luo, Appl. Catal., A, 2015, 503, 62–68 CrossRef CAS.
- K. Xia, W.-Z. Lang, P.-P. Li, L.-L. Long, X. Yan and Y.-J. Guo, Chem. Eng. J., 2016, 284, 1068–1079 CrossRef CAS.
- Y. Zhang, Y. Zhou, S. Zhang, S. Zhou, X. Sheng, Q. Wang and C. Zhang, J. Mater. Sci., 2015, 50, 6457–6468 CrossRef CAS.
- H. Xiao, J. Zhang, P. Wang, X. Wang, F. Pang, Z. Zhang and Y. Tan, Catal. Sci. Technol., 2016, 6, 5183–5195 CAS.
- P. P. Sun, G. Siddiqi, W. C. Vining, M. F. Chi and A. T. Bell, J. Catal., 2011, 282, 165–174 CrossRef CAS.
- X. Fan, J. Li, Z. Zhao, Y. Wei, J. Liu, A. Duan and G. Jiang, Catal. Sci. Technol., 2015, 5, 339–350 CAS.
- Y. W. Zhang, Y. M. Zhou, M. H. Tang, X. Liu and Y. Z. Duan, Chem. Eng. J., 2012, 181, 530–537 CrossRef.
- J. Wu, Z. M. Peng, P. P. Sun and A. T. Bell, Appl. Catal., A, 2014, 470, 208–214 CrossRef CAS.
- X. Y. Ma, Y. Y. Chai, D. G. Evans, D. Q. Li and J. T. Feng, J. Phys. Chem. C, 2011, 115, 8693–8701 CAS.
- A. D. Ballarini, C. G. Ricci, S. R. de Miguel and O. A. Scelza, Catal. Today, 2008, 133, 28–34 CrossRef.
- L. Huang, X. Zhao, L. Zhang, L. Shi, J. Zhang and D. Zhang, Nanoscale, 2015, 7, 2743–2749 RSC.
- H. Zhang, Y. Zhang, Y. Zhou, C. Zhang, M. Zhang, S. Zhao, J. Fang and X. Sheng, J. Alloys Compd., 2016, 688, 23–31 CrossRef CAS.
- S. Zhou, Y. Zhou, J. Shi, Y. Zhang, X. Sheng and Z. Zhang, J. Mater. Sci., 2015, 50, 3984–3993 CrossRef CAS.
- Y. Zhang, Y. Zhou, L. Wan, M. Xue, Y. Duan and X. Liu, Fuel Process. Technol., 2011, 92, 1632–1638 CrossRef CAS.
- S. B. Kogan, H. Schramm and M. Herskowitz, Appl. Catal., A, 2001, 208, 185–191 CrossRef CAS.
- H. Zhang, Y. Zhang, Y. Zhou, C. Zhang, X. Sheng, S. Zhao, J. Fang and M. Zhang, RSC Adv., 2016, 6, 70303–70310 RSC.
- T. C. Keller, S. Isabettini, D. Verboekend, E. G. Rodrigues and J. Pérez-Ramírez, Chem. Sci., 2014, 5, 677–684 RSC.
- H. Zhang, Y. Zhang, Y. Zhou, C. Zhang, Q. Wang, Y. Xu and M. Zhang, RSC Adv., 2016, 6, 18685–18694 RSC.
- A. Kuhlmann, F. Roessner, W. Schwieger, O. Gravenhorst and T. Selvam, Catal. Today, 2004, 97, 303–306 CrossRef CAS.
- M. Larsson, M. Hultén, E. A. Blekkan and B. Andersson, J. Catal., 1996, 164, 44–53 CrossRef CAS.
- S. Cai, J. Liu, K. Zha, H. Li, L. Shi and D. Zhang, Nanoscale, 2017, 9, 5648–5657 RSC.
|
This journal is © The Royal Society of Chemistry and the Centre National de la Recherche Scientifique 2018 |
Click here to see how this site uses Cookies. View our privacy policy here.