DOI:
10.1039/C7RA10826E
(Paper)
RSC Adv., 2017,
7, 55269-55275
Metallic 1T-TiS2 nanodots anchored on a 2D graphitic C3N4 nanosheet nanostructure with high electron transfer capability for enhanced photocatalytic performance
Received
30th September 2017
, Accepted 27th November 2017
First published on 5th December 2017
Abstract
Photocatalysis is one of the most promising technologies for solar energy conversion. With the development of photocatalysis technology, the creation of low-dimensional structure photocatalysts with improved properties becomes more and more important. Metallic 1T-TiS2 nanodots with a low-dimensional structure were introduced into environmentally friendly two-dimensional g-C3N4 (2D-C3N4) nanosheets by a solvothermal method. It was found that the ultrathin TiS2 nanodots were uniformly anchored on the surface of the 2D-C3N4. The effective suppression of electron–hole recombination was realized due to the addition of the intrinsic metallic property of 1T-TiS2 in the prepared nanocomposite. The 5 wt% TiS2/2D-C3N4 nanocomposite exhibited the best photocatalytic performance and the degradation rate towards RhB was ca. 95% in 70 min, which showed an improvement of ca. 30% in comparison with 2D-C3N4. The results indicate that the obtained TiS2/2D-C3N4 nanocomposite is a promising photocatalyst for practical applications.
Introduction
With the increasing scarcity of conventional energy resources and the deterioration of the environment, the development and utilization of renewable energy becomes more and more important.1 Solar power can be converted by photocatalysts into chemical energy to degrade pollutants, which has attracted a lot of attention in the past decades.2 Numerous researchers have devoted themselves to creating efficient photocatalysts to take full advantage of the redox ability of photogenerated carriers. TiO2 was reported to be used for hydrogen generation via water splitting under ultraviolet light.3–6 Nevertheless, the challenges of photocatalytic degradation mainly lie in the following two points: (1) the wide light absorption range and (2) the efficient separation of photogenerated electrons and holes.7,8
In recent years, researchers have found the dimension reduction of the photocatalysts can shorten the diffusion length of photogenerated carriers.9–16 Moreover, the introduction of conducting materials has been found to be able to suppress recombination of photogenerated electron (e)–hole (h) pairs of semiconductors, such as some noble metals (Ag, Au and Pt).17–22 Platinum (Pt) with the lowest Fermi level is the most effective accepter of photogenerated electrons for the photocatalytic reaction.23 However, its high material cost makes it uncompetitive for practical applications. Thus, the development of the substitute materials (noble metal-free) of the noble metals is very necessary, but still challenging to date.
Layered transition metal dichalcogenides (TMDs) such as MoS2, WSe2, TaS2 etc., have received much attention owing to their excellent catalytic activity and low cost compared to noble metals.24–30 As a prototype of TMDs, 1T-TiS2 is composed of metal Ti layer sandwiched between two S layers forming edge-sharing TiS6 octahedra with strong covalent forces.3 The adjacent S–Ti–S layers are coupled to each other by weak van der Waals interactions, providing the practical feasibility for exfoliating the bulk TiS2 to ultrathin two dimensional TiS2 nanosheets.31,32 In addition, 1T-TiS2 is a semimetal with excellent in-plane conductivities.33 It is noticeable that conductive 1T-TiS2 can replace the noble metals to be used as the accepter of the photogenerated electrons and improve the separation efficiency of the photoexcited carriers of semiconductors.
Graphitic carbon nitride (g-C3N4), a polymeric semiconductor with a low band gap of ∼2.7 eV, has an appropriate band structure for photocatalysis.34 Two dimensional C3N4 (2D-C3N4) can be prepared according to our previous report.35–37 The two dimensional structure of g-C3N4 can contribute to the separation of photogenerated e–h pairs and then the carriers could handily transfer to the surface to suppress the recombination.38–43 However, the separation efficiency of the photoexcited carriers of 2D-C3N4 are still unsatisfactory in the absence of noble metals. To further improve the photocatalytic activity of 2D-C3N4, the introduction of some conductive materials is an effective method.
Herein, the exfoliated ultrathin TiS2 nanodots were introduced into 2D-C3N4. Anchoring metallic TiS2 nanodots on 2D-C3N4 nanosheets via solvothermal method facilitated the fast transfer of the photogenerated carriers. The high photocatalytic performance of the nanocomposite resulted from the effective suppression of the e–h recombination was tested by degrading Rhodamine B (RhB). In the nanocomposites, uniformly distributed TiS2 nanodots on surface of 2D-C3N4 nanosheets did serve as the accepter of the photogenerated electrons. Additionally, the photocatalytic mechanism was also studied in detail by electron spin resonance (ESR).
Experimental
1. Synthesis of ultrathin TiS2 nanodots
Ultrathin TiS2 nanodots were prepared via liquid phase exfoliation in a co-solvent (acetonitrile/IPA = 19
:
1, by volume). Specifically, 900 mg 1T-TiS2 powder (Sigma-Aldrich) was dispersed in 300 ml co-solvent and the solution was sonicated in an ultrasonic bath at 25 °C for 4 h. Then the mixture was centrifuged at 6000 rpm for 30 min to remove any unexfoliated bulk TiS2. The supernatant was further probe sonicated for another 4 h followed by centrifugation at 10
000 rpm for 30 min. The freeze-dried supernatant was named as TiS2 nanodots.
2. Synthesis of ultrathin g-C3N4 nanosheets
Ultrathin g-C3N4 was synthesized as below. 2 g melamine were calcined at 550 °C for 4 h with 2 °C min−1 heating rate in the muffle furnace. The obtained sample was bulk g-C3N4. Then 400 mg bulk g-C3N4 was ground and heated at 550 °C for ∼30 min in the muffle furnace. After that, the obtained samples were heated at 550 °C for another ∼30 min in the muffle furnace. Finally, the obtained ultrathin g-C3N4 were white.
3. Synthesis of TiS2/2D-C3N4 nanocomposites
The TiS2/2D-C3N4 nanocomposite was prepared by solvothermal method in benzyl alcohol. An appropriate amount of ultrathin TiS2 nanodots and 70 mg 2D-C3N4 was dispersed in benzyl alcohol and sonicated for 20 min, respectively. Then a certain concentration of TiS2 nanodots was mixed with pure 2D-C3N4 and stirred for 2 h. After sonicating the mixture again for 20 min, the suspension was transferred to a stainless-steel autoclave and heated for 4 h at 140 °C. After natural cooling, the solution was washed by ethanol and water twice respectively. The washed powder was then freeze dried and used as catalyst. The TiS2/2D-C3N4 catalysts with different TiS2 content were named as x% TiS2/2D-C3N4, where “x” represent the mass percentage of TiS2 (x = 1, 3, 5, 10 wt%).
4. Material characterization
Scanning electron microscope (SEM) images of 5% TiS2/2D-C3N4 nanodots were taken on a JEOL-6500 scanning electronic microscope. Transmission electron microscope (TEM) and high resolution TEM (HRTEM) images were recorded on a JEOL-2100F at an accelerating voltage of 200 kV. X-ray diffraction (XRD) patterns of TiS2 nanodots and the nanocomposites were performed on D/MAX2500V with Cu-Kα radiation (λ = 1.54056 Å). Raman spectra of TiS2 nanodots, 2D-C3N4 and 5% TiS2/2D-C3N4 nanocomposite were acquired with a RENISHAW in Via Raman Microscope using a 532 nm laser excitation. X-ray photoelectron spectroscopy (XPS) measurements were performed to analyze the presence of TiS2 in the nanocomposites at ambient temperature using PHI Quantera with Al-Kα X-ray source. Shimadzu UV-2450 ultraviolet-visible spectrophotometer was used to collect the UV-vis absorption spectra of TiS2/2D-C3N4 nanocomposites. Composition analysis of as-prepared materials was carried on fourier transforms infrared spectrometer (FT-IR) using Nicolet Nexus 470 spectrometer. The ESR spectra were conducted on a Bruker model ESR JES-FA200 spectrometer. Photoluminescence (PL) spectroscopy experiments were conducted at excitation wavelength 377 nm using Jobin Yvon HORIBA NanoLog spectrofluorometer.
5. Photocatalytic activity measurements
For photocatalytic degradation experiment, the organic dye RhB was used as a model pollutant. In detail, 10 mg samples were added into 50 ml RhB (10 mg l−1) in a Pyrex photocatalytic reactor with a circulating water system to maintain a constant temperature (30 °C). Before irradiation, the suspensions were magnetically stirred for 30 min in the dark to ensure that RhB could reach the absorption–desorption equilibrium on the photocatalyst surface. At a certain time intervals, 3 ml aliquots were sampled and centrifuged to remove the photocatalyst nanoparticles. Then the filtrates were analyzed by recording variations of the absorption band maximum (553 nm) in the UV-vis spectra of RhB using a UV-vis spectrophotometer. The air velocity was 2 l min−1 and the photocatalytic reaction was performed under a 300 W Xe lamp with a 400 nm cutoff filter.
Results and discussions
The TiS2/2D-C3N4 nanocomposites with different content of TiS2 nanodots were prepared by solvothermal method in benzyl alcohol. The morphology of 2D-C3N4, TiS2 nanodots and the as-prepared 5% TiS2/2D-C3N4 nanocomposite were examined by AFM and TEM, as shown in Fig. 1. 2D-C3N4 nanosheets performed a micrometer-scale lateral size and thin thickness about 1–2 nm (Fig. 1a). The size and thickness of TiS2 nanodots were nanometer grade, 5–10 nm and 1–3 nm (Fig. 1b and c), respectively. Ultrathin and small TiS2 nanodots were uniformly anchored on the surface of thin 2D-C3N4 nanosheets without hard aggregations. From the HRTEM image, the lattice with spacing of 0.29 nm of TiS2 nanodots assigned to the (010) planes could be seen on the surface of 2D-C3N4 nanosheets clearly. It demonstrated that the hybridization of 2D-C3N4 nanosheets and TiS2 nanodots did not disturb the crystal structure and morphology of TiS2.
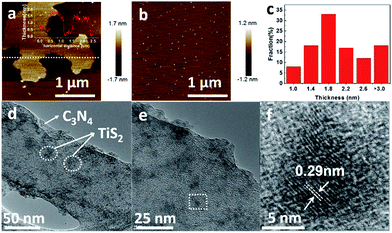 |
| Fig. 1 (a) AFM image and thickness (inset) of 2D-C3N4; (b) AFM image of TiS2 nanodots; (c) the statistics of thickness of TiS2 nanodots; (d and e) TEM images and (f) HRTEM image of 5% TiS2/2D-C3N4 composite. | |
The crystalline structure of the as-prepared TiS2/2D-C3N4 nanocomposites with different content of TiS2 nanodots were further characterized by XRD. In addition to the diffraction peaks at 12.5 and 27.7° attributed to the (100) and (002) crystal planes of 2D-C3N4, respectively,44,45 many other peaks for intralayer crystal planes at 15.5, 34.2, 44.2, 53.9, 57.7 and 65.4° of TiS2/2D-C3N4 nanocomposites were consistent with those of pure few layers of 1T-TiS2.46 Raman spectra of 5% TiS2/2D-C3N4 nanocomposite, 2D-C3N4 and TiS2 nanodots was taken to further demonstrate the presence of TiS2 in the nanocomposites (Fig. 2c). The pure TiS2 nanodots showed a peak at 227 cm−1 assigned to Eg and a peak at 332 cm−1 with a shoulder at 380 cm−1 attributed to A1g vibrational modes of 1T-TiS2.47 However, except for the significant peaks of 2D-C3N4, the peaks of TiS2 were not very clear in 5% TiS2/2D-C3N4 because of the low content of TiS2 in the nanocomposites, which was in agreement with previous publications.48 FT-IR spectra of pure 2D-C3N4 and TiS2/2D-C3N4 nanocomposites were obtained as well. Because of the low detective sensitivity and low content of TiS2 in the nanocomposites, FT-IR spectra of all hybrid only showed typical stretching mode of 2D-C3N4 heterocycles from 1250 to 1700 cm−1 and the vibrational mode of N–H bond at 3147 cm−1 respectively.48
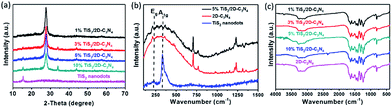 |
| Fig. 2 (a) XRD patterns of TiS2 nanodots and TiS2/2D-C3N4 nanocomposites with different content of TiS2; (b) Raman spectra of 2D-C3N4, TiS2 nanodots and 5% TiS2/2D-C3N4 nanocomposite; (c) FTIR of 2D-C3N4 and TiS2/2D-C3N4 nanocomposites. | |
The chemical states and elemental compositions of TiS2 nanodots, 2D-C3N4 and 5% TiS2/2D-C3N4 nanocomposites were further examined by XPS, as shown in Fig. 3. The C 1s spectra of both 2D-C3N4 and 5% TiS2/2D-C3N4 nanocomposites showed two peaks at 284.7 eV and 288.2 eV assigned to the sp2 C
C bonds and N
C–N2 bonds, respectively (Fig. 3a and c). The N 1s spectrum of 5% TiS2/2D-C3N4 nanocomposite with four peaks in Fig. 3b is similar with that of 2D-C3N4 in Fig. 3d. The peaks at 398.7 eV, 399.8 eV, 401.0 eV and 404.4 eV were ascribed to the sp2-hybridized nitrogen atoms in C
N–C, the tertiary nitrogen, the amino functions carrying hydrogen (C–N–H) and π-excitation, respectively.49 The C 1s and N 1s signals confirmed the presence of 2D-C3N4 in 5% TiS2/2D-C3N4 nanocomposite, which is consistent with the results in FT-IR. The binding energies of Ti 2p peaks (458.5 eV for 2p3/2 and 463.3 eV for 2p1/2) and the weak binding energies of S2− 2p3/2 and 2p1/2 peaks emerging at 161.0 eV and 162.2 eV in 5% TiS2/2D-C3N4 nanocomposite were similar with the peaks in TiS2 nanodots, which agreed well with those of 1T-TiS2.50 It demonstrated the existence of TiS2 nanodots in 5% TiS2/2D-C3N4 composite.
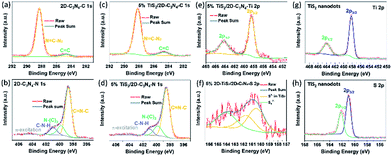 |
| Fig. 3 XPS spectra of 2D-C3N4 and 5% TiS2/2D-C3N4 nanocomposites. C 1s (a) and N 1s (b) of 2D-C3N4; C 1s (c), N 1s (d), Ti 2p (e) and S 2p (f) of 5% TiS2/2D-C3N4 nanocomposite; (g) Ti 2p3/2, 2p1/2 and (h) S 2p3/2, 2p1/2 of TiS2 QDs. | |
The presence of TiS2 nanodots in the nanocomposites was further studied by SEM images and corresponding EDS. The micro-morphology and element mapping of 5% TiS2/2D-C3N4 nanocomposite were shown in Fig. 4. The 2D nanosheets could be seen clearly in Fig. 4a and d. Because TiS2 nanodots and 2D-C3N4 nanosheets were self-assembled together, it was difficult to distinguish them from morphology. From the element mapping of 5% TiS2/2D-C3N4 nanocomposite, it could be seen that TiS2 nanodots were dispersed in the soft nanosheets of 2D-C3N4 uniformly. Ti and S elements of TiS2 nanodots were distributed in the matrix C and N elements of 2D-C3N4 in the nanocomposites, which was consistent with the TEM results. As the content of TiS2 nanodots in composite was 5%, the signals of Ti and S were much lower than those of C and N.
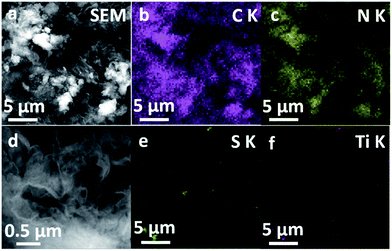 |
| Fig. 4 SEM images and EDX mapping images of 5% TiS2/2D-C3N4 nanocomposites. (a) SEM image; EDX mapping of C (b), N (c), S (e), Ti (f); (d) high amplification of SEM image. | |
The UV-vis absorption of pure TiS2 nanodots, 2D-C3N4 and as-prepared TiS2/2D-C3N4 nanocomposites were shown in Fig. 5a. The curve of 2D-C3N4 displayed a starting absorption at the edge of visible light blending into the ultraviolet, which corresponded to the band gap of 2D-C3N4 at 2.68 eV in Fig. 5b. And TiS2 nanodots could absorb UV and visible light. TiS2/2D-C3N4 nanocomposites performed similar absorption width with 2D-C3N4 nanosheets but much higher absorption value attributed to the light absorption of TiS2, and the absorption intensity at the UV and visible light region were enhanced with increasing content of TiS2 nanodots which indicated that TiS2/2D-C3N4 nanocomposites obtained more photogenerated e–h pairs at 200–700 nm. In order to investigate the influence of TiS2 QDs on the separation efficiency of the photoexcited carriers in TiS2/2D-C3N4 nanocomposites, the PL spectroscopy measurements were carried out for 2D-C3N4 and 5% TiS2/2D-C3N4 nanocomposites. As shown in Fig. 5c, the fluorescence intensity of emission peak at about 460 nm for 5% TiS2/2D-C3N4 nanocomposite was much weaker than that of 2D-C3N4 due to the low recombination rate of photo-generated charge carriers.51 Because of the higher UV-vis absorption and lower fluorescence emission intensity, more photo-generated charge carriers in 5% TiS2/2D-C3N4 nanocomposite were trapped by highly conductive TiS2 nanodots on 2D-C3N4 nanosheets.
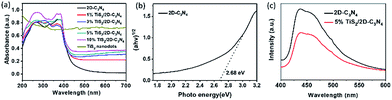 |
| Fig. 5 (a) UV-vis absorption spectra of TiS2 nanodots, 2D-C3N4 and TiS2/2D-C3N4 nanocomposites with different content of TiS2 nanodots; (b) Tauc plot of pure 2D-C3N4 nanosheets from UV vis absorption. (c) Photoluminescence spectra of pure 2D-C3N4 and 5% TiS2/2D-C3N4 nanocomposite. | |
The photocatalytic performance of the nanocomposites was mainly evaluated by photo-degradation of RhB, because RhB is a typical organic dye which is a common water pollutant and could cause long-term environmental toxicity and short-term public health damage. Fig. 6a showed the evolution of the degradation rate of RhB along with time. All the curves had a similar linear downtrend which seemed to be zero-order kinetic process. Hence, the data points were fitted according to the zero-order kinetic process:
where
k is the degradation rate constant, and
b represents the residual composition at 0 min. The
k,
b and
R2 values of the fitted curves for all the samples were listed in
Table 1. According to
R2 values of the samples (higher than 0.982), the fitted curves matched well with the obtained data.
52 So, the degradation behaviour surely followed the zero-order kinetic process. The degradation rate constant of 2D-C
3N
4 was 0.00783 min
−1. Compared with blank 2D-C
3N
4, all the TiS
2/2D-C
3N
4 nanocomposites exhibited higher photocatalytic degradation rate under the same condition. The addition of TiS
2 nanodots to 2D-C
3N
4 enhanced the photocatalytic activity obviously. As the amount of TiS
2 nanodots increase, the degradation rate of RhB was enhanced significantly. 5% TiS
2/2D-C
3N
4 nanocomposite performed the highest degradation rate among all the catalysts (0.0128 min
−1). When the loading amount of TiS
2 nanodots reached to 10 wt%, the photocatalytic degradation of RhB decreased as too much TiS
2 nanodots blocked the photo absorption of 2D-C
3N
4. The as-prepared 10% TiS
2/2D-C
3N
4 has higher
b value than 5% TiS
2/2D-C
3N
4 nanocomposite because of weaker absorption ascribed to too high loadings of TiS
2 nanodots. The highest degradation rate of TiS
2/2D-C
3N
4 nanocomposites was
ca. 95% in 70 min, which got an improvement of
ca. 30% in comparison with that of 2D-C
3N
4. The photocurrent experiment was carried out to explore the charge separation and transfer efficiency (
Fig. 6b). The measurements clearly showed that the introduction of TiS
2 nanodots enhanced the photocurrent of 2D-C
3N
4, in which the 5% TiS
2/2D-C
3N
4 nanocomposite exhibited the highest value. The photocurrent for 5% TiS
2/2D-C
3N
4 was about 2.5 times higher than that given by bare 2D-C
3N
4. The results above suggested that the introduction TiS
2 nanodots enhanced the charge separation greatly and suppressed the recombination of e–h pairs, thus an improving the photocatalytic performance.
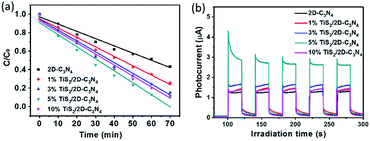 |
| Fig. 6 (a) Photocatalytic activity of RhB in the presence of the 2D-C3N4 and TiS2/2D-C3N4 nanocomposites with different content of TiS2 nanodots under visible light. (b) Transient photocurrent response of pure 2D-C3N4 and TiS2/2D-C3N4 nanocomposites. | |
Table 1 The k, b and R2 value following zero-order kinetic process of catalytic degradation
Sample |
b |
k (min−1) |
R2 |
2D C3N4 |
0.96 |
0.00783 |
0.982 |
1%TiS2/2D-C3N4 |
0.97 |
0.0105 |
0.992 |
3% TiS2/2D-C3N4 |
0.94 |
0.0120 |
0.985 |
5% TiS2/2D-C3N4 |
0.90 |
0.0128 |
0.990 |
10% TiS2/2D-C3N4 |
0.97 |
0.0125 |
0.986 |
Besides the high photocatalytic degradation efficiency, the 5% TiS2/2D-C3N4 nanocomposite showed high stability after five times of cyclic experiments (Fig. 7a). In addition, the nanocomposite still preserved the chemical structure of 2D-C3N4 and TiS2 after five cycles degradation shown by the XRD and FTIR spectra in Fig. 7b and c. The diffraction peak at 27.7° for the (002) crystal plane of 2D-C3N4 and many other peaks at 15.5, 34.2, 44.2 and 57.7° for intralayer crystal planes of TiS2 were consistent with nanocomposite before cycling. FT-IR spectra of TiS2/2D-C3N4 nanocomposites before and after cycling was similar as well.
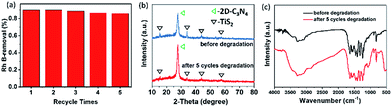 |
| Fig. 7 (a) Cycling runs for the photodegradation of RhB in the presence of 5% TiS2/2D-C3N4 nanocomposite. The chemical and crystal structure of 5% TiS2/2D-C3N4 nanocomposite before and after 5 cycles photodegradation of RhB, XRD pattern (b) and FT-IR spectra (c). | |
As discussed above, the metallic TiS2 nanodots in the system played a crucial role in the migration of electrons excited by the 2D-C3N4 semiconductor, which could efficiently suppress the recombination of e–h pairs. To gain a further insight into the photocatalytic degradation process, ESR analysis was carried out to explore the active radicals using 5,5-dimethyl-1-pyrroline N-oxide (DMPO) as a spin trapping, as shown in Fig. 8. Obviously, the ESR results showed that, when TiS2/2D-C3N4 nanocomposite were employed as photocatalyst, both O2˙− and ˙OH could be generated under visible light irradiation. According to previous reports, the top of valence band (TVB) potential of 2D-C3N4 was 1.79 V vs. RHE.53,54 The band gap was calculated to be 2.68 eV (Fig. 5b), thus the bottom of conduction band (BCB) potential of 2D-C3N4 was −0.89 V vs. RHE. Apparently, the potential energy of the photo-excited electrons at BCB potential was higher than that of O2˙−/O2 (−0.046 eV), thus the electrons possessed the ability to combine with O2 into O2˙−. For the generation of ˙OH, the holes at the TVB of 2D-C3N4 cannot oxidize H2O or OH− into ˙OH due to the lower TVB position in comparison with OH−/˙OH (1.99 eV) and H2O/˙OH (2.38 eV). The ˙OH may be generated by the further reactions of strong reduction O2˙− through an intermediate of ˙OOH:55–57
|
O2˙− + e− + H+ → ˙OOH
| (1) |
|
H2O2 + e− → ˙OH + OH−
| (3) |
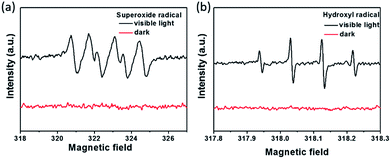 |
| Fig. 8 (a) ESR spectra of DMPO-O2˙− (a) and DMPO-˙OH (b) adducts in TiS2/2D-C3N4 aqueous dispersion systems under visible light irradiation or in the dark. | |
Fig. 9 is a schematic illustration of the synergistic effect of the photocatalytic process. In a typical photocatalytic degradation process, the 2D-C3N4 nanosheets could photogenerated e–h pairs under visible light firstly. Afterwards, the electrons kept at conduction band would be efficiently trapped by metallic TiS2 nanodots as co-catalyst. The high concentration of electrons could react with O2 to form active radicals O2˙−. Due to the strong reduction of the photogenerated electrons, the formed O2˙− also possessed very strong reduction which led to the further reactions and formation of ˙OH radicals through an intermediate of ˙OOH as listed from reaction (1) to (3). The radicals O2˙− and ˙OH were well known as effective radicals for water pollutant treatment. In addition, the hole at valence band of 2D-C3N4 could oxidize pollutant directly. The metallic nature of TiS2 nanodots and the construction of tight interface between the two components were beneficial for the separation and transfer of photo-excited carriers. Therefore, high concentration of photogenerated electrons could converge for photocatalytic reactions at TiS2 nanodots instead of recombination at 2D-C3N4 nanosheets.
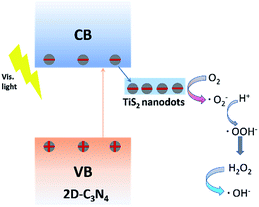 |
| Fig. 9 The degradation of mechanism of as-prepared TiS2/2D-C3N4 composites. | |
Conclusion
We utilized a simple exfoliation synthesis to get ultrathin TiS2 nanodots and the TiS2/2D-C3N4 was synthesized by a temperate solvothermal method. The TiS2 nanodots were tightly anchored on the surface of 2D-C3N4 nanosheets and the inherent metallic nature of 1T-TiS2 improved the photocatalytic degradation activity due to the effective suppression of the e–h recombination and the higher light absorption. Noteworthy, the content of the TiS2 nanodots in the prepared complex played a role in the RhB photocatalytic degradation. The 5% TiS2/2D-C3N4 exhibited the best photocatalytic performance and the degradation rate towards RhB was ca. 95% in 70 min, which got an improvement of ca. 30% in comparison with pure 2D-C3N4 nanosheets. So, the combination of ultrathin metallic TMDs with 2D graphitic C3N4 yields a promising photocatalyst for practical application.
Conflicts of interest
There are no conflicts to declare.
Acknowledgements
This research is financially supported by the National Natural Science Foundation of China (NNSFC Grant No. 51422305, 21476097).
Notes and references
- S. Cao, J. Low, J. Yu and M. Jaroniec, Adv. Mater., 2015, 27, 2150–2176 CrossRef CAS PubMed.
- H. Xu, L. Liu, X. She, Z. Mo, Y. Xu, L. Huang, Y. Song and H. Li, RSC Adv., 2016, 6, 80193–80200 RSC.
- C. M. Fang, R. A. de Groot and C. Haas, Phys. Rev. B: Condens. Matter Mater. Phys., 1997, 56, 4455–4463 CrossRef CAS.
- A. Fujishima and K. Honda, Nature, 1972, 238, 37–38 CrossRef CAS PubMed.
- M. Zhu, C. Zhai, L. Qiu, C. Lu, A. S. Paton, Y. Du and M. C. Goh, ACS Sustainable Chem. Eng., 2015, 3, 3123–3129 CrossRef CAS.
- I. Hwang, I. Jeong, J. Lee, M. J. Ko and K. Yong, ACS Appl. Mater. Interfaces, 2015, 7, 17330–17336 CAS.
- H. Tong, S. Ouyang, Y. Bi, N. Umezawa, M. Oshikiri and J. Ye, Adv. Mater., 2012, 24, 229–251 CrossRef CAS PubMed.
- J. Li, X. Zhang, F. Raziq, J. Wang, C. Liu, Y. Liu, J. Sun, R. Yan, B. Qu, C. Qin and L. Jing, Appl. Catal., B, 2017, 218, 60–67 CrossRef CAS.
- J. Shen, Y. He, J. Wu, C. Gao, K. Keyshar, X. Zhang, Y. Yang, M. Ye, R. Vajtai, J. Lou and P. M. Ajayan, Nano Lett., 2015, 15, 5449–5454 CrossRef CAS PubMed.
- M. Chhowalla, H. S. Shin, G. Eda, L. J. Li, K. P. Loh and H. Zhang, Nat. Chem., 2013, 5, 263–275 CrossRef PubMed.
- Q. Lu, Y. Yu, Q. Ma, B. Chen and H. Zhang, Adv. Mater., 2016, 28, 1917–1933 CrossRef CAS PubMed.
- Y. Sang, Z. Zhao, M. Zhao, P. Hao, Y. Leng and H. Liu, Adv. Mater., 2015, 27, 363–369 CrossRef CAS PubMed.
- S. Yang, Y. Gong, J. Zhang, L. Zhan, L. Ma, Z. Fang, R. Vajtai, X. Wang and P. M. Ajayan, Adv. Mater., 2013, 25, 2452–2456 CrossRef CAS PubMed.
- Y. Zhou, Y. Zhang, M. Lin, J. Long, Z. Zhang, H. Lin, J. C. Wu and X. Wang, Nat. Commun., 2015, 6, 8340 CrossRef PubMed.
- J. Low, S. Cao, J. Yu and S. Wageh, Chem. Commun., 2014, 50, 10768–10777 RSC.
- P. Yang, H. Ou, Y. Fang and X. Wang, Angew. Chem., 2017, 129, 4050–4054 CrossRef.
- V. Subramanian, E. E. Wolf and P. V. Kamat, Langmuir, 2003, 19, 469–474 CrossRef CAS.
- K. Awazu, M. Fujimaki, C. Rockstuhl, J. Tominaga, H. Murakami, Y. Ohki, N. Yoshida and T. Watanabe, J. Am. Chem. Soc., 2008, 130, 1676–1680 CrossRef CAS PubMed.
- S. Sakthivel, M. Shankar, M. Palanichamy, B. Arabindoo, D. Bahnemann and V. Murugesan, Water Res., 2004, 38, 3001–3008 CrossRef CAS PubMed.
- C. Han, Y. Lu, J. Zhang, L. Ge, Y. Li, C. Chen, Y. Xin, L. Wu and S. Fang, J. Mater. Chem. A, 2015, 3, 23274–23282 CAS.
- R.-B. Wei, P.-Y. Kuang, H. Cheng, Y.-B. Chen, J.-Y. Long, M.-Y. Zhang and Z.-Q. Liu, ACS Sustainable Chem. Eng., 2017, 5, 4249–4257 CrossRef CAS.
- M. Sun, J. Hu, C. Zhai, M. Zhu and J. Pan, ACS Appl. Mater. Interfaces, 2017, 9, 13223–13230 CAS.
- X. Pan and Y.-J. Xu, J. Phys. Chem. C, 2013, 117, 17996–18005 CAS.
- V. Nicolosi, M. Chhowalla, M. G. Kanatzidis, M. S. Strano and J. N. Coleman, Science, 2013, 340, 1226419 CrossRef.
- X. Huang, C. Tan, Z. Yin and H. Zhang, Adv. Mater., 2014, 26, 2185–2204 CrossRef CAS PubMed.
- H. Li, J. Wu, Z. Yin and H. Zhang, Acc. Chem. Res., 2014, 47, 1067–1075 CrossRef CAS PubMed.
- Z. Zeng, C. Tan, X. Huang, S. Bao and H. Zhang, Energy Environ. Sci., 2014, 7, 797–803 CAS.
- C. Tan, Z. Zeng, X. Huang, X. Rui, X. J. Wu, B. Li, Z. Luo, J. Chen, B. Chen, Q. Yan and H. Zhang, Angew. Chem., Int. Ed., 2015, 54, 1841–1845 CrossRef CAS PubMed.
- P.-Y. Kuang, Y.-Z. Su, K. Xiao, Z.-Q. Liu, N. Li, H.-J. Wang and J. Zhang, ACS Appl. Mater. Interfaces, 2015, 7, 16387–16394 CAS.
- D. Chu, C. Zhang, P. Yang, Y. Du and C. Lu, Catalysts, 2016, 6, 136 CrossRef.
- J. Chen, S. L. Li and Z. L. Tao, J. Am. Chem. Soc., 2003, 125, 5284–5285 CrossRef CAS PubMed.
- G. Guelou, P. Vaqueiro, J. Prado-Gonjal, T. Barbier, S. Hebert, E. Guilmeau, W. Kockelmann and A. V. Powell, J. Mater. Chem. C, 2016, 4, 1871–1880 RSC.
- U. Gupta, B. G. Rao, U. Maitra, B. E. Prasad and C. N. Rao, Chem.–Asian J., 2014, 9, 1311–1315 CrossRef CAS PubMed.
- W. Cui, J. Li, W. Cen, Y. Sun, S. C. Lee and F. Dong, J. Catal., 2017, 352, 351–360 CrossRef CAS.
- X. She, L. Liu, H. Ji, Z. Mo, Y. Li, L. Huang, D. Du, H. Xu and H. Li, Appl. Catal., B, 2016, 187, 144–153 CrossRef CAS.
- X. She, H. Xu, Y. Xu, J. Yan, J. Xia, L. Xu, Y. Song, Y. Jiang, Q. Zhang and H. Li, J. Mater. Chem. A, 2014, 2, 2563 CAS.
- X. She, H. Xu, H. Wang, J. Xia, Y. Song, J. Yan, Y. Xu, Q. Zhang, D. Du and H. Li, Dalton Trans., 2015, 44, 7021–7031 RSC.
- Q. Han, B. Wang, J. Gao, Z. Cheng, Y. Zhao, Z. Zhang and L. Qu, ACS Nano, 2016, 10, 2745–2751 CrossRef CAS PubMed.
- H. Wang, Y. Su, H. Zhao, H. Yu, S. Chen, Y. Zhang and X. Quan, Environ. Sci. Technol., 2014, 48, 11984–11990 CrossRef CAS PubMed.
- G. Zhang, Z. A. Lan and X. Wang, Angew. Chem., Int. Ed., 2016, 55, 15712–15727 CrossRef PubMed.
- Y. Cui, Y. Tang and X. Wang, Mater. Lett., 2015, 161, 197–200 CrossRef CAS.
- M. Zhu, C. Zhai, M. Sun, Y. Hu, B. Yan and Y. Du, Appl. Catal., B, 2017, 203, 108–115 CrossRef CAS.
- Y. Wang, H. Wang, F. Chen, F. Cao, X. Zhao, S. Meng and Y. Cui, Appl. Catal., B, 2017, 206, 417–425 CrossRef CAS.
- Y. Shang, X. Chen, W. Liu, P. Tan, H. Chen, L. Wu, C. Ma, X. Xiong and J. Pan, Appl. Catal., B, 2017, 204, 78–88 CrossRef CAS.
- T. Y. Ma, Y. Tang, S. Dai and S. Z. Qiao, Small, 2014, 10, 2382–2389 CrossRef CAS PubMed.
- S. Jeong, D. Yoo, M. Ahn, P. Miró, T. Heine and J. Cheon, Nat. Commun., 2015, 6, 5763 CrossRef CAS PubMed.
- S. J. Sandoval, X. K. Chen and J. C. Irwin, Phys. Rev. B: Condens. Matter Mater. Phys., 1992, 45, 14347–14353 CrossRef.
- X. Lu, Y. Jin, X. Zhang, G. Xu, D. Wang, J. Lv, Z. Zheng and Y. Wu, Dalton Trans., 2016, 45, 15406–15414 RSC.
- J. Liu, H. Xu, Y. Xu, Y. Song, J. Lian, Y. Zhao, L. Wang, L. Huang, H. Ji and H. Li, Appl. Catal., B, 2017, 207, 429–437 CrossRef CAS.
- R. J. Toh, Z. Sofer and M. Pumera, J. Mater. Chem. A, 2016, 4, 18322–18334 CAS.
- G. Dong, Y. Zhang, Q. Pan and J. Qiu, J. Photochem. Photobiol., C, 2014, 20, 33–50 CrossRef CAS.
- X. Liu, N. Chen, Y. Li, D. Deng, X. Xing and Y. Wang, Sci. Rep., 2016, 6, 39531 CrossRef CAS PubMed.
- X. She, J. Wu, H. Xu, J. Zhong, Y. Wang, Y. Song, K. Nie, Y. Liu, Y. Yang, M.-T. F. Rodrigues, R. Vajtai, J. Lou, D. Du, H. Li and P. M. Ajayan, Adv. Energy Mater., 2017, 7, 1700025 CrossRef.
- J. Yi, X. She, Y. Song, H. Xu, P. Zhang, Z. Mo, L. Liu, D. Du and H. Li, RSC Adv., 2016, 6, 112420–112428 RSC.
- M. R. Hoffmann, S. T. Martin, W. Choi and D. W. Bahnemann, Chem. Rev., 1995, 95, 69–96 CrossRef CAS.
- S. Yan, Z. Li and Z. Zou, Langmuir, 2010, 26, 3894–3901 CrossRef CAS PubMed.
- Y. Cui, J. Huang, X. Fu and X. Wang, Catal. Sci. Technol., 2012, 2, 1396–1402 CAS.
Footnote |
† Authors contributed equally to this work. |
|
This journal is © The Royal Society of Chemistry 2017 |
Click here to see how this site uses Cookies. View our privacy policy here.