DOI:
10.1039/C7RA10282H
(Paper)
RSC Adv., 2017,
7, 53172-53180
para-Aramid fiber modified by melamine polyphosphate and its flame retardancy on thermoplastic polyurethane elastomer
Received
16th September 2017
, Accepted 4th November 2017
First published on 17th November 2017
Abstract
With the increasing applications of thermoplastic polyurethane elastomer (TPU), the fire risk and smoke hazard caused by TPU have aroused wide attention. At the same time, with the promotion of aramid fiber in industry, the waste and pollution caused by aramid fiber is becoming worse. Herein, para-aramid fiber (AF) is recycled and modified by melamine polyphosphate (MP), and then applied as a flame retardant for TPU. The flame retardant and smoke suppression properties of the TPU composites are determined using the limiting oxygen index (LOI), cone calorimeter test (CCT), smoke density test (SDT) and thermogravimetric/Fourier transform infrared spectroscopy (TG-IR). The LOI test shows that the thermal stability of TPU is further improved by AF-MP. The CCT test shows that AF-MP has a better flame retardant and smoke suppression effect on TPU than pure AF. Remarkably, the pHRR and THR value for the sample with 1.00 wt% content of AF-MP decreased by 38.1% and 24.5% compared with that of the pure AF sample, where the residual mass of AF-MP was more than that of the AF sample. The SDT test shows that AF-MP has a better smoke suppression property in TPU than pure AF, particularly in the absence of a flame. The TG-IR test reveals that AF-MP further promotes the char forming process during combustion. Thus, this investigation presents great insight into the study of reusing fibers and efficient flame retardant polymers.
1. Introduction
TPU is widely used in many fields due to its excellent high tension, high tensile strength, toughness, resistance to aging properties, etc.1,2 However, similar to many other thermoplastics, due to its high flammability and the large amount of high-temperature toxic smoke released during its combustion, TPU has caused great pollution and harm to the environment.3–5 As a result, its applications in many fields are greatly limited. Therefore, the applications of effective flame retardants in TPU are quite important and urgent.6,7
Aramid fiber is a new type of high-tech synthetic fiber with excellent mechanical properties (ultra-high strength, high modulus, high temperature resistance, acid and alkali resistance, light weight, insulation, aging resistance, long life cycle, etc.), and with the gradual understanding of aramid fiber, it has been widely applied in many fields.8–10 At the same time, the waste and pollution caused by aramid fiber is becoming worse. Thus, the rational utilization and recycling of aramid fiber are necessary and significant.11
Aramid fiber is divided into meta-aramid fiber and para-aramid fiber. The main difference between these two types of aramid fibers is the position where the amide bonds with the C atom on the benzene ring.12,13 para-Aramid fiber has better resistance to high temperature and other superior properties than that of meta-aramid fiber. Zhang Chong-geng et al. prepared a flame retardant using a halogen antimony flame retardant and aramid fiber to make an insulting layer in NBR, and the best formula ratio was obtained by testing different contents of halogen antimony flame retardant and aramid fiber.14 Zeng Cui-xia et al. made a blended flame retardant fabric by mixing aramid fiber and other natural fibers (cotton, wool, etc.) in a certain proportion.15 Their research showed that the LOI increased and the mass loss of the blended flame retardant fabric decreased with an increase in the content of aramid fiber. In the field of polymer flame retardants, Chen Xi-lei et al. studied the fire safety of para-aramid fiber in TPU, and their results showed that para-aramid fiber could improve the flame retardancy and smoke suppression property of TPU considerably.16 This has opened a new field for the application of aramid fiber. However, there are some disadvantages with the use of aramid fiber. Aramid fiber is a material that is composed of highly oriented crystalline microregions with some defects and voids. Due to the steric effect of the large benzene ring in its molecular chain, it is difficult for the amide group to react with other atoms or groups. Thus, aramid fiber has poor adhesion with matrices because of its chemical inertia.17,18 In this case, some measures must be taken to reduce the surface orientation or increase the number of active groups on its surface. Only in this way can the bonding strength of the composite can be improved by forming reactive covalent bonds between its groups and the matrix. The methods for the modification of aramid fiber can be divided into groups: physical modification and chemical modification. Both methods achieve the same goal by forming some active center on the fiber surface and then enhancing the interaction between the fiber and matrix.19–21 In previous work, aramid fiber was modified by phosphoric acid and applied as a flame retardant in TPU, and the results showed that the modified aramid fiber had better flame retardancy that pure aramid fiber in TPU.11
As an intumescent flame retardant (IFR), MP not only can be used alone as a flame retardant, but also be used in combination with other flame retardants.22–24 Particularly, MP shows better flame retardancy in the coating field than ammonium polyphosphate (APP).25,26 Mo Xian-zhong et al. studied the preparation of MP and its application in intumescent fire retardant coatings, and their results showed that MP could significantly improve the thermal insulation performance of fire retardant coatings.27 It was also reported that MP had been used as a reinforcing agent with glass fiber to investigate the flame retardancy in PA66, and the results showed that MP could apparently improve the flame retardancy of glass fiber in PA66.25,28,29 Li Hong-xia et al. studied the synergistic flame retardant effect between diethyl phosphate aluminium, MP and zinc borate in TPU, and their results showed that it could promote the char forming process and improve the flame retardancy of TPU.30 In a previous work, AF was modified by phosphoric acid and then added in TPU. Serious tests were carried out and the TPU composites containing modified AF showed better flame retardancy than the TPU with pure AF.11 In this case, another idea can be proposed that there should be better flame retardancy in TPU when AF is modified by MP.
Herein, recycled para-aramid fiber (AF) is modified by MP, and TPU composites are prepared by mixing AF-MP into TPU via a melt blending method. A series of tests are conducted to study the flame retardant and smoke suppression effect of AF-MP on TPU. Subsequently, the flame retardant performance, smoke suppression effect and thermal stability of the samples are characterized via CCT, SDT and TG-IR respectively.
2. Experimental
2.1. Materials
TPU (9380A) was produced by Bayer, German. The basic properties of TPU are as follows: density: 1.11 g cm−3 (ISO1183); hardness: 82A (ISO868); tensile strength: 40 MPa (ISO527-1, -3) and elongation at break: 500% (ISO527-1, -3). para-Aramid fiber (XGPF1203) was supplied by Xiangu High-Tech. Co., Ltd. (Shenzhen, China). The basic properties of AF are as follows: density: 1.470 g cm−3 (ISO1183); short cut fiber length: 3 mm; filament diameter: 12 μm; elastic modulus: 80–120 GPa (ISO527-2) and fracture strength: 19.4–21 cN per dtex (ISO6383-1). Analytical reagent grade MP was obtained commercially.
2.2. Sample preparation
AF was added to washing liquid at a temperature of 95 °C for 2 h to remove grease, dirt and other impurities from the fiber surface. The washing liquid contained a mass concentration of 2 g L−1 sodium carbonate and 1 g L−1 twelve sodium alkyl sulfonate, and the liquor ratio was 1
:
50. Finally, AF was washed with distilled water at a temperature of 50–60 °C to neutral and then dried in a drying oven.
The pre-treated AF was soaked in a saturated solution of MP with a 1
:
20 liquor ratio at 80 °C, and kept stirring until the solution cooled to room temperature. Then, AF was filtered and dried in a drying oven at a temperature of 130 °C for 10 min. The above processes were repeated 2 times. Finally, AF was washed with distilled water at a temperature of 50–60 °C to neutral, and AF-MP was obtained after drying in a drying oven.
The TPU composites were prepared via a melt blending method. TPU was dried in a vacuum oven at 80 °C for 12 h and then placed into a mixer and mixed at a rotation speed of 30 rpm for 3 min at a temperature of 175 ± 5 °C. Then, AF-MP was added to the mixer and mixed for about 10 min to blend the polymer composites homogenously. Finally, the TPU composites were moulded with dimensions of 100 × 100 × 3 mm3 using a plate vulcanizer at a temperature of 175 ± 5 °C. The formulations of TPU composites are presented in Table 1.
Table 1 The formulations of TPU composites
Sample code |
TPU/% |
AF/% |
AF-P/% |
TPU |
100 |
0 |
0 |
AF |
99.000 |
1.000 |
0 |
AF-MP-1 |
99.750 |
0 |
0.250 |
AF-MP-2 |
99.500 |
0 |
0.500 |
AF-MP-3 |
99.000 |
0 |
1.000 |
2.3. Measurements
2.3.1. Scanning electron microscopy (SEM) and energy dispersive spectrometry (EDS). The surface characteristics of the samples were observed using a JEOL JSM 5900LV system for scanning electron microscopy (SEM) (JEOL, Japan) analysis at an accelerating voltage of 5 kV.
2.3.2. Limiting oxygen index (LOI). LOI was determined on an HC-2 oxygen index meter (Jiangning Analysis Instrument Company, China) according to the standard oxygen index test ASTM D2863. The dimensions of the samples were 100 × 6.5 × 3 mm3.
2.3.3. Cone calorimeter test (CCT). The flammability of the samples was measured using a PX-07-007 cone calorimeter device (Fire Testing Technology, UK). Samples with the dimensions of 100 × 100 × 3 mm3 were exposed to a radiant cone at a heat flux of 35 kW m−2.
2.3.4. Smoke density test (SDT). A smoke density test machine (JQMY-2, Jianqiao Co, China) was used to measure smoke characteristics according to ISO5659-2 (2006). Each specimen with dimensions of 75 × 75 × 2.5 mm3 was wrapped in aluminum foil and exposed horizontally to an external heat flux of 25 kW m−2 with or without the application of a pilot flame. Two tests were carried out for each sample.
2.3.5. Thermogravimetric analysis/infrared spectrometry (TG-IR). The thermal stability and thermal decomposition performance of the samples were tested on a thermogravimetric analyzer (DT-50) (Setaram Instrumentation Co., Led., France) at a heating rate of 20 °C min−1 under a nitrogen flow of 60 mL min−1. Furthermore, 10 mg sample was placed in an alumina crucible and the temperature ranged from 40 °C to 700 °C.Analysis of the components of the pyrolysis gas from the TG analyzer was performed using an FTIR spectrometer (170SX) (Shimadzu, Japan) in the wavenumber range of 4000–400 cm−1.
3. Results and discussion
3.1. Scanning electron microscopy (SEM) and energy dispersive spectrometry (EDS)
The SEM-EDS pictures of AF and AF-MP are shown in Fig. 1, which display the surface characteristics at the 10 μm scale. Fig. 1(A) and (B) show the surface characteristics of AF and AF-MP, and Fig. 1(C) and (D) show the elemental distribution in AF and AF-MP. It could be seen from Fig. 1(A) that there is no obvious twining between these fibers, and they are smooth and highly oriented and distributed regularly. In contrast, it could be seen in Fig. 1(B) that the fibers are rougher than pure AF, and they are curved and disorganized. This is because the physical characteristics of AF were changed by MP.
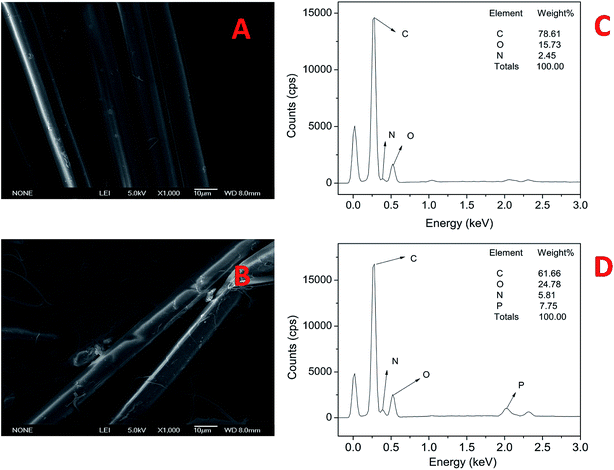 |
| Fig. 1 SEM-EDS of AF (A), (C) and AF-MP (B), (D). | |
Moreover, it could be seen from Fig. 1(C) that C and O are the main elements in AF, and there is a little amount of N element. Compared with Fig. 1(C), it could be seen from Fig. 1(D) that P element and more N element exist in AF-MP. The weight ratio of P was 7.75 wt% and that of N was up to 5.81%, which indicates that MP changed the chemical composition of AF, and the group containing P element and N element was coupled to the surface of AF successfully.
3.2. Limiting oxygen index (LOI)
LOI is defined as the minimum percentage of oxygen in an oxygen–nitrogen mixture that is just sufficient to sustain combustion of the sample after ignition. Higher LOI values make polymers more difficult to burn. The LOI test is widely used to evaluate the thermal stability properties of polymer materials, particularly for screening flame retardant formulations of polymers.2 The LOI results obtained from the TPU composites are presented in Fig. 2. It could be seen obviously that the LOI of TPU is 23.5, and that of AF is 24.5, which is slightly higher than that of pure TPU. However, the LOIs of AF-MP-1, AF-MP-2 and AF-MP-3 are 25.0, 26.5 and 27, respectively, which are much higher than those of TPU.
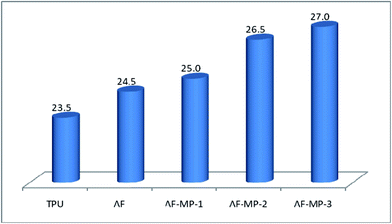 |
| Fig. 2 LOI of the TPU composites. | |
Thus, it could be concluded that AF modified by MP has better flame retardancy in TPU than AF. This is mainly because TPU and AF have the same amide bond and hydrogen bond, and AF can form a large conjugated aromatic structure with TPU.16 It is known that aramid fiber has strong resistance to heat. Thus, the addition of AF increased the viscosity and strength of TPU.31 In this case, when the TPU/AF composites were heated in CCT, the thermal stability of TPU increased, and as a result its LOI increased. Furthermore, as an important intumescent flame retardant (IFR), MP could hydrolyse at low temperature to release some polyphosphoric acid compounds and non-flammable gases, which could reduce the temperature of the polymer and dilute the oxygen concentration. In this way, the LOIs of the AF-MP samples were further improved.
3.3. Cone calorimeter test (CCT)
The cone calorimeter test (CCT) is based on the principle of oxygen consumption. It truly simulates the combustion of polymers in a real fire situation, and thus has great significance in the field of flame retardant materials. Some characteristic CCT data are shown in Table 2.
Table 2 The characteristic data tested by a cone calorimeter
Sample code |
pHRR (kW m−2) |
Mass (%) |
THR (MJ m−2) |
TSR (m2 m−2) |
pSPR (m2 s−1) |
SF (MW m−2) |
TPU |
1364 |
6.2 |
121 |
872 |
0.089 |
1172 |
AF |
655 |
7.8 |
110 |
834 |
0.073 |
718 |
AF-MP-1 |
647 |
8.3 |
95 |
793 |
0.067 |
664 |
AF-MP-2 |
520 |
9.1 |
90 |
769 |
0.065 |
587 |
AF-MP-3 |
447 |
10.8 |
83 |
721 |
0.062 |
530 |
3.3.1. Heat release rate (HRR). The HRR curves of the TPU composites are shown in Fig. 3. It could be seen from Fig. 3 that the HRR of the AF-MP composites was much lower than that of pure TPU, and even lower than that of the AF sample, particularly the pHRR. The pHRR value of pure TPU was 1364 kW m−2, whereas that of the AF sample was 655 kW m−2, and the pHRR values of the AF-MP samples were as follows: 647 kW m−2, 520 kW m−2 and 447 kW m−2. Remarkably, the pHRR of AF-MP-3 decreased by 67.2% compared with that of pure TPU and by 31.8% compared with that of the AF sample, which indicates that AF modified by MP has better flame-retardant ability in TPU than pure AF. This is mainly because AF could promote the char forming process, and furthermore, MP could improve the structure of the carbon layer. The formed carbon layer could be a barrier to stop heat and prevent the polymer from contacting air. As a result, less flammable particulates are released and the HRR decreases. Another phenomenon that could be seen is that there was only one peak for pure TPU, whereas there were two peaks for the AF and AF-MP samples. This is due to the second decomposition of the char residue.
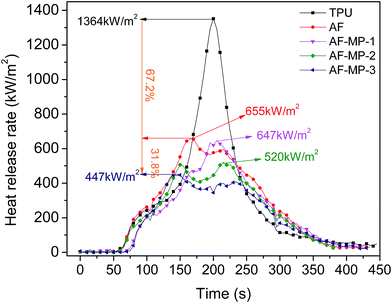 |
| Fig. 3 HRR of the TPU composites at a flux of 35 kW m−2. | |
Thus, it could be concluded that AF improves the thermal stability of TPU and promotes the char forming process due to its large conjugated aromatic structure with TPU. When the samples were heated, the heat resistance of TPU was improved due to the addition of AF. Furthermore, in the process of the formation of the carbon layer, the char became more compact because of the uniform distribution of AF. As a widely applied IFR, MP further promoted the char forming process and improved the structure of the carbon layer. The P element formed some polyphosphoric acid compounds, which catalyzed the carbonization of TPU to generate a condensed carbon layer on the surface of TPU. The carbon layer acted as a barrier from heat, thus reducing the decomposition rate of the underlying materials to form flammable gases, resulting in a decrease in HRR. The N element formed some non-flammable gases, which could dilute the concentration of flammable gases and prevent the polymer from contacting air. Thus, the HRR of the AF-MP samples further decreased compared with that of AF sample, and the flame retardancy of TPU was further improved.
3.3.2. Total heat release (THR). The THR curves of the TPU composites are shown in Fig. 4. It could be seen from Fig. 4 that the THR of the AF sample was lower than that of pure TPU at the end of the combustion. After AF-MP was added to TPU, the THR was even lower than that of the AF sample. The THR of pure TPU at the end of the combustion was 121 MJ m−2; the HRR of the AF sample was 110 MJ m−2, whereas the HRR values of the AF-MP samples were 95 MJ m−2, 90 MJ m−2, and 83 MJ m−2 respectively. With the increase in AF-MP, the THR values got lower and lower, where, the THR of AF-MP-3 decreased by 24.5% compared with that of the AF sample, remarkably. This could be explained by the fact that AF-MP improved the structure of the carbon layer and made the carbon layer more compact. The carbon layer acted as a barrier from heat and air, resulting in a lower THR, which is consistent with the HRR in Fig. 3. Above all, it also illustrates that the flame retardancy of TPU was further improved by AF-MP.
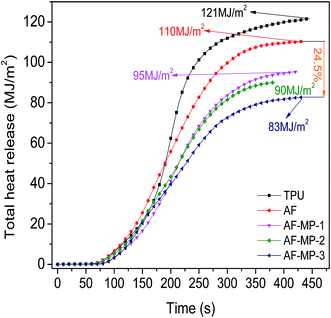 |
| Fig. 4 THR of the TPU composites at a flux of 35 kW m−2. | |
3.3.3. Smoke production rate (SPR). The SPR curves of the TPU composites are shown in Fig. 5. It can be seen that the SPR values of the sample containing AF and AF-MP are much lower than that of pure TPU overall, particularly for the peak value of SPR (pSPR). The pSPR of pure TPU was 0.089 m2 s−1, for the AF sample it was 0.073 m2 s−1, and for the AF-MP samples it was 0.067 m2 s−1, 0.065 m2 s−1 and 0.062 m2 s−1. This is mainly because AF improved the resistance of TPU to heat due to its large conjugated aromatic structure with TPU. Moreover, the existence of AF made the carbon layer more compact, which could separate heat or oxygen from the polymer and prevent smoke particles from being released into the fire. As a result, the SPR of the AF sample was lower than that of TPU. After the modification of AF by MP, MP could promote the char forming process and further improve the structure of the carbon layer, and the carbon layer acted as a barrier from heat and air. This reduced the decomposition rate of the underlying materials to form smoke particulates, resulting in a decrease in SPR, which is consistent with the HRR (Fig. 3) and THR (Fig. 4). Another special phenomenon that can be seen in Fig. 5 is that the SPR values of the AF and AF-MP samples are higher than that of pure TPU after about 210 s, which is a result of the second decomposition of the carbon layer. Overall, it can be concluded that AF-MP slows down the SPR, which is important for people in a fire accident.
 |
| Fig. 5 SPR of the TPU composites at a flux of 35 kW m−2. | |
3.3.4. Total smoke release (TSR). The TSR curves are presented in Fig. 6. It can be seen in Fig. 6 that the TSR of the AF sample is close to that of pure TPU, whereas the TSR of the AF-MP samples is much lower than that of the pure TPU and AF samples. The TSR of pure TPU at the end of the combustion was 872 m2 m−2 and that of AF sample was 834 m2 m−2. In contrast, the TSR of the AF-MP samples was 793 m2 m−2, 769 m2 m−2 and 721 m2 m−2, respectively. With an increase in the content of the AF-MP, the TSR values became lower. Remarkably, the TSR of AF-MP-3 decreased by 17.3% compared with that of pure TPU. This can be explained by the fact that AF-MP promotes the char forming process and further improves the structure of the carbon layer, and as a result, the carbon layer becomes more compact and difficult to decompose. The carbon layer acted as a barrier from heat and air, thus reducing the decomposition rate of the underlying materials to form smoke particulates, which resulted in a lower TSR. This is consistent with the SPR (Fig. 5). Thus, it can be concluded that MP efficiently improved the smoke suppression property of AF in TPU.
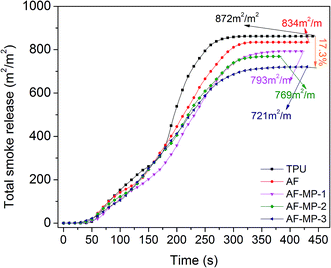 |
| Fig. 6 TSR of the TPU composites at a flux of 35 kW m−2. | |
3.3.5. Smoke factor (SF). The SF curves of the TPU composites are presented in Fig. 7. It can be seen from Fig. 7 that the SF values of the samples containing AF are much lower than that of pure TPU, and the SF values of the samples containing AF-MP are even lower than that of the AF sample. The SF value of pure TPU at the end of the combustion was about 1172 MW m−2: for the AF sample it was about 718 MW m−2, and for the AF-MP samples it was 664 MW m−2, 587 MW m−2 and 530 MW m−2, respectively. Remarkably, the SF value of AF-MP-3 decreased by 54.8% compared with that of pure TPU and 26.2% compared with that of the AF sample. Thus, it can be easily concluded that AF-MP further improves the flame retardancy and smoke suppression property of TPU compared to pure AF, which is consistent with the HRR (Fig. 3) and TSR (Fig. 6).
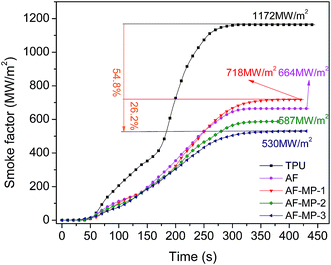 |
| Fig. 7 SF of the TPU composites at a flux of 35 kW m−2. | |
3.3.6. Mass. The residual mass curves of the TPU composites are presented in Fig. 8. It can be seen from Fig. 8 that the residual mass of the AF sample was slightly more than that of pure TPU, whereas the residual mass of the AF-MP samples was much more than that of pure TPU. The residual mass of pure TPU was 6.2%, for the AF sample, it was 7.8%, and for the AF-MP samples, it was 8.3%, 9.1% and 10.8%.
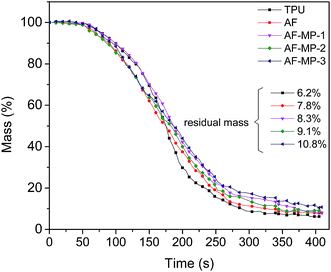 |
| Fig. 8 Mass of the TPU composites at a flux of 35 kW m−2. | |
Therefore, it is not difficult to draw the conclusion that AF-MP plays a more important role in the char forming process than AF because AF-MP improves the structure of the carbon layer from TPU composites. As a result, the carbon layer is more compact to act as a barrier from heat and air, thus reducing the decomposition rate of the underlying materials to form flammable gases and smoke particulates, and enhancing the weight. The above results are in accordance with the HRR (Fig. 3) and TSR (Fig. 6) results.
3.3.7. Digital photographs of the residues. The digital photographs of the char residues after the cone calorimeter test are shown in Fig. 9. As can be seen in Fig. 9, the carbon layer of pure TPU at the end of the combustion was fragile and porous, which indicates that more polymer under the carbon layer decomposed, releasing more heat and smoke particulates. The carbon layer of the AF sample was more integrated and firmer, and there were no obvious pores on its surface, which indicates that AF improved the structure of the carbon layer. In contrast, in the samples with AF-MP, it can be seen that the carbon layer was not only integrated and compact, but also more expansive and firm. This result proves that AF-MP further improved the structure of the carbon layer. The formed carbon layer was more compact and expansive, and acted as an efficient barrier from heat and air, thus reducing the decomposition rate of underlying materials to form flammable gases and smoke particulates. This also resulted in a lower HRR and SPR, and the weight of the char residue was enhanced, which is consistent with the HRR (Fig. 3), SPR (Fig. 5) and mass (Fig. 8) results.
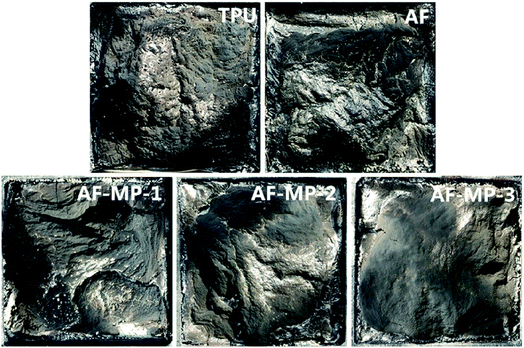 |
| Fig. 9 Digital photographs of the residues after CCT. | |
3.4. Smoke density test (SDT)
A smoke density test was carried out and the results are shown in Fig. 10. Fig. 10(A) presents the luminous flux curves of the TPU composites with flame in the SDT. It can be seen that the luminous flux of pure TPU rapidly decreased in the first 300 s and the lowest luminous flux value was obtained and it slightly increased later. However, the luminous flux of the AF sample decreased slightly slower than that of pure TPU in the first 300 s. The difference between AF and the AF-MP samples was not obvious. When AF-MP was added to TPU, the luminous flux increased after reaching the lowest luminous flux value. This is mainly because MP had changed the composition of the smoke particulates, and when the combustion finished, the particulates sank and remained stable at the bottom.
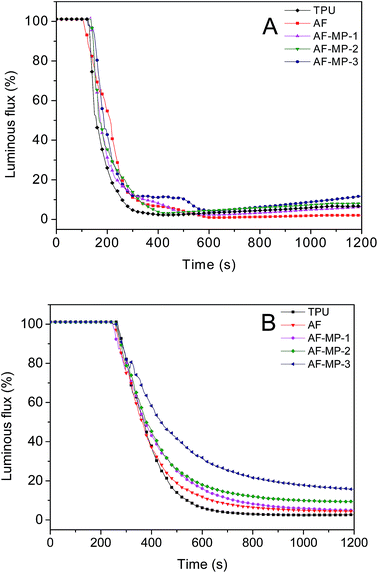 |
| Fig. 10 Luminous flux curves of the TPU composites with flame (A) and without flame (B). | |
Fig. 10(B) presents the luminous flux curves of the TPU composites without flame in the SDT. It can be seen that the luminous flux of TPU rapidly decreased in the first 500 s and the lowest luminous flux value (2.7%) was obtained at the end of the combustion. The luminous flux of the AF sample was close to that of pure TPU in the initial 400 s, and then decreased slowly and reached the lowest luminous flux value (4.5%) at the end of the combustion, which was a little higher than that of pure TPU. This is mainly because AF promotes the char forming process due to its large conjugated aromatic structure with TPU. However, after AF-MP was added to TPU, the luminous flux values decreased more slowly, and with an increase in the content of AF-MP, the luminous flux value increased at the end of the combustion. Remarkably, in the case of AF-MP-3, the lowest luminous flux of 15.7% was achieved, which was much higher than that of the pure TPU and AF samples. This could be explained by the fact that as an IFR, MP further improves the structure of the carbon layer. Furthermore, the carbon layer acted as a barrier from heat, which reduced the decomposition rate of the underlying materials to form smoke particulates, thus resulting in an increase in luminous flux. Thus, the luminous flux values were much higher than those of the AF sample. Therefore, it can be concluded that the smoke suppression property of TPU was further improved by AF-MP.
3.5. Thermogravimetric analysis/infrared spectrometry (TG-IR)
The infrared spectra from the pyrolysis of the TPU composites are presented in Fig. 11. The heating temperature range of the samples was 240–700 °C and the heating rate was 20 K min−1. It can be seen from the infrared spectra of pure TPU in Fig. 11(A) that there is a strong and broad absorption peak located at 2350 cm−1, which was formed by the cleavage of CO2. With an increase in temperature, the intensity of the absorption peak of CO2 increased gradually, reached the maximum at about 450 °C, and then began to decline gradually. When the temperature increased to 520 °C, the absorption peak of CO2 increased and remained stable, which indicates that CO2 was still being released. When the temperature increased to 340 °C, a peak located at 1750 cm−1 appeared, which was attributed to the carbonyl group (C
O) in the TPU soft segment.
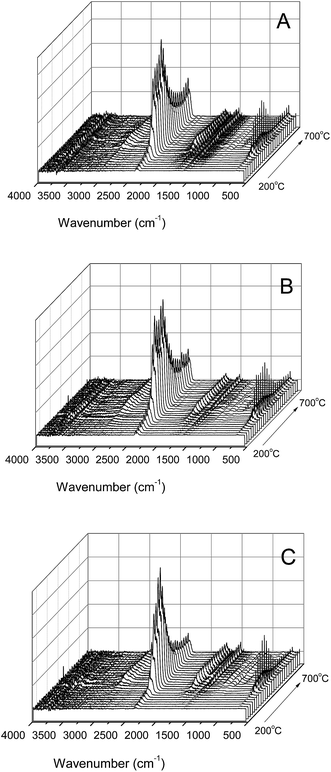 |
| Fig. 11 TG-IR curves of TPU (A), AF (B) and AF-MP-3 (C) samples. | |
It can be seen from the infrared spectrum from the pyrolysis of the AF sample in Fig. 11(B) that the characteristic absorption peak of CO2 located at about 2350 cm−1 is much lower than that of TPU in the initial stage before 360 °C. In addition, the characteristic absorption peak of CO2 for the AF sample was close to that of TPU between 360 °C and 520 °C, but lower than that of pure TPU when the temperature increased from 520 °C to 700 °C. In addition, the C
O absorption peaks located at 1750 cm−1 for the AF sample were slightly higher than those of pure TPU.
It can be seen from the infrared spectrum from the pyrolysis of the AF-MP-3 sample in Fig. 11(C) that the characteristic absorption peak of CO2 located at about 2350 cm−1 was much lower than that of pure TPU before 360 °C, which then increased and became close to that of pure TPU. When the temperature reached about 420 °C the peak started to decrease rapidly and then remained stable, which was much lower than that of the pure TPU and AF samples. Moreover, the C
O absorption peaks located at 1750 cm−1 for the AF-P-3 sample were slightly higher than that of pure TPU and AF.
Therefore, it could be easily concluded that the thermal stability of TPU increased by the addition of AF, and thus the characteristic absorption peak of CO2 in AF was much lower than that of pure TPU at a lower temperature. In addition, with time, the CO2 absorption peak in AF was lower than that of pure TPU at about 520 °C, which is because AF promoted the char forming process due to its large conjugated aromatic structure with TPU. However, in AF-MP-3, as an IFR, MP further promoted the char forming process and improved the structure of the carbon layer. Furthermore, MP could form polyphosphoric acid compounds, which catalyze the carbonization of TPU to generate a condensed carbon layer on the surface of TPU. The formed carbon layer acted as a barrier from heat and air, reducing the decomposition rate of the underlying materials to form flammable gases and smoke particulates, and as a result less CO2 was released. This is consistent with the results obtained by CCT.
4. Conclusion
Since the fire hazard caused by TPU and the pollution caused by aramid fiber are becoming more serious, some measures must be taken to alleviate this situation. Herein, research on the flame retardancy of aramid fiber modified by MP in TPU was carried out. The results show that AF-MP has better flame retardancy and smoke suppression property on TPU than pure AF. Therefore, we provide a new strategy and method to reduce the fire hazard of TPU and the pollution of aramid fiber. This is very significant for the reuse of abandoned resources and the development of green flame retardant polymers.
Conflicts of interest
There are no conflicts to declare.
Acknowledgements
The authors gratefully acknowledge the National Natural Science Foundation of China (No. 51776101, 51206084), the Major Special Projects of Science and Technology from Shandong Province (2015ZDZX11011), the Natural Science Foundation of Shandong Province (ZR2017MB016), and the Project of the State Administration of Work Safety (shandong-0039-2017AQ).
References
- G. Wypych, Handbook of Polymers, 2nd edn, 2016, pp. 686–689 Search PubMed.
- C. Jiao, H. Wang, S. Li and X. Chen, J. Hazard. Mater., 2017, 332, 176–184 CrossRef CAS PubMed.
- D. Tabuani, F. Bellucci, A. Terenzi and G. Camino, Polym. Degrad. Stab., 2012, 97, 2594–2601 CrossRef CAS.
- A. Toldy, G. Harakály, B. Szolnoki, E. Zimonyi and G. Marosi, Polym. Degrad. Stab., 2012, 97, 2524–2530 CrossRef CAS.
- X. Chen, W. Wang and C. Jiao, RSC Adv., 2016, 6, 92276–92284 RSC.
- U. Almeida Pinto, L. L. Y. Visconte, J. Gallo and R. C. R. Nunes, Polym. Degrad. Stab., 2000, 69, 257–260 CrossRef.
- H. Li, N. Ning, L. Zhang, Y. Wang, W. Liang and M. Tian, Polym. Degrad. Stab., 2014, 105, 86–95 CrossRef CAS.
- K. Akato, and G. Bhat, Structure and Properties of High-Performance Fibers, 2017, pp. 245–266 Search PubMed.
- J. K. Fink, High Performance Polymers, 2nd edn, 2014, pp. 301–320 Search PubMed.
- Z. Li, X. Cheng, S. He, X. Shi, L. Gong and H. Zhang, Composites, Part A, 2016, 84, 316–325 CrossRef CAS.
- X. Chen, W. Wang and C. Jiao, J. Hazard. Mater., 2017, 331, 257–264 CrossRef CAS PubMed.
- Z. Sun, S. Shi, X. Hu, X. Guo, J. Chen and H. Chen, Composites, Part B, 2015, 77, 38–45 CrossRef CAS.
- B. L. Deopura and N. V. Padaki, in Textiles and Fashion, 2015, pp. 7–114 Search PubMed.
- C. g. Zhang, H. l. Wang, Q. LI, L. Cong and X. h. Zhang, J. Solid Rocket Technol., 2008, 31, 635–637 CAS.
- C. Zeng, Shanghai Textile Science & Technology, 2008, 37, 47–48 Search PubMed.
- X. Chen, W. Wang, S. Li and C. Jiao, J. Hazard. Mater., 2017, 324, 789–796 CrossRef CAS PubMed.
- J. Chen, Y. Zhu, Q. Ni, Y. Fu and X. Fu, Appl. Surf. Sci., 2014, 321, 103–108 CrossRef CAS.
- R. Gu, J. Yu, C. Hu, L. Chen, J. Zhu and Z. Hu, Appl. Surf. Sci., 2012, 258, 10168–10174 CrossRef CAS.
- R. Sa, Y. Yan, Z. Wei, L. Zhang, W. Wang and M. Tian, ACS Appl. Mater. Interfaces, 2014, 6, 21730–21738 CAS.
- C. X. Wang, M. Du, J. C. Lv, Q. Q. Zhou, Y. Ren, G. L. Liu, D. W. Gao and L. M. Jin, Appl. Surf. Sci., 2015, 349, 333–342 CrossRef CAS.
- M. Xi, Y.-L. Li, S.-y. Shang, D.-H. Li, Y.-X. Yin and X.-Y. Dai, Surf. Coat. Technol., 2008, 202, 6029–6033 CrossRef CAS.
- X. Bai, G. Geng, S. Hu and A. Zhang, Paint Coat. Ind., 2012, 42(6), 64–66 CAS.
- C. Wang, J. Li and P. Ding, J. Anal. Appl. Pyrolysis, 2016, 119, 139–146 CrossRef CAS.
- S. Zhou, Z. Wang, Z. Gui and Y. Hu, Fire Mater., 2008, 32, 307–319 CrossRef CAS.
- U. Braun, B. Schartel, M. A. Fichera and C. Jäger, Polym. Degrad. Stab., 2007, 92, 1528–1545 CrossRef CAS.
- Y. Chen and Q. Wang, Polym. Adv. Technol., 2007, 18, 587–600 CrossRef CAS.
- X. Mo, Z. Liao and C. Gan, J. Funct. Mater., 2004, 35, 1725–1727 Search PubMed.
- Z. Wang, Y. Liu and Q. Wang, Eng. Plast. Appl., 2007, 35(3), 4–7 CAS.
- S. V. Levchik, A. I. Balabanovich, G. F. Levchik and L. Costa, Fire Mater., 1997, 21, 75–83 CrossRef CAS.
- H. Li, L. Zhang, Y. Wang, W. Liang and M. Tian, China Plast. Ind., 2014, 42(4), 76–80 CAS.
- L. Loureiro, V. Henrique Carvalho and S. H. Prado Bettini, Polym. Test., 2016, 56, 124–130 CrossRef CAS.
|
This journal is © The Royal Society of Chemistry 2017 |
Click here to see how this site uses Cookies. View our privacy policy here.