DOI:
10.1039/C7RA09377B
(Review Article)
RSC Adv., 2017,
7, 47083-47090
Removal of dye molecules from aqueous solution by carbon nanotubes and carbon nanotube functional groups: critical review
Received
24th August 2017
, Accepted 24th September 2017
First published on 5th October 2017
Abstract
For the removal and separation of wastewater pollutants, one widely used technique is adsorption. Different materials have been used as adsorbents. Among several adsorbents, carbon nanotubes (CNTs) are emerging as potential adsorbents because of their large surface area, defined cylindrical hollow structure, high ratio aspect, easy modification and hydrophobic wall surfaces. In this review, the capability of adsorption of dyes on CNTs and functionalized CNTs has been compiled. This paper provides data about defects, adsorption sites on CNTs and adsorption process studies under the effect of such various operational parameters as solution pH, contact time, and temperature, and deals with the mechanisms involved in the adsorption of dyes onto CNTs. According to observations from the articles reviewed, functionalized carbon nanotubes have better sorption capacity than as-grown CNTs. For the removal of dyes from aqueous solution, carbon nanotubes (CNTs) have shown good potential and some of the functional groups improve the adsorption potential according to evidence from the literature. For example, the maximum adsorption amount (qmax) of methylene blue dye on an MWCNT surface has been reported to be 100 mg g−1 while the maximum adsorption amount of methylene blue dye on functionalized MWCNT–SH surface was 166.7 mg g−1. This indicates that functionalization is beneficial in increasing the amounts of absorption. However, the development of highly efficient, cost effective environmentally friendly CNT-based nano adsorbents for their commercial applications should be the focus of still more study.
1. Introduction
Pollution of ground and running waters by industrial dyes is a threat to aquatic life and human beings and is a main environmental problem.1–4 Synthetic dye stuffs are extensively used as coloring agents in the paper, textile, gasoline, food, and pharmaceutical industries. The hydrosphere contaminated by the discharge of dyes into the environment is a notable source of pollution due to its recalcitrant nature, visibility even at very low concentrations, giving an undesirable color to the water, biological attack, and reducing sunlight penetration.5–10 The aromatic molecular structure of dyes presumably comes from coal tar-based hydrocarbons such as naphthalene, benzene, toluene, and xylene.11,12 Today, the yearly production of commercial dyes is >7 × 105 tons per year, and to date, more than 100
000 dyes are known.12–16 Therefore, a significant area of applied and basic research deals with the removal of dye pollution from industrial wastewater.17,18
To remove dyes from wastewater, some methods such as ozonation, flocculation, membrane separation, aerobic or anaerobic treatment, coagulation and adsorption are used by industry.19 Nevertheless, adsorption is one method which has been most widely used because it is inexpensive, and easy and impressive for dye removal from industrial wastewater. Various adsorbents are used in adsorption processes such as activated carbon,20–25 graphene nanosheets, multi-walled carbon nanotubes, cedar sawdust, crushed brick, magnetic chitosan/grapheme, and oxide composites.26–35 To remove dyes from aqueous solutions, activated carbon is one of the best adsorbents.36–40 Because of their large surface area and high porosity, activated carbons have high adsorption capacity. But the low regeneration and high cost of activated carbon restrict its use.41 Different studies have shown the adsorption ability of dyes on a large variety of non-conventional low-cost adsorbents, such as agricultural and industrial waste.41–53 Nonetheless, in very few cases, for non-conventional adsorbents and low-cost adsorbents, is the adsorption capacity higher than for activated carbons and these adsorbents showed mixed results. So, to develop more efficient adsorbents with a higher capacity for regeneration, the study of nanotubes is an ongoing process. One carbon allotrope is carbon nanotubes (CNTs, 1D) consisting of sp2-hybridized carbons,54 graphene (2D),53,54 as well as graphite (3D).55 Since CNTs were discovered in 1991 by Iijima,56 a variety of them have become available, such as single, double, few, and multi-walled carbon nanotubes.57–60 Carbon nanotubes (CNTs) have been intensively studied as a potential material to be used in a variety of applications based on their unusual chemical and physical properties.61 Compared with adsorbents such as clay and activated carbon, CNTs are more attractive because of their high selectivity, structural diversity and favorable physicochemical stability.62
In this paper, the adsorption capacities of dyes on carbon nanotubes and functionalized carbon nanotubes are reviewed. The results of recent research are used to compare the usage of carbon nanotubes and functionalized carbon nanotubes as the basis of adsorbents for the removal of dyes. The effect of various parameters such as experimental conditions (i.e. solution pH, contact time, initial concentration, and temperature), dyes, and adsorbent characteristics on the adsorption capacity are discussed and presented. Also, in this paper thermodynamic, kinetic, and adsorption isotherm studies are reviewed.
2. Dye classification
There are many ways to classify dyes in terms of method of application, colour, and structure.63 But the application classification is often favourable due to the extent and complexity of the nomenclature of colour from the system of chemical structure.64 Table 1 presents the usual classes of dye classification according to the chemical structure of the dyes. Table 2 shows the classification according to the application of the dyes. Dyes are usually categorized according to the charge of the particle upon dissolution in aqueous solution65 such as anionic (acid, reactive, and direct dyes), cationic (all basic dyes), and non-ionic (dispersed dyes).
Table 1 Dye classification based on the chemical structure the dye comes from63
Class |
Example |
Chromospheres |
Nitro dyes |
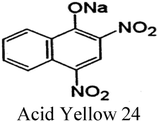 |
 |
Azo dyes |
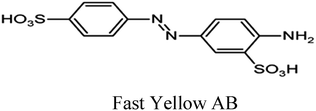 |
 |
Indigoid dyes |
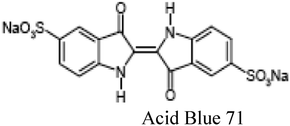 |
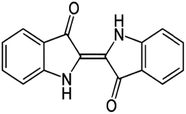 |
Anthraquinone dyes |
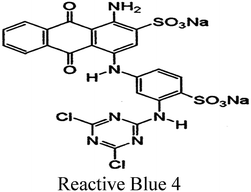 |
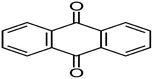 |
Triarylmethane dyes |
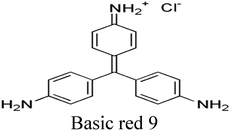 |
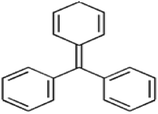 |
Nitroso dyes |
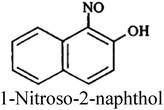 |
 |
Table 2 Dye classification according to their chemical nature (adopted from64)
Class |
Method of application |
Substrate |
Chemical types |
Direct |
Used from slightly alkaline or neutral baths containing additional electrolyte. |
Rayon, nylon, leather, paper, and cotton. |
Azo, oxazine, phthalocyanine, stilbene. |
Basic |
Used from acidic dye baths. |
Paper, inks, polyacrylonitrile, polyester, and treated nylon. |
Azo, diazahemicyanine, cyanine, xanthene, acridine, triarylmethane, oxazine, azine diphenylmethane, and anthraquinone. |
Acid |
Commonly from neutral to acidic bath. |
Silk, wool, inks, nylon, paper, and leather. |
Xanthene, triphenylmethane, anthraquinone, nitro, and azo (including nitroso, premetallized). |
Dispersed |
Often applied by lower fine aqueous dispersions temperature or high pressure/temperature methods carrier; dye may be padded on thermo and fixed cloth. |
Acrylic polyester, polyamide, plastics, and acetate. |
Azo, benzodifuranone, nitro, styryl, and anthraquinone. |
Reactive |
Reactive site on dye reacts with functional group on fibre to bind dye covalently under influence of pH and heat. |
Nylon, cotton, wool, and silk. |
Azo, phthalocyanine, anthraquinone, basic, and formazan, oxazine. |
Sulfur |
Aromatic vatted substrate with reoxidized sodium sulfide and to form insoluble sulfur-containing products on fibre. |
Cotton and rayon. |
Structures indeterminate. |
Several industries such as the paper, dye stuff, plastic, printing, textile, carpet, cosmetics, and food, use dyes in their products to provide colour. These dyes are always left over in industry and the waste is usually discharged into the environment.66,67
2.1. Dye toxicity
Dyes have great colour intensity and are easily visible even in very low concentrations.68 Complex dyes are generally based on chromium, which is carcinogenic.69 There are many aromatic structures in dye compounds that form stable complexes, which are resistant against heat, optical oxidizing agents, and biodegradation.70 Because of the presence of toxic amines in the effluent, azo dyes are classified as toxic.71,72 Degradation-based dyes are highly sustainable and have higher longevity in effluents.72 In the environment, reactive dyes cause serious trouble because they are soluble in water and give a highly coloured effluent.73 Also, having low biodegradability and being chemically stable, reactive dyes are likely to pass through conventional treatment plants, so their elimination is of high importance.74 Dyes affect the photosynthetic activity of aquatic life as they decrease the penetration of light and are replete with metals, and aromatics, which may be toxic to some aquatic life.75 Also, dyes are carcinogenic, teratogenic, or mutagenic in different microbiological species of fish. Additionally, they can severely damage human beings through dysfunction of the reproductive system, kidneys, central nervous system, brain, and liver.76
3. Dye adsorption process on CNTs
The active sites and defects of the CNT surface play an important role in dye adsorption on CNTs. CNTs consist of graphene or graphitic sheets, which have been rolled up into a cylindrical shape and exhibit a special sidewall curvature, and possess a π-conjugative structure with a highly hydrophobic surface. CNTs are called single-walled carbon nanotubes (SWCNTs) when they have one graphitic shell and multi-walled carbon nanotubes (MWCNTs) when they have several concentric graphitic shells. The main mechanisms of absorbing different dye compounds by CNTs depend on whether the dyes are cationic or anionic. In most cases, the adsorption prediction of dyes on carbon nanotubes may not be simple,77 and different possible interactions between carbon nanotubes and dyes have been proposed. Hydrophobic, van der Waals forces, π–π stacking, hydrogen bonding, and electrostatic interactions might act simultaneously or individually.78
3.1. Effective factors in dye adsorption on CNTs
Many factors are involved in dye adsorption by carbon nanotubes, such as initial concentration of dye, solution pH, temperature, and dosage of carbon nanotubes. To remove dyes in order to optimize industrial-scale development processes, an in-depth study of these parameters will be of great help. So, these factors are discussed here.79–81
3.1.1. Initial concentration of dye. The initial concentration of dye has a great effect on the removal of the dye. The initial dye concentration effect relies on the immediate relationship between the sites available for binding on the surface of the adsorbent and the concentration of the dye. As the initial concentration of the dye increases, the efficiency of dye removal decreases according to the saturation of adsorption sites on the surface of the adsorbent.82 At a low concentration of dye, there will be unoccupied binding sites on the surface of the adsorbent and when the initial concentration of dye increases, there will be insufficient sites for the dye molecules to adsorb: therefore, the efficiency of dye removal decreases.83
3.1.2. The effect of solution pH. Many articles have investigated the effect of solution acidity on the removal of the dye by CNTs from aqueous solution, and in several studies on dye adsorption it was reported that the acidity effect is one of the most important factors affecting dye removal through carbon nanotubes. Therefore, the solution pH is an effective parameter in dye removal. For example, Seow and Lim in a review article expressed that whereas for adsorption of cationic dye a high value of solution pH was preferred, a low value of solution pH is more suitable for the adsorption of anionic dye.84
3.1.3. Temperature. One important factor affecting the dye adsorption on carbon nanotubes is temperature. Adsorption is a process which can be endothermic or exothermic for different adsorbents and dyes. If increasing temperature decreases the removal efficiency of the dye, dye adsorption on carbon nanotubes will be endothermic, and if increasing temperature decreases the removal efficiency of the dye, dye adsorption on carbon nanotubes will be exothermic.85 For example, Kuo et al. examined some dye adsorption on carbon nanotubes and found that the removal of Direct Yellow 86 (DY86) dye by a carbon nanotubes surface is endothermic,86 as they observed that the adsorption capacity decreased slightly with an increase in temperature. Konicki et al. studied adsorption of Acid Red 88 (AR88) dye on a magnetic multi-walled carbon nanotubes–Fe3C nanocomposite and found that removal of Acid Red 88 dye is exothermic.87 Also, Yao et al. studied methylene blue adsorption on carbon nanotubes and found that removal of methylene blue dye was endothermic.88
3.2. Isotherm of dye adsorption on CNTs
To study the dye adsorption isotherm on CNTs, it is necessary to measure the relationship between the equilibrium pressure, the amounts adsorbed, na, and P at constant temperature:88
3.2.1. Chemical and physical adsorption. The process of dye adsorption is normally considered to be a physical process in which van der Waals power in the adsorption process is usually dominant.89–94 The adsorption of physical liquid on solid surfaces occurs in an adsorption process during electron exchange between the molecules of dyes into the solution phase and the carbon nanotubes surface, and chemical bond formation is not necessary.93–95 Unlike physical adsorption, for the molecular forces during the process of adsorption, an electron exchange reaction means that a chemical adsorption occurs between the dye molecules of the solution and the solid surface of the carbon nanotubes.94,95
3.2.2. Monolayers and multilayers. For open surfaces, adsorption consists of a layer-by-layer loading process, where the first layer is filled as θ = na/Nm = 1, where θ is the recovery of the surface, and Nm is the capacity of the monolayer. According to the result, it is understood that when θ = na/Nm < 1, we have monolayer adsorption, and when θ = na/Nm > 1, the adsorption is multilayer.To optimize the adsorption system design for the dye adsorption process, it is important to establish the most appropriate correlation for the curves of equilibrium. Various isotherm equations have been used to describe the dye adsorption equilibrium on the carbon nanotubes surface. Some of these isotherms are Langmuir and Freundlich. The Langmuir isotherm model is one of the most widely used. It is observed that the Langmuir isotherm model can be linearized in at least four different types. The Langmuir isotherm model can be expressed as:96,97,103
|
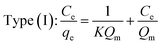 | (2) |
|
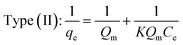 | (3) |
|
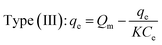 | (4) |
|
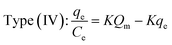 | (5) |
where
Qm (mg g
−1) and
K (L mg
−1) are Langmuir constants corresponding to dye removal capacity and adsorption energy.
3.2.3. Carbon nanotubes properties. The discovery of carbon nanotubes was very important. Because of their seamless graphite structure, and being nearly cylindrical, they have attracted much attention. Their thermal, mechanical, electrical, and physical properties make them ideal for work on SWNT and MWNT. Because of their high efficiency, the process of production of carbon nanotubes has progressed rapidly. In dye adsorption on carbon nanotubes, these properties have been taken into account because the surface area to volume ratio in CNTs is greater than in other common adsorbents. So, the chemical reaction with dye molecules for CNTs is more effective than for other common adsorbents which leads to the high contact surface of the effective collisions between the molecules of the dyes and the surface of the carbon nanotubes which in turn leads to an improvement in the efficiency of the adsorbent.124–128 Tables 3 and 4.
Table 3 A comparison of the adsorption capacities of various adsorbents for some cationic dyes
Adsorbent |
Dye |
q (mg g−1) |
Time |
Temperature (K) |
pH |
Ref. |
MWCNTs |
Malachite green |
142.85 |
80 (min) |
298 |
7 |
98 |
CNT/polyaniline composites |
Malachite green |
13.95 |
10 (min) |
293 |
7 |
99 |
MWCNT–TiO2 |
Malachite green |
— |
240 (min) |
298 |
5 |
100 |
SWCNT |
Malachite green |
4.9285 |
15 (min) |
300 |
7 |
101 |
SWCNT–NH2 |
Malachite green |
6.1340 |
15 (min) |
300 |
7 |
101 |
SWCNT–COOH |
Malachite green |
19.841 |
15 (min) |
300 |
7 |
101 |
MWCNT |
Malachite green |
55.25 |
80 (min) |
298 |
8 |
102 |
MWCNT |
Malachite green |
41.15 |
80 (min) |
318 |
8 |
102 |
MWCNT–COOH |
Malachite green |
11.63 |
10 (min) |
328 |
9 |
44 |
MWCNT–SH |
Methylene blue |
166.7 |
60 (min) |
298 |
6 |
82 |
MWCNT |
Methylene blue |
100 |
60 (min) |
298 |
6 |
82 |
Carbon nanotubes |
Methylene blue |
35.4 |
45 (min) |
273 |
7 |
88 |
Carbon nanotubes |
Methylene blue |
46.2 |
45 (min) |
298 |
7 |
88 |
Carbon nanotubes |
Methylene blue |
64.7 |
45 (min) |
333 |
7 |
88 |
Carbon nanotubes |
Methylene blue |
103.62 |
120 (min) |
290 |
7 |
93 |
Carbon nanotubes |
Methylene blue |
109.31 |
120 (min) |
300 |
7 |
93 |
Carbon nanotubes |
Methylene blue |
119.70 |
120 (min) |
310 |
7 |
93 |
Carbon nanotubes |
Methylene blue |
188.68 |
5 (hour) |
298 |
6 |
13 |
Composite of graphene–CNT |
Methylene blue |
65.79 |
30 (min) |
283 |
7 |
104 |
SWCNT |
Basic red 46 |
38.35 |
100 (min) |
298 |
9 |
105 |
SWCNT |
Basic red 46 |
33.12 |
100 (min) |
308 |
9 |
105 |
SWCNT–COOH |
Basic red 46 |
49.45 |
100 (min) |
298 |
9 |
105 |
SWCNT–COOH |
Basic red 46 |
45.33 |
100 (min) |
308 |
9 |
105 |
MWCNT |
Maxilon blue |
187.69 |
120 (min) |
303 |
10 |
106 |
Table 4 A comparison of the adsorption capacities of various adsorbents for some anionic dyes
Adsorbent |
Dye |
q (mg g−1) |
Time |
Temperature (K) |
pH |
Ref. |
MWCNT–COOH |
Methyl orange |
5.580 |
25 (min) |
298 |
2 |
32 |
Functionalized CNTs with 3-aminopropyltriethoxysilane |
Methyl orange |
42.85 |
30 (min) |
298 |
6.5 |
107 |
MWCNT |
Methyl orange |
51.74 |
2 (hour) |
298 |
7 |
108 |
MWCNT |
Methyl orange |
52.43 |
2 (hour) |
318 |
7 |
108 |
CNTs |
Methyl orange |
46 |
60 (min) |
298 |
7 |
109 |
Alkali-activated MWCNT |
Methyl orange |
149 |
60 (min) |
298 |
7 |
109 |
MWCNT |
Methyl orange |
66.09 |
120 (min) |
297 |
6.5 |
110 |
MWCNT |
Methyl orange |
60.94 |
120 (min) |
312 |
6.5 |
110 |
Composites of GO–MWCNT |
Congo red |
66.67 |
350 (min) |
303 |
5 |
111 |
Chitosan hydrogel beads impregnated with CNT |
Congo red |
450.4 |
360 (min) |
303 |
5 |
2 |
CNT/Mg(Al)O nanocomposites |
Congo red |
1250 |
75 (min) |
298 |
7 |
112 |
f-MWNTs |
Congo red |
148 |
60 (min) |
298 |
6.5 |
1 |
MWNTs |
Congo red |
148 |
— |
— |
7 |
113 |
MWCNT |
Congo red |
231.8 |
60 (min) |
298 |
11 |
114 |
MWCNT |
Reactive blue 4 |
502.5 |
4 (hour) |
298 |
2 |
115 |
SWCNT |
Reactive blue 4 |
567.7 |
4 (hour) |
298 |
2 |
115 |
MWCNT |
Reactive blue 4 |
442.0 |
4 (hour) |
298 |
2 |
116 |
SWCNT |
Reactive blue 4 |
487.6 |
4 (hour) |
298 |
2 |
116 |
MWCNTs |
Reactive black 5 |
1082.07 |
60 (min) |
298 |
2 |
117 |
MWCNT |
Reactive red M-2BE |
312.3 |
1 (hour) |
298 |
2 |
118 |
CNTs |
Procion red MX-5B |
42.92 |
24 (hour) |
281 |
6.5 |
119 |
MWCNT–Fe3C |
Direct red 23 |
172.4 |
21 (min) |
303 |
7 |
120 |
MWCNT |
Direct blue 53 |
409.4 |
3 (hour) |
298 |
2 |
121 |
MWCNTS |
Acid red 18 |
166.67 |
120 (min) |
298 |
5 |
122 |
MWCNT |
Acid blue 161 |
1000.0 |
60 (min) |
298 |
3 |
123 |
4. Conclusion
In recent years, many papers have been published on dye adsorption. In this review, the adsorption potential of carbon nanotubes and functionalized carbon nanotubes in the removal of dye molecules from wastewater has been highlighted. This paper presented dye classification according to their chemical nature and based on the dyes' chemical structure, and discussed dye toxicity. It also presented the effect of different chemical and physical conditions of adsorption on the adsorption capacity of dyes on carbon nanotubes and functionalized carbon nanotubes, such as initial concentration of dye, solution pH, and temperature. The pH of the solution is one of the main parameters in the adsorption of cationic dyes where a high value of solution pH is more suitable, whereas for anionic dye adsorption, a low value of solution pH is preferred. For the effect of initial dye concentration, because of increased interactions between dye molecules and adsorbent surface, the efficiency of dye removal will increase with an increase in the initial dye concentration, but with a further increase in initial dye, the concentration efficiency of dye removal will decrease due to saturation of the adsorption sites on the surface of the adsorbent. Also, for temperature, if the adsorption process is endothermic, as the temperature increases, the capacity for dye adsorption will increase. If the adsorption process is exothermic, with increasing temperature, the capacity for dye adsorption will decrease. Also, the toxicity of the dyes used in industry should not be neglected while they are removed through the adsorption process. So, it can be concluded that all these factors should be taken into account while the adsorption capacity of various adsorbents is evaluated from an economic point of view.
Conflicts of interest
There are no conflicts of interest.
Acknowledgements
The authors M. R. and K. H. would like to thank the Islamic Azad University, Arak Branch and author O. M. would like to thank the Islamic Azad University, Shahre-Qods Branch for their financial support.
References
- V. K. Gupta, R. Kumar, A. Nayak, T. A. Saleh and M. A. Barakat, Adv. Colloid Interface Sci., 2013, 24, 193 Search PubMed.
- S. Chatterjee, M. W. Lee and S. H. Woo, Bioresour. Technol., 2010, 101, 1800 CrossRef CAS PubMed.
- A. Ravanpaykar, A. Asfaram and M. R. Fathi emadabadi, J. Chem. Health Risks, 2012, 2, 41 Search PubMed.
- F. Güzel, Ö. Aksoy and G. Akkaya, World Appl. Sci. J., 2012, 20, 965 Search PubMed.
- P. E. Dim, Nat. Appl. Sci., 2013, 3(4), 694 CrossRef.
- V. K. Gupta, R. Jain, A. Mittal, T. A. Saleh, A. Nayak, S. Agarwal and S. Sikarwar, Mater. Sci. Eng., Proc. Conf., 2012, 32, 12 CrossRef CAS PubMed.
- T. A. Saleh and V. K. Gupta, Environ. Sci. Pollut. Res., 2012, 19, 1224 CrossRef CAS PubMed.
- V. K. Gupta, S. K. Srivastava, D. Mohan and S. Sharma, Waste Manage., 1998, 17, 517 CrossRef.
- V. K. Gupta, A. Rastogi and A. Nayak, J. Colloid Interface Sci., 2010, 342, 135 CrossRef CAS PubMed.
- A. Mittal, J. Mittal, A. Malviya and V. K. Gupta, J. Colloid Interface Sci., 2009, 340, 16 CrossRef CAS PubMed.
- V. K. Gupta, I. Ali, V. K. Saini, T. Van Gerven, B. D. Van Bruggen and C. Vandecasteele, Ind. Eng. Chem. Res., 2005, 44, 3655 CrossRef CAS.
- C. Y. Kuo, C. H. Wu and J. Y. Wu, J. Colloid Interface Sci., 2008, 327, 308 CrossRef CAS PubMed.
- B. Royer, N. F. Cardoso, E. C. Lima, J. C. P. Vaghetti, N. M. Simon, T. Calvete and R. C. Veses, J. Hazard. Mater., 2009, 164, 1213 CrossRef CAS PubMed.
- B. H. Hameed, D. K. Mahmoud and A. L. Ahmad, J. Hazard. Mater., 2008, 158, 65 CrossRef CAS PubMed.
- M. M. Ayad and A. A. El-Nasr, J. Nanostruct. Chem., 2012, 3, 3 CrossRef.
- S. T. Ong, P. S. Keng, S. L. Lee, M. H. Leong and Y. T. Hung, Int. J. Math., Phys. Eng. Sci., 2010, 5, 1270 CAS.
- V. K. Gupta, S. Agarwal and T. A. Saleh, J. Hazard. Mater., 2011, 185, 17 CrossRef CAS PubMed.
- V. K. Gupta, I. Ali, T. A. Saleh, A. Nayak and S. Agarwal, RSC Adv., 2012, 2, 6380 RSC.
- C. Y. Kuo, J. Hazard. Mater., 2008, 152, 949 CrossRef CAS PubMed.
- K. Zare, V. K. Gupta and O. Moradi, et al., J. Nanostruct. Chem., 2015, 5, 227 CrossRef CAS.
- A. Mittal, J. Mittal, A. Malviya and V. K. Gupta, J. Colloid Interface Sci., 2010, 344, 497 CrossRef CAS PubMed.
- V. K. Gupta, R. Jain, A. Nayak, S. Agarwal and M. Shrivastava, Mater. Sci. Eng., 2011, 31, 1062 CrossRef CAS.
- V. K. Gupta and A. Nayak, Chem. Eng. J., 2012, 180, 81 CrossRef CAS.
- T. A. Saleha and V. K. Gupta, J. Colloid Interface Sci., 2012, 371, 101 CrossRef PubMed.
- H. Khani, M. K. Rofouei, P. Arab, V. K. Gupta and Z. Vafaei, J. Hazard. Mater., 2010, 183, 402 CrossRef CAS PubMed.
- O. G. Apul, Q. Wang, Y. Zhou and T. Karanfil, Water Res., 2013, 47, 1648 CrossRef CAS PubMed.
- F. M. Machado, C. P. Bergmann, T. H. M. Fernandes, E. C. Lima, B. Royer, T. Calveteb and S. B. Faganc, J. Hazard. Mater., 2011, 192, 1122 CrossRef CAS PubMed.
- L. Fan, C. Luo, M. Sun, H. Qiu and X. Li, Colloids Surf., B, 2013, 103, 601 CrossRef CAS PubMed.
- F. Najafi, O. Moradi, M. Rajabi, M. Asif, I. Tyagi, S. Agarwal and V. K. Gupta, J. Mol. Liq., 2015, 208, 106 CrossRef CAS.
- S. Karthikeyana, V. K. Gupta, R. Boopathy, A. Titusa and G. Sekaran, J. Mol. Liq., 2012, 173, 153 CrossRef.
- A. K. Jain, V. K. Gupta, A. Bhatnagar and Suhas, Sep. Sci. Technol., 2003, 38, 463 CrossRef CAS.
- V. K. Gupta, A. Nayak and S. Agarwal, Environmental Engineering Research, 2015, 20(1), 1 CrossRef.
- T. A. Saleha and V. K. Gupta, Adv. Colloid Interface Sci., 2014, 211, 93 CrossRef PubMed.
- V. K. Gupta, R. Kumar, A. Nayak, T. A. Saleh and M. A. Barakat, Adv. Colloid Interface Sci., 2013, 193–194, 24 CrossRef CAS PubMed.
- R. Saravanan, E. Sacari, F. G. Mohammad, M. Khan, E. Mosquera and V. K. Gupta, J. Mol. Liq., 2016, 221, 1029 CrossRef CAS.
- A. Mittal, D. Kaur, A. Malviya, J. Mittal and V. K. Gupta, J. Colloid Interface Sci., 2009, 337, 345 CrossRef CAS PubMed.
- V. K. Gupta, A. Mittal, D. Jhare and J. Mittal, RSC Adv., 2012, 2, 8381 RSC.
- V. K. Gupta, A. Mittal, L. Kurup and J. Mittal, J. Colloid Interface Sci., 2006, 304, 52 CrossRef CAS PubMed.
- R. Saravanan, V. K. Gupta, E. Mosquera, F. Gracia, V. Narayanan and A. Stephen, J. Saudi Chem. Soc., 2015, 19, 521 CrossRef.
- R. Saravanan, M. M. Khan, V. K. Gupta, E. Mosquera, F. Gracia, V. Narayanang and A. Stephen, RSC Adv., 2015, 5, 34645 RSC.
- G. Crini, Bioresour. Technol., 2006, 97, 1061 CrossRef CAS PubMed.
- R. Saravanan, V. K. Gupta, E. Mosquera and F. Gracia, J. Mol. Liq., 2014, 198, 409 CrossRef CAS.
- R. Saravanan, S. Karthikeyan, V. K. Gupta, G. Sekaran, V. Narayanan and A. Stephen, Mater. Sci. Eng., 2013, 33, 91 CrossRef CAS PubMed.
- R. Saravanan, S. Joicy, V. K. Gupta, V. Narayanan and A. Stephen, Mater. Sci. Eng., 2013, 33, 4725 CrossRef CAS PubMed.
- A. K. Jain and V. K. Gupta, J. Hazard. Mater., 2003, 101, 31 CrossRef CAS PubMed.
- V. K. Gupta, A. Mittal, D. Jhare and J. Mittal, RSC Adv., 2012, 2, 8381 RSC.
- T. A. Saleha and V. K. Gupta, Sep. Purif. Technol., 2012, 89, 245 CrossRef.
- S. Karthikeyan, V. K. Gupta, R. Boopathy, A. Titus and G. Sekaran, J. Mol. Liq., 2012, 173, 153 CrossRef CAS.
- T. A. Saleh and V. K. Gupta, Adv. Colloid Interface Sci., 2014, 211, 93 CrossRef CAS PubMed.
- T. A. Saleh and V. K. Gupta, J. Colloid Interface Sci., 2011, 362, 337 CrossRef CAS PubMed.
- M. Yari, M. Rajabi, O. Moradi, A. Yari, M. Asif, S. Agarwal and V. K. Gupta, J. Mol. Liq., 2015, 209, 50–57 CrossRef CAS.
- B. Enayatpour, M. Rajabi, M. Yari, S. M. R. Mirkhan, F. Najafi, O. Moradi, A. K. Bharti, S. Agarwal and V. K. Gupta, J. Mol. Liq., 2017, 231, 566 CrossRef CAS.
- F. Najafi and M. Rajabi, Int. Nano Lett., 2015, 5(4), 187 CrossRef CAS.
- D. Liu, W. Zhao, S. Liu, Q. Cen and Q. Xue, Surf. Coat. Technol., 2016, 286, 354 CrossRef CAS.
- C. He, L. Sun, C. Zhang, X. Peng, K. Zhang and J. Zhong, Solid State Commun., 2012, 152, 1560 CrossRef CAS.
- T. Wumair, J. D. Lu, Z. Mingde and C. X. Kang, Ionics, 2013, 19, 1855 CrossRef CAS.
- F. L. Michael, V. De, S. H. Tawfick, R. H. Baughman and A. J. Hart, Science, 2013, 339, 535 CrossRef PubMed.
- D. Robati, S. Bagheriyan, M. Rajabi, O. Moradi and A. A. Peyghan, Phys. Rev. E, 2016, 83, 1 CAS.
- P. Kanninen, M. Borghei, J. Hakanpää, E. I. Kauppinen, V. Ruiz and T. Kallio, J. Electroanal. Chem., 2017, 793, 48 CrossRef CAS.
- M. Rezaei-Sameti and E. Samadi Jamil, J. Nanostruct. Chem., 2016, 6, 197 CrossRef.
- S. B. Fagan, A. G. S. Filho, J. O. G. Lima, J. M. Filho, O. P. Ferreira, I. O. Mazali, O. L. Alves and M. S. Dresselhaus, Nano Lett., 2004, 4, 1285 CrossRef CAS.
- M. Rajabi, O. Moradi and A. Mazlomifar, Int. J. Nano Dimens., 2015, 6, 227 Search PubMed.
- M. T. Yagub, T. K. Sen, S. Afroze and H. M. Ang, Adv. Colloid Interface Sci., 2014, 209, 172 CrossRef CAS PubMed.
- V. K. Gupta, J. Environ. Manage., 2009, 90, 2313 CrossRef CAS PubMed.
- M. J. Ahmeda, J. Environ. Chem. Eng., 2016, 4, 89 CrossRef.
- K. Hunger, Industrial Dyes: Chemistry, Properties, Applications, Wiley-VCH, 2007 Search PubMed.
- T. W. Seow and C. K. Lim, Int. J. Appl. Eng. Res., 2016, 11, 2675 Search PubMed.
- D. Robati, B. Mirza, M. Rajabi, O. Moradi, I. Tyagi, S. Agarwal and V. K. Gupta, Chem. Eng. J., 2016, 284, 687 CrossRef CAS.
- V. K. Gupta, I. Ali, Suhas and D. Mohan, J. Colloid Interface Sci., 2003, 265, 257 CrossRef CAS PubMed.
- R. Liu, B. Zhang, D. Mei, H. Zhang and J. Liu, Desalination, 2011, 268, 111 CrossRef CAS.
- D. Robati, S. Bagheriyan and M. Rajabi, Int. Nano Lett., 2015, 5(3), 179 CrossRef CAS.
- Y. Qi, M. Yang, W. Xu, S. He and Y. Men, J. Colloid
Interface Sci., 2017, 486, 84 CrossRef CAS PubMed.
- A. Ozcan, E. M. Oncu and A. S. Ozcan, J. Hazard. Mater., 2006, 129, 244 CrossRef PubMed.
- M. Rajabi, B. Mirza, K. Mahanpoor, M. Mirjalili, F. Najafi, O. Moradi, H. Sadegh, R. Shahryari-ghoshekandi, M. Asif, I. Tyagi, S. Agarwalk and V. K. Gupta, J. Ind. Eng. Chem., 2016, 34, 130 CrossRef CAS.
- G. M. S. ElShafei, I. M. A. ElSherbiny, A. S. Darwish and C. A. Philip, Chem. Eng. Res. Des., 2014, 92, 461 CrossRef CAS.
- D. Robati, S. Bagheriyan, M. Rajabi, O. Moradi and A. A. Peyghan, Phys. Rev. E, 2016, 83, 1 CAS.
- J. G. Yu, X. H. Zhao, H. Yang, X. H. Chen, Q. Yang, L. Y. Yu, J. H. Jiang and X. Q. Chen, Sci. Total Environ., 2014, 482, 241 CrossRef PubMed.
- H. Khani and O. Moradi, J. Nanostruct. Chem., 2013, 3, 73 CrossRef.
- L. Tian, J. Zhang, H. Shi, N. Li and Q. Ping, J. Dispersion Sci. Technol., 2016, 37, 1059 CrossRef CAS.
- B. A. Fil, Part. Sci. Technol., 2016, 34, 118 CrossRef CAS.
- J. Zhang, M. Liu, Z. Liu, T. Yang, Q. He, K. Yang and H. Wang, J. Sol-Gel Sci. Technol., 2017, 82, 424 CrossRef CAS.
- D. Robati, B. Mirza, R. Ghazisaeidi, M. Rajabi, O. Moradi, I. Tyagi, S. Agarwal and V. K. Gupta, J. Mol. Liq., 2016, 216, 830 CrossRef CAS.
- D. M. Ruthven, Principles of Adsorption and Adsorption Processes, J. Wiley & Sons, New York, 1984 Search PubMed.
- T. W. Seow and C. K. Lim, Int. J. Appl. Eng. Res., 2016, 11, 2675 Search PubMed.
- D. Robati, M. Rajabi, O. Moradi, F. Najafi, I. Tyagi, S. Agarwal and V. K. Gupta, J. Mol. Liq., 2016, 214, 259 CrossRef CAS.
- C. Y. Kuo, C. H. Wu and J. Y. Wu, J. Colloid Interface Sci., 2008, 327, 308 CrossRef CAS PubMed.
- W. Konicki, I. Pełech, E. Mijowska and I. Jasińska, Clean: Soil, Air, Water, 2014, 42, 284 CrossRef CAS.
- Y. Yao, F. Xu, M. Chen, Z. Xu and Z. Zhu, Bioresour. Technol., 2010, 101, 3040 CrossRef CAS PubMed.
- R. M. Tinnacher, M. Holmboe, C. Tournassat, I. C. Bourg and J. A. Davis, Geochim. Cosmochim. Acta, 2016, 177, 130 CrossRef CAS.
- G. Vilardi, L. D. Palma and N. Verdone, Chin. J. Chem. Eng., 2017 DOI:10.1016/j.cjche.2017.06.026.
- A. Jain, R. Balasubramanian and M. P. Srinivasan, Chem. Eng. J., 2015, 273, 622 CrossRef CAS.
- R. Ben-Mansour, M. A. Habib, O. E. Bamidele, M. Basha, N. A. A. Qasem, A. Peedikakkal, T. Laoui and M. Ali, Appl. Energy, 2016, 161, 225 CrossRef CAS.
- L. A. Lane, X. Qian, A. M. Smith and S. Nie, Annu. Rev. Phys. Chem., 2015, 66, 521 CrossRef CAS PubMed.
- D. M. Ruthven, S. Farooq and K. S. Knaebel, Pressure Swing Adsorption, VCH, New York, 1994 Search PubMed.
- M. Rajabi, O. Moradi and K. Zare, Int. Nano Lett., 2017, 7, 35 CrossRef CAS.
- H. Li, D. Xiao, H. He, R. Lin and P. Zuo, Met. Soc. China, 2013, 23, 2657 CAS.
- M. Yari, M. Norouzi, A. H. Mahvi, M. Rajabi, A. Yari, O. Moradi, I. Tyagi and V. K. Gupta, Desalin. Water Treat., 2016, 57, 11195 CrossRef CAS.
- M. Shirmardi, A. H. Mahvi, B. Hashemzadeh, A. Naeimabadi, G. Hassani and M. Vosoughi Niri, Korean J. Chem. Eng., 2013, 30, 1603 CrossRef CAS.
- Y. Zeng, L. Zhao, W. Wu, G. Lu, F. Xu, Y. Tong, W. Liu and J. Du, J. Appl. Polym. Sci., 2013, 127, 2475 CrossRef CAS.
- G. Daneshvar Tarigh, F. Shemirani and N. Seif Maz'haric, RSC Adv., 2015, 5, 35070 RSC.
- M. Setareh Derakhshan and O. Moradi, J. Ind. Eng. Chem., 2014, 20, 3186 CrossRef CAS.
- O. Kerkez and Ş. S. Bayazit, J. Nanopart. Res., 2014, 16, 24 CrossRef.
- Z. Shahryari, A. Soltani Goharrizi and M. Azadi, Int. J. Water Resour. Environ. Eng., 2010, 2, 016 Search PubMed.
- W. A. Khanday, F. Marrakchi, M. Asif and B. H. Hameed, J. Taiwan Inst. Chem. Eng., 2017, 70, 32 CrossRef CAS.
- O. Moradi, Fullerenes, Nanotubes, Carbon Nanostruct., 2013, 21, 286 CrossRef CAS.
- A. F. Alkaim, Z. Sadik, D. K. Mahdi, S. M. Alshrefi, A. M. Al-Sammarraie, F. M. Alamgir, P. M. Singh and A. M. Aljeboree, Korean J. Chem. Eng., 2015, 32, 2456 CrossRef CAS.
- A. Ahmad, M. H. Razali, M. Mamat, F. S. B. Mehamod and K. A. M. Amin, Chemosphere, 2017, 168, 474 CrossRef CAS PubMed.
- Y. Yao, B. He, F. Xu and X. Chen, Chem. Eng. J., 2011, 170, 82 CrossRef CAS.
- J. Ma, F. Yu, L. Zhou, L. Jin, M. Yang, J. Luan, Y. Tang, H. Fan, Z. Yuan and J. Chen, ACS Appl. Mater. Interfaces, 2012, 4, 5749 CAS.
- H. Y. Zhu, R. Jiang, L. Xiao and G. M. Zeng, Bioresour. Technol., 2010, 101, 5063 CrossRef CAS PubMed.
- M. Omaish Ansari, R. Kumar, S. A. Ansari, S. P. Ansari, M. A. Barakat, A. Alshahrie and M. H. Cho, J. Colloid Interface Sci., 2017, 496(15), 407 CrossRef PubMed.
- S. Yang, L. Wang, X. Zhang, W. Yang and G. Song, Chem. Eng. J., 2015, 275, 315 CrossRef CAS.
- A. K. Mishra, T. Arockiadoss and S. Ramaprabhu, Chem. Eng. J., 2010, 162, 1026 CrossRef CAS.
- K. Zare, H. Sadegh, R. Shahryari-ghoshekandi, B. Maazinejad, V. Ali, I. Tyagi, S. Agarwal and V. K. Gupta, J. Mol. Liq., 2015, 212, 266 CrossRef CAS.
- F. M. Machado, C. P. Bergmann, E. C. Lima, M. A. Adebayo and S. B. Fagan, Mater. Res., 2014, 17, 153 CrossRef CAS.
- F. M. Machado, C. P. Bergmann, E. C. Lima, B. Royer, F. E. de Souza, I. M. Jauris, T. Calvete and S. B. Fagan, Phys. Chem. Chem. Phys., 2012, 14, 11139 RSC.
- E. Bazrafshan, F. Kord Mostafapour, S. Rahdar and A. H. Mahvi, Desalin. Water Treat., 2015, 54, 2241 CrossRef CAS.
- F. M. Machado, C. P. Bergmann, T. H. M. Fernandes, E. C. Lima, B. Royer, T. Calvete and S. B. Fagan, J. Hazard. Mater., 2011, 192, 1122 CrossRef CAS PubMed.
- C. H. Wu, J. Hazard. Mater., 2007, 144, 93 CrossRef CAS PubMed.
- W. Konicki, I. Pełech, E. Mijowska and I. Jasinska, Chem. Eng. J., 2012, 210, 87 CrossRef CAS.
- L. D. T. Prola, F. M. Machado, C. P. Bergmann, F. E. de Souza, C. R. Gally, E. C. Lima, M. A. Adebayo, S. L. P. Dias and T. Calvete, J. Environ. Manage., 2013, 130, 166 CrossRef CAS PubMed.
- M. Shirmardi, A. Mesdaghinia, A. H. Mahavi, S. Nasseri and R. Nabizadeh, Eur. J. Chem., 2012, 9, 2371 CAS.
- F. Geyikçi, Fullerenes, Nanotubes, Carbon Nanostruct., 2013, 21, 579 CrossRef.
- R. S. Ruoff and D. C. Lorents, Carbon, 1995, 33, 925 CrossRef CAS.
- J. P. Lu, Phys. Rev. Lett., 1997, 79, 1297 CrossRef CAS.
- J. P. Salvetat, J. M. Bonard, N. H. Thomson, A. J. Kulik, L. Forró, W. Benoit and L. Zuppiroli, Appl. Phys. A, 1999, 69, 255 CrossRef CAS.
- J. Chen, M. A. Hamon, H. Hu, Y. Chen, A. M. Rao, P. C. Eklund and R. C. Haddon, Science, 1998, 282, 95 CrossRef CAS PubMed.
- M. Ohnishi, T. Shiga and J. Shiomi, Phys. Rev. B, 2017, 95, 155 CrossRef.
|
This journal is © The Royal Society of Chemistry 2017 |
Click here to see how this site uses Cookies. View our privacy policy here.