DOI:
10.1039/C7RA10185F
(Paper)
RSC Adv., 2017,
7, 53135-53144
Removal of Cu(II) from aqueous solution using Fe3O4–alginate modified biochar microspheres
Received
13th September 2017
, Accepted 13th November 2017
First published on 17th November 2017
Abstract
Magnetic microspheres (MM) were prepared using calcium alginate (CA) encapsulated biochar (BC) and Fe3O4 as a high-performance green absorbent for Cu(II) removal from aqueous solution. The effects of the initial Cu(II) concentration, initial pH value of the Cu(II) solution and equilibrium contact time were investigated. The results revealed that the adsorption capacity of MM was approximately 3 times higher than that of the magnetic biochar (MBC). The adsorption of Cu(II) by the MM was in good agreement with pseudo-second-order kinetics. The overall orders for fitting the isotherm models are Langmuir > Freundlich for Cu(II). Mechanism studies showed that coordination and ion exchange were the major mechanism for Cu(II) removal by the MM. Moreover, the presence of the magnetic particles in the microspheres allowed easy separation of the material from aqueous solutions. This study provides an effective method for biochar modification.
1. Introduction
Copper is an essential micro-nutrient needed by human beings, animals and plants at low levels, while it is toxic beyond certain limits and can also cause serious environmental issues.1 Copper can be accumulated by living organisms throughout the food chain as a highly toxic and non-biodegradable pollutant, causing adverse effects on humans.2 Adsorption is an effective technology for pollutant removal. However, most commercial adsorbents have limited capability for heavy metal removal while the cost remains as another issue. Biochar is usually generated from incomplete pyrolysis of carbon-rich materials and is considered cost-effective and favorable for heavy metals removal.3
Despite the attractiveness of biochar, one limitation for the wide application is that biochar is difficult to recycle from the treated wastewater. To tackle this, magnetic separation is a promising approach for easy and efficient recovery of solid materials. As a result, magnetically modified biochar has been widely investigated in removal of dyes and heavy metals from aqueous solution.4–6 Chemical co-precipitation of magnetic components and biochar is an easy method to prepare magnetic composite materials.7,8 The magnetic modification can improve the adsorption capacity of the hybrid biochar,7–10 while some reports have found that the efficiency of adsorption by magnetically modified biochar was correlated to its structure.11,12 In this regard, the magnetic modification has a negative impact on the adsorption capacity of biochar with poorly developed structure.11–13
Particularly, magnetic particles on the surface of biochar may impair the adsorption of heavy metals by functional groups (e.g. carboxylic and hydroxyl). Moreover, the surface loaded magnetic particles, as one can imagine, can be decomposed in acidic solutions.
Sodium alginate is a natural polymer, extracted from marine brown algae. It has great biocompatibility and biodegradability and possesses majorly β-1,4-glycosidic linked α-L-mannuronic acid and β-D-guluronic acid.14 Sodium alginate could form three-dimensional gel by the exchange of sodium ions from the β-D-guluronic acid with the divalent cations (e.g. Ca2+), which is widely used as encapsulating compounds and composite materials.15,16 The resulting CA has been widely used to immobilize small particles material, such as nanoporous MCM-41,17 graphene oxide,18 halloysite nanotube,18 activated carbon,19 silica20 and magnetic nanoparticles,21 in order to adsorb heavy metals and dyes from aqueous solutions.
This study aims at providing a better way which can address the drawback of magnetic biochar. A magnetic microsphere (MM) was prepared using CA encapsulated biochar and Fe3O4 for Cu(II) removal from aqueous solution. A series of adsorption experiments were conducted to compare the adsorption ability of MM and the biochars with and without magnetic modification for Cu(II). The adsorption characteristics of Cu(II) and the effects of experimental conditions have been systemically investigated. The mechanism of Cu(II) adsorption on CA/BC–Fe3O4 magnetic microsphere is discussed based on characterization of the materials.
2. Materials and methods
2.1 Materials
Sodium alginate was purchased from Shanghai jingchun Technology Co. Ltd. (Shanghai, China), FeCl3·6H2O, FeSO4·7H2O, CaCl2 and NaOH were purchased from Guangzhou chemical reagent factory (Guangzhou, China), Cu(NO3)2·3H2O and NaNO3 were purchased Aladdin Holdings Group, Cu standard liquid was purchased Shanghai fusheng Co. Ltd. (Shanghai, China). All chemicals with analytical grade were used without further purification.
2.2 Preparation of biochar
Coconut shell was collected from a suburb (Haikou, China), air-dried at 70 °C and ground to pass a 0.074 mm sieve. The obtained powders were used as the feedstock and pyrolyzed under nitrogen conditions in a tube furnace to produce biochar (BC). The pyrolysis temperature was raised to 200 °C at 5 °C min−1 with a further step heating up to 700 °C at 10 °C min−1 and held for 3 hours.22 The biochars were naturally cooled to room temperature and stored in airtight plastic bags.
2.3 Preparation of magnetic biochar
The magnetic biochar (MBC) was synthesized according to a modified co-precipitation method.4,9,10 FeCl3·6H2O (0.006 M) and FeSO4·7H2O (0.003 M) were added to distilled water (150 mL) under nitrogen atmosphere. Biochars (2 g) were added to above mixture and stirred for 30 min. Under vigorous mechanical stirring, NaOH solution (5 M) was added dropwise to adjust the pH to 11. The stirring continued for 1 hour and the suspension was aged at room temperature for 10 hours. The filtrate was separated by a magnet and washed with distilled water, and ethanol (3 times). The obtained magnetic biochars were dried at 50 °C in an air oven.
2.4 Preparation of magnetic particles
Fe3O4 particles were prepared through a modified hydrothermal method.23 FeCl3·6H2O (0.08 M) was dissolved in 300 mL ultra-pure water and stirred for 0.5 hour. FeSO4·7H2O (0.04 M) was dissolved separately in 100 mL ultra-pure water and then slowly added to FeCl3 solution with constant stirring under the protection of nitrogen atmosphere. Thereafter, NaOH (10 M) was added dropwise to above mixture to increase the pH to 11 and stirred for 30 min at 75 °C. The mixture was transferred to a kettle and continued to react at 160 °C for 5 hours to obtain magnetic particles. Finally, the magnetic particles were separated with a magnet and washed with water, ethanol and acetone, and dried in a vacuum oven at 70 °C for 8 hours.
2.5 Preparation of CA/BC–Fe3O4 magnetic microsphere (MM)
The CA/BC–Fe3O4 magnetic microspheres were prepared according to a modified method.24–27 3 g of sodium alginate was dissolved into 150 mL of ultra-pure water. Then 3 g of Fe3O4 was added to sodium alginate solution and vigorously stirred for 2 hours. 6 g of biochars were added into 150 mL of deionized water and stirred for 2 hours. The biochars suspension was slowly dropped into the viscous solution of sodium alginate and stirred continuously to form a homogeneous mixed solution. The obtained suspension was then dropped carefully into CaCl2 solution (0.2 M) to form CA/BC–Fe3O4 magnetic microsphere. The microspheres were kept in CaCl2 solution for 6 hours. The obtained magnetic microsphere were then washed with ultra-pure water (eight times) and separated with a magnet, dried at 60 °C in an air oven. CA microspheres were obtained by dropping a solution composed of 1% (w/v) of sodium alginate into CaCl2 solution (0.2 M). The post-processing methods of CA were the same as those of MM.
2.6 Characterization
The Cu(II) concentration was analyzed using an atomic absorption spectrophotometer (AAS, AA-7000, Shimadzu, Japan). The morphology of samples was investigated with a scanning electron microscopy equipped with (SEM, JSM-7401F, JEOL, Japan). In addition, surface element analysis was also conducted simultaneously with SEM, using energy dispersive X-ray spectroscopy (EDS). Structural and compositional characteristics of the materials were investigated by X-ray diffraction (UItima IV, Rigaku, Japan). X-ray photoelectron spectroscopy(XPS, PHI5000 Versaprobe-II, Ulvac-Phi, Japan) was used to analyze the chemical composition of the magnetic microspheres. The magnetic property was determined using a magnetic property measurement system (7404, LakeShore, USA). The Fourier transform infrared (FTIR) spectra were measured by using Nicolet 6700 infrared spectroscope (Thermo Electro Corp, USA). The thermal stability was analyzed using a TG-DSC instrument (STA 449 F3, Netzsch, USA).
2.7 Adsorption kinetic study
The adsorption experiments of BC, MBC, CA, and MM were carried out at room temperature (25 ± 1 °C). A stock solution of 80 mg L−1 Cu(II) was prepared by dissolving Cu(NO3)2 in a 0.01 mol L−1 NaNO3 solution as a back-ground electrolyte at pH 5.22 pH value of the solutions was adjusted using either 0.1 M HNO3 or 0.1 M NaOH solutions. 0.1 g of the biochars or magnetic biochars was introduced into 50 mL of Cu(II) solution in conical flasks. The flasks were placed into an incubator shaker and shaken at a constant speed (160 rpm) for a certain period of time (10 min to 32 h). After shaking, the biochars and the magnetic biochars were filtered and the concentrations of Cu(II) in the filtered solutions were analyzed using a flame atomic absorption spectrometer.28 A certain amount of the MM or CA were introduced into 500 mL of Cu(II) solution in a beaker under magnetic stirring. 1 mL of Cu(II) solution was withdrawn at different times and tested after dilution.29 All the results were obtained by taking an average of three specimens. The kinetic experiment methods for all types of adsorbents are reasonable,30–32 which can accurately reflect their adsorption kinetic characteristics. The adsorption capacity of Cu(II) at time t (qt) was then calculated using eqn (1). |
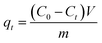 | (1) |
where C0 (mg L−1) is the initial Cu(II) ion concentration; Ct (mg L−1) is the Cu(II) ion concentration at time t; V is the volume (L) of Cu(II) ion solution and m is the dry weight (g) of the adsorbent used.
2.8 Adsorption isotherm study
The BC, MBC, CA, and MM were respectively introduced into different concentrations (40–300 mg L−1) of Cu(II) solution at room temperature (25 ± 1 °C) in a 0.01 mol L−1 NaNO3 solution as a back-ground electrolyte and shaken at a constant speed (160 rpm) for 24 h.33 The quantification method of Cu(II) is the same as the kinetic study. All the results were obtained by taking an average of three specimens. The equilibrium adsorption capacity of Cu(II) (qe) was calculated using eqn (2). |
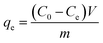 | (2) |
where C0 (mg L−1) and Ce are the initial and equilibrium concentrations of Cu(II) ions, respectively; V is the volume (L) of Cu(II) solution and m is the dry weight (g) of adsorbent used.
2.9 Desorption experiment
The reusability of MM was evaluated using consecutive adsorption–desorption cycles.34 The adsorption experiments were repeated by using the same MM. 0.1 g of metal-loaded MM was shaken in the desorbing agent (HNO3 100 mL of 0.1 mol L−1) in a 250 mL Erlenmeyer at 160 rpm in a shaker for 120 min at room temperature.16 The concentration of Cu(II) in the acidic solution was measured using AAS. All the results were obtained by taking an average of three specimens.
3. Results and discussion
3.1 Characterization of materials
3.1.1 SEM analysis. The biochar (BC) showed a clear porous structure while magnetic biochar (MBC) was covered by ferroferric oxide on the surface (Fig. 1A and B). In the latter case the original porous structure of BC was shielded.
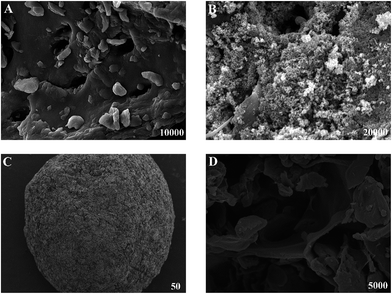 |
| Fig. 1 SEM images of (A) BC, (B) MBC, (C) the outside surface of MM, (D) the section of MM. | |
The SEM images of the surface and section of MM are shown in Fig. 1C and D. Biochar and Fe3O4 were at intervals imbedded in three-dimensional network of MM. The surface area of MM is 12.18 m2 g−1, which is microporous.
3.1.2 XRD analysis. X-ray diffraction (XRD) is an effective method to confirm the existence of Fe3O4 in composites. Fig. 2 shows the XRD patterns of prepared Fe3O4 nanoparticles (a), magnetic biochar (b) and MM (c). The diffraction peaks at 2θ = 30.1°, 35.5°, 43.1°, 53.5°, 57.0°, 62.6°, and 74.0° are assigned to the (2 2 0), (3 1 1), (4 0 0), (4 2 2), (5 1 1), (4 4 0), and (5 3 3) planes, respectively, which agree well with the database of Fe3O4 standard card (JCPDS no. 65-3107).35 No impurity peak is observed in the XRD pattern, which indicates that the Fe3O4 particles are highly crystalline cubic spinel structure.36,37
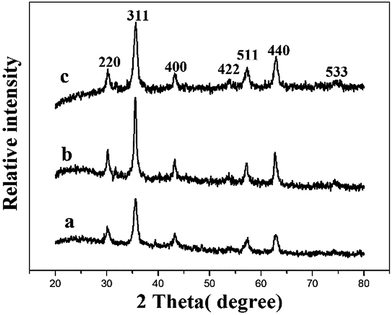 |
| Fig. 2 XRD pattern of Fe3O4 nanoparticle (a), magnetic biochar (b) and magnetic microsphere (c). | |
3.1.3 Magnetic properties. The hysteresis loops of Fe3O4 nanoparticle (a) and magnetic microsphere (b) are shown in Fig. 3. There were no remanence or coercivity, which indicated that the adsorbents exhibited typical superparamagnetic behavior.38,39 The result showed that the maximum saturation magnetization of Fe3O4 and MM were 60.8 emu g−1, 11.75 emu g−1 respectively. Thus, the MM can be separated readily between the liquid and solid phase by using a magnet.34
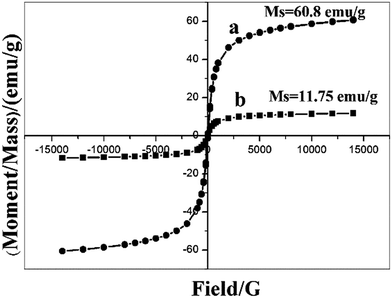 |
| Fig. 3 The magnetization curve of Fe3O4 nanoparticle (a) and magnetic microsphere (b). | |
3.1.4 Thermal analysis. Thermogravimetric analysis was used to assess the thermal stability of CA and MM. CA had three stages of mass loss as shown in Fig. 4. The initial mass loss, from room temperature to 180 °C, was attributed to the release of crystal water and the moisture evaporation.30 The second step for degradation of CA appeared around 180–440 °C, which might be associated with the fracture of glycosidic bonds, decarboxylation, decarbonylation and dehydration of alginate.40 The third step was situated at 440–710 °C, resulting from the further thermal degradation of formed residues.29,41 The MM also had three stages of mass loss and the TG curve trend was similar to CA. The main difference is that the second step of degradation for MM appeared around 230 °C, which is higher than CA about 180 °C. This result was likely attributed to the additional energy required for bond cleavage after the addition of biochar and Fe3O4. The reason might be hydrogen bonds were formed between the hydroxyl group and the carbonyl group or Fe–O group.42 The results of TG showed that the thermostability of MM was more stable than that of CA.
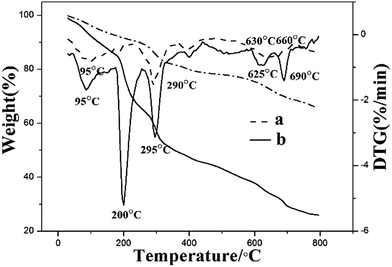 |
| Fig. 4 TG curves of magnetic microsphere (a) and calcium alginate (b). | |
3.2 Effect of pH on adsorption and stability
The effect of pH on the adsorption capacity of MM was investigated. The adsorption experiments were carried out at an initial Cu(II) concentration of 60 mg L−1 in 0.01 mol L−1 NaNO3 solution as a back-ground electrolyte. This study was carried out in a pH range from 2 to 6 since Cu(II) ions may start to precipitate above pH 6.3 All the results were obtained by taking an average of three specimens. When pH increased, the sorption capacity of Cu(II) increased quickly (Fig. 5A). This can be explained by the fact that at the lower pH, more protons (H+) were characterized by high mobility and competed with the metal ions for the active sites on the adsorbents. When increasing the pH, the concentration of H+ ions decreased, resulting in more Cu(II) absorbed.43 The pH value of the solution increased significantly after the adsorption of Cu(II). The main reason could be that the alkali metal oxide on biochar dissolved in acid solution.28 In order to enhance the accuracy of the experiment, pH = 5 was chosen as the optimum experiment condition.44 After the adsorption, Fe3O4 decomposition rate was calculated using eqn (3). |
 | (3) |
where S is Fe3O4 decomposition rate, Ce (mg L−1) is the final concentrations of Fe ions, MFe and MFe3O4 are the molecular weight of Fe and Fe3O4, V is the volume (L) of solution, and m is the weight (mg) of Fe3O4 in adsorbents used. The Fe3O4 content of CA/BC–Fe3O4 (1
:
2
:
1) magnetic microsphere is about 25% of the microsphere. The Fe3O4 decomposition rate of magnetic biochars was analyzed using the same methods. The magnetic biochars was disposed by nitric acid and the total content of Fe3O4 was measured. Fig. 5B showed that the Fe3O4 decomposition rate of MM was significantly less than those of MBC with pH lower than 3. Therefore, MM has high chemical stability than MBC in acidic solution.
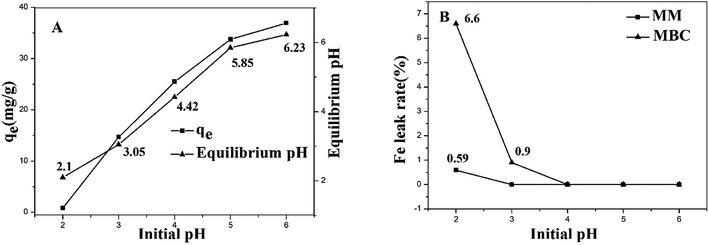 |
| Fig. 5 Effect of pH on the adsorption of Cu(II) by MM (A) and Fe decomposition rate in the solution (B). | |
3.3 Kinetics adsorption experiments
The kinetic behavior of the Cu(II) ion removal by different adsorbents used in this work was investigated by using the dynamic data. Pseudo-first-order kinetic model and pseudo-second-order kinetic model were applied to deal with the data, which are described in eqn (4) and (5).17,45 The results for non-linear curve fitting to the dynamic data were shown in Fig. 6. |
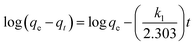 | (4) |
|
 | (5) |
where, qt and qe are the amounts of Cu(II) ions removed per unit mass of adsorbent in mg g−1 at an arbitrary contact time t (s) and at equilibrium stage. k1, k2 is the pseudo-first-order kinetic constant and pseudo-second-order kinetic constant expressed in min−1, g mg−1 min−1, respectively.
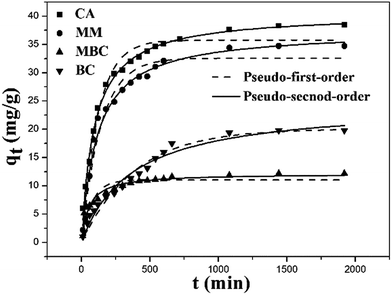 |
| Fig. 6 Kinetic adsorption plots of Cu(II) by CA, MM, MBC and BC. | |
The kinetic model parameters as well as correlation coefficient (R2) for each adsorbent are included in Table 1.
Table 1 Kinetics parameter coefficients for Cu(II) adsorption onto BC, MBC, MM and CA
Sample |
Pseudo-first-order model |
Pseudo-second-order model |
qe,cal |
k1 (10−3) |
R2 |
qe,cal |
k2 (10−4) |
R2 |
BC |
20.08 |
2.57 |
0.9724 |
24.63 |
1.1 |
0.9770 |
MBC |
11.07 |
13.23 |
0.8691 |
12.17 |
15.5 |
0.9497 |
MM |
32.57 |
7.09 |
0.9644 |
37.49 |
2.34 |
0.9811 |
CA |
35.77 |
8.32 |
0.9677 |
40.51 |
2.68 |
0.9934 |
It can be seen that the correlation coefficients (R2) for BC was nearly comparable to pseudo-first-order equation (0.9724) and pseudo-second-order equation (0.9770) model. The adsorption capacity obtained from pseudo-second-order equation fitting values was consistent with the experimental result, which suggested that the rate limiting step was governed by diffusion while the chemical adsorption also played a crucial role.46 The main reason is due to the porous nature of biochar.
The pseudo-second-order equation did describe the adsorption results of Cu(II) onto MBC. The correlation coefficients (0.9497) for MBC was superior compared to pseudo-first-order equation (0.8691) indicating that the chemisorption is the rate-controlling step.31 The main reason is that the surface of biochar was covered by ferroferric oxide, which shielded the porous structure of biochar.
The correlation coefficients of the pseudo-second-order kinetic model for MM and CA were 0.9811 and 0.9934. They are higher than the correlation coefficient derived from the pseudo-first-order model for MM (0.9644) and CA (0.9677). In addition, the adsorption capacity obtained from pseudo-second-order equation fitting values was consistent with the experiment result. All these results highlighted the chemisorption rate-controlling mechanism.47
The data showed that the kinetic constant of MBC was the highest. This could be the fact that the absorption was mainly happening on the surface of MBC. The kinetic constant of MM is higher than that of BC, indicating that MM has improved the adsorption rate of biochar. The adsorption kinetic constants of MM, CA and BC are relatively lower than MBC. The reason could be that the Cu(II) ion was gradually diffused to the interior of MM, CA and BC. This process needed more time.
3.4 Isotherms adsorption experiments
The adsorption isotherms were studied using the Langmuir and Freundlich isotherm models. The Langmuir isotherm model is described as eqn (6).18 |
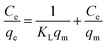 | (6) |
where, Ce (mg L−1) is the concentration of Cu(II) ions at equilibrium. qm (mg g−1) is the Langmuir adsorption maximum. KL is the coefficient of distribution of the adsorption. qe is the amount of Cu(II) ions removed per unit mass of adsorbent in mg g−1 at equilibrium stage.
The Freundlich isotherms model is described as eqn (7).48
|
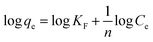 | (7) |
KF is the coefficient of distribution of the adsorption.
The Langmuir and Freundlich isotherms for all types of adsorbents are shown in Fig. 7. The results showed that the Cu(II) ion adsorption increases rapidly when a low initial Cu(II) ion concentration was used and then gradually reaches a maximum with increased Cu(II) ion concentration.
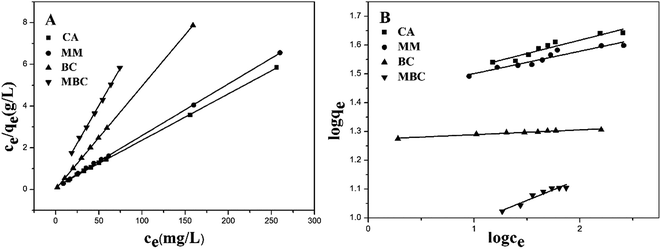 |
| Fig. 7 Adsorption isotherms of Langmuir (A) and Freundlich (B) equations for the adsorption of Cu(II) ion by CA, MM, BC and MBC. | |
The isotherms model parameters as well as the correlation coefficient (R2) for each adsorbent are reported in Table 2.
Table 2 Isotherm parameters of Cu(II) sorption onto BC, MBC, MM and CA
Sample |
Langmuir |
Freundlich |
qm |
KL |
R2 |
1/n |
KF |
R2 |
BC |
20.28 |
2.0342 |
0.9999 |
0.0162 |
18.7283 |
0.9608 |
MBC |
13.87 |
0.1680 |
0.9987 |
0.1477 |
6.9087 |
0.9226 |
MM |
40.42 |
0.2168 |
0.9996 |
0.0775 |
26.5216 |
0.9097 |
CA |
44.98 |
0.1602 |
0.9998 |
0.0730 |
26.9649 |
0.9086 |
As shown in Table 2, the correlation coefficients R2 of the Langmuir model adsorption isotherm plots are high, 0.9999, 0.9987, 0.9996 and 0.9998 for the BC, MBC, MM and CA, respectively. The R2 suggest that the Langmuir model fits the adsorption data well. The reason may be due to the homogeneous nature of active sites on the adsorbents, a monolayer adsorption occurred between the adsorbents and Cu(II) ions.20,49 The qm value of the MBC is determined to be 13.87 mg g−1, which is lower than that of biochar. Again, the surface of MBC covered with ferroferric oxide could impair the adsorption of heavy metals by functional groups in the biochar.
Table 3 shows the specific surface area, pore volume and average pore diameter of MM and CA.
Table 3 Physical properties of the MM and CA
Material |
BET Surface Area (m2 g−1) (m2 g−1) |
Pore volume (cm3 g−1) |
Average pore diameter (nm) |
MM |
12.18 |
0.036 |
10.06 |
CA |
2.72 |
0.009 |
3.14 |
It turned out that the BET surface area, pore volume and average pore diameter of MM are higher than that of CA, which is expected to be advantageous for metal ions diffusion (e.g. Cu2+ in this study). In addition, the combination of MM largely increases the colloidal stability of biochar and thus avoids the agglomeration problem.
When biochars and Fe3O4 were encapsulated in CA, the qm increased to 40.42 mg g−1. It is closer to the value of CA in the previous literature (at 42.7 mg g−1) and those in this study (at 44.98 mg g−1).30 Due to the content of CA in CA/BC–Fe3O4 (1
:
2
:
1) magnetic microsphere is only 25%, it appears a synergistic effect between biochar and Fe3O4 in CA, which enhances the maximum adsorption capacity of Cu(II) ion.
The estimated adsorption cost required by the biochars is about 19% as much as that by the CA.50 Therefore, the obtained MM is a low-cost and high efficiency adsorbent for Cu(II) removal from aqueous solution.
3.5 Comparison with other adsorbents
The adsorption capacity (qm value) for Cu(II) on MM is comparable with reported adsorbents as shown in Table 4. It can be seen that MM is suitable and promising for the removal of Cu(II) from aqueous solutions since it has a relatively high adsorption capacity.
Table 4 Comparison of various adsorbents for copper removal from water
Adsorbents |
pH |
Concentration range (mg L−1) |
Qmax (mg g−1) |
Ref. |
Amino modification biochar |
5 |
10–300 |
16.13 |
51 |
KMnO4 modified biochar |
5 |
2–250 |
12.3 |
52 |
Chitosan magnetic nanoparticles |
5 |
10–2000 |
21.5 |
53 |
Multi-walled carbon nanotubes |
5 |
10–30 |
12.34 |
54 |
Chitosan-montmorillonite composite |
5 |
2–100 |
34.9 |
55 |
Graphene oxide aerogel |
6 |
50–75 |
19.65 |
56 |
Sodium alginate magnetic nanocomposite |
7 |
50 |
18.11 |
57 |
Surfactant-modified hydroxyapatite/zeolite composite |
6 |
10–60 |
38.1 |
58 |
Alginate/biochar magnetic microspheres |
5 |
40–300 |
40.42 |
This study |
3.6 Adsorption mechanism
3.6.1 FTIR analysis. FTIR is used to determine the molecular interactions and analyze functional groups of MM before and after Cu(II) adsorption. In Fig. 8, for the magnetic microsphere a stretching vibration peak of O–H at 3409.53 cm−1, an asymmetric stretching peak of COO− at 1610.66 cm−1,15 a bending vibration peak of CH2 at 1425.34 cm−1,30 and a stretching vibration peak of Fe–O at 578.07 cm−1 were observed.59 The peaks between 1082.72 cm−1 and 1034.69 cm−1 are the stretching vibrations of C–O–C and Si–O.28,60 The FTIR spectra of MM after Cu(II) adsorption showed that some adsorption peaks generated slight displacements. The O–H, COO−, Fe–O, C–O–C and Si–O wavelengths after Cu(II) adsorption were longer to a certain extent than those before Cu(II) adsorption.61 This result may be attributed to functional groups coordinated to Cu(II).62
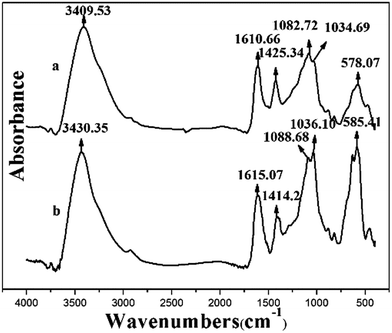 |
| Fig. 8 FTIR of MM before (a) and after (b) Cu(II) adsorption. | |
3.6.2 SEM-EDS analysis. SEM-EDS patterns of MM before Cu(II) adsorption (a), the surface (b) and section (c) of MM after Cu(II) adsorption are shown in Fig. 9. The SEM-EDX studies revealed that the weight% of Ca(II) (8.77 to 2.40, 0.78) ions in MM decreased after loading Cu(II) onto MM. Due to the MM was uneven, the metal content in different parts of MM varied slightly. However, it is still clear that the weight% of Ca(II) decreased significantly, which indicated Cu(II) exchanging Ca(II) happened on the MM.63 The weight% of Cu(II) on the surface and section of MM are 10.65% and 14.54% respectively, which show that Cu(II) ions are relatively homogenously adsorbed on the surface and internal of MM.
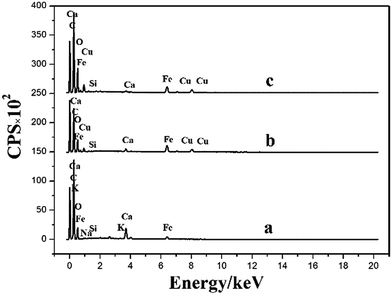 |
| Fig. 9 SEM-EDS patterns of MM before Cu(II) adsorption (a), the surface (b) and section (c) of MM after Cu(II) adsorption. | |
3.6.3 XPS analysis. Fig. 10A showed the typical XPS wide scan spectra of MM before and after Cu(II) adsorption. A new peak appeared after Cu(II) adsorption, which is in agreement with Cu(II) standard data.62 In addition, Ca(II) ions in MM were reduced obviously after Cu(II) adsorption, which is in accordance with the result of SEM-EDS. Fig. 10B and C showed the Cu 2p spectrum of Cu(II)-loaded MM and MBC. The peaks at 932, 932.5 eV and 951.8, 952.4 eV could be ascribed to Cu 2p3/2 and Cu 2p1/2, respectively. The binding energies of Cu 2p3/2 and Cu 2p1/2 were centered at 934.1 and 952.55 eV, respectively.64,65 A significant shift for Cu 2p to low binding energies was observed after Cu(II) adsorption onto MM and MBC, suggesting that coordination or ion exchange reaction occurred between Cu(II) and MM or MBC. Fig. 10D showed the Fe 2p spectrum of Cu(II)-loaded MM. The peaks at 710.5 and 723.58 eV could be ascribed to Fe 2p3/2 and Fe 2p1/2, respectively. The binding energies of Fe 2p3/2 and Fe 2p1/2 for Fe3O4 were centered at 711.1 and 724.8 eV, respectively.66 A significant shift for Fe 2p to low binding energies was also observed after Cu(II) adsorption onto MM, suggesting that coordination reaction occurred between Cu(II) and Fe3O4.
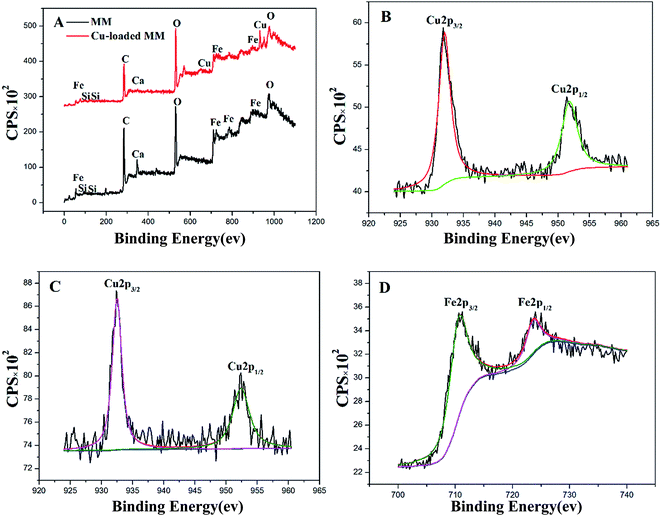 |
| Fig. 10 XPS wide scan spectra of MM and Cu-loaded MM (A), Cu 2p for MM after Cu(II) adsorption (B), Cu 2p for MBC after Cu(II) adsorption (C), Fe 2p for MM after Cu(II) adsorption (D). | |
3.6.4 XRD analysis. XRD pattern of biochar before (a) and after (b) Cu(II) adsorption are shown in Fig. 11. The diffraction peaks at 2θ = 28.3°, 40.5°, 50.1°, 58.6°, 66.3° and 73.7° are assigned to the (2 0 0), (2 2 0), (2 2 2), (4 0 0), (4 2 0) and (4 2 2) planes, respectively, which agree well with the database of KCl standard card (JCPDS no. 41-1476).67 The diffraction peaks at 2θ = 22.0° and 42.0° are assigned to the (2 0 0) and (4 2 2) planes, respectively. The angular position of the diffraction line corresponded to the amorphous structure SiO2, in accordance with the data contained in the database JCPDS-ICDD.68 The XRD pattern of loaded Cu(II) on biochars did not show new peaks, indicating that the precipitation reactions did not occur on the surface of the biochars. The mechanisms responsible for Cu(II) ion sorption by biochars are surface interactions (e.g. ion exchange, coordination) and formation of precipitates with inorganic components.1,3 Therefore, copper removal by biochar should be controlled by surface interactions. Fig. 11 showed some peaks of the biochar disappeared after absorption. This result may be attributed to some inorganic salts (e.g. KCl) dissolved in water in the process of adsorption.
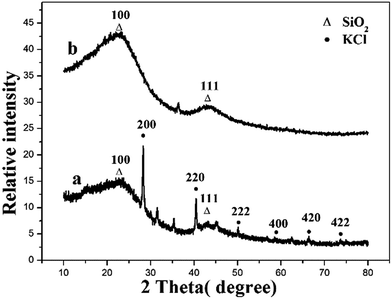 |
| Fig. 11 XRD pattern of biochar before (a) and after (b) Cu(II) adsorption. | |
3.7 Proposed mechanism
The difference of magnetic microsphere before and after Cu(II) loading has been distinguished by FTIR, SEM-EDS and XPS. The sorption mechanism is proposed in Fig. 12. The functional groups (Fe–O, O–H, Si–O and COO−) played a key role in the removal. The nature of Cu(II) abstraction took place through the ion exchange between Ca(II) and Cu(II) as well as the formation of coordination complex.
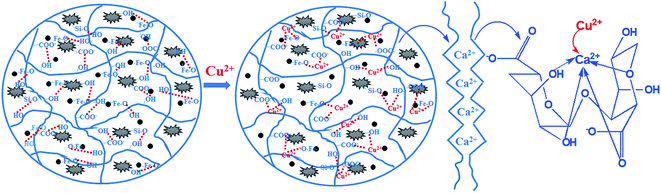 |
| Fig. 12 The mechanism of Cu(II) adsorption. | |
3.8 Recyclability
The used magnetic alginate microspheres were recycled and used as regenerated absorbent for four repeated sorption–desorption cycles (Fig. 13). The efficiency of Cu(II) was approximate 96%, which is stable and sufficiently high. The adsorption capacity of Cu(II) decreased by 9.2% in the second cycle. In the subsequent cycles, the adsorption capacity decreased slowly, therefore, the total loss of adsorption capacity throughout the 4 cycles was 19.4%. Fe3O4 decomposition rate was 1.5% in the first desorption, in addition, the total loss of Fe3O4 throughout the 4 cycles was 3.1%. There is no significant damage was observed and the spherical shape of magnetic alginate microspheres was well maintained.
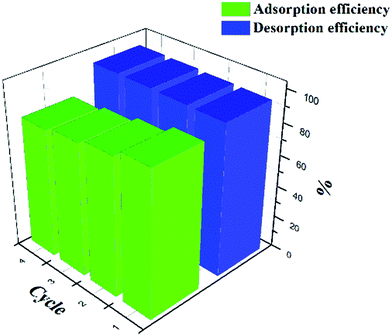 |
| Fig. 13 Recycle tests for Cu(II) adsorption onto MM. | |
4. Conclusions
In summary, we have shown that the MM has high chemical stability and adsorption capacity than MBC. It appears a synergistic effect between biochar and Fe3O4 in CA, which enhances the maximum adsorption capacity of Cu(II) ion. The maximum adsorption capacity of the MM from the Langmuir equation was 40.42 mg g−1. The magnetic microsphere showed 80.6% of the initial Cu(II) adsorption capacity after 4 cycles reuse. This research provides an effective way for biochar modification and may have great value for the application of biochar in water treatment.
Conflicts of interest
There are no conflicts to declare.
Acknowledgements
This work was supported by the Key Research and Development Project of Hainan Province of China (Project No. ZDYF2017102), Natural Science Foundation of Hainan Province of China (Project No. 20162032) and Hainan Provincial Fine Chemical Engineering Research Center opening topic fund subsidization.
References
- X.-j. Tong, J.-y. Li, J.-h. Yuan and R.-k. Xu, Chem. Eng. J., 2011, 172, 828–834 CrossRef CAS.
- F. M. Pellera, A. Giannis, D. Kalderis, K. Anastasiadou, R. Stegmann, J. Y. Wang and E. Gidarakos, J. Environ. Manage., 2012, 96, 35–42 CrossRef CAS PubMed.
- M. Li, Q. Liu, L. Guo, Y. Zhang, Z. Lou, Y. Wang and G. Qian, Bioresour. Technol., 2013, 141, 83–88 CrossRef CAS PubMed.
- M. Y. Khan, A. S. Mangrich, J. Schultz, F. S. Grasel, N. Mattoso and D. H. Mosca, J. Anal. Appl. Pyrolysis, 2015, 116, 42–48 CrossRef CAS.
- S. Y. Wang, Y. K. Tang, K. Li, Y. Y. Mo, H. F. Li and Z. Q. Gu, Bioresour. Technol., 2014, 174, 67–73 CrossRef CAS PubMed.
- S. Y. Wang, Y. K. Tang, C. Chen, J. T. Wu, Z. Huang, Y. Y. Mo, K. X. Zhang and J. B. Chen, Bioresour. Technol., 2015, 186, 360–364 CrossRef CAS PubMed.
- X. F. Tan, Y. G. Liu, Y. L. Gu, Y. Xu, G. M. Zeng, X. J. Hu, S. B. Liu, X. Wang, S. M. Liu and J. Li, Bioresour. Technol., 2016, 212, 318–333 CrossRef CAS PubMed.
- K. R. Thines, E. C. Abdullah, N. M. Mubarak and M. Ruthiraan, Renewable Sustainable Energy Rev., 2017, 67, 257–276 CrossRef CAS.
- D. Mohan, H. Kumar, A. Sarswat, M. Alexandre-Franco and C. U. Pittman, Chem. Eng. J., 2014, 236, 513–528 CrossRef CAS.
- B. Chen, Z. Chen and S. Lv, Bioresour. Technol., 2011, 102, 716–723 CrossRef CAS PubMed.
- Z. Han, B. Sani, W. Mrozik, M. Obst, B. Beckingham, H. K. Karapanagioti and D. Werner, Water Res., 2015, 70, 394–403 CrossRef CAS PubMed.
- L. Trakal, V. Veselska, I. Safarik, M. Vitkova, S. Cihalova and M. Komarek, Bioresour. Technol., 2016, 203, 318–324 CrossRef CAS PubMed.
- D. Mohan, P. Singh, A. Sarswat, P. H. Steele and C. U. Pittman Jr, J. Colloid Interface Sci., 2015, 448, 238–250 CrossRef CAS PubMed.
- R. D. C. Soltani, G. S. Khorramabadi, A. R. Khataee and S. Jorfi, J. Taiwan Inst. Chem. Eng., 2014, 45, 973–980 CrossRef CAS.
- A. F. Hassan, A. M. Abdel-Mohsen and H. Elhadidy, Int. J. Biol. Macromol., 2014, 68, 125–130 CrossRef CAS PubMed.
- X. Li, Y. Qi, Y. Li, Y. Zhang, X. He and Y. Wang, Bioresour. Technol., 2013, 142, 611–619 CrossRef CAS PubMed.
- H. Tavakoli, H. Sepehrian and R. Cheraghali, J. Taiwan Inst. Chem. Eng., 2013, 44, 343–348 CrossRef CAS.
- Y. Li, Q. Du, T. Liu, J. Sun, Y. Wang, S. Wu, Z. Wang, Y. Xia and L. Xia, Carbohydr. Polym., 2013, 95, 501–507 CrossRef CAS PubMed.
- A. Sigdel, W. Jung, B. Min, M. Lee, U. Choi, T. Timmes, S.-J. Kim, C.-U. Kang, R. Kumar and B.-H. Jeon, Catena, 2017, 148, 101–107 CrossRef CAS.
- S. Zhang, F. Xu, Y. Wang, W. Zhang, X. Peng and F. Pepe, Chem. Eng. J., 2013, 234, 33–42 CrossRef CAS.
- A. Idris, N. S. M. Ismail, N. Hassan, E. Misran and A.-F. Ngomsik, J. Ind. Eng. Chem., 2012, 18, 1582–1589 CrossRef CAS.
- Y. Yang, Z. Wei, X. Zhang, X. Chen, D. Yue, Q. Yin, L. Xiao and L. Yang, Bioresour. Technol., 2014, 171, 227–232 CrossRef CAS PubMed.
- M. F. A. Taleb, Carbohydr. Polym., 2014, 114, 65–72 CrossRef CAS PubMed.
- K. W. Jung, T. U. Jeong, H. J. Kang and K. H. Ahn, Bioresour. Technol., 2016, 211, 108–116 CrossRef CAS PubMed.
- X. Cui, X. Dai, K. Y. Khan, T. Li, X. Yang and Z. He, Bioresour. Technol., 2016, 218, 1123–1132 CrossRef CAS PubMed.
- S. T. Danalıoğlu, Ş. S. Bayazit, Ö. Kerkez Kuyumcu and M. A. Salam, J. Mol. Liq., 2017, 240, 589–596 CrossRef.
- S. Cataldo, A. Gianguzza, D. Milea, N. Muratore and A. Pettignano, Int. J. Biol. Macromol., 2016, 92, 769–778 CrossRef CAS PubMed.
- B. Zhou, Z. Wang, D. Shen, F. Shen, C. Wu and R. Xiao, Ecol. Eng., 2017, 98, 189–195 CrossRef.
- T. Wu, L. Mao and H. Wang, J. Fluorine Chem., 2017, 200, 8–17 CrossRef CAS.
- W. M. Algothmi, N. M. Bandaru, Y. Yu, J. G. Shapter and A. V. Ellis, J. Colloid Interface Sci., 2013, 397, 32–38 CrossRef CAS PubMed.
- M. Zhang, B. Gao, S. Varnoosfaderani, A. Hebard, Y. Yao and M. Inyang, Bioresour. Technol., 2013, 130, 457–462 CrossRef CAS PubMed.
- C. Zhang, B. Shan, W. Tang and Y. Zhu, Bioresour. Technol., 2017, 238, 352–360 CrossRef CAS PubMed.
- Y. Guo, W. Tang, J. Wu, Z. Huang and J. Dai, J. Environ. Sci., 2014, 26, 2123–2130 CrossRef PubMed.
- R. Verma, A. Asthana, A. K. Singh, S. Prasad and M. A. B. H. Susan, Microchem. J., 2017, 130, 168–178 CrossRef CAS.
- L. Yan, S. Li, H. Yu, R. Shan, B. Du and T. Liu, Powder Technol., 2016, 301, 632–640 CrossRef CAS.
- Y. Xu, Y. Zhou and R. Li, Colloids Surf., A, 2014, 459, 240–246 CrossRef CAS.
- L. G. Yan, K. Yang, R. R. Shan, T. Yan, J. Wei, S. J. Yu, H. Q. Yu and B. Du, J. Colloid Interface Sci., 2015, 448, 508–516 CrossRef CAS PubMed.
- Y. Chen and S. Mu, Sens. Actuators, B, 2014, 192, 275–282 CrossRef CAS.
- C. Yu, J. Geng, Y. Zhuang, J. Zhao, L. Chu, X. Luo, Y. Zhao and Y. Guo, Carbohydr. Polym., 2016, 152, 327–336 CrossRef CAS PubMed.
- C.-J. Zhang, Y. Liu, L. Cui, C. Yan and P. Zhu, J. Anal. Appl. Pyrolysis, 2016, 122, 13–23 CrossRef CAS.
- N. E. Mousa, C. M. Simonescu, R.-E. Pătescu, C. Onose, C. Tardei, D. C. Culiţă, O. Oprea, D. Patroi and V. Lavric, React. Funct. Polym., 2016, 109, 137–150 CrossRef CAS.
- E. Platero, M. E. Fernandez, P. R. Bonelli and A. L. Cukierman, J. Colloid Interface Sci., 2017, 491, 1–12 CrossRef CAS PubMed.
- N. Jiang, Y. Xu, Y. Dai, W. Luo and L. Dai, J. Hazard. Mater., 2012, 215–216, 17–24 CrossRef CAS PubMed.
- P. Regmi, J. L. Garcia Moscoso, S. Kumar, X. Cao, J. Mao and G. Schafran, J. Environ. Manage., 2012, 109, 61–69 CrossRef CAS PubMed.
- X. H. Do and B. K. Lee, J. Environ. Manage., 2013, 131, 375–382 CrossRef CAS PubMed.
- H. Jin, S. Capareda, Z. Chang, J. Gao, Y. Xu and J. Zhang, Bioresour. Technol., 2014, 169, 622–629 CrossRef CAS PubMed.
- W. Wang, L. Zong and A. Wang, Int. J. Biol. Macromol., 2013, 62, 225–231 CrossRef CAS PubMed.
- L. Liu, Y. Wan, Y. Xie, R. Zhai, B. Zhang and J. Liu, Chem. Eng. J., 2012, 187, 210–216 CrossRef CAS.
- B. Wang, C. Li and H. Liang, Bioresour. Technol., 2013, 146, 803–806 CrossRef CAS PubMed.
- X.-H. Do and B.-K. Lee, J. Environ. Manage., 2013, 131, 375–382 CrossRef CAS PubMed.
- G. X. Yang and H. Jiang, Water Res., 2014, 48, 396–405 CrossRef CAS PubMed.
- H. Wang, B. Gao, S. Wang, J. Fang, Y. Xue and K. Yang, Bioresour. Technol., 2015, 197, 356–362 CrossRef CAS PubMed.
- Y. C. Chang and D. H. Chen, J. Colloid Interface Sci., 2005, 283, 446–451 CrossRef CAS PubMed.
- I. Mobasherpour, E. Salahi and M. Ebrahimi, J. Saudi Chem. Soc., 2014, 18, 792–801 CrossRef.
- C. Hu, G. Li, Y. Wang, F. Li, G. Guo and H. Hu, Int. J. Biol. Macromol., 2017, 103, 751–757 CrossRef CAS PubMed.
- X. Mi, G. Huang, W. Xie, W. Wang, Y. Liu and J. Gao, Carbon, 2012, 50, 4856–4864 CrossRef CAS.
- M. M. Lakouraj, F. Mojerlou and E. N. Zare, Carbohydr. Polym., 2014, 106, 34–41 CrossRef CAS PubMed.
- Y. Zhan, J. Lin and J. Li, Environ. Sci. Pollut. Res., 2013, 20, 2512–2526 CrossRef CAS PubMed.
- A. R. Bagheri, M. Ghaedi, A. Asfaram, A. A. Bazrafshan and R. Jannesar, Ultrason. Sonochem., 2017, 34, 294–304 CrossRef CAS PubMed.
- B. Zhou, Z. Wang, D. Shen, F. Shen, C. Wu and R. Xiao, Ecol. Eng., 2017, 98, 189–195 CrossRef.
- H. Ren, Z. Gao, D. Wu, J. Jiang, Y. Sun and C. Luo, Carbohydr. Polym., 2016, 137, 402–409 CrossRef CAS PubMed.
- Y. T. Zhou, C. Branford-White, H. L. Nie and L. M. Zhu, Colloids Surf., B, 2009, 74, 244–252 CrossRef CAS PubMed.
- H. Roh, M.-R. Yu, K. Yakkala, J. R. Koduru, J.-K. Yang and Y.-Y. Chang, J. Ind. Eng. Chem., 2015, 26, 226–233 CrossRef CAS.
- H. Qiu, S. Zhang, B. Pan, W. Zhang and L. Lv, J. Colloid Interface Sci., 2012, 366, 37–43 CrossRef CAS PubMed.
- J. M. Lázaro Martínez, E. Rodríguez-Castellón, R. M. T. Sánchez, L. R. Denaday, G. Y. Buldain and V. Campo Dall' Orto, J. Mol. Catal. A: Chem., 2011, 339, 43–51 CrossRef.
- H. Yuan, Y. Wang, S.-M. Zhou and S. Lou, Chem. Eng. J., 2011, 175, 555–560 CrossRef CAS.
- Y. Wang, H. Wu, Z. Sárossy, C. Dong and P. Glarborg, Fuel, 2017, 197, 422–432 CrossRef CAS.
- T. Tański, W. Matysiak, Ł. Krzemiński, P. Jarka and K. Gołombek, Appl. Surf. Sci., 2017, 424, 184–189 CrossRef.
|
This journal is © The Royal Society of Chemistry 2017 |
Click here to see how this site uses Cookies. View our privacy policy here.