Conversion of furfuryl alcohol to alkyl levulinate fuel additives over Al2O3/SBA-15 catalyst†
Received
15th December 2016
, Accepted 28th February 2017
First published on 28th February 2017
Abstract
Alkyl levulinates are promising renewable chemicals in the field of transportation fuels. In this work, the production of alkyl levulinates from furfuryl alcohol was investigated over a series of Al2O3/SBA-15 catalysts prepared by the wet impregnation method. The physicochemical features of the synthesized catalysts were characterized by X-ray diffraction, N2-physisorption, SEM, TEM, temperature-programmed desorption of ammonia, pyridine-adsorbed FT-IR and ICP-OES techniques. These analyses showed that the Al2O3/SBA-15 catalysts maintained the mesoporous structure of parent SBA-15 and that alumina particles were highly dispersed in the uniform pore channels of SBA-15. Al2O3 impregnation over SBA-15 resulted in enhanced acidity and the easy accessibility of active sites to reactants. Among the catalysts, 20 wt% Al2O3/SBA-15 catalyst exhibited the best activity in the alcoholysis of furfuryl alcohol with n-butanol, giving 94% selectivity toward n-butyl levulinate in a batch process. The reaction proceeded via formation of intermediates 2-butoxymethylfuran and 5,5-dibutoxy-2-pentanone, followed by conversion to n-butyl levulinate. The effects of various reaction parameters, including alumina loading, temperature, catalyst amount, n-butanol volume, and different alcohols, were studied. Catalyst recyclability was tested and the spent catalyst characterized. The 20 wt% Al2O3/SBA-15 catalyst was also active in n-butyl levulinate synthesis using a continuous process.
1. Introduction
The US government and European Union have pledged to produce 20% of fuels and 25% of chemicals from renewable sources by 2030, in an attempt to reduce dependency on non-renewable resources, such as fossil fuels. Consequently, using renewable biomass as a fuel source and in chemical production has attracted attention in the research community, because it currently supplies 14% of global energy requirements.1,2 Various approaches have been employed to convert biomass into fuels and chemicals, including chemical conversion, biochemical conversion, gasification, and pyrolysis. These processes aim to establish biomass as a sustainable source for the manufacture of hydrocarbon transportation fuels and versatile chemicals.3 Among these conversions, the acid hydrolysis of cellulose, an abundant component of biomass, produces, among other products, furfural, a chemical intermediate with an average annual demand of 200 kt.4 Furfural can be reduced to furfuryl alcohol (FA) over copper-based catalysts in a continuous process.5 FA is used in the synthesis of various resins, including laminating resins and resins for corrosion-resistant furan polymer concrete, as well as lysine, vitamin C, and lubricants.6 Beyond these applications, FA can be used in the production of alkyl levulinates because of its availability and efficiency in alcoholysis reactions. Alkyl levulinates are emerging biomass-derived chemicals with potential applications in the transportation fuel sector and fine chemical industry. Alkyl levulinates have broader usage in flavouring and fragrance industries.7 Alkyl levulinates are regarded as green solvents due to their lower vapour pressures compared with conventional solvents, which allows their use in metallic surface degreasing processes instead of chlorinated solvents.8 Alkyl levulinates are promising starting compounds, as alternatives to levulinic acid, in the synthesis of gamma valerolactone, a versatile molecule of industrial interest.9 The most enticing feature of alkyl levulinates is their fuel additive properties. Alkyl levulinates can be regarded as second generation oxygenates, raising the oxygen content in gasoline to burn more completely and reducing the release of harmful gases. The addition of alkyl levulinates to fuels reduces smoke and NOx emissions appreciably.9–11 In particular, ethyl levulinate (EL) can be directly added to diesel fuels up to 5 wt%, with its miscibility and flow properties affording desirable fuel properties. An increase in the fuel performance of cotton-seed-derived biodiesel was observed with the addition of EL as a blending agent. The miscibility of EL with diesel fuel is low at lower temperatures, whereas butyl levulinate shows constant miscibility in diesel fuel, even at its cloud point. Minimization of engine swelling and changes in hardness were observed using butyl levulinates and alkyl levulinates of higher alcohols.11–13 The numerous applications of alkyl levulinates have led to their synthesis becoming more attractive in recent decades. High value-added alkyl levulinates could be synthesized by the alcoholysis of FA in the presence of acid catalysts. Conventionally, mineral acids like H2SO4, H3PO4, and HF are used as inexpensive homogeneous catalysts in the synthesis of alkyl levulinates. However, these acids are extremely corrosive and environmentally harmful.14 To avoid using these homogeneous acid catalysts and develop a sustainable approach, researchers have attempted to synthesize alkyl levulinates using solid acid catalysts. Consequently, solid acid catalysts, such as resins, ion exchange resins,15 sulfonic acid-functionalized SBA-15,16 mesostructured aluminosilicates,17 SO42−/TiO2,18 and metal salts,19 have been successfully used for alkyl levulinate production. Solid acid catalysts, such as organic inorganic hybrid catalysts containing ionic liquids,20 SO3H-functionalized ionic liquids,21 sulfonic acid-functionalized carbon materials,22 zirconia bifunctionalized organosilica-modified heteropoly acid,23 and organosulfonic-acid-functionalized organosilica hollow nanospheres,24 have been developed for the synthesis of alkyl levulinates. However, most of these catalysts are associated with complicated recoveries, high costs, and complex preparations. FA alcoholysis to produce alkyl levulinates is influenced by the acid site density, strength, and accessibility of active sites to reactants.9,25 Alumina is regarded as a popular catalyst support and used as an acid catalyst in various catalytic applications, such as the Fischer–Tropsch process and dehydrogenation reactions.26,27 Mesoporous silica (SBA-15) has unique characteristics, including a large surface area to disperse active components, uniform pore channels, and high thermal stability, which make it a beneficial support for various applications in catalysis.29–32 In this context, the dispersion of alumina over the large surface area of SBA-15 will enhance both the acidity and accessibility of active acidic sites to the reactants, increasing their catalytic performance in the reaction studied herein. Al2O3/SBA-15 catalysts with various loadings, ranging from 5 to 30 wt%, were prepared using the wet impregnation method and applied to the synthesis of alkyl levulinates from FA in batch and continuous processes at atmospheric pressure.
2. Experimental
2.1 Catalyst preparation
Mesoporous silica SBA-15 was prepared using P123 (M/s Sigma-Aldrich, USA) as the template and TEOS (M/s Sigma-Aldrich, USA) as the silica source, according to a reported method.28–31 In a typical synthesis, a solution containing P123/2 M HCl/TEOS/H2O in a mass ratio 2
:
60
:
4.25
:
15 was prepared and stirred at 40 °C for 24 h followed by hydrothermal treatment at 100 °C for another 24 h under static conditions. The product was collected by filtration and then dried in air at 80 °C for 12 h and calcined at 550 °C under air flow for 8 h. The resultant white solid (SBA-15) was used as a support. Al2O3/SBA-15 catalysts with various loadings (5, 10, 20, and 30 wt%) were prepared by the wet impregnation method using aluminium nitrate (M/s. S.D. Fine-Chem., India) as the alumina precursor. Briefly, an aqueous solution containing the requisite amount of aluminium nitrate was added to SBA-15 and the mixture was dried on a hot plate to complete dryness. The solid was dried in an oven at 100 °C for 12 h and then calcined at 450 °C for 5 h in static air. The resultant solid was labelled XAS, where X indicates the percentage weight of alumina. For comparison, commercial alumina (M/s. Sud Chemie, India) was also used.
2.2 Catalyst characterization
Powder X-ray diffraction patterns were recorded on an Ultima-IV X-ray diffractometer (M/s. Rigaku Corporation, Japan) using Ni-filtered Cu Kα radiation (λ = 1.5406 Å) with a 2θ scan range of 0.7–80° at 40 kV and 30 mA. The BET specific surface area, pore volume, and pore size were determined on a Quadrasorb-SI (M/s. Quantachrome Instruments, USA) by nitrogen adsorption–desorption at the temperature of liquid N2. Before measurement, the sample was degassed at 150 °C for 2 h. The composition of Al2O3 was obtained by ICP-OES (M/s. Thermo Scientific iCAP6500 DU) by dissolving the compounds in the aqua regia containing a few drops of hydrofluoric acid to digest the SBA-15. The acidic features of the catalysts were investigated by temperature-programmed desorption of ammonia. Approximately 50 mg of catalyst sample was loaded in a tubular sample tube pretreated under helium flow at 300 °C for 1 h. Subsequently, the catalyst sample was saturated with 10% NH3/He at 80 °C for 30 min. After saturation, helium was flowed for 30 min at 100 °C to completely remove physisorbed ammonia. Helium flow was continued while increasing the temperature to 800 °C at a rate of 10 °C min−1 and desorbed NH3 was monitored using TCD-equipped GC. Pyridine adsorption analysis was conducted in diffuse reflectance infrared Fourier transform (DRIFT) mode. Prior to dry pyridine adsorption, the catalyst was degassed under vacuum at 200 °C for 3 h. Excess pyridine was removed by heating the sample at 120 °C for 1 h. FT-IR spectra of the pyridine-adsorbed samples were recorded at room temperature. Electron microscopy studies of the samples were carried out by scanning electron microscopy (SEM, M/s. JEOL, Switzerland) and transmission electron microscopy (TEM) images were obtained using JEM 2000EXII apparatus (M/s. JEOL, Switzerland).
2.3 Catalytic activity
Alcoholysis of furfuryl alcohol was carried out over Al2O3/SBA-15 catalysts in a 25 mL round bottom flask equipped with a reflux condenser at atmospheric pressure. In a typical experiment, 1 mmol of furfuryl alcohol (M/s S.D. Fine chem. India), 6 mL of n-butanol (M/s. S.D. Fine chem. India) and 0.4 g of catalyst were added to the round bottom flask. The mixture was heated at 110 °C under constant stirring for 6 h. Unless otherwise specified, the applied reaction conditions were the same as mentioned above. The products were identified on a FID-equipped GC-17A (M/s. Shimadzu Instruments, Japan) with a EB-5 capillary column (30 m × 0.53 mm × 5.0 μm) and confirmed by GC-MS (M/s. QP-2010, Shimadzu Instruments, Japan) with EB-5 MS capillary column (30 m × 0.25 mm × 0.25 μm). The continuous process was performed as follows. The fixed-bed downflow reactor (id, 14 mm; length, 300 mm) was loaded with 0.4 g of catalyst and mixed with same amount of quartz particles placed in the middle of the reactor. Prior to the catalytic test, the catalyst was flushed with N2 flow at 180 °C for 1 h. The reactants (1 mmol of FA + 6 mL of n-BuOH) were fed into the reactor at a flow of 1 mL h−1 using N2 as the carrier gas, and the products were collected in an ice-cold trap.
3. Results & discussions
Powder XRD patterns of SBA-15 and Al2O3/SBA-15 samples are shown in Fig. 1. The low-angle XRD patterns showed that all samples displayed three diffraction peaks at 2θ values of around 0.9°, 1.7°, and 1.9° due to the (100), (110) and (200) reflections, respectively, from the p6mm symmetry of the 2D hexagonal pore arrangement.28–32 The d(100) and unit cell parameter values are presented in Table 1, and are in line with earlier reports.28–32 These results indicated that the mesoporous ordered structure of pristine SBA-15 was intact, even after alumina impregnation. Wide-angle XRD patterns (Fig. 1 inset) of the samples showed a broad peak in the 2θ region of 15–30°, which was characteristic of amorphous silica. No signals for crystalline Al2O3 were found, demonstrating that Al2O3 was present in an amorphous or highly dispersed form. The presence of Al2O3 was confirmed by ICP-OES analysis, with the values presented in Table 1 similar to theoretical values.
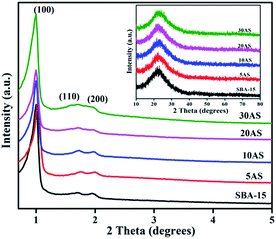 |
| Fig. 1 Low-angle XRD patterns of parent SBA-15 and Al2O3/SBA-15. Inset, wide-angle XRD patterns of Al2O3/SBA-15 samples. | |
Table 1 Textural/structural parameters and acidity of SBA-15 and various Al2O3/SBA-15 samples
Catalyst |
S
BET
(m2 g−1) |
S
BET
(m2 g−1) |
V
t
(cm3 g−1) |
D
(nm) |
d
(100)
(nm) |
a
0
(nm) |
t
(nm) |
Theoretical Al2O3 loading (wt%) |
Al2O3 loading by ICP (wt%) |
Acidity (mmol NH3 per g) |
BET surface area.
Surface area per gram of support.
Total pore volume.
Average pore size.
Periodicity of SBA-15 derived from low angle XRD.
Unit cell length.
Pore wall thickness.
|
SBA-15 |
617 |
617 |
0.92 |
5.84 |
8.83 |
10.20 |
4.36 |
0 |
0 |
0.02 |
5AS |
608 |
640 |
0.85 |
4.14 |
8.84 |
10.21 |
6.07 |
5 |
4.3 |
0.71 |
10AS |
590 |
656 |
0.86 |
4.52 |
8.82 |
10.19 |
5.67 |
10 |
9.5 |
1.27 |
20ZS |
543 |
679 |
0.81 |
5.04 |
8.86 |
10.23 |
5.19 |
20 |
18.1 |
1.61 |
30AS |
457 |
653 |
0.66 |
5.52 |
8.92 |
10.30 |
4.78 |
30 |
27.4 |
1.92 |
The N2-physisorption isotherms and pore-size distributions of SBA-15 and Al2O3/SBA-15 samples are shown in Fig. 2. All exhibited type IV isotherms with H1 hysteresis loops in accordance with the IUPAC classification of porous materials, demonstrating the mesoporous nature of these samples.28–31 This clearly indicated the intactness of the mesoporous nature of SBA-15, even with the highest amount (30 wt%) of alumina deposition. The pore size distribution curves are shown in the inset of Fig. 2. The pores were distributed within the range of 5–15 nm, showing the existence of ordered mesopores. The surface area of the pristine SBA-15 decreased with increasing Al2O3 amounts (Table 1). However, the decrease in surface area was not much as expected from the theoretical values, indicating the highly dispersed nature of the active species over SBA-15. The surface area per gram of support in XAS samples was always higher than the surface area of pristine SBA-15 (Table 1), which clearly demonstrates both the high dispersion of Al2O3 and its porous nature, which enhances the surface area.
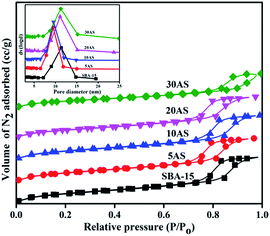 |
| Fig. 2 N2 adsorption–desorption isotherms for parent SBA-15 and various Al2O3/SBA-15 samples. Inset, pore size distributions of the same samples. | |
SEM and TEM images of SBA-15 and 20AS samples are shown in Fig. 3. The SEM images showed the presence of well-ordered hexagonal arrangements of mesoporous SBA-15 in both pristine SBA-15 and 20AS. Furthermore, the TEM images show uniform pore channels typical of mesoporous SBA-15 materials in pure SBA-15 and 20AS.28–31 Moreover, the TEM image of 20AS showed that alumina particles were highly dispersed in the uniform pore channels of SBA-15. Additionally, X-ray diffraction and N2 physisorption studies confirmed retention of the mesoporous structure of SBA-15, even after alumina deposition.
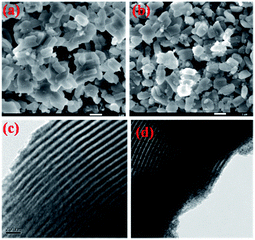 |
| Fig. 3 SEM images of (a) parent SBA-15 and (b) 20AS samples. TEM images of (c) parent SBA-15 and (d) 20AS samples. | |
The profiles of temperature-programmed desorption of ammonia (NH3-TPD) for SBA-15 and Al2O3/SBA-15 samples are shown in Fig. 4, and their corresponding total acidity values are given in Table 1. Acidic sites present in the catalysts can be classified depending on the desorption temperature of adsorbed ammonia molecules. Strong acidic sites are desorb chemisorbed ammonia molecules at higher temperatures, above 400 °C, while medium acidic sites desorb at 250–400 °C and weak acidic sites desorb at temperatures below 250 °C.33,34
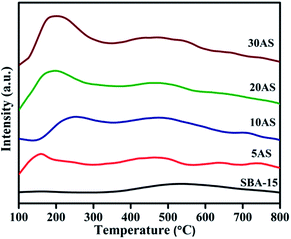 |
| Fig. 4 NH3-TPD profiles of parent SBA-15 and various Al2O3/SBA-15 samples. | |
All Al2O3/SBA-15 catalysts showed a desorption peak in the region 130–250 °C, demonstrating the presence of large amounts of weak acidic sites due to the dispersion of alumina over SBA-15. Another small desorption peak at around 480 °C was due to the presence of strong acidic sites. The total acidity of the catalysts increased with increasing alumina loading.
Pyridine-adsorbed Fourier transform infrared spectra (Py-FTIR) were recorded for SBA-15 and Al2O3/SBA-15 samples to evaluate the type of acidic sites and are depicted in Fig. 5. Pristine SBA-15 and Al2O3/SBA-15 gave two bands at 1445 and 1597 cm−1, which were attributed to pyridine coordination to surface Lewis acidic sites.35,36 All Al2O3/SBA-15 samples exhibited two bands at 1545 and 1630 cm−1, which were ascribed to protonated pyridine bonded to surface Brønsted acid sites. Additionally, a band at 1490 cm−1 appeared as a result of both Lewis and Brønsted acid sites.36,37 The intensity of these bands was observed to increase with increasing alumina loading, indicating that the dispersion of alumina on SBA-15 caused surface Lewis acidic sites and Brønsted acidic sites, which increased the total acidity of Al2O3/SBA-15 catalysts.
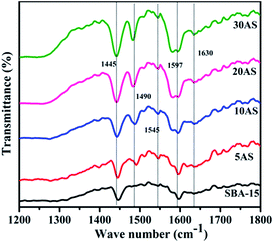 |
| Fig. 5 Py-FTIR spectra of SBA-15 and various Al2O3/SBA-15 samples. | |
3.1 Catalytic activity studies
3.1.1 Effect of Al2O3 loading.
The effect of alumina loading, from 5 to 30 wt%, on the alcoholysis of furfuryl alcohol (FA) was investigated to determine the optimum alumina loading. The results, including error bars, are shown in Fig. 6. Both pristine SBA-15 and alumina exhibited low activity, giving 23 and 72% conversion of FA with 0 and 14% selectivity for BL, respectively. The dispersion of alumina over SBA-15 resulted in full FA conversion and higher BL selectivity due to enhanced acidity and easier accessibility for reactants. By increasing the alumina loading from 5 to 20 wt%, the selectivity for BL increased from 72 to 94% with complete conversion of FA. When the loading increased from 5 to 20 wt%, the selectivity for intermediates (NMR and GC-MS patterns are shown in the ESI†) 2-butoxymethylfuran (BMF) and 5,5-dibutoxy-2-pentanone (DBP) decreased due to the increase in acidity (as evidenced by NH3-TPD studies). Therefore, the conversion of the intermediates to BL occurred. Further increasing the alumina loading gave no considerable change in activity, indicating that the acidity of the 20AS catalyst was sufficient to obtain maximum selectivity for BL in the reaction. Furthermore, the reaction was performed using BMF as the reactant instead of FA under the same reaction conditions. The conversion of BMF to BL took 4 h, giving 89% selectivity for BL. This indicated that the conversion of BMF to BL was slower than the conversion of FA to BMF. Therefore, the reaction was considered to proceed through the formation of two intermediates, 2-butoxymethylfuran (BMF) and 5,5-dibutoxy-2-pentanone (DBP), as shown in Scheme 1, in agreement with earlier reports.17,25
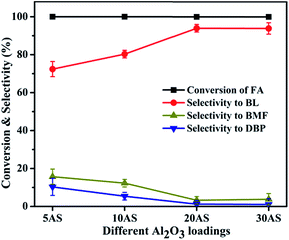 |
| Fig. 6 Effect of Al2O3 loading on FA alcoholysis. Reaction conditions: catalyst amount, 0.4 g; FA, 1 mmol; n-butanol, 6 mL; temperature, 110 °C; time, 6 h. | |
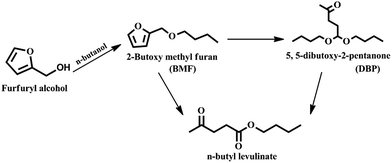 |
| Scheme 1 Conversion of furfuryl alcohol to n-butyl levulinate. | |
3.1.2 Effect of temperature.
The effect of temperature on FA alcoholysis over 20AS catalyst was evaluated in the temperature range 70–130 °C and the results are presented in Fig. 7. At a reaction temperature of 70 °C, the selectivity for BL was 25% and for BMF was 64%, with 96% conversion of FA. When the temperature was increased to 90 °C, the selectivities increased to 52% for BL and 27% for BMF, with complete conversion of FA. There was no appreciable change in selectivity with prolonged reaction time in both cases. A further increase in temperature to 110 °C increased selectivity toward BL substantially to 94%, with a drastic decrease in selectivity for intermediate BMF. Further increasing the temperature to 130 °C led to similar activity as at 110 °C. These results were ascribed to BL production from FA alcoholysis involving the formation intermediates first, followed by their conversion into product BL.17,25 As the temperature increased from 70 to 110 °C, the selectivity toward intermediate BMF decreased drastically, indicating that the conversion of BMF to BL was higher at 110 °C compared with lower temperatures (70 and 90 °C). Similar results have been reported previously, suggesting that maximum conversion of intermediate BMF could be achieved at 110 °C.20,21 Therefore, the maximum selectivity toward BL was obtained with the high conversion of intermediate BMF at 110 °C.
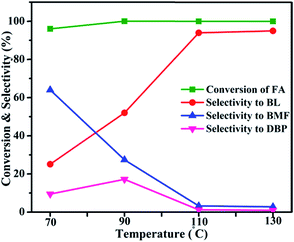 |
| Fig. 7 Effect of temperature on FA alcoholysis. Reaction conditions: catalyst amount, 0.4 g; FA, 1 mmol; n-butanol, 6 mL; time, 6 h. | |
3.1.3 Effect of catalyst amount.
The effect of catalyst amount on the FA alcoholysis over 20AS catalyst was studied by varying the catalyst amount from 0.1 to 0.5 g, with the results shown in Fig. 8. The selectivity toward BL increased with increasing catalyst amount in the reaction mixture. As the catalyst amount increased from 0.1 to 0.4 g, the selectivity toward BL increased from 48 to 94% with complete conversion of FA, while the selectivity toward intermediates (BMF and DBP) decreased. Extending the reaction time to 8 h, the selectivities toward BL using 0.1, 0.2, 0.3 and 0.4 g were 54, 78, 86 and 94.6%, respectively. There was no considerable change in selectivity toward BL with extended reaction times. Increasing the catalyst amount from 0.1 to 0.4 g tended to increase the accessibility and number of active sites for the reactants and decreased the selectivity toward intermediate BMF from 47 to 3%, indicating there was an insufficient number of acid sites to convert BMF to BL in 0.1 g of catalyst. When the catalyst amount was increased to 0.4 g, a sufficient number of acidic sites was available to achieve maximum conversion of BMF to BL. There was no change in the selectivity toward BL, despite the catalyst amount increasing to 0.5 g.
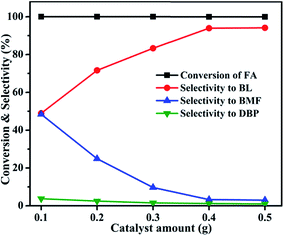 |
| Fig. 8 Effect of catalyst amount on FA alcoholysis. Reaction conditions: FA, 1 mmol; n-butanol, 6 mL; temperature, 110 °C; time, 6 h. | |
3.1.4 Effect of reaction time.
The effect of reaction time on FA alcoholysis over 20AS catalyst was examined using different time periods, up to 8 h, and the results are presented in Fig. 9. As the reaction time increased, the selectivity toward BL increased, while the selectivity toward intermediates decreased. After 2 h reaction time, the selectivity toward BL was 47%, those toward BMF and DBP were 31 and 19%, respectively. The selectivity toward BL increased with reaction time, reaching a maximum of 94% in 6 h, after which there was no further increase in selectivity toward BL. Notably, although the complete conversion of FA could be achieved in under 2 h, the maximum selectivity toward BL was achieved at 6 h with a gradual decrease in selectivity toward the intermediates. This implied that alcoholysis of FA to BL proceeded through formation of the intermediates (BMF and DBP), followed by the conversion of intermediates to BL, in agreement with previous reports.17,20,21
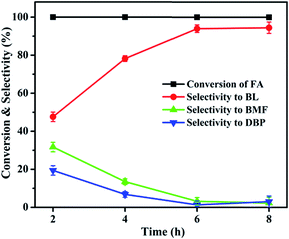 |
| Fig. 9 Effect of reaction time on FA alcoholysis. Reaction conditions: catalyst amount, 0.4 g; FA, 1 mmol; n-butanol, 6 mL; temperature, 110 °C. | |
3.1.5 Effect of n-butanol volume.
The n-butanol volume was varied from 2 to 8 mL to evaluate its effect on FA alcoholysis over 20AS catalyst, as shown in Fig. 10. Using 2 mL of n-butanol, the selectivity toward BL was 62%, with full conversion of FA. By increasing the n-butanol volume to 4 mL, the selectivity toward BL increased from 62 to 83%. Furthermore, increasing the n-butanol volume to 6 mL resulted in the largest selectivity toward BL (94%), with complete conversion of FA, while a further increase to 8 mL yielded slightly lower selectivity toward BL (92%). Increasing the n-butanol volume increased the selectivity toward BL due to the higher concentration of FA, which readily undergoes polymerization to form oligomeric products.38 To avoid such polymerization and convert the intermediates to BL, a higher amount of n-butanol was needed. The maximum selectivity toward BL in this reaction was achieved with 6 mL of n-butanol.
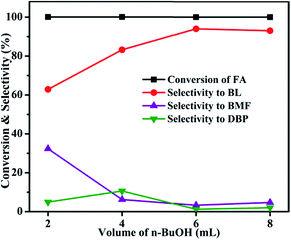 |
| Fig. 10 Effect of n-butanol volume on FA alcoholysis. Reaction conditions: catalyst amount, 0.4 g; FA, 1 mmol; temperature, 110 °C; time, 6 h. | |
3.1.6 Catalyst recyclability.
To investigate the catalyst efficiency and stability, recycling experiments were conducted under optimized reaction conditions, with the results illustrated in Fig. 11. After completing each catalytic cycle, the catalyst was recovered by centrifugation, then thoroughly washed with methanol and dried at 100 °C for 3 h before using in the next catalytic run. FA conversion was consistent for up to four cycles, while the selectivity toward BL slightly decreased from 94 to 82%. This decrease in selectivity toward BL was explained using XRD, NH3-TPD, ICP-OES, and CHNS analysis of the spent catalyst. Fig. 12 shows the XRD patterns of fresh and spent catalysts. They showed that there was no change in the low-angle or wide-angle XRD patterns, demonstrating the intactness of the mesoporous structure. Temperature-programmed desorption of ammonia was performed on the fresh and spent catalysts, showing that the total acidity of the fresh catalyst (1.51 mmol NH3 per g) was higher than that of the spent catalyst (1.1 mmol NH3 per g). ICP-OES analysis showed no significant change in alumina content between the fresh (18.1 wt%) and spent catalysts (17.9 wt%), which confirmed that the decrease in activity is not due to the loss of active species. CHNS analysis of the spent catalyst showed the presence of carbon, which was not found in the fresh catalyst. Therefore, the slight decrease in selectivity toward BL using the spent catalyst was due to the adsorption of carbonaceous species (perhaps oligomeric byproducts) on the catalyst surface, which obstructed access to the active sites of the catalyst. Furthermore, a leaching test was performed to determine whether the catalytic reaction proceeded heterogeneously or homogeneously. Under optimized reaction conditions, the reaction was conducted for 3 h, then the catalyst was removed from and the system continued reacting without catalyst for another 3 h. The results indicated that increase in selectivity toward BL after the catalyst was removed was only ∼1%, confirming that the catalytic process proceeded in a heterogeneous manner.
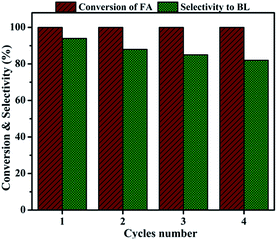 |
| Fig. 11 Catalyst recyclability. Reaction conditions: catalyst amount, 0.4 g; FA, 1 mmol; n-butanol, 6 mL; temperature, 110 °C; time, 6 h. | |
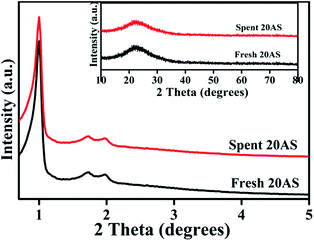 |
| Fig. 12 Low-angle and wide-angle XRD patterns of fresh and spent 20AS catalysts. | |
3.1.7 Influence of different alcohols.
The influence of different alcohols on FA alcoholysis was investigated over 20AS catalyst at their respective reflux temperatures. FA alcoholysis using methanol and ethanol gave 84 and 95% conversion, with lower selectivity toward alkyl levulinates of 4 and 34%, respectively. Using n-propanol gave 82% selectivity for n-propyl levulinate with complete conversion of FA. The selectivity toward alkyl levulinates using methanol and ethanol was much lower than that using n-butanol. The reaction temperature had a profound effect on the conversion of intermediate 2-alkoxymethylfuran into alkyl levulinate. At the lower reflux temperatures of methanol and ethanol (due to their lower boiling points compared with higher alcohols) the conversion of intermediate alkoxymethylfuran was lower, resulting in decreased selectivity toward the alkyl levulinate.
3.1.8 Continuous process.
To examine catalyst excellence, the synthesis of n-butyl levulinate from furfuryl alcohol was attempted using a continuous process at atmospheric pressure at 180 °C (near the boiling point of FA), with the results presented in Fig. 13. Under vapour phase conditions, the 20AS catalyst exhibited complete conversion of FA, with 91% selectivity toward BL. The catalytic activity was consistent during the time on stream (6 h). In both processes (batch and continuous), the 20AS catalyst showed the best catalytic activity in the selective conversion of FA to BL.
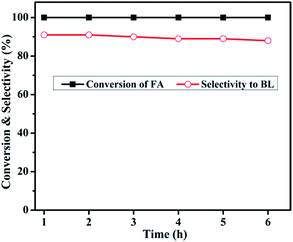 |
| Fig. 13 Reaction conditions: catalyst weight, 0.4 g; reaction temperature, 180 °C; N2 flow, 30 mL min−1; reactant feed flow, 1 mL h−1. | |
The catalytic activity of the 20AS catalyst was compared with the reported catalysts, as shown in Table 2. The catalytic conversion of FA to BL over HZSM-5 gave a 40% yield of BL in 6 h. Sulfonic-acid-functionalized SBA-15 gave 96% selectivity toward BL in 4 h.16 However, catalyst reusability was not reported. Al-TUD-1 was also active for the conversion of FA to BL, yielding 60% BL at 140 °C after 24 h.17 HY-zeolite-catalyzed conversion resulted in a lower yield of BL (3%).20 Ionic-liquid-functionalized hybrid catalysts gave a 93% yield of BL in 12 h.20 Reactions with inorganic acids HCl and H2SO4 resulted in 76 and 68% selectivity toward BL at 110 °C for 6 h, respectively. These results imply that, in addition to the acidic strength of the catalyst, the accessibility of acidic sites to reactants is crucial for the catalytic conversion of FA to BL. In the present catalyst, Al2O3/SBA-15, the active acidic sites were well dispersed over the uniform pore channels of SBA-15 resulting in higher selectivity toward BL.
Table 2 Comparison of 20AS catalyst with reported catalysts
Catalyst |
Temperature (°C) |
Time (h) |
BL selectivity/yield (%) |
Ref. |
Continuous process, P = present.
|
HZSM-5 |
110 |
6 |
40 |
16
|
SBA-SO3H |
110 |
4 |
96 |
16
|
Al-TUD-1 |
140 |
24 |
60 |
17
|
[MIMBS]3PW12O40 |
110 |
12 |
93 |
20
|
HY-zeolite |
110 |
12 |
3 |
20
|
20AS |
110 |
6 |
94 |
P |
20ASa |
180 |
6 |
91 |
P |
4. Conclusions
In conclusion, Al2O3/SBA-15 catalysts were successfully prepared by the wet impregnation method and subjected to furfuryl alcohol alcoholysis in a batch process. Characterization studies showed that Al2O3/SBA-15 catalysts retained the mesoporous structure of SBA-15, and that alumina particles were in an amorphous or highly dispersed state. Among the impregnated catalysts, 20 wt% Al2O3/SBA-15 gave complete conversion of furfuryl alcohol with 94% selectivity toward n-butyl levulinate. The catalytic activity of 20 wt% Al2O3/SBA-15 catalyst was due to the presence of accessible acidic sites widespread over SBA-15. Catalytic activity studies showed that the synthesis of n-butyl levulinate from the alcoholysis of furfuryl alcohol over 20 wt% Al2O3/SBA-15 catalyst involved the formation of intermediates 2-butoxymethylfuran and 5,5-dibutoxy-2-pentanone, which were then converted to n-butyl levulinate. The 20 wt% Al2O3/SBA-15 catalyst could be reused in up to four cycles, with only a small drop in selectivity toward BL observed, due to the obstruction of active sites by adsorbed carbonaceous species. More importantly, n-butyl levulinate synthesis was achieved in both batch and continuous vapour-phase processes at atmospheric pressure.
Acknowledgements
The authors E. S. S., K. K. S., and G. V. R. B. gratefully thank University Grant Commission, New Delhi, for financial support. The services of the analytical division of CSIR-IICT for ICP-OES analysis are deeply acknowledged.
References
- Directive, 2003/30/EC Eur. Union Parliam, Off. J. Eur. Union, 2003, http://ec.europa.eu/energy/res/legislation/doc/biofuels/en_final.pdf.
- U.S. Dep. Energy, 2002, Roadmap for biomass technologies in the United States, http://www.brdisolutions.com/pdfs/FinalBiomassRoadmap.pdf.
- S. Fernando, S. Adhikari, C. Chandrapal and N. Murali, Energy Fuels, 2006, 20, 1727 CrossRef CAS.
-
K. J. Zeitsch, The Chemistry and Technology of Furfural and its Many Byproducts, Elsevier, Amsterdam, 2000 Search PubMed.
- B. M. Nagaraja, A. H. Padmasri, B. David Raju and K. S. Rama Rao, J. Mol. Catal. A: Chem., 2007, 265, 90 CrossRef CAS.
- B. M. Nagaraja, A. H. Padmasri, P. Seetharamulu, K. Hari Prasad Reddy, B. David Raju and K. S. Rama Rao, J. Mol. Catal. A: Chem., 2007, 278, 29 CrossRef CAS.
- E. Siva Sankar, G. V. Ramesh Babu, C. R. Reddy, B. David Raju and K. S. Rama Rao, J. Mol. Catal. A: Chem., 2017, 426, 30 CrossRef.
-
N. B. Ferrer, L. G. Prats, C. E. Company and J. C. Boliart, European Patent EP2540871A1, 2013.
- A. Demolis, N. Essayem and F. Rataboul, ACS Sustainable Chem. Eng., 2014, 2, 1338 CrossRef CAS.
-
R. H. Clark, A. P. Groves, C. Morley and J. Smith, Fuel Compositions, Patent WO2004035713, 2004.
- E. Christensen, A. Williams, S. Paul, S. Burton and R. L. McCormick, Energy Fuels, 2011, 25, 5422 CrossRef CAS.
- H. Joshi, B. R. Moser, J. Toler, W. F. Smith and T. Walker, Biomass Bioenergy, 2011, 35(7), 3262 CrossRef CAS.
-
A. P. Grove, C. Morely, J. Smith and A. Stevenson, US Pat. Application 2005/0144835 A1, 2005.
- Y. Leng, J. Wang, D. R. Zhu, X. Q. Ren, H. Q. Ge and L. Shen, Angew. Chem., Int. Ed., 2009, 121, 174 CrossRef.
- J. P. Lange, W. D. van de Graaf and R. J. Haan, ChemSusChem, 2009, 2, 437 CrossRef CAS PubMed.
- P. Demma Car, R. Ciriminna, N. R. Shiju, G. Rothenberg and M. Pagliaro, ChemSusChem, 2014, 7, 835 CrossRef PubMed.
- P. Neves, M. M. Antunes, P. A. Russo, J. P. Abrantes, S. Lima, A. Fernandes, M. Pillinger, S. M. Rocha, M. F. Ribeiro and A. A. Valente, Green Chem., 2013, 15, 3367 RSC.
- G. Zhao, L. Hu, Y. Sun, X. Zeng and L. Lin, BioResources, 2014, 9, 2634 CAS.
- Y. B. Huang, T. Yang, M. Chao Zhou, H. Pan and Y. Fu, Green Chem., 2016, 18, 1516 RSC.
- Z. Zhang, K. Dong and Z. (Kent) Zhao, ChemSusChem, 2011, 4, 112 CrossRef CAS PubMed.
- G. Wang, Z. Zhang and L. Song, Green Chem., 2014, 16, 1436 RSC.
- R. L. Liu, J. Z. Chen, X. Huang and L. M. Chen, Green Chem., 2013, 15, 2895 RSC.
- D. Song, S. An, Y. Sun and Y. Guo, J. Catal., 2016, 333, 184 CrossRef CAS.
- B. Lu, S. An, D. Song, F. Su, X. Yang and Y. Guo, Green Chem., 2015, 17, 1767 RSC.
- P. Neves, S. Lima, M. Pillinger, S. M. Rocha, J. Rocha and A. A. Valente, Catal. Today, 2013, 218–219, 76 CrossRef CAS.
- M. Trueba and S. P. Trasatti, Eur. J. Inorg. Chem., 2005, 17, 3393 CrossRef.
- D. S. Maciver, H. H. Tobin and R. T. Barth, J. Catal., 1963, 2, 485 CrossRef CAS.
- D. Y. Zhao, J. L. Feng, Q. S. Huo, N. Melosh, G. H. Fredrickson, B. F. Chmelka and G. D. Stucky, Science, 1998, 279, 548 CrossRef CAS PubMed.
- E. Siva Sankar, G. V. Ramesh Babu, K. Murali, B. David Raju and K. S. Rama Rao, RSC Adv., 2016, 6, 20230 RSC.
- E. Siva Sankar, V. Mohan, M. Suresh, G. Saidulu, B. David Raju and K. S. Rama Rao, Catal. Commun., 2016, 75, 1–5 CrossRef CAS.
- G. Saidulu, E. Siva Sankar, M. Ravi Kumar, K. S. Rama Rao and B. David Raju, Catal. Sci. Technol., 2014, 4, 1813 Search PubMed.
- G. Muthu Kumaran, S. Garg, K. Soni, M. Kumar, L. D. Sharma, G. Murali Dhar and K. S. Rama Rao, Appl. Catal., A, 2006, 305, 123 CrossRef.
- A. Boreave, A. Auroux and C. Guimon, Microporous Mater., 1997, 11, 275 CrossRef CAS.
- V. Mohan, V. Venkateshwarlu, C. V. Pramod, B. D. Raju and K. S. Rama Rao, Catal. Sci. Technol., 2014, 4, 1253 CAS.
- X. Li Yang, W. L. Dai, R. Gao and K. Fan, J. Catal., 2007, 249, 278 CrossRef.
- X. Li Yang, R. Gao, W. L. Dai and K. Fan, J. Phys. Chem. C, 2008, 112, 3819 Search PubMed.
- K. Barbera, P. Lanzafame, A. Pistone, S. Millesi, G. Malandrino, A. Gulino, S. Perathoner and G. Centi, J. Catal., 2015, 323, 19 Search PubMed.
- A. Mija, P. Navard, C. Peiti, D. Babor and N. Guigo, Eur. Polym. J., 2010, 46, 1380 CrossRef CAS.
Footnote |
† Electronic supplementary information (ESI) available. See DOI: 10.1039/c6se00103c |
|
This journal is © The Royal Society of Chemistry 2017 |
Click here to see how this site uses Cookies. View our privacy policy here.