Effect of mixing bio-oil aqueous phase model compounds on hydrogen production in non-catalytic supercritical reforming†
Received
23rd June 2017
, Accepted 1st August 2017
First published on 1st August 2017
Abstract
Bio-oil derived from biomass fast pyrolysis can be processed into fuel or some chemical products, but it has a waste aqueous phase that, however, may be valorized. Supercritical reforming of this stream, simulated using mixtures of model compounds (acetic acid, acetol, 1-butanol and glucose), was experimentally studied in a tubular reactor without using a catalyst. The effect of mixing the model compounds at different operating parameters (temperature, feed composition, and residence time) on the process performance was investigated, thus addressing an important chemical aspect of biomass-based renewable energy. The experimental dry gas composition consisted of H2, CO2, CO and CH4, although the gas yields were far from equilibrium. Hydrogen yields were normally less than 2.0 moles of H2 per mole of organic feed, which are lower than those obtained for pure compounds with the same concentration. Based on the analyzed liquid samples, a series of probable reaction pathways were proposed to explain the experimental results by considering the interactions among the compounds and their formed intermediates. Thus, under tested supercritical conditions, the residence time was insufficient to reform the formed methane into hydrogen, thus leading to lower hydrogen production.
1. Introduction
Bio-oil derived from biomass fast pyrolysis can be processed into fuels or some chemical products. The oil phase can be separated from the aqueous phase by adding water. The oil phase is the valuable fraction, and the aqueous phase may be considered as waste. However, this stream contains organic compounds, such as alcohols, ketones, aldehydes, and carboxylic acids,1 so it could be re-utilized and valorized. So far, there are very few works in the literature that have studied its possible applications, mainly in catalytic reforming processes, such as steam reforming,2–4 autothermal reforming5 and aqueous phase reforming,6 which generate hydrogen and carbon monoxide in addition to carbon dioxide and methane. From an energy point of view, the main barrier is the high amount of water to be vaporized (about 80%).5 Thus, as water does not need to be vaporized, the use of supercritical water (SCW) makes it possible to perform another type of reforming process, due to its relevant thermo-physical properties, such as its high capability to solubilize gaseous organic molecules. Besides, reactions in SCW are conducted in a single phase and since SCW is extremely reactive,7 it may be possible to perform the process without adding a catalyst.
The present study focuses on the investigation of the SCW reforming (SCWR) performance of different mixtures of acetic acid, acetol, 1-butanol, and glucose (representative of the oxygenates in the aqueous fraction of bio-oil), aiming to acquire insight into how the water-rich phase of bio-oil could behave in supercritical water reforming reactions, where interactions among the compounds take place, and different gas yields might be obtained with respect to those predicted using only compounds fed separately.8 This is very important since most studies dealt with only a compound as representative of a real stream to predict its behavior. To our knowledge, no other researchers investigated this, although there are some studies performed on diluted binary mixtures such as phenol (1 wt%) plus glucose (<2 wt%),9 acetic acid (0.5 wt%) plus phenol (1.0 wt%),10 or glycerol plus methanol, somewhat more concentrated (from 5 to 20 wt%),11 although these compounds are not present in the bio-oil aqueous phase. Other previous works in this field have been also focused on some model compounds, especially glucose, obtaining reaction pathways with different levels of detail.12–14 Few studies have added one or two compounds to a third one, considered as the major compound. In some of these cases, the authors mentioned possible interactions when showing the difference between experimental and predicted (if each component reacts independently) values, but without further explanations.15,16
The main novelty presented in this paper is the full study of the supercritical reforming of the bio-oil aqueous phase using mixtures of representative model compounds without adding a catalyst, in which the effect of mixing on the gas yields, especially the hydrogen yield, under operating conditions is shown. In this way, potential pathways are proposed, which might explain the results. The successive conversion of the four compounds fed to the reactor through intermediates (all of them were detected in analysis of liquid samples) until reaching the final conversion to gas is provided, and evolution of gas yields is quantified and compared with equilibrium yields. The process performance is assessed in terms of gas yields that are compared with those obtained using pure model compounds as tested separately. The discussion is centered on how model compounds, representative of the aqueous phase of bio-oil, chemically convert and interact when mixed, thus affecting the gas yields.
The experimental study was carried out at different values of temperature, feed mixture compositions and residence times, at 240 bar. The ranges of experimental conditions are wider than those used in earlier works both in temperature and concentration or biomass loading. Besides, the experimental results are compared with simulation results obtained using a non-stoichiometric approach by Aspen Plus, both assuming equilibrium and an approach to the equilibrium temperature, which corresponds to the deviation from equilibrium conditions and might aid in predicting gas yields in this non-catalytic process.
2. Materials and methods
The experiments were carried out with acetic acid (>99.7% purity), hydroxyacetone (>95.0% purity), 1-butanol (>99.4% purity) and glucose (>99.5% purity), as well as deionized water. Fig. 1 illustrates a diagram of the experimental plant. An aqueous solution of the mixture of organic constituents is pumped by a HPLC-type pump and heated to the operating temperature in an electrical tubular furnace housing the reactor (2.0 m length; 7.92 mm ID) made of Inconel 625. The gas product leaving the reformer is cooled to 40 °C and expanded through a back-pressure valve. Next, the condensate is separated from the gas in a knockout drum. The mass flow-rate of the gas stream is measured, and a sample of this stream is continuously analyzed with a gas chromatograph (Agilent 7890A). It should be noted that the reactor material (Inconel 625, with a high content of nickel) was quite aged because it had been operating for more than 1500 h under SCW conditions for other different tests, so it is assumed that it had no catalytic activity.
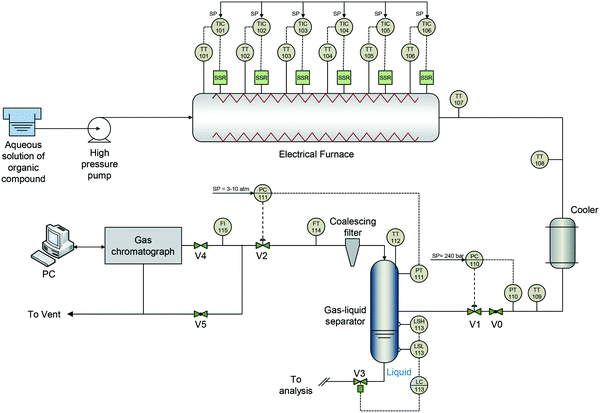 |
| Fig. 1 Scheme of the experimental plant. | |
The tests were conducted over 3–6 hours, at 240 bar and a temperature from 700 to 800 °C. The surface temperature was measured and controlled along the reactor in six points. The feed mixture compositions contained acetol, 1-butanol and/or glucose (from 2.5 to 5.0 wt%), as well as acetic acid (from 2.5 to 15 wt%). The most concentrated mixture of the model compounds was 22.5 wt%, which is a representative value of the aqueous fraction of bio-oil. Likewise, the feed flow-rate was changed between 0.5 and 1.0 L h−1, so the calculated residence time17 varied, approximately, from 20 s at 1.0 L h−1 to 40 s at 0.5 L h−1. Mixtures of two, three and four compounds (binary, ternary and quaternary mixtures) under different operating conditions were tested, carrying out up to 98 experimental tests, most of them replicated.
The analysis of liquid samples was performed using four analyzers, due to the difficulty of determining simultaneously all the tested compounds. More details can be found in the ESI.†
The performance variables were computed as follows: Hydrogen yield:
|  | (1) |
Organic compound conversion:
| 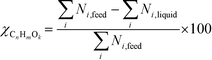 | (2) |
Carbon-to-gas efficiency:
| 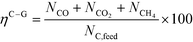 | (3) |
Carbon-to-liquid efficiency:
| 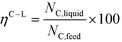 | (4) |
Carbon-to-solid efficiency:
| 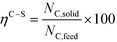 | (5) |
Carbon balance:
|  | (6) |
where
N denotes the number of moles of the compound referred in the subscript,
ηC–L gives the total organic carbon (TOC) in the liquid product, and
ηC–S takes into account the formed carbon.
NC is the number of moles of carbon.
NC,solid is the carbon residue recovered by means of vacuum filtration after washing the reactor with pressurized water, and then quantified by drying and weighing the residue. The tests with a mean error of the carbon balance of less than 10% were considered as valid experiments.
In order to compare the performance of mixtures with that of pure compounds with the same concentration (wt%), adjusted gas yields were used to take into account the real number of moles in the mixture (sum of all the moles of fed compounds, Ni), so the adjusted hydrogen yield for the mixture of several compounds is:
| 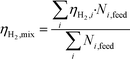 | (7) |
where
ηH2,i is the hydrogen yield for the pure
i-th compound having the same total concentration.
In this way, potential interactions between compounds can be compared using calculus with eqn (7) and the experimental result, obtained using eqn (1).
Chemical equilibrium calculations of reforming of the bio-oil aqueous phase were carried out with Aspen Plus using different mixtures of acetic acid, acetol (or hydroxyacetone), 1-butanol and glucose, both at equilibrium and using an approach to the equilibrium temperature. The non-stoichiometric approach is based on the method of minimizing the Gibbs free energy, and an R-Gibbs reactor was used to calculate the product composition and the total molar flow-rate. At equilibrium, the maximum hydrogen yield is achieved under specific conditions (temperature, pressure and feed mixture composition); alternatively, an approach to the equilibrium temperature implies evaluating the standard Gibbs free energy of each mixture at a temperature different from the reactor temperature. The thermodynamic method was the predictive Soave–Redlich–Kwong (PSRK), because it is very suitable for dealing with supercritical conditions.8 The equilibrium conversion of the mixtures of organic compounds was always 100%, as well as the carbon-to-gas efficiency.
3. Results
At 700 °C, the conversion of organic compounds was normally very high, only decreasing to 69.9–86.2% for ternary and quaternary mixtures involving high concentrations of acetic acid and glucose. In these cases, the carbon-to-liquid efficiency increased significantly up to 22.6%. At 800 °C, the conversion of organic compounds was always greater than 99.5% for all the tests, and the carbon-to-liquid efficiency was also lower than 1.5%. The carbon-to-gas efficiency was nearly always greater than 90.0%. Almost all the gas product (>98 vol%) was always H2, CO2, CO and CH4. However, in a few cases, a very small concentration of C2 (<2 vol%) was detected, which was identified as ethylene or ethane. Likewise, ηC–S was less than 0.5%. Solid characterization can be found in the ESI.†
Fig. 2 and 3 illustrate the effect of the concentration of some ternary and quaternary mixtures of organic constituents in aqueous solution on the yield of hydrogen and other gases, at 800 °C and 1.0 L h−1 or 0.5 L h−1, so the influence of residence time can be also observed in some of them. More results are shown in the ESI.† The solid lines represent equilibrium values, where a complete feedstock conversion is achieved. The symbols represent the average values of measured gas yields and error bars provide the standard deviation of those measurements. In general, the uncertainty is quite low, with most of the deviations ranging from 0.05 to 0.15 (mol/mol), and even lower for CO yields. Only in a very few cases, the error was somewhat higher, as can be seen in Fig. 2d where the H2 yield varied between 0.22 and 0.25 (mol/mol) with respect to the average value. The gas yields decrease as the feed concentration increases. Hydrogen yields were lower than 2.0, except for the mixtures without acetic acid, in which yields increased to 3.3. Likewise, at 0.5 L h−1, yields of H2 and CO2 are higher than those at 1.0 L h−1, so the residence time has a positive effect, although gas yields are still far from equilibrium.
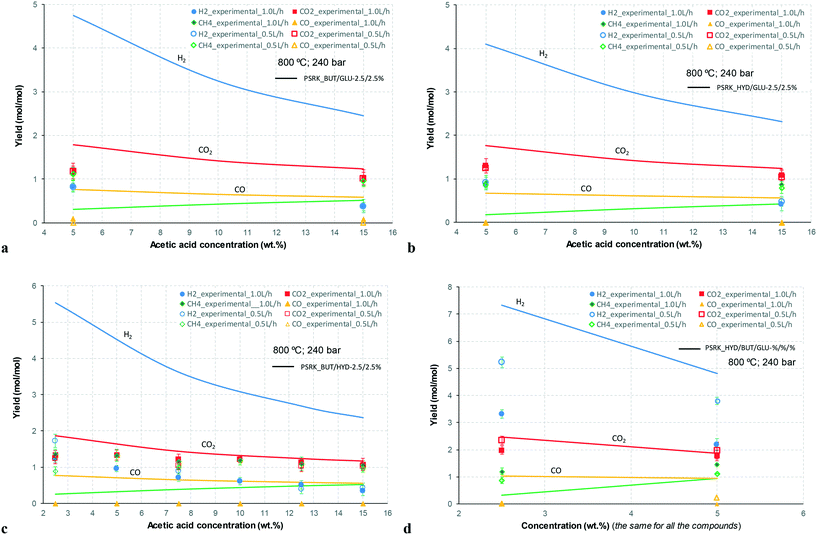 |
| Fig. 2 Effect on the gas yields of the acetic acid concentration (a) for 2.5/2.5 wt% 1-butanol/glucose, (b) for 2.5/2.5 wt% hydroxyacetone/glucose, (c) for 2.5/2.5 wt% 1-butanol/hydroxyacetone, and (d) of the glucose concentration for two concentrations of 1-butanol/hydroxyacetone (2.5/2.5/2.5 and 5.0/5.0/5.0 wt%), at 800 °C and 240 bar, both at 1.0 L h−1 and 0.5 L h−1 [H2: blue; CO2: red; CH4: green; CO: orange]. | |
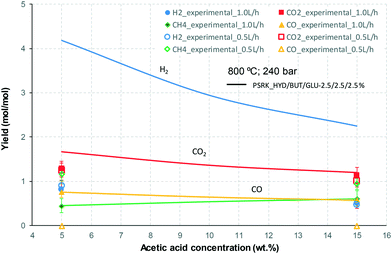 |
| Fig. 3 Effect of the acetic acid concentration on the gas yields for 2.5/2.5/2.5 wt% 1-butanol/hydroxyacetone/glucose concentrations, at 800 °C and 240 bar, both at 1.0 L h−1 and 0.5 L h−1 [H2: blue; CO2: red; CH4: green; CO: orange]. | |
At 800 °C, the binary, ternary and quaternary mixtures of acetic acid, 1-butanol, acetol and/or glucose, for all the tested concentrations, resulted in carbon-to-liquid efficiencies ranging from 0.1 to 0.4%, except for the mixture 1-butanol/glucose 5/5 wt% (0.9%). However, at 700 °C, for highly concentrated quaternary mixtures, the carbon-to-liquid efficiency was 18.2% and the glucose and acetic acid conversions were 69.9% and 97.1%, respectively. For the mixtures of acetic acid and 1-butanol 10/5 (wt%) and acetic acid and hydroxyacetone 15/5 (wt%), the carbon-to-liquid efficiency increased up to 22.1% and 12.4%. In these cases, the main organic component in the liquid product (>97.5%) was acetic acid. At 700 °C and in concentrated mixtures containing glucose, the process could lead to polymerization of some fed or intermediate compounds, thus forming char/tar. In these tests, yellowish and orange liquid effluents and a thin layer of dark brown oil-like tar were observed. However, reactor clogging did not occur.
Non-converted acetic acid and glucose were the major substances detected in the liquid samples. Other compounds were detected, such as acetone, which appeared very frequently. In those mixtures using acetol, ethanol and methanol were detected. When glucose was fed along with other compounds, the liquid after SCWR normally had phenol, and sometimes hydroxy-methyl-furfural (5-HMF), furfural, 4-hydroxy-4-methyl-2-pentanone, ethyl-acetate, 2-methyl-phenol, p-cresol, 1-hexanol, hexanaldehyde and formic acid. The latter was also detected in the binary mixture of 1-butanol and hydroxyacetone. The liquid phase was analyzed in detail to provide support to the potential reaction pathways, which might explain how the interactions among the fed compounds and intermediates affect the reforming process. Table 1 shows some analysis results of the liquid product corresponding to representative mixtures, at 1.0 L h−1, where some of the detected organic compounds are expressed in percentage points of total mass concentration. Table 1 also includes the TOC (mg L−1) and the carbon-to-liquid efficiency. The uncertainty in quantification of the liquid species was due to equipment accuracy and dilutions carried out in a few samples, ranging from ±1.5 to ±4.5%. Nevertheless, there are some unknown compounds, which may partially match some of the fed compounds that could not be measured.
Table 1 Analytical results from the liquid product of some tests from different mixtures at 240 bar and 1.0 L h−1
T (°C) |
Feed composition (wt%) |
Product liquid composition (wt%) |
TOC (mg L−1) |
η
C–L (%) |
AC |
HY |
BU |
GL |
AC |
HY |
BU |
GL |
Acetone |
Phenol |
HeOH |
Ethyl-acetate |
4H-4M-2P |
5-HMF |
MeOH |
EtOH |
Uk |
AC: Acetic acid; HY: hydroxyacetone; BU: 1-butanol; GL: glucose; HeOH: 1-hexanol; 4H-4M-2P: 4-hydroxy-4-methyl-2-pentanone; MeOH: methanol; EtOH: ethanol; Uk: others/unknown. ‘?’ means that the compound could not be measured (it may be part of the unknown).
|
800 |
|
5.0 |
|
5.0 |
|
13.9 |
|
8.6 |
3.1 |
|
35.8 |
|
29.3 |
|
|
5.2 |
4.1 |
71 |
0.13 |
700 |
|
5.0 |
|
5.0 |
5.6 |
23.8 |
|
54.1 |
4.3 |
5.4 |
4.3 |
|
0.7 |
|
|
|
1.8 |
487 |
0.88 |
800 |
|
|
5.0 |
5.0 |
4.7 |
|
20.6 |
64.6 |
1.1 |
|
0.8 |
|
1.2 |
0.1 |
1.5 |
5.4 |
0.0 |
176 |
0.23 |
700 |
|
|
5.0 |
5.0 |
13.1 |
|
? |
55.2 |
6.4 |
13.6 |
2.8 |
5.4 |
0.9 |
|
|
|
2.6 |
423 |
0.68 |
800 |
|
5.0 |
5.0 |
5.0 |
|
6.0 |
7.5 |
13.5 |
9.0 |
|
|
26.8 |
|
|
1.9 |
12.6 |
22.7 |
173 |
0.20 |
700 |
|
5.0 |
5.0 |
5.0 |
13.6 |
22.7 |
? |
51.8 |
2.1 |
6.4 |
0.6 |
|
0.2 |
|
|
|
2.6 |
1056 |
1.32 |
800 |
15.0 |
|
|
5.0 |
20.2 |
|
|
? |
|
20.9 |
7.3 |
|
|
|
36.6 |
? |
15.0 |
34 |
0.05 |
800 |
15.0 |
|
5.0 |
|
42.5 |
|
? |
|
4.2 |
|
|
|
|
|
|
46.8 |
6.5 |
40 |
0.04 |
800 |
10.0 |
|
5.0 |
|
61.3 |
|
? |
|
9.5 |
|
|
|
|
|
|
? |
29.2 |
56 |
0.08 |
700 |
10.0 |
|
5.0 |
|
98.1 |
1.4 |
? |
|
|
|
|
|
|
|
|
|
0.5 |
16 975 |
22.12 |
800 |
15.0 |
2.5 |
2.5 |
|
48.9 |
10.6 |
15.4 |
|
|
|
|
3.2 |
|
|
|
21.9 |
0.0 |
57 |
0.06 |
800 |
15.0 |
2.5 |
|
2.5 |
8.9 |
3.4 |
|
31.8 |
4.6 |
0.7 |
6.7 |
4.3 |
5.9 |
|
6.3 |
24.1 |
3.3 |
157 |
0.18 |
700 |
15.0 |
2.5 |
|
2.5 |
52.8 |
0.1 |
|
45.1 |
|
2.0 |
|
|
|
|
|
|
0.0 |
15 578 |
18.31 |
800 |
15.0 |
|
2.5 |
2.5 |
37.6 |
11.1 |
12.0 |
14.5 |
4.3 |
3.4 |
6.9 |
|
|
|
|
9.5 |
0.7 |
220 |
0.24 |
700 |
15.0 |
|
2.5 |
2.5 |
44.1 |
|
? |
46.3 |
|
0.5 |
|
|
|
|
|
|
9.1 |
19 638 |
21.38 |
800 |
15.0 |
2.5 |
2.5 |
2.5 |
36.6 |
13.9 |
7.5 |
12.1 |
6.5 |
2.2 |
|
|
|
|
1.9 |
17.9 |
1.4 |
95 |
0.09 |
700 |
15.0 |
2.5 |
2.5 |
2.5 |
36.3 |
0.1 |
? |
60.7 |
|
0.9 |
|
|
|
|
|
|
2.0 |
19 213 |
18.22 |
4. Discussion
4.1. Probable reaction pathways
The TOC value in the liquid phase was much higher than that corresponding to the sum of the values of the TOC for the aqueous solution of isolated organic compounds, especially at 700 °C. Likewise, the gas yields from reforming of mixtures decreased for any temperature and organic concentration. In addition, as the feed concentration increases, the gas yields decrease, and H2 yields are lower than those obtained separately. Thus, when feeding a mixture of several compounds, more intermediates may be formed, which delays the gas production with respect to the case of feeding a pure compound, either by lengthening the series of reactions or because they may be harder to reform. That is, when mixing compounds, they might interact with each other and/or one of them with intermediates of the other, which can be visualized by a scheme in which two compounds, A and B, are fed to the reactor, and specific paths may be followed:
A → A1 + A2; A1 → A11 + A12; A2 → A21 + A22; (…)
B → B1 + B2; B1 → B11 + B12; B2 → B21 + B22; (…)
Some new reactions between A and B, or A and any of Bij (intermediate), or B and any of Aij (intermediate), or Aij and Bij might take place, thus leading to either a longer overall pathway or intermediates harder to reform to the desired hydrogen.
The mixture of organic compounds entering the reactor in aqueous solution undergoes progressive thermal decomposition through reaction intermediates, by competing ionic and free radical reactions. In near-critical water, the high ion-product provides an opportunity for ionic reactions, while in supercritical water (SCW), at lower densities and higher temperatures, free radical reactions are favored.18 SCW can have a significant effect on the kinetics of some radical reactions, directly as a solvent and/or indirectly as a reactant in many of the reactions involved during the overall SCWR process. Such kinetic effects may promote different pathways. First, near the reactor entrance, organic compounds in aqueous solution are converted into some intermediates, and then, the reactions with free-radicals lead to bond cleavage (O–H, C–H, and C–O), so small formed compounds, such as acids, alcohols and aldehydes, are progressively converted into gases.
Fig. 4 shows a simplified scheme of reactions without including most of the intermediates shown in Fig. S1 of the ESI,† where a detailed series of probable reaction pathways are proposed and discussed.
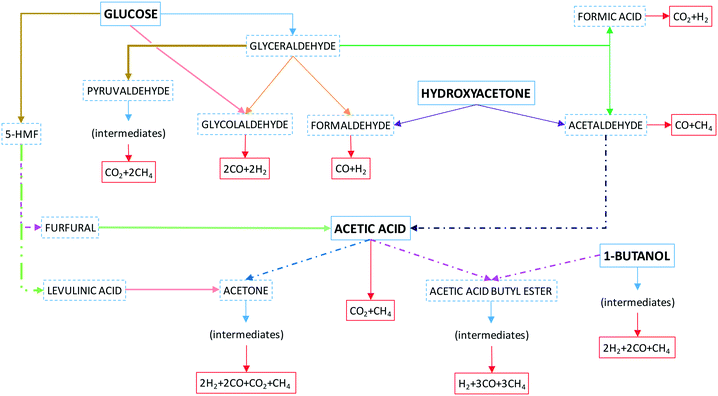 |
| Fig. 4 Simplified scheme of reaction pathways. | |
Concisely, glucose may follow various pathways to give CO and H2 if glycolaldehyde is mainly produced, or less H2 and more CH4 if glyceraldehyde is produced, or even CO2 and CH4 if the pathway was through pyruvaldehyde or decomposition through acetic acid formed from acetaldehyde. Similarly, if acetic acid is fed, it could lead to equimolar formation of CO2 and CH4. Hydroxyacetone decomposes to acetaldehyde and formaldehyde, which form CO, H2 and CH4. 1-Butanol may form CO, CH4 and ethylene. The latter reforms to H2, CH4 and CO.
Finally, once small acids, aldehydes and alcohols are converted into gas, the CH4 yield is initially higher than the H2 yield, and the latter increases as CH4 reforms with SCW and even more, if the water-gas shift (WGS) reaction takes place. In most previous studies,19–23 it has been stated that CO and CO2 produce CH4 by methanation reactions (reverse reaction of CH4 reforming). However, this is very unlikely due to the high temperatures and water amounts. Instead, CH4 must be formed from intermediates and then, it must suffer reforming with SCW.
4.2. Effect of the operating parameters
For any mixture, the gas yield decreases as the feed concentration increases, because the lower water-to-carbon molar ratio does not favor the conversion to the gas products. As the CO concentration was very low in almost all the tests, the WGS must be a relatively fast reaction, much faster than the methane reforming, considering the low H2 yields and the high CH4 yields, which are usually higher than those at equilibrium.
By increasing the residence time, the yields of H2 and CO2 become higher, although they are still far from equilibrium, because methane was not completely reformed. In this way, if CH4 was reformed at maximum, gas yields close to equilibrium values would be achieved. This was verified from the difference between the experimental and simulated (at equilibrium) CH4 yields, resulting in deviations with respect to the equilibrium lower than 10%, for those tests with a very high carbon-to-gas efficiency and very low carbon-to-liquid and carbon-to-solid efficiencies (generally, at 800 °C). Therefore, to enhance the SCWR performance, high temperature and long residence time are required to reform CH4. The latter may be achieved using a larger reactor, and the use of a suitable catalyst to increase the reaction rates and gas yields should be effective and, hence, tested.
4.3. Effect of mixing model compounds
4.3.1. Mixtures of glucose with other organic constituents.
Near the reactor entrance, the high concentrations of H+ and OH− ions accelerate the dehydration of glucose to form ring compounds (i.e., furfurals, phenol) instead of or in addition to other pathways. A high acetic acid concentration increases this effect, not only by itself but also through all the formed intermediate acids such as formic acid, lactic acid, acrylic acid and propionic acid. Acetic acid and phenols are persistent components that exist at temperatures even greater than 650 °C,24 which have been also obtained in this study, as shown in Table 1. Likewise, it has been also reported that SCWR of methanol was significantly retarded by acetic acid and phenol.10 Therefore, if both are present, these interaction effects lead to a poorer SCWR performance. Glyceraldehyde produced from glucose may be also dehydrated to form pyruvaldehyde and hence, acetic acid. Besides, furfural may be decomposed into a mixture of acetic acid and acrylic acid. Therefore, the interactions are clear between acetic acid and glucose. Thus, glucose interacts with any other organic compounds added to the feed. In this way, the H2 yield was 0.46 and 5.91 for pure acetic acid and glucose (7.5 wt%), and a mixture of 5.0/2.5 wt% acetic acid/glucose gave a H2 yield of 0.67 against the value of 1.24 obtained using eqn (7). Likewise, while the H2 yield was 3.24 and 6.07 for pure acetol and glucose (5.0 wt%), a mixture of 2.5/2.5 wt% acetol/glucose resulted in a H2 yield of 3.31 against the value of 3.95 obtained using eqn (7). However, for the mixture of 2.5/2.5 wt% 1-butanol/glucose, the experimental H2 yield was 4.28 and that calculated using eqn (7) was 4.31, i.e., no interference was detected. Table 2 shows the experimental results obtained from SCWR of single compounds related to the hydrogen yields and the gas composition at 800 °C, 240 bar and 1.0 L h−1.
Table 2 Experimental results regarding the SCW reforming of single compounds at 800 °C, 240 bar and 1.0 L h−1
Acetic acid (wt%) |
Hydroxyacetone (wt%) |
1-Butanol (wt%) |
Glucose (wt%) |
Product gas composition (vol%) (dry basis) |
Experimental H2 yield (mol/mol) |
Equilibrium H2 yield (mol/mol) |
H2 |
CO2 |
CH4 |
CO |
H2 yields are given as moles of H2 per mole of fed organic compound.
|
2.5 |
|
|
|
40.3 |
40.4 |
19.3 |
0.0 |
1.33 |
3.7 |
5.0 |
|
|
|
20.6 |
45.4 |
34.0 |
0.0 |
0.50 |
3.5 |
7.5 |
|
|
|
19.2 |
43.5 |
36.2 |
1.0 |
0.46 |
3.3 |
10.0 |
|
|
|
17.8 |
45.6 |
36.5 |
0.0 |
0.42 |
3.0 |
12.5 |
|
|
|
17.5 |
46.2 |
35.8 |
0.0 |
0.40 |
2.8 |
15.0 |
|
|
|
16.3 |
45.1 |
35.6 |
2.9 |
0.37 |
2.5 |
|
2.5 |
|
|
56.7 |
31.3 |
12.0 |
0.0 |
3.90 |
6.4 |
|
5.0 |
|
|
52.8 |
33.7 |
13.5 |
0.0 |
3.24 |
6.0 |
|
7.5 |
|
|
49.8 |
33.5 |
16.8 |
0.0 |
2.73 |
5.4 |
|
|
2.5 |
|
54.8 |
24.3 |
20.9 |
0.0 |
4.37 |
10.8 |
|
|
5.0 |
|
51.1 |
25.0 |
23.9 |
0.0 |
3.72 |
9.3 |
|
|
7.5 |
|
41.5 |
25.4 |
33.1 |
0.0 |
2.49 |
7.7 |
|
|
|
2.5 |
58.5 |
34.7 |
6.8 |
0.0 |
8.11 |
11.1 |
|
|
|
5.0 |
52.2 |
36.4 |
11.4 |
0.0 |
6.07 |
10.6 |
|
|
|
7.5 |
50.8 |
37.6 |
11.5 |
0.0 |
5.91 |
9.9 |
4.3.2. Mixtures of organic constituents without glucose.
Acetic acid and 1-butanol may interact with each other to generate acetic acid 1-butyl ester; equally, acetic acid and formed ethanol may produce ethyl acetate. Additionally, more ethylene is produced when acetic acid and 1-butanol are fed simultaneously. Hydroxyacetone interacts with any of the other fed compounds through the formed acetaldehyde. Therefore, it seems that interferences with each other should be quantitatively discovered by applying eqn (7). Thus, while the H2 yield was 3.24 and 3.72 for pure acetol and 1-butanol (5.0 wt%), a mixture of 2.5/2.5 wt% acetol/1-butanol resulted in a H2 yield of 2.12 against the value of 3.48 obtained using eqn (7). Likewise, for the mixture of 5.0/2.5 wt% acetic acid/1-butanol, the experimental H2 yield was 0.64 whereas the computed one was 1.05. Equally, for the mixture of 2.5/2.5/2.5 wt% acetic acid/acetol/1-butanol, the computed value of the H2 yield was 1.79 and the experimental one was 1.23.
4.3.3. Concluding remarks.
As can be observed in Fig. 4, acetic acid may be fed but it could be also produced from glucose and hydroxyacetone. Since acetic acid is hardly reformed, its existence in the medium must slow down the conversion to gases. Likewise, 1-butanol can react with acetic acid to form acetic acid 1-butyl ester, which must suffer a further degradation before converting into gases. Therefore, since it can be produced as an intermediate, acetic acid seems to be present in any mixture and it may be the root of interactions (or one of them), which delays the appearance of the gas phase, thus reducing gas yields regarding cases in which a single compound is fed. Thus, mixtures promote interactions through acetic acid, which worsens the process performance.
4.4. On the equilibrium assumption
The equilibrium is not always closely approached, and to better simulate these cases, an approach to the equilibrium temperature (DT) was used. Thus, the standard Gibbs free energy of each component was evaluated at a temperature different from the reactor temperature, and the equilibrium constant of reactions was calculated at the operating temperature of the reactor minus the approach temperature, since reforming is endothermic. This procedure gives an idea of how far from equilibrium the process is. Fig. 5 shows four cases where the experimental results are compared with simulation results by assuming equilibrium (DT = 0) or an approach to the equilibrium temperature (DT < 0). In the previous paper dealing with single compounds,8 adjusted DT values were between −125 and −225 °C, depending on the individual compound. Now, the values of DT are higher and range from −175 and −275 °C, for most of the tests, which match well with the poorer performance of the SCWR of mixtures in relation to that obtained for separate model compounds. These high values of the approach to the equilibrium temperature are similar to values (−210 °C) found in research studies of gasification.25,26Fig. 5 also depicts the lines that show the equilibrium gas yields once they are adjusted to different values of the approach to the equilibrium temperature. Good agreement between experimental and simulation results can be observed, so the use of a suitable DT value could predict actual gas yields for a known feed composition.
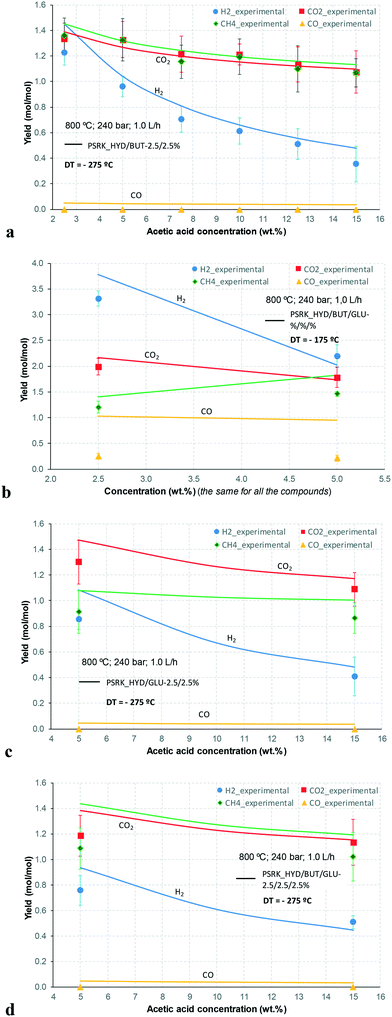 |
| Fig. 5 Effect on the gas yields of the acetic acid concentration (a) for 2.5/2.5 wt% hydroxyacetone/1-butanol, (b) of the glucose concentration for two concentrations of 1-butanol/hydroxyacetone (2.5/2.5/2.5 and 5.0/5.0/5.0 wt%), and of the acetic acid concentration (c) for 2.5/2.5 wt% hydroxyacetone/glucose and (d) for 2.5/2.5/2.5 wt% hydroxyacetone/1-butanol/glucose, at 800 °C, 240 bar and 1.0 L h−1, at different approaches to the equilibrium temperature [H2: blue; CO2: red; CH4: green; CO: orange]. | |
5. Conclusions
The supercritical reforming of mixtures of four model representative compounds of the bio-oil aqueous fraction (acetic acid, acetol (or hydroxyacetone), 1-butanol and glucose, as a precursor of levoglucosan) was experimentally studied. Interactions among glucose, acetic acid, hydroxyacetone and 1-butanol are due to the production of intermediates (and acetic acid seems to be of relevance). The latter are either harder to reform or must further react, thus hindering the reforming and decreasing the gas yields (especially, H2 yields), which were far from equilibrium. The result made evident the existence of interactions, so hydrogen yields (moles H2 per mole organic feed) were lower than those corresponding to the reforming of model compounds separately. A series of probable reaction pathways are proposed and make it possible to understand the interactions among the model compounds when they are fed as a mixture. Once the gases are formed, methane reforming and WGS reaction are the reactions that are likely to occur. The latter is much faster than the former, which explains the high CH4 yields and the low CO yields. If CH4 was reformed, the values of the concentrations and yields of gas products would be very close to those at equilibrium. Therefore, there was no sufficient residence time to reform methane, because this reaction was not fast enough. In future work, these mixtures will be tested using a catalyst to achieve higher gas yields, especially hydrogen yields.
Acknowledgements
The authors thank the Research, Technology and Innovation Centre of the University of Seville (CITIUS) for the aid given in the analyses performed by the X-ray and Microscopy Services. Likewise, Dr. Ma Sales Galletero (University of Valencia) and Dr. Javier Lasobras (University of Zaragoza) are gratefully acknowledged for their assistance with liquid analyses (Mass Spectroscopy Service). Finally, Mr. R. Moriana (University of Seville) is acknowledged for his assistance during the experiments carried out in the bench-scale plant.
References
- T. Karayildirim, J. Yanik, M. Yuksel and H. Bockhorn, Characterisation of products from pyrolysis of waste sludges, Fuel, 2006, 85, 1498–1508 CrossRef CAS.
- D. Yao, C. Wu, H. Yang, Q. Hu, M. A. Nahil, H. Chen and P. T. Williams, Hydrogen production from catalytic reforming of the aqueous fraction of pyrolysis bio-oil with modified Ni–Al catalysts, Int. J. Hydrogen Energy, 2014, 39, 14642–14652 CrossRef CAS.
- R. Xing, V. Lebarbier Dagle, M. Flake, L. Kovarik, K. O. Albrecht, C. Deshmane and R. A. Dagle, Steam reforming of fast pyrolysis-derived aqueous phase oxygenates over Co, Ni, and Rh metals supported on MgAl2O4, Catal. Today, 2016, 269, 166–174 CrossRef CAS.
- F. Bimbela, M. Oliva, J. Ruiz, L. García and J. Arauzo, Hydrogen production via catalytic steam reforming of the aqueous fraction of bio-oil using nickel-based coprecipitated catalysts, Int. J. Hydrogen Energy, 2013, 38, 14476–14487 CrossRef CAS.
- E. Ch. Vagia and A. A. Lemonidou, Thermodynamic analysis of hydrogen production via autothermal steam reforming of selected components of aqueous bio-oil fraction, Int. J. Hydrogen Energy, 2008, 33, 2489–2500 CrossRef CAS.
- C. Pan, A. Chen, Z. Liu, P. Chen, H. Lou and X. Zheng, Aqueous-phase reforming of the low-boiling fraction of rice husk pyrolyzed bio-oil in the presence of platinum catalyst for hydrogen production, Bioresour. Technol., 2012, 125, 335–339 CrossRef CAS PubMed.
- A. Serrera, F. J. Gutiérrez Ortiz and P. Ollero, Syngas methanation from the supercritical water reforming of glycerol, Energy, 2014, 76, 584–592 CrossRef CAS.
- F. J. Gutiérrez Ortiz, F. J. Campanario and P. Ollero, Supercritical water reforming of model compounds of bio-oil aqueous phase: Acetic acid, acetol, butanol and glucose, Chem. Eng. J., 2016, 298, 243–258 CrossRef.
- E. Weiss-Hortala, A. Kruse, C. Ceccarelli and R. Barna, Influence of phenol on glucose degradation during supercritical water gasification, J. Supercrit. Fluids, 2010, 53, 42–47 CrossRef CAS.
- Y. Guo, S. Z. Wang, Y. Z. Wang, J. Zhang, D. H. Xu and Y. M. Gong, Gasification of two and three-components mixture in supercritical water: Influence of NaOH and initial reactants of acetic acid and phenol, Int. J. Hydrogen Energy, 2012, 37, 2278–2286 CrossRef CAS.
- S. N. Reddy, S. Nanda and J. A. Kozinski, Supercritical water gasification of glycerol and methanol mixtures as model waste residues from biodiesel refinery, Chem. Eng. Res. Des., 2016, 113, 17–27 CrossRef CAS.
- A. Kruse and M. Faquir, Hydrothermal biomass gasification – Effects of salts, backmixing, and their interaction, Chem. Eng. Technol., 2007, 30, 749–754 CrossRef CAS.
- A. A. Peterson, F. Vogel, R. P. Lachance, M. Fröling, M. J. Antal Jr. and J. W. Tester, Thermochemical biofuel production in hydrothermal media: A review of sub- and supercritical water technologies, Energy Environ. Sci., 2008, 1, 32–65 CAS.
- T. M. Aida, K. Tajima, M. Watanabe, Y. Saito, K. Kuroda, T. Nonaka, H. Hattori, R. L. Smith Jr and K. Arai, Reactions of d-fructose in water at temperatures up to 400 °C and pressures up to 100 MPa, J. Supercrit. Fluids, 2007, 42, 110–119 CrossRef CAS.
- C. Fushimi, S. Katayama and A. Tsutsumi, Elucidation of interaction among cellulose, lignin and xylan during tar and gas evolution in steam gasification, J. Anal. Appl. Pyrolysis, 2009, 86, 82–89 CrossRef CAS.
- A. A. Peterson, R. P. Lachance and J. W. Tester, Kinetic evidence of the Maillard reaction in hydrothermal biomass processing: Glucose-Glycine interactions in high-temperature, high-pressure water, Ind. Eng. Chem. Res., 2010, 49, 2107–2117 CrossRef CAS.
- F. J. Gutiérrez Ortiz, A. Serrera, S. Galera and P. Ollero, Experimental study of the supercritical water reforming of glycerol
without the addition of a catalyst, Energy, 2013, 56, 193–206 CrossRef.
- W. Buhler, E. Dinjus, H. J. Ederer, A. Kruse and C. Mas, Ionic reactions and pyrolysis of glycerol as competing reaction pathways in near- and supercritical water, J. Supercrit. Fluids, 2002, 22, 37–53 CrossRef CAS.
- A. J. Byrd, R. B. Gupta and K. K. Pant, Hydrogen production from glycerol by reforming in supercritical water over Ru/Al2O3 catalyst, Fuel, 2008, 87, 2956–2960 CrossRef CAS.
- A. J. Byrd, K. K. Pant and R. B. Gupta, Hydrogen production from glucose using Ru/Al2O3 catalyst in supercritical water, Ind. Eng. Chem. Res., 2007, 46, 3574–3579 CrossRef CAS.
- S. N. Reddy, S. Nanda, A. K. Dalai and J. A. Kozinski, Supercritical Water Gasification of Biomass for Hydrogen Production, Int. J. Hydrogen Energy, 2014, 39, 6912–6926 CrossRef CAS.
- F. L. Resende, M. E. Neff and P. E. Savage, Noncatalytic Gasification of Cellulose in Supercritical Water, Energy Fuels, 2007, 21, 3637–3643 CrossRef CAS.
- F. L. Resende, S. A. Fraley, M. J. Berger and P. E. Savage, Noncatalytic Gasification of Lignin in Supercritical Water, Energy Fuels, 2008, 22, 1328–1334 CrossRef CAS.
- A. K. Goodwin and G. L. Rorrer, Conversion of glucose to hydrogen rich gas by supercritical water in a microchannel reactor, Ind. Eng. Chem. Res., 2008, 47, 4106–4114 CrossRef CAS.
- X. T. Li, J. R. Grace, C. J. Lim, A. P. Watkinson, H. P. Chen and J. R. Kim, Biomass gasification in a circulating fluidized bed, Biomass Bioenergy, 2004, 26, 171–193 CrossRef CAS.
- E. Esmaili, N. Mahinpey and C. J. Lim, Modified equilibrium modelling of coal gasification with in situ CO2 capture using sorbent CaO: Assessment of approach temperature, Chem. Eng. Res. Des., 2013, 91, 1361–1369 CrossRef CAS.
Footnote |
† Electronic supplementary information (ESI) available. See DOI: 10.1039/c7re00090a |
|
This journal is © The Royal Society of Chemistry 2017 |
Click here to see how this site uses Cookies. View our privacy policy here.