DOI:
10.1039/C7RA00368D
(Paper)
RSC Adv., 2017,
7, 11191-11197
Ex situ Cu(0) nanoparticle mediated SET-LRP of methyl methacrylate/styrene-methyl methacrylate in a biphasic toluene–water system†
Received
10th January 2017
, Accepted 7th February 2017
First published on 13th February 2017
Abstract
The present paper described the first successful use of ex situ copper(0) nanoparticles as an efficient catalyst vis-a-vis using toluene as an effective solvent when doped with water for SET-LRP. Copper(0) nanoparticles (Cu(0) nanoparticles) of ∼5 nm were used as a catalyst with different nitrogen(N)-ligands for the single-electron transfer mediated LRP (SET-LRP) of methyl methacrylate (MMA) using a biphasic water–toluene system as the reaction media. The polymerization was studied by varying the catalyst concentration (0.15 ppm to 28.5 ppm) as well as by varying the mole ratios of monomer, initiator and N-ligands such as N,N,N′,N′′,N′′′-pentamethyldiethylene-triamine (PMDETA), N,N,N′,N′-tetramethyl-1,6-hexanediamine(TMHDA), N,N,N′,N′-tetramethylethylenediamine (TMEDA) and N,N-dimethylhexadecylamine (DMHA). Among the various N-ligands studied PMDETA provided best control over molecular weight while TMHDA gave worst control resulting in a polydispersity of 1.15 and 2.11, respectively at high monomer conversion. The rate of polymerization (kappp) of MMA using Cu(0) nanoparticles/PMDETA at 25 °C and 70 °C was found to be 0.00076 min−1 and 0.0048 min−1, respectively. Under these polymerization conditions, the reactivity ratio of MMA and styrene (St) was found to be 0.41 and 0.23 at 70 °C, respectively.
Introduction
The progress in controlled/living radical polymerization (LRP) is remarkably fuelled by researchers for its control over polymer architectures, compositions and functionalities.1–3 The most widely used LRP techniques that are receiving the greatest attention are nitroxide-mediated radical polymerization (NMP),4 atom transfer radical polymerization (ATRP)1,5 and reversible addition-fragmentation chain transfer (RAFT).6 Among these techniques, ATRP is a metal-catalyzed process which requires an alkyl halide initiator and transition metal catalyst in the lower oxidation state, i.e. Cu(I) that is relatively sensitive to air.7 In recent years, increasing efforts have been made towards improvement in the ATRP process.1,5 To date, activators regenerated by electron transfer (ARGET-ATRP) and initiators for continuous activator regeneration (ICAR-ATRP) are two promising techniques that involve the use of oxidatively stable transition metal catalyst i.e. CuBr2 which in situ reduces to Cu(I) by using reducing agents, for example ascorbic acid in ARGET-ATRP and AIBN in ICAR-ATRP. These techniques are advantageous as they provide a remarkable reduction in the amount of the metal catalyst which is required for the ATRP.8
Around the same time that ARGET and ICAR-ATRP were being developed, Percec et al. reported an another low copper concentration method of controlled/living polymerization named as ‘‘single-electron transfer living radical polymerization’’ (SET-LRP), which is based on the use of Cu(0) as the source of the transition metal in conjunction with N-ligands and initiators.9–15 This technique has many attributes in common with ATRP, however, it uses Cu(0) in place of Cu(I) salts in the absence of an inherent oxidizing agent. Among the different methods of LRP,1,4–6 SET-LRP: Percec's technique,9–15 has several advantages, i.e., it requires low catalyst concentration, ambient polymerization temperature and resulting in ultrafast rate of polymerization along with perfect control over molecular weight with narrow polydispersity.16 There are technical merits of using Cu(0) as LRP catalyst over Cu(I) and Cu(II) complexes.17 Furthermore, the polymerization rates are higher in comparison to ATRP systems, and polymerizations are often carried out at room temperature. This is due to faster activation (kact) through the outer sphere electron transfer (OSET) process mediated by Cu(0) as compared to the inner sphere electron transfer (ISET) process in conventional ATRP.
Percec et al.9 reported that in SET-LRP, Cu(0) and Cu(II)X2 species were formed in situ through the disproportionation of Cu(I)X in the presence of N-ligands in dipolar aprotic solvents such as DMSO, DMF, alcohols, ionic liquids, and N-methyl-2-pyrolidone.18–21 The extent of disproportionation of Cu(I)X is highly dependent on the type of ligands and solvent used.22 SET-LRP of vinyl monomers at ambient temperature in DMSO, toluene and acetonitrile shows that DMSO accelerates the electron transfer activation as well as disproportionation, whereas, disproportionation is unfavourable in toluene23 and acetonitrile.24 SET-LRP can also be performed with good efficiency in binary solvent system like organic solvent–H2O.25 Zhu et al.,26 reported the use of toluene as solvent in SET-LRP using Cu(0) in situ generated from CuSO4·5H2O/N2H4·H2O as catalyst. They could not observe the designated limitation of toluene as improper solvent in SET-LRP and stated that presence of water in CuSO4·5H2O/N2H4·H2O might have played the role in making toluene as a proper solvent. It is also important to state that water has the highest intrinsic disproportionation constant for Cu(I)X.9,23,26–28
To bring the clarity of above finding, we herein report for the first time SET-LRP of MMA by using ex situ synthesized Cu(0) nanoparticles (∼5 nm) as catalyst and PMDETA as ligand in a toluene/H2O solvent system at different temperatures (Scheme 1). We have also minimized Cu(0) concentration up to 0.15 ppm with reasonable monomer conversion. To the best of our knowledge, no one has reported polymerization at this low concentration of Cu(0) as catalyst and toluene doped water as solvent. Copolymerization of MMA and St by SET-LRP was also investigated using this solvent and catalyst system.
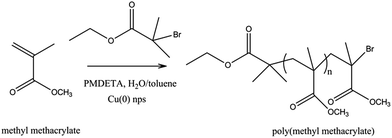 |
| Scheme 1 Synthesis of poly(methyl methacrylate) via SET-LRP using copper nanoparticles in water doped toluene solvent system. | |
Experimental
Materials
CuCl2·2H2O from Sigma Aldrich (>99.99%) was used as a precursor for the preparation of Cu(0) nanoparticles. L-Ascorbic acid was procured from Sigma Aldrich (AR grade, >99.5%) and HPLC grade deionized water was used. Methyl methacrylate (MMA) and styrene (St) were purchased from Sigma-Aldrich and were purified by passing through a neutral aluminium oxide column. Ethyl 2-bromoisobutyrate (EBriB) from Sigma-Aldrich was distilled over CaH2 under high vacuum and stored at −20 °C under N2 atmosphere. Dimethylforamide (DMF) from Sigma-Aldrich was dried with CaH2 and distilled under high vacuum for further purification. Tetrahydrofuran (THF, 99%) was refluxed over sodium and then distilled. Ligands N,N,N′,N′′,N′′′-pentamethyldiethylene-triamine (PMDETA, 99%), N,N,N′,N′-tetramethyl-1,6-hexanediamine (TMHDA, 99%), N,N,N′,N′-tetramethylethylenediamine (TMEDA, 99.5%) and N,N-dimethyl-hexadecylamine (DMHA, 95%) were obtained from Sigma-Aldrich and used as received. All the polymerization reactions were carried out in a glass ampoule (17 × 2 cm) fitted with a rubber septum and a detachable high vacuum stopcock containing Teflon coated magnetic stirrer.
Synthesis of Cu(0) nanoparticles
Cu(0) nanoparticles were synthesized from CuCl2·2H2O by following the literature procedure.29 In a typical synthesis aqueous solution of CuCl2·2H2O was prepared by dissolving CuCl2·2H2O (10 mmol, 1.70 g) in 50 ml HPLC grade deionized water and heated to 80 °C in an oil bath under stirring. Then, 50 ml of L-ascorbic acid (0.5 M) aqueous solution was added drop wise under constant stirring. The temperature was maintained until solution colour changed to dark brown. The resulting dispersed solution of copper particles was centrifuged at 8000 rpm for 15 min. Then supernatant was stored under ambient conditions, characterized by SEM, TEM and UV (λmax = 400–650 nm) and used for polymerization reactions. 200 μl of supernatant has the concentration of Cu(0) 28.5 ppm (ICP-AES). Hereafter, the concentration of Cu(0) nanoparticles will be described in ppm.
SET-LRP of MMA by using Cu(0) nanoparticles
In a typical polymerization procedure, MMA (0.018 mol) and Cu(0) nanoparticles (28.5 ppm) and water/toluene (2 ml, 1
:
0.1 (v/v)) was added into a dried and evacuated ampoule under stirring to provide a well-dispersed solution. After sealing with a rubber septum, the ampoule was evacuated and then purged with nitrogen (3 cycles) to remove oxygen. Degassed PMDETA (200 μl, 0.95 mmol) was added into the ampoule and kept in thermostatic oil bath at the desired temperature to polymerize under stirring. Then the initiator, EBriB (100 μl, 0.68 mmol) was added via a gas tight syringe to commence the polymerization. After the desired polymerization time, the reaction mixture was put in ice cold bath and diluted by THF and polymer was precipitated by adding excess of cold methanol. Obtained white colour polymer was dried under vacuum which is free of copper contamination. Mole ratio of [MMA]0/[EBriB]0/[PMDETA]0 is 100
:
4
:
5. FT-IR (ESI, Fig. S1†): ν = 1731 cm−1 (C
O), 2997–2846 cm−1 (aliphatic –CH) and peaks at 1263–1058 cm−1 (–C–O– (ester) linkage). 1H NMR (500 MHz, CDCl3, δ): 3.57 (–OCH3), peaks at 1.20, 1.04 and 0.91 ppm corresponding to the α-CH3 protons with tacticity, i.e., mm, mr, rr, respectively, 1.4–2.1 (CH2).
Chain extension reaction
A predetermined quantity of the resultant PMMA (Mn, GPC = 18
487 g mol−1, Mw/Mn = 1.24) synthesized by SET-LRP as discussed above, was used as initiator for chain extension reaction of MMA. The molar ratio of [MMA]0/[PMMA-Br]0/[PMDETA]0 was kept at 100
:
0.1
:
5. The chain extension experiment was carried out under the same condition as above. The GPC curve (Fig. 5) is monomodal and symmetrical in nature and there is a definitive shift towards higher molar mass region indicating the occurrence of chain extension process.
Copolymerization of MMA and styrene by SET-LRP using Cu(0) nanoparticles
SET-LRP of MMA and styrene in the presence of Cu(0) nanoparticles was carried out in different feed ratio of [MMA]0/[St]0. In general, mole ratio of [St]0/[MMA]0/[EBriB]0/[PMDETA]0 used is 100
:
100
:
3
:
2. In this process, monomers (MMA, 2.81 ml, 20 mmol; St, 2.61 ml, 20 mmol), initiator (EBriB, 100 μl, 0.68 mmol), catalyst (Cu(0) nanoparticles, 100 μl, 14.6 ppm), and ligand (PMDETA, 100 μl, 47.5 mmol) were added to an ampoule in the following order: Cu(0) nanoparticles, monomers, ligand, and solvent. After sealing the ampoule with a rubber septum, the ampoule was evacuated, purged with nitrogen (3 cycles) to remove oxygen and transferred to a thermostat at 70 °C, and then initiator was added. After the desired polymerization time, the reaction was quenched by cooling and diluted with THF. The polymer was precipitated in a large excess of methanol, filtered and dried in vacuum overnight. FT-IR spectrum of PMMA-co-PSt shows characteristics peaks of both MMA and St (ESI, Fig. S1†). In FT-IR spectrum vibrational peaks at 3058 and 3025 cm−1 (aromatic = C–H of St), 1491, 1448, 1600 cm−1 (phenyl stretching) of styrene and the peaks at 2921 and 2849 cm−1 (aliphatic –C–H), 1731 cm−1 (C
O) of MMA is observed.
Characterization techniques
Molecular weight distribution and polydispersity index of synthesized polymers were determined by using Agilent HPLC/GPC system comprising of 1200 infinity series precision pump, 1200 Series Diode Array detector & 1260 infinity Evaporative Light Scattering Detector. Poly(methyl methacrylate) standards were used for calibration of the system. FT-IR spectra were collected on a Nicolet 8700 FT-IR spectrometer in the region of 4000–400 cm−1. 1H NMR spectra were recorded on a Bruker Avance III 500 MHz NMR spectrometer operating at 500.13 MHz resonance frequency for 1H. Approximately 5 (w/v%) of the polymer solution was prepared in CDCl3 (Merck, 99.8% containing 0.03 v% for 1H TMS) for acquiring 1H NMR spectra. SEM images were obtained on a FEI Quanta 200 F using tungsten filament doped with lanthanum hexaboride (LaB6) as an X-ray source, fitted with an ETD (Everhart Thornley Detector), which preferentially work as a secondary electron detector. The sample for SEM was prepared by dispersing the sample on an adhesive coated carbon paper followed by gold coating. TEM images were obtained on Tecnai G2 20 TEM with acceleration voltage of 20 kV to 200 kV, magnification of 25× to 1100k×, having LaB6 cathode. UV spectra were recorded on a Perkin-Elmer Lambda-19 UV-Vis-NIR spectrometer. ICP-AES analysis was carried out by inductively coupled plasma atomic emission spectrometer (ICP-AES, DRE, PS-3000UV, Leeman Labs Inc., USA). Samples for ICP-AES were prepared by leaching out 0.01 g of sample with HNO3 (conc.), and then heated for 30 min and volume to 10 ml.
Results and discussion
Synthesis of Cu(0) nanoparticles
The UV-Vis spectrum of dispersed Cu(0) nanoparticles in aqueous medium was matches well with the literature (ESI, Fig. S2†).29 In UV-Vis spectrum, a wide shoulder in the range of 400–650 nm has been observed. The average particle size was determined by TEM and was found to be 5 nm (Fig. 1a). The SEM image of Cu(0) nanoparticles shows leaf like pattern (Fig. 1b and c), which is probably arisen due to the drying of copper solution on carbon tape.
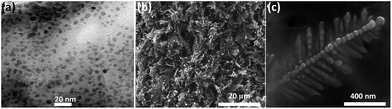 |
| Fig. 1 (a) TEM image of Cu(0) nanoparticles showing ca. 5 nm size of Cu(0) nanoparticles; (b and c) SEM image of Cu(0) nanoparticles at different magnification showing leaf like arrangement of Cu(0) nanoparticles. | |
SET-LRP of MMA using Cu(0) nanoparticles
The synthesized copper(0) nanoparticles dispersed in water were used as catalyst for SET-LRP of MMA in the presence of various N-ligands. Among the different N-based ligands such as PMDETA, TMHDA, TMEDA, and DMHA, PMDETA has been considered for the detailed study.30 The selection of a suitable solvent in SET-LRP is crucial since solvent exerts a strong influence on the polymerization kinetics. It is well known that dipolar aprotic solvents such as DMSO, DMF, NMP etc. are the preferred for SET-LRP.18–21 In addition, binary solvent systems like 50
:
50 THF/H2O,20 50
:
50 DMF/H2O,31 even beers, wine, ciders and spirits32 are also found to be effective solvents for water soluble monomers. Even, toluene which is reported to be unsuitable solvent for SET-LRP is converted into suitable by combining with phenol.33 With this background, in this work, a binary solvent system composed of toluene/H2O (1
:
0.1 v/v, for Cu(0) nanoparticles dispersed in 200 μl of water) and EBriB, an efficient initiator are used for polymerization.34 SET-LRP with different N-ligands such as PMDETA, TMHDA, TMEDA and DMHA using different concentration of Cu(0) nanoparticles was carried out to check the effect of Cu(0) nanoparticles concentration on different ligands. The molar ratio of [M]0/[I]0/[L]0 was maintained at 200
:
0.2
:
0.3 and the time of polymerization was 3 h in all the reactions. Concentrations of copper nanoparticles were varied from 28.5 ppm to 0.15 ppm (Table 1(a–e)). It was observed that when the concentration of Cu(0) nanoparticles was 7.40 ppm, monomer conversion for ligand PMDETA and TMHDA was ∼85–90 wt% in 180 min whereas for TMEDA and DMHA, conversion was ∼28 wt% only after 180 min (entry 1–4, Table 1b). Similar trend was observed when concentration of Cu(0) nanoparticles reduced to 0.75 ppm (Table 1d). Cheng et al.30 observed that there was no polymerization occurred when the concentration of Cu(0) decreases to 2.5 ppm but in the present study, polymerization with monomer conversion of 25 wt% and dispersity (Ð) 1.29 at 0.15 ppm of Cu(0) nanoparticles concentration (entry 1, Table 1e) was observed. Overall by using Cu(0) nanoparticles of 5 nm, polymerization is very fast with good conversion of monomer by using PMDETA and TMHDA as ligands. It is interesting to note that polymers with narrow polydispersity was obtained by using PMDETA as ligand at different concentration of Cu(0) nanoparticles. But with TMHDA, control over dispersity was very poor and high molecular weight of polymers was obtained. So among the different N-based ligands such as PMDETA, TMHDA, TMEDA and DMHA, PMDETA has been considered for the detailed study. The calculations of Mn,theo indicates that catalyst works well with PMDETA ligand only, while other ligands have lot of difference between Mn,theo and Mn,GPC values (Table 1a–e).
Table 1 (a–e) Effect of Cu(0) nanoparticle concentrations on various ligands with mole ratio of [M]0/[I]0/[L]0. All SET-LRP reactions were carried out at 70 °C
S. No. |
Ligand |
Conv. (%) |
Mn |
Mn,theo |
Ð |
(a) M/I/L: 200/0.2/0.3, Cu nanoparticles: 28.5 ppm, time: 3 h |
1 |
PMDETA |
45 |
65 048 |
21 345 |
1.41 |
2 |
TMEDA |
38 |
74 696 |
18 055 |
1.42 |
3 |
TMHDA |
36 |
94 880 |
17 115 |
1.44 |
4 |
DMHD |
21.1 |
17 889 |
10 112 |
1.45 |
![[thin space (1/6-em)]](https://www.rsc.org/images/entities/char_2009.gif) |
(b) M/I/L: 200/0.2/0.3, Cu nanoparticles: 7.40 ppm, time: 3 h |
1 |
PMDETA |
84.5 |
28 958 |
39 910 |
1.15 |
2 |
TMEDA |
27.7 |
134 870 |
13 214 |
1.68 |
3 |
TMHDA |
89.8 |
58 058 |
42 401 |
2.11 |
4 |
DMHD |
25.6 |
41 159 |
12 227 |
1.55 |
![[thin space (1/6-em)]](https://www.rsc.org/images/entities/char_2009.gif) |
(c) M/I/L: 200/0.2/0.3, Cu nanoparticles: 1.50 ppm, time: 3 h |
1 |
PMDETA |
60 |
— |
— |
— |
2 |
TMEDA |
15 |
— |
— |
— |
3 |
TMHDA |
27.8 |
70 108 |
13 261 |
1.74 |
4 |
DMHD |
35.1 |
88 830 |
16 692 |
1.48 |
![[thin space (1/6-em)]](https://www.rsc.org/images/entities/char_2009.gif) |
(d) M/I/L: 200/0.2/0.3, Cu nanoparticles: 0.75 ppm, time: 3 h |
1 |
PMDETA |
38 |
59 573 |
18 055 |
1.49 |
2 |
TMEDA |
21.1 |
74 234 |
10 112 |
1.74 |
3 |
TMHDA |
39.5 |
97 343 |
18 760 |
1.87 |
4 |
DMHD |
No yield |
— |
— |
— |
![[thin space (1/6-em)]](https://www.rsc.org/images/entities/char_2009.gif) |
(e) M/I/L: 200/0.2/0.3, Cu nanoparticles: 0.15 ppm, time: 3 h |
1 |
PMDETA |
25 |
13 982 |
11 945 |
1.29 |
2 |
TMEDA |
Negligible |
— |
— |
— |
3 |
TMHDA |
No yield |
— |
— |
— |
4 |
DMHD |
No yield |
— |
— |
— |
Fig. 2 shows the kinetic studies for the Cu(0) nanoparticles/PMDETA catalyzed SET-LRP of MMA initiated by EBriB in toluene/H2O solvent system at 25 °C and 70 °C. Plot of monomer conversion and ln([M]0/[M]t) versus reaction time at 25 °C are shown in Fig. 2a which follows first order polymerization kinetics with kappp = 0.00076 min−1 with an induction period of about 90 min.
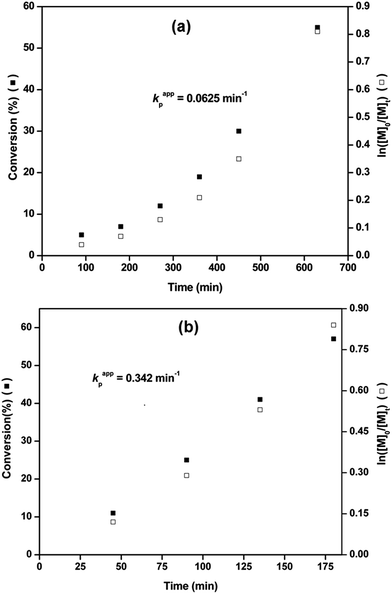 |
| Fig. 2 Plots of time versus monomer conversion and ln([M]0/[M]t) in the Cu(0) nanoparticles/PMDETA catalyzed SET-LRP of MMA initiated by EBriB at (a) 25 °C (b) 70 °C, using 5 nm particle size of Cu(0) nanoparticles. Polymerization conditions: MMA = 2 ml (1.88 g), MMA/toluene = 1 : 1 (v/v), Cu(0) nanoparticles = 28.5 ppm, [MMA]0 = 4.7, [MMA]0/[EBriB]0/[PMDETA]0 = 100 : 4 : 5. | |
Similarly, kinetic plot of SET-LRP of MMA at 70 °C under same reaction conditions shows first order reaction (kappp = 0.0048 min−1, Fig. 2b) indicating that polymerization was proceeded with an approximate constant concentration of active radicals with an induction period of about 23 min.
Fig. 3 describes the plot of number average molecular weight (Mn, GPC) and dispersity (Mw/Mn) as a function of the monomer conversion at 25 °C and 70 °C with time using Cu(0) nanoparticles dispersed in water as catalyst.
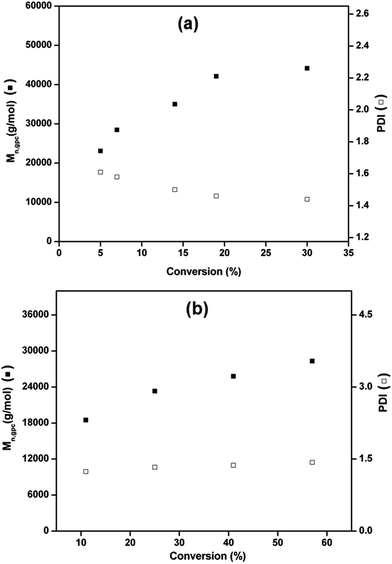 |
| Fig. 3 Plot of number average molecular weight (Mn, GPC) and Ð (Mw/Mn) as functions of the monomer conversion at (a) 25 °C, (b) 70 °C showing linear increase of molecular weight of PMMA with monomer conversion, whereas, Ð decreases from 1.6 to 1.4 with increasing conversion at 25 °C and remains below 1.5 at 70 °C. Polymerization conditions: MMA = 2 ml (1.88 gm), MMA/toluene = 1 : 1 (v/v), Cu(0) nanoparticles = 28.5 ppm, [MMA]0 = 4.7, [MMA]0/[EBriB]0/[PMDETA]0 = 100 : 4 : 5. | |
The results shows that the molecular weight of PMMA increases linearly with conversion, whereas, polydispersity decreases from 1.6 to 1.4 with increasing conversion at 25 °C (Fig. 3a). Molecular weight of PMMA increases linearly with monomer conversion whereas, dispersity remains below 1.5 for SET-LRP at 70 °C as shown in Fig. 3b.
Chain end functionality and chain extension
One of the most important criteria of “livingness” is the retention of chain end functionality in the polymer. The chain end of PMMA prepared by SET-LRP was analyzed by 1H NMR spectroscopy (Fig. 4i). The observed signals at δ = 4.08–4.2 ppm corresponds to –OCH2 and 1.12–1.19 ppm corresponds to terminal –CH3 attached to –OCH2 and two (–CH3) adjacent to carbonyl group protons of ethyl 2-bromoisbutyrate respectively. The above NMR chemical shifts of these peaks along with the compared intensities with respect to PMMA peaks confirmed that the initiator moieties of ethyl 2-bromoisbutyrate are attached to the polymer chain ends. The chemical shifts at δ = 0.8, 1.0 and 1.2 ppm can be ascribed to syndiotactic (rr), atactic (mr) and isotactic (mm) methyl groups of PMMA, respectively. The Mn determined by 1H NMR was found to be Mn, NMR = 20
195 g mol−1 which is closer to Mn as determined by GPC (Mn, GPC = 18
487 g mol−1).
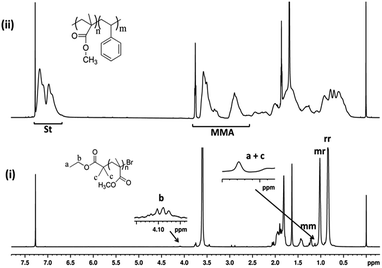 |
| Fig. 4 (i) 1H NMR spectrum of PMMA synthesized by Cu(0) nanoparticles mediated SET-LRP. Reaction conditions: [MMA]0/[EBriB]0/[PMDETA]0 = 100 : 4 : 5, Cu(0) nanoparticles = 28.5 ppm, MMA/toluene = 1 : 1 (v/v), [MMA]0 = 4.70 M, Temp = 70 °C, reaction time = 45 min, monomer conversion ∼11%; (ii) 1H NMR spectrum of copolymer of MMA and St synthesized by SET-LRP using Cu(0) nanoparticles as catalyst and PMDETA as ligand, initiated by EBriB. Reaction conditions: [St]0/[MMA]0/[EBriB]0/[PMDETA]0 = 100 : 100 : 3 : 2, Cu(0) nanoparticles = 14.3 ppm, Temp = 70 °C, reaction time = 3 h, monomer conversion ∼ 11%. | |
Further, the livingness of synthesized polymer can be investigated by the chain extension reaction. It is only possible when the retention of the chain end functionality happens to be in higher percentage of synthesized polymer.
Thus, the obtained PMMA can be used as a macro initiator to conduct a chain extension reaction to check the living character of polymer. Therefore, PMMA (Mn, GPC = 18
487 g mol−1, Mw/Mn = 1.24) obtained from above reaction was used as predecessor in chain extension experiment with fresh MMA. As shown in GPC (Fig. 5), there is a peak shift to higher molecular weight after the extended chain of PMMA (Mn, GPC = 76
566 g mol−1, Mw/Mn = 1.34). It further confirms the features of controlled/living radical polymerization of MMA by SET-LRP.
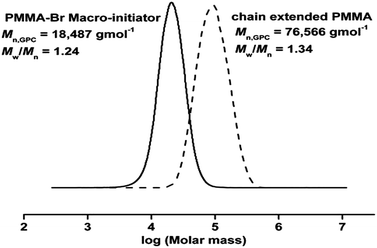 |
| Fig. 5 Monomodal GPC curves of PMMA-Br macro-initiator before (solid line) and after (dashed) chain extension with MMA. Reaction conditions: original PMMA: [MMA]0/[EBiB]0/[PMDETA]0 = 100 : 4 : 5, Cu(0) nanoparticles = 28.5 ppm, MMA/toluene = 1 : 1 (v/v), [MMA]0 = 4.70 M, Temp = 70 °C, reaction time = 45 min, monomer conversion = 11%; chain extended PMMA: [MMA]0/[PMMA-Br]0/[PMDETA]0 = 100 : 0.1 : 5, Cu(0) nanoparticles = 28.5 ppm, reaction time = 48 h, monomer conversion = 29%. | |
Effect of catalyst concentration and variation of ligands in SET-LRP
We have carried out SET-LRP with different N-ligands such as PMDETA, TMHDA, TMEDA and DMHA using water dispersed Cu(0) nanoparticles as catalyst as described in experimental section. The molar ratio of [M]0/[I]0/[L]0 used was 200
:
1.2
:
2.3 and the concentration of Cu(0) nanoparticles was 7.40 ppm, where monomer conversion for ligand PMDETA and TMHDA was ∼85–90 wt% in 90 min, whereas for TMEDA and DMHA, conversion was ∼28 wt% only after 180 min (Table 1b). Similar trend was observed when concentration of Cu(0) nanoparticles reduced to 0.75 ppm and molar ratio of [M]0/[I]0/[L]0 was kept constant as 200
:
0.2
:
0.3 (Table 1d). Cheng et al.30 observed that there was no polymerization occurred when the concentration of Cu(0) decreases to 2.5 ppm but in the present study, we observed polymerization with monomer conversion of 25 wt% and Ð 1.29 at 0.15 ppm of Cu(0) nanoparticles concentration (Table 1e). Overall by using Cu(0) nanoparticles of 5 nm, polymerization is very fast with good conversion of monomer by using PMDETA and TMHDA as ligands. It is interesting to note that polydispersity of polymers were narrow by using PMDETA ligand at different molar ratio of [M]0/[I]0/[L]0 and concentration of Cu(0) nanoparticles. But with TMHDA, control over Ð was very poor and high molecular weight of polymers was obtained.
MMA and styrene co-polymerization by SET-LRP using Cu(0) nanoparticles
The copolymerization of MMA and St using Cu(0) nanoparticles as catalyst mediated SET-LRP was carried out at 70 °C with EBriB as an initiator. The incorporation of MMA and St in copolymer has been determined from 1H NMR spectra (Fig. 4(ii)). Further, the narrow molecular weight distribution with low dispersity (Ð) is also observed after co-polymerization (ESI, Fig. S3†). It is significantly different from the homopolymers or block copolymer of this monomers, indicating the formation of random copolymers.35 The peak at 2.85 ppm was characteristic of the –OCH3 groups of MMA moiety bonded to the St indicating the formation of random copolymer of MMA and St.36,37 The aromatic protons (6.6–7.3 ppm, 5H) of St and –OCH3 protons (2.4–3.6, 3H) of MMA repeat units were chosen to calculate the composition of monomers in copolymer by their intensity ratio.38 Reactivity ratio of copolymers was determined by Fineman–Ross method39 using their respective NMR peak intensities. The parameters for calculating reactivity ratios by Fineman–Ross method are given in Table 2. The results were rSt = 0.23 and rMMA = 0.41, respectively (Fig. 6). However, in copolymer of MMA and St in free radical polymerization is rSt = 0.48–0.52 and rMMA = 0.42–0.46.17,40–45 In addition, the extended Kelen–Tüdös method also reported at high conversions.46
Table 2 Parameters of MMA and St copolymer for calculation of reactivity ratioa
Entry |
1 |
2 |
3 |
4 |
5 |
Copolymers obtained at low conversation from different monomer feed compositions ([St]0/[MMA]0 = 1 : 3, 1 : 2, 1.75 : 1, 1 : 1, 3 : 1, 2 : 1). mSt and mMMA refer to the St and MMA composition in the copolymer, respectively. MSt and MMMA refer to the feed compositions of St and MMA monomer, respectively. f = mSt/mMMA, F = MSt/MMMA. |
MMMA |
0.8 |
0.6 |
0.5 |
0.4 |
0.2 |
MSt |
0.2 |
0.4 |
0.5 |
0.6 |
0.8 |
mMMA |
0.71 |
0.62 |
0.58 |
0.45 |
0.26 |
mSt |
0.28 |
0.37 |
0.41 |
0.55 |
0.74 |
f |
0.404 |
0.608 |
0.718 |
1.228 |
1.750 |
F |
0.25 |
0.667 |
1 |
1.5 |
4 |
f/F2 |
6.466 |
1.368 |
0.716 |
0.546 |
0.109 |
f − 1/f |
−2.383 |
−0.588 |
−0.284 |
0.152 |
0.188 |
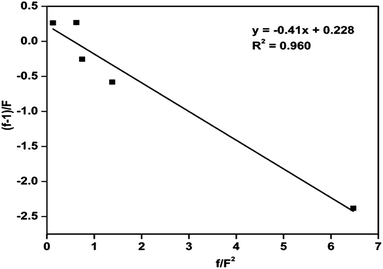 |
| Fig. 6 Fineman–Ross plot of (f − 1)/F vs. f/F2 for St and MMA, Cu(0) nps-mediated SET-LRP. | |
Conclusions
We have demonstrated the first successful SET-LRP of MMA catalyzed by using ex situ Cu(0) nps (ca. 5 nm) as catalyst in biphasic water–toluene reaction system at 25 °C and 70 °C, to monitor the molecular weight, dispersity and kinetics of polymerization. The results provided conclusive evidences: (i) toluene is a favourable solvent for SET-LRP in the presence of small amount of water, (ii) ex situ Cu(0) nps even at a concentration of 0.15 ppm gives reasonably conversion with dispersity 1.29, and drastically reduces the contamination issue of copper. Furthermore, this work provides an efficient process for the copolymerization of MMA and St. Overall; it has been observed that polymerization kinetics follow first order at 25 °C and 70 °C with retention of higher percentage of chain end functionality for further facile chain extension reaction along with good control over molecular weight showing the features of living/controlled radical polymerization.
Acknowledgements
We acknowledge Director, CSIR-Indian Institute of Petroleum (IIP) for his support and encouragement. A. Bansal, V. Panwar, N. Singhal thanks CSIR, India for providing research fellowship. A. Kumar acknowledges UGC, India for the fellowship grant. The authors thank K. L. N. Sivakumar, Raghuvir Singh, Siya Ram, C. D. Sharma and Piyush Gupta of CSIR-IIP for providing SEM, FTIR, UV-Vis, GPC and NMR results, respectively.
Notes and references
- K. Matyjaszewski, Y. Gnanou and L. Leibler, Macromolecular Engineering, Wiley-VCH, Weinheim, Germany, 2007 Search PubMed.
- W. A. Braunecker and K. Matyjaszewski, Prog. Polym. Sci., 2007, 32, 93 CrossRef CAS.
- G. Moad, E. Rizzardo and S. H. Thang, Aust. J. Chem., 2006, 59, 669 CrossRef CAS.
- C. J. Hawker, Acc. Chem. Res., 1997, 30, 373 CrossRef CAS.
-
(a) K. Matyjaszewski and J. Xia, Chem. Rev., 2001, 101, 2921 CrossRef CAS PubMed;
(b) A. Bansal, A. Kumar, P. Kumar, S. Bojja, A. K. Chatterjee, S. S. Ray and S. L. Jain, RSC Adv., 2015, 5, 21189 RSC.
- J. Chiefari, Y. K. Chong, F. Ercole, J. Kristina, J. Jeffery, T. P. T. Le, R. T. A. Mayadunne, G. F. Meijs, C. L. Moad, G. Moad, E. Rizzardo and S. H. Thang, Macromolecules, 1998, 31, 5559 CrossRef CAS.
- M. Ouchi, T. Terashima and M. Sawamoto, Chem. Rev., 2009, 109, 4963 CrossRef CAS PubMed.
- W. Jakubowski and K. Matyjaszewski, Angew. Chem. Int. Ed, 2006, 45, 4482 CrossRef CAS PubMed.
- V. Percec, T. Guliashvili, J. S. Ladislaw, A. Wistrand, A. Stjerndahl, M. J. Sienkowska, M. J. Monteiro and S. Sahoo, J. Am. Chem. Soc., 2006, 128, 14156 CrossRef CAS PubMed.
- B. M. Rosen and V. Percec, Chem. Rev., 2009, 109, 5069 CrossRef CAS PubMed.
- N. H. Nguyen, B. M. Rosen, G. Lligadas and V. Percec, Macromolecules, 2009, 42, 2379 CrossRef CAS.
- S. Fleischmann and V. Percec, J. Polym. Sci. Part A: Polym. Chem., 2010, 48, 4884 CrossRef CAS.
- P. M. Wright, G. Mantovani and D. M. Haddleton, J. Polym. Sci. Part A: Polym. Chem., 2008, 46, 7376 CrossRef CAS.
- E. L. Martin, W. Ian, O. Stephen, D. C. Anne, J. G. Anthony, F. Christopher, C. Remzi Becer and M. H. David, Polym. Chem., 2010, 1, 1086 RSC.
-
(a) K. Matyjaszewski, S. Coca, S. G. Gaynor, M. L. Wei and B. E. Woodworth, Macromolecules, 1997, 30, 7348 CrossRef CAS;
(b) K. Matyjaszewski, N. V. Tsarevsky, W. A. Braunecker, H. Dong, J. Huang, W. Jakubowski, Y. Kwak, R. Nicolay, W. Tang and J. A. Yoon, Macromolecules, 2007, 40, 7795 CrossRef CAS;
(c) C. Y. Lin, M. L. Coote, A. Gennaro and K. Matyjaszewski, J. Am. Chem. Soc., 2008, 130, 12762 CrossRef CAS PubMed.
- Z. Zhang, W. Wang, H. Xia, J. Zhu, W. Zhang and X. Zhu, Macromolecules, 2009, 42, 7360 CrossRef CAS.
-
(a) J. Gao, Z. Zhang, N. Zhou, Z. Cheng, J. Zhu and X. Zhu, Macromolecules, 2011, 44, 3227 CrossRef CAS;
(b) H. Zhang, K. Hong, M. Jablonsky and J. W. Mays, Chem. Commun., 2003, 1356 RSC.
- G. Lligadas and V. Percec, J. Polym. Sci. Part A: Polym. Chem., 2008, 46, 2745 CrossRef CAS.
- V. Percec and C. Grigoras, J. Polym. Sci. Part A: Polym. Chem., 2005, 43, 5609 CrossRef CAS.
- V. Percec, A. V. Popov, E. Ramirez-Castillo, M. Monteiro, B. Barboiu, O. Weichold, A. D. Asandei and C. M. Mitchell, J. Am. Chem. Soc., 2002, 124, 4940 CrossRef CAS PubMed.
- V. Percec, A. V. Popov, E. Ramirez-Castillo and O. Weichold, J. Polym. Sci. Part A: Polym. Chem., 2003, 41, 3283 CrossRef CAS.
- T. Jessica, H. Ben, W. Andrew, H. Simon and P. Sebastien, Polym. Chem., 2010, 1, 420 RSC.
- G. Lligadas and V. Percec, J. Polym. Sci. Part A: Polym. Chem., 2008, 46, 6880 CrossRef CAS.
- G. Lligadas, B. M. Rosen, M. J. Monteiro and V. Percec, Macromolecules, 2008, 41, 8360 CrossRef CAS.
- N. H. Nguyen, B. M. Rosen, X. Jiang, S. Fleischmann and V. Percec, J. Polym. Sci. Part A: Polym. Chem., 2009, 47, 5577 CrossRef CAS.
- Q. Zhang, Z. Zhang, W. Wang, Z. Cheng, J. Zhu, N. Zhou, W. Zhang, Z. Wu and X. Zhu, J. Polym. Sci. Part A: Polym. Chem., 2011, 49, 4694 CrossRef CAS.
- F. Fenwick, J. Am. Chem. Soc., 1926, 48, 860 CrossRef CAS.
- J. P. Desmarquest, C. Trinh-Dinh and O. Bloch, J. Electroanal. Chem., 1970, 27, 101 CrossRef CAS.
- Y. Xiong, Y. Wang, Q. Xue and X. Wu, Green Chem., 2011, 13, 900 RSC.
- Y. H. Yu, X. H. Liu, D. Jia, B. W. Cheng, F. J. Zhang, H. N. Li, P. Chen and S. Xie, J. Polym. Sci. Part A: Polym. Chem., 2013, 51, 1468 CrossRef CAS.
- C. Feng, Z. Shen, Y. Li, Y. Zhang, G. Lu and X. Huang, J. Polym. Sci. Part A: Polym. Chem., 2009, 47, 1811–1824 CrossRef CAS.
- C. Waldron, Q. Zhang, Z. Li, V. Nikolaou, G. Nurumbetov, J. Godfrey, R. McHale, G. Yilmza, R. K. Randev, M. Girault, K. McEwan, D. M. Haddleton, M. Droesbeke, A. J. Haddleton, P. Wilson, A. Simula, J. Collins, D. J. Lloyd, J. A. Burns, C. Summers, C. Houben, A. Anastasaki, M. Li, C. R. Becer, J. K. Kiviaho and N. Risangud, Polym. Chem., 2014, 5, 57 RSC.
- P. M. Wright, G. Mantovani and D. M. Haddelton, J. Polym. Sci. Part A: Polym. Chem., 2008, 46, 7376 CrossRef CAS.
- N. H. Nguyen, B. M. Rosen and V. Percec, J. Polym. Sci. Part A: Polym. Chem., 2011, 49, 1235 CrossRef CAS.
- Y. Kotani, M. Kamigaito and M. Sawamoto, Macromolecules, 1998, 31, 5582 CrossRef CAS.
- J. C. Randall, Polymer Sequence Determination, Academic, New York, 1977, p. 109 Search PubMed.
- M. Opresnik and A. Sebenik, Polym. Int., 1995, 36, 13 CrossRef CAS.
- P. Na Songkhla and J. Wootthikanokkhan, J. Polym. Sci. Part B: Polym. Phys., 2002, 40, 562 CrossRef.
- M. Finema and S. D. Ross, J. Polym. Sci., 1950, 5, 259 CrossRef.
- T. Fukuda, Y. D. Ma and H. Inagaki, Macromolecules, 1985, 18, 17 CrossRef CAS.
- R. X. E. Willemse and V. A. Herk, J. Am. Chem. Soc., 2006, 128, 4471 CrossRef CAS PubMed.
- M. Johnson, T. S. Karmo and R. Smith, Eur. Polym. J., 1978, 14, 409 CrossRef CAS.
- I. A. Maxwell, A. M. Aerdts and A. L. German, Macromolecules, 1993, 26, 1956 CrossRef CAS.
- J. J. Uebel and F. J. Dinan, J. Polym. Sci. Part A: Polym. Chem., 1983, 21, 2427 CrossRef CAS.
- S. Pal, B. Banoth, G. Rahithya, A. Dhawan and P. De, Polymer, 2012, 53, 2583 CrossRef CAS.
- S. G. Roy, K. Bauri, S. Pal, A. Goswami, G. Madras and P. De, Polym. Int., 2013, 62, 463 CrossRef CAS.
Footnote |
† Electronic supplementary information (ESI) available: Fig. S1: UV-Vis spectra, Fig. S2: FTIR spectra, Fig. S3 GPC curve of PMMA-co-PSt. See DOI: 10.1039/c7ra00368d |
|
This journal is © The Royal Society of Chemistry 2017 |
Click here to see how this site uses Cookies. View our privacy policy here.