DOI:
10.1039/C7CE01847A
(Paper)
CrystEngComm, 2018,
20, 113-121
Shape control of nickel crystals and catalytic hydrogenation performance of ruthenium-on-Ni crystals
Received
23rd October 2017
, Accepted 20th November 2017
First published on 20th November 2017
Abstract
Hierarchical nickel was synthesized by a facile hydrothermal reduction method using hydrazine hydrate as a reducing agent. The morphology of the hierarchical nickel was controlled by changing the hydrothermal temperature and surfactant. Ruthenium supported on hierarchical nickel (Ru/Ni) catalysts were obtained via the galvanic replacement reaction method. The catalytic performance of the Ru/Ni catalysts for benzene hydrogenation was also investigated. The Ru/Ni catalysts can be magnetically recovered after each reaction. The relationship between the catalytic activity and the morphology of the Ru/Ni catalyst was established in this work. The as-obtained hierarchical nickel and Ru/Ni were characterized by scanning electron microscopy (SEM), X-ray diffraction (XRD), X-ray photoelectron spectroscopy (XPS), high-sensitivity low-energy ion scattering (HS-LEIS) spectroscopy, scanning electron microscopy energy dispersive X-ray spectroscopy (SEM-EDS), SEM-EDS mapping, transmission electron microscopy (TEM) and high resolution transmission electron microscopy (HRTEM) techniques.
1 Introduction
Metallic nanomaterials are widely applied in an array of fields, such as heterogeneous catalysis and magnetic, optical and electronic fields.1–7 Their properties are almost dependent on their size, morphology and nanostructure.8,9 To obtain excellent performance, many research groups are focusing on the controllable synthesis of nanomaterials (such as nano-nickel) with a desired shape or size. A large number of hierarchical nickel structures with various morphologies, such as superfine nanoparticles, nanorings, sea-urchin-like and snow-flake-like architectures, chain-like, sphere-like and column-like nanowires, and dendritic-like, fiber-like and needle-like hierarchical nickel, were obtained via different preparation methods or by changing the reaction parameters (e.g. surfactant, solvent, concentration of reagents, temperature and magnetic field).10–17 For example, hierarchical nickel nanoparticles with the shape of urchin-like chains, smooth chains, rings and hexagonal Ni/Ni(OH)2 plates were successfully synthesized using polyvinylpyrrolidone (PVP) as a surfactant by adjusting the reaction conditions: surfactant, the amount of reagents, and temperature.18 The dendritic-like nickel nanostructure was prepared at 160 °C by a hydrothermal approach with the aid of cetyltrimethylammonium bromide (CTAB).19 Wang et al. synthesized sisal-like structural nickel at 160 °C via a hydrothermal approach with the addition of glycine and CTAB.20 The research works of Srivastava's group indicated that the reaction conditions (such as temperature and surfactant) obviously affected the shape and size of nickel powder. A relatively moderate reaction temperature was favourable for the formation of flower-like nickel, while a very high temperature destroyed the flower-like morphology. The size of the flower-like nano-nickel was varied by controlling the capping agent (triethanolamine (TEA), diethanolamine (DEA), and ethylene glycol (EG)).21
Aromatic hydrogenation is an important reaction in the chemical industry (e.g. benzene hydrogenation). The heterogeneous catalysts used for this reaction mainly include Ni-based,22,23 Pt-based,24 Pd-based,25 Ru-based,26–28 Rh-based,29 Ir-based30 and multi-metallic catalysts.31 The above-mentioned catalysts are separated from the hydrogenated products by filtration or centrifugation due to their nanoscale size, which is of relatively high cost. Because of the hierarchical nickel crystal's micrometer size and superior magnetic and heat-conducting characteristics, we selected Ni crystal as a catalyst support to synthesize Ru/Ni supported catalysts to increase their heat and mass transfer rate and reduce separation costs.
Therefore, in this work, the effect of the hydrothermal temperature on the morphology of hierarchical nickel was further investigated under the addition of ethanediamine (EDA), obtaining flower-like nickel with many sharp petals. The shape of the hierarchical nickel was controlled at 150 °C by adding different surfactants such as PVP and CTAB. The Ru supported on hierarchical nickel (Ru/Ni) catalysts were obtained by the galvanic replacement reaction method. All of the as-synthesized Ru/Ni catalysts were tested in the hydrogenation of benzene. The relationship between the morphology and the catalytic performance of the Ru/Ni catalysts was investigated. The Ru/Ni catalysts can be recycled by simple and low-cost magnetic separation because of their magnetism and micro-scale. Thus, the Ru/Ni catalysts have potential in commercial applications.
2 Experimental
The reagents used in this study were purchased from Sinopharm Chemical Reagent Co. Ltd. (Shanghai, China). All reagents were of analytical grade and used as received. The water used in this investigation was deionized water which was prepared by our group.
Preparation of hierarchical nickel
In a typical preparation of hierarchical nickel, nickel(II) chloride hexahydrate, NiCl2·6H2O, (0.7200 g) was placed in a 250 mL conical flask and dissolved in 30 mL of deionized water. Anhydrous ethanol (5 mL) was added to the solution, and then the solution was magnetically stirred for 10 min. Subsequently, 5 mL of ethanediamine (EDA, grade of purity >99.9%) was added to the solution, followed by the addition of 5 mL of aqueous NaOH solution containing 0.7250 g of NaOH and vigorous stirring for 10 min. Then 85 wt% hydrazine hydrate (N2H4·H2O, 5 mL) was injected. After agitation for 10 min, the resulting mixture was transferred into a Teflon-lined stainless-steel autoclave with a capacity of 100 mL for hydrothermal synthesis at X °C for 1 h, where X = 120 °C, 150 °C or 180 °C. After it reached the desired reaction time, the autoclave was naturally cooled to room temperature (RT), and the black solid was collected by filtration, washed thoroughly with distilled water and anhydrous ethanol, and dried in a vacuum at 60 °C for 6 h. The as-obtained samples were denoted as Ni-EDA-X, where X represents the hydrothermal temperature: 120 °C, 150 °C or 180 °C. In order to investigate the effect of surfactant on the morphology of hierarchical nickel, the addition of EDA step was replaced with that of an aqueous PVP solution (0.2000 g of PVP dissolved in 5 mL of deionized water) or aqueous CTAB solution (0.2000 g of CTAB dissolved in 5 mL of deionized water), with other hydrothermal conditions identical to those of the preparation of Ni-EDA-150. These two samples were denoted as Ni-PVP-150 and Ni-CTAB-150, respectively.
Synthesis of ruthenium supported on the hierarchical nickel (Ru/Ni) catalysts
The ruthenium supported on hierarchical nickel (Ru/Ni) catalysts were synthesized by the galvanic replacement reaction method.32–39 Briefly, a certain amount of the above as-obtained hierarchical nickel was added to an aqueous solution of RuCl3 in a pre-calculated volume and with a concentration of 9.64 × 10−3 mol L−1, and then ultrasound was applied at RT for 2 h. After filtration, washing with deionized water and anhydrous ethanol several times and drying in a vacuum oven at 60 °C for 6 h, the Ru/Ni catalysts were obtained. They were denoted as Ru/Ni-EDA-X, Ru/Ni-PVP-150 and Ru/Ni-CTAB-150. The accuracy of Ru loading onto the catalysts was obtained by using inductively coupled plasma atomic mass spectrometry (Agilent ICP-MS 4500-300). The content of Ru is 1.1 wt% in all Ru/Ni catalysts.
Characterization of the catalysts
The crystalline phases of the catalysts were determined by X-ray diffraction (XRD) measurements using a Rigaku Ultima IV X-ray diffractometer equipped with a high-speed array detection system and Cu Kα radiation (40 kV and 30 mA) as the X-ray source. The scanning 2θ range is from 10° to 90°. The morphologies, SEM-EDS spectrum and SEM-EDS elemental mapping results of the catalysts were obtained by using a field-emission scanning electron microscope (MLA650F). The chemical states and composition of the Ru and Ni element on the surface of the catalysts were recorded on a PHI Quantum 2000 scanning ESCA microprobe with monochromatic Al Kα radiation (XPS). The atomic type and composition on the outermost surface of the catalysts were determined by high-sensitivity low-energy ion scattering (HS-LEIS) (IonTOF Qtac100 low-energy ion scattering analyzer), applying 4He+ ions with a kinetic energy of 3 keV and 20Ne+ ions with a kinetic energy of 5 keV. The scattering angle was 145°. Transmission electron microscopy (TEM) and high resolution transmission electron microscopy (HRTEM) images of the samples were obtained by using a FEI TECNAI F20 high-resolution transmission electron microscope with an accelerating voltage of 200 kV.
Testing the catalysts in the benzene hydrogenation reaction
Typically, the catalytic reaction of benzene hydrogenation was performed in a high-pressure autoclave (Parr 4848). 10 mL of benzene and 0.0500 g of catalyst were mixed and added into the reactor. Then, the air in the reactor was replaced with H2, and the H2 pressure was increased to 4.8 MPa. Stirring was started at a speed of 500 rpm and the reaction mixture was heated to the desired temperature (100 °C). After the reaction was maintained at 100 °C for 0.5 h, the reactor was stopped and cooled to about 5 °C quickly in an ice-water bath. Finally, the catalysts were separated from the liquid by magnetic separation. The amount of residual benzene and hydrogenated products was determined by gas chromatography (GC) using a Shimadzu GC 2010 instrument equipped with a DB-35 60 m × 0.32 mm capillary column and a flame ionization detector (FID). The products were identified by gas chromatography-mass spectrometry (GC-MS) using a Shimadzu GC-MS 2010 instrument. The rate of benzene hydrogenation of the catalysts was determined using the equation described below:
r = nconversion of benzene/(ntotal ruthenium × t) |
where nconversion of benzene, t and ntotal ruthenium represent the moles of consumed benzene, reaction time (h) and total moles of ruthenium in the catalysts, respectively. The unit of r is molbenzene molRu−1 h−1.
3 Results and discussion
Effect of hydrothermal temperature on the morphologies of hierarchical nickel
The effect of the hydrothermal temperature on the shapes of hierarchical nickel was investigated by varying the temperature from 120 °C to 180 °C and fixing the concentration of Ni2+ ions (0.1010 mol L−1, 0.7200 g NiCl2·6H2O) and reaction time (1 h) by using EDA as the morphology-modulating agent. XRD patterns for the hierarchical nickel and Ru/Ni samples are shown in Fig. 1. In Fig. 1A, the diffraction peaks located at 2θ = 44.5°, 51.9° and 76.4° can be ascribed to the Ni(111), Ni(200) and Ni(220) planes, respectively, consistent with JCPDS card No. 04-0850.40 No other diffraction peak can be seen, which indicates that Ni(0) crystal with high purity is successfully prepared. Moreover, after the Ru atoms were loaded onto the hierarchical nickel, the XRD signal remains unchanged and there is no diffraction peak corresponding to the Ru crystallite phase (Fig. 1B), probably indicating Ru with nanoclusters or single atoms supported on the hierarchical nickel with high dispersion. The XRD patterns of the as-prepared hierarchical nickel and Ru/Ni samples are very sharp and no characteristic peaks attributed to impurities (such as NiO and Ni(OH)2) can be observed, which suggests pure and good crystallinity of the samples.
 |
| Fig. 1 (A) XRD patterns for the hierarchical nickel synthesized at different temperatures: (a) 120 °C, (b) 150 °C and (c) 180 °C. (B) XRD patterns for the samples after ruthenium was supported on the hierarchical nickel: (a) Ru/Ni-EDA-120, (b) Ru/Ni-EDA-150 and (c) Ru/Ni-EDA-180. | |
Fig. 2 shows the SEM images of the hierarchical nickel prepared at 120 °C (Ni-EDA-120). All the hierarchical nickel crystals present a flower-like morphology. The size of the microscale flower is between 1 μm and 5 μm. Each flower-like nickel structure consisted of a large number of sharp petals with a width of less than 200 nm, looking like a hedgehog. As the synthesis temperature increases up to 150 °C (Ni-EDA-150), the size of the flower-like nickel becomes smaller, but the number of the acute petals in one flower becomes larger (Fig. 3). The major reason is that the high temperature results in a large rate of crystal nucleation and growth.
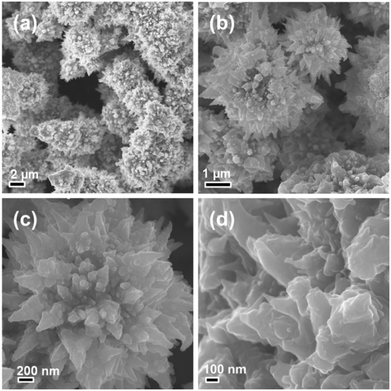 |
| Fig. 2 (a–d) SEM images of the hierarchical nickel prepared at a hydrothermal temperature of 120 °C observed under different magnifications. | |
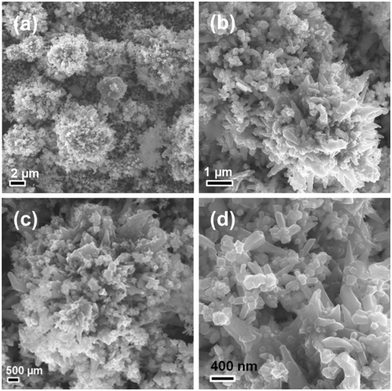 |
| Fig. 3 (a–d) SEM images of the hierarchical nickel prepared at a hydrothermal temperature of 150 °C observed under different magnifications. | |
Fig. 4 shows four typical SEM images of the Ni-EDA-180 sample, which reveals that the petals become rougher and shorter than those in the Ni-EDA-120 and Ni-EDA-150 samples. Another important phenomenon is that a lot of the flower-like nickel with a nanoscale structure is present on the surface of the bulky flower-like nickel.
 |
| Fig. 4 (a–d) SEM images of the hierarchical nickel prepared at a hydrothermal temperature of 180 °C observed under different magnifications. | |
Effect of surfactant on the morphology of hierarchical nickel
Fig. 5 shows the XRD patterns for the hierarchical nickel samples prepared by adding different surfactants with other synthesis conditions the same as in the preparation of Ni-EDA-150. The diffraction peaks of Ni(111), Ni(200) and Ni(220) of the Ni face-centered cubic (fcc) structure are obviously observed at 2θ of 44.5°, 51.9° and 76.4° (JCPDS card No. 04-0850), respectively.40 No other characteristic diffraction peak ascribed to nickel oxides or a nickel hydroxide crystallite phase is present in Fig. 5A. This indicates the high purity of the hierarchical nickel which was prepared by the hydrothermal synthesis method with the addition of various surfactants. Fig. 5B shows the XRD patterns for the hierarchical nickel-supported ruthenium (Ru/Ni) samples. The patterns are very similar to the XRD patterns for the matching hierarchical nickel, without any characteristic diffraction peak indexed as Ru-related crystallite phase. This can be probably explained by low Ru loading and high Ru dispersion in these Ru/Ni catalysts.
 |
| Fig. 5 (A) XRD patterns for the hierarchical nickel synthesized by adding different surfactants: (a) EDA, (b) PVP and (c) CTAB. (B) XRD patterns for the samples after Ru was supported on the hierarchical nickel: (a) Ru/Ni-EDA-150, (b) Ru/Ni-PVP-150 and (c) Ru/Ni-CTAB-150. | |
The morphologies of the hierarchical nickel synthesized at 150 °C by using different surfactants are shown in Fig. 6 (a–d, PVP, and e–h, CTAB). The Ni-PVP-150 sample mainly consists of quasi-nanospheres with a diameter of ∼200 nm, with many Ni particles gathering together. Fig. 6e–h display the SEM images of the Ni-CTAB-150 sample observed under different magnifications, where irregular nickel nanoparticles with a size of ∼50 nm are linked to each other. It can be inferred that the surfactant plays an important role in determining the morphology and structure of the hierarchical nickel.
 |
| Fig. 6 SEM images of the hierarchical nickel prepared by using (a–d) PVP and (e–h) CTAB as surfactants observed under different magnifications. | |
XPS characterization of the Ru/Ni catalysts
Fig. 7 shows the XPS spectra of Ni 2p and Ru 3p for the Ru/Ni-EDA-150 and Ru/Ni-CTAB-150 catalysts. As observed in the Ni 2p XPS spectrum for Ru/Ni-EDA-150 (Fig. 7A), the peaks with binding energies of 852.7, 853.9, 855.4 and 857.1 eV in the Ni 2p3/2 XPS spectra could be attributed to Ni(0), NiO, Ni(OH)2 and NiOOH species, respectively.23,41,42 By comparing the area of each peak, we can find that the Ni oxidized state species such as NiO, Ni(OH)2 and NiOOH are predominant on the surface of this catalyst. However, in the Ru/Ni-CTAB-150 catalyst, the amount of the surface Ni(0) species is much larger than that of Ru/Ni-EDA-150 (Fig. 7B). The most probable reason is that Ni-EDA-150 is flower-like while Ni-CTAB-150 is spherical, and more coordinatively unsaturated nickel atoms are present on the tips and petals of the flower-like nickel, which are very active and easily oxidized when exposed in air for a long time. The Ru 3p XPS spectra for the Ru/Ni-EDA-150 and Ru/Ni-CTAB-150 catalysts are presented in Fig. 7C and D, respectively. The BE (binding energy) at ca. 462 and 484 eV is ascribed to the Ru(0) species, and the BE at 464.2 and 486.2 eV is due to the Ru4+ species.43,44 We find that the Ru4+/Ru(0) ratio on the surface of the Ru/Ni-EDA-150 catalyst is much larger than that on the surface of the Ru/Ni-CTAB-150 catalyst. Additionally, the Ru content of these Ru/Ni catalysts is identical. Highly dispersed Ru atoms are easily oxidized in air. The above XPS results reveal that the Ru atoms loaded onto the surface of Ni-EDA-150 have better dispersion than those on the surface of Ni-CTAB-150.
 |
| Fig. 7 XPS spectra of Ni 2p for (A) Ru/Ni-EDA-150 and (B) Ru/Ni-CTAB-150, and of Ru 3p for (C) Ru/Ni-EDA-150 and (D) Ru/Ni-CTAB-150. | |
HS-LEIS tests for the Ru/Ni catalysts
The atomic composition of the outermost surface of the Ru/Ni catalysts was recorded by using high-sensitivity low-energy ion scattering, and the results are shown in Fig. 8. 4He+ HS-LEIS spectroscopy can give the signal of all the elements on the outer surface but it has low sensitivity to heavy atoms,45 so the 3 keV 4He+ HS-LEIS spectra for the Ru/Ni-EDA-150 and Ru/Ni-CTAB-150 catalysts are depicted in Fig. 8A. This reveals that oxygen, nickel and ruthenium atoms are present on the outermost surface of these catalysts. The intensity of the ruthenium signal in Ru/Ni-EDA-150 is stronger than that in Ru/Ni-CTAB-150, but the intensity of the nickel signal in Ru/Ni-EDA-150 is much lower than that in Ru/Ni-CTAB-150. This demonstrates that the Ru/Ni atomic ratio on the outermost surface of the Ru/Ni-EDA-150 catalyst is much larger than that on the outermost surface of the Ru/Ni-CTAB-150 catalyst, further indicating that the ruthenium atoms on the surface of Ru/Ni-EDA-150 have much better dispersion than those on Ru/Ni-CTAB-150 due to the same Ru loading in these Ru/Ni catalysts. This is in good agreement with the above XPS results. The 5 keV 20Ne+ HS-LEIS spectra for the Ru/Ni-EDA-150 and Ru/Ni-CTAB-150 catalysts are also displayed in Fig. 8B. Similar conclusions can be drawn.
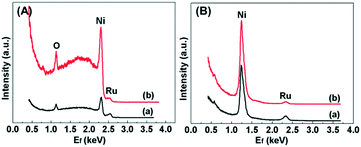 |
| Fig. 8 (A) 3 keV 4He+ HS-LEIS spectra for (a) Ru/Ni-EDA-150 and (b) Ru/Ni-CTAB-150, and (B) 5 keV 20Ne+ HS-LEIS spectra for (a) Ru/Ni-EDA-150 and (b) Ru/Ni-CTAB-150. | |
SEM-EDS and mapping analysis of the Ru/Ni-EDA-150 catalyst
A typical SEM image of the Ru/Ni-EDA-150 catalyst is shown in Fig. 9(a). There was no obvious change in shape and size after ruthenium was loaded onto the hierarchical nickel (Ni-EDA-150), suggesting good stability of the hierarchical nickel crystals. In order to further prove the presence of ruthenium on the surface of the Ru/Ni sample, SEM-EDS and elemental mapping analysis were performed and the results are displayed in Fig. 9(a–e). The SEM-EDS spectrum indicates that the Ru content on the surface (1.30 wt%) is very close to that (1.10 wt%) obtained by using inductively coupled plasma atomic mass spectrometry. The intensity of the nickel elemental map (Fig. 9(c)) is much larger than that of oxygen (Fig. 9(d)) or ruthenium (Fig. 9(e)), demonstrating that Ru was successfully supported on Ni-EDA-150.
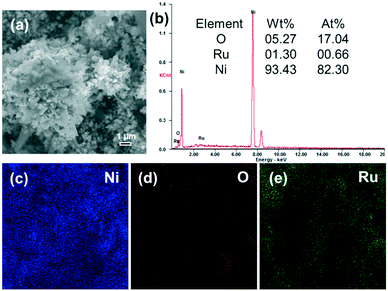 |
| Fig. 9 (a) SEM image, (b) EDS spectrum, and elemental mapping of (c) Ni (blue), (d) O (red) and (e) Ru (green) of the Ru/Ni-EDA-150 catalyst. | |
TEM and HRTEM measurements for the Ni-EDA-150 and Ru/Ni-EDA-150 samples
The TEM and HRTEM images of the Ni-EDA-150 and Ru/Ni-EDA-150 samples are displayed in Fig. 10. As shown in Fig. 10(a and b), the hierarchical nickel crystals mainly have a flower-like morphology, which is very consistent with the results of SEM characterization. The flower petals have a width of 20–100 nm and a length of 50–400 nm. The HRTEM image recorded at the edge of the tip of a petal is shown in Fig. 10c. The distance of the lattice fringe spacing (0.204 nm) corresponded to the Ni(111) planes. The TEM and HRTEM images of Ru/Ni-EDA-150 confirm that the size, shape and nanostructure of the Ni crystals remain unchanged after Ru is loaded onto Ni. The forms of Ru-on-Ni have not been distinguished by a common TEM technique in this work, suggesting that Ru may be in the form of single atoms or nanoclusters on the surface of Ni. Its form will be further characterized by atomic resolution Cs-corrected transmission electron microscopy in our follow-up research.
 |
| Fig. 10 (a and b) Typical TEM and (c) HRTEM images of the Ni-EDA-150 hierarchical nickel. (d and e) Typical TEM and (f) HRTEM images of the Ru/Ni-EDA-150 catalyst. | |
Catalytic activity of the catalysts for the hydrogenation of benzene
The benzene hydrogenation reaction was carried out to test the catalytic performance of the catalysts. The catalytic hydrogenation results are listed in Table 1. The Ni crystal catalysts displayed no activity for this reaction under the reaction conditions (Table 1, entries 1–5) due to the Ni-based catalyst with micrometer size being active for benzene hydrogenation at high temperature (≥140 °C),39 but the reaction temperature in this work was 100 °C (<140 °C). The Ru/Ni-EDA-120 catalyst exhibited low activity with 36% yield of cyclohexane and a benzene hydrogenation rate (r) of 6.8 × 103 molbenzene molRu−1 h−1 (Table 1, entry 6). The yield of cyclohexane was 74% and r was 14.0 × 103 molbenzene molRu−1 h−1 over the Ru/Ni-EDA-150 catalyst (Table 1, entry 7). When the reaction time reached 2 h, the Ru/Ni-EDA-150 catalyst realized the total conversion of benzene under the same reaction conditions, with 100% yield of cyclohexane and with an r of 9.5 × 103 molbenzene molRu−1 h−1 (entry 8 in Table 1). However, for the Ru/Ni-EDA-180 catalyst, 28% of benzene was hydrogenated to cyclohexane with inferior catalytic activity (r = 5.3 × 103 molbenzene molRu−1 h−1) (entry 9 in Table 1). The effect of surfactant on the shape of the hierarchical nickel, thus determining the catalytic behavior of Ru/Ni, is shown in entries 7, 10, and 11 in Table 1. They showed poor hydrogenation activity with a cyclohexane yield of below 20% (Ru/Ni-PVP-150, 18%, and Ru/Ni-CTAB-150, 16%). It could be easily found that the Ru/Ni-EDA-150 catalyst had the most excellent catalytic performance for the hydrogenation of benzene, and the order of the catalytic activity of the Ru/Ni catalyst is flower-like Ru/Ni > sphere-like Ru/Ni > irregular Ru/Ni particles. The reasons mainly include: (1) the high Ru dispersion in Ru/Ni-EDA-150; (2) the tips and probably the petals of the flower-like nickel in Ru/Ni-EDA-150 with more defect sites; (3) there are much more coordinative unsaturated Ru or Ni atoms at the edge of the petals in Ru/Ni-EDA-150 (flower-like) than those in other Ru/Ni catalysts with various morphologies (e.g. nanospheres); (4) certain agglomeration of the hierarchical nickel particles and probably some residual surfactants (PVP or CTAB) on the surface of the Ru/Ni-PVP-150 and Ru/Ni-CTAB-150 catalysts. Moreover, there was no obvious loss of catalytic activity of the Ru/Ni-EDA-150 catalyst when reused another four times under the same reaction conditions (Table 1, entries 12–15), suggesting its relatively good stability. Additionally, the ruthenium-on-hierarchical nickel catalysts showed considerable catalytic performance for benzene hydrogenation with respect to the Ru-based catalysts in the reported studies (see Table 2). The effect of reaction time on the conversion of benzene is presented in Fig. 11. It could be found that the rate of benzene hydrogenation of the Ru/Ni-EDA-150 catalyst increased with increasing reaction time. Benzene was totally hydrogenated to cyclohexane within 2 h.
Table 1 Catalytic performance of the as-prepared catalysts for benzene hydrogenationa
Entry |
Catalyst (0.05 g) |
Yieldb (%) |
r (molbenzene molRu−1 h−1) × 103 |
Reaction conditions: benzene (10 mL), reaction time (1 h), reaction temperature (100 °C), reaction pressure (5.3 MPa).
Yield of cyclohexane.
Reaction time (2 h).
The Ru/Ni-EDA-150 catalyst was reused in the benzene hydrogenation reaction for another four times.
|
1 |
Ni-EDA-120 |
<0.1 |
— |
2 |
Ni-EDA-150 |
<0.1 |
— |
3 |
Ni-EDA-180 |
<0.1 |
— |
4 |
Ni-PVP-150 |
<0.1 |
— |
5 |
Ni-CTAB-150 |
<0.1 |
— |
6 |
Ru/Ni-EDA-120 |
36 |
6.8 |
7 |
Ru/Ni-EDA-150 |
74 |
14.0 |
8c |
Ru/Ni-EDA-150 |
100 |
9.5 |
9 |
Ru/Ni-EDA-180 |
28 |
5.3 |
10 |
Ru/Ni-PVP-150 |
18 |
3.4 |
11 |
Ru/Ni-CTAB-150 |
16 |
3.0 |
12d |
Ru/Ni-EDA-150 |
72 |
13.7 |
13d |
Ru/Ni-EDA-150 |
70 |
13.3 |
14d |
Ru/Ni-EDA-150 |
69 |
13.1 |
15d |
Ru/Ni-EDA-150 |
69 |
13.1 |
Table 2 Catalytic activity of the Ru-based catalysts for benzene hydrogenation in the reported literature
Ref. |
Catalyst |
t
|
P
|
T
|
TOFd |
Yielde (%) |
Reaction time (h).
Reaction pressure (H2, MPa).
Reaction temperature (°C).
Turnover frequency (h−1).
Yield of cyclohexane.
2-Propanol as solvent.
Ionic liquid and water as solvent.
|
46
|
2 mol% perfluoro-tagged Ru |
0.5 |
0.1 |
60 |
29 |
34 |
26
|
Ru/CNTs |
0.5 |
4.0 |
80 |
6983 |
99.97 |
47
|
[H4Ru4(h6-C6H6)4][BF4]2 |
2.5 |
6.0 |
90 |
364 |
100 |
27
|
0.27% Ru/NFS |
2.25 |
0.29 |
25 |
5430 |
100 |
48
|
4.2 wt% Ru/C-silica |
0.53 |
8.0 |
110 |
37 700 |
99.8 |
49
|
Ru/SBA-15 |
— |
1.0 |
20 |
85.3 |
100 |
28
|
3.3 wt% Ru/MMT |
2.5 |
8 |
110 |
4000 |
100 |
50
|
4.6 wt% Ru/MCF-C |
1 |
4.0 |
130 |
17 000 |
19.8 |
50
|
4.6% Ru/rGO |
1 |
4.0 |
130 |
38 000 |
61.3 |
51
|
Ru/MOF |
1.5 |
6.0 |
60 |
3200 |
96 |
 |
| Fig. 11 Effect of reaction time on the conversion of benzene. Reaction conditions: catalyst (Ru/Ni-EDA-150-0.05 g), benzene (10 mL), reaction temperature (100 °C), reaction pressure (5.3 MPa). | |
Furthermore, as shown in Fig. 12a, the Ru/Ni-EDA-150 catalyst was a monolithic catalyst with a large size. The microstructure and morphology of the Ru/Ni-EDA-150 catalyst did not undergo obvious changes after being reused five times. This indicates that the Ru/Ni supported catalyst was highly stable in shape and microstructure after Ru was loaded onto the hierarchical nickel and the hydrogenation reaction. Additionally, the filtration-free Ru/Ni-EDA-150 was almost completely recovered through simple magnetic separation and could be reused for the next reaction (as shown in Fig. 12b), which can greatly reduce its application cost.
 |
| Fig. 12 (a) SEM image of the recycled Ru/Ni-EDA-150 catalyst after the hydrogenation reaction and (b) photograph of the mixture of the Ru/Ni-EDA-150 catalyst and reaction liquid exposed to a magnetic field. | |
4 Conclusions
In summary, hierarchical nickel samples were prepared by a simple hydrothermal synthesis method using hydrate hydrazine as the reducing agent. Their morphologies (such as flower-like and spherical) were controlled by modulating the hydrothermal temperature and surfactants. The Ru/Ni catalysts were synthesized via the method of galvanic replacement reaction. Their catalytic performance was evaluated through the benzene hydrogenation reaction. These catalysts could be easily recovered by a simple and efficient magnetic separation method, which is an environmentally friendly and economical procedure. It was found that the Ru/Ni-EDA-150 catalyst exhibited the most excellent catalytic activity among these catalysts, which can be attributed to ruthenium with better dispersion and many more coordinatively unsaturated metal atoms.
Conflicts of interest
There are no conflicts of interest to declare.
Acknowledgements
We would like to acknowledge the funding support from the National Natural Science Foundation of China (Grant No. 21763011), the Natural Science Foundation of Jiangxi Province of China (Grant No. 20161BAB213083 and 20171ACB21041), the Research Foundation of Education Bureau of Jiangxi Province of China (GJJ160666), the National Natural Science Foundation of China (21607064), the Program of 5511 Talents in Scientific and Technological Innovation of Jiangxi Province (20165BCB18014), and the Academic and Technical Leaders of the Main Disciplines in Jiangxi Province (20172BCB22018).
Notes and references
- B. Wu and N. Zheng, Nano Today, 2013, 8, 168–197 CrossRef CAS.
- L. Wu, A. Mendoza-Garcia, Q. Li and S. Sun, Chem. Rev., 2016, 116, 10473–10512 CrossRef CAS PubMed.
- S. Chen, B. Zhang, D. Su and W. Huang, ChemCatChem, 2015, 7, 3290–3298 CrossRef CAS.
- C. A. Mirkin, R. L. Letsinger, R. C. Mucic and J. J. Storhoff, Nature, 1996, 382, 607–609 CrossRef CAS PubMed.
- H. Shang, K. Pan, L. Zhang, B. Zhang and X. Xiang, Nanomaterials, 2016, 6, 103, DOI:10.3390/nano6060103.
- Y. Wang, W. He, L. Wang, J. Yang, X. Xiang, B. Zhang and F. Li, Chem. – Asian J., 2015, 10, 1561–1570 CrossRef CAS PubMed.
- X. Xiang, W. He, L. Xie and F. Li, Catal. Sci. Technol., 2013, 3, 2819–2827 CAS.
- C. Burda, X. Chen, R. Narayanan and M. A. El-Sayed, Chem. Rev., 2005, 105, 1025–1102 CrossRef CAS PubMed.
- L. Polavarapu, S. Mourdikoudis, I. Pastoriza-Santos and J. Pérez-Juste, CrystEngComm, 2015, 17, 3727–3762 RSC.
- A. Mathew, N. Munichandraiah and G. M. Rao, Mater. Sci. Eng., B, 2009, 158, 7–12 CrossRef CAS.
- T. Yamauchi, Y. Tsukahara, T. Sakamoto, T. Kono, M. Yasuda, A. Baba and Y. Wada, Bull. Chem. Soc. Jpn., 2009, 82, 1044–1051 CrossRef CAS.
- C. Gong, J. Zhang, X. Zhang, L. Yu, P. Zhang, Z. Wu and Z. Zhang, J. Phys. Chem. C, 2010, 114, 10101–10107 CAS.
- L. Sun and Q. Chen, Eur. J. Inorg. Chem., 2009, 2009, 435–440 CrossRef.
- S. Sarkar, A. K. Sinha, M. Pradhan, M. Basu, Y. Negishi and T. Pal, J. Phys. Chem. C, 2011, 115, 1659–1673 CAS.
- H. Niu, Q. Chen, M. Ning, Y. Jia and X. Wang, J. Phys. Chem. B, 2004, 108, 3996–3999 CrossRef CAS.
- F. L. Jia, L. Z. Zhang, X. Y. Shang and Y. Yang, Adv. Mater., 2008, 20, 1050–1054 CrossRef CAS.
- P. Li, N. Wang and R. Wang, Eur. J. Inorg. Chem., 2010, 2010, 2261–2265 CrossRef.
- C. Wang, X. Han, P. Xu, J. Wang, Y. Du, X. Wang, W. Qin and T. Zhang, J. Phys. Chem. C, 2010, 114, 3196–3203 CAS.
- X. Liu and S. Fu, J. Cryst. Growth, 2007, 306, 428–432 CrossRef CAS.
- Y. Wang, Q. Zhu and H. Zhang, Mater. Res. Bull., 2007, 42, 1450–1456 CrossRef CAS.
- S. Senapati, S. K. Srivastava, S. B. Singh and K. Biswas, Cryst. Growth Des., 2010, 10, 4068–4075 CAS.
- H. Li and Y. Xu, Mater. Lett., 2001, 51, 101–107 CrossRef CAS.
- Y. Sun, C. Li and A. Zhang, Appl. Catal., A, 2016, 522, 180–187 CrossRef CAS.
- J. Wang, Q. Li and J. Yao, Appl. Catal., A, 1999, 184, 181–188 CrossRef CAS.
- A. M. Zhang, J. L. Dong, Q. H. Xu, H. K. Rhee and X. L. Li, Catal. Today, 2004, 93-95, 347–352 CrossRef CAS.
- Y. Ma, Y. Huang, Y. Cheng, L. Wang and X. Li, Appl. Catal., A, 2014, 484, 154–160 CrossRef CAS.
- M. Zahmakıran, Y. Tonbul and S. Özkar, J. Am. Chem. Soc., 2010, 132, 6541–6549 CrossRef PubMed.
- S. Miao, Z. Liu, B. Han, J. Huang, Z. Sun, J. Zhang and T. Jiang, Angew. Chem., Int. Ed., 2006, 45, 266–269 CrossRef CAS PubMed.
- T. Ioannides and X. E. Verykios, J. Catal., 1993, 143, 175–186 CrossRef CAS.
- Y. Tonbul, M. Zahmakiran and S. Özkar, Appl. Catal., B, 2014, 148–149, 466–472 CrossRef CAS.
- H. Duan, D. Wang, Y. Kou and Y. Li, Chem. Commun., 2013, 49, 303–305 RSC.
- Y. Huang, Y. Ma, Y. Cheng, L. Wang and X. Li, Ind. Eng. Chem. Res., 2014, 53, 4604–4613 CrossRef CAS.
- Y. Huang, Y. Ma, Y. Cheng, L. Wang and X. Li, Catal. Commun., 2015, 69, 55–58 CrossRef CAS.
- L. Zhu, Y. Jiang, J. Zheng, N. Zhang, C. Yu, Y. Li, C.-W. Pao, J.-L. Chen, C. Jin, J.-F. Lee, C.-J. Zhong and B. H. Chen, Small, 2015, 11, 4385–4393 CrossRef CAS PubMed.
- L. Zhu, T. Zheng, J. Zheng, C. Yu, Q. Zhou, J. Hua, N. Zhang, Q. Shu and B. H. Chen, Appl. Surf. Sci., 2017, 423, 836–844 CrossRef CAS.
- S. Yang, L. Peng, C. Cao, F. Wei, J. Liu, Y.-N. Zhu, C. Liu, X. Wang and W. Song, Chem. – Asian J., 2016, 11, 2797–2801 CrossRef CAS PubMed.
- L. Zhu, T. Zheng, J. Zheng, C. Yu, N. Zhang, Q. Liao, Q. Shu and B. H. Chen, CrystEngComm, 2017, 19, 3430–3438 RSC.
- L. Zhu, S. Shan, V. Petkov, W. Hu, A. Kroner, J. Zheng, C. Yu, N. Zhang, Y. Li, R. Luque, C.-J. Zhong, H. Ye, Z. Yang and B. H. Chen, J. Mater. Chem. A, 2017, 5, 7869–7875 CAS.
- Y. Li, L. Zhu, K. Yan, J. Zheng, B. H. Chen and W. Wang, Chem. Eng. J., 2013, 226, 166–170 CrossRef CAS.
- Z. Li, Y. Su, Y. Liu, J. Wang, H. Geng, P. Sharma and Y. Zhang, CrystEngComm, 2014, 16, 8442–8448 RSC.
- P.-P. Li, W.-Z. Lang, K. Xia, L. Luan, X. Yan and Y.-J. Guo, Appl. Catal., A, 2016, 522, 172–179 CrossRef CAS.
- K. V. Manukyan, A. J. Cross, A. V. Yeghishyan, S. Rouvimov, J. J. Miller, A. S. Mukasyan and E. E. Wolf, Appl. Catal., A, 2015, 508, 37–44 CrossRef CAS.
- S. Park, D. Yoon, H. Baik and K. Lee, CrystEngComm, 2015, 17, 6852–6856 RSC.
- Y. Yamauchi, T. Ohsuna and K. Kuroda, Chem. Mater., 2007, 19, 1335–1342 CrossRef CAS.
- H. H. Brongersma, M. Draxler, M. de Ridder and P. Bauer, Surf. Sci. Rep., 2007, 62, 63–109 CrossRef CAS.
- S. Niembro, S. Donnici, A. Shafir, A. Vallribera, M. L. Buil, M. A. Esteruelas and C. Larramona, New J. Chem., 2013, 37, 278–282 RSC.
- P. Dyson, D. Ellis and D. Parker, Chem. Commun., 1999, 25–26 RSC.
- F. Su, L. Lv, F. Y. Lee, T. Liu, A. I. Cooper and X. S. Zhao, J. Am. Chem. Soc., 2007, 129, 14213–14223 CrossRef CAS PubMed.
- J. Huang, T. Jiang, B. Han, W. Wu, Z. Liu, Z. Xie and J. Zhang, Catal. Lett., 2005, 103, 59–62 CrossRef CAS.
- K. X. Yao, X. Liu, Z. Li, C. C. Li, H. C. Zeng and Y. Han, ChemCatChem, 2012, 4, 1938–1942 CrossRef CAS.
- Y. Zhao, J. Zhang, J. Song, J. Li, J. Liu, T. Wu, P. Zhang and B. Han, Green Chem., 2011, 13, 2078–2082 RSC.
|
This journal is © The Royal Society of Chemistry 2018 |
Click here to see how this site uses Cookies. View our privacy policy here.