DOI:
10.1039/C7RA00475C
(Paper)
RSC Adv., 2017,
7, 19205-19210
Hexagonal β-Na(Y,Yb)F4 based core/shell nanorods: epitaxial growth, enhanced and tailored up-conversion emission†
Received
12th January 2017
, Accepted 18th March 2017
First published on 30th March 2017
Abstract
To meet the increasing requirement, much effort has been devoted to enhance the emission intensity and tailor the emission color of rare earth phosphors. However, limited contributions have been made to the up-conversion (UC) of nanorods by complete epitaxial growth on each facet to achieve this requirement. In this study, we propose a facile epitaxial growth route to grow anisotropic hexagonal β-NaYF4:Yb3+/Ho3+@β-NaYbF4:Er3+, β-NaYF4:Yb3+/Ho3+@β-NaYF4, and β-NaYbF4:Er3+@β-NaYF4 core/shell nanorods, which were realized by adding hexagonal β-NaYF4:Yb3+/Ho3+ or β-NaYbF4:Er3+ nanorods as a core-nanostructure into a solution containing cubic α-NaYbF4:Er3+ or α-NaYF4 nanoparticles as the shell-precursor. During epitaxial growth-induced phase transformation, the precursor nanoparticles disappeared gradually in the solution and consequently corresponding β-phased shell yielded on each outer facet of each β-phased nanorod core. Eventually, the nanorod core was covered completely with a uniformly grown β-NaYbF4:Er3+ or β-NaYF4 shell. The UC emission of either β-NaYF4:Yb3+/Ho3+ or β-NaYbF4:Er3+ core can be enhanced by the outer shell due to the decrease in the number of surface defects. In addition, tailored UC emissions could be obtained by controlling the shell components and thickness, typically in the core/shell nanorods of β-NaYF4:Yb3+/Ho3+@β-NaYbF4:Er3+. The tunable colors with improved emission in these core/shell nanorods may find wider applications in multicolor labeling and anti-counterfeiting.
1. Introduction
Lanthanide-doped fluoride-based UC nanoparticles have received considerable attention in recent years due to their advantages, such as low autofluorescence, deep penetration with near-infrared (NIR) irradiation, high photo-stability, good chemical stability, and low cytotoxicity.1–4 Therefore, a wide range of studies have been taken to synthesize controllable morphologies and tunable sizes of nano-/microstructured UC crystals to find potential applications, such as sensors, infrared anti-counterfeiting labeling, biological labeling, imaging and drug delivery.5–13 Typically, the serious background noise resulting from the light excitation sources, ranging from ultraviolet to visible, limits the wide applications of down-conversion materials in the anti-counterfeiting field, while the lanthanide-doped UC materials excited by infrared light can eliminate such disadvantages.14,15 The lanthanide-doped UC phosphors with particular nanostructures and UC colors can further strengthen anti-counterfeiting.16
NaYF4 is regarded as one of the most effective UC luminescence matrices due to its low phonon energy (<400 cm−1). In addition, hexagonal β-NaYF4 always exhibits higher UC efficiency than cubic α-NaYF4.17–19 Recently, more and more efforts have been devoted to the growth of the shell on NaYF4 nanocrystals.20–22 It was reported that the coating shell can enhance the optical intensity of the core by minimizing the surface defects and consequently surface quenching. Furthermore, core/shell nanostructures can eliminate deleterious cross-relaxation between the activators, which are separated inside the different layers.23 To date, most of the studies have focused on sphere-like NaYF4 core nanocrystals with diameters ranging from 6 to 50 nm.1,5,8,24–28 However, the surface energies are not equal on different crystal faces for non-spherical crystals, and thus coating shells on larger sized or non-spherical crystals still needs further exploration. Recently, several studies have focused on synthesizing NaYF4 core-based core/shell nanorods with some oxides. For example, functional β-NaYF4@SiO2@mSiO2 core/shell nanorods have been developed in Zhao's group.3 Organic moieties, biomacromolecules and even nanoparticles can be grafted on the mesoporous silica shells to meet the applications in photo-inducing reaction, light-operated switch, multiple light responses, and so on. β-NaYF4@TiO2 nanorods have been grown to show enhanced photocatalytic activity under near-infrared irradiation.29 However, both SiO2 and TiO2 shells are optically inert and can be coated easily on the core surface by hydrolysis. Selective epitaxial growth on specific crystal planes of disk-like and rod-like β-NaYF4 have been proposed to realize multicolor UC emissions in single-particle level for anti-counterfeiting and multiplexed labeling applications.16,30 To the best of our knowledge, the growth of optically active shell completely covering β-NaYF4 or other related NaReF4 (Re = rare earth) nanorods in solution using α-NaYF4 nanoparticles as a shell precursor has never been reported.
In this article, shell-active β-NaYF4:Yb3+/Ho3+@β-NaYbF4:Er3+, and shell-inert β-NaYF4:Yb3+/Ho3+@β-NaYF4 and β-NaYbF4:Er3+@β-NaYF4 core/shell nanorods with a high reaction yield were synthesized via a facile hydrothermal method in the oleic acid–ethanol–deionized water system. The phase, morphology and core/shell nanostructure were characterized via X-ray powder diffraction (XRD), scanning electronic microscopy (SEM) and transmission electron microscopy (TEM), respectively. The UC emission of β-NaYF4:Yb3+/Ho3+ can be enhanced by coating either an optically active β-NaYbF4:Er3+ or an inert β-NaYF4 shell due to the surface passivation effect. In this way, with a coating of the inert β-NaYF4, the red emission of β-NaYbF4:Er3+ can also be improved. Tunable colors in the core/shell nanorods can be observed and they may find potential applications in multicolor labeling and anti-counterfeiting.
2. Experimental
2.1 Materials
Yttrium nitrate hexahydrate (99.9%) and ytterbium nitrate pentahydrate (99.9%) were purchased from Aladdin Reagents. Er2O3 (99.9%) and Ho2O3 (99.9%) were provided by Guangzhou Zhujiang Rare Earths Co., Ltd. and dissolved in dilute HNO3 under heating to prepare the Er(NO3)3 and Ho(NO3)3 solutions. Sodium hydroxide (NaOH, > 98%) and ammonium fluoride (NH4F, > 98%) were purchased from Guangzhou Chemical Reagent Factory. Ethanol (A.R.) and oleic acid (90%) were purchased from Tianjin Damao Chemical Reagent Factory. All the chemical reagents used in this experiment were received without further purification. Deionized (DI) water was used throughout.
2.2 Preparation
The preparation of the core nanorods. The β-NaReF4 nanorods were synthesized by a slightly modified literature procedure via a facile hydrothermal reaction.16 In a typical experiment, 5 mL oleic acid and 5 mL ethanol were first added to a 25 mL Teflon lining with vigorous stirring. Second, 1.5 mL DI water containing 7.5 mmol NaOH was added, followed by the addition of 1 mL NH4F (2 mol L−1) solution. Subsequently, 1 mL aqueous solution of Re(NO3)3 (0.4 mol L−1, Re = Y, Yb, Er and/or Ho at a certain percentage) was added. The final solution was kept stirring for another 30 min. The Teflon cup containing the resulting mixture solution was closed tightly and kept inside a stainless steel autoclave and the autoclave was transferred into an oven where it was then heated to 220 °C for 24 h. As the autoclave was cooled naturally to room temperature, the precipitates were separated by centrifugation, washed 5 times with DI water and ethanol, and finally dried in air at 70 °C for 12 h.
The synthesis of the shell precursor. The α-NaReF4 nanoparticles were synthesized using the same procedure as that for β-NaReF4 except for reaction temperature at 180 °C and reaction time of 1–4 h. After the reaction, the product was either purified for characterization or kept inside the autoclave with the mother liquid without further separation for the subsequent epitaxial growth.
The epitaxial growth of the shell on β-NaReF4 nanorods. A specific volume of α-NaReF4 nanoparticles, as shell precursor obtained for 2 h as described in the last paragraph, was poured into a 40 mL Teflon cup with vigorous stirring. Subsequently, one batch of the isolated β-NaReF4 nanorods, as described in the first paragraph in this section, was transferred into 4 mL ethanol and dispersed under ultrasonic irradiation for 10 min. The uniformly dispersed β-NaReF4 nanorods serving as core nanostructures were added dropwise into the 40 mL Teflon cup, which was kept stirring for another 30 min. The Teflon cup with a mixture of the β-phased nanorods, as core template, and the α-phased nanoparticles, as shell precursor, was then placed into an autoclave and heated at 220 °C for 12 h. As the autoclave was cooled naturally to room temperature, the precipitates were separated by centrifugation, washed 5 times with DI water and ethanol for, and then dried in air at 70 °C for 12 h. Each core template and shell precursor are denoted as the Q, P and R series. For the Q1-5 and P1-5 samples, the cores were β-NaYF4:0.20Yb3+, 0.02Ho3+ nanorods, while the shell precursors were 4, 8, 12, 16 and 20 mL of α-NaYbF4:0.02Er3+, and α-NaYF4 nanoparticles, respectively. For the R1-5 samples, the cores were β-NaYbF4:0.02Er3+ nanorods and the shell precursors were 4, 8, 12, 16 and 20 mL of α-NaYF4 colloid solutions.
2.3 Measurements
Structural characterization. To investigate the phase purity, samples were checked by X-ray powder diffraction (XRD) using a D8 ADVANCE diffractometer with Cu Kα radiation (λ = 0.154056 nm) at room temperature (RT). A step size of 0.02° was used with a scanning speed of 10° min−1 in 2θ degree. The scanning electron micrograph (SEM) was obtained using a FEI Quanta scanning electron microscope operated at 20 kV. Transmission electron microscopy (TEM) was performed on a JEOL JEM-2100 transmission electron microscope operated at 200 kV.
Up-conversion luminescence. The luminescence spectra were measured with Edinburgh Instruments FLS 920 equipped with a 5 W 980 nm laser diode.
3. Results and discussion
3.1 Cubic α-NaYbF4:0.02Er3+ shell precursor and hexagonal β-NaYF4:0.20Yb3+, 0.02Ho3+ core template
The phase purity of the cubic α-NaYbF4:0.02Er3+ obtained under 180 °C was confirmed by powder XRD. The samples displayed distinctively different XRD patterns at different reaction periods, as shown in Fig. S1.† The hydrothermal reactions for 1–4 h led to the formation of a pure cubic α phase. Weak diffraction peaks of its dynamically stable hexagonal β-NaYbF4 appeared after prolonging the reaction time to 6 h, and the peaks became more significant with longer reaction times.
The sample of α-NaYbF4:0.02Er3+ obtained for 2 h will be chosen as a typical shell precursor to build core/shell nanorods. The monodispersed cube-like nanoparticles around 18 nm in size can be identified by TEM images (Fig. 1a and c). Selected area electron diffraction (SAED) image (Fig. 1b) and the typical high-resolution transmission electron microscopy (HRTEM) image (Fig. 1d) indicate their good crystallization.
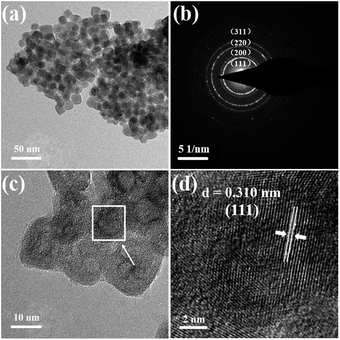 |
| Fig. 1 TEM images (a, c), SAED analysis (b) and HRTEM image (d) of α-NaYbF4:0.02Er3+ under 180 °C by hydrothermal treatment. HRTEM image were taken from the square region in (c). Legible lattice distance of 0.310 nm which matches well with the (111) crystal plane of α-NaYF4. In addition, the typical SAED further confirmed the formation of pure α-NaYF4 phase. | |
Pure hexagonal β-NaYF4:0.20Yb3+, 0.02Ho3+ was achieved by reacting 24 h under 220 °C (Fig. 2a). The morphology was investigated through SEM, as shown in Fig. 2b and uniform nanorods were observed with a length and diameter of ca. 1.5 μm and 150 nm, respectively. Fig. 2c displays a TEM image of one as-isolated β-NaYF4:0.20Yb3+, 0.02Ho3+ nanorod combined with its selected-area electron diffraction (SAED) patterns (Fig. 2d), confirming its single-crystalline nature and growth behaviour along 〈001〉 direction.
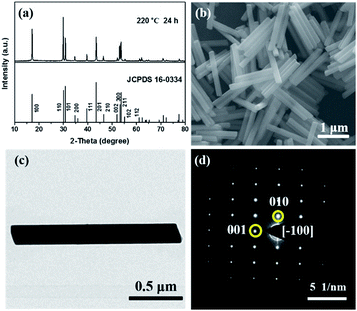 |
| Fig. 2 (a) XRD pattern, (b) SEM image, (c) TEM image of the as-synthesized β-NaYF4:0.20Yb3+, 0.02Ho3+ and (d) the SAED of the whole nanorod in TEM image. | |
3.2 β-NaYF4:Yb3+/Ho3+@β-NaYbF4:Er3+ core/shell architecture
After epitaxial growth, as described in the experimental section, no trace of α-NaYbF4 phase was detected by XRD, confirming that the α-NaYbF4:0.02Er3+ precursor had transformed completely into β-NaYbF4:0.02Er3+ (Fig. S2†). In order to study the present state of the resultant β-NaYbF4:0.02Er3+, TEM was taken into account to identify the nanostructures of Q samples obtained with different contents of the α-NaYbF4:0.02Er3+ precursor. Fig. 3a shows a scanning transmission electron microscopy (STEM) image of a single rod of Q1 sample (the component of Q samples was described in the experimental section) under high-angle annular dark-field (HAADF). The contrast between the core (dark) and shell (bright) is clearly distinguishable. The contrast can be attributed to the much larger atomic number of Yb (Z = 70) compared with Y (Z = 39).24 Considering the clearly different Yb3+ concentrations between β-NaYF4:0.20Yb3+, 0.02Ho3+ and NaYbF4:0.02Er3+, we can imagine that the much higher Yb3+ concentration sample, i.e. NaYbF4:0.02Er3+, has become the shell to cover the β-NaYF4:0.20Yb3+, 0.02Ho3+ nanorod with a lower Yb3+ component inside the core. To validate our hypothesis, we further measured the element mappings of Yb3+ and Y3+ for the specific nanorod, as presented in Fig. 3b–d. The distribution of Yb3+ and Y3+ shows that the core/shell nanostructure was formed. The corresponding EELS line scan analyses (Fig. 3e and f) revealed a higher Yb3+ component on the edge of the nanorod, which is consistent with the results of element mappings and further confirms the core/shell nanoarchitecture. In addition, the element mappings of Yb3+ and Y3+ for other Q samples are shown in Fig. 4. The coverage of Yb3+ on Y3+ becomes more significant and the shell becomes thicker with increasing volume of the precursor content. The abovementioned results indicate that the optically active α-NaYbF4:0.02Er3+ precursor changes successfully to β-NaYbF4:0.02Er3+ and consequently grows onto β-NaYF4:0.20Yb3+, 0.02Ho3+ core nanorods with epitaxial growth behavior due to the isostructure between hexagonal β-NaYbF4 and β-NaYF4.
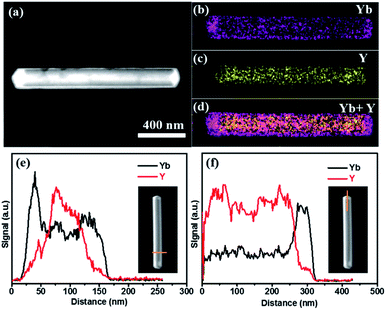 |
| Fig. 3 (a) Typical STEM in HAADF of Q1, (b) element mapping of Yb, (c) Y and (d) Yb + Y in the rod. Corresponding EELS line scan conducted through the cross section (e) and tip (f). | |
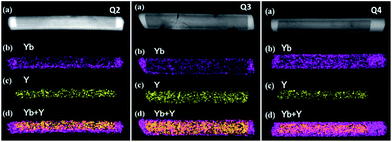 |
| Fig. 4 (a) Typical STEM in HAADF, (b) element mapping of Yb, (c) Y and (d) Yb + Y in the rod of Q2–Q4. | |
Based on the abovementioned results, the formation of hexagonal β-NaYF4:Yb3+/Ho3+@β-NaYbF4:Er3+ core/shell nanorods is shown in Scheme 1. First, the uniformly dispersed β-NaYF4:Yb3+/Ho3+ nanorods were mixed with α-NaYbF4:Er3+ nanoparticles in the mother liquid. Second, the mixture of the β-phased nanorods as the core template and the α-phased nanoparticles as shell precursor in Teflon cup was then transferred to an autoclave and heated at 220 °C for 12 h. Third, during epitaxial growth-induced phase transformation, the precursor nanoparticles gradually disappeared in the solution and consequently corresponding β-phased shell yielded on each outer facet of each β-phased nanorod core. Eventually, the nanorod core was completely covered with uniformly grown β-NaYbF4:Er3+ shell.
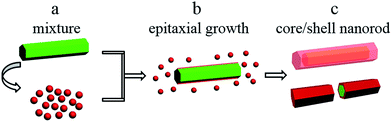 |
| Scheme 1 Illustration of the formation of hexagonal β-NaYF4:Yb3+/Ho3+@β-NaYbF4:Er3+ core/shell nanorods. | |
3.3 β-NaYF4:Yb3+/Ho3+@β-NaYbF4:Er3+ core/shell architecture
First, a comparison about UC emissions among lonely β-NaYF4:Yb3+/Ho3+, β-NaYbF4:Er3+ and core/shell nanostructured β-NaYF4:Yb3+/Ho3+@β-NaYbF4:Er3+ was made under 980 nm laser (0.2 W mm−2) excitation at ambient temperature to investigate the effect of the shell structure on the UC luminescence behaviors (Fig. 5). As shown in Fig. 5a1, β-NaYF4:0.20Yb3+, 0.02Ho3+ nanorods showed dominant emission peaks at 539 and 645 nm, which were assigned to the 5S2/5F4 → 5I8 and 5F5 → 5I8 transitions of Ho3+ ions, respectively.31 For β-NaYbF4:0.02Er3+, three emission bands centered at 519, 538 and 654 nm were observed (Fig. 5a2), which were assigned to 2H11/2 → 4I15/2, 4S3/2 → 4I15/2 and 4F9/2 → 4I15/2 transitions of Er3+, respectively.32 Among them, the red emission was remarkably significant. A faint peak attributed to 2H9/2 → 4I15/2 transition at 407 nm was found, which is due to a three-photon process. The unique UC luminescence behavior of the as-synthesized β-NaYF4:Yb3+/Ho3+@β-NaYbF4:Er3+ core/shell nanorod sample (Q5) is shown in Fig. 5a3. The typical emissions of Ho3+ and Er3+ co-existed in the sample. The emission bands at 519 and 653 nm corresponded to 2H11/2 → 4I15/2 and 4F9/2 → 4I15/2 transitions of Er3+, while the main band at 539 nm and a shoulder at 641 nm were attributed to 5S2/5F4 → 5I8 and 5F5 → 5I8 transitions of Ho3+, respectively. Two additional bands at 750 and 807 nm correspond to 5S2/5F4–5I7 transitions of Ho3+ and 4I9/2 → 4I15/2 transitions of Er3+, respectively.
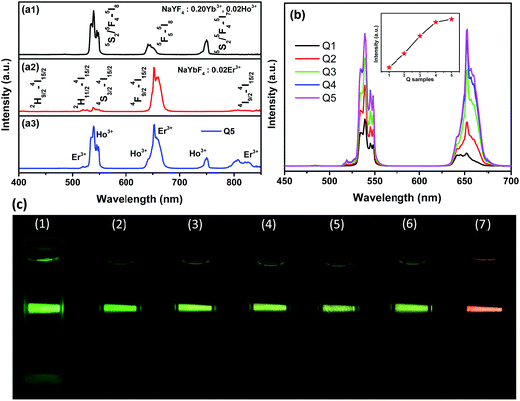 |
| Fig. 5 UC spectra of (a1) β-NaYF4:0.20Yb3+, 0.02Ho3+, (a2) β-NaYbF4:0.02Er3+, (a3) Q5, (b) Q1–Q5 samples under 980 nm laser excitation (0.2 W mm−2) at RT. (c) Corresponding luminescence photographs of the samples re-dispersion into PEG 200 under 980 nm laser excitation, samples no. 1–7 are β-NaYF4:0.20Yb3+, 0.02Ho3+, Q1, Q2, Q3, Q4, Q5, and β-NaYbF4:0.02Er3+, respectively. | |
Second, the shell thickness has a great effect on the UC emission. Fig. 5b displays the UC emission spectra of β-NaYF4:0.20Yb3+, 0.02Ho3+@β-NaYbF4:0.02Er3+ (from Q1 to Q5 sample with different amounts of each precursor) under 980 nm laser excitation. It can be seen that the emission intensities of both Er3+ and Ho3+ increase monotonically with increasing content of the precursor, i.e., the entire emission is enhanced with the shell coating. This results from surface passivation effects.8,33,34 The enhanced intensity of Er3+ was attributed to the increased content of precursor. From the corresponding luminescence photographs, as shown in Fig. 5c, we know that the successive adjustment of color output can be readily achieved by controlling the shell thickness, i.e. the volume of the precursory α-NaYbF4:Er3+ colloid solution.
Third, based on the epitaxial growth-induced phase transformation from cubic α-phase in solution to hexagonal β-one on the shell structure, the enhancement of optical performance of β-NaYF4:0.20Yb3+, 0.02Ho3+ and β-NaYbF4:0.02Er3+ (Fig. S3†) as respective cores can also be suggested by growing an optical inert β-NaYF4 material as the shell. The XRD and TEM image of α-NaYF4 precursor are shown in Fig. S4.† After epitaxial growth, the phase purity of P and R samples were confirmed by XRD, and the results are displayed in Fig. S5 and S6,† respectively. As shown in Fig. 6, the UC emission intensities of Ho3+ and Er3+ increase monotonically along with the increase of the content of α-NaYF4 as the precursor of the β-NaYF4 shell under our experimental condition. As considered previously,35 the simple mixture of optically active β-NaYF4:Yb3+/Er3+ and optically inert undoped NaYF4 would reduce the initial UC emission intensity of the optically active material. Herein, great enhancement of UC luminescence can be achieved, reflecting the surface passivation effect of the optically inert NaYF4 shell coating on β-NaYF4:0.20Yb3+, 0.02Ho3+ and β-NaYbF4:0.02Er3+ more intuitively (Fig. 6). The corresponding element mappings of Yb3+ and Y3+ for P5 and R5 (Fig. S7 and S8†) further confirm the core/shell architecture. Therefore, our proposed procedure for the core/shell nanostructure based on the epitaxial growth and the epitaxial growth-induced phase transformation may be a versatile route to realize optical enhancement and tailoring.
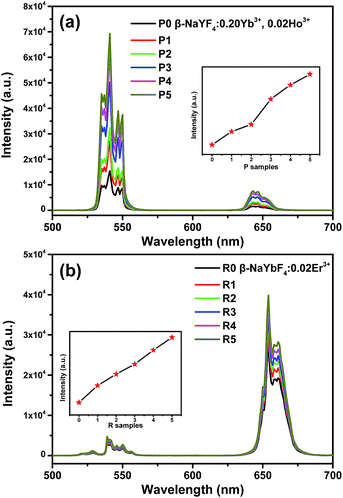 |
| Fig. 6 UC emission spectra of P0–P5 and R0–R5 under 980 nm laser excitation at RT. | |
4. Conclusions
We synthesized β-NaYF4:Yb3+/Ho3+@β-NaYbF4:Er3+ shell-active core/shell nanorods via a facile hydrothermal method. The phase, morphology, structure of α-phase precursor and β-phase nanorod template were confirmed by XRD, SEM and TEM. The different distributions of Yb3+ and Y3+ in the elemental mappings and line scan analyses proved the formation of core/shell architecture. UC luminescence enhancement was observed for β-NaYF4:Yb3+/Ho3+ after growing β-NaYbF4:Er3+ shell. In addition, the improved UC emission of β-NaYF4:Yb3+/Ho3+ and β-NaYbF4:Er3+ after the NaYF4 coating further confirms the surface passivation effect. Tailored UC emissions could be obtained by controlling the shell components and thickness in β-NaYF4:Yb3+/Ho3+@β-NaYbF4:Er3+ core/shell nanorods. The tunable colors with improved emission in these core/shell nanorods may find wider potential applications in multicolor labeling and anti-counterfeiting.
Acknowledgements
This study was financially supported by grants from the Joint Funds of the National Natural Science Foundation of China and Guangdong Province (No. U1301242), Research Fund for the Doctoral Program of Higher Education of China (RFDP) (No. 20130171130001), the National Natural Science Foundation of China (51672315, 21271190) and Guangdong Province (No. 2016A030313305), Special Fund of Guangdong Province Project for Applied Science and Technology Research and Development (No. 2016B090931007, 2015B090927002, 2013A090100010 and 2012B091000026), the Science and Technology research general project of Guangzhou (Grant No. 201607010360).
Notes and references
- M. Quintanilla, F. Q. Ren, D. L. Ma and F. Vetrone, ACS Photonics, 2014, 1, 662–669 CrossRef CAS.
- Q. Q. Su, S. Y. Han, X. J. Xie, H. M. Zhu, H. Y. Chen, C.-K. Chen, R.-S. Liu, X. Y. Chen, F. Wang and X. G. Liu, J. Am. Chem. Soc., 2012, 134, 20849–20857 CrossRef CAS PubMed.
- J. P. Yang, Y. H. Deng, Q. L. Wu, J. Zhou, H. F. Bao, Q. Li, F. Zhang, F. Y. Li, B. Tu and D. Y. Zhao, Langmuir, 2010, 26, 8850–8856 CrossRef CAS PubMed.
- Z. Chen, W. Zheng, P. Huang, D. T. Tu, S. Y. Zhou, M. D. Huang and X. Y. Chen, Nanoscale, 2015, 7, 4274–4290 RSC.
- X. Xu, Z. Wang, P. P. Lei, Y. N. Yu, S. Yao, S. Y. Song, X. L. Liu, Y. Su, L. L. Dong, J. Feng and H. J. Zhang, ACS Appl. Mater. Interfaces, 2015, 7, 20813–20819 CAS.
- S. H. Zheng, W. B. Chen, D. Z. Tan, J. J. Zhou, Q. B. Guo, W. Jiang, C. Xu, X. F. Liu and J. R. Qiu, Nanoscale, 2014, 6, 5675–5679 RSC.
- F. Wang, R. R. Deng, J. Wang, Q. X. Wang, Y. Han, H. M. Zhu, X. Y. Chen and X. G. Liu, Nat. Mater., 2011, 10, 968–973 CrossRef CAS PubMed.
- F. Wang, J. Wang and X. G. Liu, Angew. Chem., Int. Ed., 2010, 49, 7456–7460 CrossRef CAS PubMed.
- H.-Q. Wang and T. Nann, ACS Nano, 2009, 3, 3804–3808 CrossRef CAS PubMed.
- H. Zhang, Y. J. Li, I. A. Ivanov, Y. Q. Qu, Y. Huang and X. F. Duan, Angew. Chem., Int. Ed., 2010, 49, 2865–2868 CrossRef CAS PubMed.
- Z. Yin, H. Li, W. Xu, S. B. Cui, D. L. Zhou, X. Chen, Y. S. Zhu, G. S. Qin and H. W. Song, Adv. Mater., 2016, 28, 2518–2525 CrossRef CAS PubMed.
- H. Dong, L.-D. Sun, Y. F. Wang, J.-W. Xiao, D. T. Tu, X. Y. Chen and C.-H. Yan, J. Mater. Chem. C, 2016, 4, 4186–4192 RSC.
- Y. L. Dai, H. H. Xiao, J. H. Liu, Q. H. Yuan, P. A. Ma, D. M. Yang, C. X. Li, Z. Y. Cheng, Z. Y. Hou, P. P. Yang and J. Lin, J. Am. Chem. Soc., 2013, 135, 18920–18929 CrossRef CAS PubMed.
- H. H. Gorris and O. S. Wolfbeis, Angew. Chem., Int. Ed., 2013, 52, 3584–3600 CrossRef CAS PubMed.
- M. Haase and H. Schäfer, Angew. Chem., Int. Ed., 2011, 50, 5808–5829 CrossRef CAS PubMed.
- Y. H. Zhang, L. X. Zhang, R. R. Deng, J. Tian, Y. Zong, D. Y. Jin and X. G. Liu, J. Am. Chem. Soc., 2014, 136, 4893–4896 CrossRef CAS PubMed.
- H. Zhang, Y. J. Li, Y. C. Lin, Y. Huang and X. F. Duan, Nanoscale, 2011, 3, 963–966 RSC.
- M. L. Deng and L. Y. Wang, Nano Res., 2014, 7, 782–793 CrossRef CAS.
- L. M. Wang, X. Y. Li, Z. Q. Li, W. S. Chu, R. F. Li, K. Lin, H. S. Qian, Y. Wang, C. F. Wu, J. Li, D. T. Tu, Q. Zhang, L. Song, J. Jiang, X. Y. Chen, Y. Luo, Y. Xie and Y. J. Xiong, Adv. Mater., 2015, 27, 5528–5533 CrossRef CAS PubMed.
- H. Dong, L.-D. Sun, Y.-F. Wang, J. Ke, R. Si, J.-W. Xiao, G.-M. Lyu, S. Shi and C.-H. Yan, J. Am. Chem. Soc., 2015, 137, 6569–6576 CrossRef CAS PubMed.
- Y. Sun, X. J. Zhu, J. J. Peng and F. Y. Li, ACS Nano, 2013, 7, 11290–11300 CrossRef CAS PubMed.
- Y.-F. Wang, G.-Y. Liu, L.-D. Sun, J.-W. Xiao, J.-C. Zhou and C.-H. Yan, ACS Nano, 2013, 7, 7200–7206 CrossRef CAS PubMed.
- C. Zhang, L. Yang, J. Zhao, B. H. Liu, M.-Y. Han and Z. P. Zhang, Angew. Chem., Int. Ed., 2015, 54, 11531–11535 CrossRef CAS PubMed.
- K. A. Abel, J.-C. Boyer, C. M. Andrei and F. C. J. M. van Veggel, J. Phys. Chem. Lett., 2011, 2, 185–189 CrossRef CAS.
- B. Chen, D. F. Peng, X. Chen, X. S. Qiao, X. P. Fan and F. Wang, Angew. Chem., Int. Ed., 2015, 54, 12788–12790 CrossRef CAS PubMed.
- S. Ye, G. Y. Chen, W. Shao, J. L. Qu and P. N. Prasad, Nanoscale, 2015, 7, 3976–3984 RSC.
- C. X. Li and J. Lin, J. Mater. Chem., 2010, 20, 6831–6847 RSC.
- S. L. Gai, C. X. Li, P. P. Yang and J. Lin, Chem. Rev., 2014, 114, 2343–2389 CrossRef CAS PubMed.
- Y. W. Zhang and Z. L. Hong, Nanoscale, 2013, 5, 8930–8933 RSC.
- Y. H. Zhang, L. Huang and X. G. Liu, Angew. Chem., Int. Ed., 2016, 55, 5718–5722 CrossRef CAS PubMed.
- W. Gao, H. R. Zheng, Q. Y. Han, E. J. He, F. Q. Gao and R. B. Wang, J. Mater. Chem. C, 2014, 2, 5327–5334 RSC.
- M. Y. Ding, D. Q. Chen, S. L. Yin, Z. G. Ji, J. S. Zhong, Y. R. Ni, C. H. Lu and Z. Z. Xu, Sci. Rep., 2015, 5, 12745 CrossRef CAS PubMed.
- X. Y. Huang and J. Lin, J. Mater. Chem. C, 2015, 3, 7652–7657 RSC.
- D. M. Liu, X. X. Xu, F. Wang, J. J. Zhou, C. Mi, L. X. Zhang, Y. Q. Lu, C. S. Ma, E. Goldys, J. Lin and D. Y. Jin, J. Mater. Chem. C, 2016, 4, 9227–9234 RSC.
- T. Rinkel, A. N. Raj, S. Dühnen and M. Haase, Angew. Chem., Int. Ed., 2016, 55, 1164–1167 CrossRef CAS PubMed.
Footnote |
† Electronic supplementary information (ESI) available. See DOI: 10.1039/c7ra00475c |
|
This journal is © The Royal Society of Chemistry 2017 |
Click here to see how this site uses Cookies. View our privacy policy here.