DOI:
10.1039/C8GC02021C
(Paper)
Green Chem., 2018,
20, 4102-4111
Towards greener stone shot and stone wool materials: binder systems based on gelatine modified with tannin or transglutaminase†
Received
29th June 2018
, Accepted 23rd July 2018
First published on 13th August 2018
Abstract
In the pursuit of greener stone wool and related materials, the development, study and discussion of strong binder systems for such materials based on gelatine modified with tannin or transglutaminase are presented. The first systematic studies and direct comparisons of gelatines with four different gel strengths modified with 3–50% chestnut tree tannin or transglutaminase are presented and discussed. The development of these non-toxic, biopolymer-based binder systems was achieved using composite bars comprising stone shots with submillimeter diameters as a versatile model for stone wool. Contrary to conventional binder systems, the gelatine-based binder systems were able to cure at ambient temperature, and increased unaged and aged mechanical strengths combined with decreased binder solubility were generally observed as a function of increased gel strength and viscosity of the gelatine component. Several of the compositions resulted in mechanical strengths before and after ageing treatments that were within the range of conventional binder systems. Intriguingly, the gelatine-based binder compositions generally appeared less sensitive towards ageing treatment than conventional binders and in several cases even displayed mechanical strengths after ageing treatments that were at a similar level or better than the corresponding unaged strengths. The developed binder systems thus displayed unprecedented “self-healing” properties. The first DMA studies of cross-sections of the composite bars showed that these binder systems could withstand temperatures well above those required and/or commonly encountered in for example the production and general use of stone wool products. The first SEM studies of the composite bars revealed that the binders created a honeycomb-like structure around the stone shots with several thinner bridging points between adjacent stone shots. The development of this highly promising new generation of bio-inspired binder technologies is expected to enable the manufacture of greener stone wool and related materials through the use of non-toxic and natural components that enable an environmentally improved route to these materials via the reduction of adverse environmental effects such as high energy consumption and emissions during the curing process.
Introduction
Volcanic activity at Hawaii produces bundles of a fibrous material which is known as the hair of the volcanic goddess Queen Pele in the local folklore.1 This fibrous material is Nature's version of stone wool fibres and is formed as molten lava is hurled through the colder air. Inspired by this natural process, man-made stone wool fibres are conventionally produced from a stone melt by a cascade spinning process to form fibres that are on average 3–4 μm in diameter.2,3 Stone wool fibres are a remarkably versatile type of fibres and may for example be used as a component in brake pad composites. Arguably more well-known are the stone wool products (Fig. 1, left) which are for example used in fire safe insulation of buildings, acoustical insulation and as growth media.
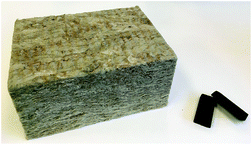 |
| Fig. 1 Examples of stone wool and model composite bars: a prototype stone wool product produced at a ROCKWOOL factory using gelatine modified with tannin as the binder system (left) and model composite bars made using stone shots and gelatine-based binder systems (right). | |
The stone wool fibres in stone wool materials are bound together by an adhesive, termed a binder, typically in an amount of 1–10 wt% of the fibres, and these materials are conventionally produced by spraying an aqueous binder system into the cloud of newly formed stone wool fibres after the cascade spinning process.2,3 The ensemble is then collected and transferred into a curing oven where the binder is cured by blowing heated air through the stone wool.2,3 Traditional stone wool binder systems are based on phenol-formaldehyde resins,4 which may for example be modified with the addition of urea.4,5 Other examples of conventional binder systems comprise acrylic-based and carbohydrate-based binders. Albeit strong, the conventional binder systems require specialised curing equipment such as extensive curing ovens or heat presses operating typically at 200–250 °C to cure properly. This limits the manufacturing possibilities and results in adverse effects such as high energy consumption, high maintenance costs and emissions that may require post-treatment. In an effort to address these issues, the invention of greener binder systems based on non-toxic biopolymers which are able to cure in the vicinity of ambient temperatures was recently published.6,7 To that end, this paper presents the development, study and discussion of highly promising binder systems based on gelatine modified with tannin or transglutaminase. Using a newly developed and highly convenient composite bar method, the first systematic studies and direct comparisons of gelatines with four different gel strengths modified with 3–50% chestnut tree tannin or transglutaminase are presented and discussed. The paper also presents the first studies of these gelatine-based binder systems by means of scanning electron microscopy (SEM) and dynamic mechanical analysis (DMA) as well as the first discussion of the important green advances that these biopolymer based binder systems are expected to deliver.
Gelatine and gelatine modification methods
Gelatine is an extremely versatile protein produced by partial denaturation and hydrolysis of collagen.8 The process may be conducted under acidic or basic conditions leading to type A and type B gelatine, respectively. During this treatment, partial cleavage of the predominantly helical structures found in collagen occurs, leading to warm-water soluble fragments of 5–800 kDa in size.8 The fraction around 100 kDa is of significance for the well-known gelling power of gelatine which is generally in the range of 50–300 bloom. High gelling power gelatines will normally be characterised by high average molecular weights whereas low gelling power gelatines generally will have low average molecular weights.8 The adhesive properties of gelatine have been recognised for thousands of years with certain forms of crude gelatine being used as glues for numerous purposes already during the New Stone Age.8 In addition to warm water solubility, gel formation and adhesive properties, gelatine is non-toxic and able to form strong films,9,10 which is altogether a rare combination of characteristics. However, while water solubility is desirable during the application of a binder system, the resulting stone wool product may encounter humid or wet conditions, for example during installation, where water solubility of the binder may be detrimental. To that end, a plethora of methods for the crosslinking and/or modification of proteins such as gelatine exist. These methods comprise reaction with enzymes such as transglutaminase,11–14 phenolics15 such as tannins,16–23 aldehydes, isocyanates, carbodiimides, epoxides, and genipin.24,25 The two first methods appeared the most appropriate and it is well established that transglutaminase catalyses the transamidation reaction between the side chains of lysine and glutamine residues of the gelatine to generate strong amide linkages.11–14 The modification of gelatine with phenolics such as tannins occurs via a complex combination of hydrogen bonding, ionic interactions and hydrophobic interactions.16–21 Covalent bonds may furthermore be formed under oxidative conditions.18,22 This occurs by oxidation of the phenolic side chains in the tannins yielding quinones which then react with nucleophiles from the gelatine such as the amino end group of the lysine side chains.
Composite bar model method
The studies presented herein are based on the use a newly developed and highly convenient composite bar model method for the development and characterisation of binder systems for stone wool and related products. The method is based on the manufacture and testing of small composite bars composed of stone shots with diameter sizes of 0.25–0.50 mm bound together by the binder system to be investigated (Fig. 1, right). The stone shots are predominantly rounded particles formed during the cascade spinning process of a stone melt in the production of stone wool fibres and thus possess the same chemical composition as the actual stone wool fibres.3 The use of stone shots with diameter sizes of 0.25–0.50 mm results in suitably porous bars which enable the investigation of a wide range of binder systems and application of a broad array of testing methods. In brief, the stone shots and 15 wt% aqueous binder solutions are mixed and shaped into bars that, after curing and drying, have a binder content of approx. 2.9 wt% of the stone shots. Bars made using conventional binder systems are cured at 200–225 °C for 1 h, while binders such as those developed in the present study are cured and dried at room temperature for 2–4 days in total. The resulting bars are then subjected to various treatments and measurements to unveil the properties of the binder system. Ageing resistance is a very important property of stone wool products since they typically remain installed for extended periods of time, and accelerated ageing is simulated by subjecting the bars to autoclave treatment (15 min/120 °C/1.2 bar) or water bath treatment (3 h/80 °C) followed by drying at room temperature. The latter test method furthermore provides information about the level of water solubility of the binder systems presented herein. After these treatments, the mechanical strength of the binder is measured by recording the maximum load force required to break the bars in a three-point bending test. For each data point, an average value is calculated on the basis of five bars that have been subjected to identical treatment. The binder content in the bars is then measured by treating the bars at 590 °C for 30 minutes. In spite of the somewhat inhomogeneous physical appearance of the stone shots, this model method is capable of predicting the relative strengths and properties of binders remarkably well across highly varied binder systems. Bars produced using conventional stone wool binder systems display unaged mechanical strengths in the range 0.25–0.40 kN. These binders commonly loose around 30–50% in strength during ageing treatment and accordingly display aged mechanical strengths in the range 0.15–0.30 kN. These approximate ranges for example comprise representative phenol-urea-formaldehyde binders (0.38 kN unaged, 0.26 kN aged) and representative carbohydrate-based systems (0.28 kN unaged, 0.14 kN aged).26
Results and discussion
Mechanical strengths and water solubilities of composite bars
The composite bar model method was applied to the first systematic study of the binder systems based on gelatine modified with the addition of 3%, 5%, 10%, 20%, 30% and 50% tannin or transglutaminase, respectively, calculated on basis of the gelatine component. IMAGEL® RL, LA, RA and AP, supplied by GELITA AG, were used as model gelatines with defined crosslinking behaviour. These gelatines are all type A gelatines from porcine skin, but are characterised by increasing gel strengths (78, 120, 181 and 305 bloom, respectively) as well as increasing viscosity (1.7, 2.1, 3.0 and 3.9 mPa s, respectively, for 6.67% aq. solutions at 60 °C). This is in addition the first time that the use of very low and very high strength gelatines has been explored. The tannin-modified binder systems were explored using all four gelatines in combination with chestnut tree tannin as model tannin and sodium hydroxide as base. For these binder systems a convenient mixing procedure was developed wherein a solution of the chestnut tree tannin in 1 M sodium hydroxide (pH 9) was added to a stirred solution of the gelatine at 50 °C made basic (pH 9) with 1 M sodium hydroxide. The resulting 15 wt% mixtures had pH 9.0–9.3 and were ready to use after a short time of stirring. The transglutaminase-modified version was studied using IMAGEL® RA and AP as model gelatines. These binders were produced by adding aqueous solutions of transglutaminase to stirred solutions of gelatine at 40 °C and the resulting 15 wt% mixtures had pH 4.4–5.1.
The mechanical strengths of the bars before and after ageing treatments and the corresponding binder contents in the bars produced with these binder compositions are shown in Fig. 2 (tannin-modified binder compositions as solid lines/markers and the corresponding transglutaminase-modified versions as dashed/hollow lines/markers; see ESI† for further details). The calculated relative changes in mechanical strengths of the bars as a result of the ageing treatments are shown in Fig. 3. Fig. 3 also shows the degree of binder solubility, calculated as loss in binder content resulting from water bath ageing.
 |
| Fig. 2 Top row: Unaged (A), autoclave aged (B) and water bath aged (C) mechanical strengths of composite bars made from stone shots and IMAGEL® AP (■, black), IMAGEL® RA (●, blue), IMAGEL® LA (▲, red) and IMAGEL® RL (⧫, green) modified with chestnut tree tannin and sodium hydroxide as well as from stone shots and IMAGEL® AP (□, black, dashed lines) and IMAGEL® RA (○, blue, dashed lines) modified with transglutaminase. Bottom row: Unaged (D), autoclave aged (E) and water bath aged (F) binder contents of the composite bars. Data for the mechanical strengths are expressed as mean ± standard error (n = 5). | |
 |
| Fig. 3 Relative change in mechanical strengths upon autoclave ageing (A) and water bath ageing (B) as well as the degree of binder solubility calculated as loss in binder content as a result of water bath ageing (C) of composite bars made from stone shots and IMAGEL® AP (■, black), IMAGEL® RA (●, blue), IMAGEL® LA (▲, red) and IMAGEL® RL (⧫, green) modified with chestnut tree tannin and sodium hydroxide as well as from stone shots and IMAGEL® AP (□, black, dashed lines) and IMAGEL® RA (○, blue, dashed lines) modified with transglutaminase. | |
As expected, composite bars produced using gelatines without the inclusion of chestnut tree tannin or transglutaminase would dissolve completely during water bath treatment at 80 °C (Fig. 2C and F, illustrated as 0 kN strength and 0% binder content; Fig. 3C, illustrated as 100% binder solubility). However, the modification of the gelatines with even small amounts of chestnut tree tannin or transglutaminase resulted in strong composite bars that would not dissolve during the water bath treatment (Fig. 2 and 3). Importantly, increased unaged and aged mechanical strengths (Fig. 2A–C) combined with decreased water solubility of the binder systems (Fig. 3C) were generally observed as a function of increased gel strength and viscosity of the gelatine component. Accordingly, the first demonstration of the use of the high gel strength gelatine IMAGEL® AP produced the strongest gelatine-based binder compositions to date. Since higher gelling power gelatines normally will be characterised by higher average molecular weights, these observations indicate that the use of gelatines with higher average molecular weights is advantageous in terms of increased binder strength and decreased water solubility. Indeed, binder solubilities down to just a few percent during the harsh water bath treatment (3 h/80 °C) were observed for several of the binder compositions based on the higher strength gelatines (Fig. 3C).
When comparing the two modification methods, similar unaged mechanical strengths were obtained in most cases when using IMAGEL® AP as the gelatine component (Fig. 2A). However, the modification of the comparatively lower gel strength and lower viscosity IMAGEL® RA gelatine with chestnut tree tannin generally produced more advantageous unaged strengths than when using transglutaminase as modification method (Fig. 2A). In spite of these differences, the mechanical strengths after water bath ageing were at comparable levels for the two modification methods (Fig. 2C), albeit the binder solubility was slightly higher for the transglutaminase modified variant than for the chestnut tree tannin modified variant (Fig. 2F and 3C). The two modification methods responded differently to autoclave ageing (Fig. 2B and 3A). Thus, while bars made with the inclusion of 3% transglutaminase were stronger after autoclave ageing than the corresponding bars made with the inclusion of 3% chestnut tree tannin, the opposite was observed for the inclusion of >10% transglutaminase or chestnut tree tannin.
Overall, the use of IMAGEL® RA modified with 3–10% chestnut tree tannin or 3–5% transglutaminase as well as IMAGEL® AP modified with 3–30% chestnut tree tannin or transglutaminase enabled the production of composite bars with unaged mechanical strengths that were within the range of conventional binder systems (0.30–0.40 kN, Fig. 2A). Gradual decreases in unaged and aged mechanical strengths as well as gradual increases in binder solubility were generally observed with the addition of increasing amounts of chestnut tree tannin or transglutaminase (>10–20%) which is presumably due to oversaturation of the binder systems with these components. Importantly, though, the gelatine-based binder systems appeared less sensitive towards ageing treatment than conventional binder systems (Fig. 3A and B). Thus, a considerably broader range of the gelatine-based binder compositions produced composite bars with mechanical strengths after ageing treatment that were within the range of conventional binder systems (0.15–0.30 kN after ageing). This was observed for the use of IMAGEL® RL modified with 5–10% chestnut tree tannin, IMAGEL® LA modified with 10–30% chestnut tree tannin as well as IMAGEL® RA and AP modified with 3–30% chestnut tree tannin or 3–20% transglutaminase (Fig. 2B and C). Intriguingly, the mechanical strengths obtained after ageing treatments were in many instances at a similar level or even better than the unaged strengths. This was for example observed for IMAGEL® RA modified with ≥10% chestnut tree tannin or 5–10% transglutaminase and for IMAGEL® AP modified with 3% chestnut tree tannin or 3% transglutaminase (Fig. 3A and B). The binder systems thus displayed unprecedented “self-healing” properties after having been subjected to the ageing conditions. Various silane-type coupling agents such as 3-aminopropylsilane are typically employed in combination with conventional binder systems to improve the adhesion to the inorganic stone surface.27 Nevertheless, irreversible losses of around 30–50% of the initial strengths are commonly observed for these binder systems after ageing treatment as mentioned above. These strength losses become even more pronounced in the absence of the coupling agents. For example, the strength loss upon ageing increases to 80% for a representative phenol-urea-formaldehyde binder when compared to the unaged reference containing 3-aminopropylsilane. In order to study if the inclusion of 3-aminopropylsilane would have an effect on the interactions between the stone surfaces and the gelatine-based binder systems presented herein, further sets of composite bars were produced from IMAGEL® RA modified with the addition of 0%, 3%, 5%, 10%, and 20% chestnut tree tannin or transglutaminase, respectively. These all comprised 0.2% 3-aminopropylsilane, calculated on basis of the binder content. No significant changes in unaged or aged strengths as well as in binder solubility were observed when compared to the aminosilane-free counterparts. Overall, the gelatine-based binder systems are thus able to generate strong interactions with the stone surface without having to include coupling agents that are typically toxic in uncured form. The observations presented herein indicate that the disruption of interactions that may occur during ageing treatments are of a more reversible nature for the gelatine-based binders than for conventional binders. Importantly, the reduced sensitivity towards ageing treatment in the gelatine-based binders may represent a possibility for reducing the binder content in stone wool products and thereby the environmental impact originating from the binders.
DMA studies of cross-sections of composite bars
The thermal behaviours and properties of composite bars produced using gelatine modified with tannin or transglutaminase as binder systems were for the first time investigated by means of dynamic mechanical analysis (DMA). Composite bars obtained from the use of IMAGEL® LA modified with 10% chestnut tree tannin and IMAGEL® RA modified with 10% transglutaminase were chosen as representative examples. Samples for the DMA measurements were obtained by cutting 2 mm thick cross-sections of these composite bars. The samples were measured in temperature ranges of 30 °C to 150 °C, 200 °C, or 250 °C with a heating rate of 3 °C min−1 and frequency setting of 1 Hz (see Fig. 4 for a representative DMA measurement). The samples were then cooled to ambient temperature, and measured at 30 °C again. The measurements reaching 250 °C allowed for determining transition onset temperatures of 213 °C and 209 °C, respectively, for the two representative gelatine-based binder systems (Table 1, measured as onset of the transition on the storage modulus curve). Increasing the frequency setting to 10 Hz did not appear to affect transition onset temperature significantly, indicating that the transition is a melting point. These values correspond well to both glass transition temperatures and melting points given in the literature for gelatine and gelatine-tannin films measured by DSC.17 As can be seen in Table 1, comparable gradual losses in strengths calculated using the storage modulus curves were observed during heating of the samples from the two different binder systems. Thus, 76–85%, 60–74%, 36–51%, 19–29% and 0–1% of the initial strengths remained at 75 °C, 100 °C, 150 °C, 200 °C, and 250 °C, respectively. Importantly, after having heated the samples to 150 °C, 200 °C or 250 °C followed by cooling and re-measuring at 30 °C, the samples would recover 94–99%, 84–97% and 83–85% of their initial strength, respectively. These findings overall show that the gelatine-based binder systems can withstand temperatures well above those required and/or commonly encountered in for example the production and general use of stone wool products. The stone wool sample depicted in Fig. 1 is indeed a prototype stone wool product produced at a ROCKWOOL factory using gelatine modified with tannin as the binder system.
 |
| Fig. 4 Representative example of a DMA measurement (storage modulus E′) of a cross-section of composite bars made using a gelatine-based binder system. | |
Table 1 Observations from DMA measurements of cross-sections of representative composite bars
Composite bars |
|
Strength of initial during heating (%) |
Strength recovery (%) |
Gelatine |
Modification method |
Transition onset temp. (°C) |
75 °C |
100 °C |
150 °C |
200 °C |
250 °C |
150 °C |
200 °C |
250 °C |
IMAGEL® LA |
10% chestnut tree tannin, NaOH |
213 (n = 2) |
85 (n = 6) |
74 (n = 6) |
51 (n = 6) |
31 (n = 4) |
0 (n = 2) |
99 (n = 2) |
84 (n = 2) |
83 (n = 2) |
IMAGEL® RA |
10% transglutaminase |
209 (n = 2) |
76 (n = 6) |
60 (n = 6) |
36 (n = 6) |
19 (n = 4) |
1 (n = 2) |
94 (n = 2) |
97 (n = 2) |
85 (n = 2) |
SEM studies of break surfaces of composite bars
The break surfaces of composite bars obtained from the use of IMAGEL® LA modified with 10% chestnut tree tannin and IMAGEL® RA modified with 10% transglutaminase were furthermore for the first time investigated by means of scanning electron microscopy (SEM). Fig. 5, top row, and Fig. 6 show the resulting images with view fields of 4.15 mm and 1.38 mm, respectively (see ESI† for larger versions). For comparison, the SEM image of the break surface of a composite bar produced using a conventional phenol-urea-formaldehyde binder as well as the SEM image of binder-free stone shots are included in Fig. 5, bottom row. The selected bars contained comparable amounts of binder and the stone shots were generally characterised by lighter shades while the binders generally had darker shades. As can be seen, intriguingly different surface morphologies between the gelatine-based binders and the conventional phenol-urea-formaldehyde binder were observed. Thus, while the phenol-urea-formaldehyde binder predominantly concentrated in few large connections between the stone shots when cured, the gelatine-based binder systems modified with chestnut tree tannin or transglutaminase created a honeycomb-like structure around the stone shots with several thinner bridging points between adjacent stone shots. The two modification methods appeared to result in comparable overall surface morphologies and the individual breaking points and surfaces can be seen in Fig. 6. These observations provide important insights into the behaviour of these gelatine-based binder systems.
 |
| Fig. 5 SEM images with view fields of 4.15 mm of break surfaces of composite bars produced using IMAGEL® LA modified with chestnut tree tannin and sodium hydroxide (top, left), IMAGEL® RA modified with transglutaminase (top, right), and a conventional phenol-urea-formaldehyde binder (bottom, left). A SEM image of binder-free stone shots is also included (bottom, right). | |
 |
| Fig. 6 SEM images with view fields of 1.38 mm of break surfaces of composite bars produced using IMAGEL® LA modified with chestnut tree tannin and sodium hydroxide (left) and IMAGEL® RA modified with transglutaminase (right). | |
Green advances
The development of this highly promising new generation of bio-inspired binder technologies is expected to enable the manufacture of greener stone wool and related materials. Thus, the use of non-toxic and natural components such as gelatines, tannins and transglutaminase avoids the production, handling and use of conventional binder components and coupling agents that are typically fossil based and/or toxic in their uncured form. Importantly, the conventional binder systems require specialised curing equipment such as curing ovens or heat presses operating typically at 200–250 °C to cure properly. This results in adverse environmental effects such as high energy consumption and emissions during the curing process that might require post-treatment. The gelatine-based binder systems are capable of curing even at ambient temperature which enables drastic reductions in energy consumption and emissions during the manufacturing process, leading to an environmentally improved production. This was indeed observed during the production of the prototype stone wool product displayed in Fig. 1 where gelatine modified with tannin was used as the binder system. However, the adaptation of an existing stone wool production system optimised throughout decades with respect to handling, dosing and curing of conventional binder systems to these new gelatine-based binders that display very different physical and chemical properties represents a considerable challenge. Nevertheless, the gelatine-based binder systems are for example also expected to impose green advances by enabling the reduction of waste streams from the stone wool production. An example is uncured spots and/or areas that may occur in conventional stone wool products arising from improper curing. Products with such flaws are typically recycled which is an energy consuming process. The capability of the gelatine-based binder systems to cure at ambient temperature will reduce or even completely eliminate such waste streams. The low temperature curing nature of the gelatine-based binder systems furthermore enables the direct manufacture of tailor-made products, possibly even on site where they are intended to be installed. This will not only reduce another waste stream of stone wool arising from cutting and fitting products but it may also improve the performance of the products. In addition, the reduced ageing sensitivity of the gelatine-based binders represents a possibility for reducing the binder content in stone wool products and thereby the environmental impact originating from the binders as mentioned above.
Conclusions
In summary, this paper has presented the development, study and discussion of highly promising binder systems for stone wool and related materials based on non-toxic and natural biopolymer components: gelatine modified with tannin or transglutaminase. Contrary to conventional binders, the gelatine-based binder compositions were able to cure at ambient temperature and the development of these binder systems was achieved using a newly developed and highly versatile composite bar model method based on the use of stone shots with submillimetre diameters having the same chemical composition as the actual stone wool fibres. The first systematic studies and direct comparisons of gelatines with four different gel strengths modified with 3–50% chestnut tree tannin or transglutaminase were presented and discussed. These studies have for the first time allowed for establishing that increased unaged and aged mechanical strengths combined with decreased binder solubilities are generally observed as a function of increased gel strength and viscosity of the gelatine component. Indeed, the first demonstration of the use of the high gel strength gelatine IMAGEL® AP produced the strongest gelatine-based binder compositions to date. These observations indicate that the use of gelatines with higher average molecular weights is advantageous for the binder systems. Several of the gelatine-based binder compositions resulted in mechanical strengths before and after accelerated ageing that were within the range of conventional binder systems. This was observed for IMAGEL® RA modified with 3–10% chestnut tree tannin or 3–5% transglutaminase as well as IMAGEL® AP modified with 3–30% chestnut tree tannin or 3–20% transglutaminase. Intriguingly, while conventional binder systems typically suffer strength losses of 30–50% during accelerated ageing treatment even in the presence of coupling agents that improve the adhesion to the inorganic stone surface, the gelatine-based binder compositions generally appeared less sensitive towards ageing treatment. Several of the binder compositions even displayed aged mechanical strengths that were at a similar level or better than the corresponding unaged strengths. This was observed for IMAGEL® RA modified with ≥10% chestnut tree tannin or 5–10% transglutaminase and for IMAGEL® AP modified with 3% chestnut tree tannin or 3% transglutaminase. The developed binder systems thus displayed unprecedented “self-healing” properties. This may for example represent a possibility for reducing the binder content in the products and thereby the environmental impact originating from the binders. The first DMA studies of cross-sections of composite bars made using representative gelatine-based binders showed that the gelatine-based binder systems could withstand temperatures well above those required and/or commonly encountered in for example the production and general use of stone wool products. The first SEM studies of the break surface of composite bars made using the gelatine-based binder systems as well as with a conventional phenol-urea-formaldehyde binder revealed intriguingly different surface morphologies. Thus, while the phenol-urea-formaldehyde binder predominantly concentrated in few large connections between the stone shots when cured, the gelatine-based binder systems modified with chestnut tree tannin or transglutaminase created a honeycomb-like structure around the stone shots with several thinner bridging points between adjacent stone shots.
The development of this new and highly promising generation of bio-inspired binder technologies is expected to enable the manufacture of greener stone wool and related materials. This is achieved through the use of non-toxic and natural components that enable an environmentally improved route to these materials via the reduction of adverse environmental effects such as high energy consumption and emissions during the curing process. This was indeed observed in the production of the prototype stone wool product displayed in Fig. 1. Further green advances are for example also expected to be obtained through reduced recycling and the direct manufacture of tailor-made products, possibly even on-site where it is intended to be installed. The study and development of these highly promising binder systems will continue and the advances will be reported in due course.
Experimental
General experimental methods
IMAGEL® RL gelatine (Type A, porcine, 78 bloom, 1.67 mPa s at 6.67%/60 °C, 11.8% loss on drying, pH 4.92 at 6.67%/60 °C), IMAGEL® LA gelatine (Type A, porcine, 120 bloom, 2.06 mPa s at 6.67%/60 °C, 11.6% loss on drying, pH 5.08 at 6.67%/60 °C), IMAGEL® RA gelatine (Type A, porcine, 180 bloom, 3.00 mPa s at 6.67%/60 °C, 11.9% loss on drying, pH 5.13 at 6.67%/60 °C) and IMAGEL® AP gelatine (Type A, porcine, 305 bloom, 3.90 mPa s at 6.67%/60 °C, 10.8% loss on drying, pH 5.31 at 6.67%/60 °C) were obtained from GELITA AG and have a defined crosslinking behaviour. Chestnut tree tannin (Vinoferm Tannorouge, food grade) was obtained from Brouwland bvba. TI transglutaminase formula was obtained from Modernist Pantry. Sodium hydroxide was obtained from Sigma-Aldrich. For simplicity, these reagents were assumed completely pure and anhydrous. Measurements of pH were performed using a Mettler Toledo SevenCompactTM S220 pH meter equipped with a Mettler Toledo InLab® Expert Pro-ISM pH electrode and temperature probe. The DMA measurements were acquired on a Mettler Toledo DMA 1 calibrated against a certified thermometer at ambient temperature and the melting points of certified indium and tin. Samples with approximate dimensions of 2.2–2.5 cm × 1.1 cm × 2 mm for the DMA measurements were obtained by cutting 2 mm thick cross-sections of composite bars. The DMA apparatus was operated in single cantilever bending mode; titanium clamps; clamp distance 1.0 cm; temperature segment type; temperature range 30-150/200/250 °C; heating rate 3 °C min−1; displacement 20 μm; frequency 1 Hz (10 Hz for transition temperature tests); single frequency oscillation mode. The measurements were evaluated using STARe software Version 12.00 and the transition temperatures are given as an average value of the transitions onsets determined on the storage modulus curves. Scanning electron microscopy (SEM) images were obtained using a Tescan VEGA3 instrument, with 20 keV acceleration voltage and back scatter detector (BSE). To avoid charging of the sample, low vacuum (10 Pa) was used. The images in the graphical abstract were obtained after gold coating of the samples using a Leica EM ACE200.
Stone shots formed during the cascade spinning process of a stone melt in the production of stone wool fibers were obtained from a ROCKWOOL factory in Denmark (for example from collection underneath the spinners) and sifted to remove shots with >1.2 mm diameter sizes as well as any remaining stone wool bundles. The stone shots were then heat treated overnight at 590 °C to remove any trace organics. After cooling, the stone shots were sifted again, this time isolating the fractions with diameter sizes of 0.25–0.50 mm while the fractions with smaller or larger diameter sizes were discarded. The stone shot fractions with diameter sizes 0.25–0.50 mm were washed thoroughly first in cold tap water and then in demineralised water. The sifted and cleaned stone shots were dried overnight at 120 °C, allowed to cool to ambient temperature, and where then stored at ambient temperature in a closed container until use.
FUNKTION heat resistant silicone forms for manufacture of bars (4 × 5 slots per form; slot top dimension: length = 5.6 cm, width = 2.5 cm; slot bottom dimension: length = 5.3 cm, width = 2.2 cm; slot height = 1.1 cm) were obtained from F&H of Scandinavia A/S.
Three-point bending tests were recorded on a Bent Tram SUT 3000/520 test machine (test speed: 10.0 mm min−1; rupture level: 50 N; nominal strength: 30 N mm−2; support distance: 40 mm; max deflection 20 mm; nominal E-modulus 10
000 N mm−2). The bars were placed with the “top face” up (i.e. the face with the dimensions length = 5.6 cm, width = 2.5 cm) in the machine.
New tin foil containers for use in measurement of binder contents of composite bars were heat-treated at 590 °C for 15 minutes prior to use to remove all organics.
Chestnut tree tannin solution
To 1 M NaOH (31.5 g) stirred at room temperature was added chestnut tree tannin (9.00 g). After stirring for at least 30 min further at room temperature, the resulting deep red-brown solution was used in the subsequent experiments.
Representative mixing example for gelatine modified with tannin in the presence of sodium hydroxide (IMAGEL® RA modified with 5% chestnut tree tannin)
A mixture of IMAGEL® RA gelatine (12.00 g) in water (66.95 g) was stirred at 50 °C for approx. 15–30 min until a clear solution was obtained (pH 4.9). 1 M NaOH (3.81 g) was then added (pH 9.2) followed by a portion of the above chestnut tree tannin solution (2.70 g; thus efficiently 0.60 g chestnut tree tannin). After stirring for 1–2 minutes further at 50 °C, the resulting brown mixture (pH 9.2) was used in the subsequent experiments. See ESI† for further details on all binder compositions comprising gelatine modified with chestnut tree tannin.
Representative mixing example for gelatine modified with transglutaminase (IMAGEL® RA modified with 5% TI transglutaminase)
A mixture of IMAGEL® RA gelatine (13.00 g) in water (70.85 g) was stirred at 40 °C for approx. 15–30 min until a clear solution was obtained (pH 5.2). A solution of TI transglutaminase (0.65 g) in water (6.50 g) at 40 °C was then added. After stirring for 1–2 minutes further at 40 °C, the resulting tan mixture (pH 4.9) was used in the subsequent experiments. See ESI† for further details on all binder compositions comprising gelatine modified with TI transglutaminase.
Manufacture of composite bars
A 15 wt% binder solution was obtained as described in the examples above. A sample of the binder solution (16.0 g for IMAGEL® RL, LA and RA; 8.40 g for IMAGEL® AP) was mixed well with shots (80.0 g for IMAGEL® RL, LA and RA; 42.0 g for IMAGEL® AP; pre-heated to 40 °C and 50 °C when used in combination with IMAGEL® RA and AP, respectively). The resulting mixture was then filled into four slots (IMAGEL® RL, LA and RA) or two slots (IMAGEL® AP) in a heat resistant silicone form for making bars. During the manufacture of each composite bar, the mixtures placed in the slots were pressed as required and then evened out with a plastic spatula to generate an even bar surface. In general, 28–32 bars were made in this fashion from each binder composition. The production of a surplus of bars allowed for discarding bars during the various treatment processes due to the presence of visual irregularities such as uneven surfaces, cracks and/or air pockets created during the manufacturing process. The resulting composite bars were then cured and dried at room temperature for 1–2 days. The bars were carefully taken out of the containers, turned upside down and left for 1–2 days further at room temperature to cure and dry completely.
Ageing treatment of composite bars
Ageing treatment of composite bars was performed by subjecting the bars to autoclave treatment (15 min/120 °C/1.2 bar) or water bath treatment (3 h/80 °C) followed by cooling to room temperature and drying for 2–3 days.
Measurement of mechanical strengths of composite bars
The maximum load force required to break composite bars was recorded in a three-point bending test. For each data point, an average value was calculated on the basis of five bars that had been subjected to identical treatment.
Measurement of binder content in composite bars
The binder content in the composite bars was measured in small tin foil containers by treatment at 590 °C. The tin foil container was weighed and four bars (usually after being broken in the three-point bending test) were placed into the tin foil container. The ensemble was weighed and was then heat-treated at 590 °C for 30 minutes. After cooling to room temperature, the weight was recorded again and the binder content was calculated as percentage of the stone shots.
Conflicts of interest
There are no conflicts to declare.
Acknowledgements
The authors gratefully thank Dorte B. Johansson, Dr Dorthe Lybye and Kenneth Ramsing from ROCKWOOL International A/S; Dr Berthold Köhler and Dr Matthias Reihmann from GELITA AG; Dr Felix Letzelter from Meissner Bolte as well as Dr Sophie Faure from Université Clermont Auvergne for fruitful discussions and suggestions.
References
-
W. D. Westervelt, Hawaiian Legends of Volcanoes, Ellis Press, Boston, 1916 Search PubMed.
- B. Širok, B. Bizjan, A. Orbanic and T. Bajcar, Chem. Eng. Res. Des., 2014, 92, 80–90 CrossRef.
-
B. Širok, B. Blagojevic and P. Bullen, Mineral Wool Production and Properties, Cambridge International Science Publishing Limited, Cambridge, 2008 Search PubMed.
-
L. Pilato, Phenolic Resins: A Century of Progress, Springer-Verlag, Berlin, 2010 Search PubMed.
- G. He and B. Riedl, J. Polym. Sci., Part B: Polym. Phys., 2003, 41, 1929–1938 CrossRef.
-
T. Hjelmgaard, WO2017194722A1, 2017 Search PubMed.
-
T. Hjelmgaard, WO2017194721A1, 2017 Search PubMed.
-
R. Schrieber and H. Gareis, Gelatine Handbook, Wiley-VCH Verlag GmbH & Co., Weinheim, 2007 Search PubMed.
- For a recent review, see:
S. Benjakul, M. Nagarajan and T. Prodpran, in Edible Films and Coatings: Fundamentals and Applications, ed. M. P. M. García, M. C. Gómez-Guillén, M. E. López-Caballero and G. V. Barbosa-Cánovas, CRC Press, Boca Raton, 2017, pp. 103–124, Films and Coatings from Collagen and Gelatin Search PubMed.
- For a recent review, see:
I. S. Arvanitoyannis, in Protein-Based Films and Coatings, ed. A. Gennadios, CRC Press, Boca Raton, 2002, pp. 275–304, Formation and Properties of Gelatin Films and Coatings Search PubMed.
- S. Kobayashi and A. Makino, Chem. Rev., 2009, 109, 5288–5353 CrossRef PubMed.
- R. A. de Carvalho and C. R. F. Grosso, Food Hydrocolloids, 2004, 18, 717–726 CrossRef.
- M. K. McDermott, T. Chen, C. M. Williams, K. M. Markley and G. F. Payne, Biomacromolecules, 2004, 5, 1270–1279 CrossRef PubMed.
- C. Chen, H. D. Embree, E. M. Brown, M. M. Taylor and G. F. Payne, Biomaterials, 2003, 24, 2831–2841 CrossRef PubMed.
-
W. Vermerris and R. Nicholson, Phenolic Compound Biochemistry, Springer Science + Business Media B. V., Dordrecht, 2008 Search PubMed.
-
C. Peña, G. Mondragon, I. Algar, I. Mondragon, J. Martucci and R. Ruseckaite, in Gelatin Production, Applications and Health Implications, ed. G. Boran, Nova Science Publishers, Inc., New York, 2013, pp 71–85, Gelatin Films: Renewable Resource for Food Packaging Search PubMed.
- C. Peña, K. de la Caba, A. Eceiza, R. Ruseckaite and I. Mondragon, Bioresour. Technol., 2010, 101, 6836–6842 CrossRef PubMed.
- X. Zhang, M. D. Do, P. Casey, A. Sulistio, G. G. Qiao, L. Lundin, P. Lillford and S. Kosaraju, Biomacromolecules, 2010, 11, 1125–1132 CrossRef PubMed.
- X. Zhang, M. D. Do, P. Casey, A. Sulistio, G. G. Qiao, L. Lundin, P. Lillford and S. Kosaraju, J. Agric. Food Chem., 2010, 58, 6809–6815 CrossRef PubMed.
- K. Yi, G. Cheng and F. Xing, J. Appl. Polym. Sci., 2006, 101, 3125–3130 CrossRef.
- R. A. Frazier, A. Papadopoulou, I. Mueller-Harvey, D. Kissoon and R. J. Green, J. Agric. Food Chem., 2003, 51, 5189–5195 CrossRef PubMed.
- G. Strauss and S. M. Gibson, Food Hydrocolloids, 2004, 18, 81–89 CrossRef.
- N. Cao, Y. Fu and J. He, Food Hydrocolloids, 2007, 21, 575–584 CrossRef.
- For a recent review, see:
M. Bertoldo and S. Bronco, in Gelatin Production, Applications
and Health Implications, ed. G. Boran, Nova Science Publishers, Inc., New York, 2013, pp. 1–29, Chemical Methods For Gelatin Crosslinking: A Review Search PubMed.
- For a recent review, see:
R. Schrieber and H. Gareis, in Gelatine Handbook, Wiley-VCH Verlag GmbH & Co., Weinheim, 2007, pp. 63–65, Chemically Modified Gelatines Search PubMed.
- See for example:
T. Hjelmgaard, P. Nissen, L. Nærum and E. L. Hansen, WO201610244A1, 2016 Search PubMed.
- D. V. Okhrimenko, A. Budi, M. Ceccato, M. Cárdenas, D. B. Johansson, D. Lybye, K. Bechgaard, M. P. Andersson and S. L. S. Stipp, ACS Appl. Mater. Interfaces, 2017, 9, 8344–8353 CrossRef PubMed.
Footnote |
† Electronic supplementary information (ESI) available: Further experimental details and data as well as large versions of figures. See DOI: 10.1039/c8gc02021c |
|
This journal is © The Royal Society of Chemistry 2018 |
Click here to see how this site uses Cookies. View our privacy policy here.