Solution processing of air-stable molecular semiconducting iodosalts, Cs2SnI6−xBrx, for potential solar cell applications†
Received
20th February 2017
, Accepted 19th March 2017
First published on 20th March 2017
Abstract
Organic–inorganic hybrid lead-based perovskite solar cells have already achieved high performance efficiency (∼20%). A major challenge with these cells, however, is their stability and environmental safety concerns due to the presence of lead. This article reports an effort to develop a new class of tin-based and air-stable molecular semiconducting iodosalts, for potential solar cell applications. The compounds are Cs2SnI6−xBrx for a range of x that provides the desired bandgaps from ∼1.3 eV to ∼2.9 eV with x < 3 being suitable for solar cell design. The Sn in this compound is in the 4+ oxidation state, and thus it is much more stable with respect to oxidation and more resistant to hydrolysis during processing and device operation. The focus of this article is on the detailed synthesis challenges in the solution processing of these compounds. A two-step solution synthesis method has been developed whereby during Step-1 a well-defined CsI crystalline film was formed for the appropriate chemical reaction with a solution of SnI during Step-2. By careful tuning of each step of the process and with the use of detailed structural, electrical and optical characterization as feedback, a series of Cs2SnI6−xBrx films were produced. The importance of having a stoichiometric compound for optimal performance of the material was revealed during solar cell fabrication. For the purpose of demonstrating a solar cell device assembly, a sandwich-type photochemical cell with an all solid state ionic conductor blended with inorganic materials and succinonitrile was employed for easy processing to obtain stable results. The cells show a conversion efficiency of 2.1% for the case of the x = 2 compound.
1 Introduction
The interest in the use of organic–inorganic hybrid perovskite compounds for application in solar cells has been primarily due to the rapid surge in cell efficiency to ∼20% during the past several years.1–6 Most of the perovskite compounds under investigation by community are based on APbI3 structures, where A can be Cs, methylamonium (CH3NH3+) or formamidinium (HC(NH2)2+).7–10 These perovskites exhibit long term instabilities associated with phase transitions, ambient hydrolysis, and photo-degradation, while the presence of a water-dispersible form of lead in solar cells and the presence of toxic additives in their hole transport layers raises environmental concerns.11–13 The fabrication of tin based ASnI3 perovskite cells has been demonstrated but these materials exhibit even greater instabilities along with phase transitions and lower Voc values. Thus, to realize commercial applications of this technology it is important to achieve analogous optical and photovoltaic performance using lead-free, toxic-additive-free, and air-stable compounds for ambient processing. Therefore, the use of a new class of environmentally benign materials with intrinsic stability and possessing beneficial optoelectronic performance can be an alternative to the current approach.
In an earlier article we demonstrated the use of Cs2SnI6 as a hole conductor in a dye sensitized solar cell.14 In the Cs2SnI6 iodosalt compound, the Sn is in the 4+ oxidation state, and much more stable with respect to oxidation and hydrolysis during device processing and operation. Cs2SnI6 is a direct bandgap (∼1.3 eV) semiconductor, and depending on doping, it can be either an n- or a p-type semiconductor suggesting an ambipolar nature of this compound.14
This paper is structured into three major parts: in Section 1, a detailed discussion on the ramifications of material structure and chemistry related challenges is presented for solution processing, along with careful characterization. To prepare for device fabrication, in Section 2, we discuss band alignment engineering among the solar cell layers to optimize the final device performance. Finally, in Section 3, we present a unique device configuration and its performances.
2 Results and discussion
2.1. Optimization of the two-step solution processes for Cs2SnI6 thin films
The focus of this section is the discussion of a series of experiments describing how we have optimized our two-step solution processes for synthesizing iodosalt Cs2SnI6−xBrx thin films to achieve suitable properties as solar photon absorbers for light to charge conversion. Our results are organized into three sections: Section 1.1 describes the thin-film optimization of the x = 0, Cs2SnI6, iodosalt. In Section 1.2 we focus on Step-1, the morphological control of the CsI film. In Section 1.3, the effects of unreacted CsI in Cs2SnI6 films are presented. Finally, in Section 1.4, we discuss Step-2 of the process where we show how we determine the optimal temperature and duration of the chemical reaction for the second step in an attempt to achieve stoichiometry for the final film.
The first step in solution-preparation of Cs2SnI6 thin films was to optimize the processing conditions in order to obtain systematic and reproducible results. We then proceeded to characterize the properties of the films during and after synthesis. It should be noted that many basic parameters such as temperature, time, spatial uniformity, and chemical reactivity are interdependent in our solution processing steps. For device fabrication, both local non-stoichiometric regions (at the nanoscale) and interfacial recombination sites needed to be minimized. This includes (external and internal) surface dangling bonds. The solar cell performance was further optimized by improving the band gap alignment between the TiO2 photo-anode and photon-absorber. To this end we determined the optimum amount of Sn doping in TiO2. The nominal open circuit voltage, Voc, of the cells using Cs2SnI6 is ∼0.26 eV. In order to increase this value, we introduced an appropriate amount of bromide in the form of Cs2SnI6−xBrx to obtain a Voc of 0.58 eV for the case of Cs2SnI4Br2. We discuss the device characteristics in terms of performance, stability and reproducibility and give examples of how to fabricate iodosalt based solar cell devices by circumventing costly materials and processing steps.
2.1.1. Two-step thin film deposition process.
We study experimentally each step of the two-step processing for developing Cs2SnI6 films: a CsI deposition in Step-1 and SnI4 treatment in Step-2. Our two-step approach consisted of first preparing solutions by dissolving various concentrations of CsI in a mixture of water and 2-isopropyl alcohol (IPA). The following three different coating processes were attempted: spin-coating, drop-coating and electro-spraying (E-spray). The results of each are shown in Fig. 1a. After drying under ambient conditions, in the case of spin-coating, clusters of CsI crystallites were formed, while for drop-coating we observed dendritic CsI crystallites. On the other hand, in the case of E-spraying, a thin film of CsI crystallites was formed. Following Step-1, a solution of SnI4 in EtOH was used to “soak” the CsI layer (this is Step-2). As shown in the middle of Fig. 1b, soon after the CsI was “soaked” with SnI4 and dried, the white film turned black. The observed color change indicated the phase transition from CsI or SnI4 to the Cs2SnI6 compound. The detailed results were examined in the next section. The Cs2SnI6 crystal adopted a face centered cubic (fcc) lattice (space group Fm
m) with a lattice parameter a of 11.6276(9) Å and consisted of discrete, regular {SnI6}2− octahedra and Cs+ cations (K2PtCl6 structure type). The crystal structure (Fig. 1b right) can be described as a defective variant of the perovskite CsSnI3, where half of the Sn sites are vacant (i.e. A2SnX6), resulting in a Werner-like coordination complex.15,16 The +4 oxidation state of Sn in Cs2SnI6 leads to its intrinsic stability. In addition, Fig. 1c shows the differences in the surface and cross-sectional morphologies in the Cs2SnI6 compound when CsI layers (from drop-coating and E-spray coating) were soaked in SnI4 solution and dried. We note that in the case of E-sprayed CsI coating, the formed Cs2SnI6 compound has a smoother surface and interfaces as shown in Fig. 1c. This was verified by using a surface profilometer (Dektak 150, Veeco Metrology Inc) with a 3D interactive display indicating large thickness variations across the drop coated film as compared with a smoother surface of the E-sprayed film. In addition, we observed much less compaction of the drop coated film compared to that of the E-sprayed sample as seen from the SEM cross section in the lower frames of Fig. 1c.
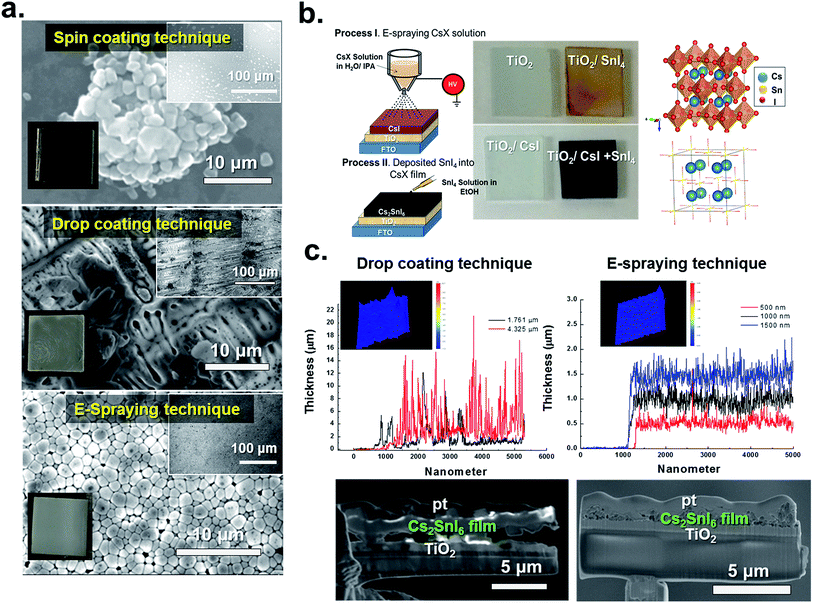 |
| Fig. 1 (a) SEM images of CsI films produced by different routes: spin coating deposition (1500 rpm, 30 s), dropping deposition and E-spray deposition. (b) Sequential solution-based deposition process for Cs2SnI6 films with photo images for each process and the crystal structure of Cs2SnI6 from the VESTA program (top: polyhedral and bottom: wireframe). (c) Thickness profiler (inset: 3D interactive display) and cross-sectional images of the Cs2SnI6 film used by the drop coating and E-spray coating techniques. | |
2.1.2. Morphological control of CsI films.
The foremost goal in Step-1 is to study how morphological control of CsI can affect Step-2 of the two-step process in synthesizing large crystallites of Cs2SnI6 to optimize the device performance. Since CsI has its own surface chemistry, we wanted to learn how its crystallites evolve and grow at different annealing temperatures (from 100 °C to 500 °C in increments of 100 °C), and what happens to the morphologies of the crystallites when they react with SnI4 solutions during Step-2. The observed morphologies of CsI as a function of annealing temperature are shown in the left column of Fig. 2a with sample thicknesses in the range of 1–1.5 μm. As the annealing temperature was increased, the grain size of CsI became larger and formed an interconnecting CsI network, while the film color remained unchanged but the thickness decreased (see ESI 1†). To choose which CsI annealing temperature (and morphology) was best suited for Step-2, we proceeded with “soaking” of all the annealed CsI samples. During the addition of the SnI4 solution, reaction with the crystalline CsI film took place as shown in the right column of SEM images of Fig. 2a. Even if a similar black color was observed all the way from room temperature to 500 °C, the “best” temperature for the Step-2 process was found to be 110 °C for 20 minutes by using the CsI sample annealed at 300 °C for 30 minutes. For CsI samples annealed at a higher temperature than this, pin holes were formed which indicated the formation of a non-continuous Cs2SnI6 film. This is particularly important for the planar cell architecture because an incomplete coverage of a perovskite film results in low-resistance shunting paths and low light absorption in the solar cell.17 The X-ray diffraction patterns of Cs2SnI6 films are shown in Fig. 2b. We show the results of two different samples: (a) CsI annealed at 100 °C and (b) CsI annealed at 300 °C for 30 min during Step-1. The process for Step-2 was exactly the same. In both cases we observe a single phase Cs2SnI6 polycrystalline film, but each film exhibits a different preferred orientation. In the case of the 100 °C annealed sample, we see the strongest Bragg peaks at 30.776 degrees with the preferential orientation along the (h00) diffraction plane, which is similar to that of the film reported by Saparov et al.18 However, for the 300 °C annealed film we observed no preferential orientation.
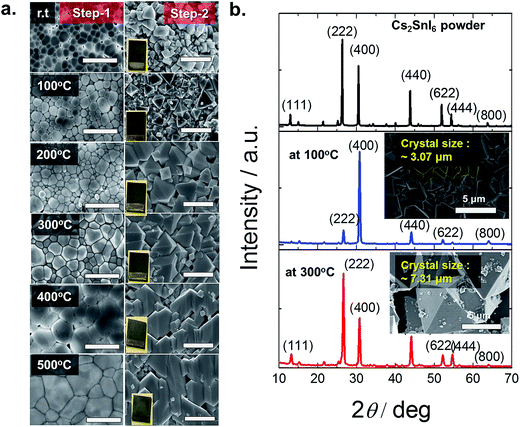 |
| Fig. 2 (a) Left column – SEM images of the E-sprayed CsI films annealed at different temperatures in air for 30 min. Corresponding right column—after the addition of SnI4 solution at 110 °C for 20 min Cs2SnI6 films were formed. The scale bar is 5 μm. (b) XRD analysis of Cs2SnI6 powder and from two different CsI annealed films at 100 °C and 300 °C. | |
A more detailed cross-sectional microstructural analysis investigation was carried out to learn how much of the CsI was converted to Cs2SnI6 in the thin films. A dual beam focused ion beam (FIB) microscope (Helios Nanolab, FEI Co.) was used to prepare cross-sectional SEM and scanning transmission electron microscopy (STEM) samples utilizing a Ga+ ion. A Pt coating was applied to protect the surface during the microscopy study. The sample was thinned by Ga+ ion etching in a FIB microscope employing a final energy of 2 kV at 24 pA. Fig. 3 displays the cross-sectional SEM and STEM images in the two differently annealed samples in Step-1, CsI annealed at 100 °C (a, b) and at 300 °C for 30 minutes (c and d). The same Step-2 was adopted for both samples: SnI4 solution treated at 110 °C for 20 min. Fig. 3(a and b) show the three different layers (labeled part-a, -b and -c) in the deposited film. The selected area diffraction patterns (SADPs) on the left side of the STEM, Fig. 3b, show that the three parts have different crystallographic structures: part-a is a Cs2SnI6 structure, part-b is a mixed structure of Cs2SnI6 and CsI, and part-c is a CsI structure. On the other hand, for the higher annealing temperature at 300 °C in Step-1, Fig. 3(c and d), the cross-sectional images of SEM and STEM show two crystalline layers, part-a and part-b. The CsI structure in part-a is not present in this sample. This indicates that in the case of 100 °C, the reaction in Step-2 was taking place much slower than that at 300 °C. In addition, as mentioned earlier, unlike the 300 °C case, the 100 °C annealed film is not fully converted into Cs2SnI6. Fewer voids are observed at the interface between the film and the substrate for the 300 °C annealed case. As shown in Fig. 3 a and c, the crystal morphologies are quite different between the two cases. The morphology for the 300 °C case is much more uniform, providing direct evidence that the conversion of CsI to Cs2SnI6 is facilitated by high temperature annealing. The orientation change in the two samples is also displayed in the SADP analyses. The (004) plane is close to the plane normal to the film in the 100 °C annealed sample, SADPs in part-a, whereas, the (222) plane is close to the plane normal to the film in the 300 °C annealed sample, SADPs in part-a of Fig. 3d. This result corresponds to XRD analysis in Fig. 2. Finally, for the case of 300 °C annealing, we still observe a mixture of Cs2SnI6 and CsI near the interface with TiO2 (Fig. 3c and d)
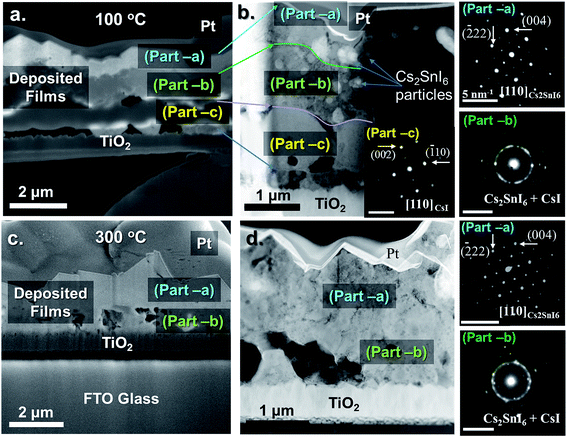 |
| Fig. 3 Cross-sectional scanning electron microscopy (SEM) and scanning transmission electron microscopy (STEM) analyses. (a) SEM and (b) STEM analyses of CsI films annealed at 100 °C in air for 30 minutes (Step-1), and SnI4 solution treated at 110 °C for 20 minutes (Step-2). (c) SEM, and (d) STEM analyses of CsI films annealed at 300 °C in air for 30 minutes with Step-2 being the same. Corresponding selective area diffraction patterns (SADPs) in the three layers (part-a, -b, and -c) are displayed on the left side of the STEM image. Different parts of the films are produced at different annealing temperatures of CsI films in Step-1 (part-a describes the diffraction pattern of crystalline Cs2SnI6, part-b is the mixed structure of Cs2SnI6 and CsI, and part-c is the CsI structure). | |
2.1.3. Influence of unreacted CsI in Cs2SnI6 films.
In this section, the influence of the remaining CsI during Cs2SnI6 conversion was investigated. For this study, six groups of samples with different rations of CsI/Cs2SnI6 were prepared by the Step-2 solution method. The CsI films were produced under identical conditions by E-spraying. To control the amount of CsI in Cs2SnI6, SnI4 solutions of several different concentrations were prepared, ranging from 5 to 15 wt%. And then this solution was dropped on the CsI film. The first series of samples are labelled Sample 1, 2 and 3 (S1: 5 wt%, S2: 10 wt%, S3: 15 wt%). For the next process, more SnI4 was repeatedly dropped in the same spot to obtain completely reacted Cs2SnI6 films. The second series of samples are labelled Sample 4, 5 and 6 (S4: 5 wt%, S5: 10 wt%, S6: 15 wt%). In our observation, however, the films prepared from SnI4 solutions with higher concentration and an excessive dropping process (over 3 times) did not result in a completely reacted uniform film (see Fig. 4b). The different amounts of CsI in the Cs2SnI6 film can be quantitatively confirmed by XRD and SEM/EDS analysis. The left of Fig. 5a shows the XRD analysis of each samples. The first series samples (Samples 1 to 3) exhibit the presence of a strong CsI peak at approximately 27.7 degrees and Cs2SnI6 at 26.5 degrees with the preferential orientation along the (110) and (222) diffraction planes, respectively, while the second series samples at over 10 wt% (Samples 5 and 6) show completely reacted Cs2SnI6 films. The quantitative analysis by XRD and SEM/EDS can provide the detailed elemental compositions of each sample. The ratio of relative peak intensity between CsI and Cs2SnI6 is plotted in Fig. 5b. As expected, the conversion ratio of Cs2SnI6 improves with increasing SnI4 content in the film. Visualized EDS graphs are also shown in Fig. 5c. The spectra reveal that the weight percent Cs/Sn ratio of S1–S4 is higher than that of the expected composition number (n = 2), but its value decreases gradually with increase of the SnI4 content (S5–S6) which corresponds to the XRD results. The detailed information is summarized in Table 1.
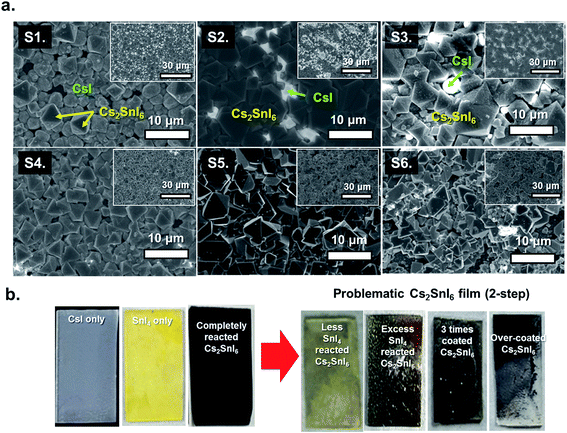 |
| Fig. 4 (a) SEM images of the controlled Cs2SnI6 film for studying the effect of remaining CsI in Cs2SnI6 films and (b) photo image of the film: completely (left) and incompletely (right) converted Cs2SnI6 films. | |
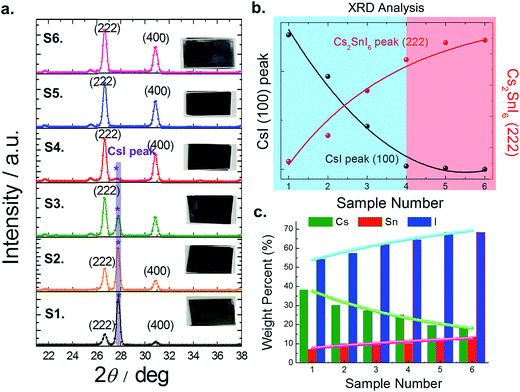 |
| Fig. 5 (a) XRD analysis of the controlled Cs2SnI6 film for studying the effect of remaining CsI in Cs2SnI6 films. (b) Graph showing CsI and Cs2SnI6 peak intensity (the presence of the CsI peak (blue) and no CsI peak (red)). (c) EDS data for the elemental analysis (Cs, Sn and I). | |
Table 1 Compositional and electrical properties of the controlled Cs2SnI6 film
Sample |
Int.I (cps deg) |
Composition region |
EDS (at wt%) |
E
g
|
Carrier concentration (×1015 cm−3) |
Mobility (cm2 V−1 s−1) |
CsI (110) |
Cs2SnI6 (222) |
CsI/Cs2SnI6 |
Cs |
Sn |
I |
Cs/Sn |
S1 |
2515(32) |
673(27) |
3.736 |
CsI-rich |
38.4 |
7.25 |
54.35 |
5.296 |
1.41 |
4.07 × 1016 |
1.779 |
S2 |
1707(16) |
535(12) |
3.191 |
CsI-rich |
30.24 |
10.18 |
57.48 |
2.970 |
1.37 |
3.85 × 1016 |
2.119 |
S3 |
950(18) |
1627(24) |
0.584 |
CsI-poor |
27.29 |
10.8 |
61.97 |
2.527 |
1.35 |
9.88 × 1015 |
4.812 |
S4 |
99(9) |
1332(16) |
0.074 |
Mostly Cs2SnI6 |
25.16 |
10.25 |
64.59 |
2.455 |
1.32 |
1.14 × 1014 |
9.072 |
S5 |
— |
1983(28) |
0.000 |
Cs2SnI6 |
19.65 |
11.82 |
68.53 |
1.662 |
1.30 |
4.86 × 1013 |
10.59 |
S6 |
— |
2006(27) |
0.000 |
Cs2SnI6 |
18.1 |
13.64 |
68.26 |
1.327 |
1.28 |
1.51 × 1015 |
2.312 |
The optical absorption spectra of each film were measured with a UV-visible spectrophotometer (Perkin Elmer LAMBDA 1050) in the wavelength range of 250–1200 nm (see Fig. 6a). Earlier, our study showed that Cs2SnI6 had a direct band gap of ∼1.3 eV at the Γ point.14 However, Cs2SnI6 crystals exhibit dispersive conduction band states due to intrinsic defects, causing an argument over the bandgap energy value.18–20 In our experimental study here using the six samples discussed above, and using EDS and XRD analysis, we now confirm that the presence of CsI in a Cs2SnI6 film can influence its bandgap (see Fig. 6b). With an increase in the percentage of CsI in Cs2SnI6, the absorption edge shifted to shorter wavelengths. The band gap of the completely reacted Cs2SnI6 film is consistent with our earlier calculation, while Cs2SnI6 films containing a high amount of CsI impurities show an increased band gap of about 0.1 eV. In our experimental observation, the carrier concentrations in these samples (at the 1.5 μm thickness) ranged from 4.86 × 1013 cm−3 to 4.07 × 1016 cm−3 and mobility ranged from 1.779 cm2 V−1 s−1 (at 1.4 eV) to 10.59 cm2 V−1 s−1 (at 1.3 eV) (see Table 1).
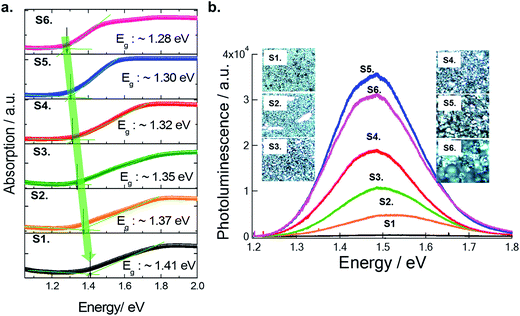 |
| Fig. 6 (a) Bandgap calculation of the controlled Cs2SnI6 film for studying the effect of remaining CsI in Cs2SnI6 films, (b) Photo-luminescence (PL) analysis for each sample with confocal microscopy images. | |
Photo-luminescence (PL) measurement can further confirm the levels of CsI in the Cs2SnI6 films. At room temperature, we observed an increased PL intensity and red-shifted PL position with decreasing amount of CsI in Cs2SnI6 crystals following the same trend as the band gap. For example, in the case of a completely reacted Cs2SnI6 film (S5), the intensity of the PL peak at 1.48 eV increases by ∼10 times and the peak position shifts to a lower energy by ∼20 meV as compared with S2. Therefore, we can appreciate that it is necessary to avoid the unreacted CsI, which leads to undesired optical and electrical properties in Cs2SnI6 films.
2.1.4. Step-2 temperature and time conditioning studies.
In this section we show how we determined the optimum processing temperature and duration for Step-2 processing. The XRD patterns and surface crystallite morphology change as a function of temperature and processing time for a typical (∼10 μm size) Cs2SnI6 crystallite are shown in Fig. 7. For these experiments, the prepared Cs2SnI6 films were placed in weighing bottles (PYREX® Weighing Bottles, VWR) with lids closed under an ambient atmosphere. The vials were then transferred to a preheated oven and heated at selected temperatures. With increasing annealing temperature and time, CsI emerges as a second phase (starred diffraction peaks in the XRD spectra in Fig. 7) due to partial decomposition of Cs2SnI6 leading to loss of SnI4. In Fig. 7a, we see that at 110 °C (for 20 min) the surface of the crystallites retains its smoothness during the reaction of CsI with SnI4 in air. However, if we increase the duration to 10 h from 20 min, very small crystallites appear on the surface of the Cs2SnI6 crystallites. With an increase in the reaction temperature to 200 °C and 4 h duration, we observed the presence of larger crystallites on the surfaces of Cs2SnI6 crystals. Quantitative elemental analysis made on each of the samples indicated that the amount of iodine observed decreases with time and temperature, and a proportional increase in the tin fraction is observed, while the relative ratio of cesium fraction was only slightly changed. At the same time, local EDS measurements indicate that the nano-crystallites on the surface of the Cs2SnI6 crystal are most likely to be Sn oxides. The results indicating a loss of I− are reasonable since SnI4 is known to have a much higher vapor pressure than CsI (SnI4 practically sublimes as the temperature approaches its melting point at ∼150 °C).21
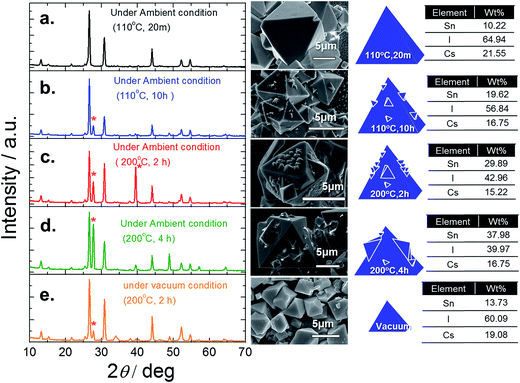 |
| Fig. 7 XRD analysis and SEM images with EDS of Cs2SnI6 films under different time and temperature treatment conditions of Step-2 with SnI4 solution (a) at 110 °C for 20 min, (b) 110 °C for 10 hours, (c) 200 °C for 2 hours, and (d) 200 °C for 4 hours in an ambient system and (e) 200 °C for 2 hours under vacuum (10−4 torr). | |
To confirm this sublimation, we took two similar fresh films and annealed one in air and the other in a vacuum at 200 °C for 4 h. As seen in Fig. 7d, the film annealed in air exhibits growth of nanoparticles on the Cs2SnI6 surface, while the sample annealed in a vacuum retained its smooth surface, Fig. 7e. XRD measurements show the differences between these two samples: the sample annealed in a vacuum maintained the Cs2SnI6 structure, containing only a small amount of CsI, while the sample annealed in air contains pronounced extra peaks from the presence of CsI crystallites due to the partial removal of SnI4 during the annealing process. Local EDS measurements performed with a focused electron beam also confirmed that the vacuum sample maintained its Cs2SnI6 composition. Furthermore, the elemental ratio of crystals with different sizes was consistent with a Cs2SnI6 composition. Thus, due to the water vapor in air (50–75% humidity, typically in our lab), we expect a significant degree of hydrolysis reaction to take place under the employed experimental conditions (200 °C for 4 h). Under these conditions, and owing to the relatively weak bonding between Sn and I, SnO2 crystallites can be formed on the Cs2SnI6 surfaces. These studies led us to conclude that for Step-2, the optimal processing conditions were 110 °C for 20 minutes.
2.2. Interfacial bandgap engineering
While the performance of the sensitizer layer is very important in a solar cell, the charge transport layers, their interfaces, and the electrodes that connect the device to the outside world are important as well. In this section we report how we have improved two interfacial junctions: (a) between nano-porous TiO2 and Cs2SnI6, by reducing the bandgap of the TiO2 through doping with Sn to improve electron transfer between the layers, and (b) the optimization of the bandgap of the sensitizer layer, so as to approach the ideal value of 1.4 eV (using an AM 1.5 solar spectrum) for a solar cell made from a single material.22 The 1.3 eV bandgap of Cs2SnI6 can be increased through incorporation of Br into the Cs2SnI6 crystal structure.18 In section 2.2, we discuss our results for Cs2SnI6−xBrx films with different values of x.
2.2.1. Sn doped TiO2 layer as a photo-anode.
Based on the conditions described above for synthesizing the light absorbing Cs2SnI6 layer, a functioning solar cell device was built using hole and electron charge transport layers optimized for performance. Lin et al. showed that the band gap of TiO2 monotonically decreased as the particle size in the range from 8 nm to 30 nm also decreased.23 Our E-sprayed TiO2 film composed of 10 nm-sized spherical particles can be expected to exhibit a lower bandgap compared with commercial TiO2 (anatase, <25 nm from Sigma-Aldrich) nanoparticles.14 The estimated bandgap of our TiO2 film showed approximately a 0.05 eV decrease and it was in good agreement with those determined by Lin. Although the smaller sized TiO2 spheres have a slightly decreased bandgap, it is not enough to be an efficient electron transport layer. In order to tailor appropriate band gap alignment for solar cell application, TiO2 was modified through the addition of Sn as a doping element. Tin is ideal for this purpose because of its structural compatibility and stability due to small lattice mismatch between TiO2 and SnO2.24,25 Most importantly, the conduction band edge of SnO2 is about 0.4 eV lower than that of TiO2.26,27 Thus we expect that Sn ions lead to an appropriate band alignment by reducing the position of the conduction band edge of TiO2. In our experiment, Sn–TiO2 films were prepared by a simple hydrothermal method and E-spraying technique similar to that discussed above. Titanium(IV) isopropoxide (100 mL) was separately mixed with a solution containing appropriate amounts of SnCl2 (Aldrich, 98%) in water. The percentage of Sn doping was tuned by using the Sn/Ti ratio in the precursor solution. A series of Sn-doped TiO2 materials with the Sn content ranging from 2 wt% to 10 wt% were successfully synthesized. The hydrothermal Sn–TiO2 solution was E-sprayed after replacing water with ethanol.
Fig. 8a shows the X-ray diffraction patterns of the TiO2 and TiO2 with different concentrations of doped Sn. With Sn contents above 2 wt%, the rutile (110) peak starts to progressively increase, whereas the anatase (101) peak diminishes. The surface morphologies of the undoped E-sprayed TiO2 and SnO2 films are shown in Fig. 8b. It can be seen that the undoped E-sprayed TiO2 is made mostly of spherical structures, while E-sprayed SnO2 shows flower-like structures with a relatively rough surface. The Eg of the TiO2 was calculated from indirect transitions (n = 1/2) and Fig. 8c shows the plots of (αhv)1/2versus hv. A perfect fit was obtained for all the samples giving the values of 3.22 eV for the bare TiO2 film, 3.07 eV for 2 wt% Sn–TiO2, and 2.98 eV for 5 wt% Sn–TiO2. Ultraviolet photoemission spectroscopy (UPS) measurements are also performed to determine the VBM. The substitution of Sn for Ti does not shift the VBM. As a result, from the observation of the band gap with varying concentration of doped Sn and EVB values, the CBM can be estimated to be −4.35 eV for 2 wt% Sn in TiO2 and −4.44 eV for 5 wt% Sn in TiO2, which are 0.15 eV and 0.24 lower than that of the ECB of pure TiO2 (−4.2 eV versus vacuum). Therefore, modification of the electron transport medium is expected to improve the electron injection from Cs2SnI6−xBrx materials.
 |
| Fig. 8 (a) XRD patterns (anatase phase labeled A, rutile R and Sn S) and (b) band gap calculation (the insets show the schematic band diagram and the surface morphologies – the scale bar is 500 nm) for the different Sn doping concentrations. | |
2.2.2. Mixed halide system, Cs2SnI6−xBrx.
The bandgap tuning achieved by substitution of Br is anticipated to enhance the Voc of a Cs2SnI6 based solar cell. With the insights provided by the above experiments we report results from our mixed-halide system, Cs2SnI6−xBrx, aiming to tune the electrical properties of the material by tweaking the band structure in an analogous manner to Pb2+ and Sn2+ perovskite systems.4,28,29 Based on the two-step studies on Cs2SnI6 discussed above, a process was also developed for the Cs2SnI6−xBrx thin film synthesis in the following manner: (i) the starting binary compounds, such as CsI, CsBr, SnI4, or SnBr4, were first dissolved in various solvents. (ii) The solution of SnI4 or SnBr4 was introduced into a CsI or CsBr film prepared by the E-spraying process, yielding a compound having the general formula Cs2SnI6−xBrx, which offers the possibility to engineer the bandgap of the materials. (iii) The films were heated in air at 110 °C for 20 min. The reaction can be described as the following equation:
(1 − x)CsI + xCsBr + SnX4 (X = I, Br) → Cs2SnI6−xBrx |
The X-ray diffraction patterns of the films thus prepared are shown in Fig. 9a. As the Br composition is gradually increased, the angle of the main peak of the (222) plane is shifted from 26.53° to 28.45°. The measured band gaps of the Cs2SnI6−xBrx films with varying substitution of Br are shown in Fig. 9b. From diffuse reflectance UV-vis-near IR measurements, we note that in this particular system, the band gap of Cs2SnBr6 is 2.9 eV, drastically different from that of Cs2SnI6 (1.3 eV). This contrasts with the much smaller difference in the band gap between CsSnBr3 (1.7 eV) and γ-CsSnI3 (1.3 eV) which is only 0.4 eV. From both XRD and optical analyses, the two-step process produced films are indeed modified by the partial halide substitution and this can be clearly observed in the measured emission (PL) which shows a clear blue shift as Br− is incorporated into the Cs2SnI6 matrix, while the intensity of the PL peak diminished with increasing Br ratio (see Fig. 9b bottom). In this graph, the intensity was normalized so that increasing noise level indicates a weaker signal. This observation constitutes an important indication that these materials can be successfully utilized as light absorbers in solar cells. The shift in the position of energy levels can be also confirmed by UPS analysis (see ESI 2†). It is noted that the Cs2SnI6 film shows the highest HOMO position at 5.40 ± 0.09 eV. By increasing the ratio of Br, there is a clear downshift of the HOMO level from 5.61 ± 0.08 eV to 6.78 ± 0.9 eV and this result is consistent with reports on analogous HOMO level shifts of CH3NH3PbI3.4,30 Furthermore, with the increase of Br composition, the color of the Cs2SnBrxI6−x films changed from dark brown to brown/red, and then to light yellow due to the widening of the bandgap, Fig. 9b. For detailed information, the lattice parameter and band gap of the Cs2SnI6−xBrx films are listed in Fig. 10. The obtained films were indeed found to form the Cs2SnI6−xBrx phases as evidenced by small changes in the lattice constant, indicating incorporation of Br− into the Cs2SnI6 lattice or incorporation of I− into the Cs2SnBr6 lattice. Unlike the CsSnI3−xBrx solid solution, the experimental band gap trend of Cs2SnI6−xBrx does not follow the characteristic Vegard's law but instead it increases steadily up to x ∼ 4 followed by an abrupt increase for x > 4 (see Fig. 10). The anomalous nature of the band gap may reflect on the molecular nature of the compounds which may be ascertained to be a random distribution of heterohalide octahedra throughout the solid. Another remarkable result obtained from these experiments lies in the crystallite morphology. SEM analysis indicates that the particle size is significantly reduced upon increasing the Br content in Cs2SnI6−xBrx with the pure Cs2SnI6 in octahedral crystallites with size around ∼1 micron whereas the pure Cs2SnBr6 has smaller (∼300 nm) crystallites of cubic shapes (Fig. 10). This morphology transformation from octahedra to cubes can be explained by the enhanced symmetry.4 Following this trend, the morphology and size of the intermediate Cs2SnI6−xBrx compositions lie in between these two extremes.
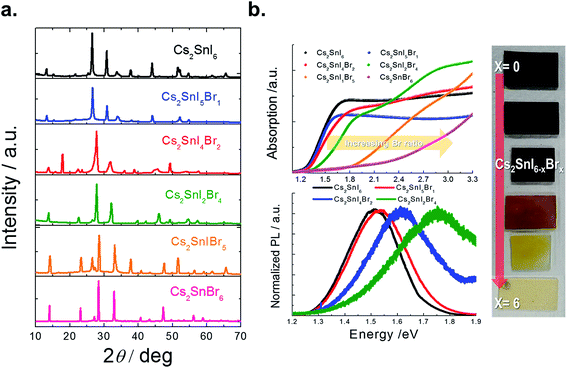 |
| Fig. 9 Characteristics of the different compositions of Cs2SnI6−xBrx: (a) XRD patterns of the film from the two-step solution-based deposition process with varying substitutions of Br (CsI and CsBr) and reacting with (SnI4 and SnBr4) materials. (b) Absorption spectra and PL analysis of various Cs2SnI6−xBrx compositions prepared by the two-step solution process. | |
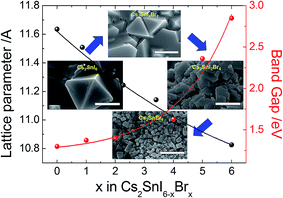 |
| Fig. 10 The change in the lattice constant and the shift in the optical band gap both indicate the solid-solution nature of the Cs2SnI6−xBrx system (inset: the surface morphologies of different compounds (note: the scale bar is 1 μm)). | |
2.3. Device configuration and performance
In our earlier effort we used a standard device fabrication procedure where layers were sequentially deposited on the cathode side of the device. But we soon found that we were having unwanted shorts in the devices coming from the edges for the adjacent layers. In addition, the roughness of the Cs2SnI6 surface layer also contributed to charge recombination in the grain boundaries. In order to improve the device performance, we adopt in this section a different device structure the so-called sandwich structure. In this scheme the two parts (anode and cathode sides) of the device are fabricated separately. Once these steps are done, the two sides are then sandwiched together using a solid state flexible HTM layer as described below. We first describe the performance of a Cs2SnI6 cell using this approach with a blend of different inorganic materials and succinonitrile (Section 3.1), followed by a discussion of cells with Br inclusion in the sensitizer to widen the bandgap (Section 3.2).
2.3.1. Cs2SnI6 device using the “sandwich” method.
The concept of the “sandwich” process is to prepare separately the cathode and the anode sides of the solar cell as illustrated in ESI 4a.† The two sides are then “sandwiched” together with a solid state HTM as a contact layer. We first discuss the importance of the contact layer in the “sandwich” method. For this concept to work well, high ionic conductivity and mechanical flexibility are two important prerequisite requirements for success. Accordingly, the use of plastic crystals which have a sufficient ion conductivity and flexibility in a stable phase is a plausible strategy to obtain effective Cs2SnI6 based solar cells.31–33 In an earlier publication,14,34 we demonstrated how we used CsSnI3 and Cs2SnI6 as a hole conductor in a dye sensitized solar cell. For the contact layer here we take the earlier approach of using Cs2SnI6 through oxidized CsSnI3 and directly synthesized Cs2SnI6 as a hole conductor and blend it with succinonitrile as a solid electrolyte layer between the anode and the cathode. Succinonitrile (SN, N
C–(CH2)2–C
N) functions as a polymer host medium for ion transport and forms a single plastic poly-crystal at room temperature and because of its high lattice stability it behaves as a solid ion conductor in the presence of Cs2SnI6. Additionally, copper thiocyanate (CuSCN) known as another p-type inorganic material with high hole mobility and compatible band position is also studied.35 The phenomenon of ion transport in our system could not be understood clearly as yet due to the lack of knowledge of the exact structural property correlations. However, macroscopic studies on the basic ionic parameters and their temperature variations provide a wealth of information regarding ion dynamics. The ionic conductivities of solid electrolytes were investigated via AC impedance spectroscopy measurements of symmetric cells with two pieces of platinized FTO glass (cell area: 0.188 cm2, thickness: 20 μm). From well-fitted spectra, one can see a well-defined semicircle at high and intermediate frequencies that is ascribed to the parallel combination of bulk resistance and bulk capacitance, which is a result of the migration of ions and the immobile polymer chains, respectively. The straight line after the semicircle at low frequencies is due to the double layer capacitance formed at the interface between the electrode and electrolyte36,37 (see Fig. 11a). The ionic conductivity of our samples was determined using a Solatron impedance analyzer (SI-1260) with an electrochemical interface (SI-1286) in a wide frequency range between 0.5 Hz and 5.0 MHz at different temperatures. The ionic conductivities σ (S cm−1) of all the samples were then calculated by using the following equation:38
where, d is the thickness of the film, and Rb and A are the resistance and cross-sectional area of the film. Rb is obtained from the complex impedance plot at the intersection of the plot and the real impedance axis. From this equation, σ data for electrolytes can be converted from resistance Rb data measured at different temperatures. The equivalent circuit and experimental results at different measuring temperatures are also shown in ESI 4.† On the basis of temperature dependent conductivity studies, we have confirmed the remarkably enhanced ionic conductivity (σ) of a blend of Cs2SnI6 and SN at 25 °C (∼1.04 × 10−3 S cm−1) and this was nearly a factor of 1000 higher with respect to that of pure SN (∼3.56 × 10−7 S cm−1) and CuSCN (at 9.14 × 10−6 S cm−1) under ambient conditions. Interestingly, the highest conducting value can be obtained by a Cs2SnI6 matrix formed by oxidized CsSnI3 powder with (P1,4)-I (2.45 × 10−3 S cm−1).39Fig. 11b bottom shows the temperature dependence of ionic conductivity as a function of 1000/T. The ionic conductivity increases with increasing temperature. The temperature dependence of the conductivity becomes insignificant in the lower temperature range, implying that the contribution of ionic conduction from various pathways may change at different temperatures. The activation energies (Ea) of each sample can be calculated by the Arrhenius type equation:
where σ0 is the pre-exponential factor, and k is the Boltzmann constant. The activation energy, Ea, can be computed from the linear-least-square fit of the data from a log
σ versus 1/T plot. Activation energy is the energy required for an ion to begin movement. When the ion has acquired sufficient energy, it is able to break away from the donor site and move to another donor site. It can be observed that the ions in highly conducting samples require lower energy for migration.40 In our system, the calculated Ea value for the different samples was decreased in the order Cs2SnI6 > CuSCN > oxidized Cs2SnI6. Interestingly, despite the poor conductivity of the CuSCN matrix system, it shows lower activation energy compared to Cs2SnI6. The lowest Ea value can be found for the oxidized Cs2SnI6. Further improvement can be found by adding (P1,4)-I into Cs2SnI6/SN.39 This blended HTM has a fast ionic conductivity from 5.67 × 10−3 S cm−1 at room temperature to 1.95 × 10−2 S cm−1 at 80 °C. Furthermore, the Cs2SnI6 blended film possesses the ability to form a free-standing and flexible film which can also help improve the mechanical contact (see Fig. 11b inset). In addition, the action of sandwiching the two halves of the device will help improve the contact of the SN/Cs2SnI6 blend with the grain boundaries of the Cs2SnI6 sensitizer, thus improving the device performance. The HOMO position is also determined via UPS (see ESI 5†). It can be seen that the CuSCN has a HOMO level of 5.2 ± 0.12 eV in accordance with the literature.35 In the case of the Cs2SnI6 matrix, a 0.1 eV difference in HOMO values is observed between the starting materials of CsSnI3 and Cs2SnI6. The devices formed by this “sandwich” process are simple and very stable under ambient conditions. This simplicity may make it possible for solar cell manufacturers to eventually replace expensive equipment. The detailed information can be seen in ESI 3.†Fig. 11c shows the XRD pattern of pure SN and the Cs2SnI6/SN films at different temperatures. Even if pure SN does not show the clear peak reported in the literature,41 two peaks at 20° and 28° can be observed. The temperature dependent phase of the Cs2SnI6/SN film was measured using an XRD equipped with a hot stage. The film was heated over the temperature range of 25 °C to 80 °C at the constant heating rate of 5 ° C min−1. The individual diffraction peaks of Cs2SnI6 and SN are clearly observed at room temperature. As the temperature increased, the intensity peak of SN gradually diminished and no diffraction peak was observed at 80 °C (melting temperature). When this heated film was cooled down to room temperature, the peak of SN with the (110) preferred orientation reappeared. This indicated that SN did not have a major effect on the decomposition of Cs2SnI6 to CsI and SnI4, but served as a solid state solvent for supporting the motion of any mobile ions.
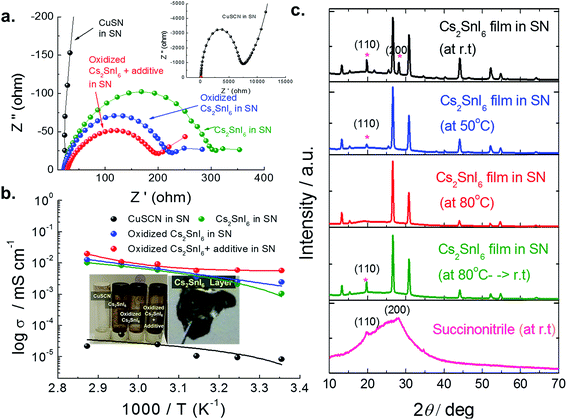 |
| Fig. 11 Different solid state ionic conductors as a HTM layer: (a) experimental and fitting impedance spectra at room temperature and (b) Arrhenius plots and photo-images of the different solid state electrolytes. (c) XRD pattern of the Cs2SnI6 mixed in succinonitrile film as a function of temperature (at r.t, 50 °C, 80 °C and cooled to room temperature). | |
2.3.2. Cs2SnI6−xBrx device using the “sandwich” method.
Solar performance with a FTO/bl-TiO2/2 wt% Sn–TiO2/Cs2SnIxBr6−x/solid state Cs2SnI6 based HTM/LPAH/FTO structure is shown in Fig. 12a. In order to obtain the best results with the Cs2SnIxBr6−x based solar cell, the two-step solution process and adding (P1,4)-I to the Cs2SnI6/SN matrix were used. Like our earlier approach, LPAH layers were selected because they increase charge species diffusion. In the J–V characteristics of the resultant devices, with increasing Br content from 0 to 4, regularly decreased Jsc and increased Voc values were obtained, corresponding to the variation of absorption and energy levels. In particular, we note that with the incorporation of Br, the Voc of our device has increased to near 0.563 eV. The best performing cell had an efficiency of about 2.05% on average and its IPCE value followed the same trend as that of MAPb(I1−xBrx)3 based cells.4 The solar performance parameters for these devices are displayed in Table 2. Their stability is also measured by operating in air for 50 days and photos of the absorbing material, Cs2SnI4Br2, are taken (see Fig. 12b). In the case of Cs2SnIxBr6−x compositions for x > 5, however, there was little solar performance, as expected, due to their wide bandgaps.
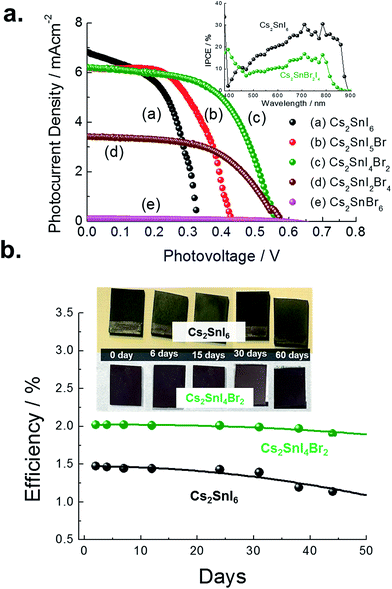 |
| Fig. 12 (a) JV characteristic curves of a series of “sandwich” typed cells with different composition of Cs2SnI6−xBrx. The inset shows the IPCE values for Cs2SnI6 (black) and Cs2SnBr2I4 (green). (b) The stability curves for 50 days are shown here for Cs2SnI6 (black), and the Cs2SnBr2I4 (green) based solar cells. | |
Table 2 Solar performance of the different compositions of Cs2SnIxBr6−x
Reaction |
Matched compound |
Calculated band gap (eV) |
JV characteristics |
V
oc (V) |
J
sc (mA cm−2) |
FF (%) |
Eff (%) |
CsI (film) + SnI4 (sol) |
Cs2SnI6 |
1.30 |
0.367 |
6.752 |
59.5 |
1.473 |
CsI : CsBr (7 : 3, film) + SnI4 (sol) |
Cs2SnI5Br |
1.375 |
0.444 |
6.576 |
55.0 |
1.601 |
CsI : CsBr (3 : 7, film) + SnI4 (sol) |
Cs2SnI4Br2 |
1.40 |
0.563 |
6.225 |
57.7 |
2.025 |
CsBr (film) + SnI4 (sol) |
Cs2SnI2Br4 |
1.63 |
0.575 |
3.413 |
54.8 |
1.081 |
CsI : CsBr (7 : 3, film) + SnBr4 (sol) |
Cs2SnIBr5 |
2.36 |
0.572 |
0.010 |
37.2 |
0.002 |
CsBr (film) + SnBr4 (sol) |
Cs2SnBr6 |
2.85 |
Non |
Non |
Non |
Non |
3 Summary and conclusion
In summary, we have reported in detail our investigation into a two-step solution process to form air-stable molecular semiconducting Cs2SnIxBr6−x iodosalt compounds for potential solar cell applications. There are many challenging processing steps as discussed in the three sections above. However, three major ones stand out: (1) how to form a stoichiometric compound throughout the iodosalt film across the length scale from nanometers to centimeters? We showed in our work that if there is an excess of CsI, in the compound, both electrical and optical performances of the material and the associated device will suffer deterioration. (2) How to form smooth and thick-enough film layers to fabricate a solar device with measurable performance? To achieve this demand, we showed how we had to optimize the CsI crystal structure in Step-1 through optimizing the annealing temperature and duration. In combination with Step-2, we had to optimize the reaction temperature and duration to obtain a thick and stoichiometric Cs2SnIxBr6−x compound. (3) How to choose film layers needed to optimize device performance with appropriate band-alignment without interfacial chemical reactions? As discussed in section 3, we did bandgap alignment engineering and developed a “sandwich” device fabrication process as an example of what can be done in our lab with no special environmental protection.
In conclusion, we have demonstrated that our two-step solution processing technique is one of many possible options to synthesize air stable Cs2SnIxBr6−x compounds. We have shown that both the materials and devices fabricated are air-stable, although with low performance, as a start. As with all materials research, to design a higher performance device, an improved starting material is necessary. Based on what we have learned, new synthesis concepts are currently being developed.
4 Experimental section
4.1. Preparation of Cs2SnI6 materials – sequential deposition of Cs2SnI6−xBrx
To coat different thickness Cs2SnI6 layers, a novel two-step coating process (electrospraying technique) has been developed in our laboratory. In the first step, a CsX solution was prepared dissolving 2 g of CsI or CsBr powder (Aldrich, 99.9%) in 1000 mL of a solvent mixture of deionized water and isopropanol (deionized water
:
isopropanol = 0.1
:
1 v/v). After sonication for 1 hour, the solutions were loaded into a plastic syringe equipped with a 27-gauge stainless steel needle. The spinning rate was controlled by using a syringe pump (KD Scientific Model 220) at 35–50 μL min−1. An electric field of 12–15 kV was applied between a metal orifice and the ground at a distance of 10 cm by using a power supply (BERTAN SERIES 205B). The CsI solution was directly e-sprayed on TiO2 spheres. The duration of electrospraying controls the thickness of the CsI or CsBr layers and this film was heated in a box furnace (Barnstead/Thermolyne Small Benchtop Muffle Furnaces) at temperatures ranging from 100 °C to 500 °C for 20 min in an ambient atmosphere. In the second step, a solution of Tin(IV) iodide (SnI4) or Tin(IV) bromide (SnBr4) in ethanol (0.1 g mL−1) was then introduced into the CsI or CsBr layer by drop coating. The drop process was repeated several times until the color of the covered CsI and CsBr layers changed from black to light yellow. This film was heated in air at 110 °C for 20 min.
4.2. Preparation for device fabrication
Unless stated otherwise, all manipulations described below were performed in air under ambient laboratory conditions.
4.2.1. Sn doped TiO2.
Sn–TiO2 sphere films were prepared by a simple hydrothermal method and electrospray technique similar to that mentioned in our earlier paper.14 Titanium(IV) isopropoxide, Ti(Oi-Pr)4 (100 mL), was separately mixed with a solution containing appropriate amounts of SnCl2·2H2O (Aldrich, 99.99%) in water. The percentage of Sn doping was tuned by using the Sn/Ti ratio in the precursor solution. A series of Sn-doped TiO2 materials with the Sn content ranging from 2 wt% to 10 wt% were successfully synthesized by the hydrothermal method. The hydrothermal Sn–TiO2 solution was electrosprayed after replacing water with ethanol.
4.2.2. Preparation of the anode.
To make a dense TiO2 blocking layer, cleaned FTO glasses were coated with 0.15 M titanium diisopropoxide bis(acetylacetonate), (Ti(Oi-Pr)2(acac)2, 75% in 1-butanol, Aldrich) solution by a spin-coating method, which was heated at 125 °C for 5 min. After the coated film was cooled down to room temperature, the same process was repeated twice with 0.3 M Ti(Oi-Pr)2(acac)2 solution in butanol. The three-time coated FTO glasses with TiO2 precursor solutions were heated at 500 °C for 15 min.
On the prepared dense TiO2 blocking layer, the dispersed Sn–TiO2 solution was electrosprayed directly onto the conducting substrates. To prepare the hierarchically structured TiO2 sphere, an electric field of 12 kV was applied between the metal orifice and the conducting substrate. The feed rate was controlled by using a syringe pump at 40–45 μL min−1. In order to form a uniform thickness in a large area, the nozzle and the substrate were placed on a motion control system with a microprocessor. The TiO2 films were annealed at 500 °C for 45 min. As a next step, TiCl4 aqueous solution has been applied to the E-sprayed TiO2 film. An aqueous stock solution of 2 M TiCl4 was diluted to 0.02 M in deionized water and the sintered electrodes were immersed into this solution and stored in an oven at 70 °C for 20 min in a closed vessel. After flushing with deionized water and drying, the electrodes were gradually sintered again at 150 °C for 15 min, at 320 °C for 10 min, and at 500 °C for 30 min.
4.2.3. Preparation of the cathode.
The electro-sprayed large-effective-surface-area polyaromatic hydrocarbon (LPAH) materials were used for our designed cell.42 For the purpose of this work, the arc was operated under the optimum conditions of 100 A and 27 V with pure hydrogen pressure in the range of 50 to 400 Torr. After one hour of arc operation a large amount (hundreds of grams) of LPAH “soot” was generated and collected from the chamber walls. The LPAH layer was coated by the E-spraying technique. The suspension prepared from about 2 g of LPAH in 1000 mL IPA was subjected to sonication for 30 min. And then, this suspension was loaded into a plastic disposable syringe (50 mL) with a steel needle (25-gauge) and a flow rate of 50 μL min−1 was maintained with a syringe pump (KD Scientific Model 220). The needle was connected to a high-voltage power supply of 12–14 kV and electrospray was conducted at a distance of 12 cm between the needlepoint and the collector. The thickness of the coating is proportional to the electrospray time. The LPAH deposited onto the FTO substrate and was sintered at 400 °C for 20 min.
4.2.4. Cell architecture.
The Cs2SnI6 powder was first prepared from oxidized fresh B-γ CsSnI3 powder.34,43 Then 5 wt% of mixed succinonitirile (99%, Sigma-Aldrich) and inorganic materials i.e. CuSCN, oxidized CsSnI3 and Cs2SnI6 powders (so called the “matrix”) were prepared for 10 h at 75 °C. This Cs2SnI6 fluid matrix was dropped on the anode under constant-temperature conditions at 80 °C in a Blue M Gravity Oven. After the matrix was melted on the anode, the active sides of the cathode were rapidly placed on the matrix/anode and then took the cell out of the box oven. After the cell was cooled to room temperature, the solidified matrix acts in holding two parts of electrodes together in a stable sandwich configuration. Finally, to avoid disassembling of the two electrodes during solar cell measurement, the edges of the air-cooled cell were sealed with epoxy. The Amosil 4 sealant was prepared by thoroughly mixing together a portion made of 100 weight units of resin (labeled as R) with 80 weight units of hardener (labeled as H). For curing of the epoxy, this cell was stored in a box for 24 h at room temperature.
4.3. Characterization
Powder and film X-ray diffraction patterns were collected in-house using a Rigaku MiniFlex 600 X-ray diffractometer (Cu Kα, 1.5406 Å) operating at 40 kV and 15 mA. Synchrotron radiation (APS, 11BM-B) was used for selected annealing temperatures of Cs2SnI6 to identify the decomposition temperature of the compounds. The obtained data were analyzed using the JANA2006 software package.44 Optical diffuse-reflectance spectra were collected at room temperature using a Shimadzu UV-3600 PC double-beam, double-monochromator spectrophotometer for powdered samples using BaSO4 as a 100% reflectance reference. XPS measurements were obtained using a monochromatic Al Kα source at hν = 1486 cm−1. A typical operating pressure for XPS and UPS measurements was 1 × 10−8 Torr. XPS spectra were collected at a pass energy of 20.0 eV and a dwell time of 10 ms. An electron flood gun was used to eliminate charging effects. All binding energies were referenced to an adventitious C(1 s) energy of 285.0 eV. UPS spectra were collected with a 21.2 eV He(1) source with a pass energy of 2.0 eV and a step size of 0.01 eV. A sample bias of −10 V was applied to determine the secondary electron cutoff value via curve fitting.
A Newport-Oriel® IQE-200 ACDC was used to measure incident photon to charge carrier efficiency (IPCE). The devices were evaluated under 100 mW cm−2 AM 1.5G simulated sunlight with a class A solar cell analyzer (Spectra Nova Tech.). A silicon solar cell fitted with a KG3 filter tested and certified by the National Renewable Energy Laboratory (NREL) was used for calibration. The KG3 filter accounts for the different light absorption between the perovskite based solar cell and the silicon solar cell, and it ensures that the spectral mismatch correction factor approaches unity.
Acknowledgements
This research was supported as part of the Argonne-Northwestern Solar Energy Research Center (ANSER), an Energy Frontier Research Center funded by the U.S. Department of Energy, Office of Science, Office of Basic Energy Sciences (award no. DE-SC0001059), and Institute for Sustainability and Energy at Northwestern (ISEN). We thank the NSF-MRSEC program through the Northwestern University Materials Research Science and Engineering Center for characterization facilities (DMR-1121262). XRD measurements were performed at the J. B. Cohen X-Ray Diffraction Facility, supported by the MRSEC program of the National Science Foundation (DMR-1121262) at the Materials Research Center of Northwestern University. Electron microscopy and elemental analysis were carried out at the Electron Probe Instrumentation Center (EPIC) at Northwestern University. The use of the Advanced Photon Source was supported by the US Department of Energy, Office of Science, Office of Basic Energy Sciences, under contract No. DE-AC02-06CH11357. We thank M. G. Kanatzidis and C. C. Stoumpos for discussions and their suggestions.
References
- M. M. Lee, J. Teuscher, T. Miyasaka, T. N. Murakami and H. J. Snaith, Efficient Hybrid Solar Cells Based on Meso-Superstructured Organometal Halide Perovskites, Science, 2012, 338(6107), 643–647 CrossRef CAS PubMed.
- J. Burschka, N. Pellet, S.-J. Moon, R. Humphry-Baker, P. Gao, M. K. Nazeeruddin and M. Gratzel, Sequential deposition as a route to high-performance perovskite-sensitized solar cells, Nature, 2013, 499(7458), 316–319 CrossRef CAS PubMed.
- M. Liu, M. B. Johnston and H. J. Snaith, Efficient planar heterojunction perovskite solar cells by vapour deposition, Nature, 2013, 501(7467), 395–398 CrossRef CAS PubMed.
- J. H. Noh, S. H. Im, J. H. Heo, T. N. Mandal and S. I. Seok, Chemical Management for Colorful, Efficient, and Stable Inorganic–Organic Hybrid Nanostructured Solar Cells, Nano Lett., 2013, 13(4), 1764–1769 CrossRef CAS PubMed.
- Y. Ogomi, A. Morita, S. Tsukamoto, T. Saitho, N. Fujikawa, Q. Shen, T. Toyoda, K. Yoshino, S. S. Pandey, T. Ma and S. Hayase, CH3NH3SnxPb(1−x)I3 Perovskite Solar Cells Covering up to 1060 nm, J. Phys. Chem. Lett., 2014, 5(6), 1004–1011 CrossRef CAS PubMed.
- F. Hao, C. C. Stoumpos, R. P. H. Chang and M. G. Kanatzidis, Anomalous Band Gap Behavior in Mixed Sn and Pb Perovskites Enables Broadening of Absorption Spectrum in Solar Cells, J. Am. Chem. Soc., 2014, 136(22), 8094–8099 CrossRef CAS PubMed.
- H.-S. Kim, C.-R. Lee, J.-H. Im, K.-B. Lee, T. Moehl, A. Marchioro, S.-J. Moon, R. Humphry-Baker, J.-H. Yum, J. E. Moser, M. Grätzel and N.-G. Park, Lead Iodide Perovskite Sensitized All-Solid-State Submicron Thin Film Mesoscopic Solar Cell with Efficiency Exceeding 9%, Sci. Rep., 2012, 2, 591 Search PubMed.
- G. E. Eperon, S. D. Stranks, C. Menelaou, M. B. Johnston, L. M. Herz and H. J. Snaith, Formamidinium lead trihalide: a broadly tunable perovskite for efficient planar heterojunction solar cells, Energy Environ. Sci., 2014, 7(3), 982–988 CAS.
- T. M. Koh, K. Fu, Y. Fang, S. Chen, T. C. Sum, N. Mathews, S. G. Mhaisalkar, P. P. Boix and T. Baikie, Formamidinium-Containing Metal-Halide: An Alternative Material for Near-IR Absorption Perovskite Solar Cells, J. Phys. Chem. C, 2014, 118(30), 16458–16462 CAS.
- G. E. Eperon, G. M. Paterno, R. J. Sutton, A. Zampetti, A. A. Haghighirad, F. Cacialli and H. J. Snaith, Inorganic caesium lead iodide perovskite solar cells, J. Mater. Chem. A, 2015, 3(39), 19688–19695 CAS.
- I. C. Smith, E. T. Hoke, D. Solis-Ibarra, M. D. McGehee and H. I. Karunadasa, A Layered Hybrid Perovskite Solar-Cell Absorber with Enhanced Moisture Stability, Angew. Chem., 2014, 126(42), 11414–11417 CrossRef.
- G. Niu, W. Li, F. Meng, L. Wang, H. Dong and Y. Qiu, Study on the stability of CH3NH3PbI3 films and the effect of post-modification by aluminum oxide in all-solid-state hybrid solar cells, J. Mater. Chem. A, 2014, 2(3), 705–710 CAS.
- M. A. Green, A. Ho-Baillie and H. J. Snaith, The emergence of perovskite solar cells, Nat. Photonics, 2014, 8(7), 506–514 CrossRef CAS.
- B. Lee, C. C. Stoumpos, N. Zhou, F. Hao, C. Malliakas, C.-Y. Yeh, T. J. Marks, M. G. Kanatzidis and R. P. H. Chang, Air-Stable Molecular Semiconducting Iodosalts for Solar Cell Applications:
Cs2SnI6 as a Hole Conductor, J. Am. Chem. Soc., 2014, 136(43), 15379–15385 CrossRef CAS PubMed.
- C. C. Stoumpos, C. D. Malliakas and M. G. Kanatzidis, Semiconducting Tin and Lead Iodide Perovskites with Organic Cations: Phase Transitions, High Mobilities, and Near-Infrared Photoluminescent Properties, Inorg. Chem., 2013, 52(15), 9019–9038 CrossRef CAS PubMed.
- Z. Xiao, H. Lei, X. Zhang, Y. Zhou, H. Hosono and T. Kamiya, Ligand-Hole in [SnI6] Unit and Origin of Band Gap in Photovoltaic Perovskite Variant Cs2SnI6, Bull. Chem. Soc. Jpn., 2015, 88(9), 1250–1255 CrossRef CAS.
- G. E. Eperon, V. M. Burlakov, P. Docampo, A. Goriely and H. J. Snaith, Morphological Control for High Performance, Solution-Processed Planar Heterojunction Perovskite Solar Cells, Adv. Funct. Mater., 2014, 24(1), 151–157 CrossRef CAS.
- B. Saparov, J.-P. Sun, W. Meng, Z. Xiao, H.-S. Duan, O. Gunawan, D. Shin, I. G. Hill, Y. Yan and D. B. Mitzi, Thin-Film Deposition and Characterization of a Sn-Deficient Perovskite Derivative Cs2SnI6, Chem. Mater., 2016, 28(7), 2315–2322 CrossRef CAS.
- A. E. Maughan, A. M. Ganose, M. M. Bordelon, E. M. Miller, D. O. Scanlon and J. R. Neilson, Defect Tolerance to Intolerance in the Vacancy-Ordered Double Perovskite Semiconductors Cs2SnI6 and Cs2TeI6, J. Am. Chem. Soc., 2016, 138(27), 8453–8464 CrossRef CAS PubMed.
- Z. Xiao, Y. Zhou, H. Hosono and T. Kamiya, Intrinsic defects in a photovoltaic perovskite variant Cs2SnI6, Phys. Chem. Chem. Phys., 2015, 17(29), 18900–18903 RSC.
- D. R. Stull, Vapor Pressure of Pure Substances. Organic and Inorganic Compounds, Ind. Eng. Chem., 1947, 39(4), 517–540 CrossRef CAS.
- W. Shockley and H. J. Queisser, Detailed Balance Limit of Efficiency of p–n Junction Solar Cells, J. Appl. Phys., 1961, 32(3), 510–519 CrossRef CAS.
- H. Lin, C. P. Huang, W. Li, C. Ni, S. I. Shah and Y.-H. Tseng, Size dependency of nanocrystalline TiO2 on its optical property and photocatalytic reactivity exemplified by 2-chlorophenol, Appl. Catal., B, 2006, 68(1–2), 1–11 CrossRef CAS.
- Y. Ling, G. Wang, D. A. Wheeler, J. Z. Zhang and Y. Li, Sn-Doped Hematite Nanostructures for Photoelectrochemical Water Splitting, Nano Lett., 2011, 11(5), 2119–2125 CrossRef CAS PubMed.
- T. Hirata, K. Ishioka, M. Kitajima and H. Doi, Concentration dependence of optical phonons in the TiO2–SnO2 system, Phys. Rev. B: Condens. Matter Mater. Phys., 1996, 53(13), 8442–8448 CrossRef CAS.
- P. V. Kamat, Photochemistry on nonreactive and reactive (semiconductor) surfaces, Chem. Rev., 1993, 93(1), 267–300 CrossRef CAS.
- S. Gubbala, V. Chakrapani, V. Kumar and M. K. Sunkara, Band-Edge Engineered Hybrid Structures for Dye-Sensitized Solar Cells Based on SnO2 Nanowires, Adv. Funct. Mater., 2008, 18(16), 2411–2418 CrossRef CAS.
- D. Sabba, H. K. Mulmudi, R. R. Prabhakar, T. Krishnamoorthy, T. Baikie, P. P. Boix, S. Mhaisalkar and N. Mathews, Impact of Anionic Br-Substitution on Open Circuit Voltage in Lead Free Perovskite (CsSnI3−xBrx) Solar Cells, J. Phys. Chem. C, 2015, 119(4), 1763–1767 CAS.
- A. Kaltzoglou, M. Antoniadou, A. G. Kontos, C. C. Stoumpos, D. Perganti, E. Siranidi, V. Raptis, K. Trohidou, V. Psycharis, M. G. Kanatzidis and P. Falaras, Optical-Vibrational Properties of the Cs2SnX6 (X = Cl, Br, I) Defect Perovskites and Hole-Transport Efficiency in Dye-Sensitized Solar Cells, J. Phys. Chem. C, 2016, 120(22), 11777–11785 CAS.
- C. Li, J. Wei, M. Sato, H. Koike, Z.-Z. Xie, Y.-Q. Li, K. Kanai, S. Kera, N. Ueno and J.-X. Tang, Halide-Substituted Electronic Properties of Organometal Halide Perovskite Films: Direct and Inverse Photoemission Studies, ACS Appl. Mater. Interfaces, 2016, 8(18), 11526–11531 CAS.
- L. Schmidt-Mende, S. M. Zakeeruddin and M. Grätzel, Efficiency improvement in solid-state-dye-sensitized photovoltaics with an amphiphilic ruthenium-dye, Appl. Phys. Lett., 2005, 86(1), 013504 CrossRef.
- P. Wang, Q. Dai, S. M. Zakeeruddin, M. Forsyth, D. R. MacFarlane and M. Grätzel, Ambient Temperature Plastic Crystal Electrolyte for Efficient, All-Solid-State Dye-Sensitized Solar Cell, J. Am. Chem. Soc., 2004, 126(42), 13590–13591 CrossRef CAS PubMed.
- D. R. MacFarlane and M. Forsyth, Plastic Crystal Electrolyte Materials: New Perspectives on Solid State Ionics, Adv. Mater., 2001, 13(12–13), 957–966 CrossRef CAS.
- I. Chung, B. Lee, J. He, R. P. H. Chang and M. G. Kanatzidis, All-solid-state dye-sensitized solar cells with high efficiency, Nature, 2012, 485(7399), 486–489 CrossRef CAS PubMed.
- P. Qin, S. Tanaka, S. Ito, N. Tetreault, K. Manabe, H. Nishino, M. K. Nazeeruddin and M. Grätzel, Inorganic hole conductor-based lead halide perovskite solar cells with 12.4% conversion efficiency, Nat. Commun., 2014, 5, 3834 CAS.
- X. Qian, N. Gu, Z. Cheng, X. Yang, E. Wang and S. Dong, Impedance study of (PEO)10LiClO4–Al2O3 composite polymer electrolyte with blocking electrodes, Electrochim. Acta, 2001, 46(12), 1829–1836 CrossRef CAS.
- W. Liu, N. Liu, J. Sun, P.-C. Hsu, Y. Li, H.-W. Lee and Y. Cui, Ionic Conductivity Enhancement of Polymer Electrolytes with Ceramic Nanowire Fillers, Nano Lett., 2015, 15(4), 2740–2745 CrossRef CAS PubMed.
- C. Meng, C. Liu, L. Chen, C. Hu and S. Fan, Highly Flexible and All-Solid-State Paper like Polymer Supercapacitors, Nano Lett., 2010, 10(10), 4025–4031 CrossRef CAS PubMed.
- B. Lee, D. B. Buchholz, P. Guo, D.-K. Hwang and R. P. H. Chang, Optimizing the Performance of a Plastic Dye-Sensitized Solar Cell, J. Phys. Chem. C, 2011, 115(19), 9787–9796 CAS.
- M. H. Buraidah, L. P. Teo, S. R. Majid and A. K. Arof, Ionic conductivity by correlated barrier hopping in NH4I doped chitosan solid electrolyte, Phys. B, 2009, 404(8–11), 1373–1379 CrossRef CAS.
- M. Echeverri, N. Kim and T. Kyu, Ionic Conductivity in Relation to Ternary Phase Diagram of Poly(ethylene oxide), Succinonitrile, and Lithium Bis(trifluoromethane)sulfonimide Blends, Macromolecules, 2012, 45(15), 6068–6077 CrossRef CAS.
- B. Lee, D. B. Buchholz and R. P. H. Chang, An all carbon counter electrode for dye sensitized solar cells, Energy Environ. Sci., 2012, 5(5), 6941–6952 CAS.
- I. Chung, J.-H. Song, J. Im, J. Androulakis, C. D. Malliakas, H. Li, A. J. Freeman, J. T. Kenney and M. G. Kanatzidis, CsSnI3: Semiconductor or Metal? High Electrical Conductivity and Strong Near-Infrared Photoluminescence from a Single Material. High Hole Mobility and Phase-Transitions, J. Am. Chem. Soc., 2012, 134(20), 8579–8587 CrossRef CAS PubMed.
-
V. Petříček, M. Dušek and L. Palatinus, Crystallographic Computing System JANA2006: General features, in Zeitschrift für Kristallographie – Crystalline Materials, 2014, vol. 229, p. 345 Search PubMed.
Footnote |
† Electronic supplementary information (ESI) available: Additional SEM images, profilometry data and transmission spectra of the CsX films. See DOI: 10.1039/c7se00100b |
|
This journal is © The Royal Society of Chemistry 2017 |
Click here to see how this site uses Cookies. View our privacy policy here.