DOI:
10.1039/C7RA09772G
(Paper)
RSC Adv., 2017,
7, 46022-46027
Cu2(BDC)2(BPY)–MOF: an efficient and reusable heterogeneous catalyst for the aerobic Chan–Lam coupling prepared via ball-milling strategy†
Received
2nd September 2017
, Accepted 14th September 2017
First published on 28th September 2017
Abstract
Nanoporous Cu2(BDC)2(BPY)–MOF was used as efficient and reusable heterogeneous catalyst to effect the aerobic cross-coupling of aromatic amines and phenyl boronic acid (Chan–Lam coupling). Ball-milling strategy was utilized for the first as a powerful green and energy-efficient method for the synthesis of this nanoporous metal–organic framework. Certain ratio of metal ion and organic linkers were held to improve the quality of nanostructures. Cu2(BDC)2(BPY) were characterized by X-ray powder diffraction (XRD), scanning electron microscopy (SEM), transmission electron microscopy (TEM) and Brunauer–Emmett–Teller (BET) surface area analysis.
Introduction
Crystalline microporous and mesoporous metal–organic frameworks (MOFs) are constructed by joining metal-containing units [secondary building units (SBUs)] with organic linkers, using strong bonds (reticular synthesis) to create open crystalline frameworks with permanent porosity.1 Bivalent or trivalent aromatic carboxylic acids or N-containing aromatics are commonly used to form frameworks with zinc, copper, chromium, aluminum, zirconium, and other elements.2–5 During the past century, extensive work was done on crystalline extended structures in which metal ions are joined by organic linkers containing Lewis base – binding atoms such as nitriles and bipyridines.6,7 A great variety of cations can be incorporated into the framework and a wide choice of functionalized organic linkers provides many possibilities to design the structures and tune the properties of the final porous materials.8,9 They encompassed void space and therefore were viewed to have the potential to be permanently porous, as is the case for zeolites.10 Since MOFs have low density, very high surface area with a large percentage of transition metals, they have emerged as interesting materials for various applications in energy storage,11 CO2 adsorption,12,13 hydrocarbon adsorption/separation,14,15 catalysis,16,17 sensor,18 magnetism,19 drug delivery,20 luminescence,21 gas storage22 and catalysis.23–26 In particular, applications in energy technologies such as fuel cells, supercapacitors, and catalytic conversions have made them objects of extensive study, industrial-scale production, and application.27 The variety of synthesis procedures was extended in the past years with the introduction of chemical vapour deposition28 mechanochemical procedures,29 flow reactors,30 and spray drying for the synthesis of MOFs.31 Waste-free sustainable syntheses require quantitative yields of products without solvent-consuming, waste-producing workup procedures.32 Organic and inorganic solid–solid syntheses by ball-milling are most useful in this aim, and already hundreds of examples of waste-free procedures, including industrial scale-up processes, are available.33 These solid–solid reactions are comparable to solvothermal reactions at higher temperatures, although there is a risk of inferior results because the benefit of self-assembled packing is lost.34 Nevertheless, there is also urgency for solvent-free reactions under efficient kneading conditions35 in the absence of solvents, because the common syntheses based on solvothermal methods often lead to the incorporation of solvent molecules in the network. Consequently, the subsequent removal of solvent can even cause the collapse of the network. In addition, sufficient amounts of pure material for broad range testing can be easily obtained typically in quantitative yields.36 Mechanochemistry for preparation of porous MOFs was first reported in 2006 by Pichon and coworkers.37 The application of mechanochemistry for the synthesis of MOFs is relatively unusual synthesis possibility, although it is currently employed by several researchers as an approach for the synthesis of metal organic compounds.38,39
Ullmann reaction (copper catalyzed N-arylation of amines)40 and the related Goldberg reaction (copper-catalyzed N-arylation of amides)41 are traditional methods for C–N bond formation in organic synthesis and pharmaceutical industry. However, the classic Ullmann amination requires high reaction temperatures, stoichiometric amounts of copper reagents, strong bases and harsh reaction condition. During the past years, great progress on the palladium-based modified Ullmann and Goldberg coupling reactions protocols have been made,42 but the drawbacks of the catalyst systems, such as air sensitivity and high cost, limit their applications. On the other hand, in 1998, the groups of Chan, Evans, and Lam independently developed Cu-mediated oxidative amination of aryl boronic acids with amines and other nucleophiles in the presence of Cu(OAc)2,43 providing a valuable alternative to traditional cross-couplings in the construction of carbon heteroatom bonds. Recently, many applications of this new method have been reported based on copper catalysts supported on the resin,44 cellulose,45 Fe3O4 magnetic nanoparticles,46 and fluorapatite,47 in heterogeneous systems and fac-[Ir(ppy)3]-assisted Cu(II),48 in homogenous systems. However, despite these important contributions, more work still needs to be done to identify new heterogeneous systems for a highly effective catalyst. As part of our ongoing work on the mechanochemistry synthesis of metal organic framework and application as catalyst in organic synthesis,49 herein we report an efficient protocol for the synthesis of Cu2(BDC)2(BPY) by ball milling technique and application of it in the cross-coupling of aromatic amines and phenyl boronic acid (Scheme 1).
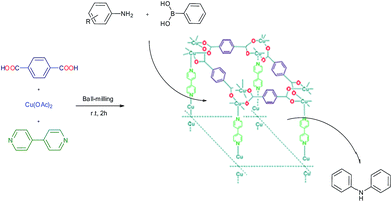 |
| Scheme 1 Synthesis of Cu2(BDC)2(BPY) by ball-milling and application as catalyst in cross-coupling of aromatic amines and phenyl boronic acid. | |
Results and discussion
The choice of an appropriate ratio of reactants is critical for the successful synthesis of desired MOFs. The best ratio of Cu(OAc)2·H2O, terephthalic acid and 4,4′-bipyridine for the synthesis of Cu2(BDC)2(BPY) with good crystalline structure and high surface area was 1
:
1
:
0.5 respectively. The MOF was synthesized by room temperature solvent-free ball-milling. The process was completed within 2 hours resulting in a green powder. To confirm the mechanochemically preparation of Cu2(BDC)2(BPY), X-ray powder diffraction was performed. The observed sharp peaks at 2theta of 8, 12, 14, 16, 18, and 28 (Fig. 1) are in a good agreement with reported in literature.50 The diffraction patterns of the mechanochemically prepared MOF samples (as synthesized and after activation) show no reflexes of the reactants. Also, XRD results indicated that Cu2(BDC)2(BPY) was formed mutually interpenetrating structure of a pair of three-dimensional frameworks.51 The loading percent of Cu was measured by means of ICP. The measured amount of copper (found: 20.83%) corresponds well with the calculated percentage for Cu2(BDC)2(BPY) (calcd 20.80%). FT-IR spectroscopy technique was employed to characterize vibrational modes of the MOF. In bidentate bridged carboxylate–Cu(II) complexes, the intense band of (COO) is usually characterized by a wavenumber in the 1600–1625 cm−1 region.
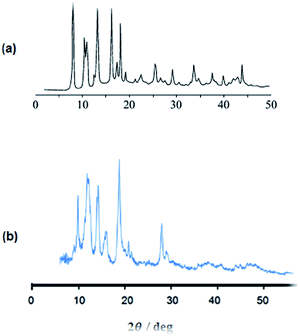 |
| Fig. 1 (a) PXRD patterns of prepared Cu2(BDC)2(BPY) in literature20 (b) PXRD patterns of mechanochemically prepared Cu2(BDC)2(BPY) (this work). | |
The asymmetric stretching mode of COO appears at 1614 cm−1. The bands at 1563, 1508 cm−1 are associated with the phenyl and pyridine modes, based on the comparison with pure BDC and 4,4′-bipyridine ligands. SEM images of Cu–MOF showed a narrow particle size distribution. Most of the particles size was in the range of 60–90 nm (Fig. 2).
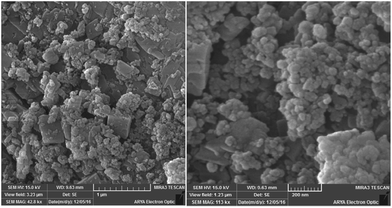 |
| Fig. 2 Scanning electron microscopy (SEM) images of the Cu2(BDC)2(BPY). | |
TEM micrograph (Fig. 3), confirmed that a crystalline and nano-scaled material was produced. It is also to emphasize that ball milling technique has resulted in producing uniformly distributed nano-scale particles. As can be observed, the appearance of squares units in the TEM images reveal the formation of Cu2(BDC)2(BPY) framework structure and shown nano-cubic morphology.51 The N2 adsorption–desorption isotherm of the MOF exhibits an intermediate mode between type I and type IV (Fig. 4) which is related to mesoporous materials and microporous materials, respectively.52
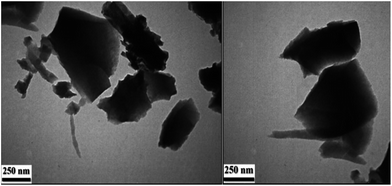 |
| Fig. 3 Transmission Electron Microscopy (TEM) images of the Cu2(BDC)2(BPY). | |
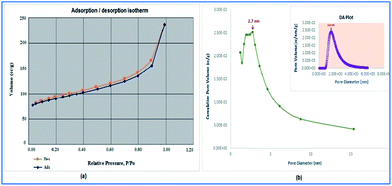 |
| Fig. 4 (a) The N2 adsorption–desorption isotherms of the mesoporous [Cu2(BDC)2(BPY)] and (b) the BJH isotherm and DA plot of mesoporous [Cu2(BDC)2(BPY)]. | |
The BET surface area and total specific pore volume are 305.5 m2 g−1 and 0.462 cm−3 g−1, respectively (Fig. 4).
The mesopore size distribution curve, calculated from Barrett Joyner–Halenda analysis, shows a pore size distribution centered at around 2.5 nm (inset of Fig. 4). The micropore diameter was calculated to be 0.6 nm by MP plot (Fig. 5).
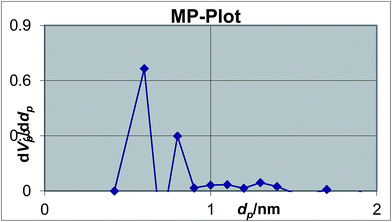 |
| Fig. 5 MP-plot of as-synthesized Cu2(BDC)2(BPY). | |
The synthetic Cu2(BDC)2(BPY) was employed as a catalyst in the aerobic cross-coupling of aromatic amines and phenyl boronic acid. It is noticeable that the nature of base and solvent greatly affect the efficiency of the coupling reaction (Table 1). The coupling reaction of aniline and phenyl boronic acid was chosen as model reaction for optimization of reaction condition. With respect to the applicability and availability, K2CO3 was employed as the base in this study. The best solvent for this coupling reaction is mixture of H2O and methanol (1
:
1) (entry 4–7). As shown in Table 2 the molar ratio of aniline and phenyl boronic acid affect the yield of reaction and the best ratio is 0.5
:
1 of aniline and phenyl boronic acid (entry 7). In another attempt, when the reaction was carried out in the presences of 30 and 40 mg of catalyst, no observable change in yield is obtained.
Table 1 Optimization of reaction conditionsa
Table 2 Evaluation of catalyst scopea
With the optimum reaction conditions in hand, the catalytic system was efficient for the coupling reaction of different aromatic amines with phenyl boronic acid and showed high selectivity for monoarylation vs. diarylation. Aromatic amines with electron-withdrawing and electron-releasing groups gave the corresponding biphenyls in good yield and the results are summarized in Table 2. Only in case of 4-nitro aniline rate of the reaction increased and reaction completed within 20 minutes. This shown that electron-withdrawing group increased the rate of cross-coupling. Moreover, the cross-coupling of 2-aminopyrimidine, 1-naphthylamine with phenylboronic acid was also accomplished with a high yield under the same conditions (Table 2, entry 1f, 1g).
A comparison with other catalytic systems in the cross-coupling reaction of aniline with phenylboronic acids demonstrated that our present Cu–MOF catalyst system exhibited a higher conversion and yield under milder conditions (Table 3).
Table 3 Comparison of activity for different catalytic systems in the cross-coupling of aromatic amines and phenyl boronic acid
Entry |
Catalyst |
Reaction condition |
Time |
Yield |
Ref. no. |
1 |
Resin supported Cu(II) |
Cat. 10 mol%, CH2Cl2, 1 atm O2, r.t. |
24 h |
32 |
23 |
2 |
Cu(OAc)2/fac-[Ir(ppy)3] |
Cat. 10 mol%, toluene/MeCN, 35 °C, blue LED irradiation |
20 |
95 |
27 |
3 |
Cu-supported-fluorapatite |
Cat. 100 mg, MeOH, r.t. |
3 |
90 |
26 |
4 |
Fe3O4–EDTA–Cu(II) |
Cat. 5 mol%, H2O, 50 °C |
2 |
95 |
25 |
5 |
Cellulose supported Cu(0) |
Cat. 25 mg, Et3N, MeOH, reflux |
2.5 |
87 |
24 |
6 |
Cu2(BDC)2DABCO–MOF |
Cat. 20 mg, K2CO3, MeOH/H2O, r.t. |
1 |
85 |
Present work |
For a heterogeneous catalyst, the recycling of the catalyst are important issues to be reviewed. To address these issues, the catalyst was recovered by simple filtration and washed with methanol and oven dried. The recovered catalyst was reused for cross-coupling of aniline and phenyl boronic acids. The result indicates that the Cu2(BDC)2BPY can be used for several cycles successfully with minimal loss of activity. A tentative mechanism for the Cu–MOF Chan–Lam coupling reaction of aromatic amines and phenyl boronic acids is shown in Scheme 2. The proposed mechanism is shown in Scheme 2.
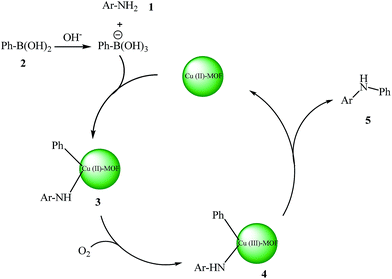 |
| Scheme 2 Proposed mechanism for cross-coupling by the Cu2(BDC)2BPY–MOF catalyst. | |
Initially, the Cu(II)–MOF catalyst could undergo ligand exchange and transmetalation with aromatic amine 1 and phenyl boronic acid 2 to generate Cu amide 3. The oxidation of Cu amide 3 by oxygen gives a copper(III) intermediate 4, which undergoes reductive elimination to give product 5. The mechanism is based on those proposed by Collman,52 Buchwald.53
The structures of all products were elucidated from their mass, and 1H-NMR spectra and melting point as described for diphenyl amine. The mass spectrum of diphenyl amine (Table 3, entry 1) displayed the molecular ion peak at m/z = 169. The 1H-NMR spectrum of diphenyl amine showed the aromatic protons gave rise to multiplets in the region δ = 6.92–7.28 ppm and N–H in 5.65 ppm.
Conclusions
Nanoporous metal–organic framework Cu2(BDC)2(BPY) was successfully synthesized by a solvent-free ball milling process. The advantages of this procedure are solvent-free conditions, short reaction times, high yield and easy work up. Also, prepared MOF samples (as synthesized and after activation) show no reflexes of the reactants and XRD results indicated that Cu2(BDC)2(BPY) was formed mutually interpenetrating structure of a pair of three-dimensional frameworks. The synthesized Cu2(BDC)2(BPY) offered high catalytic activity for cross-coupling of aromatic amines and phenyl boronic acid. So, a different range of aryl amines applicable in this reaction. Further studies on mechanochemical synthesis of other useful MOFs and development of its catalytic scope are in progress and would be presented in the future.
Experimental section
1. Materials and instruments
All reagents and starting materials including organic linker H2BDC, metal salt Cu(OAc)2·H2O, 1,4-benzenedicarboxylate (BDC, 99%), 4,4′-bipyridine (BPY) were obtained from commercially available sources such as Sigma-Aldrich and Merck and used without any further purification. X-ray powder diffraction (XRD) patterns recorded using an X'pert MPD. The sample was characterized using a scanning electron microscope (SEM) with a ZEISS scanning electron microscope at 30 kV with gold coating. FT-IR spectra were recorded with a Shimadzu 8400s FT-IR spectrometer using potassium bromide pellets. Brunauer–Emmett–Teller (BET) surface area of the samples was determined from N2 adsorption–desorption isotherms using a Quantachrome NovaWin2 analyzer. Transmission electron microscopy (TEM) was carried out using an EM10C-100 kV series microscope from the ZEISS Company, German and the actual loading of cupper was determined by Inductively Coupled Plasma (ICP) analysis on sequential plasma spectrometer, Shimadzu (ICPS-7000 ver. 2). 1H-NMR spectra were recorded at 500.1 MHz on a BRUKER DRX 500-AVANCE FT-NMR instrument with CDCl3 as solvent.
2. Ball-milling synthesis of the metal–organic framework Cu2(BDC)2(BPY)
A mixture of Cu(OAc)2·H2O (0.6 mmol), H2BDC (0.6 mmol) and BPY (0.3 mmol) with molar ratio of 1
:
1
:
0.5 were ball-milled vigorously at 30 Hz without any solvent at room temperature for 2 h. The obtained green powder was washed with DMF (2 × 10 mL). Solvent exchange was carried out with methanol (2 × 10 mL) at room temperature. To remove the guest molecules of MOFs, obtained powder was treated by heating under vacuum at 130 °C for 12 h. The resulting green powder was isolated with 96% yield and characterized by several techniques including PXRD, SEM, TEM, BET, CHN, ICP and FT-IR.
3. General procedure for the Chan–Lam coupling
To a mixture of Cu2(BDC)2BPY (20 mg) and aromatic amine (1 mmol) in H2O/MeOH (4 mL, 1
:
1), phenylboronic acid (2 mmol) was added and the resultant mixture was stirred at room temperature for 1 h. After completion of the reaction (monitored by TLC) catalyst was filtered and washed by H2O/methanol (2 mL, 1
:
1). Then, the filtrate was diluted with water (10 mL), extracted with ethyl acetate (2 × 10 mL), and the combined extracts were dried with Na2SO4. The product was purified by column chromatography (silica gel, n-hexane/EtOAc) to afford diarylamines 3a–g structure of all product was characterized by melting point and 1H-NMR spectra.
Conflicts of interest
There are no conflicts to declare.
Acknowledgements
The authors gratefully acknowledge from Science and Research Branch, Islamic Azad University and Iran university of Science and Technology (IUST) for partial financial support of this work.
Notes and references
- O. M. Yaghi, Nature, 2003, 423, 705 CrossRef CAS PubMed.
- J. R. Long and O. M. Yaghi, Chem. Soc. Rev., 2009, 38, 1213 RSC.
- J. R. Li, R. J. Kuppler and H. C. Zhou, Chem. Soc. Rev., 2009, 38, 1477 RSC.
- Y. H. Hu and L. Zhang, Adv. Mater., 2010, 22, E117 CrossRef CAS PubMed.
- D. Yuan, D. Zhao, D. Sun and H. C. Zhou, Angew. Chem., Int. Ed., 2010, 49, 5357 CrossRef CAS PubMed.
- A. F. Wells, Structural Inorganic Chemistry, Oxford Univ. Press, New York, 1984 Search PubMed.
- Y. Kinoshita, I. Matsubara, T. Higuchi and Y. Saito, Bull. Chem. Soc. Jpn., 1959, 32, 1221 CrossRef CAS.
- J. S. Seo, D. Whang, H. Lee, S. I. Jun, J. Oh, Y. J. Jeon and K. Kim, Nature, 2000, 404, 982 CrossRef CAS PubMed.
- G. Ferey, M. Latroche, C. Serre, T. Loiseau, F. Millange and A. Percheron-Guegan, Chem. Commun., 2003, 2976 RSC.
- M. Kondo, T. Yoshitomi, H. Matsuzaka, S. Kitagawa and K. Seki, Angew. Chem., Int. Ed. Engl., 1997, 36, 1725 CrossRef CAS.
- J. L. C. Rowsell, E. C. Spencer, J. Eckert, J. A. K. Howard and O. M. Yaghi, Science, 2005, 309, 1350 CrossRef CAS PubMed.
- R. Kitaura, K. Seki, G. Akiyama and S. Kitagawa, Angew. Chem., Int. Ed., 2003, 42, 428 CrossRef CAS PubMed.
- D. A. Yang, H. Y. Cho, J. Kim, S. T. Yang and W. S. Ahn, Energy Environ. Sci., 2012, 5, 6465 CAS.
- E. Haque, J. E. Lee, I. T. Jang, Y. K. Hwang, J. S. Chang, J. Jegal and S. H. Jhung, J. Hazard. Mater., 2010, 181, 535 CrossRef CAS PubMed.
- E. Haque, J. W. Jun and S. H. Jhung, J. Hazard. Mater., 2011, 185, 507 CrossRef CAS PubMed.
- S. Bhattacharjee, D. A. Yang and W. S. Ahn, Chem. Commun., 2011, 47, 3637 RSC.
- J. Kim, S. N. Kim, H. G. Jang, G. Seo and W. S. Ahn, Appl. Catal., A, 2013, 453, 175 CrossRef CAS.
- S. Achmann, G. Hagen, J. Kita, I. M. Malkowsky, C. Kiener and R. Moos, Sensors, 2009, 9, 1574 CrossRef CAS PubMed.
- S. M. Humphrey and P. T. Wood, J. Am. Chem. Soc., 2004, 126, 13236 CrossRef CAS PubMed.
- P. Horcajada, T. Chalati, C. Serre, B. Gillet, C. Sebrie, T. Baati, J. F. Eubank, D. Heurtaux, P. Clayette, C. Kreuz, J. S. Chang, Y. K. Hwang, V. Marsaud, P. Bories, L. Cynober, S. Gil, G. Férey, P. Couvreur and R. Gref, Nat. Mater., 2010, 9, 172 CrossRef CAS PubMed.
- J. Rocha, L. D. Carlos, F. A. A. Paz and D. Ananias, Chem. Soc. Rev., 2011, 40, 926 RSC.
- M. Jacoby, Chem. Eng. News, 2008, 86, 13 Search PubMed.
-
(a) D. J. Tranchemontagne, J. L. Mendoza-Cortés and M. Okeeffe, Chem. Soc. Rev., 2009, 38, 1257 RSC;
(b) M. Ranocchiari and J. A. VanBokhoven, Phys. Chem. Chem. Phys., 2011, 13, 6388 RSC.
- C. V. Nguyen, Y. T. Liao, T. C. Kang, J. E. Chen, T. Y. kawa, Y. Nakasaka, T. Masuda and K. C.-W. Wu, Green Chem., 2016, 18, 5957 RSC.
- F. K. Shieh, S. C. Wang, C. Yen, C. Wu, S. Dutta, L. Y. Chou, J. V. Morabito, P. Hu, M. H. Hsu, K. C. W. Wu and C. K. Tsung, J. Am. Chem. Soc., 2015, 137, 4276 CrossRef CAS PubMed.
- U. Mueller, J. Mater. Chem., 2006, 16, 626 RSC.
-
(a) J. S. Lee, S. B. Halligudi, N. H. Jang, D. W. Hwang, J. S. Chang and Y. K. Hwang, Bull. Korean Chem. Soc., 2010, 31, 1489 CrossRef CAS;
(b) A. Corma, H. Garcia and F. X. Llabres Xamena, Chem. Rev., 2010, 110, 4606 CrossRef CAS PubMed;
(c) L. T. L. Nguyen, K. K. A. Le, H. X. Truong and N. T. S. Phan, Catal. Sci. Technol., 2012, 2, 521 RSC;
(d) D. Saha, R. Sen, T. Maity and S. Koner, Langmuir, 2013, 29, 3140 CrossRef CAS PubMed.
- I. Stassen, D. De Vos and R. Ameloot, Chem.–Eur. J., 2016, 22, 14452 CrossRef CAS PubMed.
- M. Klimakow, P. Klobes, A. F. Thünemann, K. Rademann and F. Emmerling, Chem. Mater., 2010, 22, 5216 CrossRef CAS.
- P. W. Dunne, E. Lester and R. I. Walton, React. Chem. Eng., 2016, 1, 352 CAS.
- L. Garzón-Tovar, M. Cano-Sarabia, A. Carné-Sánchez, C. Carbonell, I. Imaz and D. Maspoch, React. Chem. Eng., 2016, 1, 533 Search PubMed.
- G. Kaupp, J. Phys. Org. Chem., 2008, 21, 630 CrossRef CAS.
- G. Kaupp, Top. Curr. Chem., 2005, 254, 95 CAS.
- E. Tullberg, F. Schacher, D. Peters and T. Frejd, Synthesis, 2006, 1183 CAS.
- S. Watano, T. Okamoto, M. Tsuhari, I. Koizumi and Y. Osako, Chem. Pharm. Bull., 2002, 50, 341 CrossRef CAS PubMed.
- G. Kaupp, J. Schmeyers and J. Boy, Chemosphere, 2001, 43, 55 CrossRef CAS PubMed.
- A. Pichon, A. Lazuen-Garay and S. L. James, CrystEngComm, 2006, 8, 211 RSC.
- D. Braga, S. L. Giaffreda, F. Grepioni, A. Pettersen, L. Maini, M. Curzi and M. Polito, Dalton Trans., 2006, 1249 RSC.
- D. Braga, M. Curzi, A. Johansson, M. Polito, K. Rubini and F. Grepioni, Angew. Chem., Int. Ed., 2006, 45, 142 CrossRef CAS PubMed.
-
(a) F. Ullmann, Ber. Dtsch. Chem. Ges., 1903, 36, 2382 CrossRef;
(b) A. J. Paine, J. Am. Chem. Soc., 1987, 109, 1496 CrossRef CAS.
-
(a) I. Goldberg, Ber. Dtsch. Chem. Ges., 1906, 39, 1691 CrossRef;
(b) H. S. Freeman, J. R. Butler and L. D. Freedman, J. Org. Chem., 1978, 43, 4975 CrossRef CAS.
-
(a) J. F. Hartwig, Angew. Chem., Int.Ed., 1998, 37, 2046 CrossRef CAS;
(b) A. R. Muci and S. L. Buchwald, Topics in Current Chemistry, Springer-Verlag, Germany, 2002, vol. 219, ch. 5 Search PubMed;
(c) M. A. McGowan, J. L. Henderson and S. L. Buchwald, Org. Lett., 2012, 14, 1432 CrossRef CAS PubMed;
(d) J. Yin, M. M. Zhao, M. A. Huffman and J. M. McNamara, Org. Lett., 2002, 4, 3481 CrossRef CAS PubMed.
-
(a) D. M. T. Chan, K. L. Monaco, R.-P. Wang and M. P. Winters, Tetrahedron Lett., 1998, 39, 2933 CrossRef CAS;
(b) P. Y. S. Lam, C. G. Clark, S. Saubern, J. Adams, M. P. Winters, D. M. T. Chan and A. Combs, Tetrahedron Lett., 1998, 39, 2941 CrossRef CAS;
(c) D. A. Evans, J. L. Katz and T. R. West, Tetrahedron Lett., 1998, 39, 2937 CrossRef CAS.
-
(a) A. Biffis, F. Filippi, G. Palma, S. Lora, C. Maccaa and B. Corain, J. Mol. Catal. A: Chem., 2003, 203, 213 CrossRef CAS;
(b) C. H. G. Chiang and T. Olsson, Org. Lett., 2004, 6, 3079 CrossRef PubMed.
- K. R. Reddy, N. S. Kumar, B. Sreedhar and M. L. Kantam, J. Mol. Catal. A: Chem., 2006, 252, 136 CrossRef CAS.
- R. Mostafalu, B. Kaboudin, F. Kazemia and T. Yokomatsu, RSC Adv., 2014, 4, 49273 RSC.
- M. L. Kantam, G. T. Venkanna, C. Sridhar, B. Sreedhar and M. B. Choudary, J. Org. Chem., 2006, 71, 9522 CrossRef CAS PubMed.
- W. J. Yoo, T. Tsukamoto and S. Kobayashi, Angew. Chem., Int.Ed., 2015, 54, 1 CrossRef.
- L. Panahi, M. R. Naimi-jamal, J. Mokhtari and A. Morsali, Microporous Mesoporous Mater., 2017, 244, 208 CrossRef CAS.
-
(a) K. Seki, Phys. Chem. Chem. Phys., 2002, 4, 1968 RSC;
(b) H. T. N. Le, T. V. Tran, N. T. S. Phan and T. Truong, Catal. Sci. Technol., 2015, 5, 851 RSC.
- S. Diring, S. Furukawa, Y. Takashima, T. Tsuruoka and S. Kitagawa, Chem. Mater., 2010, 22, 4531 CrossRef CAS.
-
(a) J. P. Collman and M. Zhong, Org. Lett., 2000, 2, 1233 CrossRef CAS PubMed;
(b) J. P. Collman, M. Zhong, L. Zeng and S. Costanzo, J. Org. Chem., 2001, 66, 1528 CrossRef CAS PubMed.
- J. C. Antilla and S. L. Buchwald, Org. Lett., 2001, 3, 2077 CrossRef CAS PubMed.
Footnote |
† Electronic supplementary information (ESI) available. See DOI: 10.1039/c7ra09772g |
|
This journal is © The Royal Society of Chemistry 2017 |
Click here to see how this site uses Cookies. View our privacy policy here.